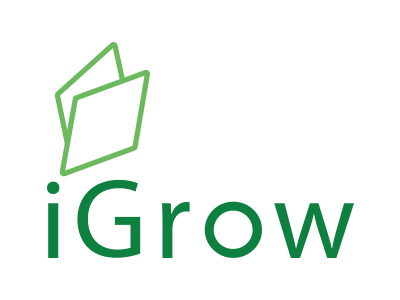
Welcome to iGrow News, Your Source for the World of Indoor Vertical Farming
How Can The World Benefit From Indoor Vertical Farming
Due to urbanization and enormous industrial development, we are losing our natural sources and farming land each year, bit by bit
by Bhok Thompson in Lifestyle
Have you ever sat down and wondered about the uncertainty of our future? With the world population growing and expanding each day, will we reach a point where we might face a scarcity of food? It has been speculated that three decades later, our world population will reach nearly 10 billion people. And feeding such a massive population is nothing less than a challenge.
Due to urbanization and enormous industrial development, we are losing our natural sources and farming land each year, bit by bit. As a matter of fact, according to a report published in 2015, our planet has lost 1/3 of its cultivable lands, which is quite alarming given the fact that our population is expanding each year.
That said, nothing can be predicted for sure about how much more arable land humanity will lose in the upcoming decades. Nonetheless, food demands will continue to grow proportionally to the growth of the world population. Many believe that vertical farming and indoor vertical farming software installation is the ultimate solution to our potential world hunger problems.
Read on to find out more about vertical farming and the future of our agriculture. Let us cover the basics first:
What Exactly is Vertical Farming?
You might have already figured out that vertical farming is all about producing and cultivating food on specifically vertically inclined surfaces. Instead of the traditional food cultivation methods of farming veggies and other food items on horizontally inclined surfaces, such as greenhouses and agriculture fields, the method of vertical farming intends to produce foods in vertically established layers with structures resembling a skyscraper. Nonetheless, the structures can also identify a shipping container and a warehouse.
For the effective production of foods in the vertical farming method, the integration of technology is mandatory. This is where the indoor vertical farming software comes in. With the integration of CEA (Controlled Environment Agriculture) technology, indoor vertical farming has been made possible.
The integration of the technology includes induced control of humidity, light, climate, temperature, and artificial gases that contribute to the possibility of growing indoor foods, herbs, and medicine. In this way, you can think of vertical farming in terms of a greenhouse where natural sunlight is induced with the help of metal reflectors and artificial light sources.
Nonetheless, indoor vertical farming’s primary goal is the optimization of food production within a limited space.
Why The World Needs Indoor Vertical Farming Software?
Vertical farming is the ultimate solution that can save us from hunger and starvation in the long run. Vertical farming allows more output and food production while using a small area of cultivation. The below-given list includes the essential benefits of vertical farming:
Preparing for The Future
As we mentioned earlier, four decades from now, our world population is more likely to expand to 10 billion. Not to mention that nearly 70% of the world population is expected to live in industrialized and urbanized areas, which will also peak food demand. The proficient use of vertical farming will prepare us for any upcoming challenges related to food scarcity.
All-Season Crop Production
Vertical farming enables us to produce more crops while using the limited square footage of the production area. If we were to make a rough estimation about the potential crop production, you could think of it in the following ways. For example, one acre of the indoor vertical farming area will allow you to produce crops worth four to six acres of outdoor capacity. Suppose you are running an indoor vertical farm inside a 30-story skyscraper that includes a basal area of five acres. With the integration of vertical farming software, you will produce food/ crops worth 2500 acres.
Unaffected by Weather and Climate Issues
Amongst the top benefits of indoor vertical farming is that this farming method is explicitly unaffected by unfavorable outside temperatures and weather conditions. Since everything is controlled and monitored inside, the crops and foods cultivated with indoor vertical farming are least affected by natural calamities. That said, indoor vertical farming allows you to produce food throughout the year without worrying about favorable weather conditions.
Indoor vertical farming is also good for biodiversity. This method is essentially environment friendly and exposes farmers to lesser risks and diseases.
The World’s First Autonomous Greenhouse Manager
Geert van der Wel started in the role of Autonomous Greenhouse Manager at Blue Radix. He represents the human support side of the Crop Controller service in addition to the smart algorithms that control greenhouses
07-04-2021 | Goedemorgen
Early February, Geert van der Wel started in the role of Autonomous Greenhouse Manager at Blue Radix. He represents the human support side of the Crop Controller service in addition to the smart algorithms that control greenhouses. Read more about how Geert helps customers and about his background. As he says himself: "I was almost literally born among tomatoes in De Lier, where my parents had a tomato greenhouse."
Name: Geert van der Wel
Home: I’ve been married to Tessa for 16 years and we have two children. We have lived in Burgundian West Brabant since 1998.
Childhood: Almost literally, I was born among the tomatoes in De Lier, where my parents had a tomato greenhouse.
Study: I completed Secondary Horticultural School in De Lier, and also undertook several (horticultural) studies.
Work experience: I worked in my parents’ tomato greenhouse right from my childhood. After finishing my studies my partner and I became owners of Kwekerij Polderwel for ten years, growing tomatoes on 2.5 hectares. We wound up this undertaking because of the construction of the A4 highway between Antwerp and Rotterdam. Then I did three years as a manager at the Nuijten plant nursery, and when this firm ceased trading I ended up at Nickerson-Zwaan in Made; it later became known as Hazera Seeds. For the first four years, I worked in the Planning & Control department, moving on to become Product Manager High-Tech Tomatoes for the final five years.
What can you do for growers as an Autonomous Greenhouse Manager?
“Blue Radix offers autonomous growing as a service. So alongside our smart algorithms controlling the greenhouse, our Crop Controller service also has a ‘human side’, and customers get daily support from an off-site Autonomous Greenhouse Manager (AGM). So as that AGM I’m constantly looking over the customer’s shoulder, and I’m their first point of contact. Right from the start, I guide clients intensively in taking their first steps into the world of algorithms. They are given an extensive onboarding program where they get explanations on the steps to autonomous growing, the operation of the algorithms, and the Crop Controller portal. I also monitor the management of the greenhouse continuously and discuss the progress on a regular basis, including through reports. My work experience has taken me through all the processes involved, from seed to the final product. This is what enables me to support our customers fully as AGM, to advise them, and to help them to realize their crop strategies.”
Blue Radix offers autonomous growing as a service; why is this important?
“Cultivation is the core business of every greenhouse company. To leave this completely to autonomous control requires a lot of trust from the customer. We are very aware that autonomous growing is still quite new and innovative. Providing good service with the support of the AGM lets us guide growers fully in working with algorithms. Our experience shows that customers are more likely to abandon their own processes and working methods step by step because there’s always someone monitoring the entire process.”
Describe your day. How do you monitor greenhouses worldwide?
“Every day I open the Crop Controller portal to see how the algorithms are behaving in terms of our various customers’ crop strategies. I contact the grower if any anomalies appear, or if there’s a technical issue I get in touch with the Blue Radix product developers. This also applies to feedback I receive from customers on how we can optimize Crop Controller still further.”
What do you like about your job? And what are your views on autonomous greenhouse management?
“In the horticultural world, it’s great to see that there’s a continuous search for innovations, and specifically for autonomous growing. I used sensors and digital tools on a small scale when I was a grower myself. But at that time I got very little guidance on how they worked and how to interpret it all. Now I use this experience to give our customers good information so that ultimately they’ll be able to grow autonomously in the best possible way!”
Got a question for Geert, or about autonomous growing generally?
Send us a message, and we’ll be happy to help you.
Expanding Controlled Environment Agriculture Beyond 'The Big 4'
Greenhouses, vertical farms, and hybrid systems (collectively known as controlled environment agriculture or CEA) continue to attract investment at a much greater scale than in previous decades
By PETER TASGAL
March 29, 2021
Greenhouses, vertical farms, and hybrid systems (collectively known as controlled environment agriculture or CEA) continue to attract investment at a much greater scale than in previous decades. In each of the past five years, there have been multiple nine-figure capital raises. Capital has been deployed across farm types:
Large-scale greenhouses (e.g., AppHarvest, Mastronardi Produce),
Regional greenhouses (e.g., Gotham Greens, Bright Farms),
Localized vertical farms (e.g., InFarm – Berlin, Kalera).
Sources of funding have expanded from almost exclusively highly-specialized private equity investors to include public equity, mezzanine debt and even commercial banks. Within these funding sources, the breadth of investors has expanded beyond agriculture-focused investors to more mainstream investors, especially those with an interest in Environmental, Social and Corporate Governance (ESG) investing.
More from The Packer: Deep dive on the economics of greenhouse growing
Despite all of the investment, the vast majority of produce grown in CEA’s across North America consists of tomatoes, cucumbers, peppers, and lettuce, and leafy greens (“The Big 4”). Most of the lettuce and leafy greens are coming from CEA’s in the U.S. In Canada, The Ontario Greenhouse Vegetable Growers include 220 members producing tomatoes, cucumbers, and peppers on over 3,000 acres of greenhouse.
In my opinion, the next leap for the industry will be expanding the breadth of products. Specifically, focusing on products the taste of which is highly important to the consumer. A strawberry, for example, is a more important purchasing decision to the average consumer compared to lettuce. Lettuce is much more likely to be eaten as part of a salad along with a variety of other ingredients. Today, you can buy at mainstream retail locations a greenhouse-grown strawberry likely grown by Mucci Farms in Ontario or Mastronardi’s Green Empire Farms in New York.
Consumer demand will continue to drive product expansion. Meeting that demand will be possible through further investment in the CEA space. Although investment has been growing, it has not met the levels of other industries where many billions of dollars have been invested on an annual basis. Investment levels in CEA are likely to become far greater over the near future as some of the largest investors in the world are focused on investments that meet and exceed ESG standards.
More from The Packer: On tour with AeroFarms
Efficient vertical farms and greenhouses meet and exceed ESG standards. The farms are closed-loop systems where everything that goes into the farm is contained and recycled. Additionally, as the environment is fully controlled, only the precise amounts of inputs are added so as to limit excess waste. Lastly, a controlled environment allows for plants to grow without chemicals and pesticides.
Combining consumers’ desire for more locally-grown produce throughout all seasons of the year with increased investor appetite should drive great growth across the industry for years to come. I believe the biggest leap will be new and exciting products coming from indoor farms. This will all be enhanced with incremental improvements in product taste, farm efficiency, and additional varieties within The Big 4 and other products to come.
Peter Tasgal is a Boston-area food agriculture consultant focused on controlled environment agriculture.
Vertical Farming Startup Oishii Raises $50m In Series A Funding
“We aim to be the largest strawberry producer in the world, and this capital allows us to bring the best-tasting, healthiest berry to everyone.”
By Sian Yates
03/11/2021
Oishii, a vertical farming startup based in New Jersey, has raised $50 million during a Series A funding round led by Sparx Group’s Mirai Creation Fund II.
The funds will enable Oishii to open vertical strawberry farms in new markets, expand its flagship farm outside of Manhattan, and accelerate its investment in R&D.
“Our mission is to change the way we grow food. We set out to deliver exceptionally delicious and sustainable produce,” said Oishii CEO Hiroki Koga. “We started with the strawberry – a fruit that routinely tops the dirty dozen of most pesticide-riddled crops – as it has long been considered the ‘holy grail’ of vertical farming.”
“We aim to be the largest strawberry producer in the world, and this capital allows us to bring the best-tasting, healthiest berry to everyone. From there, we’ll quickly expand into new fruits and produce,” he added.
Oishii is already known for its innovative farming techniques that have enabled the company to “perfect the strawberry,” while its proprietary and first-of-its-kind pollination method is conducted naturally with bees.
The company’s vertical farms feature zero pesticides and produce ripe fruit all year round, using less water and land than traditional agricultural methods.
“Oishii is the farm of the future,” said Sparx Group president and Group CEO Shuhei Abe. “The cultivation and pollination techniques the company has developed set them well apart from the industry, positioning Oishii to quickly revolutionise agriculture as we know it.”
The company has raised a total of $55 million since its founding in 2016.
Lisette Templin, Professor At Texas A&M University - A Pioneering Woman In Agriculture
Lisette Templin is the director and founder of the Texas Urban Farm United (TUFU - TAMU) a startup vertical farm she and a couple of students began in 2019
According to Lenny Geist and Anne Amoury, with Kansas Freedom Farms, one of many pioneering women in agriculture is Lisette Templin, a professor of health and kinesiology at Texas A&M University (TAMU) in College Station, Texas. Lisette Templin is the director and founder of the Texas Urban Farm United (TUFU - TAMU) a startup vertical farm she and a couple of students began in 2019.
As a faculty member overseeing Physical Education, Templin is keenly aware of how food choices and essential daily nutrition are to overall animal and human health.
She and her students received a small grant from the TAMU public health school to go vertical. Templin has a number of hydroponic growing towers in her new venue she and a few co-workers maintain. Some of the all-natural forage is donated to the university’s “12th Can” food bank program to alleviate local hunger...clearly one of Templin’s strongest passions.
Lisette Templin (Photo credits: Texas A&M University)
“Food as medicine must play a more urgent and vital role in the health of our children and the health of our country. Indoor hydroponic farms can play a pivotal role in transitioning people off of medication from chronic diseases as well as strengthen the immune system.
Micro and macronutrient dense food grown locally can effortlessly replace food that is highly inflammatory to the human body while providing the needed phytochemicals that promote health,” she wrote recently. Templin is in the process of applying for grants and financial support in hopes of raising $1 million (USD) to erect a two-story CEA facility that will be home to hydroponic growing operations on the top floor with a kitchen, cafeteria, classrooms, and offices on the ground floor.
Photo credits: Texas A&M Urban Farm United / The Eagle
“Hydroponic food is about the impact of delivering maximum nutrient density to the immediate local community. Hydroponic vertical growing technology's innate potential is its ability to eradicate food deserts across our country,” Templin says. Clearly, she’s a Texas trailblazer with tall towers to tend.
According to Lenny Geist, "we need more like Templin, to improve agriculture and promote environmental stewardship. It behooves the stuffed shirts to follow the determined bunch out on the “north 40” -- the bunch that likes to wear Gucci or Louis Vitton heels just as much as they do Justin or Tony Lama boots."
"They aren’t afraid of hard work, trying new things, and exploring what’s possible even if it means a setback or two along the way," he adds. "Since they see these as learning opportunities to get better and march forward toward their ultimate objectives having gained greater perspectives. Someday, these movers and shakers or any of their sure-to-follow feminine disciples may just give the old, stodgy stuffed shirts the boot. There are lots of reasons to believe this will be for the best."
For more information:
Lisette Templin,
Texas A&M, Texas Urban Farm United
lisettetemplin@tamu.edu
www.agrilifetoday.tamu.edu
29 Mar 2021
Evaluating Real Estate For Indoor Agriculture
Several factors need to be evaluated before purchasing or leasing a piece of real estate for CEA. Will you build new construction or rehabilitate a vacant building? Are you building a large-scale greenhouse or a small, urban vertical farm?
March 17, 2021
Traditionally, buyers of agricultural real estate have focused on rural land where primary considerations for their farm include things such as soil quality, annual rainfall amounts, and adequate drainage. Increasingly, however, agriculture start-ups are moving indoors. Compared to field-based agriculture, indoor farming allows for more crop cycles, less water usage, and the farms can be located closer to the consumer. The considerations for an indoor, or controlled environment agriculture (CEA) operation are considerably different than for outdoor farms.
Assessing Potential Real Estate for CEA
Several factors need to be evaluated before purchasing or leasing a piece of real estate for CEA. Will you build new construction or rehabilitate a vacant building? Are you building a large-scale greenhouse or a small, urban vertical farm?
Environment
Weather and terrain are important for natural light greenhouse projects. The primary limiting factor to crop production in a greenhouse is low light intensity during the winter so consult with an Ag-extension service or other resource to get that information for a proposed location. Adequate acreage is a must for not only the greenhouses themselves but, also shipping and receiving space, a retention pond (if needed), and potentially even worker housing.
Spacing
For a vertical or urban farm in an enclosed building, important factors to consider include adequate square footage to allow for proper spacing between growing systems and enough room to move the towers (if mobile) for cleaning or maintenance. Additionally, a building should have a sufficient water supply and potentially drainage, a robust HVAC system and humidity controls, and a ceiling which is high enough for the growing towers. Although indoor farms using high efficiency LED lighting, these systems, combined with pumps, humidifiers, and HVACs can use significant amounts of electricity, a developer should carefully and conservatively estimate those costs prior to negotiating those terms with a landlord or electric company. Finally, the farm should be in close enough proximity to allow for routine delivery to local customers, be they restaurants, groceries, farmers markets, or Community Supported Agriculture distributors.
Labor
In both types of farms, labor availability and cost is a critically important consideration. The cost of wages for urban farms, even for unskilled workers, will likely be higher than that of rural areas. And in the case of any real estate development, ensure prior coordination with relevant agencies has been done on permits, licenses, and zoning regulations prior to signing any leases or closing on a land contract. Prior to starting a search for a CEA project, it’s wise to seek expert help from outside consultants who can save an indoor farm developer time, money, and aggravation.
Tags real estate, indoor agriculture, cea
FRANCE: Jungle Says It’s Cracked How To Make Vertical Farms Profitable
“No matter how good your product is, if the price is higher than the alternative, then you’re dead.”
“No Matter How Good Your Product Is,
If The Price Is Higher Than The Alternative,
Then You’re Dead.”
BY FREYA PRATTY
22 MARCH 2021
Jungle, a French vertical farming company that says it can produce ten to 30 times more food than traditional greenhouses, has raised €42m in new funding.
The company also says its focus on large-scale farms will help it overcome one of the biggest challenges facing vertical farming: how to make a profit.
Jungle’s new funding, €7m of which is in equity and €35m of which is debt financing, comes from Founders Future, a French investment firm focused on impact startups. Jungle is the firm’s first investment.
The company’s funding comes as the wider industry continues to grow fast. It was worth $2.2bn in 2018 but is expected to reach $12.8bn by 2026. Investor appetite is clearly there: vertical farming giant Infarm raised $170m at the end of last year.
Jungle is building a 5,500m2 farm 80km from Paris, where crops will grow on stacked platforms. The site is already partly operational and the company has secured contracts with French supermarkets Monoprix and Intermarche.
At present, it’s growing a mixture of aromatic herbs, greens and, unlike other vertical farms, flowers. It’ll be fully operational by the end of 2021.
Less pesticides, more local and a greater yield
Gilles Dreyfus, cofounder of Jungle.
“We don’t claim to be instigating a revolution, we are part of an equation that wants to be a solution,” explains Gilles Dreyfus, who cofounded Jungle in 2015.
For Dreyfus, vertical farming has several advantages. Crops can be grown close to cities, where the majority of consumers are, thereby reducing the environmental costs of transit.
Plants can also be grown on more frequent cycles than on traditional farms because they’re not seasonally dependent, and they’re also grown without using pesticides.
“Our most popular product, Green Basil, gives 14 harvests a year in the vertical farm, compared to 3 or 4 in the South of France, where the crop grows best outdoors.”
National food sovereignty
Being able to grow crops out of season means vertical farming can help countries achieve better food sovereignty, Dreyfus says.
“We have to go further and further from the country to get crops when they’re out of season,” he says. “Brexit import taxes on food have shown the complicated situations this can lead to.”
“If the price is higher, you’re dead”
Despite the benefits, vertical farming has often struggled with how to make a profit. “Having a viable financial model and an efficient farm is the main hurdle for vertical farming,” Dreyfus says.
“No matter how good your product is, if the price is higher than the alternative, then you’re dead.”
The company believes that bigger farms is the answer.
German company Infarm, which is aiming at profitability by 2023, places microunits into supermarkets. Jungle, which is aiming at profitability in 18 months time, will focus on large-scale production facilities that then supply a whole area.
“Price depends on scale and we’re not aiming for small-scale farms, we’re aiming for less farms but a lot bigger. If you activate the economies of scale you can get a very reasonable product,” he says.
The company’s aiming to sell food at 5% more than the cost of conventional alternatives, but at 20% less than organic foods grown on farms.
For Valentine Baudouin, partner at Founders Future which has invested in Jungle, the focus on large-scale farms is the key to profitability, and what makes Jungle stand out.
“They’ve answered the economic question of vertical farming, which is very important because you have many similar enterprises that haven’t done so.”
Jungle’s vertical farm warehouse.
Beyond salad?
A criticism often leveled at the vertical farming industry is whether it can grow beyond just salad leaves and herbs.
Unlike other farms, Jungle also grows flowers for the perfume industry, but Dreyfus says the other crops its working on, including cherry tomatoes and mushrooms, won’t be in supermarkets until 2023.
“You can grow virtually anything you want, except truffles — which is a real shame actually,” says Dreyfus. “But the question shouldn’t be, can we grow it, it should be, do we have the financial model to make it work?”
Jungle’s currently got a team of 25 people based in France, but will use the new funding to double its workforce by 2022. It also plans to open two new large-scale farms in France, including one in the south that’ll be twice as big as its first site.
Freya Pratty is Sifted’s news reporter. She tweets from @FPratty
VIDEO: Inside A Shipping Container Vertical Farm
New farming models are cropping up around the world, including in Sydney, where Sprout Stack is transforming old shipping containers into commercial vertical farms
March 17, 2021
New farming models are cropping up around the world, including in Sydney, where Sprout Stack is transforming old shipping containers into commercial vertical farms.
With lighting in the containers designed to optimize plant growth, and sensors measuring temperature, humidity, and carbon dioxide, the approach is more productive than traditional farming — and uses 95 percent less water.
Take a look inside Sprout Stack’s vertical farms.
Indoor Agtech: An Evolving Landscape of 1,300+ Startups
Our Indoor AgTech Landscape 2021 provides a snapshot of the technology and innovation ecosystem of the indoor food production value chain
March 17, 2021
Editor’s note: Chris Taylor is a senior consultant on The Mixing Bowl team and has spent more than 20 years on global IT strategy and development innovation in manufacturing, design, and healthcare, focussing most recently on indoor agtech.
Michael Rose is a partner at The Mixing Bowl and Better Food Ventures where he brings more than 25 years immersed in new venture creation and innovation as an operating executive and investor across the internet, mobile, restaurant, food tech and agtech sectors.
The Mixing Bowl released its first Indoor AgTech Landscape in September 2019. This is their first update, which you can download here, and their accompanying commentary.
Since the initial release of our Indoor AgTech Landscape in 2019, the compelling benefits of growing food in a controlled indoor environment have continued to garner tremendous attention and investment.
One of the intriguing aspects of indoor agriculture is that it is a microcosm of our food system. Whether within a greenhouse or a sunless (vertical farm) environment, this method of farming spans production to consumption, with many indoor operators marketing their produce to consumers as branded products. As we explore below, the indoor ag value chain reflects a number of the challenges and opportunities confronting our entire food system today: supply chain, safety, sustainability, and labor. Of course, the Covid-19 pandemic rippled through and impacted each aspect of that system, at times magnifying the challenges, and at others, accelerating change and growth.
Invest with Impact. Click here.
Our Indoor AgTech Landscape 2021 provides a snapshot of the technology and innovation ecosystem of the indoor food production value chain. The landscape spans component technology companies and providers of complete growing systems to actual tech-forward indoor farm operators. As before, the landscape is not meant to be exhaustive. While we track more than 1,300 companies in the sector, this landscape represents a subset and serves to highlight innovative players utilizing digital and information technology to enhance and optimize indoor food production at scale.
Supply chain & safety: Where does my food come from?
The pandemic highlighted the shortcomings of the existing supply chain and heightened consumer desires to know where their food comes from, how safely it was processed and packaged, and how far it has travelled to reach them. A key aspect of indoor farming is its built-in potential to respond to these and other challenges of the current food system.
Indoor farmers can locate their operations near distribution centers and consumers, reduce food miles and touch points, potentially deliver consistently fresher produce and reduce food waste, and claim the coveted “local” distinction. The decentralized system can also add resiliency to supply chains overly dependent on exclusive sources and imports.
Growing local has many forms. Greenhouse growers tend to locate their farms outside the metropolitan area while sunless growers may operate in urban centers, such as Sustenir Agriculture in Singapore and Growing Underground in London. Growers like Square Roots co-locate their indoor farms with their partner’s regional distribution centers, and Babylon deploys its micro-farms solution on site at healthcare and senior living facilities and universities. Recently, Infarm announced it was expanding beyond its growing-in-a-grocery store model, to include decentralized deployments of high-capacity “Growing Centers” across a number of cities. Additionally, the value of “growing local” might take on a much larger meaning if your country imports most of its produce from other countries; a number of the Gulf region countries have announced major indoor growing initiatives and projects with AeroFarms, Pure Harvest, and &ever to address the region’s food dependence on other countries.
Organic produce sales jumped to double digit growth in 2020 as consumers are increasingly mindful of the healthiness of their food. The additional safety concerns due to the pandemic only accelerated this trend. While not typically organic, crops produced in the protection of indoor farms are isolated from external sources of contamination and are often grown with few or no pesticides. Human touch points are reduced as supply chains shorten and production facilities become highly automated. Through the CEA Food Safety Coalition, the industry has recently taken steps to establish production standards with a goal to keep consumers safe from foodborne illness.
Indoor farmers market their products as local, fresh, consistent and clean. This story is resonating with consumers as the growers seem to be selling everything they can produce, with many reporting significant sales growth in 2020. The direct connection to consumer concerns is also a key part of their ability to sell their branded products at a premium, which has been critical to financial viability for some growers. This connection can also enable them to collapse the supply chain further, at least at smaller scales, through direct sales and creative business models, e.g., sunless grower Willo allows subscribers to have their own “personal vertical farm plot” and watch their plants grow online.
Sustainability: Is my food part of the problem or part of the solution?
Farming, as with most industries, has been under increasing pressure to operate more sustainably, and indoor growers, with their efficient use of resources, have rightfully incorporated sustainability prominently into their narratives.
We are well aware of the impacts of climate change, including greater variability in weather patterns and growing seasons. The UN’s Food and Agriculture Organization projects that over the coming decades climate change will cause a decrease in global crop production through traditional farming practices, causing greater food insecurity. Indoor growing, which provides protection from the elements, consistent high yields per land area, and the ability to produce food year-round in diverse locations, including those unsuitable for traditional agriculture, can help mitigate this trend.
Water scarcity is projected to increase globally, presenting a national security issue and serious quality of life concerns. According to the World Bank, 70% of the global freshwater is used for agriculture. Indoor agriculture’s efficient use of water decreases use by more than 90% for the current crops under production. It is also common practice for greenhouses to capture rainwater and reuse drainage as does Agro Care, the Netherlands’ largest greenhouse tomato grower.
On the flip side, energy use, particularly in sunless facilities, is indoor growing’s sustainability challenge. Efficiency will continue to improve, but as recent analysis on indoor soilless farming from The Markets Institute at WWF indicated, there is an industry-wide opportunity to integrate alternative energy sources. Growers recognize this opportunity to decrease impact and improve bottom-line and are already utilizing alternative approaches such as cogeneration, geothermal sources, and waste heat networks. H2Orto tomatoes are grown in greenhouses heated with biogas generated hot water. Gotham Greens’ produce is grown in 100% renewable electricity-powered greenhouses, and Denmark’s Nordic Harvest will be running Europe’s largest indoor farm solely on wind power.
Labor: We’re still hiring!
There are labor challenges and opportunities throughout the food system value chain, and this couldn’t be more acute than on the farm. Farm operators—both in-field and indoor—find it difficult to attract labor for the physically demanding work. Even before the pandemic, the hardening of borders in Europe and the US created a shortage of farmworkers for both field and greenhouse production. In addition, grower and farm manager-level expertise is in short supply, exacerbated by an aging workforce and the rapid addition of new indoor facilities. While operators would like to see more trained candidates coming from university programs, they are also looking to technology and automation to relieve their labor challenges.
Automation of seedling production and post-harvest activities is already well established for most crops in indoor farming. In addition, the short growth cycle and contained habit of leafy greens lends them to mechanization. For example, the fully automated seed-through-harvest leafy green systems from Green Automation and Viscon have been deployed in major greenhouse operations like Pure Green Farms and Mucci. On the sunless side, Urban Crop Solutions has uniquely implemented automation in shipping containers, and Finland’s NetLed has developed a fully automated complete growing system. Note that many of the larger-scale sunless growers have developed their own technology stacks and have designed labor-saving automation into their systems. For example, Fifth Season has robotics deployed throughout the entire production process.
Despite numerous initiatives, the challenging daily crop care tasks and harvesting for certain crops (tomatoes, peppers, cucumbers, and berries) have not yet been automated at scale. However, planned, near-term commercial deployments of de-leafing and harvesting robots offer the promise of significantly altering labor challenges. Software technologies, like those from Nitea and Hortikey address labor management, crop registration, yield prediction, and workflow/process management for the indoor sector and strive to improve operational efficiencies for a smaller workforce.
Technologies that provide, monitor, and control climate, light, water, and nutrients are already deployed in today’s sophisticated indoor growing facilities and are fundamental to maintaining optimal conditions in these complex environments. They also form the base for the next innovation layer, i.e., crop optimization and even autonomous control of the growing environment based on imaging and sensor platforms (like from Ecoation, iUNU, and 30MHz), data analysis, machine learning, digital twins and artificial intelligence. Recent events like the Autonomous Greenhouse Challenge have successfully explored the potential of AI to “drive horticultural productivity while reducing resource use and management complexity”. Emerging commercialized autonomous growing innovations, such as the Blue Radix Crop Controller and Priva’s Plantonomy, promise to extend and enhance the reach of available grower expertise, particularly in large and multi-site operations.
Where do we go from here?
Since we created our initial Indoor AgTech Landscape, there has been positive change and reason to be optimistic about the future. But, as with any evolving market and sector of innovation, it can be a bumpy ride. Some believe CEA is not the answer to our food problems because not everything can be economically grown indoors today. We see indoor ag as just one of the approaches that can help fix our food system and it should be applied when it makes sense. For example, tomatoes sold through retail are already more than likely grown in a greenhouse. Expect more crops to be grown indoors more economically with further advancements.
One aspect of our previous landscape was to increase awareness that, despite the fervor surrounding novel sunless farming, greenhouse growing was already well-established. Dutch greenhouse growers have demonstrated the viability of indoor growing with 50-plus years of experience and more acres “under glass than the size of Manhattan.” The recent public offering and $3 billion market cap of Kentucky-based greenhouse grower AppHarvest also clearly raised awareness! Other high-profile and expanding greenhouse growers, including BrightFarms and Gotham Greens, have also attracted large investments.
The question is often asked, “which is the better growing approach, sunless or greenhouse?”. There is no proverbial “silver bullet” for indoor farming. The answer is dictated by location and the problem you are trying to solve. A solution for the urban centers of Singapore, Hong Kong and Mumbai might not be the same as one deployed on the outskirts of Chicago.
Regardless of approach, starting any type of sizable tech-enabled indoor farm is capital intensive. A recent analysis from Agritecture indicates that it can range from $5 to $11 million dollars to build out a three-acre automated farm. Some of the huge, advanced greenhouse projects being built today can exceed $100 million. Given the capital requirements for these indoor farms, some question the opportunity for venture-level returns in the sector and suggest that it is better suited to investors in real assets. Still, more than $600 million was raised by the top 10 financings in 2020 as existing players vie for leadership and expand to underserved locales while a seemingly endless stream of new companies continue to enter the market.
Looking forward, indoor farming needs to address its energy and labor challenges. In particular, the sunless approach has work to do to bring its operating costs in line and achieve widespread profitability. Additionally, to further accelerate growth and the adoption of new technologies in both greenhouse and sunless environments, the sector needs to implement the sharing of data between systems. Waybeyond is one of the companies promoting open systems and APIs to achieve this goal.
As we stated in the beginning of this piece, the indoor ag value chain reflects some of the challenges and opportunities confronting our entire food system today: supply chain, safety, sustainability, and labor. Indoor agriculture has tremendous opportunity. While it is still early for this market sector overall, it can bring more precision and agility to where and how food is grown and distributed.
While Everything Is Falling Apart, It Could Be Easy To Miss The Incredible Opportunities That Are Coming Together Right Now
Check out the awesome opportunities growing on with access to the CEA census provided by Agritecture Autogrow and global market reports by Forward Fooding and United Nations
Take a look at the state of agriculture renaissance, with thousands of companies, and millions of people working toward food system transformation designed to sustainably feed 10B people, with 70% living in cities, using less energy, water, and waste, and reversing climate change.
Check out the awesome opportunities growing on with access to the CEA census provided by Agritecture Autogrow and global market reports by Forward Fooding and the United Nations
Some of the Numbers:
5.3k+ companies
$65B invested since 2010
$17B 2020 (up from $15B 2019) 42% CAGR
21% of funding went into AgTech and CEAs
5% went to digital services
48% to food delivery
Impact is being divided into five sustainable food action tracks - 10% Access, 35% Consumption, 40% Production, 5% Equity, and 15% Resilience aimed at innovative disruption.
Out of 300+ CEAs
40% were founded in the last two years
36% got funding from family and friends
35% from angel investors
80% were operating in indoor vertical farming
49% had no agriculture experience
46% were between ages 21-30
28% prefer using Coco Coir as a soilless growing medium
Largest crops microgreens, salad greens, leafy greens and herbs.
How Vertical Farms Are Revolutionizing Agribusiness
What is vertical farming and why does it matter?
William Ramstein ・ 1 March 2021 ・ Vertical Farming
Urban planners are tasked with answering some pressing inquiries: how can farming be brought closer to consumers; is digital agriculture an essential ingredient for making cities smarter; and can vertical farming improve socio-economic disparities?
Key Takeaways:
Vertical farming uses LED, Robotics and AI to bring vegetables closer to city dwellers.
The total addressable market for vertical farming is estimated at around $700 billion.
Spread, a Japanese vertical farm is profitable but most firms fail.
Vertical farming is a great way to produce controlled supplies of a customized plant.
Vertical farming struggles with electricity costs despite reducing carbon emissions.
What is vertical farming and why does it matter?
The bedrock characteristic of cryptocurrency technology is called decentralization, a sovereign and flexible organizational system led by a commune, and today other industries like farming are catching the bug. Farming needs to change its practices in order to meet ecological objectives set up by governments and decentralization could open the door to increasing food access and reducing carbon emissions from food transportation. Smart decentralized vertical farming implies using technology like digital platforms, robotics and artificial intelligence to bring food closer to the growing demand seen in cities.
Despite the difficulty of competing against the cost structure of traditional farming, vertical farming offers numerous advantages. It grants more yield per square meter and reduces waste in both carbon and water usage. The production of vegetables is made in large and often times un-used warehouses close to city centers thus cutting transportation costs and middlemen expenses. The supply is more easily controlled, protected, and priced regardless of global weather and plants are customized to local consumer preferences. Consumers are already paying a premium on farmer’s market products, so why not vertical farm products too?
Cases of vertical farming: Nigeria is one of the most promising African nations because of its age pyramid. But with a large young population comes questions around food and water access and today, more than 170 million Nigerians need prolonged and sustainable access to these resources. Nigeria currently imports $3.5 billion worth of food products while exporting only 1/7 of that figure. Fresh Direct is Nigeria’s first Hydroponics Company (growing crops without standard soil) that combines vertical farming to its business model to reduce the distance between cities and rural farming regions.
The firm is able to produce seven to 10 times the yields because of its stackable shipping containers, which use technologies such as drip irrigation, and cold storage. Direct Farming operates with a community mindset, with the goal to inspire more young farmers to set up shop in urban centers and become urban farmers. The company also trains and finances low-skilled workers into urban farmers and increases economic productivity in unemployed youth groups.
In Japan, a company called Spread is one of the world’s most sophisticated examples of vertical farming. Their factory mainly produces lettuce. Large robotic arms transplant lettuce seedlings into pots where they are left to grow under LED lights. Believe it or not, but the factory can produce 30,000 lettuce heads a day. CEO Shinji Inada boasts of being the only large-scale vertical farm that is profitable and hopes that more widespread adoption continues growing.
However, companies like Spread and A-Plus (another similar farm in Fukushima) struggle to lower unit economics because of their low-scale operations, and they find it hard to penetrate the traditional downstream sellers. When producing high-priced lettuce by the tonne, trucking goods to the local wholesaler does not work partly because vertical farming offers customized products for specific local needs, not necessarily for broad demand. These players have thus geared their focus towards international buyers like UAE to export their goods.
Is vertical farming there yet?
Most vertical farms have failed because of the high initial costs and high operational expenses of running robotic equipment. While sunlight is free, the energy cost of running LEDs is not. The solution could be to install renewable energies like solar panels and wind turbines. However, the fixed cost of that installation would inevitably factor into the end-product, or at least on the balance sheet as a liability assuming they keep prices reasonable for consumers.
While Mr. Inada can rightly boast of turning profits, most firms toss lettuce at a loss. The industry should see more growth ahead, however, with research group IDTechEx forecasting that annual sales of $700 million could more than double to $1.5 billion in 2030. There remain technological challenges though. While many competitors boast of successfully leveraging AI and robotics and filtration, new entrants have seen problems with watering automation systems, mold, and infestations (most players do not use pesticides).
Some analysts suggest that while the excitement around vertical farms makes sense, the farming style might just end up becoming just another way of farming amongst greenhouse and open sky farms. More specifically, vertical farming will focus on high-margin crops rather than commodities like bulk grains.
While the challenges of vertical farming are clear, every country has different needs and constraints. There is a large interest from smaller island countries like Singapore or Iceland, rich economies, and countries that have a higher propensity to import due to less arable lands. Britain is a good example of a country that meets the criteria and in the context of Brexit, it makes all the more sense because of import costs and independence constraints. A potential labor crisis could soon loom too assuming seasonal workers are denied entry into the country. Vertical farms only require one-third of the manpower to run and could therefore alleviate the industry.
The market opportunity…According to research by Barclays Investment Bank, the market opportunity for vertical farms is large. Analysts estimate the size of the global fruit and vegetable market to be $1.2 trillion and the total addressable market for vertical farms to be $700 billion. The purchased energy use to produce 1kg of lettuce is 247-kilowatt hours far exceeding Netherland greenhouses’ 70-kilowatt hours consumption. With retailers being asked to meet more carbon-neutral objectives, some vertical farms believe they will be able to overcome their expense through increased demand and scale.
The pandemic has imposed many supply chains disruptions and labor shortages threatening food security in regions around the world relying heavily on imports. Vertical farming is recognized lately and since 2014, has seen a flow of funds equal to $1.8 billion according to data group Dealroom. SoftBank fundraised $140 million into Plenty, a start-up, and countries like Abu Dhabi want to build farms in deserts.
Some of the top players in the global farming market include Vertical Farm Systems (Australia), American Hydroponics (US), Agrilution (Germany), Green Sense Farms (US), Everlight Electronics (Taiwan), Koninklijke Philips (Netherlands), Sky Greens (Singapore), Illumitex (US), Urban Crop (Belgium), Aerofarms (US) and InFarm (Germany).
"We’re Retrofitting With The Variables We Have In Place"
Planted Detroit introduces new 20.000 sq. ft. growing facility
“The Square Room is a big block of pink lights with eight levels, where all our growing is done. Everything after germination is done in the same room, both harvesting of our baby greens and microgreens. Because we’re almost done with our PARS (Planted Automated Racking System), which is the big automation,” says Megan Burritt, Managing partner at Planted Detroit.
From a mix-fused downtown neighborhood in Detroit, daily deliveries of ready-to-eat salads and fresh greens are transported to local retailers and restaurants. Planted Detroit makes a large contribution to the city’s share of fresh produce.
New facility
Planted Detroit has been in the middle of the construction of its new 20.000 sq. ft growing facility. The growing space has been a massive update to the company compared to its previous 6-level growing facility which was between 1500-2000 sq. ft. The same room was used for processing, packaging, harvesting, and so on. “It was rather crowded, says Megan, but the main goal was to keep everything tight for the construction to continue in the near surrounding. We’re very serious about biosecurity and we have a daily procedure for everyone who sets foot in our grow room to go through. Making sure our greens don’t come into contact with pathogens is our top priority.
The new growing room
The Square Room, one of our growing rooms, is highly automated, including an automatic harvester to ensure work-efficiency. Once everything is big enough to be transplanted out of their plug trays, PARS (Planted Automated Racking System) will be transplanted with gutters and then go into harvesting. On the other side of PARS, the gutters are taken down and harvested through Planted’s new automatic harvester.
Delivering directly to consumers
The company wants to reach a higher volume of customers as it’s aiming to obtain a consumer brand status. Next to that, the company is always on the lookout for finding more customers through other venues. “We want to go directly to consumers via our web-store to shorten food miles as much as possible, delivering the freshest and most delicious greens,” Megan says. In order to do that the company needed to have a bit more scale, trying to maximize the space they already had.
She adds: “Our farm maybe isn’t the square footage which we could have built from scratch, but we’re retrofitting with the variables we have in place. That is why we have done a combination of a microgreen vertical nursery and PARS for baby greens. Our direct customers wanted meal solutions and we’ve been able to deliver them that. We’ve been doing everything from seed to plate basically.”
Megan Burritt, Managing partner
New projects coming up
On the same campus, 10 meters away, a new farm will be constructed, under the company's office space. In this farm herbs and edible flowers will be grown in response to different customers' demands. Megan says that Planted Detroit’s wholesale customers got them to this point as they were very interested in herbs and edible flowers. “However we weren’t able to perfect these as well in the systems that our baby greens were in perfectly. That’s why we’ve been leaning into R&D lately because once finishing the construction of Farm 2 it will have excellent growing conditions that are better than they have been for those crops.”
Edible flowers are an interesting thing, says Megan, but the company has gotten so much interest in it. According to Megan there aren’t many farms in the US that are growing them. “They’re high priced at this point. It sort of sticks to our original innovation, namely what exists here in the food system and what does not. Where can we fill the ‘does not exist niche’ and satisfy the needs of our customers.”
The company is rolling out a subscription program sometime this year and figuring out where it fits into the fresh food subscription system and how they can partner with other parties in order to get produce closer to society. “It’s great to have this ag job, applied science to be able to do. In all the things we’ve been doing is hiring these Detroiters and showing that we can really create a really great culture of work. It’s really great to see we’re contributing to a better Detroit and a better tomorrow,” Megan states.
Team expansion
During 2020 most of the team stayed on by moving around working hours, so the farm could come back in full force. By the time all equipment was in place, 10 to 12 people were added to the team to have them fully trained before the system would be functioning. “It has been really wonderful to expand the team to see what our capacity is,” says Megan.
“Luckily we’ve been able to develop systems that have been resilient. We’ve seen so many different patterns in consumer behavior but they seem to have fallen in our favor. People are eating more at home, shopping for groceries more, and that triggered our pivot focusing on direct consumers. But now, it’s perfectly in line with our strategy on how we go to market. As long as we can supply our customer needs we’ll be on the right path. Nothing but bright hopes for the future right now,” Megan affirms.
For more information:
Planted Detroit
Megan Burritt, Managing partner
megan@planteddetroit.com
www.planteddetroit.com
Author: Rebekka Boekhout
© VerticalFarmDaily.com
Eastern Kentucky Company Growing Local Economy By Growing Vegetables Year-Round
AppHarvest has created 300 jobs in Appalachia, an area not really known for growing tomatoes.
by GIL MCCLANAHAN
MOREHEAD, Ky. (WCHS) — Imagine growing fresh local tomatoes in the dead of winter. A company in Eastern Kentucky is using high-tech agriculture to grow vegetables indoors.
To View The Video, Please Click Here.
AppHarvest checks tomatoes growing inside the company's 60-acre indoor greenhouse.
(AppHarvest ) Courtesy Photo
AppHarvest opened in Rowan County, Ky. last October. They are growing more than just vegetables. They are growing the economy in an area that sorely needs it.
What's growing inside AppHarvest's 2.8-million square foot facility is capable of producing more food with less resources.
"For our first harvest to be on a day where there was a snowy mountainside could not have been any more timely. The fact that we are able to grow a great juicy flavorful tomato in the middle of January and February is what we have been working to accomplish," AppHarvest Founder and CEO Jonathan Webb said.
Webb said five months after opening its Morehead indoor farm facility, the company shipped more than a million beefsteak tomatoes to several major supermarket chains, including Kroger, Walmart and Publix. Those large bushels and bushels of tomatoes are grown using using the latest technology, no pesticides and with recycled water in a controlled environment using 90% less water than water used in open-field agriculture.
"We're just trying to get that plant a consistent environment year round with the right amount of light and the right amount of humidity and the right temperature just to grow, and the vines of our crops the tomato plant end up being 45 feet and we grow them vertically so that is how we can get so much more production," Webb said.
One of the company's more well-known investors is Martha Stewart.
"I said Martha, can I get five minutes and I told her what we are doing. She was like, look we need good healthy fruits and vegetables available at an affordable price. I love the region you are working in," Webb said.
A couple of weeks later, Webb met with Stewart at her New York office, and she decided to become an investor in the company. Some local restaurants are looking forward to the day when they can buy their vegetables locally from AppHarvest. Tim Kochendoerfer, Operating Partner with Reno's Roadhouse in Morehead, buys his vegetables from a company in Louisville.
"It will be another selling point to show that we are a local restaurant," Kochendoerfer said.
Webb points out AppHarvest is not trying to replace traditional family farming. "Absolutely not. We want to work hard with local farmers," he said.
Webb said by partnering with local farmers, more local produce can get on grocery store shelves, because last year 4 billion pounds of tomatoes were imported from Mexico.
"What we are working to replace is the imports from Mexico where you got children working for $5 a day using illegal chemical pesticides in the produce is sitting on a truck for 2-3000 miles," Webb said.
AppHarvest has already started influencing the next generation of farmers by donating high tech container farms to local schools. Students learn to grow crops, not in the traditional way, but inside recycled shipping containers. The containers can produce what is typically grown on 4 acres of land. Rowan County Senior High School was the second school to receive one. It arrived last fall.
"We sell that lettuce to our food service department and it's served in all of our cafeterias in the district," said Brandy Carver, Principal at Rowan County Senior High School.
"When we talk about food insecurity and young people going home hungry, what better way can we solve these problems by putting technology in the classroom. let kids learn, then let the kids take the food home with them and get healthy food in the cafeterias," Webb said.
AppHarvest has created 300 jobs in Appalachia, an area not really known for growing tomatoes. Local leaders believe the company will attract more business to the area.
"I fully expect in time we'll see more and more activity along that line like we do in all sectors," said Jason Slone, Executive Director of the Morehead-Rowan County Chamber of Commerce.
"We will eventually be at the top 25 grocers. Name a grocer. We've been getting phone calls from all of them," Webb said.
AppHarvest has two more indoor farming facilities under construction in Madison County, Ky., with a goal of building 10 more facilities like the one in Rowan County by the year 2025.
To find out more about AppHarvest click here.
Fresh Impact Farms Awarded Arlington's First Agriculture Grant
Arlington County received its first-ever agriculture fund grant from the state, money that will go to county-based Fresh Impact Farms.
Operating since 2018, Fresh Impact Farms uses hydroponic technology to grow a variety of speciality herbs, leafy greens, and edible flowers indoors. (Mark Hand/Patch)
ARLINGTON, VA — Arlington County received its first-ever agriculture fund grant from the state, money that will go to Fresh Impact Farms, an Arlington-based company that plans to double production at its indoor growing facility.
Virginia Gov. Ralph Northam announced Monday that he had awarded an Agriculture and Forestry Industries Development, or AFID, Fund grant to Arlington totalling $15,000 to be given to Fresh Impact Farms. The company will receive a total of $30,000 from the government, with Arlington County matching the state grant with local funds.
"Agriculture continues to be a key driver of our economic recovery in both rural and urban areas of our commonwealth," Northam said Monday in a statement. "Innovative, dynamic businesses like Fresh Impact Farms are demonstrating how exciting new opportunities can grow out of pandemic-related challenges."
"I congratulate the company on their success and am thrilled to award the first-ever AFID grant to Arlington County to support this expansion," the governor said.
In recent decades, Arlington County has grown into one of the most densely populated counties in the nation. Up until World War II, Arlington still had plenty of farmland. But over the past 60-plus years, the only farming in the county has been of the backyard and patio variety or in the community gardens in the Four Mile Run area.
Operating since 2018, Fresh Impact Farms uses proprietary hydroponic technology to grow a variety of specialty herbs, leafy greens, and edible flowers indoors.
"Governor Northam's award to Fresh Impact Farms, Arlington's only commercial farm, is an innovative way to celebrate unique uses of technology to help a small business pivot during the pandemic," Arlington County Board of Supervisors Chairman Matt de Ferranti said. "I am thrilled that Fresh Impact Farms is growing and looking to the future of a sustainable food supply."
The company will invest a total of $137,500 as part of the expansion, which will include a second grow room, a larger production facility, and an educational hub where customers, after the pandemic, will be able to see how their food is harvested.
Fresh Impact Farms' community-supported agriculture or CSA, program focuses on leafy greens and home kitchen-friendly herbs and has grown them steadily since the program's creation last April. Along with residential customers, the company now has smaller wholesale clients in the Washington, D.C., area.
The future is bright for urban agriculture, said Ryan Pierce, founder of Fresh Impact Farms, located in the back of a Lee Highway strip mall. (Mark Hand/Patch)
After the start of the pandemic, Fresh Impact Farms decided to shift its business model to a CSA delivery service in order to continue generating revenue.
"Seizing the opportunity created by more people cooking at home, the company initiated a Community Supported Agriculture program targeting area residents," the governor's office said.
"Now, with vaccinations underway and the restaurant industry poised to rebound, Fresh Impact Farms is expanding, which will allow the company to resume supplying their restaurant customers, while also meeting new demand through their CSA program," the governor's office said.
Over the next three years, the company expects to grow an additional 10,500 pounds of Virginia-grown leafy greens, herbs, and edible flowers for restaurant and CSA customers.
The future is bright for urban agriculture, said Ryan Pierce, founder of Fresh Impact Farms, located in the back of a Lee Highway strip mall.
"The support and generosity from the Commonwealth and Arlington County will be valuable as we expand our production and move towards a hybrid model of serving both the needs of restaurants and consumers," Pierce said in a statement. "As the owner of a local food business, nothing gets me more excited than seeing the community come together in support of local food."
The funds from the Arlington County Industrial Development Authority, together with the state grant, represent "an important investment in urban agriculture, sustainability, and technology," Arlington County IDA Chair Edwin Fountain said in a statement. "This project will advance the County's innovative and forward-thinking approach to developing new sectors of economic activity in Arlington."
New York’s Gotham Greens Plans Solano County Indoor Produce Farm
It will be located on 33.6 acres of agricultural land purchased from the university adjacent to Interstate 80.
GARY QUACKENBUSH
FOR THE NORTH BAY BUSINESS JOURNAL
Example of the greenhouse operated by Gotham Greens which announced plans to open in Solano County (Photo courtesy of Gotham Greens)
Gotham Greens Holdings LLC, a firm with indoor agriculture operations across the U.S., Tuesday, announced plans to build a facility next to the University of California, Davis.
The first phase of this 10-acre Solano County facility is expected to open later this year. It will be located on 33.6 acres of agricultural land purchased from the university adjacent to Interstate 80.
The company stated its plans will provide it with the ability to deliver fresh leafy greens, herbs, plant-based dressings, dips and cooking sauces to more retailers, foodservice operators and consumers on the West Coast.
“… We are partnering with one of the highest-ranked agricultural research centers in the world to advance the entire agriculture system,” said Viraj Puri, co-founder and CEO of Gotham Greens. “California is responsible for growing one-third of the country’s vegetables and two-thirds of the nation’s fruit, yet in recent years, issues surrounding drought, food safety and worker welfare have demonstrated the need for continued innovation.”
The greenhouse will generate 60 full-time jobs and provide UC students with the opportunity to learn first-hand how to sustainably grow produce year-round in a safe, clean, climate-controlled environment. The company stated its facilities use 95% less water and 97% less land than conventional farming. Nationwide, Gotham Greens has 500,000 square feet of greenhouse space at five locations staffed by 400 employees.
The UC Division of Agriculture and National Resources and the UC Davis College of Agriculture and Environmental Sciences has entered into a partnership with Gotham Greens to advance research and innovation in the areas of indoor agriculture, greenhouse technology, and urban agriculture to help advance the science, workforce technology, and profitability of indoor agriculture globally.
“We are building a Controlled Environment Agriculture Consortium to support and advance the indoor farming industry, grow more fresh produce on less land and create new jobs for Californians,” said Gabriel Youtsey, the division’s chief innovation officer. “Gotham Greens is an anchoring partner of this research and industry collaboration that we hope will spur innovation, create a new indoor farming workforce and support industry growth.”
Helene Dillard, dean of the college, said, “This partnership will offer our students the chance to learn best practices from leading experts in indoor farming.”
Gotham Greens recently raised $87 million in new equity and debt capital bringing the company’s total financing to $130 million to fuel the next phase of growth.
Founded in 2009 in Brooklyn, New York, Gotham Greens (gothamgreens.com) owns and operates greenhouses in New York, Illinois, Rhode Island, Maryland and Colorado. Its produce is available in more than 40 states and 2,000 retail stores, including Albertsons Companies (Safeway, Jewel-Osco, and Shaw’s), Whole Foods Market, Target, King Soopers, Harris Teeter, and Sprouts.
The company’s products can also be purchased through e-commerce sites including AmazonFresh, FreshDirect and Peapod.
Lead Photo: Gotham Greens
Towards Greater Profitability And Scale In CEA And Vertical Farming
The virtual Indoor AgTech Innovation Summit on June 24-25 will gather the world’s leading farm operators, retailers, food companies, investors, seed companies, and technology providers to meet, network, and cultivate new commercial partnerships
The virtual Indoor AgTech Innovation Summit on June 24-25 will gather the world’s leading farm operators, retailers, food companies, investors, seed companies, and technology providers to meet, network, and cultivate new commercial partnerships.
350+ attendees from the US, Europe, the Middle East, and Asia will participate in live-stream sessions, join roundtable discussion groups and connect directly through 1-1 video meetings and group chats.
By sharing best practices from around the globe, and facilitating new connections and collaborations, the summit offers an invaluable platform to develop new business and accelerate projects across the Indoor AgTech ecosystem.
2021 Key Themes
· Hands-Free Cultivation: Latest developments in robotics, automation and AI
· New Crops: Mapping a pathway to mass production
· Retail Insights: Understanding the drivers behind consumer demand
· Seed Optimization: Breeding a competitive advantage
· Financial Models: The investment models scaling the industry
· Advanced Growing Environments: Blurring lines between lighting and genetics
· Profitability at Scale: The technology driving down OPEX
· Food Systems: Bringing food into urban planning
· Direct to Consumer Business Models: Scaling beyond a city
· Energy Efficiency: Driving down the costs of optimum operations
All participants can schedule video 1-1 meetings with potential partners and clients throughout the summit, and for an extended period before and after the sessions.
By sharing best practices from around the globe, and facilitating new connections and collaborations, the summit offers an invaluable platform to develop new business and accelerate projects across the Indoor AgTech ecosystem.
Summit website: https://indooragtechnyc.com/
Registration:
One Summit Pass: Indoor AgTech Innovation Summit (June 24-25, 2021)
Super Early Bird Price: $195
Register before April 2
Early Bird Price: $295
Register before May 7
Standard Price: $395
Two Summit Pass: Indoor AgTech (June 24-25, 2021) and Future Food-Tech Alternative Proteins (June 22-23, 2021)
Super Early Bird Price: $445
Register before April 2
Early Bird Price: $595
Register before May 7
Standard Price: $695
https://indooragtechnyc.com/register/
Vertical Farms vs Greenhouses – The First Consideration: Location
When and where to use a vertical farm versus a greenhouse, and what factors – both economic and environmental – make the difference.
In just the past decade or so, sustainable farming has seen a high-tech makeover in the form of Controlled Environment Agriculture, or CEA, which consists of two main technologies: Vertical farms and greenhouses.
When it comes to feeding the world, it’s not a choice between vertical farms or greenhouses. We’ll need both to feed our growing global population with healthy, sustainable food, and we need to understand the ideal situation for each.
But as a business decision, it often is a choice between the two – and that’s what we hope to explain in this five-part series of articles: When and where to use a vertical farm versus a greenhouse, and what factors – both economic and environmental – make the difference.
In this first post, we’ll cover the basic differences between vertical farms and greenhouses, and why location matters so much when deciding between the two. Then stay tuned because, in the next articles, we’ll dive deeper into energy and lighting costs, automation and other expenses, environmental and crop considerations, and finally, the future of farming.
Vertical Farms vs Greenhouses: The Basics
The two technologies are often confused, but there are significant differences between them in resource use, cost, output, and, perhaps most importantly, the ideal locations for each.
Greenhouses are the more traditional technology that you’re probably familiar with: A single layer of crops, planted inside an enclosed space with walls and a ceiling made of glass or plastic to allow natural light in. They’re semi-controlled environments.
Vertical farms, on the other hand, are a much more recent invention using trays of usually hydroponic plants, stacked in floor-to-ceiling towers, with LED lights illuminating each layer, and climate control constantly adjusting the temperature, humidity and more.
In the upcoming articles in this series, we’ll dive into each part of these differences in more detail. But for now, let’s start with the first question entrepreneurs always need answering: The price tag.
Henry Gordon-Smith is the CEO of Agritecture, an independent consultancy and software creator that helps clients decide between the two technologies. As he puts it, “Vertical farming represents the most expensive, most controlled form of agriculture.”
At first blush, vertical farms are, in fact, shockingly more expensive than greenhouses – six to 10 times as costly. Gordon-Smith says vertical farming costs 2,200 to 2,600 Euro per square meter of cultivation bed space, while high-tech greenhouses cost 250 to 350 Euro per square meter of cultivation space.
Both offer a year-round source of fresh, pesticide-free, locally-grown produce, which provides better nutrition than the same foods that arrive from far away.
But what else do farmers, entrepreneurs, and investors get for all the added expense of vertical farming?
The answer is pretty simple: A more compact farm with more production per square meter, less water use, and more control over both quantity and quality. (With iFarm, this predictability is part of the package, in the form of a guaranteed yield within a precise time frame.)
For some entrepreneurs or municipalities, the cachet of implementing a high-tech farming technique that’s only been in use for less than a decade is also a factor in favour of vertical farming. But most often, the choice comes down to location.
The Ideal Location for a Vertical Farm versus a Greenhouse
The first step in determining the feasibility of building a vertical farm or greenhouse is to look at the drivers and constraints – many of which are simply location-based.
Places with limited space, such as dense urban areas, and limited access to fresh water are ideal for vertical farms. Doubly so if they have access to low-cost, renewable energy, and if they’re near a market with high demand for the crops vertical farms excel at producing: Leafy-greens, micro-greens, herbs and berries grown locally, without pesticides.
But in areas with unlimited space, lots of natural sunlight, and high-cost and/or high-carbon electricity, greenhouses may be the better option and the extra expenses of vertical farming might not make sense.
How these considerations apply in broad regions of the world is illustrated below:
Vertical Farms Nailed Tiny Salads. Now They Need To Feed The World
Vertical farming is finally growing up. But can it move from salad garnishes for the wealthy to sustainable produce for the masses?
Gartenfeld Island, in Berlin’s western suburb of Spandau, was once the bellows of Germany’s industrial revolution. It hosted Europe’s first high-rise factory and, until World War II, helped make Berlin, behind London and New York, the third-largest city on Earth.
Today’s Berlin is still a shell of its former self (there are over a hundred cities more populous), and the browbeaten brick buildings that now occupy Gartenfeld Island offer little in the way of grandeur. Flapping in the gloom of a grey November morning in 2020 is a sign which reads, in German, “The Last Days of Humanity”.
Yet inside one of these buildings is a company perched at agriculture’s avant-garde, part of the startup scene dragging Berlin back to its pioneering roots. In under eight years, Infarm has become a leader in vertical farming, an industry proponents say could help feed the world and address some of the environmental issues associated with traditional agriculture. Its staff wear not the plaid or twill of the field but the black, baggy uniform of the city’s hipsters.
Infarm has shipped over a thousand of its “farms” to shops and chefs across Europe (and a few in the US). These units, which look like jumbo vending machines, grow fresh greens and herbs in rows of trays fed by nutrient-rich water and lit by banks of tiny LEDs, each of which is more than ten times brighter than the regular bulb you’d find in your dining room. Shoppers pick the plants straight from the shelf where they’re growing.
Infarm crop science director, Pavlos Kalaitzoglou, in his Berlin lab
Credit Ériver Hijano
Gartenfeld Island, however, is home to something more spectacular. Here, in a former Siemens washing machine factory, stand four white, 18-metre-high “grow chambers”, controlled by software and served by robots. These are the company’s next generation of vertical farms: fully-automated, modular high-rises it hopes will scale the business to the next level. According to Infarm, each one of these new units uses 95 per cent less water, 99 per cent less space and 75 per cent less fertilizer than conventional land-based farming. This means higher yields, fresher produce and a smaller carbon footprint.
Agriculture is a £6 trillion global industry that has altered the face and lungs of the Earth for 12,000 years. But, unless we change our food systems, we’ll be in trouble. By 2050, the global population will be 9.7 billion, two billion more than today. Fifty-six per cent of us live in cities; by 2050 it will be 70 per cent. If the prosperity of megastates like India and China continues to soar, and our diets remain the same, we will need to double food production without razing the Amazon to do it. That sign on Gartenfeld Island might not be so alarmist.
Vertical farmers believe they are a part of the solution. Connected, precision systems have grown crops at hundreds of times the efficiency of soil-based agriculture. Located in or close to urban centres, they slash the farm-to-table time and eliminate logistics. New tech is allowing growers to tamper with light spectra and manipulate plant biology. Critics, however, question the role of vertical farms in our food future. They are towering lunchboxes for late capitalism, they argue – producing garnishes for the rich when it is the plates of the poor we must fill. Vertical farms already make money, and heavyweights including Amazon and SoftBank are investing in various companies in the hopes of cornering a market expected to be worth almost £10 billion in the next five to ten years. Infarm is leading that race in Europe. It has partnered with European retailers including Aldi, Carrefour and Marks & Spencer. In 2019 it penned a deal with Kroger, America’s largest supermarket chain. Venture capitalists have handed the firm a total of £228 million.
Not bad for a hare-brained experiment that started in a Berlin apartment.
An Infarm employee tends to a batch of seedlings in a special incubator
Credit Ériver Hijano
In 2011, a year before he moved to Berlin, Erez Galonska went off-grid. He grew up in a village in his native Israel, but the young nation was growing too, and farms made way for buildings. Soon the village was a town, and its inhabitants ever more disconnected from their natural surroundings.
Galonska’s father had studied agriculture, and the son had dreamed of recovering a connection with nature he felt he had lost. The search took him to the mountains of the Canary Islands, where he found a plot of land and got to work. He drank water from springs, drew energy from solar panels, and spent long hours farming produce he then sold or bartered at local markets.
When he met his now-wife Osnat Michaeli, “I traded it for love,” he says. “Love is stronger than anything.” In 2012, the couple, alongside Galonska’s brother Guy, who had studied Chinese medicine, moved to Berlin to work on a friend’s social media project. But the hunger for self-sufficiency remained. It was “a personal quest,” Michaeli says. “How we can be self-sufficient, live off the grid. Food is a big part of that journey.”
We meet at a Jewish restaurant in Berlin’s historic Gropius Bau art museum. It is mid-morning, and Covid-19 has cleared the tables. But a row of Infarm units whirs away quietly along one wall, producing basil, mint, wasabi rocket (a type of rocket leaf with the punchy flavour of wasabi), and other, more exotic herbs. Such produce was a pipedream for the three Infarm co-founders eight years ago. Growing crops when living on a tropical island was one thing. Doing it in a small apartment, located in the tumbledown Berlin neighbourhood of Neukölln, was quite another. Soon after moving from the Canaries, Erez Galonska typed “can you grow without soil” into Google.
Japan had taken to indoor farming in the 1970s, and this bore some helpful information on its techniques. The same was true of illegal cannabis growers, who swapped tips about hydroponics – growing with nutrient-packed water rather than soil – across subreddits.
Several trips to a DIY store later, the trio had what resembled a hydroponic farm. It was a big, chaotic Rube Goldberg machine, and it leaked everywhere. Growing wasn’t simply a case of switching on the lights and waiting. Brightness, nutrients, humidity, temperature – every tweaked metric resulted in an entirely different plant. One experiment yielded lettuce so fibrous it was like eating plastic. “We failed thousands of times,” Erez Galonska says.
Two of Infarm’s co-founders, Osnat Michaeli and Erez Galonska
Credit Ériver Hijano
Eventually, the team grew some tasty greens. They imagined future restaurant menus boasting of food grown “in-farm”, rather than simply made in-house, and founded Infarm in 2013. But there was a hitch: indoor-grown cannabis sells for around £1,000 per kilo. Lettuce for £1.20. Most of the early vertical farms required heaps of manual work and operated in the red. “It simply wasn’t a sustainable business model,” Erez Galonska says.
By 2014, they decided to roadshow their idea and shipped a 1955 Airstream trailer – a brushed-aluminium American icon – to Berlin. The trailer belonged to a former FBI agent, but it was conspicuous in a city of Volkswagens, caravans and Plattenbau buildings. Michaeli and the Galonska brothers transformed it into a mobile vertical farm, then pitched up at an urban garden collective in Berlin’s trendy Kreuzberg district. There they proselytised indoor farming to urban planners, food activists, architects and hackers, handing out salads and running workshops. Fresh, local food – even if it cost a little more – would entice a growing number of foodies who were interested in where their meals came from. The trailer cost nothing but petrol money to move, and emissions from the growing process itself were almost nil.
When the designer of a swanky hotel across town came by trailer, he asked if the team could install something similar in his restaurant. “That was really the trigger,” says Guy Galonska. “We rented a workshop and we got to develop a system for them.”
When they installed their first “farm” in a Berlin supermarket, VCs took notice and visited Infarm’s young founders at their Kreuzberg office-cum-kitchen, where they hosted dinner parties featuring Infarm crops. But a return on investment still seemed distant: some investors thought the farms were an art project. Maintaining locations manually was exhausting, and the team almost went bankrupt “two or three times,” Guy Galonska says. “I think all of us got a lot of white hair during that time,” he adds. “It was a very challenging thing to do.”
A €2 million grant from the European Union in 2016 helped. With it came deals to place Infarm units in supermarkets and restaurants across Germany. Managing them all would require something precise, connected and efficient. To become a sustainable business, Infarm would have to behave less like a farm, and more like a tech startup.
An Infarm kiosk in the Edeka Supermarket E Center in Berlin
Credit Ériver Hijano
For around 2,500 years after King Nebuchadnezzar II of Babylon gifted his wife some hanging gardens, little changed in the world of hydroponic farming. Asian farmers grew rice on giant, terraced paddies, and Aztecs built “chinampa” rigs that floated along the swamps of southern Mexico.
Life magazine published a drawing of stacked homes, each growing its own produce, in 1909, and the term “vertical farming” appeared six years later. The US Air Force fed hydroponically-grown veggies to its troops during World War II, and Nasa explored the tech as a solution for life off-planet. But vertical farming didn’t really capture public imagination until 1999, when Dickson Despommier, a Columbia University professor, devised a 30-storey skyscraper filled with farms. In 2010, Despommier published The Vertical Farm: Feeding the World in the 21st Century, which has become the industry’s utopian testament.
“I had no expectations whatsoever that this would turn commercial,” Despommier says. “We just thought it was a good idea, because we didn’t see any other way out of stopping deforestation in favour of farming, and keeping the carbon dioxide content of the atmosphere at a reasonable level. It turned out to be a crazy idea whose time has come.”
The vertical farming concept is simple: growing produce on vertically-stacked levels, rather than side by side in a field. Instead of the Sun, the vertical farm uses artificial light, and where there is ordinarily soil, growers use nutritious water or, in the case of “aeroponic” farms, an evenly-dispersed mist.
Vertical farms take up a vanishing amount of land compared to their conventional cousins. They use almost no water, don’t flush contaminating pesticides into the ecosystem, and can be built where people actually live. But, by and large, they have not functioned as businesses. Only the black-market margins of weed, and Japan’s high-income, high-import food ecosystem, have catered to profit. It costs hundreds of thousands of pounds to erect a mid-sized vertical farm, and energy use is prohibitively high.
Advances in technology are changing this. By bolting automation, machine learning and cloud-connected software on to vertical farms, firms can trim physical labour, increase capacity and maintain a dizzying range of cultivation variables. Infarm staff at a separate office to the new Berlin farm, located some 23km southeast of Spandau in the Tempelhof district, keep track of “plant recipe” settings at any one of the startup’s 1,220 in-store units, including CO2 levels, pH and growth cycles, via the company’s Farm Control Cloud Platform, a bit like a giant CCTV room. Machine learning finesses recipes, and keeps each plant as uniform as possible.
Inside the new vertical farm, trays of produce are tended by automated systems
Credit Ériver Hijano
Gartenfeld Island’s employees – mechanical and electrical engineers, software developers, crop scientists and biologists – get closer to the produce, but only just. They monitor via an iPad and feed crops into the building’s four massive grow chambers, or farms, each one about the height and width of two London buses, with ventilation systems that whoosh like a subdued turbine hall.
From there on in, robots do the hard work. Inside the farms, a robotic “plant retrieval system” – basically a tricked-out teddy picker – scoots up and down a perpendicular beam, plucking trays of plants in various stages of growth and shuffling them closer, or further, from LED lights at the summit. The firm claims this reduces service time by 88 per cent. A sliver of the window is the only way to see the device in-person: everything is hermetically sealed to keep out pests. “With automation, you invest once and then that price goes down over time,” says Orie Sofer, Infarm’s hardware lab lead. “With human labour, unfortunately, over time the price goes up.”
The number of crop plants varies depending on the produce, but there are usually just under 300 in a “farm” at any one time. Each farm yields the equivalent of 10,000 square metres of land and uses just five litres of water per kilo of food (traditional vegetable farming uses around 322 litres per kg).
Infarm is not alone in this revolution. AeroFarms, a Newark, New Jersey-based startup, feeds an aeroponic mist to roots that are separated from their leaves by a cloth. It’s most recent funding round was led by Ingka Group, the parent of Swedish furniture giant IKEA. New York’s Bowery Farming, like Infarm, focuses on automation and a proprietary dashboard called BoweryOS that, among other things, takes photos of crops in real-time for analysis. It’s £123 million in backing comes from investors including Singapore’s sovereign fund Temasek. Bowery CEO and founder Irving Fain believe his addressable market “is about a hundred billion dollars a year, just in the US, of crops that we think are good candidates for us to grow.”
Leading the vertical farming VC race is Plenty, a San Francisco-headquartered brand that has raised almost half a billion pounds in the capital since it was founded in 2013, including a 2020 Series D round led by Masayoshi Son’s $100 billion SoftBank Vision Fund. Plenty feeds its greens with water that trickles down six-metre-tall poles; infrared sensors pour data into an algorithm that nudges the plant’s growth recipe accordingly.
Plenty co-founder and chief science officer Nate Storey, who works at the company’s test farm in Wyoming, likens these deep-tech solutions to the tools that powered agriculture’s most recent revolution: “The tractor allowed farmers to be freed from constraints. Half of their land was dedicated to raising draft animals, and the tractor came along and freed them from a life where they were basically managing animals just so they could plough their land.”
For them, he says, automation is similar. “It allows us to get rid of the hardest work – the work that is unpleasant, the work [growers] don’t like to do – and focus on the work that really matters.”
Infarm kiosks inside the Beba restaurant in the Gropius Bau museum
Credit Ériver Hijano
Infarm differs from the competition on two fronts. The first is its focus on modular design: each component is compatible and scalable, like a giant, noisy LEGO set. Modularity makes it possible to install Infarm units anywhere in the world in a matter of weeks, no matter the size. That enables the company’s second USP: its business model. Infarm has no stores, selling produce instead via its remote units.
Clients tell Infarm which produce they want, and “create a schedule,” says Michaeli. “You buy the plants. Everything on the farm is controlled by Tempelhof. Everything that’s grown belongs to the client.” A chef may demand pesto that’s made from particular three-day-aged Greek and Italian basil, for example. Infarm can do that (Tim Raue, Berlin’s most famous chef, is a customer). “Everyone stops and asks about the farm,” one Berlin store manager says. “It’s great to have innovation here.”
Infarm has “two big advantages,” says Nicola Kerslake, founder of Contain Inc, a Nevada-based agtech financier. “One is that they’ve figured out how to do product onsite, which is really not very easy. And the other is that they have these great relationships with big purchasers like Marks & Spencer.”
“When you look at where the arms race is in this industry,” she continues, “it’s really been in two areas: How do I get hold of as much capital as possible, and how do I sign up the right partners? Having Marks & Spencer in your back pocket is really useful.”
It has helped encourage investors to open their chequebooks. Hiro Tamura, a partner at London VC firm Atomico, first met Infarm’s founding trio in 2018. A year later he led its £75 million Series B round. “They could roll these things out,” he says. “They worked, and they didn’t need some industrial-sized warehouse to do it. I didn’t lean in, I fell into the rabbit hole. And it was incredible. I was like, wow, these guys are thinking about time and speed to market modularity.”
Infarm ploughs a chunk of its revenue back into research. In a mezzanine-level lab sitting above the farms at Gartenfeld Island, a dozen white-coated analysts conduct tests on herbs to a soundtrack of Ariana Grande, measuring crop sugar levels, acidity, vitamins, toxicity, antioxidants and more. Via a process of phenotyping – the study of organisms’ characteristics relative to their environment – they hope to create more flavourful plants, or new tastes altogether.
“It’s not just about the hardware,” Kerslake explains. “It’s about how the hardware interacts with the rest of your farm system. And we’re starting to see a lot more sophistication on that front because the AI programs these companies started three or four years ago are now starting to bear fruit.”
Infarm’s results are high-quality: juicy lettuce, wasabi rocket that kicks, and basil that’s far more fragrant than the budget variety. “The end goal with almost everything that we’re doing is developing some sort of playbook, some sort of modular and standardised system, that we can then copy-paste to wherever we go,” says Pavlos Kalaitzoglou, Infarm’s director of plant science. Across from the lab, tomatoes and shiitake mushrooms grow in wine cellar-size chambers. They are living proof of how the firm is looking to diversify from herbs and leafy greens, whose low energy and water requirements make them the staple crop of every vertical farming startup today.
Rows of LED-illuminated produce inside one of Infarm’s four massive new grow chambers
Credit Ériver Hijano
We are in danger of farming the planet to death. Agriculture already occupies 40 per cent of all liveable land on Earth, and food production causes a quarter of all greenhouse gases. An area the size of Scotland disappears from tropical rainforests, responsible for up to a quarter of land photosynthesis, each year. Clearing more trees to feed our spiralling population will not help.
“We need to go back to the drawing board and rethink which avenues we can environmentally afford to pursue,” says Nicola Cannon, a professor at the Royal Agricultural University in Cirencester. Nitrogen fertiliser is particularly harmful to the environment, Cannon adds, “and has led us to adopt systems which have grossly exceeded the planetary boundaries.”
Current food systems are wildly inefficient: waste accounts for 25 per cent of all calories. And yet, almost a billion people suffer from hunger worldwide. These are not issues vertical farming will solve, critics, argue. Going local does little beyond satisfying consumers.
Energy is another tricky issue. Ninety per cent of Infarm’s electricity today is renewable, and it wants to reach zero emissions in the next few years. But this doesn’t factor in the environmental cost of building a steel-and-cement facility.
“Vertical farms are a round-off error to the round-off error in terms of contributing to the big levers out there,” Jonathan Foley, an environmental scientist based in Minneapolis, says. “Like most technologies that are getting a lot of venture capital and which come from Silicon Valley kind of thinking, it’s being massively overhyped at the cost of real solutions. There’s an opportunity cost to put all this technology, money and renewable energy – that could be used for other things that we need energy for – into growing arugula for rich people at $10 an ounce.”
More than half the world’s food energy comes from its three “mega-crops”: wheat, corn and rice. They require wind, seasons and micronutrients that vertical farms are unable to replicate today. These are the crops that can prevent famine in Somalia, Bangladesh or Bolivia – not lettuce. “Vertical farms are growing the edge of the plate, not the centre of the plate,” Foley says.
But Despommier says it’s too soon to criticise the young industry for not addressing issues such as crop diversity. “What you’re really seeing is a rush towards profitability to get their feet wet, and to get their ledgers in the black and to pay off their investors, before they start diversifying,” he says.
“In a world where you think that land is unlimited and that resources are unlimited, indoor farming would be nonsensical,” Plenty co-founder Storey says. “As crazy as it seems to replace the Sun with electricity, it makes sense today. And it really makes more and more sense as time goes on.”
Much of the hope vested in vertical farms rests on the light-emitting diode. This tiny bead of light is the industry’s packhorse: it is a farm’s biggest financial layout and the nucleus of its most exciting advances. Modern LEDs are nothing like the ones that powered your childhood TV. They’ve progressed at such a rate, in fact, that they’ve developed their own law to adhere to: “Haitz’s Law”. Each decade, their cost drops by a factor of ten, while the light they generate leaps by a factor of 20.
That curve will eventually plateau, experts say. But not before LEDs improve enough to allow vertical farms to profit from food closer to the middle of the plate. Infarm’s current smart LED set-up is over 50 per cent more efficient than the one that lit its first farms. Haitz’s Law has helped some companies experiment in growing potatoes, which require far more energy and water than leafy greens. Turning profit from a crop that delivers the highest calories per acre would be momentous for the industry.
The cutting edge of LED technology today is smart sensors that can regulate the brightness and spectrum of light to replicate growing outdoors – or enhance it. Much of the planet’s first flora grew only in the ocean, which looks blue because it absorbs blue light at least.
Photosynthesis, therefore, occurs best between the blue and red light spectra. By tailoring LEDs to emit only these colours, or by dimming at intervals meant to mirror a plant’s natural cycle, vertical farmers can further reduce their energy burden – like stripping a road car to its bare bones so it can drive faster.
Recent discoveries have been more surprising. Strawberries, for example, react particularly well to green light. Some spectra can increase vitamin C in concentrated fruits like kiwis, while others extend shelf-lives by almost a week. In the future, says Fei Jia, of LED firm Heliospectra, growers “can get feedback from the lighting and the plants themselves on how the lighting should be applied… to further improve the consistency of the crop quality.”
“If you judge it from what you have today, you understand what [critics] are saying,” Guy Galonska says. “How can you grow rice and wheat and save the world? And they are right. But they can’t see ten years ahead: they can’t see all the different trends that are going to support that revolution.”
Other technological advances are helping agriculture in different ways. Drones and sensors help map and streamline growing. Drip irrigation dramatically reduces the burden on dwindling water supplies. Circular production – where waste products from one process contribute to fuelling another – is becoming more commonplace, especially in livestock farming. Cell-grown or insect-based meat (or vegetarianism) will reduce our reliance on livestock, which consume 45 per cent of the planet’s crops. Infarm, and the broader vertical farm cohort, may not be saving the world today. But it wants to build taller farms, place them in public buildings like schools, and teach people the value of fresh, healthy vegetables. If 70 per cent of us are to live in cities, then cities “can become these communities of growing,” says Erez Galonska.
Ultimately, Infarm wants to build a network of tens of thousands of automated farms, each one pumping streams of data back into a giant AI system in Berlin. This “brain”, as Galonska calls it, will pour that information into algorithms to generate better food at lower costs, each new yield shaving fractions from the water, energy and nutrients required. Then, Infarm could become something closer to the dream Galonska left behind in the Canaries: truly self-sufficient.
It’s a long way from the leaky, DIY gadget he and his co-founders built in their front room. “The way the world is going now, it’s very clear to everyone it’s running in the wrong direction,” Galonska says. “We definitely believe in the power of collaboration: bringing those outside-the-box thoughts to create a new system that will generate more food, better food, much more sustainably, and help to heal the planet – because that’s the main issue on the table.”
Saudi Farmer Has Built The Region’s First Vertical Farm
“My aim is to make sure we truly become self-sufficient,” he said.
The Saudi farmer Omar Al-Jundi even he is not related to farming by degree. But that is exactly where the industrial engineer found his calling, when he built the region’s first vertical farm in the heart of Dubai. Born in Egypt to Saudi parents, Al-Jundi spent his early years in Alkhobar due to his father’s engineering firm.
The family moved to Jeddah when he was 12 years old. His last two years of schooling were spent at Bahrain School in Manama. “I wanted to graduate with an American high school diploma,” Al-Jundi said. “At the time, as a Saudi, you couldn’t attend private foreign schools.” Upon graduation, he left the region to study industrial engineering, followed by an MBA at the University of Miami in Florida. Although his father is an engineer and his mother an architect, Al Jundi delved into the world of banking for two and a half years when he moved back to Jeddah upon graduating.
“I then shifted to the hospitality industry, opened the first lounge in Jeddah along with other restaurants with my friends, and ended up selling my share and joining my father’s company,” he said. “You learn that you’re better off doing something on your own than having partners because you end up changing directions.”
After 10 years of “paying his dues” in the family business, he felt compelled to change directions. “As an Arab, you’re always closely tied to the family,” he said. “We’re blessed my father started a business and there’s a place for us in that business, but luckily, my younger brother was a lot more interested in it — I always felt my calling was somewhere else.”
In search of his true passion, he started his journey as an entrepreneur. The field he specialized in had yet to be determined. “I felt that there was a meaning for something else,” Al-Jundi said. “I was free and my family was very supportive.”
Countless research and books later, he became intrigued by the tech space, admitting he believed he would start the next Amazon. “That didn’t follow through,” he said. “Then I thought it would be in mining, but I always looked for something that was away from my comfort zone such as engineering, contracting, real estate and consulting. Just something different. It was a process.”
The young Saudi had reached a point in his life where he felt the need to do something impactful, something which added true value to the region. Eventually, two of his friends introduced him to the concept of modern farming. “I visited some orange farms in Egypt and I was in exploration research mode,” he said. “I enjoyed seeing nature — you’re a lot more relaxed. Here, when you go in and see the plants growing every day, there’s definitely a connection, because you’re seeing the end product, you’re feeling it, and I connect to them.”
The more research he immersed himself in, the more driven his interest became. At the time, the Saudi Government was focused on addressing food security and self-sufficiency. “It’s always been a big topic,” he said. “When you fly out of Riyadh, you find these big circular green spots as they’re trying to green and farm the desert, which was successful, but on the other hand, it depleted our water resources.” According to the Food and Agriculture Organization, agriculture represents around 70 per cent of water consumption in most of the GCC countries. But Al-Jundi did not give up on the thought.
After moving to Dubai in 2014, he learned about King Abdullah’s Initiative for Saudi Agricultural Investment Abroad. Half the capital needed for agricultural projects was offered to Saudis who invested in a list of 31 countries abroad to purchase land, set up a project and export the food back to the Kingdom. It gave him an idea to start his own vertical farm. “I knew it was a big topic,” he said. “I’d never heard we could grow food with no soil. I thought it was intriguing and fascinating. It was enough for me to know there was something there to explore it further.”
With more than 90 per cent of the region’s land unsuitable for agriculture, Al-Jundi set out to find a solution. He spent the following 12 weeks taking courses in aquaponics, aquaculture, hydroponics and horticulture in California and the Netherlands. He even spent time working in a cucumber greenhouse at the Delphy facility in Holland, where he acquired valuable experience in the field. “It was really professional and a great learning experience,” he said. “That’s when I knew what I wanted to do. And I knew I had to completely immerse myself in it.”
The team of Badia Farms, which he founded in Al Quoz in December last year, consists of 12 people, all of whom have experience in farming. “It took 18 months to get it up and running because we didn’t work with any technical partner,” Al-Jundi said. “I knew I was in it for the long haul, so I worked with different growers and learned.”
The 850-square-meter facility includes a “fertigation” room, which fertilizes and irrigates the 18 varieties of crops he currently grows. Gourmet seeds, some of them hybrids, such as lemon basil, cinnamon kale, wasabi, green radish, mustard, micro kale, edible flowers and cinnamon basil, are flown in from the United Kingdom and the United States every three months — from 50 to 300 kilograms at a time. The farm plans on introducing as many as 26 varieties, including sunflowers.
The seeds are placed on a type of mat made of recycled carpet that is food-certified. LED lights flood the room in a pink atmosphere, with each UV light containing a certain spectrum that is beneficial for the plants.
In the tank room, feed and water is scheduled through a computer-based on the crop, with a unique nutrient recipe for each type, including potassium, calcium, magnesium, and ammonium. UV and concentrated oxygen are also able to kill any potential bacteria or pathogens in recycled water. Once the seeds sprout, they are moved to the five stacks in the vertical farm. Four dehumidifiers regulate the humidity in the air, providing each on average with 70 litres of water a day. The eco-system created by Badia Farms uses 90 percent less water than open-field farming and recycles its water up to nine times.
“We’re using hydroponics,” Al- Jundi said. “The biggest advantage is that we do not spray pesticides, which are messing up our health. In fact, we extensively use stickers to attract insects away from the crops.” Different levels of lighting are provided for each stage of the plants before they are sent out as they were grown. “They’re intense in flavor and it’s the freshest you can get that way,” he said. “My personal favourite is chocolate mint.” With 60 clients so far, serving hotels, restaurants, and cafes, the model is a first for the region, which made it challenging to set up. “All the ones abroad are designed for different climatic conditions so none of them are applicable here, where there is extreme humidity and high temperatures,” he said. “And to convince a chef to give you his time, when you don’t have the track record, was a big challenge. I wasn’t a known farmer yet.”
The system’s structure was manufactured in Riyadh, with a plan to set up the next facility by 2020 in Jeddah. Until then, the plan is to cater to Saudi as well as the UAE. “Dubai is a good testing ground and Saudi’s vision now is to support our type of sustainable growing and ecological farms, so it’s perfectly in line with what we want to do,” Al-Jundi said. “The government is now delegated to move into sustainable growing and find viable solutions to address self-sufficiency, so it’s not a slogan anymore: it’s the real deal.”
He hopes to develop similar projects across the Kingdom in the future. “My aim is to make sure we truly become self-sufficient,” he said. “Vertical farming is one solution but it’s not the full one — the ideal solution lies in all models of modern farming. What’s close to my heart is giving people healthy food while preserving our resources, and I believe the new generations of Saudis are ambitious and want to evolve our country. We were just waiting for the opportunity and it has finally come.”
Source: Arab News
UPDATE - Vertical Farming Leader Kalera Welcomes Maria Sastre to Board of Directors
Sastre brings world-class customer service and operations experience as Kalera prepares for rapid domestic and international expansion.
A seasoned executive with experience in the food, travel, and tourism industries, Sastre brings with her over 25 years of executive leadership and experience and currently sits on the boards of esteemed, Fortune 500, multibillion dollar public and private companies, including General Mills and O’Reilly Auto Parts.
ORLANDO, Fla., Feb. 24, 2021 (GLOBE NEWSWIRE) -- Kalera (Euronext Growth Oslo ticker KAL, Bloomberg: KSLLF), one of the fastest-growing and largest vertical farming companies in the world and a leader in plant science for producing high-quality produce in controlled environments, today announced the appointment of Maria Sastre to its Board of Directors. A seasoned executive with experience in the food, travel, and tourism industries, Sastre brings with her over 25 years of executive leadership and experience and currently sits on the boards of esteemed, Fortune 500, multibillion dollar public and private companies, including General Mills and O’Reilly Auto Parts. The addition of Sastre to the board coincides with Kalera's rapid expansion into several new markets and its acquisition of Vindara Inc., the first company to develop seeds specifically designed for use in vertical indoor farm environments as well as other controlled environment agriculture (CEA) farming methods.
“We are thrilled that someone of Maria’s caliber has chosen to join Kalera’s board,” said Daniel Malechuk, Kalera CEO. “Her resume is beyond impressive, with extensive experience leading highly successful international and growing companies, and is a strong complement to our industry-leading management team and board of directors. She has proven time and again that she is invaluable in helping scale businesses, and will be an incredible asset to Kalera during this time of rapid growth, both domestically and abroad.”
In addition to her aforementioned business experience, Sastre also served on numerous civic and non-profit boards such as the Greater Miami Visitors and Convention Bureau(Chair), the Executive Advisory Board of Florida International University School of Hospitality,and the Executive Board of the United Way of Miami-Dade County. She has been recognized as one of the Top 80 U.S. Hispanics and Top 20 Latinas and has received numerous awards in the travel and hospitality industry sectors. Sastre's education includes a Bachelor's degree and a Master's in Business Administration, both from New York Institute of Technology.
“As someone with a passion for optimizing customer experiences, I am proud to join Kalera’s board as I fully believe their product is a category leader,” said Maria Sastre, new Kalera board member. “Kalera has the opportunity to serve diverse customer segments and increase accessibility to a product that is inherently safer, cleaner, fresher, more sustainable, and more nutritious and flavorful. In a world where brands are looking for ways to differentiate their products and services to their discerning customers, the Kalera portfolio is well positioned to offer the best vertical farming product solution. I trust my years of experience in operations and customer service will prove beneficial as Kalera expands into new markets.”
Sastre previously served as the President and Chief Operating Officer for Signature Aviation, the largest worldwide network of fixed-based operations and maintenance centers for private aviation. Before joining Signature, she spent eight years at Royal Caribbean Cruises LTD, where she held the positions of Vice President, International, Latin America, Caribbean and Asia; and Vice President of Hotel Operations. Her roles included strategic growth across emerging markets as well as managing all aspects of operations and the guest experience onboard Royal Caribbean's fleet of vessels. Previously, Sastre served as Vice President of Worldwide Customer Satisfaction for United Airlines, where she led the newly created customer-satisfaction division charged with refining the customer-service experience.
Kalera currently operates two growing facilities in Orlando, and is building facilities in Atlanta, Houston, Denver, Columbus, Seattle, and Hawaii. Kalera is the only controlled environment agriculture company with coast-to-coast facilities being constructed, offering grocers, restaurants, theme parks, airports and other businesses nationwide reliable access to locally grown clean, safe, nutritious, price-stable, long-lasting greens.Kalera uses a closed-loop irrigation system which enables its plants to grow while consuming 95% less water compared to field farming.
About Kalera
Kalera is a technology driven vertical farming company with unique growing methods combining optimized nutrients and light recipes, precise environmental controls, and clean room standards to produce safe, highly nutritious, pesticide-free, non-GMO vegetables with consistent high quality and longer shelf life year-round. The company’s high-yield, automated, data-driven hydroponic production facilities have been designed for rapid rollout with industry-leading payback times to grow vegetables faster, cleaner, at a lower cost, and with less environmental impact. To learn more visit www.Kalera.com.
Media Contact
Molly Antos
Phone: (847) 848-2090
Email: molly@dadascope.com
A photo accompanying this announcement is available at https://www.globenewswire.com/NewsRoom/AttachmentNg/bb487877-0d3b-4e1c-9492-9ea280c217a1