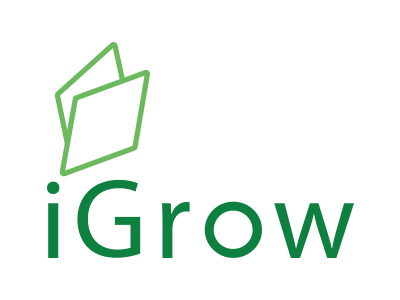
Welcome to iGrow News, Your Source for the World of Indoor Vertical Farming
AI Is Learning To Understand How Vegetables Taste
With the global demand for food escalating, vertical farms are becoming a critical component of agriculture's future. They use robotics, machine learning and artificial intelligence (AI) to automate farming and perfect the growing of greens and vegetables.
By Jennifer Kite-Powell
July 20, 2021
With the global demand for food escalating, vertical farms are becoming a critical component of agriculture's future. They use robotics, machine learning and artificial intelligence (AI) to automate farming and perfect the growing of greens and vegetables. With steady growth, the vertical farming market was had an estimated value of $4.4 billion in 2019 and is expected to reach $15.7 billion by 2025.
Fifth Season is a vertical farm in Pittsburgh that uses super-stack software and robotics to run their fully automated farming systems. And, by combining big data and AI, they have created the optimal grow recipe that determines the best flavor for the plants they grow.
"The role of AI in determining flavor is to leverage big data and AI to ensure you achieve the target flavor — sweetness, spiciness, bitterness, total degree of flavor and texture," said Austin Webb, CEO of Fifth Season.
"Our plant's individualized grow recipe is the unique mix of the different LED lights," said Webb. "The plants go through the grow room with a QR code that communicates that plant's route and tells the automated system where each plant needs to be throughout the process."
Webb says their super stack system, which serves as 'the brain' of the vertical farm maps, maps out each plant's route through the grow room based on its grow recipe and then moves the plants where they need to go.
"We use AI and data to find improvements in all aspects of crop quality, even beyond what humans think they know about flavor profiles. We call this proactive, deterministic growing compared to traditional farming, including greenhouse growing, where you have to be reactive based on weather and sunlight conditions," said Webb. "We then leverage human/chef feedback on what tastes the best and what texture is best and [..] combine that qualitative data with the 26K quantitative data points for every tray of greens per lifecycle."
"From there, we tweak our grow recipes to build the best flavor. For some vegetables, like tomatoes, experts have leveraged Brix scores, but [..] we measure flavor quality based on these factors: sweetness, spiciness, bitterness, the total degree of flavor, texture and color," said Webb. "Humans don't need to guess what iron content or Brix score is best; the brain in our farms can do that. Humans tell the grain what tastes best, and the brain will compute and tweak the grow recipes from there."
Darryn Keiller, CEO and founder of WayBeyond, says that to impact flavor, you either have to change the genetics of the crop or alter the existing biochemical profile.
"For example, growers can impact flavor by adjusting light and nutrients, which can then enhance the texture (crunch, thickness) or flavor (increased sweetness or bitterness)," said Keiller. "Once you determine the key characteristics you want in a crop, you then use machine learning or AI to automate and optimize the production process for consistent growth and be responsive to changing consumer preferences."
"Currently, vertical farms utilize seed stock bred for outdoor farming. Using AI technology, they can create their breeding stock (or lines) better suited for indoor environments. It's about refining your research and development and creating genetics perfect for your environment and management practices while ensuring continuous improvement of commercial production. The potential is huge."
Webb adds that many indoor growers sought to build an outdoor farming system that can thrive indoors; however, Fifth Season chose to apply smart manufacturing principles to agriculture that would enable them to grow food in a new way.
"We grow more than 15K pounds a week of fresh food with 90% less water than what would be required to grow that amount of fresh food on a traditional outdoor farm - and that is done on a footprint of just 25,000 square feet," added Webb.
Webb believes that scaling viable vertical farming operations that can crack code on both the technology and the consumer experience to deliver consistently fresh, nutritious and clean produce changes the consumer shopping significantly.
"It changes our entire definition of what fresh can and should taste like; it changes the ease of access and availability and convenience to fresh food, which brings so much value to consumers," said Webb. "It's another avenue for shoppers to access the freshest, highest-quality food at retail with produce that has a much longer shelf life than we're accustomed.”
Lead Photo: Greens leaving the grow environment on route to harvesting and packaging in Fifth Season's vertical farm in Pittsburgh.
Robots Take Vertical Farming To New Heights
Braddock, Pa., is where Andrew Carnegie first mass-produced steel. The city, now one-tenth its former size, is home to a new kind of industry: robotic farms that grow greens inside buildings
Braddock, Pa., Is Where Andrew Carnegie First Mass-Produced Steel. The City, Now One-Tenth Its Former size, Is Home To A New Kind Of Industry: Robotic Farms That Grow Greens Inside Buildings.
June 28, 2021
A decades-long decline of industry in Braddock has left the western Pennsylvania town in ruins. Ten miles upriver from Pittsburgh in the Mon (Monongahela) Valley, most of the city’s factories, businesses and homes were abandoned long ago and leveled. Among the ruins, a sprawling steel mill, built by Andrew Carnegie in 1874, is still producing slabs of steel, 24 hours a day, seven days a week. It’s stained blue walls and maze of giant, rust-colored pipes and vents stand in contrast to the brand-new, block-long, gleaming white structure directly across the street. The mill’s neighbor is Fifth Season, a vertical farm growing greens indoors by stacking racks of plants on top of each other.
Fifth Season is the brainchild of brothers Austin and Brac Webb, and co-founder Austin Lawrence. “We view vertical farming as really a smart manufacturing system,” says Austin Webb. “We just happen to manufacture living organisms.”
The partners consider their fledgling enterprise as more than a means to feed people, but also a chance to work with a community in need. Almost none of the old steel plant’s employees live in Braddock. Conversely, everyone hired to work at Fifth Season lives close by and in the surrounding communities. “We’re creating a workforce of the future,” Webb says. “It’s an entirely new ag-manufacturing job that hasn’t existed before.”
Since the collapse of the steel industry in Braddock, the borough has struggled to attract new business and residents.(David Kidd/Governing)
Automated City Farming
Two shifts of 20 people oversee operations at the vertical farm. And like the steel maker across the road, the work never stops. Dressed in blue scrubs and lab coats, with heads covered and gloves on their hands, workers inside the plant look more like medical research professionals than farmers. The entire process, from seed to harvest, is controlled robotically. “What we have built is the industry first, and industry only, end-to-end automated platform,” says Webb.
Fifth Season’s proprietary software allows efficiencies otherwise not attainable. Spinach, arugula and other greens move around the 60,000-square-foot facility in plastic trays, each with its own unique ID. Sensors are constantly monitoring everything from nutrient mix, carbon dioxide levels and light spectrum, in order to ensure that the greens follow their prescribed grow recipe. Every plant can be traced from any point in the process, at any time.
Webb is quick to tout the advantages of vertical farming. Fifth Season uses up to 95 percent less water and 98 percent less land than conventional farming. Water from the municipal system is filtered and proprietary nutrients added before getting to the plants directly through their roots. “It means you can replicate any form of soil environment,” he says. Whatever water is not used by the plants is retreated and recirculated, with nutrients added as needed. A peat mix is used to support the roots, but all the nutrients are in the water, not the “soil.”
“We use no herbicides and no pesticides,” Webb says. “And that’s because we have hermetically sealed environments.” The possibility of contamination is all but eliminated. Fifth Season recently received a perfect score from the Safe Quality Food (SQF) program, an international, independent body that certifies food safety management. “The second time in 25 years they gave 100 percent,” he says.
With only their faces exposed, employees work among the various conveyor belts that crisscross the high, white-walled rooms of Fifth Season’s production floor. But there are no humans in the adjacent grow room, where tightly spaced racks, supporting trays of plants, are stacked 30 feet high, bathed in an otherworldly purple-magenta glow. The dramatic color comes from the LEDs that replicate the most useful parts of the spectrum of sunlight. “You can’t control the sun,” Says Webb. “But what you can control are LEDs.”
Fifth Season’s proprietary systems allow more plants to be grown in less space. The purple-magenta LED lighting replicates the most useful parts of the spectrum of sunlight, improving growth of the greens.(Fifth Season)
Every few minutes, a robot glides forward and back along a raised guideway that runs down the center of the room, dividing the stacks in half. The machine is not much more than a plain box, just a few feet tall. A metal beam rises from its back, extending to the ceiling. Its task is to place and remove trays of plants, taking its instructions from the all-knowing software. Because they are so tightly spaced, more trays can be stacked on top of each other, resulting in greater production.
“Compared to some other vertical farms out there, we have a lot more density,” says Webb. “We’re able to have more racks that grow inside the same space.” Moving trays is a task well-suited to a machine. Not only does the robot fit into places no human could, it always knows where every tray of greens should be, and for how long.
Vertical Farming Comes to Braddock
After a five-year career in finance, Austin Webb enrolled in an MBA program at Carnegie Mellon University in Pittsburgh. “I believe that robotics will possibly disrupt every industry in the world,” he says. “And so I went to C.M.U., specifically because it’s the No. 1 school in computers, science and robotics.”
There he met Austin Lawrence, who shared his interest in controlled environment agriculture. Together they visited a few vertical farms, coming to the conclusion that what was needed was an entire robotic platform, something the two of them could not accomplish on their own. Webb’s brother Brac, a self-described engineer and entrepreneur, was soon recruited to help. Their new business was incorporated in 2016, initially as RoBotany, which later morphed into Fifth Season.
With financial backing in hand, the partners looked for a place to build, quickly settling on nearby Braddock. They broke ground in May of 2019, were installing equipment less than a year later and were at full production before the end of 2020. “I think there’s a lot of opportunity for resurgence in a place like this,” says Webb. “A lot of folks that stayed are passionate around Braddock being able to grow and thrive and we want to be a part of that.”
In the foreground, Fifth Season’s new structure stands in contrast to the steel plant behind it that still dominates the town.(David KIDD/Governing)
Andrew Carnegie’s mill was the first of many that would proliferate in the Mon Valley, making it the nation’s steel capital. The churches, schools, stores and restaurants that served the town’s 20,000 inhabitants are mostly gone now. Shops and services are few and far between for the 2,000 that remain. “The nearest grocery store is up the hill, two towns over,” says Braddock Mayor Chardae Jones. “And most people don’t have cars.” It’s a hot day in June when a few of the locals gather in a brand-new park along Braddock Avenue. Everyone agrees the park is nice, but it’s no consolation for the hospital that used to stand on the site.
Many years ago, steelworkers and their families lived close to the mill.(David Kidd/Governing)
A few blocks away, an ever-present din still emanates from Carnegie’s steel mill, and a parade of trucks continues to roll past the boarded-up stores and empty lots that line the borough’s main thoroughfare. “We have a lot of vacant buildings,” says Mayor Jones. “That’s our biggest issue.” But there are signs of a revival among the ruins.
Present Day Braddock
Against the backdrop of empty and dilapidated storefronts, “The Ohringer,” a former furniture store built in the streamline moderne style of the 1940s, has recently been completely rebuilt and modernized as apartments and studio space for artists. Applicants are expected to present their work for review and answer a few questions, one of which is “why are you interested in becoming part of Braddock’s resurgence?”
Not only does Braddock lay claim to Andrew Carnegie’s first steel mill, but also the first Carnegie library, dedicated in 1889. Narrowly escaping demolition in the 1970s, the impressive stone structure is today undergoing a comprehensive restoration and modernization. Bright yellow notices of this year’s street sweeping schedule are affixed to telephone poles near the library and all over town, an indication that the local government is still functioning.
A repurposed furniture store now provides updated living and studio space to area artists.(David Kidd/Governing)
Further up the avenue, more official-looking signs are attached to random telephone poles. “NOTICE, WRITE MORE LOVE LETTERS” says one. “NOTICE, LOVE IS FREE,” says another. The signs were placed there, unofficially, by Gisele Fetterman, wife of former mayor and current Lt. Governor John Fetterman. Among her many initiatives to improve the lives of people in Braddock, she founded the Free Store nine years ago, a place where “surplus and donated goods are received and redistributed to neighbors in need.”
Fifth Season is a regular contributor to the Free Store, having recently given them a new refrigerator and donating 100 pre-packaged salads every Thursday. “We’re treated like we’re a customer,” says Gisele Fetterman. “We’re not getting things that didn’t sell, or surplus. Our families get to come in and choose. They can feel like they are at a grocery store. There is great dignity in the process of being able to choose.”
Offering “produce grown in soil by humans in Braddock,” workers at Braddock Farms do it the old-fashioned way.(David Kidd/Governing)
There are more signs along Braddock Avenue. “BE ALERT: VEGETABLES AHEAD.” Another simply says “TURNIPS.” Back in 2007, when John Fetterman was the mayor, he encouraged a nonprofit group of community gardeners to establish a farm in Braddock. Bisected by a side street, the organic farm has expanded to a little less than an acre in size, growing greens, tomatoes, onions, peppers and eggplant. This is Nick Lubecki’s fourth year as manager of the farm. “We’re here in Braddock, so the people in Braddock are our main focus,” he says. “We want to be useful.”
At best, the little farm on Braddock Avenue can produce 13 plantings of greens in a year. It is entirely different from the computer-controlled, machine-driven, non-stop production that takes place a few blocks away at Fifth Season, where a half-acre indoors can produce the equivalent of nearly 100 acres of farmland. But higher yields don’t matter as much if a significant portion is ultimately lost in transit to the table.
Serving a Market
Localized food production means less spoilage and waste. “If it takes anywhere from five to eight days to go from California to Pittsburgh, you’ve just lost five to eight days of shelf life,” says Austin Webb. Most of what Fifth Season produces is consumed in the Pittsburgh area. “The day after it was cut, not 10 days later.” Their ready-to-eat salads can be purchased at a local supermarket chain, or delivered directly to the consumer at home, a direct response to the pandemic. Local restaurants, hospitals and universities are also customers.
Convinced they have successfully demonstrated the viability of their proprietary technology, the three partners are looking to expand beyond western Pennsylvania. “We can build these anywhere… even larger than what we have here today,” says Austin Webb. “And we don’t have to re-create the wheel. It’s not like it would take us another five years.”
Conversations are already taking place about licensing the technology, proceeding in partnership with someone else, or going it alone. “That will allow us to build a facility just like we built in Braddock, in other parts of the U.S., and other parts of the world, even faster.”
A Job You Can Walk to
Andrew Carnegie built his steel mill in the Mon Valley because he needed the river, the raw materials, and access to labor. His plant was expressly designed to use the Bessemer Process, the first method to inexpensively mass-produce steel. Nearly 150 years later, the Webb brothers and their partner Austin Lawrence chose the exact same location to showcase their own new manufacturing technology and to fill a need in the community. “Knowing that we could build these anywhere, we wanted to build in Braddock because we knew that we could create jobs,” says Austin Webb. “That we could create this new workforce of the future.”
Employed since January, John Davis lives less than a block away from Fifth Season. “I have family in Braddock. They’re very happy I’ve got a job.”(David Kidd/Governing)
Braddock resident John Davis may or may not think of himself as part of the workforce of the future. But he’s happy to have a good job. Covered head to toe in his surgical outfit, he works in the seeding department at Fifth Season, a job he’s held since January. He’s lived here for 20 years, and this is the first job he’s had that didn’t involve a commute. He walks to work from his house, half a block away.
Davis is 32 years old and anxious to put the past behind him. “To have a job that you like, where you live, it’s comfortable,” he says. “And you can see that this is going to change Braddock for the better because it gives the residents jobs and new innovations. It’s going to bring life.”
While awaiting their fate, many of Braddock’s empty buildings provide space for murals and artwork.(David Kidd/Governing)
Lead photo: Greens leave the grow room at robot farm Fifth Season, ready for harvest. (Fifth Season)
Tags: Economic DevelopmentFood AssistanceTechnology
David Kidd is a photojournalist and storyteller for Governing. He can be reached at dkidd@governing.com.
VIDEO: Ohio Company Redefines Farming By Going Indoors
Farm Manager Noah Zelkind was working on Wall Street before making the switch to 80 Acres, which houses 20 different growing rooms
The Hamilton company 80 Acres Farm will now have produce in Kroger stores across the state.
BY OLIVIA WILE
June 24, 2021
CINCINNATI — The future of farming is right here in Ohio, and it’s happening indoors.
What You Need To Know
The company 80 Acres Farms has the ability to control and change the environment of each of the rooms where produce is growing
The farm doesn't see itself as competition with other conventional farms, but instead aims to help feed a growing population
Its produce is now being sold in Kroger locations in Ohio
The company 80 Acres Farms in Hamilton, 20 miles north of Cincinnati, is one of just a handful of “vertical farms” in the world. Farm Manager Noah Zelkind was working on Wall Street before making the switch to 80 Acres, which houses 20 different growing rooms.
“We have 10 levels stacked on top of each other, 10 rows long, and 10 tables inside of each row,” said Zelkind.
The company is able to control and change the environment of each of the rooms where produce is growing. It’s technology that’s years in the making.
“We went through and tried to study nature and replicate everything that’s important about it and really make sure we’re giving the plant exactly what it needs but in the most efficient way possible.”
It's a method Zelkind said gives the company ultimate control.
"This really is the next generation of farming," he said. "We have a completely different level over the control of the entire process of growing than anything anyone has done before.”
“You're going to get the same healthy fresh lettuce whether you're in the middle of winter and it's snowing outside or you’re in the middle of the summer.”
But he said the company is not trying to compete with conventional farmers.
"We don’t see ourselves competing with farmers at all,” said Zelkind. “If you look, we’re supposed to have 10 billion people in the world in the next 20 to 30 years, and in order to feed the population, we’re going to need 70% more arable land.”
The farm's produce is now available in Kroger stores across the state.
Farm Tech Startup Iron Ox Appoints Impossible Foods and Tesla Veteran Rachel Konrad as First Independent Board Member
Iron Ox growing facilities use advanced robotics to precisely cultivate perfect, nutritious produce by giving each plant the specific attention it needs, and then getting it on a store shelf nearby within about a day of harvest
-- Konrad, who spent the past five years at Impossible Foods, joins the board of Iron Ox during a period of rapid manufacturing scale-up and retail expansion.
-- Iron Ox growing facilities use advanced robotics to precisely cultivate perfect, nutritious produce by giving each plant the specific attention it needs, and then getting it on a store shelf nearby within about a day of harvest.
-- The Series B-stage company, whose products are already a breakout seller in California, is also hiring plant scientists, engineers, greenhouse operators, and roboticists.
SAN CARLOS, Calif., June 10, 2021 /PRNewswire/ -- Iron Ox, a farming innovation company with deep expertise in robotics and artificial intelligence, has appointed former Impossible Foods and Tesla executive Rachel Konrad as its first independent board member. This appointment further demonstrates the food tech startup's growth trajectory as they scale up operations and expand their commercial footprint.
Iron Ox, which launched the world's first autonomous farm, has an industry-leading intellectual property portfolio to automate farming and produce that's fresher, cleaner, and locally grown. Thanks to the company's groundbreaking robotics, Iron Ox farms require 90% less water than traditional farms — generating 30 times more produce per acre of land.
Konrad joins Iron Ox after spending the past five years as Chief Communications Officer and a member of the senior leadership team at Impossible Foods, reporting directly to CEO Pat Brown. She previously held senior management roles at Renault-Nissan-Mitsubishi and Tesla, where she reported directly to Elon Musk as the company scaled up operations.
"We can't solve our planet's climate crisis without radical changes to the way we make food," said Konrad, who lives in the San Francisco Bay Area and enjoys cooking for her family and hiking with her rescue German Shepherd. "Iron Ox's intellectual property portfolio can usher in a new era of farming that produces food sustainably and ethically. But honestly, I was sold after my first whiff of Iron Ox basil."
"Rachel understands the unique power of disruptive startups to shift entire industries and force even the most entrenched incumbents to do the right thing for people and the planet," said Brandon Alexander, Iron Ox CEO and Co-Founder. "Her unique perspective will help Iron Ox refine and execute our ambitious strategy. As our first independent board member, we expect Rachel to help us set a new standard for inclusive governance in corporate America."
The Series B-stage company operates farms in Northern California and recently broke ground on a new 535,000 sq. ft. indoor farm in Lockhart, Texas. Today, California consumers can buy Iron Ox food throughout California at Whole Foods and at San Francisco Bay Area's upscale Biancchini's markets. Sales in Texas are expected to begin in late 2021.
The company is also hiring plant scientists, engineers, greenhouse operators and roboticists who are passionate about solving food insecurity, which is at the root of our environmental and public health crises.
For more information, and to view the job openings, visit the Iron Ox jobs page.
About Iron Ox:
Iron Ox is a farming innovation company with deep expertise in robotics and artificial intelligence, and a vision to solve global climate through food. Their approach redesigns every step of the farming process, achieving levels of precision that are impossible through traditional farming. Iron Ox produce is both local and sustainable by design, greatly reducing systemic food waste and minimizing the ecological impact of farming. For more information, visit www.ironox.com.
SOURCE: Iron Ox
Robotic Warehouse Farms Will Save The World
CEA technology is just getting started. Like the Tesla Cybertruck, we have a working concept that promises a more-than-Jetson’s-level future many of us can see the benefits of and actively want―it’s just not quite available to the masses yet
by Elle Griffin
Four years ago, Ritch Wood was looking for a better way to grow plants. As the CEO of global skincare company Nu Skin, he ran into ingredient shortages every winter when fields went dormant―and when he moved grow operations to the equator he ran into water and land shortages, along with a host of quality control issues.
Nu Skin needed reliable, quality ingredients for their skincare products. But farming was too unpredictable an industry. “If there was a way to grow indoors,” he thought, “and be able to do that 24 hours a day, 365 days a year―if we could guarantee that it was grown without any herbicides or pesticides and in a sustainable way that uses less water and land―that would be really helpful.”
At the time, controlled-environment agriculture (CEA) was in its infancy and grow-light technology had yet to take a turn for the more affordable. When he learned of an agricultural system that promised to use a fraction of the land and water used by traditional agriculture methods and had the potential to make it more affordable, Wood made an investment.
Nu Skin paid $3 million for 70 percent of the company and rights to its IP―and Grōv Technologies was born.
Grōv grass grown in the Olympus machine at the Bateman Mosida Farms. Photo from Grōv Technologies
Controlled-environment agriculture is on the rise
The theory behind CEA is that by controlling the environment in which it grows, we can control everything about a plant and what it grows into by micro-tweaking one of a thousand different characteristics―including temperature, humidity, light duration, light wavelength, dissolved oxygen in the water, and carbon dioxide saturation in the air. By tweaking the growing cycle, we can control the caloric content as well as the nutrient content and density of the plant.
“What we’ve learned through controlled-environment agriculture,” Benjamin Swan, co-founder and CEO at Sustenir in Singapore, once told National Geographic, “[is] we can actually emphasize certain characteristics of the plants. So, without using GMO, we can make our kale softer, we can actually make it sweet.”
The theoretical use cases for this technology are endless―from being able to grow in places where water is scarce (like in much of Africa), or where water is overly abundant (like Hawaii), or in places where labor is scarce (like in parts of Asia), or even in places that have long winters (like Northern Europe). Theoretically, we could have grow towers in every town and feed the whole of it no matter its natural environment.
We could even grow those foods to those cities’ exact nutritional needs―more vitamin D-rich foods in wintery places, for example. Dr. Lee Mun Wei, a senior manager at the Food Innovation and Resource Centre (FIRC) in Singapore aims to predict and prevent illness in a given population by tracking their biometric data using Apple watch-like wearables, then 3D printing nutrient-specific foods that could mitigate imbalances.
Though these technologies exist, they are still in their infancy. Singapore leads much of the research and development out of necessity. With limited land and water resources, the county is forced to import 90 percent of their food and 40 percent of their water from outside the country. As a result, they have no option but to grow vertically and desalinate water from the ocean.
Elsewhere, the industry has been slow to catch on, largely due to exorbitant startup costs, low returns, and lack of urgent need. According to a 2017 State of Farming report by L.E.K., only 27 percent of indoor, vertical farms are profitable compared with 50 percent of container farms and 75 percent of greenhouses. But one thing has spurred the industry on in recent years: cannabis.
Legalized in 39 states, demand for cannabis has created a $13.6 billion industry and enough capital to fund CEA-enabled grow operations. “When you have a crop that fetches up to $2,400 or $2,500 a pound, you need to be able to dial everything in and make it consistent and repeatable,” says Dashiel Kulander, co-founder and CEO at Boojum Group. “If the temperature swings five to 10 degrees on a cannabis plant, that will change the plant’s various cannabinoids. The goal is to create a medicine that is consistent batch after batch.”
It’s only recently that there has been some financial incentive to use CEA technologies for food use―largely driven by Big Ag players hoping to hedge out the competition. Berry farming giant Driscoll’s, for one, led a $500 million round to fund Plenty, a 2.2-acre vertical farm in California they hope will help them fulfill a contract with Albertsons. The Ingka Group, for another, led a $100 million round to fund AeroFarms, a 2.4-acre vertical farm in New Jersey that will help them fulfill a contract with Singapore Airlines.
Grōv tent at the Bateman Mosida Farms. Photo from Grōv Technologies
Grōv Tech is building CEA prototypes in Utah
By investing in Grōv Tech, Nu Skin hopes to do something similar, getting ahead of the supply chain that fuels their skincare products before the competition can beat them to it, or before climate change makes traditional methods more difficult, all while shoring up technology that could provide a farming model that is more sustainable―if only it were more economical.
“The purpose was always, can we build a better product for Nu Skin?” Wood says. “We think there’s a huge story around the ingredient sustainability, and there were a lot of ingredients we felt we could grow, but the challenge was: could we do it in an economical way?”
Grōv Tech started out with a prototype: a tower that pairs hydroponic growing technology with grow lights. But like all CEA startups, a lot of the growing process was manual and the technology was prohibitively expensive. To make something that was scalable and profitable the whole thing needed to be automated and it needed to be cheap.
With this goal in mind, Wood decided they would start by growing animal feed for Bateman’s Dairy farm. Having grown up on a dairy farm himself, Wood figured this would allow the company to scale the product while refining and automating the technology to the point that it could be replicated. And all of this would have a fortuitous effect on Nu Skin’s bottom line.
“One of our bestselling products is a weight-loss protein powder which uses whey protein,” Wood says. “So again, a very nice connection there is if the animal is eating a more sustainable product and producing better milk with better protein and it’s being done in a sustainable way―certainly that can be a benefit to Nu Skin down the road.”
One year into feeding the 20,000 animals at Bateman, the company has learned a lot. For instance: cows need a lot of magnesium, but they don’t like eating it. Now, Grōv Tech puts magnesium in the water so it’s directly absorbed into the plant and then becomes bioavailable to the cow upon eating it. And because the growing process only takes seven days, data scientists can analyze the results in real-time and adjust the components to optimize production for the next batch of feed.
According to Grōv Tech president Steven Lindsley, it’s not far off that we’ll be looking at milk production (butter, fats, and proteins) and optimizing a herd’s diet for taste, quality, and nutritional value―not to mention the wellbeing of the animal. We’ll be able to look at how many trips from the veterinarian an animal gets when they’re fed certain nutrients in their diet, and whether they can have more calves and produce the same amount of dairy on less, better quality feed. (So far, the answer to this last question is yes. When animals are fed better quality food they need less of it―just like humans.)
And if we hook all of the cows up to robotic milking equipment and connect everything to artificial intelligence, machine learning, and the Internet of Things―Lindsley’s far-flung goal―then we might be able to collect enough data to not only feed cows to their optimum health and performance ability, but humans too. And that could have ramifications not only for feeding the world, but nourishing it― just like Dr. Wei hopes to do in Singapore.
“Last year was about starting to feed animals and get data and prove out the hypothesis we have while continuing to perfect the technology and get confidence there,” Wood says. “And now we’re really to a point where we’ve got data that proves that it works and that financially it’ll be a good thing for a farmer. So now we can really take that proposition to farmers and start to scale.”
Olympus Tower Farm at Bateman Farms in Mosida, UT. Photo from Grōv Technologies
CEA technology could feed the world
Right now, Grōv Tech is focused on refining its technology right here in our own backyard. But once they do that, the plan is to expand internationally.
“Saudi Arabia has actually passed a law where you cannot use water to grow fodder or feed for animals, so all of that now has to be imported. China imports one-third of their alfalfa feed for their dairy animals because they don’t have the capability of growing it,” Wood says. “So there are countries that will probably benefit more than the US would. But we’ve got to refine the technology and get that built to where it’s ready to scale before we start spreading ourselves all around the globe.”
CEA technology is just getting started. Like the Tesla Cybertruck, we have a working concept that promises a more-than-Jetson’s-level future many of us can see the benefits of and actively want―it’s just not quite available to the masses yet. But with more than a billion dollars invested in the technology in just the past few years alone―we’re getting there. And the “there” we are heading toward is rosy indeed.
“To put it in perspective, one tower that is about 875 square feet on the ground will replace 35 to 50 acres of land,” says Lindsley. “And that will feed the animals on roughly five percent of the amount of water. The UN says that that the world will add about 2.5 billion people in the next 30 years. And we have to find a way to feed them on arguably less arable land and water. The good news is the technology is coming along to help solve that equation.”
If COVID-19 taught us anything, it’s that our food supply chain is fragile. But that’s only because our supply chain was built to grow food in California, refrigerate it so it stays fresh, then transport it 1,500 miles so we can eat a salad in the winter in Chicago. In the future, that might not be a thing. “We’re having a dry year now,” Lindsley tells me in February. “But a year ago we were in a blizzard, and even in the middle of a blizzard in February in Utah, we’re pumping out fresh, beautiful, safe green grass for animals. It’s a paradigm shift.”
“Four years ago it was a good idea,” Wood tells me of his company’s investment in CEA technology, “But four years from now it’s going to be required.”
Elle Griffin
Elle is the editor-in-chief of Utah Business and a freelance writer for Forbes, The Muse, and The Startup. She is also a literary novelist and the author of a weekly newsletter called The Novelleist. Learn more at ellegriffin.com.
USA: TEXAS - Iron Ox Breaks Ground On New Robotic Growing Facility In Lockhart
The state-of-the-art indoor facility will be fully dedicated to growing techniques harnessing the power of robotics and intelligence, enabling Iron Ox to grow sustainable, local produce to serve the Texas community
By FOX 7 Austin Digital Team
April 22, 2021
California-based company Iron Ox held a groundbreaking ceremony for its new Lockhart facility in partnership with the Economic Development Corporation of Lockhart. (City of Lockhart)
LOCKHART, Texas - A new robotic growing facility is expected to bring over 100 jobs to the city of Lockhart.
Iron Ox, a California-based company that specialized in robotics and AI-enabled farming with a mission to solve food insecurity, has begun construction on a 535,000 square-foot indoor hydroponic farm in the city.
Once completed, the farm, which sits on 25 acres of agricultural land, will significantly increase Iron Ox’s growing capacity for fresh, clean, and healthy herbs, leafy greens, berries, and vine crops, says the company. The state-of-the-art indoor facility will be fully dedicated to growing techniques harnessing the power of robotics and intelligence, enabling Iron Ox to grow sustainable, local produce to serve the Texas community.
Iron Ox, a California-based company that specialized in robotics and AI-enabled farming with a mission to solve food insecurity, has begun construction on a 535,000-square-foot indoor hydroponic farm in the city. (City of Lockhart)
The company says that Lockhart is an ideal location for greenhouse agriculture given its ample sunlight, central location near many cities, and it’s proximity to several great universities.
The indoor farm is expected to cost over $10 million to develop, says Iron Ox, with 275,000 square feet of the project anticipated to be completed by the end of this year and 260,000 square feet of the project anticipated to complete by the beginning of 2022. In total, the project will create over 100 jobs.
"The addition of Iron Ox to the Lockhart business community represents synergy between our city’s storied history in agriculture and our growing technology sector," said Lockhart Mayor Lew White in a release. "The food and beverage processing industry is one of four business sectors Lockhart has targeted in its 5-year economic growth plan. Our city’s unique advantages align perfectly with the needs of companies like Iron Ox."
Lockhart Mayor Lew White (left) and Iron Ox co-founder and CEO Brandon Alexander stand next to a concept drawing of the new Iron Ox facility being built in Lockhart. (City of Lockhart)
Iron Ox expects to complete their first harvest and to begin delivering sustainable, local produce to select chefs and retailers throughout Texas by the end of this year. It is anticipated that Lockhart’s hydroponic facility will grow thousands of pounds of fresh fruits and vegetables. Each crop type is cared for by Iron Ox’s expert growers and empowered by a robotic growing process ensuring year-round consistency, quality, and flavor says the company.
"We have made it our mission to address food security by developing autonomous greenhouses that grow a variety of local and consistently delicious food for everyone", said Iron Ox CEO and co-founder Brandon Alexander. "We’re excited to begin development of our newest indoor farm here in Lockhart—our first out-of-state facility. We look forward to further developing ties to the local community and to expanding our partnerships and distribution channels throughout the state of Texas."
Iron Ox co-founder and CEO Brandon Alexander addresses people at the groundbreaking ceremony of the new Iron Ox facility in Lockhart. (City of Lockhart)
Focused on sustainable, scalable food production for a changing climate and an ever-growing population, the Iron Ox process eases the growing pressure of food waste and labor scarcity by providing a stable supply of fresh, nutritious food for local communities, says the company.
Iron Ox says it designed its growing system around the sun, an approach that uses less energy than other modern forms of farming. Their hydroponic growing system uses 90% less water over traditional farming while growing 30 times the amount of crops per acre of land, allowing Iron Ox to deliver on its mission to increase access to premium produce for everyone.
Iron Ox currently operates two hydroponic farms located in Gilroy and San Carlos, California.
VIDEO: Indoor Farming Powered By Robotics And Technology - Plenty
Indoor farming powered by robotics and technology is enabling one California company to grow 'Plenty' of flavorful nutrient-rich and pesticide-free produce
Author: abc10.com
April 6, 2021
AppHarvest Acquires Agricultural Robotics And Artificial Intelligence Company Root AI To Increase Efficiency
Acquisition of Root AI and its signature robot, Virgo, bolsters the company’s intelligent tools to produce foods sustainably. Root AI CEO Joins AppHarvest as Chief Technology Officer
Acquisition of Root AI and its signature robot, Virgo, bolsters the company’s intelligent tools to produce foods sustainably. Root AI CEO Joins AppHarvest as Chief Technology Officer
MOREHEAD, Ky., April 08, 2021 (GLOBE NEWSWIRE) -- AppHarvest, Inc. (NASDAQ: APPH, APPHW), a leading AgTech company and Certified B Corp focused on farming more sustainably using 90 percent less water than open-field agriculture and only recycled rainwater, announced today that it has acquired Root AI, an artificial intelligence farming startup that creates intelligent robots to help manage high-tech indoor farms. The acquisition of Root AI and its robotic universal harvester, Virgo, is expected to provide AppHarvest with a baseline of harvesting support working alongside crop care specialists focused on more complex tasks. AppHarvest expects the game-changing advantage of the technology to be in the data the robots can collect as they harvest, which can help evaluate crop health, precisely predict yield and optimize overall operations of the controlled environment agriculture (CEA) facility.
“Farming as we’ve known it is broken because of the increasing number of variables such as extreme weather, droughts, fire, and contamination by animals that make our food system unreliable. Indoor farming solves for many of those challenges, and the data gathered can exponentially deliver more insights that help us predict and control crop quality and yield,” said AppHarvest Founder & CEO Jonathan Webb. “One of the key challenges in agriculture is accurately predicting yield. Many downstream decisions from work scheduling to transportation to retail planning are based on that. Any deviation between projection and actual yield can result in fire drills for numerous functions to adjust for the change, and AI can help solve for that.”
Root AI co-founder and CEO Josh Lessing will take on the role of Chief Technology Officer for AppHarvest where he will take the lead in continuing to develop the robots and their AI capabilities for the network of indoor farms that AppHarvest is building. Lessing, along with co-founder Ryan Knopf who will join AppHarvest as vice president of technology, helped establish Root AI as an early leader in employing artificial intelligence in CEA. Virgo is the world’s first universal harvester, which can be configured to identify and harvest multiple crops of varying sizes including tomatoes, peppers, cucumbers and more delicate fruits such as strawberries among others.
Though Virgo can work indoors or out, the robot’s focus has been on controlled environment agriculture. Over the past three years, it has collected the world’s largest data set of tomato images to enable it to identify more than 50 varieties in multiple growing environments and at varying stages of maturity to learn how and when to harvest.
Virgo uses a set of cameras combined with an infrared laser to generate a 3D color scan of an area to determine the work it can perform. Once it maps the tomatoes, it assesses their orientation and determines if they are ripe enough to pick. The robot can be programmed to make other quality assessments as well. The scan enables the robot to find the least obstructive and fastest route to pick the crop ahead of the arrival of the robotic arm and gripper. The robot can identify hundreds of tomatoes in a fraction of a second without having to connect to the cloud. Virgo keeps score on its success rate like a video game. A built-in feedback mechanism constantly evaluates its efficiency so it learns how to harvest any given configuration of fruit most effectively.
“A piece of food—whether that’s a tomato or a berry or a cucumber—is an outcome from many variables that are part of the growing process. Enhanced data collection for each plant through the robot can lead to insights that teach us precisely how to design better, more resilient food systems that are reliable and that produce more food with fewer resources,“ said Lessing. “Joining forces with AppHarvest is a natural fit: we want to ensure a stable, safe supply of the nutritious and healthy food that people should be eating -- grown sustainably -- and doing that at the scale of AppHarvest gives us the opportunity to make the greatest difference.”
Gathering more data through AI enables growers to use real-time information to improve a number of sustainability efforts such as detecting and eliminating pests naturally, helping indoor farms successfully grow chemical pesticide-free fruits and vegetables.
AppHarvest is investing approximately $60 million, consisting of approximately $10 million in cash and the balance in AppHarvest common shares, to acquire Root AI. The Company will issue approximately 2,328,000 shares for the transaction.
Founded in 2018, Root AI is based in Somerville, Mass., and has 19 full-time employees, all of whom are expected to join AppHarvest’s technology group to help advance the mission of building a resilient and sustainable food supply.
About AppHarvest
AppHarvest is an applied technology company building some of the world’s largest high-tech indoor farms in Appalachia that grow non-GMO, chemical pesticide-free produce using 90 percent less water than open-field agriculture and only recycled rainwater while producing yields up to 30 times that of traditional agriculture on the same amount of land with zero agricultural runoff. The Company combines conventional agricultural techniques with cutting-edge technology and is addressing key issues including improving access for all to nutritious food, farming more sustainably, building a domestic food supply, and increasing investment in Appalachia. The Company’s 60-acre Morehead, Ky. facility is among the largest indoor farms in the U.S.
For more information, visit https://www.appharvest.com/.
This Startup Wants Vertical Farmers To Hire A Robot Gardener
“By automating the production with robotics and remote monitoring, we can lower labor costs and offer solutions for food producers that are economically viable and environmentally sustainable,” the company claims on their website.
Arugula micro greens are grown at AeroFarms on February 19, 2019, in Newark, New Jersey.
Photo: Photo by Angela Weiss (Getty Images)
In recent years, vertical farming has emerged as a futurist’s solution to the world’s agricultural problems. The growing trend seeks to use controlled environments to boost food production, leveraging indoor labs where temperature, light, and nutrients can be mechanically controlled.
Yet while vertical farms have gained in popularity, they are also still very expensive. When compared to conventional farming, these farms necessitate the purchase of pricey equipment to aid human labor—a fact that, when paired with other economic pressures, has apparently led to an industry “littered with bankruptcies.”
One company hopes to change this dire picture. Enter Watney the robot.
Watney was designed by start-up Seasony. The company, which was featured today at this year’s Alchemist Accelerator’s Demo Day, has sought to make the tech-farming trend more accessible by automating away some of the more difficult labor involved.
Image: Screenshot: Youtube/TV2LORRY
“By automating the production with robotics and remote monitoring, we can lower labor costs and offer solutions for food producers that is economically viable and environmentally sustainable,” the company claims on their website.
Indeed, Watney is designed to augment (and, in many ways, replace) a human labor force—currently one of the biggest expenditures for vertical farms. Essentially an intelligent, automated cart, the robot was designed to “move and transport plant trays” within a farming hub. In techno-jargon, it is an autonomous mobile manipulation robot (AMMR), a type of machine known for moving and manipulating items on its own. It is also equipped with a camera that captures image data and sends it back to farm management software for human analysis. Watney also gathers valuable horticultural data to help farmers optimize yields, said Christopher Weis Thomasen, Seasony’s CEO and Co-Founder, in an email.
From left to right: Erkan Tosti Taskiran, Servet Coskun and Christopher Weis Thomasen.
Photo: Photo from Seasony.
“We are doing for vertical farming what the integration of autonomous mobile robots did to amazon. We are able to decrease the costs of growing food in a vertical farm by alleviating the logistics pains of working from scissor lifts,” said Thomasen.
Thomasen, a mechanical engineer, and his two co-founders electrical engineer Servet Coskun and business specialist Erkan Tosti Taskiran, were inspired to create the business while brainstorming what it would take to sustain life in outer space (Watney the robot is named after Mark Watney, the astronaut in the movie The Martian, who, after being stranded on the Red Planet, fertilizes potatoes with his own poop to survive).
“It quickly evolved to Seasony setting up a vertical farming lab and exploring the technical challenges facing the new industry. Reducing the costs related to labor is key in order to scale vertical farming and make agriculture more sustainable,” Thomasen said.
There is, of course, some debate in the farming community about the social costs incurred through the large-scale displacement of human labor.
Presumably, we will have to wait to see what that cost-saving process looks like. Seasony, which is still getting off the ground, plans to do a pilot trial with the largest vertical farm in Europe in April. It has plans to conduct further testing with several smaller vertical farms, as well, Thomasen said.
Lucas Ropek
Staff writer at Gizmodo
January Indoor Ag-Conversations Webinar | AI and Robotics For Indoor Farms
You won't want to miss our first Indoor Ag-Conversations webinar session for 2021 as our expert panel takes a deep dive into AI & Robotics
LET'S KEEP THE CONVERSATION GOING!
THURSDAY, JANUARY 21, 2020
2-3 PM EDT
You won't want to miss our first Indoor Ag-Conversations webinar
session for 2021 as our expert panel takes a deep dive into
AI & Robotics
Moderator:
Dr. Murat Kacira, Director of the Controlled Environment Agriculture Center and Professor of Biosystems Engineering Department, University of Arizona
Panelists:
Adam Greenberg, CEO, iUNU
Samuel Bertram, CEO & Co-Founder, OnePointOne
Nick Genty, CEO, AgEye Technologies
LEARN MORE & SAVE YOUR FREE SPOT!
VIDEO: How 2 Hong Kong Pioneers’ Hi-Tech Robotic Arms Can Transform Traditional Industries And Research
Technology created at Jonathan Cheung’s Inovo Robotics performs repetitive tasks that can cultivate sustainable crops and process foods in automated kitchens
Technology created at Jonathan Cheung’s Inovo Robotics performs repetitive tasks that can cultivate sustainable crops and process foods in automated kitchens
Eric Wong has transformed lab experiments with Nikyang’s automated tools that allow researchers to carry out a more reliable and systematic analysis
7 January 2021
While robotic technology has been widely used by big manufacturing companies to increase productivity, the high cost of getting started means many smaller businesses have yet to take advantage of its huge potential.
However, Inovo Robotics, a Hong Kong-based technology start-up, is working to solve this problem.
Since it was founded in 2016, the robotics company has been developing solutions for small- and medium-sized enterprises to help them adapt to automation in their everyday business practices.
Jonathan Cheung, the co-founder of the start-up, says his goal is to “democratize robots” and develop tools for all businesses to help them improve efficiency and remain competitive.
By submitting, you consent to receiving marketing emails from SCMP. If you don't want these, tick here
“We found that there is such a big disconnect to the market for small businesses to be able to benefit from affordable and flexible robots,” he says.
“There are a lot of businesses that are struggling to get staff to do monotonous tasks, so what we’re developing is really a tool that enables them to take away repetitive work.”
Jonathan Cheung, the co-founder of Inovo Robotics, says high entry costs mean that many small businesses have yet to take full advantage of automation’s full potential.
Disrupting traditional industries
One of the applications of the robotic arms has seen them used around the clock to carry out repetitive tasks that help grow high-quality, pollution-free vegetables at a futuristic farm in Hong Kong’s Tai Po district.
The farm, operated by indoor farming company Farm66 since 2018, is located inside a 20,000-square-foot (1,860-square-metre) factory building.
The use of the robotic arms to automatically sow seeds and harvest plants helps the farm to produce up to 200 tonnes of organic fresh produce, including cherry tomatoes, cabbage and basil, which is sold online and delivered to the city’s supermarkets and restaurants.
“Robots really improve the efficiency and speed of the products that are being made,” Cheung says. “In this competitive world, there is always a desire to drive costs down.”
In the case of vertical farming, the technology means minimal space and manpower are needed for the farming process, offering a glimpse of how technology will be able to transform farming in future.
Besides the vertical farm, the technology has also been used in an automated kitchen, where it helps with food processing to ensure cooking consistency. Inovo Robotics is also teaming up with a programming company to develop a system for high-resolution 3D scanning.
Inovo Robotics’ technology is being used to cultivate fresh organic produce at Farm66’s futuristic indoor farm inside an industrial factory building in Hong Kong. Photo: Farm66
Popularising robots for everyday use
Before setting up his own venture, Cheung spent more than a decade working as an engineer, when he witnessed first-hand how robots can help businesses scale their operations.
In 2016, Cheung and a colleague co-founded Inovo Robotics to popularise the everyday use of robot technology by businesses.
Its launch product, Modular Arm, with an adjustable system of six fully rotatable joints, gives the robot the flexibility to reach different positions. The robot’s modularity also gives customers an easy mechanism to choose longer or shorter arms, depending on their configurations.
Cheung says while large manufacturing companies often require tools that can automate a repetitive task, smaller businesses look for collaborative robots that can work alongside staff to complete different jobs at the same time.
“Smaller businesses tend to have smaller batch sizes and tighter spaces,” he says. “That is where a collaborative robot really comes into its own.”
Jonathan Cheung says Inovo Robotics’ modular robot technology offers small businesses a variety of options thanks to its adjustable flexible joints and the choice of using shorter or longer arms.
Inovo Robotics currently has two offices at Hong Kong Science Park, a government-run start-up incubator, and London, in the United Kingdom, as it seeks to tap into both the Asia-Pacific and European markets.
Cheung says Hong Kong has proved an ideal location to scale up his business because of its proximity to hi-tech research and an abundance of talent.
“[We can] be close to our supply chain, which allows us to manage it closely and deliver the best product to our customers,” he says.
“At any point in Hong Kong, you are probably within 25km to five or 10 great universities,” he adds. “There is a wealth of talent to be able to tap into – there are only a few countries with that level of accessibility.”
Revolutionizing academic research
Another Hong Kong start-up, Nikyang, has also developed fully automated laboratory equipment to help academic researchers increase the reliability of data collected in experiments.
Today, its automation technology has been applied in many settings, such as research institutes and pharmaceutical and biotechnology companies.
The venture was founded by Hongkonger Eric Wong in 1999 with the initial goal of helping researchers in traditional Chinese medicine (TCM) to conduct analysis in a more systematic way.
“The basic dream of Nikyang was originally to pursue TCM research to gain a better understanding,” says Wong, who graduated with a master’s degree in biochemistry in Canada.
“I thought we needed a more standardized way of doing analysis in TCM to collect valid and precise information.”
Eric Wong, the founder of automation company Nikyang, says the use of robotic technology allows researchers to conduct more systematic analysis.
When he started his business journey by reaching out to laboratories in Hong Kong and mainland China, he realized that researchers wanted to use machines to help them follow the correct procedure as closely as possible while carrying out repetitive work.
However, many automated instruments available then lacked the ability to carry out different steps in lab research, he says, rendering them error-prone when applied in studies.
To solve the problem, Wong collaborated with Chemspeed, a Switzerland-based provider of lab equipment, in developing specific instruments for TCM research.
His team has integrated Chemspeed’s tools with robotic arms and wearables to increase collaboration between researchers and machines in conducting the analysis.
However, he realized the company would not be sustainable if it focused solely on serving the TCM industry, so he later diversified the business and began developing solutions for different settings.
In 2008, Nikyang began receiving orders from petrochemical companies in China, which gave Wong a lifeline to sustain his business and pursue his dream in TCM research.
The venture now places an emphasis on boosting effectiveness by providing an immerse lab experience.
Its SmartLab product, which is still under development, is set to integrate sensor technology, smart wearables, and cloud data management to help researchers work more efficiently with machines.
Nikyang’s SmartLab, which is still under development, will integrate sensor technology, smart wearables, and cloud data management so researchers can work more efficiently with machines. Photo: Nikyang
Nikyang has its headquarters at Hong Kong Science Park, where it carries out most of its research and development work. To tap into the China market, it has also opened branches in Beijing, Shanghai, and Guangzhou to sell its products.
Wong says Hong Kong has served as an ideal location to grow his company because of its connectivity with China and different parts of the world.
“Hong Kong is definitely unique in terms of being a super-connector between the East and the West,” he says.
The city’s world-class financial market and sound legal system have also helped start-ups in raising capital and developing ideas as they embark on their journey.
Pioneering spirit
Both Wong and Cheung believe it is important for aspiring innovators to be passionate about their business vision to help them overcome challenges when developing and selling the products.
Wong, who spent a decade before he found a way to make his business sustainable, says it was vital to remain dedicated because many innovators experience failures before they can get their businesses on track.
“You need to have passion and a big heart to accept failure, and [an] even bigger heart to think and take risks,” he says.
Eric Wong, who spent a decade before finding a way to make Nikyang sustainable, says aspiring innovators should be passionate about their business vision – and not focus only on profits.
Wong also advises young entrepreneurs not to look only at making profits if they want to make a difference in the world.
“Money is only a by-product,” he says, adding that many successful pioneers often have to make substantial investments before they are able to disrupt the industry.
Cheung agrees that innovators must feel empowered to turn ideas into reality.
“My advice is to really focus on the business model,” he says. “It’s a very, very difficult journey to go on, and it’s very, very rewarding as well. And it’s very important to make sure you stay true to what you believe in.
“Having an idea that you believe in wholeheartedly, that you are willing to give your time and commitment to, is a good validation that you are on the right track.”
Morning Studio is the commercial content team of the South China Morning Post (SCMP). It aims to engage readers through storytelling while enabling the brand behind the content to achieve its marketing objectives. The Morning Studio team consists of specialists in various areas such as journalism, multimedia graphics, video production, digital technology, and marketing.
Iron Ox Announces Next Robotic Farm In Lockhart, TX
Iron Ox has purchased nearly 25 acres of land and plans to build a new, state-of-the-art facility on the property
November 6, 2020
LOCKHART, TX, — Iron Ox, a leader in robotics and AI-enabled farming with a mission to solve food insecurity, and the City of Lockhart, Texas today announced that Iron Ox will expand their operations to the city with plans to break ground on a new facility this December, bringing new tax revenue and jobs to Lockhart.
Since 2015, Iron Ox has developed hybrid robotic greenhouses that support a range of produce offerings. To bring those produce offerings to new communities, the company identified Texas as the next state in their national expansion plan with its favorable business environment and rich history of agriculture.
“We’re proud to make Lockhart our next farm outside of California,” said Brandon Alexander, Iron Ox CEO & Co-founder. “Lockhart’s city government, as well as their planning and development staff, worked diligently with us throughout this process and made us feel right at home. In addition, the city's central location within the Texas triangle and short drive from Austin, allows for strong distribution lanes of same-day grown and harvested products throughout the entire state of Texas, making the city the ideal choice for our robotic greenhouse growing platform”.
Iron Ox has purchased nearly 25 acres of land and plans to build a new, state-of-the-art facility on the property. This new facility will house the company’s natural light greenhouses, processing operations and AI-enabled robots to bring fresh, clean and healthy food to new customers and communities throughout Texas.
“The addition of Iron Ox to the Lockhart business community represents synergy between our city’s storied history in agriculture and our growing technology sector,” said Lockhart Mayor Lew White. “The food and beverage processing industry is one of four business sectors Lockhart has targeted in its 5-year economic growth plan because our city’s unique advantages align perfectly with the needs of companies like Iron Ox.”
Mike Kamerlander, Director, Economic Development, represented the Lockhart Economic Development Corporation (CEcD) on this project.
“As Lockhart continues to grow, Iron Ox and companies like it are essential to our economic vitality and future. We thank them for their investment and commitment to Lockhart.”
About Iron Ox
Iron Ox launched the world’s first autonomous farm in October 2018, leveraging advancements in plant science, machine learning, and robotics. The Iron Ox team develops AI-enabled, autonomous technology that enables fresher, more consistent produce to be grown and distributed globally. The company’s goal is to service thousands of communities with the freshest and healthiest products, while establishing global reach and impact on food security.
For more information, visit www.ironox.com.
About Lockhart Economic Development Corporation
The Lockhart Economic Development Corporation, a department within the City of Lockhart, is designed to provide a range of business and economic development assistance. To learn more about opportunities in Lockhart, visit www.lockhartedc.com.
Contact Info:
Taylor Aldredge
570-534-4754
VIDEO: AI-Controlled Vertical Farms Promise Revolution In Food Production
These upright farms take up only 2 acres yet produce 720 acres worth of fruit and vegetables. Lighting, temperature and watering are controlled by AI-controlled robots
DECEMBER 30, 2020
by Peter Grad, Tech Xplore
When you think about it, early civilizations had a rough time when it came to dinnertime. With no supermarkets, McDonald's, or Cheesecake Factories, you pretty much had to find and prepare your own meal every day. And since Uber would not be invented for another 14,000 years, primitive peoples around 12,000 BC had to walk, sometimes for miles, and learn to hunt, fish, gather and cook for their daily meals. In the rain. Even on Sundays.
Farming evolved quite a bit since then. But with a world population hurtling towards 8 billion, we face a problem. As the 18th-century economist Thomas Malthus observed, the human population increases geometrically, while food production increases only arithmetically. That means the more civilization grows and thrives, the more likely it will be unable to keep up with demands for food.
While advances in food technology have helped forestall Malthus' dire predictions, there remains a great concern for the future of food production as the Earth's population soars on a planet with shrinking farming real estate. National Geographic recently predicted that by 2050, there will be more than two billion additional mouths to feed while the Earth's irrigable land remains essentially the same.
A San Francisco agricultural-technical startup thinks it might just have an answer. Nate Storey, who co-founded the appropriately named Plenty, wants to reinvent farming.
To do so, he has constructed climate-controlled vertical farms that are so promising, they have drawn $400 million in funding from former Google Chairman Eric Schmidt, Amazon's Jeff Bezos, and SoftBank.
These upright farms take up only 2 acres yet produce 720 acres worth of fruit and vegetables. Lighting, temperature and watering are controlled by AI-controlled robots. Sunlight is emulated by LED panels, so food is grown in optimal conditions 24/7. And water is recycled and evaporated water recaptured so there is virtually no waste.
The operation is so efficient it uses 99 percent less land and 95 percent less water than normal farming operations.
"Imagine a 1,500-acre farm," Storey says. "Now, imagine that fitting inside your favorite grocery store, growing up to 350 times more. That's efficient."
It is so efficient that these rows of hanging plants produce 400 times more food per acre than a traditional farm.
AI monitors growth patterns and constantly adjusts environmental factors such as temperature, water, and light patterns to ensure ever-more efficient and economical output.
In an era that has seen food production lines disrupted by a pandemic, wildfires, and hurricanes, Plenty's approach will play a key role in ensuring future stability in the food chain.
Plenty's website explains vertical farming "free agriculture from the constraints of weather, seasons, time, distance, pests, natural disasters, and climate."
Also noteworthy is that the crops are grown "GMO-free" and use no pesticides or herbicides, according to Plenty.
Plenty will soon supply more than 400 stores in California with its produce. The company says its packaging is specially designed to keep produce fresh longer and is 100 percent recyclable.
In October, Driscoll's, a leading producer of fresh berries, reached an agreement with Plenty to produce strawberries year-round in its Laramie, Wyoming-based farming operation, currently the largest privately-owned vertical farming and research facility in the world.
The Plenty website lists several products currently offered in stores, including lettuce, arugula, bok choy, mizuna and kale.
If the first civilizations to invent farming back around 12,000 BC only had the convenience of vertical farming, maybe they could have saved 8,000 or so years by spending more time working on inventing the wheel. And ear pods.
Explore further
The yield potential of wheat grown in controlled-environment vertical farms
Lead photo: Credit: Plenty
100% Robotization Allows Constant Quality Produce
"One of the biggest bottlenecks for most vertical farms is labor-intensity and associated costs. Our first focus was to reduce manual handling," says Ard van de Kreeke, Growx's CEO and founder
"One of the biggest bottlenecks for most vertical farms is labor-intensity and associated costs. Our first focus was to reduce manual handling," says Ard van de Kreeke, Growx's CEO and founder.
Growx has recently been featured in the 75th edition of RuMoer Magazine by BOUT, a master student association program in Building Technology at TU Delft, the Netherlands. The 75th issue is dedicated to urban farming as a solution for reconnecting the urban population to their food sources.
Ard continues, "Not only to reduce cost but also to ensure a constant quality of produce. The implementation of 100% robotization was successfully introduced in 2020. This not only makes a huge difference in labor costs and produce quality but also keeps the cell extremely clean. Human interfaces are only needed for malfunctions and checks. Another additional advantage is that there is no need to keep aisles and room for personnel to move around."
Each plant (gutters) continuously records broad water and nutrients, exposure, and air quality. But also a photographic representation in visible and infra-red light. This data stream is centrally stored and analyzed with the aim of developing optimal cultivation profiles.
Growx's robots pick up the entire process from start to finish, in other words, from seeds to harvest. "As soon as the plant moves on to the next phase of the growing cycle, the robot can respond automatically. Think of different light- or water composition," says Ard.
The company created a closed-loop system, where 100% of their waste is recycled to produce energy, CO2, water, and nutrients. They use an anaerobic digester for all the waste, which results in biogas that can be used for heat pumps and CO2 for the plants to use.
The complete article can be found here.
For more information:
Growx
info@growx.co
www.growx.co
Food Trends Suppliers Should Know to Stay Ahead of the Curve in 2021
With growing concerns about climate change, sustainability and healthy living, 2021 will bring new trends to the food industry. Plant based foods are expected to increase in popularity as more people try to consciously live a more sustainable life.
From insects and pumpkin-seed oil to Brad Pitt-branded wine and transparent packaging, these are the food trends expected to take the U.S. by storm in 2021.
What Will People Be Eating in 2021?
It’s predicted that Americans will be consuming a lot more of the following foods and drinks in 2021:
Insects — According to Forbes, 2.5 billion people around the world eat cooked or raw insects regularly. Many in the U.S. still consider the concept of insect consumption a little grotesque, but attitudes are expected to shift in the coming months with several startups, including Exo cricket protein bars in New York, securing significant funding from investors.
Boxed wine — It’s hard to believe that boxes of wine were considered classy before they were tacky. But in 2021, consumer appreciation for boxed wine is predicted to return. It’s easier to store, cheaper to transport, generates half the carbon dioxide emissions, and has a longer shelf life than its glass-bottled counterparts.
Alternative oils — Whole Foods Market predicts that consumers will become more experimental in their use of oil, choosing walnut, pumpkin seed, and sunflower seed oil over traditional options like olive oil.
Celebrity alcohol — There was an arguably better time when everyone knew someone who wore the Britney Spears perfume. But in 2021, it’s all about Brad Pitt’s rosé and Cara Delevingne’s prosecco, as alcohol brands and vineyards look to drive revenue through partnering with big-name celebrities.
Kombucha — Kombucha is a fermented, lightly effervescent, sweetened black or green tea drink that first hit the mainstream in 2018. Since then, its health benefits have been lauded, and the drink has been growing in popularity. It’s gluten-free and can be filled with live probiotic cultures.
Sweet and Umami — The Green Seed Group suggests that the big flavor combination of 2021 will be umami and sweet. Think rice infused with fish sauce caramel and nori and pork floss.
How Will People Be Eating in 2021?
It’s not just what people eat and drink that will change in 2021, but the entire culture surrounding it.
COVID-19 has contributed to a rise in passionate amateur chefs. With so many people spending much of 2020 stuck at home with extra time on their hands, cooking has become something of an outlet. Indeed, 74% of respondents to a Sensodyne/OnePoll survey said they used cooking as a coping mechanism to manage the stress of being at home, 44% have learned a new recipe, and 32% have taken online cooking classes.
Reduced access to on-the-go, takeout food has seen breakfast truly become the most important meal of the day, and the demand for interesting and diverse breakfast recipes will increase into 2021. Cooking enthusiasts are also investing more time and effort in making baby food and looking for creative takes on staple meals.
Coupled with this newfound enthusiasm for cooking is, unsurprisingly, a newfound enthusiasm for health and wellbeing. Forbes reports that 54% of American consumers care more about the healthfulness of their food and beverage choices in 2020 than they did in 2010. This will see demand for superfoods, probiotics, and supplements grow in 2021, with many food suppliers already incorporating functional ingredients like vitamin C which promise to support the immune system. In a June 2020 survey conducted by GlobalData, 23% of global consumers confessed to stockpiling vitamins and supplements.
COVID-19 has certainly driven Americans to evaluate the relationship they have with food and drink but, fortunately, extreme diets and food fads are expected to lose popularity in 2021. Instead, people are expected to take a healthier and more sustainable approach to healthy living by embracing balance and moderation.
How Will Food and Drink Be Packaged in 2021?
Before COVID-19, food and drink packaging was headed in a very sustainable direction, with consumers increasingly concerned about excess waste and ocean-bound plastics.
But the pandemic has led to increased concerns about biosafety, particularly surrounding the packaging of food and drink. In recent years, many retailers have committed to eliminating unnecessary packaging, but some of these efforts will likely be undone in 2021 due to health and safety concerns and retailers’ desire to reassure their customers. Starbucks, for example, banned the use of reusable cups at the beginning of the coronavirus outbreak.
Despite these setbacks, developments in sustainable and environmentally friendly packaging will continue in 2021.
Other trends will include an increase in transparent windows within food packaging that allow consumers to assess product quality, and QR codes, which can verify product and ingredient claims.
How Will Attitudes to Sustainable Living Change in 2021?
More than two-thirds of consumers want to ensure their everyday actions have a positive impact on the environment. This includes an interest in sustainably produced items, and a shift towards the consumption of plant-based proteins: in 2020, 28% of Americans ate more proteins from plant sources than they did in 2019. Another sustainability trend will see food suppliers up-cycling underused ingredients in a bid to reduce food waste.
Although the year 2021 won’t include a country-wide shift to veganism, retailers can expect increased demand for plant-based food as consumers commit to a more balanced diet and look to reduce their meat and dairy intake.
Image Credit: Rido / Shutterstock.com
Laura Ross Dec 15, 2020
AppHarvest’s Mega-Indoor Farm Offers Economic Alternative To Coal Mining For Appalachia
AppHarvest is taking advantage in the new wave of high-tech agriculture to help feed a growing population and increase domestic work opportunities in a sustainable manner.
Inside AppHarvest's 60 acre state-of-the art indoor farm in Morehead, KY.
In the first year of business, Jonathan Webb and his growing team at AppHarvest are riding high on what he calls the “third wave” of sustainable development: high-tech agriculture, following the waves of solar energy and electric vehicles. Since launching the concept in 2017, Webb and AppHarvest have raised more than $150 million in funding while building and opening one of the largest indoor farms in the world on more than 60 acres near the Central Appalachian town of Morehead, Kentucky.
For Webb, who grew up in the area and has a background in solar energy and other large-scale sustainable projects, AppHarvest is both a homecoming and a high-profile, purpose-driven venture that addresses the need for additional production to feed a growing population and reduce imported produce.
Webb’s vision for AppHarvest was inspired in part by a National Geographic article on sustainable farming in the Netherlands, where indoor growing is part of a national agriculture network that relies on irrigation canals and other innovations. He traveled across the Atlantic Ocean to see the farmers in action, then decided it was a venture he wanted to pursue — in his home state of Kentucky, where the coal industry is in decline and unemployment levels are on the rise.
“Seeing that the world needs 50% to 70% more food by 2050, plus seeing that we’ve shifted most of our production for fruits and vegetables down to Mexico — produce imports were tripled in the last 10 to 15 years,” he says. “I would go to a grocery store, pick up a tomato, and it could be hard, discolored. That’s because it’s been sitting for two weeks on a semi truck, being bred for transportation. So first it was seeing the problem, then asking, ‘How do we solve the problem?’”
As part of my research on purpose-driven businesses and stakeholder capitalism, I recently talked with Webb about AppHarvest’s whirlwind initial year in business, successful investor fundraise, plans to go public, and B Corp Certification.
Good for Business, Good for Community
Jonathan Webb, founder and CEO of AppHarvest
“Where we’re doing what we’re doing is incredibly important. One of our biggest competitive advantages, frankly, is doing it here,” he says. “Some of the hardest-working men and women are the people in this region that power the coal mines, and all we’re trying to do is tap into that and harness that passion. It’s good for our business, but it's good for communities.”
The location has been central to AppHarvest’s benefit in another way, Webb says, as local enthusiasm for the project enabled swift construction that likely would’ve been a challenge in some other regions.
“It's all about economies of scale. We have to build a really big facility to get our costs on materials down so that we can compete with products that are being imported into the country from Mexico,” he says. “We built one of the largest facilities in about a year, so speed and scale are definitely advantages for the company, and a lot of that’s possible based on where we’re operating here in this region.”
While the Bluegrass State has been a good home for AppHarvest, Webb wants the business to be a resource for nearby communities and a beneficial workplace for residents.
“A fundamental part of the way we’re building and growing this company is that every entry-level employee gets full health care, full benefits, living wage, paid time off. So we’re not just creating jobs, we’re creating a lifestyle for your career path,” he says. “We want to see people with high school degrees in this region grow with the company and be assistant growers and head growers three, four years from now. I know this region, and I know what people can do here. Those are the success stories that I look forward to having happen.”
Creating Positive Stakeholder Impact
Producing needed food and building a stronger workforce aren’t the only goals at AppHarvest; Webb says growing produce sustainably, with minimal impact on the environment, also is paramount.
“We’re land constrained in the world, and water constrained. And we have to grow a lot more food and use fewer resources,” he says. “It’s simple in theory; it’s complex in scale. Just the fact that the place is so big is what makes this challenging. But we’re collecting rainwater on the roof and using it directly on the root of the plants. We’re growing hydroponically, and as a result we can use 90% less water than open field agriculture.
“The way we treat water and handle water and how we use rainwater efficiently is the really biggest driver of resiliency long term for us.”
In building a business to have a positive impact on workers, community, and environment, Webb also created a company that is a natural fit for the B Corporation community made up of businesses that achieve a certification based on how well they incorporate all stakeholders into their policies and practices.
“The impact side of this is incredibly important. We didn’t chase certifications,” he says. “We just did the right things: We’re paying a living wage, we're offering health care. It’s the right way to do business. And as a result, we get a huge ROI on our dollar.”
Thanks to its bottom-line success and future promise, AppHarvest has found favor with investors, including Martha Stewart and venture capitalists; and is part of a growing cohort of businesses with a social purpose that are finding traction in the public markets. The company announced in September that it’s going public through a combination with special purpose acquisition company Novus Capital Corp. (Nasdaq: NOVS).
“Why are we going public now? Because full transparency in agriculture is desperately needed,” Webb says. “We want the people who buy our fruits and vegetables to also have the ability to buy into our company. We want the record. We want the institutional rigor. It’s hard to have this spotlight this early, but it’s making us stronger.”
Christopher Marquis, Contributor
The Underwater Habitat With A Greenhouse
Swiss designer Yves Behar has unveiled his design for French ocean conservationist Fabien Cousteau's underwater pressurised research station that will be "the ocean's equivalent to the International Space Station".
29-07-2020 | Msn News/ India Block
Swiss designer Yves Behar has unveiled his design for French ocean conservationist Fabien Cousteau's underwater pressurised research station that will be "the ocean's equivalent to the International Space Station".
Behar designed the station, which is called Proteus, for the Fabien Cousteau Ocean Learning Center. It will have its own greenhouse to allow scientists to grow their own food 18 metres under the sea near Curaçao, an island in the Caribbean.
Up to 12 researchers and aquanauts – scientists who remain underwater breathing pressurised air for over 24 hours – will be able to live in Proteus at a time.
Like the International Space Station, Proteus will allow scientists to collaborate and make new discoveries in an inhospitable environment.
"The research station will enable the discovery of new species of marine life, create a better understanding of how climate change affects the ocean, and allow for the testing of advanced technologies for green power, aquaculture, and robotic exploration," Behar told Dezeen.
Living underwater in a pressurised environment, rather than just diving in, allows scientists to spend far more time in the water and only decompress at the end of their assignment.
Proteus is the result of Behar's studio Fuseproject being commissioned by Cousteau, and his non-profit the Fabien Cousteau Ocean Learning Center (FCOLC).
"We needed to understand the constraints that come from building underwater and the challenges of living in an underwater structure," Behar said.
"The social isolation, the humidity, the lack of light and lack of exercise all needed to be addressed," he explained. "I learned about these challenges from Fabien, who had the record as the person who lived longest in an underwater habitat."
© Provided by Dezeen Proteus by Yves Behar
Cousteau broke the record, previously set by his grandfather, with a 31-day-long stay in an underwater laboratory off the coast of Florida called Aquarius.
Behar used Cousteau's experience to inform the design of Proteus, which has two levels connected by a curving ramp with pods set around the edges.
Circular-shaped main spaces are designed to encourage teamwork and social interaction for the scientists. Pods around the perimeter are designed to hold specific laboratories, bathrooms and areas for sleeping.
"Both circular floors are offset to allow as much natural light as possible through skylights and portholes, and are connected by a sloping ramp which creates the opportunity for physical activity," said Behar.
Social spaces will be kept separate from the more humid areas of the wet labs and the moon pool – the space in an underwater habitat where occupants can access the water directly in a protected environment.
© Provided by Dezeen Proteus by Yves Behar
An underwater greenhouse will allow occupants to grow their own food, allowing them to stay underwater for longer and cope more comfortably with the confines of a pressurised environment where no open flames for cooking are allowed.
Behar deliberately gave the underwater habitat a retrofuturist vibe in keeping with the way science fiction has traditionally imagined underwater living.
"Fabien and I looked at many exploratory designs from the 60s and 70s, a golden era of interest for the oceans pioneered by the Cousteau family history," Behar told Dezeen.
"We felt that Proteus could incorporate a new visual language based on modern hull and composite building technology, as well as be a state-of-the-art scientific environment while delivering a comfortable social interior space."
In keeping with the Cousteau dynasty's ocean conservation goals, Proteus will be powered by renewable energy. The habitat will use a mixture of wind, solar, and Ocean Thermal Energy Conversion (OTEC), a process that produces electricity using the difference in temperature between warm water on the surface and cold water from the deep ocean.
Cousteau will head to Curaçao to map the site as soon the borders shut due to the coronavirus pandemic open, hopefully in September. Behar estimates it will then take 36 months to build and lower Proteus to the ocean floor.
Behar hopes Proteus will be one of a series of marine habitats dedicated to research and conservation. As well as scientists, the designer hopes the facility will be able to welcome civilian visitors.
"Proteus is designed to be a scientific environment, but also to create that desire in people to want to visit," he said.
"For me, it’s a lot more exciting to visit Proteus than going to Mars."
Behar embraces technology with his designs, which include plans for 3D-printed houses for impoverished farmers and a wearable UV sensor to protect against skin cancer.
The post Proteus is an underwater habitat with a greenhouse designed by Yves Behar appeared first on Dezeen.
Source: Msn News/ India Block
Photo Provided by Dezeen