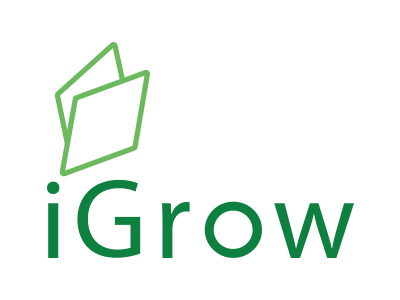
Welcome to iGrow News, Your Source for the World of Indoor Vertical Farming
LONDON: New Vertical Farm Offers Eco-Friendly Greens Picked And Delivered Within 24 Hours
London’s first delivery service for vertically-farmed, eco-friendly greens has launched from its base in the Docklands. Vertical farming is a fast-growing trend, with the global market size that was valued at $2.23 billion in 2018, projected to reach $12.77 billion by 2026
Lettuces growing vertically at Crate to Plate, a new farm in London's docklands | CRATE TO PLATE
London’s first delivery service for vertically-farmed, eco-friendly greens has launched from its base in the Docklands. Vertical farming is a fast-growing trend, with the global market size that was valued at $2.23 billion in 2018, projected to reach $12.77 billion by 2026. Crate to Plate is a clever new vertical farming venture founded by Sebastien Sainsbury who is a firm advocate of the concept of "15-minute cities" where everyone has access to fresh produce within a 15-minute walk of home. Crate to Plate offers consumers a wide range of super fresh organic lettuces, leafy greens and herbs, all picked within 24 hours, available by home delivery or at select greengrocers throughout London.
Recycled shipping containers house Crate to Plate, a vertical farm in London | ALISTAIR CARMAN
The eco-friendly farm is located in a parking lot owned by international property company Lendlease on the Isle of Dogs (Canary Wharf) inside three recycled shipping containers kitted out with LED lighting and an automated nutrient delivery system. Each 40-foot container achieves the same production as over an acre of farmland, with the site projecting to produce around six tonnes of greens each year. Not only does the urban farm use far less land but the pesticide-free produce is grown using hydroponic technology that uses 96% less water than traditional farming.
Crate to Plate, a new vertical farming initiative |. CRATE TO PLATE
Scientists and farmers at Crate to Plate carefully control the environment inside the shipping containers. Meticulously monitored vertical farming ensures that greens can be grown locally in urban environments, all year round, using minimal water, allowing produce to be delivered to consumers within 24 hours of harvest, with zero carbon footprint in transporting from farm to customer. As a result, the produce is as fresh as possible and has the highest possible nutrient value, completely free of pesticides and toxic chemicals. Lettuce, rocket, kale, pak choi, herbs, microgreens and more are harvested and delivered twice a week. The difference in taste between Crate to Plate’s greens and those you can buy from a supermarket is astonishing and delicious. And dynamite options like wasabi rocket and basil Genovese are already proving to be customer favorites.
Basil growing vertically at Crate to Plate | JOANNE SHURVELL
Produce from Crate to Plate is available in select greengrocers like Artichoke in North London and direct to consumers via their website. A £15 mixed box includes three types of lettuce, three bags of greens, and three herbs. Crate to Plate also sells to restaurants and have recently become Chef Ollie Dabbous's exclusive distributor of greens for his Michelin-starred Mayfair restaurant Hide. Crate to Plate has an ambitious UK expansion plan. A second site will open near Elephant and Castle this month, followed by other London sites and farms in other cities (Manchester, Birmingham, etc). And further ahead will be expansion to the United States.
Seedlings before they are transferred to the walls of the farm | CRATE TO PLATE
Crate to Plate’s new site in Elephant Park is part of a £2.5 billion regeneration project headed by the local council and Lendlease. One of the key aims of the development is to create a local, community-oriented ecosystem, with businesses from the area supplying residents and other retailers in the nearby community. Crate to Plate slots nicely into this concept, aiming to sell direct to local residents and to the new food businesses that are opening. Crate to Plate’s next London site is already in the works: the International Quarter London development near the 2012 Olympic Park in Stratford, east London.
With the global covid-19 pandemic fueling home deliveries and such a high-quality product on offer, it’s no surprise that Crate to Plate’s greens have sold-out every week since launching. Founder Sebastien Sainsbury says he wants “everyone to be able to get fresh leafy greens no more than a mile away from where they live.” It appears he’s off to a good start at achieving that goal and it will be fascinating to follow the progress of this sustainable new business.
Crate to Plate London home delivery boxes range from £6 to £28 depending on the selection and quantity, with no delivery charge on orders of £20 or more.
I've been writing on travel, food, fashion and culture for the past decade or so for a variety of publications. I co-founded PayneShurvell, a contemporary art gallery in London which is now an art consultancy in London and Suffolk. My photographer partner Paul Allen supplies photos for my features that often include a music or art event and our travels have taken us to under the radar music and art festivals in France, Italy, Portugal and Spain. I am the co-author of the Citysketch series of books that includes London, Paris and New York, published by Race Point and I'm the author of Fantastic Forgeries: Paint Like Van Gogh. Follow our adventures on Twitter at @jshurvell and on Instagram at @joshurvell and @andfotography
Kimbal Musk’s Quest To Start One Million Gardens
The tech veteran and restaurateur (and brother of Elon) has been preaching the ‘real food’ gospel for years — and his newest project may be his most ambitious yet
MARCH 20, 2021
The tech veteran and restaurateur (and brother of Elon) has been preaching the ‘real food’ gospel for years — and his newest project may be his most ambitious yet
By ALEX MORRIS
Million Gardens Movement
On the day he almost died, Kimbal Musk had food on the brain. The internet startup whiz, restaurateur, and younger brother of Tesla’s Elon had just arrived in Jackson Hole, Wyoming, from a 2010 TED conference where chef Jamie Oliver had spoken about the empowerment that could come from healthy eating. This was something Musk thought about a lot — food’s untapped potential, how he might be a disruptor in the culinary space — but beyond expanding his farm-to-table ethos along with his restaurant empire, Musk hadn’t yet cracked the code. Then he went sailing down a snowy slope on an inner tube going 35 miles an hour and flipped over, snapping his neck. The left side of his body was paralyzed. Doctors told the father of three that he was lucky: Surgery might bring movement back.
“I remember telling myself, ‘It’s all going to be fine,’ and then realizing that tears were streaming down the side of my face,” he says. “I was like, ‘Yeah, OK. I don’t really know what’s going on. I’m just going to, you know, let things go.’”
Musk, 48, eventually made a full recovery, but it involved spending two months on his back, which gave him plenty of time to think about the intersections of food, tech, and philanthropy. Since then, he has launched an initiative to put “learning gardens” in public schools across America (now at 632 schools and counting); courted Generation Z into the farming profession by converting shipping containers into high-tech, data-driven, year-round farms; spoken out vociferously against unethical farming practices and vociferously for the beauty and community of slow food; and this year, on the first day of spring, is kicking off a new campaign with Modern Farmer’s Frank Giustra to create one million at-home gardens in the coming year.
Aimed at reaching low-income families, the Million Gardens Movement was inspired by the pandemic, as both a desire to feel more connected to nature and food insecurity have been at the forefront of so many people’s lives. “We were getting a lot of inquiries about gardening from people that had never gardened before,” says Giustra. “People were looking to garden for a bunch of reasons: to supplement their budget, because there was a lot of financial hardship, to help grow food for other people, or just to cure the boredom that came with the lockdown. To keep people sane, literally keep people sane, they turned to gardening.”
The program offers free garden kits that can be grown indoors or outdoors and will be distributed through schools that Musk’s non-profit, Big Green, has already partnered with. It also offers free curriculum on how to get the garden growing and fresh seeds and materials for the changing growing seasons. “I grew up in the projects when I was young, in what we now call food deserts,” says EVE, one of the many celebrities who have teamed up with the organization to encourage people to pick up a free garden or to donate one. “What I love about this is that it’s not intimidating. Anyone can do this, no matter where you come from, no matter where you live. We are all able to grow something.”
Rolling Stone recently talked with Musk about the Million Gardens Movement, why shipping containers can grow the most perfect basil, and how he is channeling his family’s trademark disruptor drive to change America’s relationship with food.
How did you first get interested in food and then how did that grow into an interest in agricultural innovation?
I’ve always loved food. I started cooking for my family when I was 12, maybe even 11.
What was the first meal you made? Do you remember?
It’s actually funny. My mother is a wonderful person, great dietitian, but because she’s a dietitian, the food we ate was brown bread and yogurt or bean soup. I mean, as a kid, it drove me crazy. So I asked my mom, “If I could cook, could we get something else?” And so I went to the butcher, and I asked them, “How do you roast a chicken?” And he said, “Put it in a really hot oven for one hour.” And I was like, “Oh, how hot is hot?” He was like, “Make it as hot as your oven goes for one hour, and if it starts to burn, then just take it out.” And he gave me the chicken, and that was it. I’ve kept that recipe forever. 450, 500 degrees, one hour. That’s a great straight-up recipe.
And then my mother insisted on a vegetable, so I decided to do French fries, which was my funny way of convincing her that I’m doing a vegetable.
It is a vegetable.
I totally screwed up the French fries. I didn’t heat up the oil ahead of time, and if you don’t do that, the potatoes actually soak in the oil so you’re eating basically a sponge of oil. I made everyone throw up. But the roast chicken was delicious. Everyone loved that. And so I was encouraged to cook more. I cooked for my friends in university. I didn’t have any money, so I figured out how to cook for 40 cents a person. It was a Kraft dinner with weiner sausages. And if someone chipped in an extra dollar, I’d get actually real cheese instead of the powdered cheese.
Anyway, I studied business, and then went down to California to start a company with my brother building maps and door-to-door directions for the internet.
I read that you and your brother were sleeping in your office and showering at the YMCA and that sort of startup lifestyle made you appreciate food.
Yeah, that’s totally right. We only had enough money for rent for either an office or an apartment, so we rented an office. I had a little minibar fridge and put one of those portable cooktops above it, and that was our kitchen. But we also ate at Jack in the Box all the time because it was the only place that was open late. Ugh, 25 years later, I can still remember the items on that menu. It was just really, really not great — a huge inspiration to go focus on real food after that.
And I just did not like the lack of social connection. It’s a work-hard-go-to-sleep-and-work-hard-again culture with not much socializing in the way that I enjoy, which is eating food, eating together over a meal, talking about ideas. I kind of was suffocating a little bit.
It’s a Soylent culture.
Yeah, exactly. They actually want food to be a pill. So I kind of needed to leave. We ended up selling [our company] for a gazillion dollars when I was 27, and I had this sort of opportunity to do whatever I wanted. So I went to New York to enroll at the French Culinary Institute.
Was culinary school as brutal as people make it out to be?
Absolutely brutal. It was Full Metal Jacket, but cooking. They just totally break you down. They make sure you don’t have any faith in your own abilities — within a few months, you’re like, “I am a completely useless fool” — and then after that, they start building you up with the skills they want you to have. It was very, very hard on the ego. I managed to graduate, but I would say 70 percent of the people that start don’t finish — and you pay upfront.
I actually graduated just a few weeks before 9/11 and woke up to the sounds of the plane hitting the building. That’s how close we were. Fourteen days later, I started volunteering to feed the firefighters. We would do 16-hour days, every day — there was never a reason not to work because the alternative is you sit at home during the nightmare after 9/11, where no one was on the streets or anything. I started peeling potatoes and eventually got to the point where I would drive the food down to Ground Zero. The firefighters would come in completely gray in their face and gray in their eyes, covered in dust. And then they’d start eating, and you’d see the color come back in their face, the light in their eyes.
And you worked as a line cook after that?
Yeah, for Hugo Matheson, at his restaurant. He was the chef of a popular restaurant in Boulder, and I just wanted to learn. I was a line cook for $10 an hour for probably 18 months. And loved it. You know, it’s a submarine culture. And you get in there and everything you do in the moment is measured in the moment. It’s very much the opposite of [building] software.
You and Hugo eventually started a restaurant [The Kitchen] that practiced the farm-to-table thing before it was even really a term. Why was it so important to you to have local suppliers and organic methods? At that point, was it mainly about flavor, or was there a bigger ethic behind it?
For sure flavor was the driver. But I think that the thing that I resonated with more was the sense of this concept of community through food. You know, when I was feeding the firefighters, it was all about community. The fishermen would come and give us their fish, so we got the best fish you can imagine. The cooks were all volunteers. We were going through this really tough time. So for me, the community through food was what I loved about it.
[At The Kitchen], we literally had a basic rule to farmers saying we’ll buy whatever you grow. We said that if you can deliver by 4 p.m., then we will get it on the menu that evening.
Oh, wow.
We would get fiddlehead ferns at 4 p.m. and be trying to think, “OK, what can we do with this?” If you turn the food around that quickly, it really does show up in the flavor.
Food that had potentially been in the ground that morning.
Not potentially. Every day was working with the harvest of that day. We had 43 different farmers coming to the back door. It was awesome.
Let’s move ahead to the part of the story, after your accident, when you’re like, “All right, I’ve gotten this new lease on life and now what am I going to do with it?” Obviously, within the food space, there are a lot of choices you could have made. So how did you decide where to go from there?
So when I came out of that hospital, I resigned as CEO of my software company. I told my wife I wanted a divorce. The spiritual message I got was: Work with a way to connect kids to real food, to get kids to understand what real food is. And real food for me is food that you trust to nourish the body, trust to nourish the farmer, trust to nourish the planet. It’s very simple. Processed food would be the opposite of that. There’s no nourishment there. The farmer gets hosed and it’s terrible for the planet. So I [looked into] farm-oriented work and cooking-skills training. Turned out giving kids knives isn’t a good idea.
What? [laughter]
Yeah. Exactly. But the thing that came back to me was the value of a school garden. I actually was pretty frustrated with school gardens. I had been a philanthropic supporter of them for a few years and found them to be expensive, hard to maintain — a passionate parent would put it in, and then their kid would graduate, and it would become this mess in the corner of the schoolyard. So we [created] learning gardens. They’ve got a beautiful Fibonacci sequence layout. They’re made in a factory, but they have a natural look and feel. These are totally food-safe and can go on any school ground. They’re [wheelchair] accessible, easy to teach in, and built into the irrigation system of the school. We go in and we do 100 of them at a time. Pre-COVID we got to almost 700 schools in Denver, Chicago, Detroit, Pittsburgh, Indianapolis, Memphis, L.A.
How did you decide which cities to go into?
I believe this is useful anywhere, but what I found was low-income communities were the areas where you really needed it. Private schools or wealthier schools, they all have gardens — there’s not a private school out there that doesn’t embrace having a school garden. It’s actually the low-income schools that don’t have it. And that is also, coincidentally or not, where the obesity is. And so what I wanted to do is take what existed in private schools and put it into low-income schools and to do it in a way where it would be the most beautiful thing in the school. So instead of that sort of eyesore that was in the backyard, we said, “These have to be right next to the classroom, right next to the playground. You’re not allowed to build a fence around it. And if you don’t want to do that, great, we’ll just find another school. But these are the rules for learning garden.” And because we were doing 100 at a time, the districts would work with us, including maintenance and installation and curriculum and teacher training. Pre-COVID we were teaching almost 350,000 kids every school day.
And are there measurable effects?
Absolutely. Studies show that fifth grade in particular is the most effective grade. If you teach science in fifth grade to a kid, the exact same lesson in the garden versus in the classroom, you will get a 15-point increase on a 100-point score on their test scores.
And then if you teach kids 90 minutes a week in school, which is not hard to do because it’s beautiful and fun to be outside, you’ll double their intake of fruits and vegetables. Now they’re not eating a lot of fruits and vegetables, so the base is low, but you’re still doubling. The way I like to look at it is you’re really not trying to make them eat vegetables all the time — that’s too hard — you just try to change the course of their life by a few degrees; if you can do it by third, fourth, fifth grade, they’re going to be a different adult when they grow up. We’re not here to claim that what we do changes everything. We believe that the cafeteria needs to improve, that we need grocery stores to exist in these food deserts. There are many legs of the stool, but the school garden movement is a critical leg.
Are there any other technological innovations in this space that are really giving you hope?
I think there’s a lot of cool things going on around carbon capture with regenerative farming, because if you do farming correctly, you’ve become a wonderful carbon sink. And there needs to be an economy around it. So what is the value of a carbon credit? They’ve got value for that in Europe, but they haven’t valued it in America. So I think there’s a lot of government policy that needs to work there. But it’s a fascinating area to look at.
It’s interesting, the concept of bringing innovation to agriculture, which is—
So old school! Yeah, it’s fun. I do get frustrated that it doesn’t move fast enough. Then I’m reminded of how big this is and I’ve got my whole life to work on it. So I’m learning to embrace going a little slower. If you are in the software world, it’s more “move fast and break things,” and I think with food, it’s something in between.
Yeah, you don’t want to break the food chain.
No, people need to eat. Exactly.
And I know you’ve been advocating, too, for policies that help farmers shift to organic methods.
Yeah, I’ve been a supporter of that, but I really have pushed my energy now to work with young farmers of any kind. I’m not against organic at all. I love organic. But I’ve kind of said, “You know, we just need young farmers.” Real food doesn’t require it to be organic. If it’s a zucchini that happens to be grown conventionally, I’m still in favor of that.
It’s still a zucchini.
Right. That being said, organic is better. Farmers make more money on it. But it’s really about young farmers getting them into the business.
If you don’t mind, let me take one minute to just talk about [another initiative called] Square Roots. So there was a sort of a turning point in indoor farming technology around 2014, where you could really do quality food. Indoor farming’s been around forever, but the quality was really terrible. It would taste like water. No real flavor. But the technology of lighting really changed in 2014, and so by 2016 we said, “You know, there is a way here.” And what got me going was I really wanted to create this generation of young farmers. I love technology and I love food. And I think that if we bring the two together, we will get young people interested in farming again. And so we started out Square Roots as really a training entity.
And with Square Roots, you’re growing food in shipping containers? There’s no soil?
Yeah, we refine the nutrients [through the water]. We’ve gotten very, very thoughtful about what the nutrients are so that we can re-create as best we can the soil that they would get normally. The shipping containers, what’s beautiful about them is the fact that we can totally control the climate. For example, we have found that Genoa in Italy is where the best basil in the world is grown. It’s four weeks in June that are the best, and actually, 1997 was the best June. And so we re-create the climate of 1997 Genoa, Italy, in each of those containers to create the tastiest basil you can possibly imagine. Using data, we can monitor the growth and how they work. And every square meter of the air in there is exactly the same. That’s why containers are so valuable. Plants factories have to grow basil or cilantro or whatever all in the same climate. We get to grow arugula, basil, parsley, cilantro or whatever each in their own climate. For example, we’ve discovered that mint grows best in the Yucatan Peninsula — superhuman, grows like a weed, delicious. And we re-create that climate.
Square Roots Basil Farm in Brooklyn.
Square Roots
And the shipping containers, the idea for that was, “Let’s use things that we can recycle”?
Well, they are recycled. But no, it wasn’t that. It was actually climate control. They’re actually like refrigerators. We can drop that temperature in there to 40 degrees Fahrenheit for a particular growth cycle. If we have any pests, we don’t use pesticides, we have something called Mojave mode where we turn it into the Mojave Desert for four days. We bring the temperature up to 120 degrees, drop the humidity down to four percent and nothing can survive. That’s how we remove pests. No one else can do that unless you use these kind of containers. So it’s really a technology solution.
You’ve referred to food as being the new Internet. Do you still feel that way?
Oh, my god. Absolutely. It’s showing itself. Food is different to social media and so forth. It takes a long time to build up supply chains, get consistent growing. It’s not as fast-moving, but it is a much bigger business. Software is a $400 billion business. Food is an $18 trillion business. So the opportunity is much, much bigger in food than it is in software.
What are the top two or three things that really bother you about the industrial food system right now?
The processing of food. For some reason back in the ’70s, America just started to idolize processed food. And so what you have is a high-calorie hamburger, for example, that is nutritionally irrelevant. In other words, people were just not thinking about nutrition. And they used laboratories to adjust the flavor, chemicals to adjust the flavor, artificial ingredients. The result was a very high-calorie, highly processed kind of a Frankenstein burger that did please the pallet, but it made you feel awful afterwards.
The other one that is absolutely ludicrous is ethanol. Forty percent of our corn fields are growing ethanol. That’s 25 million acres of land that could be used to grow real food. People keep feeding us bullshit that we need to try and feed the world. We have so much food that we are turning 40 percent of it into ethanol. It takes a gallon of oil to make a gallon of ethanol. So it’s just a total boondoggle for the corn farmers and it’s terrible for the environment. In fact, it’s hilarious: It’s the only thing that both the oil industry and the environmentalists hate. Can you imagine there’s something that those two can agree on? And it’s ethanol.
Why the hell are we doing it?
It’s a subsidy for farmers. We do it because old people vote, and they control the farms, and they would all be devastated right now if the true demand of corn is what they had to deal with. And until a politician has the courage to make those hard decisions, we’re going to be stuck growing ethanol. Now, the good thing is we are all switching to electric cars, so ethanol is going to go away anyway. But for a while, the next five to 10 years, ethanol is going to be a part of what we do.
Let’s talk about the Million Gardens Movement. How did you get the idea that you wanted to do it?
Frank [Giustra] and his team pitched us on joining forces and doing the Million Gardens Movement. And we loved it. We thought it was a great idea. Because of Covid, we had been forced to pivot our model from the learning gardens because we couldn’t really teach people in the gardens anymore. And so we had done this trial of what we call little green gardens, which are round, beautiful sort of beige sacks, and you can come in and pick these up from a local school in your community. You can grow them on a windowsill as long as there’s some light. You can grow them indoors, which enables any city to be able to use them.
Say you get to a million gardens, are there any projections on what the environmental impact of that might be?
What we would be doing with these little green gardens is inspiring people to garden and empowering them to garden. The average garden generates about $600 to $700 worth of food a year. So it provides actual food to your family. You’re having a lower carbon footprint because you’re not shipping food around. It’s great for mental health. Think about Covid and how crazy we all are. This gets you out there. It connects you to your kids. Gardening is such a beautiful thing to do for yourself, for the community, for the environment.
It’s easy to think about what has been lost during this time, but I do like this idea of using COVID as an opportunity for change.
It’s obviously one of the worst things we’ve gone through as a society, but if we do this correctly, if we take this opportunity well, it could be one of the best things that’s happened to society — in a few years, we’ll look back and say, “OK, this was a good way to restart and focus more on climate change, focus more on gardening with your family, being connected to each other.” I think it has a lot of potential, as long as we take that potential and we leverage it. So the Million Gardens Movement is a part of that.
VIDEO: Farming In A Shipping Container
Transforming Unused Spaces Into Vertical Farms
Transforming Unused Spaces Into Vertical Farms
Indoor Agtech: An Evolving Landscape of 1,300+ Startups
Our Indoor AgTech Landscape 2021 provides a snapshot of the technology and innovation ecosystem of the indoor food production value chain
March 17, 2021
Editor’s note: Chris Taylor is a senior consultant on The Mixing Bowl team and has spent more than 20 years on global IT strategy and development innovation in manufacturing, design, and healthcare, focussing most recently on indoor agtech.
Michael Rose is a partner at The Mixing Bowl and Better Food Ventures where he brings more than 25 years immersed in new venture creation and innovation as an operating executive and investor across the internet, mobile, restaurant, food tech and agtech sectors.
The Mixing Bowl released its first Indoor AgTech Landscape in September 2019. This is their first update, which you can download here, and their accompanying commentary.
Since the initial release of our Indoor AgTech Landscape in 2019, the compelling benefits of growing food in a controlled indoor environment have continued to garner tremendous attention and investment.
One of the intriguing aspects of indoor agriculture is that it is a microcosm of our food system. Whether within a greenhouse or a sunless (vertical farm) environment, this method of farming spans production to consumption, with many indoor operators marketing their produce to consumers as branded products. As we explore below, the indoor ag value chain reflects a number of the challenges and opportunities confronting our entire food system today: supply chain, safety, sustainability, and labor. Of course, the Covid-19 pandemic rippled through and impacted each aspect of that system, at times magnifying the challenges, and at others, accelerating change and growth.
Invest with Impact. Click here.
Our Indoor AgTech Landscape 2021 provides a snapshot of the technology and innovation ecosystem of the indoor food production value chain. The landscape spans component technology companies and providers of complete growing systems to actual tech-forward indoor farm operators. As before, the landscape is not meant to be exhaustive. While we track more than 1,300 companies in the sector, this landscape represents a subset and serves to highlight innovative players utilizing digital and information technology to enhance and optimize indoor food production at scale.
Supply chain & safety: Where does my food come from?
The pandemic highlighted the shortcomings of the existing supply chain and heightened consumer desires to know where their food comes from, how safely it was processed and packaged, and how far it has travelled to reach them. A key aspect of indoor farming is its built-in potential to respond to these and other challenges of the current food system.
Indoor farmers can locate their operations near distribution centers and consumers, reduce food miles and touch points, potentially deliver consistently fresher produce and reduce food waste, and claim the coveted “local” distinction. The decentralized system can also add resiliency to supply chains overly dependent on exclusive sources and imports.
Growing local has many forms. Greenhouse growers tend to locate their farms outside the metropolitan area while sunless growers may operate in urban centers, such as Sustenir Agriculture in Singapore and Growing Underground in London. Growers like Square Roots co-locate their indoor farms with their partner’s regional distribution centers, and Babylon deploys its micro-farms solution on site at healthcare and senior living facilities and universities. Recently, Infarm announced it was expanding beyond its growing-in-a-grocery store model, to include decentralized deployments of high-capacity “Growing Centers” across a number of cities. Additionally, the value of “growing local” might take on a much larger meaning if your country imports most of its produce from other countries; a number of the Gulf region countries have announced major indoor growing initiatives and projects with AeroFarms, Pure Harvest, and &ever to address the region’s food dependence on other countries.
Organic produce sales jumped to double digit growth in 2020 as consumers are increasingly mindful of the healthiness of their food. The additional safety concerns due to the pandemic only accelerated this trend. While not typically organic, crops produced in the protection of indoor farms are isolated from external sources of contamination and are often grown with few or no pesticides. Human touch points are reduced as supply chains shorten and production facilities become highly automated. Through the CEA Food Safety Coalition, the industry has recently taken steps to establish production standards with a goal to keep consumers safe from foodborne illness.
Indoor farmers market their products as local, fresh, consistent and clean. This story is resonating with consumers as the growers seem to be selling everything they can produce, with many reporting significant sales growth in 2020. The direct connection to consumer concerns is also a key part of their ability to sell their branded products at a premium, which has been critical to financial viability for some growers. This connection can also enable them to collapse the supply chain further, at least at smaller scales, through direct sales and creative business models, e.g., sunless grower Willo allows subscribers to have their own “personal vertical farm plot” and watch their plants grow online.
Sustainability: Is my food part of the problem or part of the solution?
Farming, as with most industries, has been under increasing pressure to operate more sustainably, and indoor growers, with their efficient use of resources, have rightfully incorporated sustainability prominently into their narratives.
We are well aware of the impacts of climate change, including greater variability in weather patterns and growing seasons. The UN’s Food and Agriculture Organization projects that over the coming decades climate change will cause a decrease in global crop production through traditional farming practices, causing greater food insecurity. Indoor growing, which provides protection from the elements, consistent high yields per land area, and the ability to produce food year-round in diverse locations, including those unsuitable for traditional agriculture, can help mitigate this trend.
Water scarcity is projected to increase globally, presenting a national security issue and serious quality of life concerns. According to the World Bank, 70% of the global freshwater is used for agriculture. Indoor agriculture’s efficient use of water decreases use by more than 90% for the current crops under production. It is also common practice for greenhouses to capture rainwater and reuse drainage as does Agro Care, the Netherlands’ largest greenhouse tomato grower.
On the flip side, energy use, particularly in sunless facilities, is indoor growing’s sustainability challenge. Efficiency will continue to improve, but as recent analysis on indoor soilless farming from The Markets Institute at WWF indicated, there is an industry-wide opportunity to integrate alternative energy sources. Growers recognize this opportunity to decrease impact and improve bottom-line and are already utilizing alternative approaches such as cogeneration, geothermal sources, and waste heat networks. H2Orto tomatoes are grown in greenhouses heated with biogas generated hot water. Gotham Greens’ produce is grown in 100% renewable electricity-powered greenhouses, and Denmark’s Nordic Harvest will be running Europe’s largest indoor farm solely on wind power.
Labor: We’re still hiring!
There are labor challenges and opportunities throughout the food system value chain, and this couldn’t be more acute than on the farm. Farm operators—both in-field and indoor—find it difficult to attract labor for the physically demanding work. Even before the pandemic, the hardening of borders in Europe and the US created a shortage of farmworkers for both field and greenhouse production. In addition, grower and farm manager-level expertise is in short supply, exacerbated by an aging workforce and the rapid addition of new indoor facilities. While operators would like to see more trained candidates coming from university programs, they are also looking to technology and automation to relieve their labor challenges.
Automation of seedling production and post-harvest activities is already well established for most crops in indoor farming. In addition, the short growth cycle and contained habit of leafy greens lends them to mechanization. For example, the fully automated seed-through-harvest leafy green systems from Green Automation and Viscon have been deployed in major greenhouse operations like Pure Green Farms and Mucci. On the sunless side, Urban Crop Solutions has uniquely implemented automation in shipping containers, and Finland’s NetLed has developed a fully automated complete growing system. Note that many of the larger-scale sunless growers have developed their own technology stacks and have designed labor-saving automation into their systems. For example, Fifth Season has robotics deployed throughout the entire production process.
Despite numerous initiatives, the challenging daily crop care tasks and harvesting for certain crops (tomatoes, peppers, cucumbers, and berries) have not yet been automated at scale. However, planned, near-term commercial deployments of de-leafing and harvesting robots offer the promise of significantly altering labor challenges. Software technologies, like those from Nitea and Hortikey address labor management, crop registration, yield prediction, and workflow/process management for the indoor sector and strive to improve operational efficiencies for a smaller workforce.
Technologies that provide, monitor, and control climate, light, water, and nutrients are already deployed in today’s sophisticated indoor growing facilities and are fundamental to maintaining optimal conditions in these complex environments. They also form the base for the next innovation layer, i.e., crop optimization and even autonomous control of the growing environment based on imaging and sensor platforms (like from Ecoation, iUNU, and 30MHz), data analysis, machine learning, digital twins and artificial intelligence. Recent events like the Autonomous Greenhouse Challenge have successfully explored the potential of AI to “drive horticultural productivity while reducing resource use and management complexity”. Emerging commercialized autonomous growing innovations, such as the Blue Radix Crop Controller and Priva’s Plantonomy, promise to extend and enhance the reach of available grower expertise, particularly in large and multi-site operations.
Where do we go from here?
Since we created our initial Indoor AgTech Landscape, there has been positive change and reason to be optimistic about the future. But, as with any evolving market and sector of innovation, it can be a bumpy ride. Some believe CEA is not the answer to our food problems because not everything can be economically grown indoors today. We see indoor ag as just one of the approaches that can help fix our food system and it should be applied when it makes sense. For example, tomatoes sold through retail are already more than likely grown in a greenhouse. Expect more crops to be grown indoors more economically with further advancements.
One aspect of our previous landscape was to increase awareness that, despite the fervor surrounding novel sunless farming, greenhouse growing was already well-established. Dutch greenhouse growers have demonstrated the viability of indoor growing with 50-plus years of experience and more acres “under glass than the size of Manhattan.” The recent public offering and $3 billion market cap of Kentucky-based greenhouse grower AppHarvest also clearly raised awareness! Other high-profile and expanding greenhouse growers, including BrightFarms and Gotham Greens, have also attracted large investments.
The question is often asked, “which is the better growing approach, sunless or greenhouse?”. There is no proverbial “silver bullet” for indoor farming. The answer is dictated by location and the problem you are trying to solve. A solution for the urban centers of Singapore, Hong Kong and Mumbai might not be the same as one deployed on the outskirts of Chicago.
Regardless of approach, starting any type of sizable tech-enabled indoor farm is capital intensive. A recent analysis from Agritecture indicates that it can range from $5 to $11 million dollars to build out a three-acre automated farm. Some of the huge, advanced greenhouse projects being built today can exceed $100 million. Given the capital requirements for these indoor farms, some question the opportunity for venture-level returns in the sector and suggest that it is better suited to investors in real assets. Still, more than $600 million was raised by the top 10 financings in 2020 as existing players vie for leadership and expand to underserved locales while a seemingly endless stream of new companies continue to enter the market.
Looking forward, indoor farming needs to address its energy and labor challenges. In particular, the sunless approach has work to do to bring its operating costs in line and achieve widespread profitability. Additionally, to further accelerate growth and the adoption of new technologies in both greenhouse and sunless environments, the sector needs to implement the sharing of data between systems. Waybeyond is one of the companies promoting open systems and APIs to achieve this goal.
As we stated in the beginning of this piece, the indoor ag value chain reflects some of the challenges and opportunities confronting our entire food system today: supply chain, safety, sustainability, and labor. Indoor agriculture has tremendous opportunity. While it is still early for this market sector overall, it can bring more precision and agility to where and how food is grown and distributed.
Polygreens Podcast Episode: 17 - Nicola Kerslake - Contain Inc.
Nicola Kerslake founded Contain Inc, a fintech platform for indoor agriculture, that aids indoor farmers in finding lease funding for their projects
Nicola Kerslake founded Contain Inc, a fintech platform for indoor agriculture, that aids indoor farmers in finding lease funding for their projects. They're backed by Techstars' Farm to Fork program, funded by Cargill and Ecolab.
Latest Episode
GrowGroup IFS Introduces Their Own Grow Container Systems GCS 40HQ
The GCS 40HQ is available in different models. All models are in a 40ft container and includes LED technology, climate computers with remote control, and extensive control on water, temperature, humidity, CO2, and lighting
March 12, 2021
GrowGroup IFS Introduces Their Own Grow Container Systems GCS 40HQ
GrowGroup IFS introduces the GrowGroup Grow Container Systems “GCS 40HQ” for small container cluster farms, research & development, schools & universities, and pilots for new indoor farms. With this new solution now GrowGroup IFS can support also small farms in an accessible way with their unique and full approach including support with the operation through their partners GaaS Wageningen and Hoogendoorn Growth Management.
Grow Container Systems “GCS 40HQ”
The GCS 40HQ is available in different models. All models are in a 40ft container and includes LED technology, climate computers with remote control, and extensive control on water, temperature, humidity, CO2, and lighting. The basic model has a very low entry-level and is upgradeable on different levels. The client can choose for example for an upgrade to the highest quality of climate computers of partner Hoogendoorn Growth Management or the highest quality of LED technology of Signify. The client can even choose for the support with the operation through partner GaaS Wageningen.
“We support the bigger farmers with our unique and full approach on indoor farming for some time already but noticed also that smaller farmers, in particular, have a great need for this. That’s why we launch our own GCS solution right now, so all farmers can use the newest technology of indoor farming for year-round cultivation all over the world”, John Breedveld, CEO GrowGroup IFS.
GaaS Wageningen
Partner GaaS Wageningen from the Netherlands has access to a pool of more than 200 agricultural specialists. Its core business is supporting the operation of high-tech indoor farms from the small ones as the container farms up to the large ones as the big indoor factories. They have high knowledge of indoor farming and sharing their knowledge with the farmers by supporting and training them but also with schools and universities.
GrowGroup IFS
GrowGroup IFS (Innovative Farming Solutions), founded by CEO John Breedveld in Barendrecht in the Netherlands, is specialized in developing indoor farming based on the most advanced Dutch innovative farming solutions, especially in regions where normal cultivation is restricted by extreme climate and or limited space.
USA - NEW YORK STATE - Ellicottville Greens’ Investors Discuss Why They Backed The Company
Ellicottville Greens crossed a major hurdle facing many growth-oriented startups recently when it pulled in a $1 million round of Series A funding from local angel investors
By Dan Miner – Reporter, Buffalo Business First
March 10, 2021
Andrea Vossler, partner at Lippes Mathias Wexler Friedman LLP | JOED VIERA
Ellicottville Greens crossed a major hurdle facing many growth-oriented startups recently when it pulled in a $1 million round of Series A funding from local angel investors.
How did co-founders Gabe Bialkowski and Sal LaTorre convince angels to move cash into their bank account in exchange for an ownership percentage of the business?
The answer lies somewhere at the intersection of familiarity, talent, and foresight, according to Scott Friedman, chairman of Lippes Mathias Wexler Friedman law firm, and Andrea Vossler, a partner at that firm.
The duo, who invest through Varia Ventures, were the lead funders in Ellicottville Greens’ round.
Bialkowski is a computer science graduate from the Rochester Institute of Technology who has been in and out of several startups in the last decade, including a startup in Los Angeles that successfully raised seed capital.
“We worked with Gabe in the past and we find him to be bright, entrepreneurial, and collaborative,” Friedman said. “To build a great company requires real teamwork and Gabe is open to building a great team.”
Scott Friedman, chairman of Lippes Mathias Wexler Friedman LLP | JOED VIERA
The “bet the jockeys” mantra is a common beat among angel investors, who know that even the best ideas will face challenges requiring human ingenuity to overcome.
The model itself was also at the right place for an angel investment round, Vossler said. Ellicottville Greens builds organic vertical farms in shipping containers – making them cost-effective and mobile. It already has four such units in operation, allowing the team to show real-world evidence of its theoretical premise.
The company positions itself at the cutting-edge of a hot consumer trend, which is the ability to offer fresh and locally sourced produce. Its mobile units can be placed directly on a customers’ premises – an idea with major potential in the grocery space.
Ellicottville Greens' Container Farms | ELLICOTTVILLE GREENS
And finally, it uses technology to support production and operations and uses established e-commerce channels such as Produce Peddlers and Off the Muck.
“It’s an ag-tech startup in a massive market that’s continuing to grow,” Vossler said. “Gabe is taking a fairly straightforward business model and wrapping it with technology, utilizing the shipping containers to push down costs and creating significant efficiencies around the delivery of the product.”
Ellicottville Greens completed a $250,000 seed round of funding last year from Launch NY and other local angels. Bialkowski aired his company’s progress at a Jan. 27 web presentation in front of the Western New York Venture Association.
He surpassed many of his own growth and financial milestones for the year in the first quarter.
The mix of attractive leadership, market, and rapid growth was how Ellicottville Greens crossed the finish line on its Series A round. The idea, of course, is that the real race has just begun.
“As he continues to build his team and get traction, we don’t think there is any limit to the potential for this company,” Friedman said.
IN THIS ARTICLE Andrea Vossler Person Banking & Financial
NIGERIA: Fresh Direct Makes Landless Farming Possible And Appealing For City Dwellers
With about 200 million people to feed, Nigeria is battling with food security and is yet unable to produce all the food it needs
March 9, 2021
With about 200 million people to feed, Nigeria is battling with food security and is yet unable to produce all the food it needs. Coupled with that, farmers still lose a significant percentage of produce from post-harvest losses because of poor roads, lack of storage systems among others.
Most farms are located in rural areas because that is where the land is. The markets, however, are in the urban areas, and in taking the food from where it is harvested to where it is needed, a lot of damages happen to the produce. Studies carried out on post-harvest losses in some Nigerian communities show that as much as 20 – 30% of total grain production, 30 – 50% of root and tuber and a usually high percentage of fruits and vegetables are lost after harvest.
Nigeria produces about 1.5 million tons of tomatoes a year, but over 900,000 tons is lost to rot.
What if farms were located closer to the urban markets and farmers could cut down post-harvest losses by selling to the farm as soon as the produce is ready?
Agritech startup, Fresh Direct, is making this possible through its combination of hydroponics and vertical farming. The company was founded by Angel Adelaja in 2014.
Fresh Direct’s different approach to agriculture
Hydroponics is a soilless technique used to grow crops in nutrient solutions instead of in the soil. Fresh Direct grows different crops in vertical stackable containers and develops its own hydroponic system using technology and locally-sourced materials. This includes the use of metres and sensors to monitor the conditions of the plants in the stacked farm.
Farming with hydroponics
The container farms allow people in urban areas as well as people who have never farmed before to grow agricultural produce directly in places that are closer to the market. By using stackable shipping containers, the volume of crops that can be cultivated on a piece of land is increased exponentially. This allows the farmer to get as much as 10 times more yield using only 7 percent of the land that would be required if traditional farming methods are used.
“It has a lower barrier of entry because you do not need to go find land to start. You do not need a green house. You can start in your kitchen, closet, balcony or backyard.”
Angel Adelaja
Since the planting does not require soil, this system of farming is more appealing to youths because the back-breaking work that characterizes agriculture is absent. However, what this mode of farming removes in stress, it adds in creative thinking.
Suggested Read: From Farmcrowdy to Releaf, Here are the 5 Most Outstanding Agritech Startups of 2020
According to Adelaja, “What you avoid in back-breaking work you face in advanced thinking. It’s a higher level of thinking needed to calculate nutrients needed or design a system”.
The startup does not provide educational materials for city farmers, instead, it organizes periodic training to help farmers and intending-farmers get their footing.
Source: FoundersAfrica
Fresh Direct is gaining traction by involving more youths
Fresh Direct plans to get 10,000 youths interested in its Agritech model of farming. Already, the startup has urban farms in Abuja as well as mini-campuses in Osun State.
Also Read: Kenyan Insurtech Pula Closes $6M Series A to Boost Profits for Small-scale Farmers Across Africa
It teaches people who want to learn about urban farming as well as set up their own vertical farming containers. These teachings are provided in the form of periodic training that are organized by the startup. A training costs between N10,000 and N30,000 depending on how extensive the trainees want to go in urban farming.
After the training, Fresh Direct helps the trainees to get financing for the container farm with a collateral-free micro-loan that is obtained from banks. The problem of access to the market is also removed through the startup’s network of ready off-takers. After the produce is harvested, the city farmer can sell directly to Fresh Direct’s market.
Fresh Direct has raised N3 million in a pre-seed round
Since it started in 2014, Fresh Direct has raised funds from one disclosed round. It raised N1 million naira from Chivas Venture in 2016 in a pre-seed round. It raised an additional N2 million from She Leads Africa.
While players like Farmcrowdy are helping to make funds available for farmers in the country, more lucrative ways of farming like the vertical method and hydroponics can help farmers maximize their production and get more urban dwellers into the agriculture sector.
US: NEW YORK - Well-Known Investors Water Ellicottville Greens With $1M In Growth Funding
The Series A round of funding will support construction of mobile vertical farming facilities, built inside reused shipping containers, along with the acquisition of Vertical Fresh Farms, an established indoor farming operation in Buffalo.
By Dan Miner
Reporter, Buffalo Business First
March 8, 2021
Ellicottville Greens continues to push forward on its ambition with $1 million in new funding, led by well-known local investors.
The Series A round of funding will support construction of mobile vertical farming facilities, built inside reused shipping containers, along with the acquisition of Vertical Fresh Farms, an established indoor farming operation in Buffalo.
It is a natural progression for the company, which was founded in 2018 by Sal LaTorre and Gabe Bialkowski and seeks to take advantage of the national consumer drift toward locally grown, organic produce.
“We decided to go after a new round of funding because we have a lot more demand coming in than we have capacity to grow right now,” Bialkowski said. “We are focusing on growing the product and sales and that will help define everything else.”
The round was led by Scott Friedman, chairman of Lippes Mathias Wexler Friedman law firm, and Andrea Vossler, a partner at that firm. The duo run Varia Ventures, an investment vehicle and management consultancy aimed at startups in Buffalo. A group of angel investors based in Buffalo participated as well.
Ellicottville Greens raised $250,000 in seed funding last year from Launch NY and other local investors.
Ellicottville Greens has thus far established four shipping containers: three at its Ellicottville home base and one on the Eastern Hills Mall property in Clarence. It sells its products to homes and restaurants through web-based marketplaces that include Produce Peddlers and Off the Muck.
Produce Peddlers is itself a local startup founded by Gary and Gina Wieczorek.
In the long-term, Bialkowski says Ellicottville Greens has a repeatable business model that could be attractive to supermarkets since the company could set up shop nearby and deliver produce at the peak of possible freshness.
He said the firm is set up at the intersection of nationwide consumer shifts in how people consume food.
“People want to buy healthy local products,” Bialkowski says. “They’re getting more health-conscious and they want to know where their food comes from.”
Ellicottville Greens is the third local startup to announce a growth-oriented round of private funding this year. The others include Torch Labs ($25 million) and Circuit Clinical ($7.5 million).
Lead photo: Ellicottville Greens' storage containers
IN THIS ARTICLE
Advanced Container Technologies, Inc. Joins Clean Food Initiative
Through the use of the company’s GrowPods, ACTX can provide farmers, community groups, investors, and non-profit agencies with a turnkey system to grow ultra-clean and nutritious food that can not only benefit the ecology of the planet and bolster community food security but can also provide new jobs and economic opportunities
March 03, 2021 | Source: Advanced Container Technologies Inc.
Company joins movement toward sustainable alternatives to traditional food production.
CORONA, Calif., March 03, 2021 (GLOBE NEWSWIRE) -- Advanced Container Technologies, Inc. (Ticker: OTC:ACTX) stated it is joining the Clean Food Initiative and intends to become a leading force in the drive toward sustainable agriculture.
The Clean Food Initiative is focused on bringing clean, fresh, healthy food to children throughout the world, that is free from pesticides, herbicides, or harmful chemicals. Along with the practice of implementing Sustainable Agriculture Systems (SAS), the aim is to develop a global food system that uses half the water and half the soil as it does today – yet produces twice as much food.
Through the use of the company’s GrowPods, ACTX can provide farmers, community groups, investors, and non-profit agencies with a turnkey system to grow ultra-clean and nutritious food that can not only benefit the ecology of the planet and bolster community food security but can also provide new jobs and economic opportunities.
GrowPods are automated indoor micro-farms that can provide a sustainable supply of affordable safe, clean, nutritious food, while also providing jobs at a local level by promoting the growth of a skilled agricultural workforce in non-traditional settings.
Doug Heldoorn, CEO of Advanced Container Technologies, Inc., said the company’s objectives are to make agriculture sustainable, investable, manageable, scalable, and transparent.
“There is a substantial difference between meeting basic food requirements and meeting optimum nutrition requirements,” he said. “People need access to high quality foods that are rich in nutritional value. Future generations deserve access to a healthy and sustainable food supply, not a diet filled with preservatives, pesticides or chemicals.”
SAS and the Clean Food Initiative represents one of the greatest challenges of the 21st century, as well as a tangible investment opportunity with sound business growth prospects and consistent annual income generation.
“There are few problems facing mankind that are as massive as our need to change our methods of food production and distribution,” Mr. Heldoorn stated. “Fortunately, there are innovative solutions to these challenges, and we are extremely proud to be a vital participant in this agricultural and social evolution.”
For more information, call (951) 381-2555 or visit: www.advancedcontainertechnologies.com.
About Advanced Container Technologies, Inc.
Advanced Container Technologies, Inc. is in the businesses of selling and distributing hydroponic containers called GrowPods; and designing, branding, and selling proprietary medical-grade containers that can store pharmaceuticals, herbs, teas, and other solids or liquids, and can grind and shred herbs; as well as selling other products and accessories, such as humidity control inserts, odor-proof bags, lighters, and plastic lighter holders; and provides private labeling and branding for purchasers of the Company’s containers and the other products. For more information visit: www.advancedcontainertechnologies.com.
Forward-Looking Statements
This release includes predictions or information considered "forward-looking" within securities laws. These statements represent Company's current judgments but are subject to uncertainties that could cause results to differ. Readers are cautioned to not place undue reliance on these statements, which reflect management's opinions only as of the date of this release. The Company is not obligated to revise any statements in light of new information or events.
Company Contact:
(951) 381-2555
info@advancedcontainertechnologies.com
Investor Relations:
Stuart Smith
SmallCapVoice.Com, Inc.
512-267-2430
ssmith@smallcapvoice.com
Related Articles
More articles issued by Advanced Container Technologies Inc.
More articles related to: Product / Services Announcement Food
AmplifiedAg Introduces Indoor Farm Platform And Disruptive Technologies, Positioning Company For Rapid Expansion
"AmplifiedAg is on a trajectory to change how the world is feeding itself. Through the adoption of our core technologies and scalable farm platform, we're providing secure food sources and influencing a global shift to indoor farming, which will play a key role in providing food to a growing planet," said Don Taylor, CEO of AmplifiedAg, Inc
News Provided By AmplifiedAg
Mar 03, 2021
CHARLESTON, S.C., March 3, 2021 /PRNewswire/ -- With a mission to provide global access to safe food, AmplifiedAg, Inc. introduces its indoor farming platform which includes vertical farms, hydroponic systems, and its proprietary operating system with disruptive seed-to-sale SaaS-based technologies. For the past five years, AmplifiedAg has demonstrated its unparalleled ability to sustainably grow produce to scale at the highest yield, quality and nutritional value, while operating directly at the point of consumption.
AmplifiedAg, Inc. wholly-owns Vertical Roots, the largest hydroponic container farm in the world. Vertical Roots indoor farm production operates with AmplifiedAg's holistic indoor farming platform.
AmplifiedAg's compact farm design operates directly at the point of consumption, maximizes growing space, and is easily scalable in food deserts and space-limited areas. The company's proprietary OS gives farmers total transparency and control of horticulture, food safety, production and business management.
AmplifiedAg deploys indoor farms 70% faster than other CEA implementations, and directly at the point of consumption.
AmplifiedAg rapidly deploys fully functioning farms 70% faster than other CEA implementations, and at cost, that is 50% of the required capital per production pound. The company upcycles shipping containers into controlled agriculture environments with vertical hydroponic systems, LED lights, and electronics, and integrated with AmplifiedAg's proprietary operating system.
AmplifiedAg's indoor farm platform produces 86 times more crop yield per acre compared to traditional farmlands and provides reliable crop production with 365-day farming, regardless of climate and resources. The compact design maximizes the growing space and provides easy mobility and scalability in food deserts and space-limited areas.
But the heartbeat of the operation is AmplifiedAg's proprietary Operating System that features industry-exclusive traceability which tracks every detail of an individual plant's journey from its growth to distribution. This gives farmers total transparency and control of horticulture, food safety, and business management.
Farm containers' resilient architecture and segmentation minimizes the risk of crop loss due to pest and pathogen infestations. SaaS-based technologies provide real-time tracking analytics and 24/7 access for farmers to mitigate risk, control the farm environment and optimize plant growth.
AmplifiedAg's ability to quickly place farms directly in communities and distribution points drastically reduces emissions. Sustainably-focused, the farms don't use soil or pesticides and utilize up to 95% less water than traditional farming.
Wholly-owned by AmplifiedAg, Vertical Roots is the company's proofpoint and has set industry-breaking records in less than five years. Vertical Roots is the largest hydroponic container farm in the U.S., growing nutritious leafy greens with products in over 1,200 grocery stores across the Southeast.
With a proven concept for leafy greens, AmplifiedAg's horticulture expansion plan includes varied nutrient and protein-rich foods to feed the world's growing population.
Increasing threats to the planet's food production fueled Taylor, a 30-year software industry veteran, to found AmplifiedAg in 2016.
"With a growing population, less arable land, water supply and food contamination issues, climate change and environmental disasters," said Taylor, "Our planet is on a path to grow less food for more people while continuing to accelerate the degradation of the earth's fragile ecosystem. Exasperating our already critical food access issues on the planet. The only way we're going to get ourselves out of this situation is with technology. We need to grow safer food in greater volumes closer to the point of consumption while conserving and restoring the environment."
"That is what is driving all of our development and innovation, and ultimately the demand we are seeing from indoor farmers and communities across the world," concluded Taylor.
AmplifiedAg, Inc. was founded in 2016 as the parent company of Vertical Roots, Boxcar Central, a SaaS platform supporting third-party logistics companies and breweries, and Tiger Corner Farms, a CEA farm manufacturing company. AmplifiedAg has absorbed Tiger Corner Farms and Boxcar Central operations as the company presents its mobile indoor farm platform to the market.
About AmplifiedAg, Inc.
AmplifiedAg, Inc. is an ag-tech industry visionary on a mission to provide global access to safe food. The company manufactures indoor vertical farms, hydroponic systems, and disruptive seed-to-sale SaaS-based technologies. Unlike other indoor ag operations, AmplifiedAg provides holistic indoor farm solutions to grow and distribute food anywhere in the world.
AmplifiedAg owns and operates Vertical Roots, the largest hydroponic container farm in the World. Learn more at www.amplifiedaginc.com. Growing Food for a Growing World.
SOURCE AmplifiedAg
Related Link
New Freight Farms CMO Shares 4 Reasons Why He Moved From Sportswear To AgTech
After an amazing experience and professional success, James felt that he needed a change: a new challenge, a new industry, a new way to make an impact
Former Senior Director Global Marketing at Reebok shares his reasons for joining Freight Farms C-Suite
James Woolard spent the last 14 years at Reebok, heading up everything from regional Sports Marketing and Brand to Global Marketing for the brand’s Running and Style units. After an amazing experience and professional success, James felt that he needed a change: a new challenge, a new industry, a new way to make an impact. His search brought him to the world of AgTech and Freight Farms, where he saw the huge potential of both the company and the industry and knew it was just what he had been looking for. Today, James shares the four big reasons why he was so drawn to the AgTech industry, and how he believes his previous experience will help propel Freight Farms forward.
In the past, I have always resisted “building a social presence” as a result of a (very British) suspicion of people’s real motives and my own laziness in maintaining it. In truth, the former reason is an easy cover story for the latter. However, in this case, my aversion to online social platforms has been overruled by a greater feeling that I want to share: Gratitude.
I am grateful for the experiences I have had, the people I have been fortunate enough to meet, and excited by all the opportunities in the future. However, most recently I am grateful for the opportunity to become the Chief Marketing Officer of Freight Farms. There were several small reasons to make the switch–but they all scaffold up to four somewhat big reasons:
Creating a Simple Solution for a Complex Problem
A pioneer of indoor agriculture and a leader in hydroponic container farming, Freight Farms has a suite of products and technology that can revolutionize access to hyper-local fresh grown produce. Our products reflect a level of complex design and engineering on which far cleverer people than me tirelessly work; yet the solution we are creating is incredibly simple — A 2.5-acre smart farm in a 40ft freight container that can go anywhere in the world to provide food security. With already over 300 of our farms around the world, we are building a tech-connected network of farmers who are simultaneously solving food access issues in their own communities and building a new global food system–all powered by Freight Farms technology.
1 in 6 people in the world relies on food imports to feed them daily. This number is set to reach 3 in 6 by 2050.
9 counties–mostly in California–are responsible for most of the food supply within the U.S. Any disruption (fires, drought, etc) can be catastrophic to the whole system.
In the U.S., 19 million people currently live in food deserts with limited access to healthy and nutritious fresh foods.
2. Leveraging Cross-Category Experience
In addition, I am incredibly grateful to my former colleagues at Reebok and Adidas. I was lucky enough to have a robust education in the UK Sports industry and be part of and learn from an amazing Adidas leadership team. I was fortunate enough to come to the US, understand firsthand the dynamics of a global business, and meet a diverse range of interesting people. And I got to set up my family in Boston.
Now it is time to apply this experience to Freight Farms. Why the move from sports to Agtech you might ask? Yes, I needed the change and new challenge. And yes I would be lying if I said I targeted Agtech but sometimes you find what you need without realizing it. I am still a sports fan at heart — and when I first walked into the offices I walked into a locker room full of energy and talent. I was intrigued and hooked early on. I met Jon — who a decade earlier had looked at a Freight container and thought “why can’t I put a farm in there and build a business helping people anywhere in the world access fresh, hyper-local food”; I met a team of people (young, purposeful, talented ones) like Caroline, our Director of Marketing and Community Relations, with huge potential and authenticity who wanted to learn and grow; I met a new CEO in Rick and CTO in Jake with pedigree and passion; I saw a set of investors led by Ospraie Management and Spark Capital backing this all with capital.
3. Driving Profits for Company & Customers
At Freight Farms, I saw the impact I personally could have on the business. We have a thriving community of customers who have been essential in building Freight Farms’ success. The stories are inspiring, and I am eager to apply my experience to help Freight Farmers achieve their own individual success with the best possible support from our company. At the end of the day, we can’t be shy about saying “people need to make money”, because that’s the only way our mission to build a global infrastructure of local farms can succeed. I am here to embrace this and say ‘how can we create a return on investment for every stakeholder’? This is how we will grow.
4. Saying ‘No’ to Greenwashing and ‘Yes’ to Tech for Good
I am conscious of the perceived need to be on trend with “sustainability”, of the danger of falling into buzzwords and jargon that are of the moment. There is a business model and story myriad people are chasing. This is all happening parallel to a degradation of our trust in technology; as a society, we recognize it’s time to direct it towards something good. With three girls under 12 (all over using screens in Covid times), I see the benefits and dangers. We all see the power of the big brands and how algorithms are driving division. I believe people want to see positive expressions of technology beyond driving up their 401k. Combined, these two factors unlock our greatest brand strength in 2021: we already do leverage technology and data to create a truly sustainable product. There’s no need to spin, exaggerate, or greenwash. We can carry on doing exactly what we are doing with confidence that we’re creating the kind of positive impact the world needs.
That’s what is most exciting about entering the ‘Agtech’ industry: the moniker actually means something — the former (Agriculture) consistently driving change throughout history, and the latter (tech) acting as the most rapid accelerator of that change in my lifetime. It’s exhilarating, and I can’t wait to see how far we can take it.
Learn more about Freight Farms.
Freight Farms
Empowering anyone to grow food anywhere. Freight Farms makes local food accessible in any climate with the Greenery™ container farm.
Follow
3
USA - MICHIGAN: Indoor Agriculture Receives $100,000 Grant From MDARD
The indoor agriculture program is a new major brought to NMU which focuses on hands-on learning of indoor agriculture, sustainable farming practices, urban farming models, environmental infrastructure systems, helping solve the global food crisis, and more
NMU’s new indoor agriculture program recently received a $100,000 grant on Feb. 12 from Michigan’s Department of Agriculture and Rural Development to help offset the costs for a self-contained growing center.
According to MDARD’s page, the grants are to help “promote the sustainability of land-based industries and support infrastructure that benefits rural communities”.
MDARD received over 139 proposals, totaling over $11 million. The program only accepted 20 proposals, which totaled to roughly $1.7 million. This included NMU’s proposal for a self-contained growing center.
The indoor agriculture program is a new major brought to NMU which focuses on hands-on learning of indoor agriculture, sustainable farming practices, urban farming models, environmental infrastructure systems, helping solve the global food crisis, and more.
Last fall was the first semester that the program took off.
“One of the biggest challenges of growing a program is finding space, and even though there is some available around campus, and in the Jacobetti Center in particular, it still costs a lot of money to retrofit that space and make it usable for the intended purpose.” Evan Lucas, assistant professor of technology and occupational sciences, said. “We targeted this grant specifically to help alleviate the cost impact of adding space for our labs.”
Lucas went on by saying that the program submitted the idea of purchasing one to two shipping containers to enhance the curriculum. The shipping containers, depending on size and capability would be used to add growing space and diversity the type of growing space.
The program hopes that with the grant money they will be able to grow, and in turn create more space for students to work. Sarah Cormier, a junior in the indoor agriculture program, has exciting hopes for the grant money.
“I’d hope it’d encourage others to look into the program and think about food production differently,” said Cormier. “We are limited in our labs with the number of seedlings we can tend to, but with more systems we would be able to monitor more plants simultaneously.”
In turn, having more space means having room for more students. After quick shutdowns and pack-up times, last semester was hard for the program. However, Cormier felt that the experience this semester has been more straightforward.
With the COVID-19 pandemic, the program had to cut back on the amount of students able to register. This left many students on waiting lists, unable to participate in the brand new program.
“We were unfortunately not able to open up more than we did without sacrificing the hands-on aspect of growing, which we weren’t really willing to do as that kind of defeats the main purpose,” Lucas stated.
However, Lucas was quick to say how integral Kim Smith Kolosa, another assistant professor of technology and occupational sciences, was to the program.
“She has done an amazing job taking this program from literally non-existent to exceptional in no time, and we couldn’t ask for anything better at this time,” Lucas said.
TAGS: grant, indoor agriculture, news
Where Vertical Farming and Affordable Housing Can Grow Together
Some vertical farms grow greens in old warehouses, former steel mills, or other sites set apart from the heart of cities. But a new series of projects will build multistory greenhouses directly inside affordable housing developments
Some vertical farms grow greens in old warehouses, former steel mills, or other sites set apart from the heart of cities. But a new series of projects will build multistory greenhouses directly inside affordable housing developments.
“Bringing the farm back to the city center can have a lot of benefits,” says Nona Yehia, CEO of Vertical Harvest, a company that will soon break ground on a new building in Westbrook, ME, that combines a vertical farm with affordable housing. Similar developments will follow in Chicago and in Philadelphia, where a farm-plus-housing will be built in the Tioga District, an opportunity zone.
Inside each building, the ground level will offer community access, while the greenhouse fills the second, third, and fourth floors, covering 70,000 square feet and growing around a million pounds of produce a year. (The amount of housing varies by site; in Maine, there will be only 15 units of housing, though the project will create 50 new jobs.)
In Chicago, there may be a community kitchen on the first level. In each location, residents will be able to buy fresh produce on-site; Vertical Harvest also plans to let others in the neighborhood buy greens directly from the farm. While it will sell to supermarkets, restaurants, hospitals, and other large customers, it also plans to subsidize 10% to 15% of its harvest for local food pantries and other community organizations.
“By creating a large-scale farm in a food desert, we are creating a large source of healthy, locally grown food 365 days a year,” Yehia says.
Living Greens Farms Ramps Up Midwest Expansion
Living Greens Farm has upped its retail distribution with the addition of UNFI Produce Prescott, a division of United Natural Foods, Inc (UNFI)
Feb. 18th, 2021
by Melissa De Leon Chavez
FARIBAULT, MN - Living Greens Farm (LGF) has upped its retail distribution with the addition of UNFI Produce Prescott, a division of United Natural Foods, Inc. (UNFI). This new retail partnership will help LGF expand its product reach to independent, specialty, and co-op retailers throughout the upper Midwest.
According to a press release, LGF’s proprietary vertical indoor farming method yields high-quality, fresh produce. No pesticides or chemicals are used during the growing process. Throughout the growing, cleaning, and bagging process, LGF reduces handling and time to the retail shelf. All of these benefits continue to attract new users and new retail distribution.
Living Greens Farm has upped its retail distribution with the addition of UNFI Produce Prescott, a division of United Natural Foods, Inc (UNFI)
Beginning this month, LGF’s full line of products featuring ready-to-eat bagged salad products, such as Caesar Salad Kit, Southwest Salad Kit, Harvest Salad Kit, Chopped Romaine, and Chopped Butter Lettuce will be carried by UNFI Produce Prescott (formerly Alberts Fresh Produce).
Across the nation, UNFI has eight warehouses, and LGF’s products will be carried by its upper Midwest location, located just across the river from the Twin Cities in Prescott, Wisconsin.
As indoor farming becomes more popular, who will Living Greens Farm partner with next?
Stay tuned to AndNowUKnow as we cover the latest.
COMPANIES IN THIS STORY
We believe in revolutionizing how produce is grown throughout the world. Our products are fresh, local, and pesticide-free....
UNFI
UNFI is the leading independent national distributor of natural, organic and specialty foods and related products...
How Vertical Farming Is Taking Off
Food supply chains are under more scrutiny than ever in the era of coronavirus and Brexit. The vertical farming movement offers solutions to some of the biggest challenges facing agriculture today
By George Nott
5 February 2021
Food supply chains are under more scrutiny than ever in the era of coronavirus and Brexit. The vertical farming movement offers solutions to some of the biggest challenges facing agriculture today
This feature is the first in a two-part series on the future of farming
Michiel Peters has been fielding some frantic calls in recent weeks. “People are saying, ‘You have to come now! We’re sorry we didn’t call you a year earlier!’” the CEO of vertical farming company PlantLab reports.
It seems vertical farming has reached a tipping point. For a long time, any consideration of the method soon ended with unit economics. But the price of produce has been rapidly falling – to the point that it’s now beginning to compete with traditional farms. And the unique advantages of vertical farming are suddenly coming into sharp relief for manufacturers, suppliers and retailers. So much so that the sector is preparing for a huge boom in interest and investment.
Indeed, demand is so heightened that Peters and his peers are having to turn potential customers away. Could now be vertical farming’s big moment?
“It’s not really a question of ‘if’ anymore. It’s going to happen,” Peters says. “And it’s already happening. It’s a matter of scaling up now.”
The benefits lie in the vertical farming method. Produce is grown indoors under LED lights, with a plant’s roots typically suspended in nutrient-rich water or mist. Temperature, humidity and light is carefully regulated within the sealed environment, and more plants can be packed into a space, on racks that can be seven storeys high.
While yield per square metre, low water consumption and lack of soil or pesticides have long been touted as the method’s main selling points, another one is becoming increasingly important: a guaranteed, year-round supply situated right where it is needed.
“On a small island or in remote locations, vertical farms can have a tremendous impact on food supply, especially in Covid times,” says Peters. “The food chain is typically very long and sensitive. When things break down, people realise their security of supply is not always a given.”
“It’s not really a question of ‘if’ any more. It’s going to happen. It’s a matter of scaling up now”
That’s not to say vertical farming businesses have been immune from the effects of the pandemic. The construction of Amsterdam-based PlantLab’s second overseas site in the Bahamas is being thwarted by current travel restrictions, for example. But Covid, and the disruption it has wreaked on global supply chains, is ultimately helping the sector make its case.
“There’s huge interest from island economies, hot economies and countries that have a higher propensity to import and have less arable land,” says Jamie Burrows, CEO of London-based Vertical Future. “From Iceland to Singapore, they all have very similar requirements.”
Plus, the pandemic isn’t the only threat to imports, Burrows adds. “If you import a lot of food, climate change is going to impact the countries that are producing that food for you. Even now, there have been pretty significant inflections in price on shelves and availability because of small fluctuations in temperature during the key growing seasons,” he explains.
And there is yet another factor that is throwing vertical farming into the spotlight in the UK, specifically: Brexit. That’s not just down to the immediate effect of imports disruption. The local produce sector remains riddled with uncertainty over access to the many seasonal workers that used to come from the EU, with a potential labour crisis looming.
Indoor farms, which are typically highly automated, require far fewer people to run. Furthermore, with constant harvesting, a small and constant rather than large and seasonal workforce is needed.
The yield and potential of vertical farming
The market opportunity for vertical farms is huge. Barclays Research analysts estimate the size of the global fruit & vegetable market is roughly $1.2tn (£800bn), and calculate that the addressable produce market for vertical farms is closer to $700bn (£513bn), leading to an approximately $50bn (£36.7bn) market opportunity. Plus, vertical farming boasts some environmental benefits, as produce requires less water and space to grow
Jones Food Company’s Scunthorpe vertical farm is a prime example. It has 26 tennis courts of growing space, operating 365 days a year – with a staff of six.
“Imagine if you have next to no labour in a farm that big. One of your largest costs is one you can really attack,” says James Lloyd-Jones, JFC CEO, and founder.
As a bonus, businesses such as JFC can boast lower carbon emissions than outdoor farms. While energy-intensive – to make up for the lack of natural sunlight – sector argues overall carbon savings are made when indoor farms are positioned close to where produce is needed, drastically reducing food miles.
Furthermore, Peters says, “if you make the chain radically short, you don’t need to waste so much of the harvest. You can avoid it altogether.”
This element could be particularly important to retailers with ambitious carbon commitments. “Retailers are being asked more questions than they’d probably like about carbon. You can’t just fudge it any more,” says Lloyd-Jones.
It’s not all plain sailing, though. There are some major hurdles for the sector to overcome – chiefly, the huge capex needed to build an indoor farm. Because of this, many vertical farming companies, whose main interest is in providing the technology for the farms to function, are becoming farm operators and even consumer brands.
PlantLab launched its first US production site – or ‘Plant Paradise’ – in December, within a former battery factory near Indianapolis city centre.
Having spent some time “working in relative silence” on the technology, PlantLab is now a site developer and operator. Local partners distribute and brand the end product into local supermarkets. As patent holder for its indoor farming tech in 74 countries, it is also in talks with major players about licensing the IP. But, adds Peters: “We’ve started this company to change the world, not just sit behind a desk and talk about licenses.”
It helps that PlantLab can point to the success of its own farms. Because building farms yourself is necessary to prove the technology and economics, says Lloyd-Jones. “There’s a lot of vertical farming companies that are tech companies, but they don’t grow anything so the person buying is the guinea pig,” he says.
For his part, he’s looking to refine the JFC concept further before embarking on a licensing model. The company already has plenty of expertise. Ocado-backed JFC is Europe’s largest vertical high-care farming operation, its 5,000 sq m facility stacking up 12 metres high with more than 17 layers of produce. But it will go one step further with its two new sites in the Midlands and the south west, due to open by the end of this year.
They will be more technologically advanced – “it’s like we built the first iPhone in Scunthorpe. We’ve jumped to making the iPhone 8,” Lloyd-Jones says – and will provide enough produce to meet 25% of UK demand for herbs.
The end goal is to develop a “cookie cutter” vertical farm that can be quickly and cheaply built wherever needed. “Once we’re happy with that we’ll look at a licensing model where we build these facilities all round the world. But anyone building them will know they’ve been stressed, used and run at 100%,” he says.
The model for vertical farming firms then is likely to be akin to Ocado and Ocado Retail, where the latter proves the case for the former’s technology, which rivals then adopt.
So similar, in fact, that Ocado itself is looking to get involved. In February last year, it formed Infinite Acres – a joint venture with Netherlands-based automation tech provider Priva Holding BV and US-based 80 Acres Farms, a vertical farm operator and brand. Customers have two options. They can either partner with Infinite Acres to build their own farm, or they can have 80 Acres run a farm on their behalf using that same technology.
If companies get it right, the licensing model can be lucrative. See Vertical Future for proof. It has two farms in London, with three more being built, but the output of the farms is only a small part of the business. “We retain them to keep our finger on the pulse and customer trends and it validates what we’re doing,” says Burrows. “Ninety-five per cent or more of our revenue now is from technology sales and software.”
Funding flurry
That potential has prompted a flurry of investment in the sector, kicked off in 2017 by Japanese media giant SoftBank, Alphabet’s Eric Schmidt and outgoing Amazon boss Jeff Bezos’ funding of San Francisco vertical farming startup Plenty. Plenty has now raised more than $200m in venture funding.
With it has come a lot of hype. “There is a lot of hot air in vertical farming,” Burrows says. “People can make crazy claims – one company said it could grow a head of lettuce in five days, which is ridiculous. And there is a lot of smoke and mirrors and low-grade companies trying to jump on the bandwagon.
“The risk is farms will fail and make the sector look bad,” he adds. “The impact for the good companies is investors will look at the sector and say it seems risky.”
Nevertheless, the pile-on is ultimately a positive thing, says Peters. “It’s maybe a matter of culture. In the US things tend to be more hyped and people tend to promise the world – then figure out after they have the money, they still need to do all the R&D,” he explains. “But it all helps to underline it’s really happening, and makes it acceptable and credible to consumers.”
Just how big vertical farming can get remains to be seen. Barclays estimates a $50bn (£36.7bn) market opportunity. As a total share of fresh produce output, it’s “going to be a single digit for years” says Burrows. “But as a standalone sector the growth rates are very high and will continue to be.”
Indeed, although it is currently focused on a small range of herbs and leafy greens, ultimately “you can grow anything” says Lloyd-Jones. While staples like rice and wheat might not be viable now, that will soon change. Competitive prices will doubtless be added to vertical farming’s multitude of advantages.
“We don’t want to get stuck in just being a premium, niche product that will only be affordable by a small part of the market,” says Peters. “We want to change the world.” Suddenly, that aim seems within reach.
Five firms leading the global vertical farming movement
InFarm
Vertical farms don’t have to be on a grand scale. In fact, they can fit in a chiller cabinet. InFarm places production right in the supermarket aisles at clients including Whole Foods Market and M&S.
“Modern agricultural production is built on a supply chain that is vulnerable to ecological and supply shocks. The global pandemic highlighted this. Retailers are having difficulties importing fresh produce, highlighting the need to develop a local and sustainable supply chain,” says Daniel Kats, VP of corporate sales.
Source: LettUs Grow
LettUs Grow
Bristol start-up LettUs Grow specialises in aeroponic farms that fit within a shipping container. Customers can purchase the full “business in a box”, which includes the grow beds and control system.
“Unlike a traditional farm, you’re not limited by location or climate. Your container farm needs no fertile land to operate and with its advanced climate control system, every day is a perfect summer’s day with ideal growing conditions,” LettUs Grow says. The company has raised a total £3.4m.
Source: PlantLab
PlantLab
This Dutch indoor farming firm launched its Indianapolis site in December. The 54,000 sq ft farm, developed in partnership with the Englewood Community Development Corporation, will provide an annual supply of close to 45,000 kg of fresh herbs and lettuce to local supermarkets and foodservice companies.
The fresh tomatoes, cucumbers, lettuce, and herbs grown in the ‘Plant Paradise’ are being marketed under the brand name Uplift, with the tagline ‘good food on purpose’.
Source: CropOne
CropOne
The world’s largest vertical farm is being built in Dubai, a joint venture between US firm Crop One and Emirates Flight Catering.
The $40m, 130,000 sq ft controlled environment facility will produce 6,000 pounds of high-quality, herbicide and pesticide-free leafy greens, harvested daily.
“We secure our own supply chain of high-quality and locally-sourced fresh vegetables, while significantly reducing our environmental footprint,” said Saeed Mohammed, EFC CEO.
Source: AeroFarms
AeroFarms
US firm AeroFarms last year announced it was building a 90,000 sq ft vertical farm in Abu Dhabi, which will be the world’s largest indoor agriculture research centre. The facility will house research centres for plant reproduction, seed breeding, machine learning and vision as well as robotics.
The company has grown more than 800 varieties of crops and is eyeing opportunity beyond food production in other industries like pharmaceutical, cosmeceutical and nutraceutical.
The Grocer
Lead photo: Source: AeroFarms
Topics: Farming Fruit & Veg Supply chain Sustainability & environment Technology
Fifth Season Takes Vertical Farming to a Whole New Level
Fifth Season’s verdant baby spinach screams farm fresh even though it’s grown nowhere near traditional farmland. The sweet and slightly crunchy greens are grown in a Braddock warehouse on racks stacked 30 feet high. Located just a stone’s throw from U.S. Steel’s Mon Valley Works Edgar Thomson Plant, it is urban farming at its core
Image from: Pittsburgh Post-Gazzette
Fifth Season’s verdant baby spinach screams farm fresh even though it’s grown nowhere near traditional farmland. The sweet and slightly crunchy greens are grown in a Braddock warehouse on racks stacked 30 feet high. Located just a stone’s throw from U.S. Steel’s Mon Valley Works Edgar Thomson Plant, it is urban farming at its core.
What makes the vertical farming operation especially unique is that it is automated and robots call the shots. About 40 to 60 machines are involved in every step of the life of the spinach and other leafy greens, from planting the seed to providing nutrients to the final packing.
Fifth Season does employ local “farm workers” to assist the robots in seeding, harvesting, packaging, quality assurance and control using computer software, but there is no human touch involved through it all.
“The first time someone ever touches the spinach leaf with a finger is when the package is opened,” says Grant Vandenbussche, chief category officer.
Co-founded by brothers Austin and Brac Webb and Austin Lawrence, Fifth Season started a year ago. Within months it was rolling out its baby spinach, leafy greens and salad kits.
“We wanted a name that represents what we are doing,” says Austin Webb, 32, who also is the CEO. “It is a call to the fact we have created an entirely new season. It is 24/7, 365 with the technology we have built.”
None of them planned to become modern farmers, says the Carnegie Mellon University grad, but they turned to vertical farming because it was an efficient, economically sustainable way to solve land and water woes.
Image from: thespoon.tech
‘Fields’ of Greens
Fifth Season grows an equivalent production of 200 acres in 25,000 square feet of grow space. Its “fields” are stacked on top of one another in vertical shelves. When you add up all that surface area of grow space, it is more like 126,000 square feet.
“We also quickly turn crops at the farm,” Mr. Vandenbussche says.
While spinach takes about 40 days to grow outdoors and can be harvested only twice during its peak season, it takes the crop only three or four weeks to grow in the controlled environment and is harvested 19 times. Once the plants are harvested, a new cycle of reseeding begins with fresh media, seeds and nutrients.
“That’s why we get so much more productivity,” he says. “We are immediately reseeding our ‘land.’”
This controlled environment yields quality produce because it is always peak season at Fifth Season, says Chris Cerveny, who heads the Grow R&D division. Greens are grown in the same conditions year-round, getting the exact amount of nutrients and water they need. Because pests and airborne toxins also are kept at bay, crops can be produced without pesticides.
All that TLC comes through in the slightly curled baby spinach, which is sweet and not grassy. The leaf doesn’t wilt or get slimy or lose its slight crunch even after two weeks of refrigeration.
A lot of thought was given even for the curl, which gives the spinach a stronger volume, making it look full and bountiful. The curl also makes the spinach more forkable unlike its flat-leaf counterpart that is hard to stab on a plate.
Other leafy greens such as kale, mustard, Chinese cabbage, green tatsoi and purple pac choi are featured in two blends — Bridge City and Three Rivers. Fifth Season plans to roll out its Romaine lettuce in spring.
The greens also are found in four types of salad kits — Sweet Grains (blended greens, quinoa, chickpeas, corn, feta and poppy seed dressing), Crunchy Sesame (blended greens, farro, sesame sticks, dried cranberries and ginger-mandarin dressing), Toasted Tuscan (spinach, lentils, sun-dried tomatoes, bagel chips and vinaigrette), and Spiced Southwest (blended greens, black beans, pepitas, cotija cheese, corn-salsa sticks and chipotle ranch dressing) — which are available online and in Giant Eagle stores. A fifth salad kit is in the works and is being called “a shakeup of one of the most classic salads.”
While machines are a big part of what Fifth Season does, it seeks to keep human connection alive. It recently launched a recipe blog for those who have an appetite for cooking and writing, The Green Room is devoted to cataloging personal memories, dream meals and recipes via short stories.
Fifth Season also has partnered with the Penguins and is providing greens for the team’s pregame meals for the 2020-21 season.
“We want people in Pittsburgh to be able to eat the exact same delicious blend of greens that Sidney Crosby and company are eating,” Mr. Webb says. “We want people to know that there’s a new way to grow food and to eat and experience it.”
Image from: Next Pittsburgh
It’s All Under Control
Everything from seeding to packaging is done in four rooms. The process starts in the seeding and processing room, where seeds and growing media are placed inside black planter-like boxes called inserts. Each has a unique code that’s traced by a software system. The inserts go on white trays that pass through a photo station, feeding information to the computer system, and then glide into the bio dome.
There are two rooms in the bio dome, each with a grow space of 12,500 square feet. They’re lit up with a pinkish-purplish glow from high-efficiency LED light bulbs that mimic the different seasons of the year.
“They are positioned over the plants at different heights depending on stage of growth,” Mr. Cerveny says. “This is partly how we can provide consistently ideal growing conditions.”
As the plants grow, they are moved by a robot to optimize their growth cycle. Full-grown crops are transferred to the harvesting room by another robot.
“Harvesting is where it becomes like a Willy Wonka factory,” Mr. Vandenbussche says.
Long rows of trays filled with tiny plants are sent on a conveyor system to a station where workers inspect them for quality with surgical tools. After inspection, the plants are harvested by a robot and then immediately ride up a tall conveyor to be packaged and sealed in a 34- to 36-degree room so they remain fresh.
“Every crop we grow gets evaluated for maximum flavor, volume, crunch and color,” he says.
The plants’ intense, dark color is controlled by LED light bulbs, which are dialed up or down to get the correct hue. Although they never see the sun, the greens don’t get into a funk as humans might.
“What humans see in terms of light and how chlorophyll responds during photosynthesis are two different things,” Mr. Cerveny says. “Plants really only need red and blue light to grow effectively. We include some additional colors to help bring out other quality aspects of our crops, but providing the full sunlight spectrum is effectively a waste of energy, especially indoors.
“To the human eye, it looks like the plants live in a land of purple and pink lights, but they are perfectly happy there.”
Even though the environment is controlled and the software system is constantly updated, no two plants are exactly the same. Some fight for light more than others. Some might fail the quality control test and end up in a compost waste facility if their flavor is off or their color is not right.
“That is what is so amazing. We have more control than any other farmer, and yet we have limitations. Every seed is different,” Mr. Vandenbussche says. “They are plants. They are real living organisms.”
Is AppHarvest the Future of Farming?
In this video from Motley Fool Live, recorded on Jan. 28, Industry Focus host Nick Sciple and Motley Fool contributor Lou Whiteman discuss AppHarvest, one such SPAC that is looking to disrupt the agriculture industry. Here are the details on what AppHarvest wants to do, and a look at whether the company represents the future of farming.
Special purpose acquisition companies, or SPACs, are red-hot right now, with investors clamoring to get into promising young companies.
In this video from Motley Fool Live, recorded on Jan. 28, Industry Focus host Nick Sciple and Motley Fool contributor Lou Whiteman discuss AppHarvest, one such SPAC that is looking to disrupt the agriculture industry. Here are the details on what AppHarvest wants to do, and a look at whether the company represents the future of farming.
Nick Sciple: One last company I wanted to talk about, Lou, and this is one I think it's -- you pay attention to, but not one I'm super excited to run in and buy. It was a company called AppHarvest. It's coming public via a [SPAC] this year. This vertical farming space. We talked about Gladstone Land buying traditional farmland. AppHarvest is taking a very different approach, trying to lean into some of the ESG-type movements.
Lou Whiteman: Yeah. Let's look at this. It probably wouldn't surprise you that the U.S. is the biggest global farm exporter as we said, but it might surprise you that the Netherlands, the tiny little country, is No. 2. The way they do that is tech: Greenhouse farm structure. AppHarvest has taken that model and brought it to the U.S. They have, I believe, three farms in Appalachia. The pitches can produce 30x the yields using 90% less water. Right now, it's mostly tomatoes and it is early-stage. I don't own this stock either. I love this idea. There's some reasons that I'm not buying in right now that we can get into. But this is fascinating to me. We talked about making the world a better place. This is the company that we need to be successful to make the world a better place. The warning on it is that it is a SPAC. So it's not public yet. Right now, I believe N-O-V-S. That deal should close soon. [Editor's note: The deal has since closed.] I'm not the only one excited about it. I tend not to like to buy IPOs and new companies anyway. I think the caution around buying into the excitement applies here. There is a Martha Stewart video on their website talking up the company, which I love Martha Stewart, but that's a hype level that makes me want to just watch and see what they produce. This is just three little farms in Appalachia right now and a great idea. This was all over my watchlist. I would imagine I would love to hold it at some point, but just be careful because this is, as we saw SPACs last year in other areas, people are very excited about this.
Sciple: Yeah. I think, like we've said, for a lot of these companies, the prospects are great. I think when you look at the reduced water usage, better, environmentally friendly, all those sorts of things. I like that they are in Appalachia. As someone who is from the South, I like it when more rural areas get some people actually investing money there. But again, there's a lot of execution between now and really getting to a place where this is the future of farming and they're going to reach scale and all those sorts of things. But this is a company I'm definitely going to have my radar on and pay attention to as they continue to report earnings. Because you can tell yourself a story about how this type of vertical farming, indoor farming disrupts this traditional model, can be more efficient, cleaner, etc. Something to continue paying attention to as we have more information, because this company, like you said, Lou, isn't all the way public yet. We still got to have this SPAC deal finalized and then we get all our fun SEC filings and quarterly calls and all those sorts of things. Once we have that, I will be very much looking forward to seeing what the company has to say.
Whiteman: Right. Just to finish up along too, the interesting thing here is that it is a proven concept because it has worked elsewhere. The downside of that is that it needed to work there. Netherlands just doesn't have -- and this is an expensive proposition to get started, to get going. There's potential there, but in a country blessed with almost seemingly unlimited farmland for now, for long term it makes sense. But in the short term, it could be a hard thing to really get up and running. I think you're right, just one to watch.
US - NEW MEXICO: ‘Farm in a Box’ Coming To Grants
The Farm in a Box operates inside a 40-foot shipping container, shown here in Moffat County, Colo. A similar one will be set up at New Mexico State University branch campus in Grants. (Courtesy of Tri-State Generation and Transmission)
ALBUQUERQUE, N.M. — Fresh, locally produced vegetables will soon sprout from hydroponic beds in an enclosed, converted shipping container parked at New Mexico State University’s branch campus in Grants.
The 40-foot “Farm in a Box” will provide hands-on education and workforce training for local students and others interested in studying the emerging science of “indoor agriculture” as a new, potentially sustainable, enterprise that could offer fresh economic development opportunities and job creation in an area hard hit by the transition from fossil fuels to renewable energy.
NMSU, the Tri-State Generation and Transmission Association, and the National Electric Power Research Institute (EPRI) are collaborating on the project.
It’s one of several initiatives under development with local, state, and federal backing to diversify economic activity in Cibola, McKinley, and San Juan counties, where coal-fired power plants and associated mining have provided a financial mainstay for workers and communities for decades.
Both Cibola and McKinley counties are reeling from last year’s shutdown of the coal-fired Escalante Generating Station near Grants, plus the closure of Marathon Petroleum’s oil refinery in Gallup, which together eliminated hundreds of stable, high-paying jobs in those northwestern communities.
Unemployment hit 10.8% in Cibola County in December and 10.2% in McKinley County, according to the state Department of Workforce Solutions. That compares to an 8.2% average statewide unemployment rate.
To ease the impact of Escalante’s closure and assist in transitioning local communities, Tri-State provided $5 million in grants in January to four local economic development organizations. It is also now sponsoring the Farm in a Box initiative, providing $250,000 to set up and equip the high-tech container unit that houses the indoor agricultural operation, with forthcoming grants for NMSU faculty and student assistants to work on the project.
“We realize that closing such coal facilities as the Escalante plant that have traditionally employed significant workforces creates very difficult challenges for local communities to replace those jobs,” Tri-State spokesman Mark Stutz said. “Our goal is to find opportunities in support of economic development with new technologies when we can.”
Tri-State permanently closed the 253-megawatt Escalante power plant in Pruitt last summer as part of the association’s long-term plan to completely withdraw from coal generation over the next decade. It laid off about two-thirds of the plant’s 107 employees, Stutz said.
TriState also plans to close a much larger, 1.3-gigawatt coal facility in Craig, a municipality in Moffat County, Colorado, where the company sponsored another Farm in a Box project that EPRI set up last November.
“We don’t want to just walk away from these communities that we’ve been a part of for decades,” Stutz said.
High tech
EPRI has set up similar Farm in a Box projects in 13 states, said its principal technical leader Frank Sharp, project manager for the institute’s indoor agriculture-and-lighting research efforts.
It’s part of an emerging concept of indoor farming for urban areas and isolated rural communities where food could be grown year-round right where it’s consumed. It could lead to huge energy and water savings through efficient, high-tech growing processes, contributing to carbon reduction by using electricity rather than fossil fuels in agricultural operations and by eliminating long-haul transport of produce to market.
For economically stressed communities such as Cibola and McKinley counties, it could be scaled beyond shipping containers to retrofit under-used or abandoned buildings and to construct new facilities, such as greenhouses, on empty plots, Sharp said.
“It all translates into community impact, job creation, and beneficial use of electricity,” Sharp told the Journal. “Vacated buildings with the infrastructure already in place can be retrofitted, with opportunities to also build new facilities.”
Electric Power Research Institute principal technical leader Frank Sharp, left, with Tri-State Generation and Transmission Association CEO Duane Highley, inside the Farm in a Box agricultural container that was set up in Moffat County, Colo., last November. (Courtesy of Tri-State Generation and Transmission)
Research needed
Research is still needed to maximize efficiency and production, measure benefits, make contained farming systems profitable, and train the workforce. That’s where NMSU comes in, said Jay Lillywhite, agricultural economics professor and co-director of NMSU’s center of Excellence in Sustainable Food and Agricultural Systems.
NMSU faculty and students will study the entire container system, which includes vertical, hanging plastic enclosures to grow crops connected to a closed-loop plumbing system to recycle all water. Researchers will monitor all energy and water use, plant productivity, the impact of red and blue LED lighting spectrums on plant growth, and the economics of the whole operation, Lillywhite said.
“We’ll record everything and transmit all the data wirelessly to EPRI,” Lillywhite said. “It needs to be profitable. Indoor agriculture has had mixed reviews in terms of profitability, so we’ll look at a model that makes sense for New Mexico and the Southwest.”
Other applications
Opportunities extend into many disciplines beyond agriculture, including electrical engineering focused on energy efficiency and renewable generation as alternative systems, such as solar panels, are added to indoor operations, said Rolando A. Flores, dean of NMSU’s College of Agriculture, Consumer, and Environmental Sciences.
“The project has excellent potential to address social, environmental, and economic facets of sustainability, and become a resource-efficiency model for urban agriculture, provided that renewable energy can be incorporated from the beginning,” he said.
State Rep. Patricia Lundstrom, D-Grants, said indoor agriculture can offer significant opportunities alongside other initiatives to diversify the local economy.
Lundstrom sponsored legislation last year that now allows counties with coal plants that are closing to set up special economic districts with bonding and taxing authorities to invest in infrastructure, business recruitment, and retention to create jobs and promote economic development.
That led to the launch in December of the McKinley County Electric Generating Facility Economic District, which is focused on converting the Escalante site in Pruitt into a new industrial zone to recruit more businesses to the area.
“Value-added agriculture is one of the opportunities we can work to develop there with help from the partners on this project,” Lundstrom said. “It can have a significant impact as we work to recruit new, sustainable industry to the local community.”