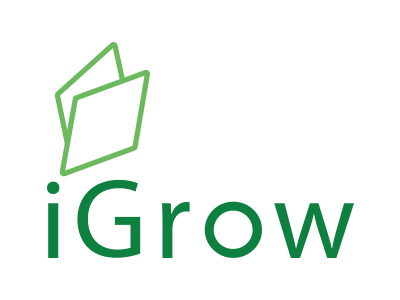
Welcome to iGrow News, Your Source for the World of Indoor Vertical Farming
Luci Faas Recognized For Her Industry Efforts As Women In Produce Honoree
The Canadian Produce Marketing Association, in partnership with Grocery Business Magazine, has developed the Women in Produce initiative to recognize the achievements of outstanding women in the produce industry
Leamington, ON (April 9th, 2021) – Nature Fresh Farms’ very own Product Development Specialist, Luci Faas, has been recognized for her excellence in the produce industry.
The Canadian Produce Marketing Association, in partnership with Grocery Business Magazine, has developed the Women in Produce initiative to recognize the achievements of outstanding women in the produce industry. Luci Faas, along with nine other women, were nominated by industry peers for their contributions to promoting produce in the industry. The ten honorees will be recognized during CPMA’s Fresh Summit virtual event on April 13th.
Last year Nature Fresh Farms launched their Compostable Cucumber wrap with Luci leading its development. The concept of a home Compostable Cucumber wrap was very new, with the initial investigation solely beginning with online research and making phone calls. After two years of trial and development, they were able to develop a film made from a starch-based material with a printed PLU in compostable ink and launched the product on the North American market.
“I have always been passionate about sustainable packaging and I am very honored by the nomination. However, I want to acknowledge the various others who worked on this film and their patience in making this innovative idea into a reality for us,” shared Luci. “I believe this will pave the way for more sustainable packaging options to grace the shelves of grocery stores across the continent.”
Luci Faas joined Nature Fresh Farms three years ago as Purchasing & Product Development, now as Product Development Specialist, Luci is responsible for sourcing innovative Nature Fresh Farms packaging and understanding its viability by initiating and monitoring shelf-life testing. She is on top of the latest industry developments in sustainable packaging and ensures all new packaging meets recognized criteria, in addition to maintaining memberships with industry associations including Sustainable Packaging Coalition and How2Recycle. Her dedication to the vigorous research, development, and implementation of industry-leading sustainable packaging solutions has been a great service for both the produce industry and the environment.
“We are extremely fortunate to have Luci’s passion, knowledge, and expertise behind our packaging development, which is why when the call for nominations came out for the Women in Produce initiative, we knew she deserved the recognition,” shared Vice President John Ketler. “We have a lot of strong women working at Nature Fresh Farms, and we feel that it is important to increase the profiles of women in this industry to engage and create awareness.”
Women play a critical role in the daily operations of farming and the agriculture industry, which is why it is important to continually support their advancement, leadership, and the diverse perspectives they bring to the industry. Nature Fresh Farms would like to acknowledge all the incredible women in the agriculture industry and congratulate the Women in Produce nominees for their accomplishments.
-30-
About Nature Fresh Farms -
Continuously expanding, Nature Fresh Farms has become one of the largest independent, vertically integrated greenhouse vegetable farms in North America. As a year-round grower with farms in Leamington, ON, Delta, OH, and Mexico, Nature Fresh Farms prides itself on consistently delivering exceptional flavor and quality to key retailers throughout North America, while continuing to innovate and introduce more viable and sustainable growing and packaging solutions.
SOURCE: Nature Fresh Farms | info@naturefresh.ca T: 519 326 1111 | www.naturefresh.ca
April Indoor Ag Science Cafe - April 20th Tuesday 10:00 AM Eastern Daylight Time
Indoor Ag Science Cafe is an open discussion forum, planned and organized by OptimIA project team supported by USDA SCRI grants
April Indoor Ag Science Cafe
April 20th Tuesday 10:00 AM Eastern
Please Sign Up!
"Plant Factories and Indoor Farming
Innovations in Japan"
AppHarvest Acquires Agricultural Robotics And Artificial Intelligence Company Root AI To Increase Efficiency
Acquisition of Root AI and its signature robot, Virgo, bolsters the company’s intelligent tools to produce foods sustainably. Root AI CEO Joins AppHarvest as Chief Technology Officer
Acquisition of Root AI and its signature robot, Virgo, bolsters the company’s intelligent tools to produce foods sustainably. Root AI CEO Joins AppHarvest as Chief Technology Officer
MOREHEAD, Ky., April 08, 2021 (GLOBE NEWSWIRE) -- AppHarvest, Inc. (NASDAQ: APPH, APPHW), a leading AgTech company and Certified B Corp focused on farming more sustainably using 90 percent less water than open-field agriculture and only recycled rainwater, announced today that it has acquired Root AI, an artificial intelligence farming startup that creates intelligent robots to help manage high-tech indoor farms. The acquisition of Root AI and its robotic universal harvester, Virgo, is expected to provide AppHarvest with a baseline of harvesting support working alongside crop care specialists focused on more complex tasks. AppHarvest expects the game-changing advantage of the technology to be in the data the robots can collect as they harvest, which can help evaluate crop health, precisely predict yield and optimize overall operations of the controlled environment agriculture (CEA) facility.
“Farming as we’ve known it is broken because of the increasing number of variables such as extreme weather, droughts, fire, and contamination by animals that make our food system unreliable. Indoor farming solves for many of those challenges, and the data gathered can exponentially deliver more insights that help us predict and control crop quality and yield,” said AppHarvest Founder & CEO Jonathan Webb. “One of the key challenges in agriculture is accurately predicting yield. Many downstream decisions from work scheduling to transportation to retail planning are based on that. Any deviation between projection and actual yield can result in fire drills for numerous functions to adjust for the change, and AI can help solve for that.”
Root AI co-founder and CEO Josh Lessing will take on the role of Chief Technology Officer for AppHarvest where he will take the lead in continuing to develop the robots and their AI capabilities for the network of indoor farms that AppHarvest is building. Lessing, along with co-founder Ryan Knopf who will join AppHarvest as vice president of technology, helped establish Root AI as an early leader in employing artificial intelligence in CEA. Virgo is the world’s first universal harvester, which can be configured to identify and harvest multiple crops of varying sizes including tomatoes, peppers, cucumbers and more delicate fruits such as strawberries among others.
Though Virgo can work indoors or out, the robot’s focus has been on controlled environment agriculture. Over the past three years, it has collected the world’s largest data set of tomato images to enable it to identify more than 50 varieties in multiple growing environments and at varying stages of maturity to learn how and when to harvest.
Virgo uses a set of cameras combined with an infrared laser to generate a 3D color scan of an area to determine the work it can perform. Once it maps the tomatoes, it assesses their orientation and determines if they are ripe enough to pick. The robot can be programmed to make other quality assessments as well. The scan enables the robot to find the least obstructive and fastest route to pick the crop ahead of the arrival of the robotic arm and gripper. The robot can identify hundreds of tomatoes in a fraction of a second without having to connect to the cloud. Virgo keeps score on its success rate like a video game. A built-in feedback mechanism constantly evaluates its efficiency so it learns how to harvest any given configuration of fruit most effectively.
“A piece of food—whether that’s a tomato or a berry or a cucumber—is an outcome from many variables that are part of the growing process. Enhanced data collection for each plant through the robot can lead to insights that teach us precisely how to design better, more resilient food systems that are reliable and that produce more food with fewer resources,“ said Lessing. “Joining forces with AppHarvest is a natural fit: we want to ensure a stable, safe supply of the nutritious and healthy food that people should be eating -- grown sustainably -- and doing that at the scale of AppHarvest gives us the opportunity to make the greatest difference.”
Gathering more data through AI enables growers to use real-time information to improve a number of sustainability efforts such as detecting and eliminating pests naturally, helping indoor farms successfully grow chemical pesticide-free fruits and vegetables.
AppHarvest is investing approximately $60 million, consisting of approximately $10 million in cash and the balance in AppHarvest common shares, to acquire Root AI. The Company will issue approximately 2,328,000 shares for the transaction.
Founded in 2018, Root AI is based in Somerville, Mass., and has 19 full-time employees, all of whom are expected to join AppHarvest’s technology group to help advance the mission of building a resilient and sustainable food supply.
About AppHarvest
AppHarvest is an applied technology company building some of the world’s largest high-tech indoor farms in Appalachia that grow non-GMO, chemical pesticide-free produce using 90 percent less water than open-field agriculture and only recycled rainwater while producing yields up to 30 times that of traditional agriculture on the same amount of land with zero agricultural runoff. The Company combines conventional agricultural techniques with cutting-edge technology and is addressing key issues including improving access for all to nutritious food, farming more sustainably, building a domestic food supply, and increasing investment in Appalachia. The Company’s 60-acre Morehead, Ky. facility is among the largest indoor farms in the U.S.
For more information, visit https://www.appharvest.com/.
How Square Roots Is Meeting Unprecedented Post-Pandemic Demand For Fresh, Healthy, Locally-Grown Food
Square Roots is expanding fast—deploying its latest indoor farm in Michigan in just three months
Square Roots Is Expanding Fast—Deploying Its Latest
Indoor Farm In Michigan In just Three Months.
To meet rapidly increasing demand for our locally-grown produce, today we’re announcing our newest indoor farm in Grand Rapids, Michigan. We broke ground in late December and planted the first seeds in March—just three months later. Now we're preparing for the first harvest, and our delicious, fresh produce will be available at grocery stores, eCommerce platforms, and restaurants across the Great Lakes region in the coming weeks.
Kimbal Musk, our Co-founder and Executive Chairman, says: “COVID-19 exposed major weaknesses in the industrial food supply chain, and accelerated the already fast-growing local farming movement. Square Roots can now deploy commercial-scale, controlled-climate farms, fast, in locations across America to meet the demand for local food, all year round. My wider mission is to bring responsibly-grown, local food to everyone in America. With Square Roots, we’re going to do it fast.”
From shovels-in-the-ground to first-seeds-planted, we built our new farm in just three months.
Growing Reliable, Fresh Produce Throughout the COVID-19 Pandemic
While COVID-19 wreaked havoc across the industrial food system, consumers increasingly valued local food, which in turn accelerated the adoption of indoor-grown produce. Consumers, forced to stay at home and cook, were able to experience the consistent peak-season flavor of our locally-grown greens. Meanwhile, retailers appreciated the reliability, longer shelf life, and complete traceability of all Square Roots’ products. As a result, we’ve seen a big increase in retail demand this year, and we’re now available in more than 200 stores (including Fresh Thyme Market, D&W Fresh Market, Whole Foods Market, FreshDirect, and more!).
In parallel, working hand-in-hand with our strategic partner Gordon Food Service—one of the largest food distributors in North America—we've been supporting and supplying restaurants throughout the pandemic. We’re as excited as anyone to see diners begin to venture out once more, and the restaurant industry bounce back strong.
Square Roots' new Michigan farm
This new farm in Michigan, our third commercial facility, is co-located with Gordon Food Service and represents another step towards a larger shared ambition to build indoor farms together across the continent—enabling local food at a national scale.
Our produce can be found at more than 200 stores across the Midwest and New York City area.
Square Roots’ Modular Farm-Tech Platform
Central to our ability to move fast and meet demand is our modular farm-tech platform. Capital-efficient and pre-fabricated inside upcycled shipping containers, ready-to-go farms can be shipped and deployed just-in-time to any site in the world, immediately creating the perfect conditions for growing the highest quality food, regardless of local climate conditions or time of year. The overall growing capacity of any Square Roots farm can seamlessly scale up or down depending on demand in the local market.
Our new two-story farm in Michigan also includes all of the necessary infrastructures to run a state-of-the-art, food-safe, and people-safe commercial operation. This includes cold storage, biosecurity, climate-controlled packaging space, distributor loading docks, and more. Meanwhile, all of our farms are Harmonized Good Agricultural Practices (GAP) certified, in line with the USDA’s standards, and operate to strict COVID-19 safety protocols to keep farmers and the local community safe.
Our farms are also cloud-connected and managed by a combination of skilled Square Roots farmers and sophisticated in-house software. Known as The Square Roots Farmer Toolbelt, our proprietary OS provides day-to-day guidance to farmers while capturing millions of data points throughout growing cycles across our network. This data can then be analyzed to determine how changes in certain environmental parameters impact factors like yield, taste, and texture. Our system learns faster as we deploy more farms and our network gets larger, all while helping farmers determine how to grow more, better-tasting food with fewer resources. Training new farmers—and empowering the next generation of leaders in indoor agriculture—has always been core to our mission, and the Farmer Toolbelt is a key enabler in our ability to offer accessible pathways for young people to enter the high-tech farming industry.
Farmers are guided through day-to-day operations by The Square Roots Farmer Toolbelt.
Responsibly-Grown, Local Food, Available Everywhere
We’ve always designed our farms to provide responsibly-grown food in areas close to the end consumer. Our hydroponic system uses 95% less water than conventional agriculture, our farms require zero pesticides, and the location of our facilities cuts down dramatically on food miles and food waste by enabling delivery of fresh produce within 24 hours of harvest, all year round. Meanwhile, our latest farm design is easily configured for both vertical and horizontal-stacked growing formats—a new and unique capability that means we can grow a wide range of crops to meet a variety of local market needs. To date, we've grown over 200 different varieties of herbs, microgreens, leafy greens, fruits, and even root vegetables—and we’re just getting started!
Keep an eye on this blog for announcements about more new farms soon. For more information about Square Roots check out our website, squarerootsgrow.com. And for daily updates, follow us on social media @squarerootsgrow.
Oishii Sees Itself As ‘The Tesla of Vertical Farming.’ Here’s How It’s Cracking CEA Strawberries
“Strawberries are the hardest crop to grow in a vertical system and it’s been every vertical farmer’s dream to grow them. Conquering strawberries allows us to grow into other crops very quickly.”
March 31, 2021
Indoor farming is best known for leafy greens and micro-herbs. But New York’s Oishii is hoping to blaze a new trail and sweeten up the segment.
“A lot of people call strawberries the holy grail of vertical farming,” Oishii founder Hiroki Koga tells AFN. “Strawberries are the hardest crop to grow in a vertical system and it’s been every vertical farmer’s dream to grow them. Conquering strawberries allows us to grow into other crops very quickly.”
The startup announced a $50 million funding round this month led by Mirai Creation Fund, part of Tokyo-based SPARX Group. Additional investors included Sony Innovation Fund — the corporate venture arm of Japanese tech giant Sony — Tokyo-based AI company PKSHA Technology, and San Francisco-based VC Social Starts.
“We’ve had multiple offers from different funds but we ultimately decided to go with SPARX because they have a very strategically aligned mandate. They’re backed by Toyota, one of the largest manufacturing companies in the world [and] vertical farming is the intersection of agriculture and manufacturing,” Koga says.
Although it may seem odd for Toyota to be interested in agrifood tech, the carmaker is working on its Woven City project located at the base of Japan’s Mount Fuji. It’s a so-called “living laboratory” where researchers live and work full-time to imagine what future cities may look like through technological innovation.
Koga is no stranger to controlled environment ag (CEA). Six years ago, he was working as a CEA consultant in Japan, helping large corporations enter the space. While Koga views Japan as the birthplace of vertical farming, he moved to the US in 2015 – around the time that the method was becoming popular in the country.
Alongside the allure of being the first to crack indoor strawberry cultivation, Koga sees the fruit as a way to address what he calls the “unit economics problem” in indoor farming. He sees strawberries as providing a very strong revenue and profit model, as well as a crop that can further “democratize” vertical farming.
“In order to democratize it, I wanted to start with something that’s truly impactful — not products that people will buy because they are sustainable — [but] something that is superior compared to what is on the market, and that would completely change people’s experience,” Koga says.
He leveraged his personal network in Japan to collaborate with farmers and research institutions on the details of indoor strawberry cultivation – from seeding all the way to harvesting. It took “countless” iterations to get the formula right, he says.
“There’s probably 20 or 30 different things that you can tweak in a given cycle of the plant. So, let’s say there are five or six different stages of the plant life cycle – if you multiply all of those, there are millions of different combinations,” he explains.
“It’s a matter of tweaking those on a daily basis to figure out what the perfect mix is.”
However, this know-how isn’t what Koga considers to be Oishii’s “secret sauce.” Rather, that’s the bees that the startup’s using handle pollination.
While Koga won’t spill the ‘bees’ about how all this works in Oishii’s context, he claims to have found a way to replicate a natural environment within an indoor vertical farm that convinces the critters they’re outside.
“They live in harmony with our farmers and robots,” is all Koga will add.
The Tesla of vertical farming
With the initial R&D under its belt, Oishii is now turning its focus to consistency and quality of the product. Its current New Jersey facility spans a few tennis courts, Koga says; but its next one will be the size of an American football field. It currently sells direct-to-consumer through its website, and through traditional retail channels like supermarkets.
But its strawberries may be out of some consumers’ grocery budgets, retailing between $15 and $50 per pack depending on the size and the number of fruits. This price point puts Oishii’s berries in the luxury food category – for now, at least.
“If you think about how Tesla started with a Roadster or Nissan started with the LEAF, we like to think we are in the Roadster camp,” Koga says.
“Our current Omakase berry is our Roadster right now, but we already have developed multiple strawberry cultivars that we can produce much more cost-efficiently. Our Model S and Model 3 will be on the market soon,” he says, referring to the latter-day models now being sold by Elon Musk’s company.
Another US vertical farming startup, Plenty, is also trying to solve the strawberry equation. It recently added Driscoll’s to its list of backers and is collaborating with the major berry producer on indoor strawberry cultivation.
Koga welcomes competition in the space, particularly if it means branching beyond leafy greens.
“It’s generally a good thing that people are following in our footsteps and expanding out of the leafy green space. The more berries the better,” he says.
“Ten years ago, we only had Tesla, maybe a few other companies. But Tesla was the one who proved that it can be done, and now there are dozens and dozens of electric car manufacturers. [The electric car] become much more widely available.”
Continuing Education: Urban Agriculture
It’s been 10,000 years since the agricultural revolution gave rise to cities. Agriculture now covers more than half of the world’s habitable land and is spreading at a rate of about 15 million acres annually
April 1, 2021
It’s been 10,000 years since the agricultural revolution gave rise to cities. Agriculture now covers more than half of the world’s habitable land and is spreading at a rate of about 15 million acres annually. Cities, meanwhile, now comprise more than half the global population (over 80 percent in developed countries), and the numbers are rising. Using current farming methods to feed a global population expected to hit 10 billion by midcentury would require adding new farmland equal in size to the continental United States.
This alarming situation is not even factoring in the impact of the climate crisis, which is expected to alter growing seasons and disrupt the phenological cycles that keep plants and their pollinators in sync. What’s more, new agricultural land mostly comes from felling biodiverse, carbon-sequestering forests to make room for mono-crops that stash very few greenhouse gases and for livestock that actually generate them. That makes the climate crisis worse and farming more difficult.
READ MORE ABOUT
In addition to land consumption, agriculture guzzles three-quarters of the fresh water used globally each year, while runoff from fields treated with herbicides, pesticides, and fertilizers contaminates significant amounts of the water that’s left. Then there’s transportation. As farms extend farther and farther from the cities they supply, food is trucked, shipped, and flown vast distances: farm to plate, the ingredients in a typical American meal travel an average of 1,500 miles. From a security perspective, the fact that most of the world’s food production is controlled by just a handful of corporations is unnerving. And from a public health perspective, the emergence of Covid-19 and other new diseases offers yet another indicator of ecological imbalance. It’s time to rethink the way we farm.
Food security, as defined by the United Nations, means that all people, at all times, have physical, social, and economic access to sufficient, safe, and nutritious food that serves their food preferences and dietary needs for an active and healthy life. Key to achieving food security in a way that’s more sustainable than current practices is urban agriculture—not as an outright replacement for rural farming, but as a crucial component in a balanced system.
Urban agriculture can take many forms: rooftop greenhouses, raised beds, and community-farming initiatives such as the City of Atlanta’s “Aglanta” program, which turns underused parcels in utility rights-of-way into farm plots eligible for U.S. Department of Agriculture certificates and associated loans. Ultimately, though, horizontal strategies are not productive enough to make a real dent in the food needs of a city. (If raised beds covered every rooftop in Manhattan, the produce grown would feed only about 2 percent of the borough’s population.) Just as cities grow vertically, so too must urban agriculture, and that means bringing it indoors.
“Controlled environments have been used for many years,” says Chieri Kubota, a professor of controlled environment agriculture (CEA) in the Department of Horticulture and Crop Science at Ohio State University. “Now that multiple issues are making conventional production outdoors more difficult, putting controlled environments in and near cities brings food production closer to potential markets—and also to younger generations of potential farmers who want to live in urban centers.”
Vertical agriculture is a type of CEA that—like high-rise buildings—stacks layers to provide usable area many times the footprint of the site. Instead of growing in soil, which is a heavy way to deliver nutrients, plants in vertical farms are grown hydroponically, aquaponically, or aeroponically. In hydroponics, plants are cultivated in nutrient-enriched water, which is captured and reused so that the system uses as little as a tenth of the water conventional agriculture needs. An aquaponic system pairs hydroponics with fish production, circulating the nutrients in the fish waste to feed the vegetables, and using the plants as a biofiltration system that returns clean water to the fish. Reducing water consumption even further—by as much as 98 percent, compared to field growing—aeroponic systems deliver nutrients in a fine mist to plant roots that are just hanging in the air. And because controlled environments exclude the weeds and pests that trouble field-grown produce, the use of herbicides and pesticides is all but eliminated.
Stacked plants may need to be rotated to make the most of available sunlight, which can be supplemented (or even substituted altogether) with LED grow lights. These can be calibrated to provide blue and red light in optimal doses for each type of plant, and timed to increase plant growth with extended days and growing seasons. (While it’s technically possible to grow any type of crop this way, for now it’s mainly leafy greens and tomatoes that are economically viable.) Cool enough to be strung right in among the plants without burning them, LEDs reduce site electricity consumption (and costs) per square foot of grow area by about a third compared to older technologies, such as high-pressure sodium. “Energy is a game-changer,” says Dickson Despommier, an emeritus professor of microbiology and public health at Columbia University, whose seminal 2010 book, The Vertical Farm: Feeding the World in the 21st Century, is widely credited with kick-starting vertical agriculture in North America. Cost-effective LED lighting opens up the possibility of converting urban and urban-adjacent building types such as parking garages, big-box stores, and shopping malls into productive local farms, he says.
With productivity rates that are orders of magnitude greater than conventional farming, high-rise growing is gaining traction worldwide. The world’s first such system began operations in 2012 in Singapore. The land-strapped city-state, which imports about 90 percent of its food, aims to grow a third of its produce locally by 2030. Indoor vertical farms in the country now produce about 80 tons of greens a year, and the Singapore Food Agency is supporting research into and development of the method as its main bet on the future.
In China, great swaths of arable land have been lost to development (more than 30 million acres between 1997 and 2008) and 20 percent of what’s left is contaminated. At the same time, the country has a strong tradition of urban-adjacent farming. When a 247-acre agricultural site, midway between Shanghai’s main international airport and the megacity’s center, recently came up for redevelopment, global design firm Sasaki proposed that, rather than create yet another tech park, the client take its agricultural mission to the next level. As a result, the Sunqiao Urban Agricultural District is slated to become one of China’s first comprehensive national agricultural zones. Sasaki’s master plan, which has received approval from the Pudong District and is now proceeding for formal approval from the City of Shanghai, expands the district’s role in Shanghai’s food network, integrating vertical agricultural production, research, and education into a dynamic public domain. In addition to research and development facilities and an agriculture production zone, the plan provides for a civic plaza showcasing productive landscapes, a science museum, an interactive greenhouse, an aquaponics display, and a destination market. “It’s urban agriculture on steroids,” says Michael Grove, chair of landscape architecture, civil engineering, and ecology at Sasaki.
The Sunqiao project will include a civic plaza with productive landscapes (top), a science museum, and an interactive greenhouse (above), among other elements. Image courtesy Sasaki, click to enlarge.
Grove identifies three primary drivers for prioritizing urban agriculture globally: the need to curtail agricultural sprawl and thereby protect ecosystems, to reclaim economic agency by diversifying control of food production, and to build community: “Food brings us together,” he says. Behind Asia’s early adoption of urban agriculture, he sees a historic understanding among the region’s societies that the well-being of the population requires systemic support. That may also be a factor in Europe, where the Netherlands is a global leader in controlled-environment technology, and Denmark is home to the world’s latest and largest vertical farm, a partnership between a Taiwanese CEA tech company and a local start-up: with growing shelves stacked 14 deep, the 75,000-square-foot wind-powered facility has the capacity to produce 1,000 metric tons of greens a year.
A hub for teaching, research, and community engagement, located within sight of downtown Columbus and designed by Erdy McHenry Architecture, supports Ohio State’s CEA efforts. Brad Feinknopf
North America has been slower to adopt vertical farming, a lag that Ohio State’s Kubota attributes in large part to the year-round, nationwide availability of produce from California, Arizona, and Florida. But now, she says, climate disruptions and shortages of viable farmland in those states, along with the increasing urbanization of the workforce, strengthen the rationale for controlled environment agriculture. To support Ohio State University’s multidisciplinary research into CEA, a one-acre vertical greenhouse is under construction within sight of downtown Columbus. As part of the facility, the recently completed Kunz-Brundige Franklin County Extension Office serves as a hub for teaching, research, and community engagement around food, health, agricultural production, and sustainability. Both buildings are designed by Philadelphia-based Erdy McHenry Architecture.
Although still tiny, vertical farming is the fastest-growing sector in U.S. agriculture. A projected compound annual growth rate (CAGR) of more than 20 percent from 2020 to 2026 is expected to bring sales to around $10 billion a year. And while significant numbers of start-ups in the capital-intensive sector have failed—as indicated by the track record of several initiatives profiled in this magazine eight years ago —experts say that’s an inevitable aspect of an emerging technology.
Among the growing number of enterprises going strong, however, is Vertical Harvest, the first vertical hydroponic greenhouse in North America. Cofounded by architect Nona Yehia, principal at GYDE Architects, the company began operations in 2016 in Jackson Hole, Wyoming. Jackson is a rural town, but it performs like a city in relevant ways: 97 percent of its developable land is already in use, and, with a four-month growing season, 98 percent of its food is imported. Inspired by Despommier’s work, the need for a local food supply, and the opportunity to provide meaningful work for community members with intellectual and physical challenges, Yehia designed a three-story greenhouse for a 30-by-100-foot municipally owned lot next to a parking garage. “The town councilor who showed us the property thought we’d put up a plastic hoop structure to extend the growing season a couple of months, employ a few people, and call it a day,” recalls Yehia. But she and her business partners wanted to grow as much food as possible, to employ as many people as possible, and to do both year-round. “That’s where the idea to grow up came from,” she says.
Vertical Harvest’s three-story CEA facility in Jackson Hole, Wyoming, produces as much food on a tenth of an acre as on a 10-acre conventional farm. Photos © Vertical Harvest (1), Hannah Hardaway (2 & 3)
With a footprint of a tenth of an acre, the greenhouse produces as much food as would a 10-acre conventional farm. It employs 30 people, more than half of whom have a disability. And it’s profitable. “It would have been easier as a nonprofit,” Yehia says, “but we were committed to creating a replicable model that is not about charity: it’s about empowerment.”
After five years of operation, Vertical Harvest is ready to expand. Construction is scheduled to start this year on a second location that incorporates affordable housing and municipal parking in Westbrooke, Maine. The new 70,000-square-foot greenhouse is expected to provide the equivalent of 50 full-time jobs and to produce 1.3 million pounds of produce a year, supplying hospitals, corporate cafeterias, schools, chefs, restaurants, and caterers, as well as individual customers. “These ecosystems can put out a lot of food,” says Yehia. “Making sure you have customers who can buy at scale is as essential to success as growing plans.”
Vertical Harvest intends to build up to 15 farms in the next five years, with agreements already in place for projects in Philadelphia and Harrisburg, Pennsylvania, and Chicago, and discussion is underway for five other locations. Like the Wyoming and Maine projects, they will integrate social value and community engagement with their agricultural mission. “It’s the perfect intersection to show what architecture can achieve in its social role in our communities,” Yehia says. And while she has run Vertical Harvest as designer, entrepreneur, and urban farmer, it’s entirely possible for architects to advocate for urban agriculture in their more usual role as prime consultants, coordinating the work of other experts.
As CEA picks up speed, the time may not be far off when every municipality will incorporate vertical farming into its civic infrastructure, valued the way public libraries and recreation centers are. “It should be something that we all expect to see when we go to cities,” Yehia says: “infrastructure that grows food and futures, and bolsters the sustainability of the community.”
Continuing Education
To earn one AIA learning unit (LU), including one hour of health, safety, and welfare (HSW) credit, read the article above and watch this video.
Then complete the quiz. Upon passing the test, you will receive a certificate of completion, and your credit will be automatically reported to the AIA. Additional information regarding credit-reporting and continuing-education requirements can be found at continuingeducation.bnpmedia.com
Learning Objectives
Explain how conventional agricultural methods contribute to climate change.
Define terms such as urban agriculture, controlled environment agriculture (CEA), and vertical agriculture.
Describe technologies relevant to CEA, such as hydroponics, aeroponics, and aquaponics.
Discuss how CEA can enhance food security and bring social value to underserved communities.
AIA/CES Course #K2104A
Lead photo: Sunqiao Urban Agricultural District has been designed by Sasaki for a site midway between Shanghai’s city center. Image courtesy Sasaki
KEYWORDS cities / climate change / urban planning
Join Our Next Conversation - April 28, 2021 | 2:00 to 3:00 pm EDT
Join us for a fun “Fireside Chat” as Indoor Ag-Con’s Content Chair Jim Pantaleo sits down with Dan to discuss this great success story
In 2010, Dan Albert began laying the groundwork for what would become Farmbox Greens, a Seattle-based vertical farm growing specialty produce for retail and foodservice customers.
In 2016, Farmbox was acquired by a regional produce company and Dan went on to scale Farmbox to serve customers in the Northwest and beyond.
Join us for a fun “Fireside Chat” as Indoor Ag-Con’s Content Chair Jim Pantaleo sits down with Dan to discuss this great success story—from the farm’s early days to those first meetings with potential restaurant customers to making the connection with Charlie’s Produce.
Jim and Dan will also talk about Dan’s newest role as Vice President of Plant Performance with Unfold.
LEARN MORE & SAVE YOUR FREE SPOT!
Spread Acquires JAS 0012 – World’s First Certification For Vertical Farms Responding To The Global Demand For Food Safety
Spread is able to contribute to global food safety and the delivery of health-associated SDGs by lowering food poisoning risk via its thorough hygiene and cultivation management practices
April 7, 2021
Kyoto, Japan. --Spread Co., Ltd. (HQ: Kyoto, Japan; CEO: Shinji Inada, hereinafter “Spread”)has acquired “JAS 0012” certification, established by the Japanese Ministry of Agriculture, Forestry and Fisheries (hereinafter “MAFF”) for evaluating hygiene and cultivation management of a vertical farm, at its Kameoka Plant (Kameoka, Kyoto), a pioneer in reaching profitability at large-scale operation, and the next generation large-scale automated Techno Farm Keihanna (Kizugawa, Kyoto) which delivers a stable operating rate of 99%. JAS 0012 is the first certification in the world to be focused exclusively on vertical farms.
Spread is able to contribute to global food safety and the delivery of health-associated SDGs by lowering food poisoning risk via its thorough hygiene and cultivation management practices. Domestically Spread is able to reassure customers of the quality and safety of vertically farmed produce and in doing so, establishes a high bar for food safety in the industry.
GLOBAL DEMAND FOR FOOD SAFETY
Fresh produce-related food poisoning is a common problem for food security. In particular, E. coli is often linked to leafy greens and outdoor-grown romaine lettuce, outbreaks have a relatively high rate of hospitalization, and are becoming more frequent. In the last decade there have been 40 leafy-greens-related outbreaks in North America, resulting in 420 hospitalizations and 8 deaths *1, *2, *3. Many view vertical farming as a solution, but not all vertical farmers operate at the same hygienic level. Even Japan considered a well-established market with more than 200 vertical farms in operation *4, had no unified standard for the industry, until MAFF established JAS 0012 to certify superior operators in 2019. Nikkei estimates that only 10-20% of Japanese vertical farmers are able to satisfy the standard *5.
SPREAD’S WAY
Spread has set its own hygiene management system since the Kameoka Plant went into operation in 2007. As first customers in Japan were reluctant to accept vertically farmed produce, Spread engaged into online and in-store educational events and helped to create a vertical farming market. With its Vegetus brand, Spread has sold over 70 million packs up until now and is present at more than 3,600 stores all over the country. Spread’s high-level hygiene and cultivation management standards have been acknowledged by the recent successful acquisition of JAS 0012. Before that, Spread’s efforts towards securing its workers’ safety, environmental sustainability, and traceability were granted “GLOBALG.A.P.” certification. With these accomplishments, Spread is ready to respond to the growing demand for safe, high-quality fresh produce.
WHAT CERTIFIES JAS 0012?
・ High-level safety management to satisfy MAFF’s standards
・ Ability to consistently grow and supply high-quality vegetables over a long term
・ Flexibility needed to respond to diversified needs of the foodservice industry
SPREAD’S HYGIENE MANAGEMENT
Air-floating bacteria monitoring
Spread inspects and regulates not only the number of bacteria in nutrient solution but also in the air to prevent contamination risk
WHAT’S JAS/JAS 0012?
JAS (Japanese Agricultural Standards) are the Japanese national standards in the field of agricultural, forestry, fisheries, and food industry, established by the MAFF. In addition to General JAS and Organic JAS, there is also Specific JAS, applied to high value-added or distinctive products. JAS 0012 is classified as Specific JAS and was established in 2019 to evaluate the hygiene and cultivation management of leafy greens in a vertical farm with artificial lighting.
Stores with Spread's production available
3,600 - October 2020
2,000 - January 2015
Transition - 2,500 January 2019
Anti-contamination measures
Employees are required to wear sanitary clothing and all products are inspected multiple times before shipping
*1 Deane Falcone “E. Coli on the Rise: Lettuce Explain” Food Safety Tech, March 10, 2021
*2 “Estimates of Foodborne Illness in the United States” CDC
*3 Sara G. Miller “Leafy greens were linked to 40 E. coli outbreaks in a decade. Most involved romaine.” NBC News, September 16, 2020
*4 Michael Dent “Vertical Farming: 2020-2030. Technologies, markets, and forecasts in indoor vertical growing” IdTechEx
*5 “Nosuisho, shokubutsukojo ni kikakushinsetsu kouhinnshitsu no saibai atooshi” [MAFF establishes new standard for vertical farm, backs high-quality cultivation] Nikkei, August 4, 2020
ABOUT SPREAD
Kameoka Plant, the Profitability Pioneer of Vertical Farming Capacity:21,000 heads/2.1t/day
Spread’s Kameoka Plant cracked one of the toughest challenges in commercial vertical farming. Since starting operations in 2007, Spread has developed sophisticated environmental control technologies, and significantly improved the overall operational efficiency at the Kameoka Plant. Together this has brought the operating rate to 97% and enabled Kameoka Plant to become profitable for the first time in 2013.
Techno Farm Keihanna. Stable Production via Innovative Technologies Capacity: 30,000 heads/3t/day
Started operations in 2018. The first vertical farm to utilize next-generation food production system Techno FarmTM. At the R&D facility attached to the farm, development of the new cultivation techniques, as well as IoT and AI systems is underway. As the mother plant of Techno FarmTM,
Techno Farm Keihanna will serve as the foundation for the never-ending evolution of new technologies.
Innovative technologies, allowing for a simultaneous increase in productivity and environmental sustainability:
・ Automated cultivation
・ Saving over 16,000 liters of water per day via water recycling
・ Advanced environmental control
・ Energy saving due to LED lighting, tailored for vertical farming usage
・ Upgrade in operational efficiency due to IoT-based management system
Next Generation Food Production System Techno FarmTM Developed by Spread with the help of partner companies, Techno FarmTM builds on the know-how developed at the Kameoka Plant in more than 10 years of its operation. Automated cultivation, water recycling, and environmental control
technologies specialized LED lighting as well as IoT and AI make for a simultaneous increase in productivity and environmental sustainability.
Spread will continue to promote this technology as an essential part of sustainable agriculture.
Over 70 Million Packs Sold in Total
*1. Vertically Farmed Vegetables Brand Vegetus
Under the concept of “Sustainable Vegetable”, Vegetus strives to be healthy for both Earth and people. Spread’s current lineup includes 3 unique varieties: crunchy Frilly Lettuce, smooth and sweet Pleated Lettuce, soft yet crispy Fringe Lettuce. Each of these delivers a clean and fresh taste and is rich in beta-carotene.
*2 Vegetus is a favorite of children, easy to prepare, and fits into any meal, not only salads or sandwiches.
URL:www.vege-tus.com (Japanese only)
Contribution to the United Nations’ Sustainable Development Goals
Spread’s contribution Promotion of sustainable food production Preventing food poisoning risk via hygiene and cultivation management practices Labor-saving through automation and digital transformation IoT-based management system for efficient cultivation Helping to reduce food loss due to most part of lettuce being edible Promoting resilient agriculture Efficient usage of land resources and pesticide-free cultivation Techno FarmTM partnership business
*1 Actual numbers of lettuce, produced and sold by Spread
*2 Vegetus clears Japanese Ministry of Health, Labor and Welfare standards for the “beta-carotene rich” vegetables (equal or more than 600μg/100g)
[Contact information]
Spread Co., Ltd. Corporate Communication Department
E-mail : info@spread.co.jp
URL : www.spread.co.jp/en
Bolivian Deforestation
Deforestation in the country has primarily been driven by the expansion of mechanized agriculture and cattle ranching.
April 9, 2021
Deforestation of The Rainforest Is Visible In Santa Cruz, Bolivia.
Deforestation in the country has primarily been driven by the expansion of mechanized agriculture and cattle ranching.
This Overview highlights the country’s struggle to expand food production in order to meet the needs of its growing population, and the sacrificial destruction of its forests that has taken place to do so.
-17.387750°, -60.562131°
Source imagery: Maxar
Vertical Farming Gaining Popularity Among Traditional Growers
They see opportunities in using techniques from vertical cultivation, for example in propagation. “It is not just about improving the quality of the young plants, but above all about the controllability of the cultivation, and thus the speed and quality,” says Koen with Mechatronix
'Where in recent years vertical farming enthusiasts have perhaps been mainly qualified as hipsters with a rather expensive hobby, this new branch of horticultural sport is steadily on the rise and traditional growers are also finding their way to the multi-layer installations.'
They see opportunities in using techniques from vertical cultivation, for example in propagation. “It is not just about improving the quality of the young plants, but above all about the controllability of the cultivation, and thus the speed and quality,” says Koen with Mechatronix.
What is the most expensive greenhouse there is? That would be an empty greenhouse, and that is exactly where, according to Koen van Mechatronix, opportunities lie for vertical farming. “In lettuce cultivation you see many nurseries working with fully automated cultivation systems. With mobile gutters, they can use the available space in the greenhouse as efficiently as possible. However, it remains difficult to adjust the speed of the preliminary cultivation to the available space in the pond. By replacing traditional, unexposed or illuminated cultivation with cultivation that is more controllable in a multi-layer system, you can plan much more precisely how many plants to set up. Accurate to the day, you know how many plants are ready to go in,” he says.
The lighting company developed a multi-layer cultivation system together with Meteor Systems: an automated track, including spray booms. In the past quarter, intensive testing was already carried out with a grower who works with floating gutters. “We have 120,000 cuttings up in the test setup. Multi-layered, of course, because otherwise, it would be too expensive in terms of floor space. Now you can grow enough cuttings on a few square meters to fill 1 / 3rd of the garden,” he shows.
The controlled cultivation makes it possible to use the entire cultivation system more intensively, which shortens the payback period and the depreciation period. “You can get more heads of lettuce from your expensive greenhouse,” Koen summarizes. “In addition, you always send exactly the same quality plants to the pond, which also gives you more control over your outgrowth. If you still adhere to the correct lighting strategy, you can start making a perfect prediction on your planning. This wasn't possible before. ”
Further opportunities
In herbs there are also opportunities for hybrid cultivation, where part of the cultivation will takes in an indoor or multi-layer cultivation system and the outgrowth will take place "as usual" in the greenhouse. “In the classic, fast-growing herbs, a full indoor cultivation is soon done, but in the woody herbs it is purely the rooting that takes place in a VF installation,” says Koen. “Total cultivation is too slow for this. Your turnaround time is too long and that makes the investment per m2 too expensive, but rooting often goes perfectly in a VF system.” In the same way, plant breeders use the techniques in part of the propagation, for example, to improve healing after grafting or to speed up cultivation from mother plants. "Ultimately, propagation is about the controllability of a known phase of the propagation."
All in all, this means that there appear to be more and more surprising opportunities for vertical farming, also in Europe. “The first major projects are starting to arrive, although we also see that people here are even less familiar with the possibilities and often depict it as expensive cultivation,” says Koen. “And of course an economic assessment must always be made. It will not be the case that complete crops will be placed indoors here tomorrow - there is always a reason to look at the sun. Where possible we use the sun, and where necessary the lighting. ”
For more information:
Koen Vangorp
MechaTronix
koen@mechatronix-asia.com
www.horti-growlight.com
8 Apr 2021
Global Food Prices Rise For 10th Month In A Row
The FAO Food Price Index, which tracks monthly changes in the international prices of commonly-traded food commodities, averaged 118.5 points in March, 2.1 percent higher than in February and reaching its highest level since June 2014
Vegetable Oils Drive FAO Food Price Index
Higher In March While Cereal Quotations Dip
Packing butter in the Russian Federation.
8 April 2021, Rome - Global food commodity prices rose in March, marking their tenth consecutive monthly increase, with quotations for vegetable oils and dairy products leading the rise, the Food and Agriculture Organization of the United Nations (FAO) reported today.
The FAO Food Price Index, which tracks monthly changes in the international prices of commonly-traded food commodities, averaged 118.5 points in March, 2.1 percent higher than in February and reaching its highest level since June 2014.
Trends varied by commodity types. The March increase was led by the FAO Vegetable Oil Price Index, which rose 8.0 percent from the previous month to hit a nearly 10-year high, with soy oil prices rising sharply due in part to the prospects of firm demand from the biodiesel sector.
The FAO Dairy Price Index increased 3.9 percent from February, with butter prices buoyed by somewhat tight supplies in Europe associated with increased demand in anticipation of a food-service sector recovery. Milk powder prices also rose, supported by a surge in imports in Asia, particularly China, due to declining production in Oceania and scarce shipping container availability in Europe and North America.
The FAO Meat Price Index also rose, by 2.3 percent from February, with imports by China and a surge in internal sales in Europe ahead of the Easter holiday celebration underpinning increasing poultry and pig meat quotations. Bovine meat prices remained steady, while ovine meat prices declined as dry weather in New Zealand led to farmers offloading animals.
By contrast, the FAO Cereal Price Index dropped by 1.8 percent, but it is still 26.5 percent higher than in March 2020. Wheat export prices declined the most, reflecting generally good supplies and favorable production prospects for 2021 crops. Maize and rice prices also declined, while those for sorghum rose.
The FAO Sugar Price Index declined 4.0 percent in the month, triggered by prospects of large exports from India, but it remained more than 30 percent above its year-earlier level.
Positive cereal crop prospects in 2021
FAO expects world cereal production in 2021 to increase for the third consecutive year and has raised its preliminary global wheat production forecast on better than-earlier-anticipated crop conditions in several countries. Global wheat production is forecast to reach a new high of 785 million tonnes in 2021, up 1.4 percent from 2020, driven by a likely sharp rebound across most of Europe and expectations of a record harvest in India.
Above-average outputs are also expected for maize, with a record harvest anticipated in Brazil and a multi-year high in South Africa, according to FAO's Cereal Supply and Demand Brief, also released today.
For the current 2020/21 marketing season, global cereal utilization is now forecast at 2 777 million tonnes, 2.4 percent higher than the previous year, driven largely by higher estimates of feed use of wheat and barley in China, where the livestock sector is recovering from African swine fever.
World cereal stocks at the end of 2021 are forecast to decline by 1.7 percent from their opening levels to 808 million tonnes. Combined with the utilization forecasts, the global cereal stock-to-use ratio for 2020/21 is foreseen to dip to a seven-year low of 28.4 percent.
FAO also raised its forecast for world trade in cereals during 2020/21 to 466 million tonnes, a 5.8 percent increase from the previous year, driven by even faster trade in coarse grains linked to unprecedented levels of maize purchases by China. Also for rice, international trade is forecast to expand by 6 percent year-on-year.
The Brief offers more details and updated assessments.
The World’s First Autonomous Greenhouse Manager
Geert van der Wel started in the role of Autonomous Greenhouse Manager at Blue Radix. He represents the human support side of the Crop Controller service in addition to the smart algorithms that control greenhouses
07-04-2021 | Goedemorgen
Early February, Geert van der Wel started in the role of Autonomous Greenhouse Manager at Blue Radix. He represents the human support side of the Crop Controller service in addition to the smart algorithms that control greenhouses. Read more about how Geert helps customers and about his background. As he says himself: "I was almost literally born among tomatoes in De Lier, where my parents had a tomato greenhouse."
Name: Geert van der Wel
Home: I’ve been married to Tessa for 16 years and we have two children. We have lived in Burgundian West Brabant since 1998.
Childhood: Almost literally, I was born among the tomatoes in De Lier, where my parents had a tomato greenhouse.
Study: I completed Secondary Horticultural School in De Lier, and also undertook several (horticultural) studies.
Work experience: I worked in my parents’ tomato greenhouse right from my childhood. After finishing my studies my partner and I became owners of Kwekerij Polderwel for ten years, growing tomatoes on 2.5 hectares. We wound up this undertaking because of the construction of the A4 highway between Antwerp and Rotterdam. Then I did three years as a manager at the Nuijten plant nursery, and when this firm ceased trading I ended up at Nickerson-Zwaan in Made; it later became known as Hazera Seeds. For the first four years, I worked in the Planning & Control department, moving on to become Product Manager High-Tech Tomatoes for the final five years.
What can you do for growers as an Autonomous Greenhouse Manager?
“Blue Radix offers autonomous growing as a service. So alongside our smart algorithms controlling the greenhouse, our Crop Controller service also has a ‘human side’, and customers get daily support from an off-site Autonomous Greenhouse Manager (AGM). So as that AGM I’m constantly looking over the customer’s shoulder, and I’m their first point of contact. Right from the start, I guide clients intensively in taking their first steps into the world of algorithms. They are given an extensive onboarding program where they get explanations on the steps to autonomous growing, the operation of the algorithms, and the Crop Controller portal. I also monitor the management of the greenhouse continuously and discuss the progress on a regular basis, including through reports. My work experience has taken me through all the processes involved, from seed to the final product. This is what enables me to support our customers fully as AGM, to advise them, and to help them to realize their crop strategies.”
Blue Radix offers autonomous growing as a service; why is this important?
“Cultivation is the core business of every greenhouse company. To leave this completely to autonomous control requires a lot of trust from the customer. We are very aware that autonomous growing is still quite new and innovative. Providing good service with the support of the AGM lets us guide growers fully in working with algorithms. Our experience shows that customers are more likely to abandon their own processes and working methods step by step because there’s always someone monitoring the entire process.”
Describe your day. How do you monitor greenhouses worldwide?
“Every day I open the Crop Controller portal to see how the algorithms are behaving in terms of our various customers’ crop strategies. I contact the grower if any anomalies appear, or if there’s a technical issue I get in touch with the Blue Radix product developers. This also applies to feedback I receive from customers on how we can optimize Crop Controller still further.”
What do you like about your job? And what are your views on autonomous greenhouse management?
“In the horticultural world, it’s great to see that there’s a continuous search for innovations, and specifically for autonomous growing. I used sensors and digital tools on a small scale when I was a grower myself. But at that time I got very little guidance on how they worked and how to interpret it all. Now I use this experience to give our customers good information so that ultimately they’ll be able to grow autonomously in the best possible way!”
Got a question for Geert, or about autonomous growing generally?
Send us a message, and we’ll be happy to help you.
California-Based Greenhouse Grower To Invest $18 Million In Warner Robins, Georgia Indoor Farm
Pete’s is expected to use 24 acres within the county for its indoor growing facility that’s designed to require 90% less land and water than traditional farming
APRIL 08, 2021
Pete’s, a longtime, California-based greenhouse grower, is expected to invest $18 million in opening their first eastern U.S. indoor agriculture facility in Warner Robins in Peach County, Gov. Brian Kemp announced Thursday. COURTESY PETE'S
WARNER ROBINS
Pete’s, a longtime, California-based greenhouse grower, is expected to invest $18 million in opening their first eastern U.S. indoor agriculture facility in Warner Robins in Peach County, Gov. Brian Kemp announced Thursday.
“Agriculture is our top industry, and Pete’s will bring another game-changing, innovative, and sustainable indoor farming facility to Georgia as we continue to feed the world from the Peach State,” Kemp said in a news release. “Georgia’s No. 1 business climate, top-notch logistics network, and commitment to innovation continue to attract jobs and opportunities for hardworking Georgians, and I thank Pete’s for investing in Peach County and the surrounding region.”
Pete’s is expected to use 24 acres within the county for its indoor growing facility that’s designed to require 90% less land and water than traditional farming.
“The food we put into our bodies has environmental implications,” Pete’s CEO Brian Cook said in a news release. “Our ethos has always been centered around taking care of our team, our local communities, and the environment. Our goal with our new Georgia facility is to expand on our mission, helping to ensure that consumers in the Southeast have access to clean, sustainable greens that are grown close to home.”
The facility will be located in the Robins International Industrial Park, which is located within Peach County.
The development is expected to generate 15 jobs, according to the release.
The company plans to fill a variety of positions including general manager, production, growing, logistics, food safety, and office manager, as well as general administrative roles. To find out how to get hired, visit eatpetes.com for additional information.
“Peach County is thrilled to welcome Pete’s to Middle Georgia,” said B.J. Walker, executive director of the Peach County Development Authority. “This new advanced agricultural project not only brings new jobs and investment into our community but also highlights Peach County as a leader in high-tech, sustainable agriculture.”
The Robins International Industrial Park is designated “Georgia Ready for Accelerated Development” certified site, with “select” status, the release said.
The GRAD Select status is “an indication that a site has met or exceeded more rigorous certification requirements to attract development,” the release said.
Founded in 1970 under the name Hollandia Produce, Pete’s is an employee-owned and operated leader in hydroponically grown living lettuce and cress, according to the release.
How CubicFarms Is Feeding A Changing World With Its Automated Indoor Growing Technology
The global supply chain today is facing significant, costly disruptions. A shipping container crisis has upended the global food trade. Devastating winter weather has impacted the U.S., and ongoing labour shortages within the farming industry show no sign of relenting as border crossings remain shut
April 7, 2021
Mark Shelling, Market One Media
CubicFarms provides sustainable and profitable commercial-scale automated indoor growing systems for local produce and fresh livestock feed. , Image courtesy of Market One Media
Supply chain – CubicFarms Garden – Foodservice – HG cattle
In an already tumultuous year, agriculture is facing supply chain disruptions and unpredictable climate changes
To combat this, CubicFarms offers new automated indoor farming systems that could revolutionize global food supplies
With multiple patents in the ag-tech space, CubicFarms is poised for further expansion
The global supply chain today is facing significant, costly disruptions. A shipping container crisis has upended the global food trade. Devastating winter weather has impacted the U.S., and ongoing labour shortages within the farming industry show no sign of relenting as border crossings remain shut.
The ability to move people and goods across long distances will always be at risk of disruption because the longer the supply chain, the more chances there are for things to go wrong.
The farming industry was already in the midst of a labour crisis even before this year, with fewer and fewer workers available to tend to fields. Now with borders being shut, it's unclear how many foreign workers will be able to return to their jobs, despite some having been issued flight exemptions.
Because of this continued downward trend, Canada is currently projected to lose 123,000 workers within a decade, according to a report done by RBC. That represents a loss of $11 billion in GDP, if the labour gap continues to widen.
Couple this labour shortage with changing weather patterns like the devastating cold snap in Texas, the shipping container crisis, and the ongoing demand for fresh produce, and you’ve got a perfect storm against the food industry.
These stacked variables have revealed just how vulnerable the global food supply chain is. Farmers are now scrambling to find sustainable alternatives to what appears to be a crumbling framework.
"We believe long food supply chains are dangerous. As a technology company in the agriculture business, we’ve seen the challenges with growing outdoors. The solution is in using technology to make locally grown produce more widely accessible, 365 days a year, not just here, but anywhere in the world.”
— Dave Dinesen, CEO, CubicFarm® Systems Corp.
Innovative new agriculture technologies like indoor vertical farming are more attractive to farmers who want the stability and consistency that come from harvesting indoor crops. Innovators in the agriculture space have already anticipated this shift and are now offering ways to safeguard against further threats to cultivation.
The technology is improving rapidly with automated, commercial-scale indoor growing systems that grow fresh produce in a controlled environment. These crops can be harvested with less labour than traditional farming, addressing the need to do more during labour shortages.
By creating the ideal indoor environment onsite, growers use LED lighting, less land, significantly less water, and less energy. In Canada and the U.S., in particular, the ability to grow fresh produce during the winter months allows farmers to expand the growing season to 12-months a year.
Disruptions to the supply chain during the ongoing pandemic have sent food distribution centres searching for more local produce. We can expect that demand to rise as the number of growers using indoor vertical farming systems increases.
A new leader in agricultural automation
For a better look at these automated indoor growing systems, Canadian ag-tech company, CubicFarm® Systems Corp. (TSXV:CUB), offers insights into how this technology is the future of agriculture.
Different from other companies in the ag-tech space, CubicFarms began with the farmers themselves. Jack Benne and his son Leo Benne visited a farm in Puerto Rico after a hurricane when they had an idea for an automated indoor growing system that could grow produce in any weather.
Being the principles behind Bevo Farms, one of the largest propagation greenhouse systems in North America, they put their considerable expertise to work on this important problem.
CubicFarms’ produce is grown onsite in an indoor, controlled environment, for delicious greens harvested at the peak of freshness, bringing food production closer to home.
The automated systems they created are now at the forefront of solving the supply chain woes of countries that must rely on outside suppliers for their fresh produce. The potential for this shift is massive.
A local supply chain would reduce long distance shipping/flights, the indoor controlled environment is pesticide and herbicide-free so there would be fewer shortages due to recall (think of the recent romaine E. coli scares), and there would be less food waste, as produce is harvested at peak freshness instead of days or even weeks in advance.
Under traditional supply chains, there is an expected amount of rot, unnecessary waste of food and profits in each shipment, and it’s a wonder that’s considered tolerable.
The CubicFarm System technology is housed within modules that are 40 ft by 8 ft, standing 9.5 ft tall. The beauty of their structure is that farmers can buy as many modules as they need and place them together, creating indoor fields with the ideal controlled environment year-round.
A patented undulating path is used to move crops throughout the module. Plants are cycled through each module on suspended trays, which periodically pass an artificial LED light source along with regulated CO².
This is different than the typical ‘rack and stack’ vertical farming setups which need more space to allow people through to seed, monitor, and harvest plants. The CubicFarm System brings the plants in a full circle once every 90 minutes.
Each module is custom-built, stainless steel container. Trays move along a patented undulating path.
This allows for harvesting to easily take place at the front of the module, while sensors monitor the plants from the inside. This also prevents leaf burning, sometimes seen in vertical farms when the plants are too close to the light and heat source, or those suffering the ill-effects of their position too high or too low in the rack for the ideal amount of CO² necessary for healthy growth.
The CubicFarm System uses a propagator, which grows seeds into seedlings, and a cultivator that takes crops from seedlings to harvest.
This is all while being provided with the necessary nutrients and using up to 95 per cent less water than traditional farming. This line can replicate the exact growing conditions to yield the perfect leafy greens, herbs, and microgreens every time.
"When you provide the optimal environment every day for a crop, it won't only reward you by growing as fast as possible, but it will also be more delicious and nutritious," Dinesen notes.
Global food distribution giant, Sysco, recently announced on their Sysco Vancouver Facebook page that they’re purchasing fresh produce from growers using the CubicFarm System.
This significant relationship is appealing to anyone looking to get into the supply chain, which can be challenging for smaller farming operations.
A new division of CubicFarms is an expert brokerage called CubicFarms Garden. This expert team provides business consulting services for growers using the CubicFarm System onsite, helping them enter the local supply chain and fostering relationships with food distribution centres.
Farmers have long been at the forefront of technology when it comes to new machinery and systems. “Farmers are the most innovative people we know,” explains Dinesen. “In technology terms, this is the Tractor 2.0. After the invention of the tractor, no one would plow a field without one. With the automated, onsite, and commercial scale of the CubicFarm System, no one would want to grow indoors without us.”
While it might sound complex, farmers who use CubicFarm System will immediately notice its simplicity. When a new unit arrives on site, it's already 90 per cent ready to go, and the remaining set up is assisted by a hands-on customer experience team.
Farmers are trained on how to maximize each module's potential and are given resources for developing new crops. With the recently announced addition of Edoardo De Martin, former Microsoft Vancouver GM, to the executive team as Chief Technology Officer, we can expect the next generation of growing technologies to use more artificial intelligence and robotics to enhance their existing automations and efficiencies.
From fresh food to livestock feed
In January of 2020, the company's success and expertise led to the acquisition of a second farmer-founded innovative company called HydroGreen Inc. Another patented indoor farming system, the HydroGreen Grow System is focused solely on the production of fresh, nutritious livestock feed. Feed that would once be grown across acres of grazing land is now produced in a module that's a fraction of that size.
It is a necessary innovation for ranchers who are facing land and water scarcity issues. Dihl Grohs developed the technology for growing nutritious livestock feed for his ranches in South Dakota, Utah, and Missouri. The concept of low-maintenance feed growing was in direct response to the areas where his cattle had limited precipitation.
Recently published university research confirms greenhouse gas reductions using HydroGreen’s hydroponic fodder system. The university study results came from a HydroGreen Grow System operating in British Columbia, the latest market for the system in CubicFarms’ backyard.
At the EcoDairy in Abbotsford, British Columbia, where they produce milk and use agritourism to educate people about where their food comes from, owner Bill Vanderkooi is using HydroGreen for his dairy cattle.
In a video interview, Vanderkooi talks about incorporating HydroGreen livestock feed into the current mixture and replacing some grain and forage in the cattle diet, measuring against a control group for differences in performance, production, and health. “At the early stage of the trial we’re seeing some positive benefits on performance.” Ongoing research into the nutritional benefits will be combined with land, water, and energy usage as factors for farmers.
The HydroGreen Grow System uses 92 percent less water and less land than traditional farming, so it’s expected that this technology will be widely embraced by the livestock industry in the future.
The fresh livestock feed can be used for a variety of animals, but it’s mainly used for dairy and beef cattle. For those facing labour shortages, the HydroGreen module operates with the push of a button and is self-cleaning. Growing predictable amounts of fresh livestock feed indoors and onsite will allow farmers to reduce the unpredictability that can be costly and dangerous to their animals and livelihoods.
The HydroGreen Grow System’s automated seeder spreads half an inch of small grain seed on the growing surface, growing from seed to feed in six days, with less land, water, labour, and energy.
CEO Dave Dinesen considers the HydroGreen Grow System to be the most automated livestock feed growing technology on the planet.
He explains, "When it comes to animal health and nutrition, the HydroGreen Grow System is giving the most nutritious and delicious livestock feed to these animals. They’re healthier, the feed is more consistent, and ranchers can become more self-sufficient.”
“It’s also automated and scalable because we have the technology to make this possible and profitable,” he adds.
“At the end of the day, we’re a technology company, not a produce or livestock feed company, so we don’t compete with farmers. They become our farmer partners and it’s our job to advance the technologies that support their businesses.”
With a $5 million investment from a top ag-tech investor, Ospraie, and a 100-module sale (their largest yet) to a farm in Surrey, B.C., CubicFarms’ momentum is only growing. It's this momentum that will continue to cultivate new acquisitions, like HydroGreen, and propel the company into an expanding market.
CubicFarms also has an R&D Innovation Centre that is continuously creating new crops and streamlined growing practices to benefit the growers using their technologies, including the CubicFarm System and the HydroGreen Grow System. It's a hopeful progression in a time when there seems to be a new crisis emerging every month. With technology like this positioned to revolutionize global food supply and essentially end hunger, it's one fewer crisis we have to face in 2021.
Learn more about CubicFarms by visiting their website here.
For more information about the CubicFarm System, watch this overview video to see it in action.
Gardening Without Borders, In Partnership With Agritecture
At Plant People, we believe everyone should have the ability to produce quality food, so we have partnered with AGRITECTURE - the leaders in urban agriculture consulting services - to empower people to bring greenery into their home during these difficult times
Even though urban gardening has been gaining popularity over the years, city dwellers have never become more aware of where and how they get their food than during the pandemic. The Food and Agriculture Organization of the United Nations states that at least 55% of the world’s population already lives in urban areas and 80% of all food produced globally is destined for consumption in urban spaces. When the food supply chain could not match demand during the pandemic, food shortages plagued cities as supermarket shelves remained empty for days. During the World Wars, Americans grew “victory gardens” to combat food shortages - and many individuals today are returning to this novel idea to gain control over their food supply and to find an escape from life in lockdown as well.
At Plant People, we believe everyone should have the ability to produce quality food, so we have partnered with AGRITECTURE - the leaders in urban agriculture consulting services - to empower people to bring greenery into their homes during these difficult times. It doesn’t matter if you have killed every plant in your tiny apartment or live in a flat where the nearest park is miles away. Embracing your green thumb and growing your own vegetable garden is only possible if you just start. Trial and error is essential.
First, when blueprinting your urban garden, do not stress about space constraints. There is a gardening method that fits every shape and size. Rooftop access is ideal, but not a necessity. You can also use a balcony, apartment wall, or even a window. Here are five, easy methods to choose from to fit your exact urban gardening needs:
Vertical gardening: As the name suggests, vertical gardening is when you hang plants along vertical surfaces, such as walls, barriers, and fences. You can also mount a series of hanging plants from a window if that is all the space you have. Herbs are best for this type of gardening.
Container gardening: Have a spare box, basket, pot, or old foosball table? Then you can container garden. Depending on the size of your planter, you can grow herbs and vegetables. Just place the container where you have an empty corner and let the seeds grow.
Hydroponic gardening: The most new-age type of gardening, hydroponic gardening uses no soil. Instead, plants grow in a solution of water and nutrients. While this can get quite technical and expensive, there are cost-efficient options that can even fit on a desk!
Rooftop gardening: The most traditional type of urban gardening. If you have the space, rooftops can easily be transformed into a vibrant vegetable and herb garden. Build (or purchase) some garden beds and viola!
Community gardening: According to a recent report by the U.S. Department of Agriculture, 9.4 million Americans' nearest grocery is more than 1 mile away in urban areas or 10 miles away in rural areas. Community gardens are combating these food deserts and bringing communities together. Do a quick Google search to see where your nearest community garden is. Not only will you help others have access to fresh produce, but you will also engage with people in your neighborhood.
Once you have identified what your urban garden will look like, purchase soil and seeds, and then, you are ready to grow your green oasis. Start off with easy vegetables like tomatoes, eggplants, and peppers. Radishes, beans, Swiss chard, kale, and sweet peas are also good options as they grow quickly. Ideally, tie the produce you are growing to the seasons in order to set you up for the most success. If you want to take your urban gardening to the next level and increase biodiversity of your city, build sustainable gardens that support pollinators and attract wildlife, such as bees and butterflies. Doing so will help create new pathways for birds with the new food source and also help cool down the city.
Urban gardening also has other advantages beyond producing nutritious food. It reduces your stress levels, cuts food costs and waste, and lowers your ecological footprint. As to urban agriculture’s broader social impact, these gardens create a safe space for communities to come together to grow food and have a hands-on education about nutrition and food access. Urban agriculture is also more than a food source; it’s a new typology of job creation and economic development. Local food demand has increased from 5 billion dollars in value in 2008 to 20 billion dollars in 2019, so urban agriculture has a strong economic value-add on top of its social, mental, and environmental benefits.
Simply put, living in a city does not mean you have to sacrifice green living. Urban gardening is a part of a growing agriculture revolution that is inspiring people to reconnect with food and nature regardless of where they live. Not to mention that you also get nutritious, fresh produce out of the experience.
A USDA study found that New York City urban gardens produce tomato plants with a yield of 4.6 pounds per plant compared with a conventional average of 0.6 pounds per plant. So grab your tools, find an empty corner, and start urban gardening - you won’t regret it!
Adding A Ground To Air Heat Transfer To An Existing Greenhouse
"A Ceres GAHT (ground to air heat transfer) System is our patented geothermal climate control technology that has helped our growers maintain comfortable growing conditions, year-round, at a fraction of the cost of a traditional HVAC system," states Ceres Greenhouse Solutions
"A Ceres GAHT (ground to air heat transfer) System is our patented geothermal climate control technology that has helped our growers maintain comfortable growing conditions, year-round, at a fraction of the cost of a traditional HVAC system," states Ceres Greenhouse Solutions. In this blog, they give advice on how to install a GAHT around a greenhouse.
The GAHT system was designed to be built with and integrate underneath a Ceres passive solar greenhouse, but it’s also possible to add a GAHT system to an existing non-Ceres or Ceres greenhouse. To do so you would need to install the GAHT pipes in the ground outside of the greenhouse footprint. Trying to install a GAHT system underneath an existing structure is generally not cost-effective nor easily accomplished. Depending on what you are using the GAHT for (heating or cooling), installing the GAHT on the outside of your greenhouse, rather than underneath, may be more beneficial for new greenhouse construction.
In this blog, we will cover GAHT installation and what makes the most sense for your climate and growing situation.
How does the GAHT work?
A GAHT system works by circulating greenhouse air underground through a series of perforated tubes. The air flowing through the tubes is either heated or cooled by the thermal mass of the soil before it’s exhausted back into the greenhouse. Depending on where you live (cold or hot climate), the GAHT system will be primarily used for heating or cooling.
The GAHT & heating
If your primary focus is keeping the greenhouse warm, it is ideal to have the GAHT system under the greenhouse because the structure will help insulate the soil underneath. Wherever you install your GAHT, It is important to insulate the sides of the system to retain as much heat as possible in the soil surrounding the pipes. We recommend insulating the outside of the greenhouse foundation if building the GAHT system underneath.
If you build an exterior GAHT, be sure to insulate the top of the system as well as the sides. A good location for an exterior GAHT, is a place with lots of sunshine, like the south or west side of the greenhouse.
The GAHT & Cooling
If your primary focus is keeping the greenhouse cool, it is ideal to have the GAHT on the outside of the greenhouse and deeper in the ground where the soil is cooler during the summer. In this case, no insulation is needed as you want to allow the heat to transfer away from the GAHT. You also want to install the system in a shaded area on the north or east side of the greenhouse. If you are going to install the GAHT system underneath the greenhouse, either because you’re limited on space or some other reason, the same recommendations about insulation and depth apply: no insulation, and the deeper the better. Installing the system deeper into the earth requires additional safety precautions to be taken to address the risk of soil collapse and personnel engulfment.
What’s important to note is that a GAHT is really only suitable for cooling a greenhouse in late Fall, Winter and early Spring. In the Summer, the sun’s energy is so powerful that the GAHT would need to be very, very large (making it very expensive) to cool the greenhouse entirely on its own. If you are able to cool the greenhouse with an evaporative cooler, this is almost always a less expensive, and higher performance option for cooling in the summer.
A benefit to cooling your greenhouse with a GAHT during the late Fall, Winter, and early Spring is that it allows you to keep your greenhouse sealed. This prevents shocking the plants with cold air from ventilation and allows CO2 supplementation to increase plant growth during these periods.
Sizing your GAHT system
One general rule for installing an external GAHT, whether you’ll mostly use it for heating or cooling, is that the excavation footprint of the GAHT system should be similar to the footprint of the greenhouse. For example, a 12×24 greenhouse requires an approximate area of 12×24 for the GAHT. This footprint correlation will ensure that there is a sufficient rate of soil-to-air heat exchange. For cooling applications, performance can be increased by increasing the size of the footprint.
For more information:
Ceres Greenhouse Solutions
1898 S. Flatiron Ct, Ste 125 Boulder,
CO 80301 USA
303-495-5006
info@ceresgs.com
www.ceresgs.com
Publication date: Wed 7 Apr 2021
Your Quick Guide To Grow Room Controllers
A grow room controller brings together all the moving parts of your cultivation facility and allows you to automate your operation
March 5, 2021
What is a Grow Room Controller?
A grow room controller brings together all the moving parts of your cultivation facility and allows you to automate your operation. With a grow room controller, you can monitor and control your climate, lighting, irrigation, fertigation, and track your crop’s success to adjust and improve each cycle. These control systems can connect to existing equipment or come with their own set of sensors to track your environment, and adjust according to your set parameters, ultimately saving you time and money.
Grow room controllers integrate with existing systems, or can be purchased with sensors and equipment for larger operations. Some systems need only a few sensors and an application for your phone or computer, while others require larger computing and monitoring devices. Which option you choose will largely depend on the size of your greenhouse or indoor growing operation.
Being able to monitor and control your indoor or greenhouse facility is crucial for consistent and desired results. These systems are a huge benefit to all crop types, including cannabis, and can be adjusted to fit your cultivation style and desired outcomes. Not only will you be able to more accurately track and monitor your crop’s progress, but you can then take that learning and replicate it or improve upon it for your next growth cycle.
The Benefits
Grow room controllers offer you complete control and oversight of your crop. Any environmental aspect that you wish to control can be monitored and adjusted with a grow room control system. More advanced systems offer automation for your whole system, allowing you to pull yourself out of the weeds (pun intended) of trying to control everything manually. Grow room controllers are also scalable, especially if you purchase a setup with that in mind, allowing you to expand your facility but keep the same environmental parameters and automation.
All greenhouse and indoor growers know that having control over your environment is crucial to achieving desired results. This means monitoring and adjusting your lighting, climate, irrigation, and fertigation to ensure consistency, which can be time-consuming. A greenhouse control system does the monitoring and adjusting for you, ensuring all of the environmental controls work together and are adjusted accurately.
With advanced control systems, you can program light preferences for your greenhouse, so if light falls below a certain threshold your lights will adjust and will turn off if it exceeds that threshold. Indoor growing can also benefit from lighting such as timers and spectrum controls. Hydroponic sensors in your medium can tell you if you need to increase or decrease water durations. Ultimately being as efficient as possible with water and electricity, which is both environmentally and economically beneficial.
This monitoring and automation are incredibly cost-effective in the long run for your greenhouse or indoor facility. The more automation you have, the less labor you need to support your cultivation, and labor is one of the most, if not the most costly aspect of a cultivation facility. Grow room and greenhouse control systems can also schedule timers and alarms for preventative maintenance so that your equipment can receive proper downtime, preventing blowouts and loss of productivity.
How to Select a Grow Room Controller
Figure 1 from GroAdvisor Webinar
The above worksheet is an example of how you can select the right grow room controller for your needs. While many focus on cost, it’s also important to take into account which system will integrate with and enhance your facility the most. Take stock of your equipment and current manual system to ensure that your new grow room controller will add value to your operation.
Finding a grow room controller that is right for your facility will help you realize your fullest growth potential. Once you have compared and found a system that can accommodate the environmental controls you’d like to track and automate, all that’s left is the installation. Once the grow room controller is installed and your parameters are set you will no longer have to manually adjust your elements, saving time and labor, which ultimately saves money.
USA: MARYLAND - BW Students Learning High-Tech Plant Growing Techniques
Bishop Walsh School is teaching students through hands-on experience about the efficient ways plants can be grown. The school recently acquired a ZipGrow Tower through federal grants, which is designed for high-density hydroponic farming
April 1, 2021
By Brandon Glass bglass@times-news.com
CUMBERLAND — Bishop Walsh School is teaching students through hands-on experience about the efficient ways plants can be grown. The school recently acquired a ZipGrow Tower through federal grants, which is designed for high-density hydroponic farming.
Mick Burkett, a teacher at Bishop Walsh, holds up pH meters. Burkett is teaching students through hands-on experience about the efficient ways plants can be grown.
“As far as food goes, of all industries, that’s one industry that’s not going away. There’s a lot of science to growing, so it’s important to have high-tech growing techniques,” said Mick Burkett, a Bishop Walsh teacher who is heading the project. “The kids are going to learn how to grow with state-of-the-art science aquaponics, hydroponics, ZipGrow towers.”
The towers are built to make easier production, irrigation, and planting, which will be important in a future where more people live closer together and planting space is limited.
Some 2,000 seed plants can be grown in a smaller than expected platform. Due to the towers being vertical, they take up much less space when compared to planting in soil in a field or a garden.
Students monitor the nutrient levels in the solutions using pH meters and add more as needed.
“The first graders, they’re learning about what is a living thing, so they’re growing mint,” said Burkett. “They’ll be able to put the mint in little pots in our maker space. They’re going to be doing everything from scratch, from growing the plant to making their own little flower pot.”
Eventually, the goal is to have food from the greenhouse and ZipGrow station on the table at Bishop Walsh, to grow enough food to sustain themselves and contribute to the community.
“Instead of farm to table, this is from BW to BW. It is great economically, it’s great for the environment,” said Burkett. “It’s good in so many ways.”
There are also plans for a spring sale at some point, where 50% of whatever is made would go back into the greenhouse and other technologies. They also want to pick out a local organization to donate to.
The genesis for the ZipGrow project was the greenhouse the school built over a year ago, which due to the pandemic has not been used yet, but will eventually be able to hold, Burkett estimated, 6,000 starter plants.
The ZipGrow station was born out of federal funding the school receives through the county and ran about $5,000, said BW Principal Jennifer Flinn.
For now, for students, it’s come as you want, as the school is not able to have clubs due to the pandemic; however, next year the expectation is there will be clubs dedicated to growing plants.
Lead photo: Bishop Walsh freshmen Michael Nowaczyk and Rianne Treadwell examine the plants on the ZipGrow Tower.
Follow staff writer Brandon Glass on Twitter @Bglass13 - Submitted Photo
A Number of Pain Points Drive Middle East (Growth) Intensification
An international consulting company says New Zealand has a real opportunity to be a partner of choice with the Middle East in providing agritech solutions to a growing agriculture sector
And NZ Suppliers Are Ready To Help Them
An international consulting company says New Zealand has a real opportunity to be a partner of choice with the Middle East in providing agritech solutions to a growing agriculture sector. Alpha Kennedy, from Prime Consulting International, told delegates at the MobileTECH Ag event in Rotorua that the United Arab Emirates and Gulf Countries are just about to begin major expansion, especially in horticulture.
"Whether it's precision agriculture, remote sensors, irrigation systems, soil regeneration and fertility, farm management, software training, robotic harvesting, pricing information or market access applications," Mr. Kennedy said. "If you have a product that fits into those focus areas there is a place for you to (partner) a customer who is willing to listen, and willing to pay. The UAE and the wider Gulf Cooperation Council (GCC) areas have a very distinct set of challenges, such as the higher cost of food imports, the high cost of production, environmental barriers, skilled workers - they all require technological solutions to overcome them. But this opportunity will not be around forever. New Zealand has a very good name as an agriculture innovator, so they will give NZ companies the time and listen, but ultimately they are moving forward quickly and will go with those who are there. There are Dutch, Irish or Israeli companies, for example, that are also keenly aware of opportunities."
Photo: some of the agritech projects underway in UAE, including vertical farming and vegetable production. Source: Alpha Kennedy's presentation at MobileTECH Ag.
New Zealand's Trade Commissioner and Consul-General to the United Arab Emirates (UAE), Kevin McKenna says the UAE is New Zealand's 10th largest trading partner.
"It is a crucial gateway for New Zealand goods and services to Africa, the rest of the Middle East and parts of Europe," he said. "The UAE and its neighbor Saudi Arabia are two of our fastest-growing export markets. The paradox in the UAE is that just two kilometres away (from Dubai's busy city centre) lies desert land that flows into rocky mountains and then more desert beyond. So, while the people will need more of our fruits and other food, they hunger for smarts to sustainably feed themselves and the populations around them. That's the challenge, but it also provides an enormous opportunity for New Zealand - we are highly respected for our agritech."
Mr. Kennedy adds that the United Arab Emirates' agriculture industry is worth more than US$3billion annually and growing by 4 percent overall, and the horticulture sector is growing by 6 percent. In 2019, horticulture produced 1.25million tonnes of field crops, fruit, and vegetables, mostly in the country's north, while vertical farms are being created in Dubai, Abu Dhabi, and Sharjah.
"There are a number of 'pain-points driving the (growth) intensification; firstly, it is hard to grow food in the UAE," he said. "It's not impossibly hard, but very hard. Summer can be above 50 degrees Celsius, and winter can be balmy in the 20s. There is also very little rainfall and the country is dependent on desalinization, which is expensive to produce and of the water that is produced, 66 percent is used for agriculture purposes. The cost of water is also subsidized and the government is looking to end those subsidies in coming years. This means that they are constantly on the lookout for tech and emerging technologies that can address these challenges."
As a result, the UAE currently imports around 90 percent of its food. Mr. Kennedy says this figure has been increasing, as has the dollar cost of importing, and with the country's population set to increase to 15 million over the next 20 years, it is imperative to increase domestic production for food security and quality of life.
"They have set some very ambitious targets and they are aiming to be the most food-secure nation by 2050," he said. "That will require a mix of domestic production, trade agreements, and the like. But these pain points are not just being experienced in the UAE but are widely experienced across the Gulf states and they all have transformation plans in place to improve food security. So, the opportunities are not just in the UAE but much broader and agriculture in the GCC is already valued at $20billion. For (NZ) companies with products, solutions, and developments, I encourage you to take advantage of these technology incubators, accelerators, and financing programs. There is a range of financial support available."
He says the future of agritech is already taking place with vertical farms coming into production in the past 18 months, and in 2020 Abu Dhabi invested US$200million in vertical farms.
Mr. McKenna is encouraging interested companies and agencies to attend and make connections at the World Expo in Dubai, which was postponed from last year, and will run for six months from October 2021.
"We have designed a discover agritech program for exporters working across all aspects of the sector," he said. "The program is going to include online learning, webinars, advisor meetings in New Zealand. Followed by a week here to look at what is going on. We are going to have project visits, we are going to meet with government departments, advisors, and partners, we will look at some of the accelerators and a specialized visit to the Agra Middle East trade show."
For more information
Alpha Kennedy
Prime Consulting International
Phone: +971 56 362 8956
mena@primeconsultants.net
www.primeconsultants.net
Publication date: Tue 6 Apr 2021
Author: Matt Russell
© HortiDaily.com
Technology Capital Markets Veteran Tom Liston Appointed VP of Corporate Development For CubicFarm Systems Corp
Liston is a technology investor, advisor, and a Chartered Financial Analyst® with over 20 years of experience in capital markets
Strong Track Record of Shareholder
Value Creation With
Disruptive Technologies
VANCOUVER, B.C., April 6, 2021 – CubicFarm® Systems Corp. (TSXV: CUB) (“CubicFarms” or the “Company”), a local chain agricultural technology company, today announced the appointment of Thomas Liston as Vice President (VP) of Corporate Development.
Thomas (Tom) Liston will provide CubicFarms with strategic business development and capital markets advisory services in his role as VP of Corporate Development. Liston is a technology investor, advisor, and a Chartered Financial Analyst® with over 20 years of experience in capital markets. He’s the founder of Water Street Corp and currently serves on several boards of directors for public and private technology companies, and he has a strong track record of shareholder value creation in that capacity. He has served on the Board of Directors of WELL Health Technologies (TSX: WELL) since April 2018 and Tantalus Systems Holding Inc. (TSX.V: GRID) since January 2021.
Prior to his current role, he was the Chief Investment Officer of a leading technology-focused venture capital firm and was responsible for leading the firm’s investments in Software-as-a-Service (SaaS), FinTech, and Healthcare Information Technology (IT) sectors. Two of these investments were among the top exits in Canadian technology in recent years.
“My focus is working with disruptive technology companies in sectors with compelling macro tailwinds, which has resulted in the delivery of strong returns for shareholders. I was drawn to CubicFarms because the Company’s best-in-class indoor growing technologies uniquely fit this theme,” said Tom Liston.
Liston began his career with Yorkton Securities as a Research Analyst covering public Software and IT Services companies. In 2003, he joined Versant Partners in the same role and was quickly promoted to Director of Research while maintaining his coverage of technology companies. In 2012, Versant Partners’ team was acquired by Cantor Fitzgerald, where he served as Director of Canadian Research and covered the technology sector. Liston has been consistently ranked among the top technology analysts in several surveys, including StarMine, Brendan Wood, Greenwich Associates, and Reuters. During his tenure as a Research Analyst, he had received more StarMine stock-picking awards than any other technology analyst.
“Tom is a capital markets veteran in technology with proven experience identifying underrecognized companies and assisting in unlocking value for shareholders. He’s uniquely experienced to work with a disruptive technology company of our size on the journey to achieve industry leadership,” said Dave Dinesen, CEO, CubicFarm Systems Corp.
A respected member of both the technology community and his alumni organizations, Liston completed a Bachelor of Business Administration degree in Finance from the University of New Brunswick (UNB) and a Master of Arts in Economics and Finance from Queen’s University. In 2017, he was the recipient of the UNB Faculty of Management’s Certificate of Achievement and UNB also recognized Liston with the Proudly UNB Alumni Award of Distinction in 2020.
About CubicFarms
CubicFarms is a local chain, agricultural technology company developing and deploying technology to feed a changing world. Its proprietary ag-tech solutions enable growers to produce high quality, predictable produce and fresh livestock feed with HydroGreen Nutrition Technology, a division of CubicFarm Systems Corp. The CubicFarms™ system contains patented technology for growing leafy greens and other crops onsite, indoors, all year round. CubicFarms provides an efficient, localized food supply solution that benefits our people, planet, and economy.
For more information, please visit www.cubicfarms.com.
On behalf of the Board of Directors
“Dave Dinesen”
Dave Dinesen, Chief Executive Officer
Neither the TSX Venture Exchange nor its Regulation Services Provider (as that term is defined in the policies of the TSX Venture Exchange) accepts responsibility for the adequacy or accuracy of this release. This news release may contain forward-looking statements which include, but are not limited to, comments that involve future events and conditions, which are subject to various risks and uncertainties. Forward-looking statements are not guarantees of future performance and actual results may vary materially from those statements. General business conditions are factors that could cause actual results to vary materially from forward-looking statements.
Media Contact:
Andrea Magee
T: 236.885.7608
E: andrea.magee@cubicfarms.com
Investor Contact:
Adam Peeler
T: 416.427.1235
E: adam.peeler@cubicfarms.com
The information transmitted herein is confidential and may contain privileged information. It is intended solely for the person or entity to which it is addressed. Any review, retransmission, dissemination, taking of any action in reliance upon, or other use of this information by persons or entities other than this sender's intended recipients is prohibited. If you received this in error, please notify the sender and delete or destroy all copies.