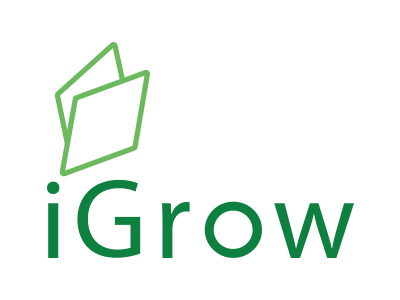
Welcome to iGrow News, Your Source for the World of Indoor Vertical Farming
Miljøgartneriet, Norway's Largest Nursery, Grows Even More Tomatoes And Peppers Year-Round By Using Philips LED Lighting
For many years, Signify has studied lighting and plants and has found the perfect lighting recipe for tomatoes, peppers, cucumbers, and other fruits and vegetables
April 6, 2021
Eindhoven, the Netherlands – Norwegian consumers are currently eating fruits and vegetables that have traveled thousands of kilometers from Southern Europe before they reach the shelves in Norwegian stores, which results in more imported food and a greater carbon footprint from its transport, compared to locally-grown crops. Now, Miljøgartneriet, Norway's largest nursery, together with its partner LOG and Signify’s horticulture LED department, are taking the first steps in shortening the farm to fork distance by growing tomatoes and peppers year-round locally, under LED lights.
The goal is to increase opportunities for local production and reduce the climate impact that comes from importing foreign produce. Signify has supplied Philips GreenPower LED toplighting compact for the 70.000 square meter greenhouse in Naerbø, Rogaland, Norway. With LED lighting, Miljøgartneriet gets the best possible conditions in the greenhouse. This is important since the lighting affects the plants' photosynthesis, and that makes proper lighting extremely important for how well the plants grow and thrive.
For many years, Signify has studied lighting and plants and has found the perfect lighting recipe for tomatoes, peppers, cucumbers, and other fruits and vegetables. Miljøgartneriet can therefore provide the plants with the right spectrum and light intensity at the right time. In this manner, they can control growth, planning and not least of all, increase productivity.
"Many supermarket chains want to be able to offer their customers fresh and tasty fruits and vegetables with a significantly lower carbon footprint than those that come from Southern Europe. This is something we can provide all year, thanks to our cooperation with Signify," said Kåre Wiig from Miljøgartneriet. "We chose Signify because they can do more than just providing LED lighting. We have a good, close cooperation with their plant experts in order to get the most out of the lighting solution so that the vegetables get the best possible growing conditions. This means that we can easily adjust production as we get better at growing vegetables and Signify can also bring in different experts if necessary."
Miljøgartneriet has installed Philips GreenPower LED toplighting compact, in combination with the GrowWise control system. This makes it possible to dim the lights so that growers can provide even light levels throughout the day and production cycle. Growers can also dim the lights when necessary. Either to save energy or when there is sufficient daylight.
Innovation in horticulture
Miljøgartneriet starts with 1 hectare of tomatoes and 0.4 hectares of peppers,and intends to eventually expand this. The vegetables are already being harvested now and on their way to the stores throughout Norway.
Even though Signify has worked witFphilh LED lighting for greenhouses since 2012, there are many producers that are still not ready for the newest greenhouse lighting technology. Henrik Nørgaard, who is the Commercial Operations Manager for Agriculture at Signify, hopes that this cooperation with Miljøgartneriet, which is one of the leading actors in the market, can inspire other growers to install Signify Horti LED lighting and increase production.
"We are really proud that Miljøgartneriet sees the potential of cultivating with our lighting. Our lighting solutions should be seen as a cornerstone of production. We start with defining what is grown, the physical framework of the greenhouse and the production goal, and based on this we create an optimal mix of micromoles, spectrum and timing; the light recipe, together with the grower. With the solution, we can avoid the overuse of both water and electricity, as well as the environmental burden with transport from Southern Europe, and instead can get fresh, locally-produced vegetables in Scandinavia year-round," said Nørgaard.
Supporting food availability through Horti-LED illustrates Signify's commitment to supporting good health and well-being (SDG3) and is the key to their commitment to double the percentage of earnings for a brighter life that benefits society, to 32%, as part of the program Brighter Lives, Better World 2025, that they launched in September of 2020.
--- END ---
For more information, please contact:
Global Marcom Manager Horticulture at Signify
Daniela Damoiseaux
Tel: +31 6 31 65 29 69
E-mail: daniela.damoiseaux@signify.com
Signify Nordics, PR Manager
Anne-Cathrine Tjørnehøj
Tel: +45 40330806
E-mail: anne-cathrine.tjornehoj@signify.com
About Signify
Signify (Euronext: LIGHT), a world leader in lighting for the professional market, the consumer market, and lighting for the Internet of Things. Our Philips-products, Interactive lighting systems, and data-activated services add value to businesses and transform private homes, buildings and public spaces. In 2020, we had sales of 6.5 billion EUR and approximately 38,000 employees in 70 countries. We utilize the full potential of light to offer a brighter life and contribute to a better world. We were carbon-neutral in 2020 and have been on the Dow Jones Sustainability World Index for four consecutive years since our listing. WE were also named Industry Leader in 2017, 2018 and 2019. News from Signify is availabel at Newsroom, Twitter, LinkedIn and Instagram. Investor information is available on the Investor page.
March Indoor Ag Science Cafe Recording Is Now Available!
This presentation 'USDA SBIR Grants Program Overview' was given by Dr. Steven Thomson & Melinda Coffman (USDA NIFA) during our 28th cafe forum on March 30th, 2021
"USDA SBIR Grants Program Overview"
Dr. Steven Thomson & Melinda Coffman
USDA NIFA
SBIR = Small Business Innovation Research
Please contact Melinda Coffman for SBIR questions.
This presentation 'USDA SBIR Grants Program Overview' was given by Dr. Steven Thomson & Melinda Coffman (USDA NIFA) during our 28th cafe forum on March 30th, 2021. Indoor Ag Science Cafe is organized by the OptimIA project team funded by USDA SCRI grant program.
Upcoming Cafes:
Tuesday, April 20th, 10 AM Eastern - 'Plant Factories and Indoor Farming Innovations in Japan' by Eri Hayashi (Japan Plant Factory Association)
Tuesday, May 18th, 11 AM Eastern - 'Smart Sensors for Indoor Farming' by Dr. Krishna Nemali (Purdue University)
Interested in giving a talk to share your thoughts and experiences? Please contact us!
Joined Up Thinking: Food & Energy Grids
This article, written by our CEO and co-founder Charlie Guy, about the connection between our energy grid and food networks, originally appeared in Volume 35 of the Journal for Food Science and Technology.
It may not always feel like it at this time of year, but on our planet we are blessed to bathe in a constant and abundant stream of energy and warmth. Effectively, all of this energy comes from the sun before being transformed, stored or used in some way. From the organic matter that once formed our fossil fuel sources, to the climatic differences that drive our weather systems and the solar panels you might have on your roof.
Food is our fundamental energy source as individuals - it powers everything that we do in our daily lives. For almost all food types, the energy used to produce it is derived from the sun (ok, mushroom-heads may argue against this, but they are still feeding on organic matter). Because of this simple concept, our food and energy systems are intrinsically intertwined. Bizarrely though, this fact is often overlooked in the food supply chain, from producers, all the way through the distribution and cold chain, right up to ourselves, the end consumers. Our current food system separates out different energy types. Heat, electricity, fuel and light often end up as mere balance sheet inputs to the production of food and many energy inputs don’t get recorded at all.
This simplified way of thinking leads to us cutting corners for the sake of cost and not considering the absolute energy impact of our food production. There are no individuals at fault here, our economic system has lined us up to think in a linear fashion for the past few centuries and this has muddied the long-held practices of stewardship for the land. Effectively, our understanding of what we give and take from nature and the sun to produce our food is no longer in balance.
If we look at the inputs and flows of energy that make up global food production, we see many areas that we may not consider when we buy food products in our local supermarkets or greengrocers. Berners-Lee et al (2018) produced a high-level analysis of the global energy flows in food production, shown in Figure 1, ultimately showing that we grow enough calories to feed everyone on our planet, but we do not use or distribute them efficiently.
Figure SEQ Figure \* ARABIC 1 - The flows of global food energy (kcal/person/day) from the amount grown to the amount eaten. For crops fed to animals, the units are based on the global human population, not animal population. The left-hand bar divides the crops grown into those that are directly edible by humans and the grass, pasture & stover that is only edible by animals. The right-hand bar divides the nutrients eaten into that required for healthy human living and net excess consumption. Animal losses include all the losses inherent in animal husbandry, such as energy used for respiration, growth, movement, and reproduction and the wastage of animal parts not used as food. DOI: https://doi.org/10.1525/elementa.310.f1
When you consider the journey of a simple soil-grown lettuce, you must consider the following energy inputs and flows as a minimum:
- Preparation – soil, seed production, transportation of seeds, drying and storage of seeds, farming infrastructure, fertilizer/pesticide production
- Growing - the sun, soil, fertilizer/pesticide application, and waste, machinery, human labor, energy use if in a greenhouse/vertical farm
- Harvesting and storage – farm machinery, fuel, refrigeration and spoilage
- Processing and packaging – transforming raw materials into products
- Transportation - cold chain refrigeration, freight by lorry, boat or long haul air travel
- Consumption - home energy usage including storage and cooking
- Waste - throughout the chain and in the home
Through each of these processes, we are either adding energy to our food on its journey to our plates or we’re losing energy through losses along the way. This is why the impact of wasting food in the home is so severe, as we are not only wasting the energy that went into producing the food, but we are also wasting the energy that was used in the supply chain along the way too. Each of these losses, even if they seem small at each stage, adds up. Taking Berners-Lee’s analysis and comparing this to electrical energy usage, the average food wasted per person is equivalent to all 7.8 billion people on our planet leaving a reasonably-sized LED TV (64W) on for 24 hours a day, 365 days a year.
Ever more work is being done in the field of lifecycle analyses to understand and bring to light the impact of our foods. These individual losses need to be understood, quantified and then reduced in our vision of a more efficient combined food and energy system.
There is a clear comparison that can be made between our current food systems and the journey that our energy systems have been on over the last few centuries. Through the various energy revolutions, we have transitioned from distributed to centralized energy and food systems. Centuries ago, we were required to balance the use of wood and food, to heat and fuel ourselves, to sustain our communities, and avoid overconsumption of either energy source. Food and fuel tended to be distributed locally to fulfill the energy needs of the community and we had a better understanding of the link between the sun, our food, our energy and the need to prevent over-consumption to remain in balance.
Fast-forward to the 21st Century and the current paradigm of large power stations that distribute electricity through grids to people, whose only connection is the vibration of their phone when they plug it in to charge. There is zero connection to how or where the energy was produced. The equivalent analogy in food production sees swathes of industrialized monocropping, focused in certain areas of the globe. Products and ingredients are shipped halfway around the world and our only connection is to open the packet and experience their flavors. Arguably there are substantial “efficiencies” and economies of scale in this kind of production model, but at what cost? Is this what we want the next chapter of our food and energy systems to look like?
Renewable energy has a huge opportunity to bring us back to a more decentralized system. In simplistic terms, the fact that the wind and sun are well distributed around the world gives the potential for much more equitable access to energy production. Renewables also bring us much closer to the only real source of energy that we have, the sun, whilst revealing our true reliance upon it as well. There are some known issues regarding renewable energy storage, but the humble chloroplasts in plants long-ago worked out how to capture this energy and store it for use later on. We can learn from this and begin to look forward with a more joined-up view of our food and energy systems. Putting our farmers and stewards at the heart of this system, ensures that links can be rebuilt between food and energy production.
So how do we link our food and energy systems back together in a way that can provide enough food for all of us in the most sustainable way? Firstly, this challenge needs to be undertaken with the concepts of sustainable intensification and circular economy principles in mind. If these are new to you, do check out the Ellen Macarthur Foundation. Secondly, we need a diversity of thinking and solutions, including both technical and business innovations. There is no silver bullet here for such a complex problem.
Many solutions in both energy and food supply are coming to the fore already, albeit independently at the moment – local energy schemes and community-supported agriculture schemes (CSAs) both enable communities to benefit from locally produced energy and food. Can we imagine a future where we bring these together into combined food and energy schemes?
Controlled environment agriculture (CEA) is one emerging practice that allows us to do things in ways that previously we have not been able to do in open-field agriculture. Using CEA, indoor farms such as greenhouses and vertical farms, enable the inputs to the growth of fresh produce to be understood, controlled and optimised. Water, nutrients, light energy and environmental conditions can all be tweaked to optimise the output of the crop and to reduce the use of resources.
These farms allow us to understand the system of growing without impacting the local environment, by ensuring efficient energy and resource flows along with recapture technologies. They enable us to build farms anywhere in the world, to grow produce in a more decentralized, resource-efficient way that can help build resilience into our food system.
Opponents of CEA will point to the increased use of energy, but this is offset by the reduced energy requirements in transportation, processing, storage, fertiliser and pesticide usage. If you understand and match your local energy and food production, this is no longer such an issue. There are still challenges for the CEA industry, but the winds are blowing in the right direction.
Increasing the renewable energy mix on the grid will reduce the cost of energy over time and is the perfect power source for indoor farms. Spiky supply and storage may appear to present an issue, but the energy profile of an indoor farm can be tuned to the supply of the grid. Plants are great at storing energy and have inherent redundancy too, hence the possibility of using plants as a new form of battery becomes very real when we see our food and energy systems as one.
There are numerous flagship examples of CEA projects implementing many of these principles worldwide. From the advanced Dutch greenhouse networks, to Sundrop Farms in Australia, to new combined heat, power and greenhouse projects in the UK such as Beeswax Dyson’s new strawberry growing facility. From Growing Underground’s vision of circular farms, to LettUs Grow’s partnership with Octopus Energy and the many projects in the pipeline with farmers around the UK looking to incorporate indoor vertical farms with existing anaerobic digestion plants. These projects show that things are moving rapidly in the right direction to bring our food and energy systems back together again.
There are still big questions to answer and challenges ahead when looking at the sustainable future of our combined food and energy systems, but we are on a very exciting journey as part of a new industry and a whole new way to look at food and energy. Joined up thinking is needed and bridges need to be rebuilt - energy and food producers will be working much closer together. To address climate change we know that we need to seriously address our energy system. And to address our energy system in full, we need to include food as a fundamental part of it.
Charlie is co-founder & Chief Executive Officer at LettUs Grow. With a background in renewable energy consultancy & engineering design, Charlie is a proponent of tech for good & passionate about all manners of sustainability, whether in food, energy, resource efficiency or waste valorisation. Charlie is also on the UKUAT (UK Urban AgriTech collective) advisory board.
Babylon Micro-Farms Expanding Its Impact With New Partnership
Babylon Micro-Farms makes indoor growing aimed at providing more farm-fresh options for college students. It is now partnering with Harvest Table Culinary Group to bring fresh produce to more colleges
April 1, 2021
CHARLOTTESVILLE, Va. (WVIR) - A company that started at the University of Virginia is hoping to expand its impact.
Babylon Micro-Farms makes indoor growing aimed at providing more farm-fresh options for college students. It is now partnering with Harvest Table Culinary Group to bring fresh produce to more colleges.
“Self-contained vertical farms use hydroponics to grow plants with 90% less water. There are no pesticides or chemicals. We can grow plants 2-3 times more quickly,” Babylon Micro-Farms CEO Alexander Olesen said.
The planting of the farms is mostly done by designated operators assigned by Babylon, but they often get students involved.
Green Life Farms Breaks Ground On Second Hydroponic Greenhouse
The hydroponic technology allows Green Life Farms to grow leafy greens in oxygenated water – without soil – then harvest and package them in a controlled environment, reducing the risk of contamination and preserving flavor and freshness
04.05.2021
By Emily Park
LAKE CITY, FLA. - Green Life Farms announced on April 1 that the company is building a second hydroponic greenhouse in Lake City, Fla.
The hydroponic technology allows Green Life Farms to grow leafy greens in oxygenated water – without soil – then harvest and package them in a controlled environment, reducing the risk of contamination and preserving flavor and freshness.
Following the success of its flagship hydroponic greenhouse in Lake Worth, Fla., and significant customer demand for its products, the new greenhouse will be 400,000 square feet and is expected to begin commercial operations in early 2022.
“Following our very successful launch in South Florida, we are proud to announce this new facility to serve North Central Florida - the Jacksonville, Gainesville, and Tallahassee regions,” said Forrest Sawlaw, chief operating officer of Green Life Farms. “In light of ongoing food safety concerns across the country, now more than ever customers are looking for locally grown, clean produce. Our innovative hydroponic technology will deliver the cleanest and freshest leafy greens, all free from GMOs, pesticides and contaminants.”
Green Life Farms will incorporate specialized ozone water management technology to filter, sanitize and store rainwater for use in the growing process, and will rely on Florida sunshine – meaning the facility will use significantly fewer natural resources.
The new greenhouse will be able to produce 18 harvests each year and use 90% less water than conventional farming. At full maturity, the greens are gently moved using a floating conveyor system to be harvested, cooled, and packaged to reach customers within a few days of harvest, instead of the 8 to 10 days it may take conventionally farmed produce to reach customers in the region.
Green Life Farms’ products include Baby Arugula, Baby Kale, Baby Romaine, Farmer’s Blend, and Butterhead Lettuce, and are currently sold at more than 120 grocery store locations throughout South Florida.
Invitation To F&A Next 2021: The Impact of Innovation!
While our aim was to physically host the upcoming edition of F&A Next at the Campus of Wageningen University & Research, another virtual summit is today’s reality. Postponing is definitely not an option. Irrespective of Covid-19, a great deal happened in 2020. Investments in global food- and agtech were increased by over 30% to some USD 26 bilion!
F&A Next invites investors, entrepreneurs, and experts to address the next challenges of our sector on Wednesday, 26 May 2021 at the 6th annual F&A Next Summit. We look forward to showcasing the next scaling food and agtech companies. Yes, we‘ll miss meeting you in person, but we’ll make sure that dialing in will be as close as possible to the real thing!
During this year's 3-hour live, virtual summit we will
bring you up to speed on the Impact of Innovation in the agrifood industry,
present eight 'Next Heroes in Food- & Agtech', and
offer you ample opportunity to virtually connect and meet with (other) startups, scale-ups, investors, and corporates in the agrifood space.
GET YOUR EARLY-BIRD TICKET WITH A 25% DISCOUNT
Book your ticket before 12 April to get a 25% discount! Apply the code: FaN@21
Stay safe, stay healthy!
The partners of F&A Next
2021 Theme: "The impact of Innovation"
Get Your eTicket to F&A 2021, 26 May
Food & Ag Innovation only started around 2014 and has definitely gained momentum ever since. in 2020 investments in global food and agtech have risen, irrespective of Covid-19 influences. The pandemic did, however, trigger changes in consumer behavior. Has ‘life as we know it’ irrevocably changed? And what about the much-needed innovation earlier in the value chain?
At F&A Next, Rob Leclerc, founding Partner of Agfunder and Nick Ferreday, Executive Director Food & Agribusiness at Rabobank, will compare notes.
AeroFarms To Go Public in $1.2 Billion Spring Valley SPAC Deal
AeroFarms was established in 2004. The company’s goal is to, “Transform agriculture by building and operating environmentally responsible farms throughout the world.”
APRIL 4, 2021
New Jersey-based company AeroFarms is set to go public in a $1.2 billion Spring Valley SPAC deal. AeroFarms was established in 2004. The company’s goal is to, “Transform agriculture by building and operating environmentally responsible farms throughout the world.”
According to a recent Bloomberg report, AeroFarms will go public in a merger with Spring Valley Acquisition Corp. Thanks to the pending merger, the two companies will have a combined equity value of $1.2 billion. AeroFarms was co-founded by David Rosenberg, Ed Harwood, and Marc Oshima. Rosenberg now serves as the CEO. Harwood is the Chief Science Officer, and Oshima is the Chief Marketing Officer.
AeroFarms: An Explainer
How does AeroFarms achieve its aim of transforming agriculture? The company utilizes a technique called indoor vertical farming. The benefits of indoor vertical farming include reduced space which results in greater productivity per square foot.
AeroFarms says this method makes productivity per square foot 390 times more effective than traditional farming methods.
The indoor vertical farming method also, as AeroFarm purports, results in using 95% less water and zero pesticides. AeroFarms has a smart strategy for keeping plants healthy. This includes a combination of smart aeroponics, light, nutrition, data, substrate, pest management, and scaling.
The AeroFarms method means that the agriculture involved is fully controlled by one entity. This allows AeroFarms complete control over every aspect of greens, herbs, and more that they grow for clients.
From the size, color, shape, and most importantly, the flavor, AeroFarms has complete control. Besides curating custom greens for food clients, AeroFarms also sells their own products at local retailers that are called Dream Greens. According to AeroFarms, Dream Greens are grown on indoor vertical AeroFarms locations in New Jersey. They are organic, pesticide-free, and non-GMO.
Potential clients can choose to use AeroFarms’ food service. The benefits of their customized food service includes year-round availability, a longer shelf life, consistent pricing, no weather interruptions, heirloom greens varieties and more.
More About AeroFarms
The AeroFarms technology was named one of TIME’S best food and drink inventions of 2019. Some of AeroFarms other financial partners include Ikea, Prudential, and Goldman Sachs. Rosenberg, who is also the CEO of AeroFarms said this about the upcoming merger and initial public offering via a Business Wire report.
“At AeroFarms, our mission is to grow the best plants possible for the betterment of humanity, and we are executing on this by taking agriculture to new heights with the latest in technology, innovation and understanding of plant science. Our technology empowers our operations – this is how we get closer to where the problems, opportunities, and solutions are. We also have the capabilities to innovate fast by turning our crops a typical 26 times per year that allows us to continuously learn and improve yield and quality while simultaneously reducing capital and operating costs.”
After the merger is completed and closed, AeroFarms will be publicly traded on Nasdaq under the ticker ARFM. The official date for the AeroFarms IPO has yet to be confirmed.
Published in Business and News
Katherine Stinson
Katherine Stinson is an award-winning journalist and Staff Reporter at Grit Daily News, where she covers Texas and Southern states' startup and entrepreneurship news. Based in San Antonio, Texas, she also contributes to ScreenRant, Outlander TV News, and San Antonio Magazine.
How Sustenir Group Makes Sustainable Farming Possible In The Island Nation
Undertaking large-scale farming is near to impossible in a country like Singapore with a land area of just 724.2 square kilometers (279.6 square meters)
The Indoor Farm Uses Methods Like Controlled Environment Agriculture, Vertical Farming, And Hydroponics To Grow Kale, Spinach And More
2 April 2021
Undertaking large-scale farming is near to impossible in a country like Singapore with a land area of just 724.2 square kilometers (279.6 square meters).
According to Singapore Food Agency, only two square kilometers of the country’s land is available for farming, which is much lesser when compared with Malaysia, which uses more than 11 times the land for farming. This explains why over 90 percent of the food items in the island nation is imported.
Despite the active measures taken by the Singapore government to transform the agriculture sector, local farmers often whine that highly nutritious items like root vegetables, fruits, herbs, goat milk and frog meat aren’t getting adequate support.
But this issue is just the tip of the iceberg — when the environmental implications of conventional farming methods are taken into account.
In general, traditional farming methods are the largest contributors to greenhouse gas emissions. Coupled with the rising population, farmers often heavily rely on nitrogen-based fertilizers to increase the yield, which inadvertently leads to nitrous oxide emissions, which further exacerbates climate change.
To take this problem head-on, Benjamin Swan started an agritech company in Singapore six years ago, which relies on a more efficient and sustainable way of farming.
The green stop
As offbeat as it may sound, the idea for a vertical farm occurred to the Australian when he couldn’t find fresh salads in Singapore’s grocery stores.
“When I first moved here from Australia over 12 years ago, I was frustrated that it was so difficult to get good produce here,” he told e27 in an interview.
But he knew that the problem did not lie with distributors or farmers because, by the time the produce is flown to Singapore from different countries, the greens are already wilting in the bag.
“The other thing that frustrated me was the food waste that would accumulate at the bottom of the bag if I didn’t eat the greens within 12 hours,” he said.
Also Read: How Fefifo aims to make farming cool again for the younger generation
But funnily enough, it was a Facebook post that brought in the real motivation for Swan to go deeper into vertical farming.
“When I read a Facebook article about vertical farming, I thought to myself, ‘hey, this is cool and I can grow myself a great salad at home’,” he said.
To gain more knowledge of the industry, Swan traveled to different countries and met experts in traditional farming. As he gained more knowledge, he realized that traditional farming is harmful to the environment.
This is when he started testing out by growing plants indoors while still holding on to his full-time job as an engineer.
Initially, he began to grow kale in the basement of a swimming pool at over 42 degrees, which was hitherto unheard of, as the item generally grows at a temperature of 18 to 20 degrees.
After 18 months of heavy research, he, along with his co-founder Martin Lavoo, launched Sustenir Group, a vertical farm that sells its products in stores like Redmart and Cold Storage.
How it works
Sustenir Group uses methods like controlled environment agriculture (CEA), vertical farming, and hydroponics to grow 52 varieties of plants like kale, lettuce, spinach, and more.
The indoor farming facility has sensors operating 24 hours to provide the company with data on the health and status of all its plants. The parameters used include humidity, temperature, and light.
After receiving data from the sensors, its system adjusts the environment for each plant accordingly.
While the majority of farmers use pesticides to manipulate the physical appearances of fruits and vegetables, Sustenir Group doesn’t use any.
“We use zero pesticides. Our produce is 100 percent clean, meaning they go beyond organic. As we know, organic products still use pesticides, albeit lesser harmful ones. Not only do we use zero pesticides, but we also make sure haze/pollution doesn’t come to the room,” Swan said.
Since Sustenir uses no chemicals, Swan claims its vegetables and fruits are not only more nutritious but also taste better — with customers coming back in surprise, seeking where he gets the vegetables from because their children enjoy the vegetables very much.
Also Read: Tunas Farm raises pre-seed funding from Gayo Capital to launch its urban farming technology
While traditional farming is a highly laborious occupation with hours spent toiling under the parched sun, the farming experience for employees at Sustenir is far different.
“Instead of someone working day and night, what happens is that everything inside the indoor farm is pre-scheduled. So we know when a plant needs to move and be harvested because we can control exactly how much solar radiation goes to the plant. It is all pre-planned,” he explained.
“It’s not like outdoor farms where you might have too much cloud coverage this month. So we have to leave the plants in for another couple of days. Everything is planned and scheduled. It’s all within our stride,” he remarked.
The future plans
In the future, Sustenir Group plans on leveraging both indoor and outdoor farming methods.
“As of now, it’s not possible to grow products like bok choy on an indoor farm. That’s why it is necessary for us to still leverage outdoor technology and improve it somewhat, so we can become more efficient with our products that are going out on land. Because the reality with indoor farming is that we can only grow limited products here,” he said.
Last year, Sustenir expanded into Hong Kong and Malaysia.
“We have just got the third market under our belt with big ambitions to build across Southeast Asia and North Asia in the coming years,” he said.
Although Sustenir’s farm is cash-flow positive, Swan said that the company is more focused on growth rather than profits.
Image Credit: Sustenir Group
Greenhouses Can Grow Lettuce And Generate Solar Power: Study
A recent study shows that lettuce can be grown in greenhouses that filter out wavelengths of light used to generate solar power, demonstrating the feasibility of using see-through solar panels in greenhouses to generate electricity
March 30, 2021
By Matt Shipman
A recent study shows that lettuce can be grown in greenhouses that filter out wavelengths of light used to generate solar power, demonstrating the feasibility of using see-through solar panels in greenhouses to generate electricity.
“We were a little surprised – there was no real reduction in plant growth or health,” says Heike Sederoff, co-corresponding author of the study and a professor of plant biology at North Carolina State University. “It means the idea of integrating transparent solar cells into greenhouses can be done.”
Because plants do not use all of the wavelengths of light for photosynthesis, researchers have explored the idea of creating semi-transparent organic solar cells that primarily absorb wavelengths of light that plants don’t rely on, and incorporating those solar cells into greenhouses. Earlier work from NC State focused on how much energy solar-powered greenhouses could produce. Depending on the design of the greenhouse, and where it is located, solar cells could make many greenhouses energy neutral – or even allow them to generate more power than they use.
But, until now, it wasn’t clear how these semi-transparent solar panels might affect greenhouse crops.
To address the issue, researchers grew crops of red leaf lettuce (Lactuca sativa) in greenhouse chambers for 30 days – from seed to full maturity. The growing conditions, from temperature and water to fertilizer and CO2 concentration, were all constant – except for light.
A control group of lettuces was exposed to the full spectrum of white light. The rest of the lettuces were divided into three experimental groups. Each of those groups was exposed to light through different types of filters that absorbed wavelengths of light equivalent to what different types of semi-transparent solar cells would absorb.
“The total amount of light incident on the filters was the same, but the colour composition of that light was different for each of the experimental groups,” says Harald Ade, co-corresponding author of the study and the Goodnight Innovation Distinguished Professor of Physics at NC State.
“Specifically, we manipulated the ratio of blue light to red light in all three filters to see how it affected plant growth,” Sederoff says.
To determine the effect of removing various wavelengths of light, the researchers assessed a host of plant characteristics. For example, the researchers paid close attention to visible characteristics that are important to growers, grocers, and consumers, such as leaf number, leaf size, and how much the lettuces weighed. But they also assessed markers of plant health and nutritional quality, such as how much CO2 the plants absorbed and the levels of various antioxidants.
“Not only did we find no meaningful difference between the control group and the experimental groups, we also didn’t find any significant difference between the different filters,” says Brendan O’Connor, co-corresponding author of the study and an associate professor of mechanical and aerospace engineering at NC State.
“There is also forthcoming work that delves into greater detail about the ways in which harvesting various wavelengths of light affects biological processes for lettuces, tomatoes and other crops,” Sederoff says.
“This is promising for the future of solar-powered greenhouses,” Ade says. “Getting growers to use this technology would be a tough argument if there was a loss of productivity. But now it is a simple economic argument about whether the investment in new greenhouse technology would be offset by energy production and savings.”
“Based on the number of people who have contacted me about solar-powered greenhouses when we’ve published previous work in this space, there is a lot of interest from many growers,” O’Connor says. “I think that interest is only going to grow. We’ve seen enough proof-of-concept prototypes to know this technology is feasible in principle, we just need to see a company take the leap and begin producing to scale.”
About this article:
The paper, “Balancing Crop Production and Energy Harvesting in Organic Solar Powered Greenhouses,” appears in the journal Cell Reports Physical Science. Co-lead authors of the paper are NC State Ph.D. students Melodi Charles and Eshwar Ravishankar. The paper was co-authored by Yuan Xiong, a research assistant at NC State; Reece Henry and Ronald Booth, Ph. D. students at NC State; Jennifer Swift, John Calero and Sam Cho, technicians at NC State; Taesoo Kim, a research scientist at NC State; Yunpeng Qin and Carr Hoi Yi Ho, postdoctoral researchers at NC State; Franky So, Walter and Ida Freeman Distinguished Professor of Materials Science and Engineering at NC State; Aram Amassian, an associate professor of materials science and engineering at NC State; Carole Saravitz, a research associate professor of plant biology at NC State; Jeromy Rech and Wei You of the University of North Carolina at Chapel Hill; and Alex H. Balzer and Natalie Stingelin of the Georgia Institute of Technology.
Our Monthly Webinar For April Is “Training The Next Generation of Aquaponic Farmers” From Researcher Sarah Milliken At The University of Greenwich, U.K.
Ms. Milliken will introduce an open access aquaponics curriculum, Aqu@teach, specifically developed for college students with a focus on entrepreneurial and transferable skills
The Webinar Will Take Place Live, Saturday,
April 17 From 11 am To 12 pm EST And Feature A Live Q&A.
Click Below To Register:
REGISTER: Training the Next Generation of Aquaponic Farmers
Ms. Milliken will introduce an open access aquaponics curriculum, Aqu@teach, specifically developed for college students with a focus on entrepreneurial and transferable skills. As soilless food production technologies become increasingly important in light of climate change and the threat of food insecurity, there is an urgent need to provide an appropriately trained workforce.
The Webinar is free to the public during the live broadcast. The Webinar will remain available for free, in perpetuity, to all Aquaponics Association Members in the Member’s Area of our Community Site.
Special thanks to Ed "Aqua-Eddie" Tivnan, Association Director of STEM Aquaponics, for organizing the webinar.
Hope to see you there!
Brian Filipowich, Chairman
Aquaponics Association
The Aquaponics Association
1240 Evarts Street, NE
Washington, DC 20018
How Square Roots Is Training Next-Gen Farmers During A Pandemic
The average age of the American farmer is 58 years old. If we're going to change the food system, we need to create more pathways for young people to launch successful careers in agriculture
Square Roots
10.08.20
The average age of the American farmer is 58 years old. If we're going to change the food system, we need to create more pathways for young people to launch successful careers in agriculture.
One of the many ways Square Roots invests in the future of farming is through our Next-Gen Farmer Training Program—aimed at new farmers or those at early stages in their careers. Farmers initially join Square Roots as Apprentice Growers. Through our proprietary training methodology—supported by our intuitive technology platform—Apprentice Growers rapidly learn the essential farm skills needed to move into permanent roles on the farm team and accelerate their careers.
We continuously evolve our training program to zero in on the skills and experiences that help employees become the best indoor farmers they can be. Throughout COVID-19, we have been committed to prioritizing people safety and plant safety which has led to changes in our day-to-day farming operations, as well as rewiring our in-flight farmer training programs in May and adapting how we run the Square Roots Next-Gen Farmer Training Program going forward. Also, after several years of training farmers, we’ve listened and learned to what farmers value from their experience at Square Roots and have incorporated that into our program going forward. Read more about what it’s like to be a grower at Square Roots and how the program has evolved:
Individual Pathways
Based on the needs of our farm production teams, apprentices are hired and onboarded, either individually or in pairs, on a rolling basis. By spacing out onboarding and training, our team is able to provide more attention and support to apprentices, allowing them to move more quickly through the training program and into permanent positions on our team. We expect most apprentices will complete their training in three to six months, but each will advance at their own pace.
Foundational Remote Learning
We have moved our training materials onto a virtual learning platform, which houses videos, interactive presentations, animated diagrams, virtual tours, and other types of content that can be brought to life beyond a typical presentation. Since COVID-19 restricts our ability to hold classroom-style learning, online learning can be self-serve, supporting different types of learning styles. It also drives consistency in training and terminology, reducing the burden on managers responsible for administering it.
Intensive ‘Boot-Camp’ Style Farm Immersion
Training for Apprentice Growers is laser focused on the skills required for new farmers to quickly become the best indoor farmers they can be. After the initial foundational onboarding, apprentices will jump into production, and, in parallel, will be equipped with the necessary context and complementary training to support expanded learning and competency much sooner. Apprentices will be supported by our software operating system the Farmer Toolbelt, empowering them to get up to speed much faster, engaging with data, and ultimately helping them become better growers. Throughout the training process, farmers will receive direct supervision by one of our experienced farm team members who will act as their training guide and provide professional and moral support.
Pathway to Permanent Employment at Square Roots
Central to Square Roots is our mission to empower Next-Gen leaders in urban farming, and the Next-Gen Farmer Training Program is one of the most direct ways we do that. The program is designed to bring young people with little or no experience up to speed in our proprietary indoor farms as quickly as possible and on to their careers in indoor farming—acting as an internal training program for permanent full-time employees on the Square Roots farm team.
The Apprentice Grower role is the first step in a career path to indoor farming at Square Roots. To start, apprentices will earn an hourly rate indexed to the area’s living wage, and receive 100% covered health benefits and equity in Square Roots. Once they’ve successfully mastered indoor growing fundamentals (we expect this to take three to six months), apprentices will be eligible to move into Associate Grower positions.
For more information and to learn about new open positions on our farm teams, follow us on social media and sign up for our newsletter for updates.
Tags: Next-Gen Farm / Farmer Training / COVID-19 Response / Updates
Continuing Education: Urban Agriculture
It’s been 10,000 years since the agricultural revolution gave rise to cities. Agriculture now covers more than half of the world’s habitable land, and is spreading at a rate of about 15 million acres annually
April 1, 2021
It’s been 10,000 years since the agricultural revolution gave rise to cities. Agriculture now covers more than half of the world’s habitable land, and is spreading at a rate of about 15 million acres annually. Cities, meanwhile, now comprise more than half the global population (over 80 percent in developed countries), and the numbers are rising. Using current farming methods to feed a global population expected to hit 10 billion by midcentury would require adding new farmland equal in size to the continental United States.
This alarming situation is not even factoring in the impact of the climate crisis, which is expected to alter growing seasons and disrupt the phenological cycles that keep plants and their pollinators in sync. What’s more, new agricultural land mostly comes from felling biodiverse, carbon-sequestering forests to make room for mono-crops that stash very few greenhouse gases and for livestock that actually generate them. That makes the climate crisis worse and farming more difficult.
In addition to land consumption, agriculture guzzles three-quarters of the fresh water used globally each year, while runoff from fields treated with herbicides, pesticides, and fertilizers contaminates significant amounts of the water that’s left. Then there’s transportation. As farms extend farther and farther from the cities they supply, food is trucked, shipped, and flown vast distances: farm to plate, the ingredients in a typical American meal travel an average of 1,500 miles. From a security perspective, the fact that most of the world’s food production is controlled by just a handful of corporations is unnerving. And from a public health perspective, the emergence of Covid-19 and other new diseases offers yet another indicator of ecological imbalance. It’s time to rethink the way we farm.
Food security, as defined by the United Nations, means that all people, at all times, have physical, social, and economic access to sufficient, safe, and nutritious food that serves their food preferences and dietary needs for an active and healthy life. Key to achieving food security in a way that’s more sustainable than current practices is urban agriculture—not as an outright replacement for rural farming, but as a crucial component in a balanced system.
Urban agriculture can take many forms: rooftop greenhouses raised beds, and community-farming initiatives such as the City of Atlanta’s “Aglanta” program, which turns underused parcels in utility rights-of-way into farm plots eligible for U.S. Department of Agriculture certificates and associated loans. Ultimately, though, horizontal strategies are not productive enough to make a real dent in the food needs of a city. (If raised beds covered every rooftop in Manhattan, the produce grown would feed only about 2 percent of the borough’s population.) Just as cities grow vertically, so too must urban agriculture, and that means bringing it indoors.
“Controlled environments have been used for many years,” says Chieri Kubota, a professor of controlled environment agriculture (CEA) in the Department of Horticulture and Crop Science at Ohio State University. “Now that multiple issues are making conventional production outdoors more difficult, putting controlled environments in and near cities brings food production closer to potential markets—and also to younger generations of potential farmers who want to live in urban centers.”
Vertical agriculture is a type of CEA that—like high-rise buildings—stacks layers to provide usable area many times the footprint of the site. Instead of growing in soil, which is a heavy way to deliver nutrients, plants in vertical farms are grown hydroponically, aquaponically, or aeroponically. In hydroponics, plants are cultivated in nutrient-enriched water, which is captured and reused so that the system uses as little as a tenth of the water conventional agriculture needs. An aquaponic system pairs hydroponics with fish production, circulating the nutrients in the fish waste to feed the vegetables, and using the plants as a biofiltration system that returns clean water to the fish. Reducing water consumption even further—by as much as 98 percent, compared to field growing—aeroponic systems deliver nutrients in a fine mist to plant roots that are just hanging in the air. And because controlled environments exclude the weeds and pests that trouble field-grown produce, the use of herbicides and pesticides is all but eliminated.
Stacked plants may need to be rotated to make the most of available sunlight, which can be supplemented (or even substituted altogether) with LED grow lights. These can be calibrated to provide blue and red light in optimal doses for each type of plant, and timed to increase plant growth with extended days and growing seasons. (While it’s technically possible to grow any type of crop this way, for now it’s mainly leafy greens and tomatoes that are economically viable.) Cool enough to be strung right in among the plants without burning them, LEDs reduce site electricity consumption (and costs) per square foot of grow area by about a third compared to older technologies, such as high-pressure sodium. “Energy is a game-changer,” says Dickson Despommier, an emeritus professor of microbiology and public health at Columbia University, whose seminal 2010 book, The Vertical Farm: Feeding the World in the 21st Century, is widely credited with kick-starting vertical agriculture in North America. Cost-effective LED lighting opens up the possibility of converting urban and urban-adjacent building types such as parking garages, big-box stores, and shopping malls into productive local farms, he says.
With productivity rates that are orders of magnitude greater than conventional farming, high-rise growing is gaining traction worldwide. The world’s first such system began operations in 2012 in Singapore. The land-strapped city-state, which imports about 90 percent of its food, aims to grow a third of its produce locally by 2030. Indoor vertical farms in the country now produce about 80 tons of greens a year, and the Singapore Food Agency is supporting research into and development of the method as its main bet on the future.
In China, great swaths of arable land have been lost to development (more than 30 million acres between 1997 and 2008) and 20 percent of what’s left is contaminated. At the same time, the country has a strong tradition of urban-adjacent farming. When a 247-acre agricultural site, midway between Shanghai’s main international airport and the megacity’s center, recently came up for redevelopment, global design firm Sasaki proposed that, rather than create yet another tech park, the client take its agricultural mission to the next level. As a result, the Sunqiao Urban Agricultural District is slated to become one of China’s first comprehensive national agricultural zones. Sasaki’s master plan, which has received approval from the Pudong District and is now proceeding for formal approval from the City of Shanghai, expands the district’s role in Shanghai’s food network, integrating vertical agricultural production, research, and education into a dynamic public domain. In addition to research and development facilities and an agriculture production zone, the plan provides for a civic plaza showcasing productive landscapes, a science museum, an interactive greenhouse, an aquaponics display, and a destination market. “It’s urban agriculture on steroids,” says Michael Grove, chair of landscape architecture, civil engineering, and ecology at Sasaki.
The Sunqiao project will include a civic plaza with productive landscapes (top), a science museum, and an interactive greenhouse (above), among other elements. Image courtesy Sasaki.
Grove identifies three primary drivers for prioritizing urban agriculture globally: the need to curtail agricultural sprawl and thereby protect ecosystems, to reclaim economic agency by diversifying control of food production, and to build community: “Food brings us together,” he says. Behind Asia’s early adoption of urban agriculture, he sees a historic understanding among the region’s societies that the well-being of the population requires systemic support. That may also be a factor in Europe, where the Netherlands is a global leader in controlled-environment technology, and Denmark is home to the world’s latest and largest vertical farm, a partnership between a Taiwanese CEA tech company and a local start-up: with growing shelves stacked 14 deep, the 75,000-square-foot wind-powered facility has the capacity to produce 1,000 metric tons of greens a year.
A hub for teaching, research, and community engagement, located within sight of downtown Columbus and designed by Erdy McHenry Architecture, supports Ohio State’s CEA efforts. Brad Feinknopf
North America has been slower to adopt vertical farming, a lag that Ohio State’s Kubota attributes in large part to the year-round, nationwide availability of produce from California, Arizona, and Florida. But now, she says, climate disruptions and shortages of viable farmland in those states, along with the increasing urbanization of the workforce, strengthen the rationale for controlled environment agriculture. To support Ohio State University’s multidisciplinary research into CEA, a one-acre vertical greenhouse is under construction within sight of downtown Columbus. As part of the facility, the recently completed Kunz-Brundige Franklin County Extension Office serves as a hub for teaching, research, and community engagement around food, health, agricultural production, and sustainability. Both buildings are designed by Philadelphia-based Erdy McHenry Architecture.
Although still tiny, vertical farming is the fastest-growing sector in U.S. agriculture. A projected compound annual growth rate (CAGR) of more than 20 percent from 2020 to 2026 is expected to bring sales to around $10 billion a year. And while significant numbers of start-ups in the capital-intensive sector have failed—as indicated by the track record of several initiatives profiled in this magazine eight years ago —experts say that’s an inevitable aspect of an emerging technology.
Among the growing number of enterprises going strong, however, is Vertical Harvest, the first vertical hydroponic greenhouse in North America. Cofounded by architect Nona Yehia, principal at GYDE Architects, the company began operations in 2016 in Jackson Hole, Wyoming. Jackson is a rural town, but it performs like a city in relevant ways: 97 percent of its developable land is already in use, and, with a four-month growing season, 98 percent of its food is imported. Inspired by Despommier’s work, the need for a local food supply, and the opportunity to provide meaningful work for community members with intellectual and physical challenges, Yehia designed a three-story greenhouse for a 30-by-100-foot municipally-owned lot next to a parking garage. “The town councilor who showed us the property thought we’d put up a plastic hoop structure to extend the growing season a couple of months, employ a few people, and call it a day,” recalls Yehia. But she and her business partners wanted to grow as much food as possible, to employ as many people as possible, and to do both year-round. “That’s where the idea to grow up came from,” she says.
Vertical Harvest’s three-story CEA facility in Jackson Hole, Wyoming, produces as much food on a tenth of an acre as on a 10-acre conventional farm. Photos © Vertical Harvest (1), Hannah Hardaway (2 & 3)
With a footprint of a tenth of an acre, the greenhouse produces as much food as would a 10-acre conventional farm. It employs 30 people, more than half of whom have a disability. And it’s profitable. “It would have been easier as a nonprofit,” Yehia says, “but we were committed to creating a replicable model that is not about charity: it’s about empowerment.”
After five years of operation, Vertical Harvest is ready to expand. Construction is scheduled to start this year on a second location that incorporates affordable housing and municipal parking in Westbrooke, Maine. The new 70,000-square-foot greenhouse is expected to provide the equivalent of 50 full-time jobs and to produce 1.3 million pounds of produce a year, supplying hospitals, corporate cafeterias, schools, chefs, restaurants, and caterers, as well as individual customers. “These ecosystems can put out a lot of food,” says Yehia. “Making sure you have customers who can buy at scale is as essential to success as growing plans.”
Vertical Harvest intends to build up to 15 farms in the next five years, with agreements already in place for projects in Philadelphia and Harrisburg, Pennsylvania, and Chicago, and discussion is under way for five other locations. Like the Wyoming and Maine projects, they will integrate social value and community engagement with their agricultural mission. “It’s the perfect intersection to show what architecture can achieve in its social role in our communities,” Yehia says. And while she has run Vertical Harvest as designer, entrepreneur, and urban farmer, it’s entirely possible for architects to advocate for urban agriculture in their more usual role as prime consultants, coordinating the work of other experts.
As CEA picks up speed, the time may not be far off when every municipality will incorporate vertical farming into its civic infrastructure, valued the way public libraries and recreation centers are. “It should be something that we all expect to see when we go to cities,” Yehia says: “infrastructure that grows food and futures, and bolsters the sustainability of the community.”
Continuing Education
To earn one AIA learning unit (LU), including one hour of health, safety, and welfare (HSW) credit, read the article above and watch this video.
Then complete the quiz. Upon passing the test, you will receive a certificate of completion, and your credit will be automatically reported to the AIA. Additional information regarding credit-reporting and continuing-education requirements can be found at continuingeducation.bnpmedia.com.
Learning Objectives
Explain how conventional agricultural methods contribute to climate change.
Define terms such as urban agriculture, controlled environment agriculture (CEA), and vertical agriculture.
Describe technologies relevant to CEA, such as hydroponics, aeroponics, and aquaponics.
Discuss how CEA can enhance food security and bring social value to underserved communities.
AIA/CES Course #K2104A
Complete the Quiz
Lead Image: KEYWORDS cities / climate change / urban planning
PODCAST: Vertical Farming Podcast - Season 3 Episode 29 - Nicholas Dyner. Nick Is The CEO of Moleaer
In this episode, Harry and Nick discuss Nick’s extensive background working in the water treatment industry
Join Harry Duran, host of Vertical Farming Podcast, as he welcomes to the show Nicholas Dyner. Nick is the CEO of Moleaer, an organization that produces commercial nanobubble generators to deliver sustainable, chemical-free water quality improvement for agriculture, reservoirs, lakes, ponds, and more.
In this episode, Harry and Nick discuss Nick’s extensive background working in the water treatment industry. Nick expounds on nanobubble technology, what it is and how it can be used to improve vertical farming and the agricultural industry as a whole. Finally, Harry and Nick talk about the ongoing struggle for universal access to safe water and how advancements in technology can help restore and improve the quality of sea life.
Listen & Subscribe
BrightFarms Founder And CEO Reflect On 10 Years of Growing Leafy Greens Indoors And Talk Future Plans
Valued at $6.8bn in the US alone (according to Research&Markets), the market for hydroponically-grown produce is no longer niche
31-Mar-2021 By Mary Ellen Shoup
Valued at $6.8bn in the US alone (according to Research&Markets), the market for hydroponically-grown produce is no longer niche and poised for strong growth over the next several years, predicts BrightFarms, a company growing a variety of leafy greens hydroponically in massive indoor greenhouses.
Please Click Here To Read The Full Article
Vertical Farming Startup Oishii Raises $50m In Series A Funding
“We aim to be the largest strawberry producer in the world, and this capital allows us to bring the best-tasting, healthiest berry to everyone.”
By Sian Yates
03/11/2021
Oishii, a vertical farming startup based in New Jersey, has raised $50 million during a Series A funding round led by Sparx Group’s Mirai Creation Fund II.
The funds will enable Oishii to open vertical strawberry farms in new markets, expand its flagship farm outside of Manhattan, and accelerate its investment in R&D.
“Our mission is to change the way we grow food. We set out to deliver exceptionally delicious and sustainable produce,” said Oishii CEO Hiroki Koga. “We started with the strawberry – a fruit that routinely tops the dirty dozen of most pesticide-riddled crops – as it has long been considered the ‘holy grail’ of vertical farming.”
“We aim to be the largest strawberry producer in the world, and this capital allows us to bring the best-tasting, healthiest berry to everyone. From there, we’ll quickly expand into new fruits and produce,” he added.
Oishii is already known for its innovative farming techniques that have enabled the company to “perfect the strawberry,” while its proprietary and first-of-its-kind pollination method is conducted naturally with bees.
The company’s vertical farms feature zero pesticides and produce ripe fruit all year round, using less water and land than traditional agricultural methods.
“Oishii is the farm of the future,” said Sparx Group president and Group CEO Shuhei Abe. “The cultivation and pollination techniques the company has developed set them well apart from the industry, positioning Oishii to quickly revolutionise agriculture as we know it.”
The company has raised a total of $55 million since its founding in 2016.
SPAIN: HPGen™ Improves Crop Yields, Reduces Irrigation System Maintenance In Almeria Greenhouse
HPNow addresses growing global challenges in clean water and sanitation through its range of on-site, autonomous, safe and sustainable hydrogen peroxide generation solutions
Located in the highly productive greenhouse area in the Almeria region in southern Spain, a greenhouse grower with cucumbers in winter and watermelons in summer ran into some irrigation issues: the soil in the region is dry, the climate warm and the operators use organic fertilizers. The plants are grown in the typical Almeria sandy soil (enarenado) and are irrigated with a modern drip irrigation system using pressure compensating non-leakage drippers.
When HPNow’s precision irrigation and agronomy experts assessed the site, it was clear that clogging of drippers leads to non-uniform irrigation and insufficient water and fertilizer delivery to part of the crop. To mitigate this, farm personnel were going through the drippers frequently to “unclog”, a manual process highly costly in man-hours.
Organic matter
Soil quality was also analyzed and the amount of organic matter in the soil, a critical parameter for the healthy growth of the plants, was very low at 0.33%. This is due to poor dissolution of organic matter fertilizers in water, which further exacerbates dripper clogging and decreases crop productivity. To overcome these issues, an HPGen™ system was installed and integrated with the drip irrigation system. The HPGen™ was installed in the irrigation room and set to automatically fill a buffer tank with Peroxide UltraPure™. Dosing was done through a proportional dosing pump, which is both simple and effective.
Improved yields
After a season of cucumber crop with HPGen™, yields were compared to previous seasons. The results with HPGen™ were of 17 kg/m2, a record for this grower, substantially higher than the average for the past 5 years of 12 kg/m2. In addition, the grower observed the quality of the fruit improved, and the fruit could remain on the plant longer, allowing for optimization in harvesting depending on market prices.
The improvement in >40% in production is explained by two factors:
· Better irrigation uniformity: After two weeks of installing the HPGen™ all drippers showed a uniform water flow, which allows for an optimal distribution of water and fertilizer throughout the field.
· Increase of soil organic content, which increased by a factor of 10 (from 0.33 to 4 %), which contributed to improving plant nutrition.
Both factors are due to the high oxidizing power of the Peroxide UltraPure™ generated by the HPGen™ system, which oxidizes organic matter in the irrigation system and makes it available to the crop. This results in better health and vigor of the plants, and in an improvement in yields.
About HPNow
HPNow addresses growing global challenges in clean water and sanitation through its range of on-site, autonomous, safe and sustainable hydrogen peroxide generation solutions. Headquartered in Copenhagen, and with representation across Europe, the Americas, and Asia, they address their clients’ water treatment needs in market segments ranging from agriculture and aquaculture, to industrial and drinking water treatment. HPNow is a technology and market leader in on-site generation of hydrogen peroxide and is continuously striving to further advance its technology and products in order to meet growing market needs and rising global demand.
Stay in the loop by following HPNow on LinkedIn and Facebook.
JD’S Plant Factory Sparks Children's Early Interest In Agriculture
JD hosted nearly 100 primary school students and their teachers for a field trip at its hydroponic plant factory in the Tongzhou district of Beijing on March 22
by Ella Kidron
March 31, 2021
JD hosted nearly 100 primary school students and their teachers for a field trip at its hydroponic plant factory in the Tongzhou district of Beijing on Mar. 22. The event was part of a larger program which started last year in which JD offers the plant factory as a high-tech educational facility for elementary and middle school students as well as families to learn hands-on.
JD Plant Factory in the Tongzhou district of Beijing
During the activity, the general manager of the plant factory, Zhongsheng Wu, gave a lecture on basic crop growth knowledge, providing the group with a preliminary understanding of hydroponic planting. Following the lecture and observation, the children got to have a taste test.
As quality and food safety is of utmost importance to JD, every student and teacher donned a white lab coat, shoe covers, masks and head coverings, and stepped into the air shower for a disinfection prior to entering the factory.
Zhongsheng Wu, general manager of JD Plant Factory, teaches students about hydroponic planting
On the weekends, the factory is usually full of parents and their kids. It is a good way for kids to get outside and have much-needed contact with nature. Parents are also delighted by their kids’ newfound love of vegetables. Wu said: “Parents come to us and say, ‘my kids never eat vegetables at home no matter what, but here they are eating veggies like little rabbits!’”
Parents show their children veggies at the plant factory
They often come home with bags of vegetables, and will also adapt to buying them online through JD.com, enhancing omni-channel conversion. Furthermore, parents will often post on their WeChat Moments (similar to a Facebook wall) too, helping raise overall awareness of the plant factory.
A boy excitedly enjoys a salad with veggies from JD Plant Factory
As the younger generation becomes increasingly tech-savvy, there are concerns that fewer people will choose to go into agriculture. According to Statista, the percentage of the workforce in agriculture from 2009 to 2019 has declined from 38.1% to 25.1%. The plant factory visit can help to pique children’s early curiosity. Wu explained: “Children are the foundation of the future of agriculture. Through our programs, they learn that agriculture can be fun, interesting, and high-tech.”
One of the teachers said at the end of the activity, “It was so well-organized. Students not only got to learn and understand the growth of a seed but also have hands-on practice.” Immersion education for kids is much needed and critical to their development. “Apart from ensuring the farm-to-table supply chain, being able to provide this type of education gives the plant factory an even greater purpose,” said Wu.
Built by JD in partnership with Mitsubishi Chemical of Japan, the plant factory gives JD an entry point at the very beginning of the supply chain and creates high-end vegetables using advanced hydroponic technology, artificial LED light source, and Internet of Things technology in a fully-closed environment. Covering 11,040 square meters, it is the largest plant factory with the combination of sunlight and artificial light in China.
(ella@jd.com)
Tags: Social Responsibility
Providing Farming Solutions At Every Customer Level
Currently, the company is running a pilot farm in Japan, in collaboration with Kaneya Co., LTD. Kaneya operates the farm, whereas Own Greens patented growing technology is used
“Since we’ve started the pilot farm in Japan, we’ve had several parties reaching out for large-scale projects throughout the country," says Lennart Bijl, Operation Manager at Own Greens. The Dutch-based company is currently finetuning farming techniques in order to create a concept that can be quickly rolled out throughout Japan, and later on worldwide.
"We’re focusing on promoting our Own Greens brand in the fresh produce market. Whereas we’re also currently expanding partnerships with market players,” Lennart adds.
Japan pilot
Currently, the company is running a pilot farm in Japan, in collaboration with Kaneya Co., LTD. Kaneya operates the farm, whereas Own Greens patented growing technology is used. The facility grows up to 300.000 crops per year, which is supplied to several local supermarkets in the area.
The growing facility in Japan
“Our large-scale solution is designed to produce large quantities of leafy greens and fresh herbs in the most efficient way possible. This unique technology makes full automation possible and ensures an ultra-clean growth chamber to prevent contamination in the system. Key terms in this concept are Safe, Simple and Scalable and multiple elements are patented by Own Greens.” The company provides solutions with a floor space of 1000-5000m2, with a cultivation area that consists of more than 5000m2.
Own Greens' products and services, can be divided into three divisions. Namely, large-scale farming projects, B2B growing chambers (PlantHome Pro) and Own Greens Home, a small grow-kit used by consumers. The Vitro Plus-owned company, works closely with Nijssen, Bever Innovations, KV techniek and Kaneya. These collaborations are focusing on three keystones, namely production, presentation and product.
Lennart Bijl checking the PlantHome Pro produce
Product testing
Own Greens has been piloting its products, at a local supermarket, Albert Heijn. “Initially we started the project to gain more awareness on vertical farming and its benefits, says Lennart. “We used flyers that visitors could take along, and our product packaging has a removable paper wrap around it which explains the production process of each product.”
As the project gained lots of attention from visitors, Own Greens is now supplying its vertically grown basil, mint and lettuce crops to the store. The living herbs and lettuce are sold on bamboo paper pots, which contain water to increase the shelf life. Customers can keep the products in their home outside the fridge for up to a month.
PlantHome indoor garden
The PlantHome can be installed in any space wanted. It’s just a case of plugging in and growing. Both the PlantHome Pro and regular PlantHome home-kit make use of separated containers that contain plugs or pads with seeds. The PlantHome Pro device has multiple layers and can grow up to 30 plants per layer. Whereas it doesn’t include automation and a climate system, the indoor farm is easy to use. The mineral- and plant capsules can easily be applied into the trays so the crops will intake all nutrients needed. Customers now include restaurants, day-care centers, and canteens.
For more information:
Lennart Bijl, manager of operations
Own Greens
lennart@owngreens.com
www.owngreens.com
Publication date: Tue 30 Mar 2021
Author: Rebekka Boekhout
© VerticalFarmDaily.com
Grower Turns To Indoor Saltwater Farming To Grow Sea Beans
Heron grows its sea beans via an indoor saltwater farm using hydroponic technology for a few reasons
Salicornia. Picklegrass. Sea asparagus.
Sea beans are a salty, long, thin vegetable that grow in saltwater.
These are just a few of the monikers Sam Norton has heard in talking to chefs about his new vegetable. However, he prefers to call them sea beans--them being a thin, long asparagus-like vegetable that grow in saltwater. It was a vegetable Norton knew of growing up in Southeastern U.S. and in turn, he studied sea beans and seawater agriculture in grad school at College of Charleston. It was there he won the Department of Agriculture’s inaugural ACRE (Agribusiness Center for Research and Entrepreneurship) startup competition in 2018 and so, Charleston, SC-based Heron Farms was born.
Seawater agriculture
Heron grows its sea beans via an indoor saltwater farm using hydroponic technology for a few reasons. “We found after a few experiments that if we kept growing them outdoors that we would run into the same problem other outdoor growers were running into--land-use constraints, salt management, seasonality, etc,” says Norton. “We decided we could solve those problems by taking them indoors.”
Sea beans are grown using hydroponic technology at an indoor saltwater farm.
Heron’s first harvest was April 14th of 2020--admittedly a challenging time. “We realized on March 10th all the restaurant customers that were going to carry our products were about to shut down,” says Norton. So the company, which was growing indoors in a shipping container farm temporarily on loan via fellow Charleston grower Vertical Roots, pivoted to retail to position its product as a premium vegetable versatile enough to eat raw, boiled, sautéed and many more ways. It’s since moved out of the Vertical Roots facility to launch its own indoor farm where it has been since August of 2020 with 30,000 square feet of saltwater marsh planted.
Retail interest
Heron’s pivot to retail has paid off in an age where home cooking and trying new products are trends that have emerged in the pandemic. Consumers are sharing on Instagram the different ways they’re using sea beans. (Norton notes it’s largely used as a garnish or as a replacement for micro greens.)
Consumers use sea beans in a number of ways, though most often as a garnish or a replacement for micro greens.
Yet, as the vaccines roll out throughout North America, restaurants and other foodservice operations are coming back online, demand could change again for Heron. “We’ve seen demand pick up actually in the past 30 days, especially in the Northeast,” says Norton.
However, that increased demand is in rhythm with Heron Farms’ plan to scale up its indoor production by launching another site in Charleston in the next six months.
For more information:
Sam Norton
Heron Farms
Tel: +1 (847) 224-3242
Sam@heronfarms.com
www.heronfarms.com
31 Mar 2021
Author: Astrid Van Den Broek
© FreshPlaza.com
Three Ways Singapore Is Designing Urban Farms To Create Food Security
Securing food during a crisis and preserving land for a livable climate is changing the focus of farming from rural areas to cities
FARMING IN THE CITY
Urban farming in Singapore
How Singapore has stimulated innovation in urban farming on a massive scale
By Clarisa Diaz | Things Reporter
March 31, 2021
Securing food during a crisis and preserving land for a livable climate is changing the focus of farming from rural areas to cities. At the forefront of this shift is Singapore, a city-sized country that aims to produce 30% of its own food by 2030. But with 90% of Singapore’s food coming from abroad, the challenge is a tall order. The plan calls for everyone in the city to grow what they can, with government grants going to those who can use technology to yield greater amounts.
“This target took into consideration the land available for agri-food production and the potential advances in technologies and innovation,” said Goh Wee Hou, the director of the Food Supply Strategies Department at the Singapore Food Agency. “Local food production currently accounts for less than 10% of our nutritional needs.”
The food items with potential for increased domestic production include vegetables, eggs, and fish. According to the Singapore Food Agency, these three types of goods are commonly consumed but are perishable and more susceptible to supply disruptions. Alternative proteins such as plant-based and lab-grown meats could also contribute to the “30 by 30” goal. In 2020, there were 238 licensed farms in Singapore.
Only 1% of Singapore’s land is being used for conventional farming. That created the constraint of growing more with less. The government has put its hopes in technology, stating that multi-story LED vegetable farms and recirculating aquaculture systems can produce 10 to 15 times more vegetables and fish than conventional farms.
Since 2017, land has been leased in two districts on the edge of the city—Lim Chu Kang and Sungei Tengah—to large-scale commercial farm projects. While the optimization of these farms to produce at maximum capacity is being determined, the idea of growing food in the more urban spaces of Singapore has emerged: from carpark rooftops to reused outdoor spaces and retrofitted building interiors.
Urban farms in Singapore
Urban farms using hydroponics on parking structure roofs
Citiponics is one of Singapore’s first rooftop farms. The hydroponic farm is on top of a carpark, a structure that services almost every neighborhood in Singapore.
Read more: How a parking lot roof was turned into an urban farm in Singapore
Installing urban farms into existing buildings
Sustenir Agriculture has created an indoor vertical farm that can retrofit into existing buildings (including office buildings). The company grows foods that can’t be produced locally, displacing imports and cutting carbon emissions.
Read more: The indoor urban farm start up that’s undercutting importers by 30%
Building a better greenhouse for urban farms in tropical climates
Natsuki’s Garden is a greenhouse in the center of the city, occupying reused space in a former schoolyard. The greenhouse is custom designed for the tropical climate to allow for better air circulation. Yielding 60-80 kg of food per square meter, the greenhouse caters to a small local market.
Read more: How a Singaporean farmer is building a better greenhouse for tropical urban farming
High production urban farms still need to be sustainable
Open to applications later this year, a new $60 million government fund will provide funding for more agritech businesses. According to the Singapore Food Agency, the fund will assist with start-up costs catering to large-scale commercial farms, no matter the location.
But as Singapore tries to advance, there are some left behind. The traditional farms that do exist in Singapore are being displaced, their knowledge no longer valued because they are not seen as hi-tech, according to Lionel Wong, the founding director at Upgrown Farming Company, a consultancy that helps equip new farming business owners across Singapore. “While we are trying to increase production, the net result could actually be reduced production because the traditional growers are being removed from the equation in the long term.”
In the long-run, high production of food within Singapore will need a sustainable market of consumers, to Wong that market isn’t completely clear at the moment. “‘30 by 30’ is really just a vision. The Food Agency deserves a lot of credit in terms of what they’re trying to push, but there’s a lot of room for improvement.” Wong continued, “productivity doesn’t necessarily equate to sustainability or profitability.”
Whether Singapore is able to produce its own food sustainably for the long-run remains to be seen. But the endeavor is certainly an exciting moment for entrepreneurs pushing the boundaries of what farming and cities can be.
Lead photo: COURTESY CITIPONICS | Singapore aims to produce 30% of its food by 2030.