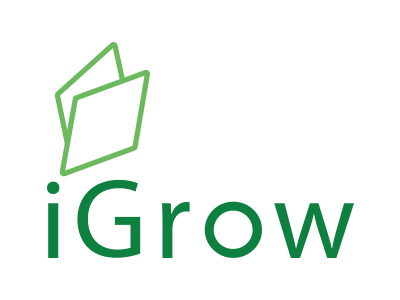
Welcome to iGrow News, Your Source for the World of Indoor Vertical Farming
How This Vertical Farm Grows 80,000 Pounds of Produce per Week
To some, the pristine growing conditions and perceived mechanical interference of a vertical farm can seem unnatural, but at Bowery Farming “interference” is actually not the goal at all. “We don’t really think about how people are involved in the growing process, but how to take people out of the growing process”
Bowery Farming uses technology to prioritize accessibility and sustainability in their produce growing operations
To some, the pristine growing conditions and perceived mechanical interference of a vertical farm can seem unnatural, but at Bowery Farming “interference” is actually not the goal at all. “We don’t really think about how people are involved in the growing process, but how to take people out of the growing process” says chief science officer Henry Sztul. “Our goal is actually to have as few people walking around our plants as possible.”
Bowery Farming is a network of vertical farms working to reengineer the growing process. Using a system of light and watering technology, Bowery is able to use 95 percent less water than a traditional outdoor farm, zero pesticides and chemicals, and grow food that tastes as good as anyone else’s.
Bowery Farming uses vertical farm-specific seeds that are optimized for flavor instead of insect resistance and durability. Seeds are mechanically pressed into trays of soil, and sent out into growing positions, or racks within the building that have their own lighting and watering systems. Each tray gets its own QR code so that they can be monitored and assigned a customized plan for water and light until they’re ready to be harvested.
Irving Fain, Bowery Farming’s founder and CEO contemplates the prediction from the United Nations that 70 to 80 percent of the world’s population will be living in and around cities in the next 30 years. “Figuring out ‘how do you feed and how do you provide fresh food to urban environments both more efficiently as well as more sustainably?’ is a very important question today, and an even more important question in the years to come.”
In Malahide, Two Friends Raise A Vertical Farm
When salesman Jack Hussey finishes his work day, he closes the laptop, leaves his home in Malahide and walks 10 minutes down the road. At the bottom of his friend’s farm sits an outhouse with a coldroom which now hosts his side business, Upfarm. A farm that goes upwards
Image from: Dublin Inquirer
When salesman Jack Hussey finishes his work day, he closes the laptop, leaves his home in Malahide and walks 10 minutes down the road. At the bottom of his friend’s farm sits an outhouse with a coldroom which now hosts his side business, Upfarm. A farm that goes upwards.
Imagine a shelf rack, says Hussey. “We’ve kitted the roofs of each shelf with an LED grow light. It’s to replicate the sunlight basically.”
A photo of the farm shows purple light beaming down on thick heads of lemongrass and basil, stacked on shelves. Yields from vertical farming are far more efficient than in-the-ground farming, Hussey said, on the phone last Friday.
He likens it to real estate. “You can have houses that are populated side by side or you can start going upwards with apartments.”
From Podcast to Table
Hussey always had an interest in food, he says. Last year he and a school friend, Bill Abbott, began to look into urban farming.
“But we were saying, is farming in the ground actually the best route to go?” Hussey says.
It’s labour intensive, which didn’t suit the two guys, who work other full-time jobs. Then, in March 2020, Hussey heard a podcast with American urban farmer Curtis Stone. He had an urban farm where he was using a spin-farming method, says Hussey. “It’s what they call it. You rotate crops out of the ground in a much more efficient way.”
“Essentially he was able to capitalise on a third acre of land. He was able to take in 80k a year,” he says.
Hussey was inspired by that, by somebody making the most of a small bit of land. So in June last year, in the middle of a pandemic and juggling working from home, Hussey and Abbot set about doing the same, albeit with a different model, and launched their vertical farm.
Image from: Farmony
How It Works
Farmony, which specialises in tech for vertical farming, sold Upfarm with the tools to get up and running – shelves, special LED lighting, a watering system and humidifiers. It is the ideal conditions for growing produce, says Framony co-founder John Paul Prior. Nutrients, hours of light, humidity and temperature are controlled in vertical farming, Prior says.
But Farmony is also a data company, Prior says. “So we capture data at all stages of the growing cycle. And we feed that back to the grower.”
This helps the grower to establish the optimum conditions, he says. “That’s not just in terms of plant growth, that’s in terms of workflow management.”
The size of an operation can be the small coldroom in Malahide that uses one Farmony module, and produces microgreens and wheatgrass for sale. Or it can be like a farm in Tipperary with 60 modules, he says. A module is 1 metre wide, 1.3 metres long and 2.5 metres tall, Prior says. Hussey says it is labour-intensive looking after a vertical farm module.
After work last Thursday, he and his dad replanted his microgreen crops into 30 different trays. “It took about two hours,” he says.
What Is the Benefit?
“So as long as you can control your temperature, your humidity, and your nutrient levels in the water, you can basically grow all year round,” says Prior. Vertical farming also means better conditions for workers, Prior says.
“If you’re working in a controlled environment, like a vertical farm, you’re working in a clean environment,” Prior says.
“You work between 18 to 22 degrees. There’s no harsh frost. There’s no extreme cold winters, equally there’s no burning-hot summers.,” says Prior.
The crop is consistent too, says Prior, thanks to the controlled environment.
“Let’s say I’m someone who loves basil and who makes a lot of pesto at home,” he says.
Getting basil of consistent quality from the supermarket can be difficult when it comes from different countries, or may have been sitting on a shelf for days after travelling thousands of miles, he says.
Image from: Farmony
Why Is this Important?
Soil quality is dropping, Hussey says. “What does that mean for outdoor growing?”
The answer, Hussey says, is vertical farming. It uses mineral-rich water so it doesn’t rely on nutrients from the ground, Hussey says.
Says Prior: “Vertical farming uses about 10 percent of the water of traditional farming.”
Prior says it takes less energy to get food from a nearby vertical farm than to ship it from afar. It was not always the case until a breakthrough in another industry, he says.
“Billions of dollars have been invested in the cannabis industry globally. It’s meant that the investment in grow-lighting technology has been huge,” he says.
“As a result, the price, the efficiency and most importantly, the energy efficiency of the lighting is really amazing” he says.
Says Hussey: “It’s not easy work but it is nice work. It’s good work.”
Fifth Season Takes Vertical Farming to a Whole New Level
Fifth Season’s verdant baby spinach screams farm fresh even though it’s grown nowhere near traditional farmland. The sweet and slightly crunchy greens are grown in a Braddock warehouse on racks stacked 30 feet high. Located just a stone’s throw from U.S. Steel’s Mon Valley Works Edgar Thomson Plant, it is urban farming at its core
Image from: Pittsburgh Post-Gazzette
Fifth Season’s verdant baby spinach screams farm fresh even though it’s grown nowhere near traditional farmland. The sweet and slightly crunchy greens are grown in a Braddock warehouse on racks stacked 30 feet high. Located just a stone’s throw from U.S. Steel’s Mon Valley Works Edgar Thomson Plant, it is urban farming at its core.
What makes the vertical farming operation especially unique is that it is automated and robots call the shots. About 40 to 60 machines are involved in every step of the life of the spinach and other leafy greens, from planting the seed to providing nutrients to the final packing.
Fifth Season does employ local “farm workers” to assist the robots in seeding, harvesting, packaging, quality assurance and control using computer software, but there is no human touch involved through it all.
“The first time someone ever touches the spinach leaf with a finger is when the package is opened,” says Grant Vandenbussche, chief category officer.
Co-founded by brothers Austin and Brac Webb and Austin Lawrence, Fifth Season started a year ago. Within months it was rolling out its baby spinach, leafy greens and salad kits.
“We wanted a name that represents what we are doing,” says Austin Webb, 32, who also is the CEO. “It is a call to the fact we have created an entirely new season. It is 24/7, 365 with the technology we have built.”
None of them planned to become modern farmers, says the Carnegie Mellon University grad, but they turned to vertical farming because it was an efficient, economically sustainable way to solve land and water woes.
Image from: thespoon.tech
‘Fields’ of Greens
Fifth Season grows an equivalent production of 200 acres in 25,000 square feet of grow space. Its “fields” are stacked on top of one another in vertical shelves. When you add up all that surface area of grow space, it is more like 126,000 square feet.
“We also quickly turn crops at the farm,” Mr. Vandenbussche says.
While spinach takes about 40 days to grow outdoors and can be harvested only twice during its peak season, it takes the crop only three or four weeks to grow in the controlled environment and is harvested 19 times. Once the plants are harvested, a new cycle of reseeding begins with fresh media, seeds and nutrients.
“That’s why we get so much more productivity,” he says. “We are immediately reseeding our ‘land.’”
This controlled environment yields quality produce because it is always peak season at Fifth Season, says Chris Cerveny, who heads the Grow R&D division. Greens are grown in the same conditions year-round, getting the exact amount of nutrients and water they need. Because pests and airborne toxins also are kept at bay, crops can be produced without pesticides.
All that TLC comes through in the slightly curled baby spinach, which is sweet and not grassy. The leaf doesn’t wilt or get slimy or lose its slight crunch even after two weeks of refrigeration.
A lot of thought was given even for the curl, which gives the spinach a stronger volume, making it look full and bountiful. The curl also makes the spinach more forkable unlike its flat-leaf counterpart that is hard to stab on a plate.
Other leafy greens such as kale, mustard, Chinese cabbage, green tatsoi and purple pac choi are featured in two blends — Bridge City and Three Rivers. Fifth Season plans to roll out its Romaine lettuce in spring.
The greens also are found in four types of salad kits — Sweet Grains (blended greens, quinoa, chickpeas, corn, feta and poppy seed dressing), Crunchy Sesame (blended greens, farro, sesame sticks, dried cranberries and ginger-mandarin dressing), Toasted Tuscan (spinach, lentils, sun-dried tomatoes, bagel chips and vinaigrette), and Spiced Southwest (blended greens, black beans, pepitas, cotija cheese, corn-salsa sticks and chipotle ranch dressing) — which are available online and in Giant Eagle stores. A fifth salad kit is in the works and is being called “a shakeup of one of the most classic salads.”
While machines are a big part of what Fifth Season does, it seeks to keep human connection alive. It recently launched a recipe blog for those who have an appetite for cooking and writing, The Green Room is devoted to cataloging personal memories, dream meals and recipes via short stories.
Fifth Season also has partnered with the Penguins and is providing greens for the team’s pregame meals for the 2020-21 season.
“We want people in Pittsburgh to be able to eat the exact same delicious blend of greens that Sidney Crosby and company are eating,” Mr. Webb says. “We want people to know that there’s a new way to grow food and to eat and experience it.”
Image from: Next Pittsburgh
It’s All Under Control
Everything from seeding to packaging is done in four rooms. The process starts in the seeding and processing room, where seeds and growing media are placed inside black planter-like boxes called inserts. Each has a unique code that’s traced by a software system. The inserts go on white trays that pass through a photo station, feeding information to the computer system, and then glide into the bio dome.
There are two rooms in the bio dome, each with a grow space of 12,500 square feet. They’re lit up with a pinkish-purplish glow from high-efficiency LED light bulbs that mimic the different seasons of the year.
“They are positioned over the plants at different heights depending on stage of growth,” Mr. Cerveny says. “This is partly how we can provide consistently ideal growing conditions.”
As the plants grow, they are moved by a robot to optimize their growth cycle. Full-grown crops are transferred to the harvesting room by another robot.
“Harvesting is where it becomes like a Willy Wonka factory,” Mr. Vandenbussche says.
Long rows of trays filled with tiny plants are sent on a conveyor system to a station where workers inspect them for quality with surgical tools. After inspection, the plants are harvested by a robot and then immediately ride up a tall conveyor to be packaged and sealed in a 34- to 36-degree room so they remain fresh.
“Every crop we grow gets evaluated for maximum flavor, volume, crunch and color,” he says.
The plants’ intense, dark color is controlled by LED light bulbs, which are dialed up or down to get the correct hue. Although they never see the sun, the greens don’t get into a funk as humans might.
“What humans see in terms of light and how chlorophyll responds during photosynthesis are two different things,” Mr. Cerveny says. “Plants really only need red and blue light to grow effectively. We include some additional colors to help bring out other quality aspects of our crops, but providing the full sunlight spectrum is effectively a waste of energy, especially indoors.
“To the human eye, it looks like the plants live in a land of purple and pink lights, but they are perfectly happy there.”
Even though the environment is controlled and the software system is constantly updated, no two plants are exactly the same. Some fight for light more than others. Some might fail the quality control test and end up in a compost waste facility if their flavor is off or their color is not right.
“That is what is so amazing. We have more control than any other farmer, and yet we have limitations. Every seed is different,” Mr. Vandenbussche says. “They are plants. They are real living organisms.”
Agritecture Partners With Harvest Returns Crowdfunding Platform To Modernize Urban Agriculture Financing
The two companies will work together to accelerate the urban farming and controlled environment agriculture (CEA) industry across the country by offering new entrepreneurs a more accessible way to raise capital. This type of farming can reduce the environmental impact of the food system and increase local food security
Image from: Harvest Returns
Fort Worth, Texas – Agritecture, LLC, an urban farming consulting and digital services firm, announced it has partnered with Harvest Returns, an agriculture investing platform.
The two companies will work together to accelerate the urban farming and controlled environment agriculture (CEA) industry across the country by offering new entrepreneurs a more accessible way to raise capital. This type of farming can reduce the environmental impact of the food system and increase local food security.
“The COVID-19 pandemic has revealed the fragility of centralized food production,” said Chris Rawley, CEO of Harvest Returns. “Developing additional indoor farms will distribute growing operations closer to where food is consumed, creating a more resilient food system.”
In 2020, the USDA offered the availability of only $3M in grants for urban agriculture and innovative production. Agritecture notes that the average CapEx, or startup cost, for controlled environment farms modeled via their Agritecture Designer digital platform is $512,000, and nearly one-third are over $1M.
Image from: Urban Ag News
“Since our founding in 2014, we’ve seen sustained, year-over-year growth in interest toward urban agriculture, especially amongst industry newcomers,” said Henry Gordon-Smith, Founder and CEO of Agritecture. This growth has only accelerated since the onset of the pandemic, according to the team at Agritecture, which reported nearly a 2x increase in website traffic since Q1 of 2020.
“Despite this increasing interest and the record levels of funding for the handful of indoor mega farms, financing continues to be one of the primary challenges for small and medium-scale CEA businesses,” Gordon-Smith notes. “Yet, we know these farms can achieve profitability with competitive payback periods, while still serving their local markets and communities.”
Gordon-Smith cites Agritecture’s 2019 and 2020 Global CEA Census Reports, produced alongside agtech solutions provider Autogrow, which show that nearly half of all CEA facilities are being started by those with no previous farming experience.
Furthermore, per their recent census, 78 percent of CEA business founders who attempted to raise money were unsuccessful in doing so through traditional financing sources, such as banks.
“By teaming up with Harvest Returns and their innovative financing platform, we can now deliver a direct link from our planning services and digital platform, Agritecture Designer, to funding opportunities for these smaller-scale facilities,” added Gordon-Smith.
Farm In A Box Planned For Bridgeport's East End
BRIDGEPORT — You will not find any vast acres of fertile soil and crops in the East End neighbourhood. So the state, city and area activists have teamed with an entrepreneur on what they all said they believe is the next best thing: farmland in a box
Image from: CT Post
BRIDGEPORT — You will not find any vast acres of fertile soil and crops in the East End neighbourhood. So the state, city and area activists have teamed with an entrepreneur on what they all said they believe is the next best thing: farmland in a box.
Joe Alvarez, founder of High Ridge Hydroponics of Ridgefield, describes it on his website as “an indoor, vertical, hydroponic, shipping container farm to be located in the most urban settings throughout the world.” And the East End — which has been labeled a “food desert” because of the lack of fresh edibles easily available to residents there — will be that urban setting.
“We’re very excited about this,” Keith Williams, head of the East End Neighborhood Revitalization Zone community group, said during a teleconference Friday announcing a $49,999 state grant for Alvarez’s project. “Fresh vegetables. Healthy. That’s what we’re all about — healthy eating.”
High Ridge’s container will produce young micro-greens from broccoli, kale, cabbage, arugula and other plants to be sold at the East End NRZ’s market as a salad mix.
“These greens are harvested after only 10 to 14 days from being planted, which is extremely quick (and) they are super concentrated in nutrition,” Alvarez said.
Friday’s teleconference included several dignitaries who pledged to do everything they can to ensure High Ridge’s success in town, including Lt. Gov. Susan Bysiewicz, state Agriculture Commissioner Bryan Hurlburt, state Sen. Marilyn Moore, state Rep. Andre Baker, Mayor Joe Ganim and Edward Lavernoich of the Bridgeport Economic Development Corporation.
“I hope this project has a lasting and positive impact on your community,” Bysiewicz said. “And I hope it will become a model for other urban areas in our state to grow their own food using innovative technology and techniques.”
“This is not just a shipping container in the city,” Hurlburt said. “This is a much larger, deeper and richer project that we get to celebrate today.”
State Rep. Joe Gresko, D-Stratford, was also included, but wearing a different hat. Gresko works for Ganim continuing a mission started by former Mayor Bill Finch to turn Bridgeport from an ex-manufacturing hub into a leader in the green and environmentally sustainable economy.
It was under Finch that the East End was previously promised an urban green house on the site of the former “Mt. Trashmore” illegal dump. That project, dubbed “Boot Camp Farms” because it would hire veterans, was announced in 2013 and was also supposed to have financial backing from the state. But the developers had no prior experience in that field and the proposal never broke ground.
Alvarez, according to his online biography, “studied environmental science at Fordham University in New York City, graduated in May of 2017 (and) has worked as a private organic gardener, an aquaponic farmer, built greenhouses, maintained greenhouses and designed several custom hydroponic growing systems.”
Hurlburt said he felt confident the new project would be a success.
Alvarez “has limited experience but he knows what he’s doing. ... I know how much Joe was calling us and emailing us and how badly he wanted this grant to make it a reality. I know his heart is right where it needs to be to make it a success.”
“We’re all in this together to make sure Joe has the support he needs to be successful,” Hurlburt emphasized.
There are still important details to be finalized, including getting a site for the shipping container and additional money to cover the full, nearly $150,000 cost. Gresko said that the NRZ was negotiating to use some property and that “when the time comes” Bridgeport will “match” additional private funds Alvarez obtains.
“We’re going to keep an eye on this and troubleshoot as we go forward any issues,” Gresko said.
Alvarez said he hopes to complete construction by the fall. And the colder months are when his crops will be the most needed, said Deborah Sims, who operates the NRZ market.
“After farmer’s market season is over, we have difficulty sourcing (fresh food),” Sims said.
“Three hundred sixty five (days) we’re going to have the greens available,” said Gresko.
Baker recalled how his East End funeral home has hosted some farmer’s markets and called the High Ridge project “a long time coming.” He also told Bysiewicz he hoped similar initiatives to offer more fresh food to his constituents will follow.
“Lieutenant governor, we’re going to be leaning on you and the governor for more support,” he said. “You’re going to hear more from us.”
“Autonomy Will Not Happen Until We Start Sharing Data”
In an emerging industry with companies eager to prove their technologies’ worth, Sensei Ag remains form-factor agnostic, meaning that the agtech company remains unbiased towards different farm hardware solutions – focusing more on software and plant biology. Sensei Ag is a market-changing agtech company that develops agile growing solutions through a highly iterative approach to farming, focused on improving the nutritional quality of fruits and vegetables while also reducing production costs. The company combines plant science, computer vision, machine learning, automation and artificial intelligence into its growing systems
In an emerging industry with companies eager to prove their technologies’ worth, Sensei Ag remains form-factor agnostic, meaning that the agtech company remains unbiased towards different farm hardware solutions – focusing more on software and plant biology.
Sensei Ag is a market-changing agtech company that develops agile growing solutions through a highly iterative approach to farming, focused on improving the nutritional quality of fruits and vegetables while also reducing production costs. The company combines plant science, computer vision, machine learning, automation and artificial intelligence into its growing systems.
According to Sensei Ag CEO Sonia Lo, remaining form factor agnostic is key to the company’s mission of providing hyper-nutritious food to as large a consumer base as possible, which it achieves through both vertical farms and greenhouses.
Image from: Sensei Ag
“We believe that the most robust data comes from operating farms of multiple types. So, not just vertical farms, but also low-tech and high-tech greenhouses. And with vertical farms, we are looking at a number of form factors. Our end goal is to be a grower’s resource and know more about growing at scale with different form factors than anyone else.”
The company is also a strong advocate for open data in the vertical farming industry, which is currently lacking, as evidenced by the siloed development of multiple systems and products, some of which cannot be easily integrated into third-party systems.
“There are lots of data flows and increasingly inexpensive farm management systems. The question, then, is the organization of data into intelligence. Intelligence facilitates autonomy, and as we manage data flows, more farms can become autonomous. But I don’t think autonomy will happen until we start sharing data. For example, we saw an automation supplier with a great robot.
The problem was the robot only works in their ecosystem, so you have to buy the whole farming solution in order for the one robot to work. Ideally, that robot would be plug and play and be able to work in greenhouses and vertical farms,” says Sonia.
Image from: Sensei Ag
According to Sonia, open data in the vertical farming industry may currently be restricted by the dominance of venture financing, which has its own return mandates to fulfill and sometimes wants a “winner takes it all” mentality for the ventures it chooses to back. While such financing has allowed the vertical farming industry to emerge, it may ultimately hinder the industry’s scalability and information sharing.
“There is definitely a capital model in Silicon Valley and in venture capital world in general which is not focused on profitability but is focused on technological achievement and market penetration. We saw this in solar and in the renewables industry when multiple venture capital funds invested in solar assets. Then, the bottom fell out because government subsidies fell away in certain jurisdictions.
I hope that agricultural infrastructure currently financed by venture capital will not necessarily follow the same pathway as solar, but will instead find a public-private partnership model. At some point, these farms need to demonstrate a profit for the debt capital markets to allow scale to occur.”
Image from: Sensei Ag
By embracing open data and transparency, Sonia explains that the vertical farming industry can further mature and iterate with technology to continue lowering costs. By continuously collecting and sharing data from different farm forms, the vertical farming industry would have better insights into the true costs which, according to Sonia, “helps drive scale because it enables the finance community to understand how the farms can be risk assessed and financed.”
Looking ahead, Sensei Ag hopes to form partnerships around the world to bring its innovative, data-driven growing systems across the globe. Taking the Middle East, China and Japan as examples, Sonia explained that the goal would be to choose strategic partners in each region whose local knowledge and business prowess would allow Sensei Ag to iterate its technologies appropriately and serve local markets, bringing cost-competitive farming techniques and nutritious, local produce around the world.
Farming Fish in the Sky
Sometime soon, Apollo Aquaculture Group will have one of the world’s largest vertical fish farms up and running in Singapore. Though construction has been delayed by COVID-19, the farm, once complete, will scale eight stories. Crucially, says the company, it won’t only be the farm’s height that sets it apart from the competition
Image from: Hakai Magazine
Sometime soon, Apollo Aquaculture Group will have one of the world’s largest vertical fish farms up and running in Singapore. Though construction has been delayed by COVID-19, the farm, once complete, will scale eight stories. Crucially, says the company, it won’t only be the farm’s height that sets it apart from the competition.
The high-tech facility will produce up to 3,000 tonnes of hybridized grouper, coral trout, and shrimp each year—with an efficiency, measured in fish per tonne of water, that is six times higher than established aquaculture operations in the Southeast Asian city-state, says spokesperson Crono Lee.
In doing so, the company hopes to become a major contributor to an ambitious plan to boost the food security of the small island city-state, which currently imports 90 percent of its food.
According to Ethan Chong Yih Tng, an engineer at the Singapore Institute of Technology who is not involved with the company, this stacking of fish farms is one of the key initiatives that geographically small Singapore is looking at to achieve its ambitious “30 by 30” target for food security—to produce 30 percent of its nutritional needs locally by 2030.
Founded in 1969, Apollo isn’t a new arrival to aquaculture in Singapore. Since the 1970s, it has been breeding ornamental fish across its 300-odd farms in the region. But when Eric Ng took over the family business in 2009, he was quick to diversify into producing marine fish as food, borrowing methods from operations in Germany, Japan, and Israel, says Lee. The outcome was a three-story farm in Lim Chu Kang, a rare green spot on the outskirts of Singapore. That aquaculture facility has been in operation for nearly a decade.
Each level of the Lim Chu Kang operation has two 135-square-meter tanks supplied with seawater by a system that filters, purifies, monitors, and recirculates water through the farm. As a result, only around five percent of the water needs to be replaced when contaminated by effluent from the fish—though Lee says the goal at both the new and existing facilities is to reduce that to zero using aquatic plants that clean and treat water naturally. That’s in contrast to significant levels of waste at Singapore’s traditional onshore pond farms, where farmers routinely clean out and replace entire tanks.
Image from: Apollo Aquaculture Group
In nearly 10 years of operating the Lim Chu Kang farm, which produces up to 200 tonnes of fish per year, the company has built up meticulous data sets on how to increase yields, says Lee—data they will apply to the new, larger facility.
“We understand the amount of water required, the condition of the water, and the amount of feed—measured down to a single gram per cubic meter of water. As a result, we’re able to produce fish in a much shorter time frame, at the right size for the market,” says Lee.
The decision to build this system up, rather than out, is a response to the lack of space in the Asian city-state. “We’re a very small country, and it’s very difficult to secure land,” says Lee. “So rather than building sideways, and expanding horizontally, why not expand vertically?”
Ever larger onshore fish farms is not the only approach the city-state is using to reach its 30 by 30 goal, however. In late 2019, for example, an offshore fish farm opened about five kilometers off Singapore’s Changi Point Ferry Terminal. Using a closed-containment system, it produces around 166 tonnes of barramundi, red snapper, and grouper each year across four tanks. The system “effectively isolates the fishes from the seawater when the quality of the surrounding water turns poor,” says Yih Tng. The self-contained system offers the control of Apollo’s vertical farm without the initial outlay on expensive land, or the high power costs.
Though Lee insists Apollo’s new eight-story farm will be economically competitive with traditional fish farms, high operating costs remain one of the primary reasons that commercial vertical closed loop fish farms remain limited globally.
In the United States, the majority of farms represented by the Recirculating Farms Coalition are outdoors, and much smaller than the Singapore operation, says founder and executive director Marianne Cufone. “That means we’re not as dependent on artificial inputs, such as temperature controls,” she explains.
“A lot of the larger systems sacrifice some of the natural benefits of [recirculating] systems in that they use a lot of energy for cooling, for heating, and for the circulating pumps. That’s not to say these outweigh the benefits, but a smaller, well-designed system can be extremely eco-efficient versus some of the larger-scale ones.”
The increased operational costs of a large facility translate to the price of the product: a 150-gram pack of Apollo’s ready-to-cook hybridised grouper fillet will set a customer back around US $12—roughly double the price of a frozen red grouper on sale at Singapore’s biggest grocer, Fair Price.
However, Cufone adds, large enclosed fish farms are becoming more prevalent in North America and the rest of the world. Few places is that growth more urgent than in Singapore—a fact only exacerbated by the spread of COVID-19.
“COVID-19 has exploded the awareness of [food insecurity] exponentially to local Singaporeans, and right now there’s a big shift in thinking toward local production,” says Lee. A shift that Apollo plans to take full advantage of.