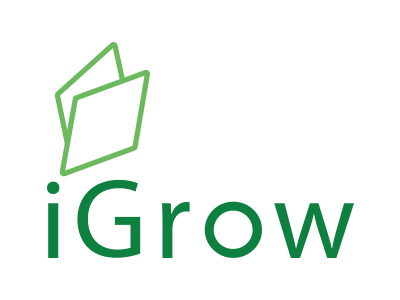
Welcome to iGrow News, Your Source for the World of Indoor Vertical Farming
A Greenhouse In A Box For Small Farmers
Hyderabad-based startup Kheyti’s focus on small farmers has attracted the interest of US-based impact investment firm Acumen
Lush growth inside a low-cost Kheyti greenhouse in Telangana.
With one-tenth of the water and pesticides required and a manifold increase in yield, greenhouses can be transformative. The catch is that their upfront investment cost puts them beyond the reach of those who need them the most—small farmers dependent on rain or borewells. But what if a minimalistic greenhouse is designed from the outset, keeping in mind the needs and limitations of small farmers?
Hyderabad-based Kheyti has partnered with manufacturing and design companies to introduce such a concept. Its modular greenhouse kit, including a drip irrigation system, occupies just a tenth of an acre and costs less than ₹1 lakh. That’s much smaller and cheaper than normal greenhouses which only large farmers can afford. Around 500 farmers in Telangana are the early adopters of this “greenhouse in a box", which comes along with inputs like the appropriate seeds and fertilizers.
It began on a 1.8-acre farm in Narayanpur village, 60km north of Hyderabad, in 2017, recalls Kaushik K., co-founder, and CEO of Kheyti. “Venkatesh and his wife Lakshmi were growing rice along with some vegetables on the side. They worked hard, but their annual income of ₹30,000 barely sufficed for a family of five. The biggest challenge for them was that they could not fully utilize even their 1.8 acres of land because their borewells would run dry in the summer months," says Kaushik.
Model farm
Kheyti had set up an R&D farm on the outskirts of Hyderabad to demonstrate its greenhouse to small farmers. Venkatesh was among the first to visit the farm. “We showed him he could grow high-quality vegetables with so much more yields. But he had only one question: How much water would it need? When we explained that for the greenhouse he would run his borewell pump for only five minutes compared to an hour’s running time for his open field, he was ready to sign up," says Kaushik.
There was a hitch. The ₹5 lakh cost of the greenhouse was relatively low but still too much to raise for the likes of Venkatesh. So, why not make it even smaller and more affordable? It’s from such interactions that Kheyti’s greenhouse designs evolved.
“Venkatesh was the first one and after getting his greenhouse, he continued to give us feedback on what we should do for the next version," recounts Kaushik.
Today, Kheyti offers a 400 sq. m greenhouse for ₹80,000, with insect netting, shade netting, and polyethylene sheets to protect crops from pests, heat and excessive rain. That compares favourably with the ₹25 lakh that a one-acre (4,047 sq. m) greenhouse of this type would cost.
How Vertical Farms Are Revolutionizing Agribusiness
What is vertical farming and why does it matter?
William Ramstein ・ 1 March 2021 ・ Vertical Farming
Urban planners are tasked with answering some pressing inquiries: how can farming be brought closer to consumers; is digital agriculture an essential ingredient for making cities smarter; and can vertical farming improve socio-economic disparities?
Key Takeaways:
Vertical farming uses LED, Robotics and AI to bring vegetables closer to city dwellers.
The total addressable market for vertical farming is estimated at around $700 billion.
Spread, a Japanese vertical farm is profitable but most firms fail.
Vertical farming is a great way to produce controlled supplies of a customized plant.
Vertical farming struggles with electricity costs despite reducing carbon emissions.
What is vertical farming and why does it matter?
The bedrock characteristic of cryptocurrency technology is called decentralization, a sovereign and flexible organizational system led by a commune, and today other industries like farming are catching the bug. Farming needs to change its practices in order to meet ecological objectives set up by governments and decentralization could open the door to increasing food access and reducing carbon emissions from food transportation. Smart decentralized vertical farming implies using technology like digital platforms, robotics and artificial intelligence to bring food closer to the growing demand seen in cities.
Despite the difficulty of competing against the cost structure of traditional farming, vertical farming offers numerous advantages. It grants more yield per square meter and reduces waste in both carbon and water usage. The production of vegetables is made in large and often times un-used warehouses close to city centers thus cutting transportation costs and middlemen expenses. The supply is more easily controlled, protected, and priced regardless of global weather and plants are customized to local consumer preferences. Consumers are already paying a premium on farmer’s market products, so why not vertical farm products too?
Cases of vertical farming: Nigeria is one of the most promising African nations because of its age pyramid. But with a large young population comes questions around food and water access and today, more than 170 million Nigerians need prolonged and sustainable access to these resources. Nigeria currently imports $3.5 billion worth of food products while exporting only 1/7 of that figure. Fresh Direct is Nigeria’s first Hydroponics Company (growing crops without standard soil) that combines vertical farming to its business model to reduce the distance between cities and rural farming regions.
The firm is able to produce seven to 10 times the yields because of its stackable shipping containers, which use technologies such as drip irrigation, and cold storage. Direct Farming operates with a community mindset, with the goal to inspire more young farmers to set up shop in urban centers and become urban farmers. The company also trains and finances low-skilled workers into urban farmers and increases economic productivity in unemployed youth groups.
In Japan, a company called Spread is one of the world’s most sophisticated examples of vertical farming. Their factory mainly produces lettuce. Large robotic arms transplant lettuce seedlings into pots where they are left to grow under LED lights. Believe it or not, but the factory can produce 30,000 lettuce heads a day. CEO Shinji Inada boasts of being the only large-scale vertical farm that is profitable and hopes that more widespread adoption continues growing.
However, companies like Spread and A-Plus (another similar farm in Fukushima) struggle to lower unit economics because of their low-scale operations, and they find it hard to penetrate the traditional downstream sellers. When producing high-priced lettuce by the tonne, trucking goods to the local wholesaler does not work partly because vertical farming offers customized products for specific local needs, not necessarily for broad demand. These players have thus geared their focus towards international buyers like UAE to export their goods.
Is vertical farming there yet?
Most vertical farms have failed because of the high initial costs and high operational expenses of running robotic equipment. While sunlight is free, the energy cost of running LEDs is not. The solution could be to install renewable energies like solar panels and wind turbines. However, the fixed cost of that installation would inevitably factor into the end-product, or at least on the balance sheet as a liability assuming they keep prices reasonable for consumers.
While Mr. Inada can rightly boast of turning profits, most firms toss lettuce at a loss. The industry should see more growth ahead, however, with research group IDTechEx forecasting that annual sales of $700 million could more than double to $1.5 billion in 2030. There remain technological challenges though. While many competitors boast of successfully leveraging AI and robotics and filtration, new entrants have seen problems with watering automation systems, mold, and infestations (most players do not use pesticides).
Some analysts suggest that while the excitement around vertical farms makes sense, the farming style might just end up becoming just another way of farming amongst greenhouse and open sky farms. More specifically, vertical farming will focus on high-margin crops rather than commodities like bulk grains.
While the challenges of vertical farming are clear, every country has different needs and constraints. There is a large interest from smaller island countries like Singapore or Iceland, rich economies, and countries that have a higher propensity to import due to less arable lands. Britain is a good example of a country that meets the criteria and in the context of Brexit, it makes all the more sense because of import costs and independence constraints. A potential labor crisis could soon loom too assuming seasonal workers are denied entry into the country. Vertical farms only require one-third of the manpower to run and could therefore alleviate the industry.
The market opportunity…According to research by Barclays Investment Bank, the market opportunity for vertical farms is large. Analysts estimate the size of the global fruit and vegetable market to be $1.2 trillion and the total addressable market for vertical farms to be $700 billion. The purchased energy use to produce 1kg of lettuce is 247-kilowatt hours far exceeding Netherland greenhouses’ 70-kilowatt hours consumption. With retailers being asked to meet more carbon-neutral objectives, some vertical farms believe they will be able to overcome their expense through increased demand and scale.
The pandemic has imposed many supply chains disruptions and labor shortages threatening food security in regions around the world relying heavily on imports. Vertical farming is recognized lately and since 2014, has seen a flow of funds equal to $1.8 billion according to data group Dealroom. SoftBank fundraised $140 million into Plenty, a start-up, and countries like Abu Dhabi want to build farms in deserts.
Some of the top players in the global farming market include Vertical Farm Systems (Australia), American Hydroponics (US), Agrilution (Germany), Green Sense Farms (US), Everlight Electronics (Taiwan), Koninklijke Philips (Netherlands), Sky Greens (Singapore), Illumitex (US), Urban Crop (Belgium), Aerofarms (US) and InFarm (Germany).
"We’re Retrofitting With The Variables We Have In Place"
Planted Detroit introduces new 20.000 sq. ft. growing facility
“The Square Room is a big block of pink lights with eight levels, where all our growing is done. Everything after germination is done in the same room, both harvesting of our baby greens and microgreens. Because we’re almost done with our PARS (Planted Automated Racking System), which is the big automation,” says Megan Burritt, Managing partner at Planted Detroit.
From a mix-fused downtown neighborhood in Detroit, daily deliveries of ready-to-eat salads and fresh greens are transported to local retailers and restaurants. Planted Detroit makes a large contribution to the city’s share of fresh produce.
New facility
Planted Detroit has been in the middle of the construction of its new 20.000 sq. ft growing facility. The growing space has been a massive update to the company compared to its previous 6-level growing facility which was between 1500-2000 sq. ft. The same room was used for processing, packaging, harvesting, and so on. “It was rather crowded, says Megan, but the main goal was to keep everything tight for the construction to continue in the near surrounding. We’re very serious about biosecurity and we have a daily procedure for everyone who sets foot in our grow room to go through. Making sure our greens don’t come into contact with pathogens is our top priority.
The new growing room
The Square Room, one of our growing rooms, is highly automated, including an automatic harvester to ensure work-efficiency. Once everything is big enough to be transplanted out of their plug trays, PARS (Planted Automated Racking System) will be transplanted with gutters and then go into harvesting. On the other side of PARS, the gutters are taken down and harvested through Planted’s new automatic harvester.
Delivering directly to consumers
The company wants to reach a higher volume of customers as it’s aiming to obtain a consumer brand status. Next to that, the company is always on the lookout for finding more customers through other venues. “We want to go directly to consumers via our web-store to shorten food miles as much as possible, delivering the freshest and most delicious greens,” Megan says. In order to do that the company needed to have a bit more scale, trying to maximize the space they already had.
She adds: “Our farm maybe isn’t the square footage which we could have built from scratch, but we’re retrofitting with the variables we have in place. That is why we have done a combination of a microgreen vertical nursery and PARS for baby greens. Our direct customers wanted meal solutions and we’ve been able to deliver them that. We’ve been doing everything from seed to plate basically.”
Megan Burritt, Managing partner
New projects coming up
On the same campus, 10 meters away, a new farm will be constructed, under the company's office space. In this farm herbs and edible flowers will be grown in response to different customers' demands. Megan says that Planted Detroit’s wholesale customers got them to this point as they were very interested in herbs and edible flowers. “However we weren’t able to perfect these as well in the systems that our baby greens were in perfectly. That’s why we’ve been leaning into R&D lately because once finishing the construction of Farm 2 it will have excellent growing conditions that are better than they have been for those crops.”
Edible flowers are an interesting thing, says Megan, but the company has gotten so much interest in it. According to Megan there aren’t many farms in the US that are growing them. “They’re high priced at this point. It sort of sticks to our original innovation, namely what exists here in the food system and what does not. Where can we fill the ‘does not exist niche’ and satisfy the needs of our customers.”
The company is rolling out a subscription program sometime this year and figuring out where it fits into the fresh food subscription system and how they can partner with other parties in order to get produce closer to society. “It’s great to have this ag job, applied science to be able to do. In all the things we’ve been doing is hiring these Detroiters and showing that we can really create a really great culture of work. It’s really great to see we’re contributing to a better Detroit and a better tomorrow,” Megan states.
Team expansion
During 2020 most of the team stayed on by moving around working hours, so the farm could come back in full force. By the time all equipment was in place, 10 to 12 people were added to the team to have them fully trained before the system would be functioning. “It has been really wonderful to expand the team to see what our capacity is,” says Megan.
“Luckily we’ve been able to develop systems that have been resilient. We’ve seen so many different patterns in consumer behavior but they seem to have fallen in our favor. People are eating more at home, shopping for groceries more, and that triggered our pivot focusing on direct consumers. But now, it’s perfectly in line with our strategy on how we go to market. As long as we can supply our customer needs we’ll be on the right path. Nothing but bright hopes for the future right now,” Megan affirms.
For more information:
Planted Detroit
Megan Burritt, Managing partner
megan@planteddetroit.com
www.planteddetroit.com
Author: Rebekka Boekhout
© VerticalFarmDaily.com
Saudi Farmer Has Built The Region’s First Vertical Farm
“My aim is to make sure we truly become self-sufficient,” he said.
The Saudi farmer Omar Al-Jundi even he is not related to farming by degree. But that is exactly where the industrial engineer found his calling, when he built the region’s first vertical farm in the heart of Dubai. Born in Egypt to Saudi parents, Al-Jundi spent his early years in Alkhobar due to his father’s engineering firm.
The family moved to Jeddah when he was 12 years old. His last two years of schooling were spent at Bahrain School in Manama. “I wanted to graduate with an American high school diploma,” Al-Jundi said. “At the time, as a Saudi, you couldn’t attend private foreign schools.” Upon graduation, he left the region to study industrial engineering, followed by an MBA at the University of Miami in Florida. Although his father is an engineer and his mother an architect, Al Jundi delved into the world of banking for two and a half years when he moved back to Jeddah upon graduating.
“I then shifted to the hospitality industry, opened the first lounge in Jeddah along with other restaurants with my friends, and ended up selling my share and joining my father’s company,” he said. “You learn that you’re better off doing something on your own than having partners because you end up changing directions.”
After 10 years of “paying his dues” in the family business, he felt compelled to change directions. “As an Arab, you’re always closely tied to the family,” he said. “We’re blessed my father started a business and there’s a place for us in that business, but luckily, my younger brother was a lot more interested in it — I always felt my calling was somewhere else.”
In search of his true passion, he started his journey as an entrepreneur. The field he specialized in had yet to be determined. “I felt that there was a meaning for something else,” Al-Jundi said. “I was free and my family was very supportive.”
Countless research and books later, he became intrigued by the tech space, admitting he believed he would start the next Amazon. “That didn’t follow through,” he said. “Then I thought it would be in mining, but I always looked for something that was away from my comfort zone such as engineering, contracting, real estate and consulting. Just something different. It was a process.”
The young Saudi had reached a point in his life where he felt the need to do something impactful, something which added true value to the region. Eventually, two of his friends introduced him to the concept of modern farming. “I visited some orange farms in Egypt and I was in exploration research mode,” he said. “I enjoyed seeing nature — you’re a lot more relaxed. Here, when you go in and see the plants growing every day, there’s definitely a connection, because you’re seeing the end product, you’re feeling it, and I connect to them.”
The more research he immersed himself in, the more driven his interest became. At the time, the Saudi Government was focused on addressing food security and self-sufficiency. “It’s always been a big topic,” he said. “When you fly out of Riyadh, you find these big circular green spots as they’re trying to green and farm the desert, which was successful, but on the other hand, it depleted our water resources.” According to the Food and Agriculture Organization, agriculture represents around 70 per cent of water consumption in most of the GCC countries. But Al-Jundi did not give up on the thought.
After moving to Dubai in 2014, he learned about King Abdullah’s Initiative for Saudi Agricultural Investment Abroad. Half the capital needed for agricultural projects was offered to Saudis who invested in a list of 31 countries abroad to purchase land, set up a project and export the food back to the Kingdom. It gave him an idea to start his own vertical farm. “I knew it was a big topic,” he said. “I’d never heard we could grow food with no soil. I thought it was intriguing and fascinating. It was enough for me to know there was something there to explore it further.”
With more than 90 per cent of the region’s land unsuitable for agriculture, Al-Jundi set out to find a solution. He spent the following 12 weeks taking courses in aquaponics, aquaculture, hydroponics and horticulture in California and the Netherlands. He even spent time working in a cucumber greenhouse at the Delphy facility in Holland, where he acquired valuable experience in the field. “It was really professional and a great learning experience,” he said. “That’s when I knew what I wanted to do. And I knew I had to completely immerse myself in it.”
The team of Badia Farms, which he founded in Al Quoz in December last year, consists of 12 people, all of whom have experience in farming. “It took 18 months to get it up and running because we didn’t work with any technical partner,” Al-Jundi said. “I knew I was in it for the long haul, so I worked with different growers and learned.”
The 850-square-meter facility includes a “fertigation” room, which fertilizes and irrigates the 18 varieties of crops he currently grows. Gourmet seeds, some of them hybrids, such as lemon basil, cinnamon kale, wasabi, green radish, mustard, micro kale, edible flowers and cinnamon basil, are flown in from the United Kingdom and the United States every three months — from 50 to 300 kilograms at a time. The farm plans on introducing as many as 26 varieties, including sunflowers.
The seeds are placed on a type of mat made of recycled carpet that is food-certified. LED lights flood the room in a pink atmosphere, with each UV light containing a certain spectrum that is beneficial for the plants.
In the tank room, feed and water is scheduled through a computer-based on the crop, with a unique nutrient recipe for each type, including potassium, calcium, magnesium, and ammonium. UV and concentrated oxygen are also able to kill any potential bacteria or pathogens in recycled water. Once the seeds sprout, they are moved to the five stacks in the vertical farm. Four dehumidifiers regulate the humidity in the air, providing each on average with 70 litres of water a day. The eco-system created by Badia Farms uses 90 percent less water than open-field farming and recycles its water up to nine times.
“We’re using hydroponics,” Al- Jundi said. “The biggest advantage is that we do not spray pesticides, which are messing up our health. In fact, we extensively use stickers to attract insects away from the crops.” Different levels of lighting are provided for each stage of the plants before they are sent out as they were grown. “They’re intense in flavor and it’s the freshest you can get that way,” he said. “My personal favourite is chocolate mint.” With 60 clients so far, serving hotels, restaurants, and cafes, the model is a first for the region, which made it challenging to set up. “All the ones abroad are designed for different climatic conditions so none of them are applicable here, where there is extreme humidity and high temperatures,” he said. “And to convince a chef to give you his time, when you don’t have the track record, was a big challenge. I wasn’t a known farmer yet.”
The system’s structure was manufactured in Riyadh, with a plan to set up the next facility by 2020 in Jeddah. Until then, the plan is to cater to Saudi as well as the UAE. “Dubai is a good testing ground and Saudi’s vision now is to support our type of sustainable growing and ecological farms, so it’s perfectly in line with what we want to do,” Al-Jundi said. “The government is now delegated to move into sustainable growing and find viable solutions to address self-sufficiency, so it’s not a slogan anymore: it’s the real deal.”
He hopes to develop similar projects across the Kingdom in the future. “My aim is to make sure we truly become self-sufficient,” he said. “Vertical farming is one solution but it’s not the full one — the ideal solution lies in all models of modern farming. What’s close to my heart is giving people healthy food while preserving our resources, and I believe the new generations of Saudis are ambitious and want to evolve our country. We were just waiting for the opportunity and it has finally come.”
Source: Arab News
7 New HDB Carpark Rooftop Sites Offered For Rental For Urban Farming In Public Tender
More local produce. Part of Singapore's efforts to strengthen its food security is increasing its capability to produce food locally
Part of Singapore's efforts to strengthen its food security is increasing its capability to produce food locally.
To do this, more sites for urban rooftop farms atop multi-storey Housing Development Board (HDB) carparks are being offered for rental, via a public tender process that was launched today (Feb. 23).
Seven new sites
Seven sites have been identified in Jurong West, Bukit Panjang, Sembawang and Woodlands, according to the Singapore Food Agency (SFA) and HDB.
The sites will be used to farm vegetables and other food crops, and will also be used to pack and store produce.
They will be tendered out as a single site (in Jurong West) and three cluster sites (in Bukit Panjang, Sembawang and Woodlands).
Screenshot from SFA and HDB
Tenderers who successfully bid for cluster sites will be awarded all sites within the cluster, to allow them to cut costs through production at scale.
Single-site farms, on the other hand, provide opportunities to "testbed innovative ideas".
Tenderers must submit their proposals via GeBiz before the tender closes on Mar. 23, 4pm.
Proposals will be assessed on their bid price, production output, design and site layout, as well as their business and marketing plans.
More information can be found on SFA's website here.
Producing food locally
This is the second time tenders were launched for rooftop urban farms on carparks here — the first took place in Sep. 2020, with nine sites being awarded.
Collectively, the nine farming systems can potentially produce around 1,600 tonnes (1,600,000kg) of vegetables per year.
Having more space for commercial farming in land-constrained Singapore is one of SFA's strategies to achieve its "30 by 30" goal — which is to produce 30 percent of Singapore's food locally by 2030.
The move is also in line with HDB’s Green Towns Programme to intensify greening in HDB estates.
“Besides contributing to our food security, Multi-Storey Car Park (MSCP) rooftop farms help to bring the community closer to local produce, thereby raising awareness and support for local produce," said Melvin Chow, Senior Director of SFA’s Food Supply Resilience Division.
Smart Agriculture Startup Bowery Farming Hires A Google Veteran As CTO
The hire comes after a year of accelerated growth at Bowery, with retail sales at outlets like Whole Foods rising 600% and e-commerce sales via Amazon and others increasing fourfold, the company says, while declining to disclose its actual sales or production figures.
One goal of high-tech indoor farming startup Bowery Farming is to use artificial intelligence and machine learning to enhance its crop yields and reduce costs. So the five-year-old Manhattan-based company has hired Google and Samsung veteran Injong Rhee as its new chief technology officer.
Rhee, who was previously Internet of Things VP at Google and chief technologist at Samsung Mobile, will focus on improving Bowery’s computer-vision system and other sensors that analyze when plants need water and nutrients, while also looking to apply the company’s accumulated historical data to new problems.
Bowery grow room near Baltimore
“Agriculture is sitting at the crux of the world’s most challenging problems like food shortages, climate change, water shortages, a lack of arable space,” Rhee tells Fortune about his decision to join the startup. “These are very challenging problems, and all of these are relevant to what Bowery tackles every day. Any advances we make here lead to a better world.”
There’s also the matter of the kale, Rhee adds.
Bowery so far has focused on growing and selling green leafy vegetables like lettuce, arugula, and kale, though it aims to add other categories of produce soon. “It was an eye-popping experience,” Rhee says of his first time trying Bowery’s kale. “How can it be so sweet and so crunchy. That was amazing.”
The hire comes after a year of accelerated growth at Bowery, with retail sales at outlets like Whole Foods rising 600% and e-commerce sales via Amazon and others increasing fourfold, the company says, while declining to disclose its actual sales or production figures. With two large warehouse-size farms in operation, in New Jersey and Maryland, Bowery is on the verge of opening its third indoor growing center in Bethlehem, Pa. The startup claims its high-tech methods, though more expensive than growing outdoors, create farms that are more than 100 times as productive per square foot as traditional outdoor farms.
“COVID was an accelerator of trends,” Bowery CEO and founder Irving Fain says. The pandemic disrupted food supply chains stretching across the globe, giving an advantage to Bowery, which sells its produce within just a few hundred miles of each farm, he says. “That amplified and accelerated a trend towards simplifying supply chains, and creating a surety of supply.”
But Bowery also faces a host of competitors, from other indoor farming startups like AeroFarms and Gotham Greens, to more traditional ag companies like John Deere and Bayer’s Monsanto, all fueling a movement toward precision farming. If one-quarter of farms worldwide adopted precision agriculture using A.I. and other data-crunching methods by 2030, farmers’ annual expenses would decline by $100 billion, or as much as 4% of the sector’s total expenses, while saving water and reducing greenhouse gas emissions, a recent study by McKinsey found.
Rhee spent 15 years as a professor of computer science at North Carolina State University, where he helped develop core Internet standards for transporting data at high speeds. He joined Samsung in 2011 where he helped lead a wide range of projects including the Bixby digital assistant, Knox security app, and Samsung Pay mobile payments service. He moved to Google in 2018 as an entrepreneur-in-residence to focus on Internet of Things projects.
Bowery has raised over $170 million in venture capital from a mix of tech figures like Amazon consumer CEO Jeff Wilke and Uber CEO Dara Khosrowshahi, well-known restaurateurs such as Tom Colicchio and David Barber, and venture capital firms including Temasek, GV, and General Catalyst.
Vertical Farming Takes Root In Taiwan
Taiwan is uniquely placed to benefit from the application of information technology to agriculture, enabling it to help provide food for an expanding global population.
Exposed root system for hydroponically grown plants at YesHealth's iFarm in Taoyuan. Photo: Jules Quartly
After becoming a world leader in semiconductors and other electronic products, Taiwan is now looking to smart agriculture as its next vine to climb. The island aims to supply much of the world’s fruit and vegetables within the next 30 years.
This might seem rather unlikely until you consider that the future of farming is not land and labor but factories and robots. Furthermore, Taiwan already possesses in abundance the tools that tomorrow’s smart farmers will use, including solar and advanced light technology, chemicals, gene editing, drones, smart sensors, software, algorithms, data mining, and big data.
Many of these technologies are being put to use in a glittering new 14-story vertical farm at Copenhagen Markets in Denmark’s capital. The first phase of construction of the 7,000-square-meter facility finished in early December. It is one of Europe’s biggest and most efficient vertical farms and was built using a blueprint of patented technologies from Taiwan’s YesHealth Group.
The result of a partnership between YesHealth and Danish agritech startup Nordic Harvest, the farm looks like a fancy warehouse from the outside. The interior is fitted with rows upon rows and columns upon columns of trays containing leafy greens, growing under an intense battery of more than 20,000 smart LED lights. The plants are tended by engineers in lab coats and guided by software that processes over 5,000 individual data points to optimize plant health.
Rows of fresh produce grown under batteries of LED lights at iFarm. Photo: Jules Quartly
The LEDs provide variable spectrum light for 100 different kinds of plants, nanobubble hydroponics oxygenate the roots and inhibit bacterial growth, and liquid microbial fertilizers derived from oyster shells, brown sugar, and soy milk provide essential nutrients for plants and soil. Even the music played to the plants is science-infused, with classical or light jazz music ranging between 115 and 250 Hertz seeming to work best.
Production at the new vertical farm is set to begin in the new year and will scale up to around 3,000 kilograms of leafy vegetables per day by the end of 2021, equating to approximately 1,000 tons of greens annually. Crucially, unlike most farms, these figures are close to guaranteed since production is not at the mercy of climate, the weather, pests and disease, pesticide residue, nitrate levels, or hundreds of other variables that affect traditional farming.
According to Jesper Hansen, YesHealth Group’s Chief Communications Officer, the partnership with Nordic Harvest has been a productive one so far. It took just five months to install the farm and all the produce is pre-sold to ensure the operation is profitable by Q3 of 2021.
“This collaboration is just the start of a long-term journey together,” Hansen said in an email from Denmark. He notes that the two partners plan to expand to other Scandinavian countries over the next several years.
Hansen credits Taiwan for its efficient development of the technology and know-how to reproduce vertical farms all over the world and calls the Danish development “a crucial milestone in our international expansion.” He adds that the company is eyeing new partners in Europe, Asia, and the MENA (the Middle East and North Africa) region.
YesHealth is the brainchild of serial tech entrepreneur Winston Tsai, who started an LCD screen company at age 21. His “eureka moment” came after being diagnosed with liver cancer and partly linking his illness to pollution in foods. After recovering, he made it his mission to produce affordable, pesticide-free produce by harnessing the power of technology.
He founded YesHealth Agri-Biotechnology Co. Ltd. in 2011 and six years later established YesHealth iFarm in Taoyuan’s Luzhu District. The iFarm cultivates an ever-expanding range of leafy vegetables and herbs in a 2,500-square-meter warehouse factory. It produces 1,500 kilograms of leafy greens per day, a yield which the company says is 100 times more efficient than a traditional farm using the same space and requires only 10% as much water. In addition, YesHealth has a farm in China’s Shenzhen, which harvests up to 2,500 kilograms per day.
A tour of iFarm is well worth a visit and introduces the wide variety of plants grown there. Photo: Jules Quartly
YesHealth’s products are sold to major retailers both in Taiwan and abroad, including restaurants, hotels, and airports. Its stated aim is to supply a total of 7,000 kilograms of leafy greens per day worldwide in 2021.
Diners enjoy a meal at iFarm’s restaurant, which overlooks the vertical farm. Photo: Jules Quartly
Having sampled the produce at the iFarm, I can confirm the arugula grown there is as tasty as any I have tried, while the lettuce and leguminous alfalfa is a perfectly clean, green, and crunchy eating experience – the result, I was informed, of an optimal growing environment and harvesting at exactly the right time.
A plate of salad featuring leafy greens grown at the iFarm site. Photo: Jules Quartly
In a sense, it’s back to the future for Taiwan, which had a largely agricultural economy up until the 1950s. Agriculture was one of the pillars supporting the nation’s economic miracle after World War II. With the help of mechanization and productivity gains, agricultural production at that time contributed around a third of Taiwan’s GDP.
In more recent times it has accounted for just 1.8-1.9% of GDP. That greatly reduced figure, which includes animal husbandry, fishing, and forestry, is not due to a decline in agricultural output per se, so much as the growth in manufacturing and the emergence of a pervasive service sector.
Taiwan has a wide range of rich, often volcanic soils that are exceptionally fertile, along with a subtropical climate that provides plentiful sun and rain. It is known as the “Fruit Kingdom” because of the quality of its fruit, with dozens of varieties ranging from bananas and papayas to wax apples and guavas. More than 100 kinds of vegetables grow all year round.
On the other hand, Taiwan’s mainly mountainous geography means just 25% of the land is suitable for farming. Meanwhile, climate change is affecting agricultural production by increasing summer temperatures and making rainfall more unpredictable. At the same time, considerable soil erosion, acidification, contamination by chemicals and heavy metals, and strong pesticide use have diminished soil quality over the last 50 years.
Furthermore, the proportion of Taiwanese involved in farming has rapidly declined, from 37% of the population in the early 1970s to the current 15% or less, according to the Yearbook of the Republic of China. Not only is the farming population declining, but it’s also ageing as well.
Those factors may not pose as much of an issue, however, since the old model of agriculture is being disrupted so dramatically that even economies of scale are being upended. Given the large size and advanced technology of the U.S., it may come as no surprise that it is the world’s biggest exporter of food as measured by value. Second on the list, however, is the Netherlands, which has just 0.045% the area of the U.S.
According to a National Geographic report in September 2017, the Netherlands’ achievement can be attributed to the work coming out of Wageningen University & Research, 80 kilometres from Amsterdam in the heart of Food Valley – the world’s agricultural equivalent of Silicon Valley in California. The university strives to come up with ways to increase yields and sustainability, and then to disseminate that knowledge.
New generation
With its strong background in information technology, Taiwan is in a good position to follow that example. The island manufactures everything required for what is known as precision agriculture, a farming management concept that uses IT to collect data from multiple sources as a means of increasing crop yields and boosting profitability. Taiwan is thus the ideal place for putting together prototypes relatively quickly and cheaply.
YesHealth, for example, makes its own LED lights through a local contractor rather than relying on a major manufacturer like Philips, which means it’s nimbler in terms of bringing focused, new tech to the market – and reaping the dividends. According to the company’s Program Manager, Dennis Jan, Taoyuan’s iFarm has the sixth generation LED lighting, while new iterations that are increasingly productive and energy-efficient are being rolled out on an almost annual basis.
The Council of Agriculture (COA) recognized some time ago the need for a precision approach to farming. In 2016, it developed the “Smart Agriculture 4.0 Program,” which was passed by the legislature a year later.
COA realized that the nation’s “calorie-based food self-sufficiency rate is relatively low” and that “shortages in food supplies and escalations in food prices” will inevitably occur as the world’s population expands from 7.5 billion to an expected 10.5 billion by 2050.
The Food and Agriculture Organization of the United Nations says that in order to meet the needs of all these additional people, about 70% more food needs to be produced. Gains achieved in improving crop yields have plateaued and are unlikely to rise again without a complete transformation of the agricultural landscape through the introduction of city farms, vertical farming, and the application of information technology.
In a written response to Taiwan Business TOPICS, COA commented: “With the rapid development of sensing technology, smart machinery devices, IoT, and big data analysis, smart agriculture has been growing in various fields.
“For example, it can monitor and control the production environment automatically to keep animals and crops in the best condition,” COA said. “It can predict harvesting dates and yields through data analysis and make adjustments to maintain a balance of production and marketing, and it can use smart automated machinery in agricultural operation to significantly reduce the labor burden.” Such uses, says the Council, “make agriculture more competitive.”
Fruitful results
Besides fruit orchards, other sectors that COA has included within Agriculture 4.0 include seedlings, mushrooms, rice, aquaculture, poultry, livestock, and offshore fisheries.
COA cites Taiwan Lettuce Village as an enterprise that has benefited from precision farming. The company halved fertilizer use but improved harvest efficiency 1.5 times by introducing a fertilization recommendation system, a harvesting date and yield prediction system, synchronous fertilizing technology, and transplanter and harvester technology.
According to COA the application of precision farming increased yield prediction accuracy by 5% and prevented 350 metric tons of overstocking. In addition, plant disease and pest control were improved through the use of a cloud-based system and machine learning algorithm. “The results were very fruitful,” COA concluded.
Agriculture 4.0 doesn’t just apply to the growing of produce; it also looks at the storage, transport, and export of goods. As an example, COA points to a relatively new fruit hybrid that was originally developed in Israel in the late 1960s. The atemoya – or pineapple sugar apple (鳳梨釋迦), as it is known in Taiwan – is a heart-shaped fruit with green, scaly skin. A cross between wax apples and the cherimoya (often referred to as Buddha’s head fruit locally), it has become synonymous with Taiwan and export success, much like the kiwi fruit and New Zealand.
Previously, 90% of the country’s atemoya exports went to China because it is so close. Later, the Taitung District Agricultural Research and Extension Station introduced a frozen whole-fruit technique that enables 95% of thawed fruit to have a “consistent ripening texture and dramatically improved the raw material quality.”
The technique involves a quick freeze to -40° Celsius, which inhibits bacteria, allowing the whole fruit to be transported at a fairly standard -18°C. After thawing, it can meet the rigorous food safety standards of Japan and South Korea.
Traditional farmers may harbor concerns about agriculture becoming a primarily manufacturing process, taking place under artificial light. However, Kevin Lin, Head of Business Development at YesHealth, insists that what the company is doing is still agriculture.
“This is nature; we are just optimizing it,” he says. “Sustainability is at the forefront of what we do, and our focus now is on ensuring the energy costs of vertical farming – such as heating and lights – are lowered and the source is sustainable.”
In this way, Lin says, Taiwan can produce cheap, healthy, and environmentally friendly food that can help feed the world, even as the global population approaches the staggering 10.5 billion mark.
“Sharing Technology Is The Only Way The Industry Will Grow”
Lack of this might lead to farmers being susceptible to misleading information, using ineffective technologies, which I’ve seen many people suffering from.
“There is a lack of know-how amongst farmers to apply those techniques in a successful way,” says Joe Swartz, Vice president and Lead horticulturalists at AmHydro. In every situation, according to Joe, from geography to the skill of the grower or climate control, all play into what types of technology should be used. This requires a lot of experience and knowledge. Lack of this might lead to farmers being susceptible to misleading information, using ineffective technologies, which I’ve seen many people suffering from.
Joe adds, “Watching many good growers that have been led down a bad path in the industry, while investing so much into technologies that are not really effective, really breaks my heart. While providers know that they aren’t effective in this particular situation. With many years of industry experience, Joe is well aware of the challenges that the industry faces these days. Within the aquaponics sector there is not one singular technology, just as in conventional farming, rather various unique technologies can be combined for different outcomes.
Lack of know-how
When asked about the kind of growers that Joe educates, he notes that there are two kinds of growers contacting him. “We have two types of growers: either growers facing challenges or new growers wanting equipment and knowledge. Both of those approaches are interesting and it’s great to be able to help them become successful. It is great to see our system helping companies to grow and develop and become a worldwide provider. Growers like that keep coming back to us. They are the ones that move the industry”.
Joe Swartz, Vice president
An essential part of being a vertical farmer, in Joe’s opinion, is having experience with working on the ground floor. Only this will teach you what it takes to manage the equipment, crops and technology. “The best growers have started in the greenhouse. Hydro-experts will get nowhere with their college degree alone,” Joe states. For that reason, AmHydro offers grower seminars and even possesses a commercial greenhouse where growers can work in order to gain experience. “Some growers don’t think that they need it as they rely on technology, but my experience is exactly the opposite.”
Fake promises
Joe observes similar trends as in the 1980s when certain technologies were promoted as ‘the farming of the future’. People talked about automatic farming, in which no farmer would be needed, new techniques and new lightings. All things we hear today were said back then. What happened afterward, according to Joe, was that some techniques turned out disappointing. Millions of dollars invested were lost, leading to the industry losing its credibility.
“As a result, investors only valid projects that already have a positive cash flow, as they have become more cautious. Some growers struggled to get funding, even though they had a viable business model. In a certain way, negative events have closed off some appetite for investments in CEA, which is a shame. It is a good investment in general, but every time we see a less than a reputable company or a technology that fails, it holds the industry back.”
Misconception
Related to that, Joe says that vertical farming still has to overcome a somewhat negative public image. “The traditional consumer, at least in the USA, have an image of farmers working on the land using sustainable methods. Now, being a conventional farmer using hydroponics I know that it is a sustainable and safe way to produce food, but there’s a public perception of automatization, as robotic food. Some people even call it “Frankenfood”. In my opinion, the more we can promote CEA as what it is, sustainable growing techniques, people will be more accepting and investors will invest more easily”.
Joe strongly senses that the vertical farming industry needs more skilled farmers and growers to meet the demand. “A lot of my work is actually training people. We want to help especially young people, new to the industry, by giving them skills, experience and knowledge. I have been blessed to have mentors when I was young and I try my best to pass that knowledge as this will help the industry along. That’s one of the reasons why we now see some consultancy firms who see economic opportunities. Sharing technology is the only way in which the industry will grow,” says Joe.
“Despite the diversity amongst growers that I meet in over 66 countries, all growers face similar problems. Funny tech flitches, pipes that break and spray water all over the greenhouse, or water pumps that break down. It doesn’t matter whether it’s a technologically advanced greenhouse or a small low-tech one. It kind of goes across the board,” says Joe laughing.
For more information:
AmHydro
Joe Swartz, Vice president and Lead horticulturalist
joe@amhydro.com
www.amhydro.com
Author: Rebekka Boekhout
© VerticalFarmDaily.com
How Vertical Farms Could Be Ready To Take-Off
A new interdisciplinary study combining biology and engineering sets down steps towards accelerating the growth of vertical farming, including the use of aeroponics which uses nutrient-enriched aerosols in place of soil, reports Science Daily
24 Jul 2020
Study identifies future research areas needed to accelerate growth of vertical farming using aeroponics.
A new interdisciplinary study combining biology and engineering sets down steps towards accelerating the growth of vertical farming, including the use of aeroponics which uses nutrient-enriched aerosols in place of soil, reports Science Daily.
Accelerate sustainable growth of vertical farming
The study was carried out by the John Innes Centre, the University of Bristol, and the aeroponic technology provider LettUs Grow. It identifies future research areas needed to accelerate the sustainable growth of vertical farming using aeroponic systems.
Dr. Antony Dodd, a group leader at the John Innes Centre and senior author of the study, says: “By bringing fundamental biological insights into the context of the physics of growing plants in an aerosol, we can help the vertical farming business become more productive more quickly while producing healthier food with less environmental impact.”
Vertical farming is a type of indoor agriculture where crops are cultivated in stacked systems with water, lighting, and nutrient sources carefully controlled.
Seven areas of future research
The study, which appears in the journal New Phytologist and is called Getting to the Roots of Aeroponic Indoor Farming, lays out seven steps – strategic areas of future research needed to underpin increased productivity and sustainability of aeroponic vertical farms.
These seek to understand:
Why aeroponic cultivation can be more productive than hydroponic or soil cultivation.
The relationship between aeroponic cultivation and 24-hour circadian rhythms of plants.
Root development of a range of crops in aeroponic conditions.
The relationship between aerosol droplet size and deposition and plant performance.
How we can establish frameworks for comparing vertical farming technologies for a range of crops.
How aeroponic methods affect microbial interactions with plant roots.
The nature of recycling of root exudates (fluids secreted by the roots of plants) within the nutrient solutions of closed aeroponic systems.
The report argues that a driver of technological innovation in vertical farms is minimizing operation costs whilst maximizing productivity – and that investment in fundamental biological research has a significant role.
Genetically tune crops to grow in vertical farms
John Innes Centre researchers have bred a line of broccoli adapted to grow indoors for a major supermarket and one of the aims of research will be to test how we can genetically tune more crops to grow in the controlled space of vertical farms.
Bethany Eldridge, a researcher at the University of Bristol studying root-environment interactions and first author of the study adds: “Given that 80% of agricultural land worldwide is reported to have moderate or severe erosion, the ability to grow crops in a soilless system with minimal fertilizers and pesticides is advantageous because it provides an opportunity to grow crops in areas facing soil erosion or other environmental issues such as algal blooms in local water bodies that may have been driven by traditional, soil-based, agriculture.”
Aeroponics is associated with very little water, automation, and high tech systems. But what is the current potential of aeroponics technology to grow food or cannabis crops economically?
Hugo Claver
Web editor for Future Farming
Lead Photo: - Photo: ThisIsEngineering
Virtual Fences, Robot Workers, Stacked Crops: Farming In 2040
It is 2040 and Britain’s green and pleasant countryside is populated by robots. We have vertical farms of leafy salads, fruit and vegetables, and livestock is protected by virtual fencing
Population growth and climate change mean we need hi-tech to boost crops, says a new report
Jamie Doward
17 Feb 2019
An AI-powered platform called Dick that can spray chemicals and fertilisers exactly where they are needed. Photograph: NFU
It is 2040 and Britain’s green and pleasant countryside is populated by robots. We have vertical farms of leafy salads, fruit and vegetables, and livestock is protected by virtual fencing. Changing diets have seen a decline in meat consumption while new biotech production techniques not only help preserve crops but also make them more nutritious.
This is the picture painted in a report from the National Farmers Union which attempts to sketch out what British food and farming will look like in 20 years’ time.
An AI-powered platform called Dick that can spray chemicals and fertilisers exactly where they are needed. Photograph: NFU
“The Future of Food 2040 report is a catalyst to encourage us all to start the debate about our food and our future so we can plan ahead,” said Andrea Graham, NFU’s head of policy services and author of the report, who interviewed 50 experts across Britain’s food chain to gauge their views. “It is also a reminder for government, at a critical time in British history, to make domestic food production a strategic priority in all policy making.”
Andrea Graham, the report’s author. Photograph: Toby Lea
While some of the predictions may seem a long way off, others are already in their infancy. “Even now, there are technologies being developed that can care for crops on a plant-by-plant basis or control the grazing of cattle without physical fences, and by 2040 this technology will be commonplace in farming,” Graham said.
The British farming sector will need to be more efficient if it is to meet a key NFU goal of producing net zero greenhouse gas emissions by 2040. “Over the next 20 years we will face potentially seismic changes in all aspects of society,” Graham added. “An increase in the global population and the need to mitigate climate change will provide opportunities for British food and farming to increase productivity and reduce its impact on the environment.”
The introduction of vertical stacking and recent advances in LED technology will expand the range of crops that can be grown using hydroponics, aquaponics and other controlled environment systems. Worldwide predictions suggest that the vertical farming industry will grow to be worth billions of pounds over the next few years. Leafy salads, and some vegetables and fruits will be widely grown using the technology. However, its high energy consumption will need to have been overcome, and certain crops will remain difficult to grow, the report acknowledges.
Another key trend will be 3D-printed food, which will produce “intricate sculptures out of everyday foodstuffs that will look good and will also be used to improve the convenience and the nutritional value of meals”. This will enable more food to be produced on demand, reducing wastage.
A robotic strawberry picker, designed by the University of Essex. Photograph: NFU
With the UK on course to be the most obese nation in Europe by 2030, a greater focus on healthy food will emerge. The popularity of flexitarian diets, which are predominantly vegetarian with only occasional meat and fish consumption, is likely to continue to increase. Already 41% of meat-eaters currently classify themselves as flexitarian, and the percentage of meat-free evening meals is on the rise in Britain, according to research from Kantar Worldpanel.
In-vitro meat, cultivated from animal cells rather than from slaughtered animals, and insect protein “may well grow in popularity depending on advances in making these protein sources more palatable, and the ability for them to be produced cost-effectively at scale”, the report says.
On farms, technology will play an increasingly pivotal role. Nano-sensors will be able to collect an array of information, such as soil data and moisture levels, reducing the need to perform daily routine jobs such as checking fuel levels and temperatures.
The use of unmanned aerial vehicles (UAVs), or drones, for sensing and mapping will become widespread, while robots will perform labour-intensive tasks such as fruit picking, milking, livestock feeding and even slaughter.
A growing premium for antibiotic-free meat will see the use of biotechnology in food production become ubiquitous. New breeding technologies, such as genome editing to produce plants and animals with enhanced immune systems and disease resistance, will also become commonplace.
“There’s some great technology out there,” Graham said. “The problem is that much of it is still just prototypes, and small-scale. “The challenge is: can we scale up? How do we go from a few scientists working with just one farmer to a much wider uptake?”