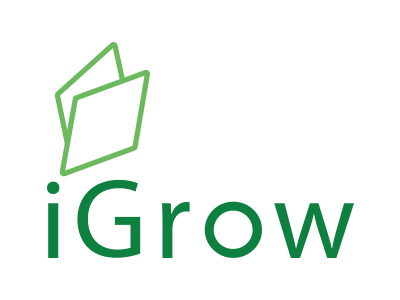
Welcome to iGrow News, Your Source for the World of Indoor Vertical Farming
VIDEO: Aquaponics Greenhouse Fueled By Renewable Energies
This is the Ekoponics system. The aquaponics greenhouse is built with an Ekodome Cosmos geodesic dome frame system, while the renewable energy station is made with an Ekodome Seed dome frame
This is the Ekoponics system. The aquaponics greenhouse is built with an Ekodome Cosmos geodesic dome frame system, while the renewable energy station is made with an Ekodome Seed dome frame.
Solar panels and vertical wind turbine-powered pumps provide energy to the system to recycle water and nutrients in a closed-loop system that provides productive and sustainable food production. It is still developing, but continuous R&D in aquaponics will help sustain healthy food production.
For more information:
Ekodome
www.ekodome.com
11 Aug 2021
USA: BOSTON - 'Space-Age Farming': Agtech Company Looks To Expand In Mass.
The company (Nasdaq: APPH) was founded in 2017 with the mission to modernize the way food is grown and delivered to large enterprises
By Miranda Perez - Inno Reporter
June 23, 2021
AppHarvest has a local office in Woburn and is looking to develop local tech centers under the direction of Chief Technology Officer Josh Lessing. AppHarvest
AppHarvest, a Kentucky-based, agriculture-tech startup, is looking to expand to Boston to further develop its tech-centered farming.
The company now has a local office in Woburn, and it's looking to develop local tech centers under the direction of its chief technology officer, Josh Lessing.
The company (Nasdaq: APPH) was founded in 2017 with the mission to modernize the way food is grown and delivered to large enterprises. It maintains indoor farms that operate year-round, using no pesticides to maintain freshness and relying on recycled rainwater to leverage sustainability.
“This brilliant technology, originally made in the Netherlands, where you could make food anywhere in the world, allows us to do it year-round, with 90% less water and with 30 times more yield per acre,” Lessing said.
The public company, which has 550 employees, is looking to “massively expand'' in upcoming projects in robotics and enterprise software for the agricultural industry.
In a statement regarding it's 2020 annual filing, the company said it a "pre-revenue state in 2020," and reported a net loss of $17.4 million, compared to $2.7 million for the year before.
AppHarvest has one fully-functional farm right now with two more being built. The goal is to have a dozen by 2025.
The existing farm is a 60-acre building, which Lessing describes as “almost like being inside of some combination of a 60-acre robot and its own world.” Inside is an entire ecosystem of insects that support the pollination of fruits and manage to keep the “bad bugs” away. The main focus is on tomatoes now, but Lessing says he plan to expand to other fruits and vegetables.
Watering is automatic, through robotic systems. Other systems are designed to handle specially designed supplemental lights.
“It's just remarkably space age farming,” Lessing said.
AppHarvest food is available in the top 25 grocery stores and in some food service locations such as Kroger and Wendy’s.
“If you talk to a farmer, there's an infinite amount of work that you can be doing at a farm and there's never enough time to get it done. AppHarvest frees us up to start doing more individualized crop care,” Lessing said.
USA: NEW JERSEY - Livingston Considers Resident's Sustainable Hydroponic Pilot Project Proposal
As the Township of Livingston continues to brainstorm ways to make the best use of its open spaces, Keith Hines and sustainable agriculture expert Tom Erickson recently proposed a hydroponic pilot project that would use a nutrient solution and water in lieu of soil for a community garden
By ELISE PHILLIPS MARGULIS
June 7, 2021
LIVINGSTON, NJ — As the Township of Livingston continues to brainstorm ways to make the best use of its open spaces, Keith Hines and sustainable agriculture expert Tom Erickson recently proposed a hydroponic pilot project that would use a nutrient solution and water in lieu of soil for a community garden.
After the duo’s initial proposal to implement the project at the Essex County Riker Hill Art Park fell through, the township is now looking into the possibility of doing so at the recently purchased Strahman Hill Park property.
Erickson recently presented a slideshow to the township illustrating how hydroponic technology works and demonstrating how hydroponic farming utilizes rain and solar power to grow healthy produce that can be donated to local food pantries.
“The project itself uses horticulture hydro-culture techniques to sustainably produce crops in an efficient organic manner with no impact to air, water or local environment, which is pretty important to us,” said Erickson, who also explained that hydroponics have a zero-carbon footprint. “We also plan on using the latest low-cost electronics to add a layer of control and monitoring that allows participation of the town administrators, fire, and police.”
According to Erickson, the hydroponic project could also provide unique educational opportunities for students interested in agricultural engineering and environmental sciences.
Erickson’s slideshow, much of which can be seen in the photos above, depicted a concept drawing of a greenhouse, plant-growing racks inside the greenhouse, the low-cost computer that would run the program, piping to transport the water and nutrient solution, sensors, a water pump, an aeration pump, a storage battery to operate the system at night and on rainy days, multiple solar panels and more.
He also demonstrated that easy-to-install solar kit power all water flow, aeration, lighting, monitoring, and security and that a basic, low-cost computer can monitor temperature, humidity, and liquid levels, security cameras, and sound or motion detectors.
“Our mission is to supplement the local food pantries in a sustainable, organic and efficient fashion with low environmental impact and potential for education,” said Erickson. “I think this has high potential to team up with the high school, the elementary school and open up doors to learning and training at the educational level.”
Hines, who is known in the Livingston area for his philanthropic endeavors, thanked the township council for considering a project that he feels would be important to the entire community.
“It's obviously incredibly high-tech stuff and really fascinating in terms of what can be accomplished with the technology and the fact that it's not going to have any footprint at all,” said Mayor Shawn Klein, who was impressed that the project has the potential to generate nutritious food for people who don't have access to it without causing problems with fertilizer or run off. “I think it sounds great, and hopefully we'll have a lot of success and be able to expand even in the same footprint as the county park or maybe even in town.”
To learn more or to view Hines and Erickson’s full presentation to the Livingston Township Council, CLICK HERE. (The slideshow can be found about 23 minutes into the hyperlinked video.)
CANADA: Quebec AI Processing Centers To Heat Gigantic Greenhouse Complex
A Quebec City entrepreneur, well known in the field of technology, is piloting a pharaonic project. Workers are working quietly on a large plot of land in Saint-Nicolas. The value of the total investment is in the billions of dollars
A Quebec City entrepreneur, well known in the field of technology, is piloting a pharaonic project. Workers are working quietly on a large plot of land in Saint-Nicolas. The value of the total investment is in the billions of dollars. And it would be only the first of a series of "campuses" at the cutting edge to be built on Quebec soil. And, there's greenhouses in it.
Developer Martin Bouchard, founder of the Copernic search engine and then of the 4Degree data centers, wants to build at least three high-intensity data processing complexes with thermal waste recovery, to which would be added a pole of applied innovation in artificial intelligence. The total estimated cost is close to 5 billion euros. Why that could be relevant for the horticultural industry? The business plan calls for the recovered heat being used to heat greenhouses. "We want to contribute to the province's food autonomy with a potential of 400 hectares of greenhouses for the first campus alone," he tells in an article on LaPresse.
Put the words artificial intelligence, innovation, circular economy, high-capacity computer servers, clean energy, greenhouse production, food autonomy; stir calmly and you will obtain the "Baiejamésienne" project on which Mr. Bouchard and his associates Vincent Thibault and Dany Perron have been working for three years on the QScale project.
QScale is a high-density data processing campus. The campuses seek to meet the needs of machine learning, which is in growing demand with the arrival of artificial intelligence in businesses. Consider the data calculations required to safely drive autonomous vehicles. Bouchard cites Tesla, Volkswagen, Pfizer and Goldman Sachs as potential clients.
The serial entrepreneur, along with private investors, has invested $30 million to start the project. The rest of the financial package will be revealed at the time of the official announcement. "We are working very hard to ensure that the ownership of the company remains entirely Quebec-based. "
The Quebec government is receptive to the project, La Presse has learned. Hydro-Quebec would have already said yes, assures Mr. Bouchard. The imprimatur of the monopoly of electricity distribution is essential because such a data center dedicated to artificial intelligence consumes twice as much power in a year as a city the size of Drummondville.
Construction has begun on the first campus located in Levis. Delivery is scheduled for November 2022. The daily newspaper Le Soleil recently outlined the project. QScale is planning a second branch in the Écoparc de Saint-Bruno-de-Montarville, on Montreal's South Shore, just behind the commuter train station.
With the heat, greenhouses are to be heated. "We want to contribute to the province's food autonomy with a potential of 400 hectares of greenhouses for the first campus alone," he insists. However, all the vegetable production in greenhouses is currently grown on 123 hectares. "We are in discussion with several players for this part of the project," says Bouchard. André Michaud, a consultant for Savoura, says he has never been contacted by QScale. He said he was puzzled when he saw the project outline.
We have a greenhouse robotization project using artificial intelligence to eventually automate physically demanding jobs," says Mr. Bouchard. In Levis, we have the adjacent farmland that corresponds to the equivalent of 80 soccer fields, enough to produce 2880 tons of raspberries and 83,200 tons of tomatoes. "
4 Jun 2021
VIDEOS: A Made-In-Canada Clean Energy Solution Wins Multiple Awards For Innovation
The Eavor-Loop is a closed system within which a proprietary working fluid is contained and circulated
Eavor’s technology consists of several Patent Pending innovations. The Eavor-Loop is a closed system within which a proprietary working fluid is contained and circulated. The working fluid is not fluid from a reservoir flowing into our wells, it is a fluid added to the closed-loop Eavor-Loop™ to create an efficient radiator, much like a vehicle radiator circulates fluid in a closed-loop to remove heat from a gasoline engine.
Eavor-Loop™ harvests heat from deep in the earth to be used for commercial heating applications (ex: greenhouses or district heating) or to be used to generate electricity using conventional heat to power engines. Eavor-Loop™ is an industrial-scale geothermal system that mitigates many of the issues with traditional geothermal systems, which rely upon using wells to produce brine from a subsurface aquifer.
The closed-loop is the key difference between Eavor-Loop™ and all traditional industrial-scale geothermal systems. Eavor-Loop™ is a buried-pipe system, which acts as a radiator or heat exchanger. It consists of connecting two vertical wells several kilometers deep with many horizontal multilateral wellbores several kilometers long. As these wellbores are sealed, a benign, environmentally friendly, working fluid is added to the closed-loop as a circulating fluid. This working fluid is contained within the system and isolated from the earth in the Eavor-Loop™. The wellbores act as pipes, not wells producing fluid from the earth.
The working fluid naturally circulates without requiring an external pump due to the thermosiphon effect of a hot fluid rising in the outlet well and a cool fluid falling in the inlet well. The working fluid contained in this closed-loop pipe system brings thermal energy to the surface where it is harvested for use in a commercial direct heat application or converted to electricity with a power generation module (heat engine).
Unlike heat pumps (or “geo-exchange”), which convert electricity to heat using very shallow wells, Eavor-Loop generates industrial-scale electricity or produces enough heat for the equivalent of 16,000 homes with a single installation.
An excellent new video by CNBC entitled 'How Geothermal Energy Could Power The Future' features Eavor CEO, John Redfern and several others in the modern geothermal industry such as Catherine Hickson of Geothermal Canada, Tim Latimer of Fervo Energy, Cindy Taff of Sage Geosystems and Joe Scherer of GreenFire Energy.
The video covers topics such as:
- What is Geothermal energy?
- Geothermal startups gain traction
- Major opportunity for oil and gas
- The future of geothermal
"Miles below the Earth’s surface, there’s enough thermal energy to power all of humanity for the foreseeable future. It’s called geothermal energy, and it’s poised to play an increasingly large role as a source of always available, renewable power. Now, there are a number of startups in the geothermal space, working to figure out how to access this heat in difficult-to-reach geographies, at a price point that makes sense. And it’s even gotten the attention of oil and gas industry giants, who are interested in greening their portfolios while sticking to their core competencies - extracting energy resources from deep within the Earth."
EUROPE: The Sustainable Farming Methods Helping Farmers Earn A Fair Income
Fair market conditions, sustainable farming, and quality standards are also some of the pillars of the EU's new Common Agricultural Policy, known as the CAP. Its future goals are to combine social, economic, and environmental approaches to create a sustainable model of European agriculture
The fruit and vegetable auction in Sint-Katelijne-Waver, Belgium, may look like a space mission control centre, but it's actually one of the most major auctions of its kind in Europe.
Every day up to 4000 tons of fresh produce are sold there. Fruit and vegetables grown by over a thousand farmers travel to its warehouses to then end up on our plates.
The farmers that sell in Sint-Katelijne-Waver are all part of the BelOrta network, one of Europe's largest fruit and vegetable selling cooperatives.
The BelOrta fruit and vegetable auctionSint - Katelijne-Waver, Belgium
The organization has strict production procedures to ensure good quality standards and prices. For growers, sustainable production also means a fair income.
Jo Lambrecht is a Sales and Marketing Manager for Belorta. He tells us that one of their goals is to get "the best possible price in the markets for the protection of growers". They also want to build consumer, buyer and grower trust to create "a long-term relationship between what happens on the field, what happens on the producer side and what happens at the consumer's home".
Fair market conditions, sustainable farming, and quality standards are also some of the pillars of the EU's new Common Agricultural Policy, known as the CAP.
Its future goals are to combine social, economic, and environmental approaches to create a sustainable model of European agriculture.
Two farms, that are part of the Belorta Network, have been able to change their production to make it more sustainable thanks to financial support from the CAP.
One of them is in the Belgian town of Putte. The thousands of tomatoes produced in the huge greenhouses there get exactly what they need.
The cogeneration system on the farm produces complementary energy which is released into the local grid. Thermal insulation screens help save heat at night, keeping the tomatoes at the right temperature for a lower cost. Natural methods also protect them from disease and the irrigation system ensures the most efficient use of water for their growth. Nothing goes to waste.
The tomato greehousePutte, Belgium
Kevin Pittoors the owner of the farm tells us "the excess water is collected and after it is purified, it is reused on the plants. So it's a closed cycle." They also use the maximum amount of rainwater in order to meet water requirements as efficiently as possible.
A LED lighting system, installed in the greenhouse, helps compensate for the lack of light during the winter months. Pittoors says the advantage of these lights is that "they consume less power", helping to "save energy" and providing "optimal light for the plants."
Why the CAP is key to agriculture
There are around 10 million farms in the EU. Some 22 million people regularly work in the sector.
Farmers' incomes are 40% lower
than those of people working in other sectors.
Weather and climate play a key role in farming
which makes it vulnerable to climate change.
Producing food takes time
so there is always a time gap between demand and production.
Source: European Commission
Farms of all sizes are playing an important role in the transition towards a more eco-friendly agriculture.
Sustainable solutions like those used in Putte's tomato production are also used on a family-owned strawberry farm in Halle.
The farm applies natural remedies to protect plants from disease as well as using new technology, like an autonomous robot that uses UV light to fight powdery mildew. It's a machine that helps reduce the use of pesticides.
The powdery mildew fighting robotHalle, Belgium
The strawberry farm tries to use a natural strategy as much as it can when fighting plant diseases.
Robin Colembie, a worker there, tells us that chemicals are always the last option. He feels that it's important to make an effort and move towards sustainable processes because it shows in the final product. "There is also a growing demand from consumers for more environmentally friendly and pesticide-free fruits".
Copyright euronews
USA: Zenat Begum Turned A Bustling Brooklyn Street Corner Into A Working Greenhouse
She reached out to Jasper Kerbs of the Cooper Union Garden Project and, with the help of several volunteers, the structure was erected in October of last year. The shop is utilizing one of the city’s outdoor vending permits and they’re in the midst of harvesting this month
The owner of Playground Coffee Shop transformed the cafe’s outdoor dining space into a project centered around care, creativity, and community
April 21, 2021
“I’m inviting people that I love to come and dress up the facade,” Zenat says of the greenhouse's verdant mural by artist Tiffany Baker. “I’m inviting people that I really respect to come and build these things because we deserve the best.”Image courtesy of Zenat Begum
To understand how a fully functioning greenhouse ended up at the busy intersection of Quincy Street and Bedford Avenue in Bed-Stuy, Brooklyn, it’s important to get to know Zenat Begum, the owner of Playground Coffee Shop.
Zenat opened the shop back in 2016, in a space that previously housed her father’s hardware store, and quickly expanded to include the Playground Annex, which houses a radio station and bookstore, as well as Playground Youth, a nonprofit organization dedicated to issues confronting the community, including literacy and food equity.
“I believe in Bed-Stuy. I believe in myself. I believe in the shop. I believe in the greenhouse,” says Playground Coffee Shop owner Zenat Begum. “These are things that are active radical attempts. We are imagining our futures because these things aren’t going to be built for us.”Image courtesy of Zenat Begum
Providing for the community is fundamental to each project that the Playground team takes on. “Every time we do something, we change and raise the bar of what should be done in our communities,” Zenat explains. “I’m talking about being able to keep implementing this really large notion and understanding of entrepreneurship into taking care of your communities.”
Shortly after the pandemic hit, Playground got to work on several mutual aid projects. The team established a take-one-leave-one library that distributes works exclusively by writers of color, assembled a network of volunteers distributing PPE and essential supplies at Black Lives Matter protests, and they worked with organizers to create a network of community fridges providing free produce 24 hours a day.
It was while working on the fridge project that the idea for the greenhouse began to crystalize, in realizing that fundamentally addressing the issues surrounding food sovereignty wasn’t, as she says, “as simple as just donating a fridge.”
Zenat cites the statistics: One in three kids in New York City are food insecure, and one in 10 in public schools experience homelessness. She probed further, looking at obesity and food deserts and gentrification. “Let’s reel it back: Why aren’t there programs that support Black and brown families who can’t support their children with adequate nourishment and nutrition?”
“It made me really frustrated. We need to have a plot of land that grows for this. We need to get an actual farm to be able to grow food for this,” Zenat says. And never having built a greenhouse before didn’t scare her off. “I don’t really have the tools,” she thought. “But I also know that, for the understanding that I have and the experience that I’ve had growing up in New York, I know what a New Yorker deserves, which is a lot more.”
She reached out to Jasper Kerbs of the Cooper Union Garden Project and, with the help of several volunteers, the structure was erected in October of last year. The shop is utilizing one of the city’s outdoor vending permits and they’re in the midst of harvesting this month.
When they’re able to resume programming, Zenat intends to teach kids in the neighborhood how to get involved and have plots so they can start growing together. “The most important thing about this is that this will be an opportunity for kids who live in Bed-Stuy to see food growing, to show them that there is life that starts at fertilizing and that we can be involved in the process of food distribution and food harvesting from the very beginning.”
“Our greenhouse is straight up on the street. I want people to see that these structures have to and should exist.”Image courtesy of Zenat Begum
And she acknowledges the responsibility and history that comes with this endeavor. “We’re on stolen land right now,” Zenat says. “We’re thinking about farming practices that date back to East Asia, which is where my family is from, and sharecropping that was implemented during the period just after slavery, which is one of the darkest times in history, period. But with all of those tragedies and travesties occurring, there is this sense of land and relationship that we have that we need to bring back to ourselves. It’s ancestral, of course, and it’s spiritual, but most importantly it’s territorial. Why is it that Black and brown people have a hard time with housing and food insecurity when we have literally created some of the most adequate and sophisticated food systems in the world? Our bodies are used to actually supply people with this type of food and nourishment.”
“So there’s many things that we’re addressing here, but I only hope that at surface level we’re talking about things that actually make a difference, which is ultimately feeding children.”
In true Playground style, the greenhouse is one of many initiatives in the works—from financial literacy courses and book clubs to bystander intervention trainings. Given Zenat’s dedication, there’s no doubt they’ll come to fruition. “The way that I love New York is so poetic. I’m like one of those gnarly girlfriends, ‘Did you eat today? Do you want water?’” She asks the city: “Did you eat today, New York? Do you want water? Do you want a pillow?”
If you’d like to support Playground Youth, there is a fundraiser underway for programming and operational costs.
Nature Fresh Farms Introduces New Program For Their Imperfect Produce
The Waste Me Nots program was recently created to leverage Nature Fresh Farms Tomatoes, Peppers, and Cucumbers that do not meet the criteria of their Quality Control team
Leamington, ON (April 13, 2021)
A recent loss-conscious program focuses on selling Nature Fresh Farms imperfect produce to reduce food waste.
The Waste Me Nots program was recently created to leverage Nature Fresh Farms Tomatoes, Peppers, and Cucumbers that do not meet the criteria of their Quality Control team. As most greenhouses hope to grow flawless quality produce, some product grows to be naturally bent or smaller in size. Although unique in shape and size, these vegetables still have the same nutritional value and flavor as their perfect counterparts. Nature Fresh Farms wants to put these pieces of produce in the spotlight, creating more of an opportunity to fight waste and give shoppers further access to nutritious foods.
‘We believe it’s important to ensure that nutritious and delicious produce does not go to waste,” shared Ray Wowryk, Director of Business Development. “By creating this program, we are helping our retailers with a ready-made waste reduction alternative.”
Since volume of this type of product is not predictable, the program cannot be guaranteed to supply specific quantities and will depend on the product grown. However, Nature Fresh Farm feels that the unpredictability is outweighed by the fact that their quality and freshness is worth rescuing and sharing with consumers, making the most of all their product grown.
“Sustainability is at the center of everything we do at Nature Fresh Farms. Not only does this encompass our packaging and growing processes but also that the food we grow gets utilized completely,” explained the Director of Sales, Matt Quiring. “The Waste Me Nots program helps us to reduce waste while allowing us to better service the price-focused shoppers looking for quality tasting products at a discounted price and let our retail partners bring in some incremental sales to the category.”
Nature Fresh Farms wants to bring more cost-effective options to its consumers and bring the focus back to the taste and freshness of the produce, not solely the look of it. They hope to break the cycle of imperfect food waste by offering discounted misshapen vegetables that there would normally not be a market for and expand the consumer’s knowledge of the type of produce they purchase.
-30-
About Nature Fresh Farms
Continuously expanding, Nature Fresh Farms has become one of the largest independent, vertically integrated greenhouse vegetable farms in North America. As a year-round grower with farms in Leamington, ON, Delta, OH, and Mexico, Nature Fresh Farms prides itself on consistently delivering exceptional flavor and quality to key retailers throughout North America, while continuing to innovate and introduce more viable and sustainable growing and packaging solutions.
SOURCE:
Nature Fresh Farms | info@naturefresh.ca T: 519 326 1111 | www.naturefresh.ca
The World’s First Autonomous Greenhouse Manager
Geert van der Wel started in the role of Autonomous Greenhouse Manager at Blue Radix. He represents the human support side of the Crop Controller service in addition to the smart algorithms that control greenhouses
07-04-2021 | Goedemorgen
Early February, Geert van der Wel started in the role of Autonomous Greenhouse Manager at Blue Radix. He represents the human support side of the Crop Controller service in addition to the smart algorithms that control greenhouses. Read more about how Geert helps customers and about his background. As he says himself: "I was almost literally born among tomatoes in De Lier, where my parents had a tomato greenhouse."
Name: Geert van der Wel
Home: I’ve been married to Tessa for 16 years and we have two children. We have lived in Burgundian West Brabant since 1998.
Childhood: Almost literally, I was born among the tomatoes in De Lier, where my parents had a tomato greenhouse.
Study: I completed Secondary Horticultural School in De Lier, and also undertook several (horticultural) studies.
Work experience: I worked in my parents’ tomato greenhouse right from my childhood. After finishing my studies my partner and I became owners of Kwekerij Polderwel for ten years, growing tomatoes on 2.5 hectares. We wound up this undertaking because of the construction of the A4 highway between Antwerp and Rotterdam. Then I did three years as a manager at the Nuijten plant nursery, and when this firm ceased trading I ended up at Nickerson-Zwaan in Made; it later became known as Hazera Seeds. For the first four years, I worked in the Planning & Control department, moving on to become Product Manager High-Tech Tomatoes for the final five years.
What can you do for growers as an Autonomous Greenhouse Manager?
“Blue Radix offers autonomous growing as a service. So alongside our smart algorithms controlling the greenhouse, our Crop Controller service also has a ‘human side’, and customers get daily support from an off-site Autonomous Greenhouse Manager (AGM). So as that AGM I’m constantly looking over the customer’s shoulder, and I’m their first point of contact. Right from the start, I guide clients intensively in taking their first steps into the world of algorithms. They are given an extensive onboarding program where they get explanations on the steps to autonomous growing, the operation of the algorithms, and the Crop Controller portal. I also monitor the management of the greenhouse continuously and discuss the progress on a regular basis, including through reports. My work experience has taken me through all the processes involved, from seed to the final product. This is what enables me to support our customers fully as AGM, to advise them, and to help them to realize their crop strategies.”
Blue Radix offers autonomous growing as a service; why is this important?
“Cultivation is the core business of every greenhouse company. To leave this completely to autonomous control requires a lot of trust from the customer. We are very aware that autonomous growing is still quite new and innovative. Providing good service with the support of the AGM lets us guide growers fully in working with algorithms. Our experience shows that customers are more likely to abandon their own processes and working methods step by step because there’s always someone monitoring the entire process.”
Describe your day. How do you monitor greenhouses worldwide?
“Every day I open the Crop Controller portal to see how the algorithms are behaving in terms of our various customers’ crop strategies. I contact the grower if any anomalies appear, or if there’s a technical issue I get in touch with the Blue Radix product developers. This also applies to feedback I receive from customers on how we can optimize Crop Controller still further.”
What do you like about your job? And what are your views on autonomous greenhouse management?
“In the horticultural world, it’s great to see that there’s a continuous search for innovations, and specifically for autonomous growing. I used sensors and digital tools on a small scale when I was a grower myself. But at that time I got very little guidance on how they worked and how to interpret it all. Now I use this experience to give our customers good information so that ultimately they’ll be able to grow autonomously in the best possible way!”
Got a question for Geert, or about autonomous growing generally?
Send us a message, and we’ll be happy to help you.
California-Based Greenhouse Grower To Invest $18 Million In Warner Robins, Georgia Indoor Farm
Pete’s is expected to use 24 acres within the county for its indoor growing facility that’s designed to require 90% less land and water than traditional farming
APRIL 08, 2021
Pete’s, a longtime, California-based greenhouse grower, is expected to invest $18 million in opening their first eastern U.S. indoor agriculture facility in Warner Robins in Peach County, Gov. Brian Kemp announced Thursday. COURTESY PETE'S
WARNER ROBINS
Pete’s, a longtime, California-based greenhouse grower, is expected to invest $18 million in opening their first eastern U.S. indoor agriculture facility in Warner Robins in Peach County, Gov. Brian Kemp announced Thursday.
“Agriculture is our top industry, and Pete’s will bring another game-changing, innovative, and sustainable indoor farming facility to Georgia as we continue to feed the world from the Peach State,” Kemp said in a news release. “Georgia’s No. 1 business climate, top-notch logistics network, and commitment to innovation continue to attract jobs and opportunities for hardworking Georgians, and I thank Pete’s for investing in Peach County and the surrounding region.”
Pete’s is expected to use 24 acres within the county for its indoor growing facility that’s designed to require 90% less land and water than traditional farming.
“The food we put into our bodies has environmental implications,” Pete’s CEO Brian Cook said in a news release. “Our ethos has always been centered around taking care of our team, our local communities, and the environment. Our goal with our new Georgia facility is to expand on our mission, helping to ensure that consumers in the Southeast have access to clean, sustainable greens that are grown close to home.”
The facility will be located in the Robins International Industrial Park, which is located within Peach County.
The development is expected to generate 15 jobs, according to the release.
The company plans to fill a variety of positions including general manager, production, growing, logistics, food safety, and office manager, as well as general administrative roles. To find out how to get hired, visit eatpetes.com for additional information.
“Peach County is thrilled to welcome Pete’s to Middle Georgia,” said B.J. Walker, executive director of the Peach County Development Authority. “This new advanced agricultural project not only brings new jobs and investment into our community but also highlights Peach County as a leader in high-tech, sustainable agriculture.”
The Robins International Industrial Park is designated “Georgia Ready for Accelerated Development” certified site, with “select” status, the release said.
The GRAD Select status is “an indication that a site has met or exceeded more rigorous certification requirements to attract development,” the release said.
Founded in 1970 under the name Hollandia Produce, Pete’s is an employee-owned and operated leader in hydroponically grown living lettuce and cress, according to the release.
Greenhouses Can Grow Lettuce And Generate Solar Power: Study
A recent study shows that lettuce can be grown in greenhouses that filter out wavelengths of light used to generate solar power, demonstrating the feasibility of using see-through solar panels in greenhouses to generate electricity
March 30, 2021
By Matt Shipman
A recent study shows that lettuce can be grown in greenhouses that filter out wavelengths of light used to generate solar power, demonstrating the feasibility of using see-through solar panels in greenhouses to generate electricity.
“We were a little surprised – there was no real reduction in plant growth or health,” says Heike Sederoff, co-corresponding author of the study and a professor of plant biology at North Carolina State University. “It means the idea of integrating transparent solar cells into greenhouses can be done.”
Because plants do not use all of the wavelengths of light for photosynthesis, researchers have explored the idea of creating semi-transparent organic solar cells that primarily absorb wavelengths of light that plants don’t rely on, and incorporating those solar cells into greenhouses. Earlier work from NC State focused on how much energy solar-powered greenhouses could produce. Depending on the design of the greenhouse, and where it is located, solar cells could make many greenhouses energy neutral – or even allow them to generate more power than they use.
But, until now, it wasn’t clear how these semi-transparent solar panels might affect greenhouse crops.
To address the issue, researchers grew crops of red leaf lettuce (Lactuca sativa) in greenhouse chambers for 30 days – from seed to full maturity. The growing conditions, from temperature and water to fertilizer and CO2 concentration, were all constant – except for light.
A control group of lettuces was exposed to the full spectrum of white light. The rest of the lettuces were divided into three experimental groups. Each of those groups was exposed to light through different types of filters that absorbed wavelengths of light equivalent to what different types of semi-transparent solar cells would absorb.
“The total amount of light incident on the filters was the same, but the colour composition of that light was different for each of the experimental groups,” says Harald Ade, co-corresponding author of the study and the Goodnight Innovation Distinguished Professor of Physics at NC State.
“Specifically, we manipulated the ratio of blue light to red light in all three filters to see how it affected plant growth,” Sederoff says.
To determine the effect of removing various wavelengths of light, the researchers assessed a host of plant characteristics. For example, the researchers paid close attention to visible characteristics that are important to growers, grocers, and consumers, such as leaf number, leaf size, and how much the lettuces weighed. But they also assessed markers of plant health and nutritional quality, such as how much CO2 the plants absorbed and the levels of various antioxidants.
“Not only did we find no meaningful difference between the control group and the experimental groups, we also didn’t find any significant difference between the different filters,” says Brendan O’Connor, co-corresponding author of the study and an associate professor of mechanical and aerospace engineering at NC State.
“There is also forthcoming work that delves into greater detail about the ways in which harvesting various wavelengths of light affects biological processes for lettuces, tomatoes and other crops,” Sederoff says.
“This is promising for the future of solar-powered greenhouses,” Ade says. “Getting growers to use this technology would be a tough argument if there was a loss of productivity. But now it is a simple economic argument about whether the investment in new greenhouse technology would be offset by energy production and savings.”
“Based on the number of people who have contacted me about solar-powered greenhouses when we’ve published previous work in this space, there is a lot of interest from many growers,” O’Connor says. “I think that interest is only going to grow. We’ve seen enough proof-of-concept prototypes to know this technology is feasible in principle, we just need to see a company take the leap and begin producing to scale.”
About this article:
The paper, “Balancing Crop Production and Energy Harvesting in Organic Solar Powered Greenhouses,” appears in the journal Cell Reports Physical Science. Co-lead authors of the paper are NC State Ph.D. students Melodi Charles and Eshwar Ravishankar. The paper was co-authored by Yuan Xiong, a research assistant at NC State; Reece Henry and Ronald Booth, Ph. D. students at NC State; Jennifer Swift, John Calero and Sam Cho, technicians at NC State; Taesoo Kim, a research scientist at NC State; Yunpeng Qin and Carr Hoi Yi Ho, postdoctoral researchers at NC State; Franky So, Walter and Ida Freeman Distinguished Professor of Materials Science and Engineering at NC State; Aram Amassian, an associate professor of materials science and engineering at NC State; Carole Saravitz, a research associate professor of plant biology at NC State; Jeromy Rech and Wei You of the University of North Carolina at Chapel Hill; and Alex H. Balzer and Natalie Stingelin of the Georgia Institute of Technology.
Why The 'Tesla Of Strawberries' Cost $5 Each
"This is an oh my god berry," one Omakase berry enthusiast gushed in Oishii's promotional Instagram video
BY HANNA CLAESON
MARCH 17, 2021
Why does the "Tesla of strawberries" cost $5 each? "This is an oh my god berry," one Omakase berry enthusiast gushed in Oishii's promotional Instagram video. To give you a more precise idea: Oishii's strawberries, berries that the company's CEO, Hiroki Koga, calls the "Tesla of strawberries" or the "happiest strawberries that you can find on this planet," are sold in three-packs (via Food Navigator and Instagram). Oishii suggests you pair your first "with a sip of perfectly brewed Japanese Oolong Tea," you're second with "a bite of creamy, bloomy rind cheese" and your third "with a glass of natural wine."
The whole experience will cost you at least four McDonald's Happy Meals; be prepared to dish out between $15.00 and $18.75 for these strawberries (they retail, says Grub Street, at between $5.00 and $6.25 a pop, depending on size) in addition to your tea, cheese, and alcohol investment.
If you do buy an Omakase berry, you shouldn't wait to eat it. Oishii, Time reports, guarantees that upon purchase, their strawberries will have been harvested and delivered on the same day to ensure that each berry is perfectly, exquisitely ripe. The company's farmers are trained, intensively, to identify the optimum "shade of red" (via Instagram). "When you bite into it, the aroma just spreads into your mouth," Koga told NPR. "Our customers say when they leave a tray of our strawberry in their room, and they come back after two or three minutes, the entire room smells like strawberry."
The science behind the "happiest strawberries on the planet"
When Oishii's CEO moved to the United States and tasted strawberries here, he was crestfallen. "It almost reminded me of cucumbers," he told NPR. So Koga traveled back to Japan and taste-tested nearly 50 varieties of strawberries before he settled on the one he'd grow in his vertical farm in New Jersey, a 15-minute drive from New York City. The variety Koga painstakingly selected contains twice as much sugar as any-old-American-supermarket strawberry. Besides that, Oishi promises "an airier texture and unexposed seeds."
To achieve perfection, Koga relied on Japanese experts to simulate the weather conditions of a "perfect day in Japan." And he doesn't simply control the temperature in his vertical farm, he also regulates "humidity and levels of CO2 and wind speed" (via NPR). Additionally, with the help of an AI machine, real, live bees pollinate the farm's strawberry flowers. Oishi claims that it's the first indoor vertical farm to achieve such natural pollination (via Instagram). The result, says Grub Street's Adam Platt, is a "diabolically uniform" berries, "you would call [them] monotonous, except they're really quite delicious."
For now, you'll only be able to try these strawberries with non-cucumber-like taste profiles if you have easy access to Manhattan. But a recent $50 million investment into Oishi may soon change that. Koga, according to Food Navigator, has already developed simpler-to-grow, cheaper, grocery-friendly strawberry varieties. He swears they have similar taste profiles to the original Omakase berry.
VIDEOS: AppHarvest CEO On Building The Third Wave of Sustainable Infrastructure
AppHarvest founder and CEO Jonathan Webb broke down what goals the agriculture technology is seeking to achieve by building a homegrown food supply in the U.S.
AppHarvest founder and CEO Jonathan Webb broke down what goals the agriculture technology is seeking to achieve by building a homegrown food supply in the U.S.
BERMUDA: Government Issues Vertical Farming Call
The Government has urged companies interested in bringing vertical farming to Bermuda to step forward through a new request for information
March 31, 2021
The Government has urged companies interested in bringing vertical farming to Bermuda to step forward through a new request for information.
The RFI calls for expressions of interest for parties who want to launch a commercial vertical farming operation “founded on principles of sustainability and environmentally friendly technology”.
Produce would be expected to be herbicide, fungicide, and pesticide-free, along with non-genetically modified.
The submission deadline for the RFI is 5 pm on Wednesday, March 31.
Submissions must include financial projections including sales volumes and corresponding revenue and relevant costs.
Wayne Furbert, the Minister for the Cabinet Office, said in November the Government had been working with US firm AeroFarms to “design and implement a vertical farming facility in Bermuda”.
Asked what the RFI meant for the relationship between the Government and AeroFarms, a spokeswoman for the Cabinet Office said the RFI was put out as part of the office’s due diligence efforts.
She said: “Through an RFI, the Government is seeking to determine if other interested parties were either contemplating or were in the process of producing commercial vertical farming in Bermuda.
“Interested entities who wish to engage further about this exciting, innovative, and environmentally sustainable project should visit www.gov.bm/procurement-notices.”
Vertical farming involves the production of crops in a controlled environment, usually indoors, using techniques such as hydroponics instead of soil and the crops grow in stacked layers.
The Government said last November that it was close to finalizing plans to bring a vertical farm to the island to help meet Bermuda’s demand for fresh produce.
Mr. Furbert said at the time the plan could reduce the cost of food production in Bermuda and generate 30 jobs.
He added that the proposal would be put to the Cabinet Committee for Economic Development later that month – but no further announcements have been made.
Vertical Farms vs Greenhouses: Energy and LED Costs And Differences [Part 2 of 5]
Lighting is one of the biggest expenses for a vertical farm, for obvious reasons – each layer in the farm needs its own LED “suns.” Agritecture Designer, a consulting software created by Gordon-Smith’s company, estimates the need at roughly 10 LEDs per square meter
Part 2 of 5] This is the second post in a 5-part series on the differences between vertical farms and greenhouses, and the considerations that will help farming entrepreneurs decide which is right for their situation.
Last week, in the first article of this series, we discussed the basic differences between vertical farms and greenhouses, including why location is such an important factor in the decision. In short: The location of a farm governs how much space will be available for it, and the source of the energy it will use.
That last part is what you might call “the elephant in the room” when it comes to indoor farming: Energy demand, and the main reason we care about it – carbon emissions. So let’s talk about that today.
Carbon Footprint Factors: Electricity (But Not Only)
One of the leading critiques of vertical farming is that replacing natural sunlight and open-air with LED bulbs and climate control requires electricity – lots of it.
“If the source of the energy is not renewable,” points out Henry Gordon-Smith, the CEO of Agritecture, an independent consultancy that helps clients decide between vertical farms and greenhouses, “Then vertical farms have enormously more carbon footprint than greenhouses.”
But the opposite is also true – where renewables are available, vertical farming can greatly reduce the carbon footprint of foods that are normally trucked long distances, or flown in from overseas.
For example, “Norway could be huge for vertical farming, because they just have so much cheap, renewable energy,” Gordon-Smith suggested.
When you tally the emissions reductions from shorter transport distances, the reduction in fertilizer use (fertilizer production is highly carbon-intense, and Controlled Environment Agriculture uses it much more efficiently than outdoor farms), plus the reduction in food waste, it’s clear that artificial light and conditioned air inside vertical farms are not the only carbon footprint factors to consider.
Bringing the Sun Indoors: Changing Electricity Costs for Farms
Lighting is one of the biggest expenses for a vertical farm, for obvious reasons – each layer in the farm needs its own LED “suns.” Agritecture Designer, a consulting software created by Gordon-Smith’s company, estimates the need at roughly 10 LEDs per square meter.
That’s a useful figure to get started, but given the variability between types of LEDs, a more precise estimate would be about 100 watts of LED power per square meter, according to Gus van der Feltz, another CEA industry expert. Van der Feltz is a co-founder and Board Member of Farmtech Society in Belgium, and project leader for Fieldlab Vertical Farming in the Netherlands.
With these lamps operating 12 to 18 hours a day in most vertical farms, the power usage from LEDs accounts for 50 to 65% of the electricity bill.
The exact amount depends on several factors: The relative efficiency of the LEDs used, compared with the efficiency of other systems in the farm (such as climate control), as well as the light requirements of each individual crop. (For example, the total electricity required for growing light-loving strawberries in an iFarm, for example, is about 117 kWh per month for each square meter of growing space, while arugula needs only about 52 kWh.)
But whether you opt for a greenhouse or a vertical farm, you’ll be growing local produce, which means your farm may be eligible for subsidies or another form of reduced electricity rate. Be sure to check with your local government and electricity providers.
It’s also important to note that greenhouses increasingly rely on LEDs as well, especially during winter in northern climates.
This may be only supplemental light, and it will vary with the location, seasonality, and how much light each crop requires – but greenhouses are still not as energy-intensive as vertical farms.
“It takes a lot of energy to produce food (with vertical farms),” says Ramin Ebrahimnejad, vice-chair of the Association for Vertical Farming, and an expert on multiple types of urban farming.
“But,” he adds, “most vertical farms in the developed world already use renewable energy. In the long term, that’s not going to be a challenge for the industry”.
As our electricity sources become more renewable (and as LED technology improves, as we’ll discuss below) energy-intense vertical farming will become both more sustainable – less carbon-intense – and more affordable.
And we can see this evolution happening in real-time: In 2020, Europe produced more electricity from renewables than from fossil fuels for the first time.
The Cost of LEDs for Vertical Farms vs Greenhouses
LEDs themselves are another major OpEx factor in vertical farming. And even though the cost per bulb varies widely, along with the efficiency, the LEDs in a vertical farm generally have to be replaced every five to 10 years, according to the Agritecture Designer software.
However, just as the cost and carbon footprint of electricity are becoming less of a hurdle for indoor farms, the LED situation is also evolving quickly.
An idea that’s become a modern certainty is that technology gets cheaper over time. As the environmental economist William Nordhaus studied in the 1990s, the declining cost of light over the centuries – from candles, to oil lamps, to ever-more-efficient light bulbs – has been changing the world and fueling innovation for millennia.
Something similar is happening with LEDs – up to a point. Moore’s Law famously predicted computing power doubling every year, and Haitz’s Law now forecasts that the cost per lumen for LED light will fall by a factor of 10 each decade, while the light produced increases 20-fold.
However, as Van der Feltz points out, this cannot continue forever and is more limited by the laws of physics than Moore’s Law. Currently, a well-designed horticultural LED system can be up to about 55% efficient – meaning 55% of the energy put in becomes photons, which plants use to grow, and 45% becomes heat. Fifty-five percent efficiency is already impressive when compared with incandescent light bulbs, for example, where energy input produces 5% light and 95% heat.
But still, for the purpose of CEA and especially in vertical farms, the remaining 45% of the energy that becomes heat is often – though not always – useless.
“In greenhouses,” Van der Feltz explains, “the additional heat is typically not all bad. Especially since auxiliary greenhouse lighting is mostly used in the darker and cooler winter months, and there are usually plenty of options for ventilation in case it gets too warm.”
But vertical farms heat up quickly, and as closed systems where opening a window is not an option, any extra heat from LEDs must be balanced with air conditioning or creatively repurposed. Van der Feltz says some indoor farms have been designed to divert excess heat to warm an adjacent building, for example.
So LED performance can still improve marginally, but not exponentially. Van der Feltz says experts estimate that another 25% efficiency improvement is possible, but LEDs will never be able to produce light energy out of thin air.
Whatever the limits of Haitz’s Law, it’s still true that while electricity and LED light bulbs are the most expensive part of a vertical farm today, they’re also the area where improvement is most imminent. (Innovation, and the laws of supply and demand, are constantly bringing down the costs of both, regardless of how much efficiency improvement is still technologically possible.) So operating a vertical farm should still become increasingly affordable over time.
Improved technology and reduced costs for LEDs are especially good news for the potential to grow even more crops in vertical farms, as different plants use different parts of the light spectrum.
iFarm is already a leader in the industry when it comes to research and development for expanding the crop selection available to vertical farmers. As LED technology improves, we’ll be able to take those efforts even further.
Other Energy Costs: Climate Control Needs in Vertical Farms vs. Greenhouses
The high energy costs of lighting a vertical farm are obvious, but the demands of climate control are often not as clear.
Since vertical farms are closed systems, with little to no air exchanged with the outside, they must be constantly cooled and dehumidified. About 20% of the electricity used on a vertical farm is for air conditioning, while dehumidifiers account for 10%.
The need for both of these increases with each layer added to a vertical farm, in order to counter the effects of plants transpiring and increasing the heat and humidity of the system.
In temperate regions, greenhouses can save energy by using natural ventilation, as the Agritecture Designer program explains: Sidewalls can roll up to allow cool air in, while hot air escapes through vents at the top of the greenhouse. Greenhouses can also opt for an evaporative cooling system, which is still more energy efficient than a fully climate-controlled system but does add humidity – another element to be controlled.
But it’s also important to remember that greenhouses are more sensitive to outside temperatures, and therefore, the operational expenses of climate control and/or the time needed for crops to mature will vary more than they will with vertical farms – especially in cold, Northern climates.
Next, in Part 3, we’ll discuss additional cost considerations for vertical farms and greenhouses, beyond electricity.
To learn more about starting a profitable vertical farming business, reach out to our friendly team at iFarm today!
Learn more
09.03.2021
Vertical Farms vs Greenhouses – The First Consideration: Location
When and where to use a vertical farm versus a greenhouse, and what factors – both economic and environmental – make the difference.
In just the past decade or so, sustainable farming has seen a high-tech makeover in the form of Controlled Environment Agriculture, or CEA, which consists of two main technologies: Vertical farms and greenhouses.
When it comes to feeding the world, it’s not a choice between vertical farms or greenhouses. We’ll need both to feed our growing global population with healthy, sustainable food, and we need to understand the ideal situation for each.
But as a business decision, it often is a choice between the two – and that’s what we hope to explain in this five-part series of articles: When and where to use a vertical farm versus a greenhouse, and what factors – both economic and environmental – make the difference.
In this first post, we’ll cover the basic differences between vertical farms and greenhouses, and why location matters so much when deciding between the two. Then stay tuned because, in the next articles, we’ll dive deeper into energy and lighting costs, automation and other expenses, environmental and crop considerations, and finally, the future of farming.
Vertical Farms vs Greenhouses: The Basics
The two technologies are often confused, but there are significant differences between them in resource use, cost, output, and, perhaps most importantly, the ideal locations for each.
Greenhouses are the more traditional technology that you’re probably familiar with: A single layer of crops, planted inside an enclosed space with walls and a ceiling made of glass or plastic to allow natural light in. They’re semi-controlled environments.
Vertical farms, on the other hand, are a much more recent invention using trays of usually hydroponic plants, stacked in floor-to-ceiling towers, with LED lights illuminating each layer, and climate control constantly adjusting the temperature, humidity and more.
In the upcoming articles in this series, we’ll dive into each part of these differences in more detail. But for now, let’s start with the first question entrepreneurs always need answering: The price tag.
Henry Gordon-Smith is the CEO of Agritecture, an independent consultancy and software creator that helps clients decide between the two technologies. As he puts it, “Vertical farming represents the most expensive, most controlled form of agriculture.”
At first blush, vertical farms are, in fact, shockingly more expensive than greenhouses – six to 10 times as costly. Gordon-Smith says vertical farming costs 2,200 to 2,600 Euro per square meter of cultivation bed space, while high-tech greenhouses cost 250 to 350 Euro per square meter of cultivation space.
Both offer a year-round source of fresh, pesticide-free, locally-grown produce, which provides better nutrition than the same foods that arrive from far away.
But what else do farmers, entrepreneurs, and investors get for all the added expense of vertical farming?
The answer is pretty simple: A more compact farm with more production per square meter, less water use, and more control over both quantity and quality. (With iFarm, this predictability is part of the package, in the form of a guaranteed yield within a precise time frame.)
For some entrepreneurs or municipalities, the cachet of implementing a high-tech farming technique that’s only been in use for less than a decade is also a factor in favour of vertical farming. But most often, the choice comes down to location.
The Ideal Location for a Vertical Farm versus a Greenhouse
The first step in determining the feasibility of building a vertical farm or greenhouse is to look at the drivers and constraints – many of which are simply location-based.
Places with limited space, such as dense urban areas, and limited access to fresh water are ideal for vertical farms. Doubly so if they have access to low-cost, renewable energy, and if they’re near a market with high demand for the crops vertical farms excel at producing: Leafy-greens, micro-greens, herbs and berries grown locally, without pesticides.
But in areas with unlimited space, lots of natural sunlight, and high-cost and/or high-carbon electricity, greenhouses may be the better option and the extra expenses of vertical farming might not make sense.
How these considerations apply in broad regions of the world is illustrated below:
Funding Now Available To Help Farmers Withe FMSA
Farmers are working to improve food safety on the farm, and prepare for Food Safety Modernization Act (FSMA) inspections, but this requires both assistance and resources
February 10, 2021
A hoop house with tomatoes and peppers grown in New Mexico. Photo Credit: USDA Photo by Bob Nichols.
Farmers are working to improve food safety on the farm, and prepare for Food Safety Modernization Act (FSMA) inspections, but this requires both assistance and resources. We are excited that the Food Safety Outreach Program (FSOP) applications have just opened up and will provide organizations with funding to assist and help farmers and small food businesses with both FSMA and food safety.
FSOP is a federal grants program that funds community-based organizations, non-governmental organizations, cooperative extension, and local, state, and tribal governments’ programs focused on food safety and FSMA. The U.S. Department of Agriculture (USDA) National Institute of Food and Agriculture (NIFA) recently announced $9.6 million in FSOP grant funding this year – the most funding ever available and an increase of almost $2 million from last year.
The deadline for applications is Thursday, April 1, 2021.
Application Details
FSOP projects should focus on outreach, education, and assistance for farmers and small processors around food safety practices and the new FSMA rules. There are two types of projects eligible organizations can pursue to receive FSOP funding: Community Outreach and Collaborative Education and Training Projects. There is no match requirement.
Community Outreach Projects
FSOP will once again offer Community Outreach Projects, to support the development of new food safety programs and to help groups build capacity to address the needs of their communities. Awards can be between $80,000 and $150,000 for projects lasting up to two years. Community Outreach Projects must:
Create, implement or expand food safety education to niche, underserved, or non-traditional audiences.
Be led by a team with a record of strong community partnerships and working with others to educate target audiences.
Create and implement a customized food safety training and outreach program for various types of farms or food processors, including those working with conservation systems, sustainable businesses, and organic food producers.
Collaborative Education and Training Projects
Collaborative Education and Training Projects aim to fund state-wide, multi-state, or multi-county food safety training projects. Grant awards are available for $200,000 to $400,000 for projects up to three years. These projects must:
Be led by a project team with a track record of community partnerships and serving the educational needs of the target audiences.
Create and execute food safety education and outreach for various types of farms or food processors, including those working with conservation systems, sustainable businesses, and organic food producers.
Additional Funds Available for Outreach to Communities of Color
An additional $150,000 is available for applications to either project type that increase outreach to communities of color through the Collaborative Engagement Supplements. Organizations applying for this supplemental support must include a significant collaboration with either one or more of the following universities, colleges, or organizations: 1890s, 1994s, Insular Areas, Alaska Native-Serving and Native Hawaiian-Serving (ANNH), Hispanic Serving Agricultural Colleges and Universities (HSACU), and community-based organizations serving socially disadvantaged populations.
Regional Centers Funds
There is also funding available for the four regional centers focusing on food safety and FSMA. Current centers include:
Southern Region: University of Florida (also “Lead Regional Center”)
Western Region: Oregon State University
North Central Region: Iowa State University
Northeast Region: University of Vermont
Program Changes for FY 2021
The FSOP RFA changes highlight a few recommendations the National Sustainable Agriculture Coalition requested, and we are thankful for NIFA’s continued partnership, and efforts to ensure these changes.
NIFA clarified that the additional Collaborative Engagement Supplements must be in direct partnership with a Minority-Serving Institution or an organization working to serve farmers of color that have been historically underserved, and that the proposed budget must adequately reflect this partnership. NSAC appreciates this clarity and looks forward to further analyzing the racial equity impact of FSOP grants.
NSAC is also excited about the new requirements for Regional Centers to partner with an 1890, 1994, ANNH, HSACUs and/or community-based organizations serving socially-disadvantaged populations within their region, which will help ensure outreach and resources to farmers of color continues to be prioritized.
NSAC also appreciates the clarity that Community Outreach Projects can be used for FSMA training for the organization’s staff with minimal food safety experience and that organizations must have relationships with the target audience.
Upcoming FSOP Webinar for Tribal Staff
On Friday, February 19, 2021, from 2:00-3:00 p.m. Eastern Time the United South and Eastern Tribes, in partnership with Intertribal Agriculture Council, Indigenous Food and Agriculture Initiative, National Sustainable Agriculture Coalition, and National Institute of Food and Agriculture, will be hosting a FSOP webinar for anyone who works with indigenous producers. For more information, and to register for the webinar, click here.
Additional Resources
For additional application details and requirements, see the FY 2021 Request for Applications.
Additional information is also available via Grants.gov and on the NIFA FSOP webpage.
You can read more about analyzing FSOP awards through an equity lens here.
You can also learn more about FSOP through the National Sustainable Agriculture Coalition’s Grassroots Guide to the Farm Bill.
Tips On How To Set Up Large Hydroponics Farms
The need for large-scale hydroponics farms will increase as urban areas get more populated each year
The need for large-scale hydroponics farms will increase as urban areas get more populated each year. Hydroponics is an innovative farming method that will solve present and future issues surrounding urban areas. Operators of large-scale hydroponics farms can sell their goods to local restaurants, businesses, and individuals so people can get their food in the same city rather than from rural farming areas. This article is going to cover the basics of how to set up a large-scale hydroponics farm.
Step 1: Flesh Out Your Business Idea
Great, you want to start a hydroponics farm. But you’ll need to plan out your business venture to ensure it is set up for success! Configure the costs associated with starting a hydroponics farm, the ongoing costs. Who’s going to be your target market? Are you trying to sell to individuals, grocery stores, or local restaurants? How are you planning to sell your products? In bulk? What is the name of your business? Does it align with your company’s values and beliefs?
Step 2: Choose a Location
When it comes to a large-scale hydroponics farm, you’ll need to decide where you want to set up shop. Since the future of farming is appealing to major cities, you may want to set up your business nearby or inside a major city. The location of your business also depends on your target audiences.
Step 3: Decide What Crops You Want to Grow
Choosing the crops you want to grow is one of the most critical factors for your hydroponics farm. Check to see if there are other hydroponics farms in the area, and if so, what are they selling? See if you can offer a product that’s not only easy to grow but also will have demand amongst your audiences. Are you planning on growing one single crop to cut costs, or do you want to grow a variety of crops to appeal to various target markets?
Step 4: Pick a Hydroponics Growing System
Look at the space you’re planning to have your hydroponics farm in and determine what kind of system will work best depending on the location and the crop. If you’re growing crops like lettuce or spinach, then an NFT setup will suffice because these crops grow fast and short, which allows for easy pickings. Larger crops such as tomatoes or fruits will benefit from vertical hydroponics growing systems. Compare the prices for various hydroponics growing systems depending on the materials, crops, location, and setup.
Step 5: Lighting
Now you’ll want to determine the light source to use to grow your plants. Lighting can lead to expensive costs, especially when powering large-scale hydroponics farms. From LEDs to HID lamps to HPS bulbs, lighting is an important factor in hydroponics farming. Each lighting source has its pros and cons, and you’ll need to study each one to determine which option best suits your needs.
Hydroponics farms are the key to the future of farming. To learn more about hydroponics and farming, subscribe to the Nick Greens YouTube channel and join our microgreens group on Facebook. We look forward to helping you reach your goals!
#hydroponicsfarm #hydroponicsfarming #hydroponicsgrowing #hydroponicfarm #hydroponicfarming
Polygreens Podcast Episode: 010 - Hydroponic Nutrient Solution
In this podcast, we’re going to discuss watering plants so that you can apply the technique to your own crops
When it comes to hydroponic nutrient solution, there are various opinions saying it’s better to use carbon filter water while others claim it’s best to use reverse osmosis water. When it comes to feeding plants, the main goal is to avoid any chances of root rot. In this podcast, we’re going to discuss watering plants so that you can apply the technique to your own crops.
Listen
Nick Greens The Nick Greens Grow Team has participated in many changes since they started developing indoor controlled agricultural environments in 2010. Our goal is to expand the vertical farming industry by helping ag-entrepreneurs manage their businesses better, avoid common mistakes, and improve crop yields based on what we have observed and developed over the past decade.
YouTube
Year-Round Under-Glass Herb Cultivation In The Heart of Berlin
ECF Farmsystems uses innovative LED lighting solutions from Fluence for today’s herb cultivation in the heart of Berlin
Urban Farming Using LEDs From Fluence by OSRAM
ECF Farmsystems uses innovative LED lighting solutions from Fluence for today’s herb cultivation in the heart of Berlin. An innovative urban farm, ECF Farm Berlin (ECF Farmsystems) uses techniques for greenhouse and vertical cultivation of basil. The farm also uses aquaponics to naturally fertilize the crops, the produce of which then goes to Rewe, Germany's second-largest supermarket chain.
Less space and more production is the name of the game at ECF Farmsystems: comprehensive lighting solutions, from growing to greenhouse culture, enable the year-round production of uniform, aromatic basil plants.
Modern agriculture thanks to LED lighting / Image: Osram
Urban cultivation from seed to finished product
On-site propagation on VertiCCs, a racking system for vertical cultivation developed by ECF Farmsystems, increases production by 35% with the same footprint and optimized supply chain from seed to finished product.
The system also ensures consistent, uniform products. This is because ECF Farmsystems completely controls the entire growing cycle with less pest infestation and more accurate yield forecasting. In addition, the VYPR lighting systems offer higher-quality light spectra compared to conventional lamp systems. In addition, thanks to VYPR solutions, greenhouse growing is no longer seasonal, as efficient crop lighting provides uniform plants with consistent productivity, regardless of local weather.
With Fluence's RAZR Series, ECF Farmsystems achieves more effective operations and a 35% increase in production without the need for new construction or remodeling. By expanding vertical growing in the plant nursery, which eliminates the need to invest in additional growing space/facilities, ECF Farmsystems saves important emission costs. Propagation on VertiCCs systems with RAZR exposure allows ECF Farmsystems to control the entire growth cycle, better manage pests, and now calculate yields more accurately.
The new RAZR module will be available in January 2021.
For more information:
fluence.science/webinars
https://en.ecf-farm.de/
https://www.osram.com/os/applications/horticulture-lighting/index.jsp
Publication date: Thu 7 Jan 2021