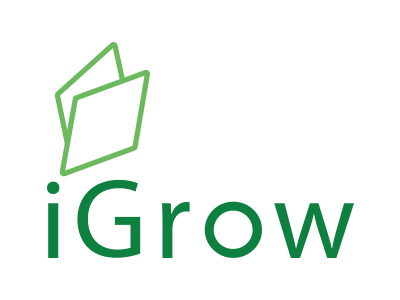
Welcome to iGrow News, Your Source for the World of Indoor Vertical Farming
Polygreens Podcast Episode: 17 - Nicola Kerslake - Contain Inc.
Nicola Kerslake founded Contain Inc, a fintech platform for indoor agriculture, that aids indoor farmers in finding lease funding for their projects
Nicola Kerslake founded Contain Inc, a fintech platform for indoor agriculture, that aids indoor farmers in finding lease funding for their projects. They're backed by Techstars' Farm to Fork program, funded by Cargill and Ecolab.
Latest Episode
GrowGroup IFS Introduces Their Own Grow Container Systems GCS 40HQ
The GCS 40HQ is available in different models. All models are in a 40ft container and includes LED technology, climate computers with remote control, and extensive control on water, temperature, humidity, CO2, and lighting
March 12, 2021
GrowGroup IFS Introduces Their Own Grow Container Systems GCS 40HQ
GrowGroup IFS introduces the GrowGroup Grow Container Systems “GCS 40HQ” for small container cluster farms, research & development, schools & universities, and pilots for new indoor farms. With this new solution now GrowGroup IFS can support also small farms in an accessible way with their unique and full approach including support with the operation through their partners GaaS Wageningen and Hoogendoorn Growth Management.
Grow Container Systems “GCS 40HQ”
The GCS 40HQ is available in different models. All models are in a 40ft container and includes LED technology, climate computers with remote control, and extensive control on water, temperature, humidity, CO2, and lighting. The basic model has a very low entry-level and is upgradeable on different levels. The client can choose for example for an upgrade to the highest quality of climate computers of partner Hoogendoorn Growth Management or the highest quality of LED technology of Signify. The client can even choose for the support with the operation through partner GaaS Wageningen.
“We support the bigger farmers with our unique and full approach on indoor farming for some time already but noticed also that smaller farmers, in particular, have a great need for this. That’s why we launch our own GCS solution right now, so all farmers can use the newest technology of indoor farming for year-round cultivation all over the world”, John Breedveld, CEO GrowGroup IFS.
GaaS Wageningen
Partner GaaS Wageningen from the Netherlands has access to a pool of more than 200 agricultural specialists. Its core business is supporting the operation of high-tech indoor farms from the small ones as the container farms up to the large ones as the big indoor factories. They have high knowledge of indoor farming and sharing their knowledge with the farmers by supporting and training them but also with schools and universities.
GrowGroup IFS
GrowGroup IFS (Innovative Farming Solutions), founded by CEO John Breedveld in Barendrecht in the Netherlands, is specialized in developing indoor farming based on the most advanced Dutch innovative farming solutions, especially in regions where normal cultivation is restricted by extreme climate and or limited space.
USA - NEW YORK STATE - Ellicottville Greens’ Investors Discuss Why They Backed The Company
Ellicottville Greens crossed a major hurdle facing many growth-oriented startups recently when it pulled in a $1 million round of Series A funding from local angel investors
By Dan Miner – Reporter, Buffalo Business First
March 10, 2021
Andrea Vossler, partner at Lippes Mathias Wexler Friedman LLP | JOED VIERA
Ellicottville Greens crossed a major hurdle facing many growth-oriented startups recently when it pulled in a $1 million round of Series A funding from local angel investors.
How did co-founders Gabe Bialkowski and Sal LaTorre convince angels to move cash into their bank account in exchange for an ownership percentage of the business?
The answer lies somewhere at the intersection of familiarity, talent, and foresight, according to Scott Friedman, chairman of Lippes Mathias Wexler Friedman law firm, and Andrea Vossler, a partner at that firm.
The duo, who invest through Varia Ventures, were the lead funders in Ellicottville Greens’ round.
Bialkowski is a computer science graduate from the Rochester Institute of Technology who has been in and out of several startups in the last decade, including a startup in Los Angeles that successfully raised seed capital.
“We worked with Gabe in the past and we find him to be bright, entrepreneurial, and collaborative,” Friedman said. “To build a great company requires real teamwork and Gabe is open to building a great team.”
Scott Friedman, chairman of Lippes Mathias Wexler Friedman LLP | JOED VIERA
The “bet the jockeys” mantra is a common beat among angel investors, who know that even the best ideas will face challenges requiring human ingenuity to overcome.
The model itself was also at the right place for an angel investment round, Vossler said. Ellicottville Greens builds organic vertical farms in shipping containers – making them cost-effective and mobile. It already has four such units in operation, allowing the team to show real-world evidence of its theoretical premise.
The company positions itself at the cutting-edge of a hot consumer trend, which is the ability to offer fresh and locally sourced produce. Its mobile units can be placed directly on a customers’ premises – an idea with major potential in the grocery space.
Ellicottville Greens' Container Farms | ELLICOTTVILLE GREENS
And finally, it uses technology to support production and operations and uses established e-commerce channels such as Produce Peddlers and Off the Muck.
“It’s an ag-tech startup in a massive market that’s continuing to grow,” Vossler said. “Gabe is taking a fairly straightforward business model and wrapping it with technology, utilizing the shipping containers to push down costs and creating significant efficiencies around the delivery of the product.”
Ellicottville Greens completed a $250,000 seed round of funding last year from Launch NY and other local angels. Bialkowski aired his company’s progress at a Jan. 27 web presentation in front of the Western New York Venture Association.
He surpassed many of his own growth and financial milestones for the year in the first quarter.
The mix of attractive leadership, market, and rapid growth was how Ellicottville Greens crossed the finish line on its Series A round. The idea, of course, is that the real race has just begun.
“As he continues to build his team and get traction, we don’t think there is any limit to the potential for this company,” Friedman said.
IN THIS ARTICLE Andrea Vossler Person Banking & Financial
NIGERIA: Fresh Direct Makes Landless Farming Possible And Appealing For City Dwellers
With about 200 million people to feed, Nigeria is battling with food security and is yet unable to produce all the food it needs
March 9, 2021
With about 200 million people to feed, Nigeria is battling with food security and is yet unable to produce all the food it needs. Coupled with that, farmers still lose a significant percentage of produce from post-harvest losses because of poor roads, lack of storage systems among others.
Most farms are located in rural areas because that is where the land is. The markets, however, are in the urban areas, and in taking the food from where it is harvested to where it is needed, a lot of damages happen to the produce. Studies carried out on post-harvest losses in some Nigerian communities show that as much as 20 – 30% of total grain production, 30 – 50% of root and tuber and a usually high percentage of fruits and vegetables are lost after harvest.
Nigeria produces about 1.5 million tons of tomatoes a year, but over 900,000 tons is lost to rot.
What if farms were located closer to the urban markets and farmers could cut down post-harvest losses by selling to the farm as soon as the produce is ready?
Agritech startup, Fresh Direct, is making this possible through its combination of hydroponics and vertical farming. The company was founded by Angel Adelaja in 2014.
Fresh Direct’s different approach to agriculture
Hydroponics is a soilless technique used to grow crops in nutrient solutions instead of in the soil. Fresh Direct grows different crops in vertical stackable containers and develops its own hydroponic system using technology and locally-sourced materials. This includes the use of metres and sensors to monitor the conditions of the plants in the stacked farm.
Farming with hydroponics
The container farms allow people in urban areas as well as people who have never farmed before to grow agricultural produce directly in places that are closer to the market. By using stackable shipping containers, the volume of crops that can be cultivated on a piece of land is increased exponentially. This allows the farmer to get as much as 10 times more yield using only 7 percent of the land that would be required if traditional farming methods are used.
“It has a lower barrier of entry because you do not need to go find land to start. You do not need a green house. You can start in your kitchen, closet, balcony or backyard.”
Angel Adelaja
Since the planting does not require soil, this system of farming is more appealing to youths because the back-breaking work that characterizes agriculture is absent. However, what this mode of farming removes in stress, it adds in creative thinking.
Suggested Read: From Farmcrowdy to Releaf, Here are the 5 Most Outstanding Agritech Startups of 2020
According to Adelaja, “What you avoid in back-breaking work you face in advanced thinking. It’s a higher level of thinking needed to calculate nutrients needed or design a system”.
The startup does not provide educational materials for city farmers, instead, it organizes periodic training to help farmers and intending-farmers get their footing.
Source: FoundersAfrica
Fresh Direct is gaining traction by involving more youths
Fresh Direct plans to get 10,000 youths interested in its Agritech model of farming. Already, the startup has urban farms in Abuja as well as mini-campuses in Osun State.
Also Read: Kenyan Insurtech Pula Closes $6M Series A to Boost Profits for Small-scale Farmers Across Africa
It teaches people who want to learn about urban farming as well as set up their own vertical farming containers. These teachings are provided in the form of periodic training that are organized by the startup. A training costs between N10,000 and N30,000 depending on how extensive the trainees want to go in urban farming.
After the training, Fresh Direct helps the trainees to get financing for the container farm with a collateral-free micro-loan that is obtained from banks. The problem of access to the market is also removed through the startup’s network of ready off-takers. After the produce is harvested, the city farmer can sell directly to Fresh Direct’s market.
Fresh Direct has raised N3 million in a pre-seed round
Since it started in 2014, Fresh Direct has raised funds from one disclosed round. It raised N1 million naira from Chivas Venture in 2016 in a pre-seed round. It raised an additional N2 million from She Leads Africa.
While players like Farmcrowdy are helping to make funds available for farmers in the country, more lucrative ways of farming like the vertical method and hydroponics can help farmers maximize their production and get more urban dwellers into the agriculture sector.
US: NEW YORK - Well-Known Investors Water Ellicottville Greens With $1M In Growth Funding
The Series A round of funding will support construction of mobile vertical farming facilities, built inside reused shipping containers, along with the acquisition of Vertical Fresh Farms, an established indoor farming operation in Buffalo.
By Dan Miner
Reporter, Buffalo Business First
March 8, 2021
Ellicottville Greens continues to push forward on its ambition with $1 million in new funding, led by well-known local investors.
The Series A round of funding will support construction of mobile vertical farming facilities, built inside reused shipping containers, along with the acquisition of Vertical Fresh Farms, an established indoor farming operation in Buffalo.
It is a natural progression for the company, which was founded in 2018 by Sal LaTorre and Gabe Bialkowski and seeks to take advantage of the national consumer drift toward locally grown, organic produce.
“We decided to go after a new round of funding because we have a lot more demand coming in than we have capacity to grow right now,” Bialkowski said. “We are focusing on growing the product and sales and that will help define everything else.”
The round was led by Scott Friedman, chairman of Lippes Mathias Wexler Friedman law firm, and Andrea Vossler, a partner at that firm. The duo run Varia Ventures, an investment vehicle and management consultancy aimed at startups in Buffalo. A group of angel investors based in Buffalo participated as well.
Ellicottville Greens raised $250,000 in seed funding last year from Launch NY and other local investors.
Ellicottville Greens has thus far established four shipping containers: three at its Ellicottville home base and one on the Eastern Hills Mall property in Clarence. It sells its products to homes and restaurants through web-based marketplaces that include Produce Peddlers and Off the Muck.
Produce Peddlers is itself a local startup founded by Gary and Gina Wieczorek.
In the long-term, Bialkowski says Ellicottville Greens has a repeatable business model that could be attractive to supermarkets since the company could set up shop nearby and deliver produce at the peak of possible freshness.
He said the firm is set up at the intersection of nationwide consumer shifts in how people consume food.
“People want to buy healthy local products,” Bialkowski says. “They’re getting more health-conscious and they want to know where their food comes from.”
Ellicottville Greens is the third local startup to announce a growth-oriented round of private funding this year. The others include Torch Labs ($25 million) and Circuit Clinical ($7.5 million).
Lead photo: Ellicottville Greens' storage containers
IN THIS ARTICLE
Advanced Container Technologies, Inc. Joins Clean Food Initiative
Through the use of the company’s GrowPods, ACTX can provide farmers, community groups, investors, and non-profit agencies with a turnkey system to grow ultra-clean and nutritious food that can not only benefit the ecology of the planet and bolster community food security but can also provide new jobs and economic opportunities
March 03, 2021 | Source: Advanced Container Technologies Inc.
Company joins movement toward sustainable alternatives to traditional food production.
CORONA, Calif., March 03, 2021 (GLOBE NEWSWIRE) -- Advanced Container Technologies, Inc. (Ticker: OTC:ACTX) stated it is joining the Clean Food Initiative and intends to become a leading force in the drive toward sustainable agriculture.
The Clean Food Initiative is focused on bringing clean, fresh, healthy food to children throughout the world, that is free from pesticides, herbicides, or harmful chemicals. Along with the practice of implementing Sustainable Agriculture Systems (SAS), the aim is to develop a global food system that uses half the water and half the soil as it does today – yet produces twice as much food.
Through the use of the company’s GrowPods, ACTX can provide farmers, community groups, investors, and non-profit agencies with a turnkey system to grow ultra-clean and nutritious food that can not only benefit the ecology of the planet and bolster community food security but can also provide new jobs and economic opportunities.
GrowPods are automated indoor micro-farms that can provide a sustainable supply of affordable safe, clean, nutritious food, while also providing jobs at a local level by promoting the growth of a skilled agricultural workforce in non-traditional settings.
Doug Heldoorn, CEO of Advanced Container Technologies, Inc., said the company’s objectives are to make agriculture sustainable, investable, manageable, scalable, and transparent.
“There is a substantial difference between meeting basic food requirements and meeting optimum nutrition requirements,” he said. “People need access to high quality foods that are rich in nutritional value. Future generations deserve access to a healthy and sustainable food supply, not a diet filled with preservatives, pesticides or chemicals.”
SAS and the Clean Food Initiative represents one of the greatest challenges of the 21st century, as well as a tangible investment opportunity with sound business growth prospects and consistent annual income generation.
“There are few problems facing mankind that are as massive as our need to change our methods of food production and distribution,” Mr. Heldoorn stated. “Fortunately, there are innovative solutions to these challenges, and we are extremely proud to be a vital participant in this agricultural and social evolution.”
For more information, call (951) 381-2555 or visit: www.advancedcontainertechnologies.com.
About Advanced Container Technologies, Inc.
Advanced Container Technologies, Inc. is in the businesses of selling and distributing hydroponic containers called GrowPods; and designing, branding, and selling proprietary medical-grade containers that can store pharmaceuticals, herbs, teas, and other solids or liquids, and can grind and shred herbs; as well as selling other products and accessories, such as humidity control inserts, odor-proof bags, lighters, and plastic lighter holders; and provides private labeling and branding for purchasers of the Company’s containers and the other products. For more information visit: www.advancedcontainertechnologies.com.
Forward-Looking Statements
This release includes predictions or information considered "forward-looking" within securities laws. These statements represent Company's current judgments but are subject to uncertainties that could cause results to differ. Readers are cautioned to not place undue reliance on these statements, which reflect management's opinions only as of the date of this release. The Company is not obligated to revise any statements in light of new information or events.
Company Contact:
(951) 381-2555
info@advancedcontainertechnologies.com
Investor Relations:
Stuart Smith
SmallCapVoice.Com, Inc.
512-267-2430
ssmith@smallcapvoice.com
Related Articles
More articles issued by Advanced Container Technologies Inc.
More articles related to: Product / Services Announcement Food
AmplifiedAg Introduces Indoor Farm Platform And Disruptive Technologies, Positioning Company For Rapid Expansion
"AmplifiedAg is on a trajectory to change how the world is feeding itself. Through the adoption of our core technologies and scalable farm platform, we're providing secure food sources and influencing a global shift to indoor farming, which will play a key role in providing food to a growing planet," said Don Taylor, CEO of AmplifiedAg, Inc
News Provided By AmplifiedAg
Mar 03, 2021
CHARLESTON, S.C., March 3, 2021 /PRNewswire/ -- With a mission to provide global access to safe food, AmplifiedAg, Inc. introduces its indoor farming platform which includes vertical farms, hydroponic systems, and its proprietary operating system with disruptive seed-to-sale SaaS-based technologies. For the past five years, AmplifiedAg has demonstrated its unparalleled ability to sustainably grow produce to scale at the highest yield, quality and nutritional value, while operating directly at the point of consumption.
AmplifiedAg, Inc. wholly-owns Vertical Roots, the largest hydroponic container farm in the world. Vertical Roots indoor farm production operates with AmplifiedAg's holistic indoor farming platform.
AmplifiedAg's compact farm design operates directly at the point of consumption, maximizes growing space, and is easily scalable in food deserts and space-limited areas. The company's proprietary OS gives farmers total transparency and control of horticulture, food safety, production and business management.
AmplifiedAg deploys indoor farms 70% faster than other CEA implementations, and directly at the point of consumption.
AmplifiedAg rapidly deploys fully functioning farms 70% faster than other CEA implementations, and at cost, that is 50% of the required capital per production pound. The company upcycles shipping containers into controlled agriculture environments with vertical hydroponic systems, LED lights, and electronics, and integrated with AmplifiedAg's proprietary operating system.
AmplifiedAg's indoor farm platform produces 86 times more crop yield per acre compared to traditional farmlands and provides reliable crop production with 365-day farming, regardless of climate and resources. The compact design maximizes the growing space and provides easy mobility and scalability in food deserts and space-limited areas.
But the heartbeat of the operation is AmplifiedAg's proprietary Operating System that features industry-exclusive traceability which tracks every detail of an individual plant's journey from its growth to distribution. This gives farmers total transparency and control of horticulture, food safety, and business management.
Farm containers' resilient architecture and segmentation minimizes the risk of crop loss due to pest and pathogen infestations. SaaS-based technologies provide real-time tracking analytics and 24/7 access for farmers to mitigate risk, control the farm environment and optimize plant growth.
AmplifiedAg's ability to quickly place farms directly in communities and distribution points drastically reduces emissions. Sustainably-focused, the farms don't use soil or pesticides and utilize up to 95% less water than traditional farming.
Wholly-owned by AmplifiedAg, Vertical Roots is the company's proofpoint and has set industry-breaking records in less than five years. Vertical Roots is the largest hydroponic container farm in the U.S., growing nutritious leafy greens with products in over 1,200 grocery stores across the Southeast.
With a proven concept for leafy greens, AmplifiedAg's horticulture expansion plan includes varied nutrient and protein-rich foods to feed the world's growing population.
Increasing threats to the planet's food production fueled Taylor, a 30-year software industry veteran, to found AmplifiedAg in 2016.
"With a growing population, less arable land, water supply and food contamination issues, climate change and environmental disasters," said Taylor, "Our planet is on a path to grow less food for more people while continuing to accelerate the degradation of the earth's fragile ecosystem. Exasperating our already critical food access issues on the planet. The only way we're going to get ourselves out of this situation is with technology. We need to grow safer food in greater volumes closer to the point of consumption while conserving and restoring the environment."
"That is what is driving all of our development and innovation, and ultimately the demand we are seeing from indoor farmers and communities across the world," concluded Taylor.
AmplifiedAg, Inc. was founded in 2016 as the parent company of Vertical Roots, Boxcar Central, a SaaS platform supporting third-party logistics companies and breweries, and Tiger Corner Farms, a CEA farm manufacturing company. AmplifiedAg has absorbed Tiger Corner Farms and Boxcar Central operations as the company presents its mobile indoor farm platform to the market.
About AmplifiedAg, Inc.
AmplifiedAg, Inc. is an ag-tech industry visionary on a mission to provide global access to safe food. The company manufactures indoor vertical farms, hydroponic systems, and disruptive seed-to-sale SaaS-based technologies. Unlike other indoor ag operations, AmplifiedAg provides holistic indoor farm solutions to grow and distribute food anywhere in the world.
AmplifiedAg owns and operates Vertical Roots, the largest hydroponic container farm in the World. Learn more at www.amplifiedaginc.com. Growing Food for a Growing World.
SOURCE AmplifiedAg
Related Link
Creating A Connected, Community Centered Urban Farm Environment
Street Farm’s micro-vertical farm works with a hydroponic growth system and is designed to be reused again and again. The designs vary in size from 8’ wide x 8’ high x 12’ long to 16’ high to 32’ long
“NYC streets are ripe with potential to start producing their own food," says Julian Lwin with Street Farm. Full and built up through the city might be, lack of space is no excuse for anyone, as Street farms’ vertical farm can be fit also in small public spaces. “We now can claim street space for sustainably grown urban greens the same way we claimed the streets for outdoor dining during COVID.”
COVID forced many countries to rethink their food system, as logistics suddenly got complicated. Also Julian became acutely aware of the need for new retail environments, finding a safer way to interact with food, and purchasing fresh produce. Via an automated dispensing think vending machines & dedicated StreetFarm app.
In this period he saw people taking their activities outside, exercising or even eating out on the streets whereas they would normally do this indoors. With that in mind, he found (conceived) Street Farm, intending to find a solution for growing fresh produce right there in the streets of NYC. “We will fabricate the farms right here in New York’s Brooklyn Navy Yard, to keep the transport emissions to an absolute minimum.” This model can be set up in any city metropolis around the globe where freshly grown produce is missing from the urban environment
Street Farm’s micro-vertical farm works with a hydroponic growth system and is designed to be reused again and again. The designs vary in size from 8’ wide x 8’ high x 12’ long to 16’ high to 32’ long. The smaller ones can be placed in gardens, allowing the larger-scale growing to be done in empty storefronts, city lots, etcetera. Julian dreams of the microfarms to be placed even in schools, libraries, and train stations to show people that food can be grown literally anywhere.
Urban “element" vertical farm
Combining the latest technologies in the field of AI and robotics for monitoring the growth and yield, the New York streets will produce lots of fresh produce for the local population. “With Street Farms we can transform New York from a food desert to a paradise of nutritious, healthy vegetables.” The plan is for the system to monitor the plant growth itself, but for the harvest to be done by employees, thus creating more jobs in the city. “We want these farms to create a connected, community-centered urban farm environment, connecting people to each other and to the food they eat.”
Julian finds it vitally important that people see tangible agriculture grown in public places, rather than hiding vertical farms in post-industrial spaces and rooftops. “Street Farms will connect the community with the products we eat. We aim for a paradigm shift in our relationship to the food we eat and our city landscape.”
Lead photo: The micro modular urban vertical farm satellite
For more information:
Lwindesign
Julian Lwin, Founder
julian@lwindesign.com
www.lwindesign.com
Publication date: Thu 25 Feb 2021
Author: Rebekka Boekhout
© VerticalFarmDaily.com
New Freight Farms CMO Shares 4 Reasons Why He Moved From Sportswear To AgTech
After an amazing experience and professional success, James felt that he needed a change: a new challenge, a new industry, a new way to make an impact
Former Senior Director Global Marketing at Reebok shares his reasons for joining Freight Farms C-Suite
James Woolard spent the last 14 years at Reebok, heading up everything from regional Sports Marketing and Brand to Global Marketing for the brand’s Running and Style units. After an amazing experience and professional success, James felt that he needed a change: a new challenge, a new industry, a new way to make an impact. His search brought him to the world of AgTech and Freight Farms, where he saw the huge potential of both the company and the industry and knew it was just what he had been looking for. Today, James shares the four big reasons why he was so drawn to the AgTech industry, and how he believes his previous experience will help propel Freight Farms forward.
In the past, I have always resisted “building a social presence” as a result of a (very British) suspicion of people’s real motives and my own laziness in maintaining it. In truth, the former reason is an easy cover story for the latter. However, in this case, my aversion to online social platforms has been overruled by a greater feeling that I want to share: Gratitude.
I am grateful for the experiences I have had, the people I have been fortunate enough to meet, and excited by all the opportunities in the future. However, most recently I am grateful for the opportunity to become the Chief Marketing Officer of Freight Farms. There were several small reasons to make the switch–but they all scaffold up to four somewhat big reasons:
Creating a Simple Solution for a Complex Problem
A pioneer of indoor agriculture and a leader in hydroponic container farming, Freight Farms has a suite of products and technology that can revolutionize access to hyper-local fresh grown produce. Our products reflect a level of complex design and engineering on which far cleverer people than me tirelessly work; yet the solution we are creating is incredibly simple — A 2.5-acre smart farm in a 40ft freight container that can go anywhere in the world to provide food security. With already over 300 of our farms around the world, we are building a tech-connected network of farmers who are simultaneously solving food access issues in their own communities and building a new global food system–all powered by Freight Farms technology.
1 in 6 people in the world relies on food imports to feed them daily. This number is set to reach 3 in 6 by 2050.
9 counties–mostly in California–are responsible for most of the food supply within the U.S. Any disruption (fires, drought, etc) can be catastrophic to the whole system.
In the U.S., 19 million people currently live in food deserts with limited access to healthy and nutritious fresh foods.
2. Leveraging Cross-Category Experience
In addition, I am incredibly grateful to my former colleagues at Reebok and Adidas. I was lucky enough to have a robust education in the UK Sports industry and be part of and learn from an amazing Adidas leadership team. I was fortunate enough to come to the US, understand firsthand the dynamics of a global business, and meet a diverse range of interesting people. And I got to set up my family in Boston.
Now it is time to apply this experience to Freight Farms. Why the move from sports to Agtech you might ask? Yes, I needed the change and new challenge. And yes I would be lying if I said I targeted Agtech but sometimes you find what you need without realizing it. I am still a sports fan at heart — and when I first walked into the offices I walked into a locker room full of energy and talent. I was intrigued and hooked early on. I met Jon — who a decade earlier had looked at a Freight container and thought “why can’t I put a farm in there and build a business helping people anywhere in the world access fresh, hyper-local food”; I met a team of people (young, purposeful, talented ones) like Caroline, our Director of Marketing and Community Relations, with huge potential and authenticity who wanted to learn and grow; I met a new CEO in Rick and CTO in Jake with pedigree and passion; I saw a set of investors led by Ospraie Management and Spark Capital backing this all with capital.
3. Driving Profits for Company & Customers
At Freight Farms, I saw the impact I personally could have on the business. We have a thriving community of customers who have been essential in building Freight Farms’ success. The stories are inspiring, and I am eager to apply my experience to help Freight Farmers achieve their own individual success with the best possible support from our company. At the end of the day, we can’t be shy about saying “people need to make money”, because that’s the only way our mission to build a global infrastructure of local farms can succeed. I am here to embrace this and say ‘how can we create a return on investment for every stakeholder’? This is how we will grow.
4. Saying ‘No’ to Greenwashing and ‘Yes’ to Tech for Good
I am conscious of the perceived need to be on trend with “sustainability”, of the danger of falling into buzzwords and jargon that are of the moment. There is a business model and story myriad people are chasing. This is all happening parallel to a degradation of our trust in technology; as a society, we recognize it’s time to direct it towards something good. With three girls under 12 (all over using screens in Covid times), I see the benefits and dangers. We all see the power of the big brands and how algorithms are driving division. I believe people want to see positive expressions of technology beyond driving up their 401k. Combined, these two factors unlock our greatest brand strength in 2021: we already do leverage technology and data to create a truly sustainable product. There’s no need to spin, exaggerate, or greenwash. We can carry on doing exactly what we are doing with confidence that we’re creating the kind of positive impact the world needs.
That’s what is most exciting about entering the ‘Agtech’ industry: the moniker actually means something — the former (Agriculture) consistently driving change throughout history, and the latter (tech) acting as the most rapid accelerator of that change in my lifetime. It’s exhilarating, and I can’t wait to see how far we can take it.
Learn more about Freight Farms.
Freight Farms
Empowering anyone to grow food anywhere. Freight Farms makes local food accessible in any climate with the Greenery™ container farm.
Follow
3
USA - MICHIGAN: Indoor Agriculture Receives $100,000 Grant From MDARD
The indoor agriculture program is a new major brought to NMU which focuses on hands-on learning of indoor agriculture, sustainable farming practices, urban farming models, environmental infrastructure systems, helping solve the global food crisis, and more
NMU’s new indoor agriculture program recently received a $100,000 grant on Feb. 12 from Michigan’s Department of Agriculture and Rural Development to help offset the costs for a self-contained growing center.
According to MDARD’s page, the grants are to help “promote the sustainability of land-based industries and support infrastructure that benefits rural communities”.
MDARD received over 139 proposals, totaling over $11 million. The program only accepted 20 proposals, which totaled to roughly $1.7 million. This included NMU’s proposal for a self-contained growing center.
The indoor agriculture program is a new major brought to NMU which focuses on hands-on learning of indoor agriculture, sustainable farming practices, urban farming models, environmental infrastructure systems, helping solve the global food crisis, and more.
Last fall was the first semester that the program took off.
“One of the biggest challenges of growing a program is finding space, and even though there is some available around campus, and in the Jacobetti Center in particular, it still costs a lot of money to retrofit that space and make it usable for the intended purpose.” Evan Lucas, assistant professor of technology and occupational sciences, said. “We targeted this grant specifically to help alleviate the cost impact of adding space for our labs.”
Lucas went on by saying that the program submitted the idea of purchasing one to two shipping containers to enhance the curriculum. The shipping containers, depending on size and capability would be used to add growing space and diversity the type of growing space.
The program hopes that with the grant money they will be able to grow, and in turn create more space for students to work. Sarah Cormier, a junior in the indoor agriculture program, has exciting hopes for the grant money.
“I’d hope it’d encourage others to look into the program and think about food production differently,” said Cormier. “We are limited in our labs with the number of seedlings we can tend to, but with more systems we would be able to monitor more plants simultaneously.”
In turn, having more space means having room for more students. After quick shutdowns and pack-up times, last semester was hard for the program. However, Cormier felt that the experience this semester has been more straightforward.
With the COVID-19 pandemic, the program had to cut back on the amount of students able to register. This left many students on waiting lists, unable to participate in the brand new program.
“We were unfortunately not able to open up more than we did without sacrificing the hands-on aspect of growing, which we weren’t really willing to do as that kind of defeats the main purpose,” Lucas stated.
However, Lucas was quick to say how integral Kim Smith Kolosa, another assistant professor of technology and occupational sciences, was to the program.
“She has done an amazing job taking this program from literally non-existent to exceptional in no time, and we couldn’t ask for anything better at this time,” Lucas said.
TAGS: grant, indoor agriculture, news
These Stacked Shipping Containers Are Actually High-Tech Farms
A major perk of the Planty Cube system is that it can be set up in multiple environments, such as restaurants, hotels and apartments
FEB 2, 2020
Credit: n.thing
For green thumb owners looking to take their plant parenting skills to the next level, allow us to introduce you to the Planty Cube, a smart vertical farming system developed by Seoul-based agricultural startup n.thing.
The hydroponic setup is based on “internet of things” technology and is comprised of a network of capsules that enables farmers to cultivate “high quality vegetables in a fully controlled environment, ensuring production over tens of times higher than ordinary farmland per unit area, CES explains. The higher crop yields are directly linked to Planty Cube’s ability to support year-round growing.
Credit: n.thing
In pursuit of n.thing’s mission to turn everyone into a farmer, Planty Cube is off to a running start as the winner of CES 2020 Best of Innovation Awards. The intricate system resembles a shipping container but upon closer inspection is actually multiple shelves of planters, or pickcells, that house seeds.
Each pickcell is connected to the modular system, which is comprised of sensors that track each plant’s health and progress, adjusts humidity and temperatures in response to unexpected environmental changes, and also allows farmers to tend to their crops remotely via a smartphone. In the place of soil, the produce is grown via a nutrient that the system delivers to each plant. The system’s enclosed design prevents pests from infiltrating the crops. Not ready for an entire farm? Planty Cube has a solution for such an agricultural conundrum: It allows growers to choose how many units they start with, leaving them with the option of adding additional units as they see fit.
Credit: n.thing
A major perk of the Planty Cube system is that it can be set up in multiple environments, such as restaurants, hotels and apartments. Its sustainable build helps to decrease environmental impact, further eliminating even more of the obstacles presented by traditional farming methods.
Kenya Foy
CONTRIBUTOR
Kenya is a Dallas-based freelance entertainment and lifestyle writer who devotes most of her free time to traveling, gardening, playing piano, and reading way too many advice columns.
Where Vertical Farming and Affordable Housing Can Grow Together
Some vertical farms grow greens in old warehouses, former steel mills, or other sites set apart from the heart of cities. But a new series of projects will build multistory greenhouses directly inside affordable housing developments
Some vertical farms grow greens in old warehouses, former steel mills, or other sites set apart from the heart of cities. But a new series of projects will build multistory greenhouses directly inside affordable housing developments.
“Bringing the farm back to the city center can have a lot of benefits,” says Nona Yehia, CEO of Vertical Harvest, a company that will soon break ground on a new building in Westbrook, ME, that combines a vertical farm with affordable housing. Similar developments will follow in Chicago and in Philadelphia, where a farm-plus-housing will be built in the Tioga District, an opportunity zone.
Inside each building, the ground level will offer community access, while the greenhouse fills the second, third, and fourth floors, covering 70,000 square feet and growing around a million pounds of produce a year. (The amount of housing varies by site; in Maine, there will be only 15 units of housing, though the project will create 50 new jobs.)
In Chicago, there may be a community kitchen on the first level. In each location, residents will be able to buy fresh produce on-site; Vertical Harvest also plans to let others in the neighborhood buy greens directly from the farm. While it will sell to supermarkets, restaurants, hospitals, and other large customers, it also plans to subsidize 10% to 15% of its harvest for local food pantries and other community organizations.
“By creating a large-scale farm in a food desert, we are creating a large source of healthy, locally grown food 365 days a year,” Yehia says.
Training Artificial Intelligence To Track Greenhouses in Antarctica and Mars
Modern technology has long become a fixture in all spheres of human life on Earth. Reaching out to other planets is a new challenge for humankind
FEBRUARY 17, 2021
Credit: Skolkovo Institute of Science and Technology
Scientists from the Skoltech Center for Computational and Data-Intensive Science and Engineering (CDISE) and the Skoltech Digital Agriculture Laboratory and their collaborators from the German Aerospace Center (DLR) have developed an artificial intelligence (AI) system that enables processing images from autonomous greenhouses, monitoring plant growth and automating the cultivation process. Their research was published in the journal IEEE Sensors.
Modern technology has long become a fixture in all spheres of human life on Earth. Reaching out to other planets is a new challenge for humankind. Since greenhouses are likely to be the only source of fresh food for Mars space crews and settlers, development of artificial intelligence (AI) and computer-vision-based technologies for plant growth automation is perceived as a priority research target. A test site is already in place for developing and testing advanced life support systems: An autonomous plant cultivation module is operating at the Antarctic Neumayer Station III near the South Pole. Right now, scientists are focusing on creating an AI system that could collect information about all the plant growth factors and seedling health and control greenhouses in autonomous mode without human involvement.
"One cannot maintain continuous communication with Neumayer III, and training computer vision models onboard requires too many resources, so we had to find a way to send a stream of plant photographs to external servers for data processing and analysis," Skoltech Ph.D. student Sergey Nesteruk explains.
As a conclusion to their research, the Skoltech team processed a collection of images from remote automated systems using their new approach based on convolutional neural networks and outperforming popular codecs by over seven times in reducing the image size without apparent quality degradation. The researchers used the information from the reconstructed images to train a computer vision algorithm which, once trained, is capable of classifying 18 plant varieties according to species at different stages of development with an accuracy of 92%. This approach makes it possible to both visually monitor the system operation and continuously gather new ML model training data in order to enhance the models' functionality.
There are plans to deploy and test the new systems right on Neumayer III, which will mark an important step towards automation of plant growing modules, thus removing yet another roadblock on the way to Mars.
Lead photo: Plant cultivation module in Antarctica. Credit: Skolkovo Institute of Science and Technology
Living Greens Farms Ramps Up Midwest Expansion
Living Greens Farm has upped its retail distribution with the addition of UNFI Produce Prescott, a division of United Natural Foods, Inc (UNFI)
Feb. 18th, 2021
by Melissa De Leon Chavez
FARIBAULT, MN - Living Greens Farm (LGF) has upped its retail distribution with the addition of UNFI Produce Prescott, a division of United Natural Foods, Inc. (UNFI). This new retail partnership will help LGF expand its product reach to independent, specialty, and co-op retailers throughout the upper Midwest.
According to a press release, LGF’s proprietary vertical indoor farming method yields high-quality, fresh produce. No pesticides or chemicals are used during the growing process. Throughout the growing, cleaning, and bagging process, LGF reduces handling and time to the retail shelf. All of these benefits continue to attract new users and new retail distribution.
Living Greens Farm has upped its retail distribution with the addition of UNFI Produce Prescott, a division of United Natural Foods, Inc (UNFI)
Beginning this month, LGF’s full line of products featuring ready-to-eat bagged salad products, such as Caesar Salad Kit, Southwest Salad Kit, Harvest Salad Kit, Chopped Romaine, and Chopped Butter Lettuce will be carried by UNFI Produce Prescott (formerly Alberts Fresh Produce).
Across the nation, UNFI has eight warehouses, and LGF’s products will be carried by its upper Midwest location, located just across the river from the Twin Cities in Prescott, Wisconsin.
As indoor farming becomes more popular, who will Living Greens Farm partner with next?
Stay tuned to AndNowUKnow as we cover the latest.
COMPANIES IN THIS STORY
We believe in revolutionizing how produce is grown throughout the world. Our products are fresh, local, and pesticide-free....
UNFI
UNFI is the leading independent national distributor of natural, organic and specialty foods and related products...
BRITISH COLUMBIA: Learning Centre Gearing Up For “Village Greens”
The Society used the $166,328 grant to buy a Growcer “growing container” to supply the community with fresh greens year-round: they have made inquiries at IGA and local restaurants and plan to donate some to the food bank
Published on February 13, 2021
By Laura Keil
Fresh, local and green aren’t words you often hear about Robson Valley products in the wintertime, but the Valemount Learning Society hopes to change that.
The Learning Centre is branching out from its usual array of employment services and courses and digging into local food, thanks to a grant last summer from Northern Development Initiative Trust. The Society used the $166,328 grant to buy a Growcer “growing container” to supply the community with fresh greens year-round: they have made inquiries at IGA and local restaurants and plan to donate some to the food bank. They are also considering a box program if other options don’t work out.
The container is currently on order and will arrive sometime in March, said Riette Kenkel, manager of the Valemount Learning Centre, and she hopes they will have their first harvest in May.
Mike Johnson, who works for VLC as an employment advisor, will run the Growcer operation, which will be called “Village Greens.” Prior to arriving in Valemount, he worked in a commercial greenhouse for 20 years, Kenkel said.
The Growcer company provides training as the food is grown hydroponically.
The container will be set up in the Valemount Industrial Park next door to Robson Valley Mushrooms and near the Valemount Community Forest offices. Kenkel said the heating costs should be offset by the well-insulated container walls, which are good to -50 degrees.
She hopes to package most of the food in biodegradable packaging.
Kenkel previously told the Goat it’s no one’s fault the fresh food supply in Valemount isn’t always consistent.
“By the time the truck gets here the produce is old, and if stuff flies off the shelf we have to wait for the next (truck),” she said. “The Learning Centre has always responded to community needs. This was something we were hearing.”
She said it’s a social enterprise, so if it makes money, that cash will be cycled back into the programs that the Valemount Learning Centre delivers.
One of the more recent programs they’ve taken on is 4-H, which has a focus on agriculture and livestock and they’ve put a call-out for people to come up with program ideas.
Kenkel says it goes beyond just agriculture, however. Projects can relate to environmental issues, learning about aspects of farming, soil, and animals- not just farm animals.
The Growcer container is self-contained and ready to go in any season using hydroponics. The Valemount Learning Centre hopes to fill the winter void, create a job or two and raise money for their other programs. //GROWCER
“It’s wide open right now for whatever the community wants it to be.”
Farmers Market management
The Society recently took over management of the Valemount Farmers’ Market from long-time organizer Christine Pelletier.
“We’re pretty excited about it,” Kenkel said. “We’re not really going to make any changes. We want to just run this next season as close to what it’s been in the past.”
She said the market will run from June 17th until September 30th this year and the rates for vendors will be the same: $10 per day plus a $10 annual membership.
Kenkel says they likely won’t sell their own fresh greens at the market, as they don’t want to compete with local growers.
“If Village Greens has something that’s marketable at the farmers market that isn’t competing with existing customers, then we might look at it. But yeah, we don’t want to compete with any of the smaller farmers that have been reliably selling lettuce, kale, basil, that kind of stuff.”
Related Posts:
USA - OHIO: Thinking And Growing Inside The Box
A brother-sister team has taken the mechanics of farming out of the field and into a freight container
FEBRUARY 10, 2021 By SIDNEY DAILY NEWS
Local Farmer Takes The Farm Indoors
By Blythe Alspaugh - balspaugh@sidneydailynews.com
PIQUA — A brother-sister team has taken the mechanics of farming out of the field and into a freight container.
“We are growing beautiful plants without the sun; there’s no soil, and so it’s all a closed-loop water system,” Britt Decker, co-owner of Fifth Season FARM, said. “We use non-GMO seeds, completely free of herbicides and pesticides, so the product is really, really clean. In fact, we recommend people don’t even wash it, because there’s no reason to.”
Fifth Season FARM is unique in many ways; the 3-acre hydroponic farm is contained in a 320-square-foot freight container that sits along 120 S. Main St. in Piqua, with everything from varying varities of lettuce, to radishes, to kale and even flowers in a climate-controlled smart farm that allows Decker and his sister, Laura Jackson, to turn crops in a six- to eight-week cycle. The crops spend 18 hours in “daytime” every day, and the farm uses 90% less water than traditional farming.
“It’s tricky because we’re completely controlling the environment in here. It’s kind of a laboratory more than a farm,” Decker said. “I think there’s about 50 of them around the world right now. These are really international, and they’re perfect for places that are food deserts where they can’t grow food because of climate or other reasons. It gives them a way to grow food in the middle of nowhere.”
Decker and Jackson, along with their brother Bill Decker, also do traditional farming and grow corn, wheat and soybeans, but Decker said they were looking for a new venture that would help lead them to a healthier lifestyle and learn something new.
“Just with the whole local food movement becoming more and more important and food traceability, we just thought it would be a great thing to bring to our community to help everyone have a healthier lifestyle,” Decker said. “People love food that’s grown right in their hometown and the shelf-life on it, when you get it home, is remarkable. It’ll keep for two weeks.”
Currently, Decker and Jackson are growing a half-dozen variety of specialty lettuces that include arugula, butterhead, and romaine, as well as specialty greens like kale and Swiss chard, and even radishes and flowers. They received their freight container at the end of July and set up their indoor farm over two weeks; while the farm has been in operation for less than six months, Decker says that they’re growing beautiful product.
They have also started growing micro-greens, said Decker. Micro-greens are immature plants which are 1 to 3 inches tall and are in a 5-inch by 5-inch container.
“People will use them as garnishments and in smoothies,” said Decker. “Since they are immature plants, they have an intense flavor.”
Decker said they are growing wheat germ, broccoli and spicy salad mixes.
They’ve also started moving forward with sales and marketing. Fifth Season FARM has partnered with the Miami County Locally Grown Virtual Market to sell their products to the community. They also take orders through their website, fifthseasonfarm.com; customers can opt to pick up their orders between 4 and 6 p.m. on Wednesdays, or Decker and Jackson will deliver products up to five miles from the farm. Decker said that Fifth Season FARM is also in discussions with three restaurants in the area about including their specialty greens on their menus.
Decker said they also plan to attend the Sidney Farmers Market when it opens for the spring/summer season.
“We’re really just getting going,” Decker said. “While we were learning to grow products, we didn’t want to overcommit to a restaurant or grocery store before we knew we could really grow a beautiful product, so we’ve been donating product every week to the food pantry at the Presbyterian Church. It feels good to plant the seeds and watch them grow, and it feels good to make sure that people who aren’t getting the proper nutrition are getting some.”
Why I Moved From California To Kansas To Grow Leafy Greens In All Seasons
Brad Fourby runs Leafy Green Farms LLC, a hydroponic shipping container farm in Pittsburg.
By Brad Fourby
January 9, 2021
The Kansas Reflector welcomes opinion pieces from writers who share our goal of widening the conversation about how public policies affect the day-to-day lives of people throughout our state. Brad Fourby runs Leafy Green Farms LLC, a hydroponic shipping container farm in Pittsburg.
Google Maps says the distance between Sacramento, California, and Pittsburg, Kansas, is 1,842 miles.
This year has been tough, with COVID shutdowns, a heart attack, bypass surgery, and the loss of a loved one. All of this slowed me down but did not stop me from leaving California and starting a year-round container farm that will provide Pittsburg with fresh leafy vegetables like lettuces, basils, and arugula.
Good nutrition starts with what is on your plate. Knowing where your food comes from and how it was grown is becoming more important to everyone.
While living in downtown Sacramento, I started Innovative Farms. I would build and help consult with others interested in aquaponics, growing fish and plants together in small places. Small towns have to wait and pay higher prices for food that has been grown and transported from California, China, Argentina, and other countries. The produce is picked early so that it may ripen in transit on ships or trucks while being treated with chemicals along the way.
Through this work, I met longtime Pittsburg residents Rob and Sara Morris, owners of Energy Group Consultants. They told me that Pittsburg and Crawford County were considered a food desert — like much of the Midwest, grocers in Crawford County import their food, while producers export what they grow, such as corn and soybeans.
I would visit the city a few times a year and got to know some of the people and businesses. I loved the vibe of the place.
Rob and Sara and I discussed increasing the farm-to-table opportunities in Pittsburg. We talked about container farming, using repurposed shipping containers that have been outfitted with computer-controlled vertical hydroponics. This highly efficient method requires no pesticides or herbicides to grow vegetables that can be harvested weekly regardless of the climate.
My previous experience with aquaponics reminded me of Freight Farms, a Boston farm manufacturer with a great track record of successful farms worldwide. Their farm design was expandable, and vegetables could grow in any weather condition.
I came up with the outline of a business plan. With three farms, my goal was to begin year-round harvests this winter in Pittsburg and support the farm-to-table lifestyle.
I began making phone calls to the city. Compared to the regulation and tax heavy California, Kansas felt welcoming to new business. I heard the term “agri-tourism,” and the idea of new agricultural developments directly helping the area was exciting for many people I spoke with.
The city planners loved the idea of a new business that supported other existing businesses like restaurants, grocers, and the farmers market community, many of them hurt by the COVID shutdowns.
Working with Pittsburg State University’s Small Business Development Center, I created a final business plan. Equity Bank signed on to assist with the Small Business Administration loan process.
So far it has been a real team effort. We really picked up steam after a call with Mike Green, Equity Bank’s small business banker. Turns out he grew up on a farm and instantly recognized the value the business would be to the entire area. We talked about how freshly picked non-chemically treated vegetables actually taste. The difference is night and day.
After that call I knew for sure Pittsburg would be the home of Leafy Green Farms.
The Kansas Healthy Food Initiative then stepped in and awarded the business $15,000 to assist with operating and equipment expenses. This kind of support was a real boost for everyone. KHFI and our farm goals are very much aligned.
It turned out that everyone agreed: Every Kansan should have access to healthy, affordable food.
The idea of more fresh food being produced in Pittsburg was something Live Well Crawford County director Brad Stroud told me he has been very supportive of. Joining their network has been a very positive experience.
We hope that by adding farms that are unique to the area that grows specialty crops, more people will visit the city and frequent some of the supporting businesses. We will take input from chefs and the community palate, and restaurants in the area will be able to offer menu items that their counterparts in large cities have no chance of offering. Our list of available herbs, roots, and vegetables is long and our variety is huge, with Firecracker Leaf Lettuce, Sylvesta Butterhead, and even Wasabi Arugula.
Sacramento County has around 1.5 million people, Crawford County 38,000. Many of my California friends and family are watching my move with great anticipation. When someone asks “Why Kansas?” my answer has remained the same since the beginning: Kansas is open for business.
Through its opinion section, the Kansas Reflector works to amplify the voices of people who are affected by public policies or excluded from public debate. Find information, including how to submit your own commentary, here.
Lead photo: A Freight Farms container on its way to a destination. (Submitted by Leafy Green Farms to Kansas Reflector)
Funding Now Available To Help Farmers Withe FMSA
Farmers are working to improve food safety on the farm, and prepare for Food Safety Modernization Act (FSMA) inspections, but this requires both assistance and resources
February 10, 2021
A hoop house with tomatoes and peppers grown in New Mexico. Photo Credit: USDA Photo by Bob Nichols.
Farmers are working to improve food safety on the farm, and prepare for Food Safety Modernization Act (FSMA) inspections, but this requires both assistance and resources. We are excited that the Food Safety Outreach Program (FSOP) applications have just opened up and will provide organizations with funding to assist and help farmers and small food businesses with both FSMA and food safety.
FSOP is a federal grants program that funds community-based organizations, non-governmental organizations, cooperative extension, and local, state, and tribal governments’ programs focused on food safety and FSMA. The U.S. Department of Agriculture (USDA) National Institute of Food and Agriculture (NIFA) recently announced $9.6 million in FSOP grant funding this year – the most funding ever available and an increase of almost $2 million from last year.
The deadline for applications is Thursday, April 1, 2021.
Application Details
FSOP projects should focus on outreach, education, and assistance for farmers and small processors around food safety practices and the new FSMA rules. There are two types of projects eligible organizations can pursue to receive FSOP funding: Community Outreach and Collaborative Education and Training Projects. There is no match requirement.
Community Outreach Projects
FSOP will once again offer Community Outreach Projects, to support the development of new food safety programs and to help groups build capacity to address the needs of their communities. Awards can be between $80,000 and $150,000 for projects lasting up to two years. Community Outreach Projects must:
Create, implement or expand food safety education to niche, underserved, or non-traditional audiences.
Be led by a team with a record of strong community partnerships and working with others to educate target audiences.
Create and implement a customized food safety training and outreach program for various types of farms or food processors, including those working with conservation systems, sustainable businesses, and organic food producers.
Collaborative Education and Training Projects
Collaborative Education and Training Projects aim to fund state-wide, multi-state, or multi-county food safety training projects. Grant awards are available for $200,000 to $400,000 for projects up to three years. These projects must:
Be led by a project team with a track record of community partnerships and serving the educational needs of the target audiences.
Create and execute food safety education and outreach for various types of farms or food processors, including those working with conservation systems, sustainable businesses, and organic food producers.
Additional Funds Available for Outreach to Communities of Color
An additional $150,000 is available for applications to either project type that increase outreach to communities of color through the Collaborative Engagement Supplements. Organizations applying for this supplemental support must include a significant collaboration with either one or more of the following universities, colleges, or organizations: 1890s, 1994s, Insular Areas, Alaska Native-Serving and Native Hawaiian-Serving (ANNH), Hispanic Serving Agricultural Colleges and Universities (HSACU), and community-based organizations serving socially disadvantaged populations.
Regional Centers Funds
There is also funding available for the four regional centers focusing on food safety and FSMA. Current centers include:
Southern Region: University of Florida (also “Lead Regional Center”)
Western Region: Oregon State University
North Central Region: Iowa State University
Northeast Region: University of Vermont
Program Changes for FY 2021
The FSOP RFA changes highlight a few recommendations the National Sustainable Agriculture Coalition requested, and we are thankful for NIFA’s continued partnership, and efforts to ensure these changes.
NIFA clarified that the additional Collaborative Engagement Supplements must be in direct partnership with a Minority-Serving Institution or an organization working to serve farmers of color that have been historically underserved, and that the proposed budget must adequately reflect this partnership. NSAC appreciates this clarity and looks forward to further analyzing the racial equity impact of FSOP grants.
NSAC is also excited about the new requirements for Regional Centers to partner with an 1890, 1994, ANNH, HSACUs and/or community-based organizations serving socially-disadvantaged populations within their region, which will help ensure outreach and resources to farmers of color continues to be prioritized.
NSAC also appreciates the clarity that Community Outreach Projects can be used for FSMA training for the organization’s staff with minimal food safety experience and that organizations must have relationships with the target audience.
Upcoming FSOP Webinar for Tribal Staff
On Friday, February 19, 2021, from 2:00-3:00 p.m. Eastern Time the United South and Eastern Tribes, in partnership with Intertribal Agriculture Council, Indigenous Food and Agriculture Initiative, National Sustainable Agriculture Coalition, and National Institute of Food and Agriculture, will be hosting a FSOP webinar for anyone who works with indigenous producers. For more information, and to register for the webinar, click here.
Additional Resources
For additional application details and requirements, see the FY 2021 Request for Applications.
Additional information is also available via Grants.gov and on the NIFA FSOP webpage.
You can read more about analyzing FSOP awards through an equity lens here.
You can also learn more about FSOP through the National Sustainable Agriculture Coalition’s Grassroots Guide to the Farm Bill.
VIDEO: Freight Farms - Greenery Tour Recording
Read about our training options and support. Take a deep dive on LED lights for growing plants. Learn more farmhand’s capabilities
Below we've included the entire recording along with additional resources to help jump start your farming project.
If you have any unanswered questions or would like to discuss your individual project, please reach out to your Account Executive rick@freightfarms.com, and they will be able to assist you
Greenery Tour Recording
Have a second to share your thoughts?
We'd love to hear your feedback on how you think the event went!
Use the button below to complete a brief survey.
Survey
Additional Resources Provided During the Event:
Read about our training options and support.
Take a deep dive on LED lights for growing plants.
Learn more farmhand’s capabilities.
Get more ideas and guidance about how to find customers here.
Learn more about the nutrients used to grow strong plants inside the Greenery.
Freight Farms, 46 Plympton St, Boston, MA 02118, US, 877-687-4326