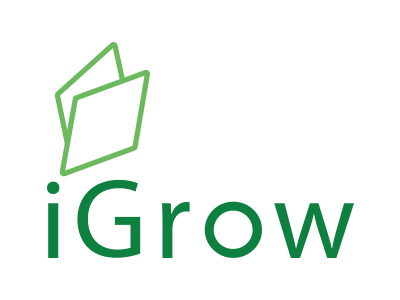
Welcome to iGrow News, Your Source for the World of Indoor Vertical Farming
Delivering The Optimal Growing Parameters
“Especially in the pharmaceutical or supplemental industry, you need an extremely strict batch control that leaves no room for variation,” says Dr Alexis Moschopoulos, Managing Director at Grobotic Systems.
The Grobotic Systems team shows off an early prototype Grobotic chamber. From left to right: Gareth Coleman (Software Developer), Richard Banks (Chief Technology Officer), Dr Alexis Moschopoulos (Managing Director), and Andrew Merson (Mechanical Engineer). Credit: UKRI.
Growing a new variety
Indoor farming has numerous growing parameters to take into account. Particularly when growing a new variety, all variables should be perfected in order to reach an optimum yield. In an indoor space, experimenting with these environmental parameters might, however, seem tricky. But what about trying out this environment in a smaller setting, such as an experimental growth chamber?
Alexis is fully aware of the challenges that vertical farmers face. The environmental control needs to be as precise as possible, as the effect of different light spectra or nutrients may have a significant impact on crop yield and quality. With this challenge in mind, Grobotic Systems brings a new solution to the market: a compact and highly instrumented growth chamber. “It’s an experimental chamber rather than a farming chamber. Therefore, you won’t use it to grow vegetables, but you can use it to identify which growing parameters are best suited to your crops,” Alexis says.
The Grobotic Systems team outside their workshop in Sheffield, England. From left to right: Dr Alexis Moschopoulos, Richard Banks, Andrew Merson, and Gareth Coleman. Credit: UKRI.
On your desk or under your bench
According to Alexis, the chamber fits on your desk or under your bench. It can apply any environmental condition preferred, including light spectra and temperature. Internet connection via the growth chambers allows users to monitor plants on their cellphones via integrated cameras and other sensors inside the chamber.
Another advantage of the chambers’ size is that they can be stacked in an array, adjusting variables in each chamber. In this way, a multi-variable experiment can help users identify which environment works most optimally for their intended crop. “When using a large cultivation room, it is hard to split the room into different temperatures. A smaller cultivation space, such as our growth chambers, can be placed anywhere, just like a personal computer. Moving away from the large expensive capital equipment and machinery to small and stackable experimental chambers saves a lot of space and money.”
Alexis first came up with the concept of the growth chamber during his PhD and postdoctoral work in plant genetics. Several prototypes are currently being used at research institutes and start-up companies. Grobotic Systems is working on a more advanced growth chamber that will be launched in the summer of 2021: “We are integrating feedback from the deployed prototypes into the design of the advanced chamber, and we will start marketing the advanced chamber later this year.”
Richard Banks designs a control system circuit board for an early prototype Grobotic chamber. Credit: UKRI.
Large-scale farms
Not only new farmers can benefit from running small-scale experiments in a growth chamber, but also large-scale, established farms, since the chamber allows them to experiment with new varieties, creating the optimal yield. This will in turn enable them to upscale their production. “Not all farmers like to invest their time in carrying out experiments, as some trust that the vertical farming technologies they buy will always work for them. However, in the end it could save them a lot of money. No one needs to use productive farm space to do the experiments, just a few manageable boxes can suffice.”
Gareth Coleman works on the chamber imaging and control systems. Credit: UKRI.
For more information:
Grobotic Systems
Dr Alexis Moschopoulos, Managing Director alexis@groboticsystems.com
www.groboticsystems.com
Author: Rebekka Boekhout
© VerticalFarmDaily.com
No Dirt? No Farm? No Problem. The Potential For Soil-Less Agriculture Is Huge
It’s a growing industry — $9.5 billion in sales is expected to nearly double in the next five years — that stems, in part, from concerns about growing enough food to feed a worldwide population expected to hit 10 billion in the next 30 years.
At Plenty’s South San Francisco hydroponics growing facility, a million plants produce leafy greens that are sold through area grocery stores. The company plans to open a farm in Compton this year.
(Plenty)
Imagine kale that doesn’t taste like a punishment for something you did in a previous life. Envision leafy greens that aren’t limp from their journey to your plate. Anticipate the intense flavor of just-picked herbs that kick up your latest culinary creation a notch or three.
Then consider the possibility that such advancements will play a role in altering the face of agriculture, becoming sources of flavorful, fresh produce in “food deserts” and making farm-to-table restaurant cuisine possible because produce is grown on the premises, even in urban areas.
This is the potential and the promise of hydroponics (a term that also includes aeroponics and aquaponics systems), the soil-less cultivation of crops in controlled environments. It’s a growing industry — $9.5 billion in sales is expected to nearly double in the next five years — that stems, in part, from concerns about growing enough food to feed a worldwide population expected to hit 10 billion in the next 30 years.
The growing method isn’t new. The Hanging Gardens of Babylon, dating to the 6th century B.C., maybe a precursor to today’s hydroponics, if they existed. (Historians disagree on that as well as where the gardens were.) Then, as now, technology is a key to giving growers, not Mother Nature, more control overproduction.
The size of today’s systems varies. They might be as simple and compact as an in-home system that’s about the size of a couple of loaves of bread stacked on top of each other. Some of the growing popularity of those units may be connected to the pandemic, according to Paul Rabaut, director of marketing for AeroGarden, which produces systems for in-home crop production.
“As soon as the pandemic was declared in mid-March and the quarantine took effect, we saw immediate growth spikes, unlike anything we’d ever seen before,” he said. Those spikes resulted, he said, from the need for entertainment beyond Netflix and jigsaw puzzles, a desire to minimize trips to the grocery store and the promise of teachable moments for kids now schooled at home.
At the other end of the spectrum are large urban farms. Plenty, for instance, has a South San Francisco hydroponics growing facility where a million plant sites produce crops, some of which are sold through area grocery stores. The company hopes to open a farm in Compton this year that’s expected to be about the size of a big-box store and will grow the equivalent of 700 acres of food.
Plenty scientists, engineers and growers at work in their South San Francisco hydroponics growing facility.
(Plenty)
“It’s a super vibrant community with a rich agricultural history,” Nate Storey, a cofounder of the vertical farming company, said of the Compton facility. “It also happens to be a food desert.
“Americans eat only about 30% of what they should be eating as far as fresh foods,” he said. “We started this company because we realized the world needed more fresh fruits and vegetables.”
As different as hydroponics growing systems are, most have this in common: The plants thrive because of the nutrients they receive and the consistency of the environment and can produce crops of fresh leafy greens and other vegetables, various herbs and sometimes fruits.
Such controlled-environment agriculture is part of the larger trend of urban farms, recognized last year by the May opening of the U.S. Department of Agriculture’s Office of Urban Agriculture and Innovative Production. The farms’ proximity to larger markets means produce can be delivered quickly to consumers, whether they’re grocery shoppers, airline passengers, students or communities in need or restaurants, an industry that has been devastated in the last year.
Today’s micro-and mega-farms have taken on increased importance, partly because of world hunger, which will increase as the population grows.
Add increasing urbanization that is gobbling available agricultural land in many countries, mix in climate change and the scramble for water to grow crops — as much as 70% of the world’s water is used for agriculture — and the planet may be at a tipping point.
No single change in the approach to feeding the world will shift the balance by itself.
Hydroponic farming is “a solution,” said Alexander Olesen, a cofounder of Babylon Micro farms in Virginia, which uses its small growing units to help corporate cafeterias, senior living centres, hotels and resorts provide fresh produce, “but they are not the solution.”
Babylon Micro farms in Virginia provides fresh produce for corporate cafeterias, senior living centers, hotels and resorts.
(Babylon Micro-Farms Inc.)
For one thing, not all crops are viable. Nearly everything can be grown using hydroponics but some crops, such as wheat, some root vegetables (including carrots, beets and onions), and melons and vining crops, are impractical. The easiest crops to grow: leafy greens, including spinach and lettuce; microgreens; herbs such as basil, cilantro, oregano and marjoram; some vegetables, such as green peppers and cucumbers; and certain fruits, including tomatoes and strawberries.
Although hydroponic farming means crops grow faster — thus increasing output — the process comes with a significant carbon footprint, according to “The Promise of Urban Agriculture,” a report by the Department of Agriculture/Agricultural Marketing Service and Cornell University Small Farms Program. Lights generate heat, which then must be removed by cooling. Lettuce grown in traditional greenhouses is far cheaper, the report says.
If these crops can be grown traditionally — in a garden or in a commercial field — why bother with growing systems that are less intuitive than planting seeds, watering and harvesting? Among the reasons:
Climate control: Such indoor agriculture generally means consistent light, temperatures, nutrients and moisture for crops no longer held hostage by nature’s cycles of drought, storms and seasons.
Environmental friendliness: Pesticides generally aren’t used and thus create no harmful runoff, unlike field-grown crops.
Productivity: Leafy greens tend to be cool-season crops, but in a controlled environment, it’s an any-time-of-year crop without the worry of depleting the soil because of overuse because, of course, there is no soil.
Use of space: AeroFarms, a former steel mill in Newark, N.J., boasts that it can produce 2 million pounds of food each year in its 70,000 square feet, or about 1.3 acres. California’s Monterey County, by contrast, uses nearly 59,000 acres — out of 24.3 million acres statewide of ranches and farms — to grow its No. 1 crop, which is leaf lettuce valued at $840.6 million, its 2019 crop report showed.
AeroFarms in Newark, N.J. boasts it can produce 2 million pounds of food each year at its 70,000-square-foot facility in Newark, N.J.
(AeroFarms)
Food safety: In E. coli outbreaks in late October and early November of last year, fingers pointed to romaine lettuce that sickened consumers in 19 states, including California. In November and December of 2019, three other outbreaks of the bacterial illness were traced to California’s Salinas Valley. A Food and Drug Administration study, released in May with results from that trio of outbreaks, “suggest(s) that a potential contributing factor has been the proximity of cattle,” whose faeces often contain the bacteria and can find its way into water systems.
That’s less of an issue with crops in controlled-environment agriculture, said Alex Tyink, president of Fork Farms of Green Bay, Wis., which produces growing systems suitable for homes and schools.
“In the field, you can’t control what goes where,” he said, including wildlife, livestock or even birds that may find their way into an open growing area.
And as for workers, “The human safety approaches that we take [with] people in our farm make it hard for them to contaminate even if they wanted to,” he said.
“Before people walk in, they gown up, put their hair in nets, beards in nets, put on eye covering and bootie covers for their shoes, then walk through a water bath.”
None of the statistics matter, though, unless the quality of soil-less crops matches or exceeds that produced traditionally.
Not a contest, new-age growers say. Flavors of leafy greens, for example, tend to be more detectable and, in some cases, more intense.
So much so that when AeroFarms introduced its baby kale in a New York grocery store, Marc Oshima, a cofounder and chief marketing officer, says he saw a woman do what he called a “happy dance” when she sampled this superfood. The version that AeroFarms produces is lighter and has a “sweet finish,” Oshima said, compared with adult kale grown in traditional ways that some say make the superfood fibrous and bitter.
Storey, the cofounder of Plenty, judged his Crispy Lettuce mix successful when his children got into a “rolling-on-the-floor fistfight” over a package of it.
Some credit for that flavor can be attributed to the time from harvest to market. Arizona and California are the top lettuce producers in the U.S., but by the time the greens get to other parts of the country, they have lost some of their oomph. AeroFarms and Plenty, for instance, distribute their commercial products to nearby grocery stores in New York and the Bay Area, respectively, where their time to market is significantly reduced.
And when was the last time you had a salad on an aeroplane flight that didn’t taste like water gone bad? Before the pandemic constricted airline traffic, AeroFarms was growing greens to be served to passengers on Singapore Airlines flights from New York’s JFK. The fresh vegetables travelled just five miles from the warehouse to Singapore’s catering kitchen, a new twist on the farm to (tray) tabletop.
Because the turnaround from harvest to market is shorter, Storey said his products often last several weeks when refrigerated.
Leafy green vegetables are grown by AeroFarms.
(Emily Hawkes)
And perhaps best of all? Growers say that because the greens have a flavorsome peppery, some like mustard — salad dressing may be optional, perhaps dispossessed in favor of the flavor of naked greens.
Getting consumers interested in vegetables and incorporating those foods into their diets is especially important, growers say, because of skyrocketing rates of obesity, diabetes and heart disease, especially for populations in food deserts.
Tyink grew up in rural Wisconsin but moved to New York to pursue a career in opera. By chance, he sampled some produce from a rooftop garden that he called life-altering. “My eating habits changed because [the greens] changed my emotional connection to food,” he said.
His exposure to homelessness and poverty on the streets of New York also focused his attention on what people consume and why. Price and convenience often drive bad food decisions and unhealthy habits.
Young farmers in training can help change those habits; some of Fork Farms’ systems are used in schools and other nonprofit organizations for children. Kids become accidental ambassadors for the nutrient-rich crops, and the fruits of their labors go to school cafeterias or to local food distribution centres in their communities.
“I really think when you lose fresh, locally produced food, you lose something of [the] culture,” said Lee Altier, professor of horticulture at Chico State University, where he has been working with students to develop its aquaponics program. “I think it is so important when communities have an awareness … that this is for their social integrity.”
As for the future, much still needs to be done to put such products in the right hands at the right time. That requires investment, innovation and technology to perfect the systems and keep costs under control, never mind persuading buyers and consumers that food that’s healthy can also be satisfying.
Is it a puzzle worth solving? Storey thinks so. “I want to live in a world where [we create] delicious, amazing things,” he said, “knowing that they are not coming at a cost that we don’t want to pay.”
About Catharine Hamm
Catharine Hamm is the former Travel editor for the Los Angeles Times and became a special contributor in June 2020. She was born in Syracuse, N.Y., to a peripatetic family whose stops included Washington, D.C.; Honolulu; and Manila. Her varied media career has taken her from McPherson, Kan., to Kansas City, Mo., San Bernardino, Salinas and L.A. Hamm has twice received individual Lowell Thomas Awards, and the Travel section has been recognized seven times during her tenure as editor. Her favourite place? Always where she’s going next.
Hydroponic Indoor Farm Plans To Be Among First Tenants In Downtown Piqua's Zolo Building
It was strategically placed in front of the Zollinger's building, a 40,000-square-foot former grocery warehouse planned as a mixed-use development with 16 loft-style residential units, a roof deck, community market/kitchen incubator and co-working space.
Fifth Season Farm, founded by a local brother-sister duo, has launched a hydroponic indoor farm inside a shipping container along Main Street in downtown Piqua.
By John Bush – Senior Reporter, Dayton Business Journal
A unique farming business has set up shop in downtown Piqua, and if all goes to plan the concept will be among the first tenants in an historic building being redeveloped in the city core.
Fifth Season Farm, founded by brother-sister duo Britt Decker and Laura Jackson, launched a hydroponic indoor farm inside a shipping container along Main Street. It was strategically placed in front of the Zollinger's building, a 40,000-square-foot former grocery warehouse planned as a mixed-use development with 16 loft-style residential units, a roof deck, community market/kitchen incubator and co-working space.
While the farm has been operating there for months, the long-term intention is to occupy space inside the the century-old building, which will be renamed the "Zolo." Chris Schmiesing, Piqua's community and economic development director, said the community market concept fits well with Fifth Season's business, and would be a welcome addition to the building.
"Part of the Zolo concept is the community market space, where local growers and producers can come and put their product on the shelves and begin to grow their business," Schmiesing said. "We're really excited to have Fifth Season Farm in there because we think it really represents the kind of innovative, entrepreneurial activity we want to see more of."
Unlike some traditional farms, Fifth Season does not use pesticides or herbicides, and utilizes non-GMO seeds. Powerful LEDs create a specific light recipe for each plant, allowing control over size and shape. There is no dirt, meaning the crops are free of bugs. The hydroponic system uses 90% less water by recycling the nutrient rich infused water in a loop system. Since it is weather controlled, temperature, relative humidity and CO2 levels remain constant all year.
"It is a complete, self-contained unit," Decker said. "The products also have a much longer shelf life because they are harvested to order."
Fifth Season currently grows about half-a-dozen varieties of lettuce, as well as specialty greens such as Swiss chard and kale. Decker said they are also growing small root vegetables such as radishes.
Currently, Fifth Season offers delivery through its website. Orders can be delivered up to five miles from its farm location, where customers can also come to pick up their products. Fifth Season produce can also be found on the Miami County Locally Grown Virtual Market. Decker said they are in discussions with local grocery stores, restaurants and gyms to carry their product as well.
When their space in the Zolo building is ready, Decker said they plan to open a marketplace and pickup location inside. He added the entire reason they placed the farm in that location was to be ready for when the redevelopment project is complete.
In June 2020, the Piqua Planning Commission unanimously approved a zoning change that allows for residential use within the building. The rezoning was a big administrative hurdle the project needed to cross, but the project still needs to be fully financed. The project missed out on the latest round of Ohio Historic Preservation Tax Credits, though Schmiesing said additional funding sources are being finalized.
Gamble Associates, a Massachusetts-based urban design and planning firm, is taking the lead on the Zolo project. Gamble Associates Principal David Gamble previously said the interior build-out will take between nine and 10 months to complete once it gets started.
Assuming everything aligns, Gamble said this project will create a "critical mass" that could have ripple effects throughout the city of Piqua.
"Piqua, in my mind, has reached an inflection point," he said in July 2020. "While there may not be a lot of transformation to date, there's been a lot of good planning and the city has very good leadership. Piqua is due for that next phase of growth. We like working here, and we're excited about this opportunity and what it can do for the city."
BrightFarms Promotes Jackie Hawkins To Director Of Food Safety & Quality
Hawkins will oversee all aspects of food safety and quality assurance as the company continues its rapid growth into new markets
BrightFarms, a leading supplier of locally grown packaged salads, recently announced that Jackie Hawkins has been promoted to director of food safety & quality. She will report directly to Josh Norbury, BrightFarms’ senior vice president of operations.
Jackie Hawkins
Hawkins will oversee all aspects of food safety and quality assurance as the company continues its rapid growth into new markets. Her responsibilities will include the development and execution of BrightFarms’ food-safety protocols across five facilities, as well as the coordination of customer, regulatory and third-party audits.
“Under Jackie’s leadership, BrightFarms is delivering the safest and freshest leafy greens to the nation’s largest retailers,” said Josh Norbury, senior vice president of operations. “She has built an industry-leading food safety program for the indoor production of leafy greens, and our rigorous protocols have set the standard for other companies in our space. We are fortunate to have her leadership and expertise as we continue to grow.”
Since joining BrightFarms in 2016, Hawkins contributions have been critical to the success of the company’s world-class operations team. She has designed and implemented the most comprehensive food-safety program in the indoor farming industry and maintains close working relationships with leading food-safety experts in the produce industry.
In 2018, Hawkins led the development of the Controlled Environment Agriculture (CEA) Food Safety Coalition, an independent and member-governed organization whose membership is comprised of controlled environment leafy greens growers who subject their production processes to external audit. She also led BrightFarms’ early adoption of IBM’s Food Trust platform to enhance traceability with blockchain technology.
“Food safety is a personal passion that I’ve dedicated my career to, and I couldn’t be more thrilled to step into my expanded role,” said Hawkins. “I’m thrilled that I have the opportunity to work for a company that places food safety at the centre of everything we do. I look forward to continuing to advance our leading protocols and providing our consumers with the safest, freshest and most nutritious greens on the market.”
Hawkins graduated from Oregon State University in 2016 with a B.S. in Environmental Science.
For more information about BrightFarms, visit www.brightfarms.com.
Vertical Farms Grow Veggies On Site At Restaurants And Grocery Stores
The Vertical Field setup retains many of the advantages of hydroponic vertical farms, but instead of the plants growing in a nutrient-packed liquid medium, the container-based pods treat their crops to real soil, supplemented by a proprietary mix of minerals and nutrients
By Paul Ridden
The Vertical Field urban farm pod can be installed in parking lots or inside warehouses, with a modular design that can grow according to customer need Vertical Field
Last month we reported that a huge vertical farming operation near Copenhagen in Denmark recently completed its first harvest. That setup uses hydroponics, but the veggies grown in Vertical Field urban farming pods take root in real soil.
Traditional agricultural farming involves the use of a lot of land and resources to grow crops, and then even more resources to harvest and transport the goods – sometimes thousands of miles – to where consumers can get to them.
As well as requiring a fraction of the growing space, controlled-environment agriculture systems such as hydroponics operations can be much more efficient, are no longer bound by season or location, the growing to harvest cycle is reduced and crops could be produced all year, and as with the Copenhagen operation, they can be set up close to where the food is purchased or consumed.
The Vertical Field setup retains many of the advantages of hydroponic vertical farms, but instead of the plants growing in a nutrient-packed liquid medium, the container-based pods treat their crops to real soil, supplemented by a proprietary mix of minerals and nutrients. The company says that it opted for geoponic production "because we found that it has a far richer flavor, color, and quality."
Vertical Field's urban farms grow walls of veggies inside recycled shipping containers
Vertical Field
"Vertical Field offers a revolutionary way to eat the freshest greens and herbs, by producing soil-based indoor vertical farms grown at the very location where food is consumed," said the company's CEO, Guy Elitzur. "Not only do our products facilitate and promote sustainable life and make a positive impact on the environment, we offer an easy-to-use real alternative to traditional agriculture. Our urban farms give new meaning to the term ‘farm to table,’ because one can virtually pick their own greens and herbs at supermarkets, restaurants or other retail sites."
The recycled and repurposed 20- or 40-ft (6/12-ft) shipping containers used to host the farms can be installed within reach of consumers, such as in the parking lot of a restaurant or out back at the grocery store. Growers can also scale up operations to more than one pod per site if needed, and the external surfaces could be covered in a living wall of decorative plants to make them more appealing.
The vertical urban farms are claimed capable of supporting the production of a wide range of fruits and veggies – from leafy greens and herbs to strawberries and mushrooms, and more. And it's reported to use up to 90 percent less water than a traditional farming setup.
"Through internal experiments with our irrigation method using data from sensors and models we have understood that this is the level of water efficiency," Vertical Field's Noa Winston told New Atlas. "Thus we arrived at an optimal irrigation protocol tailored to the needs of the plant."
According to the company's website, though pesticide-free, the system is not yet considered organic (though Vertical Field is currently in the process of attaining organic certification for the urban farm unit from the USDA). The crops also grow in a bug-free environment.
"The container is kept bug-free because it is sealed off, automated, and we limit human entry to only essential people and essential work," Winston explained. "The container farm itself is not a street vendor or a point of sale, therefore unnecessary or frequent entry does not occur."
Installing a Vertical Field urban farm in a grocery store parking lot means that consumers can benefit from fresh veggies all year long Vertical Field
Unlike some high-tech farming solutions, staff won't need special training to work with the vertical farm as the automated growing process monitors, irrigates, and fertilizes the crops as they grow thanks to arrays of sensors that continually feed data on climate, soil condition, LED lighting and so on to management software. Each vertical farm unit has its own Wi-Fi comms technology installed to enable operators to tap into the system via a mobile app.
The company told us that, by way of example, one container pilot farm offered a growing space of 400 sq ft (37 sq m) and yielded around 200 lb (90 kg) of produce per month, harvested daily. Lighting remained on for 16 hours per day. We assume that the pods are completely powered from the grid at their respective locations, though the company says that it is looking at ways to make use of solar panels as well as making more efficient use of water.
Vertical Field has been around since 2006 and has built a number of living green walls around the world since then. The soil-based vertical farm initiative was started in 2019.
Recent installations include the first Vertical Field container farm in the US at a restaurant named Farmers & Chefs in Poughkeepsie, New York, which started producing its own crops of fresh greens in mid-April 2020. Last month, following a successful pilot, Israel's largest supermarket chain, Rami Levy, signed an agreement with the company to roll vertical farms into dozens of store locations over the course of the next five years.
"The Rami Levy chain understands the social responsibility that it has for customers as related to food security and supplying the highest quality products while maintaining low prices," said the chain's Yafit Attias Levy. "Our customers bought Vertical Field's produce during the pilot and returned to purchase more. Therefore, we have decided to expand the partnership with Vertical Field to additional branches of the supermarket, and to offer fresh, high-quality, and pesticide-free produce in a way that increases shelf-life for our customers."
The Vertical Field urban farm can produce crops year round, without the use of pesticides Vertical Field
And earlier this month, Moderntrendo SRO – one of the largest agricultural distributors in Ukraine – signed up for a pilot project that will start with supermarket chain Varus, and potentially expand to other chains.
"We are extremely excited about our partnership with Moderntrendo SRO which has led to the project with Varus and will lead to more projects in the near future with more chains in Ukraine," Vertical Field's Guy Elitzur said. "One of the realizations that have surfaced during the COVID-19 crisis is the need to develop solutions that allow urban residents access to healthy food, with minimal human handling and without depending on transportation and shipping from remote locations. We are delighted to be able to provide - and expand access to - healthy, and high-quality vegetables grown right outside the consumer's door."
As well as grocery outlets and restaurants, the company sees its container-based vertical farms also being installed in hotels, universities, hospitals, and so on, in the future. The video below has more.
Grow Vegetables On-Site with Vertical Field
Source: Vertical Field
&Walsh Finds Comfort And Warmth In Rebrand For Plenty, A Sustainable IndoorVertical Farming Company
New York creative agency &Walsh is behind the rebrand for sustainable indoor vertical farming company, Plenty, featuring a bold and "approachable" custom font inspired by plants, and an identity and packaging influenced by the flavour of its produce
Written by Katy Cowan
21 January 2021
New York creative agency &Walsh is behind the rebrand for sustainable indoor vertical farming company, Plenty, featuring a bold and "approachable" custom font inspired by plants, and an identity and packaging influenced by the flavour of its produce.
It's a refreshing approach by Jessica Walsh and her team, who have avoided any of the clichéd "healthy green" visual cues like some of Plenty's competitors. With a bright and friendly colour palette and non-fussy, almost retro aesthetic, at its heart lies the crafted font, known as Plenty Custom – a humanist sans serif with leaf-like corners and terminals. "Wherever possible, the font avoids straight lines and is made up of curved and tapered strokes," as &Walsh puts it. "The stroke endings are sharp and the curves are as round as a ripe tomato."
There's a purpose behind Plenty that caught the attention of &Walsh: "What stood out to us was its commitment and desire to make the tastiest, freshest cleanest greens accessible to the masses," Jessica tells Creative Boom.
"Making greens and healthy foods flavorful and accessible to people is very important. Right now, many people turn to unhealthy, processed, and fast foods because of the price and accessibility. In the long term, this causes numerous health problems, which has become a public health issue in America."
In their research, Jessica and her team looked at what would make the brand feel more warm and accessible, while also evoking comfort and tastiness – and that's where nostalgia steps in: "Fast food companies (such as McDonald's and Wendys) often use red and yellow colours in their branding, which have been shown to make people feel hungry. Why not use this technique for healthy foods?" adds Jessica. "With the colours and type choices, we wanted to create a friendly and happy brand that also stood out on the shelf from the competition.
"Almost all greens brands use a similar design aesthetic, so we aimed for the Plenty packaging to pop off of the shelf and pique people's interest. We did extensive target audience testing on the logo and packaging throughout the process to test the new packaging and typeface design, with the final result of our work scoring higher for warmth and accessibility than the previous brand work."
OUR NEW FUTURE: German Firm Says Indoor Vertical Farm in Singapore Will Produce 1.5 Tons of ‘Leafy Greens’ Every Day
New indoor vertical farm in Singapore is expected to produce 1.5 tons of fresh leafy greens per day.
stock photo/ @rebecca_lee_creative
KEY POINTS
Henner Schwarz, CEO of German firm &ever, said that his company’s new indoor vertical farm in Singapore will produce 1.5 tons of “leafy green” produce per day.
Schwarz said he expects produce from his firm’s new research and development facility in Changi will reach a lot of Singaporeans over time and “make a small contribution to food security in Singapore.”
&ever already has an operational indoor farm in Kuwait, which has become a testing ground for indoor vertical farming.
The boss of German firm &ever has said that his company’s new indoor vertical farm in Singapore will produce 1.5 tons of “leafy green” produce every day when it is up and running in the fourth quarter of next year.
Henner Schwarz, Chief Executive Officer at &ever, told CNBC on Monday that he expects produce from his firm’s new research and development facility in Changi will reach a lot of Singaporeans over time and “make a small contribution to food security in Singapore.”
The company, which competes with more conventional food producers, sells living plants to customers that can then be harvested at home as and when they’re needed. As a result, it tastes better and fresher, Schwarz said.
Schwarz said Singapore is “not the easiest market for indoor vertical farming” as electricity is fairly expensive and there are “lots of cheap imports.”
However, &ever has been awarded a grant by the Singapore government, which decided to speed up plans to increase locally produced food after seeing how the coronavirus pandemic impacted food supplies.
Singapore’s land scarcity makes conventional farming a real challenge and the country is keen to embrace solutions that don’t have a large footprint.
In terms of price, Schwarz said: “We think that we’re pricing our products similar to existing premium organic produce that you can find on the Singapore market today.”
He added: “The price point for indoor vertical farming products in many markets in the world, for example in the U.S., is very expensive. Our system is really geared towards making a meaningful contribution and we have taken quite some time to get things right, and to have the most energy efficient solution on the market.”
In order to reduce energy consumption at its Singapore site, &ever plans to use a combination of sunlight capture systems and LED lights. It is teaming up with lighting producer Signify to carry out a number of experiments.
Wikimedia | Valcenteu
Kuwait farm
&ever already has an operational indoor farm in Kuwait, which has become a testing ground for indoor vertical farming as it has similar, but different food security issues.
“We launched our farm in Kuwait just when Covid really hit in March,” said Schwarz. “It has been quite difficult to ramp production capacity up. However, the reception in the market has really been great thus far, and the Kuwaiti people really like our produce.”
When it comes to farming, access to fresh water is a problem in many areas of the world. “We need 95% less fresh water than traditional farms,” said Schwarz.
He added: “We expect that over time, as our efficiency becomes better and better, the price points can become lower and lower.”
PUBLISHED TUE, DEC 22 2020 - 2:11 AM EST | UPDATED TUE, DEC 22 2020 - 2:12 AM EST
USA: NEW YORK - Green Amazon A Smart Vertical Farming Company Is Making The Change For Feeding Communities In Need
Green Amazon is a sustainable smart agriculture company based in Buffalo, New York. The company uses different patented pending technologies in its projects
Green Amazon is a sustainable smart agriculture company based in Buffalo, New York. The company uses different patented pending technologies in its’s projects. Normally when we think about farms on the side of a road, we might imagine acres of land, crops, and livestock roaming on expanses of grass. Green Amazon farms will be different.
The Farms will be built on the east side of Buffalo, New York. The company is paving the way for a new method of farming – The company will provide necessary food and nutrients to communities in need while also reducing the burden on the earth’s natural resources and accounting for its changing weather patterns.
Green Amazon was founded in Finger lakes, New York by Dr. Walid Nosir, the company moved to Buffalo, New York to be closer to the people and community it serves.
The company plans to build the farms where the people are and think about how to be most efficient in that delivery. Green Amazon is trying to cut the shipping cost and distributions, so our selling partners, their warehouses, and their distribution facilities are within just miles. The idea that we’re literally in their backyard, we can really be collaborating closely on understanding what their needs are and be able to grow really efficiently.
Green Amazon seeks to improve food security and work towards the United Nations Sustainable Development Goal (2015) of “No Hunger”. In the coming decades, increasing pressure on the global food supply and associated supply chains will require industry overhaul. The research team at Green Amazon believes a focus on using modern technologies in the products and their development of non-chemical fertilization and inadequate disposal or reuse of agricultural will result in a decrease of the negative environmental impacts induced by wastes.
Green Amazon Growth system will be movable and vertical. The farm’s growing room is specially regulated to minimize contamination and provide a stable, consistent environment for crops to grow. People who enter the room must wear lab coats, eye protection, gloves, and hairnets and even wipe their shoes on a disinfecting mat. Air curtains also help prevent unwanted contaminants from floating into the space. The farm also waters its crops with an aeroponics system.
Nature Fresh Farms Wins Presidents Choice Fresh Product of The Year Award
Each year the award is distributed by Loblaw Companies Limited to one of their nominees. The criteria requires the product to be unique and stand alone as first to market in Canada, additionally, it must be a commercial success
Leamington, ON (November 25, 2020) – This year Nature Fresh Farms proudly accepted the PC Fresh Product of the Year Award for their Ontario Greenhouse Mixiany Cherry Tomatoes.
Each year the award is distributed by Loblaw Companies Limited to one of their nominees. The criteria requires the product to be unique and stand alone as first to market in Canada, additionally, it must be a commercial success, that is, it needed to have generated further sales and profit, thus having a major impact on the category for the period. The winner is determined by a ballot vote by colleagues of Loblaw Companies Ltd, with the award being presented virtually this year.
“We are honored and excited to receive this award as it truly is a testament to our team’s commitment to research and development,” said Vice President John Ketler. “Innovation is an integral part of the Nature Fresh Farms identity and thanks to our Discovery Center we are able to bring fresh flavorful product, like our Mixiany Tomatoes, to market.”
The Mixiany Cherry Tomatoes were performing very well in their research trials and were officially launched in Spring of 2020. This is a significant accomplishment for Nature Fresh Farms as the criteria for the award covered products launched between Fall 2017 to Summer 2020.
“We’d like to thank the entire LBL-PC team for their support and confidence in our product,” shared Director of Sales, Matt Quiring. “Our Mixiany Cherry Tomatoes is just one example of how our devotion to quality and flavor is reflected in our products and it is extremely rewarding to see it received so well by both Loblaws and our consumers.”
Nature Fresh Farms research team works hard at identifying these new varieties that taste exceptional and continue to look for new opportunities to offer more products to consumers. PC Greenhouse Mixiany is available in supermarkets owned and operated by Loblaw Companies Ltd and can be found in Ontario, Quebec and The East.
-30-
About Nature Fresh Farms -
Continuously expanding, Nature Fresh Farms has become one of the largest independent, vertically integrated greenhouse vegetable farms in North America. As a year-round grower with farms in Leamington, ON, Delta, OH, and Mexico, Nature Fresh Farms prides itself on consistently delivering exceptional flavor and quality to key retailers throughout North America, while continuing to innovate and introduce more viable and sustainable growing and packaging solutions.
SOURCE: Nature Fresh Farms | info@naturefresh.ca T: 519 326 1111 | www.naturefresh.ca
SINGAPORE: High-Five: Developing “The World’s First Vertical Aquaculture Farm”
Singapore-based entrepreneur John Diener is committed to developing a series of urban aquaculture facilities that are able to produce shrimp, whitefish and seaweeds in high tech five-story farming systems
by Rob Fletcher
24 November 2020
Singapore-based entrepreneur John Diener is committed to developing a series of urban aquaculture facilities that are able to produce shrimp, whitefish, and seaweeds in high tech five-story farming systems.
John Diener aims to produce shrimp, tilapia, and seaweeds in five-tier facilities that can be fitted into the footprint of a standard warehouse. © Akualogix
The last decade of Diener’s career has seen him involved in a number of aquaculture-related ventures, as well as agritech startups, and the concept of a completely novel farming system came to him in 2016 when he was researching how machine learning could benefit aquaculture during a part-time MSc in aquaculture at St Andrews University.
“I have a lot of experience in data science and I wanted to find out what would happen if you reassessed the whole concept of aquaculture,” he explains.
Diener’s research led him to believe that vertical farms using cutting-edge technologies had the capacity to produce – for their footprint – an impressive amount of seafood, making them suitable for urban settings.
Three pillars
Diener describes the development of the system as resting on three pillars – biological, mechanical and digital. The biological side relates to investigating the most productive integrated-multitrophic (IMTA) system, with vannamei shrimp as the primary species.
“The business plan has been developed around shrimp – they’re a unique product in terms of their flavour profile, much like salmon are, which makes it very hard to produce substitutes. And they can also be raised at high densities,” Diener notes.
“We’ve also incorporated a filter-feeding fish – we’re currently using tilapia because they’re very robust, but will probably trial milkfish too,” he adds.
The bottom of the IMTA pyramid is taken up by sea grapes – called umibudo in Japan, where they are considered something of a delicacy.
“These are known as ‘the green caviar’ in parts of Asia, so have the potential to be sold as food. They can also be used as an ingredient in shrimp feeds, as we’re aiming to produce our own, sustainable feeds, while they also help to remove nitrates and phosphates from the water,” says Diener.
Technology
The second pillar consists of the engineering, and Diener intends to develop raceway systems four or five levels high, which are equipped with modular autonomous devices to optimise factors such as measuring water quality. The third pillar relates to the digital side of operations.
“We’re investing time and effort to develop advanced technology to manage feeding – both in terms of studying shrimp behaviour so we know when to feed and in terms of measuring the biomass in the systems, so we know how much to feed. We will also be looking to manage the water quality by feeding information into a deep learning algorithm that can control factors like pump speeds and the addition of minerals to the water,” he says.
The digital side also covers the farm’s “Aqua OS” [operational systems], ensuring all the technology works together, to simplify the management of all the tanks, Diener explains.
Launch
John Diener, founder of Akualogix
Four years after coming up with the concept Diener launched his own company, called Akualogix, in August, after finding a suitable site for a pilot-scale facility, in a building owned by the Marine Aquaculture Centre, on St John’s island in Singapore. This will, he notes, be perfect for securing proof-of-concept, before he looks to expand into a commercial-scale facility.
Initially self-funded, by Diener and the company’s co-founder, they are now looking into securing pre-series A funding in order to build a larger scale production unit.
Funding opportunities have remained robust in the agri-food sector, despite the outbreak of Covid. And as our systems are designed for an urban environment, and food security is increasingly important in Singapore and other cities around the world, we see strong investor interest
“Funding opportunities have remained robust in the agri-food sector, despite the outbreak of Covid. And as our systems are designed for an urban environment, and food security is increasingly important in Singapore and other cities around the world, we see strong investor interest,” Diener reflects.
The current farm has – he predicts – the capacity to produce 500-600 kg of shrimp per cycle, but he’s not yet sure what the yields of the tilapia or sea grapes will be – pointing out that no one has undertaken a mass balance study in such a system.
A juvenile shrimp at the pilot facility in Singapore. © Akualogix
“Our business economics is based on shrimp – making any money from the tilapia would be the icing on the cake – but the main reason we have the fish is part of the multi-trophic system and benefit the overall environment, they’re part of the filtration system,” he explains.
We will be looking at establishing commercial farms that can produce in the region of 1,000 to 1,500 tonnes of shrimp a year. It might not sound like much compared to some of the commercial salmon RAS that are now being established, but if we’re operating 20 or 30 farms that would make us one of the biggest shrimp producers in the world
Next steps
Once the pilot facility has fulfilled its potential Diener aims to establish a farm – and ultimately a network of farms – that use Akualogix’s design and equipment, establishing partnerships in a range of countries, primarily in Asia, as the concept takes off.
“We will be looking at establishing commercial farms that can produce in the region of 1,000 to 1,500 tonnes of shrimp a year. It might not sound like much compared to some of the commercial salmon RAS that are now being established, but if we’re operating 20 or 30 farms that would make us one of the biggest shrimp producers in the world,” he points out.
Diener is also looking to develop a unique, sustainable feed that’s designed specifically for producing shrimp in RAS facilities.
“The current range of commercial shrimp feeds are not great for use in RAS, and we’re looking to produce a next generation shrimp feed using sustainable ingredients. And we’re looking for a flavour enhancing additive as a finishing diet – potentially one that comes from algae,” he says.
Given the technology involved and the emphasis on sustainable feed ingredients Diener is aware that production costs are going to be considerably higher than conventional shrimp farms.
“We estimate that our cost of production will be 40-50 percent higher than shrimp produced in a pond in, say, India. But we’re close to market and can charge a premium for a fresh product that’s so sustainably produced,” he says.
Operational experience
The pilot facility holds 30,000 shrimp per cohort and 1,000 tilapia. The former are housed in a two-stage grow-out system and he aims to take them from the end of the nursery stage to harvest in 60 days, while achieving survival rates of roughly 90 percent.
However, as Diener admits, the design concepts of the system are still evolving, and there are other issues that have caused setbacks.
“It turned out that our first batch of PL [post-larvae] had pathogenic vibrio and we started seeing mortalities related to vibriosis,” he explains.
It was an unfortunate start, but a useful reminder of the importance of biosecurity.
“We decided to implement a full biosecurity package [once operating commercially], which will include our own hatcheries to prevent the introduction of pathogens,” he says.
Should the pilot facility prove productive, and investment forthcoming, Diener then aims to roll out the concept across some of Asia’s most populous coastal cities.
“There’s currently a lot of investment in salmon RAS and I think shrimp are the next species to go in that direction. If we can be a pioneer of shrimp RAS it will be a game-changer,” he concludes.
D.I.Y. Microgreens You Can Grow On Your Kitchen Counter
Think of The Rewards of Cultivating
The Tastes of Summer All Through The winter. You Can Do This.
New to microgreens? Start with something in the mustard family (Brassicaceae) that offers a quick payoff, like arugula (shown), radish or mizuna (a mild-flavored mustard). Credit...Kate Spring
By Margaret Roach
Nov. 18, 2020
Since Kate Spring and her husband, Edge Fuentes, founded Good Heart Farmstead in Vermont in 2013, she has cultivated not just mesclun, strawberries and tomatoes, but also the abundance of the patience required of a farmer. Plant parenthood reminds us: Living things take time. And sometimes they have minds of their own.
Lately, as mother to Waylon, a 7-year-old son she calls “our best crop ever,” Ms. Spring is occasionally asked to dig down even deeper, in a growing test of wills — as she did after three long days of carrot harvest. “There are those moments, like when all those root vegetables need to be washed,” she said, “and your child commandeers the hose and washes you instead.”
But there is one crop, whose time is now, that promises near-instant gratification, requiring little patience and exhibiting blessedly minimal rebellion.
Microgreens — fully developed seed leaves or cotyledons plus a true leaf or two, bigger than sprouts but smaller than baby greens — can be grown indoors in a small space, making them the ideal off-season do-it-yourself project for those who miss the vegetable garden and its in-season flavors. By investing a couple of weeks in each tray of tiny, leafy greens, root vegetables or herbs, you can enliven winter with concentrated bursts of nutrition and taste.
In the garden off-season, freshly harvested basil microgreens grown indoors punch up the summery quotient when Kate Spring, an owner of Good Heart Farmstead, serves red sauce she cooked and froze at peak tomato harvest. Credit...Kate Spring
Microgreens are a cusp-season crop at Good Heart Farmstead, an L3C, or low-profit limited-liability corporation, which means it’s “a mix between a nonprofit and for-profit business — a for-profit but with a social mission in the forefront,” Ms. Spring said. “We work on increasing food access for low-income Vermonters,” often in collaboration with the Northeast Organic Farming Association of Vermont.
The small, certified-organic operation in Worcester (Zone 4a) focuses on farm shares, or CSA subscriptions, serving up to 100 subscribers in the summer season, one of four subscription periods each year.
As the last outdoor fall greens fade, Ms. Spring and Mr. Fuentes sow microgreens in greenhouse flats to add “a nice, fresh green item in the share,” she said, that is otherwise transitioning to roots and other winter storage vegetables.
So order some seed, clear a space on the kitchen counter and call the seed-starting light into service. It’s microgreen season.
Larger seed for microgreens like chard and beets can be scattered on a level surface of an inch and a half of tamped-down, seed-starting soil, with about six to eight seeds per square inch. Credit...Kate Spring
Why Grow Microgreens?
Besides the sheer awe inherent in any version of seed-starting, there are other motivating factors. Price, for instance.
Microgreens are what farmers refer to as a high-value crop. In plastic grocery-store clamshell boxes they may run $2 to $3 an ounce ($32 to $48 a pound) — “a really premium product,” Ms. Spring said.
Microgreens are also nutrient-dense. Researchers with the University of Maryland College of Agriculture and Natural Resources and the United States Department of Agriculture evaluated vitamin and carotenoid concentrations in a range of varieties in a 2012 paper. The findings, in brief: Microgreens contained up to 40 times the nutrients of the plants’ mature leaves.
And oh, the flavor. Yes, they brighten up salads and sandwiches, but cilantro microgreens on top of black bean and sweet potato tacos, anyone? They’re highly recommended by the Spring-Fuentes household, where there are always basil microgreens as well, for punching up the summery quotient of red sauce frozen at peak tomato harvest.
“Arugula or basil or kale microgreens are also really good on eggs in the morning,” said Ms. Spring, who tends to use them “as an additive, not the main ingredient.”
Organic field pea seeds will become pea shoots, a customer favorite at Good Heart Farmstead, in Vermont. They are sown very densely and pressed into the soil after the seeds are soaked overnight. Credit...Kate Spring
Start With These Varieties
The diversity of organic microgreen seed offerings in catalogs like Johnny’s Selected Seeds and High Mowing Organic Seeds can be intimidating. Start with something in the mustard family (Brassicaceae) that promises a quick payoff, Ms. Spring suggested, like radish, arugula or mizuna (a mild-flavored mustard).
“Our favorites are basil, cilantro, Red Russian kale and the arugula and mizuna,” Ms. Spring said.
Broccoli and chard are popular, too. Catalogs also offer mixes — like a spicy one of various mustards, selected to germinate and mature on a similar timeline.
While the fields are resting, there are usually microgreens growing on Good Heart Farmstead’s greenhouse benches, to add a fresh, green item to the wintertime CSA shares. Credit...Kate Spring
The Gear
Yes, you can upcycle a cardboard egg carton or plastic sushi container into seed-sowing service, and maybe that’s a good place to begin. But once you’re hooked, a couple of standard nursery flats with drainage holes, called 1020 flats, with trays that fit beneath, will optimize the process. (In the meantime, a plastic boot tray or a rimmed baking sheet could be called into action under ad hoc seedling trays.)
You’ll also need:
A spray bottle for watering (recommended: a one-hand pressure sprayer like the Solo 418)
A germination dome to fit your flats, or paper towels
A bag of seed-starting mix and a moisture-proof tub or other container to stash it in (after each harvest, the soil can be composted, and once the plant matter breaks down, reused two or three times)
A grow light with T5 high-output fluorescent tubes on an adjustable stand (microgreens grow faster and stronger with proper overhead light than they will on a windowsill)
A fan
And, of course, seeds
You can simply can upcycle a cardboard egg carton or plastic sushi container into seed-sowing service, but once you’re hooked, a couple of standard nursery flats with drainage holes, called 1020 flats, and trays that fit beneath will optimize the process. Credit...Kate Spring
Kate Spring’s Step-by-Step Instructions
There is no one-size-fits-all growing method. “It takes some guesswork and practice, so go into it with a trial mind,” Ms. Spring said.
Experimenting with varieties, sowing density and harvest timing — an extra day or two, a half-inch taller than the last batch? — will reveal what works for you.
Using more than one flat and tray will mean fewer gaps in your supply. You could try sowing a succession crop when the current one is within a few days of harvest, or sowing slower- and faster-growing varieties at the same time.
The key is taking notes and researching the catalog websites, where the “number of days to first true leaf” will indicate how fast one variety will grow relative to another. That is especially important if you want to grow partial flats of two things. A good match for a uniform harvest pairs crops with similar days to maturity — like broccoli and Red Russian kale (both 10 to 15 days to true leaf) or basil and cilantro (16 to 25 days).
Trays of microgreens at various stages of development in the Good Heart Farmstead greenhouse benefit from the circulation provided by a fan on low nearby, which helps prevent a fungal disease called damping off. Credit...Kate Spring
Start with the right location: 65 to 70 degrees, not adjacent to a heater or a drafty window. Moisten a supply of potting soil, either in its plastic bag or in a waterproof tub, by adding a small amount of water and mixing it with your hands or a trowel. Squeeze a fistful; it should be moist enough to hold its shape, but not so wet that water drips out.
Then line your tray with an inch or so of soil, tamped down so it’s compact, with an even surface. This will help ensure that seeds have equal soil contact for even germination.
To sow the seeds, scatter them thickly, according to the packet directions, aiming for 10 to 12 seeds per square inch for small seeds like basil, mizuna or kale and six to eight seeds for larger ones like beets or chard. Gently press them into the soil.
Lightly water the seeds with a mister or spray bottle.
Cover the tray with a germination dome or a damp paper towel. (If you use a paper towel, mist it daily so it stays moist during germination.) No supplemental light is needed yet.
As soon as the seeds germinate, usually in about three to five days, remove the dome or towel and place the uncovered tray under grow lights for 16 hours a day.
Water as needed to keep the soil moist but not waterlogged. Microgreens flatten easily, so use a mist or spray, or switch to bottom watering, adding a quarter of an inch of water to the tray below; the flat’s drainage holes will allow the soil to wick up water. For even watering, trays must be on a level surface.
Airflow is important, or thickly sown microgreens can suffer from a fungal disease called damping off. A fan set on low nearby helps.
Microgreens are harvested around the time the first true leaf appears — the one that resembles an older version of the plant, often between an inch or two tall. Use sharp scissors or a harvest knife (Johnny’s and High Moving both sell Victorinox serrated knives). Eat immediately or refrigerate in a closed plastic bag or container for two to three days.
Waylon, the son of Good Heart Farmstead owners Kate Spring and her husband, Edge Fuentes, is 7 years old and a lover of pea shoots and all things salad. This year, he grew his first garden. Credit...Kate Spring
Ready to Graduate to Pea Shoots?
Pea shoots, a CSA-subscriber favorite at Good Heart Farmstead, are grown indoors in spring from organic field pea seeds, a kind of pea used for cover-cropping beds to improve the soil.
There are subtle differences in the process, Ms. Spring said: “We soak the seeds overnight, so that they have a little head start, and we really pack them in there.”
After that, the seeds take 12 to 14 days to harvest, at two to four inches high. Ms. Spring likes them on the bigger side — as does Waylon, who has all too quickly gone from sprout to shoot stage himself, his mother noted.
GreenFactory Emirates: The Largest Indoor Farm In The World To Be Developed In Abu Dhabi
GreenFactory Emirates will develop an innovative indoor farming with the world's most advanced indoor growing system from The Netherlands
Barendrecht (The Netherlands) and Abu Dhabi (UAE)
September 22, 2020
A joint venture between GrowGroup IFS from Barendrecht (The Netherlands) and RainMakers Capital Investment LLC from Abu Dhabi (UAE) will build the largest indoor farm in the world in the desert of Abu Dhabi. The GreenFactory Emirates will produce 10,000 tons of fresh produce per year on a plot of 17.5 hectares and a cultivation area of 160,000 square meters.
GreenFactory Emirates will develop an innovative indoor farming with the world's most advanced indoor growing system from The Netherlands. It is a combination of vertical and flat farming and solves the normal cultivation restrictions due to extreme climates in regions as the UAE. The facility will involve numerous leading agro-technological companies in its construction as best of breed for each component will be sourced through top-tier Dutch companies. It is now possible to cultivate high-quality vegetables 100% pesticide-free, all year round and anywhere on the planet: “Quality of Holland – Local Grown.” From seeding, harvesting, processing to "ready to eat" products will take place under one roof.
The joint venture also plans to build other indoor farms in other regions of the world where extreme climates are a challenge to normal cultivation.
Water, Co2, and waste
The GreenFactory will be saving 95% of water consumption as opposed to standard methods of cultivation as well as reducing its Co2 footprint up to 40%. By growing fresh produce locally, GreenFactory Emirates will also contribute to reducing waste in various other areas. Its contribution to slowly reducing reliance on fresh foods imports will in turn reduce waste of produce occurring during the transport process while reducing logistical traffic.
Research and development
GreenFactory Emirates will include a built-in research and development component that will help ramp up the production beyond the 56 current varieties of lettuces, leafy greens, herbs, and kale. It will also optimize its production by collecting real-time data to inform future global expansion of indoor farming. With confirmed partnerships with GAAS Wageningen and Delphy in The Netherlands, GreenFactory will benefit from live feedback provided by some of the best students and Academia in the field.
Food security
Food security is high on the UAE’s agenda. The country aims to be number 1 on the Global Food Security Index by 2051. In 2019, the UAE ranked on the 21st place on the Index, jumping an impressive 10 places from number 31 in 2018. Boosting local production and creating an enabling environment for agri-tech is a top priority for the government. The UAE strives to become a knowledge hub with regards to food production in heat, high humidity, and high salinity soil. The private sector (supermarket chains and the hospitality industry) has also set ambitious targets for itself in order to sell more local produce.
Partnership
The partnership between GrowGroup and rainMKRS is initiated and a result of an introduction made by the Embassy of the Kingdom of The Netherlands in the United Arab Emirates and the Monarch Group which has played an instrumental role in seeking opportunities and nurturing relationships.
Expo 2020 Dubai
The total project amounting to 650M AED (150M EURO) is planned in different phases in 3 years. Phase 1 will be operational before Expo 2020 Dubai in October 2021, so GreenFactory Emirates can show the world its innovations. A kick-off for more similar projects and innovations worldwide.
GrowGroup IFS
GrowGroup IFS (Innovative Farming Solutions), founded by CEO John Breedveld in Barendrecht in The Netherlands, is specialized in developing indoor farming based on the most advanced Dutch innovative farming solutions, especially in regions where normal cultivation is restricted by extreme climate and or limited space.
rainMKRS Capital Investment LLC
With offices in Abu Dhabi (UAE) and Montreal (Canada), rainMKRS is an entrepreneurial catalyst co-founded by a group of Emirati and Canadian entrepreneurs. Led by Mohamed Jouan Al-Dhaheri, Sultan Al-Nassour, Sebastien Leblond, and Jonathan Mérineau Gosselin, rainMKRS brings together the world’s most impactful companies and projects in the food and agriculture sector and UAE’s economic, educational, and investment stakeholders. rainMKRS’ objective is to help bridge the gap between these stakeholders in order to accelerate the progress on critical and strategic components in support of the UAE desire to achieve food security.
GreenFactory Emirates is its first of many initiatives in the field.
Virginia Researchers Are Studying ‘The Sound of Plants Dancing’ To Better The Future of Agriculture
Using experimental technology, the scientists are trying to figure out how the sonification of plant movements could be used to assess plant health and aid farmers who need to monitor their greens at an industrial scale
By Katherine Hafner
The Virginian-Pilot 9/7/2020
What Do Dancing Plants Sound Like?
© Virginia Tech/The Virginian-Pilot/TNS Some of the pepper plants being studied by researchers at Virginia Tech. The researchers record the plants' long-term movements  sped up into \"dances\"  then convert those patterns into sound as a way to evaluate plant health based on responses to environmental conditions.
It seems like the start of a philosophical essay question. But researchers at Virginia Tech think the answer could be one tool wielded in the future of agriculture in the commonwealth and beyond.
Using experimental technology, the scientists are trying to figure out how the sonification of plant movements could be used to assess plant health and aid farmers who need to monitor their greens at an industrial scale.
They are focused on indoor or so-called controlled-environment agriculture. Think greenhouses with LED lights and plants in hydroponic systems, using liquid nutrient solutions instead of soil.
“When you grow a plant inside a building, you really control ... introducing any insects or pathogens, minimizing the use of pesticides” and the like, said Bingyu Zhao, the lead researcher and associate professor in the School of Plant and Environmental Sciences. “But you can still have disease problems or sometimes they could have environmental stress.”
Maybe the temperature’s too high, he said, or the nitrogen levels are off. “It’s all not good for the plant growth.”
Imagine a grower using an indoor facility with dozens of rows of plants. Unlike in a small backyard garden, they can’t continuously check on every individual plant to monitor the effects of all those variables.
So Zhao got the idea to set up cameras to do it instead, using a small number of pepper plants for observation.
The high-resolution cameras capture the continuous movements of the plants. Over times, patterns develop.
These “micro movements” are mostly naked to the human eye, Zhao said. But they become apparent when sped up in time-lapse videos.
The even more unconventional part comes next.
The researchers take the data they’ve collected on plant movements and convert it into sound in a process called sonification.
In that way, a human could hear patterns present among the plants. The idea is to eventually be able to link certain sounds to indicators that a plant needs better light, for example.
Computers, analyzing the data at a large scale, could learn “what is a good sound and what is a bad sound,” Zhao said.
He works with professors across other disciplines in engineering and in the School of Performing Arts to bring together the different elements.
The plant movement project is just one part of the university’s new statewide SmartFarm Innovation Network, said Susan Duncan, associate director of the Virginia Agricultural Experiment Station.
Two years ago, the school brought together stakeholders in the agriculture and food processing fields from around Virginia to hear their concerns and interests, she said.
One big takeaway: technological innovation was on everyone’s mind. In order to maintain a future workforce and catch up with evolving needs, they needed to think outside traditional agricultural techniques, she said.
So the decentralized network was born, consisting of 11 off-campus research centers including the Hampton Roads Agricultural Research And Extension Center in Virginia Beach. Though the center in our region isn’t involved in the “dancing plants” project, it has plenty of its own areas of study, including water quality and boxwood blight disease.
There are more than 100 research projects connected to the network delving into the future of agriculture.
With growing plants indoors, for example, “you can’t just say, ’I’m going to put this LED light over my plant and see how it goes,’” Duncan said. “There’s a science behind it.”
In the operating room, surgeons often use sound to be able to keep track of routine measurements such as blood pressure while performing surgery, Duncan said.
Applying that to plants, she said, is “how they can help guide us to make decisions for them.”
“It’s kind of a cool concept. If they start ’screaming,’ whatever that sounds like, we can pay attention.”
©2020 The Virginian-Pilot (Norfolk, Va.)
Visit The Virginian-Pilot (Norfolk, Va.) at pilotonline.com
Distributed by Tribune Content Agency, LLC.
Earn CEUs With Disease Management Starting September 28, 2020
Learn how to prevent and manage diseases in nurseries and greenhouses. Disease Management is the fourth course of the award-winning Greenhouse Online Training courses offered by the University of Florida IFAS Extension
By urbanagnews
September 2, 2020
University of Florida Greenhouse Training Online Courses
Learn how to prevent and manage diseases in nurseries and greenhouses. Disease Management is the fourth course of the award-winning Greenhouse Online Training courses offered by the University of Florida IFAS Extension.
This intermediate course is designed for growers with some experience and training and offers Continuing Education Units (CEUs) for many states in the United States. Topics covered include disease cycle, how to differentiate between a disease and other issues, organic and conventional disease management options, and how to safely apply and handle fungicides. The course is offered in English and Spanish.
The course is taught by Dr. Carrie Harmon, Director of the UF/IFAS Plant Diagnostic Center in Gainesville, FL, and Executive Director of the National Plant Diagnostic Network. Growers in the course have described her as a “clear, concise and informative instructor” who help them “feel more capable identifying disease problems, and less intimidated by the disease books on the shelf.”
The course runs from September 28 to October 23, 2020, includes a personalized certificate of completion and has been approved for CEUs in several states. The cost is $US199 per participant, with discounts if you register 5 or more. The last day to register is October 5, 2020. Over 4 weeks, there are streaming video lessons, readings, and assignments (about 3-4 hours total commitment per week), which can be accessed at any time of day. Click here to register.
For more information, including discounts for registering multiple staff, email us at greenhousetraining@ifas.ufl.edu, or visit http://hort.ifas.ufl.edu/training/.
Disease Management 2020 flyer Download
Vertical Farming To Shape Food's Future Top Companies To Share Expertise At Online Congress - September 22-24, 2020
The first Vertical Farming World Congress will now be held online on 22-24 September, with numerous innovations to help develop an emerging community of leading producers, funders, suppliers, and customers. Its theme will be ‘Shaping Food’s Future
The first Vertical Farming World Congress will be held online from 22nd to 24th September, bringing together the sector’s top minds and businesses, who believe the coronavirus pandemic will accelerate the industry’s inevitable growth. With the theme ‘Shaping Food’s Future’, the event is sponsored by LED lighting solutions provider Heilux.
“This is a unique opportunity for interested investors, agriculturalists, food producers, suppliers, academics and governments,” commented Richard Hall, Chairman of event organizer Zenith Global, the food and drink experts. “There may never be a better time, because the industry is rapidly establishing itself and an online event gives a ringside seat more affordably, along with all kinds of extra features.
“In addition to the most authoritative speakers ever assembled on the sector, there will be virtual farm tours, round tables on key issues, and extensive social as well as one-to-one networking. There will be ongoing access afterwards to review presentations and continue making new connections.
“It will be difficult to beat the caliber and geographic spread of our speakers:
Our industry leadership panel has the founders and chief executives of AeroFarms and 80 Acres Farms from the United States plus Intelligent Growth Solutions and Jones Food Company from the United Kingdom.
On sustainability, we have the World Wildlife Fund; on retailing, we have Migros from Switzerland.
Investors are represented by AgFunder, Ashfords, Innovate UK, and Virgo.
Other leading contributors range from the global Association of Vertical Farming to Wageningen University.
Other talks include a view of the city of the future, a nutrition briefing, and debate about the relative merit of aeroponics, aquaponics, and hydroponics.
A technology briefing will look in-depth at operational choices, plant growth, lighting, and robotics.
Innovator case studies include growing underground, modular aeroponics, shipping containers, and success in Taiwan.”
Media partners include AgFunder, Agritecture, AOA Chile, Association of Vertical Farming, Eatable Adventures, Farm Tech Society, FoodBev Media, Hortidaily, iGrow, Japan Plant Factory Association, NextGenChef, Urban Ag News, Vertical Farming Consulting, and Vertical Farming Podcast. Full program and booking details are available at zenithglobal.com/events. There is a specially discounted rate for start-ups.
Media partners include AgFunder, Agritecture, AOA Chile, Association of Vertical Farming, Eatable Adventures, Farm Tech Society, FoodBev Media, Hortidaily, iGrow News, Japan Plant Factory Association, NextGenChef, Urban Ag News, Vertical Farming Consulting, and Vertical Farming Podcast.
Full program and booking details are available at zenithglobal.com/events.
There is a specially discounted rate for start-ups.
For further information, go to www.zenithglobal.com/events or contact events@zenithglobal.com.
It's Hard To Grow Vegetables In This Mountain Town. Then This Farmer Had An Idea
Operating an indoor farm in the snowy northwest corner of Wyoming wasn't exactly the job Yehia had envisioned for herself years ago. In 2008, after the New York City-based architect moved to Jackson to start a new firm, Yehia wanted to try something innovative in her new community
By Jeremy Harlan, CNN
September 14, 2020
Jackson, Wyoming (CNN) It was a no-brainer when it came to finding the best job for Ty Warner.
"Ty is our tomato guy," said Nona Yehia, co-founder and CEO of Vertical Harvest, an innovative three-story greenhouse in downtown Jackson, Wyoming.
Nona Yehia, the founder of Vertical Harvest in Jackson, Wyoming.
As she watched the slender 6'5" Warner carefully weave his way through a towering canopy of plants, pulling ripe tomatoes hanging above, Yehia smiled with pride. "Ty is good at every part of growing tomato plants. It is really impressive."
Operating an indoor farm in the snowy northwest corner of Wyoming wasn't exactly the job Yehia had envisioned for herself years ago. In 2008, after the New York City-based architect moved to Jackson to start a new firm, Yehia wanted to try something innovative in her new community.
"We really wanted to address the local sustainable source of food," she said.
The idea To Go Up
Jackson sits at an elevation just over 6,000 feet, nestled between Grand Teton National Park, Yellowstone National Park, and the Teton National Forest, and its location means there is very little space and conducive weather for farmers to grow fresh produce for the bustling tourist town.
"We came together to look for an out-of-the-box solution and that's where the idea to go up came from," Yehia said.
"Up" was on a 1/10 of an acre lot abutting an existing parking garage.
In July, Nona Yehia, CEO and co-founder of Vertical Harvest, announced a second vertical farm in Westbrook, Maine. The second Vertical Harvest will be five times larger than the original Wyoming farm and will open in 2022.
In the spring of 2016, Vertical Harvest began growing its first lettuce, microgreens, and tomato plants. The farm's current staff of 40 now grows year-round and cultivates the amount of produce equivalent to ten acres of traditional outdoor farming.
Yehia says all of the produce grown is distributed to 40 local restaurants and four grocery stores.
"Nona has approached it as bringing something unique to chefs that they then can use and feature all year round," said Ben Westenburg, the executive chef and partner of Persephone West Bank in nearby Wilson, Wyoming. "It's just so easy to call up Vertical Harvest and be like, 'I need some salad greens and tomatoes and some really beautiful microgreens.' And they're like, 'Okay, we'll be there tomorrow.'"
'We're pairing innovation with an underserved population'
Ty Warner, a Vertical Harvest employee, is tasked with picking and pruning hundreds of the indoor farm's tomato plants.
While planning for a new greenhouse, Yehia and her design team realized they had to do more with the project than just grow fresh greens for locals.
"There was a bigger problem," Yehia said. "People with physical and intellectual disabilities in our town who wanted to work, who wanted to find consistent and meaningful work, were not able to do so. We're pairing innovation with an under-served population and really creating a sea change of perception of what this population is able to do."
Half of Vertical Harvest's workers have physical or intellectual disabilities. Yehia, whose older brother is disabled, says every single employee, including Warner -- who is autistic -- is critical to keeping Vertical Harvest functioning.
"We can empower the most under-served in our communities just by giving them a chance and giving them something to be able to give back to," Yehia explained.
"It's hard for people with disabilities to find a job," says Sean Stone, who used to wash dishes at several restaurants in town before joining Vertical Harvest as a farmer. "I'm glad to help the community and grown them fresh produce to have."
Growing beyond Wyoming
In July, Yehia announced Vertical Harvest would be expanding to serve a second community. The new farm located in Westbrook, Maine, will open in 2022 and will be five times larger than the original Wyoming greenhouse.
The goal is to grow a million pounds of produce each year for local restaurants, grocery stores, hospitals, and schools.
Mycah Miller, a Vertical Harvest employee, packages lettuce greens to be delivered to one of four grocery stores the vertical farm services in Jackson, Wyoming.
"In moving to Maine and having a much larger space, we're excited to play out the model of providing local produce at an urban scale," she says.
Yehia believes the global pandemic this year has forced consumers and communities around the country to explore new ways to get fresher produce from closer sources.
"COVID has shined a spotlight on what we knew ten years ago when we were looking at this vertical model: We have a centralized food system and it's kept us from getting fresh, local, good-tasting food," Yehia said. "I think Covid-19 has forced people to ask why that is and how they now can get locally-grown food they like in the summertime and get it year-round. It's exactly what Vertical Harvest is about."
Hyve Indoor Farming Systems Looking To Hire Indoor Farming Technology Sales And Support Position
By urbanagnews
September 4, 2020
Indoor Farming Technology Sales & Support Position
For The Territory
of North and South America
This is an outstanding opportunity for a person who is willing to learn the
Controlled Environment Agriculture business from the ground up. There is
significant advancement potential for the right person in this rapidly growing cutting-edge company.
For Interest in applying, please send your resume and cover letter to Ron Acorn at racorn@dascom.com
Job Objective:
Develop HYVE Indoor Farming Systems business by Sales and
Support of customers
Responsibilities:
Support HYVE System sales
Take customer calls and inquires
Update and maintain data in CRM system
Proactive phone calls for follow up/appointments/GrowLab tours
Collaboratively develop Quotes and Proposals
Pricing/Availability
Program/Project support for system Implementations
Work with In House Grower to assist in Grow Lab testing and maintenance
Technical Support for customers on growing process
Technical Support for customers on grow system issues
Customer visits as needed to review locations and support projects
Relationships and Roles:
Internal / External Cooperation
Demonstrate the ability to interact and cooperate with all company employees.
Build trust, value others, communicate effectively, drive execution, foster innovation, focus on the customer, collaborate with others, solve problems creatively, and demonstrate high integrity.
Maintain professional internal and external relationships that meet company core values.
Proactively establish and maintain effective working team relationships.
Job Specifications and Requirements:
College degree in Horticulture or related experience
Desire to work in a business environment and culture with customer first attitude
Desire to be part of the future of controlled environment agriculture and a willingness to grow with the company
Demonstrate a “Can Do” attitude in a dynamic environment
Honest, ethical, good sense of humor
Self-starter with excellent communication skills
PC-literate
Logical, business-oriented thinker able to represent the company in a sales capacity as it relates to the quotation of technical equipment in a variety of applications
Willing to assist with hands-on growing and experimentation in a vertical farming environment
Organized and able to handle multiple tasks in a rapidly changing environment
Ability to travel as needed to customer sites, for trade shows, or to represent the company at organizational meetings
Singapore's Temasek Bets on 'Skyscraper Farms' As Growth Market
Temasek and German pharmaceutical major Bayer established Unfold, a 50-50 joint venture, last month. The company will develop and market seeds for vertical farming both in Singapore and at its California headquarters
Joint Venture With Bayer To Develop Seeds
To Boost Food Security In City-State
TAKASHI NAKANO, Nikkei staff writer
September 10, 2020
SINGAPORE -- Singapore's state-backed investment group Temasek Holdings has extended its business portfolio into urban farming, a concept that will aid the city-state in its quest to become more agriculturally self-sufficient.
Temasek and German pharmaceutical major Bayer established Unfold, a 50-50 joint venture, last month. The company will develop and market seeds for vertical farming both in Singapore and at its California headquarters.
Singapore produces less than 10% of the food it consumes. The government plans to raise the ratio to 30% by 2030.
Vertical farming, officials believe, is crucial to attaining that goal. The technique grows agroponic layers of crops under artificial light inside skyscrapers. Because the plants are not dependent on weather, the method is expected to generate large yields in a relatively quickly.
"Temasek is recognized as one of the leading investors in the food and agriculture segment," said Jurgen Eckhardt, head of Leaps by Bayer -- an investment arm of Bayer. "They have investments in, and relationships with, a range of vertical farming companies."
Bayer will provide plant genetic data to Unfold, which will first develop new varieties of lettuce, spinach and tomatoes, among other crops. The company will sell seeds to food producers.
Temasek will introduce companies to the technology and expertise at Unfold and other investment targets. Temasek holds a stake in Sustenir Agriculture, a Singaporean urban farming company, providing a channel for Sustenir to cultivate Unfold's high-yield seeds.
Vertical farming is projected to grow into a $12.77 billion market in 2026, according to Allied Market Research, up from $2.23 billion in 2018.
Temasek invested 3 billion euros ($3.7 billion) into Bayer in 2018 -- funding which helped Bayer complete the acquisition of U.S. seed producer Monsanto.
The company anticipates further investments in the agricultural sector.
"Whether it's in the area of an alternative protein, aquaculture, or crop science, it's an area that requires actually more capital," said Temasek International CEO Dilhan Pillay Sandrasegara. "So far it's done well for us and we're still keen to invest more in it."
Temasek has expanded its portfolio of life sciences and agribusiness investments. Allocation in the domains stood at 8% at the end of March, or five points higher than five years earlier. The size of the holdings is about $17 billion.
The coronavirus pandemic has heightened concerns over food security. Thailand and other trading partners temporarily imposed restrictions on exports. The Singaporean government doled out 30 million Singapore dollars ($22 million) in subsidies this April to help companies produce more eggs, leafy vegetables and fish.
"In Singapore, with less than 0.8% arable land, vertical farming innovation is critical," said Unfold CEO John Purcell.
This year, Temasek has invested in startups that develop meat and fish substitutes, as well as plant-based milk. GIC, another Singaporean state investor, in May picked up shares in Apeel Sciences, a U.S. company that developed an artificial peel for fruits and vegetables to extend shelf life.
The less-than-stellar portfolio performance has also factored in Temasek's investments into agribusiness. For the year ended March, the company reported a return of minus 2.3%, the first negative result in four years. Declining stock values of domestic companies such as the banking group DBS Group Holdings and the conglomerate Sembcorp Industries were behind the setback.
When Singapore Airlines sought to raise up to S$15 billion in rescue funds this March, Temasek was the first to indicate it would sign on in light of its status as a major investor in the carrier. Saddled with its role as a financial provider of last resort, the state investment group's ability to reap returns from investments in agriculture and other growth sectors will sway its performance.
Temasek has also stepped up investment in advanced medical fields such as biopharmaceuticals in the past year, with stakes in 10 companies revealed in 2020 so far.
Vertex Venture Holdings, a Temasek unit that oversees a fund specializing in the medical field, has invested in more than 20 healthcare-related startups, including American drug developer Elevation Oncology in July.
"COVID-19 has shone a light on the importance of continued R&D investment," said Lori Hu, managing director of Vertex Ventures HC. "It has revealed critical unmet needs in the health care industry. We continue to actively look at new deals."
Leveraging its broad network, Vertex took a stake in Israeli telemedicine platform operator Datos Health in April and invested in India's IVF Access Hospitals, which specializes in infertility treatments, two months later.
Through its investments in the medical field, Temasek is also involved in the global race to develop coronavirus treatments. It was part of a group of investors to pour $250 million into Germany's BioNTech, which is jointly developing a COVID-19 vaccine candidate with Pfizer. South Korean drugmaker Celltrion, in which Temasek holds a roughly 10% stake, has brought a diagnostic kit to market in the U.S. last month.
Investments in biopharmaceutical developers carry high risks, but the payoff can be large when a treatment successfully reaches the market. Holdings in unlisted companies accounted for 48% of Temasek's portfolio as of March-end, up six points from a year earlier.
Lead photo: Courtesy of Unfold - Vertical farms use hydroponics to grow crops inside buildings.
[WEBINAR] Women In Agriculture Panel - Greenhouse Grower & Indoor Ag-Conversations
Greenhouse Grower & Indoor Ag-Conversations Present Women In Agriculture Panel - Wednesday, September 16, 2020 - 2-3 pm | EST
GREENHOUSE GROWER &
INDOOR AG-CONVERSATIONS PRESENT
WOMEN IN AGRICULTURE PANEL
WEDNESDAY, SEPTEMBER 16, 2020
2-3 PM | EST
SAVE YOUR FREE SPOT!
Moderated by Janeen Wright, Editor, Greenhouse Grower
Our Panel Includes
Corinne Wilder, Vice President, Global Commercial Operations, Fluence By OSRAM
Amy Samples, Director of Community Outreach and
People Programs, AppHarvest
Erika Summers, Sales Engineer, LMS Building Systems
Charlotte Prud'Homme, Founder, Generation Permaculture Design
During this insightful AND inspiring 60-minute session, our panelists will discuss:
How can we as women in agriculture be the change we want to see in our industry
What challenges face women in the different sectors of the agriculture industry
How can we empower other women and what can we do to inspire the next generation of women in agriculture
And more!
Join us! And, if you can't make the live session, register anyway and you'll get the recording in an email after the webinar
LEARN MORE
SPECIAL THANKS TO OUR INDOOR AG-CON 2020
EXHIBITORS, SPONSORS, MEDIA ALLIES &
INDUSTRY PARTNERS
Indoor Ag-Con, 950 Scales Road, Building #200, Suwanee, GA 30024, United States
“We Are Developing A Sustainable Technology That Uses 75% Less LED Lighting”
Verde Compacto, a Mexican start-up, producer of container farms and indoor farming growing technologies, has seen significant demand for their growing systems during the pandemic
Verde Compacto, a Mexican start-up, producer of container farms and indoor farming growing technologies, has seen significant demand for their growing systems during the pandemic.
"COVID is driving this market forward because people want to know what is behind their food and their diets. Logistic chains in countries like South Korea and Arab countries are really dependent on imports. They are trying to implement urban technologies to strengthen their supply chains. As we’re focusing on growing systems, we are trying to turn this into reality. We are growing food in a more sustainable way where everyone can benefit from it”, Juan Gabriel Succar, Co-Founder and CCO of Verde Compacto says.
The company has an R&D container farm, Huvster, with several labs and small scale systems. The company sells some of its crops locally to better understand the urban business model, as Verde Compacto is educating the future indoor growers.
The Huvster growing container
Succar continues: “We are providing the knowledge to any grower that wants to have an urban farm and we are helping them throughout the process by constructing a farm to their needs.” The company does not only build container farms, which is their standard model but also provides custom made projects such as warehouses or buildings. Or on a smaller scale like supermarkets and restaurants. “We provide the knowledge to install a farm at any size”.
Decreasing LED use
Verde Compacto is looking to improve the electricity use for its growing solutions. “We are developing a sustainable technology that uses 75% less LED lighting, which is part of a sustainable R&D project. The tests are still running but they have delivered positive results. In the end, our technology used for indoor farms allows us to rotate the lamps. Rather than using four lamps at one spot, Verde Compacto can use one light that is constantly rotating. That's why we can make such a big impact on light usage”, Succar affirms.
Lack of quality and water
“Every business model and location has different benefits. As we are one of the largest agricultural countries in the world, we can offer excellent fresh produce quality. The sad story is that all the good fruits and vegetables are exported, thus there is a lack of quality products here in Mexico”, Succar says.
Succar says that Verde Compacto’s technology can build a profitable business model to deliver excellent quality and healthy food to the Mexican society. He notes that the central Mexican region sees a big challenge: a large water shortage. “With our solution, companies still see an opportunity to grow food and maintain their quality by using fewer resources”, Succar notes.
Sustainability
“We always try to give the best options possible regarding our client’s budget, business model, and capabilities. Verde Compacto is cooperating with solar panels to give access to clients for installing these solutions. “Renewable energy, in the end, really depends on the client. Our goal is to make vertical farming as sustainable as we can”, Succar states. At the end of October this year the company will install the first urban farm in Salamanca, Mexico which will be run on 100% solar energy.
Price opportunities
Succar: “In Mexico, we provide our produce at a lower price level than supermarkets. This is done on purpose, to get people to know about vertical farming. Sometimes we are on the same price level.”
Olivier Kappetein, EU representative at Verde Compacto notes: “We have a financial stimulator and we found out that we can bring product prices down. Consumers would pay less compared to supermarket prices as they are unbelievably high. In the United Arab Emirates, locally grown products are unfindable. An iceberg lettuce costs around €7.60 (9 USD) or more. We could get that price down by at least 350% and still make a profit if we were to sell our produce there. We are aiming to sell high-quality food and that’s what they are looking for.”
Pre- and post COVID story
Verde Compacto has a pre- COVID story and a post-COVID story regarding any company expansions. The pre-COVID story was to expand to all Latin American countries, as a priority. They started several alliances and promoted the Verde Compacto technology in Latin America. However, the economy in Latin America was really affected during the pandemic.
“Thus, countries depending on imports saw a great opportunity in our technology for constant production. We didn’t get behind on the expansion actually. Right now, we are working with associations to open different commercial offices in several countries in Latin America. We will be expanding there at the beginning of next year. We are also exploring different options in different parts of the world, expanding globally. One of the regions is Northern Europe because we saw the need for farming technology in those countries. Especially in Luxemburg, where there’s limited fresh produce available.
“The most common problem in vertical farming is the unawareness of the consumer”, Kappetein adds. “They don’t know what it has to offer. It’s still an investment that needs to be made. There is still a greater focus on organic produce as they are aware of the great benefits that come along.”
The Verde Compacto team
Forage
Verde Compacto has been developing its own R&D department, generating knowledge that is also used for new product lines. Succar continues: “We are developing indoor farming systems that are not limited to leafy greens and herbs, but also for forage e.g.. Forage is eaten by grazing cattle mostly. With our hydro system, we can feed cows e.g. with using fewer resources in a more profitable way. The meat and milk industry is impacting the ecosystem significantly. Implementing this technology will help us to make this type of agriculture more sustainable.” The company is also exploring the opportunities of launching indoor strawberries, with the greatest focus on Europe.
For more information:
Verde Compacto
Juan Gabriel Succar, Co-founder, and CCO
juan.gabriel@verdecompacto.com
Olivier Kappetein, EU representative
olivier.kappetein@verdecompacto.com
Phone: +316 14 62 13 10.
www.verdecompacto.com
Publication date: Tue 8 Sep 2020
Author: Rebekka Boekhout
© HortiDaily.com