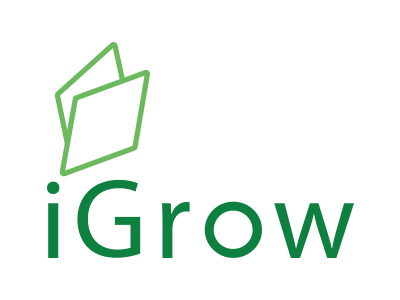
Welcome to iGrow News, Your Source for the World of Indoor Vertical Farming
Sustainable Agriculture Technology Can Help Egypt’s Water Crisis
Suweilem said hydroponics is an ideal way to deal with water scarcity and climate change, stressing the need for Arab countries that suffer from a shortage of agricultural lands due to their desert nature, including Egypt, to rely on this type of agriculture
The project of an Egyptian student consisting of using the Sinai environment for sustainable agriculture with the use of less water may be a solution to Egypt’s water scarcity problem.
A picture shows the UAE's al-Badia Farms in Dubai, an indoor vertical farm using innovative hydroponic technology to grow fruits and vegetables all year round, on August 4, 2020. - Badia Farms is the Middle East's Based in downtown Dubai, the farms ground-breaking methods sustainably grow crops without sunlight, soil or pesticides. The farm uses 90% less water compared to open field farming. The companys vision is to revolutionise the agricultural industry in Middle East to provide a solution for the regions food security. Photo by KARIM SAHIB/AFP via Getty Images.
March 6, 2021
Egyptian student Nada Ayman's project dubbed the Cultural Desert Gravity Center uses the Sinai environment as its main agricultural tool. It also won the 36th Cycle at the 2020 World Architecture Festival.
The project — designed to be built as a cultural center in Wadi el-Weshwash in the town of Nuweiba in south Sinai — uses the surrounding environment, including the mountains, to build an integrated center providing organic nutritional products and natural herbs used in manufacturing medicines and fragrance products. A tourist and entertainment complex offering various educational and entertainment activities is also on the horizon, said Ayman.
Ayman, a student at the Faculty of Applied Arts at Zagazig University, told Al-Monitor via phone she chose the project based on the spiritual meaning of mountains.
She noted, “I was nominated by my professors to participate in the architecture competition. The World Architecture Festival has been in place since 2006, and it has a section dedicated to interior design.”
Ayman said the project consists of a hydroponic farm, which is a system to grow crops without soil. The roots of the plants grow in a liquid nutrient solution that is recycled and reused repeatedly through plants. The hydroponic farm produces medicinal plants, used in the manufacture of medicine, and crops that bear fruit to be served with meals in the farm’s restaurant.
Ayman added, “This type of agriculture uses 70% less water than regular agriculture to produce 100% organic products without using soil or fertilizers. Edible products are served at the restaurant of the farm, while herbal and fragrance products are used to manufacture therapeutic oil for the therapeutic center.”
She chose Wadi el-Weshwash because it is located next to a region of rich valleys whose water and minerals can be utilized in organic agriculture.
The design of the complex features a library, a restaurant and an art studio, Ayman said, noting that the design reached the final stage of the competition and was chosen among five others.
Atef Suweilem, a professor of agricultural engineering at Zagazig University, said the hydroponic agricultural method consists of either growing the seeds of plants or herbs in a nutritive water solution containing the main 12 to 16 nutrients plants need — or growing the plants in an inert solid material so they do not interact with the nutritive solution. Using this method does not require the use of chemical fertilizers, the surplus of which usually seeps into the soil in traditional agriculture, according to Suweilem.
Hydroponic agriculture also protects the plants from pests that live in the soil, as is the case in traditional agriculture, he said, adding that ancient Egyptians were the first to know hydroponics, and perhaps the papyrus plant is the most prominent example of this type of agriculture.
Suweilem said hydroponics is an ideal way to deal with water scarcity and climate change, stressing the need for Arab countries that suffer from a shortage of agricultural lands due to their desert nature, including Egypt, to rely on this type of agriculture.
Yasser Ahmed, an expert in agriculture and a former professor at the Egyptian Agricultural Research Center, stressed the need for Egypt to turn to hydroponics in the near future, as it helps save water and energy and increases productivity. Ahmed said hydroponic agriculture uses 95% less water compared to traditional agriculture. Leaf crops consume about 30% less water than traditional agriculture, and if the cultivation of these crops is expanded on the hydroponic farm, that method can be used widely, he said.
“This is the future of agriculture. We do not want to depend on imports. We hope we will have local production throughout the year, regardless of climate change, weather, rain or drought,” Ahmed said.
Of all sectors in Egypt, the agricultural sector consumes the largest share of water — meaning it consumes roughly more than 85% of the country’s share of irrigation water. Although Egypt has lost some of its fertile lands due to urban sprawl, there is an attempt to balance this through the expansion of agricultural areas in the desert. The total cultivated land was estimated at 9.3 million acres — 3.2 million acres of which are in lands recently reclaimed by the state and 6.9 million acres in other lands, according to the latest 2019 statistics of the Central Agency for Public Mobilization and Statistics.
Agriculture is essential to the Egyptian economy, as its added-value represents about 14.5% of the gross domestic product. In 2016, agricultural income reached 256.9 billion Egyptian pounds ($16.3 billion). The sector also employs 29.6% of the working population and represents 11% of all exports. Because of the water shortage, the government issued measures in January 2018 to limit the cultivation of water-intensive crops such as rice.
Rasha Mahmoud
@R_ma7moud200
TOPICS COVERED Agriculture and farming Water Issues Sinai
Read more: https://www.al-monitor.com/pulse/originals/2021/03/egypt-project-agriculture-sinai-water-scarcity-crisis.html#ixzz6oQLQrjPl
Fresh Impact Farms Awarded Arlington's First Agriculture Grant
Arlington County received its first-ever agriculture fund grant from the state, money that will go to county-based Fresh Impact Farms.
Operating since 2018, Fresh Impact Farms uses hydroponic technology to grow a variety of speciality herbs, leafy greens, and edible flowers indoors. (Mark Hand/Patch)
ARLINGTON, VA — Arlington County received its first-ever agriculture fund grant from the state, money that will go to Fresh Impact Farms, an Arlington-based company that plans to double production at its indoor growing facility.
Virginia Gov. Ralph Northam announced Monday that he had awarded an Agriculture and Forestry Industries Development, or AFID, Fund grant to Arlington totalling $15,000 to be given to Fresh Impact Farms. The company will receive a total of $30,000 from the government, with Arlington County matching the state grant with local funds.
"Agriculture continues to be a key driver of our economic recovery in both rural and urban areas of our commonwealth," Northam said Monday in a statement. "Innovative, dynamic businesses like Fresh Impact Farms are demonstrating how exciting new opportunities can grow out of pandemic-related challenges."
"I congratulate the company on their success and am thrilled to award the first-ever AFID grant to Arlington County to support this expansion," the governor said.
In recent decades, Arlington County has grown into one of the most densely populated counties in the nation. Up until World War II, Arlington still had plenty of farmland. But over the past 60-plus years, the only farming in the county has been of the backyard and patio variety or in the community gardens in the Four Mile Run area.
Operating since 2018, Fresh Impact Farms uses proprietary hydroponic technology to grow a variety of specialty herbs, leafy greens, and edible flowers indoors.
"Governor Northam's award to Fresh Impact Farms, Arlington's only commercial farm, is an innovative way to celebrate unique uses of technology to help a small business pivot during the pandemic," Arlington County Board of Supervisors Chairman Matt de Ferranti said. "I am thrilled that Fresh Impact Farms is growing and looking to the future of a sustainable food supply."
The company will invest a total of $137,500 as part of the expansion, which will include a second grow room, a larger production facility, and an educational hub where customers, after the pandemic, will be able to see how their food is harvested.
Fresh Impact Farms' community-supported agriculture or CSA, program focuses on leafy greens and home kitchen-friendly herbs and has grown them steadily since the program's creation last April. Along with residential customers, the company now has smaller wholesale clients in the Washington, D.C., area.
The future is bright for urban agriculture, said Ryan Pierce, founder of Fresh Impact Farms, located in the back of a Lee Highway strip mall. (Mark Hand/Patch)
After the start of the pandemic, Fresh Impact Farms decided to shift its business model to a CSA delivery service in order to continue generating revenue.
"Seizing the opportunity created by more people cooking at home, the company initiated a Community Supported Agriculture program targeting area residents," the governor's office said.
"Now, with vaccinations underway and the restaurant industry poised to rebound, Fresh Impact Farms is expanding, which will allow the company to resume supplying their restaurant customers, while also meeting new demand through their CSA program," the governor's office said.
Over the next three years, the company expects to grow an additional 10,500 pounds of Virginia-grown leafy greens, herbs, and edible flowers for restaurant and CSA customers.
The future is bright for urban agriculture, said Ryan Pierce, founder of Fresh Impact Farms, located in the back of a Lee Highway strip mall.
"The support and generosity from the Commonwealth and Arlington County will be valuable as we expand our production and move towards a hybrid model of serving both the needs of restaurants and consumers," Pierce said in a statement. "As the owner of a local food business, nothing gets me more excited than seeing the community come together in support of local food."
The funds from the Arlington County Industrial Development Authority, together with the state grant, represent "an important investment in urban agriculture, sustainability, and technology," Arlington County IDA Chair Edwin Fountain said in a statement. "This project will advance the County's innovative and forward-thinking approach to developing new sectors of economic activity in Arlington."
SweGreen Becomes Partner In Viable Cities
Viable Cities is an innovation program for smart and sustainable cities. The aim is to accelerate the transition to inclusive and climate-neutral cities by 2030 with digitalization and citizen engagement as enablers
03-03-2021 | Swegreen
SWEDEN- Farming as a Service becomes a new tool in the fight against climate change as the FoodTech enterprise SweGreens joins the Swedish Strategic Innovation Program, Viable Cities.
Viable Cities is an innovation program for smart and sustainable cities. The aim is to accelerate the transition to inclusive and climate-neutral cities by 2030 with digitalization and citizen engagement as enablers.
SweGreen is an innovation company based in Stockholm focused on futuristic, smart, and circular solutions for controlled-environment urban farming. SweGreen own technologies which enables integration of smart vertical farming solutions into real-estate properties. Recently SweGreen has introduced a service for urban production of leafy greens, called Farming as a Service (FaaS), which allows clients to produce greens under their license and close to the city population.
Sweden inspires many other nations and has a leading position in the transition of urbanization context and fighting the climate change through smart and sustainable solutions that could be implemented in cities, says Sepehr Mousavi, member representative, and Chief Sustainability Officer at SweGreen.
Smart urban farming in infrastructure-integrated settings and by harnessing urban resources could be an exponential factor in localizing the food chains in Sweden and cutting back the carbon footprint associated with our food production and supply, he continues.
Viable Cities is growing steadily and new members like SweGreen are joining the current member pool, the likes of Swedish municipalities, Swedish universities and research institutes and other leading innovation companies. Running from 2017 to 2030, the program gathers partners from industry, academia, public and civil society organizations, and jointly funded by the Swedish Innovation Agency (Vinnova), the Swedish Energy Agency and Formas with a total investment of 1 billion SEK (about 100 million EUR).
Viable Cities is coordinated by KTH Royal Institute of Technology.
Together with our member organizations and other stakeholders, we aim to accelerate the transition to climate-neutral cities by 2030 with a good life for all within planetary boundaries, says Olga Kordas, Program Director of Viable Cities and a researcher at KTH Royal Institute of Technology.
Transforming our food systems are one of the key challenges, Olga Kordas continues, and we are happy to be joined by SweGreen to co-create solutions for the future.
Andreas Dahlin, CEO of SweGreen, highlights:
We are honored to be part of such a committed and influential strategic program and partner pool as Viable Cities’. We hope to contribute with innovations around the concept of Farming as a Service, which really could impact food production today and in the future. The ability to produce fresh and nutrient food close to the consumer will be one of the big missions for the food industry in the upcoming decades.
For more information:
Sepehr Mousavi, CSO SweGreen, sepehr.mousavi@swegreen.se +46(0)73-3140043
Andreas Dahlin, CEO SweGreen, andreas.dahlin@swegreen.se +46(0)70-9240032
Åsa Minoz, Head of Communications, Viable Cities, asa.minoz@viablecities.se +46(0)722108826
SweGreen is a Swedish GreenTech company that offers digital, efficient, and circular solutions for urban cultivation in a closed and controlled environment. By combining computer science, advanced technology, and plant sciences, SweGreen contributes to the development of urban sustainable food production. The company was established in 2019 and provides consumer products such as various leafy greens and herbs under the brand of Stadsbondens. www.www.swegreen.com
Source and Photo Courtesy of Swegreen
A Fully Automated Three-Dimensional Vertical Farm Comes Into Operation
Eponic Agriculture Co. Ltd is a supplier of indoor farming equipment. Alice, the company's director, introduced the recently fully automated production system of a stereochemical vertical farm
Eponic Agriculture Co. Ltd is a supplier of indoor farming equipment. Alice, the company's director, introduced the recently fully automated production system of a stereochemical vertical farm.
"The current three-dimensional indoor farms on the market are based on semi-automated workflow, with some links requiring additional equipment configuration and no continuity in the whole planting system. In order to solve this problem, we developed and designed a complete automated planting system, including the processes from sowing to planting, full-spectrum planting light control, fertilization, harvesting, and cleaning. Which are all done by automated equipment. Whereas all procedures can be controlled by intelligent software with real-time monitoring, data collection, and many other functions."
Benefits of an automated farm
When talking about the advantages of the automated equipment, Alice said, "Take our recently built 20-layer vertical farm as an example. First of all, the mechanical sowing time is 10 times-30 times faster than manual sowing. And on top of that, the use of automated equipment can realize precise planting and efficient communication of multi-layer planting surfaces. The 20-layer vegetable trays are automatically transferred to the ground for uniform watering, harvesting, and cleaning. This greatly improves productivity.
Secondly, the use of lift trucks is required when handling high-level crops. There are certain safety hazards in using lift trucks in a small space. While operating the automated equipment, only a tablet computer is needed to control the whole planting process, which is much safer and more convenient."
Although automated vertical farm systems have many advantages, their application in China is not yet popular. "In terms of production design, we have gone through countless experiments to design the most suitable software program. As well as hardware equipment for practical planting applications. Luckily after a long period of research, we finally chose the most cost-effective and suitable materials. The R&D investment is large and time-consuming.”
From a cost point of view, according to Alice, a fully automatic system is 2-3 times higher in costs than the semi-automatic system which is currently used more often. Most traditional agricultural companies find it difficult to accept such high initial costs. Thirdly, the automated system requires high technical requirements for farm managers. Managers need to have an understanding of both planting technology and software. Alice adds: “It is for these three reasons that the application of fully automated stereoscopic systems is not very common in China and other countries."
Automated planting
"Although the application is not yet widespread, I think fully automated stereoscopic planting is a trend. Urbanization has led to a reduction in arable land and soil pollution has triggered problems with pests and pesticide residues in fruits and vegetables, and the development of three-dimensional agriculture is the only way to maximize and optimize output in a limited area. Currently, stereoscopic planting plants still require a lot of manual labor to operate. As labor costs rise and planting techniques require more precision, the use of automated equipment will be a future trend," Alice notes.
"Automated systems are a trend, not only in China but also globally. Urbanization has been moving forward, in the face of soil pollution, pesticides and pests, etc. The planting area is gradually reduced and three-dimensional agriculture must be developed in order to quantify planting. Three-dimensional agriculture can be located near the city, and reduce the transport distance, people can eat the freshest vegetables, to achieve local supply. Therefore it is necessary to promote automated, intelligent planting systems in order to achieve efficient planting and sustainable development." Alice said.
Industry experience
Eponic Agriculture Co. Ltd's head office, Dahua Intelligent Electronics, has a twenty-five-year history division. The team has been focusing on the development and production of intelligent control systems and industrial lighting. Alice said that based on years of technical foundation, we developed full-spectrum LED planting lights which have been approved and applied by the USDA. Over the years, we have received technical support and affirmation from several agricultural doctors from Europe and the United States, focusing on the development and production of automated stereoscopic planting equipment.
According to Alice, the company has laboratories and showrooms in the US, Australia and Africa. This year, the company is planning on opening new showrooms and laboratories in Europe. “We are expanding our global reach and continue to optimize our growing systems to be a better supplier of fully automated growing equipment."
For more information:
Eponic Agriculture Co. Ltd
Alice Ou, Director
aliceou@eponicagriculture.com
www.eponicagriculture.com
Author: Rebekka Boekhout
© VerticalFarmDaily.com
Belgian Bio-Planet Now Sells Vertically-Farmed Coriander Too
For us, the story didn't end with sustainable basil.
Just under a year ago, Bio-Planet first introduced its basil to the market. This came from this Belgian store's self-developed vertical farm. "This cultivation method differs from conventional farming. It requires less water and space and fewer nutrients. That results in herbs with tiny ecological footprints. For us, the story didn't end with sustainable basil. We now have the technique down for coriander. We've been selling this second vertically-farmed herb since 19 February. That's in the Bio-Planet webshop and 31 stores", says a representative from this supermarket chain.
"Consistent, year-round quality"
"The Colruyt Group is the only retailer in Belgium with its a self-developed vertical farm. It grew basil plants for Bio-Planet last year. That was in a closed system, in two rows, one above the other. The group could, therefore, test out its vertical farm for a year. That was in all aspects, from production through logistics to sales. And the results are impressive. In a challenging year, we managed to guarantee a stable production of quality basil plants," says Jan Van Holsbeke, Bio-Planet's Manager.
"The global pandemic ensured it wasn't the easiest test year. We had to scale up our vertical farm. That's was due to the increased sales in our stores. At the same time, this demonstrates the power of indoor multilayer cultivation. We can create the perfect growing conditions, regardless of the weather. That means the herbs have consistent, year-round quality. And we can match production to demand." And demand there certainly was. More people bought fresh basil from Bio-Planet last year than the previous year.
"Coriander with a tiny environmental footprint"
Bio-Planet sees potential in this new farming method. They can grow herbs with a minimal ecological footprint. "Up to 20 times less space is needed the same number of plants. They also need 50% fewer nutrients and 90% less water. The herbs are 100% pure too because no pesticides are used," adds the company spokesperson.
"We integrated the farm into one of the group's distribution centres. So, transportation was cut five-fold. The farm uses purified rainwater that's collected on the DC's roof. It has self-developed, energy-efficient LED lighting and an innovative ventilation system. These make the farm very energy efficient. Moreover, the system runs on 100% green electricity. This is generated by wind turbines and solar panels."
“All these factors make the farm and its herbs very sustainable. That's crucial for Bio-Planet. We want to offer our shoppers sustainable, local, innovative products. We think other herbs and even leafy green vegetables can be vertically-farmed too. This, however, requires more research and investment. Also, the technology has to be further developed," concludes Jan.
Join Harry Duran, Host of Vertical Farming Podcast, As He Welcomes To The Show Founder of Heron Farms, Sam Norton
It is the mission of Heron Farms to create a sustainable agricultural system and restore the marsh using earth’s most abundant resource: seawater
Season 2 Episode 25 Description
Join Harry Duran, host of Vertical Farming Podcast, as he welcomes to the show Founder of Heron Farms, Sam Norton. It is the mission of Heron Farms to create a sustainable agricultural system and restore the marsh using earth’s most abundant resource: seawater.
In this episode, Harry and Sam talk all about sea beans, Sam’s fact-finding mission to Bangladesh to learn more about how seawater crops are grown, and the work Heron Farms is doing with other brands to help rebuild salt marshes across the globe.
VERTICAL FARMING PODCAST
Listen & Subscribe
Smart Agriculture Startup Bowery Farming Hires A Google Veteran As CTO
The hire comes after a year of accelerated growth at Bowery, with retail sales at outlets like Whole Foods rising 600% and e-commerce sales via Amazon and others increasing fourfold, the company says, while declining to disclose its actual sales or production figures.
One goal of high-tech indoor farming startup Bowery Farming is to use artificial intelligence and machine learning to enhance its crop yields and reduce costs. So the five-year-old Manhattan-based company has hired Google and Samsung veteran Injong Rhee as its new chief technology officer.
Rhee, who was previously Internet of Things VP at Google and chief technologist at Samsung Mobile, will focus on improving Bowery’s computer-vision system and other sensors that analyze when plants need water and nutrients, while also looking to apply the company’s accumulated historical data to new problems.
Bowery grow room near Baltimore
“Agriculture is sitting at the crux of the world’s most challenging problems like food shortages, climate change, water shortages, a lack of arable space,” Rhee tells Fortune about his decision to join the startup. “These are very challenging problems, and all of these are relevant to what Bowery tackles every day. Any advances we make here lead to a better world.”
There’s also the matter of the kale, Rhee adds.
Bowery so far has focused on growing and selling green leafy vegetables like lettuce, arugula, and kale, though it aims to add other categories of produce soon. “It was an eye-popping experience,” Rhee says of his first time trying Bowery’s kale. “How can it be so sweet and so crunchy. That was amazing.”
The hire comes after a year of accelerated growth at Bowery, with retail sales at outlets like Whole Foods rising 600% and e-commerce sales via Amazon and others increasing fourfold, the company says, while declining to disclose its actual sales or production figures. With two large warehouse-size farms in operation, in New Jersey and Maryland, Bowery is on the verge of opening its third indoor growing center in Bethlehem, Pa. The startup claims its high-tech methods, though more expensive than growing outdoors, create farms that are more than 100 times as productive per square foot as traditional outdoor farms.
“COVID was an accelerator of trends,” Bowery CEO and founder Irving Fain says. The pandemic disrupted food supply chains stretching across the globe, giving an advantage to Bowery, which sells its produce within just a few hundred miles of each farm, he says. “That amplified and accelerated a trend towards simplifying supply chains, and creating a surety of supply.”
But Bowery also faces a host of competitors, from other indoor farming startups like AeroFarms and Gotham Greens, to more traditional ag companies like John Deere and Bayer’s Monsanto, all fueling a movement toward precision farming. If one-quarter of farms worldwide adopted precision agriculture using A.I. and other data-crunching methods by 2030, farmers’ annual expenses would decline by $100 billion, or as much as 4% of the sector’s total expenses, while saving water and reducing greenhouse gas emissions, a recent study by McKinsey found.
Rhee spent 15 years as a professor of computer science at North Carolina State University, where he helped develop core Internet standards for transporting data at high speeds. He joined Samsung in 2011 where he helped lead a wide range of projects including the Bixby digital assistant, Knox security app, and Samsung Pay mobile payments service. He moved to Google in 2018 as an entrepreneur-in-residence to focus on Internet of Things projects.
Bowery has raised over $170 million in venture capital from a mix of tech figures like Amazon consumer CEO Jeff Wilke and Uber CEO Dara Khosrowshahi, well-known restaurateurs such as Tom Colicchio and David Barber, and venture capital firms including Temasek, GV, and General Catalyst.
How Vertical Farming Is Taking Off
Food supply chains are under more scrutiny than ever in the era of coronavirus and Brexit. The vertical farming movement offers solutions to some of the biggest challenges facing agriculture today
By George Nott
5 February 2021
Food supply chains are under more scrutiny than ever in the era of coronavirus and Brexit. The vertical farming movement offers solutions to some of the biggest challenges facing agriculture today
This feature is the first in a two-part series on the future of farming
Michiel Peters has been fielding some frantic calls in recent weeks. “People are saying, ‘You have to come now! We’re sorry we didn’t call you a year earlier!’” the CEO of vertical farming company PlantLab reports.
It seems vertical farming has reached a tipping point. For a long time, any consideration of the method soon ended with unit economics. But the price of produce has been rapidly falling – to the point that it’s now beginning to compete with traditional farms. And the unique advantages of vertical farming are suddenly coming into sharp relief for manufacturers, suppliers and retailers. So much so that the sector is preparing for a huge boom in interest and investment.
Indeed, demand is so heightened that Peters and his peers are having to turn potential customers away. Could now be vertical farming’s big moment?
“It’s not really a question of ‘if’ anymore. It’s going to happen,” Peters says. “And it’s already happening. It’s a matter of scaling up now.”
The benefits lie in the vertical farming method. Produce is grown indoors under LED lights, with a plant’s roots typically suspended in nutrient-rich water or mist. Temperature, humidity and light is carefully regulated within the sealed environment, and more plants can be packed into a space, on racks that can be seven storeys high.
While yield per square metre, low water consumption and lack of soil or pesticides have long been touted as the method’s main selling points, another one is becoming increasingly important: a guaranteed, year-round supply situated right where it is needed.
“On a small island or in remote locations, vertical farms can have a tremendous impact on food supply, especially in Covid times,” says Peters. “The food chain is typically very long and sensitive. When things break down, people realise their security of supply is not always a given.”
“It’s not really a question of ‘if’ any more. It’s going to happen. It’s a matter of scaling up now”
That’s not to say vertical farming businesses have been immune from the effects of the pandemic. The construction of Amsterdam-based PlantLab’s second overseas site in the Bahamas is being thwarted by current travel restrictions, for example. But Covid, and the disruption it has wreaked on global supply chains, is ultimately helping the sector make its case.
“There’s huge interest from island economies, hot economies and countries that have a higher propensity to import and have less arable land,” says Jamie Burrows, CEO of London-based Vertical Future. “From Iceland to Singapore, they all have very similar requirements.”
Plus, the pandemic isn’t the only threat to imports, Burrows adds. “If you import a lot of food, climate change is going to impact the countries that are producing that food for you. Even now, there have been pretty significant inflections in price on shelves and availability because of small fluctuations in temperature during the key growing seasons,” he explains.
And there is yet another factor that is throwing vertical farming into the spotlight in the UK, specifically: Brexit. That’s not just down to the immediate effect of imports disruption. The local produce sector remains riddled with uncertainty over access to the many seasonal workers that used to come from the EU, with a potential labour crisis looming.
Indoor farms, which are typically highly automated, require far fewer people to run. Furthermore, with constant harvesting, a small and constant rather than large and seasonal workforce is needed.
The yield and potential of vertical farming
The market opportunity for vertical farms is huge. Barclays Research analysts estimate the size of the global fruit & vegetable market is roughly $1.2tn (£800bn), and calculate that the addressable produce market for vertical farms is closer to $700bn (£513bn), leading to an approximately $50bn (£36.7bn) market opportunity. Plus, vertical farming boasts some environmental benefits, as produce requires less water and space to grow
Jones Food Company’s Scunthorpe vertical farm is a prime example. It has 26 tennis courts of growing space, operating 365 days a year – with a staff of six.
“Imagine if you have next to no labour in a farm that big. One of your largest costs is one you can really attack,” says James Lloyd-Jones, JFC CEO, and founder.
As a bonus, businesses such as JFC can boast lower carbon emissions than outdoor farms. While energy-intensive – to make up for the lack of natural sunlight – sector argues overall carbon savings are made when indoor farms are positioned close to where produce is needed, drastically reducing food miles.
Furthermore, Peters says, “if you make the chain radically short, you don’t need to waste so much of the harvest. You can avoid it altogether.”
This element could be particularly important to retailers with ambitious carbon commitments. “Retailers are being asked more questions than they’d probably like about carbon. You can’t just fudge it any more,” says Lloyd-Jones.
It’s not all plain sailing, though. There are some major hurdles for the sector to overcome – chiefly, the huge capex needed to build an indoor farm. Because of this, many vertical farming companies, whose main interest is in providing the technology for the farms to function, are becoming farm operators and even consumer brands.
PlantLab launched its first US production site – or ‘Plant Paradise’ – in December, within a former battery factory near Indianapolis city centre.
Having spent some time “working in relative silence” on the technology, PlantLab is now a site developer and operator. Local partners distribute and brand the end product into local supermarkets. As patent holder for its indoor farming tech in 74 countries, it is also in talks with major players about licensing the IP. But, adds Peters: “We’ve started this company to change the world, not just sit behind a desk and talk about licenses.”
It helps that PlantLab can point to the success of its own farms. Because building farms yourself is necessary to prove the technology and economics, says Lloyd-Jones. “There’s a lot of vertical farming companies that are tech companies, but they don’t grow anything so the person buying is the guinea pig,” he says.
For his part, he’s looking to refine the JFC concept further before embarking on a licensing model. The company already has plenty of expertise. Ocado-backed JFC is Europe’s largest vertical high-care farming operation, its 5,000 sq m facility stacking up 12 metres high with more than 17 layers of produce. But it will go one step further with its two new sites in the Midlands and the south west, due to open by the end of this year.
They will be more technologically advanced – “it’s like we built the first iPhone in Scunthorpe. We’ve jumped to making the iPhone 8,” Lloyd-Jones says – and will provide enough produce to meet 25% of UK demand for herbs.
The end goal is to develop a “cookie cutter” vertical farm that can be quickly and cheaply built wherever needed. “Once we’re happy with that we’ll look at a licensing model where we build these facilities all round the world. But anyone building them will know they’ve been stressed, used and run at 100%,” he says.
The model for vertical farming firms then is likely to be akin to Ocado and Ocado Retail, where the latter proves the case for the former’s technology, which rivals then adopt.
So similar, in fact, that Ocado itself is looking to get involved. In February last year, it formed Infinite Acres – a joint venture with Netherlands-based automation tech provider Priva Holding BV and US-based 80 Acres Farms, a vertical farm operator and brand. Customers have two options. They can either partner with Infinite Acres to build their own farm, or they can have 80 Acres run a farm on their behalf using that same technology.
If companies get it right, the licensing model can be lucrative. See Vertical Future for proof. It has two farms in London, with three more being built, but the output of the farms is only a small part of the business. “We retain them to keep our finger on the pulse and customer trends and it validates what we’re doing,” says Burrows. “Ninety-five per cent or more of our revenue now is from technology sales and software.”
Funding flurry
That potential has prompted a flurry of investment in the sector, kicked off in 2017 by Japanese media giant SoftBank, Alphabet’s Eric Schmidt and outgoing Amazon boss Jeff Bezos’ funding of San Francisco vertical farming startup Plenty. Plenty has now raised more than $200m in venture funding.
With it has come a lot of hype. “There is a lot of hot air in vertical farming,” Burrows says. “People can make crazy claims – one company said it could grow a head of lettuce in five days, which is ridiculous. And there is a lot of smoke and mirrors and low-grade companies trying to jump on the bandwagon.
“The risk is farms will fail and make the sector look bad,” he adds. “The impact for the good companies is investors will look at the sector and say it seems risky.”
Nevertheless, the pile-on is ultimately a positive thing, says Peters. “It’s maybe a matter of culture. In the US things tend to be more hyped and people tend to promise the world – then figure out after they have the money, they still need to do all the R&D,” he explains. “But it all helps to underline it’s really happening, and makes it acceptable and credible to consumers.”
Just how big vertical farming can get remains to be seen. Barclays estimates a $50bn (£36.7bn) market opportunity. As a total share of fresh produce output, it’s “going to be a single digit for years” says Burrows. “But as a standalone sector the growth rates are very high and will continue to be.”
Indeed, although it is currently focused on a small range of herbs and leafy greens, ultimately “you can grow anything” says Lloyd-Jones. While staples like rice and wheat might not be viable now, that will soon change. Competitive prices will doubtless be added to vertical farming’s multitude of advantages.
“We don’t want to get stuck in just being a premium, niche product that will only be affordable by a small part of the market,” says Peters. “We want to change the world.” Suddenly, that aim seems within reach.
Five firms leading the global vertical farming movement
InFarm
Vertical farms don’t have to be on a grand scale. In fact, they can fit in a chiller cabinet. InFarm places production right in the supermarket aisles at clients including Whole Foods Market and M&S.
“Modern agricultural production is built on a supply chain that is vulnerable to ecological and supply shocks. The global pandemic highlighted this. Retailers are having difficulties importing fresh produce, highlighting the need to develop a local and sustainable supply chain,” says Daniel Kats, VP of corporate sales.
Source: LettUs Grow
LettUs Grow
Bristol start-up LettUs Grow specialises in aeroponic farms that fit within a shipping container. Customers can purchase the full “business in a box”, which includes the grow beds and control system.
“Unlike a traditional farm, you’re not limited by location or climate. Your container farm needs no fertile land to operate and with its advanced climate control system, every day is a perfect summer’s day with ideal growing conditions,” LettUs Grow says. The company has raised a total £3.4m.
Source: PlantLab
PlantLab
This Dutch indoor farming firm launched its Indianapolis site in December. The 54,000 sq ft farm, developed in partnership with the Englewood Community Development Corporation, will provide an annual supply of close to 45,000 kg of fresh herbs and lettuce to local supermarkets and foodservice companies.
The fresh tomatoes, cucumbers, lettuce, and herbs grown in the ‘Plant Paradise’ are being marketed under the brand name Uplift, with the tagline ‘good food on purpose’.
Source: CropOne
CropOne
The world’s largest vertical farm is being built in Dubai, a joint venture between US firm Crop One and Emirates Flight Catering.
The $40m, 130,000 sq ft controlled environment facility will produce 6,000 pounds of high-quality, herbicide and pesticide-free leafy greens, harvested daily.
“We secure our own supply chain of high-quality and locally-sourced fresh vegetables, while significantly reducing our environmental footprint,” said Saeed Mohammed, EFC CEO.
Source: AeroFarms
AeroFarms
US firm AeroFarms last year announced it was building a 90,000 sq ft vertical farm in Abu Dhabi, which will be the world’s largest indoor agriculture research centre. The facility will house research centres for plant reproduction, seed breeding, machine learning and vision as well as robotics.
The company has grown more than 800 varieties of crops and is eyeing opportunity beyond food production in other industries like pharmaceutical, cosmeceutical and nutraceutical.
The Grocer
Lead photo: Source: AeroFarms
Topics: Farming Fruit & Veg Supply chain Sustainability & environment Technology
London Food Bank Is Going Greener With Greenhouse
CTV's Nick Paparella check in on the progress as the food bank aims to grow some of its own fresh produce for use during the winter months.
Nick Paparella CTV News London Reporter
Inside the London Food Bank's greenhouse in London, Ont. on Friday, Jan. 29, 2021. (Nick Paparella / CTV News)
LONDON, ONT. -- The outdoors may be covered in a blanket of white in January, but at the London Food Bank these days everything seems to be coming up green.
After a year of planning and with donations from the community, the new greenhouse is bearing fruit - or in this case vegetables.
“This is what Londoners a few years ago wanted more than anything else, to donate funds towards fresh fruits, fresh produce and that's what they have done,” says Glen Pearson from the London Food Bank. “So we've just taken it to a different level so we can grow our own as well.”
The man with the green thumb here is horticulturalist Luis Reyes.
“A couple of weeks ago we received the heaters and since then you can see the growth in only a couple of weeks,” says Reyes.
Like many from the food bank, Reyes is passionate about helping those in need.
“I am a grower and that's what I like to do and now to do it directly to people makes me proud,” he says.
The greenhouse is expected to grow about 15,000 plants a year which amounts to about four tons of food.
“You're not going to get anything fresher than this in a supermarket,“ says Reyes. “So probably you're going to harvest today here and the people or clients are going to receive it tomorrow or the same day.”
In the winter months, they are growing cold-weather plants like lettuce, spinach and even kale, but once summer arrives they will switch to tomatoes, cucumbers and fruit-bearing plants.
Adds Pearson, “It just expands the nutrition we're able to give to other people.”
Does Vertical Farming Actually Work?
Essentially, Bowery grows greens and other veggies in a nutrient-rich tray of water, which is consistently recycled in a closed-loop system
Feb. 03, 2021
In the outskirts of Newark, New Jersey, tucked between a packaging manufacturer and an aquatics center lies a farm. Except, if you're driving down the nearby highway you probably wouldn't be able to tell that this particular farm is churning out thousands of pounds of greens each year. In fact, all you'll see is a bunch of buildings, because this is a vertical farming operation called AeroFarms, which grows all their food in a warehouse. Like the owners of AeroFarms, tech enthusiasts across the world have embraced the dream of vertical farming, exclaiming that their operations are the answer to feeding a growing global population, combating climate change, and eradicating food deserts.
The many-shelved farming operation that is AeroFarms is just one of many companies that use vertical space to grow vegetables. What sets AeroFarms apart, however, is that it grows in a fine mist filled with nutrients instead of a typical growing environment like Rockwool and nutrient-rich water. But AeroFarms is an outlier in the vertical farming space. The typical vertical farm looks a lot more like that at Bowery, a company that uses a more traditional hydroponics system to grow their produce.
Essentially, Bowery grows greens and other veggies in a nutrient-rich tray of water, which is consistently recycled in a closed-loop system. This system is then replicated en masse and expanded not horizontally, but vertically to maximize space. But because all these plants are stacked on top of each other, access to light becomes a big obstacle, which means that each shelf is equipped with LED lights to act as artificial sunlight. Some operations like Plenty go even further by shining only the beneficial colors in the light spectrum for growth. While some of these large-scale vertical farms can quickly become laden with advanced technologies like robotic arms and AI monitoring systems, at their most basic, vertical farms use a combination of artificial sunlight and vertical space to maximize the amount of yield per acre. These food factories seem promising, but they also seem like a lot of work. So why are people so excited about them? For that answer and a deeper behind-the-scenes look at vertical farming, make sure to check out the video above.
Our Changing Climate is an environmental YouTube channel that explores the intersections of social, political, climatic, and food-based issues. The channel dives into topics like zero waste and nuclear energy in order to understand how to effectively tackle climate change and environmental destruction.
VIDEO: This Company Is Solving America's Food Issues One Backyard At A Time
Love & Carrots lowers our carbon footprint by making sustainable food sources very, very local
Love & Carrots lowers our carbon footprint by making sustainable food sources very, very local
By Richie Hertzberg | January 6, 2021
The average American has an annual carbon footprint of 16 tons, which ranks among the highest in the world. In fact, it's about quadruple the global average. One of the most significant contributing factors to our elevated carbon emissions is where we get out food, which is often shipped from far away, especially for those of us who live in cities.
A plucky business called Love & Carrots, which began a decade ago with one woman and a truck, is addressing this national issue by installing produce gardens across the Washington D.C. area. They’ve installed more than 1000 gardens in almost a decade of business.
Natalie Carver, director of horticulture said, “Our founder Meredith Sheperd saw so many sunny yards not being used for food. And saw the opportunity to start a business and start building gardens in all these sunny pockets across the city."
Unlike most businesses, as Love & Carrots scales, it reduces the overall carbon footprint by bringing city residents as close as possible to their food sources…their own backyards.
Nearly 30% of our food-related carbon emissions comes from transportation. Whether we’re importing bananas from Guatemala, or trucking carrots across the country from the main producer in Bakersfield, California, there is a tremendous amount of energy wasted by shipping perishable food long distances in short amounts of time.
The cost of convenience is not just environmental—you can taste it in the quality and freshness of the fruits and vegetables you eat. “When I first started harvesting in my garden, I realized that the food that I buy in local stores is not really what it tastes like,” says Yong Lee, a Love & Carrots garden owner. “So my palate had to get used to the fact that 'carrot' actually tastes like a stronger version of the carrot you get at a store.
Love & Carrots offers a full-service, turn-key operation. People interested in a garden receive a consultation on the optimal place for their garden as well as a top to bottom installation. If they want it, they can receive garden coaching to help them manage their produce and even have Love and Carrots staff manage the garden in its entirety.
The company's goal, however, stretches from Washington DC all the way back to America's biggest carrot patch in Bakersfield, California. It aims to be a national model, creating a ripple effect across the country. "Our goal is to expose as many people as possible to sustainable practices and smart growing," the company says, "so they can use that knowledge themselves and continue to share it with others."
CANADA: Company To Set Up Indoor Vertical Farm In Red Deer
A new era of farming is on its way to central Alberta. Foundation Farms Corporation, a subsidiary of GME Innotainment will be building an indoor vertical farm at a warehouse in Red Deer this year
Jan. 27, 2021
Foundation Farms Corp will be building its first indoor vertical farm in Alberta in the coming months. (Screenshot, Foundation Farms Corp website)
A new era of farming is on its way to central Alberta.
Foundation Farms Corporation, a subsidiary of GME Innotainment will be building an indoor vertical farm at a warehouse in Red Deer this year.
In a press release, the company said they hope to see the farm go into production in the second half of 2021. They are leasing 2,000 square feet of a 15,000 square foot warehouse to build the farm.
They said plans include manufacturing and assembly of future vertical farm units. It will also provide regional product sales and distribution headquarters for the company’s products.
“We have an ambitious growth plan that includes the deployment of numerous vertical farms throughout North America,” said Ed Kroeker, CEO of Foundation Farms.
“We are also assembling plans for additional innovative agriculture ventures that continue the theme of sustainability and local sourcing of food products for today’s consumers. The ability to establish our E-ROOTS vertical farm alongside our new manufacturing and assembly plant provides the opportunity to leapfrog our growth.”
The E-ROOTS system that they use incorporates hydrodynamic and ultrasonic cavitation equipment as the core technology, along with air injection to enhance crop production through natural root stimulation
The process is designed to create a supersaturated oxygen condition for the water-based nutrient solution that is fed to the plants. No chemicals are used in the process.
According to the Foundation Farms Corp. website, they grow herbs, leafy greens, microgreens, and edible flowers. Foundation Farms claims that their plants are 30 percent more productive than traditional soil-based growing, that they grow three times faster and use 95 percent less water.
They also say their model is more direct to the consumer than the traditional model.
“While the current socio-economic situation throughout North America and indeed most of the world has devastated many business sectors, the demand for sustainable and localized food production has never been greater than it is today,” said Yves R. Michel, GMEV CEO.
Sustainable Food Leads £6m Research Project To Transform The UK food System
Food security and sustainability are among the greatest challenges facing the world today, and traditional approaches of intensifying food production are coming under criticism for not looking at the whole picture of how we produce, and supply food to the nation
By India Education Diary Bureau Admin
January 10, 2021
A new £6m research project titled Healthy soil, healthy food, healthy people (H3) seeks to transform the UK food system from the ground up via an integrated programme of interdisciplinary research.
Social and natural scientists from the Institute for Sustainable Food at the University of Sheffield will collaborate on a whole-system approach to emphasise the links between production and consumption and identify practical paths towards food system transformation.
Food security and sustainability are among the greatest challenges facing the world today, and traditional approaches of intensifying food production are coming under criticism for not looking at the whole picture of how we produce, and supply food to the nation.
The Covid-19 pandemic also shone a light on the fragility of the UK’s food systems resilience and how its reliance on foreign imports during a global crisis meant people in the UK experienced empty shelves, and shortages of basic staples such as flour and pasta.
The H3 consortium – which draws on the combined strength of researchers from the University of Sheffield, University of Leeds, University of Bristol, University of Cambridge and City, University of London as well as a wide range of stakeholders from government, business and civil society – will focus its research on horticulture, hydroponics and hybrid farms, and on the health benefits of biofortification and increased fibre consumption.
This is an exciting, once-in-a-lifetime, opportunity to use cutting-edge research to have a genuinely transformative effect on the health and sustainability of the UK food system.
“We are delighted that the Institute for Sustainable Food will be leading one of the four consortia to be funded by the UK Research and Innovation’s Transforming the UK Food System for Healthy People and a Healthy Environment programme.
Professor Peter Jackson
Co-director of the Institute for Sustainable Food at the University of Sheffield
The project will identify practical paths towards food system interventions: on farm, in food manufacturing and retail, and improve dietary health and environmental sustainability of the agri-food industry in the UK.
This will include finding ways to increase the production of health-promoting vegetables while reducing reliance on harmful agricultural inputs and imported food by integrating hydroponic production systems within conventional soil-based farms. The project will also look at how improving the microbiomes of growing mediums has the potential to increase nutrients in our food systems and reduce our reliance on pesticides.
We are absolutely delighted by this award and excited to apply the food systems-level thinking we’ve developed at the Institute for Sustainable Food to the real world.
“Backed up by our world-leading research, this work has huge transformational potential to improve the sustainability, the quality, and the equity of our agri-food system here in the UK. Working closely with our external partners will add a real world perspective to shape how our initiatives are applied.
“In terms of fighting the climate crisis, this kind of transformational research is sorely needed. We are delighted that the Institute for Sustainable Food will be leading the way in developing and applying that research.”
Standardization To Build A Vertical Farming Industry or Building Customized Farms That Keep Cost High?
“Are we thinking about standardization so we can build a vertical farming industry or are we going to build a bunch of customized farms that keep costs unnecessarily high?
There are a lot of new ideas being trialed within the indoor farming space. “One of the hurdles I see is that it’s expected that there are standardized products available that will fit the new vertical farming systems being developed. Many farmers request that manufacturers develop custom components and equipment to meet the specifications of their system and their requirements, assuming that their systems will be the ones adopted by the industry and standardized,” says Chris Higgins, CEO of Hort Americas.”
According to Chris vertical farmers mostly don’t always take into account the required size and scale needed for custom made products. As an example, many of the new farming systems don’t fit the current substrate industry models. And that in itself is ok. Unfortunately, many of these farms aren’t large enough to afford the customizations needed to keep their produce profitable. That then creates additional work for these new farming businesses. Instead of being able to focus on growing, they’re trying to figure out the best way to manage a non-existent supply channel. “Growers keep designing new irrigation models and growing systems without thought of how they are going to source a substrate, consistently and cost-effectively.”
Chris Higgins
Chris says that there is a lot to learn from the Dutch greenhouse industry. Over the years they have built a great model that supports the commercial greenhouse industry really well. Namely, building a commercial vegetable greenhouse around a single crop, with the scale required to manage cost, labor, and the supply channel. “They are focused on reducing labor by using automation and getting as much efficiency out of the system and supply channel as possible. Dutch and other northern European farms grow several vegetable crops in greenhouses that are quite similar to each other. Here in the USA, the vertical farming industry is new. We are still finding ourselves. Defining our plan, and building learning to build out an industry that will support potential growth.”
“Are we thinking about standardization so we can build a vertical farming industry or are we going to build a bunch of customized farms that keep costs unnecessarily high? Factories are all about processes and standardization. Plant factories should be no different.” Chris wonders whether it’s really a problem to treat an indoor farm as a factory when building it. He states that substrates requirements are a simple yet good example of how there has not been much thought to standardization. But, how planning and simple changes could help farmers be more successful sooner.
A second hurdle Chris sees is a desire to become organic. “Building a new farm is challenging enough! Building a successful indoor hydroponic organic farm with new growers is even more challenging.” Indoor and vertical farmers are rightfully focused on food safety issues. Much of a successful food safety program is based on the ability to have tracking, tracing, consistencies and guarantees. This requires growers to need input products that can fit that model. Unfortunately truly organic products do not always fit that mold. Organics inputs can be hard to standardize as they are often not manufactured in a traditional way causing them to be influenced by outside variables in which only mother nature controls.
This can be seen within the peat moss substrate industry. “The vertical farming industry needs organic substrates to be delivered in a customized fashion, timely and in the highest of qualities. However, the peat moss industry has not necessarily evolved over time with this focus in mind. The industry has evolved to provide a very cost-competitive product to ‘large’ greenhouse growers. A smaller footprint farm that needs the highest of quality in a custom package may simply not have the volume needed to interest a supplier. However, many small farms using a similar product can work together to create the volume that will encourage the suppliers to change their strategies and put the energy and effort needed into new product development.”
So how can an industry be formed in such a competitive time where entrepreneurs are fighting for investor dollars? “Simple, focus on the business practices that truly make your new farming business unique. Then leverage the supporting horticulture industries and use what's available to you in a standardized package. This will allow you to grow quickly and focus on what makes you successful.”
For more information:
Hort Americas
Chris Higgins, CEO
chiggins@hortamericas.com
www.hortamericas.com
Publication date: Fri 8 Jan 2021
Author: Rebekka Boekhout
© VerticalFarmDaily.com
A Monster Wind Turbine Is Upending An Industry
Twirling above a strip of land at the mouth of Rotterdam’s harbor is a wind turbine so large it is difficult to photograph. The turning diameter of its rotor is longer than two American football fields end to end
G.E.’s Giant Machine, Which
Can Light Up A Small Town,
Is Stoking A Renewable-Energy Arms Race
By Stanley Reed
January 1, 2021
Twirling above a strip of land at the mouth of Rotterdam’s harbor is a wind turbine so large it is difficult to photograph. The turning diameter of its rotor is longer than two American football fields end to end. Later models will be taller than any building on the mainland of Western Europe.
Packed with sensors gathering data on wind speeds, electricity output and stresses on its components, the giant whirling machine in the Netherlands is a test model for a new series of giant offshore wind turbines planned by General Electric. When assembled in arrays, the wind machines have the potential to power cities, supplanting the emissions-spewing coal- or natural gas-fired plants that form the backbones of many electric systems today.
G.E. has yet to install one of these machines in ocean water. As a relative newcomer to the offshore wind business, the company faces questions about how quickly and efficiently it can scale up production to build and install hundreds of the turbines.
But already the giant turbines have turned heads in the industry. A top executive at the world’s leading wind farm developer called it a “bit of a leapfrog over the latest technology.” And an analyst said the machine’s size and advance sales had “shaken the industry.”
A New Generation of Wind Turbines
General Electric’s prototype for a new offshore wind turbine, the Haliade-X, is the largest ever built.
London Eye - Ferris wheel GE Haliade-X 13MW - wind turbine Empire State Building
HEIGHT: 443 feet HEIGHT: 853 feet HEIGHT: 1,050 feet
Source: General Electric
The prototype is the first of a generation of new machines that are about a third more powerful than the largest already in commercial service. As such, it is changing the business calculations of wind equipment makers, developers, and investors.
The turning diameter of the Haliade-X’s rotor is longer than two American football fields.Credit...Ilvy Njiokiktjien for The New York Times
The G.E. machines will have a generating capacity that would have been almost unimaginable a decade ago. A single one will be able to turn out 13 megawatts of power, enough to light up a town of roughly 12,000 homes.
The turbine, which is capable of producing as much thrust as the four engines of a Boeing 747 jet, according to G.E., will be deployed at sea, where developers have learned that they can plant larger and more numerous turbines than on land to capture breezes that are stronger and more reliable.
The race to build bigger turbines has moved faster than many industry figures foresaw. G.E.’s Haliade-X generates almost 30 times more electricity than the first offshore machines installed off Denmark in 1991.
In coming years, customers are likely to demand even bigger machines, industry executives say. On the other hand, they predict that, just as commercial airliners peaked with the Airbus A380, turbines will reach a point where greater size no longer makes economic sense.
“We will also reach a plateau; we just don’t know where it is yet,” said Morten Pilgaard Rasmussen, chief technology officer of the offshore wind unit of Siemens Gamesa Renewable Energy, the leading maker of offshore turbines.
The turbine is so large that it will be able to generate enough power to light up a town of 12,000 homes. Credit...Ilvy Njiokiktjien for The New York Times
Although offshore turbines now account for only about 5 percent of the generating capacity of the overall wind industry, this part of the business has taken on an identity of its own and is expected to grow faster in the coming years than land-based wind.
Offshore technology took hold in Northern Europe in the last three decades and is now spreading to the East Coast of the United States as well as Asia, including Taiwan, China and South Korea. The big-ticket projects costing billions of dollars that are possible at sea are attracting large investors, including oil companies like BP and Royal Dutch Shell, that want to quickly enhance their green energy offerings. Capital investment in offshore wind has more than tripled over the last decade to $26 billion, according to the International Energy Agency, the Paris-based forecasting group.
G.E. began making inroads in wind power in 2002 when it bought Enron’s land-based turbine business — a successful unit in a company brought down in a spectacular accounting scandal — at a bankruptcy auction. It was a marginal force in the offshore industry when its executives decided to try to crack it about four years ago. They saw a growing market with only a couple of serious Western competitors.
Still, G.E.’s bosses figured that to become a leader in the more challenging marine environment, they needed to be audacious. They proceeded to more than double the size of their existing offshore machine, which came to G.E. through its acquisition of the power business of France’s Alstom in 2015. The idea was to gain a lead on key competitors like Siemens Gamesa and Vestas Wind Systems, the Danish-based turbine maker.
A larger turbine produces more electricity and, thus, more revenue than a smaller machine. Size also helps reduce the costs of building and maintaining a wind farm because fewer turbines are required to produce a given amount of power.
These qualities create a powerful incentive for developers to go for the largest machine available to aid their efforts to win the auctions for offshore power supply deals that many countries have adopted. These auctions vary in format, but developers compete to provide power over a number of years for the lowest price.
The prototype is on a piece of land in Rotterdam Harbor, but the Haliade-X is designed as an offshore turbine, to be planted in relatively shallow sea water. Credit...Ilvy Njiokiktjien for The New York Times
“What they are looking for is a turbine that allows them to win these auctions,” said Vincent Schellings, who has headed design and production of the G.E. turbine. “That is where turbine size plays a very important role.”
Among the early customers is Orsted, a Danish company that is the world’s largest developer of offshore wind farms. It has a preliminary agreement to buy about 90 of the Haliade-X machines for a project called Ocean Wind off Atlantic City, N.J.
“I think they surprised everybody when they came out with that machine,” said David Hardy, chief executive of Orsted’s offshore business in North America.
As a huge buyer of turbines, Orsted wants to help “establish this new platform and create some volume for G.E.” so as to promote competition and innovation, Mr. Hardy said.
The G.E. turbine is selling better than its competitors may have expected, analysts say.
On Dec. 1, G.E. reached another preliminary agreement to provide turbines for Vineyard Wind, a large wind farm off Massachusetts, and it has deals to supply 276 turbines to what is likely to be the world’s largest wind farm at Dogger Bank off Britain.
One day turbines will reach a size limit, but “we just don’t know where it is yet,” said Morten Pilgaard Rasmussen of Siemens Gamesa Renewable Energy. Credit...Carsten Snejbjerg for The New York Times
These deals, with accompanying maintenance contracts, could add up to $13 billion, estimates Shashi Barla, principal wind analyst at Wood Mackenzie, a market research firm.
The waves made by the G.E. machine have pushed Siemens Gamesa to announce a series of competing turbines. Vestas, which until recently had the industry’s biggest machine in its stable, is also expected to unveil a new entry soon.
“We didn’t move as the first one, and that of course we have to address today,” said Henrik Andersen, the chief executive of Vestas.
To pull off its gambit, G.E. had to start “pretty much from scratch,” Mr. Schellings said. The business unit called G.E. Renewable Energy is spending about $400 million on design, hiring engineers and retooling factories at St. Nazaire and Cherbourg in France.
To make a blade of such extraordinary length that doesn’t buckle from its own weight, G.E. called on designers at LM Wind Power, a blade maker in Denmark that the company bought in 2016 for $1.7 billion. Among their innovations: a material combining carbon fiber and glass fiber that is lightweight yet strong and flexible.
Offshore turbines account for only about 5 percent of the generating capacity of the overall wind industry, but that number is expected to grow. Credit...Ilvy Njiokiktjien for The New York Times
G.E. still must work out how to manufacture large numbers of the machines efficiently, initially at the plants in France and, possibly later, in Britain and the United States. With a skimpy offshore track record, G.E. also needs to show that it can reliably install and maintain the big machines at sea, using specialized ships and dealing with rough weather.
“G.E. has to prove a lot to asset owners for them to procure G.E. turbines,” Mr. Barla said.
Bringing out bigger machines has been easier and cheaper for Siemens Gamesa, G.E.’s key rival, which is already building a prototype for a new and more powerful machine at its offshore complex at Brande on Denmark’s Jutland peninsula. The secret: The company’s ever-larger new models have not strayed far from a decade-old template.
“The fundamentals of the machine and how it works remain the same,” said Mr. Rasmussen, the unit’s chief technology officer, leading to a “starting point that was a little better” than G.E.’s.
There seems to be plenty of room for competition. John Lavelle, the chief executive of G.E.’s offshore business, said the outlook for the market “gets bigger each year.”
Stanley Reed has been writing from London for The Times since 2012 on energy, the environment and the Middle East. Prior to that, he was London bureau chief for BusinessWeek magazine. @stanleyreed12 • Facebook
A version of this article appears in print on Jan. 2, 2021, Section B, Page 1 of the New York edition with the headline: A Monster Wind Turbine Is Upending an Industry. Order Reprints | Today’s Paper | Subscribe
Indoor Farming Industry Gets Boost From COVID-19
Leading indoor farming companies, like BrightFarms, offer hydroponically grown, “cleaner than organic” packaged salads that results in a higher-quality product that consumers can trust
By Steve Bradley
The coronavirus pandemic has caused a major shift in dining out and led many Americans to become more familiar with their kitchens than ever before. In fact, according to the 2020 “America Gets Cooking” report commissioned annually by Hunter, a food and beverage public relations and marketing communications consultant, more than half (54 percent) of Americans report they are cooking more during the pandemic.
Thirty-nine percent said in a survey they are trying to eat healthier, with many saying they are becoming adventurous in the kitchen, trying new ingredients, brands, and products. Salads and vegetables are two of the top five food items survey respondents say they are preparing more.
This presents a tremendous opportunity for grocers to meet this demand for preparing meals at home, as well as a growing desire to maintain a healthy diet during the pandemic to assist in fighting off the unwanted pounds associated with staying at home.
Fresh produce can play a key role in eating healthy but is not something that can easily be ordered through an online retailer like non-perishable goods. Shoppers like to hold and visually inspect produce for freshness, firmness, crispness, color, and other desirable characteristics.
In short, fresh produce is a primary driver of traffic into grocery stores.
Additionally, consumers also want to know that what they are buying can be trusted. Salmonella, E-coli and other pathogens have unfortunately made their way into our fresh produce supply, causing massive recalls, illnesses, and even deaths. Consumers want to know they are buying a safe product and – increasingly – want to know more about where it came from and how it was grown. Words like “organic,” “non-GMO” and “locally sourced,” have become part of everyday language for many Americans.
Leading indoor farming companies, like BrightFarms, offer hydroponically grown, “cleaner than organic” packaged salads that results in a higher-quality product that consumers can trust. Even produce labeled “organic” has likely been treated with chemicals such as pesticides and herbicides. This also means the consumption of water, land, and costs associated with shipping produce are dramatically reduced. Additionally, locally grown means the quality is preserved through a much shorter shipping process, while also relying on less fuel due to shorter travels to market.
Controlled-environment agriculture ensures produce is not subjected to the whims of nature, such as drought, excessive rain, or other weather patterns.
In many ways, the BrightFarms’ model of bringing local produce around the U.S. into commercial stores has the potential to disrupt the multi-billion-dollar leafy greens industry. Few people could have likely imagined 10 years ago that hailing a taxicab would no longer be the “go to” for getting around town. Similarly, corporations, with the ability to look around corners and see the future, are re-imagining how consumers get high-quality local produce onto dining room tables.
We need to feed a growing population in a more efficient way – not tied to any one certain geographic area. Investments in cleantech-focused on resource efficiency, resiliency, and adaptation. Local, sustainable, controlled environment produce consumers can trust gives us that opportunity.
We believe it is possible to make the world a better place – building a better future for the next generation – while also growing business and creating jobs.
Steve Bradley serves as vice president of Cox Cleantech at Cox Enterprises, Inc. based in Atlanta, Georgia.
OUR NEW FUTURE: German Firm Says Indoor Vertical Farm in Singapore Will Produce 1.5 Tons of ‘Leafy Greens’ Every Day
New indoor vertical farm in Singapore is expected to produce 1.5 tons of fresh leafy greens per day.
stock photo/ @rebecca_lee_creative
KEY POINTS
Henner Schwarz, CEO of German firm &ever, said that his company’s new indoor vertical farm in Singapore will produce 1.5 tons of “leafy green” produce per day.
Schwarz said he expects produce from his firm’s new research and development facility in Changi will reach a lot of Singaporeans over time and “make a small contribution to food security in Singapore.”
&ever already has an operational indoor farm in Kuwait, which has become a testing ground for indoor vertical farming.
The boss of German firm &ever has said that his company’s new indoor vertical farm in Singapore will produce 1.5 tons of “leafy green” produce every day when it is up and running in the fourth quarter of next year.
Henner Schwarz, Chief Executive Officer at &ever, told CNBC on Monday that he expects produce from his firm’s new research and development facility in Changi will reach a lot of Singaporeans over time and “make a small contribution to food security in Singapore.”
The company, which competes with more conventional food producers, sells living plants to customers that can then be harvested at home as and when they’re needed. As a result, it tastes better and fresher, Schwarz said.
Schwarz said Singapore is “not the easiest market for indoor vertical farming” as electricity is fairly expensive and there are “lots of cheap imports.”
However, &ever has been awarded a grant by the Singapore government, which decided to speed up plans to increase locally produced food after seeing how the coronavirus pandemic impacted food supplies.
Singapore’s land scarcity makes conventional farming a real challenge and the country is keen to embrace solutions that don’t have a large footprint.
In terms of price, Schwarz said: “We think that we’re pricing our products similar to existing premium organic produce that you can find on the Singapore market today.”
He added: “The price point for indoor vertical farming products in many markets in the world, for example in the U.S., is very expensive. Our system is really geared towards making a meaningful contribution and we have taken quite some time to get things right, and to have the most energy efficient solution on the market.”
In order to reduce energy consumption at its Singapore site, &ever plans to use a combination of sunlight capture systems and LED lights. It is teaming up with lighting producer Signify to carry out a number of experiments.
Wikimedia | Valcenteu
Kuwait farm
&ever already has an operational indoor farm in Kuwait, which has become a testing ground for indoor vertical farming as it has similar, but different food security issues.
“We launched our farm in Kuwait just when Covid really hit in March,” said Schwarz. “It has been quite difficult to ramp production capacity up. However, the reception in the market has really been great thus far, and the Kuwaiti people really like our produce.”
When it comes to farming, access to fresh water is a problem in many areas of the world. “We need 95% less fresh water than traditional farms,” said Schwarz.
He added: “We expect that over time, as our efficiency becomes better and better, the price points can become lower and lower.”
PUBLISHED TUE, DEC 22 2020 - 2:11 AM EST | UPDATED TUE, DEC 22 2020 - 2:12 AM EST
The Nation’s First Saltwater Hydroponic Farm In Charleston, SC
Did you know that it’s possible to harvest crops using saltwater? Charleston is home to the first-ever indoor saltwater hydroponics farm that utilizes ocean water – aka the world’s most abundant resource – to grow food
Heron Farms saltwater hydroponics | Photo provided by Heron Farms
Agriculture is cool, but Lowcountry agriculture is even cooler.
Did you know that it’s possible to harvest crops using saltwater? Charleston is home to the first-ever indoor saltwater hydroponics farm that utilizes ocean water – aka the world’s most abundant resource – to grow food.
Saltwater hydroponic farming at Heron Farms | Photo provided by Heron Farms
Heron Farms, located at 1783 Harmon St., was established by Sam Norton in 2018. Sam grew up on a barrier island off the coast of South Carolina where his family home flooded more frequently + severely every year due to the sea level rise. The same issue was seen during his trip to Bangladesh, where he witnessed saltwater intrusion into coastal rice paddies upending the lives of many farmers in Asia.
This led to the idea of treating sea level rise as a free resource that could be used for agriculture instead of just an environmental problem.
Sam’s concept took shape and won the ACRE Startup Competition from the SC Department of Agriculture + the Charleston-based Harbor Accelerator Startup Competition. Following these achievements, Heron Farms was created and the idea became a reality in June 2018.
So, how does saltwater hydroponics work?
The first step in understanding the process is studying up on general hydroponic farming. Simply put, this method of indoor farming eliminates soil use by utilizing an alternative root anchor for plants + growing them directly in water (think: “hydro” = water). The inside setting eliminates the barriers of land use constraints + seasonality of crops. Plants receive controlled amounts of water, oxygen, nutrients + light that promotes the growth cycle. The difference with Heron Farms is that in all other cases, fresh water is used.
Why saltwater?
Along with the reasons mentioned above, the micronutrients of seawater that are transferred into the plants are a great source of minerals in our daily diets. Additionally, seawater irrigation allows the company to use less freshwater than any farm in the U.S.
What crops are grown?
Heron Farms sea beans | Photo provided by Heron Farms
Heron Farms’ first crop is sea beans – salicornia europaea – an edible plant that grows in the salt marsh. These types of saltwater-tolerant plants are known as halophytes, which have evolved to tolerate salt across its whole life cycle. Learn about cooking + eating sea beans here.
What makes this local company even cooler? For every pound of sea beans sold at Heron Farms, the company replants a sq. ft. of salt marsh along coastal South Carolina + Bangladesh using a custom seed-dropping drone. So far, 30,000 sq. ft. have been planted.
Heron Farms has been invited by Seawater Solutions to present at the 2021 UN Climate Change Conference in Glasgow, Scotland, where the Charleston-based company will build a second saltwater hydroponics farm.
Heron Farm’s future location in Glasgow, Scotland | Image provided by Heron Farms
Meet The Green Man of Ludhiana Who Has Created Vertical Gardens Across City From Waste Plastic Bottles
A man has started turning plastic waste into vertical farms in order to recycle in a new way.
Aimed at reducing waste of plastic and also as an attempt to reduce air pollution, Mehra said under his instructions, the vertical gardens have come up in many places including schools, colleges, gurudwaras, churches, police stations, government offices and railway stations.
Using waste plastic, an IRS officer Rohit Mehra (in grey sweater) set up Vertical Gardens to tackle air pollution in Ludhiana. (Credit: ANI/Twitter)
In today's time when there is a huge need to recycle waste and reduce the use of plastic, Rohit Mehra, Additional Commissioner in the Income Tax Department, has shown an inspiring path to follow when he used 70 tonnes of discarded plastic bottles to act as planting pots for vertical gardens in Ludhiana.
Aimed at reducing waste of plastic and also as an attempt to reduce air pollution, Mehra said under his instructions, the vertical gardens have come up in many places including schools, colleges, gurudwaras, churches, police stations, government offices and railway stations.
Speaking to news agency ANI on Sunday, Mehra said, “Using at least 70 tonnes of waste plastic bottles as pots, we have set up more than 500 vertical gardens at public places.”
Speaking about what made him turn to this unique idea of using plastic, Mehra said he started thinking of the copious amount of plastic waste and pollution that plagues the cities when his child some 4 years ago, one fine day informed him that their school had declared holidays due to high air pollution. Mehra said he pondered how the situation has turned so bad that they cannot even breathe in fresh air and provide the same to their children. This made him take note of the worsening situation and he decided to do something about it.
Mehra, who is know as the Green Man of Ludhiana due to his conservation work at the trees, has also created 25 mini forests ranging between 500 sq feet to 4 acres in 2 years, along with the vertical gardens. To broaden his understanding of quick growing of trees, he studied ancient Indian texts like the Vrikshayurveda that talks about the science of growing plants and forest. He also stumbled across the Japanese technique of Miyawaki.
He added, “It is a cost-effective and space-efficient solution for urban greenery. The vertical gardens also save the environment as you reuse plastic wastes as pots. Thanks to drip irrigation, these gardens save 92 per cent water."
Mehra said that after the establishment of the vertical gardens, they had checked the air quality index (AQI) of the city by a scientist associated with the Punjab Agricultural University and found a 75 per cent reduction in air pollution, thus making their venture a success.
USA: NEW YORK - Green Amazon A Smart Vertical Farming Company Is Making The Change For Feeding Communities In Need
Green Amazon is a sustainable smart agriculture company based in Buffalo, New York. The company uses different patented pending technologies in its projects
Green Amazon is a sustainable smart agriculture company based in Buffalo, New York. The company uses different patented pending technologies in its’s projects. Normally when we think about farms on the side of a road, we might imagine acres of land, crops, and livestock roaming on expanses of grass. Green Amazon farms will be different.
The Farms will be built on the east side of Buffalo, New York. The company is paving the way for a new method of farming – The company will provide necessary food and nutrients to communities in need while also reducing the burden on the earth’s natural resources and accounting for its changing weather patterns.
Green Amazon was founded in Finger lakes, New York by Dr. Walid Nosir, the company moved to Buffalo, New York to be closer to the people and community it serves.
The company plans to build the farms where the people are and think about how to be most efficient in that delivery. Green Amazon is trying to cut the shipping cost and distributions, so our selling partners, their warehouses, and their distribution facilities are within just miles. The idea that we’re literally in their backyard, we can really be collaborating closely on understanding what their needs are and be able to grow really efficiently.
Green Amazon seeks to improve food security and work towards the United Nations Sustainable Development Goal (2015) of “No Hunger”. In the coming decades, increasing pressure on the global food supply and associated supply chains will require industry overhaul. The research team at Green Amazon believes a focus on using modern technologies in the products and their development of non-chemical fertilization and inadequate disposal or reuse of agricultural will result in a decrease of the negative environmental impacts induced by wastes.
Green Amazon Growth system will be movable and vertical. The farm’s growing room is specially regulated to minimize contamination and provide a stable, consistent environment for crops to grow. People who enter the room must wear lab coats, eye protection, gloves, and hairnets and even wipe their shoes on a disinfecting mat. Air curtains also help prevent unwanted contaminants from floating into the space. The farm also waters its crops with an aeroponics system.