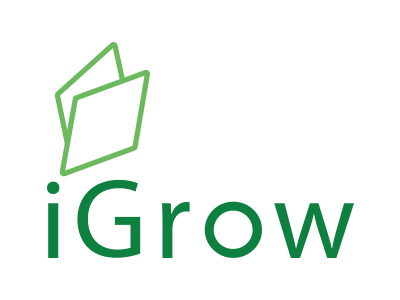
Welcome to iGrow News, Your Source for the World of Indoor Vertical Farming
USA - VIRGINIA: Fairfax Hydroponic Farm Expanding, Creating 29 Jobs In Herndon
Beanstalk, an indoor hydroponic farm in Fairfax County, plans to expand its operation, investing $2 million and creating 29 jobs, Gov. Ralph Northam announced Monday
Beanstalk Plans To Invest $2 Million In Project
MAY 24, 2021
BY KATE ANDREWS
Beanstalk, an indoor hydroponic farm in Fairfax County, plans to expand its operation, investing $2 million and creating 29 jobs, Gov. Ralph Northam announced Monday.
Owners Mike and Jack Ross, brothers from Alexandria, started the business in 2018 and sell fresh salad mixes and fresh herbs to grocery stores and at farmers’ markets. The new facility, to be built in Herndon, will produce specialty herbs and pesticide-free leafy greens year-round with its proprietary hydroponic technology, Northam’s office said in a news release. In 2018, Jack Ross won the state’s STEM Catalyst Award for developing an automated indoor growing prototype, which later led to Beanstalk’s automated production system.
“Fairfax County is the perfect place for a startup like Beanstalk to put down roots and grow their company,” Northam said in a statement. “We are pleased to support a project that blends agriculture, Virginia’s oldest and largest industry, with technology, one of the fastest-growing sectors of our economy. Innovative entrepreneurs like Mike and Jack Ross are demonstrating how STEM fields can help cultivate new techniques like hydroponics that make fresh produce more accessible.”
The Virginia Department of Agriculture and Consumer Services (VDACS) and the Virginia Economic Development Partnership (VEDP) worked with Fairfax County and the Fairfax County Economic Development Authority (FCEDA) to secure the project for the commonwealth. Northam also approved a $100,000 grant from the Governor’s Agriculture and Forestry Industries Development Fund, which Fairfax County will match with local funds. The Virginia Jobs Investment Program will support job creation and training at no cost to the company.
“Jack and I are incredibly proud to be developing our technology and growing local produce in Virginia,” Michael Ross said in a statement. “Being ‘Virginia Grown’ ourselves, we are excited to be bringing new technology to the industry and new jobs to our home state.
Bowery Farming Unveils Research And Breeding Hub, Farm X
Farm X is one of the largest and most sophisticated vertical farming R&D facilities in the world, and will further accelerate the commercialization of products specifically designed for Bowery’s indoor system
May 18, 2021
NEW YORK, May 18, 2021 /PRNewswire/ — Bowery Farming, the largest vertical farming company in the United States, today announced the opening of Farm X, its newest state-of-the-art innovation hub for plant science in Kearny, N.J., adjacent to Bowery’s original R&D Center of Excellence and first commercial farm.
Farm X is one of the largest and most sophisticated vertical farming R&D facilities in the world, and will further accelerate the commercialization of products specifically designed for Bowery’s indoor system.
From the cultivation of strawberries, root vegetables, tomatoes, peppers and beyond, to the discovery of the next generation of wildly flavorful leafy greens, Farm X expands Bowery’s R&D capacity by nearly 300%.
“We’re proud to be the largest vertical farming company in the United States that is consistently and reliably delivering our customers a wide variety of high quality, flavorful produce that’s local, safe and sustainable,” said Irving Fain, founder, and CEO of Bowery Farming.
“From day one, our R&D team has been working tirelessly to unlock the next frontier in agriculture, and Farm X enables us to expedite the discovery of new vibrant crops and pioneering technological advancements that will further accelerate our momentum as the category leader.”
Bowery’s world-class team of plant breeders, plant physiologists, biochemists, and more, are constantly innovating from seed-to-shelf. At Farm X, they will be able to test more, faster—ultimately accelerating the discovery of new crops, growing recipes, and efficiency improvements that can be replicated at scale across the company’s network of commercial farms.
Featuring proprietary, highly customizable, modular growing environments managed and monitored by new technology developed in-house, Farm X will further unlock the next phase of Bowery’s growth.
Farm X also features a sensory lab where Bowery will continue its quest for the perfect cultivars for indoor growing, as well as launch the first-ever on-site breeding program at a vertical farming company.
Under the new breeding program, Bowery’s team will be able to develop varieties that thrive in its unique growing conditions and evaluate each one for optimal taste, quality and yield, rather than to survive outdoors, pest-resistance, and long-haul transportation. While a traditional breeding program takes up to ten years, Bowery’s controlled indoor environment and 24/7 monitoring of crops will enable the company to bring new groundbreaking products to market at scale in a fraction of the time.
Bowery’s R&D team works year-round to uncover flavor-packed produce and bring new and exciting culinary experiences to consumers. Beyond the cultivation of new fruits and vegetables at Farm X, they are also developing the next generation of greens.
The Farmer’s Selection category, which launched in January 2021, emerged as a way to let consumers in on the process, bringing the thrill of discovering a new ingredient at your local farm stand to the grocery store. Bowery is launching a new small-batch green every four months under this new category.
The first greens released, Bowery Mustard Frills — hearty mustard greens with a tingly start and a fiery, wasabi-style finish — were available through April 2021. Green Sorrel, bright, tart baby greens with a zing and the next release in the series, is now available from May through August 2021.
Farm X also serves as an experimental space for innovation in farm design, data science, computer vision, autonomous robotics, hardware, and software that can be deployed in Bowery’s growing network of commercial farms.
As Bowery continues to advance the integration of proprietary smart farming technology, it recently announced Injong Rhee (formerly VP at Google and CTO of Samsung Mobile) as its Chief Technology Officer. Rhee will ensure that every farm continues to benefit from the collective intelligence of the BoweryOS, the company’s proprietary operating system which integrates software, hardware, sensors, computer vision systems, machine learning models and robotics to orchestrate and automate the entirety of operations.
Rhee’s team is ensuring the advanced technological learnings discovered at Farm X will be seamlessly integrated and applied at scale across Bowery’s network.
Bowery has experienced more than 750% brick-and-mortar sales growth, and more than quadrupled sales with e-commerce partners, including Amazon, since early 2020. Bowery’s newest commercial farm in Bethlehem, Pennsylvania, will bring local, pesticide-free produce, harvested year-round at peak freshness, to a surrounding population of 50 million people within a 200-mile radius, and will be its largest and most technologically-advanced commercial farm yet, further automating the growing process from seed to store.
About Bowery Farming
Bowery Farming, the Modern Farming Company, was founded in 2015 with the belief that technology and human ingenuity can grow better food for a better future. Propelled by its proprietary software system, the BoweryOS, Bowery builds smart indoor vertical farms that deliver a wide variety of Protected Produce — in little time, near cities they serve, for a truly local approach.
Bowery’s farms are growing the next generation of vibrant and flavorful produce. With BoweryOS, farms are 100 times more productive on the same footprint of land than traditional agriculture and grow traceable pesticide-free produce with a fraction of the water and land.
The largest vertical farming company in the U.S., Bowery’s produce is available in more than 850 grocery stores and via e-commerce platforms serving the Tri-state and Mid-Atlantic region, including Amazon Fresh, Giant Food, Walmart, Weis, Whole Foods Market, Albertsons Companies and specialty grocers.
Based in New York City, Bowery has raised more than $172.5 million from leading investors, including Temasek and GV (formerly Google Ventures), General Catalyst, GGV Capital, First Round Capital, Henry Kravis, Jeff Wilke, and Dara Khosrowshahi, as well as some of the foremost thought leaders in food, including Tom Colicchio, José Andres, and David Barber of Blue Hill.
Tagged greenhouse, research, technology, vertical farming
5 Things To Check When Comparing Lighting Designs For LED Grow Lights
As a grower, you invest in supplemental LED grow lights because they power the yield and quality of your crops.
May 17, 2021
· When you compare different lighting designs, make sure to compare apples with apples.
· These are the 5 things to check when comparing lighting designs for LED grow lights.
Eindhoven, the Netherlands – As a grower, you invest in supplemental LED grow lights because they power the yield and quality of your crops. In fact, the rule of thumb is that 1% light output equals 1% crop yield. So, it is vital that your LED lighting investment delivers the full performance you paid for.
The performance is determined by the light intensity and light uniformity of the LED grow lights you use. If the installed light intensity is lower than what has been designed, there will be less yield. If the uniformity is inconsistent, individual plants will grow and develop at different rates and there will be uneven production in your greenhouse.
Before you start
When you compare different lighting designs, make sure to compare apples with apples. This means taking 3 things into account:
1. Verify the credibility of the performance claims that manufacturers make
2. Make sure that DIALux calculation software is used for the lighting design. This calculation software is independent and commonly used in the horticulture market.
3. Check which input parameters have been used for each lighting design. It is easy to tweak the input parameters and give the impression of a more positive light level and uniformity within the lighting design. So which parameters are crucial?
Most important input parameters to check
• Is the right product specified? Check if the exact product that you have selected for your project has been used in the lighting design; with the right light output (PPF in µmol/s) and spectrum (blue/red/white/far red/…)
• Are your specific design values used like the average light level at your crop (PPFD in µmol/m2/s) and the overall light uniformity?
• What are the standard settings? The height of the grow light and crop (free height), reflection factors, and size and position of the area that is used in the uniformity calculation have an impact on the average light level and overall uniformity.
#1 Check the free height
The first input parameter to check is the free height specifying the distance between the LED module and the head of the crop. The free height can seriously impact the overall uniformity value. In case of high-wire tomato crops, with a limited free height of 1.50 to 2.50m, realizing a good overall uniformity value can be a challenge. An optimistic free height or calculating uniformity on floor level as if there is no crop will positively impact the overall uniformity value.
The free height is calculated by measuring the eventual top of the crop and the mounting height of the LED grow light.
#2 Check the reflection factors
Another important parameter to check, are the reflection factors used in the lighting plan. A reflection factor indicates the amount of light that is reflected by walls and other objects in a space. DIALux calculation software has originally been designed for indoor spaces like offices, where you will get reflection off the walls, ceiling, and floors that impact the light level on your desk. To avoid being too optimistic about the outcome, the reflection values in DIALux are set at 0% for a greenhouse lighting design, because the glass in a greenhouse does not reflect the light from the grow lights.
#3 Check the area that has been used to make light intensity calculations.
The next thing to check is the defined calculation surface. The size of the calculation area and the position of the grow lights within that area will seriously impact the average amount of active photons that reaches the surface of the crop (PPFD value in µmol/m2/s). When comparing lighting design results from different manufacturers, make sure that the calculation surface shows an equal number of maximum (peaks) and minimum (dips) light intensity values. Only then you receive a realistic average PPFD value in the lighting design.
In the below example, you will see two positions of a calculation area within the same light plan, which will generate far better average light intensity values in the B situation, because the light intensity is calculated with an area that shows more grow light (peaks), and consequently less areas with the minimal amount of grow lights, which will not represent the reality after installation
Position of measurement grid defines the outcome of average light intensity
#4 Check the size of the calculation surface
Another important factor is the size of the calculation surface that will impact the overall uniformity value. When comparing lighting design results from different manufacturers, make sure the same calculation surface has been applied.
To represent a real-life situation, a calculation for the full compartment area should be made that includes the edges of the greenhouse. In case of a typical production area, a centred area is used. You may understand that a full compartment will generate lower uniformity levels, because of the lower light intensities at the edges. So, make sure you always compare either full compartments or smaller areas.
#5 Check the used uniformity
The final parameter to check is the uniformity being used. Uniformity can be expressed in different ways. When you run the DIALux lighting design software, it provides you with different types of uniformity. When comparing lighting design results from different manufacturers, make sure the same type of uniformity is applied. For a horticulture application, we prefer to express uniformity as the average light intensity divided by the maximum light intensity, which represents real-life situations best.
In Summary
When comparing lighting designs there are lots of tweaks that suppliers can possibly make to finetune their plan. In case you want to make a proper comparison, you have to take a few parameters into account.
- Is the specified product with the right spectrum and efficiency used in the calculations?
- Is the right light level for your crop used and the right overall light uniformity?
- Are the settings comparable:
o Is the free height correctly defined?
o Are the reflection factors set to 0%?
o Does the measurement grid have an even number of light and dark spots in it.
o Are you comparing full compartment or small centered area numbers?
o And is the defined uniformity similar in the lighting designs?
Read our other blog and learn how to evaluate the performance claims of an LED grow light.
Grow with the pros
You want to be sure to get a rapid return on your investment and have all aspects of your project carried out professionally. With Signify, your project is in experienced hands. Signify is the global leader in the lighting sector and has built up a substantial track record in more than 1000 projects in the horticultural lighting market since 1995. This includes over two decades of dedicated experience developing tailor-made, LED-based light recipes that help growers speed up growth, increase yield and improve the quality of plants. With cutting-edge LED innovations at our command, we can custom-build a science-based solution for you.
Pascal van Megen is an application engineer at Signify with a background in mechanical engineering. As an application engineer, Pascal ensures that growers are provided with high-end horticulture lighting designs. He is providing internal and external training to customers and partners in the application of the Philips LED Horticulture products and systems. He acts as a consultant to customers and engineers, to drive continuous improvement of Philips LED lighting solutions.
--- END ---
For further information, please contact:
Global Marcom Manager Horticulture at Signify
Daniela Damoiseaux
Tel: +31 6 31 65 29 69
E-mail: daniela.damoiseaux@signify.com
About Signify
Signify (Euronext: LIGHT) is the world leader in lighting for professionals and consumers and lighting for the Internet of Things. Our Philips products, Interact connected lighting systems, and data-enabled services, deliver business value and transform life in homes, buildings, and public spaces. With 2020 sales of EUR 6.5 billion, we have approximately 37,000 employees and are present in over 70 countries. We unlock the extraordinary potential of light for brighter lives and a better world. We achieved carbon neutrality in 2020, have been in the Dow Jones Sustainability World Index since our IPO for four consecutive years, and were named Industry Leader in 2017, 2018, and 2019. News from Signify is located at the Newsroom, Twitter, LinkedIn, and Instagram. Information for investors can be found on the Investor Relations page.
VIDEO: Vertical Farms Could Take Over The World
As the global population continues to increase, vertical farming is becoming a more widely recognized and viable solution to our food production problem
By JACK BERNING
May 22, 2021
Vertical Farming Offers Better Tasting,
More Sustainable Produce.
Will It Take Over Farming
As We Know It?
As the global population continues to increase, vertical farming is becoming a more widely recognized and viable solution to our food production problem. Vertical farming is a type of indoor farming where crops are grown in stacked layers, rather than spread out across large plots of land.
To View The Video, Please Click Here
These futuristic farms aren't just going to have an impact on how we survive here on Earth; they could also enable us to create a food source beyond our planet, without a dependence on the outdoor climate or arable land.
Although the task sounds unimaginable, developments in controlled environment agriculture are proving that it is very much possible. Adopting these sustainable farming practices could lead to a monumental shift in how we produce food, both for today and the future of humanity.
Vertical Farming Advantages
Vertical farms offer many benefits over traditional farming practices — an increased crop yield with a smaller land requirement, more control over the resulting flavor and cleanliness of crops, and the prospect of better access to healthy foods in underserved communities, to name a few.
Because these farms are constructed completely indoors using LED lights, their output isn't subject to the natural elements that typically affect plant production such as adverse weather, insects, and seasons.
Vertical farms offer more control over the resulting flavor and cleanliness of crops, and the prospect of better access to healthy foods in underserved communities.
They're better for the environment because they require less energy and put out less pollution, without a need for heavy machinery, pesticides, or fertilizers. Vertical farms often use soil-less farming methods like aquaponics, hydroponics, and aeroponics, which requires just 10% of the amount of water consumed by conventional outdoor farms.
Think of a vertical farm as a plant factory — one that enables farmers to predictably grow anything, anywhere, from strawberries to kale. The idea was first introduced in 1999 by Dickson Despommier, a professor at Columbia University. Despommier and his students came up with designs for a "skyscraper farm" that could feed 50,000 people. Though the structure has yet to be built, they successfully managed to popularize the ideology behind vertical farming systems.
Output isn't subject to the natural elements that typically affect plant production such as adverse weather and insects.
So, why wasn't the skyscraper farm ever built? The answer sheds light on one of the most prominent vertical farming disadvantages — cost. A single farm can cost a hundred million dollars to construct, and a lack of data surrounding the long-term economic feasibility of vertical farms has caused some investors to shy away.
However, this hasn't stopped vertical farmers from persisting to disrupt the food production industry. Vertical farming has already been adopted in countries like China, Japan, and other parts of Asia. In fact, the market for vertical farming in that region is expected to increase 24% by 2026. And in the U.S., some vertical farming companies are already selling their produce in stores.
More Produce With Less Resources
One of those companies is Plenty, headquartered in San Francisco, California. Plenty was founded in 2014 by Matt Barnard and Nate Storey with a simple yet powerful mission to improve the lives of plants, people, and the planet.
Plenty already has established vertical farms in the San Francisco Bay Area, Wyoming, and Washington. These farms supply fresh produce including kale, arugula, and lettuce to major grocery stores like Whole Foods and Safeway.
The team at Plenty recently began construction on a new farm in the Bay Area that they call Tigris. Tigris will be its largest and most efficient farm yet, capable of growing a million plants at a time.
With Plenty's vertical farming technology, 700 acres of farmland can be condensed into a structure the size of a big-box store. Plenty's farms harvest 365 days per year and shrink growth cycles to about 10 days for many of their products.
This results in a yield increase of about 700% as compared to traditional farming, all while saving about a million gallons of water per week and using just one percent of the land that traditional farms use.
The secret to this astronomical efficiency lies in the technology. Plenty's farms are equipped with air handling units that capture transpired water, allowing them to recirculate 99% of the water back into the system. They also use LED light bulbs and, seeking to be as efficient as possible, the bulbs are designed in a grid format that maximizes the amount of energy absorbed by the plants.
These systems allow farm operators to have more control over their crop yield — all the way down to a plant's flavor profile. Blue LED lighting, for example, can create a crispier crunch in kale leaves. Additionally, without a need for pesticides, their products are completely organic.
Plenty's farm saves about a million gallons of water per week and uses just 1% of the land that traditional farms use.
"When you grow things outside, the elements are much more unpredictable," Shireen Santosham, the head of strategic initiatives for Plenty, explains. "If you grow indoors, you can control a lot of those factors in ways that are accessible to outdoor growers. And the result is that our produce can be hundreds of times cleaner."
Not only is the produce cleaner, it's also higher quality. Because Plenty's products are grown in urban areas and don't have to be shipped across the country, the brand doesn't have to prioritize shelf life. Less transportation needs also reduces their carbon footprint.
What could all of this mean for the future? That every place in the world, regardless of climate, could sustainably grow the same nutrient-rich and flavorful crops. And it could someday result in the colonization of other planets, as well.
"We can give the world back — a lot," says Storey. "We can give the world back land. We can give back the jungles of Borneo to the orangutans. We can give back the Amazon to the planet. We can give back the midwest to the buffalo. We can give back the things that we've taken. And we can be a lot less extractive."
Upward Farms Opens New Aquaponic Operation In Brooklyn, New York
The new facility is located in Greenpoint, Brooklyn, New York, and utilizes Upward’s next-generation technology to advance the company’s growth
May 19th, 2021
BROOKLYN, NY - Innovation and sustainability are two facets of the fresh produce industry that are growing like wildflowers, and one company seeing the effects of this expansion is Upward Farms, the aquaponics vertical farming company. The New York-based grower has announced the opening of a cutting-edge new headquarters that will continue to support Upward’s commercial production, research, and development.
Jason Green, Chief Executive Officer, and Co-Founder, Upward Farms“Upward Farms’ new facility successfully scales our vertical farming model. Controlled environments and ecological farming are not at odds but are powerful compliments for the next generation of farming. We’re delivering higher yields, disease resistance, safety, and sustainability in a platform that can be deployed anywhere in the world, regardless of climate,” said Jason Green, Chief Executive Officer, and Co-Founder. “The pandemic underscores the importance of shoring up supply chains to be more local for transparency, safety, and efficiency. Localized produce is especially important from a food safety standpoint. As vertical farms scale, we can create a supply chain that’s fundamentally more resilient than shipping produce around the country, if not around the world.”
The new facility is located in Greenpoint, Brooklyn, New York, and utilizes Upward’s next-generation technology to advance the company’s growth. According to a press release, the operation is powered by end-to-end automation and is USDA Certified Organic, making it one of the first Certified Organic vertical farms in the Northeast region of the U.S.
Upward Farms has announced the opening of a cutting-edge new headquarters that will continue to support the company's commercial production, research, and development
In addition to its state-of-the-art technology, the new headquarters includes a fishery that is Monterey Bay Aquarium Seafood Watch “Best Choice” rated, and sustainably farms mercury-free, antibiotic-free, and hormone-free striped bass.
Upward Farms’ ready-to-eat microgreen mixes are currently available in all Brooklyn Whole Foods locations and are anticipated to be available in all New York City Whole Foods stores within the next few months.
The new operation is powered by end-to-end automation and is USDA Certified Organic, making it one of the first Certified Organic vertical farms in the Northeast region of the U.S.
As consumer trends continue to shift toward fresh, organic produce and online purchase of groceries, Upward Farms is offering consistent product availability, quality, and scalability for locally grown greens. The grower is expecting further expand as demand increases and has already raised approximately $150 million to date from investors to spark growth.
For more news regarding vertical farming and other growing practices gaining traction across the industry, stick with AndNowUKnow.
[Upcoming Webinars] Communicating Sustainability, Financing Indoor Ag
This panel will explore the best practices for communicating and reporting on sustainability with the hopes of encouraging the industry to mature
Indoor Ag-Con
SUSTAINABILITY, FINANCING HEADLINE
MAY | JUNE INDOOR AG-CONVERSATIONS SCHEDULE
MAY 26, 2021 10:00 AM - 11:00 AM EDT
Indoor Ag-Con & Agritecture invite you to join us for this important session.
Despite a decade of innovation and funding in vertical farming, many businesses do not communicate accurate information about the sustainability of their technology or operations. Whether it's unsubstantiated claims of water savings, carbon reduction, circularity, or overall sustainability, many companies do not avoid greenwashing in their marketing. This panel will explore the best practices for communicating and reporting on sustainability with the hopes of encouraging the industry to mature.
Moderator:
Henry Gordon-Smith, Founder & CEO, Agritecture
Panelists:
Sara Segergren, Project Portfolio Leader, Sustainability Innovation and Development,
Ingka Group | IKEA
Sam Norton, Founder, Heron Farms
Lisa Causarano, International Accounts Manager, Schneider Electric
SAVE YOUR FREE SPOT!
JUNE 8 & 9, 2021 1:00 PM - 4:30 PM EDT EACH DAY
Join Indoor Ag-Con, Brad McNamara & FarmTech Society for this
2-day SPECIAL EDITION of Indoor Ag-Conversations.
DAY 1 | JUNE 8, 2021 -- 1:00 PM - 4:30 PM
During 3 in-depth panel discussions with successful entrepreneurs and their investors, host Brad McNamara will push for first-hand accounts of each round to pull back the curtain on what it takes to fund an idea and create an investment-grade business in CEA.
DAY 2 | JUNE 9, 2021 -- 1:00 PM - 4:30 PM
2020 was a big year for Controlled Environment Agriculture -- and the next two years are likely to see unprecedented growth and change in the sector.
On day 2 of our Indoor Ag-Conversations 'Seed to Scale' event, the host FarmTech Society will focus on the maturing of the industry as CEA "crosses the chasm" into mainstream adoption.
LEARN MORE & SAVE THE DATE
INDOOR AG-CON - IN PERSON!
OCTOBER 4-5, 2021
We can't wait to see our industry colleagues again in October! We've got an incredible program lined up from you. Check out our expo hall floor, which is filling up quickly. And, explore our educational offerings, including keynotes from top indoor ag CEOS, panel discussions diving deep into 3 tracks - business & marketing; science & technology; alternative crops & growing methods.
And, of course, a full roster of networking opportunities, too!
JOIN US!
SPECIAL THANKS TO INDOOR AG-CON 2021 SPONSORS & MEDIA ALLIES
Indoor Ag-Con, 950 Scales Road, Building #200, Suwanee, GA 30024, United States
RUSSIA: A Unique Vertical Farm Can Produce 10 Times More Seed Potatoes A Year
Less than a year after the opening of the World-class Scientific Center "Agrotechnologies for the Future", Russian scientists had a breakthrough: the first-ever vertical farm with dynamic LED lighting
Less than a year after the opening of the World-class Scientific Center "Agrotechnologies for the Future", Russian scientists had a breakthrough: the first-ever vertical farm with dynamic LED lighting.
FEDERAL RESEARCH CENTRE «FUNDAMENTALS OF BIOTECHNOLOGY» OF THE RUSSIAN ACADEMY OF SCIENCE
The pandemic has interfered with technological production chains in many areas of agriculture, making the restoration of the Russian seed bank a priority of national food safety. Furthermore, pests and weather conditions prevent the production of standardized raw materials in needed quantities every year. It is only economically efficient to grow high-value crops such as berries or herbs in automated greenhouses. Potatoes, peppers, tomatoes, and oilseeds which are needed much more do not fall into this group.
A team from the Federal Research Center for Biotechnology of the Russian Academy of Sciences rose to the challenge and presented the first pre-production prototype of a vertical farm. The prototype was developed in the framework of the "Smart City Farm" project initiated by the World-class Scientific Center "Agrotechnologies for the Future" that was opened in 2020. Scientists have grown healthy potato for further multiplication in the field.
The crop rapid seed reproduction facility combines state-of-the-art digital technology with organic farming techniques. The vertical City Farm has controlled conditions: dynamic lighting, an automatic irrigation system, pathogen-free air, and nutrients supplied to the plant from a special substrate. A unique feature of the innovative farm is the individually adjustable LED lighting with different spectral composition preferred for specific varieties and for different periods of plant growth.
The complex makes it possible to grow products with specified properties under controlled conditions on an industrial scale with more than ten times the productivity from 1 m2 per year. It has also managed to achieve six harvests a year on the City Farm. This is because of unlocking the natural potential of varieties under controlled vertical farm conditions that do not depend on climate, weather or seed contamination risks.
"Our goal was to develop a universal multifunctional tool that would tap into the natural potential of different varieties, increase their productivity, and improve quantitative parameters. We used nature-like technologies and adjustable LED lighting without adding any genetic modifications. Our complex is based on the extensive researches of the RAS Biotechnology Research Centre. It is economically viable for industrial cultivation of the crops in demand. In addition, it is completely environmentally friendly and waste-free," said Vasiliy Zotov, a Candidate of Biological Sciences, and the head of the project.
The vertical farm consists of module stands with automated watering and multichannel LED lighting systems, as well as a set of microclimate and substrate sensors. Currently, the team is developing databases and analyzes the effect of adjustable lighting on various crops at different stages: from in vitro to nursery plants and final products. In particular, the team studies the influence of adjustable lighting on the morphogenesis and production process (including the biosynthesis of secondary metabolites) in different varieties of plants, including future generations.
"Another important feature of the vertical farm and the controlled vegetation technology developed for it is their flexibility and universal nature. The system can be easily changed to fit a particular task. For example, lighting can be chosen and automatically adjusted to secure the growth of other plants: flowers, berries, potatoes, beetroots, or even wheat", said Dmitry Kravchenko, a Candidate of Agricultural Sciences, a senior researcher at the Federal Research Center for Biotechnology of the Russian Academy of Sciences, and a development and agricultural support specialist in the project.
The team has already received the first commercial orders from major agricultural producers and potato processing companies. In the future, the scientists plan to develop a technology for controlled vegetation of essential-oil-bearing plants and vegetables, such as tomatoes and peppers.
Lead Image: IMAGE: THE MODULE STAND WITH AUTOMATED WATERING AND MULTICHANNEL LED LIGHTING SYSTEMS. view more
CREDIT: FEDERAL RESEARCH CENTER FOR BIOTECHNOLOGY OF THE RUSSIAN ACADEMY OF SCIENCES
###
Disclaimer: AAAS and EurekAlert! are not responsible for the accuracy of news releases posted to EurekAlert! by contributing institutions or for the use of any information through the EurekAlert system.
VIDEO: Indoor Farming Biz AppHarvest Delivered Sales In First Earnings As Public Company
AppHarvest, the tech-forward indoor vertical farming company that went public in February, released its first earnings report showing Q1 net sales of $2.3 million for its tomato harvest
May 17, 2021
AppHarvest, the tech-forward indoor vertical farming company that went public in February, released its first earnings report showing Q1 net sales of $2.3 million for its tomato harvest. The stock ($APPH) was up on the news, rising to more than $13 a share in morning trading, but still well short of its closing high of $38.
Founder and CEO Jonathan Webb spoke to Cheddar about the company's challenges in building a facility and harvesting its product amid a pandemic and pointed to expanding in the future. "Our thesis is that controlled-environment agriculture will be growing almost all fruit and vegetable production at scale indoors," Webb said.
Vertical Harvest Maine, Sodexo Pair For Local Produce On College Campuses
n August 2021, Vertical Harvest Maine (VHM) will break ground on a 70,000 square foot, four-story farm in downtown Westbrook. Developer TDB LLC says that the master plan integrates residential apartments, commercial space, and four stories of parking
Indoor Farming Partnership Will
Increase Local Produce Served
On Maine’s College Campuses
May 18, 202|
Source: Sodexo SA
Westbrook, Maine, May 18, 2021 (GLOBE NEWSWIRE) -- Sodexo, a global foodservice provider and one of Maine’s largest employers, today announced that it will source as much as 80-percent of its lettuce products from Vertical Harvest Maine, the State’s newest hydroponic urban farm, and the first vertical greenhouse in the United States. The produce will be served at all fourteen Sodexo partners, including collegiate campuses from Fort Kent to South Portland. Earlier this year, Sodexo pledged to spend at least $1M at local Maine farms and food producers in 2021.
“We are a global company that is committed to spending locally,” says Varun Avasthi, Director of Strategic Partnerships, Sodexo. “One challenge we face when sourcing local food is Maine’s short outdoor growing season. The partnership with Vertical Harvest will be a game-changer for Sodexo’s ability to buy fresh produce twelve months per year,” Avasthi added.
In August 2021, Vertical Harvest Maine (VHM) will break ground on a 70,000 square foot, four-story farm in downtown Westbrook. Developer TDB LLC says that the master plan integrates residential apartments, commercial space, and four stories of parking. The company plans to grow over 1-million pounds per year of local produce, create 50 jobs, and hire Mainers with physical and intellectual disabilities, in coordination with State and local agencies. This year, Fast Company recognized Vertical Harvest in their annual “World Changing Ideas” awards, which honors businesses that are innovating solutions to world problems.
“VHM’s output will displace out-of-state produce and will not compete with local, traditional farms,” says Nona Yehia, Vertical Harvest founder. With the majority of Maine’s produce imported, VHM founders say indoor farming will have a positive impact on Maine’s agricultural output. “VHM is extremely proud to grow local food, and to create meaningful jobs for Maine’s underemployed,” Yehia says. The Westbrook location is the second for Vertical Harvest, the first is in Jackson Hole, WY.
“This partnership illustrates how strategically the Maine business community works together,” says Glenn Cummings, President, University of Southern Maine. “The partnership between Sodexo and VHM enforces our commitment to serving Maine-grown food whenever possible – it is a win-win,” Cummings said.
“This project exemplifies the goals and vision of Maine’s 10-Year Economic Development Strategy,” said Heather Johnson, Commissioner of the Department of Economic and Community Development.
Sodexo is one of Maine’s largest employers, with 760 employees and a $21M payroll. It serves 13,000 meals daily at colleges and hospitals across Maine, including Central Maine Medical Center and Southern Maine Community College. In 2015, Sodexo founded The Maine Course, a local organization with a mission to increase the company’s local food spend annually. Sodexo and VHM will prepare for the first harvest, which is planned for the Fall 2022 academic year.
# # #
About Sodexo North America” Sodexo North America is part of a global, Fortune 500 company with a presence in 64 countries. Sodexo is a leading provider of integrated food, facilities management, and other services that enhance organizational performance, contribute to local communities and improve quality of life for millions of customers in corporate, education, healthcare, senior living, sports and leisure, government, and other environments daily. Sodexo is committed to supporting diversity and inclusion and safety while upholding the highest standards of corporate responsibility and ethical business conduct. In support of local communities across the U.S., in 2020, the Sodexo Stop Hunger Foundation mobilized 10,000 Sodexo volunteers to distribute 4.1 million meals to help 5.9 million children and adults meet their immediate food needs. Since 1996, the Stop Hunger Foundation has contributed $36.7 million to help feed children in America impacted by hunger. To learn more about Sodexo, visit us.sodexo.com, and connect with us on Facebook, Instagram, LinkedIn, Twitter and YouTube.
Photo Credit: Harriman and GYDE ArchitectsPhoto Credit: Harriman and GYDE Architects
Contact Data
Dasha Ross-Smith
Sodexo
Dasha.Ross-Smith@sodexo.com
Squamish Nation Grows Plans For Food Security With A Hydroponic Farm
While the outside of this 40-foot container is rather striking, it’s what’s on the inside that counts. 🌱
While The Outside of This 40-Foot Container Is Rather Striking,
It’s What’s On The Inside That Counts. 🌱
May 19, 2021
By: Elisia Seeber
A big bright orange container has just landed in the Sḵwx̱wú7mesh Úxwumixw (Squamish Nation) community of X̱wemelch'stn in North Vancouver.
While the outside of the 40-foot container is rather striking, it’s what’s on the inside that counts.
The container is a Growcer hydroponic modular farm that will support the community's wellness by allowing them to grow a year-round supply of fresh produce, including leafy greens, herbs and traditional medicinal plants.
Creating a sustainable healthy source of produce and increasing food sovereignty has long been a goal for the Squamish Nation, and the hydroponic farm is another piece of the puzzle, said Kelley McReynolds, director of Squamish Nation’s Ayás Méńmen Child and Family Services.
“Part of the reason that we started to look at ways that we could [provide food] was working from our values as Squamish people and our values around food sharing,” she said.
“Traditionally, we as a community, and as families, would go out and hunt and we would gather out on the lands and the waters and we’d bring it back to our community and people would only take what they need, and the rest of it would be shared.”
Through the launch of a food distribution program about four years ago, McReynolds said the team began breaking down the stigmas and fears around food insecurity and shifting back to their traditional ways, to ensure everyone in the community felt comfortable receiving food.
“We didn't want to look at the food as being a form of charity, or only for those who don’t have food,” she said.
Hydroponic farm idea sprouts
When the COVID-19 pandemic hit, McReynolds said food security worries increased for some members and the team started thinking further outside of the box about how they could address future food scarcity.
That’s when the idea for the hydroponic farm sprouted.
Squamish Nation has looked at more traditional styles of farming, and also has 19 garden boxes set up outside of their office where they grow fruit and vegetables and a traditional medicine garden.
“We plant every year and we harvest that to give to community,” McReynolds said. “We do a lot of training with our youth and our families to help them understand the plants, gardening and harvesting."
She said a thought they always had was, “think what we could do if we had farmland, we could feed so many more people.”
“But, you know, we live in a city and you don't have access to that kind of open space,” McReynolds said.
“So, when we looked at this option of the hydroponic farm and saw that it's the size of a shipping container, we thought, ‘that's pretty cool.’ It comes with all the equipment you need inside there. And, you can get it set up and within five to six weeks you are ready to make your first harvest and it yields approximately 450 heads of produce per week. That's a lot.
“We thought, ‘wow, that's amazing.’”
The founders of the ingenious technology and social enterprise came up with the idea based on their firsthand experience of food insecurity in Nunavut in 2015 and wanted to create a system that allowed communities to grow fresh produce anytime, anywhere, in any climate.
The growing technology was first deployed in food insecure, remote communities, but has since expanded to partner with schools, non-profits, and non-remote communities who see value in growing food locally – like Squamish Nation.
The electronically run hydroponic farms cost around $180,000 to set up and will produce fresh food for around 30 years, according to Growcer.
How does the modular hydroponic farm work?
Hydroponics is a soil-free growing method that uses nutrient-rich water to grow plants using less space, time, and crop inputs.
“The modular farms are automated to provide full environmental control,” Growcer’s website states, adding that plant growth factors such as light, nutrients, temperature, humidity, carbon dioxide, and water are monitored in real-time.
Once set up, a range of 140 leafy green plants can be grown in as little as six weeks.
“It's all brand new to us,” McReynolds said, adding that Growcer would be training staff this week and continue to provide support through their hydroponic farming journey.
“We’re all really excited.”
Squamish Nation to open Food Pantry and Community Kitchen
Produce from the new farm will be shared with families serviced by Ayás Méńmen, the youth centre and the future Smeḵw'ú7ts (Food Sharing) Community Kitchen and S7ílhen (Food) Pantry, which is hoped to be up and running by the summertime.
“We will continue to do monthly food distribution, but we will also have food on our shelves and in the freezers for any of our members who are in need … whatever the situation may be,” McReynolds said.
The hope for the community kitchen is to build a healthy community by providing a safe place for members to learn and improve their food preparation and cooking skills through workshops, which may start on Zoom during the pandemic. Ayás Méńmen also plans to host a six-week program for community members to meet once a week to cook and take a meal home for their families.
“I think what excites me about that is we are such relational people,” McReynolds said. “To be able to come together and learn and share and grow and laugh and tell stories, that's so healthy and therapeutic and it brings joy to your heart just being able to be together.”
While there’s still a bit of work to be done before the hydroponic farm starts producing the goods, McReynolds has more big plans.
“I have this vision of us being able to do a Friday night or Saturday afternoon market where we can have the fresh produce, we can have music, we can maybe have food trucks and we can gather together,” she said.
“I just think it's just a great opportunity for us to celebrate who we are as farmers and come together as a community.”
Elisia Seeber is the North Shore News’ Indigenous and civic affairs reporter. This reporting beat is made possible by the Local Journalism Initiative.
"Together We Are Expanding Our Facility In Sweden"
"Our expansion will enable us to offer our sustainably-grown salads to more Swedish households throughout the year, so we are looking forward to an exciting time," says Andreas Wilhelmsson, CEO of Ljusgårda
"Our expansion will enable us to offer our sustainably-grown salads to more Swedish households throughout the year, so we are looking forward to an exciting time," says Andreas Wilhelmsson, CEO of Ljusgårda.
In April, the first batch of salads was harvested in the company's new premises – and already now, Ljusgårda can deliver significantly more locally-grown salad to Swedish households, all year round. When the new 7000-m2 indoor farm, of which 2500 m2 growing area, is completed in the summer, Ljusgårda will become one of Europe's largest vertical farms.
"We are delighted to help Ljusgårda to produce local, climate-smart salads, says Henrik Nørgaard, Nordic Commercial Director of Agriculture at Signify[1]. "Ljusgårda shares our vision of a sustainable transformation within agriculture and is focusing in particular on quality and flavor."
Supporting the expansion
Andreas continues, "Signify has extensive experience of advanced lighting solutions and works with other large-scale indoor farms. They provide us access to lighting experts who can help us to continuously improve production. Signify is also one of the few suppliers with the capacity to deliver in line with our growth plan. Together we are expanding our facility in Sweden. Signify’s controllable light spectrum enables us to optimize the light for cultivation and produce the highest quality crops," Andreas continues.
Andreas Wilhelmsson
More than 70% of the fruit and vegetables consumed in Sweden today are imported by truck, ship, or plane from other countries. With the aim of making food production more sustainable, Swedish vertical farmer and salad producer Ljusgårda plans to increase its production 20-fold and expand its cultivation capacity to produce at least 60 tons of salads a month, which is the equivalent of around 1 million bags.
Signify is helping the Swedish vertical growers to expand their production facility in Tibro. By expanding its cultivation area from 300 m2 to 2500 m2, Ljusgårda will be able to supply fresh, locally produced salad all year round. Signify is providing the company with its latest high-tech solutions: Philips GreenPower LED production modules and the Philips GrowWise control system. These allow the light spectrum and lighting levels to be controlled, resulting in improved quality and higher yields per square meter.
As a result, Ljusgårda can ensure that its salads are tasty and nutritious. LED lighting also makes it simpler to predict growth levels, which means that it is easier for Ljusgårda to adapt its production to market demand during the season. The lighting is managed by the Philips GrowWise control system to schedule growth cycles well in advance and to allow for greater automation.
Making an impact
Henrik adds, "This is important to Signify because of our strategic goal of helping our customers accelerate the use of sustainable farming to improve agriculture’s impact on climate change. By using the latest lighting systems in vertical farming, Ljusgårda can supply salads that meet the highest food safety standards. The right lighting also results in plants of a higher quality and a higher percentage of crops being consumed, reducing food waste.'
"Additionally, by helping Ljusgårda to grow locally we contribute to significantly reducing the food miles these salads have to travel before making it to Swedish consumers. We are therefore proudly taking part in the journey from the first green shoots to more consumers being able to enjoy Swedish salads all year round," Henrik states.
Today, Ljusgårda's salads are sold in more than 60 ICA supermarkets, mainly in the Swedish regions of Västra Götaland and Småland. With the expansion of the facility and production on a much larger scale, Ljusgårda aims to supply sustainable Swedish salads to stores throughout Sweden.
Supporting food availability through horticulture LEDs illustrates Signify's commitment to supporting good health and wellbeing (SDG3). It is key to Signify's commitment to doubling the percentage of our revenues for brighter lives, which benefit society, to 32%. "This is part of our Brighter Lives, Better World 2025 program, which was launched in September 2020."
For more information:
Signify
Daniele Damoiseaux, Global Marcom Manager Horticulture
For more information:
Ljusgårda
info@ljusgarda.se
www.ljusgarda.se
Sources used:
[1] Climate-smart agriculture is an integrated approach to managing landscapes—cropland, livestock, forests, and fisheries—that addresses the interlinked challenges of food security and accelerating climate change.
11 May 2021
Latest Research On Indoor Farming Now Just A Click Away
OptimIA is a website featuring research results from six horticulture, engineering, and agricultural economics professors and Extension specialists
By Brian Sparks
May 19, 2021
Greenhouse growers now have access to a new online resource to help make their indoor farming businesses more productive and profitable. OptimIA is a website featuring research results from six horticulture, engineering, and agricultural economics professors and Extension specialists, and their graduate students and technicians, at Michigan State University, The Ohio State University, Purdue University, and the University of Arizona. Born from a four-year, USDA grant-funded project, the website is one tool researchers are making available to anyone interested in overcoming the technological, environmental, and financial challenges common to indoor farming.
In addition to the latest published research, the website offers trade articles authored by OptimIA project scientists, indoor production research highlights, recorded webinars presented by top national and international indoor farming experts, upcoming events related to indoor farming and the OptimIA project, and FAQs.
The OptimIA project’s ultimate goal is to define the environmental parameters within which leafy greens such as lettuce perform best in indoor vertical farms. While the work of each project researcher is unique, it all centers around the effects of light, carbon dioxide, humidity, temperature, air movement, and economics (operating, labor, equipment, etc.) on the sustainability and profitability of using indoor farms to produce leafy greens and microgreens.
The site will be frequently updated with new research results, as they become available.
To access the OptimIA project website, click here.
OptimIA is funded by the USDA‘s Specialty Crop Research Initiative.
Crisis Looming In Trucking And Shipping; Here Is What’s At Stake for Horticulture
Spear called on the Senate panel to advance a bipartisan surface transportation infrastructure bill this year, focused on roads and bridges, that’s responsibly funded with a modernized user-fee system
By American Trucking Associations
May 12, 2021
American Trucking Associations President and CEO Chris Spear told the Senate Commerce, Science & Transportation Committee this week that growing pressures on the U.S. supply chain are fast approaching crisis levels, and that immediate action from Congress is needed to ensure our economic recovery is not derailed by further disruptions.
In testimony before the Subcommittee on Surface Transportation, during a hearing titled “Freight Mobility: Strengthening America’s Supply Chains and Competitiveness,” Spear outlined the trucking industry’s key priorities on infrastructure, workforce, safety, and the environment, detailing specific legislative steps lawmakers must take to ensure the integrity and longevity of the nation’s supply lines as the economy climbs out of the COVID-19 crisis.
“Investments in our supply chain are desperately needed, including the roads and bridges that connect our ports, rail yards, and airports to the National Highway System. Do that, and you will witness measurable efficiencies, including gains in productivity and safety, job growth, and sustainable employment, and historic reductions in carbon emissions,” Spear told members of the committee in his opening remarks.
The trucking industry moves more than 72% of the nation’s freight tonnage, and over the next decade, trucks will be tasked with moving 2.4 billion more tons of freight than they do today. Breakdowns in surface transportation infrastructure, as well as a severe and widening truck driver and diesel technician shortage, threaten the industry’s ability to keep goods moving safely and on time.
Freight bottlenecks and congestion on the National Highway System already cost the trucking industry an annual 1.2 billion hours of lost productivity, which is equivalent to more than 425,000 drivers sitting idle for an entire year — adding $75 billion to the cost of freight transportation. In addition, the industry currently faces a shortfall of nearly 61,000 drivers and will need to hire roughly 1.1 million new drivers over the next decade to keep pace with the economy’s increased freight demands.
Spear called on the Senate panel to advance a bipartisan surface transportation infrastructure bill this year, focused on roads and bridges, that’s responsibly funded with a modernized user-fee system. He also called on lawmakers to pass the DRIVE-Safe Act, legislation to remedy the driver shortage by promoting opportunity and enhancing safety training for emerging members of the trucking workforce. The bipartisan bill is backed by more than 117 organizations representing all levels of the U.S. supply chain.
A transcript of his opening remarks is available here.
'Acute' Pallet Shortages Putting Fresh Produce Supply At Risk
The shortages are "acute," according to United Fresh Produce Association’s letter to the industry in a news release
A Pallet Shortage Is Affecting
The Produce Industry In Many Ways
By AMY SOWDER
May 19, 2021
Severe pallet shortages are inflicting a widespread effect on the produce industry — including the availability of produce to consumers.
The shortages are "acute," according to United Fresh Produce Association’s letter to the industry in a news release.
The association detailed a multitude of issues that are impacting pallet availability, including:
Efforts of wholesalers, distributors and retailers to ensure sufficient inventory of non-perishables given previous pandemic-related impacts;
Availability of lumber to repair and build new pallets;
The escalating price of lumber when it is available;
Nonperishable inventory dwell time increase; and
Lack of available trucks to relocate pallets.
“The lack of pallets is adding stress to a supply chain that is already facing significant challenges, which include a lack of available trucks and shipping containers, ongoing labor challenges, fluctuating fuel costs, pandemic-related challenges, and a pending shortage of resin used to make reusable containers and pallets,” according to the release. “At this time, expectations are that the pallet shortage will continue for months, perhaps for the balance of 2021 – all at a time when many North American produce items are just beginning seasonal harvests and shipments.”
Listen to United Fresh’s John Hollay discuss this pallet issue with retail and Produce Market Guide editor Ashley Nickle in our Tip of the Iceberg podcast episode.
The issue has a wide and deep scope of negative impacts, according to United Fresh:
The shortage of lumber and wood products has increased the cost of raw lumber 200% to 350% and is making the cost of wood pallets increase incrementally;
In one example, in the past few weeks, pallet costs have increased more than 400%, if the pallets are even available, and often they are not;
One farmer was told by one pallet supplier that they are not taking any new customers due to an inability to fill even existing customer demand;
Companies are forced to bring pallets from other jurisdictions, thereby incurring border and transportation costs; and
Pallets are being held in-house due to delayed and canceled orders from pallet services, leading to higher storage charges and increased congestion within operations.
Company leaders along the supply chain need to collaborate to balance organizational goals relative to overall availability of goods with availability of food.
“If there is not a concerted effort across the supply chain to ensure pallet availability for shipment of produce, there is little doubt that it will be very difficult, if not impossible, for the grower-shipper community to meet buyer, and ultimately consumer, demand for produce,” according to United Fresh.
Also, growers and shippers are trying to comply with pallet requirement specifications, but this is even more challenging.
United Fresh’s stance is that temporary modifications or exceptions to pallet requirements — as long as those exceptions don’t jeopardize safety — would help greatly until this pallet shortage is resolved.
All partners in the supply chain should have regular conversations with their pallet suppliers to understand the situation and pallet inventories and availability, according to the release.
“We welcome the opportunity to work collaboratively with all parties within the supply chain to mitigate the impacts of the current shortages and will reach out to stakeholders to identify a path forward that provides solutions to this increasingly disruptive threat and enables the continued flow of goods,” according to United Fresh.
Learn more details with this interview.
Lead Photo courtesy Michael Gaida/Pixabay
Hydroponic Farming: Need of The Hour During Pandemic And Its Growing Trend In India
Hydroponic farming is thriving in India. One of the major factors driving its growth is also the technology curve that diminishes costs and helps in scaling its operations
May 19, 2021
According to the World Economic Forum, the global population is expected to reach nearly 10 billion by 2050, making the requirement of food 60 percent higher than it is today.
Agriculture in India has always been governed by variables - weather, quality of soil and seed, availability of water, skilled labour, etc.
By Shivendra Singh,
The onset of the COVID-19 pandemic has made everyone housebound. Right after the announcement of the lockdown, people rushed to grocery stores to stock up shelf-stable items like packed, frozen food and other essentials. That’s when many Indians realised the need for nutrition, health outcomes of food and how vulnerably it is dependent on supply chain and climate change.
On the other hand, scientists are stressing over the past decades that human actions are pushing life towards disaster. The steep surge in the demand for food production, transportation and processing are putting enormous pressure on the planet. According to the World Economic Forum, the global population is expected to reach nearly 10 billion by 2050, making the requirement of food 60 percent higher than it is today. The report also suggests that there will be a shortage of arable land to meet this burgeoning demand for food production.
The anticipated scenario of food requirement and shortages spurred many Indians to consider planting vegetables in their backyard or rooftop. This has enabled people to invest in high tech urban farming systems and produce fresh vegetables more efficiently.
The Revolution of Hydroponic Farming
Agriculture in India has always been governed by variables – weather, quality of soil and seed, availability of water, skilled labour, etc. Additionally, the increase in food production in India has always been at the expense of the water supply. As per the estimates, around 70 percent of the world’s freshwater is used for agriculture, on the other hand, the 70percent of water contamination also comes from agriculture. With the integration of technology in agriculture, it has become easier to grow food in cities through urban farming or high-tech hydroponic farms. This is becoming key to improving nutrition and dealing with the disruptions in the food supply chain.
Hydroponic has been around for decades but with the efforts of new-age agritech startups, it is evolving into innovative urban farming methods. Hydroponic farming which simply means growing fresh vegetables and fruits in nutrient-rich water instead of soil requires less space and resources. Based on modernised techniques, soil-less farming results in higher productivity in a controlled climate and with no risk of the attack of the pests and insects. Agritech startups in the market are providing every possible support for hydroponic farming set-up. For the first time in India, few agritech startups are providing Buy Back option for hydroponic produce as well as Bank Guarantee. It will further boost the hydroponic farming technique in the country.
Given the present ‘stay at home’ scenario, hydroponic farming is gradually becoming a household trend in India. The hydroponic systems are designed in a way that provide healthier, fresh and more nutritious produce with longer shelf life. The technology helps in saving valuable water, land and labour resources that further creates an efficient ecosystem. Moreover, the controlled growing system enables the production of food with no use of harmful chemicals resulting in 100 percent residue-free farming.
Immunity has become the new buzzword
The pandemic had made it necessary to understand the importance of adequate nutrition to maximize their health, boost immunity and reduce the risk and impact of the virus. Having a strong and resilient immune system is the need of the hour. Thus, the devastating aftermath of the pandemic should be a catalyst to expand our taste, knowledge and awareness and contribute to building a more efficient and sustainable food system.
Usually, human beings underestimate the power of good choices and individual behavioural change in creating a healthier food system. Adopting a hydroponic farming system helps align the food habits with the wellbeing of the planet and helps people turn from being ‘junk foodies’ to genuine chemical-free food lovers. As a result, it helps consumers become more concerned about the environment and reshape their eating habits to reduce the vulnerability of the disease.
Bottomline
Hydroponic farming is thriving in India. One of the major factors driving its growth is also the technology curve that diminishes costs and helps in scaling its operations. Further, integration of Artificial Intelligence and Data Analytics measure important indicators that help in food/crop planning and hence help connect in the food security ecosystem. Besides the technological factors, the need for creating a smarter and green market in highly populous nations also creates space for hydroponic farming (rooftop or vertical farming) to grow as a trend.
(The author is Founder, Barton Breeze, India’s Fastest Growing Commercial Hydroponic Farm Specialist. Views expressed are personal and do not reflect the official position or policy of the Financial Express Online.)
Upward Farms Launches First Organic Vertical Farm In The US Northeast
Upward Farms, an aquaponics vertical farming company, has opened its new headquarters in Greenpoint, Brooklyn, New York
MAY 19, 202
Upward Farms, An Aquaponics Vertical FarmingCompany,
Has Opened Its New Headquarters
In Greenpoint, Brooklyn, New York
The innovative new facility – which is Upward Farms’ first – utilizes the company’s next-generation technology in both commercial production and research and development.
The operation, powered by breakthrough end-to-end automation, is USDA Certified Organic, making Upward Farms the first and only Certified Organic vertical farm in the Northeast region.
It includes a fishery that is Monterey Bay Aquarium Seafood Watch “Best Choice” rated, and it sustainably farms mercury-free, antibiotic-free and hormone-free striped bass.
Upward Farms’ ready-to-eat microgreen mixes are currently available in all Brooklyn Whole Foods Market locations and are expected to be available in all New York City Whole Foods Market locations in the coming months.
Jason Green, Upward Farms CEO and co-founder says: “Upward Farms’ new facility successfully scales our vertical farming model. Controlled environments and ecological farming are not at odds, but are powerful compliments for the next generation of farming.
“We’re delivering higher yields, disease resistance, safety, and sustainability in a platform that can be deployed anywhere in the world, regardless of climate.
“The pandemic underscores the importance of shoring up supply chains to be more local for transparency, safety, and efficiency. Localized produce is especially important from a food safety standpoint.
“As vertical farms scale, we can create a supply chain that’s fundamentally more resilient than shipping produce around the country, if not around the world.”
As consumers continue to gravitate toward fresh, organic produce and purchase more groceries online, Upward Farms offers consistent product availability, quality, and scalability for locally grown greens.
According to the Organic Produce Network, US organic produce sales rose by 14 percent in 2020 compared to 2019, outpacing growth in conventional produce and highlighting the increased demand in a post-Covid world for organic fresh produce.
Previously sold under the brand names Seed & Roe and Edenworks, Upward Farms microgreens are a best-selling product in the salad category where sold.
Two Upward Farms’ microgreen blends – Mighty Microgreens Mix and Spicy Microgreens Mix – will soon be at Whole Foods Market stores across New York City.
The Company anticipates further growth to answer demand in the US Northeast and beyond. The Company has raised approximately $150 million to date from investors that include Prime Movers Lab, Tribe Capital, and strategic investors from the food, agriculture, and consumer packaged goods spaces.
Ohio State Graduates Find Success With Hydroponic Farming
The small hydroponic farm grows fresh exotic and artisan greens from around the world
By Dennis Biviano, Columbus
May 18, 2021
COLUMBUS, Ohio — James Hu and Andrew Herczak attended Ohio State, both starred on the fencing team and now the friends are business partners, co-owning Columbus Artisan Growers.
What You Need To Know
The OSU grads said there were a lot of challenges in growing their business
The farm grows fresh exotic and artisan greens
The vegetables are harvested for seven Columbus restaurants
The small hydroponic farm grows fresh exotic and artisan greens from around the world.
Although the start-up has experienced some ups, downs, and pivots during the pandemic, past experience taught them there's no quitting in this team.
“There's a lot of things that we learned at Ohio State, especially on the fencing team, is I think really, is really a driving factor of why we are doing what we are, especially how we survived through the pandemic, just fighting through everything. That was one of the things our coach really drilled into us,” said Hu.
Herczak, who is originally from Poland, said he's always grown up with a passion for plants and gardening.
He said everyone is looking for quality and organic these days.
The best part for him harvesting for seven local restaurants for edible foods and garnishes.
'These are native to South and southern America. We also harvest them for their flowers as well — has a little kick of spice. A lot of restaurants like that, that unique flavor, plus the unique texture on it,” said Herczak.
Even though hydroponic farming is their new labor of love, Herczak still practices fencing during his downtime at their downtown Columbus facility.
Just like many competitors and competitions both have faced in the past, Herczak and Hu said they have aspirations of advancing well beyond the Buckeye State.
“We definitely want to reach everywhere in the United States, even go international. We think the business model of a small hydroponic farm is more viable then we see some of the larger, big players in the field,” said Hu.
For more information on Columbus Artisan Growers, click here.
NYC’s Bowery Farming Unveils Farm X - A Science, Breeding Hub
Farm X will accelerate the commercialization of products specifically designed for Bowery’s indoor system. The hub will expand the company’s research and development capacity by almost 300%, including cultivation of strawberries, root vegetables, tomatoes, and peppers
By AMY SOWDER
May 18, 2021
(Photos courtesy Bowery Farming)
New York City-based vertical grower Bowery Farming has opened Farm X, an innovation hub for plant science in Kearny, N.J., next to Bowery’s original R&D Center of Excellence and first commercial farm.
Farm X will accelerate the commercialization of products specifically designed for Bowery’s indoor system, according to a news release. The hub will expand the company’s research and development capacity by almost 300%, including cultivation of strawberries, root vegetables, tomatoes, and peppers.
“From day one, our R&D team has been working tirelessly to unlock the next frontier in agriculture, and Farm X enables us to expedite the discovery of new vibrant crops and pioneering technological advancements that will further accelerate our momentum as the category leader,” founder and CEO Irving Fain said in the release.
At Farm X, Bowery’s plant breeders, plant physiologists, biochemists, and others will be able to test more, faster—ultimately accelerating the discovery of new crops, growing recipes, and efficiency improvements that can be replicated at scale across the company’s network of commercial farms.
Farm X also features a sensory lab where Bowery will seek ideal cultivars for indoor growing, as well as launch an onsite breeding program. In that program, Bowery’s team will develop varieties that thrive in its unique growing conditions and evaluate each one for optimal taste, quality and yield. Bowery’s controlled indoor environment and around-the-clock crop monitoring should increase the speed and efficiency of these goals.
Researchers are also developing new greens, such as the Farmer’s Selection category, which launched in January. Bowery plans to release a new, small-batch green every four months under this new category. The first, Bowery Mustard Frills — “hearty mustard greens with a tingly start and a fiery, wasabi-style finish,” according to the release — was available through April 2021. Green Sorrel, bright, tart baby greens with a zing and the next release in the series, is now available from May through August.
Farm X also serves as an experimental space for innovation in farm design, data science, computer vision, autonomous robotics, hardware, and software that can be deployed in Bowery’s growing network of commercial farms.
To further that mission, Bowery hired Injong Rhee, formerly vice president at Google and chief technology officer of Samsung Mobile, as its chief technology officer. Rhee will work on ensuring that every farm continues to benefit from the collective intelligence of the BoweryOS, the company’s proprietary operating system which integrates software, hardware, sensors, computer vision systems, machine learning models and robotics to orchestrate and automate the entirety of operations. The technological learnings discovered at Farm X will be integrated and applied at scale across Bowery’s network.
Bowery has experienced more than 750% brick-and-mortar sales growth, and more than quadrupled sales with e-commerce partners, including Amazon, since early 2020, according to the release. Bowery’s newest commercial farm in Bethlehem, Pa., will bring local produce year-round to a surrounding population of 50 million people within a 200-mile radius.
Vertical Farming: Sustainable Food Never Tasted So Good
Vertical farming enables the ability to grow food closer to large population centers and also reduces the “food miles” associated with distribution thus reducing the carbon footprint
Richard Howells | Brand Contributor
May 5, 2021
There’s a lot of good press these days about the potential of vertical farming to help address climate change. The idea is to use hydroponics and other techniques to grow food “soil-lessly” (if that’s a word) in vertically stacked layers.
Vertical farming enables the ability to grow food closer to large population centers and also reduces the “food miles” associated with distribution thus reducing the carbon footprint.
But not so fast.
Mark Korzilius from &ever GmbH – a vertical farming startup with a farm in Kuwait and one coming in Singapore – disagrees with the food miles argument. Here’s why.
Quality first: Iceberg no more!
In a recent interview on the Climate21 podcast with Tom Raftery, Korzilius urges us to “forget about transportation in order to justify vertical farming.” Instead, the focus needs to be on bringing the best product to the consumer. Quality, in this case, means healthy, leafy greens.
“You want to have high nutrients, high in secondary metabolites, everything that is extremely valuable for your body,” said Korzilius.
To most of us, the antithesis of healthy leafy greens is iceberg lettuce. However, as Korzilius explained, it tends to be cut, bagged, and refrigerated for distribution.
“This is where a lot of the carbon footprint comes from,” said Korzilius. “And let’s be honest, iceberg in foul-smelling bags is less than appetizing.”
Instead, &ever follows a “harvest on demand” process. It distributes its leafy greens as potted plants – like you might see with basil or other herbs in your grocery store. Korzilius claims that the customer receives the best-tasting, locally grown leafy greens available, without plastic or refrigeration needed. The chef at the Four Seasons in Kuwait, reportedly, thinks the coriander is the best he’s ever tasted!
Greater control and higher yield, too
&ever’s operations are entirely indoors, where the climate is controlled. This is crucial for successful yields. Growing spinach, for example, is notoriously difficult with vertical farming. But by experimenting with the right seeds, lighting, and temperature, &ever has found the right recipe.
One key advantage is that &ever can grow without pesticides – which, in the end, is just another form of energy. It can also optimize light spectrums to achieve desired results. Many of its crops run on 18 hours of light and six hours of darkness.
The result is higher yields over the course of a year. &ever can grow 18 cycles a year, compared to maybe seven for a traditional greenhouse. And, says Korzilius, it can do it with 85% less water.
Complexity managed
Korzilius also makes the point that tracking all the variables – such as light, temperature, water, production cycles, energy costs, growing recipes, and more – makes for a lot of complexity. SAP is working with &ever to help manage it all. Vertical farming is a high-tech endeavor where control is the key to success. We’re proud to help be part of the solution. Hopefully, this approach to growing food will help minimize carbon output while also delivering delicious food – from (vertical) farm to table.
Listen to the podcast here and be sure to check out the latest research from Oxford Economics on how to “Build a Resilient and Sustainable Supply Chain.”
I've been working in the supply chain management and manufacturing space for over 25 years, and I'm responsible for driving the market direction and positioning of SAP’s Supply Chain Management and IOT solutions. Prior to joining SAP in 2004, I spent 15 years with Marcam Solutions where I was VP of Marketing for the companies Process ERP solutions. I have also implemented ERP and SCM systems at companies such as Nestle, Gillette, Colgate Palmolive, Rohm & Haas, Wyeth, Royal Worcester Spode and Dairy Crest. I hold a Bachelor of Science degree in Computer Science from the University of Mid Glamorgan in the UK. Follow me @howellsrichard
Lead photo: Vertical farm and its employees taking care of plant growth. Plant food production in vertically stacked layers. GETTY
Modular Hydroponic Growing Spaces In Freight Containers For Local Food Production
Freight Farms’ design was the first containerized vertical growing environment using hydroponic technology
May 17, 2021
Southeastern Pennsylvania Correspondent
A Massachusetts company has developed a unique, hydroponic growing environment in closed 40-foot freight containers that are being used world-wide to grow produce in areas with bad soil or weather conditions not conducive to outdoor growing.
Bay State natives Jon Friedman and Brad McNamara were developing rooftop greenhouses in the early 2000s when they realized a modular, hydroponic container might be a more viable solution.
Hydroponics wasn’t something new. Historians believe this soilless gardening can be traced back to hanging gardens of Babylon in Iraq built by King Nebuchadnezzar about 600 BC. Nutrient-rich water was pumped to the gardens from the Euphrates river to sustain its plants. A water-based growing thread continued through history and in the 1930s a University of California scientist, William Gericke, coined the term from the Greek word “hydro” (water) and “ponics” (work).
Friedman and McNamara, who were building outdoor, roof-based gardens on older residential buildings, looked outside the box, and turned their focus to widely available shipping containers.
They thought they could provide the equivalent of 2 acres of growing space in traditional 40-foot-by-8-foot containers and extend growing seasons year-round everywhere — especially in areas that couldn’t support traditional outdoor agriculture or in parts of the world affected most by climate change.
They named their company Freight Farms and placed their first container less than a decade ago. Now the concept is catching on worldwide.
View Photos From Freight Farms
Freight Farms’ design was the first containerized vertical growing environment using hydroponic technology. It was initially funded by a Kickstarter campaign in 2012, where they raised the funds to build a prototype to allow local food production to be available to everyone, anywhere.
The first commercial unit was installed at Boston Latin School, the oldest public school in the U.S., to produce fresh produce for the school cafeteria as well as serving as a teaching classroom for high school students.
“The company has placed 350 units in 48 states and 32 foreign countries,” Friedman said.
The company also introduced proprietary software called “farmhand” to help automate many farm processes, and is manufacturing its 10th generation container, the Greenery S, incorporating the latest technology and automation for vertical, hydroponics growing.
Growing Strong
Hydroponic Operation Supplies High-End Restaurants
Art Petrosemolo, Southeastern Pennsylvania Correspondent
Although the Freight Farms container units are capable of growing a variety of produce, leafy greens are its specialty and the best choice for farmers looking to sell their harvests year-round.
Containers also have been embraced by educational institutions to supply fresh vegetables for cafeterias and serve as learning and teaching space.
St. Joseph College in Standish, Maine, has been operating a Freight Farms unit for years to both supply fresh vegetables to its dining facilities as well as for student employment.
The site also has been a tool for community involvement with St. Joseph students working with a town Institute for Local Food System Innovation utilizing the Freight Farms container in partnership with a large hydroponic farm and commercial processing kitchen for events and agritourism.
With a decade head start in the business, Freight Farms does not have major competition in hydroponics container gardening production, although, in recent years, it has seen significant growth in multiple indoor soil- and water-based farming formats including warehouses, greenhouses and pods that are addressing growing produce year-round.
Climate change has increased concern about food production for growing populations worldwide with extreme weather conditions and higher levels of carbon dioxide in the atmosphere.
Friedman and McNamara have always been aware that the challenge to expansion for stand-alone, container gardening is the cost of power and each new rendition of their growing units has addressed both power consumption and automation to be more efficient.
Their latest Greenery S model uses growing lights that are 50% more efficient than previous models and the technology allows farmers to choose pre-set growing modes to maintain higher yields — 20% higher than earlier models — while prioritizing energy use.
Addressing affordable and clean power for customers, Freight Farms recently partnered with Arcadia, a Washington, D.C., energy company to offer affordable, renewable power options for customers.
Going forward, Friedman said growing container units will continue to become more efficient, allowing owners to increase their growing yield while having more control of their energy use to power the unit.
Slide Show Photos:
Lights and plant arrangements in Freight Farms new Greenery S model container.
Photo provided by Freight Farms
Leafy greens grow in Freight Farms’ own Greenery Farm container.
Photo provided by Freight Farms
This Freight Farms container is ready for shipment.
Photo provided by Freight Farms
Freight Farms' containers under construction in their Vermont facility.
Photo provided by Freight Farms
Lexy Basquette, Freight Farm’s on-site farmer, checks on some of her growing plants.
Photo provided by Freight Farms
Greenhouses, Vertical Farming and Urban Ag: Controlled-Environment Agriculture Has Growth Potential
Paul Post, New York Correspondent