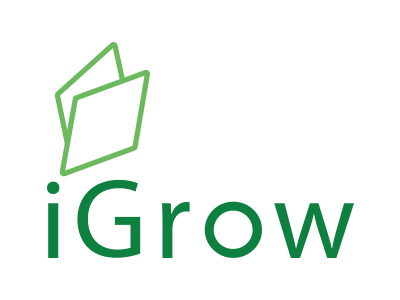
Welcome to iGrow News, Your Source for the World of Indoor Vertical Farming
N.Thing To Export Smart Farms To UAE After $3 Million Deal
The contract, set to proceed next month, will allow the firm to construct vertical smart farming containers in the UAE by December this year.
May 17, 2021
South Korean agriculture technology company N.Thing said Monday that it has recently inked a $3 million deal with Sarya Holdings in the United Arab Emirates to export smart farms.
The contract, set to proceed next month, will allow the firm to construct vertical smart farming containers in the UAE by December this year. The container can reduce the use of water up to 98 percent compared to a typical farm and cultivate crops in any environment, whether that is in Siberia, the Middle East, or Seoul.
“The UAE reached out to N.Thing as food security emerged as a key issue amid the coronavirus outbreak,” a company official said.
In February last year, Sarya Holdings conducted a proof of concept test on N.Thing’s container to verify the technology. During the test, Sarya planted four different vegetables -- batavia, kale, Boston lettuce, and oakleaf -- in eight test containers and observed their growth cycles, nutrients, quality, and more.
The test proved that N.Thing’s smart farm containers built in the UAE can produce up to 1.5 metric tons of crops per container, which was 42 percent more than initial estimates.
N.Thing received the best innovation award at the Consumer Electronics Show last year.
Lead photo: The interior of N.Thing’s smart farm container (N.Thing)
By Kim Byung-wook (kbw@heraldcorp.com)
USA: INDIANA - 5 Acres of Food In 80 Feet: Urban Farmer Grows A Garden In The Heart of Indianapolis
An unassuming plot of land sits on the eastside of Indianapolis on 30th Street. From the outside, it looks like an empty lot with a couple of shipping containers on it. But inside those containers is an entire garden
May 6, 2021
An unassuming plot of land sits on the eastside of Indianapolis on 30th Street. From the outside, it looks like an empty lot with a couple of shipping containers on it. But inside those containers is an entire garden.
And among the plants, you can find DeMario Vitalis.
Vitalis is the first in Indiana to own a hydroponic farm inside of a shipping container. The unique method involves planting seedlings of plants such as herbs and lettuces on vertical panels and feeding them controlled levels of water, nutrients, and light — no soil required.
It’s a mode of farming uniquely suited for urban environments. Vitalis is able to produce almost 5 acres of food a year from two 40-foot shipping containers. It also uses 99% less water than traditional farming, according to the company that makes the containers.
Vitalis sells his fresh herbs, lettuces, and more to people in the community through online platforms such as Market Wagon.
The climate control is a huge advantage for Vitalis, who set up his farm, called New Age Provisions, in the latter half of last year. Regardless of the outside weather, he can grow anything he wants.
“It can be 30 degrees outside and raining,” he said, “but inside it’s 65 degrees. In here I’m watching Netflix and planting seeds.”
Even though he now spends much of his time dedicated to plants, Vitalis wasn’t a farmer when he started all of this. He was just an entrepreneur looking for his next project, and farming — which connected to his history as a descendent of enslaved people and Southern sharecroppers — felt like the right choice.
“It was just a way to become an entrepreneur,” he said, “and also get back into the type of occupation my ancestors once had.”
‘It’s in his blood’
Vitalis was looking for something that would put a piece of property he owned to use, and he had a hunch shipping containers were key.
At first, he thought he would set up some modular tiny homes built out of containers. But then he came across Freight Farms, a Boston-based company that could cram 2.5 acres of production into one shipping container, and the decision was made.
Although born in San Francisco, Vitalis’ family is originally from the South, and he moved around quite a bit before settling in Indiana.
“Three of my four grandparents started off from the South,” Vitalis said, “So we were part of that Black migration when we moved eventually from the South to San Francisco on the West Coast.”
After living in Germany, Kansas, and other places as his stepfather moved around with the military, Vitalis’ mother decided to move him to Indianapolis, where he stayed and attended Arlington High School and Purdue University.
Vitalis’ mother Barbara Johnson is a cook, so food has always been important to the family. And the herbs and vegetables grown by her son, she said, are “absolutely wonderful.”
“I just believe that you can always inspire a person with a good meal,” she said.
Even so, farming or food production was never anything they did at home, she said. But she knows it’s something he feels close to because of the family’s history.
“I guess it was just in his blood,” she said.
Vitalis was one of the first Black owners of a Freight Farms shipping container in the country, said Caroline Katsiroubas, marketing, and communications director for the company.
“He, in particular, wanted to be a catalyst for more Black farmers to join the Freight Farming community,” she said, “and I’ve definitely seen the impact.”
Overcoming learning, funding hurdles
It wasn’t easy learning how to grow food.
Despite two degrees from Purdue University, Vitalis doesn’t have a background in farming and had to put himself through some education before diving into his urban farm. He took online classes and even visited Freight Farms in Boston to learn about the equipment and process.
“It does take a learning curve,” he said. “It’s not easy to learn how to farm; you have to learn how to react to the plants.”
Sometimes his daughter will help him with the planting. Johnson, too, will help out and trim plants, clean or help with planting, and occasionally brings her grandson along. Understanding how the farm works was a learning curve for her, too.
“I didn’t know anything about hydroponic farming,” she said. “When I saw that wall of plants, I didn’t think it was possible.”
Funding was another obstacle. The farms cost $100,000 each.
After some research, Vitalis found that the U.S. Department of Agriculture will supply loans for these types of businesses, so he requested $50,000 to help him pay for one container and was promptly denied.
The people evaluating the profitability of these containers simply didn’t understand how it worked or how much it could produce, he said. But instead of giving up, he pushed back. Black farmers have historically been discriminated against when trying to obtain USDA loans, and he was motivated to make sure his business plan was being fairly evaluated.
“There’s a history behind that,” he said. “I was just one of many.”
Vitalis appealed the decision and won. Then, he turned around and asked for $200,000 instead — and got it.
Finally one day, a semi-trailer pulled up outside his property with the containers, picked them up with an enormous crane, and plopped them right down behind the nearby building.
“It was pretty interesting to see a big old 40-foot container fly over a building,” Vitalis said. “It was not easy, but you know, God was on my side and I was able to get through the hurdles that were put in my way.”
How hydroponics works
In a hydroponic farm, everything is vertical — and everything is controlled.
At first, the plants start as seedlings or seeds and are placed on shelves under LED lights, and water flushed with nutrients is dispensed to them with attached machines.
After a few weeks, the plants are large enough to transfer to a series of vertical panels that roll along tracks. These panels are also connected to machines for dosing water and nutrients and placed in between LED lights. The water circulating through the plants is saved and re-cycled through the system, conserving water and nutrients.
Although space may seem tight, one container can output the equivalent of 1,000 heads of lettuce each week, Katsiroubas said.
And throughout the whole process, Vitalis controls the light, temperature, nutrients, and water. The plants live in a perfectly contained ecosystem that’s never under threat from drought, flooding or pests.
“It has its own brain,” Vitalis said.
It’s a big advantage, he said, because he can grow food year-round and he doesn’t have to worry about pesticides or herbicides. It’s also “hyper-local,” he said. When he gets an order, the food comes from the planter into the customer’s hands within a matter of hours.
David Bosley, Vitalis’ former boss at Cummins, Inc., used Vitalis’ greens for his Thanksgiving meal and said he was impressed by the packaging and freshness. At first, he said, the idea of a hydroponics farm was surprising.
“I thought it was rather novel,” he said, “but I also thought, well that’s just like DeMario.”
Nobody was surprised that Vitalis made New Age Provisions happen.
He’s always been one to tackle a project without giving up, Bosley said. And he’s always been a trailblazer and hard worker, his mother said. She thinks it’s something he may have picked up from her, since she worked multiple jobs and attended school while caring for him and his siblings.
“I’m even more amazed with my son,” Johnson said. “He‘s satisfying a need in the community and following a dream. It was his vision and he brought it to fruition.”
Contact IndyStar reporter London Gibson at 317-419-1912 or lbgibson@gannett.com. Follow her on Twitter @londongibson.
Connect with IndyStar’s environmental reporters: Join The Scrub on Facebook.
IndyStar's environmental reporting project is made possible through the generous support of the nonprofit Nina Mason Pulliam Charitable Trust.
US: NEBRASKA - The Bay, Beyond School Bells Launch Youth-Focused 'Freight Farm'
In partnership with Beyond School Bells, The Bay is launching The Greenery, a self-contained hydroponic farm housed in a repurposed shipping container
Apr 25, 2021
A 40-foot-long shipping container in the parking lot of The Bay will soon be filled with a whole lot of green.
In partnership with Beyond School Bells, The Bay is launching The Greenery, a self-contained hydroponic farm housed in a repurposed shipping container. Members of Beyond School Bells and The Bay gathered with local leaders Saturday to officially launch the program.
Much like The Bay’s other youth-focused programs, The Greenery is designed to allow students access to engaging, hands-on activities — in this case growing food.
“We are thrilled about the opportunity to be able to turn kids on to sustainable agriculture,” said Andrew Norman, executive director and co-founder of The Bay’s parent organization Rabble Mill. “A lot of the kids in our neighborhood have never seen anything like this; none of us have.”
The Greenery setup is designed by the Boston-based company Freight Farms. Beyond School Bells was able to purchase the unit through a partnership with the Ben Hormel Harris Foundation, said state Sen. Anna Wishart, the director of partnerships for Beyond School Bells. Several local companies and individuals donated their time to help get it up and running.
Through vertical planting that doesn’t require soil, the shipping container is able to house 13,000 plants at a time, or about as much food as a 2.5-acre farm. Throughout the container are thousands of red and blue LED lights that can be precisely controlled through the trailer’s high-tech programming to provide the perfect amount and color of light for each plant, said Doak Field, director of operations at Freight Farms.
The setup is also water-efficient, as the water that flows throughout the trailer is repumped through the cycle.
“Everything is just way more efficient than growing outside,” Field said. “You can get the exact science down to whatever you need to grow.”
Field said the team hopes to start planting the container within the next two weeks and is planning to start with greens such as lettuces and kale, as well as herbs.
The program leaders plan to sell the food grown at the Greenery at local farmers’ markets or through weekly community-supported agriculture projects. They'll also source produce to local restaurants.
While many of the similar freight farm projects that have popped up across the country have been for-profit and run by adults, Lincoln’s will be one of only a few that are not-for-profit and youth-focused, Wishart said.
Beyond School Bells works statewide to provide after-school opportunities for students like The Greenery, she said.
“Our goal is to ensure that every kid, no matter where they grow up in Nebraska, has access to quality out-of-school programming and this freight farm is absolutely an example of that,” she said.
The project will offer an opportunity for students to learn a variety of skills, Wishart said, and University of Nebraska-Lincoln honor students will also play a role in mentoring younger students working on the project.
“This also creates an incredible platform for youth to learn entrepreneurship and about sustainable, high-tech agriculture and future careers in that space,” Wishart said.
The Greenery project is part of a series of environmental-focused projects across the state that Beyond School Bells is working on, the organization's network lead Jeff Cole said.
“This will be the crown jewel,” he said. “But we're already starting to do investments in rural Nebraska around outdoor classrooms, environmental education, and a series of other things across the state.”
Lincoln Mayor Leirion Gaylor Baird said she sees the project as an example of innovative, environmentally friendly solutions that can help move the city forward.
“This is such a wonderful demonstration of how we can take better care of the Earth, create greater value for everyone in our community and hand something on to the next generation, something that they can have a leadership role in,” Gaylor Baird said.
Lead Photo: Jeff Cole of Beyond School Bells talks to visitors about the Greenery, a 40-foot-long shipping container that will operate as a high-tech hydroponic farm at The Bay. The container has space to vertically grow over 13,000 plants — the equivalent of a 2.5-acre farm. FRANCIS GARDLER, Journal Star
CANADA (YT): Tackling Food Insecurity Above The 60th Parallel
ColdAcre Food Systems is based in Whitehorse, Yukon, one of the northernmost provinces in Canada. The company was incorporated in August 2019 and specializes in controlled environment agriculture.
In the northernmost territories of Canada, agricultural development is underway but must contend with the cold climate, variable photoperiod and other environmental challenges. It comes as little surprise, then, that interest in controlled environment agriculture is on the rise. ColdAcre Food Systems is one of the companies that supports this endeavor and has installed multiple growing systems in northwestern Canada.
ColdAcre Food Systems is based in Whitehorse, Yukon, one of the northernmost provinces in Canada. The company was incorporated in August 2019 and specializes in controlled environment agriculture. Prior to its incorporation, ColdAcre primarily sold retrofitted shipping containers and also operated its own container farm to supply the Whitehorse market with fresh greens and herbs.
According to chief executive officer Carl Burgess, “the original intent was to sell and provide growing systems but we immediately identified an opportunity and a need to demonstrate commercial production north of the 60th parallel year-round.”
With its incorporation in 2019, ColdAcre thus based itself on four pillars:
Growing produce for the Whitehorse market and beyond
Selling prefabricated and custom growing systems for its clients
Providing consultation and pathfinding services
Active learning and engagement in various projects.
Growing produce for the Whitehorse market
When ColdAcre first began producing greens and herbs, the company started with three dozen products but have since narrowed its product line in order to have a robust supply and client demand. ColdAcre has also recently begun producing mushrooms. Explaining the Yukon’s consumer base, Carl says that the territory is the size of Spain yet is home to only 40,000 people. Whitehorse is the territory’s capital and its businesses service much of the territory, as well as southern Alaska, northern British Columbia and the western Northwest Territories.
As such, Whitehorse acts as an important hub for northern residents and has a relatively robust food demand. According to Carl, “some people drive 1,000 km to buy goods and groceries in Whitehorse a few times a year. That said, the Yukon only produces 1% of the food that is purchased and consumed in the territory.”
Importing most of its consumables carries the double burden of a heavy carbon footprint and limited nutritional quality. “When comparing the quality of fresh produce between Vancouver and Whitehorse, there is a significantly lower quality in the Yukon, which is only heightened when you go further north. Producing locally also virtually eliminates waste and the carbon footprint of production,” says Carl.
Selling growing systems
ColdAcre also continues to sell prefabricated and custom growing systems for clients through Canada’s northwestern region. While the company began with CropBox and has had success doing so, ColdAcre has found that its clients typically require more customization. Moreover, working with an American company has subjected ColdAcre to a higher degree of volatility with respect to changes in the dollar and availability of equipment, according to Carl.
With respect to its technology, Carl also explained that ColdAcre’s technology “is not necessarily unique, but that the skillset and assembly is. In the Yukon, we face the challenge of growing lettuce when it’s 40°C outside in the summer or down to -53°C. We address these extremes using high-tech and smart-tech solutions. We customize the whole management and contingency for potential crises specific to a client or area.”
Consultation and active learning
ColdAcre has also committed to providing consultation and pathfinding services to growers regardless of whether the grower is using a ColdAcre system or not. As Carl explains, “we think that our growing challenge are everyone’s challenges so if we can solve ours, we’d like to share.”
ColdAcre also has multiple research partners throughout northern Canada and while the projects are generally northern-based, the results have applications in various settings.
2020 and 2021 at a glance
In all four pillars, ColdAcre has reported increased interest in the past year. The fragility of Yukon’s food system was heightened by the COVID-19 pandemic and ensuing supply chain disruptions. As such, the interest in local food production and stabilized food system has surged in the territory. ColdAcre’s production has been sold out since October 2019 and the company will be tripling its production in the coming months. According to Carl, ColdAcre’s proximity to market channels allows the company to compete with imported commodities from California and Mexico and demand a reasonable premium. Similarly, the company is reportedly experiencing an increased demand for its systems for residential, office, and educational purposes.
Most recently, ColdAcre shipped a 53-foot container farm to Inuvik, a community in the Arctic Circle and whose community greenhouse will use the shipping container to produce fresh produce year-round.
For more information:
Carl Burgess, CEO
ColdAcre
carl@coldacre.ca
www.coldacre.ca
Publication date: Fri 9 Apr 2021
Author: Rebekka Boekhout
© VerticalFarmDaily.com
Vertical Growing Solutions That Are Easily Multiplied Increasing The Management Scale of Each Grower
GrowSpec offers three main products, each with numerous product lines contained therein. These three products include LED grow lights, vertical grow systems, and container farms
GrowSpec is an indoor farming equipment supplier established in 2015. GrowSpec offers three main products, each with numerous product lines contained therein. These three products include LED grow lights, vertical grow systems, and container farms. According to GrowSpec CEO Alvis Ma, these products can be used to produce a variety of crops indoors.
LED Grow Lights
GrowSpec offers six different types of LED lighting: AgriSpec, AgriBar, Sun Ray, Panel, SlimSpec, and Quantum. According to the company’s website, AgriSpec is a high-performance top-lighting solution with dimmable capabilities to allow growers to transition from vegetative to regenerative growth (i.e., flowering). The lights’ slim configuration enables installation in low rooms, racking systems, etc. While AgriBar and Sun Ray are both advertised as applicable for greenhouses as well as indoor farms, Panel is more specifically designed for indoor growing as the wide panels are somewhat wide for greenhouse use yet provide high light uniformity for indoor environments.
Vertical Grow Systems
GrowSpec also designs a number of vertical grow systems, all consisting of racks with integrated power supply, control system, and PVC trays so that each 4’x 8’ tray can be managed independently. Among these product lines in VertiDrip, a modular rack consisting of GrowSpec’s lighting, drip irrigation, airflow system, power supply, and touchscreen controls. The company’s VertiGro follows similar principles. GrowSpec’s main grow system, which was previously featured in IGrow (Combining Hydroponic And Aeroponic In Vertical Farming — iGrow) is VertiAero, which uses aeroponic technology. According to Alvis, VertiAero is patent pending in both the United States and Europe and offers various savings to growers.
“VertiAero reduces operational costs by 40%. In terms of electricity, we use 30% less. With nutrients, we save 85% because we use aeroponics rather than soil, so the root area is sealed and water losses are reduced. Our vertical grow systems are designed to optimize farm’s operation, they can match up with different irrigation systems so as to meet growers’ different preferred cultivation skills, and easily multiplied increasing the management scale of each grower,” explains Alvis.
Moreover, Alvis explained that having an integrated ventilation system in every rack of GrowSpec’s vertical grow systems helps to decrease plant disease.
“With inadequate ventilation, some plants will have diseases like powdery mildew or botrytis. But if you have full ventilation and every leaf can be blown with air, you will seldom have those diseases,” says Alvis.
Alvis also explained that the racks are space-efficient by both having an adjustable height and by being horizontally mobile using a mechanical assist. This, according to Alvis, allows growers to fit more racks into a grow room.
Container Farms
GrowSpec’s third product offering is container farms, which are equipped with GrowSpec’s vertical grow systems. According to Alvis, GrowSpec’s container farms are ideal both for production and for research as the conditions are highly modifiable and allow growers to test various things.
“If people want to do research, they can use this container to do so. They can set up irrigation, lighting, temperature of the root zone, temperature of the canopy, light intensity, etc. It is the perfect toy for them.”
Efficiency and scalability as priorities
Across GrowSpec’s three product types (LEDs, vertical grow systems and container farms), the company has emphasized improved resource use efficiency and scalability so that growers can easily increase production over time.
“For installation, we design our systems in modules so that they are very easy to install. It is a complex system yet easy to install. And it is scalable. It is easy to design the grow room because every rack is independent. The rack height is also customizable, and the power is integrated so that there is one main cable per rack, this allows requires the systems to be easy to maintenance ” explains Alvis.
GrowSpec also reports increased crop productivity by allowing growers to produce seven crops per year rather than four crops in traditional farming systems.
For more information:
USA: ILLINOIS - Glenview's Wiseacre Farm To Be Featured On History Channel
"We were connected to this opportunity through Freight Farms, a hydroponic farming container company in Boston. Our farm was built and distributed by Freight Farms," said Yael Sheinfeld, whose father, Aviad, founded Wiseacre Farm
This Sunday's Episode of "Modern Marvels"
Will Highlight Innovative Hydroponic Techniques
March 23, 2021
The Wiseacre Farm crew (left to right): Sam Sheinfeld, Yael Sheinfeld and Aviad Sheinfeld. (Photo by Wiseacre Farm)
GLENVIEW, IL — Back in December of last year, a television production crew from the History Channel made a special visit to Glenview. Wiseacre Farm, a family-owned hydroponic farm, will be featured this Sunday as part of the network's "Modern Marvels" program.
Yael Sheinfeld, who handles marketing for the farm at 1975 N Lake Terrace, said the team at Wiseacre hasn't seen the episode titled, "Future of Food," yet. It is set to air at 9 p.m.
"We were connected to this opportunity through Freight Farms, a hydroponic farming container company in Boston. Our farm was built and distributed by Freight Farms," said Yael Sheinfeld, whose father, Aviad, founded Wiseacre Farm. "We're so grateful for the experience, and are very excited for the episode to air."
Aviad Sheinfeld shows off Wiseacre Farm during an episode of "Modern Marvels" on The History Channel. (Courtesy of Wiseacre Farm)
Sunday's episode of "Modern Marvels," hosted by food author and culinary entrepreneur Adam Richman, showcases Wiseacre's innovative hydroponic farming process as the future of food, highlighting the farm's mission to grow clean, fresh produce within the community that it serves.
"It was exciting for the film crew to visit the farm. Our farming team (Aviad Sheinfeld and his dad, Sam Sheinfeld) talked through each step of the plant life cycle and delivery process while the crew filmed," Yael Sheinfeld said. "[We also] participated in sit-down interviews where we discussed the concept behind the farm, how we started it, etc."
Yael Sheinfeld said that due to COVID-19 restrictions, the entire film crew for the episode was local.
Founder Aviad Sheinfeld talks about Wiseacre Farm during the episode of "Modern Marvels" titled, "Future of Food." (Photo by Wiseacre Farm)
Wiseacre Farm works to shorten the path from farm to table, promote and practice environmental sustainability, and educate consumers about the origins of their food.
"We're a family-owned hydroponic farm in Glenview that provides fresh, hyperlocal greens to the community," Yael Sheinfeld said. "We currently offer home delivery and farmside pickup options."
Wiseacre greens are available through home delivery subscriptions and weekly farmside pickup. Wiseacre Farm also makes frequent donations to local food pantries, working to ensure that fresh greens are accessible to all.
More information about Wiseacre Farm can be found here: https://www.wiseacre.farm/.
AUSTRALIA: VIDEO - Shipping Container Farms: Check Out This Craze In Modified Containers
Greenhouses, hydroponics, and mushroom farms – converted shipping containers can produce protein and vegetables for all your needs
Greenhouses, hydroponics, and mushroom farms – converted shipping containers can produce protein and vegetables for all your needs. Even if you’re not an environmentalist, there are business opportunities to be had in delivering extremely fresh food to people in urban environments like Brisbane. Given the changing climate and topsoil loss we are facing, shipping container farms could well be an answer to these issues.
Over the years in the Gateway Gazette, we have published a number of stories that look at producing food in converted shipping containers. Reflecting on what we have published and looking at the detail of what can be done, let’s consider the possibilities that come with shipping container farms.
Open Top Container Greenhouse
One of the most cost-effective ways of using a shipping container as a food-producing unit is by attaching a glass top to an open-top shipping container.
In this video, Urban Farm Units looked at the concept of a greenhouse-container. An open-top 20-foot container would have a greenhouse attached to the top with shelving units directly under the glass. This allows photosynthesis to take place in the normal way.
Seedlings can be started in the lower part of the unit, which is warmed by the light and heat from the outside.
One step down from slapping a greenhouse on top of an open-top container would be to use a flat rack container and to have the greenhouse on the base (Gateway Containers can supply both open-top and flat rack containers).
The concept is an improvement on the one in the video, as long as you keep the greenhouse within the dimensions of a 20ft standard or high-cube container, it would be possible to lift and move the container farm from place to place.
This might be useful where you have an agreement with property developers or a council to use vacant plots of land in a city for agriculture. When the site is ready to be developed you can stick it all on a truck and move it to the next plot.
The concept of a shipping container greenhouse is:
Cheap to buy
Mobile
And often won’t need planning permission for a permanent site
Could this be something you’d consider? Contact us at Gateway Containers to discuss your needs!
Mushie Container Farm!
Image source: King Oyster Mushrooms Facebook
In 2019 we reported how Belgrave, Vic-based John Ford has developed a shipping container mushroom farm. This could produce protein for people as an alternative to meat or for anyone who loves the taste of freshly cut shrooms.
Mushrooms of any kind don’t store well and are best eaten as soon as possible after cutting. This is why having a mushroom farm close to restaurants could be a money-spinner.
This requires no modification from a basic shipping container, you could even install the racking inside the container yourself.
In their lifecycle, mushroom mycelium live out of sight of the world until they are stressed and get the impression that they are facing death. When stressed they flower to produce spores – those flowers are the mushrooms that many of us love to eat.
A shipping container is perfect to take advantage of such a lifecycle. Logs or other media are infected with the mycelium and left to rot for a certain time. By altering the environmental conditions, so you deliberately stress the fungi and they flower.
In our article, we reported how John Ford is producing mushroom species that are famed for their delicate taste but don’t travel well at all – shiitake and oyster mushrooms. As a sideline to his main income as a marine biologist restoring seagrass habitats near Belgrave, he produces freshly cut shrooms for local people and restaurants.
For you as an entrepreneur, mushroom growing would require buying a used shipping container and setting it up as a mushroom farm. If you are planning an urban mushroom container farm, you can take advantage of the fact that you can treat the container as a mobile unit and not as a permanent base. Shipping containers are also pretty inexpensive to buy and convert.
Hydroponics – The Rolls Royce of Shipping Container Farms
Image source: ABC
The hydroponics concept is highly developed for the use of fresh food and can be set up for high density vegetable farming in shipping containers. This requires a fair bit more modification than the two systems we describe above.
Unlike the Urban Farm Units company, several companies have managed to survive over the years selling their hydroponic container farm businesses to entrepreneurs and restaurants around the world.
Modular Farms is a company we featured in our blog originally based in Canada, but who recently set up shop over here in Australia. According to their website, they “design and manufacture container farm systems that can be used to grow food in most locations on earth.”
These systems strive to get around some of the issues we face here. Cities like Brisbane get far too much water sometimes and then face droughts for years on end. The Australian Food Services News reported, “With a focus on sustainability, Modular Farms’s hydroponic, closed-loop system uses 95% less water than a typical outdoor farm.”
Topsoil erosion is a problem, especially in prolonged droughts when it gets blown away as dust. Hydroponics use media like rock wool and even used mattresses to house the plants’ root systems and feed them nutrients via a watering system.
With our ever more extreme climate, food often has to be imported into cities from hundreds or thousands of miles away. A hydroponic container farm can enable you to grow many vegs very close to markets and restaurants.
This has been observed by global homewares retail giant IKEA, which in 2019 announced it was piloting growing vegetables in its stores for use at its restaurants. We reported, “While selling hydroponic indoor growing equipment to customers, IKEA is feeding its staff with lettuce and other vegetables grown in a container outside its Malmö and Helsingborg stores.”
Image source: ABC
There are a few downsides to hydroponics. Firstly, while some types of plants are happy enough growing in hydroponics – the simpler ones producing leaves and flowers (like broccoli!) – others aren’t so happy, such as cassava, wheat, and potatoes.
The next big issue is that for a high-intensity farm, not unlike factory farming chickens, you need to be ultra-clean in your production as the arrival of a destructive disease or fungus could wipe you out very quickly.
Container Fish Farm Too?
In theory, it is possible to run a fish farm connected to the hydroponics container farm, with you largely feeding the fish and collecting their feces and other waste to feed the plants. The plants would clean the fishes’ water and make it habitable for them as reed beds do in nature. This a concept that is in development but hasn’t caught on commercially yet.
How Can Gateway Containers Help?
We can provide and convert an insulated container for you to get started with and advise you how to best make further additions without compromising the overall structure.
If any or all of these ideas have caught your interest – or you just know about these concepts and need a shipping container to make it possible – then get in touch with us today to discuss your needs!
Posted on February 22, 2021
By Mark FinneganOtherShipping ContainerModified Shipping ContainersLeave a comment
US: NEW YORK - 21st Century Fund Awards FeedMore WNY $100,000 For Expanded Freight Farms Greenery
In 2020, FeedMore WNY served more than 16 million meals to WNYers who were homebound due to quarantine
by queenseyes
March 17, 2021
Recognizing the needs of the community is an integral component of the 21st Century Fund. Making sure that those needs are met is another. The Fund – “a giving circle open to anyone who wants to give back in Western New York” – designates significant awards to worthy organizations that submit applications for consideration. This year, FeedMore WNY is the recipient of $100,000, which will allow the non-profit to continue on with its efforts to feed those struggling during the pandemic.
In 2020, FeedMore WNY served more than 16 million meals to WNYers who were homebound due to quarantine. This was accomplished via the group’s 300 pantries, soup kitchens, emergency shelters, etc., throughout Erie, Niagara, Cattaraugus, and Chautauqua counties.
FeedMore WNY will be using the significant funds to expand its GrowMore for Good project, by allowing the organization to double its capacity, which in turn will ensure that fresh produce will be available to over 129,000 individuals. The expansion of a FeedMore-operated Freight Farms Greenery™ (the organization’s second hydroponic container farm) means that FeedMore will be able to produce 200 lbs. of produce each week. The group’s initial hydroponic “container farm” will supplement the effort. This food will be harvested and distributed within 24 to 48 hours, according to FeedMore.
This is an incredible effort that will allow more people to access healthy foods, instead of relying upon less wholesome canned foods.
In order to receive the crucial funding, FeedMore WNY made it to the final four, out of a streamlined pool of 30 applicants, before coming away with top honors. Homespace, Jericho Road, and OLV Charities were the other three finalists – all four projects can be found here.
Members* from across the country ended up casting their votes for FeedMore WNY, knowing how imperative it is to get healthy foods into the hands and onto the tables of disadvantaged households. The existence of ‘food deserts’ and the fight for ‘food justice’ go hand-in-hand. Compounded by the pandemic, it’s more important than ever to offer people food security, for healthier futures.
“FeedMore and all the clients we serve across Erie, Niagara, Cattaraugus and Chautauqua counties are overwhelmingly grateful for the generous support from the 21st Century Fund which will allow us to purchase our second container farm. The indoor, vertical growing, hydroponic farm will allow us to double our output of crops to enable us to put fresh, nutritious and fragile produce into our clients’ hands within 48 hours of harvest,” said Tara A. Ellis, FeedMore president and CEO.
“Our giving circle is a great way to introduce people to philanthropy,” said Ted Borowiak, 21st Century Fund Co-Chair. “We are always accepting members and encourage anyone including families, school groups or organizations to learn more about our membership options. Once you are a member, you are a member for life, allowing you to stay informed on new projects underway and make an impact in our community over and over again.”
The next 21st Century Fund grant process will open in the fall of 2021. For more information about the 21st Century Fund and membership details, visit www.21stcenturyfund.org.
*Members pay a one-time fee to join the 21st Century Fund and come together every other year to vote on awarding a $100,000 grant to one deserving organization for a specific project that will benefit the community. The 2018 winner chosen by members was the Niagara Falls Boys & Girls Club’s 17th Street Clubhouse Revitalization Project.
Tagged with:21st Century Fund, FeedMore WNY, food deserts, Freight Farms Greenery, GrowMore for Good, Tara A. Ellis, Ted Borowiak
Providing A Sustainable Growing Solution For Farmers, Using Renewable Energy in Container Farming
Recently, Freight Farms and Arcadia have partnered to provide Freight Farms' U.S. customers with access to clean energy for their everyday operations
“The past year has really proved our proposition as it has never been proven before,” says Rick Vanzura, CEO at FreightFarms. “The pandemic put a huge focus on supply chain security, local food access, and how to handle disruption to a supply chain, and we saw that having a modular farming solution that can be put next to people where they need food fits in perfectly. Some segments have suffered, while our farms have proven to be a great solution.” The company has seen demand going up, with 2020 being a record year: Freight Farms tripled revenue versus the prior year and set a record for orders.
Recently, Freight Farms and Arcadia have partnered to provide Freight Farms' U.S. customers with access to clean energy for their everyday operations. With this partnership, Freight Farms and Arcadia are taking strides to align their respective industries, moving indoor farming into a more sustainable future. Freight Farms’ customers can now connect the utility for their container farm to Arcadia to match 100% of the farm’s electrical usage with clean energy.
Tackling sustainability pillars
“We already have a number of current farmers that have signed up with the Arcadia energy offering. It was a really important milestone for us as sustainability has been a core mission since the founding of the company.” Rick identifies the sustainability pillars in farming as soil conservation, water conservation, food miles, and energy usage. “At Freight Farms, we have always performed very strongly in the first three categories. Our farms have no effect on soil; they use very little water (5 gallons/day, or 19 L/day), and they reduce food miles significantly, sometimes to zero. What remained for us to solve and why the Arcadia partnership is so crucial is energy,” Rick notes.
Before the Arcadia partnership, energy was the only unsolved part of the sustainability pillars Freight Farms hadn’t tackled yet. The recent partnership has given access to clean energy to all small business farmers. “With the presence of clean energy, we believe there hasn’t been a more sustainable farming solution similar to this one before.
Freight Farms looks at sustainability through the triangle of labor, yield, and power. They are increasing the output per unit of input. According to Rick, Freight Farms is far down the road in the development of greater efficiencies in their farms, focusing on optimizing for yield per unit of power and continuing to research renewable energy options. Rick says that “Everybody’s success is a collective success as we’re all relying on the industry as a whole... We’re all bound by this mission to create a more sustainable planet. Therefore, anything we can do in our own small way, we’re ready to do.”
Improving farm efficiency
On the product side, the company is doing updates to everything. “We made our farms more efficient, delivering value in several aspects, working on different renewable energy in all forms. The ROI has never been better than this farm, because of the intersection of output and efficiency gains. As we’re big believers in helping the industry as a whole for good, our ultimate goal is to be NET zero ultimately.”
While Freight Farms customers already span 46 U.S. states and 32 countries, Rick believes that the company will expand into more locations this year. This growth is stimulated by recent investment and team expansion. “By the end of 2021, we’re expecting to be in every US state and several other countries. Ospraie Ag Science led our last fundraising round, where they invested heavily in our ability to do research. Therefore, we’ve added lots of strength to the team over the last year.”
Collaborations
As a plug of vertical farming, Freight Farms is collaborating with MIT sustainability lab students together on a project. The project is about working in conjunction with the government, and public- and private partnerships around sustainability. “The goal is to be part of something where brilliant people are willing to donate their time and energy. This is just one example of many where people want to pitch in and help as we all want to have a more sustainable planet,” Rick notes.
“We’re not trying to solve for renewable energy on a location by location basis. That would be the route to go with today, but it’s a solution limited to the United States as of now,” Rick affirms. Freight Farms is always on the lookout for partners worldwide where its services can be made available.
For more information:
Rick Vanzura, CEO
Freight Farms
+1 877 687 4326
info@freightfarms.com
www.freightfarms.com
Publication date: Wed 17 Mar 2021
Author: Rebekka Boekhout
© VerticalFarmDaily.com
VIDEO: Farming In A Shipping Container
Transforming Unused Spaces Into Vertical Farms
Transforming Unused Spaces Into Vertical Farms
New Sustainability Partnership Launched Between Sodexo And ZipGrow Inc.
Sodexo, world leader in Quality of Life Services, has joined forces with ZipGrow Inc., the manufacturer of the world’s most installed vertical hydroponic equipment, to develop a unique program to introduce sustainable growing systems to facilities throughout Canada and the United States of America
Burlington, March 11, 2021: Today, two international industry leaders have launched a first-of-its-kind partnership to develop more sustainable local food chains throughout North America.
Sodexo, world leader in Quality of Life Services, has joined forces with ZipGrow Inc., the manufacturer of the world’s most installed vertical hydroponic equipment, to develop a unique program to introduce sustainable growing systems to facilities throughout Canada and the United States of America.
One of Sodexo’s primary goals is to ensure all our operations are industry-leading from a sustainability perspective. “This new partnership with ZipGrow Inc. not only enables us to reduce our carbon emissions of distance traveled for food source, onsite food waste, and packaging requirements, but also to introduce innovative technology to our facilities and team members”, said Normand St-Gelais, Director of Corporate Responsibility, Sodexo Canada.
ZipGrowTM technology is a patented system that utilizes both hydroponic growing systems and vertical planes to maximize production volume within a small footprint. Primarily growing leafy greens such as lettuce and kale, along with herbs and small fruiting crops such as strawberries, ZipGrow systems will be installed in Sodexo locations including educational institutions, conference facilities, and corporate food service centres.
“Having been installed throughout the world over the past decade, our system enables growers, both big and small, to access fresh produce no matter where they are located”, explains Eric Lang, President of ZipGrow Inc. “We are excited to move ahead with this new partnership with Sodexo. Together we will be able to introduce sustainable food to Sodexo locations throughout North America.”
“As a Chef, we are always looking for ways to introduce the freshest possible produce to our kitchens”, said Chef Davide Del Brocco, Sustainability Manager, Sodexo Canada. “By having a grow system on site, we can now not only customize our produce to meet our upcoming needs, but we can also now harvest fresh greens and use them that same day.”
“Having like-minded partners like ZipGrow who understand what is important to us and who are aligned with our values and goals is crucial in working together for a Better Tomorrow." said Andrea Cantin, Corporate Social Responsibility Coordinator, Sodexo Canada. With Sodexo and ZipGrow Inc. both having company values strongly embedded in sustainability, this new partnership will see this innovative agriculture technology being introduced to multiple Sodexo facilities in Canada and the US.
About Sodexo
Sodexo delivers a wide range of customized solutions, designed to optimize work and living environments. Sodexo has been providing food and facilities management services in Canada for over 40 years, with a focus on enhancing safety, work process, and well-being. Sodexo is a market leader in Canada. Sodexo has been recognized as a top employer for the past seven consecutive years. Sodexo is proud to have created the Sodexo Stop Hunger Foundation, an independent charitable organization that has raised over $3 million to fight hunger and donated more than one million meals to at-risk youth across Canada since 2007. Sodexo is included in the CAC 40, FTSE 4 Good, and DJSI indices.
Key figures (as of November 2020)
420,000 employees
1st in its sector in both the Dow Jones Sustainability Index (DJSI) and the 2020 SAM sustainability yearbook 64 countries
100 million consumers served daily
About ZipGrow Inc.
ZipGrow Inc. is an international leader in indoor, vertical farming technology. Our flagship product, the ZipGrowTM Tower, is a core component of many of the world’s most innovative farms; from indoor hydroponic warehouses to vertical aquaponic greenhouses and high-density container farms. For more information contact hello@zipgrow.com or at 1-855-ZIPGROW.
Contacts
Media
Caroline Desvaux
Tel: +1 514 476 2158
Caroline.desvaux@sodexo.com
Eastern Kentucky Company Growing Local Economy By Growing Vegetables Year-Round
AppHarvest has created 300 jobs in Appalachia, an area not really known for growing tomatoes.
by GIL MCCLANAHAN
MOREHEAD, Ky. (WCHS) — Imagine growing fresh local tomatoes in the dead of winter. A company in Eastern Kentucky is using high-tech agriculture to grow vegetables indoors.
To View The Video, Please Click Here.
AppHarvest checks tomatoes growing inside the company's 60-acre indoor greenhouse.
(AppHarvest ) Courtesy Photo
AppHarvest opened in Rowan County, Ky. last October. They are growing more than just vegetables. They are growing the economy in an area that sorely needs it.
What's growing inside AppHarvest's 2.8-million square foot facility is capable of producing more food with less resources.
"For our first harvest to be on a day where there was a snowy mountainside could not have been any more timely. The fact that we are able to grow a great juicy flavorful tomato in the middle of January and February is what we have been working to accomplish," AppHarvest Founder and CEO Jonathan Webb said.
Webb said five months after opening its Morehead indoor farm facility, the company shipped more than a million beefsteak tomatoes to several major supermarket chains, including Kroger, Walmart and Publix. Those large bushels and bushels of tomatoes are grown using using the latest technology, no pesticides and with recycled water in a controlled environment using 90% less water than water used in open-field agriculture.
"We're just trying to get that plant a consistent environment year round with the right amount of light and the right amount of humidity and the right temperature just to grow, and the vines of our crops the tomato plant end up being 45 feet and we grow them vertically so that is how we can get so much more production," Webb said.
One of the company's more well-known investors is Martha Stewart.
"I said Martha, can I get five minutes and I told her what we are doing. She was like, look we need good healthy fruits and vegetables available at an affordable price. I love the region you are working in," Webb said.
A couple of weeks later, Webb met with Stewart at her New York office, and she decided to become an investor in the company. Some local restaurants are looking forward to the day when they can buy their vegetables locally from AppHarvest. Tim Kochendoerfer, Operating Partner with Reno's Roadhouse in Morehead, buys his vegetables from a company in Louisville.
"It will be another selling point to show that we are a local restaurant," Kochendoerfer said.
Webb points out AppHarvest is not trying to replace traditional family farming. "Absolutely not. We want to work hard with local farmers," he said.
Webb said by partnering with local farmers, more local produce can get on grocery store shelves, because last year 4 billion pounds of tomatoes were imported from Mexico.
"What we are working to replace is the imports from Mexico where you got children working for $5 a day using illegal chemical pesticides in the produce is sitting on a truck for 2-3000 miles," Webb said.
AppHarvest has already started influencing the next generation of farmers by donating high tech container farms to local schools. Students learn to grow crops, not in the traditional way, but inside recycled shipping containers. The containers can produce what is typically grown on 4 acres of land. Rowan County Senior High School was the second school to receive one. It arrived last fall.
"We sell that lettuce to our food service department and it's served in all of our cafeterias in the district," said Brandy Carver, Principal at Rowan County Senior High School.
"When we talk about food insecurity and young people going home hungry, what better way can we solve these problems by putting technology in the classroom. let kids learn, then let the kids take the food home with them and get healthy food in the cafeterias," Webb said.
AppHarvest has created 300 jobs in Appalachia, an area not really known for growing tomatoes. Local leaders believe the company will attract more business to the area.
"I fully expect in time we'll see more and more activity along that line like we do in all sectors," said Jason Slone, Executive Director of the Morehead-Rowan County Chamber of Commerce.
"We will eventually be at the top 25 grocers. Name a grocer. We've been getting phone calls from all of them," Webb said.
AppHarvest has two more indoor farming facilities under construction in Madison County, Ky., with a goal of building 10 more facilities like the one in Rowan County by the year 2025.
To find out more about AppHarvest click here.
AmplifiedAg Introduces Indoor Farm Platform And Disruptive Technologies, Positioning Company For Rapid Expansion
"AmplifiedAg is on a trajectory to change how the world is feeding itself. Through the adoption of our core technologies and scalable farm platform, we're providing secure food sources and influencing a global shift to indoor farming, which will play a key role in providing food to a growing planet," said Don Taylor, CEO of AmplifiedAg, Inc
News Provided By AmplifiedAg
Mar 03, 2021
CHARLESTON, S.C., March 3, 2021 /PRNewswire/ -- With a mission to provide global access to safe food, AmplifiedAg, Inc. introduces its indoor farming platform which includes vertical farms, hydroponic systems, and its proprietary operating system with disruptive seed-to-sale SaaS-based technologies. For the past five years, AmplifiedAg has demonstrated its unparalleled ability to sustainably grow produce to scale at the highest yield, quality and nutritional value, while operating directly at the point of consumption.
AmplifiedAg, Inc. wholly-owns Vertical Roots, the largest hydroponic container farm in the world. Vertical Roots indoor farm production operates with AmplifiedAg's holistic indoor farming platform.
AmplifiedAg's compact farm design operates directly at the point of consumption, maximizes growing space, and is easily scalable in food deserts and space-limited areas. The company's proprietary OS gives farmers total transparency and control of horticulture, food safety, production and business management.
AmplifiedAg deploys indoor farms 70% faster than other CEA implementations, and directly at the point of consumption.
AmplifiedAg rapidly deploys fully functioning farms 70% faster than other CEA implementations, and at cost, that is 50% of the required capital per production pound. The company upcycles shipping containers into controlled agriculture environments with vertical hydroponic systems, LED lights, and electronics, and integrated with AmplifiedAg's proprietary operating system.
AmplifiedAg's indoor farm platform produces 86 times more crop yield per acre compared to traditional farmlands and provides reliable crop production with 365-day farming, regardless of climate and resources. The compact design maximizes the growing space and provides easy mobility and scalability in food deserts and space-limited areas.
But the heartbeat of the operation is AmplifiedAg's proprietary Operating System that features industry-exclusive traceability which tracks every detail of an individual plant's journey from its growth to distribution. This gives farmers total transparency and control of horticulture, food safety, and business management.
Farm containers' resilient architecture and segmentation minimizes the risk of crop loss due to pest and pathogen infestations. SaaS-based technologies provide real-time tracking analytics and 24/7 access for farmers to mitigate risk, control the farm environment and optimize plant growth.
AmplifiedAg's ability to quickly place farms directly in communities and distribution points drastically reduces emissions. Sustainably-focused, the farms don't use soil or pesticides and utilize up to 95% less water than traditional farming.
Wholly-owned by AmplifiedAg, Vertical Roots is the company's proofpoint and has set industry-breaking records in less than five years. Vertical Roots is the largest hydroponic container farm in the U.S., growing nutritious leafy greens with products in over 1,200 grocery stores across the Southeast.
With a proven concept for leafy greens, AmplifiedAg's horticulture expansion plan includes varied nutrient and protein-rich foods to feed the world's growing population.
Increasing threats to the planet's food production fueled Taylor, a 30-year software industry veteran, to found AmplifiedAg in 2016.
"With a growing population, less arable land, water supply and food contamination issues, climate change and environmental disasters," said Taylor, "Our planet is on a path to grow less food for more people while continuing to accelerate the degradation of the earth's fragile ecosystem. Exasperating our already critical food access issues on the planet. The only way we're going to get ourselves out of this situation is with technology. We need to grow safer food in greater volumes closer to the point of consumption while conserving and restoring the environment."
"That is what is driving all of our development and innovation, and ultimately the demand we are seeing from indoor farmers and communities across the world," concluded Taylor.
AmplifiedAg, Inc. was founded in 2016 as the parent company of Vertical Roots, Boxcar Central, a SaaS platform supporting third-party logistics companies and breweries, and Tiger Corner Farms, a CEA farm manufacturing company. AmplifiedAg has absorbed Tiger Corner Farms and Boxcar Central operations as the company presents its mobile indoor farm platform to the market.
About AmplifiedAg, Inc.
AmplifiedAg, Inc. is an ag-tech industry visionary on a mission to provide global access to safe food. The company manufactures indoor vertical farms, hydroponic systems, and disruptive seed-to-sale SaaS-based technologies. Unlike other indoor ag operations, AmplifiedAg provides holistic indoor farm solutions to grow and distribute food anywhere in the world.
AmplifiedAg owns and operates Vertical Roots, the largest hydroponic container farm in the World. Learn more at www.amplifiedaginc.com. Growing Food for a Growing World.
SOURCE AmplifiedAg
Related Link
USA - OHIO: Thinking And Growing Inside The Box
A brother-sister team has taken the mechanics of farming out of the field and into a freight container
FEBRUARY 10, 2021 By SIDNEY DAILY NEWS
Local Farmer Takes The Farm Indoors
By Blythe Alspaugh - balspaugh@sidneydailynews.com
PIQUA — A brother-sister team has taken the mechanics of farming out of the field and into a freight container.
“We are growing beautiful plants without the sun; there’s no soil, and so it’s all a closed-loop water system,” Britt Decker, co-owner of Fifth Season FARM, said. “We use non-GMO seeds, completely free of herbicides and pesticides, so the product is really, really clean. In fact, we recommend people don’t even wash it, because there’s no reason to.”
Fifth Season FARM is unique in many ways; the 3-acre hydroponic farm is contained in a 320-square-foot freight container that sits along 120 S. Main St. in Piqua, with everything from varying varities of lettuce, to radishes, to kale and even flowers in a climate-controlled smart farm that allows Decker and his sister, Laura Jackson, to turn crops in a six- to eight-week cycle. The crops spend 18 hours in “daytime” every day, and the farm uses 90% less water than traditional farming.
“It’s tricky because we’re completely controlling the environment in here. It’s kind of a laboratory more than a farm,” Decker said. “I think there’s about 50 of them around the world right now. These are really international, and they’re perfect for places that are food deserts where they can’t grow food because of climate or other reasons. It gives them a way to grow food in the middle of nowhere.”
Decker and Jackson, along with their brother Bill Decker, also do traditional farming and grow corn, wheat and soybeans, but Decker said they were looking for a new venture that would help lead them to a healthier lifestyle and learn something new.
“Just with the whole local food movement becoming more and more important and food traceability, we just thought it would be a great thing to bring to our community to help everyone have a healthier lifestyle,” Decker said. “People love food that’s grown right in their hometown and the shelf-life on it, when you get it home, is remarkable. It’ll keep for two weeks.”
Currently, Decker and Jackson are growing a half-dozen variety of specialty lettuces that include arugula, butterhead, and romaine, as well as specialty greens like kale and Swiss chard, and even radishes and flowers. They received their freight container at the end of July and set up their indoor farm over two weeks; while the farm has been in operation for less than six months, Decker says that they’re growing beautiful product.
They have also started growing micro-greens, said Decker. Micro-greens are immature plants which are 1 to 3 inches tall and are in a 5-inch by 5-inch container.
“People will use them as garnishments and in smoothies,” said Decker. “Since they are immature plants, they have an intense flavor.”
Decker said they are growing wheat germ, broccoli and spicy salad mixes.
They’ve also started moving forward with sales and marketing. Fifth Season FARM has partnered with the Miami County Locally Grown Virtual Market to sell their products to the community. They also take orders through their website, fifthseasonfarm.com; customers can opt to pick up their orders between 4 and 6 p.m. on Wednesdays, or Decker and Jackson will deliver products up to five miles from the farm. Decker said that Fifth Season FARM is also in discussions with three restaurants in the area about including their specialty greens on their menus.
Decker said they also plan to attend the Sidney Farmers Market when it opens for the spring/summer season.
“We’re really just getting going,” Decker said. “While we were learning to grow products, we didn’t want to overcommit to a restaurant or grocery store before we knew we could really grow a beautiful product, so we’ve been donating product every week to the food pantry at the Presbyterian Church. It feels good to plant the seeds and watch them grow, and it feels good to make sure that people who aren’t getting the proper nutrition are getting some.”
Vertical Farming At A Crossroads As Pandemic Shifts Focus To Fresh Produce
Getting the right business model to balance resource usage with socio-economic conditions is crucial to capturing new markets. Speakers will discuss the issues at the forthcoming Agri-TechE event on Thursday 25th February 2021
15-02-2021
Getting the right business model to balance resource usage with socio-economic conditions is crucial to capturing new markets. Speakers will discuss the issues at the forthcoming Agri-TechE event on Thursday 25th February 2021.
Although growing crops all year round with Controlled Environment Agriculture (CEA) has been proposed as a method to localize food production and increase resilience against extreme climate events, the efficiency and limitations of this strategy need to be evaluated for each location. Research by Luuk Graamans of Wageningen University & Research, a speaker at the upcoming Agri-TechE event on CEA, has revealed that integration with urban energy infrastructure can make vertical farms more viable.
“The pandemic has shifted the conversation to the global connectivity of countries, where people started questioning the sustainability and resilience of the international food network,” comments Luuk. “The big question is should countries or large cities (mainly) rely on imports to feed their citizens?
His research around the modeling of vertical farms shows that these systems are able to achieve higher resource use efficiencies, compared to more traditional food production, except for electricity. So, the vertical farm needs to offer additional benefits to off-set this increased energy use. One example his team has investigated is whether vertical farms could also provide heat.
“We investigated if vertical farms could provide not just food for people living in densely populated areas and also heat their homes using waste heat. We found that CEA can contribute to stabilizing the increasingly complex energy grid.”
This balance between complex factors both within the growing environment and the wider socio-economic conditions means that the rapidly growing CEA industry is beginning to diversify with different business models emerging.
Jack Farmer is CSO at LettUs Grow, the company has just launched its Drop & GrowTM growing units, which offer a complete farming solution, in a shipping container. He says that everyone in the vertical farming space is going to hit a crossroads, “Vertical farming, with its focus on higher value and higher density crops, is effectively a subset of the broader horticultural sector. All the players in the vertical farming space are facing a choice – to scale vertically and try to capture as much value in that specific space, or to diversify and take their technology expertise broader.”
LettUs Grow is focused on being the leading technology provider in containerized farming. Jack continues: “Drop & Grow:24, is primarily focused on people entering the horticultural space, and we expect it to be one of the most productive, ethical, and easy to use container farms on the market. This year is looking really exciting – supermarkets are investing to ensure a sustainable source of food production in the UK, which is what CEA provides. We’re also seeing a growth in ‘experiential’ food and retail and that’s also where we see our Drop & Grow container farm fitting in.”
Kate Hofman, CEO, GrowUp agrees, the company launched the UK’s first commercial-scale vertical farm in 2014. She comments: “It will be really interesting to see how the foodservice world recovers after lockdown – the rough numbers are that supermarket trade was up at least 11% in the last year – so retail still looks like a really good direction to go in. If we want to have an impact on the food system in the UK and change it for the better, we’re committed to partnering with those big retailers to help them deliver on their sustainability and values-driven goals.
“Our focus is very much as a salad grower that grows a fantastic product that everyone will want to buy. And we’re focusing on bringing down the cost of sustainable food, which means doing it at a big enough scale to gain the economies of production that are needed to be able to sell at everyday prices.”
The economics are an important part of the discussion. Recent investment in the sector has come from the Middle East, and other locations, where abundant solar power and scarce resources are driving interest in CEA. Luuk’s research has revealed a number of scenarios where CEA has a strong business case.
However, for the UK, CEA should be seen as a continuum from glasshouses to vertical farming. “Greenhouses can incorporate the technologies from vertical farms to increase climate control and to enhance their performance under specific climates.” Luuk continues.
It is this aspect that is grabbing the attention of conventional fresh produce growers in open field and covered crop production.
James Green is Director of Agriculture at G’s, one of Europe’s leading fresh produce growers. He explains: “There’s a balance in all of these systems between energy costs for lighting, energy costs for cooling, costs of nutrient supply, and then transportation and the supply and demand. At the end of the day, sunshine is pretty cheap and it comes up every day…
“I think a blended approach, where you’re getting as much benefit as you can from nature but you’re supplementing it and controlling the growth conditions, is what we are aiming for, rather than the fully artificially lit ‘vertical farming’.”
Luuk, Jack and Kate are to join a discussion with conventional vegetable producers, vertical farmers and technology providers at the Agri-TechE event “Controlled Environment Agriculture is growing up” 25th February 2021.
Find out more: agri-tech-e.co.uk/upcoming-events/
Agri-TechE is a business-focused membership organization, supporting the growth of a world-leading network of innovative farmers, producers, scientists, technologists, and entrepreneurs who share a vision of increasing the productivity, profitability, and sustainability of agriculture.
Together we aim to help turn challenges into business opportunities and facilitate mutually beneficial collaboration.
Agri-TechE
Farming Goes Indoors
THE pandemic has shone a light on many of the gaps that exist in the country’s economy. And one of these is the need for better food security, an issue that resonated with Gerard Lim long before Covid-19
By JOY LEE
06 Feb 2021
Beyond profits: Lim, seen here briefing an investor, says the company is also looking at creating new high-valued jobs and generate income for local communities.
THE pandemic has shone a light on many of the gaps that exist in the country’s economy. And one of these is the need for better food security, an issue that resonated with Gerard Lim long before Covid-19.
Many years ago, he started noticing that most of the vegetables sold in local supermarkets and grocers were not necessarily the best of quality as top-grade vegetables grown here were mainly exported. That means locals were consuming lower grade vegetables.
Additionally, a lot of the vegetables that can be grown in Malaysia were, in fact, imported.
Lim wasn’t a farmer but he knew that technology could help boost quality production for local consumption and improve the local supply chain for vegetables.
“My exposure and experience with farming started about five years ago when I introduced smart farming solutions using sensors, the Internet of Things, and Big Data to various farmers. But I found that many farmers in Malaysia were smallholders who could not afford the technology.
“I knew that if I wanted to move the needle, I had to adopt the technology and build large commercial scale, industrial-grade farms to achieve better economies of scale.
“What was compelling to me was that I was not alone in wanting better quality food and vegetables. There was a ready and strong demand from friends and contacts who wanted the same good quality, clean and fresh vegetables, ” he points out.
Lim has vast experience with tech startups and had previously served in the Malaysian Communications and Multimedia Commission (MCMC).
When he left the regulatory body last year, the time seemed right to embark on a venture that would focus on scaling up smart farming. And with the Covid-19 pandemic ongoing, it became even more evident that there was a need to grow food and vegetables closer to where they are consumed.
He founded Agroz Group Sdn Bhd, an agritech and indoor vertical farming company, to simplify the distribution supply chain of vegetables while reducing the long- and mid-haul transport of vegetables from far away farms. This is done by establishing indoor vertical farms to grow vegetables in local neighbourhoods instead.
Lim is targeting to build 100,000 sq ft of indoor vertical farms in Malaysia this year to make Agroz the largest indoor vertical farm operator in Malaysia.
While it should seem like a no-brainer to support a move into the agriculture industry at a time like this, Lim notes that it is not all straightforward. A lot of stakeholders do not understand that smart farming is different from traditional farms.
“Malaysia does not have policies to support the use of advanced technologies for smart farming, urban farming and indoor vertical farming. So, existing special grants, incentives and loans are provided for the use of chemical fertilisers and pesticides for traditional farming but there are no grants, incentives and loans for the use of technology in smart farming, ” he says.
This makes it a challenge for the company to access ongoing assistance for the agriculture industry.
The lack of policy support and guidelines also make it difficult for them to get funding from financial institutions. Lim says most banks in Malaysia were not particularly supportive of indoor vertical farming as they do not understand these new modern, high-tech forms of farming.
Agroz is currently seeking to raise RM100mil through the issuance of redeemable convertible preference shares to fund its expansion.
Lim says the company has drawn interest from several investors, both local and foreign, and they are in the midst of evaluating some of these offers. He is, however, open to any other interest.
To sweeten the deal for potential investors, Lim is looking at exit plans in five years’ time, either through an initial public offering or via a trade sale to a special purpose acquisition company.
At the moment, Agroz has a small farm in Seri Kembangan, Selangor. It is in the midst of building a 3,000 sq ft farm in Sg Buloh and upgrading a commercial-scale indoor vertical farm in Shah Alam to 90,000 sq ft.
Lim believes Agroz’s indoor vertical farms will complement traditional farming.
“Customers who demand for higher quality will prefer to buy their vegetables from sources like Agroz, which delivers clean, fresh and quality vegetables from farms that you can see and are located within your neighbourhood.
“At the same time, we need to recognise that the market is huge with Malaysia importing over RM5bil worth of vegetables in 2019 alone. And this number is increasing.
“So it will take an entire industry of indoor vertical farmers to grow clean and fresh vegetables in farms within the city before we even make a dent in the traditional agriculture space. Taking even a 10% share, which is only RM500mil, of the multi-billion ringgit market would take some time, ” he says.
However, its efforts, and perhaps that of many other budding agritech companies that have popped up in recent times, are moving in the right direction.
Lim points out that Malaysia ranks 28th on the 2019 Global Food Security (GFS) Index, according to the Economist Group. Singapore, on the other hand, which hardly produces its own food, has topped the index two years in a row, in 2018 and 2019.
A myriad of advanced technologies to ensure that the methods and approach of growing food is repeatable, scalable and traceable to feed a growing population is key to achieving better sufficiency to meet domestic demands.
“We also aim to create hundreds of new high-valued jobs and generate income in our local communities heading into this post-Covid-19 era, ” Lim says.
In some countries, green jobs have been mulled over as a potential area to generate jobs to help with economic recovery. This could also be a space that policymakers could explore further.
Currently, Agroz’s produce is sold directly to consumers through a subscription programme and also supplied to neighbourhood grocers, eateries, restaurants and the hospitality industry.
The company is already growing 200kg of produce per month and will soon have the capacity to grow 1 tonne per day from the various farms already committed.
Once its 100,000 sq ft of indoor vertical farms is achieved, it is expected to produce 3 tonnes of vegetables every day.
Agroz has a current order book of RM5mil to license its technology including supply of its indoor vertical farm systems to warehouses and land asset owners as well as through supply of vegetable products to consumers and businesses. Lim says its got more orders in the pipeline.
TAGS / KEYWORDS:SME , Startup , Indoor Farming , Agroz ,
TOPIC: Corporate News SME
Columbia Vertical Farm Uses Technology To Cut Plastic Pollution And Boost Sustainability
The new packaging comes at no extra cost to the customer and will be cheaper in the long-run for Vertical Roots
Vertical Roots is the largest hydroponic container farm in the country. They grow and package lettuce varieties and have recently implemented a packaging process that reduces plastic with a resealable film. TRACY GLANTZ TGLANTZ@THESTATE.COM
With the use of agricultural technology, Vertical Roots farm in West Columbia created a packaging system for its leafy greens that cut down the company’s plastic usage by 30% and extends the shelf life of the lettuce.
In 2015, high school friends Andrew Hare and Matt Daniels created the idea for Vertical Roots, now the largest hydroponic container farm in the country. Hare is the general manager of the company and Daniels acts as the chief horticulturist.
The first Vertical Roots opened in Charleston and expanded with its second farm site in West Columbia in 2019. Vertical Roots parent company, AmplifiedAg, manufactures the container farms and farm technology of which Vertical Roots operates.
The farms are part of a growing industry called controlled environmental agriculture (CEA) that uses technology to ramp up nutrient-rich food production year around.
Hydroponics helps the farm uses 98% less water than traditional farming, according to Hare. Their technology creates an indoor environment to grow lettuce on the East Coast. Most lettuce in the U.S. comes from California and Arizona, where temperatures do not fluctuate much throughout the year, travelling 2,000 miles from farm to table. Vertical Roots offers a solution for local lettuce.
“Our mission is to revolutionize the way communities grow, distribute and consume food,” said Hare. As populations grow, Hare said the ability to produce enough food is a global concern.
VERTICAL ROOTS AGRICULTURAL INNOVATION
As a company committed to sustainability, Vertical Roots had to address its plastic usage and the consumer demand for environmentally friendly products.
“I think everyone can agree that the amount of plastic that’s consumed and used globally is a bit of a problem,” said Hare.
If Vertical Roots were to completely opt-out of using plastics, as much as 40% of the lettuce would be damaged in transportation to the retailers, Hare said. So the company decided to still use plastic containers in order to cut out food waste, but it changed the amount and type of plastic used.
By replacing the conventional “clamshell” plastic lids that you see on a container of lettuce at the grocery store, Vertical Roots cut down more than 30% of plastic usage by creating a resealable film lid. The new packaging comes at no extra cost to the customer and will be cheaper in the long-run for Vertical Roots, according to Hare.
The farm also uses recycled plastic that can also be recycled again after use. Tiny perforations in the film lid of the packaging allow air to leave the lettuce container and extends the product’s freshness, making Vertical Roots lettuce last around 14 days on the shelf.
“We tested respiration and condensation with each lettuce variety, and ultimately found that we could extend the freshness and shelf life of our salad mixes even more,” said Hare.
Vertical Roots, at the S.C. Farmer’s Market, is the largest hydroponic container farm in the country. They grow and package lettuce varieties. Tracy Glantz TGLANTZ@THESTATE.COM
GROWTH IN THE AGRICULTURAL TECHNOLOGY INDUSTRY
In the first three quarters of 2020, a record $754 million of venture capital was invested in the vertical farming industry, according to PitchBook data. This was a 34% increase from the entire previous year, Bloomberg reported in a January article.
A 2019 report from Global Market Insights showed that the vertical farming market size, or the number of potential customers or unit sales, surpassed $3 billion in 2018 and said it, “will exhibit a massive compound annual growth rate (CAGR) of over 27% from 2019 to 2026.”
In vertical farms, crops are harvested on several vertical layers indoors, where farmers can grow year-round by controlling light, temperature, water and other factors, according to the U.S. Department of Agriculture.
Vertical agriculture is also seen as a growing industry because it “could help increase food production and expand agricultural operations as the world’s population is projected to exceed 9 billion by 2050,” according to the USDA.
However, some are skeptical about the future of vertical farming for several reasons. The farms use LED light bulbs to grow crops, which require a lot of energy and money to operate.
Also, the farms mostly produce greens, which are low in calories because they take less water and light. The new farming technology is marketed as a way to combat world hunger, but in poorer countries, low-calorie greens are not as beneficial, according to Bloomberg.
THE FUTURE OF VERTICAL ROOTS
Despite a tough year due to COVID-19, Vertical Roots will open two more indoor, container farms in Georgia and Florida in 2021.
The company lost revenue from foodservice customers like restaurants, schools and universities during the pandemic, said Hare.
Those food service customers accounted for about half of Vertical Roots’ business, Hare said. Grocery store business stayed steady and even grew during the pandemic. As schools and restaurants are slowly reopening, Vertical Roots is gaining business back.
The West Columbia farm location produces about $1.5 million pounds of produce per year, said Hare. Vertical Roots lettuce is in 1,200 different grocery stores in 11 states, including Lowes Foods stores, Publix, Harris Teeter and Whole Foods Market chains.
Hare said the company is constantly working on sustainable initiatives, including figuring out a way to reduce light energy consumption by 20-25%, thinking about compostable packaging systems and finding ways to use less water at the farms.
In the future, Vertical Roots hopes to offer a larger variety of produce. The team is experimenting with growing foods like tomatoes, cucumbers, peppers, herbs and mushrooms to see if they could be viable products.
At 25,000 square feet, the world's first indoor vertical farm is also one of the largest farms. Located 120 miles south of Seoul, South Korea, fruits and vegetables grow without soil, bathed in light from pink LEDs. BY META VIERS
1 of 3
Vertical Roots, at the S.C. Farmer’s Market, is the largest hydroponic container farm in the country. They grow and package lettuce varieties. TRACY GLANTZ TGLANTZ@THESTATE.COM
Israeli Agritech Company, Vertical Field In UAE Project
Vertical Field develops vertical agricultural farms that enable crops to grow in the city
27 January 2021
Israeli agritech company Vertical Field, which specializes in vertical farming, has signed an agreement with Emirates Smart Solutions & Technologies (ESST) a company that develops innovative agricultural projects in the Persian Gulf, to deploy pilot vertical farms as a first stage to full-scale deployments in the United Arab Emirates.
Vertical Field develops vertical agricultural farms that enable crops to grow in the city. Vertical Field’s technology enables produce to grow on a bed of soil (geoponically) inside repurposed shipping containers. Vertical Field claims that its advanced technologies enable high-quality crops to grow quickly and efficiently in optimum conditions without the use of chemical fertilizers or pesticides. These customizable urban farms can grow a range of fresh crops for supermarkets, restaurants, urban farmer’s markets, and distribution centers. Vertical Field says that its technology is more efficient and less wasteful than conventional agricultural methods, using 90% less water, and growing precise quantities of produce in a controlled environment.
Produce inside Vertical Field’s containers can therefore grow 365 days a year, are not limited to seasonality constraints, weather conditions, extreme climate events, or geographic location. The farms are modular, expandable, and moveable, and can be managed automatically. Produce is grown in a sterile container with minimal human interference. Crops that are currently grown in the farm include: several varieties of lettuce, basil, parsley, kale, mint, and more, which are sold at competitive prices.
Under the UAE agreement, Vertical Field will conduct a pilot project that will ascertain the most suitable crops for the local market. The first stage of the project will be launched in the United Arab Emirates, and is expected to expand into a multimillion-dollar partnership that will include deployments in additional states of the Gulf region. The first farm will be installed in Umm Al Quwain as part of a research, development, and training center, which is expected to support additional projects in the rest of the Gulf states.
According to market research firm Markets and Markets, in 2020, the vertical farming industry reached $2.9 billion, and it is expected to reach $7.3 billion by 2025. Approximately 80% of the agricultural consumption in the Emirates is imported from around the world, equivalent to over $10 billion (2018). The rising costs of shipping food as well as an increased desire for food security and regional independence has played a strong role in the development of the ESST-Vertical Field partnership.
Vertical Field CEO Guy Elitzur said, "This collaborative project is a first-of-its-kind partnership that offers Vertical Field’s innovative agricultural technologies to the Emirates and the Gulf Region. The Makalde Group brings forty years of experience and wide knowledge in the field of agricultural inputs and resources and we bring innovative technology.
"Arid desert regions face many challenges surrounding the production of high-quality agricultural produce at low prices. With the help of various agricultural technologies and new developments we believe that we can successfully align the demands of the market with competitive prices without compromising quality- and most importantly with increased access and availability."
Maher Makalde, CEO and Partner of ESST said, "Our goal is to establish food security that is independent of imports and to develop a high-quality agricultural infrastructure that reaches the retail market."
Published by Globes, Israel business news - en.globes.co.il - on January 27, 2021
© Copyright of Globes Publisher Itonut (1983) Ltd. 2021
Hydroponic Indoor Farm Plans To Be Among First Tenants In Downtown Piqua's Zolo Building
It was strategically placed in front of the Zollinger's building, a 40,000-square-foot former grocery warehouse planned as a mixed-use development with 16 loft-style residential units, a roof deck, community market/kitchen incubator and co-working space.
Fifth Season Farm, founded by a local brother-sister duo, has launched a hydroponic indoor farm inside a shipping container along Main Street in downtown Piqua.
By John Bush – Senior Reporter, Dayton Business Journal
A unique farming business has set up shop in downtown Piqua, and if all goes to plan the concept will be among the first tenants in an historic building being redeveloped in the city core.
Fifth Season Farm, founded by brother-sister duo Britt Decker and Laura Jackson, launched a hydroponic indoor farm inside a shipping container along Main Street. It was strategically placed in front of the Zollinger's building, a 40,000-square-foot former grocery warehouse planned as a mixed-use development with 16 loft-style residential units, a roof deck, community market/kitchen incubator and co-working space.
While the farm has been operating there for months, the long-term intention is to occupy space inside the the century-old building, which will be renamed the "Zolo." Chris Schmiesing, Piqua's community and economic development director, said the community market concept fits well with Fifth Season's business, and would be a welcome addition to the building.
"Part of the Zolo concept is the community market space, where local growers and producers can come and put their product on the shelves and begin to grow their business," Schmiesing said. "We're really excited to have Fifth Season Farm in there because we think it really represents the kind of innovative, entrepreneurial activity we want to see more of."
Unlike some traditional farms, Fifth Season does not use pesticides or herbicides, and utilizes non-GMO seeds. Powerful LEDs create a specific light recipe for each plant, allowing control over size and shape. There is no dirt, meaning the crops are free of bugs. The hydroponic system uses 90% less water by recycling the nutrient rich infused water in a loop system. Since it is weather controlled, temperature, relative humidity and CO2 levels remain constant all year.
"It is a complete, self-contained unit," Decker said. "The products also have a much longer shelf life because they are harvested to order."
Fifth Season currently grows about half-a-dozen varieties of lettuce, as well as specialty greens such as Swiss chard and kale. Decker said they are also growing small root vegetables such as radishes.
Currently, Fifth Season offers delivery through its website. Orders can be delivered up to five miles from its farm location, where customers can also come to pick up their products. Fifth Season produce can also be found on the Miami County Locally Grown Virtual Market. Decker said they are in discussions with local grocery stores, restaurants and gyms to carry their product as well.
When their space in the Zolo building is ready, Decker said they plan to open a marketplace and pickup location inside. He added the entire reason they placed the farm in that location was to be ready for when the redevelopment project is complete.
In June 2020, the Piqua Planning Commission unanimously approved a zoning change that allows for residential use within the building. The rezoning was a big administrative hurdle the project needed to cross, but the project still needs to be fully financed. The project missed out on the latest round of Ohio Historic Preservation Tax Credits, though Schmiesing said additional funding sources are being finalized.
Gamble Associates, a Massachusetts-based urban design and planning firm, is taking the lead on the Zolo project. Gamble Associates Principal David Gamble previously said the interior build-out will take between nine and 10 months to complete once it gets started.
Assuming everything aligns, Gamble said this project will create a "critical mass" that could have ripple effects throughout the city of Piqua.
"Piqua, in my mind, has reached an inflection point," he said in July 2020. "While there may not be a lot of transformation to date, there's been a lot of good planning and the city has very good leadership. Piqua is due for that next phase of growth. We like working here, and we're excited about this opportunity and what it can do for the city."