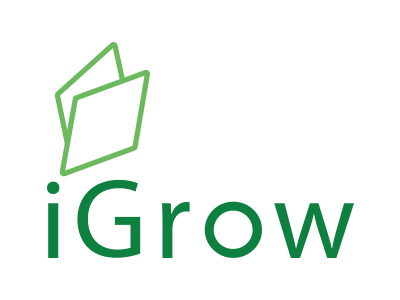
Welcome to iGrow News, Your Source for the World of Indoor Vertical Farming
BrightFarms Launches Multimillion-Dollar R&D Hub in Greater Cincinnati
BrightFarms, a New York-based grower of indoor leafy greens since 2013, is forming BrightLabs, a new innovation and research hub, at its Wilmington greenhouse. BrightLabs, overall, will represent a tenfold increase in the company’s research capabilities, while increasing profitability and delivering new product innovations.
By Liz Engel - Staff reporter
June 24, 2021
An indoor farming company is investing millions in Ohio with the debut of a new research and development hub.
BrightFarms, a New York-based grower of indoor leafy greens since 2013, is forming BrightLabs, a new innovation and research hub, at its Wilmington greenhouse. BrightLabs, overall, will represent a tenfold increase in the company’s research capabilities, while increasing profitability and delivering new product innovations.
Steve Platt is the CEO of BrightFarms. (Jenn Erickson)
CEO Steve Platt declined to disclose the exact investment but told me it’s in the multimillions. The project is being launched as part of the company’s $100 million Series E funding round in October led by media conglomerate Cox Enterprises.
“BrightFarms as a company has been growing very consistently, and the indoor farming industry is at an inflection point,” Platt said. “We’ve perfected how we grow – among competitors, we’ve developed the most profitable model for the production of indoor leafy greens – but now’s the time to invest behind R&D to secure an advantage for the future. It’s essential to stay ahead of the curve.”
Like others in the indoor farming space, BrightFarms lauds the fact that its lettuce is healthier, tastier, looks better, is more nutritious, and, particularly for customers in Ohio, fresher than field-grown produce hauled in from states like California and Arizona. Today the company’s five greenhouses in Ohio, Virginia, Illinois, Pennsylvania produce 9 million pounds of produce each year.
But unlike several outfits, particularly vertical farms that use purple-hued LED lighting, BrightFarms leverages natural sunshine. Its souped up, high-tech greenhouses grow spinach, romaine, arugula and more using a hydroponic system, or water instead of soil.
Wilmington, which celebrated its first harvest in 2018, isn’t the company’s largest greenhouse in terms of size or production, but Platt said it made a good host for the innovation hub because of its centralized location. It’s close to customers and easily accessible from its other farms. He also credited the workforce and level of academic talent available from universities nearby.
BrightFarms celebrated its first harvest in Wilmington in 2018. BrightLabs is investing millions to build out an innovation and research hub at the site. (Brian Mollenkopf)
Phase one for BrightLabs includes a new, approximately 1,350 square foot lab that has been built at the Wilmington greenhouse site. BrightFarms will also dedicate space on the farm for the BrightLabs team to work.
Platt said BrightLabs will focus on three key areas:
Biotech. BrightFarms wants to study the environments in which plants grow to increase yield, flavor, and texture.
Agtech. BrightOS, the company’s proprietary AI software system, acts as the company’s central nervous system, Platt said, collecting millions of data points from its fives farms to streamline operations. How can the company improve that technology?
Product innovation. BrightFarms recently launched NutriGreens, a new lettuce packed with antioxidants – double the amount, Platt said, found in a serving of blueberries. BrightFarms wants more advances like that.
BrightLabs itself will be led by Matt Lingard, a former Bayer plant scientist and Ph.D. with over 15 years of experience, who joined BrightFarms in May as its VP of agriculture and science. Platt said the BrightLabs team will include four employees to start.
“We’re the leading grower of indoor spinach – in the U.S. we grow 90% of the indoor spinach that’s sold – but we want to double our production on that. How do we come out with new types of spinach that can grow even better in a hydroponic system?” he said.
“We’re taking on a massive industry and a complicated, broken system – where greens are grown all in one location, shipped thousands of miles across the country, generally with pesticide reside, there’s a food-borne illness, and the product isn’t that good,” Platt added. “We have a simpler system and a better product, but we need to deliver that at a price point and at a volume that competes with what’s coming out of California. If we’re trying to unseat this big gorilla, we can’t be this niche that’s only affordable to people who drive Teslas.”
Overall, there’s billions being invested in the industry. New York City-based Bowery Farming, in late May, announced a $300 million funding round with a $2.3 billion valuation. Kentucky-based AppHarvest merged with a special purpose acquisition company in February, an IPO approach that’s gaining ground in 2021, and is now worth $1.5 billion.
BrightFarms, with its Series E, has raised more than $200 million in total. In addition to launching BrightLabs, it plans to use the funds to expand its network of regional indoor farms – new farms are currently under development in Massachusetts and Texas – and grow its retail footprint. Locally, BrightFarms is available at Sam’s Club, Walmart and Pipkin Produce as well as Food Lion and Kroger in other markets.
The company said by the end of 2021 its leafy greens will be available at over 3,500 stores.
“It’s amazing. Even when I joined the company two years ago, we were convincing people this was the future. Now customers are coming to us saying, ‘We want to replace field grown with indoor-grown,’” he said. “We think the future is here.”
Lead photo: BrightFarms grows leafy greens like spinach, romaine, and arugula in high-tech, computer-controlled greenhouses.
Highlighting The Potential of Dutch Horticulture In Vertical Farming
Indoor Farming Holland aims to bring companies together to see where their knowledge can be developed and applied in the vertical farming space. “We’re focusing on the combination of technical solutions with plant science, where Holland has a great proposition.”
“The Dutch are falling behind when it comes to vertical farming,” says Judith van Heck, Community Builder at Indoor Farming Nederland. “As we’re so tremendously good at greenhouse growing there is relatively less interest in building vertical farms in the Netherlands. In comparison to countries such as the US, this has resulted in lower investments. That’s why we started the initiative Indoor Farming Nederland. We want to help the Dutch horticulture sector to develop the potentially very interesting sector, and we also want to highlight the international potential of Dutch horticulture in vertical farming.”
Indoor Farming Holland aims to bring companies together to see where their knowledge can be developed and applied in the vertical farming space. “We’re focusing on the combination of technical solutions with plant science, where Holland has a great proposition. We, therefore, believe that we can obtain optimal results from vertical farms and take the lead on that,” Judith notes.
“Due to many things happening around vertical farming and innovative solutions that are brought to market, we’ve created a government-backed organization to stimulate indoor farming amongst Dutch horticultural companies,” says Gus van der Feltz, project leader for the Fieldlab Vertical Farming. In the Fieldlab Vertical Farming, an important collaboration is established between South Holland knowledge institutions and companies that are engaged in the production of vertically grown products, the sale of vertically grown products, and suppliers of technologies for vertical farms.
Gus van der Feltz and Judith van Heck
Increasing awareness
The Fieldlab is supported by the European Fund for Regional Development of the European Union and the Province of South Holland. Now, the organization’s activities consist of four different ‘packages’ which they’d like to elaborate on throughout the Dutch horticulture industry. Vertical Farming Zuid-Holland received a subsidy to develop a foundation for potential market entrants that consists of four different packages.
The Fieldlab, working together with Indoor Farming Nederland, wants to increase awareness of the added value of vertical farming. Firstly, by using market research to understand consumers, growers, retailers, and the supply chain’s perspective on vertical farming. “Through market research, we want to highlight the benefits and processes that could be improved,” says Gus. Secondly, the organization will do research and testing to generate knowledge on vertical farming and recipes through development and innovations by Dutch horticulture companies.
Thirdly, “we want to educate and train people,” says Gus. “We’re working on developing training programs specifically focusing on vertical farming. From the technical side of things to running a farm and selling your produce successfully.” Last but not least, a sector-related platform is to be constructed to create a long-term and sustainable network the industry can fall back to. In collaboration with Vertical Farming Fieldlab, for the industry to further develop knowledge in Dutch horticulture, the organization consists of multiple companies, such as Own Greens, Delphy, Signify, WUR Bleiswijk, Vertify, Logiqs, Proeftuin Westland, InHolland, WUR Wageningen, Future Crops (Poeldijk).
Judith explains that the community works with jointly formulated ambitions. “We help this cluster of companies to obtain as much knowledge as needed. We stimulate them to co-create on several challenges. One of the ambitions is to communicate the potential of the cluster and indoor farming products to various target groups. Amongst other things, we are creating a white paper regarding the general statements about vertical farming and the complex reality of it.” Next to that, the organization is exploring the feasibility of a collective market intelligence tool to see where vertical farming can add value internationally. However, the community aims to not only help Dutch entrepreneurs but the collective market. One of the ambitions, for instance, is to communicate the potential of the cluster to various target groups within, but especially also outside, the Netherlands.
Amongst other things, Indoor Farming Nederland will create a whitepaper that states all facts concerning vertical farming. Next to that, the organization is exploring the feasibility of a collective market intelligence tool to see where vertical farming can add value internationally. They’re doing so by looking at climate, population density, food patterns, availability of water, and energy. Also by analyzing where the most potential is for vertical farming, or hybrid solutions even, in combination with greenhouses.
For more information:
Indoor Farming Nederland
Gus van der Feltz, Project leader
gus@feltzwerk.nl
Judith van Heck, Community Builder
judith@imagro.nl
Publication date: Wed 16 Jun 2021
Author: Rebekka Boekhout
© HortiDaily.com
Singapore: Mega-Farm, Research Center To Open By December 2021
&ever is currently building a mega-farm in Singapore with support from the Singapore Food Agency, SFA, and the Economic Development Board, EDB, and will be launched by the end of 2021. The mega-farm will be 15m high and have an annual production capacity of up to 500,000 kg of leafy greens.
&ever
“We’re really happy to have launched in Munich and consumers really like our harvest-on-demand concept,” says Franz Drack, Chief Marketing Officer at &ever. "We just need to see how to increase the accessibility of our solutions. I’d love to see 200 vertical farms in Europe with this technology in the next five years."
Although it all started in Hamburg, &ever is currently headquartered in Munich which is also where the grow tower showroom is located. In 2020, &ever opened its first commercial farm in Kuwait, spanning 3,400 m2 and with a daily output capacity of 550 kg. The farm provides its leafy greens to Kuwaiti restaurants and retailers. The company also recently launched a grow tower in an EDEKA Stadler+Honner “Die Frisch-Nachbarn” supermarket in Unterfôhring near Munich.
Mega-farm and research center
&ever is currently building a mega-farm in Singapore with support from the Singapore Food Agency, SFA, and the Economic Development Board, EDB, and will be launched by the end of 2021. The mega-farm will be 15m high and have an annual production capacity of up to 500,000 kg of leafy greens.
In addition to the mega-farm, &ever will be establishing Singapore as its global R&D center to accelerate knowledge development and transfer to the mega-farm. The R&D center will focus on improving energy use efficiency through optimized lighting strategies and improving crop quality by evaluating different seed and substrate combinations. Moreover, &ever will be working to develop non-invasive crop monitoring processes through vision systems.
“We’re getting tremendous support from our local partners EDB, SFA and A*Star; everyone is keen to get this farm online. This farm is what we are most excited about this year,” Franz notes. To better address consumer demand, &ever conducted market research in Singapore by speaking with potential consumers and foodservice providers. This research has allowed &ever to explore the balance between western and eastern leafy green species to be grown in the mega-farm.
“Our team under the lead of our country manager, Kerstin Köhler, have worked with food service providers who are very good at telling us what products are needed and wanted. Some products are very interesting for certain segments of the value chain, so we try to talk to a lot of different people,” says Franz.
&ever is continuing to focus on leafy greens, microgreens and herbs for the time being. While there is a lot of interest in fruits (like strawberries), Franz explains that the company is focused on keeping its product range simple to perfect the growing process.
&ever's growing tower
Rebranding efforts
In recent months, the vertical farming industry has seen major players taking a new approach to product branding by using brightly colored packaging. &ever is also focused on bright, enticing packaging designed to represent the company’s values and production process.
“We will start using colors that represent what we’re actually doing. Yellow for the light, blue for the water and green for our greens. It allows the brand to stand out and visually signals to consumers that things are changing. This shows that we are a new type of agricultural company. Stay tuned for that in the second half of 2021.” explains Franz.
Franz also notes that &ever’s products are also sold living, whereas many indoor farms sell cut greens, packaged in clamshells or other packaging materials. Moreover, &ever is also looking into direct-to-consumer sales of leafy greens.
In building its mega-farm, putting its products on European shelves and rebranding, &ever is eager to continue growing by getting consumers excited and developing more farm projects across the world.
&ever is a German agtech company offering three growing solutions, each addressing a different level of production. The &ever grow box is a small-scale system that allows growers to produce 15-30 kg of leafy greens per day in a small footprint. The company’s medium-sized solution is the &ever grow tower which is a small room containing a circular cultivation module.
Young plants are first transplanted in the inner circle and are gradually pushed further to the outer circles as new plants are introduced to the system. In pushing the plants further, the older plants receive more available space to continue growing without crowding neighboring plants. The grow towers provide a customizable output of 20-50 kg of leafy greens per day. Finally, &ever also develops large-scaled production system which it calls mega-farms.
For more information:
Franz Drack, CMO
&ever
local@andever.de
www.and-ever.com
Publication date: Tue 8 Jun 2021
Author: Rebekka Boekhout
© VerticalFarmDaily.com
New Vertical Farm In Oshawa Will Harvest Fresh Greens Year-Round
Founder Derrik Stevenson started the business as a way to follow his passions after being laid off from an office job as a result of the pandemic.
May 22, 2021
A new vertical farm is open in Oshawa with plans to harvest local greens year-round.
Mighty Harvest Produce, located at 871 Wilson Rd. S., is growing leafy greens and herbs hydroponically, which means without the use of soil.
Founder Derrik Stevenson started the business as a way to follow his passions after being laid off from an office job as a result of the pandemic.
“I decided, I’m not going to look for a job. I’m going to create my own job,” says Stevenson, who is vegan and has an interest in sustainability and fresh food.
Right now you can find greens like kale and salad blends growing at Mighty Harvest as well as herbs such as parsley, marjoram, and anise basil.
Stevenson says growing greens indoors has benefits for the environment as well as the people who eat them.
“The ultra freshness is what sets us apart from the grocery store,” he says, explaining how greens sold in Ontario often make a long journey from California or Arizona. “I can harvest on a Wednesday night and be selling the product on Thursday.”
Vertical farming uses 90 per cent less water than conventional agriculture and Mighty Harvest does not use pesticides or herbicides.
Stevenson says customers may be surprised to learn Mighty Harvest Greens are not certified organic — it’s because Canadian regulations don’t allow certification for produce that’s not grown in soil.
Mighty Harvest is open Thursday and Friday from 1 to 6 p.m. and Saturday from 9 a.m. to 2 p.m. and can be found at the Whitby's Farmers Market on Wednesdays.
Vertical Farming Startup Oishii Raises $50m In Series A Funding
“We aim to be the largest strawberry producer in the world, and this capital allows us to bring the best-tasting, healthiest berry to everyone.”
By Sian Yates
03/11/2021
Oishii, a vertical farming startup based in New Jersey, has raised $50 million during a Series A funding round led by Sparx Group’s Mirai Creation Fund II.
The funds will enable Oishii to open vertical strawberry farms in new markets, expand its flagship farm outside of Manhattan, and accelerate its investment in R&D.
“Our mission is to change the way we grow food. We set out to deliver exceptionally delicious and sustainable produce,” said Oishii CEO Hiroki Koga. “We started with the strawberry – a fruit that routinely tops the dirty dozen of most pesticide-riddled crops – as it has long been considered the ‘holy grail’ of vertical farming.”
“We aim to be the largest strawberry producer in the world, and this capital allows us to bring the best-tasting, healthiest berry to everyone. From there, we’ll quickly expand into new fruits and produce,” he added.
Oishii is already known for its innovative farming techniques that have enabled the company to “perfect the strawberry,” while its proprietary and first-of-its-kind pollination method is conducted naturally with bees.
The company’s vertical farms feature zero pesticides and produce ripe fruit all year round, using less water and land than traditional agricultural methods.
“Oishii is the farm of the future,” said Sparx Group president and Group CEO Shuhei Abe. “The cultivation and pollination techniques the company has developed set them well apart from the industry, positioning Oishii to quickly revolutionise agriculture as we know it.”
The company has raised a total of $55 million since its founding in 2016.
Bowery Farming Lettuce Now In 275 Acme, Safeway Stores
The company now serves almost 800 grocery stores and major e-commerce platforms after this partnership with Albertsons Cos. Inc.
By AMY SOWDER
03/23/2021
New York City-based vertical grower Bowery Farming has placed its products in 275 Safeway and Acme stores in the Northeast and Mid-Atlantic.
The company now serves almost 800 grocery stores and major e-commerce platforms after this partnership with Albertsons Cos. Inc., which oversees the Acme and Safeway banners, according to a news release.
“Whether our customers shop with us in store or through our websites and apps, they expect to find fresh and sustainable produce for delicious meals at home,” Ricardo Dimarzio, produce sales manager of Albertsons’ Mid-Atlantic division, said in the release. “We’re proud to offer Bowery Farming’s innovative and sustainable produce to help meet customer demand for high-quality local indoor-grown greens and herbs.”
*700% growth is only for brick-and-mortar store sales
Bowery builds high-tech indoor farms close to the cities it serves. BoweryOS, its proprietary operating system, uses sensors, vision systems, machine learning and automation to monitor and control the variables in crop growth.
Every new farm the company builds benefits from the collective knowledge of the operating system, improving the entire network of farms.
Bowery’s greens and herbs grow in completely controlled environments year-round, independent of weather and seasonality.
“We’re proud to partner with Albertsons Cos. to bring millions of shoppers our local, wildly delicious protected produce and meet unprecedented demand for our growing category, which we believe is the next frontier of agriculture,” Katie Seawell, Bowery’s chief commercial officer, said in the release.
Five of Bowery’s most popular stock-keeping units are now available in 164 Acme stores (Pennsylvania, New Jersey, New York, Connecticut, Delaware and Maryland) and 111 Safeway stores (Maryland, Virginia and Washington, D.C.).
The initial five products are baby butter lettuce, crispy leaf, spring blend, kale blend and basil.
Bowery has seen nearly 700% growth in sales since January 2020 with brick-and-mortar grocery retailers, and more than quadrupled its sales with e-commerce platforms, including Amazon, according to the release.
To sustain this growth and meet demand for its produce, Bowery is building its largest and most technologically advanced farm yet in Bethlehem, Pa., which will further automate the growing process from seed to store and expand its reach throughout the East Coast.
The company also has two commercial farms in Kearny, N.J., and Nottingham, Md.
Local Vertical Farm Startup Joins Growing Global Market
Ortaliza Urban Farms is a dream that has been sprouting for some time now.
What if there was a more sustainable way to provide fresh, truly local greens to our communities? And what if there was a way to do it while bringing diverse flavors to the table year-round?
It sounds like an ambitious goal. But it is one that Carina Biacchi and her partner, Alvaro Fernandes, are set to meet.
Ortaliza Urban Farms is a dream that has been sprouting for some time now.
Carina Biacchi is no stranger to business. With a bachelor’s and postgrads in business administration, she has worked in several different sectors, from NGOs to massive corporations. “I’ve mostly worked in sales and marketing” Carina states. “And I have entrepreneurship in my DNA. My parents were entrepreneurs long before I was born.”
And as formidable as Carina is, she is among good company. Alvaro Fernandes, her partner, is an Agronomist Engineer. “He’s a passionate specialist in controlled environment agriculture” Carina explains.
When the two met they quickly started dreaming about their own indoor farm. Years passed, and the two immigrated to Canada and started a family. But those entrepreneurial sparks continued to fly.
“It took us a while to build our lives in Canada,” Carina states. “But we continued to research the idea we had. We kept visiting other businesses in the industry and we even traveled to New York and other areas to see what they had to offer in terms of vertical farms.”
But what is vertical farming? Vertical farming is a growing worldwide phenomenon set to add significant value to the food system. Food security and sustainability continue to be some of the top concerns for city planners, and venture capital firms are investing big into vertical farm operations.
And what is an urban farm? Simply put, urban farming is growing food in urban areas. “We’re located right on Main Street,” Carina states. “In a commercial zoning area. That is pretty unique by itself, and the town of Kingsville has proven to be the perfect partner to help us launch our dream.”
A hyper-local farm-to-plate experience
And while Ortaliza is not the first micro green seller in the region, they are the first to create a storefront, creating an exciting farm-to-plate experience, loaded with flavor and freshness.
“We are truly local!” Carina stresses. “Sometimes, when you see that something is “local” on your grocery shelves, it’s actually from another part of the Province. That might be fine for large vegetables, but greens are special. Think of all the nutrients you would get from a full vegetable but concentrated to deliver all that deliciousness in every single bite. Microgreens require just-picked freshness, so we are super, hyper-local. We’re only growing and selling here in our County.”
This business model, Carina explains, also allows them to reduce food mileage and consequently, food waste. “Leafy greens in Canada can sometimes travel thousands of miles before reaching their destination” Carina reports. “And it can take up to two weeks for the produce to get there. We have a commitment to sustainability, and we will always be local, no matter where we spread our roots to in the future.”
One of Ortaliza’s business Advisors, Adam Castle of WEtech Alliance says the launch of this business in Kingsville represents a unique opportunity for the Startup. “Here we are in the very heart of greenhouse agriculture, not just for Canada but seconded only to Holland from a global perspective,” says Castle. “So you’re planting yourself in a community that lives and breathes agriculture, who knows the value of being able to see where your food comes from and how it’s grown, at a time when the average consumer is more engaged than ever in providing the freshest, most sustainably grown food they can for themselves and their family. I applaud Kingsville for making room at their table for new kinds of agriculture, and being a business-friendly partner that our clients can count on.
“…it certainly fits hand-in-hand with the innovation and the diversification that we’re trying to identify with.”
One enthusiastic supporter of this innovative new business is Nelson Santos, the Mayor of Kingsville and the Deputy Warden of Essex.
“This isn’t your typical business, but it certainly fits in with the entrepreneurial spirit that we have in our community,” Nelson explains. “And it certainly fits hand-in-hand with the innovation and the diversification that we’re trying to identify with. They are touching on all the different aspects of what the community is looking for. Their business is one that is certainly going to turn quite a few heads. It’s very exciting, both in regards to the food aspect and the extension of agriculture.”
Ortaliza is now taking pre-orders for their home delivery service at www.Ortaliza.ca, which promises to deliver a lot more than leafy goodness.
“We want to be more than a farm-to-table service,” says Carina. “We want our customers to think of us as their weekly dose of living, natural vitamins that add easy nutrition to just about every recipe they can think of!”
To learn more and become a friend of the farm, head to www.ortaliza.ca or find them on social media at @OrtalizaFarms
How Vertical Farms Are Revolutionizing Agribusiness
What is vertical farming and why does it matter?
William Ramstein ・ 1 March 2021 ・ Vertical Farming
Urban planners are tasked with answering some pressing inquiries: how can farming be brought closer to consumers; is digital agriculture an essential ingredient for making cities smarter; and can vertical farming improve socio-economic disparities?
Key Takeaways:
Vertical farming uses LED, Robotics and AI to bring vegetables closer to city dwellers.
The total addressable market for vertical farming is estimated at around $700 billion.
Spread, a Japanese vertical farm is profitable but most firms fail.
Vertical farming is a great way to produce controlled supplies of a customized plant.
Vertical farming struggles with electricity costs despite reducing carbon emissions.
What is vertical farming and why does it matter?
The bedrock characteristic of cryptocurrency technology is called decentralization, a sovereign and flexible organizational system led by a commune, and today other industries like farming are catching the bug. Farming needs to change its practices in order to meet ecological objectives set up by governments and decentralization could open the door to increasing food access and reducing carbon emissions from food transportation. Smart decentralized vertical farming implies using technology like digital platforms, robotics and artificial intelligence to bring food closer to the growing demand seen in cities.
Despite the difficulty of competing against the cost structure of traditional farming, vertical farming offers numerous advantages. It grants more yield per square meter and reduces waste in both carbon and water usage. The production of vegetables is made in large and often times un-used warehouses close to city centers thus cutting transportation costs and middlemen expenses. The supply is more easily controlled, protected, and priced regardless of global weather and plants are customized to local consumer preferences. Consumers are already paying a premium on farmer’s market products, so why not vertical farm products too?
Cases of vertical farming: Nigeria is one of the most promising African nations because of its age pyramid. But with a large young population comes questions around food and water access and today, more than 170 million Nigerians need prolonged and sustainable access to these resources. Nigeria currently imports $3.5 billion worth of food products while exporting only 1/7 of that figure. Fresh Direct is Nigeria’s first Hydroponics Company (growing crops without standard soil) that combines vertical farming to its business model to reduce the distance between cities and rural farming regions.
The firm is able to produce seven to 10 times the yields because of its stackable shipping containers, which use technologies such as drip irrigation, and cold storage. Direct Farming operates with a community mindset, with the goal to inspire more young farmers to set up shop in urban centers and become urban farmers. The company also trains and finances low-skilled workers into urban farmers and increases economic productivity in unemployed youth groups.
In Japan, a company called Spread is one of the world’s most sophisticated examples of vertical farming. Their factory mainly produces lettuce. Large robotic arms transplant lettuce seedlings into pots where they are left to grow under LED lights. Believe it or not, but the factory can produce 30,000 lettuce heads a day. CEO Shinji Inada boasts of being the only large-scale vertical farm that is profitable and hopes that more widespread adoption continues growing.
However, companies like Spread and A-Plus (another similar farm in Fukushima) struggle to lower unit economics because of their low-scale operations, and they find it hard to penetrate the traditional downstream sellers. When producing high-priced lettuce by the tonne, trucking goods to the local wholesaler does not work partly because vertical farming offers customized products for specific local needs, not necessarily for broad demand. These players have thus geared their focus towards international buyers like UAE to export their goods.
Is vertical farming there yet?
Most vertical farms have failed because of the high initial costs and high operational expenses of running robotic equipment. While sunlight is free, the energy cost of running LEDs is not. The solution could be to install renewable energies like solar panels and wind turbines. However, the fixed cost of that installation would inevitably factor into the end-product, or at least on the balance sheet as a liability assuming they keep prices reasonable for consumers.
While Mr. Inada can rightly boast of turning profits, most firms toss lettuce at a loss. The industry should see more growth ahead, however, with research group IDTechEx forecasting that annual sales of $700 million could more than double to $1.5 billion in 2030. There remain technological challenges though. While many competitors boast of successfully leveraging AI and robotics and filtration, new entrants have seen problems with watering automation systems, mold, and infestations (most players do not use pesticides).
Some analysts suggest that while the excitement around vertical farms makes sense, the farming style might just end up becoming just another way of farming amongst greenhouse and open sky farms. More specifically, vertical farming will focus on high-margin crops rather than commodities like bulk grains.
While the challenges of vertical farming are clear, every country has different needs and constraints. There is a large interest from smaller island countries like Singapore or Iceland, rich economies, and countries that have a higher propensity to import due to less arable lands. Britain is a good example of a country that meets the criteria and in the context of Brexit, it makes all the more sense because of import costs and independence constraints. A potential labor crisis could soon loom too assuming seasonal workers are denied entry into the country. Vertical farms only require one-third of the manpower to run and could therefore alleviate the industry.
The market opportunity…According to research by Barclays Investment Bank, the market opportunity for vertical farms is large. Analysts estimate the size of the global fruit and vegetable market to be $1.2 trillion and the total addressable market for vertical farms to be $700 billion. The purchased energy use to produce 1kg of lettuce is 247-kilowatt hours far exceeding Netherland greenhouses’ 70-kilowatt hours consumption. With retailers being asked to meet more carbon-neutral objectives, some vertical farms believe they will be able to overcome their expense through increased demand and scale.
The pandemic has imposed many supply chains disruptions and labor shortages threatening food security in regions around the world relying heavily on imports. Vertical farming is recognized lately and since 2014, has seen a flow of funds equal to $1.8 billion according to data group Dealroom. SoftBank fundraised $140 million into Plenty, a start-up, and countries like Abu Dhabi want to build farms in deserts.
Some of the top players in the global farming market include Vertical Farm Systems (Australia), American Hydroponics (US), Agrilution (Germany), Green Sense Farms (US), Everlight Electronics (Taiwan), Koninklijke Philips (Netherlands), Sky Greens (Singapore), Illumitex (US), Urban Crop (Belgium), Aerofarms (US) and InFarm (Germany).
A Fully Automated Three-Dimensional Vertical Farm Comes Into Operation
Eponic Agriculture Co. Ltd is a supplier of indoor farming equipment. Alice, the company's director, introduced the recently fully automated production system of a stereochemical vertical farm
Eponic Agriculture Co. Ltd is a supplier of indoor farming equipment. Alice, the company's director, introduced the recently fully automated production system of a stereochemical vertical farm.
"The current three-dimensional indoor farms on the market are based on semi-automated workflow, with some links requiring additional equipment configuration and no continuity in the whole planting system. In order to solve this problem, we developed and designed a complete automated planting system, including the processes from sowing to planting, full-spectrum planting light control, fertilization, harvesting, and cleaning. Which are all done by automated equipment. Whereas all procedures can be controlled by intelligent software with real-time monitoring, data collection, and many other functions."
Benefits of an automated farm
When talking about the advantages of the automated equipment, Alice said, "Take our recently built 20-layer vertical farm as an example. First of all, the mechanical sowing time is 10 times-30 times faster than manual sowing. And on top of that, the use of automated equipment can realize precise planting and efficient communication of multi-layer planting surfaces. The 20-layer vegetable trays are automatically transferred to the ground for uniform watering, harvesting, and cleaning. This greatly improves productivity.
Secondly, the use of lift trucks is required when handling high-level crops. There are certain safety hazards in using lift trucks in a small space. While operating the automated equipment, only a tablet computer is needed to control the whole planting process, which is much safer and more convenient."
Although automated vertical farm systems have many advantages, their application in China is not yet popular. "In terms of production design, we have gone through countless experiments to design the most suitable software program. As well as hardware equipment for practical planting applications. Luckily after a long period of research, we finally chose the most cost-effective and suitable materials. The R&D investment is large and time-consuming.”
From a cost point of view, according to Alice, a fully automatic system is 2-3 times higher in costs than the semi-automatic system which is currently used more often. Most traditional agricultural companies find it difficult to accept such high initial costs. Thirdly, the automated system requires high technical requirements for farm managers. Managers need to have an understanding of both planting technology and software. Alice adds: “It is for these three reasons that the application of fully automated stereoscopic systems is not very common in China and other countries."
Automated planting
"Although the application is not yet widespread, I think fully automated stereoscopic planting is a trend. Urbanization has led to a reduction in arable land and soil pollution has triggered problems with pests and pesticide residues in fruits and vegetables, and the development of three-dimensional agriculture is the only way to maximize and optimize output in a limited area. Currently, stereoscopic planting plants still require a lot of manual labor to operate. As labor costs rise and planting techniques require more precision, the use of automated equipment will be a future trend," Alice notes.
"Automated systems are a trend, not only in China but also globally. Urbanization has been moving forward, in the face of soil pollution, pesticides and pests, etc. The planting area is gradually reduced and three-dimensional agriculture must be developed in order to quantify planting. Three-dimensional agriculture can be located near the city, and reduce the transport distance, people can eat the freshest vegetables, to achieve local supply. Therefore it is necessary to promote automated, intelligent planting systems in order to achieve efficient planting and sustainable development." Alice said.
Industry experience
Eponic Agriculture Co. Ltd's head office, Dahua Intelligent Electronics, has a twenty-five-year history division. The team has been focusing on the development and production of intelligent control systems and industrial lighting. Alice said that based on years of technical foundation, we developed full-spectrum LED planting lights which have been approved and applied by the USDA. Over the years, we have received technical support and affirmation from several agricultural doctors from Europe and the United States, focusing on the development and production of automated stereoscopic planting equipment.
According to Alice, the company has laboratories and showrooms in the US, Australia and Africa. This year, the company is planning on opening new showrooms and laboratories in Europe. “We are expanding our global reach and continue to optimize our growing systems to be a better supplier of fully automated growing equipment."
For more information:
Eponic Agriculture Co. Ltd
Alice Ou, Director
aliceou@eponicagriculture.com
www.eponicagriculture.com
Author: Rebekka Boekhout
© VerticalFarmDaily.com
Vertical Farms Nailed Tiny Salads. Now They Need To Feed The World
Vertical farming is finally growing up. But can it move from salad garnishes for the wealthy to sustainable produce for the masses?
Gartenfeld Island, in Berlin’s western suburb of Spandau, was once the bellows of Germany’s industrial revolution. It hosted Europe’s first high-rise factory and, until World War II, helped make Berlin, behind London and New York, the third-largest city on Earth.
Today’s Berlin is still a shell of its former self (there are over a hundred cities more populous), and the browbeaten brick buildings that now occupy Gartenfeld Island offer little in the way of grandeur. Flapping in the gloom of a grey November morning in 2020 is a sign which reads, in German, “The Last Days of Humanity”.
Yet inside one of these buildings is a company perched at agriculture’s avant-garde, part of the startup scene dragging Berlin back to its pioneering roots. In under eight years, Infarm has become a leader in vertical farming, an industry proponents say could help feed the world and address some of the environmental issues associated with traditional agriculture. Its staff wear not the plaid or twill of the field but the black, baggy uniform of the city’s hipsters.
Infarm has shipped over a thousand of its “farms” to shops and chefs across Europe (and a few in the US). These units, which look like jumbo vending machines, grow fresh greens and herbs in rows of trays fed by nutrient-rich water and lit by banks of tiny LEDs, each of which is more than ten times brighter than the regular bulb you’d find in your dining room. Shoppers pick the plants straight from the shelf where they’re growing.
Infarm crop science director, Pavlos Kalaitzoglou, in his Berlin lab
Credit Ériver Hijano
Gartenfeld Island, however, is home to something more spectacular. Here, in a former Siemens washing machine factory, stand four white, 18-metre-high “grow chambers”, controlled by software and served by robots. These are the company’s next generation of vertical farms: fully-automated, modular high-rises it hopes will scale the business to the next level. According to Infarm, each one of these new units uses 95 per cent less water, 99 per cent less space and 75 per cent less fertilizer than conventional land-based farming. This means higher yields, fresher produce and a smaller carbon footprint.
Agriculture is a £6 trillion global industry that has altered the face and lungs of the Earth for 12,000 years. But, unless we change our food systems, we’ll be in trouble. By 2050, the global population will be 9.7 billion, two billion more than today. Fifty-six per cent of us live in cities; by 2050 it will be 70 per cent. If the prosperity of megastates like India and China continues to soar, and our diets remain the same, we will need to double food production without razing the Amazon to do it. That sign on Gartenfeld Island might not be so alarmist.
Vertical farmers believe they are a part of the solution. Connected, precision systems have grown crops at hundreds of times the efficiency of soil-based agriculture. Located in or close to urban centres, they slash the farm-to-table time and eliminate logistics. New tech is allowing growers to tamper with light spectra and manipulate plant biology. Critics, however, question the role of vertical farms in our food future. They are towering lunchboxes for late capitalism, they argue – producing garnishes for the rich when it is the plates of the poor we must fill. Vertical farms already make money, and heavyweights including Amazon and SoftBank are investing in various companies in the hopes of cornering a market expected to be worth almost £10 billion in the next five to ten years. Infarm is leading that race in Europe. It has partnered with European retailers including Aldi, Carrefour and Marks & Spencer. In 2019 it penned a deal with Kroger, America’s largest supermarket chain. Venture capitalists have handed the firm a total of £228 million.
Not bad for a hare-brained experiment that started in a Berlin apartment.
An Infarm employee tends to a batch of seedlings in a special incubator
Credit Ériver Hijano
In 2011, a year before he moved to Berlin, Erez Galonska went off-grid. He grew up in a village in his native Israel, but the young nation was growing too, and farms made way for buildings. Soon the village was a town, and its inhabitants ever more disconnected from their natural surroundings.
Galonska’s father had studied agriculture, and the son had dreamed of recovering a connection with nature he felt he had lost. The search took him to the mountains of the Canary Islands, where he found a plot of land and got to work. He drank water from springs, drew energy from solar panels, and spent long hours farming produce he then sold or bartered at local markets.
When he met his now-wife Osnat Michaeli, “I traded it for love,” he says. “Love is stronger than anything.” In 2012, the couple, alongside Galonska’s brother Guy, who had studied Chinese medicine, moved to Berlin to work on a friend’s social media project. But the hunger for self-sufficiency remained. It was “a personal quest,” Michaeli says. “How we can be self-sufficient, live off the grid. Food is a big part of that journey.”
We meet at a Jewish restaurant in Berlin’s historic Gropius Bau art museum. It is mid-morning, and Covid-19 has cleared the tables. But a row of Infarm units whirs away quietly along one wall, producing basil, mint, wasabi rocket (a type of rocket leaf with the punchy flavour of wasabi), and other, more exotic herbs. Such produce was a pipedream for the three Infarm co-founders eight years ago. Growing crops when living on a tropical island was one thing. Doing it in a small apartment, located in the tumbledown Berlin neighbourhood of Neukölln, was quite another. Soon after moving from the Canaries, Erez Galonska typed “can you grow without soil” into Google.
Japan had taken to indoor farming in the 1970s, and this bore some helpful information on its techniques. The same was true of illegal cannabis growers, who swapped tips about hydroponics – growing with nutrient-packed water rather than soil – across subreddits.
Several trips to a DIY store later, the trio had what resembled a hydroponic farm. It was a big, chaotic Rube Goldberg machine, and it leaked everywhere. Growing wasn’t simply a case of switching on the lights and waiting. Brightness, nutrients, humidity, temperature – every tweaked metric resulted in an entirely different plant. One experiment yielded lettuce so fibrous it was like eating plastic. “We failed thousands of times,” Erez Galonska says.
Two of Infarm’s co-founders, Osnat Michaeli and Erez Galonska
Credit Ériver Hijano
Eventually, the team grew some tasty greens. They imagined future restaurant menus boasting of food grown “in-farm”, rather than simply made in-house, and founded Infarm in 2013. But there was a hitch: indoor-grown cannabis sells for around £1,000 per kilo. Lettuce for £1.20. Most of the early vertical farms required heaps of manual work and operated in the red. “It simply wasn’t a sustainable business model,” Erez Galonska says.
By 2014, they decided to roadshow their idea and shipped a 1955 Airstream trailer – a brushed-aluminium American icon – to Berlin. The trailer belonged to a former FBI agent, but it was conspicuous in a city of Volkswagens, caravans and Plattenbau buildings. Michaeli and the Galonska brothers transformed it into a mobile vertical farm, then pitched up at an urban garden collective in Berlin’s trendy Kreuzberg district. There they proselytised indoor farming to urban planners, food activists, architects and hackers, handing out salads and running workshops. Fresh, local food – even if it cost a little more – would entice a growing number of foodies who were interested in where their meals came from. The trailer cost nothing but petrol money to move, and emissions from the growing process itself were almost nil.
When the designer of a swanky hotel across town came by trailer, he asked if the team could install something similar in his restaurant. “That was really the trigger,” says Guy Galonska. “We rented a workshop and we got to develop a system for them.”
When they installed their first “farm” in a Berlin supermarket, VCs took notice and visited Infarm’s young founders at their Kreuzberg office-cum-kitchen, where they hosted dinner parties featuring Infarm crops. But a return on investment still seemed distant: some investors thought the farms were an art project. Maintaining locations manually was exhausting, and the team almost went bankrupt “two or three times,” Guy Galonska says. “I think all of us got a lot of white hair during that time,” he adds. “It was a very challenging thing to do.”
A €2 million grant from the European Union in 2016 helped. With it came deals to place Infarm units in supermarkets and restaurants across Germany. Managing them all would require something precise, connected and efficient. To become a sustainable business, Infarm would have to behave less like a farm, and more like a tech startup.
An Infarm kiosk in the Edeka Supermarket E Center in Berlin
Credit Ériver Hijano
For around 2,500 years after King Nebuchadnezzar II of Babylon gifted his wife some hanging gardens, little changed in the world of hydroponic farming. Asian farmers grew rice on giant, terraced paddies, and Aztecs built “chinampa” rigs that floated along the swamps of southern Mexico.
Life magazine published a drawing of stacked homes, each growing its own produce, in 1909, and the term “vertical farming” appeared six years later. The US Air Force fed hydroponically-grown veggies to its troops during World War II, and Nasa explored the tech as a solution for life off-planet. But vertical farming didn’t really capture public imagination until 1999, when Dickson Despommier, a Columbia University professor, devised a 30-storey skyscraper filled with farms. In 2010, Despommier published The Vertical Farm: Feeding the World in the 21st Century, which has become the industry’s utopian testament.
“I had no expectations whatsoever that this would turn commercial,” Despommier says. “We just thought it was a good idea, because we didn’t see any other way out of stopping deforestation in favour of farming, and keeping the carbon dioxide content of the atmosphere at a reasonable level. It turned out to be a crazy idea whose time has come.”
The vertical farming concept is simple: growing produce on vertically-stacked levels, rather than side by side in a field. Instead of the Sun, the vertical farm uses artificial light, and where there is ordinarily soil, growers use nutritious water or, in the case of “aeroponic” farms, an evenly-dispersed mist.
Vertical farms take up a vanishing amount of land compared to their conventional cousins. They use almost no water, don’t flush contaminating pesticides into the ecosystem, and can be built where people actually live. But, by and large, they have not functioned as businesses. Only the black-market margins of weed, and Japan’s high-income, high-import food ecosystem, have catered to profit. It costs hundreds of thousands of pounds to erect a mid-sized vertical farm, and energy use is prohibitively high.
Advances in technology are changing this. By bolting automation, machine learning and cloud-connected software on to vertical farms, firms can trim physical labour, increase capacity and maintain a dizzying range of cultivation variables. Infarm staff at a separate office to the new Berlin farm, located some 23km southeast of Spandau in the Tempelhof district, keep track of “plant recipe” settings at any one of the startup’s 1,220 in-store units, including CO2 levels, pH and growth cycles, via the company’s Farm Control Cloud Platform, a bit like a giant CCTV room. Machine learning finesses recipes, and keeps each plant as uniform as possible.
Inside the new vertical farm, trays of produce are tended by automated systems
Credit Ériver Hijano
Gartenfeld Island’s employees – mechanical and electrical engineers, software developers, crop scientists and biologists – get closer to the produce, but only just. They monitor via an iPad and feed crops into the building’s four massive grow chambers, or farms, each one about the height and width of two London buses, with ventilation systems that whoosh like a subdued turbine hall.
From there on in, robots do the hard work. Inside the farms, a robotic “plant retrieval system” – basically a tricked-out teddy picker – scoots up and down a perpendicular beam, plucking trays of plants in various stages of growth and shuffling them closer, or further, from LED lights at the summit. The firm claims this reduces service time by 88 per cent. A sliver of the window is the only way to see the device in-person: everything is hermetically sealed to keep out pests. “With automation, you invest once and then that price goes down over time,” says Orie Sofer, Infarm’s hardware lab lead. “With human labour, unfortunately, over time the price goes up.”
The number of crop plants varies depending on the produce, but there are usually just under 300 in a “farm” at any one time. Each farm yields the equivalent of 10,000 square metres of land and uses just five litres of water per kilo of food (traditional vegetable farming uses around 322 litres per kg).
Infarm is not alone in this revolution. AeroFarms, a Newark, New Jersey-based startup, feeds an aeroponic mist to roots that are separated from their leaves by a cloth. It’s most recent funding round was led by Ingka Group, the parent of Swedish furniture giant IKEA. New York’s Bowery Farming, like Infarm, focuses on automation and a proprietary dashboard called BoweryOS that, among other things, takes photos of crops in real-time for analysis. It’s £123 million in backing comes from investors including Singapore’s sovereign fund Temasek. Bowery CEO and founder Irving Fain believe his addressable market “is about a hundred billion dollars a year, just in the US, of crops that we think are good candidates for us to grow.”
Leading the vertical farming VC race is Plenty, a San Francisco-headquartered brand that has raised almost half a billion pounds in the capital since it was founded in 2013, including a 2020 Series D round led by Masayoshi Son’s $100 billion SoftBank Vision Fund. Plenty feeds its greens with water that trickles down six-metre-tall poles; infrared sensors pour data into an algorithm that nudges the plant’s growth recipe accordingly.
Plenty co-founder and chief science officer Nate Storey, who works at the company’s test farm in Wyoming, likens these deep-tech solutions to the tools that powered agriculture’s most recent revolution: “The tractor allowed farmers to be freed from constraints. Half of their land was dedicated to raising draft animals, and the tractor came along and freed them from a life where they were basically managing animals just so they could plough their land.”
For them, he says, automation is similar. “It allows us to get rid of the hardest work – the work that is unpleasant, the work [growers] don’t like to do – and focus on the work that really matters.”
Infarm kiosks inside the Beba restaurant in the Gropius Bau museum
Credit Ériver Hijano
Infarm differs from the competition on two fronts. The first is its focus on modular design: each component is compatible and scalable, like a giant, noisy LEGO set. Modularity makes it possible to install Infarm units anywhere in the world in a matter of weeks, no matter the size. That enables the company’s second USP: its business model. Infarm has no stores, selling produce instead via its remote units.
Clients tell Infarm which produce they want, and “create a schedule,” says Michaeli. “You buy the plants. Everything on the farm is controlled by Tempelhof. Everything that’s grown belongs to the client.” A chef may demand pesto that’s made from particular three-day-aged Greek and Italian basil, for example. Infarm can do that (Tim Raue, Berlin’s most famous chef, is a customer). “Everyone stops and asks about the farm,” one Berlin store manager says. “It’s great to have innovation here.”
Infarm has “two big advantages,” says Nicola Kerslake, founder of Contain Inc, a Nevada-based agtech financier. “One is that they’ve figured out how to do product onsite, which is really not very easy. And the other is that they have these great relationships with big purchasers like Marks & Spencer.”
“When you look at where the arms race is in this industry,” she continues, “it’s really been in two areas: How do I get hold of as much capital as possible, and how do I sign up the right partners? Having Marks & Spencer in your back pocket is really useful.”
It has helped encourage investors to open their chequebooks. Hiro Tamura, a partner at London VC firm Atomico, first met Infarm’s founding trio in 2018. A year later he led its £75 million Series B round. “They could roll these things out,” he says. “They worked, and they didn’t need some industrial-sized warehouse to do it. I didn’t lean in, I fell into the rabbit hole. And it was incredible. I was like, wow, these guys are thinking about time and speed to market modularity.”
Infarm ploughs a chunk of its revenue back into research. In a mezzanine-level lab sitting above the farms at Gartenfeld Island, a dozen white-coated analysts conduct tests on herbs to a soundtrack of Ariana Grande, measuring crop sugar levels, acidity, vitamins, toxicity, antioxidants and more. Via a process of phenotyping – the study of organisms’ characteristics relative to their environment – they hope to create more flavourful plants, or new tastes altogether.
“It’s not just about the hardware,” Kerslake explains. “It’s about how the hardware interacts with the rest of your farm system. And we’re starting to see a lot more sophistication on that front because the AI programs these companies started three or four years ago are now starting to bear fruit.”
Infarm’s results are high-quality: juicy lettuce, wasabi rocket that kicks, and basil that’s far more fragrant than the budget variety. “The end goal with almost everything that we’re doing is developing some sort of playbook, some sort of modular and standardised system, that we can then copy-paste to wherever we go,” says Pavlos Kalaitzoglou, Infarm’s director of plant science. Across from the lab, tomatoes and shiitake mushrooms grow in wine cellar-size chambers. They are living proof of how the firm is looking to diversify from herbs and leafy greens, whose low energy and water requirements make them the staple crop of every vertical farming startup today.
Rows of LED-illuminated produce inside one of Infarm’s four massive new grow chambers
Credit Ériver Hijano
We are in danger of farming the planet to death. Agriculture already occupies 40 per cent of all liveable land on Earth, and food production causes a quarter of all greenhouse gases. An area the size of Scotland disappears from tropical rainforests, responsible for up to a quarter of land photosynthesis, each year. Clearing more trees to feed our spiralling population will not help.
“We need to go back to the drawing board and rethink which avenues we can environmentally afford to pursue,” says Nicola Cannon, a professor at the Royal Agricultural University in Cirencester. Nitrogen fertiliser is particularly harmful to the environment, Cannon adds, “and has led us to adopt systems which have grossly exceeded the planetary boundaries.”
Current food systems are wildly inefficient: waste accounts for 25 per cent of all calories. And yet, almost a billion people suffer from hunger worldwide. These are not issues vertical farming will solve, critics, argue. Going local does little beyond satisfying consumers.
Energy is another tricky issue. Ninety per cent of Infarm’s electricity today is renewable, and it wants to reach zero emissions in the next few years. But this doesn’t factor in the environmental cost of building a steel-and-cement facility.
“Vertical farms are a round-off error to the round-off error in terms of contributing to the big levers out there,” Jonathan Foley, an environmental scientist based in Minneapolis, says. “Like most technologies that are getting a lot of venture capital and which come from Silicon Valley kind of thinking, it’s being massively overhyped at the cost of real solutions. There’s an opportunity cost to put all this technology, money and renewable energy – that could be used for other things that we need energy for – into growing arugula for rich people at $10 an ounce.”
More than half the world’s food energy comes from its three “mega-crops”: wheat, corn and rice. They require wind, seasons and micronutrients that vertical farms are unable to replicate today. These are the crops that can prevent famine in Somalia, Bangladesh or Bolivia – not lettuce. “Vertical farms are growing the edge of the plate, not the centre of the plate,” Foley says.
But Despommier says it’s too soon to criticise the young industry for not addressing issues such as crop diversity. “What you’re really seeing is a rush towards profitability to get their feet wet, and to get their ledgers in the black and to pay off their investors, before they start diversifying,” he says.
“In a world where you think that land is unlimited and that resources are unlimited, indoor farming would be nonsensical,” Plenty co-founder Storey says. “As crazy as it seems to replace the Sun with electricity, it makes sense today. And it really makes more and more sense as time goes on.”
Much of the hope vested in vertical farms rests on the light-emitting diode. This tiny bead of light is the industry’s packhorse: it is a farm’s biggest financial layout and the nucleus of its most exciting advances. Modern LEDs are nothing like the ones that powered your childhood TV. They’ve progressed at such a rate, in fact, that they’ve developed their own law to adhere to: “Haitz’s Law”. Each decade, their cost drops by a factor of ten, while the light they generate leaps by a factor of 20.
That curve will eventually plateau, experts say. But not before LEDs improve enough to allow vertical farms to profit from food closer to the middle of the plate. Infarm’s current smart LED set-up is over 50 per cent more efficient than the one that lit its first farms. Haitz’s Law has helped some companies experiment in growing potatoes, which require far more energy and water than leafy greens. Turning profit from a crop that delivers the highest calories per acre would be momentous for the industry.
The cutting edge of LED technology today is smart sensors that can regulate the brightness and spectrum of light to replicate growing outdoors – or enhance it. Much of the planet’s first flora grew only in the ocean, which looks blue because it absorbs blue light at least.
Photosynthesis, therefore, occurs best between the blue and red light spectra. By tailoring LEDs to emit only these colours, or by dimming at intervals meant to mirror a plant’s natural cycle, vertical farmers can further reduce their energy burden – like stripping a road car to its bare bones so it can drive faster.
Recent discoveries have been more surprising. Strawberries, for example, react particularly well to green light. Some spectra can increase vitamin C in concentrated fruits like kiwis, while others extend shelf-lives by almost a week. In the future, says Fei Jia, of LED firm Heliospectra, growers “can get feedback from the lighting and the plants themselves on how the lighting should be applied… to further improve the consistency of the crop quality.”
“If you judge it from what you have today, you understand what [critics] are saying,” Guy Galonska says. “How can you grow rice and wheat and save the world? And they are right. But they can’t see ten years ahead: they can’t see all the different trends that are going to support that revolution.”
Other technological advances are helping agriculture in different ways. Drones and sensors help map and streamline growing. Drip irrigation dramatically reduces the burden on dwindling water supplies. Circular production – where waste products from one process contribute to fuelling another – is becoming more commonplace, especially in livestock farming. Cell-grown or insect-based meat (or vegetarianism) will reduce our reliance on livestock, which consume 45 per cent of the planet’s crops. Infarm, and the broader vertical farm cohort, may not be saving the world today. But it wants to build taller farms, place them in public buildings like schools, and teach people the value of fresh, healthy vegetables. If 70 per cent of us are to live in cities, then cities “can become these communities of growing,” says Erez Galonska.
Ultimately, Infarm wants to build a network of tens of thousands of automated farms, each one pumping streams of data back into a giant AI system in Berlin. This “brain”, as Galonska calls it, will pour that information into algorithms to generate better food at lower costs, each new yield shaving fractions from the water, energy and nutrients required. Then, Infarm could become something closer to the dream Galonska left behind in the Canaries: truly self-sufficient.
It’s a long way from the leaky, DIY gadget he and his co-founders built in their front room. “The way the world is going now, it’s very clear to everyone it’s running in the wrong direction,” Galonska says. “We definitely believe in the power of collaboration: bringing those outside-the-box thoughts to create a new system that will generate more food, better food, much more sustainably, and help to heal the planet – because that’s the main issue on the table.”
Saudi Farmer Has Built The Region’s First Vertical Farm
“My aim is to make sure we truly become self-sufficient,” he said.
The Saudi farmer Omar Al-Jundi even he is not related to farming by degree. But that is exactly where the industrial engineer found his calling, when he built the region’s first vertical farm in the heart of Dubai. Born in Egypt to Saudi parents, Al-Jundi spent his early years in Alkhobar due to his father’s engineering firm.
The family moved to Jeddah when he was 12 years old. His last two years of schooling were spent at Bahrain School in Manama. “I wanted to graduate with an American high school diploma,” Al-Jundi said. “At the time, as a Saudi, you couldn’t attend private foreign schools.” Upon graduation, he left the region to study industrial engineering, followed by an MBA at the University of Miami in Florida. Although his father is an engineer and his mother an architect, Al Jundi delved into the world of banking for two and a half years when he moved back to Jeddah upon graduating.
“I then shifted to the hospitality industry, opened the first lounge in Jeddah along with other restaurants with my friends, and ended up selling my share and joining my father’s company,” he said. “You learn that you’re better off doing something on your own than having partners because you end up changing directions.”
After 10 years of “paying his dues” in the family business, he felt compelled to change directions. “As an Arab, you’re always closely tied to the family,” he said. “We’re blessed my father started a business and there’s a place for us in that business, but luckily, my younger brother was a lot more interested in it — I always felt my calling was somewhere else.”
In search of his true passion, he started his journey as an entrepreneur. The field he specialized in had yet to be determined. “I felt that there was a meaning for something else,” Al-Jundi said. “I was free and my family was very supportive.”
Countless research and books later, he became intrigued by the tech space, admitting he believed he would start the next Amazon. “That didn’t follow through,” he said. “Then I thought it would be in mining, but I always looked for something that was away from my comfort zone such as engineering, contracting, real estate and consulting. Just something different. It was a process.”
The young Saudi had reached a point in his life where he felt the need to do something impactful, something which added true value to the region. Eventually, two of his friends introduced him to the concept of modern farming. “I visited some orange farms in Egypt and I was in exploration research mode,” he said. “I enjoyed seeing nature — you’re a lot more relaxed. Here, when you go in and see the plants growing every day, there’s definitely a connection, because you’re seeing the end product, you’re feeling it, and I connect to them.”
The more research he immersed himself in, the more driven his interest became. At the time, the Saudi Government was focused on addressing food security and self-sufficiency. “It’s always been a big topic,” he said. “When you fly out of Riyadh, you find these big circular green spots as they’re trying to green and farm the desert, which was successful, but on the other hand, it depleted our water resources.” According to the Food and Agriculture Organization, agriculture represents around 70 per cent of water consumption in most of the GCC countries. But Al-Jundi did not give up on the thought.
After moving to Dubai in 2014, he learned about King Abdullah’s Initiative for Saudi Agricultural Investment Abroad. Half the capital needed for agricultural projects was offered to Saudis who invested in a list of 31 countries abroad to purchase land, set up a project and export the food back to the Kingdom. It gave him an idea to start his own vertical farm. “I knew it was a big topic,” he said. “I’d never heard we could grow food with no soil. I thought it was intriguing and fascinating. It was enough for me to know there was something there to explore it further.”
With more than 90 per cent of the region’s land unsuitable for agriculture, Al-Jundi set out to find a solution. He spent the following 12 weeks taking courses in aquaponics, aquaculture, hydroponics and horticulture in California and the Netherlands. He even spent time working in a cucumber greenhouse at the Delphy facility in Holland, where he acquired valuable experience in the field. “It was really professional and a great learning experience,” he said. “That’s when I knew what I wanted to do. And I knew I had to completely immerse myself in it.”
The team of Badia Farms, which he founded in Al Quoz in December last year, consists of 12 people, all of whom have experience in farming. “It took 18 months to get it up and running because we didn’t work with any technical partner,” Al-Jundi said. “I knew I was in it for the long haul, so I worked with different growers and learned.”
The 850-square-meter facility includes a “fertigation” room, which fertilizes and irrigates the 18 varieties of crops he currently grows. Gourmet seeds, some of them hybrids, such as lemon basil, cinnamon kale, wasabi, green radish, mustard, micro kale, edible flowers and cinnamon basil, are flown in from the United Kingdom and the United States every three months — from 50 to 300 kilograms at a time. The farm plans on introducing as many as 26 varieties, including sunflowers.
The seeds are placed on a type of mat made of recycled carpet that is food-certified. LED lights flood the room in a pink atmosphere, with each UV light containing a certain spectrum that is beneficial for the plants.
In the tank room, feed and water is scheduled through a computer-based on the crop, with a unique nutrient recipe for each type, including potassium, calcium, magnesium, and ammonium. UV and concentrated oxygen are also able to kill any potential bacteria or pathogens in recycled water. Once the seeds sprout, they are moved to the five stacks in the vertical farm. Four dehumidifiers regulate the humidity in the air, providing each on average with 70 litres of water a day. The eco-system created by Badia Farms uses 90 percent less water than open-field farming and recycles its water up to nine times.
“We’re using hydroponics,” Al- Jundi said. “The biggest advantage is that we do not spray pesticides, which are messing up our health. In fact, we extensively use stickers to attract insects away from the crops.” Different levels of lighting are provided for each stage of the plants before they are sent out as they were grown. “They’re intense in flavor and it’s the freshest you can get that way,” he said. “My personal favourite is chocolate mint.” With 60 clients so far, serving hotels, restaurants, and cafes, the model is a first for the region, which made it challenging to set up. “All the ones abroad are designed for different climatic conditions so none of them are applicable here, where there is extreme humidity and high temperatures,” he said. “And to convince a chef to give you his time, when you don’t have the track record, was a big challenge. I wasn’t a known farmer yet.”
The system’s structure was manufactured in Riyadh, with a plan to set up the next facility by 2020 in Jeddah. Until then, the plan is to cater to Saudi as well as the UAE. “Dubai is a good testing ground and Saudi’s vision now is to support our type of sustainable growing and ecological farms, so it’s perfectly in line with what we want to do,” Al-Jundi said. “The government is now delegated to move into sustainable growing and find viable solutions to address self-sufficiency, so it’s not a slogan anymore: it’s the real deal.”
He hopes to develop similar projects across the Kingdom in the future. “My aim is to make sure we truly become self-sufficient,” he said. “Vertical farming is one solution but it’s not the full one — the ideal solution lies in all models of modern farming. What’s close to my heart is giving people healthy food while preserving our resources, and I believe the new generations of Saudis are ambitious and want to evolve our country. We were just waiting for the opportunity and it has finally come.”
Source: Arab News
UPDATE - Vertical Farming Leader Kalera Welcomes Maria Sastre to Board of Directors
Sastre brings world-class customer service and operations experience as Kalera prepares for rapid domestic and international expansion.
A seasoned executive with experience in the food, travel, and tourism industries, Sastre brings with her over 25 years of executive leadership and experience and currently sits on the boards of esteemed, Fortune 500, multibillion dollar public and private companies, including General Mills and O’Reilly Auto Parts.
ORLANDO, Fla., Feb. 24, 2021 (GLOBE NEWSWIRE) -- Kalera (Euronext Growth Oslo ticker KAL, Bloomberg: KSLLF), one of the fastest-growing and largest vertical farming companies in the world and a leader in plant science for producing high-quality produce in controlled environments, today announced the appointment of Maria Sastre to its Board of Directors. A seasoned executive with experience in the food, travel, and tourism industries, Sastre brings with her over 25 years of executive leadership and experience and currently sits on the boards of esteemed, Fortune 500, multibillion dollar public and private companies, including General Mills and O’Reilly Auto Parts. The addition of Sastre to the board coincides with Kalera's rapid expansion into several new markets and its acquisition of Vindara Inc., the first company to develop seeds specifically designed for use in vertical indoor farm environments as well as other controlled environment agriculture (CEA) farming methods.
“We are thrilled that someone of Maria’s caliber has chosen to join Kalera’s board,” said Daniel Malechuk, Kalera CEO. “Her resume is beyond impressive, with extensive experience leading highly successful international and growing companies, and is a strong complement to our industry-leading management team and board of directors. She has proven time and again that she is invaluable in helping scale businesses, and will be an incredible asset to Kalera during this time of rapid growth, both domestically and abroad.”
In addition to her aforementioned business experience, Sastre also served on numerous civic and non-profit boards such as the Greater Miami Visitors and Convention Bureau(Chair), the Executive Advisory Board of Florida International University School of Hospitality,and the Executive Board of the United Way of Miami-Dade County. She has been recognized as one of the Top 80 U.S. Hispanics and Top 20 Latinas and has received numerous awards in the travel and hospitality industry sectors. Sastre's education includes a Bachelor's degree and a Master's in Business Administration, both from New York Institute of Technology.
“As someone with a passion for optimizing customer experiences, I am proud to join Kalera’s board as I fully believe their product is a category leader,” said Maria Sastre, new Kalera board member. “Kalera has the opportunity to serve diverse customer segments and increase accessibility to a product that is inherently safer, cleaner, fresher, more sustainable, and more nutritious and flavorful. In a world where brands are looking for ways to differentiate their products and services to their discerning customers, the Kalera portfolio is well positioned to offer the best vertical farming product solution. I trust my years of experience in operations and customer service will prove beneficial as Kalera expands into new markets.”
Sastre previously served as the President and Chief Operating Officer for Signature Aviation, the largest worldwide network of fixed-based operations and maintenance centers for private aviation. Before joining Signature, she spent eight years at Royal Caribbean Cruises LTD, where she held the positions of Vice President, International, Latin America, Caribbean and Asia; and Vice President of Hotel Operations. Her roles included strategic growth across emerging markets as well as managing all aspects of operations and the guest experience onboard Royal Caribbean's fleet of vessels. Previously, Sastre served as Vice President of Worldwide Customer Satisfaction for United Airlines, where she led the newly created customer-satisfaction division charged with refining the customer-service experience.
Kalera currently operates two growing facilities in Orlando, and is building facilities in Atlanta, Houston, Denver, Columbus, Seattle, and Hawaii. Kalera is the only controlled environment agriculture company with coast-to-coast facilities being constructed, offering grocers, restaurants, theme parks, airports and other businesses nationwide reliable access to locally grown clean, safe, nutritious, price-stable, long-lasting greens.Kalera uses a closed-loop irrigation system which enables its plants to grow while consuming 95% less water compared to field farming.
About Kalera
Kalera is a technology driven vertical farming company with unique growing methods combining optimized nutrients and light recipes, precise environmental controls, and clean room standards to produce safe, highly nutritious, pesticide-free, non-GMO vegetables with consistent high quality and longer shelf life year-round. The company’s high-yield, automated, data-driven hydroponic production facilities have been designed for rapid rollout with industry-leading payback times to grow vegetables faster, cleaner, at a lower cost, and with less environmental impact. To learn more visit www.Kalera.com.
Media Contact
Molly Antos
Phone: (847) 848-2090
Email: molly@dadascope.com
A photo accompanying this announcement is available at https://www.globenewswire.com/NewsRoom/AttachmentNg/bb487877-0d3b-4e1c-9492-9ea280c217a1
Plenty Ranked Number One on Prestigious FoodTech 500
Plenty came in first on the ranked list of 500 and out of a total of 2,000 nominees.
SOUTH SAN FRANCISCO, Calif.
Plenty, the flavor-first vertical farming company with a mission to improve the lives of people, plants, and the planet, today announced its #1 ranking on the esteemed Forward Fooding 2020 FoodTech 500.
Referred to as the “Fortune 500 list of agrifood companies,” the FoodTech 500 highlights global entrepreneurial talent at the intersection of food, technology and sustainability. Forward Fooding’s proprietary algorithms evaluate a business on its size, digital footprint and sustainability as measured against the United Nations Sustainable Development Goals. Plenty came in first on the ranked list of 500 and out of a total of 2,000 nominees.
“It is an honor to be included on the FoodTech 500 and we are thrilled to be ranked first,” said Nate Storey, co-founder and CSO of Plenty. “The world is in need of an agricultural revolution, and there are many exciting areas where innovators are changing the future of food. At Plenty, we’re focused on using our proprietary, scalable vertical farming technology to deliver the freshest, most favorable produce year-round, while preserving our most precious resources.”
Plenty grows pesticide-free, non-GMO produce that tastes like it was fresh-picked from the garden because it was. The company ships from its farm to local stores every day. The farm’s controlled environment means the company can grow leafy greens year-round, regardless of the season. Plenty’s leafy greens are so clean, there is no need to wash because there is nothing to wash away - no bleaches, chemicals, soil or pesticides. The company wants the first person to touch their produce to be the consumer opening the package in their kitchen. Plenty plants are cultivated in an optimum growing environment, reaching peak flavors and nutrient value year-round, across every harvest.
The world is running out of usable land for growing crops and the global water supply is under severe threat of depletion. Plenty was founded on the need to create a more sustainable way to grow food using less land and water. Plenty yields hundreds of acres of crops in a building the size of a big box retailer, without cutting down a single tree, and using a fraction of the water required in the field. It’s San Francisco-based farm uses 100% renewable energy, and its greens are stored in 100% recyclable packaging and shipped locally to minimize the transportation footprint. Plenty’s data analytics and machine learning capabilities deliver 200 years’ worth of data each year, helping to quickly iterate and improve farm yield, quality and efficiency.
“The FoodTech 500 was created to shine a spotlight on the leading global innovators across the AgriFoodTech ecosystem, from farm to fork, who are making impactful solutions to better our food system,” said Alessio D’Antino, Forward Fooding founder and CEO. “This year’s list focused on understanding the driving factors behind the leading companies’ success and innovation, and we were thrilled to learn more about the top industry players, like Plenty, that are transforming our food system.”
The list represents 38 technology domains within the AgriFood space, including the broad categories of alternative proteins, farm management and precision farming, and vertical/indoor farming. The full ranking and more data about the 2020’s FoodTech 500 and its methodology can be found here.
About ForwardFooding
Forward Fooding is the world’s first collaborative platform for the food & beverage industry via FoodTech Data Intelligence and corporate-startup collaboration. Data services include The FoodTech Data Navigator data subscription service and facilitating corporate-startup collaboration through bespoke innovation programs and FoodTech consultancy.
To learn more visit: www.ForwardFooding.com
About Plenty
Plenty is an American farming technology company that frees agriculture from the constraints of land, weather, seasons, time, distance, pests, natural disasters, and climate. The company’s plant scientists, engineers, and farmers have developed its indoor vertical farming technology to grow nutrient-rich and pesticide-free plants with extraordinary flavor. The Plenty platform is designed to grow multiple crops in a building the size of a retail box store, yielding hundreds of acres using a fraction of the water and other precious resources. Plenty's flagship farm and headquarters are located in South San Francisco, and the company operates the largest of its kind Research and Development farm in Laramie, Wyoming. Plenty is currently building the world's highest-output, vertical, indoor farm in Compton, California.
View source version on businesswire.com:https://www.businesswire.com/news/home/20210301005069/en/
CONTACT: Jane Gideon
KEYWORDS: CALIFORNIA UNITED STATES NORTH AMERICA
INDUSTRY KEYWORD: ENVIRONMENT TECHNOLOGY OTHER TECHNOLOGY FOOD/BEVERAGE AGRICULTURE SUPPLY CHAIN MANAGEMENT RETAIL NATURAL RESOURCES SCIENCE OTHER SCIENCE
SOURCE: Plenty
Copyright Business Wire 2021.
PUB: 03/01/2021
BRITISH COLUMBIA: Agri-Tech To Anchor New Okanagan Falls Industrial Park
“This really is the future of agriculture,” said Monique Janower, senior marketing and strategy director for Avery Group.
JOE FRIES
A vertical farming operation similar to this is planned for an Okanagan Falls industrial park.
USDA/Special to The Herald
Vertical farming could be what finally helps a light-industrial park take root in Okanagan Falls.
Avery Group purchased the 110-acre former Weyerhaeuser mill site for $3.2 million in July 2020, and this week received tentative rezoning approval from the board of the Regional District of Okanagan-Similkameen.
The application, which would down-zone the site from its current heavy-industrial rating, is now set for a public hearing March 18.
At the heart of the redevelopment plan is a 30-acre lot on which Avery Group wants to build a vertical farming facility, in which rows of crops would be stacked on top of one another in a warehouse-like environment.
“This really is the future of agriculture,” said Monique Janower, senior marketing and strategy director for Avery Group.
Potential crops include lettuce and leafy greens that vertical farming operations around the world had parlayed into a $2-billion industry as of 2018, according to Forbes Business Insights, which projects the market will expand to $12 billion by 2026.
The rest of the land at 1655 Maple St. would then be subdivided into lots ranging from 2.5 to 15 acres for a variety of uses, ranging from storage and food packaging to beverage processing and light manufacturing.
Janower, who cautioned there are still many regulatory hurdles to be cleared, said there has nonetheless been “tremendous interest” from potential buyers due to the relative rarity of new industrial land and the site’s central proximity to Alberta and the Lower Mainland.
Avery Group is owned by Garry Peters, who has deep ties to the area, according to Janower, so the company appreciates the site’s context within the community.
“We understand we’re not just creating bricks and mortar,” said Janower. “It’s very much tied to regional economic development of the area.”
The rezoning application already has the support of RDOS staff and a key community group.
“Rezoning of the property could potentially bring an influx of new and growing industrial businesses to Okanagan Falls,” Matt Taylor, president of the Okanagan Falls Community Association, wrote in a letter to the RDOS board.
“This in turn could lead to additional employment, a need for more residences and even more tourism. These factors would all contribute to and support the community.”
Since the 2007 closure of Weyerhaeuser, the site has been the subject of multiple development proposals, including an industrial park, residential development and, most recently, a cannabis production facility.
If rezoning is granted, Avery Group will then apply for the RDOS development permit required for the vertical farming operation. At the same time, it will apply to the B.C. government for subdivision. If all goes well, the company expects the park to be open for business in 2022.
Babylon Micro-Farms Establishes New Corporate Headquarters In Richmond, Virginia
The company has developed disruptive technology - a cloud-based platform that operates vertical farms through a mobile phone app that controls all aspects of farming at the touch of a button
Richmond, VA (February 2021) Babylon Micro-Farms has chosen Richmond, Virginia as the site for their corporate headquarters, opening a new office and R & D space in historic Scott’s Addition. The move from Charlottesville was driven by the company’s growth and need for a larger talent pool - they had been courted by California and Arizona as an up-and-coming tech company in the indoor ag-tech space.
The company has developed disruptive technology - a cloud-based platform that operates vertical farms through a mobile phone app that controls all aspects of farming at the touch of a button. The indoor ag-tech industry is projected to grow globally from USD $121.26 billion in 2019 to USD $167.42 billion by 2025, a compound annual growth rate of 5.4% according to the latest report released by Market Data Forecast last week.
Babylon’s CEO and Co-Founder, Alexander Olesen, commented on the move. “Richmond is the perfect launchpad for our next phase of growth. It has a dynamic business eco-system and gives Babylon the chance to build an even stronger foundation for the future with everything it has to offer.”
Babylon began hiring locally in Richmond prior to the move, scaling up their operations in preparation for the anticipated increase in sales in 2021. Graham Smith, CTO and Co-Founder of Babylon, said “Our growth has been based on significant R & D we were able to accomplish because of support from The Center for Innovative Technology, the National Science Foundation and investors that understood early on the potential for this technology. Richmond offers a hub where innovation and industry intersect and having our headquarters here will fuel our expansion.”
The company expects to triple its workforce in the next three years, adding jobs in every department, from assembly to engineering. For more information visit www.babylonmicrofarms.com or contact janet@babymicrofarms.com for interview requests.
Babylon Micro-Farms team, from left to right: Alexander Olesen, CEO and co-founder; Marc Oosterhuis, COO; and Graham Smith, CTO, and co-founder. Courtesy of Babylon Micro Farms
ABOUT BABYLON MICRO-FARMS
At the touch of a button, Babylon Micro-Farms delivers a simple, yet engaging indoor growing experience. Babylon helps senior living communities, hospitals, schools, and hospitality companies showcase their commitment to providing fresh, nutritious produce and sustainability to their residents, employees, and customers.
They have designed a complete on-site farming service that makes growing simple for anyone, thanks to their plug-and-play Micro-Farms and Guided Growing App. Babylon offers the most affordable, efficient, and advanced vertical farming platform available, remotely managed through the cloud with unparalleled customer service. Since their humble beginnings as a social entrepreneur student project, Babylon have attracted investors from Silicon Valley, been awarded a grant from the National Science Foundation to support their research, patented a groundbreaking technology, and received recognition by Virginia's Governor Northam for their contribution as a technology innovator following their successful application for funding from the Center for Innovative Technology.
Babylon has designed a software platform to reclaim the decentralized food system of the 21st Century - using modular vertical farms that enables anyone to grow local produce on-site, all year round, indoors. They launched their first products focusing on the health care and senior living markets where our vertical farms provide access to food-as-medicine quality food and a variety of therapeutic activities.
Website:
https://www.babylonmicrofarms.com/
Press Contact:
Sharon Rettinger
CGTN Conversations: Chinese Firms Add Strength To Dubai's Future Tech Ecosystem
CGTN Digital's International Editor Abhishek G. Bhaya spoke with Faisal Al Hawi, the head of Accelerator and Incubators at the Dubai Future Foundation, and Stuart Oda, the founder and CEO of Alesca Life.
Over the decades, the Gulf city of Dubai has emerged as a land of innovation and a place where the future could be felt right now in the present. The city is actively encouraging global collaborations to drive innovation and future technology in the United Arab Emirates and internationally through its Dubai Future Accelerators (DFA) initiative that was launched in 2016 under the aegis of Dubai Future Foundation.
In recent years, many Chinese tech firms and start-ups – which are known for their technological prowess – have partnered with DFA to contribute to their mission of imagining, designing and co-creating solutions for future challenges.
One such successful initiative has come from Beijing-headquartered Alesca Life, an agro-tech company that is creating next-generation urban farming solutions that consume five per cent water and 30 per cent energy vis-à-vis conventional farming.
To get an overview of DFA's future innovation agenda and how Chinese firms are contributing in making that vision a reality, CGTN Digital's International Editor Abhishek G. Bhaya spoke with Faisal Al Hawi, the head of Accelerator and Incubators at the Dubai Future Foundation, and Stuart Oda, the founder and CEO of Alesca Life.
Al Hawi is responsible for creating a myriad of programs that connect different stakeholders, government and private, with innovative startups and companies from around the world to experiment with and making Dubai the testbed for future ideas.
Oda is an investment banker-turned- urban farmer with a passion for innovation and sustainability. He founded Alesca Life in 2013 with an aim to make food production more localized and data-driven.
Edited excerpts:
Bhaya: Faisal, please tell us a bit about the vision of the DFA initiative and what it aims to achieve and also some of the main areas and technologies it has tasted success in the past four years?
Al Hawi: Dubai Future Accelerators is an initiative that was born four years ago under the Dubai Future Foundation. The vision was pretty much straightforward – to put Dubai as a leading city of the world when it comes to technology innovation. Our mission is to turn Dubai into a global testbed for innovations and technologies. The DFA looks around for all the start-ups in the global scene, trying to understand the technology needs, the partner needs, the local ecosystem needs, and trying to bridge the gap between these two players of the market.
We do this in what we call the Area 2071, which is like the heart of our ecosystem in Dubai and we've had tremendous success. Throughout the four years, we've run eight cohorts, the eighth cohort is ongoing as we speak. We've engaged with more than 300 start-ups and over 60 pilot projects were produced out of DFA and more than 150 memoranda of understanding or commercial agreements were signed with different government entities and private sector partners.
Dubai Future Accelerators is positioned in a way that basically bridges the gap between the big players, be it government or private sector, and the start-up innovators from around the world.
Bhaya: How many Chinese firms and start-ups have availed the DFA program so far? Please name some of the major projects the Chinese entities have undertaken in the UAE as part of the DFA initiative.
Al Hawi: We've worked with Chinese companies ever since Cohort 1 back in 2016. So, Alesca Life is one of them. Shellpay, which was a fintech company working with the General Directorate of Immigration in Dubai, was another company. There was another company called Future Trends, working with Dubai Health Authority on medical imaging, and utilizing the technologies of AI and machine learning to optimize the diagnosis of late-stage cancers.
Yitu Technology is another Chinese AI-based company which worked very closely with [UAE's largest telecom service provider] Etisalat on solving some of their telecom related issues. So these are just to name a few companies that worked with us.
We really understand the strength Chinese ecosystem brings to our ecosystem. And I think we complement each other in a lot of areas.
Another example, broader than just Dubai Future Accelerators, is within Area 2071, where SenseTime actually has an office here, and they work very closely with the AI office, in a couple of strategic projects.
So, the partnership is growing stronger and stronger, year after year. And we definitely believe that there are areas specifically in the fourth industrial revolution technologies, blockchain, AI and IoT and the likes that we will definitely materialize more and more outcomes and success moving forward.
Bhaya: Stuart, what is the story behind Alesca Life?
Oda: Seven years ago, I started Alesca Life here in Beijing. The vision of the company is to democratize access to fresh and nutritious food by democratizing the means and the knowledge of production.
And the more research that I was doing, it became very clear that one of the most pressing challenges over the next decades wasn't so much actually related to connectivity, as these things were becoming easier with the proliferation of smartphones and computers, but access to fresh and nutritious food. And so, my team and I wanted to find a way in which we can make this access a lot easier. And wherever it made sense to localize that fresh food production, and wherever food production currently existed to make it more data driven.
So we set on this journey seven years ago, and we currently have our teams and offices across Japan, China, and the United Arab Emirates and we have partnerships across many more countries. We're developing precision farming tools to accomplish, to increase the productivity, the profitability, and the predictability of food production by up to 10 times.
Bhaya: The urban farming technologies including vertical farms and data-driven food production are certainly relevant for an arid region like the Arabian Peninsula. How did your partnership with DFA come about and what has been the journey like in the UAE for Alesca Life?
Oda: In 2016, our team was selected into the DFA program as part of Cohort 1. It was actually our first entry into the Gulf region. We knew that the technology had huge promise and potential in the region, and we wanted to make a serious commitment to the region. The DFA program was kind enough to offer us a spot in Cohort 1.
It has been hugely transformational in two ways. You know, the way in which business is done in the Middle East is very different. And to be able to have an organization like DFA, both providing the meaningful introductions, reducing some of the barriers related to the company's formation, and then also just the credibility that is bestowed on some of the companies that get to go through the program. All three of these things contributed enormously to our success in the region.
Through this program we've also been able to find meaningful strategic partnerships to mitigate some of the challenges related to concentration of supply chain, for example, even being in a place like China, to have manufacturing bases and other places in other countries, is beneficial for us.
So, right after the DFA program, we had an opportunity to localize the manufacturing of our container farm in the Emirates of Ajman in the UAE, so that we can serve our customers and our base in the GCC (Gulf Cooperation Council) and also to showcase our commitment to the region that we're not just there to sell our systems, but that we are there for the long term.
Bhaya: The year 2020 has been a watershed in many ways for the world due to the COVID-19 pandemic, reinforcing our increasing reliance on digital and AI technologies without which we can't imagine a future. How did the global crisis impact the long-term vision of DFA?
Al Hawi: The pandemic has definitely affected everyone. At DFA, we realized that innovation is the way to be resilient for the future, prepared for the future and understanding exactly the problems of today that potentially, and unfortunately, led us into the pandemic. We had just a very short drop-in time in which everybody had to just realign ourselves, and that was around March. But we immediately resumed back in October.
Not just the DFA, I think all the government entities, as well as start-ups, realized how important a role they play in this ecosystem. And Cohort 8, that is currently ongoing and will last until the end of March, is specifically looking at challenges that will basically be more specific around life after COVID.
I'll share a couple of examples. The Dubai Roads and Transport Authority (RTA) is looking into new solutions of shared mobility. We are very much accustomed to the ride-hailing apps and public transport systems. But that has changed forever. So they (RTA) are really being proactive in trying to foresight what new models of public transport and shared mobility will be out there. And we're really excited to see what comes out as solutions in a couple of weeks' time.
Another entity which is really looking at how things might evolve in the health care sector is the Dubai Health Authority. They are focusing on preventive health care measures, solutions and products, but not only from a sense of being preventive or proactive but in a sense of also democratizing access to that device.
Bhaya: Food security is already a global concern and going to be a top challenge in the future. It did aggravate last year due to the supply-chain disruption caused by the pandemic. What are some of the innovative solutions that Alesca Life offers to meet this challenge and has COVID-19 triggered a sense of greater urgency?
Oda: This is a great point. Pre-pandemic, in 2018-19, a lot of the interest and investment from governments, companies and investors was in food tech, which was related to food delivery and meal kits at home. And it was really focused on one thing, which was consumer convenience. What has happened in 2020, with the pandemic and now that we're in 2021, is that the focus has shifted materially from food tech to agtech - agricultural technology, which is focused on resilience. It's about community resilience, as opposed to consumer convenience.
So, one of the solutions, the benefits or the outcomes of the pandemic, was a renewed interest in agtech. And by that, I mean, local food production is in control of your own supply chain for fresh and nutritious food. So, since the pandemic has happened, since the lockdowns have begun, I've probably spoken to individuals and government entities from over 30 countries that are interested in finding ways in which they can secure a minimum supply of local fresh food production in their own countries, in their own communities.
The shift has accelerated towards this localization, towards this decentralized form of food production that can happen almost anywhere. And one of the solutions that we're providing for this is to bundle all of our precision farming tools – our monitoring equipment, our automation systems, our farm management and software tools, and even our latest computer vision AI cameras – and bundle all these products together to create an incredibly capital efficient indoor farm. And this allows both governments, at large scale, and even community, at a smaller scale, to be able to be in control of their local food production needs.
Interviewer and script: Abhishek G Bhaya
Video editors: Meiyi Yan & Wu Chutian
Cover image: Du Chenxin
Infographics: Jia Jieqiong
Director: Mei Yan
Signify Adds Automatic Intensity Adjustment Plus Year-Long Recipe Modulations To Horticultural Controls
There’s something for both the greenhouse and the vertical farm in the GrowWise tweaks, which in some cases rely on tying to other systems’ sensors.
The Signify toplights at Belgium’s De Glastuin lettuce greenhouse automatically dim or brighten as daylight levels changes. (Photo credit: All images courtesy of Signify.)
Signify has enhanced the control system for its greenhouse LED lighting so that toplights can react immediately to changes in daylight conditions and adjust brightness accordingly. The company has also added year-long control settings intended to allow vertical farmers — but not greenhouses — to program seasonal variations in LED spectral content over a 365-day period.
Both upgrades are intended to reduce manual labor and improve overall cost efficiencies, Signify said.
Until now, greenhouse farmers could dim or brighten their Signify toplights by instructing the lights to do so via the control system, called GrowWise. Signify has now modified GrowWise software so that it can take readings from daylight sensors that are part of separate systems. GrowWise then instantly and automatically adjusts artificial light intensity emitted by the toplights, called Philips GreenPower LED.
“The lighting can be used much more efficiently since it gives us the flexibility to reduce light levels at any moment we need to,” said Wouter de Bruyn, the owner of Belgian lettuce grower De Glastuin, an early user of the new automatic feature.
Whereas Signify is known in office settings to build sensors into its smart luminaires, the GrowWise controls make use of sensors that are part of climate control systems and greenhouse management systems from companies such as Priva, Hoogendern Growth Management, and Ridder, all based in Holland.
Planet Farms’ Luca Travaglini backs up Signify’s point that prescribing a year of spectral content improves efficiency and helps keep down manual labor costs in controlled environment agriculture (CEA) operations such as vertical farms.
“The climate computer is equipped with a daylight sensor that sends actual light measurements to the GrowWise Control System so we can adapt our light levels automatically to ensure an even light level throughout the day and season,” de Bruyn said at De Glastuin, based in Kontich.
“Dynamic lighting in a greenhouse is the next step in improving the cost efficiency and quality for the cultivation process,” said Udo van Slooten, business leader, horticulture LED solutions at Signify. “It allows growers to effortlessly maintain a consistent level of light throughout the day to produce the best possible crops. The system compensates for cloudy weather and creates a more controlled growing environment for your crop.”
In another upgrade to GrowWise, vertical farmers who want to prescribe modulations in spectral content are no longer limited to 24 hours of looped recipe cycles. Rather, they can order up a year’s worth of shifts for controlled environment agriculture (CEA) operations.
The year-long programming feature is aimed at vertical farmers rather than at greenhouses because the lights that Signify provides for vertical farms support controllable spectral changes, whereas the greenhouse toplights do not. Signify refers to its GreenPower LED vertical farm lights as “production modules” rather than as “toplights.” Toplights and production modules can both be programmed for intensity over a year, but the intention of the year-long feature is oriented toward spectral content.
Compared to greenhouses, vertical farms tend to make much less, if any, use of natural light. In vertical farms, the lights are mounted much closer to the crop in stacked shelves.
One of the first users of the year-round feature is Italy’s greens and lettuce grower Planet Farms.
“Now we can easily create custom light recipes and set them to run year-round to provide the right light recipe with the right light intensity at the right time throughout the crop’s growth cycle,” said Planet Farms co-founder Luca Travaglini. “By automating our full light strategy during the growth cycle, for the whole year, we can run our operations very efficiently and keep our manual labor costs low. That makes it easier for us to maintain consistent quality as we scale up our production.”
The horticultural market is a key growth sector for Signify, especially as it maps out a strategy to maintain profits in the pandemic economy, in which last week it reported a yearly rise amid rigorous cost controls that now include a small number of layoffs. CEO Eric Rondolat is targeting a big chunk of what he has quantified as a $2 billion general horticultural lighting market by 2023.
MARK HALPER is a contributing editor for LEDs Magazine, and an energy, technology, and business journalist (markhalper@aol.com).
Delivering The Optimal Growing Parameters
“Especially in the pharmaceutical or supplemental industry, you need an extremely strict batch control that leaves no room for variation,” says Dr Alexis Moschopoulos, Managing Director at Grobotic Systems.
The Grobotic Systems team shows off an early prototype Grobotic chamber. From left to right: Gareth Coleman (Software Developer), Richard Banks (Chief Technology Officer), Dr Alexis Moschopoulos (Managing Director), and Andrew Merson (Mechanical Engineer). Credit: UKRI.
Growing a new variety
Indoor farming has numerous growing parameters to take into account. Particularly when growing a new variety, all variables should be perfected in order to reach an optimum yield. In an indoor space, experimenting with these environmental parameters might, however, seem tricky. But what about trying out this environment in a smaller setting, such as an experimental growth chamber?
Alexis is fully aware of the challenges that vertical farmers face. The environmental control needs to be as precise as possible, as the effect of different light spectra or nutrients may have a significant impact on crop yield and quality. With this challenge in mind, Grobotic Systems brings a new solution to the market: a compact and highly instrumented growth chamber. “It’s an experimental chamber rather than a farming chamber. Therefore, you won’t use it to grow vegetables, but you can use it to identify which growing parameters are best suited to your crops,” Alexis says.
The Grobotic Systems team outside their workshop in Sheffield, England. From left to right: Dr Alexis Moschopoulos, Richard Banks, Andrew Merson, and Gareth Coleman. Credit: UKRI.
On your desk or under your bench
According to Alexis, the chamber fits on your desk or under your bench. It can apply any environmental condition preferred, including light spectra and temperature. Internet connection via the growth chambers allows users to monitor plants on their cellphones via integrated cameras and other sensors inside the chamber.
Another advantage of the chambers’ size is that they can be stacked in an array, adjusting variables in each chamber. In this way, a multi-variable experiment can help users identify which environment works most optimally for their intended crop. “When using a large cultivation room, it is hard to split the room into different temperatures. A smaller cultivation space, such as our growth chambers, can be placed anywhere, just like a personal computer. Moving away from the large expensive capital equipment and machinery to small and stackable experimental chambers saves a lot of space and money.”
Alexis first came up with the concept of the growth chamber during his PhD and postdoctoral work in plant genetics. Several prototypes are currently being used at research institutes and start-up companies. Grobotic Systems is working on a more advanced growth chamber that will be launched in the summer of 2021: “We are integrating feedback from the deployed prototypes into the design of the advanced chamber, and we will start marketing the advanced chamber later this year.”
Richard Banks designs a control system circuit board for an early prototype Grobotic chamber. Credit: UKRI.
Large-scale farms
Not only new farmers can benefit from running small-scale experiments in a growth chamber, but also large-scale, established farms, since the chamber allows them to experiment with new varieties, creating the optimal yield. This will in turn enable them to upscale their production. “Not all farmers like to invest their time in carrying out experiments, as some trust that the vertical farming technologies they buy will always work for them. However, in the end it could save them a lot of money. No one needs to use productive farm space to do the experiments, just a few manageable boxes can suffice.”
Gareth Coleman works on the chamber imaging and control systems. Credit: UKRI.
For more information:
Grobotic Systems
Dr Alexis Moschopoulos, Managing Director alexis@groboticsystems.com
www.groboticsystems.com
Author: Rebekka Boekhout
© VerticalFarmDaily.com
Columbia Vertical Farm Uses Technology To Cut Plastic Pollution And Boost Sustainability
The new packaging comes at no extra cost to the customer and will be cheaper in the long-run for Vertical Roots
Vertical Roots is the largest hydroponic container farm in the country. They grow and package lettuce varieties and have recently implemented a packaging process that reduces plastic with a resealable film. TRACY GLANTZ TGLANTZ@THESTATE.COM
With the use of agricultural technology, Vertical Roots farm in West Columbia created a packaging system for its leafy greens that cut down the company’s plastic usage by 30% and extends the shelf life of the lettuce.
In 2015, high school friends Andrew Hare and Matt Daniels created the idea for Vertical Roots, now the largest hydroponic container farm in the country. Hare is the general manager of the company and Daniels acts as the chief horticulturist.
The first Vertical Roots opened in Charleston and expanded with its second farm site in West Columbia in 2019. Vertical Roots parent company, AmplifiedAg, manufactures the container farms and farm technology of which Vertical Roots operates.
The farms are part of a growing industry called controlled environmental agriculture (CEA) that uses technology to ramp up nutrient-rich food production year around.
Hydroponics helps the farm uses 98% less water than traditional farming, according to Hare. Their technology creates an indoor environment to grow lettuce on the East Coast. Most lettuce in the U.S. comes from California and Arizona, where temperatures do not fluctuate much throughout the year, travelling 2,000 miles from farm to table. Vertical Roots offers a solution for local lettuce.
“Our mission is to revolutionize the way communities grow, distribute and consume food,” said Hare. As populations grow, Hare said the ability to produce enough food is a global concern.
VERTICAL ROOTS AGRICULTURAL INNOVATION
As a company committed to sustainability, Vertical Roots had to address its plastic usage and the consumer demand for environmentally friendly products.
“I think everyone can agree that the amount of plastic that’s consumed and used globally is a bit of a problem,” said Hare.
If Vertical Roots were to completely opt-out of using plastics, as much as 40% of the lettuce would be damaged in transportation to the retailers, Hare said. So the company decided to still use plastic containers in order to cut out food waste, but it changed the amount and type of plastic used.
By replacing the conventional “clamshell” plastic lids that you see on a container of lettuce at the grocery store, Vertical Roots cut down more than 30% of plastic usage by creating a resealable film lid. The new packaging comes at no extra cost to the customer and will be cheaper in the long-run for Vertical Roots, according to Hare.
The farm also uses recycled plastic that can also be recycled again after use. Tiny perforations in the film lid of the packaging allow air to leave the lettuce container and extends the product’s freshness, making Vertical Roots lettuce last around 14 days on the shelf.
“We tested respiration and condensation with each lettuce variety, and ultimately found that we could extend the freshness and shelf life of our salad mixes even more,” said Hare.
Vertical Roots, at the S.C. Farmer’s Market, is the largest hydroponic container farm in the country. They grow and package lettuce varieties. Tracy Glantz TGLANTZ@THESTATE.COM
GROWTH IN THE AGRICULTURAL TECHNOLOGY INDUSTRY
In the first three quarters of 2020, a record $754 million of venture capital was invested in the vertical farming industry, according to PitchBook data. This was a 34% increase from the entire previous year, Bloomberg reported in a January article.
A 2019 report from Global Market Insights showed that the vertical farming market size, or the number of potential customers or unit sales, surpassed $3 billion in 2018 and said it, “will exhibit a massive compound annual growth rate (CAGR) of over 27% from 2019 to 2026.”
In vertical farms, crops are harvested on several vertical layers indoors, where farmers can grow year-round by controlling light, temperature, water and other factors, according to the U.S. Department of Agriculture.
Vertical agriculture is also seen as a growing industry because it “could help increase food production and expand agricultural operations as the world’s population is projected to exceed 9 billion by 2050,” according to the USDA.
However, some are skeptical about the future of vertical farming for several reasons. The farms use LED light bulbs to grow crops, which require a lot of energy and money to operate.
Also, the farms mostly produce greens, which are low in calories because they take less water and light. The new farming technology is marketed as a way to combat world hunger, but in poorer countries, low-calorie greens are not as beneficial, according to Bloomberg.
THE FUTURE OF VERTICAL ROOTS
Despite a tough year due to COVID-19, Vertical Roots will open two more indoor, container farms in Georgia and Florida in 2021.
The company lost revenue from foodservice customers like restaurants, schools and universities during the pandemic, said Hare.
Those food service customers accounted for about half of Vertical Roots’ business, Hare said. Grocery store business stayed steady and even grew during the pandemic. As schools and restaurants are slowly reopening, Vertical Roots is gaining business back.
The West Columbia farm location produces about $1.5 million pounds of produce per year, said Hare. Vertical Roots lettuce is in 1,200 different grocery stores in 11 states, including Lowes Foods stores, Publix, Harris Teeter and Whole Foods Market chains.
Hare said the company is constantly working on sustainable initiatives, including figuring out a way to reduce light energy consumption by 20-25%, thinking about compostable packaging systems and finding ways to use less water at the farms.
In the future, Vertical Roots hopes to offer a larger variety of produce. The team is experimenting with growing foods like tomatoes, cucumbers, peppers, herbs and mushrooms to see if they could be viable products.
At 25,000 square feet, the world's first indoor vertical farm is also one of the largest farms. Located 120 miles south of Seoul, South Korea, fruits and vegetables grow without soil, bathed in light from pink LEDs. BY META VIERS
1 of 3
Vertical Roots, at the S.C. Farmer’s Market, is the largest hydroponic container farm in the country. They grow and package lettuce varieties. TRACY GLANTZ TGLANTZ@THESTATE.COM
This Startup Wants Vertical Farmers To Hire A Robot Gardener
“By automating the production with robotics and remote monitoring, we can lower labor costs and offer solutions for food producers that are economically viable and environmentally sustainable,” the company claims on their website.
Arugula micro greens are grown at AeroFarms on February 19, 2019, in Newark, New Jersey.
Photo: Photo by Angela Weiss (Getty Images)
In recent years, vertical farming has emerged as a futurist’s solution to the world’s agricultural problems. The growing trend seeks to use controlled environments to boost food production, leveraging indoor labs where temperature, light, and nutrients can be mechanically controlled.
Yet while vertical farms have gained in popularity, they are also still very expensive. When compared to conventional farming, these farms necessitate the purchase of pricey equipment to aid human labor—a fact that, when paired with other economic pressures, has apparently led to an industry “littered with bankruptcies.”
One company hopes to change this dire picture. Enter Watney the robot.
Watney was designed by start-up Seasony. The company, which was featured today at this year’s Alchemist Accelerator’s Demo Day, has sought to make the tech-farming trend more accessible by automating away some of the more difficult labor involved.
Image: Screenshot: Youtube/TV2LORRY
“By automating the production with robotics and remote monitoring, we can lower labor costs and offer solutions for food producers that is economically viable and environmentally sustainable,” the company claims on their website.
Indeed, Watney is designed to augment (and, in many ways, replace) a human labor force—currently one of the biggest expenditures for vertical farms. Essentially an intelligent, automated cart, the robot was designed to “move and transport plant trays” within a farming hub. In techno-jargon, it is an autonomous mobile manipulation robot (AMMR), a type of machine known for moving and manipulating items on its own. It is also equipped with a camera that captures image data and sends it back to farm management software for human analysis. Watney also gathers valuable horticultural data to help farmers optimize yields, said Christopher Weis Thomasen, Seasony’s CEO and Co-Founder, in an email.
From left to right: Erkan Tosti Taskiran, Servet Coskun and Christopher Weis Thomasen.
Photo: Photo from Seasony.
“We are doing for vertical farming what the integration of autonomous mobile robots did to amazon. We are able to decrease the costs of growing food in a vertical farm by alleviating the logistics pains of working from scissor lifts,” said Thomasen.
Thomasen, a mechanical engineer, and his two co-founders electrical engineer Servet Coskun and business specialist Erkan Tosti Taskiran, were inspired to create the business while brainstorming what it would take to sustain life in outer space (Watney the robot is named after Mark Watney, the astronaut in the movie The Martian, who, after being stranded on the Red Planet, fertilizes potatoes with his own poop to survive).
“It quickly evolved to Seasony setting up a vertical farming lab and exploring the technical challenges facing the new industry. Reducing the costs related to labor is key in order to scale vertical farming and make agriculture more sustainable,” Thomasen said.
There is, of course, some debate in the farming community about the social costs incurred through the large-scale displacement of human labor.
Presumably, we will have to wait to see what that cost-saving process looks like. Seasony, which is still getting off the ground, plans to do a pilot trial with the largest vertical farm in Europe in April. It has plans to conduct further testing with several smaller vertical farms, as well, Thomasen said.
Lucas Ropek
Staff writer at Gizmodo