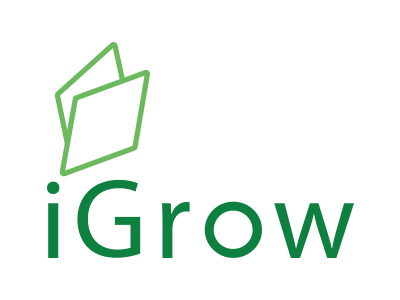
Welcome to iGrow News, Your Source for the World of Indoor Vertical Farming
Bowery’s Founder, Irving Fain, On The Future of Vertical Farming
At one point in the not-so-distant past, vertical farming’s role in our future agricultural system was far from certain. Growing leafy greens in warehouse-like environments controlled by tech seemed like a compelling business, but one that had yet to prove itself either economically or as an important source of food for a growing world population
Image from: The Spoon
At one point in the not-so-distant past, vertical farming’s role in our future agricultural system was far from certain. Growing leafy greens in warehouse-like environments controlled by tech seemed like a compelling business, but one that had yet to prove itself either economically or as an important source of food for a growing world population.
That, at least, was a common sentiment Irving Fain, CEO and founder of Bowery, met with when he started his vertical farming company five years ago. “There was a bit of skepticism around it,” he told me over a call recently, suggesting that five years ago, there were a lot more “ifs” than “whens” in terms of vertical farming’s future.
Fain, Bowery, and the entire vertical farming industry get a much warmer reception nowadays. Investment dollars are pouring into the space. Around the world, companies, scientists, and food producers are using the method to not just supply upscale grocery stores with greens but experiment with breeds of produce, feed underserved populations, and grow food in non-arable regions. As Fain suggested when we spoke, the last 12 months seem to have turned those “ifs” into definite “whens.”
Bowery’s last 12 months also illustrate this change. Fain said that Bowery went from under 100 retail locations about a year ago to nearly 700 right now, and will be in more than 1,000 “in the coming months.” Its produce is in a number of food retailers around the Mid-Atlantic and Northeast, including Whole Foods Market, Giant Food, Stop & Shop, Walmart, and Weis Markets. And in 2020, the company experienced “more than 4x growth” with e-commerce partners.
While the pandemic is responsible for some of this popularity, Fain insists it is not the only reason for the eventful year. “It’s definitely bigger than the pandemic,” he said. “What you’re seeing is a food system that’s evolving and [people have a desire] to see transparency and traceability in the food system.” These, he says, are issues the traditional food supply chain isn’t really able to address right now, hence the opportunity for companies like Bowery, which effectively cut multiple steps out of the supply chain.
Bowery grows its greens (lettuces, herbs, and some custom blends) inside industrial spaces where crops are stacked vertically in trays and fed nutrients and water via a hydroponic system. Technology controls all elements of the farm, from the temperature inside to how much light each plants get. The company currently operates two farms, one in New Jersey and the other in Maryland. A third is planned for Pennsylvania.
Technology, in particular, is something Bowery has big plans for. On top of a retail expansion, Bowery also added some notable personnel to its staff, including Injong Rhee, formerly the Internet of Things VP at Google as well a chief technologist at Samsung. Having such technology chops onboard will be vital in order for Bowery to realize many of its ambitions around advanced automation, which has the potential to optimize many parts of the seed-to-store process for vertically grown greens.
For example, Bowery’s farms are equipped with sensors and cameras that are constantly collecting data — “billions” of points, according to the company — that can be used to not just observe the current state of plant health but also predict the most optimal growing conditions for each crop. Elements like temperature, humidity levels, nutrient levels, and light intensity can all be adjusted, via the BoweryOS software, to create those optimal conditions. The end result is more consistent crop production, better yields, more flavorful food, and, ideally, a better nutritional profile for the greens compared to what conventional produce offers.
The system can also, through automation and AI, detect problems with plants. In a recent interview with Venture Beat, Bowery Chief Science Officer Henry Sztul used the example of butterhead lettuce yellowing at the edges during growth. Bowery’s system is technologically advanced enough at this point that it is starting to understand the conditions that create those yellowing edges. That foreknowledge, in turn, will allow growers to adjust the crop “recipe” (see above mixture of lights, temperature, etc.) to avoid the problem.
It took Bowery years to get to this point in terms of what its technology is capable of doing. “The system [for] indoor farming that you choose has a direct impact on the crops you’ll be able to grow, on the margins you’ll be able to generate, and on the return profile of the business itself,” said Fain. “And so being incredibly intentional and thoughtful about what technology you use is something we spent a lot of time on because it has an extraordinarily important economic impact.”
On a less technically complex note, controlled ag from Bowery and others also goes some way towards reinventing the supply food chain. Rather than greens being harvested in, say, Mexico and shipped via a complex distribution process all the way to Baltimore, they are packaged up at the farm and distributed to nearby retailers, usually those within a day’s drive “It is much more sustainable. It is much more efficient, and it’s more reliable, and those things have been important to consumers long before COVID,” said Fain.
Bowery will continue to innovate on both the technology and supply side of its business, as well as with the food itself. The company just launched a new specialty product line that will experiment with different flavors of greens and change frequently.
In terms of tech, Bowery’s latest farm, currently being built in Bethlehem, Pennsylvania, will incorporate even more automation than the company’s two existing farms. That location is slated to open later in 2021. When it does, Bowery will be capable of serving nearly 50 million people within a 200-mile radius.
The company hopes to expand its geographic reach much wider some day, building farms near most major U.S. cities and beyond. Given the increased confidence in the vertical farming sector as a whole, now looks to be the optimal time to move towards those ambitions.
by Jennifer Marston, The Spoon
BRITISH COLUMBIA: Learning Centre Gearing Up For “Village Greens”
The Society used the $166,328 grant to buy a Growcer “growing container” to supply the community with fresh greens year-round: they have made inquiries at IGA and local restaurants and plan to donate some to the food bank
Published on February 13, 2021
By Laura Keil
Fresh, local and green aren’t words you often hear about Robson Valley products in the wintertime, but the Valemount Learning Society hopes to change that.
The Learning Centre is branching out from its usual array of employment services and courses and digging into local food, thanks to a grant last summer from Northern Development Initiative Trust. The Society used the $166,328 grant to buy a Growcer “growing container” to supply the community with fresh greens year-round: they have made inquiries at IGA and local restaurants and plan to donate some to the food bank. They are also considering a box program if other options don’t work out.
The container is currently on order and will arrive sometime in March, said Riette Kenkel, manager of the Valemount Learning Centre, and she hopes they will have their first harvest in May.
Mike Johnson, who works for VLC as an employment advisor, will run the Growcer operation, which will be called “Village Greens.” Prior to arriving in Valemount, he worked in a commercial greenhouse for 20 years, Kenkel said.
The Growcer company provides training as the food is grown hydroponically.
The container will be set up in the Valemount Industrial Park next door to Robson Valley Mushrooms and near the Valemount Community Forest offices. Kenkel said the heating costs should be offset by the well-insulated container walls, which are good to -50 degrees.
She hopes to package most of the food in biodegradable packaging.
Kenkel previously told the Goat it’s no one’s fault the fresh food supply in Valemount isn’t always consistent.
“By the time the truck gets here the produce is old, and if stuff flies off the shelf we have to wait for the next (truck),” she said. “The Learning Centre has always responded to community needs. This was something we were hearing.”
She said it’s a social enterprise, so if it makes money, that cash will be cycled back into the programs that the Valemount Learning Centre delivers.
One of the more recent programs they’ve taken on is 4-H, which has a focus on agriculture and livestock and they’ve put a call-out for people to come up with program ideas.
Kenkel says it goes beyond just agriculture, however. Projects can relate to environmental issues, learning about aspects of farming, soil, and animals- not just farm animals.
The Growcer container is self-contained and ready to go in any season using hydroponics. The Valemount Learning Centre hopes to fill the winter void, create a job or two and raise money for their other programs. //GROWCER
“It’s wide open right now for whatever the community wants it to be.”
Farmers Market management
The Society recently took over management of the Valemount Farmers’ Market from long-time organizer Christine Pelletier.
“We’re pretty excited about it,” Kenkel said. “We’re not really going to make any changes. We want to just run this next season as close to what it’s been in the past.”
She said the market will run from June 17th until September 30th this year and the rates for vendors will be the same: $10 per day plus a $10 annual membership.
Kenkel says they likely won’t sell their own fresh greens at the market, as they don’t want to compete with local growers.
“If Village Greens has something that’s marketable at the farmers market that isn’t competing with existing customers, then we might look at it. But yeah, we don’t want to compete with any of the smaller farmers that have been reliably selling lettuce, kale, basil, that kind of stuff.”
Related Posts:
Indoor Farming Company With Backing From Ubben Aims to Solve The Problems With America’s Produce
The agriculture technology company focuses on building an indoor farm in Appalachia. The company combines agricultural techniques with cutting-edge technology and including access for all to nutritious food, farming, and building a homegrown food supply. The company operates a 60-acre controlled environment, agriculture facility in Morehead, Kentucky, which grows juicy beefsteak tomatoes and tomatoes on the vine
Image from: AppHarvest
Company: AppHarvest Inc. (APPH)
The agriculture technology company focuses on building an indoor farm in Appalachia. The company combines agricultural techniques with cutting-edge technology and including access for all to nutritious food, farming, and building a homegrown food supply. The company operates a 60-acre controlled environment, agriculture facility in Morehead, Kentucky, which grows juicy beefsteak tomatoes and tomatoes on the vine. It also operates a 60-acre indoor farm, outside Richmond, Kentucky, where it cultivates fresh fruits and veggies.
The company’s technological systems monitor the pollination across all 68 bays and 684 rows of plants. AppHarvest is only the fourth U.S. public Certified B corporation. A B corporation is a company that has (1) achieved a high standard of social and environmental performance as measured by the B Impact Assessment, (2) verified their scores through transparency requirements, and (3) made a legal commitment to consider all stakeholders, not just shareholders. Any company can apply to be one.
Stock Market Value: $3.3 billion ($33.26 per share)
Image from: CNBC
Activist:
Inclusive Capital
Percentage Ownership:
12.05%
Average Cost:
n/a
Activist Commentary:
Inclusive Capital Partners was formed in 2020 by ValueAct founder Jeff Ubben, to leverage capitalism and governance in pursuit of a healthy planet and the health of its inhabitants. The firm seeks long-term shareholder value through active partnership with companies whose core businesses contribute solutions to this pursuit. Inclusive is a returns driven fund with a focus on environmental and social investing.
Their primary focus is on environmental and social value creation, which leads to shareholder value creation. It is the successor to the ValueAct Spring Fund, which was launched in January 2018 and merged into Inclusive in 2020.
Inclusive is building a huge network and has accessed experts in industries such as energy, electrification, water, agriculture, food production, particulates, education and human rights. Just like ValueAct’s constructive, patient investment style, Inclusive will seek to earn the trust of managers, board members and institutional investors.
Jeff Ubben serves as the portfolio manager and Eva Zlotnicka serves as vice president. Eva has a pre-existing relationship with ValueAct through their interactions with Morgan Stanley, where she served as a VP and U.S. lead for the Global Sustainability Research Team. At Morgan Stanley, she worked to help address and raise awareness of environmental and social issues both inside and outside of corporations.
What’s Happening:
Jeff Ubben was appointed to the company’s Board in connection with the company’s business combination with Novus Capital.
Behind the Scenes:
This was initially an investment of ValueAct Spring Fund, which was converted into Inclusive Capital in 2020. Jeff Ubben first met AppHarvest founder Jonathan Webb in 2017 and has been involved with the company since the 2018 Series A round, working with Webb to put the management team together and develop a strong balance sheet. The company went public on February 1, 2021 through a $100 million SPAC transaction and a $375 million PIPE investment. Jeff Ubben is on the board where he can continue to help the company execute.
AppHarvest plans on having 12 facilities by 2025. The goal here is to make Kentucky the Netherlands of North America. The Netherlands (at 16,000 square miles) is the second largest agricultural exporter in the world, using greenhouse technology to feed two-thirds of all of Europe. In comparison, the state of Kentucky is 40,000 square miles and the US is 3.8 million square miles. AppHarvest’s motivation is first and foremost to benefit society, but if successful would have extraordinary financial returns as well.
As of 2018, 69% of fresh vine crops in the U.S. were imported, mostly from Mexico. These crops are pesticide-laden and grown using labor practices not up to U.S. standards. Moreover, they sit at the border for days and are driven 2,000+ miles to their destination, using tons of diesel fuel and resulting in less fresh produce. AppHarvest produces crops with no pesticides with greater nutrient density, and from their central location can reach 70% of the U.S. population in one day resulting in 80% less diesel fuel and much lower emissions. However, the larger environmental and economic benefit is in how the crops are grown — using 90% less water and yielding thirty times more per acre.
Moreover, AppHarvest’s resources are nature based – the greenhouse structure allows them to use 12 hours of sunlight per day and they collect the heavy Kentucky rainfall for their system resulting in a much less adverse effect on the water supply while greatly decreasing their cost of production by not having to pay for water. The greenhouse system also eliminates any weather or seasonal constraints, allowing the company to grow more efficiently 365 days per year.
While the company has no historic revenue, they just made their first delivery of beefsteak tomatoes on January 19, 2021, to customers that include Walmart, Kroger and Publix
BELGIUM: Bio-Planet Unveils New Store Concept In Braine-l'Alleud
The renovated Bio-Planet store also houses sustainable coriander plants grown in the vertical farms in Halle. The vertical farms require 20 times less room and 90% less water than the classic culture and run entirely on green electricity
Feb 19, 2021
Colruyt's organic supermarket chain Bio-Planet has launched a new store concept in its renovated outlet in Braine-l'Alleud in the Walloon Brabant province of Belgium.
The new concept focuses on sustainability with features such as a separate greenhouse for fruit and vegetables, recycled shopping baskets, and circular construction materials.
'Best Storage Conditions'
Store manager, Olivier Verzwymelen, commented, "The greenhouse is connected with the refrigerated fresh market and benefits from the cold flowing through.
"Without using extra energy, we reach a temperature of 9°C and a humidity of 75% in the greenhouse - the best storage conditions allowing us to counter food waste."
The store is equipped with a new Ecotap refill station for laundry, dishwashing and cleaning products.
The retailer aims to introduce refills for personal care products in the future.
The renovated Bio-Planet store also houses sustainable coriander plants grown in the vertical farms in Halle.
The vertical farms require 20 times less room and 90% less water than the classic culture and run entirely on green electricity, Colruyt added.
Bio-Planet manager, Jan Van Holsbeke, added, "We are convinced that the coriander will have the same success as our basil plants, introduced in March 2020."
Colruyt Group introduced the vertically grown basil under its Boni Selection store brand.
A Sustainable Store
Bio-Planet is testing vegetable panels from the Belgian start-up Circular Matters for the store's interior.
The 100% recyclable panels are made of fibre and a binding agent from residual flows from agriculture and the food industry.
Other initiatives include propane refrigeration and led lighting.
The store features an expanded service counter with room for over 350 kinds of meat, cheese, cold cuts, veggie, and vegan products.
It is also the first Bio-Planet store with its own bakery, which offers traditional pastries, fruit cakes, crumble and brownies, as well as bread and baguettes.
The shop will also allow customers to pick up their 'Collect&Go' orders placed on the Bio-Planet webshop.
The retailer plans to roll out the new store concept to 30 other stores.
© 2021 European Supermarket Magazine – your source for the latest retail news. Article by Dayeeta Das. Click subscribe to sign up to ESM: The European Supermarket Magazine.
In Retail tagged: Belgium / Sustainability / Colruyt Group / Bio-Planet
VIDEO: Is Tom Vilsack The Changed Person He Says He Is To Lead USDA Again?
For decades, USDA has misappropriated resources in supporting a factory farming system that harms communities, threatens human health, perpetuates racial inequity, and destroys natural ecosystems
For decades, USDA has misappropriated resources in supporting a factory farming system that harms communities, threatens human health, perpetuates racial inequity, and destroys natural ecosystems.
02-15-21
Gene Baur - Another View contributor
After heading up the U.S. Dairy Export Council, Tom Vilsack is in line to reprise his role as secretary of the US Department of Agriculture. Social justice, family farm, and sustainable agriculture groups have raised legitimate concerns about his longtime support of unjust and extractive practices, but at his confirmation hearing, Vilsack said that it’s a different time and he’s a different person, and that he now supports a more equitable and regenerative food system.
Let’s hope Vilsack has truly learned from past missteps and rises to the moment. He has huge opportunities to bring together diverse constituencies around common interests by reforming agriculture. We all benefit from access to wholesome food, produced in a just and compassionate way without destroying the planet or exploiting people and other animals.
For decades, USDA has misappropriated public resources in supporting a factory farming system that harms communities, threatens human health, perpetuates racial inequity, and destroys natural ecosystems. Raising and slaughtering animals by the billions demands inordinate resources, using 10 times more land in the US than plant-based farming. It is a major contributor to the climate crisis, the loss of biodiversity, and other ecological hazards, causing forests and other ecosystems to be destroyed to produce food for farm animals.
ANOTHER VIEW: Vilsack has the right stuff to move the Agriculture Department forward
Vast expanses of land are used for grazing and to produce corn, soybeans and other commodities to feed farm animals. It is far more efficient to grow crops to feed people directly, which could free up millions of acres to help sequester greenhouse gasses, create habitat for wildlife, and preserve natural ecosystems for future generations. Government programs should actively encourage this transition and remove all support, including financial instruments like carbon trading, that enable extractive practices linked to animal agriculture. Incentivizing biodigesters to turn animal excrement into energy at industrial farms, for example, is a short-sighted response to a chronic problem that allows agribusiness to further consolidate power, while greenwashing an untenable system.
Crowding animals by the thousands into factory farms increases risks for virulent pathogens and infectious diseases, including possibly future pandemics. These toxic conditions also sicken workers, disproportionately harming people of color, like the essential workers forced into slaughterhouses that were COVID-19 hotspots. Despite these and other hazards, however, most USDA funding, including COVID relief, has been used to perpetuate this unhealthy and unjust system, which concentrates wealth into the hands of fewer larger operations at the expense of family farmers, exploited workers and disenfranchised citizens.
We must shift USDA support and incentives away from industrialized animal agriculture, and toward a more resilient and equitable system that produces fruits, vegetables, legumes, whole grains and other nourishing foods. Our government should stop underwriting excess dairy production, for example, and distributing surplus artery-clogging cheese through food assistance programs. It is in our nation’s interest for the USDA to incentivize the production and distribution of nutritious plant-based foods instead. We could save billions of dollars in health care costs every year, while lightening our ecological footprint and creating meaningful jobs and opportunities through a diversified, community-centered, plant-based food system.
Concerns about food insecurity during the pandemic spurred a gardening movement, similar to the victory gardens during World War II that provided 40% of our nation’s produce. USDA’s vast network of land grant colleges and cooperative extension offices should build on this by supporting community gardens, urban agriculture, farmers markets and similar endeavors that provide fresh and healthy food, especially in communities that need it most. In some areas, there might also be opportunities for low-income housing to be connected with farming and food enterprises. Schools, churches, and other institutions, including those that serve vulnerable populations, can be enlisted to train the next generation of farmers. USDA food assistance programs that incentivize fresh fruits and vegetables should be expanded and leveraged to support local agriculture.
Industrial animal agriculture has perpetuated racism and structural inequity, often with USDA support. Most farm owners are white, but most agricultural workers are people of color, and they are commonly subjected to dangerous conditions. Black and brown communities experience environmental racism with pollution spilling out of factory farms, and they disproportionately lack access to wholesome food, which leads to elevated rates of diabetes, obesity, and other diet-related ailments. Recognizing this, Vilsack said, “I will ensure all programming is equitable and work to root out generations of systemic racism.”
At his confirmation hearing, Vilsack quoted Robert F. Kennedy about seeing things as they are, and aspiring to dream of things that are yet to be. Let’s hope we’re at an inflection point and that our incoming USDA secretary has truly changed and will actively work to manifest those dreams and the unfulfilled promises of our nation.
Gene Baur is president and co-founder of Farm Sanctuary, America’s first farm animal sanctuary and advocacy organization.
Growing Sprouts In A Former Slaughterhouse
Grow Up FARM has recently launched a new product, named Eat-Grow-Repeat: small pea shoots that grow on a small hemp-square in a bag. "Rip off the upper section of the bag, and the bottom of the bag is now the pot," Lasse Vilmar, Chief Executive Grower of the company, explains
Grow Up FARM has recently launched a new product, named Eat-Grow-Repeat: small pea shoots that grow on a small hemp-square in a bag. "Rip off the upper section of the bag, and the bottom of the bag is now the pot," Lasse Vilmar, Chief Executive Grower of the company, explains. "Place the bottom of the bag with pea plants on your table and the growth will continue. Harvest completely fresh pea sprouts for your salad bowl. Keep watering and within a week they will grow out once again."
Developing innovative packaging is a new field for Grow Up FARM, as the company has been working with mainly sprouts for three generations already. The Ringsted-based family business started with Lasse’s grandparents growing sprouts in the ‘60s. Lasse himself took over in 2013. “At that time, we were looking for new products to shoot the market. Our eyes fell on Koppert Cress and other companies that were doing microgreens. All of a sudden, it was like a light bulb that went off, and it felt like a natural direction to pursue”.
GrowUp FARM owners Jens Essemann and Lasse Vilmar
The new product had already been planned for quite some time, but the launch was accelerated the world-wide plot twist that the pandemic created. “We had just geared up and planned everything for the summer season to start, with all its parties and weddings. In the end, we only got to deliver one or two full batches before the lock-down”.
Although the company for years had focused on companies rather than local customers, selling to people in the area got them through the first lock-down. “We searched for Facebook community pages to advertise to local customers. Luckily we got rid of most of our stock that way, even though we only sold in large commercial-sized boxes. We combined different varieties in one box so that people had a chance to eat all of it. I even borrowed a van from a nearby car dealer on which I taped some of our roll-up banners. Like an old-school farmer I stood there, selling my produce. It was a fun period, but also nerve-wracking because we had no ideas when we could be able to continue our regular growing process again”.
Unlike the sprouts that Lasse has been working with for years, the microgreens are grown in a vertical farm. The building once was a poultry slaughterhouse, and the coolers have been turned into growing chambers. Isolation is important, as sprouts are grown completely in the dark. Even more importantly, isolation is needed for strict hygiene reasons.
“Growing sprouts is considered high-care production in the EU. The beans need a warm and moist environment, which are ideal circumstances for bacteria and molds. You need to be sure that the equipment is sterilized and that the water is drink-water quality. It takes a lot of control and procedures”. Most of the watering, which takes 400 liters every 3 hours per batch, is for cooling purposes. “The temperature in the core of the sprout-mass can rise to 70 degrees, so the sprouts could basically cook themselves”.
The sprouts are sold to both supermarkets and retailers, which makes it less vulnerable regarding covid-restrictions. Also, the Eat-Grow-Repeat plants are sold exclusively to supermarkets. “We’re doing 2000 bags delivery each week, and in a month we will launch the product to other supermarkets. The reviews have been raving, so we are quite proud of what we have achieved so far”.
Keeping an eye on the environment
The company strives to keep its packaging material as environmentally friendly as possible. The foodservice products are 100% recyclable, consisting only of FSC-cardboard and organic biodegradable hemp. Its current consumer packaging only consists of 6g of recyclable PE-plastic and organic biodegradable hemp, no pots or cardboard.
The Eat-Grow-Repeat product, with pea shoots
“Our farm is not much different from other vertical farms,” says Lasse. We are entirely electrified, and we have chosen an energy company (NaturEnergi) that pushes sustainable energy. This way our energy is constantly getting more sustainable.” In 2019 approximately 50% of the energy produced in Denmark came from wind and solar. “Ultimately we aim to plaster our roof with solar panels,” Lasse adds.
For more information:
Grow Up FARM
Lasse Vilmar, Owner and Chief Executive Grower
lasse@growupfarm.dk
www.growupfarm.dk
Source: Publication date: Thu 11 Feb 2021
Source: Author: Rebekka Boekhout
© VerticalFarmDaily.com
WIA Demeter Award Nominations And Scholarship Applications Now Accepted
Now in its ninth year, the Women in Agribusiness Demeter Award of Excellence recognizes women who have achieved excellence in their field and/or who have demonstrated an outstanding contribution to the agribusiness industry.
BOSTON, 2021 – In keeping with its commitment to grow opportunities and provide recognition for women in the agribusiness sector, Women in Agribusiness (WIA) has announced that nominations and applications are now being accepted for its 2021 award and scholarship programs.
Now in its ninth year, the Women in Agribusiness Demeter Award of Excellence recognizes women who have achieved excellence in their field and/or who have demonstrated an outstanding contribution to the agribusiness industry. The WIA Scholarship Program – which last year saw nearly 30 ag students benefit from the generosity of sponsors like Hancock Natural Resource Group, Motif FoodWorks and Rabobank – provides the potential to make life-changing industry connections, explore the many ag career options, and gain firsthand knowledge of the trends and issues facing the industry today.
“Over the years, we have grown our Women in Agribusiness community to expand much farther than simply hosting an annual event, though that is the very popular stronghold of our offerings,” said Joy O’Shaughnessy, event director, and chief operating officer of HighQuest Group, the parent company of Women in Agribusiness. “We have nurtured the opportunities and grown them to include membership, global year-long meet ups, a career center, a resource center, and a weekly blog. We have come to be full circle in elevating women in the industry, such that those already at a certain rung are lifting others while they climb. The Demeter Award and Scholarship program are indicative of this as well.”
2021 WIA Demeter Award of Excellence
Nomination forms for the Women in Agribusiness Demeter Award of Excellence are available on the WIA website. There is no limit to the number of entries, which will be accepted through Saturday, July 10, 2021, and self-nominations are permissible as well. Up to three nominees will be chosen and each recipient will be invited to accept her award at the 10th anniversary 2021 Women in Agribusiness Summit in Minneapolis this year, September 21-23.
Criteria for nomination for the award, includes.
Woman with a minimum of 10 years of experience in the ag and/or food industry;
Woman who is a positive example to other women in the industry;
Woman who breaks down barriers and serves as a resource for others; and
Woman who consistently exemplifies professionalism.
Last year’s recipients were Ponsi Trivisvavet, an agtech pioneer and entrepreneur; Priscila Vansetti Machado, a decades-long contributor to the ag sector, notable for numerous “firsts” for women in the industry; and Amy Wu, an award-winning journalist turned author and agtech advocate for women.
Student Scholarships
WIA Student Scholarship applicants must be full-time undergraduate or graduate students attending an accredited college or university, and majoring in agribusiness or a related field. Sponsorships from industry companies, such as AgIS Capital, Cargill, Mitsui & Company, and Nutrien make these scholarships possible. Students, who receive assistance with the costs for attending the WIA Summit, hail from colleges such as Florida A&M University, Texas A&M University, and the University of Saskatchewan.
Applications, which are available here, are being accepted until Wednesday, June 30, 2021.
Learn more at womeninag.com. Follow us @Womeninagri, like us on Facebook, and visit us on LinkedIn.
# #
About Women in Agribusiness
Women in Agribusiness is a business unit of HighQuest Group, a global agribusiness consulting, events and media firm. The Women in Agribusiness initiative took root in 2012, and now includes WIA Membership, WIA Demeter Award of Excellence, Student Scholarships, WIA Career Connector, WIA Resource Center, and the WIA Today blog. Learn more at womeninag.com.
US - SOUTH CAROLINA: VIDEO: Columbia Vertical Farm Uses Technology To Cut Plastic Pollution And Boost Sustainability
With the use of agricultural technology, Vertical Roots farm in West Columbia created a packaging system for its leafy greens that cut down the company’s plastic usage by 30% and extends the shelf life of the lettuce
FEBRUARY 01, 2021
Vertical Roots is the largest hydroponic container farm in the country. They grow and package lettuce varieties and have recently implemented a packaging process that reduces plastic with a resealable film. TRACY GLANTZ TGLANTZ@THESTATE.COM
With the use of agricultural technology, Vertical Roots farm in West Columbia created a packaging system for its leafy greens that cut down the company’s plastic usage by 30% and extends the shelf life of the lettuce.
In 2015, high school friends Andrew Hare and Matt Daniels created the idea for Vertical Roots, now the largest hydroponic container farm in the country. Hare is the general manager of the company and Daniels acts as the chief horticulturist.
The first Vertical Roots opened in Charleston and expanded with its second farm site in West Columbia in 2019. Vertical Roots parent company, AmplifiedAg, manufactures the container farms and farm technology of which Vertical Roots operates.
The farms are part of a growing industry called controlled environmental agriculture (CEA) that uses technology to ramp up nutrient-rich food production year-round.
Hydroponics helps the farm uses 98% less water than traditional farming, according to Hare. Their technology creates an indoor environment to grow lettuce on the East Coast. Most lettuce in the U.S. comes from California and Arizona, where temperatures do not fluctuate much throughout the year, traveling 2,000 miles from farm to table. Vertical Roots offers a solution for local lettuce.
“Our mission is to revolutionize the way communities grow, distribute and consume food,” said Hare. As populations grow, Hare said the ability to produce enough food is a global concern.
VERTICAL ROOTS AGRICULTURAL INNOVATION
As a company committed to sustainability, Vertical Roots had to address its plastic usage and the consumer demand for environmentally friendly products.
“I think everyone can agree that the amount of plastic that’s consumed and used globally is a bit of a problem,” said Hare.
If Vertical Roots were to completely opt-out of using plastics, as much as 40% of the lettuce would be damaged in transportation to the retailers, Hare said. So the company decided to still use plastic containers in order to cut out food waste, but it changed the amount and type of plastic used.
By replacing the conventional “clamshell” plastic lids that you see on a container of lettuce at the grocery store, Vertical Roots cut down more than 30% of plastic usage by creating a resealable film lid. The new packaging comes at no extra cost to the customer and will be cheaper in the long-run for Vertical Roots, according to Hare.
The farm also uses recycled plastic that can also be recycled again after use. Tiny perforations in the film lid of the packaging allows air to leave the lettuce container and extends the product’s freshness, making Vertical Roots lettuce last around 14 days on the shelf.
“We tested respiration and condensation with each lettuce variety, and ultimately found that we could extend the freshness and shelf life of our salad mixes even more,” said Hare.
GROWTH IN THE AGRICULTURAL TECHNOLOGY INDUSTRY
In the first three quarters of 2020, a record $754 million of venture capital was invested in the vertical farming industry, according to PitchBook data. This was a 34% increase from the entire previous year, Bloomberg reported in a January article.
A 2019 report from Global Market Insights showed that the vertical farming market size, or the number of potential customers or unit sales, surpassed $3 billion in 2018 and said it, “will exhibit a massive compound annual growth rate (CAGR) of over 27% from 2019 to 2026.”
In vertical farms, crops are harvested on several vertical layers indoors, where farmers can grow year-round by controlling light, temperature, water, and other factors, according to the U.S. Department of Agriculture.
Vertical agriculture is also seen as a growing industry because it “could help increase food production and expand agricultural operations as the world’s population is projected to exceed 9 billion by 2050,” according to the USDA.
However, some are skeptical about the future of vertical farming for several reasons. The farms use LED light bulbs to grow the crops, which require a lot of energy and money to operate.
Also, the farms mostly produce greens, which are low in calories because they take less water and light. The new farming technology is marketed as a way to combat world hunger, but in poorer countries, low-calorie greens are not as beneficial, according to Bloomberg.
THE FUTURE OF VERTICAL ROOTS
Despite a tough year due to COVID-19, Vertical Roots will open two more indoor, container farms in Georgia and Florida in 2021.
The company lost revenue from foodservice customers like restaurants, schools, and universities during the pandemic, said Hare.
Those food service customers accounted for about half of Vertical Roots’ business, Hare said. Grocery store business stayed steady and even grew during the pandemic. As schools and restaurants are slowly reopening, Vertical Roots is gaining business back.
The West Columbia farm location produces about $1.5 million pounds of produce per year, said Hare. Vertical Roots lettuce is in 1,200 different grocery stores in 11 states, including Lowes Foods stores, Publix, Harris Teeter, and Whole Foods Market chains.
Hare said the company is constantly working on sustainable initiatives, including figuring out a way to reduce light energy consumption by 20-25%, thinking about compostable packaging systems and finding ways to use less water at the farms.
In the future, Vertical Roots hopes to offer a larger variety of produce. The team is experimenting with growing foods like tomatoes, cucumbers, peppers, herbs and mushrooms to see if they could be viable products.
USA - OHIO: Thinking And Growing Inside The Box
A brother-sister team has taken the mechanics of farming out of the field and into a freight container
FEBRUARY 10, 2021 By SIDNEY DAILY NEWS
Local Farmer Takes The Farm Indoors
By Blythe Alspaugh - balspaugh@sidneydailynews.com
PIQUA — A brother-sister team has taken the mechanics of farming out of the field and into a freight container.
“We are growing beautiful plants without the sun; there’s no soil, and so it’s all a closed-loop water system,” Britt Decker, co-owner of Fifth Season FARM, said. “We use non-GMO seeds, completely free of herbicides and pesticides, so the product is really, really clean. In fact, we recommend people don’t even wash it, because there’s no reason to.”
Fifth Season FARM is unique in many ways; the 3-acre hydroponic farm is contained in a 320-square-foot freight container that sits along 120 S. Main St. in Piqua, with everything from varying varities of lettuce, to radishes, to kale and even flowers in a climate-controlled smart farm that allows Decker and his sister, Laura Jackson, to turn crops in a six- to eight-week cycle. The crops spend 18 hours in “daytime” every day, and the farm uses 90% less water than traditional farming.
“It’s tricky because we’re completely controlling the environment in here. It’s kind of a laboratory more than a farm,” Decker said. “I think there’s about 50 of them around the world right now. These are really international, and they’re perfect for places that are food deserts where they can’t grow food because of climate or other reasons. It gives them a way to grow food in the middle of nowhere.”
Decker and Jackson, along with their brother Bill Decker, also do traditional farming and grow corn, wheat and soybeans, but Decker said they were looking for a new venture that would help lead them to a healthier lifestyle and learn something new.
“Just with the whole local food movement becoming more and more important and food traceability, we just thought it would be a great thing to bring to our community to help everyone have a healthier lifestyle,” Decker said. “People love food that’s grown right in their hometown and the shelf-life on it, when you get it home, is remarkable. It’ll keep for two weeks.”
Currently, Decker and Jackson are growing a half-dozen variety of specialty lettuces that include arugula, butterhead, and romaine, as well as specialty greens like kale and Swiss chard, and even radishes and flowers. They received their freight container at the end of July and set up their indoor farm over two weeks; while the farm has been in operation for less than six months, Decker says that they’re growing beautiful product.
They have also started growing micro-greens, said Decker. Micro-greens are immature plants which are 1 to 3 inches tall and are in a 5-inch by 5-inch container.
“People will use them as garnishments and in smoothies,” said Decker. “Since they are immature plants, they have an intense flavor.”
Decker said they are growing wheat germ, broccoli and spicy salad mixes.
They’ve also started moving forward with sales and marketing. Fifth Season FARM has partnered with the Miami County Locally Grown Virtual Market to sell their products to the community. They also take orders through their website, fifthseasonfarm.com; customers can opt to pick up their orders between 4 and 6 p.m. on Wednesdays, or Decker and Jackson will deliver products up to five miles from the farm. Decker said that Fifth Season FARM is also in discussions with three restaurants in the area about including their specialty greens on their menus.
Decker said they also plan to attend the Sidney Farmers Market when it opens for the spring/summer season.
“We’re really just getting going,” Decker said. “While we were learning to grow products, we didn’t want to overcommit to a restaurant or grocery store before we knew we could really grow a beautiful product, so we’ve been donating product every week to the food pantry at the Presbyterian Church. It feels good to plant the seeds and watch them grow, and it feels good to make sure that people who aren’t getting the proper nutrition are getting some.”
“COVID Is Helping The World to Re-Examine Its Values” - Says Plenty's Co-Founder Nate Storey
According to Dr. Nate Storey, co-founder and chief science officer at Plenty, supply chain disruptions have sometimes resulted in Plenty’s greens being the only fresh products on grocery store shelves
With all the health concerns and supply chain disruptions resulting from the pandemic, many consumers are looking for locally and responsibly produced fruits and vegetables. And Plenty is firing on all cylinders to meet this increased demand.
According to Dr. Nate Storey, co-founder and chief science officer at Plenty, supply chain disruptions have sometimes resulted in Plenty’s greens being the only fresh products on grocery store shelves. The company has also seen its purchase rates increase during the pandemic, with more people consuming fresh produce. As the world looks forward to a post-pandemic “new normal,”, Nate is optimistic about the future of Plenty and indoor farming
Dr. Nate Storey, co-founder and chief science officer
“I expect that even after COVID, we will see these trends continuing. Once people really get used to eating fresh products, especially ours which are consistently good, it will be very hard for them to go back to old habits. COVID is helping us re-examine our values,” says Nate.
With respect to consumer trends in 2021, Plenty expects an extension of trends that emerged in 2020, namely the increasing number of people who are exploring home cooking options, which has also fostered an awareness of high-quality ingredients. According to Nate, “when home cooking, it doesn’t take long to really start valuing high-quality ingredients. So I think that we’ll see a growth in the quality-focused parts of the produce industry. I think that we’re going to see a trend towards boosting immune health and creating snackable products, as people begin to incorporate more produce into snacks.”
Plenty's recently launched product packaging
As such, quality is of the utmost importance to Plenty. The company approaches quality from three main angles, one being the real value of the product. As Nate explains, ensuring real value of their products means a commitment to offering consumers an attractive product whose packaging attracts consumers and preserves the product as long as possible.
“We ask ourselves: how can we give people three weeks, a month or as much time as possible? Hopefully, the product is consumed within a few days but for people who are watching their budgets, knowing that the product will last improves the value of the product,” says Nate.
More importantly, the company is focused on the quality of the greens themselves. Through careful varietal selection and precise control of the growing environment, Plenty produces greens with the best loft, consistency, texture and nutritional quality. The company’s third approach to quality, according to Nate, is its commitment to delivering a consistent product every day of the week. This consistent production, a major advantage of indoor farming overall, allows growers to eliminate seasonality so that consumers can count on the greens’ quality at any time of the year.
Propagation space in Plenty's San Francisco farm
Plenty’s commitment to the highest quality standards is reflected in the company’s mission, which is the provision of fresh, healthy food to people all over the world. As Nate explains, field-based agriculture currently produces only 30% of the global population’s needs for a healthy diet.
“We’re in the business of figuring out how we produce massive amounts of produce for consumers and make sure that they can supplement their diets with enough fruits and vegetables. Vertical farming and Plenty works to fill the void between 30% of what the world needs and 100% of what the world needs,” says Nate.
Plenty is also addressing consumers’ desire for sustainably produced fruits and vegetables by constantly working to improve water, space and energy use efficiency. Aside from environmental sustainability, the company strives for social sustainability by working to integrate itself into the communities where the farms are located by creating jobs and becoming a part of the local food system and culture.
For more information:
Plenty
Lizi Sprague
lizi@spronguepr.com
www.plenty.ag
Source: Publication date: Fri 12 Feb 2021
Source: Author: Rebekka Boekhout
© VerticalFarmDaily.com
Yasai To Establish First Zürich Vertical Farm, Strategic Partnership Announced
iFarm with Yasai AG (Switzerland) and Logiqs B.V. (Netherlands) are proud to announce the beginning of a long-term cooperation. With the launch of the first vertical farm project in Zurich, Yasai AG announced the signing of a strategic agreement with equipment and tech suppliers
Image from: Urban Ag News
iFarm with Yasai AG (Switzerland) and Logiqs B.V. (Netherlands) are proud to announce the beginning of a long-term cooperation.
With the launch of the first vertical farm project in Zurich, Yasai AG announced the signing of a strategic agreement with equipment and tech suppliers. The company involved Logiqs and iFarm as technology partners in the construction of a pilot facility, with 673 sq. m of growing area and with a design capacity of 20 tons of fresh herbs per year.
The Dutch company Logiqs will act as a supplier of automated shelving systems and grow lights. iFarm will supply the nutrient solution management system, climate control equipment, and the Growtune software platform which enables flow chart implementation and control over production conditions and processes. Going forward, the partners plan to scale up the experience of rapidly constructing an automated, compact, high-performance vertical farm, gained in a Swiss project, across the globe.
Image from: Urban Ag News
Mark Essam Zahran (co-founder Yasai):
The project will not just be limited to the testing and fine-tuning of state-of-the-art innovative solutions. We expect to lay the groundwork for large-scale industrial vertical farming in smart cities and showcase the incredible benefits of a circular economy. A plantation in the largest Swiss city, one of the most expensive cities in the world, will help us assess the economic prospects and give other European cities an example of how to produce an abundant yield without harming the planet, plants, and people.
Gert-Jan van Staalduinen (owner Logiqs):
The Swiss project opens up interesting prospects for us. We expect a fruitful collaboration with Yasai experts and a beneficial exchange of best practices with iFarm. With our vast experience in implementing automation and logistics systems on farms, we will be able to build a technologically advanced farm in the very heart of Europe.
Kirill Zelenski (CEO iFarm Europe):
We appreciate how meticulous and scrupulous Yasai is and are impressed by their passion and drive. We are just as inspired by the prospect of working with seasoned professionals from Logiqs. We hope that our software technologies will perfectly complement their hardware and the project as a whole will become a lasting benchmark for the industry and will serve as the beginning of a long-term cooperation.
Video: Babylon Micro-Farms To Expand, Relocate To Richmond
Co-founded in 2017 by University of Virginia students Alexander Olesen and Graham Smith, Babylon Micro-Farms started when Olesen and Smith first designed a low-cost micro-farm to provide nutritious produce for food-insecure refugees in the Middle East
Richmond—Governor Ralph Northam today announced that Babylon Micro-Farms, a Virginia-based company that develops and produces remotely controlled, indoor hydroponic systems for growing fresh herbs, vegetables, and salad greens, will invest $140,000 to expand operations and relocate to the City of Richmond. Babylon’s new location in Scott’s Addition will enable the company to expand its capabilities in manufacturing, software development, and research and development so it can begin distributing nationally and internationally. Virginia successfully competed with Arizona and California for the project, which will create 24 new jobs.
“We are thrilled to celebrate the growth of innovative Virginia businesses like Babylon Micro-Farms,” said Governor Northam. “The company’s dynamic, high-tech systems are helping to address food insecurity during the pandemic and getting fresh, local produce into the hands of more people. This expansion demonstrates the success that entrepreneurs can find in our Commonwealth, while also maintaining a strong commitment to environmental sustainability.”
Co-founded in 2017 by University of Virginia students Alexander Olesen and Graham Smith, Babylon Micro-Farms started when Olesen and Smith first designed a low-cost micro-farm to provide nutritious produce for food-insecure refugees in the Middle East. Motivated by the desire to bring benefits of sustainable hydroponic farming to those who need it most, the pair set out to develop technology that would automate the complex aspects of indoor farming and in doing so, make this transformative method of crop production accessible to anyone. Babylon’s key innovation was developing a technology system that enables its own staff to remotely manage the light, water, and nutrients for its farming systems.
“The demand for Babylon Micro-Farms’ engineered indoor farming systems is growing in assisted living facilities, student centers, restaurants, and across the globe,” said Secretary of Commerce and Trade Brian Ball. “This expansion will enhance the company’s development and distribution of its products, and the addition of 24 new jobs is welcome as we work toward economic recovery amid this global health crisis.”
“Richmond is an exciting city with a rapidly expanding start-up and technology scene,” said Alexander Olesen, CEO, and Co-Founder of Babylon Micro-Farms. “We hope to attract some of the leading talent to our new headquarters in Scott’s Addition.”
The Virginia Economic Development Partnership worked with the City of Richmond to secure the project for Virginia. Babylon Micro-Farms is eligible to receive state benefits from the Virginia Enterprise Zone Program, administered by the Virginia Department of Housing and Community Development. Funding and services to support the company’s employee training activities will be provided through the Virginia Jobs Investment Program.
“Richmond has proven to be fertile ground for innovative companies, and Babylon Micro-Farms’ environmentally friendly, technology-driven, indoor farming methods provide healthy food options for many people,” said Richmond Mayor Levar Stoney. “We’re excited to welcome them to Richmond, and look forward to the company growing its product and its presence in our city.”
“Babylon Micro-Farms’ relocation to the City of Richmond and the expansion of its operations represents an exciting opportunity for the city,” said Senator Ghazala Hashmi. “Not only is the venture bringing new jobs, the company’s use of innovative technologies for indoor farming offers a model for fresh and healthy produce that is grown locally and within urban settings. I am delighted that the company will be a part of Scott’s Addition.”
“We are excited to welcome Babylon Micro-Farms to Richmond,” said Delegate Jeffrey Bourne. “We admire the company’s ingenuity and commitment to sustainability and food accessibility. Its presence will be a great addition to our community as well as create valuable new jobs.”
AeroFarms Hires These New Executives
Newark, N.J.-based AeroFarms has hired several executives from companies such as Google, Earthbound Farm, PepsiCo, Kraft, Campbell’s Soup Co., and Tata Consumer Products
By AMY SOWDER
February 11, 2021
Newark, N.J.-based AeroFarms has hired several executives from companies such as Google, Earthbound Farm, PepsiCo, Kraft, Campbell’s Soup Co., and Tata Consumer Products.
Most recently, Dane Almassy joined the company as vice president of sales, according to a news release.
Almassy has more than 20 years of experience including time at Earthbound Farm, Aurora Organic Dairy, and PepsiCo.
Since 2004, AeroFarms has been working in not only vertical, aeroponic farming, but other aspects of agriculture, from genetics to post-harvest. The company’s more than 850 crop varieties can extend beyond food uses to pharmaceutical, cosmeceutical, and nutraceutical.
AeroFarms has been in major expansion mode with major announcements in 2020:
The build-out of a large research and development indoor vertical farm in Abu Dhabi in the United Arab Emirates;
Launch of the municipal indoor vertical farming program in Jersey City, N.J.; and
The World Economic Forum Healthy Communities and Cities initiative.
To help meet this growth, AeroFarms has made other key hires.
Andreas Sokollek, Stacy Kimmel, Ph.D., and MaryAlice Feinstein joined AeroFarms more than a year ago as chief operating officer, vice president of research and development, and chief people officer respectively, and Mark Boyland joined the summer of 2020 as general counsel.
“These key executive hires, each with deep industry expertise, have been helping us further capitalize on opportunities around the world as we continue to scale and build out our incredible culture and team, all aligned around our mission of growing the best plants possible for the betterment of humanity,” co-founder and CEO David Rosenberg said in the release.
Also, AeroFarms added in 2020 to its board of directors James “Jim” C. Borel, who has more than 40 years of experience in the global agriculture and food industry, including executive vice president and member of the DuPont Office of the Chief Executive.
Lead photo: AeroFarms hires several top executives. - (File photo courtesy AeroFarms)
These 2 Companies Are Putting Big Money Into Hawaii’s Agricultural Future. Will Their Bets Pay Off?
A pair of companies backed by a billionaire and a pension fund are trying to revitalize fallow farmland in the state
A pair of companies backed by a billionaire and a pension fund are trying to revitalize fallow farmland in the state.
02-15-21
On Lanai, where shreds of black plastic in the soil are the last vestiges of the island’s defunct pineapple fields, a sliver of long-abandoned farmland is getting an encore — and a reinvention.
In six high-tech greenhouses, a futuristic vision of food-growing is underway — one in which nutrient density and flavor are automated.
It doesn’t matter that the red dirt below the greenhouse is eroded or peppered with plastic that once served as Dole pineapple plantation’s weed control. In fact, the hydroponic tomatoes and leafy greens grown here by Sensei Ag don’t depend on soil at all.
The ag-tech company founded by Larry Ellison, the Oracle founder who owns nearly all of Lanai’s acreage, and Dr. David Agus, a physician, and medical researcher, is pioneering tools to produce affordable food in places like Lanai that — despite its history as an agricultural plantation — lack traditional farming essentials like water and fertile soil.
Sensei Farms Lanai, a two-acre indoor farming pilot project by Larry Ellison’s Sensei Ag, produced 35,000 pounds of produce in less than three months last year. Sensei Ag
In doing so, the company is redeploying a scrap of neglected farmland into active agriculture in an attempt to buck an unsettling trend: Hawaii imports more than 85% of its food.
Hawaii has tens of thousands of acres of fallow former sugar and pineapple plantation lands. There are many reasons why this land isn’t being used for farming — inadequate infrastructure, soil erosion, the sky-high price of agricultural real estate. All of these challenges and more make growing food on old plantation acreage unaffordable for most farming operations.
Putting more of this stagnant acreage into food production, however, is a worthwhile goal, experts say, because it could help the state wean itself off of a reliance on the cargo ships and planes that deliver food supplies to the islands.
“When you bring up Hawaii to anyone anywhere on earth, what they think of is paradise on earth,” said Vincent Mina, president of the Maui Farmers Union United. “But what paradise do you know of that brings in 85% of its food?”
State Efforts Have Fallen Short
Re-fashioning former sugar and pineapple plantations into viable food farms is what the Hawaii Agribusiness Development Corp. was designed to do.
However, a scathing state audit in January said that the 25-year-old state agency has so far failed its mission because “the economic void created when plantations ceased production remains mostly unfilled.”
Larry Jefts, one of the state’s largest produce producers, recently expanded his farm footprint with access to ADC lands in Central Oahu that had lain fallow since Del Monte stopped pineapple production nearly two decades ago.
The problem, according to Jefts, is not that the ADC is inert. It’s the state’s poor land use policy that has allowed some farmland to be developed, as well as society’s lack of commitment to local agriculture.
The Agribusiness Development Corp. has failed in its mission to reinvent Hawaii’s agricultural sector, two recent reports say. Office of the Auditor
“The problem is there’s no will here,” Jefts said. “Good farm ground is coming out to go into solar energy farms because the people who own it can make more money in solar. If they charged that much money to the farmers, the farmers would fail and imported foods would take over.”
Yet while Jefts is farming on a portion of the 1,200-acre Whitmore Project — land left vacant by Del Monte in 2004 and then acquired by the ADC for local agriculture in 2012 — hundreds of acres attached to the project remain fallow almost 10 years later.
That’s in part due to the time-intensive, bureaucratic process of securing money, permits, and contracts to build and repair the infrastructure required to make more of the acreage farmable, said Sen. Donovan Dela Cruz, a champion of the project.
It’s one thing to acquire the land, he said. But it’s another challenge entirely to ready it for farmers who need water, roads, electricity for refrigeration, and food safety-compliant facilities in order to make their businesses financially viable.
“With our state, there’s so many good intentions but just no money to put through to implementation,” said Kirsten Oleson, associate professor of ecological economics at the University of Hawaii College of Tropical Agriculture and Human Resources.
“If we’re serious about doubling production of food that is grown and eaten here, it would take some time to rethink policy and some pretty large and potentially risky investment that the state’s coffers don’t have.”
While state efforts flounder, a pair of new agriculture companies backed by a billionaire and a pension fund are stepping in with lofty goals to revitalize fallow farmland with diversified agriculture operations that aim to help Hawaii wean itself off of imported foods.
A Billionaire’s Bid To Boost Food Security
On Lanai, Sensei Ag is sidestepping many of the traditional high-yield farming requirements: lots of land, lots of water, lots of hard manual labor.
Founded by Oracle billionaire Larry Ellison, left, and medical researcher David Agus, Sensei Ag’s goal is to grow food that is more sustainable and nourishing than if it were farmed traditionally.
Sensei Ag
Although the company’s two-acre greenhouse farm is just a scrap of the 20,000 farmed acres that earned Lanai the moniker of the world’s largest pineapple plantation, yields from hydroponics can be far greater than those from conventional soil farming.
Sensei Ag CEO Sonia Lo projects the company will harvest 500,000 pounds of food for statewide consumption in 2021, including Swiss chard, basil, tomatoes, cucumber and eggplant.
“What we’re doing is we’re competing against the likes of Organic Girl that’s coming in from California or Earthbound Farms,” Lo said. “It’s pretty straightforward given that our stuff is a day old or two days old by the time it gets on a shelf as opposed to two weeks or three weeks old.”
Hydroponic growing is capital-intensive, however. Sensei Ag’s approach benefits from the fact that it’s bankrolled by Ellison, one of the richest people in the world.
Lo declined to reveal the amount of financial investment it took for the Lanai pilot project to achieve its inaugural harvest last October, but she acknowledged the role of Ellison’s wealth.
Yet while the cost to build a state-of-the-art greenhouse is out-of-reach for most farmers, indoor farming offers growers a chance to capture significant long-term financial savings since producing food this way requires significantly less land and water than traditional outdoor farming.
According to Lo, Sensei Farms Lanai requires about 10% of the amount of water it would take to produce a similar harvest in the dirt.
With this in mind, Sensei Ag’s mission includes efforts to make greenhouse farming more accessible. The company is aggregating risk assessment data in hopes that it will encourage banks to finance indoor growing mechanisms such as greenhouses and vertical farms. The company is also writing a playbook for people who want to build a successful indoor farm business, Lo said.
The rise of this kind of high-tech, high-yield farming could be a key to making Hawaii-farmed foods more competitive, according to Jesse Cooke, vice president of investments and analytics at the Ulupono Initiative.
“Using a hydroponic system, you could guarantee that every week you would have the same amount of quantity and the same quality (of produce) — and that’s what you need to sell to a large grocer,” Cooke said. “A lot of outdoor operations can’t guarantee that because they’re at the whim of nature itself.”
Brian Miyamoto, executive director of the Hawaii Farm Bureau Federation, agrees that indoor farming could be a game-changer — if Hawaii farmers can figure out how to raise enough capital to build the infrastructure without sabotaging future profits.
“We can grow a lot of things here in Hawaii as far as food products,” Miyamoto said. “What we struggle with is doing it competitively — that’s why we import so much.”
Hawaii can’t rely on billionaires to make the upfront investment in high-tech indoor farming, Oleson said. Rather, the state needs to follow in the footsteps of other countries that enacted public policies to encourage this kind of agriculture.
In places like Israel and the Netherlands, high-tech greenhouses are important food production tools, Oleson said.
Beyond policy and economics, Oleson said there are aesthetic and cultural considerations associated with scaling up indoor farming in the islands.
“You’re not looking across rolling green landscapes, you’re looking at lands with big infrastructure on it so there’s sometimes social pushback,” Oleson said. “I’m not a Native Hawaiian, but I would be very curious to know the response of the local community to that kind of agriculture because it’s very divorced from the earth.”
Will Mahi Pono’s ‘Serious Amount Of Money’ Pay Off?
On Maui, a partnership between a California farm management company and a Canadian pension fund is producing food on fallow land resulting from the 2016 closure of the state’s last sugar grower.
Since Mahi Pono bought 41,000 acres of Hawaiian Commercial & Sugar Co.’s former sugar cane fields in 2019, the company has begun growing some of Hawaii’s top food imports — potatoes and onions — in hopes of winning over some of that market share.
Mahi Pono’s mission to produce foods that Hawaii imports heavily and that are agriculturally possible to grow here is a smart one, according to Oleson. But she said it could be difficult for the company to compete with the price point for potatoes and onions imported from the mainland.
In 2016, Hawaii’s last remaining sugar grower shut down an operation that had run for 146 years. Now the 40,000 acres are owned by Mahi Pono, the marriage of a California farm management company and a Canadian pension fund. The company is growing produce with plans to reduce the state’s reliance on imports. Courtesy: Mahi Pono
It might also prove hard to convince consumers to pay more for locally grown potatoes and onions as opposed to more perishable produce.
“Potatoes and onions can sit on a boat and the quality doesn’t decline quite as fast, but all of us know what happens when you buy a box of spinach from Costco and if you don’t eat it that night it turns to slime,” Oleson said. “So the concern is growing foods locally where the freshness really matters.”
But Mahi Pono is growing more than just root vegetables. The company planted over a half million avocado and breadfruit trees, as well as rows of trees to shelter crops from the wind. The company plans to plant its 1 millionth tree by the end of June, according to community relations director Tiare Lawrence.
The company is also growing produce ranging from tangelos and finger limes to broccoli and eggplants, and it’s leasing affordable land and water to small farmers for an annual fee of $150 per acre.
Ultimately, Mahi Pono’s staple crops will be citrus, papaya, macadamia nuts, and coffee, Lawrence said.
And while the company is exporting papayas to Canada, and eventually plans to export coffee, macadamia nuts, and citrus to markets outside the state, the majority of the food produced by Mahi Pono will feed Hawaii’s people, Lawrence said.
“I personally think these lands can be brought into production,” Lawrence said. “We’ve seen it across Hawaii where farmers have been able to take former sugar and pineapple lands and turn it into a thriving farm and I refuse to entertain doomsday scenarios.”
Mahi Pono is growing red, yellow, and white potatoes with the goal of stealing away some of the Hawaii market share from mainland-grown potatoes. Courtesy: Mahi Pono
But the farm enterprise faces many challenges.
With an average wind speed of 30 miles per hour in the Central Maui plains, there are erosion issues, as well as crop damage from pests, deer, and pigs.
“We really can’t plant a field unless we fence it in, so that adds to our costs,” Lawrence said.
There’s also the problem of the former plantation’s aging, outdated infrastructure.
“Mahi Pono has spent a serious amount of money in updating the irrigation systems and making repairs to wells,” Lawrence said.
If Mahi Pono can surmount these challenges and find success, Cooke of Ulupono said the operation will be an example to follow.
“If they can get it up and running, that could be one of the hugest transformations that Hawaii has seen, especially going towards local food for local consumption,” Cooke said. “The worry is that it doesn’t work and somehow the land gets zoned residential and a housing development goes up.”
“Hawaii Grown” is funded in part by grants from the Ulupono Fund at the Hawaii Community Foundation, the Marisla Fund at the Hawaii Community Foundation, and the Frost Family Foundation.
Brittany Lyte is a reporter for Civil Beat. You can reach her by email at blyte@civilbeat.org or follow on Twitter at @blyte
Use the RSS feed to subscribe to Brittany Lyte's posts today
Vertical Farming At A Crossroads As Pandemic Shifts Focus To Fresh Produce
Getting the right business model to balance resource usage with socio-economic conditions is crucial to capturing new markets. Speakers will discuss the issues at the forthcoming Agri-TechE event on Thursday 25th February 2021
15-02-2021
Getting the right business model to balance resource usage with socio-economic conditions is crucial to capturing new markets. Speakers will discuss the issues at the forthcoming Agri-TechE event on Thursday 25th February 2021.
Although growing crops all year round with Controlled Environment Agriculture (CEA) has been proposed as a method to localize food production and increase resilience against extreme climate events, the efficiency and limitations of this strategy need to be evaluated for each location. Research by Luuk Graamans of Wageningen University & Research, a speaker at the upcoming Agri-TechE event on CEA, has revealed that integration with urban energy infrastructure can make vertical farms more viable.
“The pandemic has shifted the conversation to the global connectivity of countries, where people started questioning the sustainability and resilience of the international food network,” comments Luuk. “The big question is should countries or large cities (mainly) rely on imports to feed their citizens?
His research around the modeling of vertical farms shows that these systems are able to achieve higher resource use efficiencies, compared to more traditional food production, except for electricity. So, the vertical farm needs to offer additional benefits to off-set this increased energy use. One example his team has investigated is whether vertical farms could also provide heat.
“We investigated if vertical farms could provide not just food for people living in densely populated areas and also heat their homes using waste heat. We found that CEA can contribute to stabilizing the increasingly complex energy grid.”
This balance between complex factors both within the growing environment and the wider socio-economic conditions means that the rapidly growing CEA industry is beginning to diversify with different business models emerging.
Jack Farmer is CSO at LettUs Grow, the company has just launched its Drop & GrowTM growing units, which offer a complete farming solution, in a shipping container. He says that everyone in the vertical farming space is going to hit a crossroads, “Vertical farming, with its focus on higher value and higher density crops, is effectively a subset of the broader horticultural sector. All the players in the vertical farming space are facing a choice – to scale vertically and try to capture as much value in that specific space, or to diversify and take their technology expertise broader.”
LettUs Grow is focused on being the leading technology provider in containerized farming. Jack continues: “Drop & Grow:24, is primarily focused on people entering the horticultural space, and we expect it to be one of the most productive, ethical, and easy to use container farms on the market. This year is looking really exciting – supermarkets are investing to ensure a sustainable source of food production in the UK, which is what CEA provides. We’re also seeing a growth in ‘experiential’ food and retail and that’s also where we see our Drop & Grow container farm fitting in.”
Kate Hofman, CEO, GrowUp agrees, the company launched the UK’s first commercial-scale vertical farm in 2014. She comments: “It will be really interesting to see how the foodservice world recovers after lockdown – the rough numbers are that supermarket trade was up at least 11% in the last year – so retail still looks like a really good direction to go in. If we want to have an impact on the food system in the UK and change it for the better, we’re committed to partnering with those big retailers to help them deliver on their sustainability and values-driven goals.
“Our focus is very much as a salad grower that grows a fantastic product that everyone will want to buy. And we’re focusing on bringing down the cost of sustainable food, which means doing it at a big enough scale to gain the economies of production that are needed to be able to sell at everyday prices.”
The economics are an important part of the discussion. Recent investment in the sector has come from the Middle East, and other locations, where abundant solar power and scarce resources are driving interest in CEA. Luuk’s research has revealed a number of scenarios where CEA has a strong business case.
However, for the UK, CEA should be seen as a continuum from glasshouses to vertical farming. “Greenhouses can incorporate the technologies from vertical farms to increase climate control and to enhance their performance under specific climates.” Luuk continues.
It is this aspect that is grabbing the attention of conventional fresh produce growers in open field and covered crop production.
James Green is Director of Agriculture at G’s, one of Europe’s leading fresh produce growers. He explains: “There’s a balance in all of these systems between energy costs for lighting, energy costs for cooling, costs of nutrient supply, and then transportation and the supply and demand. At the end of the day, sunshine is pretty cheap and it comes up every day…
“I think a blended approach, where you’re getting as much benefit as you can from nature but you’re supplementing it and controlling the growth conditions, is what we are aiming for, rather than the fully artificially lit ‘vertical farming’.”
Luuk, Jack and Kate are to join a discussion with conventional vegetable producers, vertical farmers and technology providers at the Agri-TechE event “Controlled Environment Agriculture is growing up” 25th February 2021.
Find out more: agri-tech-e.co.uk/upcoming-events/
Agri-TechE is a business-focused membership organization, supporting the growth of a world-leading network of innovative farmers, producers, scientists, technologists, and entrepreneurs who share a vision of increasing the productivity, profitability, and sustainability of agriculture.
Together we aim to help turn challenges into business opportunities and facilitate mutually beneficial collaboration.
Agri-TechE
Join Harry Duran, Host of Vertical Farming Podcast, As He Welcomes To The Show Co-Founders of Babylon MicroFarms, Alexander Olesen and Graham Smith
In this episode, Harry talks to Alexander and Graham about the genesis of Babylon MicroFarms, why AgTech and vertical farming are critical to the advancement of our society, and technological developments that have been made in vertical farming
Season 2 Episode 24 Description
Join Harry Duran, host of Vertical Farming Podcast, as he welcomes to the show co-founders of Babylon MicroFarms, Alexander Olesen and Graham Smith. Alexander and Graham met at the University of Virginia where they first designed a low-cost micro-farm to provide nutritious produce for food-insecure refugees in the Middle East. They were initially inspired by the desire to bring the benefits of sustainable hydroponic farming to those who need it the most.
In this episode, Harry talks to Alexander and Graham about the genesis of Babylon MicroFarms, why AgTech and vertical farming are critical to the advancement of our society, and technological developments that have been made in vertical farming.
VERTICAL FARMING PODCAST
Listen & Subscribe
Why I Moved From California To Kansas To Grow Leafy Greens In All Seasons
Brad Fourby runs Leafy Green Farms LLC, a hydroponic shipping container farm in Pittsburg.
By Brad Fourby
January 9, 2021
The Kansas Reflector welcomes opinion pieces from writers who share our goal of widening the conversation about how public policies affect the day-to-day lives of people throughout our state. Brad Fourby runs Leafy Green Farms LLC, a hydroponic shipping container farm in Pittsburg.
Google Maps says the distance between Sacramento, California, and Pittsburg, Kansas, is 1,842 miles.
This year has been tough, with COVID shutdowns, a heart attack, bypass surgery, and the loss of a loved one. All of this slowed me down but did not stop me from leaving California and starting a year-round container farm that will provide Pittsburg with fresh leafy vegetables like lettuces, basils, and arugula.
Good nutrition starts with what is on your plate. Knowing where your food comes from and how it was grown is becoming more important to everyone.
While living in downtown Sacramento, I started Innovative Farms. I would build and help consult with others interested in aquaponics, growing fish and plants together in small places. Small towns have to wait and pay higher prices for food that has been grown and transported from California, China, Argentina, and other countries. The produce is picked early so that it may ripen in transit on ships or trucks while being treated with chemicals along the way.
Through this work, I met longtime Pittsburg residents Rob and Sara Morris, owners of Energy Group Consultants. They told me that Pittsburg and Crawford County were considered a food desert — like much of the Midwest, grocers in Crawford County import their food, while producers export what they grow, such as corn and soybeans.
I would visit the city a few times a year and got to know some of the people and businesses. I loved the vibe of the place.
Rob and Sara and I discussed increasing the farm-to-table opportunities in Pittsburg. We talked about container farming, using repurposed shipping containers that have been outfitted with computer-controlled vertical hydroponics. This highly efficient method requires no pesticides or herbicides to grow vegetables that can be harvested weekly regardless of the climate.
My previous experience with aquaponics reminded me of Freight Farms, a Boston farm manufacturer with a great track record of successful farms worldwide. Their farm design was expandable, and vegetables could grow in any weather condition.
I came up with the outline of a business plan. With three farms, my goal was to begin year-round harvests this winter in Pittsburg and support the farm-to-table lifestyle.
I began making phone calls to the city. Compared to the regulation and tax heavy California, Kansas felt welcoming to new business. I heard the term “agri-tourism,” and the idea of new agricultural developments directly helping the area was exciting for many people I spoke with.
The city planners loved the idea of a new business that supported other existing businesses like restaurants, grocers, and the farmers market community, many of them hurt by the COVID shutdowns.
Working with Pittsburg State University’s Small Business Development Center, I created a final business plan. Equity Bank signed on to assist with the Small Business Administration loan process.
So far it has been a real team effort. We really picked up steam after a call with Mike Green, Equity Bank’s small business banker. Turns out he grew up on a farm and instantly recognized the value the business would be to the entire area. We talked about how freshly picked non-chemically treated vegetables actually taste. The difference is night and day.
After that call I knew for sure Pittsburg would be the home of Leafy Green Farms.
The Kansas Healthy Food Initiative then stepped in and awarded the business $15,000 to assist with operating and equipment expenses. This kind of support was a real boost for everyone. KHFI and our farm goals are very much aligned.
It turned out that everyone agreed: Every Kansan should have access to healthy, affordable food.
The idea of more fresh food being produced in Pittsburg was something Live Well Crawford County director Brad Stroud told me he has been very supportive of. Joining their network has been a very positive experience.
We hope that by adding farms that are unique to the area that grows specialty crops, more people will visit the city and frequent some of the supporting businesses. We will take input from chefs and the community palate, and restaurants in the area will be able to offer menu items that their counterparts in large cities have no chance of offering. Our list of available herbs, roots, and vegetables is long and our variety is huge, with Firecracker Leaf Lettuce, Sylvesta Butterhead, and even Wasabi Arugula.
Sacramento County has around 1.5 million people, Crawford County 38,000. Many of my California friends and family are watching my move with great anticipation. When someone asks “Why Kansas?” my answer has remained the same since the beginning: Kansas is open for business.
Through its opinion section, the Kansas Reflector works to amplify the voices of people who are affected by public policies or excluded from public debate. Find information, including how to submit your own commentary, here.
Lead photo: A Freight Farms container on its way to a destination. (Submitted by Leafy Green Farms to Kansas Reflector)
The Top 5 Hydroponic Growing Mediums You Should Use
Hydroponics is a farming method that doesn’t require soil to grow plants or foods. Soil is not used in this form of farming
Hydroponics is a farming method that doesn’t require soil to grow plants or foods. Soil is not used in this form of farming. Other hydroponic growing mediums are used instead. This article is going to cover the five best hydroponic growing mediums to use for your garden.
Read
Selecting The Right Growing Medium
In this episode, Joe and Nick will discuss the right growing medium for greenhouse and indoor hydroponic farming.
Latest Episode
Funding Now Available To Help Farmers Withe FMSA
Farmers are working to improve food safety on the farm, and prepare for Food Safety Modernization Act (FSMA) inspections, but this requires both assistance and resources
February 10, 2021
A hoop house with tomatoes and peppers grown in New Mexico. Photo Credit: USDA Photo by Bob Nichols.
Farmers are working to improve food safety on the farm, and prepare for Food Safety Modernization Act (FSMA) inspections, but this requires both assistance and resources. We are excited that the Food Safety Outreach Program (FSOP) applications have just opened up and will provide organizations with funding to assist and help farmers and small food businesses with both FSMA and food safety.
FSOP is a federal grants program that funds community-based organizations, non-governmental organizations, cooperative extension, and local, state, and tribal governments’ programs focused on food safety and FSMA. The U.S. Department of Agriculture (USDA) National Institute of Food and Agriculture (NIFA) recently announced $9.6 million in FSOP grant funding this year – the most funding ever available and an increase of almost $2 million from last year.
The deadline for applications is Thursday, April 1, 2021.
Application Details
FSOP projects should focus on outreach, education, and assistance for farmers and small processors around food safety practices and the new FSMA rules. There are two types of projects eligible organizations can pursue to receive FSOP funding: Community Outreach and Collaborative Education and Training Projects. There is no match requirement.
Community Outreach Projects
FSOP will once again offer Community Outreach Projects, to support the development of new food safety programs and to help groups build capacity to address the needs of their communities. Awards can be between $80,000 and $150,000 for projects lasting up to two years. Community Outreach Projects must:
Create, implement or expand food safety education to niche, underserved, or non-traditional audiences.
Be led by a team with a record of strong community partnerships and working with others to educate target audiences.
Create and implement a customized food safety training and outreach program for various types of farms or food processors, including those working with conservation systems, sustainable businesses, and organic food producers.
Collaborative Education and Training Projects
Collaborative Education and Training Projects aim to fund state-wide, multi-state, or multi-county food safety training projects. Grant awards are available for $200,000 to $400,000 for projects up to three years. These projects must:
Be led by a project team with a track record of community partnerships and serving the educational needs of the target audiences.
Create and execute food safety education and outreach for various types of farms or food processors, including those working with conservation systems, sustainable businesses, and organic food producers.
Additional Funds Available for Outreach to Communities of Color
An additional $150,000 is available for applications to either project type that increase outreach to communities of color through the Collaborative Engagement Supplements. Organizations applying for this supplemental support must include a significant collaboration with either one or more of the following universities, colleges, or organizations: 1890s, 1994s, Insular Areas, Alaska Native-Serving and Native Hawaiian-Serving (ANNH), Hispanic Serving Agricultural Colleges and Universities (HSACU), and community-based organizations serving socially disadvantaged populations.
Regional Centers Funds
There is also funding available for the four regional centers focusing on food safety and FSMA. Current centers include:
Southern Region: University of Florida (also “Lead Regional Center”)
Western Region: Oregon State University
North Central Region: Iowa State University
Northeast Region: University of Vermont
Program Changes for FY 2021
The FSOP RFA changes highlight a few recommendations the National Sustainable Agriculture Coalition requested, and we are thankful for NIFA’s continued partnership, and efforts to ensure these changes.
NIFA clarified that the additional Collaborative Engagement Supplements must be in direct partnership with a Minority-Serving Institution or an organization working to serve farmers of color that have been historically underserved, and that the proposed budget must adequately reflect this partnership. NSAC appreciates this clarity and looks forward to further analyzing the racial equity impact of FSOP grants.
NSAC is also excited about the new requirements for Regional Centers to partner with an 1890, 1994, ANNH, HSACUs and/or community-based organizations serving socially-disadvantaged populations within their region, which will help ensure outreach and resources to farmers of color continues to be prioritized.
NSAC also appreciates the clarity that Community Outreach Projects can be used for FSMA training for the organization’s staff with minimal food safety experience and that organizations must have relationships with the target audience.
Upcoming FSOP Webinar for Tribal Staff
On Friday, February 19, 2021, from 2:00-3:00 p.m. Eastern Time the United South and Eastern Tribes, in partnership with Intertribal Agriculture Council, Indigenous Food and Agriculture Initiative, National Sustainable Agriculture Coalition, and National Institute of Food and Agriculture, will be hosting a FSOP webinar for anyone who works with indigenous producers. For more information, and to register for the webinar, click here.
Additional Resources
For additional application details and requirements, see the FY 2021 Request for Applications.
Additional information is also available via Grants.gov and on the NIFA FSOP webpage.
You can read more about analyzing FSOP awards through an equity lens here.
You can also learn more about FSOP through the National Sustainable Agriculture Coalition’s Grassroots Guide to the Farm Bill.
USA: Wichita, Kansas - Fidelity Bank’s New ‘Car Park’ Adding Ground-Floor Restaurant, Rooftop Urban Farm
Called Rise Farms, it will include 5,000 square feet of space where fresh vegetables and herbs will be grown in raised beds, large planters, and a 24x70-foot long hoop house
Fidelity Bank is embarking on a $51 million project to build a 10-story tower next to its existing five-story headquarters at Main and English. It also plans a new 505-stall parking garage. BY JAIME GREEN
The ground level of Fidelity Bank’s new five-story “car park” on Market between Waterman and English will soon have a new 4,000-square-foot restaurant on its main level.
And that’s not even the biggest news to come out of the project this week.
In addition to the restaurant — which Fidelity isn’t ready to share details about quite yet — the new parking garage will also be home to a rooftop urban farm that bank officials say will be the largest in the Midwest.
Called Rise Farms, it will include 5,000 square feet of space where fresh vegetables and herbs will be grown in raised beds, large planters, and a 24x70-foot long hoop house. The food the farm produces will be used not only by the new ground-level restaurant tenant but also by other restaurants around Wichita. Fidelity Bank employees also will be beneficiaries of the produce, and the first crops should be ready by fall.
The rooftop project will include a private event center with retractable garage doors where Fidelity can house small events and gatherings during warm weather seasons as well as a 5,622 square-foot solar farm featuring 204 solar panels, which produce 380 watts each. The panels, which weigh about 35,000 pounds, are already up and running and producing enough energy to provide the power for the car park and its first-floor tenants.
A rendering of what Fidelity Bank’s rooftop Rise Farms will look like Courtesy FIDELITY BANK
The car park, which has 405 stalls, 24 electric car charging stations employees can use, and daytime public parking on the ground level, just opened and is the first part of a $51 million Fidelity Bank expansion project that also will include a new 10-story, 135,000 square-foot office tower at 100 E. English, where the bank’s parking deck is. Construction on that hasn’t started yet.
The idea for the rooftop farm came about after Fidelity polled its employees about what types of tenants they would like to see move into the 17,000 square feet of retail space on the car park’s ground level, said Aaron Bastian, Fidelity’s president, and CEO. Overwhelmingly, they said they’d want a restaurant.
In the course of meeting with potential restaurant tenants, Bastian said, one suggested the idea of raising fresh produce on the roof.
Bastian, who said that local food culture is a topic he’s passionate about, liked the idea, but bank leadership decided they’d need to consult with an expert to pull it off.
“When we started talking about this idea, we wanted to go out and find people we could partner with to help create what we think could really be a cool downtown amenity,” Bastian said.
Fidelity has since partnered with Leah Dannar-Garcia, the owner of Firefly Farm at West 21st Street North and North 159th Street East, who already raises produce that she sells to about 38 Wichita restaurants. She’ll be in charge of the farm and will offer its produce for sale to restaurants on her route. The ground-floor restaurant, though, will get first dibs.
Fidelity Bank’s new car park in downtown Wichita just opened to employees. By fall, it will have a ground-floor restaurant and a rooftop farm. Courtesy FIDELITY BANK
Dannar-Garcia has been working with the bank for about a year, she said and has mapped out her growing plans in detail. Once it gets going, she’ll have plants growing in beds and containers along both the north and west sides of the building as well as in the climate-controlled hoop house. The bank envisions a program in which Fidelity employees will be able to volunteer to work the farm, and they’ll also set up some type of program where employees can get boxes of fresh produce to take home.
Once it’s fully functioning, the farm will produce vegetables like beets, carrots, broccoli, cauliflower, sweet potatoes, and Brussels sprouts as well as greens like arugula, Swiss chard, and spinach. It’ll also grow herbs, including parsley, cilantro, and Greek oregano.
“We’re going to grow in all four seasons on this farm, so we’ll have spring, summer, fall, and winter crops,” Dannar-Garcia said.
The project is a “natural extension” of the bank’s health, wellness, and green initiatives, it says. One goal of the farm is that it produces zero wasted food.
“Whether that means it gets donated, we haven’t defined that yet,” said Melissa Knoeber, executive vice president at Fidelity who is also the bank’s director of culture and talent. “But that’s really important to us.”
Construction on Rise Farms should start in the spring, and the first crops should be ready by fall.
COURTESY FIDELITY BANK
DENISE NEIL
316-268-6327
Denise Neil has covered restaurants and entertainment since 1997. Her Dining with Denise Facebook page is the go-to place for diners to get information about local restaurants. She’s a regular judge at local food competitions and speaks to groups all over Wichita about dining.