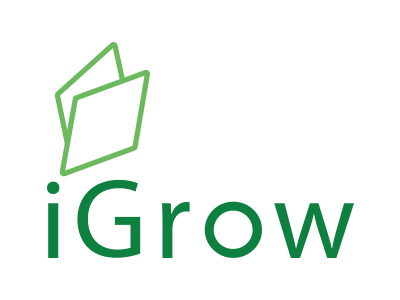
Welcome to iGrow News, Your Source for the World of Indoor Vertical Farming
A Greenhouse In A Box For Small Farmers
Hyderabad-based startup Kheyti’s focus on small farmers has attracted the interest of US-based impact investment firm Acumen
Lush growth inside a low-cost Kheyti greenhouse in Telangana.
With one-tenth of the water and pesticides required and a manifold increase in yield, greenhouses can be transformative. The catch is that their upfront investment cost puts them beyond the reach of those who need them the most—small farmers dependent on rain or borewells. But what if a minimalistic greenhouse is designed from the outset, keeping in mind the needs and limitations of small farmers?
Hyderabad-based Kheyti has partnered with manufacturing and design companies to introduce such a concept. Its modular greenhouse kit, including a drip irrigation system, occupies just a tenth of an acre and costs less than ₹1 lakh. That’s much smaller and cheaper than normal greenhouses which only large farmers can afford. Around 500 farmers in Telangana are the early adopters of this “greenhouse in a box", which comes along with inputs like the appropriate seeds and fertilizers.
It began on a 1.8-acre farm in Narayanpur village, 60km north of Hyderabad, in 2017, recalls Kaushik K., co-founder, and CEO of Kheyti. “Venkatesh and his wife Lakshmi were growing rice along with some vegetables on the side. They worked hard, but their annual income of ₹30,000 barely sufficed for a family of five. The biggest challenge for them was that they could not fully utilize even their 1.8 acres of land because their borewells would run dry in the summer months," says Kaushik.
Model farm
Kheyti had set up an R&D farm on the outskirts of Hyderabad to demonstrate its greenhouse to small farmers. Venkatesh was among the first to visit the farm. “We showed him he could grow high-quality vegetables with so much more yields. But he had only one question: How much water would it need? When we explained that for the greenhouse he would run his borewell pump for only five minutes compared to an hour’s running time for his open field, he was ready to sign up," says Kaushik.
There was a hitch. The ₹5 lakh cost of the greenhouse was relatively low but still too much to raise for the likes of Venkatesh. So, why not make it even smaller and more affordable? It’s from such interactions that Kheyti’s greenhouse designs evolved.
“Venkatesh was the first one and after getting his greenhouse, he continued to give us feedback on what we should do for the next version," recounts Kaushik.
Today, Kheyti offers a 400 sq. m greenhouse for ₹80,000, with insect netting, shade netting, and polyethylene sheets to protect crops from pests, heat and excessive rain. That compares favourably with the ₹25 lakh that a one-acre (4,047 sq. m) greenhouse of this type would cost.
"We’re Retrofitting With The Variables We Have In Place"
Planted Detroit introduces new 20.000 sq. ft. growing facility
“The Square Room is a big block of pink lights with eight levels, where all our growing is done. Everything after germination is done in the same room, both harvesting of our baby greens and microgreens. Because we’re almost done with our PARS (Planted Automated Racking System), which is the big automation,” says Megan Burritt, Managing partner at Planted Detroit.
From a mix-fused downtown neighborhood in Detroit, daily deliveries of ready-to-eat salads and fresh greens are transported to local retailers and restaurants. Planted Detroit makes a large contribution to the city’s share of fresh produce.
New facility
Planted Detroit has been in the middle of the construction of its new 20.000 sq. ft growing facility. The growing space has been a massive update to the company compared to its previous 6-level growing facility which was between 1500-2000 sq. ft. The same room was used for processing, packaging, harvesting, and so on. “It was rather crowded, says Megan, but the main goal was to keep everything tight for the construction to continue in the near surrounding. We’re very serious about biosecurity and we have a daily procedure for everyone who sets foot in our grow room to go through. Making sure our greens don’t come into contact with pathogens is our top priority.
The new growing room
The Square Room, one of our growing rooms, is highly automated, including an automatic harvester to ensure work-efficiency. Once everything is big enough to be transplanted out of their plug trays, PARS (Planted Automated Racking System) will be transplanted with gutters and then go into harvesting. On the other side of PARS, the gutters are taken down and harvested through Planted’s new automatic harvester.
Delivering directly to consumers
The company wants to reach a higher volume of customers as it’s aiming to obtain a consumer brand status. Next to that, the company is always on the lookout for finding more customers through other venues. “We want to go directly to consumers via our web-store to shorten food miles as much as possible, delivering the freshest and most delicious greens,” Megan says. In order to do that the company needed to have a bit more scale, trying to maximize the space they already had.
She adds: “Our farm maybe isn’t the square footage which we could have built from scratch, but we’re retrofitting with the variables we have in place. That is why we have done a combination of a microgreen vertical nursery and PARS for baby greens. Our direct customers wanted meal solutions and we’ve been able to deliver them that. We’ve been doing everything from seed to plate basically.”
Megan Burritt, Managing partner
New projects coming up
On the same campus, 10 meters away, a new farm will be constructed, under the company's office space. In this farm herbs and edible flowers will be grown in response to different customers' demands. Megan says that Planted Detroit’s wholesale customers got them to this point as they were very interested in herbs and edible flowers. “However we weren’t able to perfect these as well in the systems that our baby greens were in perfectly. That’s why we’ve been leaning into R&D lately because once finishing the construction of Farm 2 it will have excellent growing conditions that are better than they have been for those crops.”
Edible flowers are an interesting thing, says Megan, but the company has gotten so much interest in it. According to Megan there aren’t many farms in the US that are growing them. “They’re high priced at this point. It sort of sticks to our original innovation, namely what exists here in the food system and what does not. Where can we fill the ‘does not exist niche’ and satisfy the needs of our customers.”
The company is rolling out a subscription program sometime this year and figuring out where it fits into the fresh food subscription system and how they can partner with other parties in order to get produce closer to society. “It’s great to have this ag job, applied science to be able to do. In all the things we’ve been doing is hiring these Detroiters and showing that we can really create a really great culture of work. It’s really great to see we’re contributing to a better Detroit and a better tomorrow,” Megan states.
Team expansion
During 2020 most of the team stayed on by moving around working hours, so the farm could come back in full force. By the time all equipment was in place, 10 to 12 people were added to the team to have them fully trained before the system would be functioning. “It has been really wonderful to expand the team to see what our capacity is,” says Megan.
“Luckily we’ve been able to develop systems that have been resilient. We’ve seen so many different patterns in consumer behavior but they seem to have fallen in our favor. People are eating more at home, shopping for groceries more, and that triggered our pivot focusing on direct consumers. But now, it’s perfectly in line with our strategy on how we go to market. As long as we can supply our customer needs we’ll be on the right path. Nothing but bright hopes for the future right now,” Megan affirms.
For more information:
Planted Detroit
Megan Burritt, Managing partner
megan@planteddetroit.com
www.planteddetroit.com
Author: Rebekka Boekhout
© VerticalFarmDaily.com
Eastern Kentucky Company Growing Local Economy By Growing Vegetables Year-Round
AppHarvest has created 300 jobs in Appalachia, an area not really known for growing tomatoes.
by GIL MCCLANAHAN
MOREHEAD, Ky. (WCHS) — Imagine growing fresh local tomatoes in the dead of winter. A company in Eastern Kentucky is using high-tech agriculture to grow vegetables indoors.
To View The Video, Please Click Here.
AppHarvest checks tomatoes growing inside the company's 60-acre indoor greenhouse.
(AppHarvest ) Courtesy Photo
AppHarvest opened in Rowan County, Ky. last October. They are growing more than just vegetables. They are growing the economy in an area that sorely needs it.
What's growing inside AppHarvest's 2.8-million square foot facility is capable of producing more food with less resources.
"For our first harvest to be on a day where there was a snowy mountainside could not have been any more timely. The fact that we are able to grow a great juicy flavorful tomato in the middle of January and February is what we have been working to accomplish," AppHarvest Founder and CEO Jonathan Webb said.
Webb said five months after opening its Morehead indoor farm facility, the company shipped more than a million beefsteak tomatoes to several major supermarket chains, including Kroger, Walmart and Publix. Those large bushels and bushels of tomatoes are grown using using the latest technology, no pesticides and with recycled water in a controlled environment using 90% less water than water used in open-field agriculture.
"We're just trying to get that plant a consistent environment year round with the right amount of light and the right amount of humidity and the right temperature just to grow, and the vines of our crops the tomato plant end up being 45 feet and we grow them vertically so that is how we can get so much more production," Webb said.
One of the company's more well-known investors is Martha Stewart.
"I said Martha, can I get five minutes and I told her what we are doing. She was like, look we need good healthy fruits and vegetables available at an affordable price. I love the region you are working in," Webb said.
A couple of weeks later, Webb met with Stewart at her New York office, and she decided to become an investor in the company. Some local restaurants are looking forward to the day when they can buy their vegetables locally from AppHarvest. Tim Kochendoerfer, Operating Partner with Reno's Roadhouse in Morehead, buys his vegetables from a company in Louisville.
"It will be another selling point to show that we are a local restaurant," Kochendoerfer said.
Webb points out AppHarvest is not trying to replace traditional family farming. "Absolutely not. We want to work hard with local farmers," he said.
Webb said by partnering with local farmers, more local produce can get on grocery store shelves, because last year 4 billion pounds of tomatoes were imported from Mexico.
"What we are working to replace is the imports from Mexico where you got children working for $5 a day using illegal chemical pesticides in the produce is sitting on a truck for 2-3000 miles," Webb said.
AppHarvest has already started influencing the next generation of farmers by donating high tech container farms to local schools. Students learn to grow crops, not in the traditional way, but inside recycled shipping containers. The containers can produce what is typically grown on 4 acres of land. Rowan County Senior High School was the second school to receive one. It arrived last fall.
"We sell that lettuce to our food service department and it's served in all of our cafeterias in the district," said Brandy Carver, Principal at Rowan County Senior High School.
"When we talk about food insecurity and young people going home hungry, what better way can we solve these problems by putting technology in the classroom. let kids learn, then let the kids take the food home with them and get healthy food in the cafeterias," Webb said.
AppHarvest has created 300 jobs in Appalachia, an area not really known for growing tomatoes. Local leaders believe the company will attract more business to the area.
"I fully expect in time we'll see more and more activity along that line like we do in all sectors," said Jason Slone, Executive Director of the Morehead-Rowan County Chamber of Commerce.
"We will eventually be at the top 25 grocers. Name a grocer. We've been getting phone calls from all of them," Webb said.
AppHarvest has two more indoor farming facilities under construction in Madison County, Ky., with a goal of building 10 more facilities like the one in Rowan County by the year 2025.
To find out more about AppHarvest click here.
Vertical Farms vs Greenhouses – The First Consideration: Location
When and where to use a vertical farm versus a greenhouse, and what factors – both economic and environmental – make the difference.
In just the past decade or so, sustainable farming has seen a high-tech makeover in the form of Controlled Environment Agriculture, or CEA, which consists of two main technologies: Vertical farms and greenhouses.
When it comes to feeding the world, it’s not a choice between vertical farms or greenhouses. We’ll need both to feed our growing global population with healthy, sustainable food, and we need to understand the ideal situation for each.
But as a business decision, it often is a choice between the two – and that’s what we hope to explain in this five-part series of articles: When and where to use a vertical farm versus a greenhouse, and what factors – both economic and environmental – make the difference.
In this first post, we’ll cover the basic differences between vertical farms and greenhouses, and why location matters so much when deciding between the two. Then stay tuned because, in the next articles, we’ll dive deeper into energy and lighting costs, automation and other expenses, environmental and crop considerations, and finally, the future of farming.
Vertical Farms vs Greenhouses: The Basics
The two technologies are often confused, but there are significant differences between them in resource use, cost, output, and, perhaps most importantly, the ideal locations for each.
Greenhouses are the more traditional technology that you’re probably familiar with: A single layer of crops, planted inside an enclosed space with walls and a ceiling made of glass or plastic to allow natural light in. They’re semi-controlled environments.
Vertical farms, on the other hand, are a much more recent invention using trays of usually hydroponic plants, stacked in floor-to-ceiling towers, with LED lights illuminating each layer, and climate control constantly adjusting the temperature, humidity and more.
In the upcoming articles in this series, we’ll dive into each part of these differences in more detail. But for now, let’s start with the first question entrepreneurs always need answering: The price tag.
Henry Gordon-Smith is the CEO of Agritecture, an independent consultancy and software creator that helps clients decide between the two technologies. As he puts it, “Vertical farming represents the most expensive, most controlled form of agriculture.”
At first blush, vertical farms are, in fact, shockingly more expensive than greenhouses – six to 10 times as costly. Gordon-Smith says vertical farming costs 2,200 to 2,600 Euro per square meter of cultivation bed space, while high-tech greenhouses cost 250 to 350 Euro per square meter of cultivation space.
Both offer a year-round source of fresh, pesticide-free, locally-grown produce, which provides better nutrition than the same foods that arrive from far away.
But what else do farmers, entrepreneurs, and investors get for all the added expense of vertical farming?
The answer is pretty simple: A more compact farm with more production per square meter, less water use, and more control over both quantity and quality. (With iFarm, this predictability is part of the package, in the form of a guaranteed yield within a precise time frame.)
For some entrepreneurs or municipalities, the cachet of implementing a high-tech farming technique that’s only been in use for less than a decade is also a factor in favour of vertical farming. But most often, the choice comes down to location.
The Ideal Location for a Vertical Farm versus a Greenhouse
The first step in determining the feasibility of building a vertical farm or greenhouse is to look at the drivers and constraints – many of which are simply location-based.
Places with limited space, such as dense urban areas, and limited access to fresh water are ideal for vertical farms. Doubly so if they have access to low-cost, renewable energy, and if they’re near a market with high demand for the crops vertical farms excel at producing: Leafy-greens, micro-greens, herbs and berries grown locally, without pesticides.
But in areas with unlimited space, lots of natural sunlight, and high-cost and/or high-carbon electricity, greenhouses may be the better option and the extra expenses of vertical farming might not make sense.
How these considerations apply in broad regions of the world is illustrated below:
Hydroponics Farming: Why Hydroponic Farms Are Trending In India?
As per reports, India’s hydroponics market is expected to grow at a compound annual growth rate of 13.53% between 2020 and 2027.
Hydroponics is slowly gaining popularity in India and attracting more and more farmers. Basically, hydroponics is a type of horticulture and a subset of hydroculture, which is a method of growing plants, usually crops, without soil, by using mineral nutrient solutions in an aqueous solvent.
Hydroponic farming can be done in a small space also like a balcony which is a soil-less, water-based farming process. Rather than using soil for plant nutrition, crops are fed nutrient-rich water, negating a lot of the baggage that comes with soil-based methods.
Hydroponics is the practice of growing plants in a nutrient-rich solution, skipping the soil. “It has been practised for centuries, so it is not a new technology," points out Akhila Vijayaraghavan, the founder-director of Coimbatore’s Parna Farms, adding the Hanging Gardens of Babylon are believed to have been hydroponically grown. “The Aztecs created vast hydroponic systems using rafts called chinampas," she says.
The film piqued Gopal’s interest, and he began reading about the method to grow plants without soil. “We started working with hydroponics as a project in 2012. At that time, we didn’t know much about the plight of farmers and how a technology like this could add value," said Gopal. The idea was to create awareness among the right audience and sell “through prototypes and hobby kits."
Urban farmers are taking to hydroponics, a water-smart solution to grow pesticide-free produce on rooftops and terraces. As per reports, India’s hydroponics market is expected to grow at a compound annual growth rate of 13.53% between 2020 and 2027.
What is Hydroponics
Hydroponics is a branch of hydroculture, in which plants are grown without soil by using water solvent which consists of minerals nutrient solution. Terrestrial plants may be grown with their roots only, roots are exposed to the nutritious liquid, or roots may be supported physically by a medium like gravel.
Plants are also grown through a process called photosynthesis, in which plants use sunlight and a chemical inside their leaves called chlorophyll to convert carbon dioxide and water into glucose and oxygen, as shown in reaction.
6CO2 + 6H2O → C6H12O6(Glucose)+ 6O2
The nutrients we use in hydroponic systems may come from different sources, such as fish excrement, duck manure, or chemical fertilisers.
1Advantages of Hydroponics
Plantation without soil
We can grow plants in places where the land is limited, doesn't exist, or is contaminated. In the early time period, Hydroponics was a successful technique used to supply fresh vegetables for troops in Wake Island. It has been considered as the future farming to grow foods for astronauts in space by NASA.
Better use of space and location
All those plants need are provided and maintained in a system, you can grow plants in a small apartment, bedrooms or kitchen as long as you have some spaces.
Roots of plants usually expand and spread out in search of foods, and oxygen in the soil but in the case of Hydroponics, roots are sunk in a tank full of oxygenated nutrient solution and are directly in contact with vital minerals. This means that you can grow your plants closer, and consequently huge space savings.
Climate control
Hydroponic growers can have total control over climate, temperature, humidity, light, the composition of the air. This means you can grow foods all year, regardless of the season. Farmers can produce foods at the right time to maximize their profits.
Water-saving
Plants grown by the process of hydroponically can use 10% of water, as compared to one grown on the field because water is recirculated, in this method. Plants will take up the water they need, while run-off water will be captured and return to the system. Water loss in this system will only occur in two forms - evaporation and leaks from the system.
Use of nutrients
You can have 100% control of the nutrients (foods) that plants need in this method. Before planting, growers can check what are plants requirement and what amounts of nutrients needed at particular stages and at what percentage they should be mixed with water.
Better growth rate
Do hydroponic plants grow faster than in soil? Yes, because you can set conditions favourable to the plant’s growth like temperature, lights, moisture, and especially nutrients. As plants are placed in favourable conditions, nutrients are provided in sufficient amounts and come into direct contacts with the root systems. Therefore, plants do not waste valuable energy in the search for diluted nutrients in the soil and put their complete focus on growth.
Vertical Farms Nailed Tiny Salads. Now They Need To Feed The World
Vertical farming is finally growing up. But can it move from salad garnishes for the wealthy to sustainable produce for the masses?
Gartenfeld Island, in Berlin’s western suburb of Spandau, was once the bellows of Germany’s industrial revolution. It hosted Europe’s first high-rise factory and, until World War II, helped make Berlin, behind London and New York, the third-largest city on Earth.
Today’s Berlin is still a shell of its former self (there are over a hundred cities more populous), and the browbeaten brick buildings that now occupy Gartenfeld Island offer little in the way of grandeur. Flapping in the gloom of a grey November morning in 2020 is a sign which reads, in German, “The Last Days of Humanity”.
Yet inside one of these buildings is a company perched at agriculture’s avant-garde, part of the startup scene dragging Berlin back to its pioneering roots. In under eight years, Infarm has become a leader in vertical farming, an industry proponents say could help feed the world and address some of the environmental issues associated with traditional agriculture. Its staff wear not the plaid or twill of the field but the black, baggy uniform of the city’s hipsters.
Infarm has shipped over a thousand of its “farms” to shops and chefs across Europe (and a few in the US). These units, which look like jumbo vending machines, grow fresh greens and herbs in rows of trays fed by nutrient-rich water and lit by banks of tiny LEDs, each of which is more than ten times brighter than the regular bulb you’d find in your dining room. Shoppers pick the plants straight from the shelf where they’re growing.
Infarm crop science director, Pavlos Kalaitzoglou, in his Berlin lab
Credit Ériver Hijano
Gartenfeld Island, however, is home to something more spectacular. Here, in a former Siemens washing machine factory, stand four white, 18-metre-high “grow chambers”, controlled by software and served by robots. These are the company’s next generation of vertical farms: fully-automated, modular high-rises it hopes will scale the business to the next level. According to Infarm, each one of these new units uses 95 per cent less water, 99 per cent less space and 75 per cent less fertilizer than conventional land-based farming. This means higher yields, fresher produce and a smaller carbon footprint.
Agriculture is a £6 trillion global industry that has altered the face and lungs of the Earth for 12,000 years. But, unless we change our food systems, we’ll be in trouble. By 2050, the global population will be 9.7 billion, two billion more than today. Fifty-six per cent of us live in cities; by 2050 it will be 70 per cent. If the prosperity of megastates like India and China continues to soar, and our diets remain the same, we will need to double food production without razing the Amazon to do it. That sign on Gartenfeld Island might not be so alarmist.
Vertical farmers believe they are a part of the solution. Connected, precision systems have grown crops at hundreds of times the efficiency of soil-based agriculture. Located in or close to urban centres, they slash the farm-to-table time and eliminate logistics. New tech is allowing growers to tamper with light spectra and manipulate plant biology. Critics, however, question the role of vertical farms in our food future. They are towering lunchboxes for late capitalism, they argue – producing garnishes for the rich when it is the plates of the poor we must fill. Vertical farms already make money, and heavyweights including Amazon and SoftBank are investing in various companies in the hopes of cornering a market expected to be worth almost £10 billion in the next five to ten years. Infarm is leading that race in Europe. It has partnered with European retailers including Aldi, Carrefour and Marks & Spencer. In 2019 it penned a deal with Kroger, America’s largest supermarket chain. Venture capitalists have handed the firm a total of £228 million.
Not bad for a hare-brained experiment that started in a Berlin apartment.
An Infarm employee tends to a batch of seedlings in a special incubator
Credit Ériver Hijano
In 2011, a year before he moved to Berlin, Erez Galonska went off-grid. He grew up in a village in his native Israel, but the young nation was growing too, and farms made way for buildings. Soon the village was a town, and its inhabitants ever more disconnected from their natural surroundings.
Galonska’s father had studied agriculture, and the son had dreamed of recovering a connection with nature he felt he had lost. The search took him to the mountains of the Canary Islands, where he found a plot of land and got to work. He drank water from springs, drew energy from solar panels, and spent long hours farming produce he then sold or bartered at local markets.
When he met his now-wife Osnat Michaeli, “I traded it for love,” he says. “Love is stronger than anything.” In 2012, the couple, alongside Galonska’s brother Guy, who had studied Chinese medicine, moved to Berlin to work on a friend’s social media project. But the hunger for self-sufficiency remained. It was “a personal quest,” Michaeli says. “How we can be self-sufficient, live off the grid. Food is a big part of that journey.”
We meet at a Jewish restaurant in Berlin’s historic Gropius Bau art museum. It is mid-morning, and Covid-19 has cleared the tables. But a row of Infarm units whirs away quietly along one wall, producing basil, mint, wasabi rocket (a type of rocket leaf with the punchy flavour of wasabi), and other, more exotic herbs. Such produce was a pipedream for the three Infarm co-founders eight years ago. Growing crops when living on a tropical island was one thing. Doing it in a small apartment, located in the tumbledown Berlin neighbourhood of Neukölln, was quite another. Soon after moving from the Canaries, Erez Galonska typed “can you grow without soil” into Google.
Japan had taken to indoor farming in the 1970s, and this bore some helpful information on its techniques. The same was true of illegal cannabis growers, who swapped tips about hydroponics – growing with nutrient-packed water rather than soil – across subreddits.
Several trips to a DIY store later, the trio had what resembled a hydroponic farm. It was a big, chaotic Rube Goldberg machine, and it leaked everywhere. Growing wasn’t simply a case of switching on the lights and waiting. Brightness, nutrients, humidity, temperature – every tweaked metric resulted in an entirely different plant. One experiment yielded lettuce so fibrous it was like eating plastic. “We failed thousands of times,” Erez Galonska says.
Two of Infarm’s co-founders, Osnat Michaeli and Erez Galonska
Credit Ériver Hijano
Eventually, the team grew some tasty greens. They imagined future restaurant menus boasting of food grown “in-farm”, rather than simply made in-house, and founded Infarm in 2013. But there was a hitch: indoor-grown cannabis sells for around £1,000 per kilo. Lettuce for £1.20. Most of the early vertical farms required heaps of manual work and operated in the red. “It simply wasn’t a sustainable business model,” Erez Galonska says.
By 2014, they decided to roadshow their idea and shipped a 1955 Airstream trailer – a brushed-aluminium American icon – to Berlin. The trailer belonged to a former FBI agent, but it was conspicuous in a city of Volkswagens, caravans and Plattenbau buildings. Michaeli and the Galonska brothers transformed it into a mobile vertical farm, then pitched up at an urban garden collective in Berlin’s trendy Kreuzberg district. There they proselytised indoor farming to urban planners, food activists, architects and hackers, handing out salads and running workshops. Fresh, local food – even if it cost a little more – would entice a growing number of foodies who were interested in where their meals came from. The trailer cost nothing but petrol money to move, and emissions from the growing process itself were almost nil.
When the designer of a swanky hotel across town came by trailer, he asked if the team could install something similar in his restaurant. “That was really the trigger,” says Guy Galonska. “We rented a workshop and we got to develop a system for them.”
When they installed their first “farm” in a Berlin supermarket, VCs took notice and visited Infarm’s young founders at their Kreuzberg office-cum-kitchen, where they hosted dinner parties featuring Infarm crops. But a return on investment still seemed distant: some investors thought the farms were an art project. Maintaining locations manually was exhausting, and the team almost went bankrupt “two or three times,” Guy Galonska says. “I think all of us got a lot of white hair during that time,” he adds. “It was a very challenging thing to do.”
A €2 million grant from the European Union in 2016 helped. With it came deals to place Infarm units in supermarkets and restaurants across Germany. Managing them all would require something precise, connected and efficient. To become a sustainable business, Infarm would have to behave less like a farm, and more like a tech startup.
An Infarm kiosk in the Edeka Supermarket E Center in Berlin
Credit Ériver Hijano
For around 2,500 years after King Nebuchadnezzar II of Babylon gifted his wife some hanging gardens, little changed in the world of hydroponic farming. Asian farmers grew rice on giant, terraced paddies, and Aztecs built “chinampa” rigs that floated along the swamps of southern Mexico.
Life magazine published a drawing of stacked homes, each growing its own produce, in 1909, and the term “vertical farming” appeared six years later. The US Air Force fed hydroponically-grown veggies to its troops during World War II, and Nasa explored the tech as a solution for life off-planet. But vertical farming didn’t really capture public imagination until 1999, when Dickson Despommier, a Columbia University professor, devised a 30-storey skyscraper filled with farms. In 2010, Despommier published The Vertical Farm: Feeding the World in the 21st Century, which has become the industry’s utopian testament.
“I had no expectations whatsoever that this would turn commercial,” Despommier says. “We just thought it was a good idea, because we didn’t see any other way out of stopping deforestation in favour of farming, and keeping the carbon dioxide content of the atmosphere at a reasonable level. It turned out to be a crazy idea whose time has come.”
The vertical farming concept is simple: growing produce on vertically-stacked levels, rather than side by side in a field. Instead of the Sun, the vertical farm uses artificial light, and where there is ordinarily soil, growers use nutritious water or, in the case of “aeroponic” farms, an evenly-dispersed mist.
Vertical farms take up a vanishing amount of land compared to their conventional cousins. They use almost no water, don’t flush contaminating pesticides into the ecosystem, and can be built where people actually live. But, by and large, they have not functioned as businesses. Only the black-market margins of weed, and Japan’s high-income, high-import food ecosystem, have catered to profit. It costs hundreds of thousands of pounds to erect a mid-sized vertical farm, and energy use is prohibitively high.
Advances in technology are changing this. By bolting automation, machine learning and cloud-connected software on to vertical farms, firms can trim physical labour, increase capacity and maintain a dizzying range of cultivation variables. Infarm staff at a separate office to the new Berlin farm, located some 23km southeast of Spandau in the Tempelhof district, keep track of “plant recipe” settings at any one of the startup’s 1,220 in-store units, including CO2 levels, pH and growth cycles, via the company’s Farm Control Cloud Platform, a bit like a giant CCTV room. Machine learning finesses recipes, and keeps each plant as uniform as possible.
Inside the new vertical farm, trays of produce are tended by automated systems
Credit Ériver Hijano
Gartenfeld Island’s employees – mechanical and electrical engineers, software developers, crop scientists and biologists – get closer to the produce, but only just. They monitor via an iPad and feed crops into the building’s four massive grow chambers, or farms, each one about the height and width of two London buses, with ventilation systems that whoosh like a subdued turbine hall.
From there on in, robots do the hard work. Inside the farms, a robotic “plant retrieval system” – basically a tricked-out teddy picker – scoots up and down a perpendicular beam, plucking trays of plants in various stages of growth and shuffling them closer, or further, from LED lights at the summit. The firm claims this reduces service time by 88 per cent. A sliver of the window is the only way to see the device in-person: everything is hermetically sealed to keep out pests. “With automation, you invest once and then that price goes down over time,” says Orie Sofer, Infarm’s hardware lab lead. “With human labour, unfortunately, over time the price goes up.”
The number of crop plants varies depending on the produce, but there are usually just under 300 in a “farm” at any one time. Each farm yields the equivalent of 10,000 square metres of land and uses just five litres of water per kilo of food (traditional vegetable farming uses around 322 litres per kg).
Infarm is not alone in this revolution. AeroFarms, a Newark, New Jersey-based startup, feeds an aeroponic mist to roots that are separated from their leaves by a cloth. It’s most recent funding round was led by Ingka Group, the parent of Swedish furniture giant IKEA. New York’s Bowery Farming, like Infarm, focuses on automation and a proprietary dashboard called BoweryOS that, among other things, takes photos of crops in real-time for analysis. It’s £123 million in backing comes from investors including Singapore’s sovereign fund Temasek. Bowery CEO and founder Irving Fain believe his addressable market “is about a hundred billion dollars a year, just in the US, of crops that we think are good candidates for us to grow.”
Leading the vertical farming VC race is Plenty, a San Francisco-headquartered brand that has raised almost half a billion pounds in the capital since it was founded in 2013, including a 2020 Series D round led by Masayoshi Son’s $100 billion SoftBank Vision Fund. Plenty feeds its greens with water that trickles down six-metre-tall poles; infrared sensors pour data into an algorithm that nudges the plant’s growth recipe accordingly.
Plenty co-founder and chief science officer Nate Storey, who works at the company’s test farm in Wyoming, likens these deep-tech solutions to the tools that powered agriculture’s most recent revolution: “The tractor allowed farmers to be freed from constraints. Half of their land was dedicated to raising draft animals, and the tractor came along and freed them from a life where they were basically managing animals just so they could plough their land.”
For them, he says, automation is similar. “It allows us to get rid of the hardest work – the work that is unpleasant, the work [growers] don’t like to do – and focus on the work that really matters.”
Infarm kiosks inside the Beba restaurant in the Gropius Bau museum
Credit Ériver Hijano
Infarm differs from the competition on two fronts. The first is its focus on modular design: each component is compatible and scalable, like a giant, noisy LEGO set. Modularity makes it possible to install Infarm units anywhere in the world in a matter of weeks, no matter the size. That enables the company’s second USP: its business model. Infarm has no stores, selling produce instead via its remote units.
Clients tell Infarm which produce they want, and “create a schedule,” says Michaeli. “You buy the plants. Everything on the farm is controlled by Tempelhof. Everything that’s grown belongs to the client.” A chef may demand pesto that’s made from particular three-day-aged Greek and Italian basil, for example. Infarm can do that (Tim Raue, Berlin’s most famous chef, is a customer). “Everyone stops and asks about the farm,” one Berlin store manager says. “It’s great to have innovation here.”
Infarm has “two big advantages,” says Nicola Kerslake, founder of Contain Inc, a Nevada-based agtech financier. “One is that they’ve figured out how to do product onsite, which is really not very easy. And the other is that they have these great relationships with big purchasers like Marks & Spencer.”
“When you look at where the arms race is in this industry,” she continues, “it’s really been in two areas: How do I get hold of as much capital as possible, and how do I sign up the right partners? Having Marks & Spencer in your back pocket is really useful.”
It has helped encourage investors to open their chequebooks. Hiro Tamura, a partner at London VC firm Atomico, first met Infarm’s founding trio in 2018. A year later he led its £75 million Series B round. “They could roll these things out,” he says. “They worked, and they didn’t need some industrial-sized warehouse to do it. I didn’t lean in, I fell into the rabbit hole. And it was incredible. I was like, wow, these guys are thinking about time and speed to market modularity.”
Infarm ploughs a chunk of its revenue back into research. In a mezzanine-level lab sitting above the farms at Gartenfeld Island, a dozen white-coated analysts conduct tests on herbs to a soundtrack of Ariana Grande, measuring crop sugar levels, acidity, vitamins, toxicity, antioxidants and more. Via a process of phenotyping – the study of organisms’ characteristics relative to their environment – they hope to create more flavourful plants, or new tastes altogether.
“It’s not just about the hardware,” Kerslake explains. “It’s about how the hardware interacts with the rest of your farm system. And we’re starting to see a lot more sophistication on that front because the AI programs these companies started three or four years ago are now starting to bear fruit.”
Infarm’s results are high-quality: juicy lettuce, wasabi rocket that kicks, and basil that’s far more fragrant than the budget variety. “The end goal with almost everything that we’re doing is developing some sort of playbook, some sort of modular and standardised system, that we can then copy-paste to wherever we go,” says Pavlos Kalaitzoglou, Infarm’s director of plant science. Across from the lab, tomatoes and shiitake mushrooms grow in wine cellar-size chambers. They are living proof of how the firm is looking to diversify from herbs and leafy greens, whose low energy and water requirements make them the staple crop of every vertical farming startup today.
Rows of LED-illuminated produce inside one of Infarm’s four massive new grow chambers
Credit Ériver Hijano
We are in danger of farming the planet to death. Agriculture already occupies 40 per cent of all liveable land on Earth, and food production causes a quarter of all greenhouse gases. An area the size of Scotland disappears from tropical rainforests, responsible for up to a quarter of land photosynthesis, each year. Clearing more trees to feed our spiralling population will not help.
“We need to go back to the drawing board and rethink which avenues we can environmentally afford to pursue,” says Nicola Cannon, a professor at the Royal Agricultural University in Cirencester. Nitrogen fertiliser is particularly harmful to the environment, Cannon adds, “and has led us to adopt systems which have grossly exceeded the planetary boundaries.”
Current food systems are wildly inefficient: waste accounts for 25 per cent of all calories. And yet, almost a billion people suffer from hunger worldwide. These are not issues vertical farming will solve, critics, argue. Going local does little beyond satisfying consumers.
Energy is another tricky issue. Ninety per cent of Infarm’s electricity today is renewable, and it wants to reach zero emissions in the next few years. But this doesn’t factor in the environmental cost of building a steel-and-cement facility.
“Vertical farms are a round-off error to the round-off error in terms of contributing to the big levers out there,” Jonathan Foley, an environmental scientist based in Minneapolis, says. “Like most technologies that are getting a lot of venture capital and which come from Silicon Valley kind of thinking, it’s being massively overhyped at the cost of real solutions. There’s an opportunity cost to put all this technology, money and renewable energy – that could be used for other things that we need energy for – into growing arugula for rich people at $10 an ounce.”
More than half the world’s food energy comes from its three “mega-crops”: wheat, corn and rice. They require wind, seasons and micronutrients that vertical farms are unable to replicate today. These are the crops that can prevent famine in Somalia, Bangladesh or Bolivia – not lettuce. “Vertical farms are growing the edge of the plate, not the centre of the plate,” Foley says.
But Despommier says it’s too soon to criticise the young industry for not addressing issues such as crop diversity. “What you’re really seeing is a rush towards profitability to get their feet wet, and to get their ledgers in the black and to pay off their investors, before they start diversifying,” he says.
“In a world where you think that land is unlimited and that resources are unlimited, indoor farming would be nonsensical,” Plenty co-founder Storey says. “As crazy as it seems to replace the Sun with electricity, it makes sense today. And it really makes more and more sense as time goes on.”
Much of the hope vested in vertical farms rests on the light-emitting diode. This tiny bead of light is the industry’s packhorse: it is a farm’s biggest financial layout and the nucleus of its most exciting advances. Modern LEDs are nothing like the ones that powered your childhood TV. They’ve progressed at such a rate, in fact, that they’ve developed their own law to adhere to: “Haitz’s Law”. Each decade, their cost drops by a factor of ten, while the light they generate leaps by a factor of 20.
That curve will eventually plateau, experts say. But not before LEDs improve enough to allow vertical farms to profit from food closer to the middle of the plate. Infarm’s current smart LED set-up is over 50 per cent more efficient than the one that lit its first farms. Haitz’s Law has helped some companies experiment in growing potatoes, which require far more energy and water than leafy greens. Turning profit from a crop that delivers the highest calories per acre would be momentous for the industry.
The cutting edge of LED technology today is smart sensors that can regulate the brightness and spectrum of light to replicate growing outdoors – or enhance it. Much of the planet’s first flora grew only in the ocean, which looks blue because it absorbs blue light at least.
Photosynthesis, therefore, occurs best between the blue and red light spectra. By tailoring LEDs to emit only these colours, or by dimming at intervals meant to mirror a plant’s natural cycle, vertical farmers can further reduce their energy burden – like stripping a road car to its bare bones so it can drive faster.
Recent discoveries have been more surprising. Strawberries, for example, react particularly well to green light. Some spectra can increase vitamin C in concentrated fruits like kiwis, while others extend shelf-lives by almost a week. In the future, says Fei Jia, of LED firm Heliospectra, growers “can get feedback from the lighting and the plants themselves on how the lighting should be applied… to further improve the consistency of the crop quality.”
“If you judge it from what you have today, you understand what [critics] are saying,” Guy Galonska says. “How can you grow rice and wheat and save the world? And they are right. But they can’t see ten years ahead: they can’t see all the different trends that are going to support that revolution.”
Other technological advances are helping agriculture in different ways. Drones and sensors help map and streamline growing. Drip irrigation dramatically reduces the burden on dwindling water supplies. Circular production – where waste products from one process contribute to fuelling another – is becoming more commonplace, especially in livestock farming. Cell-grown or insect-based meat (or vegetarianism) will reduce our reliance on livestock, which consume 45 per cent of the planet’s crops. Infarm, and the broader vertical farm cohort, may not be saving the world today. But it wants to build taller farms, place them in public buildings like schools, and teach people the value of fresh, healthy vegetables. If 70 per cent of us are to live in cities, then cities “can become these communities of growing,” says Erez Galonska.
Ultimately, Infarm wants to build a network of tens of thousands of automated farms, each one pumping streams of data back into a giant AI system in Berlin. This “brain”, as Galonska calls it, will pour that information into algorithms to generate better food at lower costs, each new yield shaving fractions from the water, energy and nutrients required. Then, Infarm could become something closer to the dream Galonska left behind in the Canaries: truly self-sufficient.
It’s a long way from the leaky, DIY gadget he and his co-founders built in their front room. “The way the world is going now, it’s very clear to everyone it’s running in the wrong direction,” Galonska says. “We definitely believe in the power of collaboration: bringing those outside-the-box thoughts to create a new system that will generate more food, better food, much more sustainably, and help to heal the planet – because that’s the main issue on the table.”
7 New HDB Carpark Rooftop Sites Offered For Rental For Urban Farming In Public Tender
More local produce. Part of Singapore's efforts to strengthen its food security is increasing its capability to produce food locally
Part of Singapore's efforts to strengthen its food security is increasing its capability to produce food locally.
To do this, more sites for urban rooftop farms atop multi-storey Housing Development Board (HDB) carparks are being offered for rental, via a public tender process that was launched today (Feb. 23).
Seven new sites
Seven sites have been identified in Jurong West, Bukit Panjang, Sembawang and Woodlands, according to the Singapore Food Agency (SFA) and HDB.
The sites will be used to farm vegetables and other food crops, and will also be used to pack and store produce.
They will be tendered out as a single site (in Jurong West) and three cluster sites (in Bukit Panjang, Sembawang and Woodlands).
Screenshot from SFA and HDB
Tenderers who successfully bid for cluster sites will be awarded all sites within the cluster, to allow them to cut costs through production at scale.
Single-site farms, on the other hand, provide opportunities to "testbed innovative ideas".
Tenderers must submit their proposals via GeBiz before the tender closes on Mar. 23, 4pm.
Proposals will be assessed on their bid price, production output, design and site layout, as well as their business and marketing plans.
More information can be found on SFA's website here.
Producing food locally
This is the second time tenders were launched for rooftop urban farms on carparks here — the first took place in Sep. 2020, with nine sites being awarded.
Collectively, the nine farming systems can potentially produce around 1,600 tonnes (1,600,000kg) of vegetables per year.
Having more space for commercial farming in land-constrained Singapore is one of SFA's strategies to achieve its "30 by 30" goal — which is to produce 30 percent of Singapore's food locally by 2030.
The move is also in line with HDB’s Green Towns Programme to intensify greening in HDB estates.
“Besides contributing to our food security, Multi-Storey Car Park (MSCP) rooftop farms help to bring the community closer to local produce, thereby raising awareness and support for local produce," said Melvin Chow, Senior Director of SFA’s Food Supply Resilience Division.
Plenty Ranked Number One on Prestigious FoodTech 500
Plenty came in first on the ranked list of 500 and out of a total of 2,000 nominees.
SOUTH SAN FRANCISCO, Calif.
Plenty, the flavor-first vertical farming company with a mission to improve the lives of people, plants, and the planet, today announced its #1 ranking on the esteemed Forward Fooding 2020 FoodTech 500.
Referred to as the “Fortune 500 list of agrifood companies,” the FoodTech 500 highlights global entrepreneurial talent at the intersection of food, technology and sustainability. Forward Fooding’s proprietary algorithms evaluate a business on its size, digital footprint and sustainability as measured against the United Nations Sustainable Development Goals. Plenty came in first on the ranked list of 500 and out of a total of 2,000 nominees.
“It is an honor to be included on the FoodTech 500 and we are thrilled to be ranked first,” said Nate Storey, co-founder and CSO of Plenty. “The world is in need of an agricultural revolution, and there are many exciting areas where innovators are changing the future of food. At Plenty, we’re focused on using our proprietary, scalable vertical farming technology to deliver the freshest, most favorable produce year-round, while preserving our most precious resources.”
Plenty grows pesticide-free, non-GMO produce that tastes like it was fresh-picked from the garden because it was. The company ships from its farm to local stores every day. The farm’s controlled environment means the company can grow leafy greens year-round, regardless of the season. Plenty’s leafy greens are so clean, there is no need to wash because there is nothing to wash away - no bleaches, chemicals, soil or pesticides. The company wants the first person to touch their produce to be the consumer opening the package in their kitchen. Plenty plants are cultivated in an optimum growing environment, reaching peak flavors and nutrient value year-round, across every harvest.
The world is running out of usable land for growing crops and the global water supply is under severe threat of depletion. Plenty was founded on the need to create a more sustainable way to grow food using less land and water. Plenty yields hundreds of acres of crops in a building the size of a big box retailer, without cutting down a single tree, and using a fraction of the water required in the field. It’s San Francisco-based farm uses 100% renewable energy, and its greens are stored in 100% recyclable packaging and shipped locally to minimize the transportation footprint. Plenty’s data analytics and machine learning capabilities deliver 200 years’ worth of data each year, helping to quickly iterate and improve farm yield, quality and efficiency.
“The FoodTech 500 was created to shine a spotlight on the leading global innovators across the AgriFoodTech ecosystem, from farm to fork, who are making impactful solutions to better our food system,” said Alessio D’Antino, Forward Fooding founder and CEO. “This year’s list focused on understanding the driving factors behind the leading companies’ success and innovation, and we were thrilled to learn more about the top industry players, like Plenty, that are transforming our food system.”
The list represents 38 technology domains within the AgriFood space, including the broad categories of alternative proteins, farm management and precision farming, and vertical/indoor farming. The full ranking and more data about the 2020’s FoodTech 500 and its methodology can be found here.
About ForwardFooding
Forward Fooding is the world’s first collaborative platform for the food & beverage industry via FoodTech Data Intelligence and corporate-startup collaboration. Data services include The FoodTech Data Navigator data subscription service and facilitating corporate-startup collaboration through bespoke innovation programs and FoodTech consultancy.
To learn more visit: www.ForwardFooding.com
About Plenty
Plenty is an American farming technology company that frees agriculture from the constraints of land, weather, seasons, time, distance, pests, natural disasters, and climate. The company’s plant scientists, engineers, and farmers have developed its indoor vertical farming technology to grow nutrient-rich and pesticide-free plants with extraordinary flavor. The Plenty platform is designed to grow multiple crops in a building the size of a retail box store, yielding hundreds of acres using a fraction of the water and other precious resources. Plenty's flagship farm and headquarters are located in South San Francisco, and the company operates the largest of its kind Research and Development farm in Laramie, Wyoming. Plenty is currently building the world's highest-output, vertical, indoor farm in Compton, California.
View source version on businesswire.com:https://www.businesswire.com/news/home/20210301005069/en/
CONTACT: Jane Gideon
KEYWORDS: CALIFORNIA UNITED STATES NORTH AMERICA
INDUSTRY KEYWORD: ENVIRONMENT TECHNOLOGY OTHER TECHNOLOGY FOOD/BEVERAGE AGRICULTURE SUPPLY CHAIN MANAGEMENT RETAIL NATURAL RESOURCES SCIENCE OTHER SCIENCE
SOURCE: Plenty
Copyright Business Wire 2021.
PUB: 03/01/2021
Aquaponics In The Heart of Zurich
Umami creates microgreens in the city centre
They produce greens, but they travel to work by streetcar and don't need to put on weatherproof clothing. That's because Umami employees will harvest vegetables and herbs already in the early growth stages, as so-called microgreens. And they do so in a largely self-built facility, on the 4th floor of an office building in Zurich's Kreis 4 district.
Full-time producers instead of restaurant operators
In the beginning, the three friends Manuel Vock, Robin Bertschinger and Denis Weinberg wanted to open a restaurant. They wanted to produce half of the products themselves. At the same time, Manuel Vock was researching aquaponics systems for his bachelor's thesis. He introduced the principle to his friends, and the team began building a prototype set-up in a former archive in 2016.
That was the end of their restaurant plan and at the same time the beginning of completely self-produced food. The guys grew several varieties of microgreens and sold them to restaurateurs who were excited to have a regional product. "Up to that point, microgreens from the Netherlands were the only alternative," says Luca Grandjean, who joined the team of Umamigos (as Umami employees call themselves) in 2019.
The aquapinic facility / Image: Umami
Microgreens
Microgreens, unlike sprouts, grow on a substrate or in soil, require light and nutrients, and are consumed without roots. They are vegetables or spice plants that are harvested immediately after their cotyledons develop. As a result, microgreens contain a high concentration of vitamins and trace elements. The small plants are used as nutritional supplements and can add sweetness and spice to different dishes.
Fish excrement as fertilizer
Regionality is not the only plus of the little plants. Umami grows the microgreens in a cycle based on nature; the only input is fish feed. But even this is actually food waste and, additionally, insects that Umami produces via scraps.
African cichlids (tilapias) and other fish species swim in various tanks, and their excretions enrich the water with nitrogen and other micronutrients. The enriched water flows into the system to the tray on which the microgreens thrive.
These are sown on a hemp-based substrate and positioned in hard trays so that their roots can touch the water, absorbing the nutrients. The water, now purified by the plants, flows back to the fish, who recharge it. Thanks to this recirculation system, only about 1% of the water needs to be replaced with fresh drinking water each month. "That's about two bathtubs full of water. Just what is lost to evaporation," Grandjean says.
Aquaponics
Aquaponics refers to a process in food production that combines raising fish in aquaculture and cultivating crops in hydroponics. There are various combinations, such as the cultivation of tomatoes and the production of tilapias, as described in this article.
Not just fish and microgreens are part of the 'ecosystem', as the Umamigos like to call their jungle. Mussels, shrimp, snails, algae and many other plants also contribute to the Umami ecosystem. "We are copying nature. Yet we have learnt that the more players there are in the cycle, the better the system works," says Luca Grandjean. This might seem to be a contradiction, but he explains: "If there are just two actors in the system and something happens to one of them, the system is quickly unbalanced."
Nomen est omen
Their most important element, he says, is Zurich's tap water; it sets the pace. "We have no soil percolation, 95% less water loss than conventional agricultural systems," Grandjean says.
Environmentally-friendly production, free of chemicals, strikes a chord with consumers. Above all, however, the products have to taste right, says Luca Grandjean. It's no coincidence that the three friends named their startup Umami when they founded it in 2015. The Japanese word means tasty or spicy, and is one of the five basic tastes, alongside sweet, sour, bitter and salty.
"The glutamate found in meat, for example, tastes umami," Grandjean explains. He adds: "The microgreens are very palatable and don't contain glutamate, but our fish do." He is referring to the license to sell fish that the Umamigos recently obtained.
For more information: https://www.eat-umami.ch/
Climate Corps America: The Urban Farms Transforming How America’s Most Vulnerable Communities Eat
Urban farms not only promote healthy eating but have the ability to transform industrial cities.
Louise Boyle
The microwave plays a significantly more important role to urban farming in Baltimore than you might first imagine.
“Our butternut squash comes from a seed which makes it little and easily microwaveable,” Gwen Kokes, food and farm programme director at Civic Works, told The Independent. “For our [customers] this is really important as it might be too expensive to turn on the gas to cook or the oven might not be working.”
The squash, along with a range of produce, is grown at Real Food Farm, one branch of Civic Works urban service corps program in Maryland’s largest city.
The farm started about a decade ago and spans eight acres in northeast Baltimore with four fields, more than 100 fruit trees, a greenhouse for seedlings, and eight “hoop houses” which, for the uninitiated, are a sort of passive greenhouse with crops planted directly in the soil but sheltered by heavy-duty plastic sheets stretched over frames.
The farm produces 5,000 pounds of fruit and vegetables each year to be sold for reduced cost at farmers’ markets in low-income neighbourhoods across Baltimore. A mobile market, operating out of a box truck, also visits all 12 senior centres in the city.
“In total, we distribute about 100,000 pounds of food every year,” says Ms Kokes. “We buy from other urban farms in a 50-mile radius, prioritising Black-owned farms. Sometimes we have donations from Hungry Harvest, a programme to reduce food waste from grocery stores, and we’ve been adding pantry and hygiene items so that it’s more of a one-stop shop.”
Civic Works is part of AmeriCorps, the federal agency for service and volunteering programmes in the US. To tackle the climate crisis, President Biden has called for “reinvigorating and repurposing” the agency into a so-called “Civilian Climate Corps” to provide jobs while ramping up clean energy and sustainability to “heal our public lands and make us less vulnerable to wildfires and floods”.
“Biden’s plan could be huge for us,” Ms Kokes said. “I think it can grow exponentially. There’s plenty of demand for these jobs.”
The non-profit also runs programmes to mentor students, fix up abandoned houses and makes homes safer for seniors by doing minor DIY like adding handrails and ramps.
AmeriCorps estimates that its existing network – 25,000 participants in about 130 programmes – could be scaled up to 500,000 young people and veterans over the next five years.
Around 19 million people in the US live in “food deserts”. The term is believed to have been coined in Scotland in the early 1990s by a public housing resident, referring to areas where healthy, fresh options are scarce and packaged and fast food has proliferated.
The term is now seen as having negative connotations, implying that “low healthy food access is a naturally occurring phenomenon, rather than the result of underlying structural inequities”, according to a 2018 study by John Hopkins. (Baltimore residents told researchers they preferred the term “Healthy Food Priority Areas”.)
Researchers also point to the systemic racism at the heart of Americans’ access to food. It’s difficult to improve diet and health, for example, if prices for nutritious food are far beyond your budget, and there’s no public transport to take you stores.
“The fact that predominantly black neighbourhoods, on average, have fewer stores and poorer quality [food] compared to their white counterparts means something,” Ashanté M. Reese, professor of sociology and anthropology at Spelman College who studies race and food inequity, told HuffPost .
Baltimore is one of America’s poorest cities. In 22 of the city’s 668 Census tracts, at least 40 per cent of residents live below the poverty line. Even before Covid, the unemployment rate in the poorest neighbourhoods hovered above 15 per cent, triple that of wealthier areas.
Lack of access to healthy food in Baltimore is one layer of racial inequality that has plagued the city since the early 20th century, when deliberate policies were put in place to separate the city’s white and Black residents.
In the city’s Greenmount East neighbourhood the average life expectancy is around 66 years while four miles away in the wealthier Roland Park, the average life expectancy is 84 years, according to Kaiser Health News.
That’s where organisations like Real Food Farm step in. Those who are unemployed or on low-incomes and using government nutrition assistance programmes get double the value for their dollar if it’s spent at the farmers’ market, for example.
Urban farms not only promote healthy eating but have the ability to transform industrial cities.
“Motor City” Detroit, once the backbone of the car industry, has suffered a well-documented decline since its mid-20th century heyday. But its industrial wastelands have been transformed by urban farming with at least 1,400 farms and gardens in the city. In Pittsburgh, Hilltop Urban Farm is set to become the largest urban farm in the country. Baltimore has around 17 urban farms and upwards of 75 community gardens that grow food, according to Baltimore magazine.
Civic Works’ role on the frontline of food insecurity meant that its teams were well-positioned to adapt during the Covid pandemic, delivering boxes of fresh produce and basic necessities to the most vulnerable at no cost. They also worked with public bodies and local charities to deliver donations.
“During lockdown, Baltimore City public school system had to get rid of those little cartons of milk really fast. We have thousands of customers so we focused on getting those out to them,” Ms Kokes said.
From March through the end of July, the programme’s teams ran a free programme delivering boxes of produce, meals and hygiene kits to about 1,000 households a week. They went on to launch a discounted local produce programme, delivering boxes with about $15-$20 of food for $5 with free delivery, mostly to seniors.
Urban farms will play a role in mitigating how climate change impacts urban areas. Cities are often several degrees hotter than rural areas due to the “urban heat island effect” caused by dark-coloured roads and buildings. Increasing vegetation cover can help curb rising temperatures.
Urban farms can also lower the risk of flooding during heavy downpours and help retain water in dry areas, according to a paper in the journal Earth’s Future.
Research in 2018 from Arizona State University and Google found that urban agriculture could save the energy equivalent of 9 million home air conditioning units and produce up to 180m tonnes of food globally. Along with supplying almost the entire recommended consumption of vegetables for city dwellers, it would cut food waste and reduce emissions from transportation of produce, the study found.
Maryland is among the states most vulnerable to climate change, facing both rising sea levels and heightened storm intensity. Government data predicts that Maryland’s sizeable farming community could suffer costly losses during extreme droughts and heat waves.
Ms Kokes says that more extreme and unpredictable weather has impacted their operations in recent years.
“With day-to-day farming, we have to get ‘swamp ready’,” she said. “2018 was the worst for Maryland farmers as the rain was astronomical. We took a huge hit. It was very humbling because we had to reckon with our limitations, and partner with others to be a reliable source of food.
“Irregular weather patterns especially in the spring make it really difficult to know when to plant. We’ve [also] had early frost in October. Our farmer Stewart is a very smart, science-oriented guy and thankfully, there’s resources that we can lean on to translate this unpredictability into clear language.”
Around 3,000 students from kindergarten to high school have visited Real Food Farm over the years to learn about agriculture. Separately, programmes like Future Harvest are preparing the farmers of the future. But it’s important that Real Food Farm’s mission stays relevant to the communities they are in, Ms Kokes said.
“Environmentalism, from our perspective and our work, has to be people-focused,” she said. “We’re not talking about weather patterns when people are hungry and just want affordable produce in their neighbourhood.”
Belgian Bio-Planet Now Sells Vertically-Farmed Coriander Too
For us, the story didn't end with sustainable basil.
Just under a year ago, Bio-Planet first introduced its basil to the market. This came from this Belgian store's self-developed vertical farm. "This cultivation method differs from conventional farming. It requires less water and space and fewer nutrients. That results in herbs with tiny ecological footprints. For us, the story didn't end with sustainable basil. We now have the technique down for coriander. We've been selling this second vertically-farmed herb since 19 February. That's in the Bio-Planet webshop and 31 stores", says a representative from this supermarket chain.
"Consistent, year-round quality"
"The Colruyt Group is the only retailer in Belgium with its a self-developed vertical farm. It grew basil plants for Bio-Planet last year. That was in a closed system, in two rows, one above the other. The group could, therefore, test out its vertical farm for a year. That was in all aspects, from production through logistics to sales. And the results are impressive. In a challenging year, we managed to guarantee a stable production of quality basil plants," says Jan Van Holsbeke, Bio-Planet's Manager.
"The global pandemic ensured it wasn't the easiest test year. We had to scale up our vertical farm. That's was due to the increased sales in our stores. At the same time, this demonstrates the power of indoor multilayer cultivation. We can create the perfect growing conditions, regardless of the weather. That means the herbs have consistent, year-round quality. And we can match production to demand." And demand there certainly was. More people bought fresh basil from Bio-Planet last year than the previous year.
"Coriander with a tiny environmental footprint"
Bio-Planet sees potential in this new farming method. They can grow herbs with a minimal ecological footprint. "Up to 20 times less space is needed the same number of plants. They also need 50% fewer nutrients and 90% less water. The herbs are 100% pure too because no pesticides are used," adds the company spokesperson.
"We integrated the farm into one of the group's distribution centres. So, transportation was cut five-fold. The farm uses purified rainwater that's collected on the DC's roof. It has self-developed, energy-efficient LED lighting and an innovative ventilation system. These make the farm very energy efficient. Moreover, the system runs on 100% green electricity. This is generated by wind turbines and solar panels."
“All these factors make the farm and its herbs very sustainable. That's crucial for Bio-Planet. We want to offer our shoppers sustainable, local, innovative products. We think other herbs and even leafy green vegetables can be vertically-farmed too. This, however, requires more research and investment. Also, the technology has to be further developed," concludes Jan.
VIDEO: Indoor Ag Sci Cafe Discusses Indoor Farming In Mexico With Karla Garcia, Hort Americas
“Indoor Farming in Mexico: Current Status and Opportunities”
With Karla Garcia
Microgreens FLN & Hort Americas
This presentation ‘Indoor Farming in Mexico: Current Status and Opportunities’ was given by Karla Garcia (Microgreens FLN & HortAmericas) during our 27th cafe forum on February 23rd, 2021. Indoor Ag Science Cafe is organized by the OptimIA project team funded by USDA SCRI grant program.
The Café presentations are available from YouTube channel.
Upcoming Cafes:
March 30, 11am EST – ‘USDA SBIR (Small Business Innovation Research) Grants Program Overview’ by Dr. Steven Thomson & Melinda Coffman (USDA NIFA)
Interested in giving a talk to share your thoughts and experiences? Contact them
Dr. Peter Quinn Appointed As New Chair of CHAP
Peter holds an MBA and BSc(Hons) & Ph.D. in Epigenetics & Microbiology and has published on the importance of nutrition to improve health and wellness in society
Crop Health and Protection (CHAP) one of the four UK Agri-Tech Centres of Innovation, has appointed Dr. Peter Quinn, CEO of Genius Foods, to be its new Non-Executive Chairman, following the retirement, earlier this year, of John Chinn.
Peter brings extensive business leadership experience to the CHAP Board, having held Chief Executive, Managing Director, and Non-Executive Director roles. He has a background in creating enterprise value across a range of complex FMCG brand and private label markets in food and drink, manufacturing and retail, biotech, and agri-tech.
He is currently CEO of Genius Foods and was previously divisional MD of Samworth Brothers. In addition, he holds several NED positions in the Agri-Tech/Produce sector. He is an expert in transformational turnarounds and the creation of growth and value strategies through organizational alignment and ingenuity.
He is also passionate about building business cultures committed to people and has served on the Boards of BITC Charities, dedicated to creating opportunities for disadvantaged young people through education and personal development.
Peter holds an MBA and BSc(Hons) & Ph.D. in Epigenetics & Microbiology and has published on the importance of nutrition to improve health and wellness in society.
As Chairman of CHAP, he is committed to the vital function of science, technology and collaborative innovation to transform UK agriculture and sustainable food production.
CHAP CEO Fraser Black said: “CHAP is experiencing an exciting period of growth and development and Peter is well-placed to help us cement our position at the centre of the UK agritech innovation sector. His commercial, non-profit, and academic experience are a perfect fit for CHAP. I look forward to working with him to ensure CHAP continues to act as a catalyst for innovation in UK agribusiness. This will enable us to achieve our vision of making the UK a global leader in the development of applied agri-technologies, to help secure our future by nourishing a growing population sustainably while delivering economic, environmental and health benefits to society.”
Peter Quinn said: “I am delighted to be appointed to the Board of CHAP as Non-Executive Chairman. There has never been a more critical time to invest in the future of UK agriculture and sustainable food production. CHAP plays a pivotal role in creating world-class innovations through collaborations between scientists, farmers, and industry to transform the productivity of UK agriculture. CHAP is the nexus for new ideas and ingenuity that will deliver agricultural solutions for tomorrow’s world.”
About Crop Health and Protection (CHAP)
Crop Health and Protection (CHAP), funded by Innovate UK, is one of four UK Agri-Tech Centres. CHAP’s vision is for the UK to be a global leader in the development of applied Agri-Technologies, to help secure our future by nourishing a growing population sustainably while delivering economic, environmental and health benefits to society. CHAP acts as a unique, independent nexus between the UK government, researchers, and industry, building innovation networks to identify and accelerate the development of cutting-edge solutions to drive incremental, transformative, and disruptive changes in sustainable crop productivity.
Website: www.chap-solutions.co.uk Twitter: @CHAP_Enquiries
For further information contact:
Darren Hassall (Marketing Manager): darren.hassall@chap-solutions.co.uk
Tel: +44 (0)7866 799152
IGS Signs Significant Export Deal With Jungle To Supply French Retail Market
The first growth towers will be in production by early 2021, scaling incrementally to a minimum of 17 towers by the end of 2021
Scottish Technology to Create One of
Europe’s Largest Vertical Farms
Edinburgh, Scotland – 17 September 2020 - Indoor agritech specialist IGS has today announced a significant export deal with experienced French urban agriculturalists, Jungle. The multi-million-pound deal will introduce IGS indoor growing platforms to Jungle’s operations, initially outside Paris, to grow a variety of crops to supply major French retailers.
The first growth towers will be in production by early 2021, scaling incrementally to a minimum of 17 towers by the end of 2021. Jungle will grow a range of herbs and salads to supply select retailers across France. The company will utilize the patented IGS plug-and-play vertical farming platform to widen its portfolio and produce new varieties through an ongoing program of crop trials.
Jungle’s indoor growing operations will also develop a variety of botanicals to provide natural ingredients to a world-leading flavor and fragrance business.
Jungle’s ethos is focused on sustainable food production, with superior quality of crops grown through a more efficient model, re-localizing the supply chain, considerably reducing waste and using no chemicals. With extensive experience in the indoor growing space, the company has achieved recognition in the highly competitive retail market in France for the quality of its produce.
To increase the scale of production sustainably, while maintaining its commitment to high-quality, delicious, and pesticide-free produce, the company conducted an extensive search to identify the best technology partner.
After a thorough and competitive review of the market, IGS was selected as the most economically viable and environmentally friendly system capable of meeting Jungle’s requirements to reach the industrial scale required by its customers. IGS offers its customers a highly controllable platform, designed to maximize productivity whilst minimizing energy and water consumption.
When completed, the nine-meter-high growth towers will be housed alongside a 1,500 m2 service area on Jungle’s site outside Paris. This will provide approximately 5,200 m2 of growing space, producing up to 425 tonnes per annum when fully operational, making it one of the largest vertical farms in Europe.
IGS CEO, David Farquhar, commented: “In recent months, global markets have been challenged considerably and export agreements have become more difficult to fulfill. The announcement of this deal is an exciting one not just for IGS, but also for the UK’s Agri-tech sector as we showcase our international capability to support economic recovery post-coronavirus. The Jungle team has a strong reputation for excellence and sustainability both of its produce and approach.
“Jungle needs a reliable, productized system that can meet its ambitious growth plans in France and beyond and IGS has proven to be exactly that, following a rigorous selection process. This deal is proof that our unwavering commitment to innovative, practical design, based on a deep understanding of delivering optimum growing conditions, is what customers want. The deployment of the system for Jungle begins immediately and I am encouraged by how well our teams are collaborating as we move forward together.”
Gilles Dreyfus, CEO of Jungle commented: “This partnership agreement is a significant step forward for Jungle and our ability to deliver at scale for our customers. We have established Jungle as a grower of superior produce with major French retailers and have plans to build on this reputation as we look at operations in other regions. We are proud to be innovators in our sector and it is important that we find people and organizations that share this same vision.
“We undertook a very serious assessment of the market and IGS was a clear leader in our eyes. What we can offer our customers through the partnership with IGS puts us at a different level in terms of scale, flexibility, and potential to expand and develop our produce portfolio. The IGS approach, both with the technology and the team, is such that we feel completely aligned and able to work collaboratively now and into the future.”
IGS has received recognition from the Scottish Government for the exciting export opportunities it is bringing to the Scottish market. Trade Minister Ivan McKee MSP said: “This significant contract underlines IGS’ standing as a global leader in agricultural innovation which will help everyone farm more sustainably. IGS’ growth has been driven by a focus on quality, innovation and scientific expertise and shows what Scottish companies can achieve with the right support in place.
“International exports have a central role to play in our economic recovery from COVID-19. The Scottish Government has set an ambitious target of increasing the value of exports from 20 percent to 25 percent of GDP by the end of the decade and I look forward to IGS helping us achieve that goal.”
In addition, Scottish Enterprise which has worked closely with IGS since 2018, welcomes this strategic export announcement. Neil Francis, International Trade Director at Scottish Enterprise, said: “We congratulate IGS on securing this export deal, which will ensure the company’s innovative technology is delivered to a global marketplace.
“Scottish Enterprise has worked closely with IGS over the past couple of years, both through our investment arm, the Scottish Investment Bank, and Scottish Development International. We look forward to continuing support IGS as it demonstrates its capabilities in the agritech sector.
“International trade will be key to Scotland’s economic recovery and help deliver the future, sustainable growth we all want to see. Working with our partners, Scottish Enterprise will continue to do all we can to support companies access overseas markets.
Ends
Notes to editors:
For more information: please contact Kate Forster, IGS on kate@intelligentgrowthsolutions.com or call +44 7787 534 999 or Gilles Dreyfus, Jungle on gdreyfus@jungle.bio.
About IGS:
Founded in 2013, IGS brought together decades of farming and engineering experience to create an agritech business with a vision to revolutionize the indoor growing market. Its commitment to innovation has continued apace and it has evolved the applications of its technology beyond agriculture to create solutions for a wide variety of indoor environments which enhance life for plants and people alike.
IGS launched its first vertical farming demonstration facility in August 2018.
For more information visit www.intelligentgrowthsolutions.com or connect with us on Twitter and LinkedIn.
About Jungle:
Jungle originated in Portugal in 2016 and maintains a Research and Development facility in Lisbon. It identified strong demand from the retail market in France and opened operations there in 2019. Further European operations are under consideration as the demand for healthy, sustainable and locally-sourced produce increases.