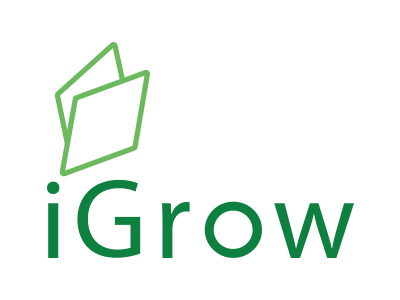
Welcome to iGrow News, Your Source for the World of Indoor Vertical Farming
Agritech: Precision Farming With AI, IoT and 5G
For a company that grows and delivers vegetables, Boomgrow Productions Sdn Bhd’s office is nothing like a farm, or even a vertical farm. Where farms are bedecked with wheelbarrows, spades and hoes, Boomgrow’s floor plan is akin to a co-working space with a communal island table, several cubicles, comfortable armchairs, a cosy hanging rattan chair and a glass-walled conference room in the middle
Image from: Photo by Mohd Izwan Mohd Nazam/The Edge
For a company that grows and delivers vegetables, Boomgrow Productions Sdn Bhd’s office is nothing like a farm, or even a vertical farm.
Where farms are bedecked with wheelbarrows, spades and hoes, Boomgrow’s floor plan is akin to a co-working space with a communal island table, several cubicles, comfortable armchairs, a cosy hanging rattan chair and a glass-walled conference room in the middle.
At a corner, propped up along a walkway leading to a rectangular chamber fitted with grow lights, are rows of support stilts with hydroponic planters developed in-house and an agricultural technologist perched on a chair, perusing data. “This is where some of the R&D work happens,” says Jay Dasen, co-founder of the agritech start-up.
But there is a larger farm where most of the work behind this high-tech initiative is executed. Located a stone’s throw from the city centre in Ampang is a 40ft repurposed shipping container outfitted with perception technologies and artificial intelligence (AI) capabilities that mimic the ideal environment to produce more than 50,000kg of vegetables a year.
Stacked in vertical layers, Boomgrow’s vegetables are grown under artificial lights with Internet of Things (IoT) sensors to detect everything from leaf discolouration to nitrate composition. This is coupled with AI and machine learning algorithms.
Boomgrow is the country’s first 5G-connected vertical farm. With the low latency and larger bandwidth technology, the start-up is able to monitor production in real time as well as maintain key parameters, such as temperature and humidity, to ensure optimal growth conditions.
When Jay and her co-founders, K Muralidesan and Shan Palani, embarked on this initiative six years ago, Boomgrow was nowhere near what it is today.
The three founders got together hoping to do their part in building a more sustainable future. “I’ve spent years advising small and large companies on sustainability, environmental and social governance disclosures. I even embarked on a doctorate in sustainability disclosure and governance,” says Jay.
“But I felt a deep sense of disconnect because while I saw companies evolving in terms of policies, processes and procedures towards sustainability, the people in those organisations were not transforming. Sustainability is almost like this white noise in the background. We know it’s important and we know it needs to be done, but we don’t really know how to integrate it into our lives.
“That disconnect really troubled me. When we started Boomgrow, it wasn’t a linear journey. Boomgrow is something that came out of meaningful conversations and many years of research.”
Shan, on the other hand, was an architect who developed a taste for sustainable designs when he was designing modular structures with minimal impact on their surroundings between regular projects. “It was great doing that kind of work. But I was getting very dissatisfied because the projects were customer-driven, which meant I would end up having debates about trivial stuff such as the colour of wall tiles,” he says.
As for Murali, the impetus to start Boomgrow came from having lived overseas — while working in capital markets and financial services — where quality and nutritious produce was easily available.
Ultimately, they concluded that the best way to work towards their shared sustainability goals was to address the imminent problem of food shortage.
“By 2050, the world’s population is expected to grow to 9.7 billion people, two-thirds of whom will be in Asia-Pacific. Feeding all those people will definitely be a huge challenge,” says Jay.
“The current agricultural practice is not built for resilience, but efficiency. So, when you think of farming, you think of vast tracts of land located far away from where you live or shop.
“The only way we could reimagine or rethink that was to make sure the food is located closer to consumers, with a hyperlocal strategy that is traceable and transparent, and also free of pesticides.”
Having little experience in growing anything, it took them a while to figure out the best mechanism to achieve their goal. “After we started working on prototypes, we realised that the tropics are not designed for certain types of farming,” says Jay.
“And then, there is the problem of harmful chemicals and pesticides everywhere, which has become a necessity for farmers to protect their crops because of the unpredictable climate. We went through many iterations … when we started, we used to farm in little boxes, but that didn’t quite work out.”
They explored different methodologies, from hydroponics to aquaponics, and even started growing outdoors. But they lost a lot of crops when a heat wave struck.
That was when they started exploring more effective ways to farm. “How can we protect the farm from terrible torrential rains, plant 365 days a year and keep prices affordable? It took us five years to answer these questions,” says Jay.
Even though farmers all over the world currently produce more than enough food to feed everyone, 820 million people — roughly 11% of the global population — did not have enough to eat in 2018, according to the World Health Organization. Concurrently, food safety and quality concerns are rising, with more consumers opting for organically produced food as well as safe foods, out of fear of harmful synthetic fertilisers, pesticides, herbicides and fungicides.
According to ResearchAndMarkets.com, consumer demand for global organic fruit and vegetables was valued at US$19.16 billion in 2019 and is anticipated to expand at a compound annual growth rate (CAGR) of 6.5% by 2026.
Meanwhile, the precision farming market was estimated to be US$7 billion in 2020 and is projected to reach US$12.8 billion by 2025, at a CAGR of 12.7% between 2020 and 2025, states MarketsandMarkets Research Pte Ltd.
Malaysia currently imports RM1 billion worth of leafy vegetables from countries such as Australia, China and Japan. Sourcing good and safe food from local suppliers not only benefits the country from a food security standpoint but also improves Malaysia’s competitive advantage, says Jay.
Unlike organic farming — which is still a soil-based method — tech-enabled precision farming has the advantage of catering for increasing demand and optimum crop production with the limited resources available. Moreover, changing weather patterns due to global warming encourage the adoption of advanced farming technologies to enhance farm productivity and crop yield.
Boomgrow’s model does not require the acres of land that traditional farms need, Jay emphasises. With indoor farms, the company promises a year-round harvest, undisturbed by climate and which uses 95% less water, land and fuel to operate.
Traditional farming is back-breaking labour. But with precision technology, farmers can spend less time on the farm and more on doing other things to develop their business, she says.
Boomgrow has secured more than RM300,000 in funding via technology and innovation grants from SME Corporation Malaysia, PlaTCOM Ventures and Malaysia Digital Economy Corporation, and is on track to build the country’s largest indoor farms.
Image from: Boomgrow
The company got its chance to showcase the strength of its smart technology when Telekom Malaysia Bhd (TM) approached it to be a part of the telco’s Smart Agriculture cluster in Langkawi last October.
“5G makes it faster for us to process the multiple data streams that we need because we collect data for machine learning, and then AI helps us to make decisions faster,” Jay explains.
“We manage the farm using machines to study inputs like water and electricity and even measure humidity. All the farm’s produce is lab-tested and we can keep our promise that there are no pesticides, herbicides or any preserving chemicals. We follow the food safety standards set by the EU, where nitrate accumulation in plant tissues is a big issue.”
With TM’s 5G technology and Boomgrow’s patent-pending technology, the latter is able to grow vegetables like the staple Asian greens and highland crops such as butterhead and romaine lettuce as well as kale and mint. While the company is able to grow more than 30 varieties of leafy greens, it has decided to stick to a selection of crops that is most in demand to reduce waste, says Jay.
As it stands, shipping containers are the best fit for the company’s current endeavour as containerised modular farms are the simplest means of bringing better food to local communities. However, it is also developing a blueprint to house farms in buildings, she says.
Since the showcase, Boomgrow has started to supply its crops to various hotels in Langkawi. It rolled out its e-commerce platform last year after the Movement Control Order was imposed.
“On our website, we promise to deliver the greens within six hours of harvest. But actually, you could get them way earlier. We harvest the morning after the orders come in and the vegetables are delivered on the same day,” says Jay.
Being mindful of Boomgrow’s carbon footprint, orders are organised and scheduled according to consumers’ localities, she points out. “We don’t want our delivery partners zipping everywhere, so we stagger the orders based on where consumers live.
“For example, all deliveries to Petaling Jaya happen on Thursdays, but the vegetables are harvested that morning. They are not harvested a week before, three days before or the night before. This is what it means to be hyperlocal. We want to deliver produce at its freshest and most nutritious state.”
Plans to expand regionally are also underway, once Boomgrow’s fundraising exercise is complete, says Jay. “Most probably, this will only happen when the Covid-19 pandemic ends.”
To gain the knowledge they have today, the team had to “unlearn” everything they knew and take up new skills to figure what would work best for their business, says Jay. “All this wouldn’t have been possible if we had not experimented with smart cameras to monitor the condition of our produce,” she laughs.
How This Vertical Farm Grows 80,000 Pounds of Produce per Week
To some, the pristine growing conditions and perceived mechanical interference of a vertical farm can seem unnatural, but at Bowery Farming “interference” is actually not the goal at all. “We don’t really think about how people are involved in the growing process, but how to take people out of the growing process”
Bowery Farming uses technology to prioritize accessibility and sustainability in their produce growing operations
To some, the pristine growing conditions and perceived mechanical interference of a vertical farm can seem unnatural, but at Bowery Farming “interference” is actually not the goal at all. “We don’t really think about how people are involved in the growing process, but how to take people out of the growing process” says chief science officer Henry Sztul. “Our goal is actually to have as few people walking around our plants as possible.”
Bowery Farming is a network of vertical farms working to reengineer the growing process. Using a system of light and watering technology, Bowery is able to use 95 percent less water than a traditional outdoor farm, zero pesticides and chemicals, and grow food that tastes as good as anyone else’s.
Bowery Farming uses vertical farm-specific seeds that are optimized for flavor instead of insect resistance and durability. Seeds are mechanically pressed into trays of soil, and sent out into growing positions, or racks within the building that have their own lighting and watering systems. Each tray gets its own QR code so that they can be monitored and assigned a customized plan for water and light until they’re ready to be harvested.
Irving Fain, Bowery Farming’s founder and CEO contemplates the prediction from the United Nations that 70 to 80 percent of the world’s population will be living in and around cities in the next 30 years. “Figuring out ‘how do you feed and how do you provide fresh food to urban environments both more efficiently as well as more sustainably?’ is a very important question today, and an even more important question in the years to come.”
Bringing The Future To life In Abu Dhabi
A cluster of shipping containers in a city centre is about the last place you’d expect to find salad growing. Yet for the past year, vertical farming startup Madar Farms has been using this site in Masdar City, Abu Dhabi, to grow leafy green vegetables using 95 per cent less water than traditional agriculture
Amid the deserts of Abu Dhabi, a new wave of entrepreneurs and innovators are sowing the seeds of a more sustainable future.
Image from: Wired
A cluster of shipping containers in a city centre is about the last place you’d expect to find salad growing. Yet for the past year, vertical farming startup Madar Farms has been using this site in Masdar City, Abu Dhabi, to grow leafy green vegetables using 95 per cent less water than traditional agriculture.
Madar Farms is one of a number of agtech startups benefitting from a package of incentives from the Abu Dhabi Investment Office (ADIO) aimed at spurring the development of innovative solutions for sustainable desert farming. The partnership is part of ADIO’s $545 million Innovation Programme dedicated to supporting companies in high-growth areas.
“Abu Dhabi is pressing ahead with our mission to ‘turn the desert green’,” explained H.E. Dr. Tariq Bin Hendi, Director General of ADIO, in November 2020. “We have created an environment where innovative ideas can flourish and the companies we partnered with earlier this year are already propelling the growth of Abu Dhabi’s 24,000 farms.”
The pandemic has made food supply a critical concern across the entire world, combined with the effects of population growth and climate change, which are stretching the capacity of less efficient traditional farming methods. Abu Dhabi’s pioneering efforts to drive agricultural innovation have been gathering pace and look set to produce cutting-edge solutions addressing food security challenges.
Beyond work supporting the application of novel agricultural technologies, Abu Dhabi is also investing in foundational research and development to tackle this growing problem.
In December, the emirate’s recently created Advanced Technology Research Council [ATRC], responsible for defining Abu Dhabi’s R&D strategy and establishing the emirate and the wider UAE as a desired home for advanced technology talent, announced a four-year competition with a $15 million prize for food security research. Launched through ATRC’s project management arm, ASPIRE, in partnership with the XPRIZE Foundation, the award will support the development of environmentally-friendly protein alternatives with the aim to "feed the next billion".
Image from: Madar Farms
Global Challenges, Local Solutions
Food security is far from the only global challenge on the emirate’s R&D menu. In November 2020, the ATRC announced the launch of the Technology Innovation Institute (TII), created to support applied research on the key priorities of quantum research, autonomous robotics, cryptography, advanced materials, digital security, directed energy and secure systems.
“The technologies under development at TII are not randomly selected,” explains the centre’s secretary general Faisal Al Bannai. “This research will complement fields that are of national importance. Quantum technologies and cryptography are crucial for protecting critical infrastructure, for example, while directed energy research has use-cases in healthcare. But beyond this, the technologies and research of TII will have global impact.”
Future research directions will be developed by the ATRC’s ASPIRE pillar, in collaboration with stakeholders from across a diverse range of industry sectors.
“ASPIRE defines the problem, sets milestones, and monitors the progress of the projects,” Al Bannai says. “It will also make impactful decisions related to the selection of research partners and the allocation of funding, to ensure that their R&D priorities align with Abu Dhabi and the UAE's broader development goals.”
Image from: Agritecture
Nurturing Next-Generation Talent
To address these challenges, ATRC’s first initiative is a talent development programme, NexTech, which has begun the recruitment of 125 local researchers, who will work across 31 projects in collaboration with 23 world-leading research centres.
Alongside universities and research institutes from across the US, the UK, Europe and South America, these partners include Abu Dhabi’s own Khalifa University, and Mohamed bin Zayed University of Artificial Intelligence, the world’s first graduate-level institute focused on artificial intelligence.
“Our aim is to up skill the researchers by allowing them to work across various disciplines in collaboration with world-renowned experts,” Al Bannai says.
Beyond academic collaborators, TII is also working with a number of industry partners, such as hyperloop technology company, Virgin Hyperloop. Such industry collaborations, Al Bannai points out, are essential to ensuring that TII research directly tackles relevant problems and has a smooth path to commercial impact in order to fuel job creation across the UAE.
“By engaging with top global talent, universities and research institutions and industry players, TII connects an intellectual community,” he says. “This reinforces Abu Dhabi and the UAE’s status as a global hub for innovation and contributes to the broader development of the knowledge-based economy.”
[WEBINAR] Hiring For Indoor Farming | Human Resources In 2021
During this insightful session, our panel will touch on the hot areas of hiring in the Indoor Vertical Farming market today
WHAT'S HAPPENING IN THE INDOOR FARMING JOB MARKET? JOIN THE CONVERSATION & FIND OUT!
SAVE YOUR SPOT
HIRING FOR INDOOR VERTICAL FARMING: HUMAN RESOURCES IN 2021
WEDNESDAY, FEBRUARY 17, 2021
2-3 PM EDT
During this insightful session, our panel will touch on the hot areas of hiring in the Indoor Vertical Farming market today, including:
• Disciplines Hiring Manager are Seeking (computer science, A/I, robotics, engineering, & more)
• Expansion and Hiring Regions
• How Academia Can Help With Farmers of the Future | NextGen Farmers
MODERATOR
Tim Hammerich, Senior Director for Strategic Communications, Cogent Consulting and creator |host of “Future of Agriculture” podcast
PANELISTS
MaryAlice Feinstein, Chief People Officer, People Operations, AeroFarms
Brac Webb, Co-founder, and CTO, Fifth Season
Keri Gasiorowski, Chief Human Resources Officer, Kalera Inc.
LEARN MORE & REGISTER
SPECIAL THANKS TO OUR INDOOR AG-CON
EXHIBITORS, SPONSORS, MEDIA ALLIES &
INDUSTRY PARTNERS
Indoor Ag-Con, 950 Scales Road, Building #200, Suwanee, GA 30024, United States
“Autonomy Will Not Happen Until We Start Sharing Data”
In an emerging industry with companies eager to prove their technologies’ worth, Sensei Ag remains form-factor agnostic, meaning that the agtech company remains unbiased towards different farm hardware solutions – focusing more on software and plant biology. Sensei Ag is a market-changing agtech company that develops agile growing solutions through a highly iterative approach to farming, focused on improving the nutritional quality of fruits and vegetables while also reducing production costs. The company combines plant science, computer vision, machine learning, automation and artificial intelligence into its growing systems
In an emerging industry with companies eager to prove their technologies’ worth, Sensei Ag remains form-factor agnostic, meaning that the agtech company remains unbiased towards different farm hardware solutions – focusing more on software and plant biology.
Sensei Ag is a market-changing agtech company that develops agile growing solutions through a highly iterative approach to farming, focused on improving the nutritional quality of fruits and vegetables while also reducing production costs. The company combines plant science, computer vision, machine learning, automation and artificial intelligence into its growing systems.
According to Sensei Ag CEO Sonia Lo, remaining form factor agnostic is key to the company’s mission of providing hyper-nutritious food to as large a consumer base as possible, which it achieves through both vertical farms and greenhouses.
Image from: Sensei Ag
“We believe that the most robust data comes from operating farms of multiple types. So, not just vertical farms, but also low-tech and high-tech greenhouses. And with vertical farms, we are looking at a number of form factors. Our end goal is to be a grower’s resource and know more about growing at scale with different form factors than anyone else.”
The company is also a strong advocate for open data in the vertical farming industry, which is currently lacking, as evidenced by the siloed development of multiple systems and products, some of which cannot be easily integrated into third-party systems.
“There are lots of data flows and increasingly inexpensive farm management systems. The question, then, is the organization of data into intelligence. Intelligence facilitates autonomy, and as we manage data flows, more farms can become autonomous. But I don’t think autonomy will happen until we start sharing data. For example, we saw an automation supplier with a great robot.
The problem was the robot only works in their ecosystem, so you have to buy the whole farming solution in order for the one robot to work. Ideally, that robot would be plug and play and be able to work in greenhouses and vertical farms,” says Sonia.
Image from: Sensei Ag
According to Sonia, open data in the vertical farming industry may currently be restricted by the dominance of venture financing, which has its own return mandates to fulfill and sometimes wants a “winner takes it all” mentality for the ventures it chooses to back. While such financing has allowed the vertical farming industry to emerge, it may ultimately hinder the industry’s scalability and information sharing.
“There is definitely a capital model in Silicon Valley and in venture capital world in general which is not focused on profitability but is focused on technological achievement and market penetration. We saw this in solar and in the renewables industry when multiple venture capital funds invested in solar assets. Then, the bottom fell out because government subsidies fell away in certain jurisdictions.
I hope that agricultural infrastructure currently financed by venture capital will not necessarily follow the same pathway as solar, but will instead find a public-private partnership model. At some point, these farms need to demonstrate a profit for the debt capital markets to allow scale to occur.”
Image from: Sensei Ag
By embracing open data and transparency, Sonia explains that the vertical farming industry can further mature and iterate with technology to continue lowering costs. By continuously collecting and sharing data from different farm forms, the vertical farming industry would have better insights into the true costs which, according to Sonia, “helps drive scale because it enables the finance community to understand how the farms can be risk assessed and financed.”
Looking ahead, Sensei Ag hopes to form partnerships around the world to bring its innovative, data-driven growing systems across the globe. Taking the Middle East, China and Japan as examples, Sonia explained that the goal would be to choose strategic partners in each region whose local knowledge and business prowess would allow Sensei Ag to iterate its technologies appropriately and serve local markets, bringing cost-competitive farming techniques and nutritious, local produce around the world.
Advice For New Vertical Farmers: Grower Spotlight on Andrew Worrall
Andrew is LettUs Grow’s Farm Manager, he manages two of our sites across Bristol and has brought a wealth of knowledge into the company through his previous experience in indoor farming roles across the UK including at Grow Up, Raynor Foods & RootLabs. In this three part interview, we explore what it’s been like to move from animal husbandry to indoor farming, the lessons he’s learned along the way, what it’s like working at LettUs Grow and his advice for those new to indoor growing.
Last week we spoke about running a farm at LettUs Grow. What excites you about vertical farming?
It’s the future of the industry. Also, the amount of salad that these farms can produce for their local community. We want to be able to eat salad all year round and we import to make that happen. However, just a small farm can easily provide for its local community, very efficiently and all year round. The sustainability element is also exciting: with our salad there’s no food miles, it’s very minimalistic. You could use an electric van or bike to distribute this crop if you wanted to. It’s a step forward in terms of what we need to do to take care of our planet.
What do you think are the biggest downsides to vertical farming?
It’s still a new technology and it can be expensive. The biggest roadblock facing the industry is that we need more people and companies to collaborate together to make sure we can build these farms at a sensible rate, so we can provide farms to anyone. We want to be able to provide farms to people, communities and countries that don’t have a lot of money, so that they can provide affordable fresh produce to local people.
How has vertical farming impacted your life?
Massively! I wanted to find my passion, a job that I loved - that was very important to me. It’s satisfying to be in a position now where I’m very happy to be doing what I do and I look forward to going into work. I was happy to make the move from London to Bristol. I would have moved even further if it meant being able to continue working within this industry.
Image from: LettUs Grow
How do you see vertical farming playing a part in the future?
When indoor farming first came about, it had a reputation of being competition for outdoor farming, which just isn’t the case. There’s so much we can’t grow that outdoor farming can provide, such as cereal crops. I’m glad we’re at a stage where indoor and outdoor farms can start to work together to optimise both methods. With these new relationships, there should be a good increase in the amount of indoor farms you’ll be seeing. What LettUs Grow offers with DROP & GROW™ is an exciting project because that’s a 40ft shipping container which can be placed pretty much anywhere. It’s not that big - it could go in a car park or behind a restaurant, but actually provide quite a lot of salad to that area.
How much of our food should be grown this way?
Good question. If you had asked me a while back I would have just said salad, but now I’ve changed my mind. Indoor farming can have a massive impact on propagation, especially aeroponics, because of how we aerate and nourish our roots. We could start lettuce for greenhouse projects and we can also propagate tomatoes, strawberries and tree whips. Propagating trees in this way could potentially be hugely beneficial and it’s something we want to do more of.
We can also quickly grow large amounts of microgreens, baby leafs, herbs and we can grow fruiting crops like strawberries. We are slowly chipping away and it’s really exciting. I’m waiting to see if I can ever say I’ve grown or propagated every crop that can be grown in these farms!
What do you think are the biggest benefits of vertical farming?
How fast these crops can grow! The turnover can be as short as 5 days from seed, depending on the crop. Also how clean it can be - I’m very dedicated to making sure these farms are built to ensure they are easy to be maintained and clean. The most exciting part is the crop growth rate though - it’s incredible how fast our crop grows from seed to plate. In a very well maintained growing calendar, which Ostara® is great for supporting, you can optimise your beds so that the day you harvest can also be the day you germinate onto that same bed. Your farms can be forever providing salad at very fast rates.
Image from: LettUs Grow
What was the biggest change you encountered during your years indoor farming?
Moving from being a production grower to an R&D grower. It has been a great change! As a production grower I knew what I needed to know about growing the plant safely and getting it onto a plate so it was good for the consumer. Now I’m fully optimising, learning and understanding the plants completely, so that I can help the grower that I used to be. We spend a lot of time on crop recipes to make sure that whoever we sell our farms to can start up very quickly and they won’t have to spend months developing their crops. If they have the customers and clients behind them, they can buy DROP & GROW and start producing salad as soon as it's been commissioned.
What was the biggest change you encountered in the industry?
More and more people are speaking about what’s going on in the industry and getting involved. I get so many messages on LinkedIn with people who want to get into this career. It’s exciting to see that indoor growing is a career people can access now. When I was developing my skills I didn’t know I would end up in indoor farming. There are more opportunities than ever before. For example, our Crop Technician is doing a placement here for 2 years. The aim is that they can gain the skill sets and knowledge they need to then go off and do the same practice in any farm they want.
What advice do you have for people who are looking to start a career in growing?
Reach out to companies who are already out there. You could start off part-time or as an assistant. If you are patient and dedicated then it’s a journey I promise you won’t regret. It takes a lot of work, but the outcome is amazing - you’ll be learning so much about this new technology. You’ll also build great relationships: there are so many amazing people in this industry who are so interesting, with different backgrounds, who are willing to share their knowledge. You can always learn more and other people are a great source of that.
What about for those looking to start a vertical farming business?
Do your homework. There are people out there who you can reach out to and it’s very easy to get information. It’s very easy to get excited about the idea and jump straight into it, because it is exciting and can be very rewarding, but it’s really important to do it step by step. Know how to scale properly, learning the differences between a small and larger farm. Understand how many people you’ll need and the logistics. I’d also advise people to get some practical work experience before you buy. You want to start the company knowing the tricks of the trade.
Image from: LettUs Grow
LettUs Grow Blog: www.lettusgrow.com/blog/advice-for-vertical-farmers
Giant Vertical Farm Opens in Denmark
The produce grown here will be harvested 15 times a year, despite never seeing soil or daylight. It is lit up around the clock by 20,000 specialized LED lightbulbs
DECEMBER 7, 2020
by Camille Bas-Wohlert
First developed around a decade ago, vertical farms have taken off in Asia and the United States
A purple glow illuminates stacked boxes where lettuce, herbs and kale will soon be sprouting at one of Europe's biggest "vertical farms" which has just opened in a warehouse in an industrial zone in Copenhagen.
Fourteen layers of racks soar from floor to ceiling in this massive, 7,000-square-metre (75,350-square-foot) hangar used by Danish start-up Nordic Harvest.
The produce grown here will be harvested 15 times a year, despite never seeing soil or daylight. It is lit up around the clock by 20,000 specialized LED lightbulbs.
Danish Nordic Harvest raises DKK 62 million. DKK to one of Europe's largest vertical farms
In this futuristic farm, little robots deliver trays of seeds from aisle to aisle.
The large aluminum boxes are mostly empty for now, but lettuce and other leafy greens will soon be growing.
Some 200 tonnes of produce are due to be harvested in the first quarter of 2021, and almost 1,000 tonnes annually when the farm is running at full capacity by the end of 2021, explains Anders Riemann, founder and chief executive of Nordic Harvest.
That would make the Taastrup warehouse one of Europe's biggest vertical farms.
These urban facilities have unsurprisingly received a cool welcome from rural farmers, who have questioned their ability to feed the planet and criticised their electricity consumption.
But Riemann stresses the environmental benefits of his farm, with produce grown close to consumers and its use of green electricity.
A robot, used to plant seeds and check the plants while growing, moves past vertical racks at 'Nordic Harvest' in Taastrup, a suburb west of Copenhagen
"A vertical farm is characterized by not harming the environment by recycling all the water and nutrition or fertilizer," says Riemann, who uses no pesticides.
In Denmark, a world leader in wind farms, about 40 percent of electricity consumption is wind-based.
"In our case, we use 100 percent energy from windmills which makes us CO2-neutral," he adds.
While he wouldn't disclose how much Nordic Harvest's electricity bill comes to, he said the power came with "wind certificates" registered on the Danish commodities exchange.
These legal documents guarantee that "the amount of electricity you consume in one year is equivalent to the electricity produced by numbered windmills offshore".
Slow start in Europe
First developed around a decade ago, vertical farms have taken off in Asia and the United States, which is home to the world's biggest.
The idea has slowly started to catch on in Europe.
Urban farming could even allow land exploited by single-culture farming to be reforested, Riemann said.
Shelves of the vertical plant farm 'Nordic Harvest' where lettuce, herbs and kale will soon be growing
"We moved the forests in order to have fields," he laments, noting that now farmers like him can bring "some of the food production back into the cities where you can grow on much smaller land and space-optimized in height".
His farm uses one liter of water per kilogram of produce, or 40 times less than underground farms and 250 times less than in fields, he says.
The names of his clients remain confidential, but they include caterers, restaurants, and even supermarkets.
According to a poll conducted by the Danish Farmers Union, 95 percent of Danes are ready to change their consumer behavior to protect the environment.
Nordic Harvest's products are however not labeled as organic.
"The EU regulation dictates that the word organic is linked to the word 'soil' so if you take soil out of the equation you can't name it organic anymore," he says.
But "we grow on the same terms as organic: we don't use pesticides or insecticides".
Meanwhile, Aarhus University agriculture professor Carl-Otto Ottosen notes that Denmark "doesn't have a space problem" and companies like Riemann's are largely a novelty that won't threaten Danish farming traditions.
"It works in Japan or Shanghai, where there's no space to farm and where they want quality products," he says.
But despite what polls suggest, Ottosen insists Danes are still more inclined to buy products based on "price, not taste".
Dutch Scale-Up PlantLab Launches First Production Site In USA
In Indianapolis, PlantLab has entered into a joint venture with Englewood Community Development Corporation, which works to promote the sustainable development of urban corridors
Annual Harvest of 420,000 Kilos For Indianapolis Residents
Den Bosch (The Netherlands), December 7, 2020 – PlantLab, the Dutch indoor farming pioneer, has opened a new production site in Indianapolis (Indiana). This first-ever ‘Plant Paradise’ in the United States is growing vegetables for the local population at a site that was previously unthinkable - a former battery factory near the city center.
In Indianapolis, PlantLab has entered into a joint venture with Englewood Community Development Corporation, which works to promote the sustainable development of urban corridors. The fresh vegetables are being marketed under the brand name ‘Uplift, good food for purpose’. “Our collaboration allows us to deliver greater value to the population of Indianapolis,” explains Michiel Peters, CEO of PlantLab. “This is also very much in line with our global mission: we not only increase the supply of sustainable and healthy fresh food for local clients but also create local jobs in a completely new sector.”
First harvest
This week, the first herbs and heads of lettuce will be harvested at the 54,000 square feet growing site for delivery to local supermarkets and foodservice companies. PlantLab is growing various kinds of tomatoes, cucumbers, lettuce, and herbs in Indianapolis. The new location will provide an annual supply of close to 1,000,000 pounds of fresh vegetables as well as jobs for roughly 30-70 persons. Chris Arnold, CEO Uplift: “It tastes like I went out to my backyard garden, picked it, and put it in my bowl.”
The new production site, the former battery factory of P.R. Mallory, was once the pride of the city, also producing batteries for army vehicles during World War II. After the factory fell into decline in the 1970s, a joint effort by the municipality, NGOs, and businesses breathed new life into the area with the construction of a new campus.
The United States and the Bahamas
Indianapolis is the first American city where the Dutch scale-up PlantLab is opening an indoor production facility. The Bahamas will soon follow. PlantLab’s production sites can be located anywhere in the world, even on barren soil or in urban areas. Thanks to optimized temperature, moisture, and light regulation, the crops grow to their full potential, while at the same time needing only 5% of the water used in conventional farming. Light is provided by specially developed LEDs, which radiate the exact color of light needed by the plant for photosynthesis.
PlantLab has a dedicated R&D center in Den Bosch (the Netherlands), the largest such center in the world for vertical farming, as well as a commercial production site in Amsterdam. PlantLab holds patents for its indoor farming technology in 74 different countries, including the US. Its indoor farming patent applies to the method used for regulating the root/substrate temperature as well as the evaporation and leaf temperature of the crop. Many of the indoor farming systems presently in use may constitute a violation of PlantLab’s intellectual property.
Globally patented technology
Over the last 10 years, PlantLab has worked hard to realize a breakthrough via its extremely efficient and globally patented technology for innovative urban farming. The new technology is already being put into practice at its commercial production site in Amsterdam, the capital of the Netherlands, as well as at this new location in Indianapolis. The breakthrough technology makes it possible to grow day-fresh, healthy, delicious vegetables on a large scale very near to the consumer without the need for any chemical crop control agents. On a production site no bigger than two American football fields, it is now possible to grow enough produce to supply a city of 100,000 residents with 200 g of fresh vegetables each on a daily basis.
This summer, PlantLab received an injection of €20 million of growth capital from De Hoge Dennen Capital. The scale-up intends to use these funds to launch indoor production sites in various locations, including the Netherlands, the United States, and the Bahamas.
About PlantLab
PlantLab specializes in technology for innovative urban farming, the sustainable food supply of the future. The company was founded in 2010 in Den Bosch with the goal of optimizing the production of food for our planet. Over the last 10 years, the company has already invested € 50 million in the development of technology that makes it possible to grow healthy, day fresh vegetables close to the consumer anywhere in the world without the use of chemical crop agents sustainable and environmentally friendly, while at the same time reducing water consumption to an absolute minimum. Enough crops can be grown on an area no bigger than two football fields to supply a city of 100,000 residents with 200 g of fresh vegetables every day. As the new technology can be used everywhere and always, it also makes it possible to radically shorten the logistic chain year-round. The benefits: superior product quality, longer shelf life, much less food wastage, and no CO2 emissions or nuisance associated with long-distance transport. PlantLab aims to make its technology accessible to everyone and therefore bring fresh and sustainably grown food within reach for everyone.
Note for the editors, not for publication
For more information and for requesting interviews with the initiators, please contact Koolhoven & Partners: plantlab@koolhovenenpartners.nl or +31 85 4017175.
You can download royalty-free images here.
PlantLab, the Dutch indoor farming pioneer, has opened a new production site in Indianapolis (Indiana). On the left Chris Arnold, CEO of Uplift, on the right co-founder of PlantLab Leon van Duijn. Click on the picture to download the royalty-free image in a high resolution.
SINGAPORE: High-Five: Developing “The World’s First Vertical Aquaculture Farm”
Singapore-based entrepreneur John Diener is committed to developing a series of urban aquaculture facilities that are able to produce shrimp, whitefish and seaweeds in high tech five-story farming systems
by Rob Fletcher
24 November 2020
Singapore-based entrepreneur John Diener is committed to developing a series of urban aquaculture facilities that are able to produce shrimp, whitefish, and seaweeds in high tech five-story farming systems.
John Diener aims to produce shrimp, tilapia, and seaweeds in five-tier facilities that can be fitted into the footprint of a standard warehouse. © Akualogix
The last decade of Diener’s career has seen him involved in a number of aquaculture-related ventures, as well as agritech startups, and the concept of a completely novel farming system came to him in 2016 when he was researching how machine learning could benefit aquaculture during a part-time MSc in aquaculture at St Andrews University.
“I have a lot of experience in data science and I wanted to find out what would happen if you reassessed the whole concept of aquaculture,” he explains.
Diener’s research led him to believe that vertical farms using cutting-edge technologies had the capacity to produce – for their footprint – an impressive amount of seafood, making them suitable for urban settings.
Three pillars
Diener describes the development of the system as resting on three pillars – biological, mechanical and digital. The biological side relates to investigating the most productive integrated-multitrophic (IMTA) system, with vannamei shrimp as the primary species.
“The business plan has been developed around shrimp – they’re a unique product in terms of their flavour profile, much like salmon are, which makes it very hard to produce substitutes. And they can also be raised at high densities,” Diener notes.
“We’ve also incorporated a filter-feeding fish – we’re currently using tilapia because they’re very robust, but will probably trial milkfish too,” he adds.
The bottom of the IMTA pyramid is taken up by sea grapes – called umibudo in Japan, where they are considered something of a delicacy.
“These are known as ‘the green caviar’ in parts of Asia, so have the potential to be sold as food. They can also be used as an ingredient in shrimp feeds, as we’re aiming to produce our own, sustainable feeds, while they also help to remove nitrates and phosphates from the water,” says Diener.
Technology
The second pillar consists of the engineering, and Diener intends to develop raceway systems four or five levels high, which are equipped with modular autonomous devices to optimise factors such as measuring water quality. The third pillar relates to the digital side of operations.
“We’re investing time and effort to develop advanced technology to manage feeding – both in terms of studying shrimp behaviour so we know when to feed and in terms of measuring the biomass in the systems, so we know how much to feed. We will also be looking to manage the water quality by feeding information into a deep learning algorithm that can control factors like pump speeds and the addition of minerals to the water,” he says.
The digital side also covers the farm’s “Aqua OS” [operational systems], ensuring all the technology works together, to simplify the management of all the tanks, Diener explains.
Launch
John Diener, founder of Akualogix
Four years after coming up with the concept Diener launched his own company, called Akualogix, in August, after finding a suitable site for a pilot-scale facility, in a building owned by the Marine Aquaculture Centre, on St John’s island in Singapore. This will, he notes, be perfect for securing proof-of-concept, before he looks to expand into a commercial-scale facility.
Initially self-funded, by Diener and the company’s co-founder, they are now looking into securing pre-series A funding in order to build a larger scale production unit.
Funding opportunities have remained robust in the agri-food sector, despite the outbreak of Covid. And as our systems are designed for an urban environment, and food security is increasingly important in Singapore and other cities around the world, we see strong investor interest
“Funding opportunities have remained robust in the agri-food sector, despite the outbreak of Covid. And as our systems are designed for an urban environment, and food security is increasingly important in Singapore and other cities around the world, we see strong investor interest,” Diener reflects.
The current farm has – he predicts – the capacity to produce 500-600 kg of shrimp per cycle, but he’s not yet sure what the yields of the tilapia or sea grapes will be – pointing out that no one has undertaken a mass balance study in such a system.
A juvenile shrimp at the pilot facility in Singapore. © Akualogix
“Our business economics is based on shrimp – making any money from the tilapia would be the icing on the cake – but the main reason we have the fish is part of the multi-trophic system and benefit the overall environment, they’re part of the filtration system,” he explains.
We will be looking at establishing commercial farms that can produce in the region of 1,000 to 1,500 tonnes of shrimp a year. It might not sound like much compared to some of the commercial salmon RAS that are now being established, but if we’re operating 20 or 30 farms that would make us one of the biggest shrimp producers in the world
Next steps
Once the pilot facility has fulfilled its potential Diener aims to establish a farm – and ultimately a network of farms – that use Akualogix’s design and equipment, establishing partnerships in a range of countries, primarily in Asia, as the concept takes off.
“We will be looking at establishing commercial farms that can produce in the region of 1,000 to 1,500 tonnes of shrimp a year. It might not sound like much compared to some of the commercial salmon RAS that are now being established, but if we’re operating 20 or 30 farms that would make us one of the biggest shrimp producers in the world,” he points out.
Diener is also looking to develop a unique, sustainable feed that’s designed specifically for producing shrimp in RAS facilities.
“The current range of commercial shrimp feeds are not great for use in RAS, and we’re looking to produce a next generation shrimp feed using sustainable ingredients. And we’re looking for a flavour enhancing additive as a finishing diet – potentially one that comes from algae,” he says.
Given the technology involved and the emphasis on sustainable feed ingredients Diener is aware that production costs are going to be considerably higher than conventional shrimp farms.
“We estimate that our cost of production will be 40-50 percent higher than shrimp produced in a pond in, say, India. But we’re close to market and can charge a premium for a fresh product that’s so sustainably produced,” he says.
Operational experience
The pilot facility holds 30,000 shrimp per cohort and 1,000 tilapia. The former are housed in a two-stage grow-out system and he aims to take them from the end of the nursery stage to harvest in 60 days, while achieving survival rates of roughly 90 percent.
However, as Diener admits, the design concepts of the system are still evolving, and there are other issues that have caused setbacks.
“It turned out that our first batch of PL [post-larvae] had pathogenic vibrio and we started seeing mortalities related to vibriosis,” he explains.
It was an unfortunate start, but a useful reminder of the importance of biosecurity.
“We decided to implement a full biosecurity package [once operating commercially], which will include our own hatcheries to prevent the introduction of pathogens,” he says.
Should the pilot facility prove productive, and investment forthcoming, Diener then aims to roll out the concept across some of Asia’s most populous coastal cities.
“There’s currently a lot of investment in salmon RAS and I think shrimp are the next species to go in that direction. If we can be a pioneer of shrimp RAS it will be a game-changer,” he concludes.
D.I.Y. Microgreens You Can Grow On Your Kitchen Counter
Think of The Rewards of Cultivating
The Tastes of Summer All Through The winter. You Can Do This.
New to microgreens? Start with something in the mustard family (Brassicaceae) that offers a quick payoff, like arugula (shown), radish or mizuna (a mild-flavored mustard). Credit...Kate Spring
By Margaret Roach
Nov. 18, 2020
Since Kate Spring and her husband, Edge Fuentes, founded Good Heart Farmstead in Vermont in 2013, she has cultivated not just mesclun, strawberries and tomatoes, but also the abundance of the patience required of a farmer. Plant parenthood reminds us: Living things take time. And sometimes they have minds of their own.
Lately, as mother to Waylon, a 7-year-old son she calls “our best crop ever,” Ms. Spring is occasionally asked to dig down even deeper, in a growing test of wills — as she did after three long days of carrot harvest. “There are those moments, like when all those root vegetables need to be washed,” she said, “and your child commandeers the hose and washes you instead.”
But there is one crop, whose time is now, that promises near-instant gratification, requiring little patience and exhibiting blessedly minimal rebellion.
Microgreens — fully developed seed leaves or cotyledons plus a true leaf or two, bigger than sprouts but smaller than baby greens — can be grown indoors in a small space, making them the ideal off-season do-it-yourself project for those who miss the vegetable garden and its in-season flavors. By investing a couple of weeks in each tray of tiny, leafy greens, root vegetables or herbs, you can enliven winter with concentrated bursts of nutrition and taste.
In the garden off-season, freshly harvested basil microgreens grown indoors punch up the summery quotient when Kate Spring, an owner of Good Heart Farmstead, serves red sauce she cooked and froze at peak tomato harvest. Credit...Kate Spring
Microgreens are a cusp-season crop at Good Heart Farmstead, an L3C, or low-profit limited-liability corporation, which means it’s “a mix between a nonprofit and for-profit business — a for-profit but with a social mission in the forefront,” Ms. Spring said. “We work on increasing food access for low-income Vermonters,” often in collaboration with the Northeast Organic Farming Association of Vermont.
The small, certified-organic operation in Worcester (Zone 4a) focuses on farm shares, or CSA subscriptions, serving up to 100 subscribers in the summer season, one of four subscription periods each year.
As the last outdoor fall greens fade, Ms. Spring and Mr. Fuentes sow microgreens in greenhouse flats to add “a nice, fresh green item in the share,” she said, that is otherwise transitioning to roots and other winter storage vegetables.
So order some seed, clear a space on the kitchen counter and call the seed-starting light into service. It’s microgreen season.
Larger seed for microgreens like chard and beets can be scattered on a level surface of an inch and a half of tamped-down, seed-starting soil, with about six to eight seeds per square inch. Credit...Kate Spring
Why Grow Microgreens?
Besides the sheer awe inherent in any version of seed-starting, there are other motivating factors. Price, for instance.
Microgreens are what farmers refer to as a high-value crop. In plastic grocery-store clamshell boxes they may run $2 to $3 an ounce ($32 to $48 a pound) — “a really premium product,” Ms. Spring said.
Microgreens are also nutrient-dense. Researchers with the University of Maryland College of Agriculture and Natural Resources and the United States Department of Agriculture evaluated vitamin and carotenoid concentrations in a range of varieties in a 2012 paper. The findings, in brief: Microgreens contained up to 40 times the nutrients of the plants’ mature leaves.
And oh, the flavor. Yes, they brighten up salads and sandwiches, but cilantro microgreens on top of black bean and sweet potato tacos, anyone? They’re highly recommended by the Spring-Fuentes household, where there are always basil microgreens as well, for punching up the summery quotient of red sauce frozen at peak tomato harvest.
“Arugula or basil or kale microgreens are also really good on eggs in the morning,” said Ms. Spring, who tends to use them “as an additive, not the main ingredient.”
Organic field pea seeds will become pea shoots, a customer favorite at Good Heart Farmstead, in Vermont. They are sown very densely and pressed into the soil after the seeds are soaked overnight. Credit...Kate Spring
Start With These Varieties
The diversity of organic microgreen seed offerings in catalogs like Johnny’s Selected Seeds and High Mowing Organic Seeds can be intimidating. Start with something in the mustard family (Brassicaceae) that promises a quick payoff, Ms. Spring suggested, like radish, arugula or mizuna (a mild-flavored mustard).
“Our favorites are basil, cilantro, Red Russian kale and the arugula and mizuna,” Ms. Spring said.
Broccoli and chard are popular, too. Catalogs also offer mixes — like a spicy one of various mustards, selected to germinate and mature on a similar timeline.
While the fields are resting, there are usually microgreens growing on Good Heart Farmstead’s greenhouse benches, to add a fresh, green item to the wintertime CSA shares. Credit...Kate Spring
The Gear
Yes, you can upcycle a cardboard egg carton or plastic sushi container into seed-sowing service, and maybe that’s a good place to begin. But once you’re hooked, a couple of standard nursery flats with drainage holes, called 1020 flats, with trays that fit beneath, will optimize the process. (In the meantime, a plastic boot tray or a rimmed baking sheet could be called into action under ad hoc seedling trays.)
You’ll also need:
A spray bottle for watering (recommended: a one-hand pressure sprayer like the Solo 418)
A germination dome to fit your flats, or paper towels
A bag of seed-starting mix and a moisture-proof tub or other container to stash it in (after each harvest, the soil can be composted, and once the plant matter breaks down, reused two or three times)
A grow light with T5 high-output fluorescent tubes on an adjustable stand (microgreens grow faster and stronger with proper overhead light than they will on a windowsill)
A fan
And, of course, seeds
You can simply can upcycle a cardboard egg carton or plastic sushi container into seed-sowing service, but once you’re hooked, a couple of standard nursery flats with drainage holes, called 1020 flats, and trays that fit beneath will optimize the process. Credit...Kate Spring
Kate Spring’s Step-by-Step Instructions
There is no one-size-fits-all growing method. “It takes some guesswork and practice, so go into it with a trial mind,” Ms. Spring said.
Experimenting with varieties, sowing density and harvest timing — an extra day or two, a half-inch taller than the last batch? — will reveal what works for you.
Using more than one flat and tray will mean fewer gaps in your supply. You could try sowing a succession crop when the current one is within a few days of harvest, or sowing slower- and faster-growing varieties at the same time.
The key is taking notes and researching the catalog websites, where the “number of days to first true leaf” will indicate how fast one variety will grow relative to another. That is especially important if you want to grow partial flats of two things. A good match for a uniform harvest pairs crops with similar days to maturity — like broccoli and Red Russian kale (both 10 to 15 days to true leaf) or basil and cilantro (16 to 25 days).
Trays of microgreens at various stages of development in the Good Heart Farmstead greenhouse benefit from the circulation provided by a fan on low nearby, which helps prevent a fungal disease called damping off. Credit...Kate Spring
Start with the right location: 65 to 70 degrees, not adjacent to a heater or a drafty window. Moisten a supply of potting soil, either in its plastic bag or in a waterproof tub, by adding a small amount of water and mixing it with your hands or a trowel. Squeeze a fistful; it should be moist enough to hold its shape, but not so wet that water drips out.
Then line your tray with an inch or so of soil, tamped down so it’s compact, with an even surface. This will help ensure that seeds have equal soil contact for even germination.
To sow the seeds, scatter them thickly, according to the packet directions, aiming for 10 to 12 seeds per square inch for small seeds like basil, mizuna or kale and six to eight seeds for larger ones like beets or chard. Gently press them into the soil.
Lightly water the seeds with a mister or spray bottle.
Cover the tray with a germination dome or a damp paper towel. (If you use a paper towel, mist it daily so it stays moist during germination.) No supplemental light is needed yet.
As soon as the seeds germinate, usually in about three to five days, remove the dome or towel and place the uncovered tray under grow lights for 16 hours a day.
Water as needed to keep the soil moist but not waterlogged. Microgreens flatten easily, so use a mist or spray, or switch to bottom watering, adding a quarter of an inch of water to the tray below; the flat’s drainage holes will allow the soil to wick up water. For even watering, trays must be on a level surface.
Airflow is important, or thickly sown microgreens can suffer from a fungal disease called damping off. A fan set on low nearby helps.
Microgreens are harvested around the time the first true leaf appears — the one that resembles an older version of the plant, often between an inch or two tall. Use sharp scissors or a harvest knife (Johnny’s and High Moving both sell Victorinox serrated knives). Eat immediately or refrigerate in a closed plastic bag or container for two to three days.
Waylon, the son of Good Heart Farmstead owners Kate Spring and her husband, Edge Fuentes, is 7 years old and a lover of pea shoots and all things salad. This year, he grew his first garden. Credit...Kate Spring
Ready to Graduate to Pea Shoots?
Pea shoots, a CSA-subscriber favorite at Good Heart Farmstead, are grown indoors in spring from organic field pea seeds, a kind of pea used for cover-cropping beds to improve the soil.
There are subtle differences in the process, Ms. Spring said: “We soak the seeds overnight, so that they have a little head start, and we really pack them in there.”
After that, the seeds take 12 to 14 days to harvest, at two to four inches high. Ms. Spring likes them on the bigger side — as does Waylon, who has all too quickly gone from sprout to shoot stage himself, his mother noted.
UrbanKisaan Is Betting On Vertical Farming To Bring Pesticide-Free Vegetables To Consumers And Fight India’s Water Crisis
Severe droughts have drained rivers and reservoirs across parts of India, and more than half a billion people in the world’s second-most populous nation are estimated to run out of drinking water by 2030
September 17, 2020
Image Credits: UrbanKisaan
Disrupt Is Happening Right Now!
It's Not Too Late To Get In On The Action!
Severe droughts have drained rivers and reservoirs across parts of India, and more than half a billion people in the world’s second-most populous nation are estimated to run out of drinking water by 2030.
Signs of this are apparent in farms, which consume the vast majority of total water supplies. Farmers have been struggling in India to grow crops, as they are still heavily reliant on rainwater. Those with means have shifted to grow crops such as pearl millet, cow peas, bottle gourd, and corn — essentially anything but rice — that use a fraction of the water. But most don’t have this luxury.
If that wasn’t enough, Indian cities are facing another challenge: The level of harmful chemicals used in vegetables has gone up significantly over the years.
A Hyderabad-headquartered startup, which is competing in the TechCrunch Disrupt Startup Battlefield this week, thinks it has found a way to address both of these challenges.
Across many of its centers in Hyderabad and Bangalore that look like spaceships from the inside, UrbanKisaan is growing crops, stacked one on top of another.
Vertical farming, a concept that has gained momentum in some Western markets, is still very new in India. The model brings with it a range of benefits. Vihari Kanukollu, the co-founder and chief executive of UrbanKisaan, told TechCrunch in an interview that the startup does not use any soil or harmful chemicals to grow crops and uses 95% less water compared to traditional farms.“
We have built a hydroponic system that allows water to keep flowing and get recycled again and again,” he said. Despite using less water, UrbanKisaan says it produces 30% more crops. “We grow to at least 30-40 feet of height. And it has an infinite loop there,” he said.Kanukollu, 26, said that unlike other vertical farming models, which only grow lettuce and basil, UrbanKisaan has devised technology to grow over 50 varieties of vegetables.
The bigger challenge for UrbanKisaan was just convincing businesses like restaurant chains to buy from it. “Despite us offering much healthier vegetables, businesses still prefer to go with traditionally grown crops and save a few bucks,” he said.
So to counter it, UrbanKisaan sells directly to consumers. Visitors can check in to centers of UrbanKisaan in Hyderabad and Bangalore and buy a range of vegetables.
The startup, backed by Y Combinator and recently by popular South Indian actress Samantha Akkineni, also sells kits for about $200 that anyone can buy and grow vegetables in their own home.
Kanukollu, who has a background in commerce, started to explore the idea about UrbanKisaan in 2018 after being frustrated with not being able to buy fresh, pesticide-free vegetables for his mother, he said.
Luckily for him, he found Sairam Palicherla, a scientist who has spent more than two decades studying farming. The duo spent the first year in research and engaging with farmers.
Today, UrbanKisaan has more than 30 farms. All of these farms turned profitable in their first month, said Kanukollu.“
We are currently growing at 110% average month on month in sales and our average bill value has gone up by 10 times in the last 6 months,” he said.
The startup is also working on reaching a point within the next three months to achieve $150,000 in monthly recurring revenue.
The startup has spent the last few quarters further improving its technology stack. Kanukollu said they have cut down on power consumption from the LED lights by 50% and reduced the cost of manufacturing by 60% per tube.
Kanukollu said the startup works with five farmers currently and is working out ways to find a viable model to bring it to every farmer.
It is also developing a centralized intelligence atop convolutional neural networks to achieve real-time detection to find more harvestable produce, and detect deficiencies in the farm.
UrbanKisaan, which has raised about $1.5 million to date, plans to expand to more metro cities in the country in the coming quarters.
Netled Partners Up With Agritech Start-Up Vertigo Farms – A Focus On New Kinds of Vertical Farming Applications
Vertigo Farms is the first publicly known European actor to produce natural extracts from plants grown indoors. Mainly herbs are grown and processed in a sustainable manner with no use of chemicals, all-year-round, regardless of weather conditions
26th August 2020 by johannak
Netled and a Polish agritech start-up Vertigo Farms have announced a new technology partnership. Vertigo Farms will use Netled’s Vera® vertical farming technology in its indoor growing projects. The collaboration has already started, and the goal is to have the first plants growing at the beginning of 2021.
Vertigo Farms is the first publicly known European actor to produce natural extracts from plants grown indoors. Mainly herbs are grown and processed in a sustainable manner with no use of chemicals, all-year-round, regardless of weather conditions.
“At Vertigo Farms, we believe that vertical farming serves the future not only for direct consumption purposes, but it may also serve as base for highest quality natural extracts for food, cosmetics and pharma industries”, comments Dawid Drzewiecki, the CEO of Vertigo Farms.
The company works with research laboratories and universities to develop methods for optimal conditions and nutrition of plants to boost their growth. Each type of plant requires a different approach. For start, the company will experiment with Safflower, Lovage, and Opium poppy, but there will be more species along the way.
Niko Kivioja, CEO of Netled, comments the newly formed partnership: “Vertigo Farms has a very interesting approach to produce natural extracts. Netled is proud to be Vertigo’s technology partner. In addition to this, our crop specialist team is especially excited to have insight into the new, more exotic plants growing in a vertical farming environment. Globally, we see massive opportunities to produce crops which have very high-quality standards in vertical farms, alongside the more common leafy greens.”
The mission of Vertigo Farms is to process and deliver the highest quality natural ingredients with the use of state-of-the-art solutions. Thus, the goal is a great fit with Netled, as the company aims to provide the best technology, expertise, and guidance for vertical farming projects and actors all around the globe.
Read more about Netled’s Vera® Vertical Farm: https://netled.fi/vertical-farming-vera/
Read more about Vertigo Farms: http://vertigofarms.eu/
Facebook Twitter LinkedIn Share
Filed Under: NewsTagged With: indoor farming, indoor farming technology, indoor growing, sustainable growing, vertical farm, vertical farming, vertical farming expertise, vertical farming technique, vertical farming technology
"Spend Less Time On Your Controls, But More Quality Time With Your Plants"
Practical insights from the Autonomous Greenhouse Challenge
When your team wins the Autonomous Greenhouse Challenge, you may safely call yourself an expert on autonomous cultivation. René Beerkens, who's been with Hoogendoorn Growth Management for twenty years, and Evripidis Papadopoulos, who worked as a Data & Algorithm specialist for Hoogendoorn during the challenge and is now back to LetsGrow.com as a Researcher & Data Analyst, were both involved with winning team AuTomatoes, and from the Hoogendoorn headquarters, they shared some of their insights with growers.
Plant Empowerment
At the heart of Hoogendoorn's holistic approach, René explains, is the concept of Plant Empowerment, which evolved from Next Generation Growing. "We're not only a technical supplier, but also spend an awful lot of time on research and development", René introduces his company.
"The Dutch have a vast history of experience growing plants, mostly by trial and error", he continues. Having learned the laws of physics and completed a lot of research on plant development, growers have moved on from trial and error to a data-driven approach.
Data-driven
This begs the question: why data-driven growing? "We lack experts in the field", René says, "investors want a quick return on investment (they want to invest in something that works from the start), but the main thing is, we want to leave planet Earth in a better way than we found it, using less resources."
The Autonomous Greenhouse Challenge was a perfect opportunity to put this data-driven approach to the test. Using a variety of sensors that measured things like air temperature, humidity, CO2, EC and root temperature, plant temperature, and light levels, a range of data was collected, which was all gathered in one central place so the team could access it wherever they were.
This team featured members from various disciplines, who met once a week. The dashboard, built on the LetsGrow.com platform and customized for Hoogendoorn, helped them analyze data and make the appropriate decisions. As Evripidis puts it, this allows you to "save time for yourself, and due to the holistic approach you find space for further optimization."
Results
The main attraction of the webinar was, of course, the results that participation in the challenge yielded. Using a data-driven strategic approach, the team built their strategies based on historical data from outside conditions. During the challenge, the AI system made adjustments to accommodate the changing circumstances, as can be seen in the below graph showing the ratio temperature radiation (RTR).
"You can't be at your computer daily," Evripidis explains, "so the algorithm made changes automatically, based on feedback from the crop."
It may sound scary to give your precious crops into the hands of an autonomous computer, but the holistic approach taken by team AuTomatoes at least provides the grower with the peace of mind that they can actually see the crop, even when they're not in the greenhouse. The slide below shows how that looks in the dashboard.
René explains that you can also make time-lapses with the dashboard and compare day by day development with the pictures, which is arguably better comparing than just looking at the plants in the greenhouse, because changes in the crop become more noticeable.
Data Driven Operational approach
The next graph shows two identical days with the outside temperature and wind speed the same. In the first day (on the left), the temperature fluctuates a lot, as Evripidis points out. On the second day, the temperature doesn't fluctuate so much, thanks to an intervention in ventilation from the autonomous system, which is of course more favorable to the crop.
While growers are fully focused on ventilation or temperature, Evripidis explains how they came up with VO control. "We keep the windows as closed as possible to trap humidity, so that the temperature is not too high, stomata will remain open, and photosynthesis is maximized. If you trap humidity, you also trap CO2, so it's a win-win situation." With VO control it's not necessary to work with P-band anymore. Growers can set five setpoints, the rest will be done automatically.
René and Evripidis also discussed how the autonomous cultivation system dealt with irrigation and assimilates during the challenge. More about the former can be found in this article from Godfrey Dol on HortiDaily, and Hoogendoorn shared some information on realizing an optimized assimilates balance in this article.
Quality time
In conclusion, it can be said that a grower can do much more based on data. "We had a grower who had never grown tomatoes in the Netherlands, and he did quite well using just data", René shares, telling growers that they can "spend less time on your controls, but more quality time with your plants."
As Evripidis puts it: "We're trying to assist, not take over - we make the car, you drive the car." Or to use another metaphor, as René did: "A plane can fly itself, but the pilot still has to know what happens in the background. We can do a lot with data, but we're still dealing with organisms that are much cleverer than us - they've evolved for millions of years, we are just catching up in the last few years."
For more information:
Hoogendoorn Growth Management
info@hoogendoorn.nl
www.hoogendoorn.nl
Publication date: Mon 7 Sep 2020
Author: Jan Jacob Mekes
© HortiDaily.com
Urban Vertical Farming: The Key To A Sustainable Future
By 2050, the forecast is that we will have an extra 2 billion people on the planet. Many of these people will live in urban areas. And we have already used a third of arable farmland in the past 40 years
Living in a dense city population can make you wonder, "where does our food come from?" When you live in urban areas like Houston, New York City, or Seattle, it's rare that you notice farms on your drive to work.
The idea that our food is grown hundreds to thousands of miles away can be worrisome. What if something were to happen to those farms? Our resources would cut off and we would have limited access to foods. This is why vertical farming in urban areas is critical to ensure cities can be sustainable food leaders.
What is vertical farming?
Vertical farming is the practice of growing crops/foods in vertically stacked layers. This is usually done indoors and in a controlled environment. This method optimizes plant growth and allows the use of soilless techniques such as hydroponics.
How does vertical farming work?
Vertical farming needs several things to work. We'll cover each one below:
Physical Layout - The purpose of farming indoors is to maximize volume. We do this by maximizing the output efficiency per square meter. This is why you will see physical layouts in the form of skyscrapers or vertical tower-like structures.
Lighting - To optimize crop growth, a need for artificial and natural lights are essential.
Growing Medium - There are several different growing mediums for vertical farming. These methods include hydroponics, aeroponics, and aquaponics. Coco Coir, Rockwool, ,Biostrate, Vericulite, Perlite, SunShine #4 and Black Gold are great mediums used in indoor farming.
Sustainability Features - Sustainable features often used with vertical farming feature rainwater tanks, wind turbines, and spaces with low energy costs.
Why is urban vertical farming important?
By 2050, the forecast is that we will have an extra 2 billion people on the planet. Many of these people will live in urban areas. And we have already used a third of arable farmland in the past 40 years.
We need to come up with other sustainable ways to grow food to ensure we can feed everyone. Vertical farming allows us to grow healthy, accessible foods within a few acres of land, close to home.
This is critical for urban areas because they will become more populated over time. Instead of relying on faraway food sources, we need to take matters into our own hands. By establishing urban vertical farming settings, we'll be able to control and grow our own food sources.
Vertical farming also uses 95% less water than traditional farming methods. The use of water needed to grow crops traditionally is wasteful. To be able to handle an influx in population, vertical farming is a sustainable solution.
How does vertical farming benefit us?
There are many reasons why vertical farming is the future of farming. By building vertical farms, there will be an increase in job opportunities. There will be easier access to healthier and attainable foods. With food grown close to home, we will always be aware of where our food comes from.
Because of the controlled environment, there is a higher chance of growth success. We will be able to grow crops year-round and have larger yields. Crops will not be exposed to harsh weather conditions since they'll be grown indoors. Urban vertical farming methods should start being adopted right now.
The Takeaway
To prepare for the upcoming increase in food demand, urban areas need to adopt sustainable policies. People should start growing their food indoors as well as increasing the demand for high-tech farming methods.
IDTechEx Identifies Innovative Companies Changing The Face of Vertical Farming
Vertical farming, the practice of growing crops indoors under tightly controlled conditions, is continuing to expand rapidly
Sep 02, 2020
BOSTON, Sept. 2, 2020,/PRNewswire/ -- Vertical farming, the practice of growing crops indoors under tightly controlled conditions, is continuing to expand rapidly. By using LED lighting tailored to the exact needs of the crop, alongside advanced hydroponic growing systems, and growing crops in vertically stacked trays, vertical farms can achieve yields hundreds of times higher than the same area of traditional farmland.
Investors and entrepreneurs alike are excited about the potential of vertical farming to revolutionize the global food system and some vertical farming companies have raised dizzying amounts of money. Plenty, a San Francisco-based start-up, and the most well-funded vertical farm, has raised $401 million in funding, with backers including SoftBank, Alphabet Chairman Eric Schmidt, and Amazon CEO Jeff Bezos. Fellow US start-ups AeroFarms and Bowery Farming are not far behind, with $238 million and $167.5 million in funding, respectively.
While there has been much attention on these companies and their exploits, there are dozens of other companies in the industry developing their own approaches to vertical farming. Here, we explore some of the most innovative vertical farming start-ups, based on the recent IDTechEx report, "Vertical Farming 2020-2030".
Freight Farms
Freight Farms is a Boston-based vertical farming company that manufactures "container farms", vertical farming systems installed into 40' mobile containers. Alongside its container farms, Freight Farms provides the farmhand software, a hydroponic farm management, and automation platform that also connects users with other Freight Farms customers. Container farms have many advantages - they are easy to transport, compact, and relatively cheap to set up in comparison to other vertical farming systems. Container farms are often turnkey systems, too, meaning that they require much less experience and expertise to operate than either a factory-scale vertical farm or indeed a traditional farm.
Freight Farms recently released its most advanced container farming system, the Greenery, which it believes is the most advanced container farming system in the world. The Greenery is a turnkey system that uses an array of sensors to continuously monitor the growing conditions inside the farm, with the farmhand software automatically making adjustments and planning watering cycles in order to provide the optimum environment for growing crops and allowing users to control their Greenery remotely from a smartphone.
80 Acres – Collaboration, Food Experience
Despite their potential, many vertical farming start-ups have struggled over the years with the labor costs and power requirements for running a high-tech indoor farm. This has often forced producers to sell their crops at a much higher price than conventionally farmed leafy greens. Additionally, many founders of vertical farming companies have little experience in the food industry and can struggle with the day-to-day realities of running a food production industry.
80 Acres is an Ohio-based vertical farming start-up aiming to overcome these challenges by constructing the world's first fully automated indoor farm. The company was founded in November 2015 by Tisha Livingston and Mike Zelkind, who between them have over 50 years' experience in the food industry. Collaboration is also important to 80 Acres. The company believes that vertical farming is a very multidisciplinary field, requiring collaboration between partners who are experts in their own discipline. Signify (formerly Philips Lighting) developed the LEDs used in the facility and Dutch greenhouse automation company Priva developed the control and fertigation systems, with 80 Acres using its experience in food to bring the system together and integrate the technology.
The company currently operates a 75,000 square foot facility in Hamilton, a suburb of Cincinnati, which is set to expand to 150,000 square feet in summer 2020 following a $40 million investment from Virgo Investment Group. When completed, 80 Acres claims this facility will be the world's first fully automated indoor farm. The farm will be automated from seeding to growing to harvesting, using robotics, artificial intelligence, data analytics, and around-the-clock monitoring sensors and control systems to optimize every aspect of growing produce indoors.
Jones Food Company
Jones Food Company is a British vertical farming start-up that operates Europe's largest vertical farm out of a warehouse in Scunthorpe, UK. It was founded in 2016 by James Lloyd-Jones and Paul Challinor, who wanted to build the largest vertical farming facility that they could in order to help overcome some of the operational problems plaguing the industry and bring vertical farming to the mainstream. After visiting several vertical farms in Japan, they decide that the only way to make vertical farming a success is to focus on scale and automation.
Jones Food Company focuses on maximizing automation and robotics in their facility to minimize operating costs, with its facility being modeled on a car factory, with the growing process resembling a production line - over the 25-day growing period, plants move from one end of the facility to another. Much of the work is done by machines, helping to reduce labor costs. Harvesting is carried out by bespoke machines and the heavy lifting is performed by a robot called Frank. This focus on automation means that only six employees are required to operate the Scunthorpe facility.
Jones Food Company has partnered with UK online grocery company Ocado, which currently owns about 70% of the business. Through this partnership, Jones Food Company is aiming to set up vertical farms next to Ocado's grocery depots, meaning that fresh produce could be delivered to shoppers within an hour of being picked.
Infarm
Infarm is a Berlin-based start-up that sells modular, hydroponic vertical farms for growing leafy greens and herbs in supermarkets, schools, and offices. A single two-square meter unit can grow 8,000 plants in a year, with the company claiming its farms use 95% less water than soil-based farms, take up 99.5% less space, use zero chemical pesticides, need 90% less transportation, and use 75% less fertilizer.
Infarm has partnered with several major supermarkets across Europe, where it has currently deployed over 500 farms in stores and distribution centers. The company is also beginning to expand in the USA, having recently partnered with Kroger to trial its indoor farms in two QFC stores in Seattle. In the UK, it has partnered with supermarket chain Marks & Spencer, which is trialing in-store urban farming in seven locations in London, growing Italian basil, Greek basil, Bordeaux basil, mint, mountain coriander, thyme, and curly parsley.
The company's business model is based around an "agriculture-as-a-service" model. The modular farms remain the property of Infarm, which receives income per harvested plant. Infarm then coordinates with clients such as retailers and takes care of the farm including installation, cultivation, harvesting, and maintenance. Aside from the regular visits by service personnel to plant new plants, the farms are controlled remotely. This modular, data-driven, and distributed approach — a combination of big data, IoT, and cloud analytics — sets Infarm apart from competitors. From a price point, Infarm is attractive for supermarkets, which get a better product at the same price. In addition, the plants, especially herbs, are harvested fresh, preserving color, smell, flavor, and nutrients.
For more information about the vertical farming industry and the innovative companies operating within the space, please see the recent IDTechEx report, "Vertical Farming 2020-2030", www.IDTechEx.com/VertFarm or for the full portfolio of related research available from IDTechEx please visit www.IDTechEx.com/Research.
IDTechEx guides your strategic business decisions through its Research, Consultancy, and Event products, helping you profit from emerging technologies. For more information on IDTechEx Research and Consultancy, contact research@IDTechEx.com or visit www.IDTechEx.com.
Ikea Just Shared Its Garden Sphere Design For Free
Blueprints for IKEA’s Garden Sphere are available for free download, distribution, and reuse. The product design allows any users to feed an entire street, block, or even neighborhood, depending on population
IKEA's idea lab Space 10 created a sustainable, spherical garden for urban environments called The Growroom with open-source blueprint and instructions.
IKEA is making its garden sphere design free to access.
May 12, 2020
Blueprints for IKEA’s Garden Sphere are available for free download, distribution, and reuse. The product design allows any users to feed an entire street, block, or even neighborhood, depending on population.
The Growroom gardening sphere design makes it easy to grow fresh produce in dense urban areas. The multi-tiered, spherical design mimic some forms of verticle gardening by maximizing airspace. The structure’s designers, architects Sine Lindholm and Mads-Ulrik Husumtoin are part of Space 10—IKEA’s innovative idea lab.
The entire Growroom frame can be constructed with just a few supplies: plywood, screws, a hammer, and access to a local fab lab. Experts suggest small workshops offering digital fabrication are increasingly commonplace. “This means most people — in theory — could produce almost anything themselves,” the company press release read.
Community-grown food minimizes the distance traveled and other contributing factors in food production’s carbon footprint. Many people do not have ready access to fresh produce and outdoor space. The Growroom can help facilitate shared access to both.
“Local food represents a serious alternative to the global food model. It reduces food miles and our pressure on the environment and educates our children about where food actually comes from,” Space 10 noted on its website. “The challenge is that traditional farming takes up a lot of space — and space is a scarce resource in our urban environments.”
The Growroom could increase access to fresh produce in urban areas. | Image/bellinghammakers
IKEA And Sustainability
IKEA emphasizes sustainability in several other areas of its business. In its 2018 sustainability report, IKEA estimated its climate footprint to be 26.9 million tons of carbon dioxide equivalent. Following this, the home furnishings retail giant announced plans to invest over $220 million in efforts to become “climate positive.”
IKEA has also banned all single-use plastic from its cafes to minimize waste and preserve the environment. Instead, the company now uses alternatives such as wooden cutlery and paper straws. The retailer says it sources all materials from sustainable suppliers.
STAFF WRITER | BRISTOL, UNITED KINGDOM | CONTACTABLE VIA: LIAM@LIVEKINDLY.COM
Liam writes about environmental and social sustainability, and the protection of animals. He has a BA Hons in English Literature and Film and also writes for Sustainable Business Magazine. Liam is interested in intersectional politics and DIY music.
USA - COLORADO - Geodesic Growing Dome Nears Completion On CMC Campus, Benefits Multiple Programs
When it’s done, the dome will be full of trees, flowers and edible plants, offering a hands-on and in-person experience for students enrolled in the college’s sustainability studies, permaculture and culinary programs
August 27, 2020
STEAMBOAT SPRINGS — A geodesic growing dome has been erected at Bear Park on the Colorado Mountain College Steamboat Springs campus off of Crawford Avenue. The structure will serve, in part, as a greenhouse, extending the growing season and benefiting the sustainability studies program as well as others.
The dome is one part of an expansion project that was approved two years ago, allowing the college to construct the dome, a teaching pavilion, and a restroom. While the outside of the dome is complete, plumbing and electric are still being installed. The inside will take time to fill as well. Tina Evans, CMC professor of sustainability studies, expects the entire project to be completed sometime next summer.
When it’s done, the dome will be full of trees, flowers, and edible plants, offering a hands-on and in-person experience for students enrolled in the college’s sustainability studies, permaculture, and culinary programs.“
Clearly, its benefit is as an educational space, a demonstration space for growing in our region,” Evans said. “It’s really an awesome venue for learning about growing food year-round in the challenging environment in a mountain community.”
Evans said the Steamboat Springs growing season is 59 days and occurs in the summer when few students are on campus. The dome will allow year-round growing.
The design of the inside and outside gardens at Bear Park, where the dome is located, was created using permaculture, which creates beneficial relationships between all the elements of the garden. Some plants provide shade, and others offer ground cover. Some will draw in pollinators, and others repel pests. The strength of one plant benefits all of them.
“We’re trying to create systems that take care of themselves a little bit more than our food systems do in monoculture agriculture,” Evans said. “We’ll have nitrogen-fixing plants in with other plants. We’ll grow plants that provide really good mulch that pull nutrients up from the soil.”
The dome, which was funded by the Yampa Valley Electric Association’s Roundup program, the Craig-Scheckman Family Foundation, and an anonymous donor, was purchased from a Colorado company called Growing Spaces. The structure is 42 feet in diameter or nearly 1,400 square feet. The triangle panels, made of polycarbonate, are not only structurally strong but hold in heat and disperse light better than other materials like glass.
The interior of the dome will also be home to an aquaculture project of large water tanks filled with fish, although Evans isn’t sure what type of fish yet.
The water-filled with fish excrement will serve as fertilizer. The water tanks, as well as the cement, stones and the soil, are all thermal masses, or materials that absorb and release heat slowly. Having many thermal mass materials inside the dome will help the structure retain heat longer.
To help maintain an ideal temperature, a climate battery will be installed below the dome. When the dome gets too hot, the battery will pull air into the cool ground. When temperatures in the dome drop, stored hot air in the battery tubes will be released back into the structure.
“We hope to maintain a Mediterranean-like climate where it doesn’t freeze in there or freeze often,” Evans said. “We will have heaters in there for some of those days where it’s 30 below … but we expect to avoid running them.”
Evans and her colleagues won’t truly know what the climate in the dome will be like until it’s completed and they start planting.
Lead photo: A new geodesic dome on the Colorado Mountain College's Steamboat Springs campus is nearing completion.
John F. Russell
To reach Shelby Reardon, call 970-871-4253, email sreardon@SteamboatPilot.com or follow her on Twitter @ByShelbyReardon.
The Science of Sananbio - Research and Development
Led by a team of 38 scientists and another 100 R&D professionals, Sananbio is investing heavily in the science that is sustainable, local, and fresh indoor food and crop production. With deep expertise in photobiology, plant nutrition, and plant cultivation techniques, we are at the forefront of sustainable indoor agriculture.
RESEARCH AND DEVELOPMENT
Led by a team of 38 scientists and another 100 R&D professionals, Sananbio is investing heavily in the science that is sustainable, local, and fresh indoor food and crop production. With deep expertise in photobiology, plant nutrition, and plant cultivation techniques, we are at the forefront of sustainable indoor agriculture.
PHOTOBIOLOGY/SPECTRAL RESEARCH
Photobiology is an evolving area of science that studies the interactions of light on living organisms. One of Sananbio’s core focuses is the optimization of lighting spectrum’s that allow plants to thrive at all stages of growth. Through the latest’s developments in LED lighting technology in conjunction with years of scientific research, Sananbio is working to understand the synergy that exists between artificial light and plants. Our unique spectra has been trialed on a multitude of cultivars and our results have shown that by optimizing the spectrum based off of the cultivar we are able to increase nutritional value, drive unique genetic expression, increase active naturally occurring chemical compounds, and shorten flowering times.
PLANT NUTRITION
Sananbio’s team of elite plant scientist’s have worked tirelessly to develop proprietary nutrient blends that support a wide array of cultivars at different life stages of growth while growing in a controlled environment setting. With so much of our food today lacking proper nutritional value, our team is working to understand the most effective way grow nutritionally dense food sustainably in a indoor vertical farm. This cutting-edge science will lead to breakthroughs in the way we grow our food, how and when it is consumed, how it is transported to ensure maximum nutritional value.
VERTICAL FARM DESIGN and SUPPORT EQUIPMENT RESEARCH
With a team of scientists, senior designers, engineers, and product developers solely dedicated to understanding building the eco-systems that support thriving vertical farms, Sananbio is positioned at the fore-front of the science of vertical farming design and plant factory operations. We are focused on providing a holistic solution that allows us to partner with our clients from the ideation phase to the execution of their indoor vertical farm. Our research has given way to various patents in areas of plant growth illumination, hydroponic cultivation equipment, and accessories/equipment for industrial plant production. Great grow technology and equipment is just one aspect that must be taken in to account when venturing in to indoor vertical farming. Know before you grow.
THE TECHNOLOGY BEHIND SANANBIO
INNOVATION AT OUR CORE
RESEARCH AND DEVELOPMENT THAT IS DRIVING INNOVATION IN LED LIGHTING
Manufacturing Capacity
Sanan Opto-electronics, a sister company of Sananbio, is the world’s largest LED chip manufacturer accounting for 20% of the global chip production capacity. Sanan Group, our parent company, has built the infrastructure that allows Sananbio to capitalize upon cutting-edge technology development while providing the production capacity to support global market adoption of our technologies in the Ag-Tech space.
Vertical Integration
The vertical integration of the Sanan Group gives Sananbio a massive competitive advantage by allowing us to control our supply chain. This insight and perspective gives us unmatched flexibility in to our production capacity, global reach, and technological know-how. The diversity of industries we support gives us the versatility to respond to rapidly evolving markets as consumer demands shift.
Research and Development
A subset of the semiconductor industry, LED technology is incredibly research and development intensive sector and Sanan Opto is a global leader in this space. With 470 PhD’s and 502 engineers from all over the world, Sanan Opto possess the largest talent pool in the world dedicated to active research into LED technology.
The Technique Behind Watering Microgreens From The Bottom
When it comes to watering microgreens, there are various opinions saying it’s better to water from the bottom while others claim it’s best to water from the top
When it comes to watering microgreens, there are various opinions saying it’s better to water from the bottom while others claim it’s best to water from the top. When it comes to watering microgreens, the main goal is to avoid any chances of mold growth. In this article, we’re going to discuss watering microgreens from the bottom so that you can apply the technique to your own crops.
What Is The Point of Watering Microgreens From The Bottom?
Watering microgreens from the bottom is a technique adopted by farmers who sell microgreens to restaurants still in their seedling containers. This allows for microgreens to still grow upon and after delivery. When it comes to watering your microgreens from the bottom, remember to water your microgreens when the top of the soil feels dry. The size of your container can determine how many times a week you’ll need to water. For half-pint containers, you can expect to water your microgreens once a day, while full pint containers may need watering every other day.
How To Water Your Microgreens From The Bottom
Watering your microgreens from the bottom is a simple and easy process. We’ll break down the steps for you here:
Set Up A Pool of Water
It’s best to pour room-temperature filtered water into a bowl or a small tub until the water is half as deep as the microgreen container you have. Do not use cold water during this process since it can stunt the growth of the microgreens.
Put Your Microgreen Container In The Water
There should be holes at the bottom of your microgreen container, so when you place the container in the pool of water the soil will soak up the water. You should let the soil soak up the water for less than a minute or until the soil feels evenly moist. Once you can feel the moistened soil, remove the container from the water.
Empty Surplus Water
After removing the container from the water, you’ll want to place it somewhere where it can drain for a few minutes to remove any excess water. Remember tore fill water when needed especially if you’re working with more than four containers of microgreens. If you’re growing more than four types of microgreens, it’s best to use a large basin for this watering process since it will take less time rather than watering one container at a time.
Throw Out Leftover Water
At this point, you’ve successfully watered your microgreens from the bottom and you can toss out the pool of water. You may find leftover soil in this water, and if so, make sure you don’t allow it to go through the drain because it can cause clogging issues. Throw out the water outside or use a drain catcher to catch any soil remnants.
Watering microgreens from the bottom is another fantastic way to water and care for your plants. Our purpose at the Nick Greens Grow Team is to inform and educate our followers about the ease of growing your own food from home. Want to learn more about new and innovative farming methods? Subscribe to our blog and YouTube channel for weekly updates!
#growingmicrogreens #microgreens #microgreen #wateringmicrogreensfromthebottom #wateringmicrogreens
Automated Vertical Indoor Farming Set To Sprout
Vertical farming, which utilizes vertically-stacked layers of crops grown in climate-controlled facilities, utilizes significantly less water and soil than traditional agriculture
Vertical Farms Could Make Use of Abandoned Professional
Spaces As The Pandemic Grinds On
By Greg Nichols for Robotics
August 20, 2020
A Finish startup has been climbing the walls during the pandemic. At least the crops it helps grow in vertical gardens have been, including greens, berries, and vegetables in areas like the Middle East.
Vertical farming, which utilizes vertically-stacked layers of crops grown in climate-controlled facilities, utilizes significantly less water and soil than traditional agriculture. Increasingly we're seeing examples of the concept scaling to industrial-levels, which is good news with populations booming, arable land in ever-shorter supply, and waning interest in agriculture among city-bound youth.
iFarm has figured out a smart value proposition in the still-nascent market as a developer of vertical farm management technology, essentially an operating system that utilizes tremendous volumes of sensor data to fine tune automated crop growing. The company believes it's entering a market primed for steep growth.
"Investors can participate in the worldwide network of vertical farms and receive a rate of return well above bank deposit rates.", says Alex Lyskovsky, co-founder and President of iFarm. "We already have a group of financial partners involved in the development of our farms, and now there is a direct opportunity for this type of investment in Finland, UK, Switzerland, Netherlands, Russia and UAE."
One of the interesting advantages of vertical farming, particularly in a pandemic when so many professional spaces stand empty, is that it's possible to utilize the urban environment to facilitate crop growing. By growing crops closer to city dwellers, the company can offer logistics efficiencies and unparalleled freshness.
This at a time when traditional farming is less and less viable. Global agricultural productivity is suddenly slowing for the first time in decades. No one is quite sure why, but it's likely a systemic problem related to the rise of monocultures and the overuse of fertilizers, which add harmful salts to soils. Farmers are also aging globally as younger generations migrate to cities. That's largely because a productivity boom over the last century has kept food prices low, which makes farming unattractive economically. It's a double whammy now that that productivity can no longer be taken for granted without major rethinks to the food supply chain.
Vertical farming and other smart agriculture innovations may offer realistic alternatives, and they've captured imaginations due to novel use of space and cutting edge technologies. iFarm's Growtune tech platform allows growers to leverage technologies like computer vision, machine learning, and huge volumes of data. The system can enable farming operations to spread vertical farms across distributed networks while still maintaining centralized control. And if there's any doubt that farming has changed, the level of control is staggering. The Growtune platform can determine the plant's weight, as well as growth deviations or pathologies, and build a system that improves crop quality and characteristics on its own. According to iFarm, the optimization will reduce labor costs for crops like strawberries, cherry tomatoes, sweet peppers, radish, and others.
"The 2020 pandemic exposed the problems of the global food system – food supplies, sowing and harvesting were disrupted across the globe", says Mikhail Taver, Managing Partner at Gagarin Capital. "iFarm is taking a novel approach to agriculture, offering an automated solution to grow crops close to the consumer and ensure food security. We believe that the future of the food market lies in modern technologies and are excited to support the project on its way."