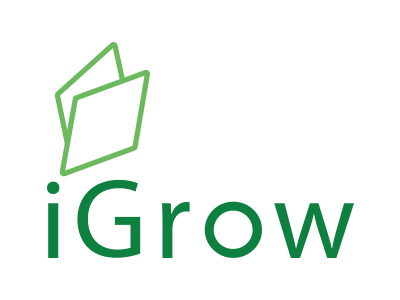
Welcome to iGrow News, Your Source for the World of Indoor Vertical Farming
May 18th, 9 am EST - Webinar On How To Invest In CEA With Confidence
Agritecture is hosting a series of webinars, starting with How to invest in CEA with confidence
Agritecture is hosting a series of webinars, starting with How to invest in CEA with confidence. The CEA sector is heating up and is expected to grow 5x over the next 10 years. Investment in CEA has surpassed $2.0B across North America and Europe. Join Henry Gordon-Smith, Founder & CEO at Agritecture, for this 1-hour live webinar to learn more about how to invest confidently in the CEA industry.
How To invest In Controlled
Environment Agriculture With
Confidence
May 18 - 9 am EST
The lineup of speakers include:
Louisa Burwood Taylor, Head of Media & Research at AgFunder
Robert Glanville, Senior Advisor at REG Consulting LLC
Andrew Carter, Co-Founder & CEO at Smallhold
Darren Thompson, CFO at Bowery Farming
Djavid Amidi Abraham, Director Of Consulting at Agritecture
Click Here To Register!
For more information, you can check out our events listing here.
Agritecture
www.agritecture.com
RSVP Reminder: April Indoor Ag Science Cafe - April 20th Tuesday 10:00 AM Eastern Daylight Time
Indoor Ag Science Cafe is an open discussion forum, planned and organized by OptimIA project team supported by USDA SCRI grants
April Indoor Ag Science Cafe
April 20th Tuesday 10:00 AM Eastern
Please Sign Up!
"Plant Factories and Indoor Farming
Innovations in Japan"
Vertical Farming World Congress Raises Expectations
Plans have been announced for the 2nd Vertical Farming World Congress, which will take place on 20-22 September 2021. The event will be available online, with the aim for as many delegates as possible to meet in person at London Heathrow
Plans have been announced for the 2nd Vertical Farming World Congress, which will take place on 20-22 September 2021. The event will be available online, with the aim for as many delegates as possible to meet in person at London Heathrow.
With the theme of ‘Raising Expectations’, the conference sessions offer numerous highlights including:
Industry leadership with InFarm, Kalera, and YesHealth
Market opportunity with HortAmericas, Rabobank and VeggiTech
Customer and investor panels featuring Metro and S2G Ventures
Regional pioneers from AgroUrbana in Chile to 808 Factory in Japan
Nutrition and crop development with 80 Acres and Vertical Field
Technology and service development with Grow Group IFS and Swegreen
Industry policy discussion with Association for Vertical Farming, Farm Tech Society, Japan Plant Factory Association, and UK Urban AgriTech.
There will also be a range of other attractions, notably:
Presentation of the 2021 Vertical Farming World Awards covering crops, technology, sustainability, and commercial initiatives
Visits to various vertical farms online and to Vertical Future’s new Mini Crops operation in East London
Introductory workshop on planning an urban farming business with Agritecture.
The Congress is sponsored by Vertical Future and the Awards are sponsored by Cultivatd.
“This will be the stand-out event of the year for vertical farming, which has attracted so much investor and consumer attention in the past 12 months,” commented Richard Hall, Chairman of Congress organizers Zenith Global, the global food and drink experts. “Vertical farming chimes perfectly with concerns for fresh nutrition locally, providing new solutions on sustainability and to address complicated supply chains.”
“Last year, delegates said they would be happy to stay online for reasons of convenience and affordability as well as ease of networking and access to the recording. Many, however, still want to meet in person, so we shall be offering both options, with a guarantee of a refund for anyone unable to travel at the last minute due to national government coronavirus restrictions,” he concluded.
Full program and booking details for the Congress and entry information for the Awards are available at zenithglobal.com/events or by emailing events@zenithglobal.com.
CANADA (YT): Tackling Food Insecurity Above The 60th Parallel
ColdAcre Food Systems is based in Whitehorse, Yukon, one of the northernmost provinces in Canada. The company was incorporated in August 2019 and specializes in controlled environment agriculture.
In the northernmost territories of Canada, agricultural development is underway but must contend with the cold climate, variable photoperiod and other environmental challenges. It comes as little surprise, then, that interest in controlled environment agriculture is on the rise. ColdAcre Food Systems is one of the companies that supports this endeavor and has installed multiple growing systems in northwestern Canada.
ColdAcre Food Systems is based in Whitehorse, Yukon, one of the northernmost provinces in Canada. The company was incorporated in August 2019 and specializes in controlled environment agriculture. Prior to its incorporation, ColdAcre primarily sold retrofitted shipping containers and also operated its own container farm to supply the Whitehorse market with fresh greens and herbs.
According to chief executive officer Carl Burgess, “the original intent was to sell and provide growing systems but we immediately identified an opportunity and a need to demonstrate commercial production north of the 60th parallel year-round.”
With its incorporation in 2019, ColdAcre thus based itself on four pillars:
Growing produce for the Whitehorse market and beyond
Selling prefabricated and custom growing systems for its clients
Providing consultation and pathfinding services
Active learning and engagement in various projects.
Growing produce for the Whitehorse market
When ColdAcre first began producing greens and herbs, the company started with three dozen products but have since narrowed its product line in order to have a robust supply and client demand. ColdAcre has also recently begun producing mushrooms. Explaining the Yukon’s consumer base, Carl says that the territory is the size of Spain yet is home to only 40,000 people. Whitehorse is the territory’s capital and its businesses service much of the territory, as well as southern Alaska, northern British Columbia and the western Northwest Territories.
As such, Whitehorse acts as an important hub for northern residents and has a relatively robust food demand. According to Carl, “some people drive 1,000 km to buy goods and groceries in Whitehorse a few times a year. That said, the Yukon only produces 1% of the food that is purchased and consumed in the territory.”
Importing most of its consumables carries the double burden of a heavy carbon footprint and limited nutritional quality. “When comparing the quality of fresh produce between Vancouver and Whitehorse, there is a significantly lower quality in the Yukon, which is only heightened when you go further north. Producing locally also virtually eliminates waste and the carbon footprint of production,” says Carl.
Selling growing systems
ColdAcre also continues to sell prefabricated and custom growing systems for clients through Canada’s northwestern region. While the company began with CropBox and has had success doing so, ColdAcre has found that its clients typically require more customization. Moreover, working with an American company has subjected ColdAcre to a higher degree of volatility with respect to changes in the dollar and availability of equipment, according to Carl.
With respect to its technology, Carl also explained that ColdAcre’s technology “is not necessarily unique, but that the skillset and assembly is. In the Yukon, we face the challenge of growing lettuce when it’s 40°C outside in the summer or down to -53°C. We address these extremes using high-tech and smart-tech solutions. We customize the whole management and contingency for potential crises specific to a client or area.”
Consultation and active learning
ColdAcre has also committed to providing consultation and pathfinding services to growers regardless of whether the grower is using a ColdAcre system or not. As Carl explains, “we think that our growing challenge are everyone’s challenges so if we can solve ours, we’d like to share.”
ColdAcre also has multiple research partners throughout northern Canada and while the projects are generally northern-based, the results have applications in various settings.
2020 and 2021 at a glance
In all four pillars, ColdAcre has reported increased interest in the past year. The fragility of Yukon’s food system was heightened by the COVID-19 pandemic and ensuing supply chain disruptions. As such, the interest in local food production and stabilized food system has surged in the territory. ColdAcre’s production has been sold out since October 2019 and the company will be tripling its production in the coming months. According to Carl, ColdAcre’s proximity to market channels allows the company to compete with imported commodities from California and Mexico and demand a reasonable premium. Similarly, the company is reportedly experiencing an increased demand for its systems for residential, office, and educational purposes.
Most recently, ColdAcre shipped a 53-foot container farm to Inuvik, a community in the Arctic Circle and whose community greenhouse will use the shipping container to produce fresh produce year-round.
For more information:
Carl Burgess, CEO
ColdAcre
carl@coldacre.ca
www.coldacre.ca
Publication date: Fri 9 Apr 2021
Author: Rebekka Boekhout
© VerticalFarmDaily.com
VIDEO: Indoor Farming Powered By Robotics And Technology - Plenty
Indoor farming powered by robotics and technology is enabling one California company to grow 'Plenty' of flavorful nutrient-rich and pesticide-free produce
Author: abc10.com
April 6, 2021
iFarm Partners With Contain Inc., Increases Accessibility of Vertical Farms
Dedicated to securing lease financing for indoor growers, Contain Inc. works with private lenders to facilitate leases and create custom insurance solutions
On February 11th, 2021, iFarm officially became a partner with and an official vendor of Contain Inc., an indoor agriculture fintech platform operating in North America and Europe that connects indoor growers with the resources they need. Growers now have the opportunity to lease iFarm vertical farms through Contain Inc.
Dedicated to securing lease financing for indoor growers, Contain Inc. works with private lenders to facilitate leases and create custom insurance solutions. The company organises financing for all indoor farming needs, including LED, greenhouse equipment, and entire plant growth systems like vertical farms.
Why Lease Financing is Important
Building or equipping a vertical farm can require significant amounts of capital, yet indoor growers typically lack financing options when compared to their outdoor farming counterparts. 75% of indoor growers are looking for funding, and many will not receive it from traditional agriculture banks and traditional business banks as farm lending in the United States declined at an average pace of 2% throughout 2020. While it is slightly easier to seek financing options in Europe, there is still great room for improvement.
By becoming an equipment vendor, iFarm has made its vertical farms more accessible to those who are interested in vertical farming but face the obstacle of high capital investment. Through Contain Inc., indoor growers can now lease iFarm’s vertical farms and LED systems without a need for high investment. By acquiring vertical farming equipment more easily, prospective indoor farmers can also scale their operations more quickly and cost-effectively.
How It Works
If you would like to start your indoor farming journey with iFarm, but need financial support, simply sign up to Contain Inc.’s exclusive leasing platform and complete a simple application form. The application requires you to input company basics, financial essentials (i.e. what amount is needed for lease), primary equipment to be purchased, and principal financial institutions. The algorithms can match you to a pool of 28 equipment and financial lenders, ranging from small shops to some of the largest banks in the world. The minimum lease size is typically around $75,000 with no upper limit. Contain Inc. will review your application and decide whether you are eligible for financial support.
Contain Inc. also provides a “Leasing Calculator”, which is a short quiz to help growers figure out their odds of obtaining lease financing offers through Contain Inc.
Get in touch with iFarm today to discuss how to invest in or to lease vertical farming technology.
Entrepreneurs See Hydroponics As Farming Solution In Libya
Conventional Agriculture Struggles In Mostly-Desert North African Country
Conventional Agriculture Struggles
In Mostly-Desert North African Country.
11/04/2021
TRIPOLI--Under a yellow tarpaulin stretched over an arched metal frame, Siraj Bechiya and his partner inspect their hydroponically-grown lettuce, pioneers of the method in mostly-desert Libya where conventional agriculture struggles.
Zip ties, punctured plastic cups as pots and PVC tubing bought in DIY shops hold the precious crops at “Green Paradise” — so dubbed by the two young Libyan entrepreneurs spearheading the project.
But the ad hoc nature of the materials hasn’t stopped the plants from thriving, their long white roots nourished by water rich with nutrients and oxygen.
Bechiya and his partner, Mounir, have been working tirelessly on their project for months in the small town of Qouwea, 40 kilometres east of the capital Tripoli, erecting a tunnel-shaped greenhouse surrounded by breeze-block walls on a semi-arid site.
Their hope is to demystify hydroponic farming, which “guarantees a good yield in small spaces”, uses little water and doesn’t need pesticides, 20-year-old Bechiya said.
Soilless farming has gained ground in many countries but is still in its infancy in Libya.
But in a country whose territory is 90 percent arid desert, the method could offer a path toward more food self-sufficiency, Bechiya believes.
Challenges to farming
Agriculture remains a marginal sector in Libya, where the economy is dominated by hydrocarbons, the country boasting the most abundant oil reserves in Africa.
Arable land barely makes up three percent of Libya’s territory and is under threat, as rapid urbanisation eats up the fertile strip along the Mediterranean coast.
Another major challenge to farming in Libya is the lack of water where agriculture needs it most.
The Great Man-Made River — a pharaonic project realised by the toppled long-time ruler Muammar Gadhafi more than 30 years ago — carries drinking water pumped from groundwater tables in the south to the northern cities where most Libyans live.
But this resource is not infinite, and the GMMR’s network has been heavily damaged in the decade of conflict that has ravaged Libya since Kadhafi’s ouster in a 2011 NATO-backed uprising.
In the face of these challenges, Bechiya and Mounir set out to train in hydroponics two years ago in neighbouring Tunisia.
“When we came back, it was imperative that we move from theory to practice,” Bechiya said.
“We started with some vegetables in the house and we were surprised by people’s enthusiasm.”
New Techniques
In theory, hydroponics can guarantee higher yields and profits than conventional farming, which is at risk from weather, water shortages, and pollution from unregulated pesticide use.
“With more space in the greenhouse, the idea was able to take off. We will continue to develop it… and improve quality,” said Bechiya, as he measured the acidity of the water feeding his young lettuce.
“Libyan consumers don’t want produce full of pesticides anymore, but organic produce,” he added.
While not saturated with pesticides, hydroponic products, poo-pooed as bland by detractors, generally are not labeled organic.
Agronomist Abdelkafi al-Amrouni said the method “paves the way toward the introduction of new agricultural techniques in Libya” to compensate for water shortages.
There are still obstacles to widespread hydroponic use, however.
“It’s complicated and very expensive to get supplies in Libya,” even as the country tries to turn the page on a decade of chaos, Amrouni said.
Such costs could make the products ultimately prohibitively pricey.
But Bechiya is not deterred.
“You have to be patient and believe in your idea,” he said.
Lead photo: Project manager checks a plantation of hydroponically grown lettuce, in a greenhouse in the small town of Qouwea, about 40 kilometres east of Libya’s capital Tripoli. (AFP)
USA: Local Farm Brings Hope To Food Desert
A hydroponic produce farm in Indianapolis is filling a need in food deserts around the city. Food deserts are areas where grocery stores aren’t easily accessible. More than 200,000 people live in food deserts in Indy, according to a study published by SAVI
Q&A: Mario Vitalis
April 13, 2021
Mario Vitalis, farmer, owner, and founder of New Age Provisions, holds plants grown on his farm.
INDIANAPOLIS — A hydroponic produce farm in Indianapolis is filling a need in food deserts around the city.
Food deserts are areas where grocery stores aren’t easily accessible. More than 200,000 people live in food deserts in Indy, according to a study published by SAVI.
Mario Vitalis, farmer, owner, and founder of New Age Provisions farm, uses advanced hydroponics and vertical planting to grow year-round.
It all starts inside a shipping container on an old car lot on East 10th Street. A step inside transports visitors to a lush, green garden of produce. A variety of herbs, leafy greens, microgreens, and hemp are grown inside.
The location allows Vitalis to provide fresh produce to the community, one of the city’s many food deserts. The farm also provides produce to restaurants in Indianapolis.
“I’ve always known the city life — but there is a nagging desire to get back to my roots,” Vitalis said. “As an African American, my roots made it from slaves in the field, to sharecroppers in the South, to farming in the city.
“As a descendent of slaves, this farm enables me to get back to the type of living where our people once lived off the land. Having an urban farm allows me to connect to a long history of farming that has been forgotten.”
Vitalis shared his story with AgriNews.
Tell me a little bit about your farm.
“We are a hydroponic commercial farm. We officially started farming in August 2020.”
What was your inspiration to grow things?
“I wanted to be involved in agriculture, to be able to provide fresh food to the community independent of the supply chain, and independent of herbicides, pesticides, and contaminants.”
Indiana has several food deserts. Did that inspire you to fill a need in the community?
“Yes, it did. It provides us with the equipment to do so, as well. We’re the first company in Indiana to own this piece of equipment, the Freight Farms Greenery. We’re currently the only African American owner of the equipment. We want to be able to provide food and also provide a new way of farming. We want people to see it and have access to it.”
How does the farming system work?
“It’s called a Greenery and it’s built by Freight Farms, based in Boston. It’s essentially a hydroponic farming system in a 40-foot shipping container. If you can imagine those shipping containers that go up and down the highway, you go inside of one of these and grow vegetables. It has everything you need to do that. It has a seedling table and growth tower with different types of hydroponic methods.”
Basil grows at a hydroponic produce farm in Indianapolis.
What are some of the features of the technology?
“It has its own dosing system to control nutrients. You can control humidity, temperature and pH levels. You can check your settings and programming on a computer. There’s an app that goes with it, as well. So, you can control your farm from your phone. The technology is state of the art.”
What are some of the challenges you’ve faced as a new farmer?
“I think the biggest challenge is developing a market and getting our name out there. There’s also a learning curve to farming. I didn’t have any experience. So, I had to learn what to do and how to operate.”
What do you enjoy most about growing things?
“Seeing the plant life cycle from seed to seedling into a full plant. I also enjoy the environment. Since we’re in an enclosed environment, we can grow year-round and it’s always 65 degrees.”
Do you have any advice for minorities interested in farming?
“Right now there are so few minority farmers in general. For African American farmers, the best thing they can do is get land and find ways to cultivate the land or make use of it. Good land is becoming a scarce resource. If they’re interested in farming, there’s funding available from USDA for Black and minority farmers. There are different avenues out there. But it all starts with land and a business plan. After that you just have to have motivation and knowledge to do it.”
Anything else you’d like to share about your farm?
“Our farm is local on the east side of Indianapolis. We grow hydroponically without herbicides, pesticides or contaminants.”
How can people purchase your products?
“They can go online to our website www.newageprovisions.com. We deliver. Or, you can purchase through Market Wagon or Hoosier Harvest Market.”
US: VIRGINIA - Senior Project Brings Daily Salads For School Lunches
Students Set Up A Hydroponic System In The School Lab
Two Upper School Seniors at the Hampton Roads Academy (HRA) constructed a hydroponic unit for the school's hydroponics lab. About a year ago two students, Ava and Cooper, were asked to construct a new hydroponics unit for the school. They immediately agreed to work on the project, with their first task to create a new system for the school's 1,000 sq. ft. 'Martha H. Patten Hydroponics Lab'. After approval, they picked up the supplies needed and set up the system.
Ava and Cooper set up the hydroponic system by themselves, making use of the additional growing lights, nutrient dosers, Rockwool, and water pumps. However, the project wasn't without struggles. At one point, the system turned out to have some leaks and a PCV pipe was disconnected from the system. They later improved the system to remedy the problems.
The first harvest was successfully done and enough for 200 salads. Throughout the year, all harvested produce went directly to HRA's school lunches. During their project, Ava and Cooper made it their goal to educate other students at the HRA on hydroponic farming. After a while, many students had expressed their interest in the hydroponic lab. Given that response, the seniors held information sessions to teach students how they could get involved.
Ava and Cooper have said to be thankful for the opportunity to create a hydroponic lab for the school. Their main goal to keep educate and inspire others to create their own hydroponic system as they see it as 'the future of sustainable farming.'
Click on the video below to see the complete story.
For more information:
Hampton Roads Academy
739 Academy Lane
Newport News, VA 23602
+1 (757) 884-9100
admissions@hra.org
www.hra.org
6 April 2021
Author: Rebekka Boekhout
© VerticalFarmDaily.com
Lead photo:
Ava and Cooper at the 'Martha H. Patten Hydroponics Lab
Taking Indoor Farming Operations To New Heights
Conveyor systems technology can help indoor farming operations grow to new heights while improving productivity, efficiency and ergonomics, according to Ultimation Industries LLC, a leader in conveyor technology and automation for over 30 years
Conveyor Systems Technology From Ultimation Industries
Conveyor systems technology can help indoor farming operations grow to new heights while improving productivity, efficiency and ergonomics, according to Ultimation Industries LLC, a leader in conveyor technology and automation for over 30 years.
“Harnessing unused vertical space through the use of motorized and overhead conveyors helps indoor farmers maximize their footprint while achieving greater efficiencies in food production and improved ergonomics,” said Richard Canny, president of Ultimation Industries.
Customized and automated
Ultimation is a provider of customized conveyor and automation solutions for indoor agriculture. They design and build systems for vertical farms of all sizes, including a major system for a West Coast-based vertical farming system which is among the world’s largest.
In a typical indoor agriculture facility, workers move through the growing area to plant, monitor and harvest crops. Multi-tier operations may use time-consuming and potentially dangerous lifts to take employees up and down as they perform their daily tasks. Conveyor technology can move plants through automated systems as they grow, bringing them down to the operator level when needed for more efficient, and ergonomically friendly, handling.
Multiple choice
The conveyors and industrial automation equipment used in vertical farming include many of the traditional conveyor types such as gravity roller, belt, and skate wheel or flow rail conveyors. These conveyors are among the most versatile because they help reduce the manual labor of carrying items by hand.
Larger systems use vertical elevators or Power and Free conveyors. Power and Free conveyors are the ultimate in space and volume optimization for vertical farming systems as they enable tight concentration of product in some areas while also enabling separation of the products for movement to processing areas.
Reducing costs
More recently, the technology used in larger vertical farming systems is including motorized and overhead conveyors. These systems take advantage of unused vertical space above a working area and bring plants down to an operator level when needed.
“Using robotics and conveyors has been shown to help vertical farms maximize their growing operations and reduce costs. We believe that indoor farming systems are best optimized through a balanced use of low-cost material handling systems for slow-growing areas. They are complemented by more sophisticated conveyors and other devices for faster moving material handling tasks,” said Canny.
Ultimation’s indoor agriculture solutions range from simple flow rail systems up to more comprehensive systems for larger indoor vertical farming facilities. The company's systems meet food-safe requirements for lubricants, oils, and greases.
“As indoor farmers work to achieve greater efficiencies in food production, conveyor systems technology is likely to be part of any economically viable and scalable solution,” said Canny.
For more information:
Kali Cresent, Sales, and Marketing Manager
Ultimation Industries, LLC
kcresent@ultimation.net
+1 586-771-1881
www.ultimation.net
9 Apr 2021
Explore The Sixth Edition of Clima, Powered by IGS
In this edition, we look at why precision farming and Controlled Environment Agriculture (CEA) techniques are becoming more mainstream, and the skills and talent required to make this approach a success
In this edition, we look at why precision farming and Controlled Environment Agriculture (CEA) techniques are becoming more mainstream, and the skills and talent required to make this approach a success. Technology is having a greater impact on agriculture than ever before, and this is only set to increase. It will bring with it a wider and more advanced agricultural ecosystem that requires a skilled, knowledgeable, and committed workforce, with as great an appetite for innovation and capacity to problem solve as any generation before.
Discover more on this topic in the sixth edition of Clima today.
Bringing future talent to Agriculture 4.0
We discuss the emerging influences on education and skills development across Agriculture and Horticulture with two senior leaders from Scotland’s Rural College (SRUC). We spoke to Professor Fiona Burnett, Head of Connect for Impact in SRUC’s Knowledge and Information Hub, and Ruth Vichos, Lecturer in Horticulture, about the evolution of Agriculture 4.0, and how technology is impacting skills evolution and teaching mechanisms.
Listen To The Full Interview
Flushing Hydroponic Systems: Nutrient Imbalance, Waste, And An Alternative Solution
We recommend that hydroponic growers flush their systems every month to every few months, depending on the type of system they’re running. But why? We’re also fans of the recirculating system because it conserves water and nutrients
We recommend that hydroponic growers flush their systems every month to every few months, depending on the type of system they’re running. But why? We’re also fans of the recirculating system because it conserves water and nutrients.
Article from | ZipGrow
04/06/21
Is flushing hydroponic systems wasteful?
We recommend that hydroponic growers flush their systems every month to every few months, depending on the type of system they’re running. But why? We’re also fans of recirculating system because it conserves water and nutrients, so it seems counterintuitive to dump gallons of nutrient solution every few months.
Let’s talk about why this is necessary and how you can practice conservation.
The problem: nutrient imbalance
The main reason for flushing a hydroponic system is a nutrient imbalance. Hydroponic fertilizers are specifically formulated for specific crops (you can buy nutrients for a type of crop, like greens or flowers), but each farmer grows a different combination of crops in different conditions, and the ratios in which plants take up nutrients is usually just a little bit off.
This nutrient imbalance is also affected by metal components if the system has any. Zinc and aluminum ions can cause toxicities if they accumulate over time. While it’s easy to just use plastic tanks and fittings or to coat the metal components in your system with epoxy to reduce leaching, sometimes the presence of metal is unavoidable.
Another reason that growers flush their system is a hygiene practice. Algae and many plant pathogens can survive in the water, and regular cleaning with a mild bleach or peroxide solution or another oxidizing agent is a preventative measure.
Two solutions: flushing and mass balancing
Most hydroponic growers take care of this nutrient balance problem by flushing the system and starting from scratch with nutrients. This is certainly the easiest method. Be sure to check with your local town or municipality to follow the correct disposal procedure.
This practice can have a downside, however, because often the solution dumped from a system when it is being flushed isn’t used elsewhere. This can be wasteful.
The alternative to flushing a hydroponic system is to learn to mass balance. To do this, growers would get their water tested for individual nutrient levels. This usually has to be done through a lab.
Then the grower would adjust each individual nutrient to its proper level.
The reason that many growers choose to flush over mass balancing is that lab tests can be pricey (you’ll probably have to pay at least $50, and sometimes up to $500). Still, this option can be cost-effective, depending on the size of the system and access to lab testing.
Ultimately, how you choose to deal with a nutrient balance is up to you.
The content & opinions in this article are the author’s and do not necessarily represent the views of AgriTechTomorrow
Indoor & Vertical Farming, Monitoring & Growing Fertilizer, Hydroponics
Vertical Farming: A Solution To Waste And Inefficiency In The Food Supply Chain?
The global food supply chain is in trouble. The coronavirus pandemic is only the latest crisis to highlight the inefficiencies and spotty reliability of the traditional model for getting food from farm to consumer
April 12, 2021
Robert J. Bowman, SupplyChainBrain
The global food supply chain is in trouble. The coronavirus pandemic is only the latest crisis to highlight the inefficiencies and spotty reliability of the traditional model for getting food from farm to consumer. Repeated instances of contamination reveal inadequacies in quality control and the tracking of product throughout the supply chain. And environmental concerns are raising serious questions about the impact of large-scale farming on the land, water, and air.
There’s a clear need for alternative methods of food production. One is vertical farming, a system of growing crops in stacked layers, spaced 24 to 36 inches apart, usually in greenhouse environments. Vertical farms can be constructed within any type of confined space, including dedicated buildings, shipping containers and even abandoned mineshafts. The equivalent of 60 acres of produce can be squeezed into a single greenhouse, with layers stacked six levels or more high.
Further advantages of vertical farming include complete protection from weather and crop pests, without the need for pesticides or other chemicals, and drastic reductions in water use. A pound of lettuce that requires 41 gallons of water with conventional farming needs just two gallons with vertical farming — in all, up to 99% less water than field-grown produce.
One such system is in operation outside Boston, Massachusetts by Crop One, which markets its products under the FreshBox Farms brand. In business for eight years, Crop One claims to be the oldest vertical farmer in North America, in terms of continuous commercial production.
Crop One grows a wide variety of leafy produce, including lettuce, arugula, basil, and spinach. From its location in Millis, Massachusetts, it supplies sellers within a radius of approximately 100 miles, with a presence in more than 35 grocery stores in the Northeast, according to chief executive officer Craig Ratajcyzk.
The location was chosen to cut down on the large volumes of produce that are typically shipped into the Boston area from California, Arizona, Texas, and South and Central America. “Those are really long supply chains,” Ratajcyzk says. “Right now, we’re within an hour’s drive of all the markets we serve.” Crop One also sources its seed stock locally, he adds, although he acknowledges the need to diversify supply in order to reduce the risk of supply-chain disruptions.
Indoor farming allows Crop One to grow to produce all year round, Ratajcyzk says. Currently, its output stands at around three tons a day, serving 10 customers in the Boston area and an overseas account that in turn sells to some 20 retailers.
The company has big ambitions to expand its production and marketing reach, and Ratajcyzk sees no problem in scaling up. Currently, he says, “the whole CEA [controlled environmental agriculture] industry represents a small fraction of the global demand market.” But recent storms and cold weather in large portions of the U.S. have highlighted the need for a method of farming that isn’t susceptible to the whims of Mother Nature.
“The industry is growing substantially,” Ratajcyzk declares, with producers increasingly being drawn to a method of farming that dramatically boosts crop yield within a limited space.
The technology can even extend to fruit-bearing trees. “A traditional orange tree maybe 15 or 20 feet,” Ratajcyzk says. “Why not a 10-foot tree producing twice as many oranges?”
The chief downside of vertical farming at the moment is one of cost. The price of an initial building containing the equivalent of a 60-hectare farm has been estimated at $100 million. Expenses include heavy energy consumption for supplemental lighting, temperature and humidity controls, fertilizer, and maintenance of proper carbon dioxide levels.
A Cornell University study from 2014 called vertical farms “pie in the sky,” estimating that a single loaf of bread containing wheat grown in a vertical farm would cost $27. Current economics would therefore appear to limit vertical farming to high-end products, although producers are banking that costs will plummet as the technology catches on. The net environmental advantages should also serve to boost its popularity in the coming years.
Vertical farming is “small, but growing every day,” says Ratajcyzk. “It’s a difficult model to establish, but if you’ve been around for five years-plus, then you have a higher probability of success.” He’s hoping for federal, state, and local support of the fledgling technique.
“I can’t really think of a downside to this industry,” he says.
Lead photo: Photo: Bloomberg
USA: Delaware Entrepreneurs Start Growing Crops In Water. Will Hydroponic Farms Catch On?
Bill Jordan of Millsboro is an accidental farmer who's growing crops without soil. “I was going to make alcohol from corn or peaches to supplement fuel when fuel prices got stupid,” Jordan recalled, but he quickly realized that was not profitable
Delaware News Journal
Bill Jordan of Millsboro is an accidental farmer who's growing crops without soil.
“I was going to make alcohol from corn or peaches to supplement fuel when fuel prices got stupid,” Jordan recalled, but he quickly realized that was not profitable.
As part of his research, though, he saw that some hydroponic farms use what’s left of the corn or peaches from the alcohol-making process as a fertilizer.
“That’s what led me to it,” he said.
About 15 years ago when he lived in Maryland, he started taking courses on hydroponics and visiting hydroponic farms. He built his own greenhouse and supplemented his income by building greenhouses for others.
After moving to Delaware, he started Fresh Harvest Hydroponics in Millsboro, specializing in a variety of hydroponically-grown lettuces and herbs that are pesticide-free and herbicide-free.
The plants are raised in three climate-controlled greenhouses. The largest has the capacity to grow 50,000 heads of lettuce at one time.
Before the pandemic, he was selling to wholesalers like Sysco and Teddy Bear Fresh, along with Hocker’s grocery stores in Sussex County and restaurants like Fager’s Island in Ocean City, Maryland.
“COVID really hurt us,” Jordan said. “A lot of restaurants just are not buying. Right now, we’re just doing farmers markets and onsite sales, trying to keep our head above water.”
He and one employee are able to maintain the operation, but before the pandemic, the business had several other employees.
However, Jordan said hydroponics has been a profitable business.
“It’s done well for me. It cost me a certain amount to start, but I had it paid off in about a year,” he said. “If COVID ever lifts enough, if people aren’t scared to go back to restaurants, I’ll do pretty well.”
He’s convinced that the indoor crop is superior to field grown.
“Hydroponics can grow bigger, faster, and healthier plants,” he said. “The taste is better. My basil is much stronger than field-grown because it has the right nutrients every day. We test our water on a daily basis.”
Christel Folke is an applied agriculture instructor at the Owens Campus of Delaware Technical and Community College in Georgetown. She said while hydroponic start-up and maintenance costs are the main hurdles, the process has a long list of advantages.
“It’s a controlled environment. The grower has complete control of the lighting, heat, humidity, water, and nutrients. A lot of diseases usually come from the soil, but with hydroponics, you eliminate most of that risk. You still have some pests and disease, but it is easier to control, and we use natural methods,” Folke said, speaking about the college’s hydroponic system.
Saving water is another plus because the water is targeted at the roots, with much less evaporation compared to overhead irrigation outdoors.
The plants have a longer shelf life, Jordan said. Some hydroponic growers like him sell plants with the roots.
“With the root system attached, lettuce can last two weeks or more,” he said. “The shelf life on hydroponics crushes anything else.”
Fuel your hometown's passion and plug into the stories that define it.
Like with other greenhouse operations, farmers can grow year-round if they have heating and cooling systems.
Hydroponics is starting to attract more attention in Delaware.
‘Life-changing experience’ turns hobby into a business
In Dover, Doug Wood was a special education teacher in the Capital School District who started aquaponics as a hobby, raising fish to supply nutrient-rich water which is filtered and used to grow crops like lettuce.
“I was selling mainly to my fellow teachers. They really liked it and they said, ‘You should do this for real.’ Then I went through a life-changing event when I lost my mother to cancer, and I started thinking, ‘You only go around once,’ and decided to pursue it as a career,” Wood said.
He also wanted to help people eat a healthier diet in an effort to prevent cancer.
“I’ve always known we consume more chemicals, more man-made stuff, than we ever have," Wood said. "What really sparked me was trying to grow with no chemicals, no pesticides."
After attending a seminar at an aquaponics company, he decided to jump in, starting 302 Aquaponics with his wife, Katie.
With the help of another former teacher, Jomelle Bowen, who majored in plant science in college, they set up the two-part operation. One section is for fish tanks and water filtration systems, and the other is for dozens of shallow “table tanks” in which the lettuce floats in containers with the roots dangling in the water below.
No soil is used. A man-made, rock-like granular material is used to help anchor the roots.
After a little over a year in business, they now have almost 20,000 square feet in greenhouses. Together with 10 other employees, they harvest about 600 heads of lettuce a day, close to 220,000 per year, with the capacity to raise 350,000 heads per year, all in under a quarter acre.
“We are basically turning over nine crops per year,” Wood said.
They raise fish to supply the nutrients for the lettuce. The water the fish are in goes through several filtration steps and then is used to grow the plants. After the solids are filtered out, “good bacteria” are added to break down the fish waste that has dissolved in the water, creating a natural fertilizer in the water.
They raise tilapia, a tropical fish that grows well in the warmer temperatures inside the greenhouse.
Lettuce is a profitable crop. But those profits came after more of a challenge than he expected.
“When we first started production, it was three weeks before COVID struck. After that, our sales were a fourth of what they should’ve been,” he said. “We were giving a lot of [lettuce] away, to the Food Bank and shelters.”
So he went to farmers’ markets, locally-owned grocery stores and offered sales directly to customers for pickup at his farm or at a variety of locations throughout the state.
“I have a refrigerated delivery van. If I didn’t have that, I don’t know what I would have done,” he said. “A lot of people didn’t want to go in stores, but they would preorder and I’d deliver to them in my van.”
Business at restaurants started picking up as capacity restrictions eased, and schools reopened.
“Sales have done really well in the last four months,” Wood said.
He sells lettuce to restaurants, three school districts – Smyrna, Caesar Rodney, and Colonial – and grocery stores like Janssen’s Market in Greenville and Hocker’s Supermarkets in Bethany Beach and Clarksville.
“My big market is at the beach with restaurants and independently-owned grocery stores,” he said.
So far, he hasn’t sold to wholesalers because the profits would be too small. But he thinks he’s on the ground floor of what could be a big business.
“Consumers are becoming much more aware of the product they’re buying, where it’s coming from, and they’re willing to pay a little more for a cleaner, more sustainable product,” he said.
Why isn’t it more widespread?
While the hydroponics business is starting to sprout in Delaware, there are some big operations in other states.
AppHarvest in Morehead, Kentucky began trading on the Nasdaq stock exchange Feb. 1. Already operating a 60-acre high-tech indoor facility, the company plans to use funds from the stock offering to build 12 more large-scale indoor farms. In February, the company broke its record by harvesting more than 120,000 pounds of tomatoes in a single day.
Another major operation is AeroFarms in Newark, New Jersey, with a 70,000 square-foot greenhouse in a former steel mill, a 30,000 square-foot growing space in a former paintball and laser tag arena and a 5,500 square-foot research and development farm in a former nightclub. The company reports it can grow more than 2 million pounds of produce a year.
AppHarvest and AeroFarms confirm the advantages of hydroponics: saving land, saving water, a year-round growing season and eliminating man-made pesticides and herbicides, opting for natural solutions.
However, the high start-up costs can be demonstrated in AppHarvest’s financial forecasts. It estimates 2021 net revenue of $21 million, but a loss of $41 million because of expenses which include building more indoor farming systems.
Another reason hydroponics hasn’t taken off: “Not every crop can be grown that way,” said Kellie Michaud, agriscience teacher at Smyrna High School. “It’s a niche.”
Some plants grow well when they’re constantly in water, but others don’t. Some are just too large to be practical in a greenhouse. Indoor farmers need crops that take up little space and reach maturity quickly.
Michaud said some of the best performers are lettuce, greens, herbs, tomatoes, peppers, celery, and strawberries.
What could turn the tide?
Smyrna High agriscience teacher Keith Shane said scarcity of land could spur more hydroponic operations.
“If the state of Delaware continues at the rate of development we have seen, I could see hydroponics becoming a little bit more mainstream,” Shane said. “I don’t know if that future will be in our lifetime, but I honestly think it will be a niche – a pretty sustainable niche. I don’t see it going away.”
At Delaware Technical Community College in Georgetown, Dr. Daniele Kidd agrees.
“We’ve got to figure out how to feed the growing population,” said Kidd, the chair of the college’s applied agriculture department. “Other countries where land is scarce like Japan, they have skyscrapers that are basically indoor greenhouses.”
In Delaware, even with farm preservation programs, many farms have been sold to developers.
“It would be very difficult to start a farm in our area, to buy 50 acres,” Kidd said. “It would be expensive and might not make financial sense, but with hydroponics, you can make a living on three to four acres.”
Jordan, at Fresh Harvest Hydroponics, believes this system of farming will become much more widespread.
“There are tons of advantages to hydroponics, and they’re not making any more land,” he said.
Ben Mace covers real estate and business news. He can be reached at rmace@gannett.com.
US: VIRGINIA - Brooke Point High School Installs Babylon Vertical Garden
“The Babylon garden is an important hands-on STEM learning tool that will benefit our students in many ways,” said Stafford County Public Schools Superintendent Dr. Scott Kizner. “The fact that we are saving 2005 square feet of farmland in a booming county is also of great benefit to our community.”
April 3, 2021 | Schools & Education
From Stafford County Schools
High School students participating in the Culinary Arts, Business, IT, and IB Environmental Science programs at Brooke Point High School (BPHS) in Stafford are taking gardening to a whole new level, vertically. The school has partnered with Babylon Micro-Farms, Inc, to install a 15 square foot, hydroponic, vertical garden in its culinary arts room.
“The Babylon garden is an important hands-on STEM learning tool that will benefit our students in many ways,” said Stafford County Public Schools Superintendent Dr. Scott Kizner. “The fact that we are saving 2005 square feet of farmland in a booming county is also of great benefit to our community.”
The garden will grow herbs, microgreens, and leafy greens. Students in the culinary arts program will use the produce in their menus, business students will develop a plan for using future crops, IT students will study how the app works and the AI functions of the garden, and IB Environmental students will study the impact of the garden on reducing environmental concerns that are associated with traditional farming.
“It’s important to me that we expose our students to innovative technology and ideas to inspire them to invent and create a more sustainable community,” said BPHS Principal Tim Roberts. “I am excited to see this important learning taking place, and to be able to provide our students with different strategies and ways of thinking in a very tangible way that promotes positive change.”
The garden is remotely managed by Babylon to ensure optimal growing conditions for the plants. Students will use an app that allows them to follow along with live data alerts, growing support, and the harvest schedule. The Babylon garden will initially grow crops that support the culinary arts program. After the first harvest, the garden is expected to produce $500 in produce per month.
Babylon vertical gardens produce three times the yield of traditional gardens, are grown without pesticides, resulting in 95% less food and 99% less plastic waste, and produce 71% fewer carbon emissions. According to Babylon, the Micro-Farms bring people closer to what they eat, create transparency in the food chain, build healthier relationships with food, and create an opportunity to change the story of how food is made.
Green Bronx Machine and Stephen Ritz - Our New PBS TV Show Featuring Leslie Ladybug And Tower Garden
This week we debut our friend Leslie Ladybug, who moves into a new Tower Garden home - Basil Towers - teaching all about seeds, vertical farming, healthy living, and growing food with children all year long - using 90% less water and 90% less space
I could not be more proud of Green Bronx Machine and our new series: Let's Learn debuting on PBS today. This series, designed to inspire healthy living, healthy learning, equity, empathy, compassion, and wellness features a series of diverse and inclusive characters right from our Bronx classroom!
This week we debut our friend Leslie Ladybug, who moves into a new Tower Garden home - Basil Towers - teaching all about seeds, vertical farming, healthy living, and growing food with children all year long - using 90% less water and 90% less space. Leslie teaches us that you too can grow food all year long and have fun doing it!
WATCH THE EPISODE NOW
AND SHARE IT!
And, you can find teacher and student resources to accompany all the fun and learning right on the GBM website.
We hope you'll tune in and share all the learning! Stay tuned to meet Patti the Pigeon, Sammy the Shark, Bobby the Bear, Sam the Squirrel, Artie the Ant, Mr. Met, and General Sequoia - the world's biggest tree - in weekly episodes coming soon!
With love from the Bronx, to the world, your pal,
Can Vertical Farming Be A Viable Method Of Controlled Environment Production?
Fifth Season is using its fully integrated, automated operating system to crack the economics code for vertical farming with the potential to integrate with greenhouse operations.
Fifth Season is using its fully integrated, automated operating system to crack the economics code for vertical farming with the potential to integrate with greenhouse operations.
To say that controlled environment agriculture is drawing a lot of interest and dollars from the investment world would be an understatement. Austin Webb, co-founder, and CEO at Fifth Season, a vertical farm operation in Pittsburgh, Pa., estimates that over $3 billion has been invested in the CEA industry during the last four years alone, excluding debt and merger and accusations activities for greenhouse operations.
“For indoor ag overall, including both vertical farming and greenhouse, about half that equity investment has been for vertical farming,” Webb said. “There were a lot of dollars that came into this space early on. The unfortunate piece to that is there was a lot of overhype and false promises made in this space. A lot of those dollars came in too early for some of these companies and overall were wasted.
“There has been an industry-wide struggle to make the economics of vertical farming work. All of these companies talk about what they are going to do in the future, but the issue is they have negative unit economics. They lose money for every pound of produce they sell. In many cases, they will say that they will make the economics work in the future, but only after they build more production facilities.”
Webb said negative economics has had a major impact on the vertical farm industry.
“The false promises and the negative economics have held the industry back, overshadowed companies that are building substantial vertical farming solutions that work and pushed additional dollars to incremental greenhouse solutions,” he said. “Moving forward we will continue to see more dollars come into CEA and into vertical farming specifically. This will include public markets and SPAC (special purpose acquisition company) activity.
“Overall, there will be more money invested in CEA. This will include investments that are mediocre. The important element will be investments made into tech platforms designed for scalability and repeatability. This is the only way that volume requirements for wholesale buyers can be met to unlock indoor ag as a material participant in overall market share.”
Need for a mindset change
Even with additional investment dollars coming into the CEA industry, Webb doesn’t expect it to be enough to make traditional vertical farming companies a success.
“Unfortunately, even though significant dollars have been invested in vertical farming, much of it has been wasted,” he said. “The incremental mindset a lot of people in this industry have had is to simply convert farming from outdoors to indoors. In doing so, all they inevitably did was bring people from outdoors and put them indoors. The mindset was to create a growing platform to produce leafy greens and then sprinkle on some technology. The technology was sort of an afterthought.
“There were a lot of companies throwing out buzz words without having actual practicality in regards to robotics, artificial intelligence, and automation. All the money that has been invested has been going toward continued R&D, but at a level which has companies creating technical debt.”
The thing that has helped Fifth Season avoid the technology issues other vertical farms have encountered is the way the company developed and designed its operating system.
Fifth Season has created a manufacturing platform that is fully automated from end-to-end including growing, processing, and packaging.
“We had a completely different mindset,” Webb said. “We took a blank slate to really design this holistically from beginning to end. We think of this as manufacturing a living organism. As a result, we’ve created an IoT–connected smart manufacturing platform that is an industry-first, industry-only, fully end-to-end automated platform—not just growing, but also processing and packaging. There are other operations that have automation here or there, but nothing else truly automated from beginning to end.
“More importantly, we have integrated the system so it is completely run by our proprietary software platform. We don’t have a bunch of automated equipment that runs on its own controls. Instead, we have a combination of our own proprietary tech and some off-the-shelf equipment such as conveyors. All of the electromechanical systems sit within our software skin and are run by our in-house built firmware and software brain. We have a pathfinding algorithm where when we receive an order from a customer, our system is sequencing out the schedule completely on a daily, weekly and monthly basis.”
Fifth Season worked with Hort Americas and GE Current, a Daintree company, to develop its automated grow room.
“Partnering together on our solution helped us validate that there was a path for our vertical farm to have favorable economics,” Webb said. “Being able to bounce ideas and technologies off of the Hort Americas team allowed us to push the boundaries of innovative thinking in terms of our approach and how we wanted to use technology to solve the complex issues that are limiting vertical farming. We were able to think differently, knowing we had the Hort Americas team as both a check and enabler, which ultimately created a successful collaboration.”
Partnering with Hort Americas also gave Fifth Season the opportunity to incorporate Current’s LED technology into its unique growing platform.
“We did a lot of things differently with our proprietary design and in so doing there were certain things that we couldn’t necessarily handle ourselves,” Webb said. “Working with Hort Americas and Current enabled us to move very quickly while making smart, capital-efficient decisions, as opposed to designing the LEDs ourselves or over-paying for unnecessary functionality.
“We worked with Current in key areas that made big differences related to the integration of our design. We leveraged Current’s significant expertise in regards to light spectrum strategy and the corresponding impact on plant science and quality.”
Creating an economic advantage
Webb said Fifth Season’s unique platform has allowed the company to unlock positive unit economics where it can offer a market price that works for wholesalers and consumers.
“We have been able to make money per pound and make vertical farming economically sustainable,” he said. “Our platform has enabled us to make a stepwise function change in labor costs and efficiency and in energy costs. For labor, we have 2x+ less labor costs than other companies in this space. We also measure and track energy down to every individual bot. We have over 60 bots that are all integrated into one robotics system. We measure and track how to optimize energy utilization to all of those bots.
Fifth Season’s unique operating platform has allowed the company to unlock positive unit economics enabling it to offer a market price that works for wholesalers and consumers.
“Finally we have made a stepwise function change in pounds to fixed costs ratio. That’s because we have been able to remove large aisle ways and manual inefficient storage and retrieval. We have created a patent-pending solution around our automated storage retrieval, which ties to the rest of our system. In the end, we are able to remove all human involvement from the grow room and are able to achieve 2x+ the growing capacity.”
Another advantage of the platform Fifth Season has created is the need for raising additional capital compared to some other vertical farms.
“We have raised just over $40 million to date,” Webb said. “There are multiple vertical farm companies that have raised $200 to $400 million+. The reason we haven’t had to raise that much capital is because of our mindset about engineering, grow science, and operations in the same R&D pipeline. It has allowed us to catch up and to surpass the rest of the industry in a fraction of the time with a fraction of the capital.
“As we move forward and look at raising additional capital, what’s different is we don’t have to use our equity capital to build more farms for all the hard costs associated with real estate, equipment and building facilities. We can if we want to and if it makes sense for our equity partners, but it is not required. We have been able to unlock positive unit economics which means we have been able to unlock non-dilutive capital to build additional facilities more capital efficiently. Overall, we have built a scalable, repeatable platform, which is what investors need to see.”
What’s ahead for vertical farming?
Webb said there will be a few select companies that have approached indoor ag and vertical farming with a solution that works and will thrive. There will also be a number of companies that are large and excessive that will eventually disappear.
“There will be some consolidation in this industry,” he said. “Some companies won’t be consolidated because they don’t have a tech platform that is investable in terms of the synergies of wanting to acquire that footprint. Consolidation will be selective in some cases.
“There is a lot of production regardless of footprint and money going into leafy greens. There are companies in this space that have no intention of doing anything different than that. I think that focus will run them into a leafy greens race to the bottom. It all comes down to no sustainable competitive advantage.”
Webb also sees the potential for synergy between vertical farms and greenhouses.
“We have built a scalable system that allows us to do a number of crops and then do asset management across different applications,” he said. “We also have the technology that is applicable from an asset management production operations standpoint that works for greenhouses as well.
“We will be able to unlock with this technology what many others won’t necessarily be able to do. Fifth Season will not only be a company that has vertical farm and greenhouse footprints but also is one that uses those footprints in a collaborative way for specific crops. For example, a crop could be in a vertical farm environment for part of its life and in a greenhouse for another part of its life. This will create cross-category and cross footprint combinations.”
For more: Fifth Season, (412) 899-2268; hello@fifthseasonfresh.com; https://www.fifthseasonfresh.com/
Lead photo: Austin Webb, co-founder, and CEO at Fifth Season, said even though significant dollars have been invested in vertical farming, much of it has been wasted. Photos courtesy of Fifth Season
This article is property of Urban Ag News and was written by David Kuack, a freelance technical writer in Fort Worth, Texas.
CHINA: $500 Billion To Bring All World Crop Farming Indoors
China will build 2 Million hectares (20 billion square meters) of controlled environment greenhouses by 2025 and this will produce half of their vegetables and crop needs
Brian Wang | April 3, 2021
China will build 2 Million hectares (20 billion square meters) of controlled environment greenhouses by 2025 and this will produce half of their vegetables and crop needs. Temperature, humidity, lighting would all be under controlled conditions. It would not matter if there were new extreme temperature swings outside or if there was drought. The needed food and water would be immune to any projected climate change over the next 500-1000 years.
Alibaba sells greenhouses for as little as 70 cents per square meter. The bulk, high volume cost to the manufacturer is about 50 cents per square meter. If installation labor costs are 50% of the 2 million hectare project then it would cost about $20 billion for the 2 million hectare project. $40 billion would be sufficient for China to make 40 billion square meters of climate-controlled greenhouses which could produce all vegetables and crops. It would cost $260 billion to make greenhouses for the food production of the entire world.
Indoor climate-controlled agriculture has almost no need for pesticides and uses 7% of the water. This would take up 3-5% of the total land area of open-air farming.
Additional funds could be provided for higher demand from population growth and for some level of automation, sensors and other systems.
There is an economic analysis of smaller scale greenhouse and vertical farming. The all-in delivered cost of a pound of greens grown in a commercial greenhouse is estimated to be $2.33 per pound. It cost $18.3 million to build 280,000 square feet (2.6 hectares) of commercial greenhouse in the USA. The total cost to grow would be just over $3.0 million per year for 2 million pounds of greens or $1.52 per pound. BrightFarms employs 165 people for the three greenhouses. $1.10 per pound consists of employee costs.
The cost estimates for greenhouses could be brought down to $1 per pound or less with large-scale construction. Below are costs for 2.8 hectare systems in the USA.
There is value to having national food security and not having to depend on imported food. Ten billion to twenty billion dollars per year in indoor farm subsidies closes the cost gap with open-air farming.
China’s controlled environment system will have a lot of automation and lower construction costs because of the massive scale and lower costs in China.
PNAS – Wheat yield potential in controlled-environment vertical farms
Wheat growing is vastly more land and water-efficient but costs are not yet competitive with open-air farming.
Wheat is the most important food crop worldwide, grown across millions of hectares. Wheat yields in the field are usually low and vary with weather, soil, and crop management practices. We show that yields for wheat grown in indoor vertical farms under optimized growing conditions would be several hundred times higher than yields in the field due to higher yields, several harvests per year, and vertically stacked layers. Wheat grown indoors would use less land than field-grown wheat, be independent of climate, reuse most water, exclude pests and diseases, and have no nutrient losses to the environment. However, given the high energy costs for artificial lighting and capital costs, it is unlikely to be economically competitive with current market prices. Wheat grown on a single hectare of land in a 10-layer indoor vertical facility could produce from 700 ± 40 t/ha (measured) to a maximum of 1,940 ± 230 t/ha (estimated) of grain annually under optimized temperature, intensive artificial light, high CO2 levels, and a maximum attainable harvest index. Such yields would be 220 to 600 times the current world average annual wheat yield of 3.2 t/ha. Independent of climate, season, and region, indoor wheat farming could be environmentally superior, as less land area is needed along with reuse of most water, minimal use of pesticides and herbicides, and no nutrient losses.
Meat production could also be brought under climate control. The feed for cows, pigs, chicken and fish could be either brought into greenhouses or converted to insects. Insect feed can be twenty to one hundred times more space and water-efficient.
Meat can be converted into cell-based production in large vats. This would be similar to the industrial production of beer.
There would be zero risk of mass starvation caused by temperature or drought-induced crop failure.
There may not be a need to bring all crops indoors. But if China brings half of all of their crops indoors in five years it clearly shows that civilization can bring all crops and farming indoors at any time. The cost as I have shown is less than 0.5% of global GDP for the crops and a few percent to deal with the meat and feed as well.
It is likely only truly economical (even with China’s mass production) to bring vegetable and fruit farming indoors. If China has indoor vegetable and fruit production at $1 per pound then other countries could follow at different levels based upon how cost-competitive indoor farming is against open-air farming for a particular crop. There is also the question if people will pay more for greenhouse crops. Greenhouses allow for year-round crop production. This means consistent prices and availability for fruits and vegetable year round. It also means indoor farms can be inside of cities for fruit and vegetables that are fresh from the tree and vine. The greenhouse crops would also be mostly or completely free of pesticides. Indoor farming share will grow as efficiency and costs are improved.
I think 20-60% of all crops (mainly higher-value fruits and vegetables) globally will go indoors by 2030 and gradually more as indoor becomes a lower cost and superior product to outdoor farming. Greenhouse farmed fruits and vegetables can have a higher quality versus outdoor grown fruits and vegetables.
Some of the advantages of protected culture greenhouse crops are:
Season extension is just one of the advantages gained from greenhouse growing. Protected crops are less apt to be damaged by wind, rain, and hail so the percentage of marketable products is higher. Yield is often higher as well, if you can provide optimum growing conditions for each crop. Greenhouses protect crops from many diseases, particularly those that are soilborne and splash onto plants in the rain. And greenhouse crops may be protected from common field pests. Of course, greenhouse crops have their own particular problems such as foliar disease, aphids, and whiteflies, so vigilance is still required.
SOURCES- Alibaba, PNAS, agfunder news
4 Microgreens Recipes To Add To Your Cookbook
Because of their nutrient-dense properties, microgreens can be ten times stronger than their adult vegetable counterparts
Microgreens are flavor-packed tiny vegetables that should be added to your book of recipes. Because of their nutrient-dense properties, microgreens can be ten times stronger than their adult vegetable counterparts. Not only that, but they can serve as a great addition to any meal, adding a boost of flavor to WOW your palette and your guests! Keep reading to learn about the 4 microgreen recipes you should add to your cookbook today.
Recipe #1: Microgreens Pesto via Hamama
If you’re a fan of pesto (who isn’t?), then try this delicious pesto recipe, substituting the basil leaves with microgreens! For this recipe, you’re going to need 6 cloves of garlic, 1⁄4 cup of pumpkin seeds, 1⁄4 tsp of salt, 1⁄3 cup of olive oil, and 1 package of microgreens (kale is a good option to use for this). Once you have your ingredients, add them all to your food processor, and blend the ingredients until you reach your preferred consistency.
Recipe #2: Microgreens Salad with Lime Vinaigrette via Everyday Dish
Salads are a great way to get your daily vegetable intake, and substituting traditional leaves with microgreens packs that nutritional punch! For this delicious salad, you’ll need 1 package of microgreens (your choice), 6 radishes (halved and sliced), 2 tbsp lime juice, 1⁄8 tsp dry mustard powder, 1⁄4 tsp salt, 4 tbsp olive oil, and salt and pepper to taste. Mix your ingredients together aside from the microgreens and radishes to create the dressing. Then mix your ingredients when you’re ready to serve!
Recipe #3: Microgreens Tabouli via Hamama
Tabouli is a delicious Middle Eastern dish that pairs well with anything. To make this recipe, you’ll need 1⁄2 cup bulgur, 1⁄2 cup water, 1 package of microgreens (your choice), 1 bunch of cilantro chopped, 1 bunch of parsley chopped, 1 bunch of mint chopped, 4 stalks of chopped green onions, 1-2 cups of cherry tomatoes, 1-2 garlic cloves minced, 2 tbsp lemon juice, 2 tbsp olive oil, and salt & pepper to taste. First, cook your bulgur. While it’s cooking, make your dressing by whisking the lemon juice, olive oil, garlic, and salt & pepper. Cool down your bulgur. Once all ingredients are prepped, mix together in a large bowl and serve!
Recipe #4: Strawberry Microgreen Salad via Real Healthy Recipes
We’re including another salad recipe because microgreens salads are one of the best ways to get a healthy dose of nutrients and taste delicious! For this recipe, you’ll need 3 cups of organic microgreens (your choice), 1 cup of sliced strawberries, chopped walnuts, and strawberry dressing (6 strawberries, 1 tbsp balsamic vinegar, 1 tsp raw honey, 2 tbsp olive oil, salt & pepper to taste. Then blend the ingredients to make the sauce). Mix all of these ingredients together to make your strawberry microgreens salad!
Want to learn more about all of the things you can do with microgreens? Join our Facebook Microgreens Group to learn from experts and beginners alike. You can also listen to our Polygreens podcast to learn all there is to know about agriculture.
#microgreensrecipes, #microgreensrecipe, #usingmicrogreensathome, #usingmicrogreens
Polygreens Podcast Episode 21 - Dan Ovadya
Dan Ovadya stumbled into his career passion growing super sweet Chandler strawberries in low-tech greenhouses on the Israel-Jordan border in 1991