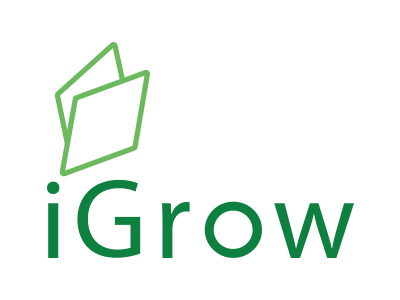
Welcome to iGrow News, Your Source for the World of Indoor Vertical Farming
VIDEO: Local-For-Local Food Production In Climate Containers
Bosman Van Zaal is getting more and more questions about the use of Grow & Roll climate containers for food production, equipped with cultivation systems with multiple cultivation layers. Organizations that are committed to local food products are showing particular interest
18-12-2020 | Goedemorgen
NETHERLANDS- Bosman Van Zaal is getting more and more questions about the use of Grow & Roll climate containers for food production, equipped with cultivation systems with multiple cultivation layers. Organizations that are committed to local food products are showing particular interest.
Under own management
The Grow & Roll climate containers have been developed in-house since 2016 and adapted to applications by third parties. In 2019, for example, an entrepreneur from the United States, together with several other companies from the Green Innovators Group, developed a closed climate unit in a sea container for research and cultivation of plant material. The results of this research will form the basis for large-scale Vertical Farming in the future.
The knowledge gained has led to further development at Bosman Van Zaal, as a result of which the climate containers are now also suitable for food production on location.
Multilayer cultivation
Vertical Farming is one of the solutions to the problem of the growing demand for food. A multi-layer system uses less surface area, energy, and water. And production takes place all year round, resulting in higher yields.
Tailor-made climate
Each unit is equipped with various installations, which together determine the climate in the container in an integrated way, controlled by a climate computer. Systems for heating, cooling, ventilation, water, air, and water purification, fertilization, CO2 and LED lighting are often the ingredients for an optimally closed climate, anywhere in the world, on an outdoor site, or in a building. Peripheral equipment or hardware are easy to install, allowing this flexible form of food production to continue to take place quickly and efficiently, even in the longer term.
Housing
For practical reasons, standard sea containers are widely used because they are relatively easy to transport and move. Because of their handy dimensions, these units are also suitable for placing in buildings, possibly stacked. In this way, the vertical food production is taken even further.
Bosman Van Zaal
Bosman Van Zaal develops, produces, and builds complete horticultural projects at home and abroad. The projects are based on the latest developments and the latest insights for the sustainable and efficient cultivation of food crops, ornamentals, and plants for the cosmetics and pharmaceutical industries. For more information, please visit www.bosmanvanzaal.com.
10 Ways Square Roots’ Farm-Tech Platform Empowers The Next Generation of Farmers
Square Roots’ scalable “farmer-first” platform brings fresh, healthy food to urban areas all year-round, while simultaneously training future generations of farmers to maintain sustainability in the future.
Square Roots is building a distributed network of indoor, modular farms, farmed by a new generation of farmers, to grow local food for people in cities all over the world. Here’s why it’s working.
Square Roots Super Farms are scalable, resilient and smart, and can be built fast. (Image: Via Chicago Architects + Diseñadores)
Square Roots’ scalable “farmer-first” platform brings fresh, healthy food to urban areas year-round, while simultaneously training future generations of farmers. With production farms in Brooklyn, New York, and Grand Rapids, Michigan (with more to come in 2020!), Square Roots has a mission to bring local, real food to people in cities across the world while empowering the next generation of leaders in urban farming.
Whether we’re in the farms tweaking CO2 levels, or in a board meeting plotting a pathway for what the company looks like in 2050, every decision we make is guided to help us achieve our mission faster, smarter, and with as much impact as possible.
Choices we’ve made around our technology platform are a good illustration of that. Our platform needs to bring fresh, healthy food to urban areas year-round, consistently, sustainability, and on any continent in the world. At the same time, it must also be a welcoming environment, conducive to training future generations of farmers to be productive, fast.
Central to our platform is the decision we made very early in the company’s life to build a distributed network of modular Climate Containers, as opposed to following the plant factory template.
Inside a Square Roots Climate Container, data-empowered farmers work with optimum growing conditions, all year round.
There are a lot of smart people in this industry, many with different visions for the optimum architecture and model for indoor farming (e.g. plant factories). But all working hard to bring better food to market — which, given our wider vision to bring real food to everyone, is wonderful to see. The more of us working on the real food revolution the better — and we want all of these systems to flourish. But here are 10 reasons why we think container farming rocks:
1. Speed to Market
Today we can enter a new market and open a Square Roots “Super Farm” — with 25 Climate Containers, cold storage, biosecurity infrastructure, and everything else you need to run a food-safe farm at scale — in less than three months, like we did in partnership with Gordon Food Service last Fall. That time period is only coming down. In comparison, building a plant factory can cost tens of millions of dollars, as well as take years to construct. We want to get real food to more people, and fast!
2. Easy to Scale
To meet increasing market demand, we simply add Climate Containers to any existing deployment. This means just-in-time capital deployment, and also just-in-time technology deployment. This is really important in an industry where the technology is improving fast. You don’t want to spend years and millions to open a big farm full of old tech that immediately needs a refresh.
3. Climate Control
I was an early investor in Chicago’s Farmed Here, one of the first and largest plant factories in the US. There, I saw first-hand how much the team struggled to control the climate in a building that size. Plants don’t like it when you get it wrong. And neither do landlords — the humidity can wreak havoc with the underlying infrastructure. In our programmable Climate Containers, each one built inside a 320 square foot shipping container, optimum conditions for a variety of crops can easily be maintained. The perfect climate for each variety can be seamlessly replicated — in any market — to ensure consistent quality every time, at every harvest.
Alyssa Patton, Square Roots Next-Gen Farmer, harvesting fresh, local basil inside a Climate Container in Grand Rapids, Michigan.
4. Diversity of Products
Multiple containers on our Super Farms allow for multiple climates, which lets us grow multiple crops at the same time to satisfy local market demands. For example, basil requires a completely different climate than chives to grow well, so it’s practically impossible to grow these two products together in a way that tastes good if you have a giant farm with one mono climate. The ability to grow multiple quality SKUs is particularly important in the retail market, where product variety is key to getting shelf real estate. Having multiple climates also means we can tackle many niches in any local market (e.g. using one container on a Super Farm to grow something exotic like Shiso or Mustard Greens), giving us a lot of business flexibility while keeping things interesting for our teams of farmers.
5. Sustainable Systems
As with most hydroponic growers, Square Roots uses zero pesticides, and 90% less water than outdoor farms. We can also be clever about energy usage. For example, we make it “daytime” in the farm by turning on our grow lights overnight when there is excess energy in the grid, and the cost per kilowatt-hour is lower. However, if for some reason we need to be in the farms during “daytime,” we can put a Climate Container into “harvest mode” — which dims the lights, and configures the climate to be optimum conditions for people at work — before seamlessly switching back to plant growing mode once we’re done.
6. Location
Our modular architecture means we can be very creative in repurposing existing city infrastructure when we look for locations to build a farm. We can pop up on an empty parking lot like we did in Brooklyn, New York, or build a campus on the headquarters of a major distribution company like we did with Gordon Food Service, or even build into a new development. This flexibility means we can build our Super Farms literally in the same zip code as the end consumer. This means fresher and tastier products for the customer, fewer food miles (most industrial food is shipped in from the other side of the world!), and less food waste. It also helps to get consumers more connected to their food and the people who grow it — they can simply jump on a subway or in their car, and come visit one of our farms!
7. Food Safety and System Resilience
All indoor farms need to be prepared for bad things to happen. While there is way less risk in a controlled environment versus an outdoor farm, it’s inevitable that you will get some sort of pest outbreak, powdery mildew, or some other issue at some point while you’re managing a complex ecosystem full of living, breathing plants. If that ever should happen in one of our Climate Containers, we can quickly shut it down and reboot that single node while the rest of the network keeps going strong. I’ve seen this happen in a plant factory, with one big mono climate, and you lose all your crops.
8. Faster Learning
Our farms are cloud-connected, and we collect millions of data points that we analyze to determine how changes in certain environmental parameters can impact factors like yield, taste, and texture of the final product. More climates in more containers means more feedback loops, which means faster learning. To systematize this learning, we’ve built The Square Roots Farmer Toolbelt — a software which is now the OS for the whole company as we all learn faster together.
9. The Network Gets Smarter as it Scales
Square Roots’ cloud-connected farms and data-empowered farmers learn from each other, enabling us to replicate success from one location to another, seamlessly. Working with Gordon Food Service to build farms across their network of distribution centers and retail stores brings us closer to the vision of a distributed network of indoor farms, bringing local, real food to people in cities across the world—while empowering thousands of next-gen leaders in urban farming through our unique training program.
10. Sense of Responsibility
Perhaps this is unique to Square Roots and our Next-Gen Farmer Training Program, but because we grow in modular Climate Containers, we’re able to give all our young farmers a personalized understanding of their individual impact on the overall business. The Square Roots Farmer Toolbelt provides day-to-day instructions on a per-farmer and per-crop basis, as well as a means for data capture, and real time analysis of both plant health and business metrics. All this information is accessible from the tablets that everyone on our farm team carries everyday. This system also ensures that we track every aspect of production — who does what, when, and how, from seed to sales. This is a goldmine of data, that not only helps us improve operations, but also implicitly provides traceability. In December 2018, we started exposing this data to consumers in the form of our Transparency Timeline. On every package of Square Roots produce, you can simply scan a QR code and get a complete story of where your food comes from — seed to shelf.
Simply scan the QR code on every Square Roots package to see where your food comes from.
Our Super Farm platform is exciting in terms of scalability, resilience, and efficiency, and it’s a really wonderful environment for our farmers to farm in. For urban consumers it means local farmers growing your food with love — which is why it tastes absolutely delicious. And technology enables us to grow a ton of food in a very small area, in ways that make a lot of business sense too. It’s a classic example of “doing well by doing good”.
It has been an exciting journey to our Super Farm platform. When we launched Square Roots back in 2016, we were very focused on figuring out the Farmer Training Program model — as we knew that farmers bring love to the food, the program would create enormous impact over time, and it would also be a long term engine of growth. So we partnered with a number of 3rd parties who could provide parts of the growing system for us, while we got the training program right. (In many ways, that was like Tesla sourcing our chassis from Lotus for the first Roadster). After that initial phase, and finding out what the urban farming world needs — i.e. higher quality yields with much lower costs to drive scalable unit economics, and ultra-high standards of biosecurity to support operations that are first class in food safety—we have developed our own technology specifically tailored to our model. This enables us to grow local food at incredible scale in ways that make sense for people, planet, and profits.
Our partnership with Gordon Food Service was announced at the end of March 2019, and our first co-located farm opened just six months later in Grand Rapids, Michigan — marking our next step of bringing local food to people in cities all across North America while training thousands of future farmers. Which, in a neat and circular way, brings us right back to the mission statement we started this post with.
Of course, we still have lots of work to do and we have a lot of exciting announcements coming this year as we grow! And, we’re always looking to talk with great people — from hardware and software engineers to farmers and plant scientists. So feel free to check our website and get in touch.
This article was originally published on the Indoor Ag-Con blog by Kimbal Musk on March 4, 2020.
Published by Dani Kliegerman for iGrow News
100% Robotization Allows Constant Quality Produce
"One of the biggest bottlenecks for most vertical farms is labor-intensity and associated costs. Our first focus was to reduce manual handling," says Ard van de Kreeke, Growx's CEO and founder
"One of the biggest bottlenecks for most vertical farms is labor-intensity and associated costs. Our first focus was to reduce manual handling," says Ard van de Kreeke, Growx's CEO and founder.
Growx has recently been featured in the 75th edition of RuMoer Magazine by BOUT, a master student association program in Building Technology at TU Delft, the Netherlands. The 75th issue is dedicated to urban farming as a solution for reconnecting the urban population to their food sources.
Ard continues, "Not only to reduce cost but also to ensure a constant quality of produce. The implementation of 100% robotization was successfully introduced in 2020. This not only makes a huge difference in labor costs and produce quality but also keeps the cell extremely clean. Human interfaces are only needed for malfunctions and checks. Another additional advantage is that there is no need to keep aisles and room for personnel to move around."
Each plant (gutters) continuously records broad water and nutrients, exposure, and air quality. But also a photographic representation in visible and infra-red light. This data stream is centrally stored and analyzed with the aim of developing optimal cultivation profiles.
Growx's robots pick up the entire process from start to finish, in other words, from seeds to harvest. "As soon as the plant moves on to the next phase of the growing cycle, the robot can respond automatically. Think of different light- or water composition," says Ard.
The company created a closed-loop system, where 100% of their waste is recycled to produce energy, CO2, water, and nutrients. They use an anaerobic digester for all the waste, which results in biogas that can be used for heat pumps and CO2 for the plants to use.
The complete article can be found here.
For more information:
Growx
info@growx.co
www.growx.co
Agrifood Tech Firms Are Flocking To Singapore, With Perfect Day The Latest To Land
US alt-dairy startup Perfect Day revealed today that it will set up an R&D facility in Singapore, with the city-state’s minister for trade and industry predicting “many other companies” will be joining it to take advantage of the growing agrifood tech ecosystem there
December 20, 2020
US alt-dairy startup Perfect Day revealed today that it will set up an R&D facility in Singapore, with the city-state’s minister for trade and industry predicting “many other companies” will be joining it to take advantage of the growing agrifood tech ecosystem there.
A*STAR's headquarters in Singapore. Image credit: A*STAR
California-based Perfect Day is establishing the joint R&D center in collaboration with Singapore’s Agency for Science, Technology, and Research (A*STAR.)
This center will bring together A*STAR’s expertise in areas such as taste analytics, cell biology, and protein biotech. The aim of the collaboration is to “build analytical platforms to characterize and quantify the key components in dairy food products that provide their distinctive taste and feel,” the startup said in a statement.
Founded in 2014, Perfect Day produces ‘animal-free’ dairy products using microflora to ferment sugars to create the same proteins, casein, and whey present in animal milk.
The startup is just the latest international agrifood tech company to set up shop in Singapore.
Invest with Impact. Click here.
Last month, German indoor farming firm &ever said it would establish its global R&D center in the city-state to carry out research into energy efficiency and yield optimization for indoor vertical farms. It’s also constructing a “mega-farm” in the east of Singapore with an annual production capacity of over 500 tons that is set to open by the end of 2021.
In October, US alt-protein startup Eat Just announced it would invest a total of $100 million with investor Proterra to build Asia’s first plant-based protein factory in Singapore. Earlier this month, the city-state handed Eat Just the world’s first regulatory approval for a cell-based, cultured meat product, clearing its ‘lab-grown’ chicken bites for sale to the public.
Swiss food industry majors Buhler and Givaudan announced the launch of a joint innovation center in Singapore in February to explore textures and tastes for plant-based protein products. French animal feed firm Adisseo set up an aquaculture R&D center in Singapore back in December 2019 to research aquatic animal health and nutrition.
Citing data from AgFunder, Singapore Minister of Trade & Industry Chan Chun Sing said that the global agrifood sector is “primed for growth” with investment into agrifoodtech startups growing 47% year-on-year in 2018 and a further 17% in 2019 to reach $19.8 billion. [Disclosure: AgFunder is AFN‘s parent company.]
With its “unique farm-to-fork ecosystem and track record for technical capabilities, quality branding, and intellectual property [IP] protection, Singapore aims to capture a significant share of the wave of economic opportunities in agrifoodtech,” Chan told reporters at a press conference announcing Perfect Day’s partnership with A*STAR.
Alt-protein products like those being developed by Perfect Day, Just Eat, and local players including Shiok Meats and TurtleTree Labs — which announced its $6.2 million pre-Series A round last week — have a critical role to play in feeding countries and cities like Singapore, where arable land is minimal and primary food sources are typically located far away.
“Alternative proteins will add to the suite of options we have without being restrained by factors like the [amount] of land and other natural resources we have. Overall, [they provide] a much more efficient, sustainable way to feed the population, across Asia, where demand will go up proportionally with the growth of the middle class,” Chan said.
But the buck doesn’t need to stop at Singapore securing its own nutritional needs, he added.
“We are not limiting our aspirations just to the domestic market. The larger market for this sector is really [the] growing needs for the Asia-Pacific, that we hope to capture. Look at China, Indonesia, India – as people become more affluent, as they seek higher quality food products, there will be a bigger market for these kinds of products. How do we feed a growing population in a sustainable manner that is also good for the environment? So our sense is not just how big the local market is, but how big the global market can be.”
“We want to make sure the core IP, the core R&D happens here – so the high-value part of the value chain is housed in Singapore, and we can attract the investment and the people to come here,” Chan said.
He noted that in addition to the arrival of foreign startups and corporates, as well as the growth of local players, a variety of domestic and international investors are contributing to the development of Singapore’s agrifood tech ecosystem.
“We are also building a vibrant cluster of financing firms across various stages, for example, New Protein Capital, EDBI, Temasek, and Proterra, as well as a base of global agrifood accelerators [such as] Big Idea Ventures‘ alternative proteins accelerator and GROW Accelerator […] Our eventual aim is to build up the talent pool with the expertise to deploy more than S$90 million [$67.5 million] of capital.” [Disclosure: GROW Accelerator is operated by AgFunder, AFN‘s parent company.]
Returning to Perfect Day’s R&D center announcement, Chan said it is another “milestone in our ongoing journey.”
“There will be many other companies joining us to build up our ecosystem,” he continued. “We’re optimistic this can become a new pillar of our economic development, providing us with greater [economic] diversity, food security for Singapore, and new opportunities in countries beyond Singapore.”
Singapore sovereign fund Temasek led Perfect Day’s $140 million Series C round in December 2019.
Got a news tip? Email me at jack@agfunder.com or find me on Twitter at @jacknwellis
alt dairy, asia, Europe, Germany, indoor agriculture, indoor farming, singapore, United States, urban agriculture, urban farming, vertical farming
2-Acre Vertical Farm Run By AI And Robots Out-Produces 720-Acre Flat Farm
A San Fransisco start-up is changing the vertical farming industry by utilizing robots to ensure optimal product quality
Plenty is an ag-tech startup in San Francisco, co-founded by Nate Storey, that is reinventing farms and farming. Storey, who is also the company’s chief science officer, says the future of farms is vertical and indoors because that way, the food can grow anywhere in the world, year-round; and the future of farms employ robots and AI to continually improve the quality of growth for fruits, vegetables, and herbs. Plenty does all these things and uses 95% less water and 99% less land because of it.
In recent years, farmers on flat farms have been using new tools for making farming better or easier. They’re using drones and robots to improve crop maintenance, while artificial intelligence is also on the rise, with over 1,600 startups and total investments reaching tens of billions of dollars. Plenty is one of those startups. However, flat farms still use a lot of water and land, while a Plenty vertical farm can produce the same quantity of fruits and vegetables as a 720-acre flat farm, but on only 2 acres!
Storey said:
“Vertical farming exists because we want to grow the world’s capacity for fresh fruits and vegetables, and we know it’s necessary.”
Plenty’s climate-controlled indoor farm has rows of plants growing vertically, hung from the ceiling. There are sun-mimicking LED lights shining on them, robots that move them around, and artificial intelligence (AI) managing all the variables of water, temperature, and light, and continually learning and optimizing how to grow bigger, faster, better crops. These futuristic features ensure every plant grows perfectly year-round. The conditions are so good that the farm produces 400 times more food per acre than an outdoor flat farm.
Storey said:
“400X greater yield per acre of ground is not just an incremental improvement, and using almost two orders of magnitude less water is also critical in a time of increasing environmental stress and climate uncertainty. All of these are truly game-changers, but they’re not the only goals.”
Another perk of vertical farming is locally produced food. The fruits and vegetables aren’t grown 1,000 miles away or more from a city; instead, at a warehouse nearby. Meaning, many transportation miles are eliminated, which is useful for reducing millions of tons of yearly CO2 emissions and prices for consumers. Imported fruits and vegetables are more expensive, so society’s most impoverished are at an extreme nutritional disadvantage. Vertical farms could solve this problem.
Storey said:
“Supply-chain breakdowns resulting from COVID-19 and natural disruptions like this year’s California wildfires demonstrate the need for a predictable and durable supply of products can only come from vertical farming.”
(Credit: Reuters)
Plenty’s farms grow non-GMO crops and don’t use herbicides or pesticides. They recycle all water used, even capturing the evaporated water in the air. The flagship farm in San Francisco is using 100% renewable energy too.
Furthermore, all the packaging is 100% recyclable, made of recycled plastic, and specially designed to keep the food fresh longer to reduce food waste.
Storey told Forbes:
“The future will be quite remarkable. And I think the size of the global fresh fruit and vegetable industry will be multiples of what it is today.”
Plenty has already received $400 million in investment capital from SoftBank, former Google chairman Eric Schmidt, and Amazon’s Jeff Bezos. It’s also struck a deal with Albertsons stores in California to supply 430 stores with fresh produce.
Ideally, the company will branch out, opening vertical farms across the country and beyond. There can never be too many places graced by better food growing with a less environmental cost.
Here’s a TechFirst podcast about the story behind Plenty:
Published by Dani Kliegerman for iGrow.News
The Nation’s First Saltwater Hydroponic Farm In Charleston, SC
Did you know that it’s possible to harvest crops using saltwater? Charleston is home to the first-ever indoor saltwater hydroponics farm that utilizes ocean water – aka the world’s most abundant resource – to grow food
Heron Farms saltwater hydroponics | Photo provided by Heron Farms
Agriculture is cool, but Lowcountry agriculture is even cooler.
Did you know that it’s possible to harvest crops using saltwater? Charleston is home to the first-ever indoor saltwater hydroponics farm that utilizes ocean water – aka the world’s most abundant resource – to grow food.
Saltwater hydroponic farming at Heron Farms | Photo provided by Heron Farms
Heron Farms, located at 1783 Harmon St., was established by Sam Norton in 2018. Sam grew up on a barrier island off the coast of South Carolina where his family home flooded more frequently + severely every year due to the sea level rise. The same issue was seen during his trip to Bangladesh, where he witnessed saltwater intrusion into coastal rice paddies upending the lives of many farmers in Asia.
This led to the idea of treating sea level rise as a free resource that could be used for agriculture instead of just an environmental problem.
Sam’s concept took shape and won the ACRE Startup Competition from the SC Department of Agriculture + the Charleston-based Harbor Accelerator Startup Competition. Following these achievements, Heron Farms was created and the idea became a reality in June 2018.
So, how does saltwater hydroponics work?
The first step in understanding the process is studying up on general hydroponic farming. Simply put, this method of indoor farming eliminates soil use by utilizing an alternative root anchor for plants + growing them directly in water (think: “hydro” = water). The inside setting eliminates the barriers of land use constraints + seasonality of crops. Plants receive controlled amounts of water, oxygen, nutrients + light that promotes the growth cycle. The difference with Heron Farms is that in all other cases, fresh water is used.
Why saltwater?
Along with the reasons mentioned above, the micronutrients of seawater that are transferred into the plants are a great source of minerals in our daily diets. Additionally, seawater irrigation allows the company to use less freshwater than any farm in the U.S.
What crops are grown?
Heron Farms sea beans | Photo provided by Heron Farms
Heron Farms’ first crop is sea beans – salicornia europaea – an edible plant that grows in the salt marsh. These types of saltwater-tolerant plants are known as halophytes, which have evolved to tolerate salt across its whole life cycle. Learn about cooking + eating sea beans here.
What makes this local company even cooler? For every pound of sea beans sold at Heron Farms, the company replants a sq. ft. of salt marsh along coastal South Carolina + Bangladesh using a custom seed-dropping drone. So far, 30,000 sq. ft. have been planted.
Heron Farms has been invited by Seawater Solutions to present at the 2021 UN Climate Change Conference in Glasgow, Scotland, where the Charleston-based company will build a second saltwater hydroponics farm.
Heron Farm’s future location in Glasgow, Scotland | Image provided by Heron Farms
Plants Have A Body Clock As Well Research Shows
This research highlights a single letter change in their DNA code can potentially decide whether a plant is a lark or a night owl
This research highlights a single letter change in their DNA code can potentially decide whether a plant is a lark or a night owl. The findings may help farmers and crop breeders to select plants with clocks that are best suited to their location, helping to boost yield and even the ability to withstand climate change.
The circadian clock is the molecular metronome that guides organisms through day and night -- cockadoodledooing the arrival of morning and drawing the curtains closed at night. In plants, it regulates a wide range of processes, from priming photosynthesis at dawn through to regulating flowering time.
These rhythmic patterns can vary depending on geography, latitude, climate, and seasons -- with plant clocks having to adapt to cope best with the local conditions.
Researchers at the Earlham Institute and John Innes Centre in Norwich wanted to better understand how much circadian variation exists naturally, with the ultimate goal of breeding crops that are more resilient to local changes in the environment -- a pressing threat with climate change.
To investigate the genetic basis of these local differences, the team examined varying circadian rhythms in Swedish Arabidopsis plants to identify and validate genes linked to the changing tick of the clock.
Click here to access the complete research.
21 Dec 2020
Published by Dani Kliegerman for iGrow.News
Belgian Lettuce Grower De Glastuin Achieves Increased Production And Faster Growth Cycles Thanks To A Full LED Solution From Signify
Belgian farmers are using LED lights in an innovative way to enhance lettuce production
December 17, 2020
Eindhoven, the Netherlands – Since the introduction of Philips GreenPower LED Toplighting Compact from Signify (Euronext: LIGHT), the world leader in lighting, many vegetable, fruit and horticulture growers have made the choice to fully equip their greenhouses with LEDs. By combining this LED lighting with the GrowWise Control System, it is possible to both control and dim the light, giving growers a high degree of flexibility. This solution has now also found its way into lettuce growing; De Glastuin in Belgium opted for 100% LED grow lights from Signify.
Each type of lettuce requires a different amount of light. Heat is also a limiting factor when growing lettuce. As a result, in many periods it is not possible to illuminate the crops because too much heat accumulates in the greenhouse. Thanks to LED lighting, which emits less heat, it is possible to light the crop for longer hours, resulting in a increased production and faster growth cycles. The combination with the GrowWise Control System also allows the lighting to be dimmed. For example, to keep the light intensity the same on sunny days while maintaining light uniformity or to prevent climate fluctuations.
This summer, lettuce grower De Glastuin expanded its existing 1.75 hectare greenhouse with HPS lighting by 0.75 hectares. In this new part of the greenhouse, Philips GreenPower LED Toplighting Compact is installed together with the GrowWise Control System. The modules in the new part of the LED greenhouse have an output of 1800 µmol/s and require only 520 W (3.5 µmol/J). They provide a light level of 90 µmol/s/m². De Glastuin is pleased with the high quality and longer shelf life of the lettuce."With Toplighting Compact in combination with the GrowWise Control System, we can automatically adjust the amount of LED light to the amount of daylight at any given moment. As a result, there are fewer fluctuations in light intensity during the day. The lighting is much more efficient, dimmable and it offers us flexibility by allowing us to provide less light at any time," says Wouter de Bruyn, business manager at De Glastuin.
"De Glastuin's choice of Signify reinforces our conviction that we have chosen the right approach to make it easier for growers to switch to LED," says Udo van Slooten, Business Leader Horticulture LED Solutions at Signify.
The first Toplighting Compact was introduced in 2019 as a 1-on-1 replacement of HPS lighting to enable an easy transition to LED. The Toplighting Compact can be mounted on an existing HPS connection. This saves time and money during installation. In new greenhouses, installation is even easier thanks to easy-to-install brackets. The universal design of this system gives growers the possibility to fully equip their greenhouse with LED lights or to change their current set-up into a hybrid system with LED and HPS lighting. Signify's Compact range is also equipped with optics with normal and wide beam angles. The wide beam angle is ideal for growers looking for optimal light distribution or for lower greenhouses, for example. For crops where a greater distance between the plant and the grow light is possible, the normal beam is a better option.
More information about the Philips Horticulture LED solutions from Signify is available on the website.
For further information, please contact:
Global Marcom Manager Horticulture at Signify
Daniela Damoiseaux
Tel: +31 6 31 65 29 69
E-mail: daniela.damoiseaux@signify.com
About Signify
Signify (Euronext: LIGHT) is the global market leader in lighting for professionals and consumers and lighting for the Internet of Things. Our Philips products, Interact connected lighting systems and data-enabled services, deliver business value and transform life in homes, buildings, and public spaces. In 2019, we achieved sales of EUR 6.2 billion with approximately 37,000 employees in more than 70 countries. We unlock the extraordinary potential of light for better lives and a more sustainable world. We achieved CO2 neutrality by 2020 and have been on the Dow Jones Sustainability Index since our IPO in 2016. We were named Industry Leader in 2017, 2018 and 2019. Signify news can be found in the Newsroom, on Twitter, LinkedIn, and Instagram. Information for investors can be found on the Investor Relations page.
VIDEO: The Ohio State University Announces Ground-Breaking For The Controlled Environment Food Production Research Complex
This new, unique facility will support the needs of our faculty and students unlocking human potential for innovation
This new, unique facility will support the needs of our faculty and students unlocking human potential for innovation. This greenhouse of the future will be a place for collaborative research, sustainable food production, and distinguish Ohio State from other institutions. The CEFPRC will be located at the Waterman Agricultural and Natural Resources Laboratory.
This facility will provide technology and research that will impact all Ohioans and beyond.
Tagged Education Greenhouse Ohio State University Research Vertical Farming
Most Americans Have Roundup in Their Bodies. Researchers Say One Week of Eating Organic Can Help
Organic, pesticide-free eating is an important factor in health and is something consumers should remain conscious of when shopping.
Photo courtesy of Scott Warman, Unsplash.
One week of eating organic can dramatically reduce pesticide levels in the body, according to a recent study conducted by the Health Research Institute, Commonweal Institute, and Friends of the Earth.
The group of researchers tracked the pesticide levels of four families across the United States. They took measurements after six days on a non-organic diet and again after six days on an organic diet.
The study, and a companion study published last year, found 16 different kinds of pesticides and chemicals in every participant. But after six days of organic eating, these compounds decreased an average of 60.5 percent—and some as much as 95 percent. Glyphosate, the main ingredient in Roundup and the most used pesticide in the world, dropped an average of 70 percent.
A study by agricultural economist Charles Benbrook finds that the use of glyphosate has spiked 15-fold globally since genetically modified, “Roundup Ready” crops were introduced in 1996. The percentage of Americans with traceable levels of glyphosate in their bodies rose from 12 percent in 1972 to 70 percent by 2014, according to researchers at the University of California San Diego.
Glyphosate exposure has been associated with a wide range of health problems. Researchers have flagged glyphosate as a probable carcinogen, and the chemical has been linked to kidney disease, reproductive issues, DNA damage, hormone and digestion disruptions, fatty liver disease, and more.
The recent study poses organic eating as a straightforward way to avoid glyphosate. But the authors also recognize that organic food isn’t always accessible.
To improve the availability of organic foods in the United States, the team calls for top-down policy changes—like stricter regulations on pesticide use, more federal research into the effects of pesticides, and aid for farmers as they transition to organic farming.
“Our federal pesticide policy system is broken, and we need people shouting about that,” Dr. Kendra Klein, a co-author of the study and Senior Staff Scientist at Friends of the Earth, tells Food Tank. “Companies like Bayer, Syngenta, and Dow are spending millions lobbying, and they’re also spending tens of millions of dollars to shape the narrative and perpetuate myths, like the myth that we need pesticides to feed the world.”
Klein points out that just 1 percent of U.S. federal agricultural research dollars go towards ecological farming, and pesticide regulations are few and far between. In fact, the U.S. Environmental Protection Agency (EPA) has loosened some pesticide restrictions in recent years. Between 1993 and 2008, the EPA raised the threshold for glyphosate residues on oats from 0.1 ppm to 30 ppm.
Larry Bohlen, Chief Operating Officer at HRI Labs and another co-author of the study, also emphasizes a lack of resources for farmers who want to transition to organic farming. He explains that universities and government training programs have taught farmers how to use pesticides for decades. “If they placed models of successful organic farming side-by-side with the synthetic chemical models, farmers would have choices instead of just one option,” Bohlen tells Food Tank.
Stringent pesticide regulations might seem like a lofty goal in the U.S., says Klein, but change is already underway abroad. Earlier this year, the European Union announced plans to halve the use of “high risk” pesticides by 2030 and make at least 25 percent of farmland organic.
To spur change in the U.S., Bohlen urges consumers to vote with their wallets, if they’re able. “Each person’s purchase is a small vote that, when considered collectively, sends a signal back to the grocer and the farmer about what type of food is desired. It’s your purchase that has one of the biggest effects on land, farmer, and consumer health.”
Content like this article is only possible because of Food Tank members. Please join today and get exclusive member benefits at FoodTank.com/Join.
Meet The Green Man of Ludhiana Who Has Created Vertical Gardens Across City From Waste Plastic Bottles
A man has started turning plastic waste into vertical farms in order to recycle in a new way.
Aimed at reducing waste of plastic and also as an attempt to reduce air pollution, Mehra said under his instructions, the vertical gardens have come up in many places including schools, colleges, gurudwaras, churches, police stations, government offices and railway stations.
Using waste plastic, an IRS officer Rohit Mehra (in grey sweater) set up Vertical Gardens to tackle air pollution in Ludhiana. (Credit: ANI/Twitter)
In today's time when there is a huge need to recycle waste and reduce the use of plastic, Rohit Mehra, Additional Commissioner in the Income Tax Department, has shown an inspiring path to follow when he used 70 tonnes of discarded plastic bottles to act as planting pots for vertical gardens in Ludhiana.
Aimed at reducing waste of plastic and also as an attempt to reduce air pollution, Mehra said under his instructions, the vertical gardens have come up in many places including schools, colleges, gurudwaras, churches, police stations, government offices and railway stations.
Speaking to news agency ANI on Sunday, Mehra said, “Using at least 70 tonnes of waste plastic bottles as pots, we have set up more than 500 vertical gardens at public places.”
Speaking about what made him turn to this unique idea of using plastic, Mehra said he started thinking of the copious amount of plastic waste and pollution that plagues the cities when his child some 4 years ago, one fine day informed him that their school had declared holidays due to high air pollution. Mehra said he pondered how the situation has turned so bad that they cannot even breathe in fresh air and provide the same to their children. This made him take note of the worsening situation and he decided to do something about it.
Mehra, who is know as the Green Man of Ludhiana due to his conservation work at the trees, has also created 25 mini forests ranging between 500 sq feet to 4 acres in 2 years, along with the vertical gardens. To broaden his understanding of quick growing of trees, he studied ancient Indian texts like the Vrikshayurveda that talks about the science of growing plants and forest. He also stumbled across the Japanese technique of Miyawaki.
He added, “It is a cost-effective and space-efficient solution for urban greenery. The vertical gardens also save the environment as you reuse plastic wastes as pots. Thanks to drip irrigation, these gardens save 92 per cent water."
Mehra said that after the establishment of the vertical gardens, they had checked the air quality index (AQI) of the city by a scientist associated with the Punjab Agricultural University and found a 75 per cent reduction in air pollution, thus making their venture a success.
Start-Up Launches London’s First Delivery Service For Vertically-Farmed Eco-Friendly Greens
A London-based company is offering vertically-farmed, ultra fresh produce delivered straight to Londoners doors.
Crate To Plate Says All Its Greens Are Picked
Within 24-hours of Being Delivered To Your Door
Crate To Plate grow greens both vertically and horizontally, without soil, inside giant crates on the Isle of Dogs / Crate To Plate
A start-up is offering to deliver vertically-farmed vegetables to Londoners homes within 24 hours of harvesting in a first for the capital.
Crate to Plate, founded by former banker and scion of the supermarket dynasty, Sebastien Sainsbury, currently grows all its leafy greens inside three giant shipping containers on the Isle of Dogs.
The type of indoor farming the start-up uses has been tipped as the future of food production, and investors have spotted the trend.
The company, launched in London earlier this year, grows salad and herbs using hydroponics - which means seeds are grown year-round on vertical and horizontal racks without any soil or pesticides. The amount of water, light and “specially mixed” nutrients each kale or basil plant receives is carefully controlled.
(Crate To Plate staff include agriculture MA students / Crate To Plate)
The process uses around 95% less water than traditional farming, in a tiny space. In recent film A Life on Our Planet, David Attenborough recently warned of the critical importance of moving away from exhaustive farming practices to innovative solutions.
At the height of the November lockdown the team - which includes agriculture MA students - branched out into high-end “leafy veg box” deliveries spanning Zones 1-3. Each delivery is made on electric vehicle.
A £15 variety “farm to table” box will buy you 3 lettuce varieties, 3 bags of other leafy greens and 4 herbs - all harvested within 24-hours of arriving at your door.
Crate To Plate is now planning to expand around the capital. A second site is opening in Elephant & Castle in the new year, and the firms aims to have up to 15 “farms” by 2021. Each will produce up to six tonnes of fresh food per year.
Sainsbury, who previously founded the Hush Restaurant and organic baby food company Goodness Gracious, told the Standard he began exploring the business idea in 2015, after visiting a hydroponic farmer in Canada.
“I’m all about food wattage. One of the reasons I set up this business is for the environmental sustainability element of it. “Now technology has enabled us to move from growing on one row [as on the Canadian farm ] to growing both vertically and horizontally,” he said. Of the veg boxes, he said: “I did a bit of research and Londoners’ searches for ‘where does my food come from?’ increased by 40% in the pandemic.
“The pandemic was an opportunity to focus on home delivery. We’ve been sold out every week.”
“Everyone is talking about 15 minute cities now. Effectively that was what I was talking about - I want everyone to be able to get fresh leafy greens no more than a mile away from where they live.”
Critics of vertical farming have said it is just too expensive a method to realistically become the future of UK farming. But Sainsbury said the team is already working with farmers around the country to get them on board, with the aim of eventually expanding UK-wide.
Published by Dani Kliegerman for iGrow.News
After The Chaos of 2020, Will Indoor Farming Be In Our Future?
“Rather than growing out in an outdoor field, we’re growing up,” says Forward Greens CEO and Founder, Ken Kaneko. “We’re able to control the temperature, the humidity, the airflow, as well as the lighting,” he says
VANCOUVER, Wash. — The year 2020 has forced a number of disruptions to our daily lives, so what if we have more years like it in the future? How will we make sure our communities can survive by getting vital resources, like food?
The answer may be growing inside an old Hewlett Packard plant at the Vancouver Tech Campus in Washington.
Forward Greens is probably not what you picture when you think “farm”: vertical floor to ceiling stacks of planters filled with microgreens and baby greens, growing under LED lights
Forward Greens, Vancouver, Wash.
“Rather than growing out in an outdoor field, we’re growing up,” says Forward Greens CEO and Founder, Ken Kaneko. “We’re able to control the temperature, the humidity, the airflow, as well as the lighting,” he says.
From arugula to kale to broccoli, everything growing inside this urban, indoor farm wouldn’t be growing outside on a chilly November day in the Pacific Northwest.
From start to finish, the whole process of farming is essentially done in one room. In just a week or two, the greens are on their way to grocery stores in Portland, Vancouver, and Seattle.
Kaneko, who had worked for Intel and more recently, Apple, founded Forward Greens in 2017 after a trip to Japan. There, he stumbled upon his first vertical farm.
“I thought, ‘man, it would be great if I can bring this back to the Pacific Northwest and essentially do it better, cheaper, and more efficiently,'” said Kaneko.
Kaneko says Forward Greens never uses any pesticides, fungicides or herbicides and it uses 95% less water and 99% less land than traditional outdoor farming. But, he says, it uses a lot of energy to power the lights.
“Any engineering problem has a balance of cost, time, environmental impact, but the whole mission of this business is to balance those in a positive way towards the environment,” Kaneko said.
So could this be the farming of the future?
OSU Professor of Horticulture, Gail Langellotto, is pretty certain that it’s not. “In the near future, I can’t imagine a future where only agriculture is indoor agriculture,” she says, pointing to the high start-up costs, the higher cost of labor, and the expensive and taxing energy use.
She says traditional, outdoor farming will be difficult to replace because of the efficiency, precision and scale the industry has mastered and is constantly improving.
But Langellotto adds that if we have more years like 2020, with the pandemic and destructive wildfires on top of climate change, indoor farming will be an asset. She says urban farming is robust to disruptions in the local food system.
“If there are some supply and transport issues that delay or limit the amount of food that can be brought into urban areas from more rural, further out regions, then you already have an urban food production system in the proximity of where the majority of people live,” Langellotto said.
Kaneko is encouraged by the fact that urban farms can be a huge asset, saying, “we don’t know what’s going to happen with respect to the wildfires, the pandemic, the climate, so we’re able to provide local and sustainable food regardless of all those parameters.”
And that may be why Kaneko says demand for indoor farms is increasing. In fact, he’s expanding and doubling production at the Vancouver location in the next couple months. But he’s looking even further ahead to an even brighter future.
He hopes to put a Forward Greens in every metropolitan area, so we don’t fall to the fate of those HP printers that used to be built where his plants now grow.
KATU2 ABC Forward Greens
by Wesleigh Ogle, Thursday, December 3rd 2020
Published by Dani Kliegerman, iGrow News
Kalera To Open Hawaii’s Largest Vertical Farming Facility, Bringing Fresh, Locally-Grown Greens And Food Supply Chain Security To An Island That Imports 90% of Its Produce
The new facility will provide produce to one of the most remote population centers in the world as tourism begins to resume operation during COVID
The new facility will provide produce to one of the most remote population centers in the world as tourism begins to resume operation during COVID
December 22, 2020
ORLANDO, Fla., Dec. 22, 2020 (GLOBE NEWSWIRE) -- Tech-driven vertical farming company Kalera (Euronext Growth Oslo ticker KAL, Bloomberg: KSLLF), today announced it will open a facility in Honolulu, Hawaii in 2021. Kalera’s Hawaiian location will be the Company’s eighth facility announced, making it one of the fastest-growing vertical farming companies in the United States. It will also be the largest vertical farming operation in the state, providing approximately 60 jobs to the local community upon opening.
The news of this facility comes on the heels of a string of exciting updates from Kalera, including the announcement of upcoming facilities in Atlanta, Houston, Denver, Seattle, and Columbus; the addition of two new members to the Board of Directors, including Red Lobster CEO, Kim Lopdrup; and the completion of over $150 million in fundraising this year.
With millions of heads of lettuce to be grown per year, Kalera’s Honolulu facility will provide a rare and much needed local source of fresh, non-GMO, clean, living lettuces and microgreens to retailers, restaurants and other customers. 90% of Hawaii’s greens are currently grown on the mainland United States and shipped into the state – an expensive 2,500-mile journey that can take over 10 days and require many touchpoints and opportunities for contamination. Kalera’s location within city limits will shorten travel time from days and weeks to hours, preserving nutrients, freshness, and flavor.
“The pandemic has really shown us how important sustainability is to Hawaii’s future… One of my goals for a sustainable Hawaii is to double local food production and a bright spot of the pandemic is that more families are consuming locally produced food and attempting to grow their own food. Every little bit helps as we try to work towards our sustainability goals,” said David Ige, Governor of Hawaii. “I believe a mix of traditional farming and new technologies is the wave of the future for agriculture in Hawaii. Innovations like vertical farming help farmers be more productive while using less resources – especially water. That’s why it’s exciting that a company like Kalera is making an investment to bring their operations to Hawaii, where we are sensitive to reducing our impact on the environment. I think technologies such as vertical farming and hydroponics also have appeal to younger people and could help attract more young farmers to the field.”
Kalera’s hydroponic systems allow their lettuce to grow while consuming 95% less water than field farmed lettuces and while eliminating the need for chemical pesticide or fertilizer use. Paired with shorter shipping times, Kalera’s operations are more eco-friendly than traditional farming. Additionally, Kalera’s efficient growing methods produce yields that are 300-400 times that of traditional farming, allowing the company to maintain conventional pricing in supermarkets.
“In addition to providing a bounty of fresh, affordable, and delicious lettuces and microgreens to restaurants, cruise lines, resorts, hotels, and retailers, Kalera’s Honolulu location will increase food security and resilience on the island,” said Daniel Malechuk, Chief Executive Officer for Kalera. “With price inflation impacting almost all produce that reaches Hawaii due to prolonged shipping times, Kalera’s affordably priced products will increase access to a stable supply of healthy food for Hawaiian citizens and tourists.”
Distributors anticipate locally grown greens will improve their business.
“Vertical farming is a great way to provide our customers with the freshest quality products grown in a food-safe and sustainable manner while supporting local farming,” said Dwight Otani, founder, and president of D. Otani Produce, Hawaii's largest wholesaler, providing local hotels, restaurants, business institutions and retailers with the highest quality produce.
ABOUT KALERA
Kalera is a technology-driven vertical farming company with unique growing methods combining optimized nutrients and light recipes, precise environmental controls, and cleanroom standards to produce safe, highly nutritious, pesticide-free, non-GMO vegetables with consistently high quality and longer shelf life year-round. The company’s high-yield, automated, data-driven hydroponic production facilities have been designed for rapid rollout with industry-leading payback times to grow vegetables faster, cleaner, at a lower cost, and with less environmental impact.
Media Contact: Molly Antos
Phone: (847) 848-2090
Email: molly@dadascope.com
Vera Vertical Farming Technology Introduced in Finland’s Largest Retail Group
Finland’s largest retailer is now carrying produce farmed in vertical-farming centers to provide ultra-fresh produce year round.
Netled And Pirkanmaan Osuuskauppa Sign A New Long-Term Cooperation Agreement
In the photo: Ville Jylhä, COO of Pirkanmaan Osuuskauppa
Netled has entered into a significant long-term cooperation agreement with Pirkanmaan Osuuskauppa, a regional operator of S-Group, the largest retail chain in Finland.
Netled’s Vera Instore Premium Growing Cabinets, offering a range of herbs and salads, will now be a regular feature in Prisma retail stores in the Pirkanmaa area. Herbs and some of the leafy greens are grown in-store in the cabinets, and are harvested directly off the shelf. The growing conditions are fully automated and controlled remotely.
The newly opened Prisma Pirkkala is Finland’s first hypermarket to launch the new Vera Instore Cabinets. In addition, Netled will deliver to the hypermarket salads and herbs grown on its own vertical farm nearby, thereby allowing customers to get same-day harvested herbs and salads all year round.
”With this newly formed collaboration we can offer consumers fresh, ultra-locally produced products and at the same time introduce them to vertical farming as a method of ecological, urban farming”, says Ville Jylhä, COO of Pirkanmaan Osuuskauppa.
S-Group is a customer-owned Finnish network of companies in the retail and service sectors, with more than 1 800 outlets in Finland. The group offers services in areas such as, supermarket trade, department store, and speciality store trade. As the largest retail group in Finland, S-Group’s main focus is also on sustainable food and innovative ways it can offer healthy and responsibly produced food to its customers.
Netled Ltd. is Finland’s leading provider of turn-key vertical farming systems and innovative greenhouse lighting solutions.
”As the leading vertical farming technology provider in Finland, we have developed an extensive range of products for all segments of vertical farming. Instore growing systems are a rapid-growth segment, and our cutting-edge Vera technology puts us at the forefront of the instore space”, says Niko Kivioja, CEO of Netled Ltd.
“The agreement with Pirkanmaan Osuuskauppa is just the latest proof of concept, and is also a clear signal to potential customers, investors and other global partners that Vera technology is a game changer.”
18th December 2020 by johannak
More information:
Niko Kivioja
CEO, Netled Ltd
+358 50 360 8121
Robert Brooks, Investor Relations and Communications Manager
+358 50 484 0003
FDA Closes Investigations Into 2 E. coli Outbreaks; No Source Found
The Food and Drug Administration on Dec. 18 reported the investigations were completed, and the Centers for Disease Control and Prevention announced two of the three outbreaks were over
By CHRIS KOGER | December 18, 2020
Investigations into two of three E. coli outbreaks from this fall have been completed, and although the traceback process led authorities to farms, samples did not confirm link any particular food or source in either outbreak.
The Food and Drug Administration on Dec. 18 reported the investigations were completed, and the Centers for Disease Control and Prevention announced two of the three outbreaks were over. The FDA refers to the “Outbreak Unknown Source” 1, 2 and 3. Investigations into outbreaks 1 and 3 are over.
Outbreak 1
The CDC reported 32 people in 12 states became sick in Outbreak Unknown Source 1. The strain of E. coli identified in the investigation is genetically similar to a strain linked to a spring 2018 outbreak from romaine lettuce, according to the FDA. No food source was identified in the recent outbreak, however.
“FDA and state partners also conducted on-site inspections on farms of interest, though information collected in these inspections did not link these farms to the outbreak,” according to the FDA’s update.
Outbreak 3
The CDC reported 18 people in 9 states became sick in Outbreak Unknown Source 3. The FDA identified several potential food sources during interviews with people who became sick, but no farm was identified as a common source.
The FDA and state agencies conducted investigations at “farms of interest,” but information and samples collected did not lead to a source of the E. coli.
“The investigation of a farm does not mean that the farm is linked to an outbreak,” according to the FDA notice. “The results of an investigation into a farm may well lead to that firm being ruled out of the investigation.”
Outbreak 2
The investigation into Outbreak Unknown Source 2 is ongoing, according to the FDA. The CDC reports 39 cases, according to the CDC’s last update, which was Nov. 23. At that time, 22 of the people who became sick had been interviewed, with 16 reporting they ate spinach and 15 saying they ate romaine.
Lead photo: (Courtesy Food and Drug Administration)
Kalera To Open Vertical Farming Facility In Ohio, Bringing Fresh, Locally-Grown Greens To The Midwest
With this news, Kalera enters the Midwest, giving the region’s grocers, restaurants, theme parks, airports, schools, and hospitals reliable access to clean, safe, nutritious, price-stable, long-lasting vertically-grown greens. The facility will generate approximately 65 jobs
12/21/2020
The New Facility Is The Seventh To Be Announced
by Kalera, Marking Its Nationwide Presence
December 21, 2020
ORLANDO, Fla., Dec. 21, 2020 (GLOBE NEWSWIRE) -- Kalera (Euronext Growth Oslo ticker KAL, Bloomberg: KSLLF), one of the fastest-growing vertical farming companies in the United States, today announced it will begin construction on a facility in the Columbus, Ohio area, slated to open in 2021. With this news, Kalera enters the Midwest, giving the region’s grocers, restaurants, theme parks, airports, schools, and hospitals reliable access to clean, safe, nutritious, price-stable, long-lasting vertically-grown greens. The facility will generate approximately 65 jobs.
The announcement of the Columbus facility comes on the heels of a series of announcements made by Kalera, including new facilities to be built in Atlanta, Houston, Denver, and Seattle; the addition of two new members to the Board of Directors, including the CEO of Red Lobster, Kim Lopdrup; and the completion of over $150 million in fundraising this year.
“With most of the nation’s greens grown on the West Coast, we’re thrilled to be able to provide Midwest customers year-round access to hyper-local produce. With our centrally located farm facility, we are able to reduce travel times from days and weeks to mere hours,” said Daniel Malechuk, Kalera CEO. “Many regions across the country, including the Midwest, typically only have access to produce that is bred to endure long shipping times, sacrificing flavor and freshness for durability. We’re proud and excited for our Midwest customers to experience the enhanced flavor and nutrition profile of greens that are picked and delivered at the height of freshness.”
As of this announcement, Kalera is slated to have seven commercial growing facilities open and operating across the US by the end of next year. Kalera currently operates two growing facilities in Orlando and is constructing facilities in Atlanta, Houston, Seattle, and Denver which will also open in 2021.
Kalera utilizes cleanroom technology and processes to eliminate the use of chemicals and remove exposure to pathogens. Kalera's plants grow while consuming 95% less water compared to field farming.
"We welcome Kalera’s plans for its first investment in Ohio, which brings an innovative hydroponic agriculture operation and 65 new jobs to the Columbus Region,” said JobsOhio President and CEO J.P. Nauseef. “Demand for Kalera’s non-GMO produce has soared, and Ohio talent at this advanced facility will utilize the latest in vertical hydroponic farming technology to expand its growing U.S. customer base.”
City officials anticipate Kalera's operations will provide many benefits for Columbus residents.
“We’re happy to welcome Kalera to Columbus – a high-growth company doing really cutting edge work with sustainably sourced and locally grown produce,” said City of Columbus Mayor Andrew J. Ginther. “Columbus continues to be a location company choose to create, test, and launch innovative technologies and businesses.”
About Kalera
Kalera is a technology-driven vertical farming company with unique growing methods combining optimized nutrients and light recipes, precise environmental controls, and cleanroom standards to produce safe, highly nutritious, pesticide-free, non-GMO vegetables with consistently high quality and longer shelf life year-round. The company’s high-yield, automated, data-driven hydroponic production facilities have been designed for rapid rollout with industry-leading payback times to grow vegetables faster, cleaner, at a lower cost, and with less environmental impact.
ARGENTINA: Substrate Cultivation And Hydroponics: A Technology on The Rise
“It was found that with hydroponics, productivity and profitability are increased between 30 and 50%, due to the greater efficiency in the use of the surface and natural resources, and it reduces the use of agrochemicals”, Analía Puerta, coordinator National of the “Tierra Sana” Project, carried out by INTA together with UNIDO (United Nations Organization for Industrial Development), within the framework of the Montreal Protocol
INTA, together with national universities, producers, and companies, promotes this production system that has grown in the last 5 years as an efficient and sustainable alternative. During 2021, the institution will be part of the organization of the Virtual International Symposium that will bring together the main national and international referents on the subject.
The cultivation in substrate and hydroponics consists of the production of vegetables without the use of the soil, for this reason, they are also called "cultivation systems without soil". When the roots develop in water it is called "hydroponics" and, when they do so in a solid medium, different from the soil, "substrate cultivation", using a great diversity of substrates and/or mixtures of them.
It is a production system that arises from the high degradation of soils, as a consequence of unsustainable management and inadequate practices, which is on the rise among producers as an alternative. This will be one of the topics that will be addressed on March 30 and April 6 and 8, 2021 in virtual form at the International Symposium on Substrate Culture and Hydroponics.
“It was found that with hydroponics, productivity and profitability are increased between 30 and 50%, due to the greater efficiency in the use of the surface and natural resources, and it reduces the use of agrochemicals”, Analía Puerta, coordinator National of the “Tierra Sana” Project, carried out by INTA together with UNIDO (United Nations Organization for Industrial Development), within the framework of the Montreal Protocol.
"In Argentina, the system began to be implemented more than 20 years ago in the ornamental sector, and it grew considerably in the last 5 years, extending to other sectors such as horticulture, citrus, and even for the production of green forage", underlined Puerta.
Along these lines, the most important productions in the hydroponic system correspond to leafy vegetables, such as lettuce, arugula and chard and, in the substrate system, the cultivation of tomatoes, strawberries and, to a lesser extent, peppers stands out.
In addition, the coordinator highlighted, “the well-being of workers is increased, since it improves the ergonomics of all operations, especially those of harvest, and the borders of the productive regions are expanded, allowing production in areas not suitable for cultivation, either due to health problems or the high real estate value of the surface ”.
Another benefit of these techniques is to allow access to fresh vegetables in specific situations, such as in places where the soil is not suitable for production, or directly where there is no soil, such as patios, terraces, landfills, contributing additionally to the promotion of short circuits of production and commercialization of vegetables.
According to Puerta, "it is important to highlight that this production alternative can be adapted to different production levels, from family farming to small, medium and large companies."
Puerta: "In Argentina, the system began to be implemented more than 20 years ago in the ornamental sector, and has grown considerably in the last 5 years".
This production system has established itself as a technology of recognized efficiency and massive implementation in developed and highly technical countries, such as Japan, the Netherlands, Spain and the United States.
According to data from 2015, the world area of crops under this production system (hydroponics and substrate) reaches 40 thousand hectares, with the Netherlands being the country with the largest covered area, with 5 thousand hectares, Spain with 2,500, Belgium and the United Kingdom with 2,000, Japan 1,500, as well as China, France 1,000, Israel 750, Canada 500 and the United States 250 hectares.
"Currently, there are productions of this type in all provinces of the country and, not only in traditional production areas, but there is a massive growth in urban areas," said the coordinator of "Tierra Sana". Along these lines, he added: "With this system the producer becomes independent of the quality of the soil and when the production is carried out undercover, the environmental conditions can be modified, especially the temperature, light intensity, and humidity of the environment".
Nowadays, there are commercial and self-consumption productions from the north to the south of the country, including promising experiences for the supply in the Argentine Antarctica. "In this sense, INTA has been contributing to the consolidation of this production alternative, through numerous research and extension activities carried out by agents from the different units of the country," said Puerta.
To date, there have been countless workshops and training courses and demonstration plots of strawberries and vegetables have been installed in the main productive areas of the country, promoted by the “Tierra Sana” project, in cooperation with units referring to the subject, and together to companies, producers and universities.
On the other hand, it should be noted that the development of these activities is part of the sustainable development goals ("SDG") outlined by current public policies according to the guidelines of the United Nations (UN) and being prioritized on the agenda. 2020-2030.
It is a production system that arises from the high degradation of soils, as a consequence of unsustainable management and inadequate practices, which is on the rise among producers as an alternative.
International Symposium
Currently, INTA is organizing an International Symposium on Substrate Culture and Hydroponics together with 5 universities in the country (UBA, UCC, UNLu, UNLP, UNNOBA), within the framework of the 41st Argentine Congress of Horticulture (ASAHO).
The event will take place on March 30 and April 6 and 8, 2021 in virtual form. It will have the participation of national and international referents who will speak about the latest advances in the field and exchange knowledge with the participants, productions from Argentina and other countries will be visited through virtual tours and there will also be a space for the presentation of scientific and Of disclosure.
Their reception is already open and is until December 31st. There are different registration modalities in order to offer a wide range of possibilities to participants.
"Through all these activities, it is hoped to be able to contribute to the consolidation of a scientific, technical and productive network that includes actors from the public and private sectors around the production of food in an efficient and sustainable way", concluded Puerta.
4 Young Visionaries Built A Thriving Business
Recently, in one of our most popular webinars of all time, Wihelmsson fired us up with Ljusgårda’s amazing story – building a thriving modern farm in what was once a factory, by “replacing the tractor with lights and the shovel with an iPad.”
17-12-2020
It all began in 2017 when three friends, Magnus Crommert, Cristoffer Barath and Erik Lundgren decided to try modern indoor farming. Our own Plant & Light Expert, Ida Fällström, remembers when Magnus visited our Göteborg office, introduced us to his team’s vision of modern farming, and left with an ELIXIA LED grow light under his arm. With that LED grow light, he started to conduct tests in his garage while the rest of the business took form, including bringing on a young business visionary, Andreas Wihelmsson, as partner and CEO. Fast forward to today, and their operation has grown to become Ljusgårda AB, a successful and sustainable climate certified farm in Tibro, Sweden.
Recently, in one of our most popular webinars of all time, Wihelmsson fired us up with Ljusgårda’s amazing story – building a thriving modern farm in what was once a factory, by “replacing the tractor with lights and the shovel with an iPad.” An enthusiastic evangelist for modern vertical farming, Wihelmsson explained, “We took the concept of farming outdoors and brought it indoors, creating a controlled ecosystem where we can grow under optimal conditions year-round. We have a facility here of 7,000 square meters. A year from now, we will have outgrown this facility and we will begin building the next one.” He continued, “If someone would have told me years ago that I would be growing salad for a living, I would have thought they were joking. Yet today thousands of families are eating our salad every week.”
What are the secrets to Ljusgårda’s overwhelming success? Here are 5 key things we learned in our webinar about starting a successful vertical farm:
5 Habits of a Highly Successful Vertical Farm
1. Quality Comes First
Wihelmsson commented that “More than 70% of all the fruits and vegetables Sweden eats are imported from other countries.” This leads not only to higher emissions but it also negatively affects plant quality and nutrients due to the transportation time. Because indoor vertical farming enables Ljusgårda to grow locally, they always get their products to store within 24 hours of harvest to retain quality and nutrition.
2. Give Your Customers What They Really Want (Not What You Think They Want)
Ljusgårda produces salad greens, including lettuce and arugula, for Swedish tables year-round. Wihelmsson noted, “When it comes to making a produce buying decision in Sweden, 7 out of 10 people say that one of the most important factors is that it's Swedish. Sustainability and price are also very important. We provide a great tasting Swedish product that is sustainable, and we sell it at roughly the same price as imported products.”
When it comes to giving customers what they want on an individual crop level, Ljusgårda is able to use LED grow lighting and intelligent controls to influence every phase of plant growth, from biomass development to finish and flavour. Wihelmsson commented, “One very interesting experience we had was with our rocket salad, the first product we launched. I remember our initial tryouts and it tasted terrible.” He laughed, “We were by far growing the worst tasting rocket salad in the world, but we became better. We developed a good product with a robust peppery flavour, and we went to grocery stores for people to try it. Their polite reactions were that it was okay, so we knew that we had it dead wrong. We progressed by altering our rocket salad’s flavour through lighting control and conducting countless in-house and in-store taste tests.”
Wihelmsson continued, “We realized that Swedes didn’t want a traditional strong rocket salad. They wanted a mild one. We have a term in Sweden, Lagom, which relates to balance – not too little, not too much. We ended up producing a milder rocket and outsold all other products in that store.” He concluded, “You don't always know what the customer actually wants until you test in person and can see their reaction. If in the future customers demand a spicier rocket salad, we can achieve that with our flexible LED lighting. We have the ability to control taste, nutrition, quality, colour, biomass, almost everything – because light has a huge effect on the plants. You just first need to figure out what your customer wants in their food.”
3. Control Your Light to Optimize Your Production
An intelligent LED lighting strategy can help you achieve your crop goals. We have worked with Ljusgårda to accelerate their production of arugula and reduce their production time by 19%, by making adjustments to their lighting strategies. Wihelmsson commented, “For us, light control is very important to our production. If we look at our collaboration with Heliospectra, we chose to go with ELIXIA LEDs because we needed maximum flexibility. The other reason was their positive effect on reducing power consumption.”
Ljusgårda has also found that flexible LEDs can help them control risk and even save crops. Wihelmsson noted, “Now that we have been running this farm for a few years, we’ve come to see that our flexible lights can actually be used to compensate for human errors, or things like the water tank failing or other issues. In such cases we have been able to change the spectrum to recovery lighting. Our LED lighting has meant a lot to us and the flexibility has been extremely important.”
4. Automate Step by Step (and Plan Several Steps Ahead)
Wihelmsson talked about the company’s approach to automation, “We had to redesign the system to be able to get it automated step by step and growing-wise it's been working. For us most steps in production will be semi-automated, leveraging a machine but with human beings still involved, while other steps will be fully automated.”
He cautioned, “You need to do the math and see where automation makes economic sense for you. Our approach is to look at what takes up the most labour, what is most costly in the whole economic calculation, and address it. We also run the numbers to plan ahead. For example, we are preparing some processes for automation, but we won't automate them until production volumes hit certain critical numbers. Overall, it’s best to take it one step at a time, starting with a semi-automated approach.”
5. Keep it Simple and Learn from Others
Rather than focusing on the high-tech aspects of their operation, Ljusgårda found that their consumers responded better to a simpler, more straightforward message. Wihelmsson commented, “We know that our consumers want local produce, and so it says three times on the bag that our salad is from Sweden. We keep our messaging and packaging simple, ensuring people know that we are passionate about growing great tasting, nutritious, and sustainable food that they can eat in good conscience year-round. This simple, positive message has helped put our bag salad in the top three in each and every store, and it’s even number one in several of them.”
If you are interested in starting your own vertical farming operation or taking your farm to the next level, Wihelmsson suggested that you try to learn from others who have succeeded. He commented, “We have something we like to call common farmer sense. It's a direct translation from Swedish, and it basically consists of us questioning all the solutions that are out there and always telling ourselves not to reinvent the wheel. See if any industry or any other grower has already taken an approach you want to try. Take a look at it, learn from it, and then start growing from there.”
Watch the entire webinar here.
Source and Photo Courtesy of Agritech Tomorrow
PODCAST: Charlie McKenzie - CropWalk
He is the Director of Partnership and Co-founder of CropWalk, a pest, disease, and production insights provider
Joe Swartz & Nick Greens | 12/18/2020
Charlie is a father of two, husband, horticulturist, biocontrol advisor, friend, and Georgia Bulldawg.
He is the Director of Partnership and Co-founder of CropWalk, a pest, disease, and production insights provider.