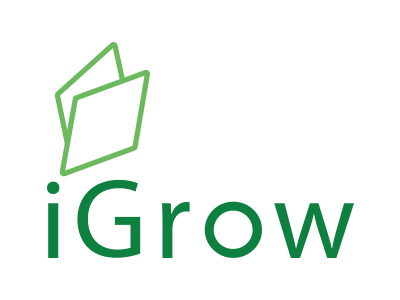
Welcome to iGrow News, Your Source for the World of Indoor Vertical Farming
FRANCE: Jungle Says It’s Cracked How To Make Vertical Farms Profitable
“No matter how good your product is, if the price is higher than the alternative, then you’re dead.”
“No Matter How Good Your Product Is,
If The Price Is Higher Than The Alternative,
Then You’re Dead.”
BY FREYA PRATTY
22 MARCH 2021
Jungle, a French vertical farming company that says it can produce ten to 30 times more food than traditional greenhouses, has raised €42m in new funding.
The company also says its focus on large-scale farms will help it overcome one of the biggest challenges facing vertical farming: how to make a profit.
Jungle’s new funding, €7m of which is in equity and €35m of which is debt financing, comes from Founders Future, a French investment firm focused on impact startups. Jungle is the firm’s first investment.
The company’s funding comes as the wider industry continues to grow fast. It was worth $2.2bn in 2018 but is expected to reach $12.8bn by 2026. Investor appetite is clearly there: vertical farming giant Infarm raised $170m at the end of last year.
Jungle is building a 5,500m2 farm 80km from Paris, where crops will grow on stacked platforms. The site is already partly operational and the company has secured contracts with French supermarkets Monoprix and Intermarche.
At present, it’s growing a mixture of aromatic herbs, greens and, unlike other vertical farms, flowers. It’ll be fully operational by the end of 2021.
Less pesticides, more local and a greater yield
Gilles Dreyfus, cofounder of Jungle.
“We don’t claim to be instigating a revolution, we are part of an equation that wants to be a solution,” explains Gilles Dreyfus, who cofounded Jungle in 2015.
For Dreyfus, vertical farming has several advantages. Crops can be grown close to cities, where the majority of consumers are, thereby reducing the environmental costs of transit.
Plants can also be grown on more frequent cycles than on traditional farms because they’re not seasonally dependent, and they’re also grown without using pesticides.
“Our most popular product, Green Basil, gives 14 harvests a year in the vertical farm, compared to 3 or 4 in the South of France, where the crop grows best outdoors.”
National food sovereignty
Being able to grow crops out of season means vertical farming can help countries achieve better food sovereignty, Dreyfus says.
“We have to go further and further from the country to get crops when they’re out of season,” he says. “Brexit import taxes on food have shown the complicated situations this can lead to.”
“If the price is higher, you’re dead”
Despite the benefits, vertical farming has often struggled with how to make a profit. “Having a viable financial model and an efficient farm is the main hurdle for vertical farming,” Dreyfus says.
“No matter how good your product is, if the price is higher than the alternative, then you’re dead.”
The company believes that bigger farms is the answer.
German company Infarm, which is aiming at profitability by 2023, places microunits into supermarkets. Jungle, which is aiming at profitability in 18 months time, will focus on large-scale production facilities that then supply a whole area.
“Price depends on scale and we’re not aiming for small-scale farms, we’re aiming for less farms but a lot bigger. If you activate the economies of scale you can get a very reasonable product,” he says.
The company’s aiming to sell food at 5% more than the cost of conventional alternatives, but at 20% less than organic foods grown on farms.
For Valentine Baudouin, partner at Founders Future which has invested in Jungle, the focus on large-scale farms is the key to profitability, and what makes Jungle stand out.
“They’ve answered the economic question of vertical farming, which is very important because you have many similar enterprises that haven’t done so.”
Jungle’s vertical farm warehouse.
Beyond salad?
A criticism often leveled at the vertical farming industry is whether it can grow beyond just salad leaves and herbs.
Unlike other farms, Jungle also grows flowers for the perfume industry, but Dreyfus says the other crops its working on, including cherry tomatoes and mushrooms, won’t be in supermarkets until 2023.
“You can grow virtually anything you want, except truffles — which is a real shame actually,” says Dreyfus. “But the question shouldn’t be, can we grow it, it should be, do we have the financial model to make it work?”
Jungle’s currently got a team of 25 people based in France, but will use the new funding to double its workforce by 2022. It also plans to open two new large-scale farms in France, including one in the south that’ll be twice as big as its first site.
Freya Pratty is Sifted’s news reporter. She tweets from @FPratty
Indoor Agtech: An Evolving Landscape of 1,300+ Startups
Our Indoor AgTech Landscape 2021 provides a snapshot of the technology and innovation ecosystem of the indoor food production value chain
March 17, 2021
Editor’s note: Chris Taylor is a senior consultant on The Mixing Bowl team and has spent more than 20 years on global IT strategy and development innovation in manufacturing, design, and healthcare, focussing most recently on indoor agtech.
Michael Rose is a partner at The Mixing Bowl and Better Food Ventures where he brings more than 25 years immersed in new venture creation and innovation as an operating executive and investor across the internet, mobile, restaurant, food tech and agtech sectors.
The Mixing Bowl released its first Indoor AgTech Landscape in September 2019. This is their first update, which you can download here, and their accompanying commentary.
Since the initial release of our Indoor AgTech Landscape in 2019, the compelling benefits of growing food in a controlled indoor environment have continued to garner tremendous attention and investment.
One of the intriguing aspects of indoor agriculture is that it is a microcosm of our food system. Whether within a greenhouse or a sunless (vertical farm) environment, this method of farming spans production to consumption, with many indoor operators marketing their produce to consumers as branded products. As we explore below, the indoor ag value chain reflects a number of the challenges and opportunities confronting our entire food system today: supply chain, safety, sustainability, and labor. Of course, the Covid-19 pandemic rippled through and impacted each aspect of that system, at times magnifying the challenges, and at others, accelerating change and growth.
Invest with Impact. Click here.
Our Indoor AgTech Landscape 2021 provides a snapshot of the technology and innovation ecosystem of the indoor food production value chain. The landscape spans component technology companies and providers of complete growing systems to actual tech-forward indoor farm operators. As before, the landscape is not meant to be exhaustive. While we track more than 1,300 companies in the sector, this landscape represents a subset and serves to highlight innovative players utilizing digital and information technology to enhance and optimize indoor food production at scale.
Supply chain & safety: Where does my food come from?
The pandemic highlighted the shortcomings of the existing supply chain and heightened consumer desires to know where their food comes from, how safely it was processed and packaged, and how far it has travelled to reach them. A key aspect of indoor farming is its built-in potential to respond to these and other challenges of the current food system.
Indoor farmers can locate their operations near distribution centers and consumers, reduce food miles and touch points, potentially deliver consistently fresher produce and reduce food waste, and claim the coveted “local” distinction. The decentralized system can also add resiliency to supply chains overly dependent on exclusive sources and imports.
Growing local has many forms. Greenhouse growers tend to locate their farms outside the metropolitan area while sunless growers may operate in urban centers, such as Sustenir Agriculture in Singapore and Growing Underground in London. Growers like Square Roots co-locate their indoor farms with their partner’s regional distribution centers, and Babylon deploys its micro-farms solution on site at healthcare and senior living facilities and universities. Recently, Infarm announced it was expanding beyond its growing-in-a-grocery store model, to include decentralized deployments of high-capacity “Growing Centers” across a number of cities. Additionally, the value of “growing local” might take on a much larger meaning if your country imports most of its produce from other countries; a number of the Gulf region countries have announced major indoor growing initiatives and projects with AeroFarms, Pure Harvest, and &ever to address the region’s food dependence on other countries.
Organic produce sales jumped to double digit growth in 2020 as consumers are increasingly mindful of the healthiness of their food. The additional safety concerns due to the pandemic only accelerated this trend. While not typically organic, crops produced in the protection of indoor farms are isolated from external sources of contamination and are often grown with few or no pesticides. Human touch points are reduced as supply chains shorten and production facilities become highly automated. Through the CEA Food Safety Coalition, the industry has recently taken steps to establish production standards with a goal to keep consumers safe from foodborne illness.
Indoor farmers market their products as local, fresh, consistent and clean. This story is resonating with consumers as the growers seem to be selling everything they can produce, with many reporting significant sales growth in 2020. The direct connection to consumer concerns is also a key part of their ability to sell their branded products at a premium, which has been critical to financial viability for some growers. This connection can also enable them to collapse the supply chain further, at least at smaller scales, through direct sales and creative business models, e.g., sunless grower Willo allows subscribers to have their own “personal vertical farm plot” and watch their plants grow online.
Sustainability: Is my food part of the problem or part of the solution?
Farming, as with most industries, has been under increasing pressure to operate more sustainably, and indoor growers, with their efficient use of resources, have rightfully incorporated sustainability prominently into their narratives.
We are well aware of the impacts of climate change, including greater variability in weather patterns and growing seasons. The UN’s Food and Agriculture Organization projects that over the coming decades climate change will cause a decrease in global crop production through traditional farming practices, causing greater food insecurity. Indoor growing, which provides protection from the elements, consistent high yields per land area, and the ability to produce food year-round in diverse locations, including those unsuitable for traditional agriculture, can help mitigate this trend.
Water scarcity is projected to increase globally, presenting a national security issue and serious quality of life concerns. According to the World Bank, 70% of the global freshwater is used for agriculture. Indoor agriculture’s efficient use of water decreases use by more than 90% for the current crops under production. It is also common practice for greenhouses to capture rainwater and reuse drainage as does Agro Care, the Netherlands’ largest greenhouse tomato grower.
On the flip side, energy use, particularly in sunless facilities, is indoor growing’s sustainability challenge. Efficiency will continue to improve, but as recent analysis on indoor soilless farming from The Markets Institute at WWF indicated, there is an industry-wide opportunity to integrate alternative energy sources. Growers recognize this opportunity to decrease impact and improve bottom-line and are already utilizing alternative approaches such as cogeneration, geothermal sources, and waste heat networks. H2Orto tomatoes are grown in greenhouses heated with biogas generated hot water. Gotham Greens’ produce is grown in 100% renewable electricity-powered greenhouses, and Denmark’s Nordic Harvest will be running Europe’s largest indoor farm solely on wind power.
Labor: We’re still hiring!
There are labor challenges and opportunities throughout the food system value chain, and this couldn’t be more acute than on the farm. Farm operators—both in-field and indoor—find it difficult to attract labor for the physically demanding work. Even before the pandemic, the hardening of borders in Europe and the US created a shortage of farmworkers for both field and greenhouse production. In addition, grower and farm manager-level expertise is in short supply, exacerbated by an aging workforce and the rapid addition of new indoor facilities. While operators would like to see more trained candidates coming from university programs, they are also looking to technology and automation to relieve their labor challenges.
Automation of seedling production and post-harvest activities is already well established for most crops in indoor farming. In addition, the short growth cycle and contained habit of leafy greens lends them to mechanization. For example, the fully automated seed-through-harvest leafy green systems from Green Automation and Viscon have been deployed in major greenhouse operations like Pure Green Farms and Mucci. On the sunless side, Urban Crop Solutions has uniquely implemented automation in shipping containers, and Finland’s NetLed has developed a fully automated complete growing system. Note that many of the larger-scale sunless growers have developed their own technology stacks and have designed labor-saving automation into their systems. For example, Fifth Season has robotics deployed throughout the entire production process.
Despite numerous initiatives, the challenging daily crop care tasks and harvesting for certain crops (tomatoes, peppers, cucumbers, and berries) have not yet been automated at scale. However, planned, near-term commercial deployments of de-leafing and harvesting robots offer the promise of significantly altering labor challenges. Software technologies, like those from Nitea and Hortikey address labor management, crop registration, yield prediction, and workflow/process management for the indoor sector and strive to improve operational efficiencies for a smaller workforce.
Technologies that provide, monitor, and control climate, light, water, and nutrients are already deployed in today’s sophisticated indoor growing facilities and are fundamental to maintaining optimal conditions in these complex environments. They also form the base for the next innovation layer, i.e., crop optimization and even autonomous control of the growing environment based on imaging and sensor platforms (like from Ecoation, iUNU, and 30MHz), data analysis, machine learning, digital twins and artificial intelligence. Recent events like the Autonomous Greenhouse Challenge have successfully explored the potential of AI to “drive horticultural productivity while reducing resource use and management complexity”. Emerging commercialized autonomous growing innovations, such as the Blue Radix Crop Controller and Priva’s Plantonomy, promise to extend and enhance the reach of available grower expertise, particularly in large and multi-site operations.
Where do we go from here?
Since we created our initial Indoor AgTech Landscape, there has been positive change and reason to be optimistic about the future. But, as with any evolving market and sector of innovation, it can be a bumpy ride. Some believe CEA is not the answer to our food problems because not everything can be economically grown indoors today. We see indoor ag as just one of the approaches that can help fix our food system and it should be applied when it makes sense. For example, tomatoes sold through retail are already more than likely grown in a greenhouse. Expect more crops to be grown indoors more economically with further advancements.
One aspect of our previous landscape was to increase awareness that, despite the fervor surrounding novel sunless farming, greenhouse growing was already well-established. Dutch greenhouse growers have demonstrated the viability of indoor growing with 50-plus years of experience and more acres “under glass than the size of Manhattan.” The recent public offering and $3 billion market cap of Kentucky-based greenhouse grower AppHarvest also clearly raised awareness! Other high-profile and expanding greenhouse growers, including BrightFarms and Gotham Greens, have also attracted large investments.
The question is often asked, “which is the better growing approach, sunless or greenhouse?”. There is no proverbial “silver bullet” for indoor farming. The answer is dictated by location and the problem you are trying to solve. A solution for the urban centers of Singapore, Hong Kong and Mumbai might not be the same as one deployed on the outskirts of Chicago.
Regardless of approach, starting any type of sizable tech-enabled indoor farm is capital intensive. A recent analysis from Agritecture indicates that it can range from $5 to $11 million dollars to build out a three-acre automated farm. Some of the huge, advanced greenhouse projects being built today can exceed $100 million. Given the capital requirements for these indoor farms, some question the opportunity for venture-level returns in the sector and suggest that it is better suited to investors in real assets. Still, more than $600 million was raised by the top 10 financings in 2020 as existing players vie for leadership and expand to underserved locales while a seemingly endless stream of new companies continue to enter the market.
Looking forward, indoor farming needs to address its energy and labor challenges. In particular, the sunless approach has work to do to bring its operating costs in line and achieve widespread profitability. Additionally, to further accelerate growth and the adoption of new technologies in both greenhouse and sunless environments, the sector needs to implement the sharing of data between systems. Waybeyond is one of the companies promoting open systems and APIs to achieve this goal.
As we stated in the beginning of this piece, the indoor ag value chain reflects some of the challenges and opportunities confronting our entire food system today: supply chain, safety, sustainability, and labor. Indoor agriculture has tremendous opportunity. While it is still early for this market sector overall, it can bring more precision and agility to where and how food is grown and distributed.
US: NORTH CAROLINA: CraftGrown Farms Offers Fresh Microgreens, Lettuce And Herbs
All of the growing is done inside, allowing CraftGrown Farms to produce year-round and the ability to expand its growing capacity
BY JESSICA MAURER
March 10, 2021
CraftGrown Farms involves a hydroponic farm on Castle Street. (Photo courtesy of CraftGrown Farms)
Randall Rhyne’s career has included teaching high school biology and earth science as well as serving in the Army Reserve, with deployments to Iraq and Syria.
After visiting Wilmington last year, he fell in love with the city and decided to relocate from Virginia.
While serving overseas, Rhyne and his unit often had little to no access to fresh food, relying on MREs or snacks like Pop-Tarts. He often longed for fresh produce.
One spring when he was in the Syrian desert, he saw trucks hauling locally grown produce and found himself thinking that if the locals were able to grow their own food in the middle of a civil war, in a desert, there was no reason why he couldn’t do this at home. As soon as he returned to Virginia, Rhyne got to work.
Now, having secured a Castle Street storefront and growing space across from Luna Café on Castle Street last fall, Rhyne has created CraftGrown Farms, an indoor, hydroponic farm selling nutrient-dense microgreens, hydroponic lettuce, and herbs to local restaurants and the public.
All of the growing is done inside, allowing CraftGrown Farms to produce year-round and the ability to expand its growing capacity.
Rhyne said the response so far has been remarkable; in fact, he’s already outgrown his initial vertical grow system.
“It’s a great problem to have,” Rhyne said.
He said new customers are usually so excited about what they’ve tried that they want to take home more than they need.
“I’m an old school believer in the quality of the sale and even though these items have a good shelf life, I try to discourage people from buying too much at once,” Rhyne said.
CraftGrown Farms only harvests what it sells, so the produce is picked right in front of the customer, providing maximum flavor and freshness.
There are currently about a dozen microgreen blends available, as well as leafy greens such as kale, arugula, and tatsoi. The microgreens will keep in a vegetable crisper for two weeks, and all of the lettuce is sold with the root ball intact to preserve flavor and freshness.
“These are not your everyday lettuces,” Rhyne said.
CraftGrown Farms is located at 603 Castle St. and is open from noon to 6 p.m. Monday through Friday and 10 a.m. to 4 p.m. on Saturday.
Have a tip for Restaurant Roundup? Email us at: restaurant@wilmingtonbiz.com.
Vertical Farms vs Greenhouses – The First Consideration: Location
When and where to use a vertical farm versus a greenhouse, and what factors – both economic and environmental – make the difference.
In just the past decade or so, sustainable farming has seen a high-tech makeover in the form of Controlled Environment Agriculture, or CEA, which consists of two main technologies: Vertical farms and greenhouses.
When it comes to feeding the world, it’s not a choice between vertical farms or greenhouses. We’ll need both to feed our growing global population with healthy, sustainable food, and we need to understand the ideal situation for each.
But as a business decision, it often is a choice between the two – and that’s what we hope to explain in this five-part series of articles: When and where to use a vertical farm versus a greenhouse, and what factors – both economic and environmental – make the difference.
In this first post, we’ll cover the basic differences between vertical farms and greenhouses, and why location matters so much when deciding between the two. Then stay tuned because, in the next articles, we’ll dive deeper into energy and lighting costs, automation and other expenses, environmental and crop considerations, and finally, the future of farming.
Vertical Farms vs Greenhouses: The Basics
The two technologies are often confused, but there are significant differences between them in resource use, cost, output, and, perhaps most importantly, the ideal locations for each.
Greenhouses are the more traditional technology that you’re probably familiar with: A single layer of crops, planted inside an enclosed space with walls and a ceiling made of glass or plastic to allow natural light in. They’re semi-controlled environments.
Vertical farms, on the other hand, are a much more recent invention using trays of usually hydroponic plants, stacked in floor-to-ceiling towers, with LED lights illuminating each layer, and climate control constantly adjusting the temperature, humidity and more.
In the upcoming articles in this series, we’ll dive into each part of these differences in more detail. But for now, let’s start with the first question entrepreneurs always need answering: The price tag.
Henry Gordon-Smith is the CEO of Agritecture, an independent consultancy and software creator that helps clients decide between the two technologies. As he puts it, “Vertical farming represents the most expensive, most controlled form of agriculture.”
At first blush, vertical farms are, in fact, shockingly more expensive than greenhouses – six to 10 times as costly. Gordon-Smith says vertical farming costs 2,200 to 2,600 Euro per square meter of cultivation bed space, while high-tech greenhouses cost 250 to 350 Euro per square meter of cultivation space.
Both offer a year-round source of fresh, pesticide-free, locally-grown produce, which provides better nutrition than the same foods that arrive from far away.
But what else do farmers, entrepreneurs, and investors get for all the added expense of vertical farming?
The answer is pretty simple: A more compact farm with more production per square meter, less water use, and more control over both quantity and quality. (With iFarm, this predictability is part of the package, in the form of a guaranteed yield within a precise time frame.)
For some entrepreneurs or municipalities, the cachet of implementing a high-tech farming technique that’s only been in use for less than a decade is also a factor in favour of vertical farming. But most often, the choice comes down to location.
The Ideal Location for a Vertical Farm versus a Greenhouse
The first step in determining the feasibility of building a vertical farm or greenhouse is to look at the drivers and constraints – many of which are simply location-based.
Places with limited space, such as dense urban areas, and limited access to fresh water are ideal for vertical farms. Doubly so if they have access to low-cost, renewable energy, and if they’re near a market with high demand for the crops vertical farms excel at producing: Leafy-greens, micro-greens, herbs and berries grown locally, without pesticides.
But in areas with unlimited space, lots of natural sunlight, and high-cost and/or high-carbon electricity, greenhouses may be the better option and the extra expenses of vertical farming might not make sense.
How these considerations apply in broad regions of the world is illustrated below:
GoodLeaf Farms Launches Aggressive Expansion Plans
GoodLeaf will bring its innovative and proprietary controlled-environment agriculture technology to more Canadian markets over the coming year
NEWS PROVIDED BY
McCain invests in a national network of vertical farms to bring tasty, local food to Canadians
GUELPH, ON, - With the closure of a successful new funding round, GoodLeaf Farms is embarking on an aggressive growth and expansion plan to build a national network of vertical farms that will bring fresh, delicious, nutritious and locally grown leafy greens to Canadians across the country.
Backed by a sizeable investment from McCain Foods Limited — which has increased its total investment in GoodLeaf to more than $65 million — GoodLeaf will bring its innovative and proprietary controlled-environment agriculture technology to more Canadian markets over the coming year, providing more Canadian consumers with year-round local food that is typically imported from the Southern United States or Mexico.
"From our start in Truro to our first commercial farm in Guelph, GoodLeaf has built a strong foundation for future growth," says Barry Murchie, Chief Executive Officer of GoodLeaf. "We want to be a global leader in vertical farming. Our first step to accomplishing that is ensuring we have a strong footprint in Canada, giving Canadians access to top quality, nutrient-dense, sustainably grown and pesticide-free leafy greens 365 days a year."
GoodLeaf opened its first commercial vertical farm in Guelph, Ont., in the fall of 2019. By the end of 2021, GoodLeaf is planning two more indoor vertical farms — one to serve the grocery and foodservice networks in Eastern Canada, and one for Western Canada.
The exact locations will be announced shortly.
"It is our intention to build farms that support the Canadian grocery store network, foodservice industry and consumers," says Mr Murchie. "We want to change what people are eating by providing a fresh, healthy and local alternative that, until now, hasn't been available in Canada. We are driving a new way to grow food, with disruptive technology that brings consumers leafy greens from their own backyard. This is a fundamental game-changer."
GoodLeaf's vertical farm grows to produce on hydroponic trays stacked in multiple horizontal levels. A proprietary system of specialized LED lights is engineered to emulate the spring sun, giving plants the light they crave to maximize photosynthesis. The indoor controlled environment is almost clinical, meaning there are no pesticides, herbicides or fungicides used. It is also immune to weather extremes, such as summer droughts or late spring frosts that can be lethal to crops.
Furthermore, having a local source of year-round food is vital to Canada's food security and sovereignty, concerns that were in the spotlight at the height of the COVID-19 pandemic as shoppers were faced with rapidly dwindling supplies on grocery store shelves.
At its 45,000-square-foot Guelph farm, every day GoodLeaf is harvesting microgreens (Spicy Mustard Medley, Asian Blend, Micro Arugula, Micro Radish and Pea Shoots) and baby greens (Ontario Baby Kale, Ontario Baby Arugula and Ontario Spring Mix) for Ontario grocery stores, ensuring a local supply of fresh, nutrient-dense leafy greens all year long.
GoodLeaf produce is exceptional in a salad, as a topping for burgers and sandwiches, as a kick of nutrients in a smoothie or as an ingredient to elevate your favourite dish.
Follow GoodLeaf Farms on Instagram @goodleaffarms and Like it on Facebook at /GoodLeafFarms.
About GoodLeaf Farms:
With a passion for delicious, nutrient-rich greens, GoodLeaf was founded in Truro, NS, in 2011. Using innovative technology and leveraging multi-level vertical farming, GoodLeaf has created a controlled and efficient indoor farm that can grow fresh produce anywhere in the world, 365 days of the year. The system combines innovations in LED lighting with leading-edge hydroponic techniques to produce sustainable, safe, pesticide-free, nutrient-dense leafy greens. GoodLeaf has ongoing R&D Programs in collaboration with the University of Guelph, Dalhousie University and Acadia University.
Learn more at goodleaffarms.com.
About McCain Foods (Canada)
McCain Foods (Canada) is the Canadian division of McCain Foods Limited, an international leader in the frozen food industry. McCain Foods is the world's largest manufacturer of frozen potato specialities, and also produces other quality products such as appetizers, vegetables and desserts that can be found in restaurants and retail stores in more than 160 countries around the world. In Canada, the company has eight production facilities with approximately 2,400 employees and, in addition to its famous French fries and potato specialities, makes frozen desserts, snacks and appetizers.
SOURCE GoodLeaf Farms
For further information: Michelle Hann, Senior Consultant, Digital and Communications, Enterprise Canada, mhann@enterprisecanada.com, 613-716-2118
Introducing Vertical Farming To Mexico And Beyond
Above all else, Karma Verde Fresh is a social enterprise whose purpose, according to Tagino, “is to transform the lives of individuals and communities through the creation of accessible food options, that have positive economic and sustainable impacts on the environment.”
Karma Verde Fresh (KVF) is a vertical farm based in Monterrey, Nuevo León (northeastern Mexico), producing a variety of seedlings, leafy greens, strawberries, and beans, and manufacturing its own cultivation systems which can be installed in any urban environment to promote local agriculture.
First established in 2016 by Leo Lobato and Rafael Cuellar, Karma Verde Fresh sought to master vertical agriculture before developing its own system and initially purchased four vertical racks systems from a Dutch company. The company quickly realized that for vertical farming to be successful in Mexico and other developing countries, the technology needs to be both efficient and financially accessible so that any sized growers can participate in the development of their own urban, peri-urban or rural farms.
(F.l.t.r.) Leo Lobato and Rafael Cuellar, co-founders of KVF
According to Tagino, the company’s communications and social media manager, high capital and operating costs are the main barriers to vertical farming.
Technique available to anyone
This has led the company to develop its own technology within Mexico and make it as accessible as possible, all with the goal of providing as many communities with nutritious produce. Today, KVF has increased its cultivation grow racks by more than 89% in the same footprint and their solar LED lights use 21% less energy.
“We know that there are super sophisticated farms across the world, with high automation. That is one way, but in order to impact communities that are left behind, are looking for job opportunities, vertical farming needs to be affordable,” says Tagino.
Once Karma Verde Fresh successfully developed its own cultivation system, the company developed a digital strategy to reach its potential and future customers through various social media platforms which include Facebook, Instagram, and Twitter.
Pushing R&D
Aside from its strong social media presence to attract young customers and entrepreneurs, Karma Verde Fresh also strongly emphasizes the importance for scientific research in the vertical farming industry, publishing their first scientific research report in Cyprus at an international sustainable agriculture conference in March in conjunction with Dr. Gilda Carrasco of the University of Talca.
KVF's salad mix
“Back in 2018, we learned that vertical agriculture really needs the scientific research community to be on board because they can give us the best science for improving growing conditions. In 2019, we started our first laboratories at two UANL campuses (Universidad Autónoma de Nuevo León) and the UAAAN in Coahuila, and in 2021-2023, we’ll be installing cultivation systems at different universities across Mexico, Central America, and as far away as Chile,” says Leo.
By installing cultivation systems at numerous universities, Karma Verde Fresh hopes to attract youth to vertical farming and to develop businesses in the regions where the systems are being established. The company is also immersing itself in the academic world by collaborating on research projects and participating with NCERA-101, a research committee focused on exchanging information about technologies in controlled environment agriculture (CEA).
Expansion plans
Through these research collaborations, the company is creating models that it can replicate across Mexico. Thanks to the American Chamber Mexico, the company met Ken Moskal, now an angel investor and a new corporate structure will allow Karma Verde Fresh to transition out of its start-up phase. While the company hopes to attract investment fund managers, Leo also explained that Karma Verde Fresh is taking its time to grow organically, invest its own money and only bring in outside investments if needed.
Karma Verde Fresh plans to fund its growth mostly through sales of seedlings, produce to restaurants and selling the KVF systems through the national distribution network developed through Mexico’s Industrial Chamber CANACINTRA’s Ag Sector.
Above all else, Karma Verde Fresh is a social enterprise whose purpose, according to Tagino, “is to transform the lives of individuals and communities through the creation of accessible food options, that have positive economic and sustainable impacts on the environment.”
Their purpose garnered the attention of the Inter-American Institute for Cooperation in Agriculture (IICA). The organization asked Karma Verde Fresh to join an alliance, which was signed in 2020 and will work to build cultivation systems in food banks in the country’s most food-insecure regions, as well as the first Vertical Agriculture Tech and Trainer Certification Program in Mexico City.
Sustainable systems
Another interesting initiative of Karma Verde Fresh is its solution called the Rolling Thunder Service. By developing 40-day forecasts over Mexico, the company will be able to better forecast severe meteorological events and begin producing seedlings in its racking systems ahead of such events. When severe storms damage agricultural crops, the company will be able to provide to healthy seedlings to help farmers recover quickly.
The company is guided by three core values: consciousness, innovation and collaboration. With respect to innovation, Tagino explained that it isn’t simply about buying innovation but about actually innovating in the countries seeking to build sustainable agricultural systems. That is ultimately why the company decided to develop its own vertical racks and LEDs. The company’s commitment to collaboration is evidenced by its numerous university partners and research projects.
“Not only are our processes enriched by the different perspectives and knowledge, but it generates a bigger impact among the communities and ecosystems where the collaborations occur,” says Tagino.
For more information:
Karma Verde Fresh
Blvd. Díaz Ordaz #130,
Col. Santa María, Piso 10, Torre 3,
64650, Monterrey, Nuevo León, México
+52 (81) 8851-8261
Leo Lobato, Co-Founder
leo@karmaverdefresh.com
Tagino Lobato, Communication Manager
tagino@karmaverdefresh.com
www.karmaverdefresh.com
Publication date: Thu 25 Feb 2021
Author: Rebekka Boekhout
© VerticalFarmDaily.com
Agritech: Precision Farming With AI, IoT and 5G
For a company that grows and delivers vegetables, Boomgrow Productions Sdn Bhd’s office is nothing like a farm, or even a vertical farm. Where farms are bedecked with wheelbarrows, spades and hoes, Boomgrow’s floor plan is akin to a co-working space with a communal island table, several cubicles, comfortable armchairs, a cosy hanging rattan chair and a glass-walled conference room in the middle
Image from: Photo by Mohd Izwan Mohd Nazam/The Edge
For a company that grows and delivers vegetables, Boomgrow Productions Sdn Bhd’s office is nothing like a farm, or even a vertical farm.
Where farms are bedecked with wheelbarrows, spades and hoes, Boomgrow’s floor plan is akin to a co-working space with a communal island table, several cubicles, comfortable armchairs, a cosy hanging rattan chair and a glass-walled conference room in the middle.
At a corner, propped up along a walkway leading to a rectangular chamber fitted with grow lights, are rows of support stilts with hydroponic planters developed in-house and an agricultural technologist perched on a chair, perusing data. “This is where some of the R&D work happens,” says Jay Dasen, co-founder of the agritech start-up.
But there is a larger farm where most of the work behind this high-tech initiative is executed. Located a stone’s throw from the city centre in Ampang is a 40ft repurposed shipping container outfitted with perception technologies and artificial intelligence (AI) capabilities that mimic the ideal environment to produce more than 50,000kg of vegetables a year.
Stacked in vertical layers, Boomgrow’s vegetables are grown under artificial lights with Internet of Things (IoT) sensors to detect everything from leaf discolouration to nitrate composition. This is coupled with AI and machine learning algorithms.
Boomgrow is the country’s first 5G-connected vertical farm. With the low latency and larger bandwidth technology, the start-up is able to monitor production in real time as well as maintain key parameters, such as temperature and humidity, to ensure optimal growth conditions.
When Jay and her co-founders, K Muralidesan and Shan Palani, embarked on this initiative six years ago, Boomgrow was nowhere near what it is today.
The three founders got together hoping to do their part in building a more sustainable future. “I’ve spent years advising small and large companies on sustainability, environmental and social governance disclosures. I even embarked on a doctorate in sustainability disclosure and governance,” says Jay.
“But I felt a deep sense of disconnect because while I saw companies evolving in terms of policies, processes and procedures towards sustainability, the people in those organisations were not transforming. Sustainability is almost like this white noise in the background. We know it’s important and we know it needs to be done, but we don’t really know how to integrate it into our lives.
“That disconnect really troubled me. When we started Boomgrow, it wasn’t a linear journey. Boomgrow is something that came out of meaningful conversations and many years of research.”
Shan, on the other hand, was an architect who developed a taste for sustainable designs when he was designing modular structures with minimal impact on their surroundings between regular projects. “It was great doing that kind of work. But I was getting very dissatisfied because the projects were customer-driven, which meant I would end up having debates about trivial stuff such as the colour of wall tiles,” he says.
As for Murali, the impetus to start Boomgrow came from having lived overseas — while working in capital markets and financial services — where quality and nutritious produce was easily available.
Ultimately, they concluded that the best way to work towards their shared sustainability goals was to address the imminent problem of food shortage.
“By 2050, the world’s population is expected to grow to 9.7 billion people, two-thirds of whom will be in Asia-Pacific. Feeding all those people will definitely be a huge challenge,” says Jay.
“The current agricultural practice is not built for resilience, but efficiency. So, when you think of farming, you think of vast tracts of land located far away from where you live or shop.
“The only way we could reimagine or rethink that was to make sure the food is located closer to consumers, with a hyperlocal strategy that is traceable and transparent, and also free of pesticides.”
Having little experience in growing anything, it took them a while to figure out the best mechanism to achieve their goal. “After we started working on prototypes, we realised that the tropics are not designed for certain types of farming,” says Jay.
“And then, there is the problem of harmful chemicals and pesticides everywhere, which has become a necessity for farmers to protect their crops because of the unpredictable climate. We went through many iterations … when we started, we used to farm in little boxes, but that didn’t quite work out.”
They explored different methodologies, from hydroponics to aquaponics, and even started growing outdoors. But they lost a lot of crops when a heat wave struck.
That was when they started exploring more effective ways to farm. “How can we protect the farm from terrible torrential rains, plant 365 days a year and keep prices affordable? It took us five years to answer these questions,” says Jay.
Even though farmers all over the world currently produce more than enough food to feed everyone, 820 million people — roughly 11% of the global population — did not have enough to eat in 2018, according to the World Health Organization. Concurrently, food safety and quality concerns are rising, with more consumers opting for organically produced food as well as safe foods, out of fear of harmful synthetic fertilisers, pesticides, herbicides and fungicides.
According to ResearchAndMarkets.com, consumer demand for global organic fruit and vegetables was valued at US$19.16 billion in 2019 and is anticipated to expand at a compound annual growth rate (CAGR) of 6.5% by 2026.
Meanwhile, the precision farming market was estimated to be US$7 billion in 2020 and is projected to reach US$12.8 billion by 2025, at a CAGR of 12.7% between 2020 and 2025, states MarketsandMarkets Research Pte Ltd.
Malaysia currently imports RM1 billion worth of leafy vegetables from countries such as Australia, China and Japan. Sourcing good and safe food from local suppliers not only benefits the country from a food security standpoint but also improves Malaysia’s competitive advantage, says Jay.
Unlike organic farming — which is still a soil-based method — tech-enabled precision farming has the advantage of catering for increasing demand and optimum crop production with the limited resources available. Moreover, changing weather patterns due to global warming encourage the adoption of advanced farming technologies to enhance farm productivity and crop yield.
Boomgrow’s model does not require the acres of land that traditional farms need, Jay emphasises. With indoor farms, the company promises a year-round harvest, undisturbed by climate and which uses 95% less water, land and fuel to operate.
Traditional farming is back-breaking labour. But with precision technology, farmers can spend less time on the farm and more on doing other things to develop their business, she says.
Boomgrow has secured more than RM300,000 in funding via technology and innovation grants from SME Corporation Malaysia, PlaTCOM Ventures and Malaysia Digital Economy Corporation, and is on track to build the country’s largest indoor farms.
Image from: Boomgrow
The company got its chance to showcase the strength of its smart technology when Telekom Malaysia Bhd (TM) approached it to be a part of the telco’s Smart Agriculture cluster in Langkawi last October.
“5G makes it faster for us to process the multiple data streams that we need because we collect data for machine learning, and then AI helps us to make decisions faster,” Jay explains.
“We manage the farm using machines to study inputs like water and electricity and even measure humidity. All the farm’s produce is lab-tested and we can keep our promise that there are no pesticides, herbicides or any preserving chemicals. We follow the food safety standards set by the EU, where nitrate accumulation in plant tissues is a big issue.”
With TM’s 5G technology and Boomgrow’s patent-pending technology, the latter is able to grow vegetables like the staple Asian greens and highland crops such as butterhead and romaine lettuce as well as kale and mint. While the company is able to grow more than 30 varieties of leafy greens, it has decided to stick to a selection of crops that is most in demand to reduce waste, says Jay.
As it stands, shipping containers are the best fit for the company’s current endeavour as containerised modular farms are the simplest means of bringing better food to local communities. However, it is also developing a blueprint to house farms in buildings, she says.
Since the showcase, Boomgrow has started to supply its crops to various hotels in Langkawi. It rolled out its e-commerce platform last year after the Movement Control Order was imposed.
“On our website, we promise to deliver the greens within six hours of harvest. But actually, you could get them way earlier. We harvest the morning after the orders come in and the vegetables are delivered on the same day,” says Jay.
Being mindful of Boomgrow’s carbon footprint, orders are organised and scheduled according to consumers’ localities, she points out. “We don’t want our delivery partners zipping everywhere, so we stagger the orders based on where consumers live.
“For example, all deliveries to Petaling Jaya happen on Thursdays, but the vegetables are harvested that morning. They are not harvested a week before, three days before or the night before. This is what it means to be hyperlocal. We want to deliver produce at its freshest and most nutritious state.”
Plans to expand regionally are also underway, once Boomgrow’s fundraising exercise is complete, says Jay. “Most probably, this will only happen when the Covid-19 pandemic ends.”
To gain the knowledge they have today, the team had to “unlearn” everything they knew and take up new skills to figure what would work best for their business, says Jay. “All this wouldn’t have been possible if we had not experimented with smart cameras to monitor the condition of our produce,” she laughs.
Meet The Advisory Board - Indoor AgTech Innovation Summit, June 24-25
The virtual Indoor AgTech Innovation Summit on June 24-25 will explore how controlled environment agriculture and vertical farming can reach greater profitability and scale, both in the US and globally
The virtual Indoor AgTech Innovation Summit on June 24-25 will explore how controlled environment agriculture and vertical farming can reach greater profitability and scale, both in the US and globally.
Demand for fresh, local, nutritious and pesticide-free production has never been higher. But how can growers drive down energy consumption as they scale up to meet this demand? Which new crops can be optimized for an indoor environment? And how do we bridge the gap between producer and consumer?
We're putting together a powerful two days of interactive sessions and breakout discussion groups, steered by our valued Advisory Board of internationally recognized farm operators, food retailers, investors, seed companies, and technology providers.
MEET THE ADVISORY BOARD
More than 30 of the biggest names in the indoor agriculture and CEA community are helping to shape this June’s program:
SEE OUR ADVISORY BOARD
OUR EXPERTS SAY
"Indoor agriculture is booming as consumers continually demand the quality, variety and flavor that indoor-grown produce can bring. I look forward to the summit bringing together thoughtful content and expertise in the world of Indoor AgTech."
Liliana Esposito
Chief Communications Officer
WENDY'S, USA
"It's time for growers and the sales community to support the data and technology requirements throughout the supply chain that will enable complete product transparency and timely traceability. Data aggregation as in GS1 and technology such as QR codes on packaging have proven to be value-added for growers, distributors, and consumers."
Sean Walsh
North America Director of Fruits, Vegetables, and Dairy
GORDON FOOD SERVICE, USA
"Our capabilities are increasingly driven by AI, machine learning, internet of things, and blockchain, which all enable greater visibility and clarity on how to improve our products and services. We look to intentionally combine human and technological capabilities, so that our tech investments empower our employees and all our partners and customers along the supply chain."
Elyse Lipman
Chief Strategy Officer
LIPMAN FAMILY FARMS, USA
"I'm interested to see a significant dispersion of the food systems so quality produce becomes more affordable by removing all the friction between the producers and actual consumers. This will resolve a significant level of problems and issues we face such as food wastage, supply chain issues, food safety, and costs."
Jessica Naomi Fong
General Manager & Co-Founder
COMMON FARMS, HONG KONG
The program is coming together quickly, so if you’d like to be involved by showcasing your technology or sharing your experiences in a panel discussion, please get in touch with me now!
We look forward to hosting the indoor agtech community again in June.
Best wishes,
Oscar Brennecke
Conference Producer
Indoor AgTech Innovation Summit
oscar.brennecke@rethinkevents.com
+44 (0)1273 789989
SUMMIT PARTNERS
Platinum Partner:
HOSTED ALONGSIDE
Gold Partners:
Take A Virtual Tour of The New CEA Center
“What OHCEAC is unique about is that we are integrative, interdisciplinary, and inclusive team conducting collaborative research to respond to CEA stakeholder needs
18-02-2021 | Urban Ag News
US, Ohio- Dr. Chieri Kubota, the Director of the new center focusing on controlled environment agriculture and protected cultivation hosted this event to introduces the programs and membership at The Ohio State University.
“What OHCEAC is unique about is that we are integrative, interdisciplinary, and inclusive team conducting collaborative research to respond to CEA stakeholder needs. Our focus inclusively covers various production systems and crop types. We use the terminology of CEA as having a very broad meaning including soil-bassed or soilless systems under various types of climate control or modification structures.”
Source and Photo Courtesy of Urban Ag News
Vertical Farming ‘At a Crossroads’
Although growing crops all year round with Controlled Environment Agriculture (CEA) has been proposed as a method to localize food production and increase resilience against extreme climate events, the efficiency and limitations of this strategy need to be evaluated for each location
Building the right business model to balance resource usage with socio-economic conditions is crucial to capturing new markets, say speakers ahead of Agri-TechE event
Image from: Fruitnet
Although growing crops all year round with Controlled Environment Agriculture (CEA) has been proposed as a method to localize food production and increase resilience against extreme climate events, the efficiency and limitations of this strategy need to be evaluated for each location.
That is the conclusion of research by Luuk Graamans of Wageningen University & Research, a speaker at the upcoming Agri-TechE event on CEA, which takes place on 25 February.
His research shows that integration with urban energy infrastructure can make vertical farms more viable. Graamans’ research around the modelling of vertical farms shows that these systems are able to achieve higher resource use efficiencies, compared to more traditional food production, except when it comes to electricity.
Vertical farms, therefore, need to offer additional benefits to offset this increased energy use, Graamans said. One example his team has investigated is whether vertical farms could also provide heat.
“We investigated if vertical farms could provide not just food for people living in densely populated areas and also heat their homes using waste heat. We found that CEA can contribute to stabilizing the increasingly complex energy grid.”
Diversification
This balance between complex factors both within the growing environment and wider socio-economic conditions means that the rapidly growing CEA industry is beginning to diversify with different business models emerging.
Jack Farmer is CSO at vertical producer LettUs Grow, which recently launched its Drop & Grow growing units, offering a complete farming solution in a shipping container.
He believes everyone in the vertical farming space is going to hit a crossroads. “Vertical farming, with its focus on higher value and higher density crops, is effectively a subset of the broader horticultural sector,” he said.
"All the players in the vertical farming space are facing a choice – to scale vertically and try to capture as much value in that specific space, or to diversify and take their technology expertise broader.”
LettUs Grow is focussed on being the leading technology provider in containerised farming, and its smaller ‘Drop & Grow: 24’ container is mainly focussed on people entering the horticultural space.
Opportunities in retail
“This year is looking really exciting,” he said. “Supermarkets are investing to ensure a sustainable source of food production in the UK, which is what CEA provides. We’re also seeing a growth in ‘experiential’ food and retail and that’s also where we see our Drop & Grow container farm fitting in.”
Kate Hofman, CEO, GrowUp agrees. The company launched the UK’s first commercial-scale vertical farm in 2014.
“It will be really interesting to see how the foodservice world recovers after lockdown – the rough numbers are that supermarket trade was up at least 11 per cent in the last year – so retail still looks like a really good direction to go in.
“If we want to have an impact on the food system in the UK and change it for the better, we’re committed to partnering with those big retailers to help them deliver on their sustainability and values-driven goals.
“Our focus is very much as a salad grower that grows a fantastic product that everyone will want to buy. And we’re focussed on bringing down the cost of sustainable food, which means doing it at a big enough scale to gain the economies of production that are needed to be able to sell at everyday prices.”
Making the Numbers Add Up
The economics are an important part of the discussion. Recent investment in the sector has come from the Middle East, and other locations, where abundant solar power and scarce resources are driving interest in CEA. Graamans’ research has revealed a number of scenarios where CEA has a strong business case.
For the UK, CEA should be seen as a continuum from glasshouses to vertical farming, he believes. “Greenhouses can incorporate the technologies from vertical farms to increase climate control and to enhance their performance under specific climates."
It is this aspect that is grabbing the attention of conventional fresh produce growers in open field and covered crop production.
A Blended Approach
James Green, director of agriculture at G’s, thinks combining different growing methods is the way forward. “There’s a balance in all of these systems between energy costs for lighting, energy costs for cooling, costs of nutrient supply, and then transportation and the supply and demand. At the end of the day, sunshine is pretty cheap and it comes up every day.
“I think a blended approach, where you’re getting as much benefit as you can from nature but you’re supplementing it and controlling the growth conditions, is what we are aiming for, rather than the fully artificially lit ‘vertical farming’.”
Graamans, Farmer and Hofman will join a discussion with conventional vegetable producers, vertical farmers and technology providers at the Agri-TechE event ‘Controlled Environment Agriculture is growing up’ on 25 February 2021.
CGTN Conversations: Chinese Firms Add Strength To Dubai's Future Tech Ecosystem
CGTN Digital's International Editor Abhishek G. Bhaya spoke with Faisal Al Hawi, the head of Accelerator and Incubators at the Dubai Future Foundation, and Stuart Oda, the founder and CEO of Alesca Life.
Over the decades, the Gulf city of Dubai has emerged as a land of innovation and a place where the future could be felt right now in the present. The city is actively encouraging global collaborations to drive innovation and future technology in the United Arab Emirates and internationally through its Dubai Future Accelerators (DFA) initiative that was launched in 2016 under the aegis of Dubai Future Foundation.
In recent years, many Chinese tech firms and start-ups – which are known for their technological prowess – have partnered with DFA to contribute to their mission of imagining, designing and co-creating solutions for future challenges.
One such successful initiative has come from Beijing-headquartered Alesca Life, an agro-tech company that is creating next-generation urban farming solutions that consume five per cent water and 30 per cent energy vis-à-vis conventional farming.
To get an overview of DFA's future innovation agenda and how Chinese firms are contributing in making that vision a reality, CGTN Digital's International Editor Abhishek G. Bhaya spoke with Faisal Al Hawi, the head of Accelerator and Incubators at the Dubai Future Foundation, and Stuart Oda, the founder and CEO of Alesca Life.
Al Hawi is responsible for creating a myriad of programs that connect different stakeholders, government and private, with innovative startups and companies from around the world to experiment with and making Dubai the testbed for future ideas.
Oda is an investment banker-turned- urban farmer with a passion for innovation and sustainability. He founded Alesca Life in 2013 with an aim to make food production more localized and data-driven.
Edited excerpts:
Bhaya: Faisal, please tell us a bit about the vision of the DFA initiative and what it aims to achieve and also some of the main areas and technologies it has tasted success in the past four years?
Al Hawi: Dubai Future Accelerators is an initiative that was born four years ago under the Dubai Future Foundation. The vision was pretty much straightforward – to put Dubai as a leading city of the world when it comes to technology innovation. Our mission is to turn Dubai into a global testbed for innovations and technologies. The DFA looks around for all the start-ups in the global scene, trying to understand the technology needs, the partner needs, the local ecosystem needs, and trying to bridge the gap between these two players of the market.
We do this in what we call the Area 2071, which is like the heart of our ecosystem in Dubai and we've had tremendous success. Throughout the four years, we've run eight cohorts, the eighth cohort is ongoing as we speak. We've engaged with more than 300 start-ups and over 60 pilot projects were produced out of DFA and more than 150 memoranda of understanding or commercial agreements were signed with different government entities and private sector partners.
Dubai Future Accelerators is positioned in a way that basically bridges the gap between the big players, be it government or private sector, and the start-up innovators from around the world.
Bhaya: How many Chinese firms and start-ups have availed the DFA program so far? Please name some of the major projects the Chinese entities have undertaken in the UAE as part of the DFA initiative.
Al Hawi: We've worked with Chinese companies ever since Cohort 1 back in 2016. So, Alesca Life is one of them. Shellpay, which was a fintech company working with the General Directorate of Immigration in Dubai, was another company. There was another company called Future Trends, working with Dubai Health Authority on medical imaging, and utilizing the technologies of AI and machine learning to optimize the diagnosis of late-stage cancers.
Yitu Technology is another Chinese AI-based company which worked very closely with [UAE's largest telecom service provider] Etisalat on solving some of their telecom related issues. So these are just to name a few companies that worked with us.
We really understand the strength Chinese ecosystem brings to our ecosystem. And I think we complement each other in a lot of areas.
Another example, broader than just Dubai Future Accelerators, is within Area 2071, where SenseTime actually has an office here, and they work very closely with the AI office, in a couple of strategic projects.
So, the partnership is growing stronger and stronger, year after year. And we definitely believe that there are areas specifically in the fourth industrial revolution technologies, blockchain, AI and IoT and the likes that we will definitely materialize more and more outcomes and success moving forward.
Bhaya: Stuart, what is the story behind Alesca Life?
Oda: Seven years ago, I started Alesca Life here in Beijing. The vision of the company is to democratize access to fresh and nutritious food by democratizing the means and the knowledge of production.
And the more research that I was doing, it became very clear that one of the most pressing challenges over the next decades wasn't so much actually related to connectivity, as these things were becoming easier with the proliferation of smartphones and computers, but access to fresh and nutritious food. And so, my team and I wanted to find a way in which we can make this access a lot easier. And wherever it made sense to localize that fresh food production, and wherever food production currently existed to make it more data driven.
So we set on this journey seven years ago, and we currently have our teams and offices across Japan, China, and the United Arab Emirates and we have partnerships across many more countries. We're developing precision farming tools to accomplish, to increase the productivity, the profitability, and the predictability of food production by up to 10 times.
Bhaya: The urban farming technologies including vertical farms and data-driven food production are certainly relevant for an arid region like the Arabian Peninsula. How did your partnership with DFA come about and what has been the journey like in the UAE for Alesca Life?
Oda: In 2016, our team was selected into the DFA program as part of Cohort 1. It was actually our first entry into the Gulf region. We knew that the technology had huge promise and potential in the region, and we wanted to make a serious commitment to the region. The DFA program was kind enough to offer us a spot in Cohort 1.
It has been hugely transformational in two ways. You know, the way in which business is done in the Middle East is very different. And to be able to have an organization like DFA, both providing the meaningful introductions, reducing some of the barriers related to the company's formation, and then also just the credibility that is bestowed on some of the companies that get to go through the program. All three of these things contributed enormously to our success in the region.
Through this program we've also been able to find meaningful strategic partnerships to mitigate some of the challenges related to concentration of supply chain, for example, even being in a place like China, to have manufacturing bases and other places in other countries, is beneficial for us.
So, right after the DFA program, we had an opportunity to localize the manufacturing of our container farm in the Emirates of Ajman in the UAE, so that we can serve our customers and our base in the GCC (Gulf Cooperation Council) and also to showcase our commitment to the region that we're not just there to sell our systems, but that we are there for the long term.
Bhaya: The year 2020 has been a watershed in many ways for the world due to the COVID-19 pandemic, reinforcing our increasing reliance on digital and AI technologies without which we can't imagine a future. How did the global crisis impact the long-term vision of DFA?
Al Hawi: The pandemic has definitely affected everyone. At DFA, we realized that innovation is the way to be resilient for the future, prepared for the future and understanding exactly the problems of today that potentially, and unfortunately, led us into the pandemic. We had just a very short drop-in time in which everybody had to just realign ourselves, and that was around March. But we immediately resumed back in October.
Not just the DFA, I think all the government entities, as well as start-ups, realized how important a role they play in this ecosystem. And Cohort 8, that is currently ongoing and will last until the end of March, is specifically looking at challenges that will basically be more specific around life after COVID.
I'll share a couple of examples. The Dubai Roads and Transport Authority (RTA) is looking into new solutions of shared mobility. We are very much accustomed to the ride-hailing apps and public transport systems. But that has changed forever. So they (RTA) are really being proactive in trying to foresight what new models of public transport and shared mobility will be out there. And we're really excited to see what comes out as solutions in a couple of weeks' time.
Another entity which is really looking at how things might evolve in the health care sector is the Dubai Health Authority. They are focusing on preventive health care measures, solutions and products, but not only from a sense of being preventive or proactive but in a sense of also democratizing access to that device.
Bhaya: Food security is already a global concern and going to be a top challenge in the future. It did aggravate last year due to the supply-chain disruption caused by the pandemic. What are some of the innovative solutions that Alesca Life offers to meet this challenge and has COVID-19 triggered a sense of greater urgency?
Oda: This is a great point. Pre-pandemic, in 2018-19, a lot of the interest and investment from governments, companies and investors was in food tech, which was related to food delivery and meal kits at home. And it was really focused on one thing, which was consumer convenience. What has happened in 2020, with the pandemic and now that we're in 2021, is that the focus has shifted materially from food tech to agtech - agricultural technology, which is focused on resilience. It's about community resilience, as opposed to consumer convenience.
So, one of the solutions, the benefits or the outcomes of the pandemic, was a renewed interest in agtech. And by that, I mean, local food production is in control of your own supply chain for fresh and nutritious food. So, since the pandemic has happened, since the lockdowns have begun, I've probably spoken to individuals and government entities from over 30 countries that are interested in finding ways in which they can secure a minimum supply of local fresh food production in their own countries, in their own communities.
The shift has accelerated towards this localization, towards this decentralized form of food production that can happen almost anywhere. And one of the solutions that we're providing for this is to bundle all of our precision farming tools – our monitoring equipment, our automation systems, our farm management and software tools, and even our latest computer vision AI cameras – and bundle all these products together to create an incredibly capital efficient indoor farm. And this allows both governments, at large scale, and even community, at a smaller scale, to be able to be in control of their local food production needs.
Interviewer and script: Abhishek G Bhaya
Video editors: Meiyi Yan & Wu Chutian
Cover image: Du Chenxin
Infographics: Jia Jieqiong
Director: Mei Yan
Bringing The Future To life In Abu Dhabi
A cluster of shipping containers in a city centre is about the last place you’d expect to find salad growing. Yet for the past year, vertical farming startup Madar Farms has been using this site in Masdar City, Abu Dhabi, to grow leafy green vegetables using 95 per cent less water than traditional agriculture
Amid the deserts of Abu Dhabi, a new wave of entrepreneurs and innovators are sowing the seeds of a more sustainable future.
Image from: Wired
A cluster of shipping containers in a city centre is about the last place you’d expect to find salad growing. Yet for the past year, vertical farming startup Madar Farms has been using this site in Masdar City, Abu Dhabi, to grow leafy green vegetables using 95 per cent less water than traditional agriculture.
Madar Farms is one of a number of agtech startups benefitting from a package of incentives from the Abu Dhabi Investment Office (ADIO) aimed at spurring the development of innovative solutions for sustainable desert farming. The partnership is part of ADIO’s $545 million Innovation Programme dedicated to supporting companies in high-growth areas.
“Abu Dhabi is pressing ahead with our mission to ‘turn the desert green’,” explained H.E. Dr. Tariq Bin Hendi, Director General of ADIO, in November 2020. “We have created an environment where innovative ideas can flourish and the companies we partnered with earlier this year are already propelling the growth of Abu Dhabi’s 24,000 farms.”
The pandemic has made food supply a critical concern across the entire world, combined with the effects of population growth and climate change, which are stretching the capacity of less efficient traditional farming methods. Abu Dhabi’s pioneering efforts to drive agricultural innovation have been gathering pace and look set to produce cutting-edge solutions addressing food security challenges.
Beyond work supporting the application of novel agricultural technologies, Abu Dhabi is also investing in foundational research and development to tackle this growing problem.
In December, the emirate’s recently created Advanced Technology Research Council [ATRC], responsible for defining Abu Dhabi’s R&D strategy and establishing the emirate and the wider UAE as a desired home for advanced technology talent, announced a four-year competition with a $15 million prize for food security research. Launched through ATRC’s project management arm, ASPIRE, in partnership with the XPRIZE Foundation, the award will support the development of environmentally-friendly protein alternatives with the aim to "feed the next billion".
Image from: Madar Farms
Global Challenges, Local Solutions
Food security is far from the only global challenge on the emirate’s R&D menu. In November 2020, the ATRC announced the launch of the Technology Innovation Institute (TII), created to support applied research on the key priorities of quantum research, autonomous robotics, cryptography, advanced materials, digital security, directed energy and secure systems.
“The technologies under development at TII are not randomly selected,” explains the centre’s secretary general Faisal Al Bannai. “This research will complement fields that are of national importance. Quantum technologies and cryptography are crucial for protecting critical infrastructure, for example, while directed energy research has use-cases in healthcare. But beyond this, the technologies and research of TII will have global impact.”
Future research directions will be developed by the ATRC’s ASPIRE pillar, in collaboration with stakeholders from across a diverse range of industry sectors.
“ASPIRE defines the problem, sets milestones, and monitors the progress of the projects,” Al Bannai says. “It will also make impactful decisions related to the selection of research partners and the allocation of funding, to ensure that their R&D priorities align with Abu Dhabi and the UAE's broader development goals.”
Image from: Agritecture
Nurturing Next-Generation Talent
To address these challenges, ATRC’s first initiative is a talent development programme, NexTech, which has begun the recruitment of 125 local researchers, who will work across 31 projects in collaboration with 23 world-leading research centres.
Alongside universities and research institutes from across the US, the UK, Europe and South America, these partners include Abu Dhabi’s own Khalifa University, and Mohamed bin Zayed University of Artificial Intelligence, the world’s first graduate-level institute focused on artificial intelligence.
“Our aim is to up skill the researchers by allowing them to work across various disciplines in collaboration with world-renowned experts,” Al Bannai says.
Beyond academic collaborators, TII is also working with a number of industry partners, such as hyperloop technology company, Virgin Hyperloop. Such industry collaborations, Al Bannai points out, are essential to ensuring that TII research directly tackles relevant problems and has a smooth path to commercial impact in order to fuel job creation across the UAE.
“By engaging with top global talent, universities and research institutions and industry players, TII connects an intellectual community,” he says. “This reinforces Abu Dhabi and the UAE’s status as a global hub for innovation and contributes to the broader development of the knowledge-based economy.”
US - OHIO: Thinking And Growing Inside The Box
A brother-sister team has taken the mechanics of farming out of the field and into a freight container. “We are growing beautiful plants without the sun; there’s no soil, and so it’s all a closed-loop water system,” Britt Decker, co-owner of Fifth Season FARM, said
A brother-sister team has taken the mechanics of farming out of the field and into a freight container.
“We are growing beautiful plants without the sun; there’s no soil, and so it’s all a closed-loop water system,” Britt Decker, co-owner of Fifth Season FARM, said. “We use non-GMO seeds, completely free of herbicides and pesticides, so the product is really, really clean. In fact, we recommend people don’t even wash it, because there’s no reason to.”
Fifth Season FARM is unique in many ways; the 3-acre hydroponic farm is contained in a 320-square-foot freight container that sits along 120 S. Main St. in Piqua, with everything from varying varities of lettuce, to radishes, to kale and even flowers in a climate-controlled smart farm that allows Decker and his sister, Laura Jackson, to turn crops in a six- to eight-week cycle. The crops spend 18 hours in “daytime” every day, and the farm uses 90% less water than traditional farming.
“It’s tricky because we’re completely controlling the environment in here. It’s kind of a laboratory more than a farm,” Decker said. “I think there’s about 50 of them around the world right now. These are really international, and they’re perfect for places that are food deserts where they can’t grow food because of climate or other reasons. It gives them a way to grow food in the middle of nowhere.”
Image from: Sidney Daily News
Decker and Jackson, along with their brother Bill Decker, also do traditional farming and grow corn, wheat and soybeans, but Decker said they were looking for a new venture that would help lead them to a healthier lifestyle and learn something new.
“Just with the whole local food movement becoming more and more important and food traceability, we just thought it would be a great thing to bring to our community to help everyone have a healthier lifestyle,” Decker said. “People love food that’s grown right in their hometown and the shelf-life on it, when you get it home, is remarkable. It’ll keep for two weeks.”
Image from: AgFunder News
Currently, Decker and Jackson are growing a half-dozen variety of specialty lettuces that include arugula, butterhead and romaine, as well as specialty greens like kale and Swiss chard, and even radishes and flowers. They received their freight container at the end of July and set up their indoor farm over two weeks; while the farm has been in operation for less than six months, Decker says that they’re growing beautiful product.
They have also started growing micro-greens, said Decker. Micro-greens are immature plants which are 1 to 3 inches tall and are in a 5-inch by 5-inch container.
“People will use them as garnishments and in smoothies,” said Decker. “Since they are immature plants, they have an intense flavor.”
Decker said they are growing wheat germ, broccoli and spicy salad mixes.
They’ve also started moving forward with sales and marketing. Fifth Season FARM has partnered with the Miami County Locally Grown Virtual Market to sell their products to the community. They also take orders through their website, customers can opt to pick up their orders between 4 and 6 p.m. on Wednesdays, or Decker and Jackson will deliver products up to five miles from the farm. Decker said that Fifth Season FARM is also in discussions with three restaurants in the area about including their specialty greens on their menus.
Decker said they also plan to attend the Sidney Farmers Market when it opens for the spring/summer season.
“We’re really just getting going,” Decker said. “While we were learning to grow products, we didn’t want to overcommit to a restaurant or grocery store before we knew we could really grow beautiful product, so we’ve been donating product every week to the food pantry at the Presbyterian Church. It feels good to plant the seeds and watch them grow, and it feels good to make sure that people who aren’t getting the proper nutrition are getting some.”
Signify Adds Automatic Intensity Adjustment Plus Year-Long Recipe Modulations To Horticultural Controls
There’s something for both the greenhouse and the vertical farm in the GrowWise tweaks, which in some cases rely on tying to other systems’ sensors.
The Signify toplights at Belgium’s De Glastuin lettuce greenhouse automatically dim or brighten as daylight levels changes. (Photo credit: All images courtesy of Signify.)
Signify has enhanced the control system for its greenhouse LED lighting so that toplights can react immediately to changes in daylight conditions and adjust brightness accordingly. The company has also added year-long control settings intended to allow vertical farmers — but not greenhouses — to program seasonal variations in LED spectral content over a 365-day period.
Both upgrades are intended to reduce manual labor and improve overall cost efficiencies, Signify said.
Until now, greenhouse farmers could dim or brighten their Signify toplights by instructing the lights to do so via the control system, called GrowWise. Signify has now modified GrowWise software so that it can take readings from daylight sensors that are part of separate systems. GrowWise then instantly and automatically adjusts artificial light intensity emitted by the toplights, called Philips GreenPower LED.
“The lighting can be used much more efficiently since it gives us the flexibility to reduce light levels at any moment we need to,” said Wouter de Bruyn, the owner of Belgian lettuce grower De Glastuin, an early user of the new automatic feature.
Whereas Signify is known in office settings to build sensors into its smart luminaires, the GrowWise controls make use of sensors that are part of climate control systems and greenhouse management systems from companies such as Priva, Hoogendern Growth Management, and Ridder, all based in Holland.
Planet Farms’ Luca Travaglini backs up Signify’s point that prescribing a year of spectral content improves efficiency and helps keep down manual labor costs in controlled environment agriculture (CEA) operations such as vertical farms.
“The climate computer is equipped with a daylight sensor that sends actual light measurements to the GrowWise Control System so we can adapt our light levels automatically to ensure an even light level throughout the day and season,” de Bruyn said at De Glastuin, based in Kontich.
“Dynamic lighting in a greenhouse is the next step in improving the cost efficiency and quality for the cultivation process,” said Udo van Slooten, business leader, horticulture LED solutions at Signify. “It allows growers to effortlessly maintain a consistent level of light throughout the day to produce the best possible crops. The system compensates for cloudy weather and creates a more controlled growing environment for your crop.”
In another upgrade to GrowWise, vertical farmers who want to prescribe modulations in spectral content are no longer limited to 24 hours of looped recipe cycles. Rather, they can order up a year’s worth of shifts for controlled environment agriculture (CEA) operations.
The year-long programming feature is aimed at vertical farmers rather than at greenhouses because the lights that Signify provides for vertical farms support controllable spectral changes, whereas the greenhouse toplights do not. Signify refers to its GreenPower LED vertical farm lights as “production modules” rather than as “toplights.” Toplights and production modules can both be programmed for intensity over a year, but the intention of the year-long feature is oriented toward spectral content.
Compared to greenhouses, vertical farms tend to make much less, if any, use of natural light. In vertical farms, the lights are mounted much closer to the crop in stacked shelves.
One of the first users of the year-round feature is Italy’s greens and lettuce grower Planet Farms.
“Now we can easily create custom light recipes and set them to run year-round to provide the right light recipe with the right light intensity at the right time throughout the crop’s growth cycle,” said Planet Farms co-founder Luca Travaglini. “By automating our full light strategy during the growth cycle, for the whole year, we can run our operations very efficiently and keep our manual labor costs low. That makes it easier for us to maintain consistent quality as we scale up our production.”
The horticultural market is a key growth sector for Signify, especially as it maps out a strategy to maintain profits in the pandemic economy, in which last week it reported a yearly rise amid rigorous cost controls that now include a small number of layoffs. CEO Eric Rondolat is targeting a big chunk of what he has quantified as a $2 billion general horticultural lighting market by 2023.
MARK HALPER is a contributing editor for LEDs Magazine, and an energy, technology, and business journalist (markhalper@aol.com).
Columbia Vertical Farm Uses Technology To Cut Plastic Pollution And Boost Sustainability
The new packaging comes at no extra cost to the customer and will be cheaper in the long-run for Vertical Roots
Vertical Roots is the largest hydroponic container farm in the country. They grow and package lettuce varieties and have recently implemented a packaging process that reduces plastic with a resealable film. TRACY GLANTZ TGLANTZ@THESTATE.COM
With the use of agricultural technology, Vertical Roots farm in West Columbia created a packaging system for its leafy greens that cut down the company’s plastic usage by 30% and extends the shelf life of the lettuce.
In 2015, high school friends Andrew Hare and Matt Daniels created the idea for Vertical Roots, now the largest hydroponic container farm in the country. Hare is the general manager of the company and Daniels acts as the chief horticulturist.
The first Vertical Roots opened in Charleston and expanded with its second farm site in West Columbia in 2019. Vertical Roots parent company, AmplifiedAg, manufactures the container farms and farm technology of which Vertical Roots operates.
The farms are part of a growing industry called controlled environmental agriculture (CEA) that uses technology to ramp up nutrient-rich food production year around.
Hydroponics helps the farm uses 98% less water than traditional farming, according to Hare. Their technology creates an indoor environment to grow lettuce on the East Coast. Most lettuce in the U.S. comes from California and Arizona, where temperatures do not fluctuate much throughout the year, travelling 2,000 miles from farm to table. Vertical Roots offers a solution for local lettuce.
“Our mission is to revolutionize the way communities grow, distribute and consume food,” said Hare. As populations grow, Hare said the ability to produce enough food is a global concern.
VERTICAL ROOTS AGRICULTURAL INNOVATION
As a company committed to sustainability, Vertical Roots had to address its plastic usage and the consumer demand for environmentally friendly products.
“I think everyone can agree that the amount of plastic that’s consumed and used globally is a bit of a problem,” said Hare.
If Vertical Roots were to completely opt-out of using plastics, as much as 40% of the lettuce would be damaged in transportation to the retailers, Hare said. So the company decided to still use plastic containers in order to cut out food waste, but it changed the amount and type of plastic used.
By replacing the conventional “clamshell” plastic lids that you see on a container of lettuce at the grocery store, Vertical Roots cut down more than 30% of plastic usage by creating a resealable film lid. The new packaging comes at no extra cost to the customer and will be cheaper in the long-run for Vertical Roots, according to Hare.
The farm also uses recycled plastic that can also be recycled again after use. Tiny perforations in the film lid of the packaging allow air to leave the lettuce container and extends the product’s freshness, making Vertical Roots lettuce last around 14 days on the shelf.
“We tested respiration and condensation with each lettuce variety, and ultimately found that we could extend the freshness and shelf life of our salad mixes even more,” said Hare.
Vertical Roots, at the S.C. Farmer’s Market, is the largest hydroponic container farm in the country. They grow and package lettuce varieties. Tracy Glantz TGLANTZ@THESTATE.COM
GROWTH IN THE AGRICULTURAL TECHNOLOGY INDUSTRY
In the first three quarters of 2020, a record $754 million of venture capital was invested in the vertical farming industry, according to PitchBook data. This was a 34% increase from the entire previous year, Bloomberg reported in a January article.
A 2019 report from Global Market Insights showed that the vertical farming market size, or the number of potential customers or unit sales, surpassed $3 billion in 2018 and said it, “will exhibit a massive compound annual growth rate (CAGR) of over 27% from 2019 to 2026.”
In vertical farms, crops are harvested on several vertical layers indoors, where farmers can grow year-round by controlling light, temperature, water and other factors, according to the U.S. Department of Agriculture.
Vertical agriculture is also seen as a growing industry because it “could help increase food production and expand agricultural operations as the world’s population is projected to exceed 9 billion by 2050,” according to the USDA.
However, some are skeptical about the future of vertical farming for several reasons. The farms use LED light bulbs to grow crops, which require a lot of energy and money to operate.
Also, the farms mostly produce greens, which are low in calories because they take less water and light. The new farming technology is marketed as a way to combat world hunger, but in poorer countries, low-calorie greens are not as beneficial, according to Bloomberg.
THE FUTURE OF VERTICAL ROOTS
Despite a tough year due to COVID-19, Vertical Roots will open two more indoor, container farms in Georgia and Florida in 2021.
The company lost revenue from foodservice customers like restaurants, schools and universities during the pandemic, said Hare.
Those food service customers accounted for about half of Vertical Roots’ business, Hare said. Grocery store business stayed steady and even grew during the pandemic. As schools and restaurants are slowly reopening, Vertical Roots is gaining business back.
The West Columbia farm location produces about $1.5 million pounds of produce per year, said Hare. Vertical Roots lettuce is in 1,200 different grocery stores in 11 states, including Lowes Foods stores, Publix, Harris Teeter and Whole Foods Market chains.
Hare said the company is constantly working on sustainable initiatives, including figuring out a way to reduce light energy consumption by 20-25%, thinking about compostable packaging systems and finding ways to use less water at the farms.
In the future, Vertical Roots hopes to offer a larger variety of produce. The team is experimenting with growing foods like tomatoes, cucumbers, peppers, herbs and mushrooms to see if they could be viable products.
At 25,000 square feet, the world's first indoor vertical farm is also one of the largest farms. Located 120 miles south of Seoul, South Korea, fruits and vegetables grow without soil, bathed in light from pink LEDs. BY META VIERS
1 of 3
Vertical Roots, at the S.C. Farmer’s Market, is the largest hydroponic container farm in the country. They grow and package lettuce varieties. TRACY GLANTZ TGLANTZ@THESTATE.COM
IPO Planned To Improve Revenues Indoors
Light Science Technologies has gained the funding from Intuitive Investments Group plc (IIG), ahead of going public on the London Stock Exchange in the next six months.
8-01-2021| Business Live
“We believe that there is no better time to be involved in both agritech and medtech." A company which makes technology to improve indoor crop yields has received a £1 million investment ahead of a planned IPO.
Light Science Technologies has gained the funding from Intuitive Investments Group plc (IIG), ahead of going public on the London Stock Exchange in the next six months.
The business, based on the Hilton Business Park, Derby, provides lighting and plant growing and monitoring technology for agriculture in partnership with university research teams.
Its agricultural tech can be used in three main indoor settings – vertical farming (where crops such as tomatoes are grown in vertically stacked layers), greenhouses and medicinal plants.
Its patent-pending, sustainable light unit combines interchangeable LEDs, power and technology to help reduce costs and generate maximum yields over 25 years.
Its real-time monitoring and control technology can also be used to link technicians, farmers, and facility managers with their crops to provide instant production data.
Management said that with better light quality and energy savings, its light, science and technology products increase cycles.
It also supplies technology to clients in the electronics, audio, automotive, AI technology and pest control sectors.
The move to become a publicly listed company follows significant investment in its team and operations over the past few years which, the business said, has “brought to market a fully updateable, bespoke and intelligent lighting solution that provides optimal yield”.
The company is also due to launch its own in-house growth and laboratory service in the spring, focusing on plant growth and performance to help farmers with their crops.
Chief executive Simon Deacon said: “We believe that there is no better time to be involved in both agritech and medtech as two rapidly expanding sectors which are going to be responsible for spearheading some of the most significant global developments over the coming decade and beyond.
“IIG’s investment is not just a reflection of its commitment to LSTH as a fast-growing business backed by almost 30 years’ expertise in light technology but also of its awareness of the importance in achieving a better, more sustainable approach to agricultural production as well as pioneering potential life-saving solutions in digital health innovation.”
Light Science Technologies is IIG’s first investment following its own successful IPO and admission to AIM in December, as it seeks to attract investors with its life sciences portfolio.
IIG chairman David Evans said: “LSTH has the key ingredients for success; it has an excellent management team, a deep knowledge of the light spectrum and the application of that knowledge to areas where substantial growth can be obtained.
“I am personally excited about the potential diagnostic applications in the digital health sector, such as non-invasive haemoglobin measurement, as well as the developments in vertical farming technology that will underpin the long-term growth of LSTH.”
The investment follows recent funding for Light Science Technologies from Innovate UK which will see it work over the next six months with Nottingham Trent University to develop a growing sensor and transmission node for vertical farms.
Photo: Light Science Technologies designs lighting, science and plant monitoring technology.
Source and Photo Courtesy of BusinessLive
“Sharing Technology Is The Only Way The Industry Will Grow”
Lack of this might lead to farmers being susceptible to misleading information, using ineffective technologies, which I’ve seen many people suffering from.
“There is a lack of know-how amongst farmers to apply those techniques in a successful way,” says Joe Swartz, Vice president and Lead horticulturalists at AmHydro. In every situation, according to Joe, from geography to the skill of the grower or climate control, all play into what types of technology should be used. This requires a lot of experience and knowledge. Lack of this might lead to farmers being susceptible to misleading information, using ineffective technologies, which I’ve seen many people suffering from.
Joe adds, “Watching many good growers that have been led down a bad path in the industry, while investing so much into technologies that are not really effective, really breaks my heart. While providers know that they aren’t effective in this particular situation. With many years of industry experience, Joe is well aware of the challenges that the industry faces these days. Within the aquaponics sector there is not one singular technology, just as in conventional farming, rather various unique technologies can be combined for different outcomes.
Lack of know-how
When asked about the kind of growers that Joe educates, he notes that there are two kinds of growers contacting him. “We have two types of growers: either growers facing challenges or new growers wanting equipment and knowledge. Both of those approaches are interesting and it’s great to be able to help them become successful. It is great to see our system helping companies to grow and develop and become a worldwide provider. Growers like that keep coming back to us. They are the ones that move the industry”.
Joe Swartz, Vice president
An essential part of being a vertical farmer, in Joe’s opinion, is having experience with working on the ground floor. Only this will teach you what it takes to manage the equipment, crops and technology. “The best growers have started in the greenhouse. Hydro-experts will get nowhere with their college degree alone,” Joe states. For that reason, AmHydro offers grower seminars and even possesses a commercial greenhouse where growers can work in order to gain experience. “Some growers don’t think that they need it as they rely on technology, but my experience is exactly the opposite.”
Fake promises
Joe observes similar trends as in the 1980s when certain technologies were promoted as ‘the farming of the future’. People talked about automatic farming, in which no farmer would be needed, new techniques and new lightings. All things we hear today were said back then. What happened afterward, according to Joe, was that some techniques turned out disappointing. Millions of dollars invested were lost, leading to the industry losing its credibility.
“As a result, investors only valid projects that already have a positive cash flow, as they have become more cautious. Some growers struggled to get funding, even though they had a viable business model. In a certain way, negative events have closed off some appetite for investments in CEA, which is a shame. It is a good investment in general, but every time we see a less than a reputable company or a technology that fails, it holds the industry back.”
Misconception
Related to that, Joe says that vertical farming still has to overcome a somewhat negative public image. “The traditional consumer, at least in the USA, have an image of farmers working on the land using sustainable methods. Now, being a conventional farmer using hydroponics I know that it is a sustainable and safe way to produce food, but there’s a public perception of automatization, as robotic food. Some people even call it “Frankenfood”. In my opinion, the more we can promote CEA as what it is, sustainable growing techniques, people will be more accepting and investors will invest more easily”.
Joe strongly senses that the vertical farming industry needs more skilled farmers and growers to meet the demand. “A lot of my work is actually training people. We want to help especially young people, new to the industry, by giving them skills, experience and knowledge. I have been blessed to have mentors when I was young and I try my best to pass that knowledge as this will help the industry along. That’s one of the reasons why we now see some consultancy firms who see economic opportunities. Sharing technology is the only way in which the industry will grow,” says Joe.
“Despite the diversity amongst growers that I meet in over 66 countries, all growers face similar problems. Funny tech flitches, pipes that break and spray water all over the greenhouse, or water pumps that break down. It doesn’t matter whether it’s a technologically advanced greenhouse or a small low-tech one. It kind of goes across the board,” says Joe laughing.
For more information:
AmHydro
Joe Swartz, Vice president and Lead horticulturalist
joe@amhydro.com
www.amhydro.com
Author: Rebekka Boekhout
© VerticalFarmDaily.com
"CEA Can Increase Its U.S. Market Share By 5x Over The Next 10 Years"
Investment in CEA has surpassed $2.0B across North America and Europe spurring new start-ups, innovation and corporate engagement across the supply chain
S2G Ventures rResearches
Controlled Environment Agriculture Market:
Investment in CEA has surpassed $2.0B across North America and Europe spurring new start-ups, innovation and corporate engagement across the supply chain. With increased demonstration of the viability of controlled growing, a newly launched report predicts that CEA will support more than 10% of US vegetable and herb production by 2025 leading to significant opportunities for growers over the next decade.
The new report, Growing Beyond the Hype: Controlled Environment Agriculture, launched by S2G Ventures reveals how innovation in the field of Controlled Environment Agriculture (CEA), including greenhouse and indoor farming, will lead to ripple effects across the food system and more sustainable methods of production. S2G Ventures is a multi-stage investment firm committed to advancing sustainable solutions in food and ag – its portfolio companies include Beyond Meat, sweetgreen, Lavva, Apeel Sciences and more. The report predicts the maturation of CEA will lead to differentiated, quality products, cost-competitive pricing and a more resilient, traceable and trustworthy supply chain. These new supply chains may represent a transition for the changing urban real estate landscape post-covid.
"Controlled farming has the potential to offer consumers and supply chain stakeholders resilient, sustainable, local, high-quality products," said Walter Robb, Executive-in Residence at S2G Ventures and former co-CEO of Whole Foods. "It is a growing part of our evolving food system and can work alongside outdoor production to mitigate climate risk and help solve systemic nutrition and food access challenges."
S2G Ventures expects that CEA will have far-reaching implications for the future of our food system in three key areas.
Local production and controlled environments will lead to a more resilient, traceable and trustworthy supply chain
Despite being a $1.2 trillion global industry, fresh produce faces significant supply and demand challenges resulting in a systemic lack of high-quality, affordable products reaching consumers. According to the Lancet, only 36% of the global population in 2015 had adequate availability of fruits and vegetables to meet the WHO age-specific minimum nutrition targets.
In the United States, for example, the fresh produce market is challenged by the limitations of outdoor production, including climate, field loss exposure, resource intensiveness, and limited ability to iterate or diversify, as well as geographic constraints resulting in products traveling 7-10 days on average from farm to consumer. As a result, the U.S. is reliant on other countries to meet demand with 53% of fresh fruit and 32% of fresh vegetables imported annually according to the FDA.
If just 13% of vegetables and herbs shift to local CEA production by 2025, the United States can add $2.3bn additional production capacity and reduce our need for fresh vegetable imports by 15%. Local production can save up to 9 Trillion food miles through shorter transportation routes minimizing shelf life time spent in transit and reducing the amount of food waste by retailers and consumers. Additionally, controlled environments improve food safety, traceability and consistency of production.
Technology and operations advancements drive improvements to CEA unit economics that can compete with or beat outdoor production.
In order to gain market share, CEA production must become cost competitive with outdoor production. High upfront capex costs of facilities and equipment as well as energy costs, labor and product inputs, have historically made costs of CEA growing prohibitive. But innovation of grow inputs, improved grow systems, and optimization of facility productivity are driving more cost-effective production. Those innovations combined with CEA's higher number of grow cycles, 10+ for Greenhouse and 20+ for Indoor, will enable CEA to achieve unit economics that are at cost parity with outdoor.
CEA will usher in the next wave of biodiversity, nutrient density, and flavor innovation providing retailers with differentiated, quality products.
According to the UN's Food and Agriculture Organization, about 75 percent of the world's food comes from just 5 animal species and 12 plants. Almost half of our plant-derived calories come from just three foods: wheat, corn and rice. Germplasm for these plants are bred for long storage time and disease resistance, at the expense of flavor, color, and nutritional value. The lack of biodiversity and nutritional value in our global diet restricts the value that plant molecules can play in human health.
Indoor Agriculture offers new grow formats, methods and technologies that promise to increase the quality, consistency and diversity of produce. Advancements in CEA-tailored seeds bred for traits such as flavor, color, nutrient density and ripening will expose consumers to new flavors and more varied products. Ultimately, indoor agriculture will support customized grow recipes as IP, branded produce, local production of hard to access specialty ingredients, spices and superfoods and eventually inputs for food as medicine.
"Controlled growing is a critical solution to address both the current supply challenges brought to light by COVID and the pressures on outdoor growing exacerbated by climate change," said Sanjeev Krishnan, S2G Ventures Managing Director and Chief Investment Officer. "We believe CEA can grow its US market share by five times over the next 10 years in response to these pressures and continued consumer demand for fresh produce."
The report
Growing Beyond the Hype: Controlled Environment Agriculture is based on S2G Ventures desktop research and interviews with over 20 industry experts including CEA growers, systems providers, policymakers, academic institutions, outdoor growers, ag input suppliers, philanthropists, and other investors. The report outlines the opportunity for CEA to resolve the current lack of high-quality, affordable produce driven by limitations in outdoor production and customer geography and outlines three areas indoor production must overcome to take significant market share including cost, product selection and productivity.
To read the full report, download at https://www.s2gventures.com/reports
3 Dec 2020
RII And ACEEE Awarded USDA Grant To Transform Controlled Environment Agriculture Toward Resource Conservation And Efficiency
“As an industry-leading indoor vertical farming company with two farms and over 126,000 sq. ft. of growing space which can produce over 500,000 lbs. of fresh food each year, Fifth Season is committed to this exciting project,” said Grant Vandenbussche, Chief Category Officer, Fifth Season
Washington, D.C. (November 9, 2020) – Resource Innovation Institute (RII) and the American Council for an Energy-Efficient Economy (ACEEE) will receive nearly $600,000 over three years from the Conservation Innovation Grants (CIG) program at the United States Department of Agriculture’s Natural Resources Conservation Service. The project was one of 24 projects selected for the 2020 program. RII and ACEEE will jointly implement the project through 2023.
Authorized by the 2002 Farm Bill, the CIG program helps develop the tools, technologies, and strategies to support next-generation conservation efforts on working lands and develop market-based solutions to resource challenges.
The awarded proposal, titled Data-Driven Market Transformation for Controlled Environment Agriculture, will characterize key performance indicators, baseline data, and facility-level benchmarking for controlled environmental agriculture facilities. The project will develop a comprehensive suite of data tools, coupled with a market intervention strategy to address barriers to energy conservation, adoption of energy-efficient technologies, access to energy use data, and best practices.
“We’ve been assessing energy and water use in the energy-intensive cannabis cultivation sector for years and have built a set of vetted tools and resources that will now be extended to the broader controlled environment agriculture marketplace,” said Derek Smith, Executive Director of Resource Innovation Institute. “We appreciate the support of the USDA as well as leading producers, supply chain actors, universities, utilities, governments, standards organizations, and other project partners.”
“Market transformation is a proven strategy for creating and sustaining energy efficiency improvements in energy-intensive market sectors,” said Jennifer Amann, ACEEE’s Buildings Program Director. “With USDA’s support, we’ll engage leading CEA market actors, utilities, and policymakers to demonstrate market transformation’s potential to drive resource efficiency in the fast-growing and innovative CEA market.”
“Agricultural innovation has long played a key role in Oregon’s rural economy, and has made countless contributions to our state for generations,” said Oregon’s U.S. Senator Jeff Merkley, who serves as the top Democrat on the Senate Appropriations subcommittee that funds the USDA. “I’m pleased that this funding will help Oregonians keep us at the cutting edge of the newest technology in sustainable agriculture, and I will continue to partner with our state’s researchers and farmers to make sure Oregon agriculture continues to thrive.”
“The world’s population is increasing, but available agricultural land is decreasing. Through science and innovation, we can help farmers improve the health of their operations and productivity on their lands while protecting the natural resources we all depend on,” said Natural Resources Conservation Service Acting Chief Kevin Norton. “The new systems, tools, and technologies being developed through CIG are helping us ensure the longevity of American agriculture.”
Additional support includes:
Fifth Season
“As an industry-leading indoor vertical farming company with two farms and over 126,000 sq. ft. of growing space which can produce over 500,000 lbs. of fresh food each year, Fifth Season is committed to this exciting project,” said Grant Vandenbussche, Chief Category Officer, Fifth Season. “We will benchmark the resource efficiency performance of our facilities, evaluate potential efficiency upgrades, and be featured in case studies demonstrating the financial and environmental results of our projects.”
Fluence by OSRAM
Fluence is a leading global provider of energy-efficient LED lighting solutions for commercial agriculture production. Fluence regularly contributes to RII’s cultivation guidance and serves as an industry-leading voice for RII on efficient energy consumption for LED lighting in CEA facilities. “We are increasingly observing global growers commit to more energy-efficient cultivation solutions at their facilities,” said Corinne Wilder, Vice President of Global Business Operations for Fluence. “This grant underscores the important work RII has already done for growers and we will enthusiastically recruit cultivators to engage with this project to not only help improve the efficiency of their own operations but those of the entire CEA industry.”
Grodan
“For more than 50 years, Grodan has developed Precision Growing methods proven to reduce water and nutrient use while maximizing crop quality and yield. Vertical farms and greenhouses are critical to the future of global food and medicine production as well as minimizing resource usage with technologies such as recirculation,” said Gonneke Gerkema, North American Business Director, Grodan. “This project collaboration brings together several key companies who share the same vision of industry benchmarking combined with Data-Driven decision making to generate water-use efficiencies that will benefit the cultivators, the industry, and indeed the environment.”
Northwest Power & Conservation Council
“Indoor agriculture is a significant part of the driving force behind forecast growing electric loads in agriculture,'' said Ben Kujala, Director of Power Planning, Northwest Power & Conservation Council. “The Council supports looking for opportunities for cost-effective energy efficiency and demand management within the growing indoor agriculture sector as part of its power planning and conservation responsibilities. As project advisor, Council staff commit to engage and educate stakeholders.”
For more information, go to ResourceInnovation.org/CEA. To schedule an interview with an RII representative, please contact Ellie Malone at ellie@themaverickpr.com or 262-337-3312.
About Resource Innovation Institute: Advancing Resource Efficiency to Cultivate a Better Agricultural Future
Resource Innovation Institute (RII) is a non-profit organization whose mission is to advance resource efficiency to cultivate a better agricultural future. Founded in 2016 to address the resource impacts of cannabis cultivation, RII is extending its services to other energy-intensive horticultural sectors. Its PowerScore benchmarking platform represents the world’s largest dataset on indoor agriculture energy use. RII’s Technical Advisory Council, which includes a Policy Working Group and a Utility Working Group, is the leading multi-disciplinary body assessing the environmental impacts and best practices associated with cultivation resource issues. RII’s Board of Directors includes the American Council for an Energy Efficient Economy (ACEEE) and a former board member of the US Green Building Council. RII is funded by utilities, foundations, governments and industry leaders. Visit our website at ResourceInnovation.org. Follow us on LinkedIn, Facebook, Twitter and Instagram.
# # #
CEA Startup AppHarvest To Go Public, Expects $475m Funding At $1bn Valuation
“We are about to plant our first crop in a 60-acre, controlled environment, chemical-free farm. No one else in America is doing something at that scale. Investors look at that,” Peter Spac, AppHarvest’s newly appointed chief financial officer, told AFN.
October 1, 2020
US controlled environment agriculture (CEA) startup AppHarvest has announced a merger with NASDAQ-listed special purpose acquisition company (SPAC) Novus Capital, enabling it to go public.
The deal is slated to bring in $475 million in gross proceeds for Kentucky-based AppHarvest, including a private investment in public equity (PIPE) transaction worth $375 million from existing and new investors including Fidelity Management & Research Company, Inclusive Capital, and Novus. This commitment, at $10 per share, values the company at $1 billion.
“I can’t say this was the exact plan but what accelerated all of this was Covid-19,” AppHarvest CEO Jonathan Webb told AFN. “Typically, you would do 40 to 60 meetings to get a couple of investors. We had 22 meetings and had almost 20 ‘yeses.’ Very few passed on this deal and we eventually had to cancel meetings.”
Webb describes the SPAC transaction and PIPE financing experience as “absolutely phenomenal.”
A SPAC is formed with the sole purpose of raising capital through an IPO in order to acquire an existing privately-held company and take it public. Also referred to as ‘blank check companies,’ the mechanism has existed for several years but has received increased attention of late. This year alone, more than 50 SPACs have been formed in the US, collectively raising around $36.2 billion as of last month.
Invest with Impact. Click here.
PIPE deals effectively allow institutional investors to buy larger quantities of public company stock, typically at a discount to public market prices.
“AppHarvest is a unique and compelling investment opportunity that is redefining American agriculture by improving access for all to fresh non-GMO produce, growing more with fewer resources, and creating an agtech hub from within Appalachia,” Novus chairman Bob Laikin said in a statement.
“With significant tailwinds from heightened investor focus on ESG initiatives and the secular shift to plant-based foods, we believe AppHarvest is well-positioned to execute on its strategy for rapid growth and value creation,” he continued.
AppHarvest — which raised $28 million in its Series C round in August — is launching what it describes as the world’s largest greenhouse later this year, consisting of a 2.76 million square foot facility in Morehead, Kentucky. The system it uses reportedly reduces water usage by 90% compared to traditional open-field agriculture, while also eliminating runoff.
Its first crop will be non-GMO tomatoes, which will be provided to a number of US grocers.
Other AppHarvest investors include TV cook Martha Stewart, VC veteran Peter Thiel, ValueAct Capital’s Spring Fund, Revolution’s Rise of the Rest Seed Fund, Equilibrium Capital, and Narya – the new VC firm co-founded by JD Vance, author of best-selling Appalachian memoir Hillbilly Elegy.
“We are about to plant our first crop in a 60-acre, controlled environment, chemical-free farm. No one else in America is doing something at that scale. Investors look at that,” Peter Spac, AppHarvest’s newly appointed chief financial officer, told AFN.
“We have a phenomenal growing team. We have a phenomenal team of sustainability experts. They’re looking at a company and even though its pre-revenue it has all the necessary ingredients to succeed.”
AppHarvest knows it’s far from being the only player in the CEA game. But it’s confident in its approach.
“We aren’t burning through cash with pointless R&D when we can buy incredible technologies over in the Netherlands,” Webb says.
“The other thing is scale. Part of it is that building big stuff fast in the US is very hard. You have to get permitting, communities’ [buy-in], state and federal support, infrastructure, inspections. What we’ve proven through a global pandemic is that we can build one of the largest facilities in the world on time, on budget, at a record pace.”
Moving forward, AppHarvest is focused on bringing its beefsteak and on-the-vine tomatoes to market. The first harvest at its Morehead facility is slated for early 2021. It hopes to expand into leafy greens, berries, cucumbers, and bell peppers in the future.