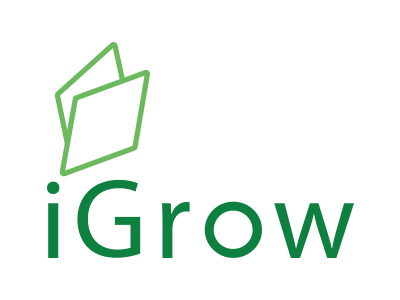
Welcome to iGrow News, Your Source for the World of Indoor Vertical Farming
POLAND: The Only Way Is Up! Puławy Vertical Farm First In Europe To Supply Beauty And Health Industries With Plant Extract From Herbs
Vertigo Farms, located in the Puławy Science and Technology Park in the east of Poland grows 11, 000 plants on an area of 300 square metres using 4 metres high metal constructions resembling shelving units, a capacity which would require an area 100 times larger if using a traditional farm
BLANKA KONOPKA
APRIL 20, 2021
Established by the husband and wife team Anna and Dawid Drzewiecki after their observations of where different plant extracts came from in cosmetics and natural supplements, the company’s innovation is based on their unique form of production, combining the growth of plants and the production of extracts in one place.
An ‘experimental’ start-up has become the first in Europe to utilize a vertical farm to both grow herbs and produce plant extracts for the beauty, health, and pharmaceutical industries.
Vertigo Farms, located in the Puławy Science and Technology Park in the east of Poland grows 11, 000 plants on an area of 300 square metres using 4 metres high metal constructions resembling shelving units, a capacity which would require an area 100 times larger if using a traditional farm.
Vertigo Farms grows 11, 000 plants on an area of 300 square metres using 4 metres high metal constructions resembling shelving units, a capacity which would require an area 100 times larger if using a traditional farm. CC BY 4.0
Established by husband and wife team Anna and Dawid Drzewiecki after their observations of where different plant extracts came from in cosmetics and natural supplements, the company’s innovation is based on their focus on vertical farming for the cosmetics and pharmaceutical industry as well as their unique form of production, combining the growth of plants and the production of extracts in one place.
The two-processes of growth and production have hitherto been separate in other companies in the same field, with sites often large distances apart.
Dawid Drzewiecki told Puls Biznesu: “Our idea was to shorten the supply chain and make it independent of logistics.
The process starts from seeds which are first kept under lamps and with constant access to water before they sprout.Vertigo Farms/Facebook
“These needs were strongly highlighted by the pandemic. Last year, there were delays in production due to difficulties in transport due to closed borders.
“More importantly, climate change is more often disrupting the production of plants, which our method of cultivation enables us to avoid.”
The farm, which is the only vertical farm in Poland focusing on delivery to the cosmetics and pharmaceutical industry, currently produces three plant types: basil, coriander and bakuchi, the latter being a herb from Asia often used as a substitute of retinol, a popular ingredient used in anti-ageing and acne creams.
Plants are grown under violet lamps with the continual monitoring of various indicators.Vertigo Farms/Facebook
The process starts from seeds which are first kept under lamps and with constant access to water before they sprout when they are transferred to the 4m units whose shelves are comprised of gutters with peat plant pots where plants are grown under violet lamps with the continual monitoring of various indicators.
The plants are then picked, dried, and passed through a machine to extract extracts from them for use in creams, oils, and dietary supplements. The whole process requires the service of just four people.
The ambitious company, which sees themselves as filling a niche due to the small number of companies producing plant extracts for the cosmetics, health, and pharma sectors, has big expansion plans.
The oil from plants grown on vertical farms.Vertigo Farms/Facebook
Earlier this year, it signed an important deal for innovative vertical farming technology with a leading Finnish company specialising in the building of vertical farms.
The technology will enable the company to experiment with tropical plants and to grow a wider variety of herbs.
Their aim is to expand to 10-20 plant types by 2022-2023.
TAGS: TECHNOLOGY, START-UP, STARTUP, HERBS, PHARMACY, PLANTS, FARM, VERTICAL FARM, VERTIGO FARMS, DAWID DRZEWIECKI, ANNA DRZEWIECKA
Sustainable Impacts Indoor Farming May Have On Environment
This article identifies the potential environmental effects large-scale indoor farming may have on air, water, and soil. We begin with an overview of what indoor farming is with a focus on greenhouses and indoor vertical farms (eg, plant factories)
Mar 18, 2021, | Knowledge Base, Learning, Research Paper
By Center of Excellence
Figure 1. Map of research and knowledge domain of indoor farming.
Abstract
This article identifies the potential environmental effects large-scale indoor farming may have on air, water, and soil. We begin with an overview of what indoor farming is with a focus on greenhouses and indoor vertical farms (eg, plant factories). Next, the differences between these 2 primary methods of indoor farming are presented based on their structural requirements, methods of growing, media, nutrient sources, lighting requirements, facility capacity, and methods of climate control. We also highlight the benefits and challenges facing indoor farming. In the next section, an overview of research and the knowledge domain of indoor and vertical farming is provided. Various authors and topics for research are highlighted. In the next section, the transformative environmental effects that indoor farming may have on air, soil, and water are discussed. This article closes with suggestions for additional research on indoor farming and its influence on the environment.
Citation
Stein EW. The Transformative Environmental Effects Large-Scale Indoor Farming May Have On Air, Water, and Soil. Air, Soil and Water Research. January 2021. doi:10.1177/1178622121995819
Introduction
Open field farming has been practiced the same way for centuries as the primary means of growing food. Its origins can be traced back to wheat production 11 000 years ago in the Middle East, which later spread to the Mediterranean, North Africa, and elsewhere.1 Given limitations on the amount of arable land, water scarcity, increased awareness of sustainable development, and the well-documented environmental effects of open-field agriculture, other farming methods have been developed in the past few decades. The primary alternative to open field farming is referred to as indoor farming, which has received relatively little attention in terms of environmental impacts. The goal of this article is to introduce indoor farming in its many forms to environmental scientists, outline key areas of research, and highlight the effects large-scale indoor farming could have on the environment. Research needs to be done to better understand the cumulative and transformative environmental effects indoor farming methods may have on water, air, and soil as it realizes its potential to supply a significant portion of the population with fresh food.
What Is Indoor Farming?
Indoor farming is a relatively new method of growing vegetables and other plants under controlled environmental conditions. These farm systems are variously referred to as indoor farms, vertical farms, vfarms, zfarms, greenhouses, controlled environment agriculture (CEA), and plant factories.2,3 Indoor farms are sometimes confused with urban farms, which typically represent small outdoor farms or gardens to grow vegetables that are located in urban areas. It also should be noted that mushrooms have been grown indoors in compost under controlled conditions without light for more than one hundred years.4 For the purposes of this article, we will focus on characteristics of controlled environment indoor vertical farms and greenhouses, which are the primary architectures used for the large-scale production of leafy greens and other vegetables that require natural or artificial light.
The many faces of indoor farming
Greenhouses have been the workhorse for indoor growers for decades, especially in the production of flowers and ornamental plants. The modern high-tech greenhouse designs were pioneered in the Netherlands and have since been embraced all over the world. Several examples of these farms are evident throughout the United States and the largest span hundreds of acres. For example, according to Greenhouse Grower,5 Altman Plants (CA) has almost 600 acres under glass followed by Costa Farms (FL) with 345 acres. These are mainly used in the production of ornamental plants.
For vegetables, greenhouses were originally designed for tomatoes but now are used in the production of kale, microgreens, lettuces, herbs, squash, and other types of fresh produce. These greenhouses, formerly located in rural areas, are now being positioned near urban and peri-urban areas to bring operations closer to population centers to save money and reduce the carbon footprint associated with transportation miles. For example, BrightFarms (brightfarms.com) has greenhouse operations located just outside of Philadelphia and Cincinnati to produce lettuces and other leafy greens. Gotham Greens (gothamgreens.com) situated its first greenhouse on top of a warehouse in Brooklyn, NY and has since expanded to other cities. AppHarvest (appharvest.com) is a venture located in Kentucky whose greenhouses cover more than 60 acres to produce tomatoes and other vegetables. What is common to greenhouse design is that all growing takes place on a single level, they are clothed in materials such as glass that transmit natural sunlight, and include climate control and irrigation equipment. They may also use a modest amount of supplemental artificial lighting during winter months.6
Growing leafy greens and other plants in buildings has emerged in the past 25 years whereby plants are grown vertically and hydroponically using artificial lights. Indoor vertical farms are typically located in warehouses or similar structures that have been retrofitted to provide superior heating, ventilation, and cooling (HVAC) for the benefit of plant production and racking systems to support the production systems.7-9 The PVC grow systems transport nutrient-rich water to the root zone of the plants, and the water is then returned to the main reservoir. Designed as closed re-circulating systems, indoor vertical farms only use a fraction of the amount of water as greenhouses or open-field methods (see also section “Water Use”). The advent of cost-effective LED lighting technologies has allowed farmers to provide the plants with just the right wavelengths of light, intensity, and photo-period to optimize growth.10 Other advances include automation, IoT, and artificial intelligence; ie, all of the information technologies that contribute to “smart farming.”11
Although modern LEDs are very efficient compared to HID, high-pressure sodium, or florescent lamps, the capital and operating costs of these artificial lighting systems are significant,10 as are the climate control systems that are also required. Greenhouses, for example, require significant investment in heating and cooling equipment to maintain stable temperatures and humidity, which results in significant operating costs in buildings with low R-value membranes (eg, glass). The chief benefit of this design is that the light comes free, although growing is limited to a single level. Indoor vertical farms, however, can benefit from well-insulated structures that reduce heating and cooling costs and growing can take place on multiple levels. That said, these savings come at the expense of relatively high electricity usage for artificial lighting.10 These operating costs can be mitigated with the increasing efficiencies of LED’s, sensing systems that modulate light to the maximum required for the plants, pairing indoor farms with renewable energy sources such as solar and geo-thermal, and architectures that favor energy efficiency.9
Methods of indoor farms
Indoor farms are characterized by several parameters:
Growing Method and Media
Source of Nutrients
Lighting Requirements
Facility Capacity
Climate Control
Economics
Most indoor farms use hydroponic methods of growing; i.e, plants are grown in water. Seeding takes place in an inert material such as stone-wool or peat, which is irrigated with nutrient–rich water. Water is administered using a variety of techniques ranging from fine mist sprayers (aeroponics), to shallow water (NFT) irrigation, to deep water culture (DWC) immersion to flood and drain methods.9 All are effective and have their pros and cons. Nutrients for larger-scale hydroponic production systems typically come from dissolved salts that ionize in the water. In some smaller systems, the nutrients come from the nutrient-rich water of fish farms (ie, aquaponic systems) that are proximate to and coupled with the plant production system.
In greenhouse production facilities, most lighting comes from the sun, which may be supplemented with artificial light, especially in the northern latitudes during winter. Plant factories and vertical farms, however, use only artificial lighting but are designed to maximize growing area using stacking methods. One common design is characterized by horizontal multi-tier growing systems starting at ground level that may include up to a dozen growing levels or tiers. Aerofarms (aerofarms.com) and Bowery Farms (boweryfarming.com) use this type of design for their production processes. An alternative is to use vertical drip irrigation grow systems. This design is characterized by vertical multi-site growing systems starting at ground level that extend upwards of 8 ft. In these systems, plants grow “sideways” toward artificial lights that are positioned at a right angle. Plenty, Inc. (plenty.ag) uses systems like these obtained in the acquisition of Bright Agrotech. Several examples of vertical farming ventures can also be found in Al-Kodmany.
All indoor farming methods share the characteristic of offering CEA. Controlled environment agriculture offers the grower complete control over several environmental variables including, but not limited to: light intensity and wavelength, photo-period, wind velocity, temperature, and humidity. Water culture is further managed to obtain optimal results based on nutrient levels, PH, and dissolved oxygen.9,12 In most cases, pesticides and herbicides are eliminated. More advanced farms such as Fifth Season (fifthseasonfresh.com) benefit from extensive use of sensors, IoT, robotics, automation, and control systems designed to optimize yields and minimize labor. Another valuable aspect of CEA farms is their ability to produce plants with certain desired morphologies and nutritional profiles based on the control of lighting wavelength, temperature, and nutrient levels. Sharath Kumar et al13 go so far as to suggest that with CEA, we are moving from genetic to environmental modification of plants.
Benefits and challenges of indoor vertical farms
Several benefits are associated with vertical farming,9 although the industry is not without its challenges (see Table 1). The principal sustainable benefits of indoor vertical farming are a large reduction in the use of water (see also section “Water Use”), the reduction or elimination of pesticides, and mitigation of the effects of excess fertilizer run-off. From an economic perspective, the ability to control the environment results in a stable supply chain, price stability, long-term contracts with distributors and retail markets, and high yields per square foot. The elimination of pesticides puts produce grown this way on par with organics, which command premium pricing. Indoor farms, if designed correctly, can reduce labor costs and may be located closer to urban centers. Some see a role for indoor farms to ameliorate food deserts, unemployment, and as a means to re-purpose abandoned buildings and lots.3,9,14-16 Finally, vertical farms provide resilience to climate change, flooding, droughts, etc.
However, the vertical farming industry is facing some key challenges. For instance, currently only a very small portion of fresh vegetables are produced indoors. The one exception is the mushroom industry, which represents a US$1.15 billion industry.17 Second, the USDA does not clearly identify vegetable production by method; eg, greenhouse, open field, vertical farm, etc, so data are not readily available. Third, profits have been elusive, especially for vertical farms.18 According to the 2019 Global CEA Census Report only 15% of shipping container farms and 37% of indoor vertical farms were profitable vs. 45% for greenhouse operations.19 Another limitation of indoor farming is that a relatively small number of cultivars can be grown using indoor farming methods.
The primary ones are leafy greens, herbs, microgreens, tomatoes, and peppers, although berries, root vegetables, and other more exotic plants are being trialed.19 Another challenge for indoor farm start-ups are the high capital costs, which can range from US$50-150/ft2 for greenhouses to US$150-400/ft2 for vertical farms. For example, AppHarvest had to raise over US$150 million to fund its 60-acre greenhouse complex.20 Aerofarms raised US$42 million for a 150 000 ft2 vertical farm,21 which equates to over US$280/ft2. Cosgrove22 further reports that access to capital is impeding the growth of indoor farming, especially for smaller farms. One reason that indoor vertical farms are not easily profitable is that they have to compete against conventional farms, which still enjoy a cost advantage.
As a result, indoor farms typically price product toward the high end and along the lines of pricing for organics,2 which limits market penetration. The 2 major factors contributing to the high costs of indoor and vertical farm operations are energy10,23,24 and labor, which account for nearly 3 quarters of the total.2,24 Despite these challenges, venture capital continues to pour money into indoor farming and agtech in the hopes of driving cost down and maintaining growth. Dehlinger25 reported that US$2.8 billion was invested by venture capitalists in Agtech companies in 2019.
Finally, the industry is struggling to share knowledge, establish standards, and create best practices, although progress is being made. For example, the Center of Excellence for Indoor Agriculture established a “Best in Class” award for growers and manufacturers (indoorgacenter.org). Indoor Ag-Con (indoor.ag) and the Indoor Agtech Innovation Summit (rethinkevents.com) hold online events and annual conferences to help promote knowledge sharing. Several specialized industry news outlets now exist including Vertical Farm Daily (verticalfarmdaily.com), Urban Ag News (urbanagnews.com), iGrow (igrow.news), Hortidaily (hortidaily.com), AgFunder Network (agfundernews.com), and others.
Read more >>>
Keywords: Indoor farming, vertical farming, vfarm, zfarm, plant factory, water, air, soil, sustainability, carbon cycles, drought, information technology, greenhouse gases, climate change, environment, agtech
Robotic Warehouse Farms Will Save The World
The theory behind CEA is that by controlling the environment in which it grows, we can control everything about a plant and what it grows into by micro-tweaking one of a thousand different characteristics―including temperature, humidity, light duration, light wavelength, dissolved oxygen in the water, and carbon dioxide saturation in the air
by Elle Griffin
Four years ago, Ritch Wood was looking for a better way to grow plants. As the CEO of global skincare company Nu Skin, he ran into ingredient shortages every winter when fields went dormant―and when he moved grow operations to the equator he ran into water and land shortages, along with a host of quality control issues.
Nu Skin needed reliable, quality ingredients for their skincare products. But farming was too unpredictable an industry. “If there was a way to grow indoors,” he thought, “and be able to do that 24 hours a day, 365 days a year―if we could guarantee that it was grown without any herbicides or pesticides and in a sustainable way that uses less water and land―that would be really helpful.”
At the time, controlled-environment agriculture (CEA) was in its infancy and grow-light technology had yet to take a turn for the more affordable. When he learned of an agricultural system that promised to use a fraction of the land and water used by traditional agriculture methods and had the potential to make it more affordable, Wood made an investment.
Nu Skin paid $3 million for 70 percent of the company and rights to its IP―and Grōv Technologies was born.
Grōv grass grown in the Olympus machine at the Bateman Mosida Farms. Photo from Grōv Technologies
Controlled-environment agriculture is on the rise
The theory behind CEA is that by controlling the environment in which it grows, we can control everything about a plant and what it grows into by micro-tweaking one of a thousand different characteristics―including temperature, humidity, light duration, light wavelength, dissolved oxygen in the water, and carbon dioxide saturation in the air. By tweaking the growing cycle, we can control the caloric content as well as the nutrient content and density of the plant.
“What we’ve learned through controlled-environment agriculture,” Benjamin Swan, co-founder and CEO at Sustenir in Singapore, once told National Geographic, “[is] we can actually emphasize certain characteristics of the plants. So, without using GMO, we can make our kale softer, we can actually make it sweet.”
The theoretical use cases for this technology are endless―from being able to grow in places where water is scarce (like in much of Africa), or where water is overly abundant (like Hawaii), or in places where labor is scarce (like in parts of Asia), or even in places that have long winters (like Northern Europe). Theoretically, we could have grow towers in every town and feed the whole of it no matter its natural environment.
We could even grow those foods to those cities’ exact nutritional needs―more vitamin D-rich foods in wintery places, for example. Dr. Lee Mun Wei, a senior manager at the Food Innovation and Resource Centre (FIRC) in Singapore aims to predict and prevent illness in a given population by tracking their biometric data using Apple watch-like wearables, then 3D printing nutrient-specific foods that could mitigate imbalances.
Though these technologies exist, they are still in their infancy. Singapore leads much of the research and development out of necessity. With limited land and water resources, the county is forced to import 90 percent of their food and 40 percent of their water from outside the country. As a result, they have no option but to grow vertically and desalinate water from the ocean.
Elsewhere, the industry has been slow to catch on, largely due to exorbitant startup costs, low returns, and lack of urgent need. According to a 2017 State of Farming report by L.E.K., only 27 percent of indoor, vertical farms are profitable compared with 50 percent of container farms and 75 percent of greenhouses. But one thing has spurred the industry on in recent years: cannabis.
Legalized in 39 states, demand for cannabis has created a $13.6 billion industry and enough capital to fund CEA-enabled grow operations. “When you have a crop that fetches up to $2,400 or $2,500 a pound, you need to be able to dial everything in and make it consistent and repeatable,” says Dashiel Kulander, co-founder and CEO at Boojum Group. “If the temperature swings five to 10 degrees on a cannabis plant, that will change the plant’s various cannabinoids. The goal is to create a medicine that is consistent batch after batch.”
It’s only recently that there has been some financial incentive to use CEA technologies for food use―largely driven by Big Ag players hoping to hedge out the competition. Berry farming giant Driscoll’s, for one, led a $500 million round to fund Plenty, a 2.2-acre vertical farm in California they hope will help them fulfill a contract with Albertsons. The Ingka Group, for another, led a $100 million round to fund AeroFarms, a 2.4-acre vertical farm in New Jersey that will help them fulfill a contract with Singapore Airlines.
Grōv tent at the Bateman Mosida Farms. Photo from Grōv Technologies
Grōv Tech is building CEA prototypes in Utah
By investing in Grōv Tech, Nu Skin hopes to do something similar, getting ahead of the supply chain that fuels their skincare products before the competition can beat them to it, or before climate change makes traditional methods more difficult, all while shoring up technology that could provide a farming model that is more sustainable―if only it were more economical.
“The purpose was always, can we build a better product for Nu Skin?” Wood says. “We think there’s a huge story around the ingredient sustainability, and there were a lot of ingredients we felt we could grow, but the challenge was: could we do it in an economical way?”
Grōv Tech started out with a prototype: a tower that pairs hydroponic growing technology with grow lights. But like all CEA startups, a lot of the growing process was manual and the technology was prohibitively expensive. To make something that was scalable and profitable the whole thing needed to be automated and it needed to be cheap.
With this goal in mind, Wood decided they would start by growing animal feed for Bateman’s Dairy farm. Having grown up on a dairy farm himself, Wood figured this would allow the company to scale the product while refining and automating the technology to the point that it could be replicated. And all of this would have a fortuitous effect on Nu Skin’s bottom line.
“One of our bestselling products is a weight-loss protein powder which uses whey protein,” Wood says. “So again, a very nice connection there is if the animal is eating a more sustainable product and producing better milk with better protein and it’s being done in a sustainable way―certainly that can be a benefit to Nu Skin down the road.”
One year into feeding the 20,000 animals at Bateman, the company has learned a lot. For instance: cows need a lot of magnesium, but they don’t like eating it. Now, Grōv Tech puts magnesium in the water so it’s directly absorbed into the plant and then becomes bioavailable to the cow upon eating it. And because the growing process only takes seven days, data scientists can analyze the results in real-time and adjust the components to optimize production for the next batch of feed.
According to Grōv Tech president Steven Lindsley, it’s not far off that we’ll be looking at milk production (butter, fats, and proteins) and optimizing a herd’s diet for taste, quality, and nutritional value―not to mention the wellbeing of the animal. We’ll be able to look at how many trips from the veterinarian an animal gets when they’re fed certain nutrients in their diet, and whether they can have more calves and produce the same amount of dairy on less, better quality feed. (So far, the answer to this last question is yes. When animals are fed better quality food they need less of it―just like humans.)
And if we hook all of the cows up to robotic milking equipment and connect everything to artificial intelligence, machine learning, and the Internet of Things―Lindsley’s far-flung goal―then we might be able to collect enough data to not only feed cows to their optimum health and performance ability, but humans too. And that could have ramifications not only for feeding the world, but nourishing it― just like Dr. Wei hopes to do in Singapore.
“Last year was about starting to feed animals and get data and prove out the hypothesis we have while continuing to perfect the technology and get confidence there,” Wood says. “And now we’re really to a point where we’ve got data that proves that it works and that financially it’ll be a good thing for a farmer. So now we can really take that proposition to farmers and start to scale.”
Olympus Tower Farm at Bateman Farms in Mosida, UT. Photo from Grōv Technologies
CEA technology could feed the world
Right now, Grōv Tech is focused on refining its technology right here in our own backyard. But once they do that, the plan is to expand internationally.
“Saudi Arabia has actually passed a law where you cannot use water to grow fodder or feed for animals, so all of that now has to be imported. China imports one-third of their alfalfa feed for their dairy animals because they don’t have the capability of growing it,” Wood says. “So there are countries that will probably benefit more than the US would. But we’ve got to refine the technology and get that built to where it’s ready to scale before we start spreading ourselves all around the globe.”
CEA technology is just getting started. Like the Tesla Cybertruck, we have a working concept that promises a more-than-Jetson’s-level future many of us can see the benefits of and actively want―it’s just not quite available to the masses yet. But with more than a billion dollars invested in the technology in just the past few years alone―we’re getting there. And the “there” we are heading toward is rosy indeed.
“To put it in perspective, one tower that is about 875 square feet on the ground will replace 35 to 50 acres of land,” says Lindsley. “And that will feed the animals on roughly five percent of the amount of water. The UN says that that the world will add about 2.5 billion people in the next 30 years. And we have to find a way to feed them on arguably less arable land and water. The good news is the technology is coming along to help solve that equation.”
If COVID-19 taught us anything, it’s that our food supply chain is fragile. But that’s only because our supply chain was built to grow food in California, refrigerate it so it stays fresh, then transport it 1,500 miles so we can eat a salad in the winter in Chicago. In the future, that might not be a thing. “We’re having a dry year now,” Lindsley tells me in February. “But a year ago we were in a blizzard, and even in the middle of a blizzard in February in Utah, we’re pumping out fresh, beautiful, safe green grass for animals. It’s a paradigm shift.”
“Four years ago it was a good idea,” Wood tells me of his company’s investment in CEA technology, “But four years from now it’s going to be required.”
Elle is the editor-in-chief of Utah Business and a freelance writer for Forbes, The Muse, and The Startup. She is also a literary novelist and the author of a weekly newsletter called The Novelist.
Learn more at ellegriffin.com.
Explore The Sixth Edition of Clima, Powered by IGS
In this edition, we look at why precision farming and Controlled Environment Agriculture (CEA) techniques are becoming more mainstream, and the skills and talent required to make this approach a success
In this edition, we look at why precision farming and Controlled Environment Agriculture (CEA) techniques are becoming more mainstream, and the skills and talent required to make this approach a success. Technology is having a greater impact on agriculture than ever before, and this is only set to increase. It will bring with it a wider and more advanced agricultural ecosystem that requires a skilled, knowledgeable, and committed workforce, with as great an appetite for innovation and capacity to problem solve as any generation before.
Discover more on this topic in the sixth edition of Clima today.
Bringing future talent to Agriculture 4.0
We discuss the emerging influences on education and skills development across Agriculture and Horticulture with two senior leaders from Scotland’s Rural College (SRUC). We spoke to Professor Fiona Burnett, Head of Connect for Impact in SRUC’s Knowledge and Information Hub, and Ruth Vichos, Lecturer in Horticulture, about the evolution of Agriculture 4.0, and how technology is impacting skills evolution and teaching mechanisms.
Listen To The Full Interview
The World’s First Autonomous Greenhouse Manager
Geert van der Wel started in the role of Autonomous Greenhouse Manager at Blue Radix. He represents the human support side of the Crop Controller service in addition to the smart algorithms that control greenhouses
07-04-2021 | Goedemorgen
Early February, Geert van der Wel started in the role of Autonomous Greenhouse Manager at Blue Radix. He represents the human support side of the Crop Controller service in addition to the smart algorithms that control greenhouses. Read more about how Geert helps customers and about his background. As he says himself: "I was almost literally born among tomatoes in De Lier, where my parents had a tomato greenhouse."
Name: Geert van der Wel
Home: I’ve been married to Tessa for 16 years and we have two children. We have lived in Burgundian West Brabant since 1998.
Childhood: Almost literally, I was born among the tomatoes in De Lier, where my parents had a tomato greenhouse.
Study: I completed Secondary Horticultural School in De Lier, and also undertook several (horticultural) studies.
Work experience: I worked in my parents’ tomato greenhouse right from my childhood. After finishing my studies my partner and I became owners of Kwekerij Polderwel for ten years, growing tomatoes on 2.5 hectares. We wound up this undertaking because of the construction of the A4 highway between Antwerp and Rotterdam. Then I did three years as a manager at the Nuijten plant nursery, and when this firm ceased trading I ended up at Nickerson-Zwaan in Made; it later became known as Hazera Seeds. For the first four years, I worked in the Planning & Control department, moving on to become Product Manager High-Tech Tomatoes for the final five years.
What can you do for growers as an Autonomous Greenhouse Manager?
“Blue Radix offers autonomous growing as a service. So alongside our smart algorithms controlling the greenhouse, our Crop Controller service also has a ‘human side’, and customers get daily support from an off-site Autonomous Greenhouse Manager (AGM). So as that AGM I’m constantly looking over the customer’s shoulder, and I’m their first point of contact. Right from the start, I guide clients intensively in taking their first steps into the world of algorithms. They are given an extensive onboarding program where they get explanations on the steps to autonomous growing, the operation of the algorithms, and the Crop Controller portal. I also monitor the management of the greenhouse continuously and discuss the progress on a regular basis, including through reports. My work experience has taken me through all the processes involved, from seed to the final product. This is what enables me to support our customers fully as AGM, to advise them, and to help them to realize their crop strategies.”
Blue Radix offers autonomous growing as a service; why is this important?
“Cultivation is the core business of every greenhouse company. To leave this completely to autonomous control requires a lot of trust from the customer. We are very aware that autonomous growing is still quite new and innovative. Providing good service with the support of the AGM lets us guide growers fully in working with algorithms. Our experience shows that customers are more likely to abandon their own processes and working methods step by step because there’s always someone monitoring the entire process.”
Describe your day. How do you monitor greenhouses worldwide?
“Every day I open the Crop Controller portal to see how the algorithms are behaving in terms of our various customers’ crop strategies. I contact the grower if any anomalies appear, or if there’s a technical issue I get in touch with the Blue Radix product developers. This also applies to feedback I receive from customers on how we can optimize Crop Controller still further.”
What do you like about your job? And what are your views on autonomous greenhouse management?
“In the horticultural world, it’s great to see that there’s a continuous search for innovations, and specifically for autonomous growing. I used sensors and digital tools on a small scale when I was a grower myself. But at that time I got very little guidance on how they worked and how to interpret it all. Now I use this experience to give our customers good information so that ultimately they’ll be able to grow autonomously in the best possible way!”
Got a question for Geert, or about autonomous growing generally?
Send us a message, and we’ll be happy to help you.
Gardening Without Borders, In Partnership With Agritecture
At Plant People, we believe everyone should have the ability to produce quality food, so we have partnered with AGRITECTURE - the leaders in urban agriculture consulting services - to empower people to bring greenery into their home during these difficult times
Even though urban gardening has been gaining popularity over the years, city dwellers have never become more aware of where and how they get their food than during the pandemic. The Food and Agriculture Organization of the United Nations states that at least 55% of the world’s population already lives in urban areas and 80% of all food produced globally is destined for consumption in urban spaces. When the food supply chain could not match demand during the pandemic, food shortages plagued cities as supermarket shelves remained empty for days. During the World Wars, Americans grew “victory gardens” to combat food shortages - and many individuals today are returning to this novel idea to gain control over their food supply and to find an escape from life in lockdown as well.
At Plant People, we believe everyone should have the ability to produce quality food, so we have partnered with AGRITECTURE - the leaders in urban agriculture consulting services - to empower people to bring greenery into their homes during these difficult times. It doesn’t matter if you have killed every plant in your tiny apartment or live in a flat where the nearest park is miles away. Embracing your green thumb and growing your own vegetable garden is only possible if you just start. Trial and error is essential.
First, when blueprinting your urban garden, do not stress about space constraints. There is a gardening method that fits every shape and size. Rooftop access is ideal, but not a necessity. You can also use a balcony, apartment wall, or even a window. Here are five, easy methods to choose from to fit your exact urban gardening needs:
Vertical gardening: As the name suggests, vertical gardening is when you hang plants along vertical surfaces, such as walls, barriers, and fences. You can also mount a series of hanging plants from a window if that is all the space you have. Herbs are best for this type of gardening.
Container gardening: Have a spare box, basket, pot, or old foosball table? Then you can container garden. Depending on the size of your planter, you can grow herbs and vegetables. Just place the container where you have an empty corner and let the seeds grow.
Hydroponic gardening: The most new-age type of gardening, hydroponic gardening uses no soil. Instead, plants grow in a solution of water and nutrients. While this can get quite technical and expensive, there are cost-efficient options that can even fit on a desk!
Rooftop gardening: The most traditional type of urban gardening. If you have the space, rooftops can easily be transformed into a vibrant vegetable and herb garden. Build (or purchase) some garden beds and viola!
Community gardening: According to a recent report by the U.S. Department of Agriculture, 9.4 million Americans' nearest grocery is more than 1 mile away in urban areas or 10 miles away in rural areas. Community gardens are combating these food deserts and bringing communities together. Do a quick Google search to see where your nearest community garden is. Not only will you help others have access to fresh produce, but you will also engage with people in your neighborhood.
Once you have identified what your urban garden will look like, purchase soil and seeds, and then, you are ready to grow your green oasis. Start off with easy vegetables like tomatoes, eggplants, and peppers. Radishes, beans, Swiss chard, kale, and sweet peas are also good options as they grow quickly. Ideally, tie the produce you are growing to the seasons in order to set you up for the most success. If you want to take your urban gardening to the next level and increase biodiversity of your city, build sustainable gardens that support pollinators and attract wildlife, such as bees and butterflies. Doing so will help create new pathways for birds with the new food source and also help cool down the city.
Urban gardening also has other advantages beyond producing nutritious food. It reduces your stress levels, cuts food costs and waste, and lowers your ecological footprint. As to urban agriculture’s broader social impact, these gardens create a safe space for communities to come together to grow food and have a hands-on education about nutrition and food access. Urban agriculture is also more than a food source; it’s a new typology of job creation and economic development. Local food demand has increased from 5 billion dollars in value in 2008 to 20 billion dollars in 2019, so urban agriculture has a strong economic value-add on top of its social, mental, and environmental benefits.
Simply put, living in a city does not mean you have to sacrifice green living. Urban gardening is a part of a growing agriculture revolution that is inspiring people to reconnect with food and nature regardless of where they live. Not to mention that you also get nutritious, fresh produce out of the experience.
A USDA study found that New York City urban gardens produce tomato plants with a yield of 4.6 pounds per plant compared with a conventional average of 0.6 pounds per plant. So grab your tools, find an empty corner, and start urban gardening - you won’t regret it!
A Number of Pain Points Drive Middle East (Growth) Intensification
An international consulting company says New Zealand has a real opportunity to be a partner of choice with the Middle East in providing agritech solutions to a growing agriculture sector
And NZ Suppliers Are Ready To Help Them
An international consulting company says New Zealand has a real opportunity to be a partner of choice with the Middle East in providing agritech solutions to a growing agriculture sector. Alpha Kennedy, from Prime Consulting International, told delegates at the MobileTECH Ag event in Rotorua that the United Arab Emirates and Gulf Countries are just about to begin major expansion, especially in horticulture.
"Whether it's precision agriculture, remote sensors, irrigation systems, soil regeneration and fertility, farm management, software training, robotic harvesting, pricing information or market access applications," Mr. Kennedy said. "If you have a product that fits into those focus areas there is a place for you to (partner) a customer who is willing to listen, and willing to pay. The UAE and the wider Gulf Cooperation Council (GCC) areas have a very distinct set of challenges, such as the higher cost of food imports, the high cost of production, environmental barriers, skilled workers - they all require technological solutions to overcome them. But this opportunity will not be around forever. New Zealand has a very good name as an agriculture innovator, so they will give NZ companies the time and listen, but ultimately they are moving forward quickly and will go with those who are there. There are Dutch, Irish or Israeli companies, for example, that are also keenly aware of opportunities."
Photo: some of the agritech projects underway in UAE, including vertical farming and vegetable production. Source: Alpha Kennedy's presentation at MobileTECH Ag.
New Zealand's Trade Commissioner and Consul-General to the United Arab Emirates (UAE), Kevin McKenna says the UAE is New Zealand's 10th largest trading partner.
"It is a crucial gateway for New Zealand goods and services to Africa, the rest of the Middle East and parts of Europe," he said. "The UAE and its neighbor Saudi Arabia are two of our fastest-growing export markets. The paradox in the UAE is that just two kilometres away (from Dubai's busy city centre) lies desert land that flows into rocky mountains and then more desert beyond. So, while the people will need more of our fruits and other food, they hunger for smarts to sustainably feed themselves and the populations around them. That's the challenge, but it also provides an enormous opportunity for New Zealand - we are highly respected for our agritech."
Mr. Kennedy adds that the United Arab Emirates' agriculture industry is worth more than US$3billion annually and growing by 4 percent overall, and the horticulture sector is growing by 6 percent. In 2019, horticulture produced 1.25million tonnes of field crops, fruit, and vegetables, mostly in the country's north, while vertical farms are being created in Dubai, Abu Dhabi, and Sharjah.
"There are a number of 'pain-points driving the (growth) intensification; firstly, it is hard to grow food in the UAE," he said. "It's not impossibly hard, but very hard. Summer can be above 50 degrees Celsius, and winter can be balmy in the 20s. There is also very little rainfall and the country is dependent on desalinization, which is expensive to produce and of the water that is produced, 66 percent is used for agriculture purposes. The cost of water is also subsidized and the government is looking to end those subsidies in coming years. This means that they are constantly on the lookout for tech and emerging technologies that can address these challenges."
As a result, the UAE currently imports around 90 percent of its food. Mr. Kennedy says this figure has been increasing, as has the dollar cost of importing, and with the country's population set to increase to 15 million over the next 20 years, it is imperative to increase domestic production for food security and quality of life.
"They have set some very ambitious targets and they are aiming to be the most food-secure nation by 2050," he said. "That will require a mix of domestic production, trade agreements, and the like. But these pain points are not just being experienced in the UAE but are widely experienced across the Gulf states and they all have transformation plans in place to improve food security. So, the opportunities are not just in the UAE but much broader and agriculture in the GCC is already valued at $20billion. For (NZ) companies with products, solutions, and developments, I encourage you to take advantage of these technology incubators, accelerators, and financing programs. There is a range of financial support available."
He says the future of agritech is already taking place with vertical farms coming into production in the past 18 months, and in 2020 Abu Dhabi invested US$200million in vertical farms.
Mr. McKenna is encouraging interested companies and agencies to attend and make connections at the World Expo in Dubai, which was postponed from last year, and will run for six months from October 2021.
"We have designed a discover agritech program for exporters working across all aspects of the sector," he said. "The program is going to include online learning, webinars, advisor meetings in New Zealand. Followed by a week here to look at what is going on. We are going to have project visits, we are going to meet with government departments, advisors, and partners, we will look at some of the accelerators and a specialized visit to the Agra Middle East trade show."
For more information
Alpha Kennedy
Prime Consulting International
Phone: +971 56 362 8956
mena@primeconsultants.net
www.primeconsultants.net
Publication date: Tue 6 Apr 2021
Author: Matt Russell
© HortiDaily.com
"We See An Ever-Increasing Interest In Hydroponic Growing"
Quentin has noticed that this movement is already going on in Mexico. “Little by little, farmers and growers are changing their ways
Quentin Gomis, Biogrow Substrates,
On The Mexican Market
"Ever since I was a little boy, my dad took me to the greenhouses where he worked. From a very young age I knew everything about growing tomatoes: the planting, the seedlings, taking care of the growth, and picking them," says Quentin Gomis. He has just been hired as the new commercial manager for Biogrow Substrates in Mexico and, together with their local partner Toyo Kasei, will help this market grow. “I have always believed the future of agriculture should be sustainable, and now it’s the turn of my generation to help move the industry even more in that direction,” he says.
Responsible products
Quentin has noticed that this movement is already going on in Mexico. “Little by little, farmers and growers are changing their ways. The world is changing and consumers are becoming more and more demanding with regard to ecologically responsible products. It’s a big challenge for growers to change their ways of working and the transition to becoming sustainable can also be a synonym of “big investment."
However, growing in a more sustainable way also presents the growers with many advantages. “We see an ever-increasing interest in hydroponic growing, which is in large part due to growers noticing that they can produce up to three times more when using coco peat substrate compared to growing the conventional way.”
Growing demand, growing supply
A growing demand for substrate also means a growing supply, Quentin has noticed. “About 5 years ago, there were only a few coco peat substrate brands, now there must be around 20. So, we could say it is a crowded market and competition is tough, nonetheless, there are always gaps to fill as agricultural techniques are constantly evolving.” New techniques and equipment are what growers are looking for and that is where Biogrow comes in. Quentin will strengthen the service and technical support the company offers to their Mexican customers. “Growers from all over the world are now looking for solutions to help them respond to this growing demand for planet-friendly food. At Biogrow we produce substrates that come from a sustainable resource and respect the environment. At the same time, we accompany our customers all the way through the process from technical support to the delivery at the doors of the greenhouse. This includes a dedicated technical support and logistics team, on-time deliveries and of course maintaining the same substrate quality and efficiency year on year.”
Cooperative base
Quentin is well aware of the challenges and opportunities that growers face. “We give around-the-clock technical support to our customers and we know from first-hand experience what is required to optimize yield and productivity. At Biogrow, we are not only selling coco-based substrates, we are also growers working for growers,” he says, referring to the cooperative that forms the base of the company. “In France, where our head office is located, our primary activity for decades has been growing fruit and vegetables. It’s thanks to this long-established growing experience that we’ve been able to develop our substrate range over the last 25 years."
“Ultimately, we want to build on the solid base we already have here in Mexico, strengthen the link to our customers and accompany them over the years to come, so that they can grow better and more sustainably. A win/win situation for everyone involved,” he concludes. “It really is an exciting time to be part of this industry and see all the positive changes that are happening, especially regarding the industry-wide drive towards sustainability.”
For more information:
Bio-Grow
Quentin Gomis
q.gomis@bio-grow.com
www.bio-grow.com
Toyo Kasei
www.toyokasei.com.mx
Publication date: Tue 6 Apr 2021
Author: Arlette Sijmonsma
© HortiDaily.com
Expanding Controlled Environment Agriculture Beyond 'The Big 4'
Greenhouses, vertical farms, and hybrid systems (collectively known as controlled environment agriculture or CEA) continue to attract investment at a much greater scale than in previous decades
By PETER TASGAL
March 29, 2021
Greenhouses, vertical farms, and hybrid systems (collectively known as controlled environment agriculture or CEA) continue to attract investment at a much greater scale than in previous decades. In each of the past five years, there have been multiple nine-figure capital raises. Capital has been deployed across farm types:
Large-scale greenhouses (e.g., AppHarvest, Mastronardi Produce),
Regional greenhouses (e.g., Gotham Greens, Bright Farms),
Localized vertical farms (e.g., InFarm – Berlin, Kalera).
Sources of funding have expanded from almost exclusively highly-specialized private equity investors to include public equity, mezzanine debt and even commercial banks. Within these funding sources, the breadth of investors has expanded beyond agriculture-focused investors to more mainstream investors, especially those with an interest in Environmental, Social and Corporate Governance (ESG) investing.
More from The Packer: Deep dive on the economics of greenhouse growing
Despite all of the investment, the vast majority of produce grown in CEA’s across North America consists of tomatoes, cucumbers, peppers, and lettuce, and leafy greens (“The Big 4”). Most of the lettuce and leafy greens are coming from CEA’s in the U.S. In Canada, The Ontario Greenhouse Vegetable Growers include 220 members producing tomatoes, cucumbers, and peppers on over 3,000 acres of greenhouse.
In my opinion, the next leap for the industry will be expanding the breadth of products. Specifically, focusing on products the taste of which is highly important to the consumer. A strawberry, for example, is a more important purchasing decision to the average consumer compared to lettuce. Lettuce is much more likely to be eaten as part of a salad along with a variety of other ingredients. Today, you can buy at mainstream retail locations a greenhouse-grown strawberry likely grown by Mucci Farms in Ontario or Mastronardi’s Green Empire Farms in New York.
Consumer demand will continue to drive product expansion. Meeting that demand will be possible through further investment in the CEA space. Although investment has been growing, it has not met the levels of other industries where many billions of dollars have been invested on an annual basis. Investment levels in CEA are likely to become far greater over the near future as some of the largest investors in the world are focused on investments that meet and exceed ESG standards.
More from The Packer: On tour with AeroFarms
Efficient vertical farms and greenhouses meet and exceed ESG standards. The farms are closed-loop systems where everything that goes into the farm is contained and recycled. Additionally, as the environment is fully controlled, only the precise amounts of inputs are added so as to limit excess waste. Lastly, a controlled environment allows for plants to grow without chemicals and pesticides.
Combining consumers’ desire for more locally-grown produce throughout all seasons of the year with increased investor appetite should drive great growth across the industry for years to come. I believe the biggest leap will be new and exciting products coming from indoor farms. This will all be enhanced with incremental improvements in product taste, farm efficiency, and additional varieties within The Big 4 and other products to come.
Peter Tasgal is a Boston-area food agriculture consultant focused on controlled environment agriculture.
Our Monthly Webinar For April Is “Training The Next Generation of Aquaponic Farmers” From Researcher Sarah Milliken At The University of Greenwich, U.K.
Ms. Milliken will introduce an open access aquaponics curriculum, Aqu@teach, specifically developed for college students with a focus on entrepreneurial and transferable skills
The Webinar Will Take Place Live, Saturday,
April 17 From 11 am To 12 pm EST And Feature A Live Q&A.
Click Below To Register:
REGISTER: Training the Next Generation of Aquaponic Farmers
Ms. Milliken will introduce an open access aquaponics curriculum, Aqu@teach, specifically developed for college students with a focus on entrepreneurial and transferable skills. As soilless food production technologies become increasingly important in light of climate change and the threat of food insecurity, there is an urgent need to provide an appropriately trained workforce.
The Webinar is free to the public during the live broadcast. The Webinar will remain available for free, in perpetuity, to all Aquaponics Association Members in the Member’s Area of our Community Site.
Special thanks to Ed "Aqua-Eddie" Tivnan, Association Director of STEM Aquaponics, for organizing the webinar.
Hope to see you there!
Brian Filipowich, Chairman
Aquaponics Association
The Aquaponics Association
1240 Evarts Street, NE
Washington, DC 20018
Vertical Farming Startup Oishii Raises $50m In Series A Funding
“We aim to be the largest strawberry producer in the world, and this capital allows us to bring the best-tasting, healthiest berry to everyone.”
By Sian Yates
03/11/2021
Oishii, a vertical farming startup based in New Jersey, has raised $50 million during a Series A funding round led by Sparx Group’s Mirai Creation Fund II.
The funds will enable Oishii to open vertical strawberry farms in new markets, expand its flagship farm outside of Manhattan, and accelerate its investment in R&D.
“Our mission is to change the way we grow food. We set out to deliver exceptionally delicious and sustainable produce,” said Oishii CEO Hiroki Koga. “We started with the strawberry – a fruit that routinely tops the dirty dozen of most pesticide-riddled crops – as it has long been considered the ‘holy grail’ of vertical farming.”
“We aim to be the largest strawberry producer in the world, and this capital allows us to bring the best-tasting, healthiest berry to everyone. From there, we’ll quickly expand into new fruits and produce,” he added.
Oishii is already known for its innovative farming techniques that have enabled the company to “perfect the strawberry,” while its proprietary and first-of-its-kind pollination method is conducted naturally with bees.
The company’s vertical farms feature zero pesticides and produce ripe fruit all year round, using less water and land than traditional agricultural methods.
“Oishii is the farm of the future,” said Sparx Group president and Group CEO Shuhei Abe. “The cultivation and pollination techniques the company has developed set them well apart from the industry, positioning Oishii to quickly revolutionise agriculture as we know it.”
The company has raised a total of $55 million since its founding in 2016.
Three Ways Singapore Is Designing Urban Farms To Create Food Security
Securing food during a crisis and preserving land for a livable climate is changing the focus of farming from rural areas to cities
FARMING IN THE CITY
Urban farming in Singapore
How Singapore has stimulated innovation in urban farming on a massive scale
By Clarisa Diaz | Things Reporter
March 31, 2021
Securing food during a crisis and preserving land for a livable climate is changing the focus of farming from rural areas to cities. At the forefront of this shift is Singapore, a city-sized country that aims to produce 30% of its own food by 2030. But with 90% of Singapore’s food coming from abroad, the challenge is a tall order. The plan calls for everyone in the city to grow what they can, with government grants going to those who can use technology to yield greater amounts.
“This target took into consideration the land available for agri-food production and the potential advances in technologies and innovation,” said Goh Wee Hou, the director of the Food Supply Strategies Department at the Singapore Food Agency. “Local food production currently accounts for less than 10% of our nutritional needs.”
The food items with potential for increased domestic production include vegetables, eggs, and fish. According to the Singapore Food Agency, these three types of goods are commonly consumed but are perishable and more susceptible to supply disruptions. Alternative proteins such as plant-based and lab-grown meats could also contribute to the “30 by 30” goal. In 2020, there were 238 licensed farms in Singapore.
Only 1% of Singapore’s land is being used for conventional farming. That created the constraint of growing more with less. The government has put its hopes in technology, stating that multi-story LED vegetable farms and recirculating aquaculture systems can produce 10 to 15 times more vegetables and fish than conventional farms.
Since 2017, land has been leased in two districts on the edge of the city—Lim Chu Kang and Sungei Tengah—to large-scale commercial farm projects. While the optimization of these farms to produce at maximum capacity is being determined, the idea of growing food in the more urban spaces of Singapore has emerged: from carpark rooftops to reused outdoor spaces and retrofitted building interiors.
Urban farms in Singapore
Urban farms using hydroponics on parking structure roofs
Citiponics is one of Singapore’s first rooftop farms. The hydroponic farm is on top of a carpark, a structure that services almost every neighborhood in Singapore.
Read more: How a parking lot roof was turned into an urban farm in Singapore
Installing urban farms into existing buildings
Sustenir Agriculture has created an indoor vertical farm that can retrofit into existing buildings (including office buildings). The company grows foods that can’t be produced locally, displacing imports and cutting carbon emissions.
Read more: The indoor urban farm start up that’s undercutting importers by 30%
Building a better greenhouse for urban farms in tropical climates
Natsuki’s Garden is a greenhouse in the center of the city, occupying reused space in a former schoolyard. The greenhouse is custom designed for the tropical climate to allow for better air circulation. Yielding 60-80 kg of food per square meter, the greenhouse caters to a small local market.
Read more: How a Singaporean farmer is building a better greenhouse for tropical urban farming
High production urban farms still need to be sustainable
Open to applications later this year, a new $60 million government fund will provide funding for more agritech businesses. According to the Singapore Food Agency, the fund will assist with start-up costs catering to large-scale commercial farms, no matter the location.
But as Singapore tries to advance, there are some left behind. The traditional farms that do exist in Singapore are being displaced, their knowledge no longer valued because they are not seen as hi-tech, according to Lionel Wong, the founding director at Upgrown Farming Company, a consultancy that helps equip new farming business owners across Singapore. “While we are trying to increase production, the net result could actually be reduced production because the traditional growers are being removed from the equation in the long term.”
In the long-run, high production of food within Singapore will need a sustainable market of consumers, to Wong that market isn’t completely clear at the moment. “‘30 by 30’ is really just a vision. The Food Agency deserves a lot of credit in terms of what they’re trying to push, but there’s a lot of room for improvement.” Wong continued, “productivity doesn’t necessarily equate to sustainability or profitability.”
Whether Singapore is able to produce its own food sustainably for the long-run remains to be seen. But the endeavor is certainly an exciting moment for entrepreneurs pushing the boundaries of what farming and cities can be.
Lead photo: COURTESY CITIPONICS | Singapore aims to produce 30% of its food by 2030.
VIDEO: What Makes Organic Food "Organic"?
Organic food is no longer a niche market. Sales of organic food products in the European Union have more than doubled over the last decade - from €16.3 billion in 2008 to €37.4 billion in 2018 - and demand continues to grow
The EU is the second-largest consumer of organic food in the world. - Copyright nsplaUsh
Organic food is no longer a niche market.
Sales of organic food products in the European Union have more than doubled over the last decade - from €16.3 billion in 2008 to €37.4 billion in 2018 - and demand continues to grow.
However, many Europeans are still unsure of what "organic" really means. Is it natural? Free of pesticides? Locally grown?
Well not exactly. Here are some of the conditions food products must meet in order to be considered organic in the EU:
No synthetic fertilizers
Natural fertilizers, such as compost and seaweed derivatives, are essential to maintaining fertile and healthy soil. So organic food must be grown with these products, rather than synthetic fertilizers that are used in conventional farming, and which tend to be made of harsher chemical ingredients including nitrogen compounds, phosphorus, and potassium.
"Organic farming improves soil structures and quality and enhances biodiversity. Studies have shown that organic farming present 30% more of biodiversity in the fields", explains Elena Panichi, Head of Unit at DG Agriculture and Rural Development (DG AGRI).
No synthetic pesticides
Farmers need to fight weeds and pests. Organic farmers are only allowed to use naturally-derived pesticides, made from plants, animals, microorganisms, or minerals.
"These chemicals are of a natural origin. For instance, essential oils, plant extracts, that are listed in the relevant regulation, and are authorized, following a process that implies a scientific committee to assess the effect on the environment", says Panichi.
Organic farms also have techniques such as crop rotation or planting different crops on the same plot of land, to help to prevent soil-borne diseases.
Natural predators, such as ladybugs, can also be an effective method of pest control.
However, it is important to remember that just because something is “natural”, it doesn’t automatically make it harmless to either people or the environment.
No GMOs
To be certified as “organic”, food cannot contain products made from genetically modified crops.
This rule is the same for organic meat and other livestock products. Besides, the animals are to be raised on 100% organic feed.
Antibiotics as a last resort
The animals we eat, or whose products we consume, need to be kept disease-free. Many conventional farmers routinely use antibiotics for disease prevention. These can end up making their way into the food chain.
Excessive antibiotics are not good for people or animals because they can help create superbugs. Antimicrobial resistance is a global concern. Every year, around 33, 000 people die in the EU, due to infections from antibiotic-resistant bacteria.
On organic farms, the use of antibiotics is severely restricted. Farmers control disease by limiting the number of animals they raise and using methods such as a healthy diet for their livestock. They are only allowed to use antibiotics when absolutely necessary for an animal's health, in order to avoid suffering, and when natural remedies such as phytotherapeutic and homeopathic medicines are not effective.
"If in conventional [farming], sometimes antibiotics are given as preventive tools, inorganics, antibiotics can be given as a last resort if there are no other methods to intervene. Normally, the higher animal welfare standards applied in organics already keep animals in a healthier status that prevent the use of antibiotics", explains Panichi.
However, studies have shown that antibiotic use on farms is on the decline. Sales of animal antibiotics in the EU have fallen by more than 34% between 2011 and 2018.
Better animal welfare
Organic farmers must provide the environmental conditions necessary for animals to express their natural behavior, such as adequate outdoor space. This is not compulsory in conventional farming.
There are additional rules such as the prohibition on caging or mutilation unless absolutely necessary for health reasons.
What "organic" doesn't mean
Locally grown
Europeans are the second largest consumers of organic in the world. Local supply can’t meet demand yet, so a large number of organic products are imported.
China, Ukraine, Dominican Republic and Ecuador are the main EU trade partners for organic food imports.
"Green" packaging
Words like “natural”, “green” or “eco” on labels and packaging do not necessarily mean a product is organic.
Healthy
There's a wide range of organic product on supermarket shelves, from burgers to pizzas, from cheese to wine. The health implications of consuming excess fats, salt, or sugar don't disappear just because a food product is organic. Too much fat, salt, and sugar are still bad for you, whether it is organic or not.
How can you be sure that the “organic” food you’re buying is actually organic?
EU organic logo European Commission
The most reliable way to know if a product is organic is if it has this official EU logo.
The white leaf on a green background means that EU rules on production, processing, handling, and distribution, have been followed and that the product contains at least 95% organic ingredients. This logo can only be used on products that have been certified by an authorized control agency or body.
Some countries have also created their own organic logos. They are optional and complementary to the EU's leaf. This is the French one, for instance.
French organic logo Agence Bio
New rules coming in 2022
EU rules on organic production will change soon. In 2022, Europe will have legislation with stricter controls.
Panichi believes it will bring a "substantial improvement" to the organic sector.
"We have to bear in mind that the new organic legislation is not a revolution, but it's an evolution of the organic legislation that started in the past years and has been kept evolving together with the sector".
The new legislation will harmonize rules for non-EU and EU producers. It will also simplify procedures for small farms in order to attract new producers, thanks to a new system of group validation.
The list of organic foods is expected to grow, with the addition of products such as salt and cork. The possibility of certifying insects as organic is also expected in the rules.
What is the future of organics?
"Surfaces in Europe are increasing or as well as all over the world, and they are increasing at a fast pace," says Panichi.
As part of its Farm To Fork strategy, the EU has committed to increasing organic production, with the goal of 25% of all agricultural land being used for organic farming by 2030. In 2019, it was only around 8%.
By 2030, Europe also aims to reduce the use of harmful chemicals and hazardous pesticides by 50%.
Buying organic food is still too expensive for many. One of Farm To Fork's main goals is to make healthy, sustainable food more accessible and affordable to all Europeans. A French family 2019 shows that a basket of eight organic fruits and eight organic vegetables is, on average, twice as expensive as a basket of non-organic products.
Note: The requirements listed in this article are just some of the conditions necessary for a product to be considered organic. If you want to know more about what is needed to obtain the green logo, please check the EU regulation.
Lead photo: EU organic logo European Commission
Three Way To Maximize A Vertical Farm's Potential
Population growth and urbanization are forcing global food production to a crossroads
17 March 2021
By Abhay Thosar, Ph.D., director of horticulture services for Fluence by OSRAM
Previously published in the February 2021 issue of Inside Grower.
Population growth and urbanization are forcing global food production to a crossroads. Overall, migration to high-density areas increases access to health care, higher-paying jobs, education, and other socio-economic opportunities. But it also places more strain on existing infrastructure and demand for resources, leading to greater water scarcity, energy consumption, waste, and, perhaps most importantly, threats to the food supply, prices, and quality.
The economically disadvantaged will be the first to pay the price of increased urbanization. As prices increase and access to quality food sources decreases, the nutritional health of poor populations will decline. Over the next several years, the responsibility of bridging the gap between projected food supply and demand in urban areas will largely fall on vertical farms, an industry that is expected to nearly quadruple by 2025 to about $16 billion. The COVID-19 pandemic could accelerate that growth rate even further.
The vertical farming industry still has challenges to overcome. Production costs remain relatively high and, as a young market, knowledge gaps in operational best practices in critical areas like facility design and environmental conditions threaten long-term sustainability and profitability. The evolving economic dynamic with supermarkets is forcing vertical farms to scale quickly as they attempt to grow and supply a wider variety of crops while maintaining the buyer’s standards around produce size, quality, and nutritional value.
And, as we look to the future, new innovations in lighting strategies, facility design, cultivation best practices, and automation mean that vertical farming operations have to be constantly adapting and seeking new operational advantages. This is just as true for new market entrants and relatively established players alike, and each will be critical to not only maintaining profitability, but ensuring that food production in urban areas can increase with demand.
With that in mind, here are three critical factors vertical farmers need to consider to meet market expectations, improve efficiency and ultimately grow, cultivate and distribute larger quantities of quality food to more people in a smaller area.
Facility design as a function of market demand
The history and growth of the vertical farming market are largely driven by two trends at the consumer and buyer levels. A decade ago, consumers asking questions about how, where, and when their food was grown was practically unheard of. Things are different today. People want to know the provenance behind the food they buy and ensure it is chemical-free and safe to eat. Every product has become more than a label, it’s become a story that consumers want to hear, and one that has an equally significant impact in where they shop and what they buy.
Supermarkets have taken notice. Beyond that, though, vertical farming operations have given supermarkets one more option in addition to the existing supply chains on which they’ve relied for food production and distribution. Vertical farms play an even more important role during large-scale disruption events like the COVID-19 pandemic or massive recalls. As a result, supermarkets—which value the consistent supply of produce above all—are turning to their local vertical farming operations and, in some cases, even investing in them directly. The increased attention, however, comes at a cost (literally and metaphorically). Supermarkets are demanding that the vertical farms supplying them grow a wider variety of crops—lettuce, tomatoes, cucumbers, leafy greens, microgreens, herbs—more consistently while also meeting unique specifications around weight, aesthetic, nutritional value and a variety of other factors that are ultimately dictated by the vertical farm’s environment and the grower’s expertise.
Vertical farmers are quickly realizing they need to expand their portfolio from potentially a handful of crops to a few dozen or more, raising a range of questions on how to design or retrofit their facilities and adjust environmental conditions that favor any given crop.
The first decision many vertical farmers face is the growing technique that will be most scalable and viable for their operation. Hydroponics, aeroponics and aquaponics have all emerged as viable options with varying degrees of success, but they’re far from interchangeable.
In the end, there is no universal solution for every vertical farm. Cultivators should closely consider their buyers’ expectations, and how those expectations might change over time. Then, cultivators must assess the full range of their crops’ needs and how each might respond differently to various environmental factors and lighting strategies.
Strike a balance between environmental factors
The next set of factors governing facility design, investment and day-to-day operations should always be the environmental conditions themselves.
How air flows into and across each rack of a vertical farm is one of the most unique and important challenges vertical farms have to solve. Ignoring or failing to closely monitor airflow is often a death blow to entire sections of crops and to profitability, yield, and consistency as a result. Air movement helps to maintain temperature, humidity, and transpiration at each rack, and lack of it creates wide temperature swings or large gaps between crops at the bottom and crops at the top. It’s an incredibly fragile balance to strike. Everything from the number of access points into a warehouse—there should only be one access point—to HVAC and circulation systems affect air movement.
As a best practice, the maximum difference between the temperature at the top-most rack and the bottom-most rack should be no more than two degrees Fahrenheit. In practical scenarios, cultivators facing large temperature fluctuations can also consider placing crops that prefer relatively warmer temperatures—such as basil, oregano, chives, sage or thyme—at the top and simply let the laws of thermodynamics do the rest.
Carbon dioxide enrichment is a slightly easier condition to manage but no less important and changes based on temperature and lighting strategy. CO2 enrichment, too, can fluctuate based on the number of access points into a warehouse (again, there should only be one). Enriching a cultivation environment with carbon dioxide stimulates photosynthesis and plant growth, the rate of which is critically dependent on the difference between CO2 concentrations in the air and in the leaf cells.
The law of diminishing returns puts a cap on the amount of carbon dioxide cultivators should be introducing. CO2 is by no means the only factor governing plant growth, but vertical farms have the advantage of being able to closely monitor and control CO2 levels. To do so properly, however, they shouldn’t shy away from significant investments in both handheld devices—which allow cultivators to measure carbon dioxide levels at each rack, each plant, and each leaf—but also large-scale control systems that can measure and track CO2 throughout the entire warehouse.
Humidity levels govern a plant’s transpiration rate and the aperture sizes of its stomata, ultimately affecting how much water it moves from its root zone to release back into the warehouse. When a plant’s stomata open, they release water while also collecting carbon dioxide, making the balance of humidity, temperature, and carbon dioxide all the more crucial. Different plant types in different growth stages have different transpiration rates, adding even more complexity to how a vertical farm is designed and managed. The most common way to express humidity is relative humidity, the percentage of water vapor in the air at a given temperature compared to the total amount of water the air can hold at that temperature. In vertical farming, however, vapor pressure deficit (VPD) is the more accurate way to gauge humidity’s effect on plant growth. VPD remains an interesting discussion among researchers as the industry seeks to understand the differences between VPDs for air and leaves as well as exact VPD calculations.
Every environmental factor in a vertical farm affects the others to some degree. Nearly everything can be controlled; it’s both the advantage and the challenge native to the market. No factor, however, is more important to photosynthesis than its primary driver: light. Each factor—CO2, temperature, airflow, humidity, fertilizer, irrigation, VPD—need to be fine-tuned with changes to light quantity and quality to optimize plant performance and response.
Designing an effective lighting strategy
The design and implementation of an effective lighting strategy is and always will be the primary driver of your vertical farm’s success. In environments as complex as vertical farms, identifying the correct light intensity, spectra, photoperiod, and configuration will determine how other environmental factors work together to optimize a facility for plant yield and quality.
The first of these, the fixtures themselves, carry more implications for vertical farms than other cultivation spaces; in a vertical farm, plants receive no other source of light. The sun isn’t the safety blanket that it is for greenhouses. This simple and obvious fact means that vertical farmers have to find efficiencies in ways others don’t, which can manifest across a variety of operational metrics. Light efficacy, for instance, becomes more important. Most vertical farms are located in urban areas and are likely paying a premium for electricity. Maximizing micromoles per watt and reducing energy waste becomes more than a sustainability initiative, it’s critical to overall profitability.
Similarly, vertical farms operating warehouses measuring in the tens of thousands of square feet need fixtures with a good form factor without sacrificing light intensity. The right configuration means vertical farms can squeeze more racks into their facilities while also putting the lights closer to the plants for better results.
Beyond the hardware specifications, lighting design and strategy consist of several key factors: light intensity, light quality (or spectra), and light bar configuration. Each should be rooted in a facility’s overarching goals—typically defined by the consumer or buyer. Lighting strategies can be customized by crop, yielding specific plant chemistries or changes in biomass. Differences in spectra and light intensity can affect a crop’s coloration, shelf life, taste, and smell. Desired crop characteristics should be determined upfront in conjunction with the prospective buyer, therefore guiding a lighting designer to identify the optimal strategy to accomplish a facility’s goals.
Light quantity is the first and foremost aspect when it comes to optimizing the productivity of the crop. It is important to target the correct mols/day for each crop. Light quality (or spectra) is defined by measuring light’s wavelength in nanometers (nm). Wavelengths of light that drive photosynthesis are primarily found within 400 to 700nm—a range identified as photosynthetically active radiation (PAR). In a vertical farming environment, broad, white light has proven effective for tissue culture, propagation, and vegetative growth—while also serving the more practical function of making it easier for human eyes to diagnose and observe crops day in and day out. As the body of research into LED applications has expanded, it’s become clear that lighting strategies need to shift based on the growth stage. The days of bombarding plants with the same intensity and spectra are quickly fading. More and more research is showing that different cultivars respond to different lighting strategies at different stages of their maturation. More nuanced, customized lighting strategies are increasingly leading to tangible business outcomes for cultivators: longer shelf life, improved aesthetic, enhanced nutritional value, faster cycle times, and higher yields.
LED improvements will continue to drive costs down, while more in-depth research will discover and confirm a new set of lighting strategies and operational best practices to help vertical farmers meet future market demand for increased food production while also improving profitability. Overall, the future for vertical farms is bright and ripe for even broader innovation. Automation—the final frontier of food production—will mean even greater control of agricultural environments. That future is on the horizon. For now, though, vertical farms just need to stick to what they can control, which is pretty much everything else.
About Abhay
Abhay Thosar is the director of horticulture services at Fluence by OSRAM, where he is responsible for managing a team of horticulture specialists that enhances how cultivators grow their crops, optimize their lighting strategies and increase profitability in their operations. He holds a Ph.D. in plant physiology from Gujarat Agricultural University and spent more than a decade at leading greenhouses and nurseries throughout the U.S.
AUSTRALIA: VIDEO - Shipping Container Farms: Check Out This Craze In Modified Containers
Greenhouses, hydroponics, and mushroom farms – converted shipping containers can produce protein and vegetables for all your needs
Greenhouses, hydroponics, and mushroom farms – converted shipping containers can produce protein and vegetables for all your needs. Even if you’re not an environmentalist, there are business opportunities to be had in delivering extremely fresh food to people in urban environments like Brisbane. Given the changing climate and topsoil loss we are facing, shipping container farms could well be an answer to these issues.
Over the years in the Gateway Gazette, we have published a number of stories that look at producing food in converted shipping containers. Reflecting on what we have published and looking at the detail of what can be done, let’s consider the possibilities that come with shipping container farms.
Open Top Container Greenhouse
One of the most cost-effective ways of using a shipping container as a food-producing unit is by attaching a glass top to an open-top shipping container.
In this video, Urban Farm Units looked at the concept of a greenhouse-container. An open-top 20-foot container would have a greenhouse attached to the top with shelving units directly under the glass. This allows photosynthesis to take place in the normal way.
Seedlings can be started in the lower part of the unit, which is warmed by the light and heat from the outside.
One step down from slapping a greenhouse on top of an open-top container would be to use a flat rack container and to have the greenhouse on the base (Gateway Containers can supply both open-top and flat rack containers).
The concept is an improvement on the one in the video, as long as you keep the greenhouse within the dimensions of a 20ft standard or high-cube container, it would be possible to lift and move the container farm from place to place.
This might be useful where you have an agreement with property developers or a council to use vacant plots of land in a city for agriculture. When the site is ready to be developed you can stick it all on a truck and move it to the next plot.
The concept of a shipping container greenhouse is:
Cheap to buy
Mobile
And often won’t need planning permission for a permanent site
Could this be something you’d consider? Contact us at Gateway Containers to discuss your needs!
Mushie Container Farm!
Image source: King Oyster Mushrooms Facebook
In 2019 we reported how Belgrave, Vic-based John Ford has developed a shipping container mushroom farm. This could produce protein for people as an alternative to meat or for anyone who loves the taste of freshly cut shrooms.
Mushrooms of any kind don’t store well and are best eaten as soon as possible after cutting. This is why having a mushroom farm close to restaurants could be a money-spinner.
This requires no modification from a basic shipping container, you could even install the racking inside the container yourself.
In their lifecycle, mushroom mycelium live out of sight of the world until they are stressed and get the impression that they are facing death. When stressed they flower to produce spores – those flowers are the mushrooms that many of us love to eat.
A shipping container is perfect to take advantage of such a lifecycle. Logs or other media are infected with the mycelium and left to rot for a certain time. By altering the environmental conditions, so you deliberately stress the fungi and they flower.
In our article, we reported how John Ford is producing mushroom species that are famed for their delicate taste but don’t travel well at all – shiitake and oyster mushrooms. As a sideline to his main income as a marine biologist restoring seagrass habitats near Belgrave, he produces freshly cut shrooms for local people and restaurants.
For you as an entrepreneur, mushroom growing would require buying a used shipping container and setting it up as a mushroom farm. If you are planning an urban mushroom container farm, you can take advantage of the fact that you can treat the container as a mobile unit and not as a permanent base. Shipping containers are also pretty inexpensive to buy and convert.
Hydroponics – The Rolls Royce of Shipping Container Farms
Image source: ABC
The hydroponics concept is highly developed for the use of fresh food and can be set up for high density vegetable farming in shipping containers. This requires a fair bit more modification than the two systems we describe above.
Unlike the Urban Farm Units company, several companies have managed to survive over the years selling their hydroponic container farm businesses to entrepreneurs and restaurants around the world.
Modular Farms is a company we featured in our blog originally based in Canada, but who recently set up shop over here in Australia. According to their website, they “design and manufacture container farm systems that can be used to grow food in most locations on earth.”
These systems strive to get around some of the issues we face here. Cities like Brisbane get far too much water sometimes and then face droughts for years on end. The Australian Food Services News reported, “With a focus on sustainability, Modular Farms’s hydroponic, closed-loop system uses 95% less water than a typical outdoor farm.”
Topsoil erosion is a problem, especially in prolonged droughts when it gets blown away as dust. Hydroponics use media like rock wool and even used mattresses to house the plants’ root systems and feed them nutrients via a watering system.
With our ever more extreme climate, food often has to be imported into cities from hundreds or thousands of miles away. A hydroponic container farm can enable you to grow many vegs very close to markets and restaurants.
This has been observed by global homewares retail giant IKEA, which in 2019 announced it was piloting growing vegetables in its stores for use at its restaurants. We reported, “While selling hydroponic indoor growing equipment to customers, IKEA is feeding its staff with lettuce and other vegetables grown in a container outside its Malmö and Helsingborg stores.”
Image source: ABC
There are a few downsides to hydroponics. Firstly, while some types of plants are happy enough growing in hydroponics – the simpler ones producing leaves and flowers (like broccoli!) – others aren’t so happy, such as cassava, wheat, and potatoes.
The next big issue is that for a high-intensity farm, not unlike factory farming chickens, you need to be ultra-clean in your production as the arrival of a destructive disease or fungus could wipe you out very quickly.
Container Fish Farm Too?
In theory, it is possible to run a fish farm connected to the hydroponics container farm, with you largely feeding the fish and collecting their feces and other waste to feed the plants. The plants would clean the fishes’ water and make it habitable for them as reed beds do in nature. This a concept that is in development but hasn’t caught on commercially yet.
How Can Gateway Containers Help?
We can provide and convert an insulated container for you to get started with and advise you how to best make further additions without compromising the overall structure.
If any or all of these ideas have caught your interest – or you just know about these concepts and need a shipping container to make it possible – then get in touch with us today to discuss your needs!
Posted on February 22, 2021
By Mark FinneganOtherShipping ContainerModified Shipping ContainersLeave a comment
USA: CALIFORNIA - Futuristic Vertical Farm Aims To Bring Fresh Produce And Jobs To Compton
The vertical farm will contain rows upon rows of crops with the capacity to produce 365 harvests of high quality leafy greens per year
The vertical farm will contain rows upon rows of crops with the capacity to produce 365 harvests of high-quality leafy greens per year. "From day one it's perfectly controlled...We don't use pesticides, there's nothing to wash off, it's usually not touched by human hands ever, and so we have a safe clean product that is ready to eat right out of the package", the owner says.
When we talk about farming, we don't often think of Compton. But the future of farming could soon be coming to life there. A company is building a massive vertical farm that would save water, land, and eliminate the need for pesticides.
It is still under construction, but when this unassuming 95,000-square-foot warehouse is up and running, the inside will look like something out of the future-- rows of vertical crops with LED lights replacing the sun.
"From day one, it's perfectly controlled. We don't spray any pesticides. There's no birds flying over our field pooping on the produce. There's nothing to wash off. It's usually not touched by human hands ever. And so we have a safe, clean product that is ready to eat right out of the package" says the owner.
Read the complete article and watch the video at www.news.yahoo.com.
22 Mar 2021
CANADA: Bringing Fresh Greens To Albertans And Making Hydroponics More Accessible
While the vertical farming industry typically prides itself on high levels of automation, Vertical Roots is taking a different approach that doesn’t rely on technology and automation
Mike and Becky Newhook first took an interest in local agriculture nearly 20 years ago, during a visit to the Philippines where most of the people they met were farmers. When they visited the region 18 years later, those same people were still farming.
One thing led to another, and the couple began working with the locals over Skype to set up two aquaponic farms and begin producing 20,000 heads of lettuce, which isn’t otherwise produced in the region. While those aquaponic farms are locally owned and operated, Mike and Becky continued in their pursuit of local food systems back home in Tofield, Alberta. That is how, at the beginning of the pandemic, Vertical Roots Canada was established.
Vertical Roots is a hydroponic farm founded in 2020 by Mike and Becky Newhook as well as their partners Brent and Evelyn Harley. While the farm began in the Newhook’s garage, it has expanded to Brent and Evelyn’s property in Beaver County, Alberta. It currently runs out of a 600 sq-ft building, although only 386 sq-ft is currently used for production. At this point, the major challenges to production are limited amperage and the limited access to potable water, requiring that water be trucked in. Vertical Roots hopes to expand to 1,500-2,000 sq-ft with all operations occurring under the same roof, from plant propagation to growing, testing, and harvesting.
While the vertical farming industry typically prides itself on high levels of automation, Vertical Roots is taking a different approach that doesn’t rely on technology and automation. The farm focuses on hands-on growing and relatively small-scale production. But according to Mike, that hasn’t hurt their business in the slightest as the company is expanding within a year of its establishment.
“We’re not about producing in warehouses and supplying major companies. People seemed to say that if you aren’t producing 20,000 heads of lettuce, then you’ll be left behind. But that hasn’t been the case at all,” says Mike. Vertical Roots sells its greens through subscriptions, to the Mayfair Royal Golf Club, and to local restaurants. The interest in local food has never been higher, according to the Newhooks, as consumers have flocked to the farm and maxed out the supply.
“When people are ordering from larger suppliers, the quality is lower. They are paying the same price or lower for a product that they can only use half of. We’ve learned that people are willing to pay more for a head of lettuce if it means that they can use all of it rather than only a portion of it,” says Becky.
Throughout the Newhooks experience, they’ve found the hydroponics community to occasionally be difficult to collaborate with, as the industry tends to keep its cards close and not share its experiences. They also struggled with having consultants make technical recommendations that didn’t ultimately make sense for their business. According to Mike, this lackluster knowledge sharing in vertical farming is part of why many vertical farms have failed.
As such, Vertical Roots is committed to being a transparent company that welcomes people and questions. The company has also developed a prototype system which it plans to commercialize by autumn 2021, which will be complemented by educational resources and consulting also provided by the farm. Vertical Roots already has 3-4 growers pursuing them to build a farm once the systems are available for sale.
“Our product is where we want it to be; we just need to keep repeating it. We want to master all four seasons before beginning to sell. While you are growing indoors, the season does impact climate control inside the farm,” explains Mike. In the future, Vertical Roots hopes to explore opportunities in northern Canada, as the rates of food insecurity and food prices are exorbitant throughout the region.
For more information:
Vertical Roots Canada
info@verticalroots.ca
www.verticalroots.ca
Publication date: Fri 19 Mar 2021
Author: Rebekka Boekhout
© VerticalFarmDaily.com
FRANCE: Jungle Says It’s Cracked How To Make Vertical Farms Profitable
“No matter how good your product is, if the price is higher than the alternative, then you’re dead.”
“No Matter How Good Your Product Is,
If The Price Is Higher Than The Alternative,
Then You’re Dead.”
BY FREYA PRATTY
22 MARCH 2021
Jungle, a French vertical farming company that says it can produce ten to 30 times more food than traditional greenhouses, has raised €42m in new funding.
The company also says its focus on large-scale farms will help it overcome one of the biggest challenges facing vertical farming: how to make a profit.
Jungle’s new funding, €7m of which is in equity and €35m of which is debt financing, comes from Founders Future, a French investment firm focused on impact startups. Jungle is the firm’s first investment.
The company’s funding comes as the wider industry continues to grow fast. It was worth $2.2bn in 2018 but is expected to reach $12.8bn by 2026. Investor appetite is clearly there: vertical farming giant Infarm raised $170m at the end of last year.
Jungle is building a 5,500m2 farm 80km from Paris, where crops will grow on stacked platforms. The site is already partly operational and the company has secured contracts with French supermarkets Monoprix and Intermarche.
At present, it’s growing a mixture of aromatic herbs, greens and, unlike other vertical farms, flowers. It’ll be fully operational by the end of 2021.
Less pesticides, more local and a greater yield
Gilles Dreyfus, cofounder of Jungle.
“We don’t claim to be instigating a revolution, we are part of an equation that wants to be a solution,” explains Gilles Dreyfus, who cofounded Jungle in 2015.
For Dreyfus, vertical farming has several advantages. Crops can be grown close to cities, where the majority of consumers are, thereby reducing the environmental costs of transit.
Plants can also be grown on more frequent cycles than on traditional farms because they’re not seasonally dependent, and they’re also grown without using pesticides.
“Our most popular product, Green Basil, gives 14 harvests a year in the vertical farm, compared to 3 or 4 in the South of France, where the crop grows best outdoors.”
National food sovereignty
Being able to grow crops out of season means vertical farming can help countries achieve better food sovereignty, Dreyfus says.
“We have to go further and further from the country to get crops when they’re out of season,” he says. “Brexit import taxes on food have shown the complicated situations this can lead to.”
“If the price is higher, you’re dead”
Despite the benefits, vertical farming has often struggled with how to make a profit. “Having a viable financial model and an efficient farm is the main hurdle for vertical farming,” Dreyfus says.
“No matter how good your product is, if the price is higher than the alternative, then you’re dead.”
The company believes that bigger farms is the answer.
German company Infarm, which is aiming at profitability by 2023, places microunits into supermarkets. Jungle, which is aiming at profitability in 18 months time, will focus on large-scale production facilities that then supply a whole area.
“Price depends on scale and we’re not aiming for small-scale farms, we’re aiming for less farms but a lot bigger. If you activate the economies of scale you can get a very reasonable product,” he says.
The company’s aiming to sell food at 5% more than the cost of conventional alternatives, but at 20% less than organic foods grown on farms.
For Valentine Baudouin, partner at Founders Future which has invested in Jungle, the focus on large-scale farms is the key to profitability, and what makes Jungle stand out.
“They’ve answered the economic question of vertical farming, which is very important because you have many similar enterprises that haven’t done so.”
Jungle’s vertical farm warehouse.
Beyond salad?
A criticism often leveled at the vertical farming industry is whether it can grow beyond just salad leaves and herbs.
Unlike other farms, Jungle also grows flowers for the perfume industry, but Dreyfus says the other crops its working on, including cherry tomatoes and mushrooms, won’t be in supermarkets until 2023.
“You can grow virtually anything you want, except truffles — which is a real shame actually,” says Dreyfus. “But the question shouldn’t be, can we grow it, it should be, do we have the financial model to make it work?”
Jungle’s currently got a team of 25 people based in France, but will use the new funding to double its workforce by 2022. It also plans to open two new large-scale farms in France, including one in the south that’ll be twice as big as its first site.
Freya Pratty is Sifted’s news reporter. She tweets from @FPratty
Eeden Farms Sees Phenomenal Market Response To Pioneering Concept
Lincoln Deal II, the founder of Eeden Farms, said: “The response has been phenomenal. Most days, we are combing growing and facilitating tours because the interest level is so high among restaurants and hotels
An Eeden Farms worker plants seeds for a sustainable future. (PHOTO: EEDEN FARMS)
NASSAU, BAHAMAS — A tech-enabled containerized farming company has seen a “phenomenal” response to its offering, according to its founder, who told Eyewitness News “the demand is definitely there”.
Lincoln Deal II, the founder of Eeden Farms, said: “The response has been phenomenal. Most days, we are combing growing and facilitating tours because the interest level is so high among restaurants and hotels.
Lincoln Deal II.
“A lot of the restaurants and hotels are enamored by how fresh the produce is, that they can get it farm-to-table and it’s Bahamian. The demand is definitely there.”
Eeden Farms, located in the BRON Business Centre, Airport Industrial Park, officially launched back in February.
The company currently utilizes three repurposed shipping containers equivalent to 15 acres of farmland and offers fresh organic produce year-round. Its farm system was created by Boston-based Freight Farms, the world’s leading manufacturer of container farm technology.
Deal defended the containerized farming concept, noting that Eeden Farms is the first company to have Freight Farm’s newest model of containerized farms.
“The technology that we are utilizing has never been used here before,” said Deal.
“We are the pioneers of this technology here in The Bahamas despite what misinformation may put out there. We were the first to receive this model from Freight Farms and they own the patent on this particular technology.”
Caroline Katsiroubas, director of marketing and community relations at Freight Farms, told Eyewitness News: “Eeden Farms represents the first entry of our technology into that region and that market. It began in 2020 but the journey didn’t start there. We have been working with him (Deal) for quite a few years, having first met at a conference in 2016.
“We’re in 32 countries right now. In terms of who our client base is, we have a very diverse kind of network of people who are interested in operating the system and it has infinite applications.”
Tags Always a headline ahead, Bahamas news, ewnews, ewnews.com, Eyewitness News, Eyewitness News Online, Nassau Bahamas, www.ewnews.com
About Natario McKenzie
View all posts by Natario McKenzie →
Lead photo: Eeden Farms. (BIS PHOTO/KRISTAAN INGRAHAM)
US: NORTH CAROLINA: CraftGrown Farms Offers Fresh Microgreens, Lettuce And Herbs
All of the growing is done inside, allowing CraftGrown Farms to produce year-round and the ability to expand its growing capacity
BY JESSICA MAURER
March 10, 2021
CraftGrown Farms involves a hydroponic farm on Castle Street. (Photo courtesy of CraftGrown Farms)
Randall Rhyne’s career has included teaching high school biology and earth science as well as serving in the Army Reserve, with deployments to Iraq and Syria.
After visiting Wilmington last year, he fell in love with the city and decided to relocate from Virginia.
While serving overseas, Rhyne and his unit often had little to no access to fresh food, relying on MREs or snacks like Pop-Tarts. He often longed for fresh produce.
One spring when he was in the Syrian desert, he saw trucks hauling locally grown produce and found himself thinking that if the locals were able to grow their own food in the middle of a civil war, in a desert, there was no reason why he couldn’t do this at home. As soon as he returned to Virginia, Rhyne got to work.
Now, having secured a Castle Street storefront and growing space across from Luna Café on Castle Street last fall, Rhyne has created CraftGrown Farms, an indoor, hydroponic farm selling nutrient-dense microgreens, hydroponic lettuce, and herbs to local restaurants and the public.
All of the growing is done inside, allowing CraftGrown Farms to produce year-round and the ability to expand its growing capacity.
Rhyne said the response so far has been remarkable; in fact, he’s already outgrown his initial vertical grow system.
“It’s a great problem to have,” Rhyne said.
He said new customers are usually so excited about what they’ve tried that they want to take home more than they need.
“I’m an old school believer in the quality of the sale and even though these items have a good shelf life, I try to discourage people from buying too much at once,” Rhyne said.
CraftGrown Farms only harvests what it sells, so the produce is picked right in front of the customer, providing maximum flavor and freshness.
There are currently about a dozen microgreen blends available, as well as leafy greens such as kale, arugula, and tatsoi. The microgreens will keep in a vegetable crisper for two weeks, and all of the lettuce is sold with the root ball intact to preserve flavor and freshness.
“These are not your everyday lettuces,” Rhyne said.
CraftGrown Farms is located at 603 Castle St. and is open from noon to 6 p.m. Monday through Friday and 10 a.m. to 4 p.m. on Saturday.
Have a tip for Restaurant Roundup? Email us at: restaurant@wilmingtonbiz.com.