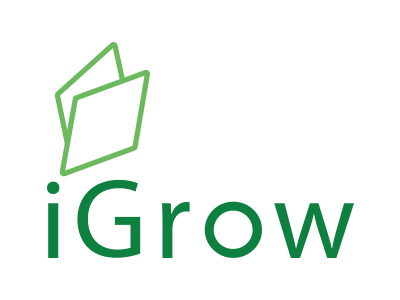
Welcome to iGrow News, Your Source for the World of Indoor Vertical Farming
VIDEO: Indoor Ag Sci Cafe Discusses Indoor Farming In Mexico With Karla Garcia, Hort Americas
“Indoor Farming in Mexico: Current Status and Opportunities”
With Karla Garcia
Microgreens FLN & Hort Americas
This presentation ‘Indoor Farming in Mexico: Current Status and Opportunities’ was given by Karla Garcia (Microgreens FLN & HortAmericas) during our 27th cafe forum on February 23rd, 2021. Indoor Ag Science Cafe is organized by the OptimIA project team funded by USDA SCRI grant program.
The Café presentations are available from YouTube channel.
Upcoming Cafes:
March 30, 11am EST – ‘USDA SBIR (Small Business Innovation Research) Grants Program Overview’ by Dr. Steven Thomson & Melinda Coffman (USDA NIFA)
Interested in giving a talk to share your thoughts and experiences? Contact them
Babylon Micro-Farms Establishes New Corporate Headquarters In Richmond, Virginia
The company has developed disruptive technology - a cloud-based platform that operates vertical farms through a mobile phone app that controls all aspects of farming at the touch of a button
Richmond, VA (February 2021) Babylon Micro-Farms has chosen Richmond, Virginia as the site for their corporate headquarters, opening a new office and R & D space in historic Scott’s Addition. The move from Charlottesville was driven by the company’s growth and need for a larger talent pool - they had been courted by California and Arizona as an up-and-coming tech company in the indoor ag-tech space.
The company has developed disruptive technology - a cloud-based platform that operates vertical farms through a mobile phone app that controls all aspects of farming at the touch of a button. The indoor ag-tech industry is projected to grow globally from USD $121.26 billion in 2019 to USD $167.42 billion by 2025, a compound annual growth rate of 5.4% according to the latest report released by Market Data Forecast last week.
Babylon’s CEO and Co-Founder, Alexander Olesen, commented on the move. “Richmond is the perfect launchpad for our next phase of growth. It has a dynamic business eco-system and gives Babylon the chance to build an even stronger foundation for the future with everything it has to offer.”
Babylon began hiring locally in Richmond prior to the move, scaling up their operations in preparation for the anticipated increase in sales in 2021. Graham Smith, CTO and Co-Founder of Babylon, said “Our growth has been based on significant R & D we were able to accomplish because of support from The Center for Innovative Technology, the National Science Foundation and investors that understood early on the potential for this technology. Richmond offers a hub where innovation and industry intersect and having our headquarters here will fuel our expansion.”
The company expects to triple its workforce in the next three years, adding jobs in every department, from assembly to engineering. For more information visit www.babylonmicrofarms.com or contact janet@babymicrofarms.com for interview requests.
Babylon Micro-Farms team, from left to right: Alexander Olesen, CEO and co-founder; Marc Oosterhuis, COO; and Graham Smith, CTO, and co-founder. Courtesy of Babylon Micro Farms
ABOUT BABYLON MICRO-FARMS
At the touch of a button, Babylon Micro-Farms delivers a simple, yet engaging indoor growing experience. Babylon helps senior living communities, hospitals, schools, and hospitality companies showcase their commitment to providing fresh, nutritious produce and sustainability to their residents, employees, and customers.
They have designed a complete on-site farming service that makes growing simple for anyone, thanks to their plug-and-play Micro-Farms and Guided Growing App. Babylon offers the most affordable, efficient, and advanced vertical farming platform available, remotely managed through the cloud with unparalleled customer service. Since their humble beginnings as a social entrepreneur student project, Babylon have attracted investors from Silicon Valley, been awarded a grant from the National Science Foundation to support their research, patented a groundbreaking technology, and received recognition by Virginia's Governor Northam for their contribution as a technology innovator following their successful application for funding from the Center for Innovative Technology.
Babylon has designed a software platform to reclaim the decentralized food system of the 21st Century - using modular vertical farms that enables anyone to grow local produce on-site, all year round, indoors. They launched their first products focusing on the health care and senior living markets where our vertical farms provide access to food-as-medicine quality food and a variety of therapeutic activities.
Website:
https://www.babylonmicrofarms.com/
Press Contact:
Sharon Rettinger
PODCAST: What Do Saltwater Vertical Farming And Sustainable Coastlines Have In Common?
In the podcast, Heron Farms, a sea beans cultivator, is featured. Heron Farms uses its vertical farm and is also restoring marshland from their home base in Charleston, South Carolina
A podcast by Evolve.ag
Recently Evolve.ag held a podcast on 'What do saltwater vertical farming and sustainable coastlines have in common?'. Their series focuses on what's trending in food and food tech.
In the podcast, Heron Farms, a sea beans cultivator, is featured. Heron Farms uses its vertical farm and is also restoring marshland from their home base in Charleston, South Carolina.
In this episode, Wendy Yared, a food anthropologist, speaks with Sam Norton, the founder of Heron Farms. Inspired by the marsh he grew up playing in, he started the first saltwater vertical farm in the US. Heron Farms grows a type of Salicornia, also known as a sea bean. This plant provides high levels of nutrients like vitamin A, vitamin C, and, not surprisingly, sodium chloride. Chefs sometimes use it as a replacement for salt on fish dishes, like Crudo or ceviche. Beyond the farm, they're also using Salicornia to remediate salt marshes.
They talk about the ecological benefits of Salicornia and how marshland restoration can help turn seawater into a resource instead of a concern for people living in coastal areas. During the podcast, they also dive into the challenges of starting a vertical farm. And how important it is to balance the negative aspects of controlled environment agriculture, like expensive lighting and plastic, with activities that support the ecosystem.
Click here to access the podcast.
For more information:
Wendy Yared, food anthropologist
26 Feb 2021
Jersey City Housing Authority To Host Vertical Farms
The partnership aims to provide more access to healthy food
Partnership Aims To Provide
More Access To Healthy Food
February 25, 2021
AeroFarms will construct and maintain 10 farming sites, the first of which will be built at the Curries Woods Community Resource Center as part of a new agreement between the city, AeroFarms, and the Jersey City Housing Authority.
Vertical farms will provide free nutritious food to residents in need now that the Jersey City Council has adopted a resolution approving an agreement between AeroFarms, the city, and the Housing Authority.
The new agreement means that vertical farms will be opened at Curries Woods and Marion Gardens.
The public housing farms, which will be funded by the city, will increase healthy food access where needed most and encourage residents to live healthier lifestyles.
The Jersey City Department of Health and Human Services (HHS), AeroFarms, and Jersey City Housing Authority will collaborate with the Boys & Girls Club and Head Start Early Childhood Learning programs to support produce distribution and healthy eating education.
“We’ve worked hard to keep the Vertical Farming Program a priority despite the impacts from this pandemic, which have disproportionately affected the more economically challenged areas and exacerbated societal issues such as healthy food access,” said Mayor Steven Fulop.
“We’re taking an innovative approach to a systemic issue that has plagued urban areas for far too long by taking matters into our own hands to provide thousands of pounds of locally-grown, nutritious foods that will help close the hunger gap and will have an immeasurable impact on the overall health of our community for years to come.”
City farming
AeroFarms will construct and maintain the farming sites. The first will be built at the Curries Woods Community Resource Center. The Boys & Girls Club and Head Start will integrate the vertical farm as a learning tool for youth within their educational programming.
Head Start, operated by Greater Bergen Community Action, plans to integrate greens into its early childhood meals.
AeroFarms indoor vertical farming technology uses up to 95 percent less water and no pesticides versus traditional field farming.
According to the city, the JCHA-Aerofarms Advisory Committee will be formed to provide strategic oversight and guidance throughout the program.
The steering committee will include Jersey City residents and stakeholders from the Boys & Girls Club and Head Start.
The city’s Vertical Farming Program will consist of eight additional vertical farms throughout Jersey City in senior centers, schools, public housing complexes, and municipal buildings.
The 10 sites will grow 19,000 pounds of vegetables annually using water mist and minimal electricity, according to the city.
The food is free to residents if they participate in five healthy eating workshops, and they will have the option of participating in a quarterly health screening.
“As a Certified B Corporation, we applaud Mayor Fulop’s leadership and advocacy to bring healthier food options closer to the community, and we are excited to launch together the nation’s first municipal vertical farming program that will have a far-lasting positive impact for multiple generations to come,” said Co-Founder and CEO of AeroFarms David Rosenberg.
The city’s Health and Human Service Department will run the program with a health-monitoring component to track participants’ progress under a greener diet, monitoring their blood pressure, cholesterol, diabetes, and obesity.
Crops will be integrated with other Healthy Food Access initiatives, including senior meal programs, according to the city.
“Access to healthy food and proper nutrition is directly linked to a person’s mental and physical health, and can decrease risks of chronic diseases while increasing life expectancy,” said Stacey Flanagan, director of Health and Human Service for Jersey City. “This past year has shed light on the health disparities that exist in urban areas nationwide, which is why we’ve remained focused on closing gaps where healthy food access is most needed, specifically for our low-income, youth, and senior populations.”
Healthy food initiatives
The Vertical Farming Program is part of the broader initiative from the World Economic Forum (WEF) toward partnerships with cities.
Jersey City is the first in the world to be selected by WEF to launch the Healthy City 2030 initiative, which aims to catalyze new ecosystems that will enable socially vibrant and health-centric cities and communities.
The vertical farming initiative is the latest and broadest effort Jersey City has launched around food access, including more than 5,000 food market tours for seniors to educate them on healthy eating, and the “Healthy Corner Store” initiative.
According to a 2018 city report, much of Jersey City could be described as a “food desert.”
The USDA defines a food desert as “a low-income census tract where either a substantial number or share of residents has low access to a supermarket or large grocery store.”
This means at least 500 people or 33 percent of the population live more than a mile from a supermarket or large grocery store.
According to the city, these deserts have led to an increased rate of diabetes, heart disease, obesity, and other diet-related illnesses in the more marginalized communities of Jersey City.
“We are thrilled that the vertical farms that will be installed at JCHA sites to enable some of our most vulnerable residents, including low-income households, children, and seniors, to have access to fresh, green produce that is nutritious, delicious, and easy to prepare,” said Vivian Brady-Phillips, director of the JCHA.
For updates on this and other stories check www.hudsonreporter.com and follow us on Twitter @hudson_reporter. Marilyn Baer can be reached at Marilynb@hudsonreporter.com.
Swegreen’s New In-Store Farming Service Will Be Scandinavia’s Biggest
Swegreen's innovative in-store service will make the Ica Maxi megamarket in Linköping, located in Mid-Sweden, the first of all Sweden’s megamarkets to offer fresh herbs and salad grown from seed to finished plant inside the store
March 01, 2021
Swegreen’s board member Pierre Mohlin meets up with Milleriine Axelsson who will be responsible for the in-store growing unit from Ica Maxi’s side.
Swegreen launches ‘NextGen’ of super-efficient in-store vertical farming service when Ica Maxi megastore in Linköping puts the company’s Farming-as-a-Service growing unit for leafy greens right at the entrance of the store. The new vertical farm will be Scandinavia’s largest in-store cultivation.
Swegreen's innovative in-store service will make the Ica Maxi megamarket in Linköping, located in Mid-Sweden, the first of all Sweden’s megamarkets to offer fresh herbs and salad grown from seed to finished plant inside the store. Every day, several hundred fresh leafy vegetables can be harvested for the store's customers.
- It won’t get more locally produced than this, says Ica Maxi Linköping's CEO Tomas Lundvall.
The actual cultivation facility, which takes place in the middle of the store entrance, will have glass walls from floor to ceiling. This, together with an eye-catching light from the plants' LED system, will leave a clear mark on the entrance to the store when the installation is ready later this spring.
- We have chosen a central place for cultivation to really clarify our commitment to a greener and more climate-smart food production. The cultivation will be a destination in itself for our customers, and once they get the opportunity to taste these crops, many will understand what fantastic quality such a cultivation system offers, says Tomas Lundvall CEO and owner of the megamarket.
- Our salad and our herbs will simply be the smartest greens in town, he adds.
The new in-store plant is based on hydroponic cultivation technology. Nutrition comes directly from the water, which can be recycled. The system can also recover energy, carbon dioxide and nutrients. Behind the innovation is the all-Swedish technology company Swegreen, which has developed both the cultivation room itself and the AI-based control system which, via a cloud service, controls and optimizes the environment in the cultivation.
- We are very proud to work with the team for Ica Maxi in Linköping for this installation, their commitment to hyper-local and climate-smart produced food shows that this is a megastore at the forefront, says Swegreen's CEO Andreas Dahlin.
- Ordinary vegetables sold in Swedish supermarkets have traveled an average of 3,000 kilometers, while these crops have not been transported at all. Of course, it gives better taste, better consistency and durability - and also better nutritional value, he continues.
The new in-store service will start delivering leafy greens in May, and it will then be able to supply the megastore with different kinds of herbs such as coriander, dill, and parsley, and also lettuce and cabbage. The crops will also be used for in-house production in the store's own kitchen, and in future, there will be the possibility of more types of vegetables.
Swegreen is an all-Swedish ESG AgTech company combining advanced technology with data and plant science to efficient produce high quality and climate smart leafy greens in urban environment. Swegreen offers a prescription based growing service called Farming-as-a-Service (FaaS). With it, any supermarket or restaurant owner can supply their customers with fresh, nutritious, well-tasting and hyper-locally produced leafy greens all year. See more at www.swegreen.com
ICA Maxi Stormarknad Linköping was established in 1993 as one of the ICA Groups first Maxi megamarkets in Sweden. It’s the largest of its kind in the region and one of the largest ICA-stores all categories. The total sales area is 8,000 sqm and it employs around 300 persons. See more at: www.ica.se/butiker/maxi/linkoping/maxi-ica-stormarknad-linkoping-8900/start/
GoodLeaf Farms Launches Aggressive Expansion Plans
GoodLeaf will bring its innovative and proprietary controlled-environment agriculture technology to more Canadian markets over the coming year
NEWS PROVIDED BY
McCain invests in a national network of vertical farms to bring tasty, local food to Canadians
GUELPH, ON, - With the closure of a successful new funding round, GoodLeaf Farms is embarking on an aggressive growth and expansion plan to build a national network of vertical farms that will bring fresh, delicious, nutritious and locally grown leafy greens to Canadians across the country.
Backed by a sizeable investment from McCain Foods Limited — which has increased its total investment in GoodLeaf to more than $65 million — GoodLeaf will bring its innovative and proprietary controlled-environment agriculture technology to more Canadian markets over the coming year, providing more Canadian consumers with year-round local food that is typically imported from the Southern United States or Mexico.
"From our start in Truro to our first commercial farm in Guelph, GoodLeaf has built a strong foundation for future growth," says Barry Murchie, Chief Executive Officer of GoodLeaf. "We want to be a global leader in vertical farming. Our first step to accomplishing that is ensuring we have a strong footprint in Canada, giving Canadians access to top quality, nutrient-dense, sustainably grown and pesticide-free leafy greens 365 days a year."
GoodLeaf opened its first commercial vertical farm in Guelph, Ont., in the fall of 2019. By the end of 2021, GoodLeaf is planning two more indoor vertical farms — one to serve the grocery and foodservice networks in Eastern Canada, and one for Western Canada.
The exact locations will be announced shortly.
"It is our intention to build farms that support the Canadian grocery store network, foodservice industry and consumers," says Mr Murchie. "We want to change what people are eating by providing a fresh, healthy and local alternative that, until now, hasn't been available in Canada. We are driving a new way to grow food, with disruptive technology that brings consumers leafy greens from their own backyard. This is a fundamental game-changer."
GoodLeaf's vertical farm grows to produce on hydroponic trays stacked in multiple horizontal levels. A proprietary system of specialized LED lights is engineered to emulate the spring sun, giving plants the light they crave to maximize photosynthesis. The indoor controlled environment is almost clinical, meaning there are no pesticides, herbicides or fungicides used. It is also immune to weather extremes, such as summer droughts or late spring frosts that can be lethal to crops.
Furthermore, having a local source of year-round food is vital to Canada's food security and sovereignty, concerns that were in the spotlight at the height of the COVID-19 pandemic as shoppers were faced with rapidly dwindling supplies on grocery store shelves.
At its 45,000-square-foot Guelph farm, every day GoodLeaf is harvesting microgreens (Spicy Mustard Medley, Asian Blend, Micro Arugula, Micro Radish and Pea Shoots) and baby greens (Ontario Baby Kale, Ontario Baby Arugula and Ontario Spring Mix) for Ontario grocery stores, ensuring a local supply of fresh, nutrient-dense leafy greens all year long.
GoodLeaf produce is exceptional in a salad, as a topping for burgers and sandwiches, as a kick of nutrients in a smoothie or as an ingredient to elevate your favourite dish.
Follow GoodLeaf Farms on Instagram @goodleaffarms and Like it on Facebook at /GoodLeafFarms.
About GoodLeaf Farms:
With a passion for delicious, nutrient-rich greens, GoodLeaf was founded in Truro, NS, in 2011. Using innovative technology and leveraging multi-level vertical farming, GoodLeaf has created a controlled and efficient indoor farm that can grow fresh produce anywhere in the world, 365 days of the year. The system combines innovations in LED lighting with leading-edge hydroponic techniques to produce sustainable, safe, pesticide-free, nutrient-dense leafy greens. GoodLeaf has ongoing R&D Programs in collaboration with the University of Guelph, Dalhousie University and Acadia University.
Learn more at goodleaffarms.com.
About McCain Foods (Canada)
McCain Foods (Canada) is the Canadian division of McCain Foods Limited, an international leader in the frozen food industry. McCain Foods is the world's largest manufacturer of frozen potato specialities, and also produces other quality products such as appetizers, vegetables and desserts that can be found in restaurants and retail stores in more than 160 countries around the world. In Canada, the company has eight production facilities with approximately 2,400 employees and, in addition to its famous French fries and potato specialities, makes frozen desserts, snacks and appetizers.
SOURCE GoodLeaf Farms
For further information: Michelle Hann, Senior Consultant, Digital and Communications, Enterprise Canada, mhann@enterprisecanada.com, 613-716-2118
LEDs Light the Way to Efficient Urban Farming
The global pandemic has turned the world upside down, bringing unprecedented change to the way we live, work and play. But the crisis has also paved the way for important new innovations
By Mike Martens, Senior Manager, Illumination Marketing at Osram Opto Semiconductors, North America
The global pandemic has turned the world upside down, bringing unprecedented change to the way we live, work and play. But the crisis has also paved the way for important new innovations. For instance, massive disruption to the global supply chain is now compelling many nations to ramp up their indoor and urban farming efforts to secure their food supply and feed their people.
Take the desert nation of the United Arab Emirates. Amid the ongoing pandemic, the country is experiencing something of a food crisis. That’s why it recently announced a $100 million investment in cutting-edge indoor farming facilities that can help feed its population. The effort will include the creation of the world’s largest vertical farm to help solve the challenge of local food production.
A key component of vertical farming is LED technology. In places across the globe where farmland is limited, innovative LED lighting solutions offer a major advantage because they can provide the exact light composition that various plants need for ideal growth or to develop certain characteristics. Plants can also be grown in a very space-saving manner and with considerably higher yields thanks to these lighting solutions.
LEDs are more efficient
For decades, traditional high-pressure sodium (HPS) lamps were commonly used for greenhouses and other horticultural purposes but they bring with them many challenges. They have a short lifespan and are often only suitable for top lighting in greenhouses due to their high heat output.
This is a big problem for greenhouse owners because efficient energy use is essential to economic production. In traditional greenhouse and urban farming setups, HPS lights are often inefficient. They do provide light for plants, but it is often not the most efficient wavelength range because the lamps cannot be customized to provide ideal growing conditions for different types of plants.
HPS lights often generate a lot of heat , causing considerable evaporation and ultimately limiting crop yield. What’s more, due to this heat production, HPS fixtures often cannot be placed very close to plant canopy, preventing more efficient vertical-farm setups. After all, you don’t want to singe your produce.
The good news is that innovative LED technologies can alleviate many of these concerns. For starters, LEDs produce almost no radiated heat, allowing for the light fixtures to be placed closer to plants and for plants to be stacked much higher, enabling farmers to grow more produce in smaller spaces while simultaneously reducing water costs.
LED lights also offer customizable wavelengths for different plants’ needs, allowing greenhouse operators and urban farmers to grow specific plants in their optimal conditions. For instance, LEDs can be tailored to supply light with a higher amount of red or blue content, generating exactly the wavelengths the plant, such as iceberg lettuce, tomatoes and basil need for optimal growth.
Urban farming is not a new phenomenon, but LEDs have the power to take it to the next level and more efficiently feed the world. In terms of sheer numbers, LEDs have an average lifespan of 50,000 hours compared to 8,000 hours for HPS lamps, making LEDS much more economical (and better for the environment). Indeed, vertical farms that leverage LED technology can achieve 40% energy savings compared to traditional lighting methods like HPS lamps. And due to the optimized light spectrum at 450, 660 and 730 nanometers, LEDs can provide the perfect lighting for all types of plants, allowing growers to adjust the lighting exactly to the needs of various crops.
LEDs grow healthier produce
LED are the most efficient lighting technologies to date for growing produce. They not only help produce fresh food in smaller spaces without the use of pesticides, they also make it easier for consumers in urban areas to obtain fresh and healthy food quickly, a must, considering the planet’s ever-growing population and ever-decreasing farmland.
Consumers in urban areas often rely on produce grown in faraway places that is brought to them on trucks using fossil fuels. This produce is often grown with pesticides to keep insects away, as well as fertilizers, so plants can be grown throughout the year, even in suboptimal conditions. All of these factors contribute to climate change and more polluted water sources. With horticultural LEDs, these issues can be mitigated.
LEDs also provide optimal growing conditions in any environment with minimal water waste, while reducing the need for pesticides in indoor growing environments. Communities then have the ability to grow produce closer to home, which allows consumers to learn more easily what exactly goes into their food and greatly reduces the fossil fuel usage to get produce from the (urban) farm to their tables. Urban farming has great potential to make positive impacts on local environments and communities. It’s more sustainable and decreases communities’ reliance on foods shipped in at great cost from around the globe.
LEDs light the way
As we grapple with the many concerns facing our modern society, it is imperative to invest in efficient and time-saving technology of all types. LEDs are one of these technologies. Indeed, they light the way to the farms of the future. They will have an enormously beneficial impact on agriculture by dramatically increasing crop production and putting food on every table more efficiently.
Elevate Farms To Expand In New Zealand And New Jersey By Late 2021
Other than building high-tech production facilities and growing leafy greens, Elevate is also in the business of proving its detractors wrong as the company is on track to produce 1 million pounds of leafy greens in one of its 5,000-square foot facilities in Niagara, Ontario
Producing 1 million lbs of Leafy Greens Per Year
Other than building high-tech production facilities and growing leafy greens, Elevate is also in the business of proving its detractors wrong as the company is on track to produce 1 million pounds of leafy greens in one of its 5,000-square foot facilities in Niagara, Ontario.
Elevate is a vertical farming company located in Toronto, Ontario and
producing leafy greens in state-of-the-art facilities. With its Niagara facility spanning 20,000 square feet with a cultivation area spanning 5,000 square feet, it can produce as much food as 100 acres of land-based agriculture. This, according to chief strategy officer Travis Kanellos, is critical to people’s understanding of vertical agriculture and its benefits over other conservation agriculture methods. While organic agriculture strives to improve soil health and conserve biodiversity, the global agricultural land base still cannot support the growing population.
Travis Kanellos, Chief Strategy Officer
Further, organic certifications do not necessarily prohibit the use of any and all chemicals, but instead, greatly restrict the list of certified agrochemicals. Organic agriculture is thus only part of a global agricultural solution, while vertical farming should also play an increasingly important role as it does not use any agrochemicals and demonstrates unparalleled planting density.
Elevate primarily produces leafy greens but has also successfully grown tomatoes, strawberries, beans, and various plant proteins during research trials. With many vertical farms producing crops with low caloric value, such as microgreens and herbs, Elevate is eager to broaden this range and include higher value, higher calorie crops. Nevertheless, Elevate has had significant success producing leafy greens and is reportedly one of few profitable vertical farming facilities that is actually delivering its forecasted yields, which Kanellos attributes to the company’s diligent approach and scientific partnerships.
“Typically we’ve seen the industry of indoor farming; secure funding, build the farms and expect everything to come to them. But building it then trying to figure it out is backwards to us. We’ve spent years of research and commercialized production with intellectual property. When you build a company through 15 years of R&D, along with our core team’s execution track record and all of the experience from our academic partners, we feel that is a pretty good recipe for success.”
The company’s most important partnership is with Intravision, a Norwegian agtech company with additional offices in Toronto and Shanghai. The company’s products include controlled environment systems, LED lighting, and research tools. However, Intravision does not limit itself to simply supplying products; the company also develops partnerships to continuously research and improve production methods in indoor agriculture. So while Intravision does supply much of the hardware for Elevate farms, the two companies have a strong partnership and collaborate throughout project implementation, crop production and aligned business interests.
Looking ahead, Elevate aims to have its pilot facility operating at 100% capacity in the coming months. Also, the company plans to build and begin operating facilities in New Zealand and New Jersey by late 2021.
“Our pilot facility in Toronto allowed us to reach out and develop global relationships. What started in Canada with the 1,000 square foot pilot facility in Toronto has led to agreements across Canada and New Zealand for the construction of more than 10 facilities, with each slated to produce 1 million pounds of produce annually,” says Kanellos.
Elevate is currently deeply entrenched in implementing artificial intelligence to optimize its production systems as well as vision systems to generate actual predictive outcomes. Kanellos is keen on Elevates future stating “we believe the next step for Elevate, aside from global scale, is to deepen the ability for our facilities to become autonomous. Our field-grown yields, profitability at wholesale market prices are great first steps but true AI and facility optimization sets the groundwork for years to come.”
Lead photo: Panoramic view of the pilot facility
For more information:
Elevate Farm
Travis Kanellos, Chief Strategy Officer
+1 905-580-2388
Tkanellos@elevate.farm
www.elevate.farm
For more information:
Intravision Canada
www.intravisiongroup.com
Publication date: Fri 26 Feb 2021
Author: Rebekka Boekhout
© VerticalFarmDaily.com
Would You Like To Host A Strategic HQ In Decentralized Agriculture And Food Supply Systems
Our vision is to strengthen community resiliency and reduce food insecurity on a global scale over time
We would appreciate a city location in Central Europe in order to facilitate our EU-labelled strategy.
Our vision is to strengthen community resiliency and reduce food insecurity on a global scale over time.
For questions and tentative interest please contact:
thomas.tapio@gmail.com
Strasbourg 27th February, 2021 🇫🇷🇪🇺
PODCAST: Join Harry Duran, host of Vertical Farming Podcast, as he welcomes to the show speaker, futurist, and Chief Sustainability Officer at SweGreen, Sepehr Mousavi
Season 2 Episode 26
Join Harry Duran, host of Vertical Farming Podcast, as he welcomes to the show speaker, futurist, and Chief Sustainability Officer at SweGreen, Sepehr Mousavi. Sepehr is a sustainability strategist, innovation catalyst, and a passionate futurist with an international and multicultural background. His organization, SweGreen, is the number one AgTech company in Sweden and is revolutionizing the vertical farming industry by providing futuristic, smart, and circular solutions for controlled-environment growing systems.
In this episode, Harry and Sepehr discuss Sepehr’s unique background and vertical farming origin story. They delve deep into the concepts of symbiosis, smart real estate solutions, and the importance of Research and Development. Finally, Sepehr speaks to the importance of educating the world on vertical farming and what excites him the most about the future of SweGreen and the AgTech industry.
VERTICAL FARMING PODCAST
Listen & Subscribe
Creating A Connected, Community Centered Urban Farm Environment
Street Farm’s micro-vertical farm works with a hydroponic growth system and is designed to be reused again and again. The designs vary in size from 8’ wide x 8’ high x 12’ long to 16’ high to 32’ long
“NYC streets are ripe with potential to start producing their own food," says Julian Lwin with Street Farm. Full and built up through the city might be, lack of space is no excuse for anyone, as Street farms’ vertical farm can be fit also in small public spaces. “We now can claim street space for sustainably grown urban greens the same way we claimed the streets for outdoor dining during COVID.”
COVID forced many countries to rethink their food system, as logistics suddenly got complicated. Also Julian became acutely aware of the need for new retail environments, finding a safer way to interact with food, and purchasing fresh produce. Via an automated dispensing think vending machines & dedicated StreetFarm app.
In this period he saw people taking their activities outside, exercising or even eating out on the streets whereas they would normally do this indoors. With that in mind, he found (conceived) Street Farm, intending to find a solution for growing fresh produce right there in the streets of NYC. “We will fabricate the farms right here in New York’s Brooklyn Navy Yard, to keep the transport emissions to an absolute minimum.” This model can be set up in any city metropolis around the globe where freshly grown produce is missing from the urban environment
Street Farm’s micro-vertical farm works with a hydroponic growth system and is designed to be reused again and again. The designs vary in size from 8’ wide x 8’ high x 12’ long to 16’ high to 32’ long. The smaller ones can be placed in gardens, allowing the larger-scale growing to be done in empty storefronts, city lots, etcetera. Julian dreams of the microfarms to be placed even in schools, libraries, and train stations to show people that food can be grown literally anywhere.
Urban “element" vertical farm
Combining the latest technologies in the field of AI and robotics for monitoring the growth and yield, the New York streets will produce lots of fresh produce for the local population. “With Street Farms we can transform New York from a food desert to a paradise of nutritious, healthy vegetables.” The plan is for the system to monitor the plant growth itself, but for the harvest to be done by employees, thus creating more jobs in the city. “We want these farms to create a connected, community-centered urban farm environment, connecting people to each other and to the food they eat.”
Julian finds it vitally important that people see tangible agriculture grown in public places, rather than hiding vertical farms in post-industrial spaces and rooftops. “Street Farms will connect the community with the products we eat. We aim for a paradigm shift in our relationship to the food we eat and our city landscape.”
Lead photo: The micro modular urban vertical farm satellite
For more information:
Lwindesign
Julian Lwin, Founder
julian@lwindesign.com
www.lwindesign.com
Publication date: Thu 25 Feb 2021
Author: Rebekka Boekhout
© VerticalFarmDaily.com
PHILIPPINES: Smart Farming In Metro 3rd
Cong. Kiko recently visited the demo farm developed by TUPV in Talisay City where Director Eric Malooy showcased a single mini farm-set-up using aquaponics technology with lettuce, pepper, tomatoes and tilapia ready for harvesting
Food security is among the priority development thrusts of Cong. Kiko Benitez for the Third District and the proposal of the Technological University of the Philippines-Visayas (TUPV) focusing on micro-farming through aquaponics offers positive potential for both urban and rural communities.
Cong. Kiko recently visited the demo farm developed by TUPV in Talisay City where Director Eric Malooy showcased a single mini farm-set-up using aquaponics technology with lettuce, pepper, tomatoes and tilapia ready for harvesting.
The project that will pool the efforts and resources of TUPV, the Congressional District Office, Negros Women for Tomorrow Foundation and IF Green Technologies targets the development of a sustainable business model for food security, increased production of healthy food choices, training of beneficiary communities on aquaponics technology assisted farming and financial literacy. Micro-financing for expansion plans and marketing support through an e-commerce platform for the produce is also a vital component of the project.
In the meeting with Cong. Kiko, Director Malooy and key TUPV representatives also introduced the solar powered water supply technology and disaster preparedness technologies – flood prediction, detection and monitoring through analytics, air quality monitoring, and data-driven disaster monitoring and response.*
Introducing Vertical Farming To Mexico And Beyond
Above all else, Karma Verde Fresh is a social enterprise whose purpose, according to Tagino, “is to transform the lives of individuals and communities through the creation of accessible food options, that have positive economic and sustainable impacts on the environment.”
Karma Verde Fresh (KVF) is a vertical farm based in Monterrey, Nuevo León (northeastern Mexico), producing a variety of seedlings, leafy greens, strawberries, and beans, and manufacturing its own cultivation systems which can be installed in any urban environment to promote local agriculture.
First established in 2016 by Leo Lobato and Rafael Cuellar, Karma Verde Fresh sought to master vertical agriculture before developing its own system and initially purchased four vertical racks systems from a Dutch company. The company quickly realized that for vertical farming to be successful in Mexico and other developing countries, the technology needs to be both efficient and financially accessible so that any sized growers can participate in the development of their own urban, peri-urban or rural farms.
(F.l.t.r.) Leo Lobato and Rafael Cuellar, co-founders of KVF
According to Tagino, the company’s communications and social media manager, high capital and operating costs are the main barriers to vertical farming.
Technique available to anyone
This has led the company to develop its own technology within Mexico and make it as accessible as possible, all with the goal of providing as many communities with nutritious produce. Today, KVF has increased its cultivation grow racks by more than 89% in the same footprint and their solar LED lights use 21% less energy.
“We know that there are super sophisticated farms across the world, with high automation. That is one way, but in order to impact communities that are left behind, are looking for job opportunities, vertical farming needs to be affordable,” says Tagino.
Once Karma Verde Fresh successfully developed its own cultivation system, the company developed a digital strategy to reach its potential and future customers through various social media platforms which include Facebook, Instagram, and Twitter.
Pushing R&D
Aside from its strong social media presence to attract young customers and entrepreneurs, Karma Verde Fresh also strongly emphasizes the importance for scientific research in the vertical farming industry, publishing their first scientific research report in Cyprus at an international sustainable agriculture conference in March in conjunction with Dr. Gilda Carrasco of the University of Talca.
KVF's salad mix
“Back in 2018, we learned that vertical agriculture really needs the scientific research community to be on board because they can give us the best science for improving growing conditions. In 2019, we started our first laboratories at two UANL campuses (Universidad Autónoma de Nuevo León) and the UAAAN in Coahuila, and in 2021-2023, we’ll be installing cultivation systems at different universities across Mexico, Central America, and as far away as Chile,” says Leo.
By installing cultivation systems at numerous universities, Karma Verde Fresh hopes to attract youth to vertical farming and to develop businesses in the regions where the systems are being established. The company is also immersing itself in the academic world by collaborating on research projects and participating with NCERA-101, a research committee focused on exchanging information about technologies in controlled environment agriculture (CEA).
Expansion plans
Through these research collaborations, the company is creating models that it can replicate across Mexico. Thanks to the American Chamber Mexico, the company met Ken Moskal, now an angel investor and a new corporate structure will allow Karma Verde Fresh to transition out of its start-up phase. While the company hopes to attract investment fund managers, Leo also explained that Karma Verde Fresh is taking its time to grow organically, invest its own money and only bring in outside investments if needed.
Karma Verde Fresh plans to fund its growth mostly through sales of seedlings, produce to restaurants and selling the KVF systems through the national distribution network developed through Mexico’s Industrial Chamber CANACINTRA’s Ag Sector.
Above all else, Karma Verde Fresh is a social enterprise whose purpose, according to Tagino, “is to transform the lives of individuals and communities through the creation of accessible food options, that have positive economic and sustainable impacts on the environment.”
Their purpose garnered the attention of the Inter-American Institute for Cooperation in Agriculture (IICA). The organization asked Karma Verde Fresh to join an alliance, which was signed in 2020 and will work to build cultivation systems in food banks in the country’s most food-insecure regions, as well as the first Vertical Agriculture Tech and Trainer Certification Program in Mexico City.
Sustainable systems
Another interesting initiative of Karma Verde Fresh is its solution called the Rolling Thunder Service. By developing 40-day forecasts over Mexico, the company will be able to better forecast severe meteorological events and begin producing seedlings in its racking systems ahead of such events. When severe storms damage agricultural crops, the company will be able to provide to healthy seedlings to help farmers recover quickly.
The company is guided by three core values: consciousness, innovation and collaboration. With respect to innovation, Tagino explained that it isn’t simply about buying innovation but about actually innovating in the countries seeking to build sustainable agricultural systems. That is ultimately why the company decided to develop its own vertical racks and LEDs. The company’s commitment to collaboration is evidenced by its numerous university partners and research projects.
“Not only are our processes enriched by the different perspectives and knowledge, but it generates a bigger impact among the communities and ecosystems where the collaborations occur,” says Tagino.
For more information:
Karma Verde Fresh
Blvd. Díaz Ordaz #130,
Col. Santa María, Piso 10, Torre 3,
64650, Monterrey, Nuevo León, México
+52 (81) 8851-8261
Leo Lobato, Co-Founder
leo@karmaverdefresh.com
Tagino Lobato, Communication Manager
tagino@karmaverdefresh.com
www.karmaverdefresh.com
Publication date: Thu 25 Feb 2021
Author: Rebekka Boekhout
© VerticalFarmDaily.com
AppHarvest, Inc. Announces Full-Year 2020 Financial Results
AppHarvest was in a pre-revenue state in 2020 as the company scaled to prepare to become a publicly-traded company and as it ramped up to plant its first crop at its flagship facility, which began harvesting in January of 2021. In 2020
Company Introduces First Quarter 2021 Outlook and Updates Full-Year 2021 Forecast
MOREHEAD, Ky. — AppHarvest, Inc. (NASDAQ: APPH, APPHW) (“AppHarvest” or “the Company”), a leading AgTech company and Certified B Corp building and operating some of the country’s largest high-tech indoor farms to sustainably grow affordable, nutritious, chemical pesticide-free non-GMO fruits and vegetables at scale using up to 90 percent less water than traditional open-field agriculture and 100 percent recycled rainwater, announced today its financial results for the full year ended December 31, 2020.
Fiscal Year 2020 Highlights
Net loss of $17.4 million, compared to $2.7 million in the prior year period in 2019
Adjusted EBITDA loss of $15.7 million, compared to $2.6 million in the prior year period in 2019
AppHarvest was in a pre-revenue state in 2020 as the company scaled to prepare to become a publicly-traded company and as it ramped up to plant its first crop at its flagship facility, which began harvesting in January of 2021. In 2020, AppHarvest implemented its pioneering AgTech platform, which the company developed through international and advanced technology partnerships with the Dutch government, GE, Signify, Priva, Moleaer, Ecoation and others. Powered by these technologies, AppHarvest is able to drive higher crop yields. The Dutch government is a proven partner with the Netherlands being the No. 2 food exporter in the world because of its controlled environment farming expertise. AppHarvest is leveraging this model at a scale to effectively serve the U.S. market and introduce innovations such as a hybrid lighting array with traditional high-pressure sodium grow lights with LEDs that result in 40 percent reduced energy use. AppHarvest utilizes technology that continuously analyzes data from sophisticated digital monitoring systems composed of more than 300 sensors to analyze micro-climates to optimize growth with tomato plants reaching upwards of 40-feet tall and the first farm alone is expected to produce over 40 million pounds of tomatoes annually.
Business Combination
On January 29, 2021, AppHarvest and Novus Capital Corp., a special purpose acquisition company, completed their business combination to form AppHarvest, Inc. The common stock and warrants of AppHarvest, Inc. began trading on Nasdaq under the new ticker symbols “APPH” and “APPHW,” respectively, on Monday, February 1, 2021. Please see the press release dated February 1, 2021, on AppHarvest’s Investor Relations website for more details related to the business combination at https://investors.appharvest.com/news-and-events/news-releases.
Subsequent to the business combination, AppHarvest had 97,925,153 shares of common stock outstanding. The business combination provided the Company approximately $475.0 million of unrestricted cash, including $375.0 million in gross proceeds from the fully committed common stock PIPE. The transaction proceeds will be used to fund operations, including building additional high-tech controlled environment indoor farms, support growth and for other general corporate purposes, including to fund potential future investments and acquisitions.
First Quarter 2021 Outlook and Fiscal Year 2021 Forecast
The Company currently expects the following results for its first quarter ended March 31, 2021:
Net revenue to be in the range of $2.1 million to $2.6 million
Adjusted EBITDA loss to be in the range of $14 million to $16 million
The Company currently expects the following results for its fiscal year ending December 31, 2021:
Net revenue to be in the range of $20 million to $25 million
Adjusted EBITDA loss to be in the range of $43 million to $45 million
The Company noted that its expectations are based on information available at the time of this release, and are subject to changing conditions, many of which are outside the Company’s control.
“Our favorable crop yields and market pricing currently support a 2021 sales outlook that is better than we expected in December 2020,” said AppHarvest Founder & Chief Executive Officer Jonathan Webb. “In January 2021, we delivered our first harvest of tomatoes from our flagship 63-acre indoor farm and began shipping to select national grocery retailers. We remain focused on our mission to build a resilient domestic food system for the U.S. to support this outlook in our first year as a public company.”
In addition to better than anticipated crop yields and pricing, the Company has benefited from a temporary decline in market supply related to recent extreme winter weather conditions that prevented transport of produce through Texas from Mexico and that resulted in significant amounts of food waste. Part of AppHarvest’s mission is to create a climate-resilient domestic food system for the U.S. to prevent such supply chain disruptions.
About AppHarvest
AppHarvest, a public benefit corporation, and Certified B Corp, is an applied technology company building some of the world’s largest indoor farms in Appalachia. The Company combines conventional agricultural techniques with cutting-edge technology and is addressing key issues including improving access for all to nutritious food, farming more sustainably, building a home-grown food supply, and increasing investment in Appalachia. The Company’s 63-acre Morehead, Kentucky facility is among the largest indoor farms in the U.S. For more information, visit https://www.appharvest.com/.
This Week On Green Sense Radio Show: FEEDING A RAPIDLY GROWING Global POPULATION!
The world’s population is predicted to reach 10 billion people in the next 30 years. How we feed them using less land and water has led to a lot of exciting developments in high-tech, indoor agriculture
To listen to the entire interview, visit https://www.greensensefarms.com/radio-show
The world’s population is predicted to reach 10 billion people in the next 30 years. How we feed them using less land and water has led to a lot of exciting developments in high-tech, indoor agriculture. Chris Higgins is co-owner of Hort Americas and founder of Urban Ag News. He shares his insight about controlled environment agriculture (CEA) and talks about the challenges and opportunities facing greenhouse and vertical farms during these uncertain times.
This week on Green Sense Radio Show:
FEEDING A RAPIDLY GROWING Global POPULATION!
Vertical Farming Brings Tremendous Efficiency
The company started five years ago and has made considerable strides in growing vegetables in an eco-friendly and automated indoor environment
20 February 2021
Mike Zelkind is CEO and co-founder of a vertical farming company, 80 Acres Farms, based in the United States. The company started five years ago and has made considerable strides in growing vegetables in an eco-friendly and automated indoor environment. Today 80 Acres Farms, along with technical sister company Infinite Acres, proves vertical farming is more than just a vision of the future. "It's all about controlling the micro-climate, and we can do that better than anyone else because of the patented climate technology developed by Infinite Acres."
Mike Zelkind had been active in the food industry for decades with deep experience working with traditional farms and supply chains before founding 80 Acres Farms with Tisha Livingston. "The current food supply chains are very good, food is available everywhere, but the quality is not always as it should be. Food travels way too many miles, and it's not always sustainably grown." When Zelkind and Livingston sought to change how people eat, they wanted to bring high-tech greenhouses to North America. They went on a quest around the world, starting with the Netherlands, studying greenhouses.
The "lightbulb" went on while visiting a greenhouse on the sunniest day in the middle of June. The white-washed greenhouse, blocking out the heat of the sunlight but still supplementing sunlight with artificial lights. "That's when we realized; greenhouses still have to add supplemental lighting, which requires capital and energy to run them, but heating and cooling those greenhouses isn't free, and you don't control the environment that well. You have no control over the microclimate, which means you can't control the plants' stress response and drive nutrition. We thought there has to be a better way."
In 2016, the vertical farming industry was starting to develop. 80 Acres built their first commercial farm and quickly realized that to scale the business into something meaningful, egoless collaboration was essential. They collaborated with companies such as Priva. "This resulted in an excellent relationship, which eventually led to the creation of Infinite Acres," says Zelkind. Priva, 80 Acres, and Ocado formed Infinite Acres in 2019 to scale vertical farming globally."
Next level of controlled environment
Zelkind would like to emphasize that he values all forms of agriculture and horticulture. "Let's be clear: I am very pro-farmer, in every way- the demand for fresh food for a rising population is crucial. Vertical Farms are expensive to build, but with much higher yields and drastically improved control to maximize nutrition, we can take farming to a whole new level. Farming is a tough job, and there are not that many top growers available worldwide. We thought we could do it differently and find a way to make it easier to get those good results consistently."
Six years ago, Zelkind knew the technology did not exist to scale vertical farming. "But the trends were moving in the right direction. Data science has become more prevalent and LED lights cheaper, automation was improving, sensors were improving, and crop science was advancing rapidly. With the right collaborative partners, 80 Acres Farms has built eight vertical farms since 2016. Their latest fully-automated farm is a culmination of their years of learning. "We wanted to grow significant commercial volumes with a broad range of produce– not just lettuce, but also tomatoes, cucumbers, strawberries, etc. We knew that once we could start growing these products in commercial volumes, it would become interesting for retailers. We want to offer a high-quality product at a reasonable price, not cheap, but at the right price. It is all about value." Zelkind concluded, "Serving the consumer is the core of 80 Acres Farms. Customers have spoken! They want; flavorful, clean, fresh, sustainably grown produce, with transparency– at a fair price."
Failure turned into success
It all sounds straightforward, but it isn't, says Zelkind. "To get where we are today, we had to keep going forward. At first, we designed and built all the technical installations, and we failed– but we kept testing and sharing knowledge with our partners. We were fortunate to have started with relatively small farms, making it possible to learn quickly. And over the years, failure turned into success." Zelkind continued, "We still have a long road ahead of us. If you compare this to a soccer match, we have only passed 15 minutes in the first half. On the other hand, two years ago, we weren't even on the field."
The food-growing process that takes place at 80 Acres Farms is not that different from traditional greenhouses, Zelkind says. "With vertical farming, it's all about controlling the micro-climate, and we can do that better than anyone else because of the patented climate technology developed by Infinite Acres." The consistent temperature, humidity, and airspeed customized for each crop. Advanced lighting controls allow 80 Acres Farms to deliver the exact spectrum and intensity of light for each crop and growing phase. 80 Acres Farms uses a proprietary interlaced network of vision and sensor technology to monitor all aspects of the growing environment to assure high quality and high yield growth. Intelligent fertigation systems infuse the right amount and type of nutrients at precisely the right time and free of harmful contaminants. "Through our Infinite Acres Collaboration, we are willing to sell those technologies and license those techniques because we want to bring that to the world. We can't scale up fast enough ourselves, so there is no reason to keep this knowledge from others."
Push the crops on command
After all, it's still crop science, Zelkind continues. "It's not just pure technology, but also about knowing how a plant grows, breathes, trans-evaporates, and uptakes nutrients. We believe that's where machine learning and data science come into play. With good technology, we can optimize CO2, root zone temperature, airflow, and all of these things to come up with the right recipe for every crop and grow at a very high level of efficiency. We can push those crops and stress those crops on command instead of randomly because of weather influences. We control the crops¬– so our plants grow differently. We can gain tremendous efficiency in our cultivation. We can use different techniques and recipes to make lettuce redder or to get more tomatoes on a tranche."
In a certain way, you could say 80 Acres Farms is reinventing horticulture. "We are getting the most out of the original genetics of the crops. Dutch greenhouses are the most efficient because the Netherlands has the right climate, and the temperature drops naturally. Dutch growers have learned how to grow the best crops possible within those natural environmental conditions. But the recipes are not necessarily the best for the plant's genetics; they are the best for optimizing those crops for those conditions.
80 Acres Farms doesn't have variable conditions. We can control how much the temperature has to drop. It's all about giving the crop what it needs. Can 80 Acres Farms' tomato taste completely different and sweeter? Absolutely! We can achieve that more easily and in a cheaper way. Once you have built the infrastructure, it doesn't cost anything to control that. Zelkind continues, "If you keep doing things the same way as you are doing today, vertical farming is way too expensive, but who says you have to do everything in the same way? We are doing it differently, and we are successful with that. For us, this is the future of horticulture."
Cambridge Engineers Unveil Digital Twin To Support The ‘Future of Farming’
Hydroponic farming challenges traditional methods in favour of soil-less, water-based farming processes. To ensure the ongoing operational success of farms such as these, Cambridge engineers have developed a virtual forecasting model to provide bespoke feedback to farmers
Hydroponic farming challenges traditional methods in favour of soil-less, water-based farming processes. To ensure the ongoing operational success of farms such as these, Cambridge engineers have developed a virtual forecasting model to provide bespoke feedback to farmers.
The researchers show how a Digital Twin can faithfully represent the reality of an environment – in this case a unique hydroponic farm in London (Growing Underground) – through real-time data analytics and modelling, including the integration of a tailored temperature forecasting model to assist farmers’ decision-making. Their findings are published in the Cambridge University Press journal Data-Centric Engineering.
With hydroponic farming – often termed the ‘future of farming’ – on the rise across the UK and globally, the researchers believe that Digital Twins are particularly suited to bespoke environments such as these, providing an opportunity to move away from a ‘one size fits all’ approach, in favour of a virtual representation that can cater to a farm’s changing operational conditions.
Growing Underground is situated in repurposed WW2 air raid shelters that are 33 metres below the streets in Clapham, London. Crops are grown year-round in a pesticide-free environment controlled by LED lights, ventilation, dehumidifiers, and irrigation tanks. The farm grows 12 times more per unit area than traditional greenhouse farming in the UK but also consumes four times more energy per unit area. Therefore, finding ways to minimise the energy use while maximising crop growth and maintaining optimal growing conditions is key to the ongoing operational success of this farm and others like it.
The researchers show how the development of a Digital Twin can be useful not only for informing farm operators in real time, but it can also help them to prepare for the future. Data creation, data analysis and data-centric modelling were all required to create the Digital Twin for Growing Underground. This involved an extensive monitoring system that combined wireless sensors with manual data records to track the observable environmental conditions in the underground farm; identifying the influencing variables on energy use and crop yield; and helping to forecast potential future operational scenarios, as well as providing feedback on the influence of recent events on the farm environment.
The Digital Twin can also provide enhanced data to help assist farmers in the decision-making process, offering advice specific to the needs of the farm. For example, the researchers identified that the LED lights have the greatest influence on daily temperature fluctuations in the farm and so they created a bespoke temperature forecasting model that predicts extreme temperatures. This model can be integrated into the Digital Twin and it is easy to implement, making use of temperature and energy meter readings. It is also flexible to the addition of more data as it becomes available and provides feedback on operational changes that can reduce energy use and control the farm environment more effectively.
Location of sensors in Growing Underground. A side view of a typical bench is indicated at the centre of the farm, showing how four LED lights span the length of each bench. The blue arrows indicate the air circulation throughout the farm. Credit: Melanie Jans-Singh
Dr Ruchi Choudhary, Reader in Architectural Engineering, said: “As we move towards more innovative agricultural practices, such as hydroponic farming, there is a greater need for an intelligent Digital Twin over a simple monitoring system. The Digital Twin we have developed for the unique hydroponic farm, Growing Underground, can observe, process, and interpret farm data (i.e. energy, weather, live sensor data and manual records) that leads to tangible outcomes. This can include warnings (i.e. concerning temperature fluctuations that require changes to ventilation, heat, light); causal relationships (resource use efficiency, crop health); operational suggestions (using a forecasting model); and a prediction of future conditions."
Melanie Jans-Singh, lead author and Ph.D. student, added: “In essence, our Digital Twin becomes the urban-integrated farm operator’s 24/7 smart ‘companion’, a living digital reference, providing bespoke feedback on the effectiveness of the measures taken in real-time. This is in addition to longer-term forecasting and informed decision-making, with control processes that are robust to human error. It is suited to mid to large scale processes, often seen in civil engineering, where sensor maintenance will also be an issue.”
Melanie Jans-Singh, Kathryn Leeming, Ruchi Choudhary, Mark Girolami. ‘Digital twin of an urban-integrated hydroponic farm.’ Data-Centric Engineering (2020). DOI: 10.1017/dce.2020.21
For more information:
University of Cambridge
Infarm Heralds The Next Generation of Cloud-Enabled Farming
Infarm Heralds The Next Generation of Cloud-Enabled Farming
Infarm introduces its new high-capacity, cloud-connected Growing Centers - a major step in the company's efforts to accelerate the benefits to people and planet by building a scalable, sustainable and resilient global farming network
NEWS PROVIDED BY Infarm
Feb 23, 2021
Berlin, Germany -- February 23, 2021, Infarm, the world's fastest-growing urban farming company already available in 10 countries and 30 cities in thousands of stores, continued the rollout of its vision for a global interconnected, sustainable, and highly efficient farming ecosystem.
©Infarm
Infarm, the world’s fastest-growing urban farming company, has introduced its new high-capacity, automated, modular Growing Center - a local farm and distribution center in one, that can generate the crop-equivalent of up to 10,000 m2 of farmland, with up to 400 times higher efficient food production than soil-based agriculture. The cloud-connected, high-yield centers join Infarm’s expanding global network of self-learning farms that improve plant yield, taste, and nutritional value while reducing the use of natural resources. Credit: Infarm/diephotodesigner.de (PRNewsfoto/Infarm)
As part of its goal to drive innovation within the USD 3 trillion global fruit and vegetable market[1], Infarm today introduced its new high-capacity, automated, modular Growing Center - a local farm and distribution center in one, that can generate the crop-equivalent of up to 10,000 m2 of farmland, with up to 400 times higher efficient food production than soil-based agriculture.
The cloud-connected, high-yield growing centers join Infarm's expanding global network of self-learning farms that improve plant yield, taste, and nutritional value constantly, while further reducing the use of natural resources. With 50,000 m2 of farming facilities and hundreds of farms in store locations, Infarm is already providing fresh produce to 50% of the world's largest food retailers. The rapid deployment capability of the new high-yield Growing Centers will drive additional global growth and scalability to match the needs of retailers of any size in any location, with the goal of growing the network to 500,000 m2 by 2025.
A Growing Center is comprised of dozens of modular farming units, each standing between 10 and 18 meters high, occupying a 25 m2 ground footprint and requiring just six weeks to build, yielding the crop-equivalent of 10,000 m2 of farmland. This modular, data-driven, and distributed approach -- a combination of big data, IoT, and cloud analytics, in addition to rapid growth at a global scale -- sets Infarm apart from any other farming solution.
"Access to fresh, local, and sustainable food is a growing challenge, as people shift towards cities and climate change accelerates," explains Erez Galonska, co-founder and CEO of Infarm. "Today we're adding speed to scale with new technology that allows us to deploy a Growing Center to any city in the world in a fraction of the time, space and capital investment of most large-scale farming solutions today. Both the farms and the software that powers them were designed to make fresh food more accessible for everyone, everywhere."
Many of the world's leading food retailers are already taking part in Infarm's farming network, including Empire Company Ltd (Safeway, Sobeys, ThriftyFoods), Whole Foods Markets, Marks & Spencer, Kroger, Kinokuniya, Aldi, Amazon, Auchan, Casino, E.Leclerc, Edeka, Intermarché, Irma, Kaufland, Metro, Migros, Selgros, Summit and in Germany, Canada, Denmark, France, Japan, Luxembourg, the Netherlands, the United Kingdom, the United States and Switzerland.
Growing a new food system for people and the planet
"The entire Infarm network is connected to a central farming brain that gathers more than 50,000 growth, color, and spectral data points through a plant's lifetime," explains Guy Galonska, co-founder and Chief Technology Officer at Infarm. "We've collected more than 300 billion data points throughout our farming network to date. These data enable us to perfect our growing recipes and improve yield, quality, and nutritional value while reducing the production price constantly."
The large-scale Infarm Growing Centers integrate farming units that can each save up to 10,000,000 liters of water per year, compared to soil-based agriculture for similar crops, while contributing up to 40% energy savings over previous Infarm technologies.
By 2025 Infarm plans to establish 100 Growing Centers - equivalent to 1.5 million m2 of farmland and producing 450,000,000 plants across its network, including expanding to new markets. This year, 15 Infarm Growing Centers are already planned/or under construction in major urban centers, including London, Paris, Copenhagen, Toronto, Vancouver, Seattle and Tokyo.
Additional features of the new Infarm technology:
An automated mechanical farming system that is cloud controlled;
Environmental settings like CO2, temperature, light, pH and growth cycles can be set, monitored, analyzed online across all farms;
Recirculates 20 liters of water condensation per hour and, saving more than up to 10,000,000 liters of water per year compared to soil-based agriculture for similar crops;
Smart LED management supports energy efficiency offering contributes up to 40% energy savings & up to 25% savings on initial investment.
Infarm uses 95% less water, 90% less transport and zero chemical pesticide than soil-based agriculture with the majority of electricity use throughout the Infarm network coming from renewable energy. To date, the Infarm network has saved more than 40,000,000 liters of water and 50,000 square meters of land.
[1] Wyman, O. (2021). Disruption in fruit and vegetable distribution - Fruit Logistica Trend Report 2018 [Ebook] (p. 12). Berlin, Germany: Fruit Logistica, Messe Berlin GmbH. Retrieved from https://www.oliverwyman.com/content/dam/oliver-wyman/v2-de/publications/2018/Feb/Fruit_Logistica_Trend_Report_2018.pdf
About Infarm
Infarm was founded in Berlin in 2013 by Osnat Michaeli and the brothers Erez and Guy Galonska. Passionate to become self-sufficient and eat better, they were growing their own food, enjoying all the flavor and nutrients, without the chemical pesticides and transport kilometers. With the aim to share the goodness of own-grown produce with everyone, they developed a smart modular farming system, that allows distribution of farms throughout the urban environment, growing fresh produce in any available space and fulfilling any market demand. Today, with cutting edge R&D, patented technologies, and a leading multi-disciplinary team, Infarm is growing a worldwide farming network helping cities become self-sufficient in their food production, while significantly improving the safety, quality, and environmental footprint of our food.
With a multinational team of more than 800 people globally, Infarm has partnered with more than 30 major food retailers including Aldi Süd, Amazon Fresh, Auchan, Casino, E.Leclerc, Edeka, Empire Company Ltd (Safeway, Sobeys, ThriftyFoods), Farmdrop, Intermarché, Irma, Kaufland, Kinokuniya, Kroger, Marks & Spencer, Metro, Migros, Selfridges, Selgros, Summit and Whole Foods Market in Canada, Denmark, France, Germany, Japan, Luxembourg, the Netherlands, the United Kingdom, the United States and Switzerland, deployed more than 1200 farms in stores and distribution centres, saved more than 40,000,000 liters of water and 50,000 square meters of land.
Photo - https://mma.prnewswire.com/media/1442283/Infarm.jpg
SOURCE Infarm
Also from this source
Whole Foods Market partners with Infarm to offer a more...
SCOTLAND: Elevate Your Meals With Microgreens Produced by Aberdeenshire’s Vertical Shoots Urban Farms
Turning your hobby into a business is not always the goal. But when Brindha Shayana and Sathya Vasudevan discovered their passions for vertical farming, they knew it was the only way forward
18/02/2021
Vertical Shoots Urban Farms produces an array of microgreens in Westhill, Aberdeenshire. © Supplied by Brindha Shayana
Turning your hobby into a business is not always the goal. But when Brindha Shayana and Sathya Vasudevan discovered their passions for vertical farming, they knew it was the only way forward.
Both qualified engineers working in the oil, gas, and service sector, Brindha and Sathya were eager to switch things up and start with a clean slate. This was to involve growing microgreens in their Westhill-based home.
And now, two years on, their produce can be seen in a line-up of local stores and is featured as part of dishes created by north-east restaurants, cafes, and bistros.
With that said, there’s no doubt that their business, Vertical Shoots Urban Farms, will continue to grow.
But what’s the process in growing microgreens, you may ask? Well, we caught up with the partners to find out all about the process, as well as what encouraged them to start their own business.
So, Sathya and Brindha, have you always wanted to start your own business?
Sathya: We were always keen to do something different but never had the idea of starting a business.
A few years ago while we were shopping in a supermarket, a question sprung into our mind asking, where does the food we eat come from? Since then, we started to look into the origin of every product we purchased and it amazed us how foods were produced in different countries and distributed around the world in such a massive scale.
Brindha: At the same time, we also felt how important it is to grow the essential food we eat closer to the end consumer. This triggered an interest to take up a hobby growing herbs.
The pair of us started to do loads of experiments and trials day in and day out. At one point, we started to share our produce with family and friends.
The more we thought about getting local produce out to people, we realised how challenging it is to produce any kind of food and distribute it to the community. This gave us the push to think ‘why not start a business and face these challenges to do our part in solving a global issue and contribute towards a sustainable future’. This sounded exciting and we kick-started our journey.
For those that don’t know, what do you offer?
S: Vertical Shoots are currently offering a wide range of micro salads. They come in different shapes, colour, and flavours. We supply them to restaurants, cafes, bistros, and stock micro salad boxes in shops for home consumers to use in salads, smoothies or alongside any dish.
B: For restaurants, cafes and bistros, we grow the varieties they request based on their need. Our lovely customers include Buchanan Bistro in Banchory, Inverurie’s Fennel Restaurant, Rothesay Rooms in Ballater, JK Fine Foods, Replenish in Stonehaven, and much more.
For home consumers, we offer variety boxes – spicy mix, rainbow mix and flavour punch – which will include a variety of greens with different flavour tones. These are available for direct home delivery.
That’s very interesting. Why did you choose microgreens?
S: Two years ago, we started to think of doing something related to farming and had to start with a clean slate (with no previous experience).
So, we started growing leafy greens as a hobby, gradually learning and experimenting each day. And after some research, we came across hydroponics – soilless farming with plant roots suspended in water filled with nutrients – and vertical farming, which enables the use of any urban space to grow a substantial amount of greens.
B: This sounded fantastic and we converted a small shed in our back garden into an indoor farm. Both of us were experimenting in this setup for a year.
With every seed germinating and shoots cropping up, this became a serious hobby with great interest and it kept progressing. Then we kick-started our journey with Vertical Shoots in March last year with our aim to utilize underused urban spaces in an effective way.
Am I right in saying that the pair of you wanted to offer products that redefined the way we eat salads?
S: Yes, exactly that. When we tried microgreens ourselves for the first time, we felt it was so different from the usual salad greens we eat. Microgreens bring in a nice flavour and their colour and texture just brighten up the plate. I am sure people who have tried microgreens would agree with what we think.
B: When we looked around in the supermarkets, we could not find any such product apart from micro salad cress in very few shops. So, this triggered an idea to start growing a range of micro salads and make it more available for the local community to try and experience the goodness of micro salads or microgreens.
What encouraged you guys to launch Vertical Shoots Urban Farms? Were there any obstacles?
S: There is so much going on in this world trying to move towards a sustainable future. Innovative ideas are being implemented to revolutionize every sector. Just looking around getting to know about the new happenings encouraged us to take a step trying to do something different and be a part of this change. This thought lead to the start of our journey with Vertical Shoots Urban Farms.
B: It was the beginning of the first lockdown when we started our journey. With the restrictions in place, it was difficult to approach other businesses and customers. Slowly we started to take baby steps which got us going.
We still have a long way to go, but we have started marching towards our vision.
You mentioned that it was difficult to approach other businesses and customers, understandably. So how have you gone about promoting the business?
S: This is a work in progress as we are fairly new. To get our name out, we are active on social media, like Instagram, sharing what we do. Also, we have visited many restaurants, cafes and bistros to spread our name. Some of the people we met were amazing and kind enough to spread a word about us.
Vertical Shoots also has a regular stall at the Westhill Farmer’s Market. With the Covid-19 restrictions, it is not easy to get a space in all the farmer’s market. Hopefully, things will change and we can attend many more.
B: We also stock our greens in local shops to make our products accessible to the people of Aberdeen and Aberdeenshire. This will help us to spread our name within the local community even more.
What’s the process involved in producing them? And how are they distributed?
S: All our greens are grown hydroponically. The pair of us sow the seeds to start with and germinate them in a dark room for the first few days. Then, we transfer them under lights for a number of days and continuously monitored.
Each variety prefers a certain growing condition. During the growing process, we maintain the ideal temperature, humidity, sufficient air circulation and nutrition to get the optimum growth. At the end of the growing stage, we harvest on the day of the delivery, box and deliver to our customers.
By growing the greens closer to the end consumer, the customers can take advantage of a longer shelf life and freshest greens on their plate.
Can you explain a bit more for our readers about vertical farming?
S: Vertical farming is a method of farming where the greens are produced vertically in racks in a controlled environment. By this approach, larger quantities of produce can be grown in a small space.
The produce is grown hydroponically (roots suspended in water) or by aeroponics (roots suspended in a mist). We use hydroponics to grow our greens. Since the greens are grown indoors, light is provided to the plants through LED with a certain spectrum of light mostly containing blue and red. Nutrients for the growth of plants are supplied through the water.
B: By this method of farming, there can be a great saving in water consumption compared to traditional methods. With the controlled environment in place, crops which are not possible to be grown locally can be grown; for example, basil which requires warmer temperature. Vertical farming methods can be used to grow leafy greens, few types of fruits and flowers.
Vertical Shoots Urban Farms’ new indoor farm, where they grow their fresh produce.
© Supplied by Brindha Shayana
Why do you think the demand for microgreens is constantly on the rise?
S: The need for healthy nutritious food is increasing day by day. A lot of people are also looking towards a vegan diet. Microgreens tick all the boxes required for a healthy living.
Greens harvested in its early stages of growth are nutrient-dense compared to a mature green – they also taste and look great. We could also consume leaves of some of the vegetable crops such as cabbage, broccoli, radish etc. so there are so many varieties of microgreens, which can be consumed as a salad. This makes eating salads more interesting.
B: Additionally, microgreens can be grown indoors all-year-round and are not season dependent. So, it can be grown closer to the end consumer reducing food miles which ticks the box on sustainability.
Growing microgreens can also be a hobby which would interest many. This way people can get their hands on growing and enjoy the greens grown by themselves in their own space which could be exciting and satisfying.
Other than microgreens, do you grow anything else?
B: Offering microgreens is just a start at Vertical Shoots Urban Farms. We are working our way towards offering baby greens, mature greens and edible flowers. Hopefully, we will increase our range of products in the near future.
Over the past two years, what have been the main highlights of running Vertical Shoots?
S: You learn something new each day and it is always a treat to see these beautiful greens grow up. New ideas, experiments and DIYs on the farm keeps us thinking all the time. It gives a sense of satisfaction that we are working on something which is essential for our day-to-day living and trying to find innovative ways to grow crops closer to the end consumer for a sustainable future. This keeps us motivated to do more each day.
B: Two years ago, our experiments just started on our study table. Slowly the experiments got bigger and encroached into our living space and now we have built our own fully functional indoor vertical farm. Starting from scratch, we now grow about 15 varieties of micro salads and there are many more to be added on to the list.
You’re both clearly very passionate about the business, which is amazing to see. What are your upcoming plans?
S: Microgreens are something new for many in the local community as we rarely see these in the supermarkets. We have noticed many customers who come over to our stall at the farmer’s market really chuffed to see these micro salads as they couldn’t find them locally. On the flip side, we do come across people who don’t have any idea on microgreens but are really excited to try them out!
B: As a local urban farmer, we would like to get these healthy greens into as many homes as possible and see people consuming them in their daily food.
In addition to serving cafes, restaurants and bistros, we aim to have our produce in many more outlets and do more direct home deliveries to make it accessible to the local community. As a business, we always look to keep adding more products to our offering.
Visit Vertical Shoots Urban Farms on Facebook or Instagram to find out more information.
Top Tips to Growing Your Own Microgreens
There are loads of materials available online to guide you on how to grow each variety of microgreens.
The best way to learn is to try it yourself, so below are some tips provided by Brindha Shayana and Sathya Vasudevan of Vertical Shoots Urban Farms to get you started.
Microgreens are grown in two steps: Step 1 – germinating the seeds and Step 2 – propagating the seedlings under light (sunlight or LEDs). It is as simple as that.
Start simple. Look around your kitchen cupboard to see if you have any seeds which you use for your daily cooking. Seeds like mustards, fennel, coriander, fenugreek and many others used in cooking can be used to grow as microgreens. Although bear in mind that sometimes older seeds may not germinate well. If you are buying seeds, then make sure you buy the right seeds for microgreens which are not chemically treated and are suitable for consumption.
To grow microgreens, you need a medium. You could use kitchen towels as a start. Soak about three layers of the paper towels in water and sprinkle the seeds on top. Spray some water and then cover with a lid to maintain humidity. Keep it in the dark for three-to-four days. Check once a day to keep them moist.
Once the seeds have germinated, remove the lid and place them on the window sill. In the winter time when it is dark most days you could use a study lamp with a daylight LED bulb for lighting. Water them once a day and not let the medium dry out. Keep them well ventilated and maintain a room temperature about 20C (for cool crops).
Once the microgreens are about two inches tall with the first set of leaves well developed, they are good to harvest. Cut the greens just over the medium and enjoy them in your dishes. Most of the microgreens are ready within 10-14 days.
Keep it simple when you grow microgreens for the first time. If you fail on the first trial don’t worry, it takes a few trials to get the trick of growing. Once you get to know about the basics you could start experimenting with different mediums and a variety of seeds.
Finally, if you need any help with growing your microgreens, we are happy to help. Just message us on Instagram – @verticalshoots