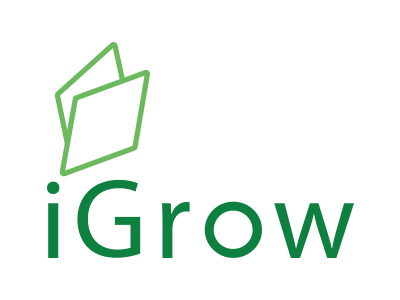
Welcome to iGrow News, Your Source for the World of Indoor Vertical Farming
Babylon Micro-Farms Establishes New Corporate Headquarters In Richmond, Virginia
The company has developed disruptive technology - a cloud-based platform that operates vertical farms through a mobile phone app that controls all aspects of farming at the touch of a button
Richmond, VA (February 2021) Babylon Micro-Farms has chosen Richmond, Virginia as the site for their corporate headquarters, opening a new office and R & D space in historic Scott’s Addition. The move from Charlottesville was driven by the company’s growth and need for a larger talent pool - they had been courted by California and Arizona as an up-and-coming tech company in the indoor ag-tech space.
The company has developed disruptive technology - a cloud-based platform that operates vertical farms through a mobile phone app that controls all aspects of farming at the touch of a button. The indoor ag-tech industry is projected to grow globally from USD $121.26 billion in 2019 to USD $167.42 billion by 2025, a compound annual growth rate of 5.4% according to the latest report released by Market Data Forecast last week.
Babylon’s CEO and Co-Founder, Alexander Olesen, commented on the move. “Richmond is the perfect launchpad for our next phase of growth. It has a dynamic business eco-system and gives Babylon the chance to build an even stronger foundation for the future with everything it has to offer.”
Babylon began hiring locally in Richmond prior to the move, scaling up their operations in preparation for the anticipated increase in sales in 2021. Graham Smith, CTO and Co-Founder of Babylon, said “Our growth has been based on significant R & D we were able to accomplish because of support from The Center for Innovative Technology, the National Science Foundation and investors that understood early on the potential for this technology. Richmond offers a hub where innovation and industry intersect and having our headquarters here will fuel our expansion.”
The company expects to triple its workforce in the next three years, adding jobs in every department, from assembly to engineering. For more information visit www.babylonmicrofarms.com or contact janet@babymicrofarms.com for interview requests.
Babylon Micro-Farms team, from left to right: Alexander Olesen, CEO and co-founder; Marc Oosterhuis, COO; and Graham Smith, CTO, and co-founder. Courtesy of Babylon Micro Farms
ABOUT BABYLON MICRO-FARMS
At the touch of a button, Babylon Micro-Farms delivers a simple, yet engaging indoor growing experience. Babylon helps senior living communities, hospitals, schools, and hospitality companies showcase their commitment to providing fresh, nutritious produce and sustainability to their residents, employees, and customers.
They have designed a complete on-site farming service that makes growing simple for anyone, thanks to their plug-and-play Micro-Farms and Guided Growing App. Babylon offers the most affordable, efficient, and advanced vertical farming platform available, remotely managed through the cloud with unparalleled customer service. Since their humble beginnings as a social entrepreneur student project, Babylon have attracted investors from Silicon Valley, been awarded a grant from the National Science Foundation to support their research, patented a groundbreaking technology, and received recognition by Virginia's Governor Northam for their contribution as a technology innovator following their successful application for funding from the Center for Innovative Technology.
Babylon has designed a software platform to reclaim the decentralized food system of the 21st Century - using modular vertical farms that enables anyone to grow local produce on-site, all year round, indoors. They launched their first products focusing on the health care and senior living markets where our vertical farms provide access to food-as-medicine quality food and a variety of therapeutic activities.
Website:
https://www.babylonmicrofarms.com/
Press Contact:
Sharon Rettinger
Little Leaf Farms Raises $90M to Grow Its Greenhouse Network
Massachusetts-based Little Leaf Farms has raised $90 million in a debt and equity financing round to expand its network of hydroponic greenhouses on the East Coast. The round was led by Equilibrium Capital as well as founding investors Bill Helman and Pilot House Associates. Bank of America also participated.
by Jennifer Marston
Image from: Little Leaf Farms
Massachusetts-based Little Leaf Farms has raised $90 million in a debt and equity financing round to expand its network of hydroponic greenhouses on the East Coast. The round was led by Equilibrium Capital as well as founding investors Bill Helman and Pilot House Associates. Bank of America also participated.
Little Leaf Farms says the capital is “earmarked” to build new greenhouse sites along the East Coast, where its lettuce is currently available in about 2,500 stores.
The company already operates one 10-acre greenhouse in Devins, Massachusetts. Its facility grows leafy greens using hydroponics and a mixture of sunlight supplemented by LED-powered grow lights. Rainwater captured from the facility’s roof provides most of the water used on the farm.
According to a press release, Little Leaf Farms has doubled its retail sales to $38 million since 2019. And last year, the company bought180 acres of land in Pennsylvania on which to build an additional facility. Still another greenhouse, slated for North Carolina, will serve the Southeast region of the U.S.
Little Leaf Farms joins the likes of Revol Greens, Gotham Greens, AppHarvest, and others in bringing local(ish) greens to a greater percentage of the population. These facilities generally pack and ship their greens on the day of or day after harvesting, and only supply retailers within a certain radius. Little Leaf Farms, for example, currently servers only parts of Massachusetts, Pennsylvania, New York, and New Jersey.
The list of regions the company serves will no doubt lengthen as the company builds up its greenhouse network in the coming months.
Agritech: Precision Farming With AI, IoT and 5G
For a company that grows and delivers vegetables, Boomgrow Productions Sdn Bhd’s office is nothing like a farm, or even a vertical farm. Where farms are bedecked with wheelbarrows, spades and hoes, Boomgrow’s floor plan is akin to a co-working space with a communal island table, several cubicles, comfortable armchairs, a cosy hanging rattan chair and a glass-walled conference room in the middle
Image from: Photo by Mohd Izwan Mohd Nazam/The Edge
For a company that grows and delivers vegetables, Boomgrow Productions Sdn Bhd’s office is nothing like a farm, or even a vertical farm.
Where farms are bedecked with wheelbarrows, spades and hoes, Boomgrow’s floor plan is akin to a co-working space with a communal island table, several cubicles, comfortable armchairs, a cosy hanging rattan chair and a glass-walled conference room in the middle.
At a corner, propped up along a walkway leading to a rectangular chamber fitted with grow lights, are rows of support stilts with hydroponic planters developed in-house and an agricultural technologist perched on a chair, perusing data. “This is where some of the R&D work happens,” says Jay Dasen, co-founder of the agritech start-up.
But there is a larger farm where most of the work behind this high-tech initiative is executed. Located a stone’s throw from the city centre in Ampang is a 40ft repurposed shipping container outfitted with perception technologies and artificial intelligence (AI) capabilities that mimic the ideal environment to produce more than 50,000kg of vegetables a year.
Stacked in vertical layers, Boomgrow’s vegetables are grown under artificial lights with Internet of Things (IoT) sensors to detect everything from leaf discolouration to nitrate composition. This is coupled with AI and machine learning algorithms.
Boomgrow is the country’s first 5G-connected vertical farm. With the low latency and larger bandwidth technology, the start-up is able to monitor production in real time as well as maintain key parameters, such as temperature and humidity, to ensure optimal growth conditions.
When Jay and her co-founders, K Muralidesan and Shan Palani, embarked on this initiative six years ago, Boomgrow was nowhere near what it is today.
The three founders got together hoping to do their part in building a more sustainable future. “I’ve spent years advising small and large companies on sustainability, environmental and social governance disclosures. I even embarked on a doctorate in sustainability disclosure and governance,” says Jay.
“But I felt a deep sense of disconnect because while I saw companies evolving in terms of policies, processes and procedures towards sustainability, the people in those organisations were not transforming. Sustainability is almost like this white noise in the background. We know it’s important and we know it needs to be done, but we don’t really know how to integrate it into our lives.
“That disconnect really troubled me. When we started Boomgrow, it wasn’t a linear journey. Boomgrow is something that came out of meaningful conversations and many years of research.”
Shan, on the other hand, was an architect who developed a taste for sustainable designs when he was designing modular structures with minimal impact on their surroundings between regular projects. “It was great doing that kind of work. But I was getting very dissatisfied because the projects were customer-driven, which meant I would end up having debates about trivial stuff such as the colour of wall tiles,” he says.
As for Murali, the impetus to start Boomgrow came from having lived overseas — while working in capital markets and financial services — where quality and nutritious produce was easily available.
Ultimately, they concluded that the best way to work towards their shared sustainability goals was to address the imminent problem of food shortage.
“By 2050, the world’s population is expected to grow to 9.7 billion people, two-thirds of whom will be in Asia-Pacific. Feeding all those people will definitely be a huge challenge,” says Jay.
“The current agricultural practice is not built for resilience, but efficiency. So, when you think of farming, you think of vast tracts of land located far away from where you live or shop.
“The only way we could reimagine or rethink that was to make sure the food is located closer to consumers, with a hyperlocal strategy that is traceable and transparent, and also free of pesticides.”
Having little experience in growing anything, it took them a while to figure out the best mechanism to achieve their goal. “After we started working on prototypes, we realised that the tropics are not designed for certain types of farming,” says Jay.
“And then, there is the problem of harmful chemicals and pesticides everywhere, which has become a necessity for farmers to protect their crops because of the unpredictable climate. We went through many iterations … when we started, we used to farm in little boxes, but that didn’t quite work out.”
They explored different methodologies, from hydroponics to aquaponics, and even started growing outdoors. But they lost a lot of crops when a heat wave struck.
That was when they started exploring more effective ways to farm. “How can we protect the farm from terrible torrential rains, plant 365 days a year and keep prices affordable? It took us five years to answer these questions,” says Jay.
Even though farmers all over the world currently produce more than enough food to feed everyone, 820 million people — roughly 11% of the global population — did not have enough to eat in 2018, according to the World Health Organization. Concurrently, food safety and quality concerns are rising, with more consumers opting for organically produced food as well as safe foods, out of fear of harmful synthetic fertilisers, pesticides, herbicides and fungicides.
According to ResearchAndMarkets.com, consumer demand for global organic fruit and vegetables was valued at US$19.16 billion in 2019 and is anticipated to expand at a compound annual growth rate (CAGR) of 6.5% by 2026.
Meanwhile, the precision farming market was estimated to be US$7 billion in 2020 and is projected to reach US$12.8 billion by 2025, at a CAGR of 12.7% between 2020 and 2025, states MarketsandMarkets Research Pte Ltd.
Malaysia currently imports RM1 billion worth of leafy vegetables from countries such as Australia, China and Japan. Sourcing good and safe food from local suppliers not only benefits the country from a food security standpoint but also improves Malaysia’s competitive advantage, says Jay.
Unlike organic farming — which is still a soil-based method — tech-enabled precision farming has the advantage of catering for increasing demand and optimum crop production with the limited resources available. Moreover, changing weather patterns due to global warming encourage the adoption of advanced farming technologies to enhance farm productivity and crop yield.
Boomgrow’s model does not require the acres of land that traditional farms need, Jay emphasises. With indoor farms, the company promises a year-round harvest, undisturbed by climate and which uses 95% less water, land and fuel to operate.
Traditional farming is back-breaking labour. But with precision technology, farmers can spend less time on the farm and more on doing other things to develop their business, she says.
Boomgrow has secured more than RM300,000 in funding via technology and innovation grants from SME Corporation Malaysia, PlaTCOM Ventures and Malaysia Digital Economy Corporation, and is on track to build the country’s largest indoor farms.
Image from: Boomgrow
The company got its chance to showcase the strength of its smart technology when Telekom Malaysia Bhd (TM) approached it to be a part of the telco’s Smart Agriculture cluster in Langkawi last October.
“5G makes it faster for us to process the multiple data streams that we need because we collect data for machine learning, and then AI helps us to make decisions faster,” Jay explains.
“We manage the farm using machines to study inputs like water and electricity and even measure humidity. All the farm’s produce is lab-tested and we can keep our promise that there are no pesticides, herbicides or any preserving chemicals. We follow the food safety standards set by the EU, where nitrate accumulation in plant tissues is a big issue.”
With TM’s 5G technology and Boomgrow’s patent-pending technology, the latter is able to grow vegetables like the staple Asian greens and highland crops such as butterhead and romaine lettuce as well as kale and mint. While the company is able to grow more than 30 varieties of leafy greens, it has decided to stick to a selection of crops that is most in demand to reduce waste, says Jay.
As it stands, shipping containers are the best fit for the company’s current endeavour as containerised modular farms are the simplest means of bringing better food to local communities. However, it is also developing a blueprint to house farms in buildings, she says.
Since the showcase, Boomgrow has started to supply its crops to various hotels in Langkawi. It rolled out its e-commerce platform last year after the Movement Control Order was imposed.
“On our website, we promise to deliver the greens within six hours of harvest. But actually, you could get them way earlier. We harvest the morning after the orders come in and the vegetables are delivered on the same day,” says Jay.
Being mindful of Boomgrow’s carbon footprint, orders are organised and scheduled according to consumers’ localities, she points out. “We don’t want our delivery partners zipping everywhere, so we stagger the orders based on where consumers live.
“For example, all deliveries to Petaling Jaya happen on Thursdays, but the vegetables are harvested that morning. They are not harvested a week before, three days before or the night before. This is what it means to be hyperlocal. We want to deliver produce at its freshest and most nutritious state.”
Plans to expand regionally are also underway, once Boomgrow’s fundraising exercise is complete, says Jay. “Most probably, this will only happen when the Covid-19 pandemic ends.”
To gain the knowledge they have today, the team had to “unlearn” everything they knew and take up new skills to figure what would work best for their business, says Jay. “All this wouldn’t have been possible if we had not experimented with smart cameras to monitor the condition of our produce,” she laughs.
Vertical Farming ‘At a Crossroads’
Although growing crops all year round with Controlled Environment Agriculture (CEA) has been proposed as a method to localize food production and increase resilience against extreme climate events, the efficiency and limitations of this strategy need to be evaluated for each location
Building the right business model to balance resource usage with socio-economic conditions is crucial to capturing new markets, say speakers ahead of Agri-TechE event
Image from: Fruitnet
Although growing crops all year round with Controlled Environment Agriculture (CEA) has been proposed as a method to localize food production and increase resilience against extreme climate events, the efficiency and limitations of this strategy need to be evaluated for each location.
That is the conclusion of research by Luuk Graamans of Wageningen University & Research, a speaker at the upcoming Agri-TechE event on CEA, which takes place on 25 February.
His research shows that integration with urban energy infrastructure can make vertical farms more viable. Graamans’ research around the modelling of vertical farms shows that these systems are able to achieve higher resource use efficiencies, compared to more traditional food production, except when it comes to electricity.
Vertical farms, therefore, need to offer additional benefits to offset this increased energy use, Graamans said. One example his team has investigated is whether vertical farms could also provide heat.
“We investigated if vertical farms could provide not just food for people living in densely populated areas and also heat their homes using waste heat. We found that CEA can contribute to stabilizing the increasingly complex energy grid.”
Diversification
This balance between complex factors both within the growing environment and wider socio-economic conditions means that the rapidly growing CEA industry is beginning to diversify with different business models emerging.
Jack Farmer is CSO at vertical producer LettUs Grow, which recently launched its Drop & Grow growing units, offering a complete farming solution in a shipping container.
He believes everyone in the vertical farming space is going to hit a crossroads. “Vertical farming, with its focus on higher value and higher density crops, is effectively a subset of the broader horticultural sector,” he said.
"All the players in the vertical farming space are facing a choice – to scale vertically and try to capture as much value in that specific space, or to diversify and take their technology expertise broader.”
LettUs Grow is focussed on being the leading technology provider in containerised farming, and its smaller ‘Drop & Grow: 24’ container is mainly focussed on people entering the horticultural space.
Opportunities in retail
“This year is looking really exciting,” he said. “Supermarkets are investing to ensure a sustainable source of food production in the UK, which is what CEA provides. We’re also seeing a growth in ‘experiential’ food and retail and that’s also where we see our Drop & Grow container farm fitting in.”
Kate Hofman, CEO, GrowUp agrees. The company launched the UK’s first commercial-scale vertical farm in 2014.
“It will be really interesting to see how the foodservice world recovers after lockdown – the rough numbers are that supermarket trade was up at least 11 per cent in the last year – so retail still looks like a really good direction to go in.
“If we want to have an impact on the food system in the UK and change it for the better, we’re committed to partnering with those big retailers to help them deliver on their sustainability and values-driven goals.
“Our focus is very much as a salad grower that grows a fantastic product that everyone will want to buy. And we’re focussed on bringing down the cost of sustainable food, which means doing it at a big enough scale to gain the economies of production that are needed to be able to sell at everyday prices.”
Making the Numbers Add Up
The economics are an important part of the discussion. Recent investment in the sector has come from the Middle East, and other locations, where abundant solar power and scarce resources are driving interest in CEA. Graamans’ research has revealed a number of scenarios where CEA has a strong business case.
For the UK, CEA should be seen as a continuum from glasshouses to vertical farming, he believes. “Greenhouses can incorporate the technologies from vertical farms to increase climate control and to enhance their performance under specific climates."
It is this aspect that is grabbing the attention of conventional fresh produce growers in open field and covered crop production.
A Blended Approach
James Green, director of agriculture at G’s, thinks combining different growing methods is the way forward. “There’s a balance in all of these systems between energy costs for lighting, energy costs for cooling, costs of nutrient supply, and then transportation and the supply and demand. At the end of the day, sunshine is pretty cheap and it comes up every day.
“I think a blended approach, where you’re getting as much benefit as you can from nature but you’re supplementing it and controlling the growth conditions, is what we are aiming for, rather than the fully artificially lit ‘vertical farming’.”
Graamans, Farmer and Hofman will join a discussion with conventional vegetable producers, vertical farmers and technology providers at the Agri-TechE event ‘Controlled Environment Agriculture is growing up’ on 25 February 2021.
Bowery’s Founder, Irving Fain, On The Future of Vertical Farming
At one point in the not-so-distant past, vertical farming’s role in our future agricultural system was far from certain. Growing leafy greens in warehouse-like environments controlled by tech seemed like a compelling business, but one that had yet to prove itself either economically or as an important source of food for a growing world population
Image from: The Spoon
At one point in the not-so-distant past, vertical farming’s role in our future agricultural system was far from certain. Growing leafy greens in warehouse-like environments controlled by tech seemed like a compelling business, but one that had yet to prove itself either economically or as an important source of food for a growing world population.
That, at least, was a common sentiment Irving Fain, CEO and founder of Bowery, met with when he started his vertical farming company five years ago. “There was a bit of skepticism around it,” he told me over a call recently, suggesting that five years ago, there were a lot more “ifs” than “whens” in terms of vertical farming’s future.
Fain, Bowery, and the entire vertical farming industry get a much warmer reception nowadays. Investment dollars are pouring into the space. Around the world, companies, scientists, and food producers are using the method to not just supply upscale grocery stores with greens but experiment with breeds of produce, feed underserved populations, and grow food in non-arable regions. As Fain suggested when we spoke, the last 12 months seem to have turned those “ifs” into definite “whens.”
Bowery’s last 12 months also illustrate this change. Fain said that Bowery went from under 100 retail locations about a year ago to nearly 700 right now, and will be in more than 1,000 “in the coming months.” Its produce is in a number of food retailers around the Mid-Atlantic and Northeast, including Whole Foods Market, Giant Food, Stop & Shop, Walmart, and Weis Markets. And in 2020, the company experienced “more than 4x growth” with e-commerce partners.
While the pandemic is responsible for some of this popularity, Fain insists it is not the only reason for the eventful year. “It’s definitely bigger than the pandemic,” he said. “What you’re seeing is a food system that’s evolving and [people have a desire] to see transparency and traceability in the food system.” These, he says, are issues the traditional food supply chain isn’t really able to address right now, hence the opportunity for companies like Bowery, which effectively cut multiple steps out of the supply chain.
Bowery grows its greens (lettuces, herbs, and some custom blends) inside industrial spaces where crops are stacked vertically in trays and fed nutrients and water via a hydroponic system. Technology controls all elements of the farm, from the temperature inside to how much light each plants get. The company currently operates two farms, one in New Jersey and the other in Maryland. A third is planned for Pennsylvania.
Technology, in particular, is something Bowery has big plans for. On top of a retail expansion, Bowery also added some notable personnel to its staff, including Injong Rhee, formerly the Internet of Things VP at Google as well a chief technologist at Samsung. Having such technology chops onboard will be vital in order for Bowery to realize many of its ambitions around advanced automation, which has the potential to optimize many parts of the seed-to-store process for vertically grown greens.
For example, Bowery’s farms are equipped with sensors and cameras that are constantly collecting data — “billions” of points, according to the company — that can be used to not just observe the current state of plant health but also predict the most optimal growing conditions for each crop. Elements like temperature, humidity levels, nutrient levels, and light intensity can all be adjusted, via the BoweryOS software, to create those optimal conditions. The end result is more consistent crop production, better yields, more flavorful food, and, ideally, a better nutritional profile for the greens compared to what conventional produce offers.
The system can also, through automation and AI, detect problems with plants. In a recent interview with Venture Beat, Bowery Chief Science Officer Henry Sztul used the example of butterhead lettuce yellowing at the edges during growth. Bowery’s system is technologically advanced enough at this point that it is starting to understand the conditions that create those yellowing edges. That foreknowledge, in turn, will allow growers to adjust the crop “recipe” (see above mixture of lights, temperature, etc.) to avoid the problem.
It took Bowery years to get to this point in terms of what its technology is capable of doing. “The system [for] indoor farming that you choose has a direct impact on the crops you’ll be able to grow, on the margins you’ll be able to generate, and on the return profile of the business itself,” said Fain. “And so being incredibly intentional and thoughtful about what technology you use is something we spent a lot of time on because it has an extraordinarily important economic impact.”
On a less technically complex note, controlled ag from Bowery and others also goes some way towards reinventing the supply food chain. Rather than greens being harvested in, say, Mexico and shipped via a complex distribution process all the way to Baltimore, they are packaged up at the farm and distributed to nearby retailers, usually those within a day’s drive “It is much more sustainable. It is much more efficient, and it’s more reliable, and those things have been important to consumers long before COVID,” said Fain.
Bowery will continue to innovate on both the technology and supply side of its business, as well as with the food itself. The company just launched a new specialty product line that will experiment with different flavors of greens and change frequently.
In terms of tech, Bowery’s latest farm, currently being built in Bethlehem, Pennsylvania, will incorporate even more automation than the company’s two existing farms. That location is slated to open later in 2021. When it does, Bowery will be capable of serving nearly 50 million people within a 200-mile radius.
The company hopes to expand its geographic reach much wider some day, building farms near most major U.S. cities and beyond. Given the increased confidence in the vertical farming sector as a whole, now looks to be the optimal time to move towards those ambitions.
by Jennifer Marston, The Spoon
Smart Agriculture Startup Bowery Farming Hires A Google Veteran As CTO
The hire comes after a year of accelerated growth at Bowery, with retail sales at outlets like Whole Foods rising 600% and e-commerce sales via Amazon and others increasing fourfold, the company says, while declining to disclose its actual sales or production figures.
One goal of high-tech indoor farming startup Bowery Farming is to use artificial intelligence and machine learning to enhance its crop yields and reduce costs. So the five-year-old Manhattan-based company has hired Google and Samsung veteran Injong Rhee as its new chief technology officer.
Rhee, who was previously Internet of Things VP at Google and chief technologist at Samsung Mobile, will focus on improving Bowery’s computer-vision system and other sensors that analyze when plants need water and nutrients, while also looking to apply the company’s accumulated historical data to new problems.
Bowery grow room near Baltimore
“Agriculture is sitting at the crux of the world’s most challenging problems like food shortages, climate change, water shortages, a lack of arable space,” Rhee tells Fortune about his decision to join the startup. “These are very challenging problems, and all of these are relevant to what Bowery tackles every day. Any advances we make here lead to a better world.”
There’s also the matter of the kale, Rhee adds.
Bowery so far has focused on growing and selling green leafy vegetables like lettuce, arugula, and kale, though it aims to add other categories of produce soon. “It was an eye-popping experience,” Rhee says of his first time trying Bowery’s kale. “How can it be so sweet and so crunchy. That was amazing.”
The hire comes after a year of accelerated growth at Bowery, with retail sales at outlets like Whole Foods rising 600% and e-commerce sales via Amazon and others increasing fourfold, the company says, while declining to disclose its actual sales or production figures. With two large warehouse-size farms in operation, in New Jersey and Maryland, Bowery is on the verge of opening its third indoor growing center in Bethlehem, Pa. The startup claims its high-tech methods, though more expensive than growing outdoors, create farms that are more than 100 times as productive per square foot as traditional outdoor farms.
“COVID was an accelerator of trends,” Bowery CEO and founder Irving Fain says. The pandemic disrupted food supply chains stretching across the globe, giving an advantage to Bowery, which sells its produce within just a few hundred miles of each farm, he says. “That amplified and accelerated a trend towards simplifying supply chains, and creating a surety of supply.”
But Bowery also faces a host of competitors, from other indoor farming startups like AeroFarms and Gotham Greens, to more traditional ag companies like John Deere and Bayer’s Monsanto, all fueling a movement toward precision farming. If one-quarter of farms worldwide adopted precision agriculture using A.I. and other data-crunching methods by 2030, farmers’ annual expenses would decline by $100 billion, or as much as 4% of the sector’s total expenses, while saving water and reducing greenhouse gas emissions, a recent study by McKinsey found.
Rhee spent 15 years as a professor of computer science at North Carolina State University, where he helped develop core Internet standards for transporting data at high speeds. He joined Samsung in 2011 where he helped lead a wide range of projects including the Bixby digital assistant, Knox security app, and Samsung Pay mobile payments service. He moved to Google in 2018 as an entrepreneur-in-residence to focus on Internet of Things projects.
Bowery has raised over $170 million in venture capital from a mix of tech figures like Amazon consumer CEO Jeff Wilke and Uber CEO Dara Khosrowshahi, well-known restaurateurs such as Tom Colicchio and David Barber, and venture capital firms including Temasek, GV, and General Catalyst.
Bringing The Future To life In Abu Dhabi
A cluster of shipping containers in a city centre is about the last place you’d expect to find salad growing. Yet for the past year, vertical farming startup Madar Farms has been using this site in Masdar City, Abu Dhabi, to grow leafy green vegetables using 95 per cent less water than traditional agriculture
Amid the deserts of Abu Dhabi, a new wave of entrepreneurs and innovators are sowing the seeds of a more sustainable future.
Image from: Wired
A cluster of shipping containers in a city centre is about the last place you’d expect to find salad growing. Yet for the past year, vertical farming startup Madar Farms has been using this site in Masdar City, Abu Dhabi, to grow leafy green vegetables using 95 per cent less water than traditional agriculture.
Madar Farms is one of a number of agtech startups benefitting from a package of incentives from the Abu Dhabi Investment Office (ADIO) aimed at spurring the development of innovative solutions for sustainable desert farming. The partnership is part of ADIO’s $545 million Innovation Programme dedicated to supporting companies in high-growth areas.
“Abu Dhabi is pressing ahead with our mission to ‘turn the desert green’,” explained H.E. Dr. Tariq Bin Hendi, Director General of ADIO, in November 2020. “We have created an environment where innovative ideas can flourish and the companies we partnered with earlier this year are already propelling the growth of Abu Dhabi’s 24,000 farms.”
The pandemic has made food supply a critical concern across the entire world, combined with the effects of population growth and climate change, which are stretching the capacity of less efficient traditional farming methods. Abu Dhabi’s pioneering efforts to drive agricultural innovation have been gathering pace and look set to produce cutting-edge solutions addressing food security challenges.
Beyond work supporting the application of novel agricultural technologies, Abu Dhabi is also investing in foundational research and development to tackle this growing problem.
In December, the emirate’s recently created Advanced Technology Research Council [ATRC], responsible for defining Abu Dhabi’s R&D strategy and establishing the emirate and the wider UAE as a desired home for advanced technology talent, announced a four-year competition with a $15 million prize for food security research. Launched through ATRC’s project management arm, ASPIRE, in partnership with the XPRIZE Foundation, the award will support the development of environmentally-friendly protein alternatives with the aim to "feed the next billion".
Image from: Madar Farms
Global Challenges, Local Solutions
Food security is far from the only global challenge on the emirate’s R&D menu. In November 2020, the ATRC announced the launch of the Technology Innovation Institute (TII), created to support applied research on the key priorities of quantum research, autonomous robotics, cryptography, advanced materials, digital security, directed energy and secure systems.
“The technologies under development at TII are not randomly selected,” explains the centre’s secretary general Faisal Al Bannai. “This research will complement fields that are of national importance. Quantum technologies and cryptography are crucial for protecting critical infrastructure, for example, while directed energy research has use-cases in healthcare. But beyond this, the technologies and research of TII will have global impact.”
Future research directions will be developed by the ATRC’s ASPIRE pillar, in collaboration with stakeholders from across a diverse range of industry sectors.
“ASPIRE defines the problem, sets milestones, and monitors the progress of the projects,” Al Bannai says. “It will also make impactful decisions related to the selection of research partners and the allocation of funding, to ensure that their R&D priorities align with Abu Dhabi and the UAE's broader development goals.”
Image from: Agritecture
Nurturing Next-Generation Talent
To address these challenges, ATRC’s first initiative is a talent development programme, NexTech, which has begun the recruitment of 125 local researchers, who will work across 31 projects in collaboration with 23 world-leading research centres.
Alongside universities and research institutes from across the US, the UK, Europe and South America, these partners include Abu Dhabi’s own Khalifa University, and Mohamed bin Zayed University of Artificial Intelligence, the world’s first graduate-level institute focused on artificial intelligence.
“Our aim is to up skill the researchers by allowing them to work across various disciplines in collaboration with world-renowned experts,” Al Bannai says.
Beyond academic collaborators, TII is also working with a number of industry partners, such as hyperloop technology company, Virgin Hyperloop. Such industry collaborations, Al Bannai points out, are essential to ensuring that TII research directly tackles relevant problems and has a smooth path to commercial impact in order to fuel job creation across the UAE.
“By engaging with top global talent, universities and research institutions and industry players, TII connects an intellectual community,” he says. “This reinforces Abu Dhabi and the UAE’s status as a global hub for innovation and contributes to the broader development of the knowledge-based economy.”
In Malahide, Two Friends Raise A Vertical Farm
When salesman Jack Hussey finishes his work day, he closes the laptop, leaves his home in Malahide and walks 10 minutes down the road. At the bottom of his friend’s farm sits an outhouse with a coldroom which now hosts his side business, Upfarm. A farm that goes upwards
Image from: Dublin Inquirer
When salesman Jack Hussey finishes his work day, he closes the laptop, leaves his home in Malahide and walks 10 minutes down the road. At the bottom of his friend’s farm sits an outhouse with a coldroom which now hosts his side business, Upfarm. A farm that goes upwards.
Imagine a shelf rack, says Hussey. “We’ve kitted the roofs of each shelf with an LED grow light. It’s to replicate the sunlight basically.”
A photo of the farm shows purple light beaming down on thick heads of lemongrass and basil, stacked on shelves. Yields from vertical farming are far more efficient than in-the-ground farming, Hussey said, on the phone last Friday.
He likens it to real estate. “You can have houses that are populated side by side or you can start going upwards with apartments.”
From Podcast to Table
Hussey always had an interest in food, he says. Last year he and a school friend, Bill Abbott, began to look into urban farming.
“But we were saying, is farming in the ground actually the best route to go?” Hussey says.
It’s labour intensive, which didn’t suit the two guys, who work other full-time jobs. Then, in March 2020, Hussey heard a podcast with American urban farmer Curtis Stone. He had an urban farm where he was using a spin-farming method, says Hussey. “It’s what they call it. You rotate crops out of the ground in a much more efficient way.”
“Essentially he was able to capitalise on a third acre of land. He was able to take in 80k a year,” he says.
Hussey was inspired by that, by somebody making the most of a small bit of land. So in June last year, in the middle of a pandemic and juggling working from home, Hussey and Abbot set about doing the same, albeit with a different model, and launched their vertical farm.
Image from: Farmony
How It Works
Farmony, which specialises in tech for vertical farming, sold Upfarm with the tools to get up and running – shelves, special LED lighting, a watering system and humidifiers. It is the ideal conditions for growing produce, says Framony co-founder John Paul Prior. Nutrients, hours of light, humidity and temperature are controlled in vertical farming, Prior says.
But Farmony is also a data company, Prior says. “So we capture data at all stages of the growing cycle. And we feed that back to the grower.”
This helps the grower to establish the optimum conditions, he says. “That’s not just in terms of plant growth, that’s in terms of workflow management.”
The size of an operation can be the small coldroom in Malahide that uses one Farmony module, and produces microgreens and wheatgrass for sale. Or it can be like a farm in Tipperary with 60 modules, he says. A module is 1 metre wide, 1.3 metres long and 2.5 metres tall, Prior says. Hussey says it is labour-intensive looking after a vertical farm module.
After work last Thursday, he and his dad replanted his microgreen crops into 30 different trays. “It took about two hours,” he says.
What Is the Benefit?
“So as long as you can control your temperature, your humidity, and your nutrient levels in the water, you can basically grow all year round,” says Prior. Vertical farming also means better conditions for workers, Prior says.
“If you’re working in a controlled environment, like a vertical farm, you’re working in a clean environment,” Prior says.
“You work between 18 to 22 degrees. There’s no harsh frost. There’s no extreme cold winters, equally there’s no burning-hot summers.,” says Prior.
The crop is consistent too, says Prior, thanks to the controlled environment.
“Let’s say I’m someone who loves basil and who makes a lot of pesto at home,” he says.
Getting basil of consistent quality from the supermarket can be difficult when it comes from different countries, or may have been sitting on a shelf for days after travelling thousands of miles, he says.
Image from: Farmony
Why Is this Important?
Soil quality is dropping, Hussey says. “What does that mean for outdoor growing?”
The answer, Hussey says, is vertical farming. It uses mineral-rich water so it doesn’t rely on nutrients from the ground, Hussey says.
Says Prior: “Vertical farming uses about 10 percent of the water of traditional farming.”
Prior says it takes less energy to get food from a nearby vertical farm than to ship it from afar. It was not always the case until a breakthrough in another industry, he says.
“Billions of dollars have been invested in the cannabis industry globally. It’s meant that the investment in grow-lighting technology has been huge,” he says.
“As a result, the price, the efficiency and most importantly, the energy efficiency of the lighting is really amazing” he says.
Says Hussey: “It’s not easy work but it is nice work. It’s good work.”
Ensuring Singapore's Food Security Despite the Odds
As with most issues that impact national security in Singapore, it often seems that the odds are stacked against us. Food security — access to safe and nutritious food — is a challenge on several fronts. Singapore is a small city-state with limited resources, with only 1 per cent of land available for food production, and over 90 per cent of food is imported from an increasingly disrupted world. The Covid-19 pandemic has further amplified the gravity of safeguarding food security
Image from: Reuters
As with most issues that impact national security in Singapore, it often seems that the odds are stacked against us. Food security — access to safe and nutritious food — is a challenge on several fronts.
Singapore is a small city-state with limited resources, with only 1 per cent of land available for food production, and over 90 per cent of food is imported from an increasingly disrupted world. The Covid-19 pandemic has further amplified the gravity of safeguarding food security. The city-state has been proactively planning for long-term food security through the Singapore Food Agency’s (SFA) strategy of “three food baskets” — diversifying food sources, growing locally and growing overseas. This approach has served the Republic well in securing a supply of safe food.
DIVERSIFIED SOURCING IS KEY
Singapore’s food importers leverage the nation’s connectivity and the global free trade environment to import from multiple sources in about 170 countries and regions worldwide. Should there be a disruption to any one source, importers are able to tap alternative food sources and ensure supply remains stable. Lockdown measures brought about by Covid-19 underscored Singapore’s vulnerabilities to supply disruptions in food.
It was not by luck that the Republic’s food supply remained stable and market shelves continued to be promptly restocked — it was the result of a deliberate whole-of-government strategy to diversify food sources. To keep the nation’’s diversified food supply lines intact amid the Covid-19 global pandemic, SFA worked closely with the Ministry of Trade and Industry and Enterprise Singapore (ESG) to monitor Singapore’s food supply situation. Together with the Ministry of Foreign Affairs, these economic agencies worked with like-minded countries to maintain open trade links.
LOCAL PRODUCTION AN IMPORTANT BUFFER
SFA drives innovation in local farms with the ambitious goal of producing 30 per cent of Singapore’s nutritional needs by 2030 as part of our “30 by 30” plan. To meet this goal, we need a holistic and long-term approach to space-planning, boosting agri-food technology and developing local agri-specialists. To facilitate and support the establishment of high-technology and productive farms in Singapore, SFA tenders out land based on qualitative criteria such as production capability, production track record, relevant experience and qualifications, innovation and sustainability.
In addition, a masterplan for the greater Lim Chu Kang (LCK) region, spanning about 390ha of land, will be undertaken in consultation with stakeholders over the next two to three years. The redeveloped LCK agri-food cluster will produce more than three times its current food production.
Building on the above efforts to grow Singapore’s high-tech agri-tech sector, SFA will continue to partner with the Economic Development Board and ESG to attract best-in-class global agri-tech companies, as well as to nurture promising homegrown agri-tech companies into local champions and help them to expand overseas.
EXPLORING ALTERNATIVE, UNDERUTILISED SPACES
Urban food solutions are expected to play a key role in global food security. While there are progressive enterprises operating out of farmlands and industrial estates, some agricultural game-changers are also taking root in unconventional areas — indoors, on rooftops and in underutilised spaces.
SFA worked with the Singapore Land Authority to introduce an urban farm at the former Henderson Secondary School site, which was transformed into Singapore’s first integrated space comprising an urban farm, childcare centre and nursing home within a state property. The farm space within the site was awarded in May 2019 to social enterprise City Sprouts, and it has become a vibrant destination for the young and old to learn about urban farming and enjoy a relaxing day out.
Citiponics, the first commercial farm located on a multi-storey car park in a residential neighbourhood, harvested its first yield of vegetables in April 2019. In September 2020, another nine sites atop multi-storey car parks were awarded for urban farming.
The successful bidders included proposals for hydroponic and vertical farming systems with a variety of innovative features, such as the Internet of Things (IoT), blockchain technology and automated climate control. These sites have the potential to collectively produce around 1,600 tonnes of vegetables annually.
Image from: Ciitiponics
TAPPING TECH
The Agriculture Productivity Fund (APF) supports local farms in their capability development and drive towards higher productivity. Through APF, SFA co-funds the adoption of farming systems to better control environmental variables, test-bed technologies and boost production capabilities. Between October 2014 and September 2020, a total of almost S$42 million has been committed to 115 farms.
The Covid-19 pandemic presented greater impetus to speed up local food production capacities. In September 2020, SFA awarded S$39.4 million to nine companies under the 30x30 Express Grant to quickly ramp up food-farm outputs over the next six months to two years. With advanced robotic and digital systems increasingly being used in farming, Singapore’s vegetables farmers have also become innovative agri-engineers and specialists in their own right.
With support from the 30x30 Express Grant, urban farming engineering solutions firm Indoor Farm Factory Innovation will set up an indoor vegetable farm with a vertical integration growth system up to 8m in height in a fully controlled and pesticide-free environment. The farm will leverage artificial intelligence farming systems integrated with IoT monitoring, dosing irrigation and an advanced environmental control system to achieve optimum growing conditions all year round.
Seng Choon, a chicken egg farm that has been in business for more than 30 years, has also proved itself a modernist in its operations. The company uses a computer that scans eggs to ascertain if they are clean; while feeding systems, temperature controls and waste cleaning systems have been automated with SFA’s support. Singapore’s efforts at ensuring food security would not be complete without support from consumers. To boost recognition of local produce among consumers, SFA brought the industry and public together to create a new “SG Fresh Produce” logo.
Farmers have been using this emblem on their packaging since August 2020. A website was also launched to provide a trove of information on locally farmed food. While the Covid-19 pandemic has led to import restrictions, it also helped to accelerate support for local produce. With public support for local farmers and other key measures, Singapore can beat the odds in ensuring food security in this ever-evolving, ever-disrupted world.
Organic: The Battle for a Single Word
Throughout history, when we see great leaps forward in technology, there are always pushbacks from the old world who want to maintain the status-quo. This can be for a variety of reasons and come from a variety of people. Sometimes, the resistance comes from workers, an example of this would be the fierce opposition from workers who protested the mechanisation of their jobs brought about by the industrial revolution. They were often referred to as luddites because of the propensity to destroy the new machines that were taking their jobs
Throughout history, when we see great leaps forward in technology, there are always pushbacks from the old world who want to maintain the status-quo. This can be for a variety of reasons and come from a variety of people. Sometimes, the resistance comes from workers, an example of this would be the fierce opposition from workers who protested the mechanisation of their jobs brought about by the industrial revolution. They were often referred to as luddites because of the propensity to destroy the new machines that were taking their jobs.
On the other hand, there can be examples of when the resistance to innovations come from industry competitors who don’t want to lose the dominance they once had. An example of this can be seen through the fossil fuel industries continuous attempts to limit the growth of renewables by lobbying governments to pursue policies more favourable to them.
Today we are seeing resistance to a new green revolution through innovation in the vertical farming sector primarily from industry competitors or even protective policy makers. Politico recently reported on a story regarding a fight between a Danish vertical farming company, called Nordic Harvest, and the EU whereby the former was prohibited from labelling their crops as organically produced. The reason given for this was that EU regulation demanded that anything being described as organic had to be produced in soil. This seems to be the antithesis to their Farm to Fork strategy as it heavily handicaps innovative indoor vertical farming companies.
Image from: Nord Harvest
Now this may not seem much like a significant infringement on the indoor vertical farming sector, but what this does is make it more difficult for companies, such as Nordic Harvest, to indicate to consumers their green credentials. Moreover, under the EU’s Green Public Procurement rules, indoor vertical farming companies gain a smaller share in food market than it normally would have due to the ruling on the definition of organics. The unfortunate aspect of this is that words only mean what we define them as, so the personal opinions of the individuals who made this decision are going down this direction for reasons not non-partisan.
Now there may so semi-legitimate reasons to resist the rise of indoor vertical farming, but it is clear that this will be the future of farming and it must not be kneecapped by ill-intentioned actors. The limitations of the sector, such as intense energy use or limited crop varieties, can only be solved if there is financial and legislative support from the powers that be.
This is clear with the recent certification of Sky Greens in Singapore as organic whereby the central government has been forward thinking. Speaking of their decision, the chair of the Food Standards Committee stated:
“The certification may allow local urban farms to expand into markets outside of Singapore. Having a national organic certification will help local urban farms to be on equal footing with the US…”
The Food Standards Committee in Singapore defined organic differently from the EU affirming that as long as they avoid mineral fertilisers or other pesticides and herbicides, which indoor vertical farms operating on controlled environment agriculture adheres to. At full capacity, Sky Greens can produce up to half a tonne of salads daily without LEDs and using gravity to collect rainwater to avoid pests. An important point to note however is that the vast majority of Singapore is urbanised with no domestic traditional rural farming industry.
Image from: Sky Greens
Another problematic component of this EU ruling is that may prove controversial is its impact on trade. Any vertical farming company from a country not with the restrictive rules and the EU that wanted to export their food produced in a vertical farm, they would as need to abide by these rules. For example, with basil being one of the major herbs produced in vertical farms, we often see it being used in Pesto. Unfortunately, this would not be able to be marketed as organic. With the EU being the largest trading bloc in the entire world, this will affect the global fortunes of the sector. We are also seeing this happen in the US but due to many legal appeals and challenges, they have not currently implemented the same rules as the EU.
So, with all this in mind, it is important to be aware of the pushback that will inevitably happen due to a green revolution brought about by innovation in the indoor vertical farming sector. The debate surrounding the definition of the word organic is only the start. We already see concerted efforts to ban synthetic meat companies from using words such as hamburger, hot dog or steak. However, even with this uneven playing field, indoor vertical farming is on track to increase its market share significantly over the next decade and beyond while traditional farming methods are on the decline.
The Future of the Food Supply Chain Lives on a Rooftop in Montreal
The world’s biggest commercial rooftop greenhouse sits atop a former Sears warehouse in a semi-industrial northwestern quarter of Montreal. Early every morning, staff pick fresh vegetables, then bring them downstairs, where they get packed into heavy-duty plastic totes along with the rest of the day’s grocery orders.
Image from: Lufa Farms
The world’s biggest commercial rooftop greenhouse sits atop a former Sears warehouse in a semi-industrial northwestern quarter of Montreal. Early every morning, staff pick fresh vegetables, then bring them downstairs, where they get packed into heavy-duty plastic totes along with the rest of the day’s grocery orders.
Tablets loaded with custom pick-and-pack software tell them where to put what: This basket has lettuce, tomatoes, and cucumbers, plus some chicken, eggs, and milk. The next one has eggplant, cashew Parmesan, tomato sauce, fresh pasta, and vegan ground round crumble. Whatever Luca doesn’t grow in its four greenhouses comes from local farms and producers, mostly from within 100 miles.
This is a modern foodie’s dream: a tech-forward online shop full of locally grown, pesticide-free, ethically-sourced products at reasonable price points, delivered once a week to either your doorstep or a local pickup point in your neighborhood.
It’s stunning to think Lufa was founded by two people who’d never even grown a tomato before, let alone sold one. “We said, ‘Instead of learning how the food world works, let’s just come up with what we feel the food world should be,’” says Mohamed Hage, 39, who cofounded Lufa with Lauren Rathmell in 2009.
To them, it looked like this: rooftop greenhouses that bring agriculture into cities. No pesticides, herbicides, or fungicides. Composting their green waste. Selling direct-to-consumer the same day the food is harvested. Capturing and reusing rainwater. Reusable packaging.
That’s exactly what they now have—and they feed a portion of Montreal, the second-biggest city in Canada, with it.
Image from: Lufa Farms
Back in the warehouse, workers poke at their tablets, checking off items as they’re packed into the boxes.
Customers—Lufavores, as the company calls them—typically place their orders a few days before delivery through the online store, dubbed “the Marketplace,” which Lufa built from scratch in 2012. That’s how Lufa’s suppliers know how much product to provide: They get forecasts first, then final order numbers, through their Lufa software. Some items, like frozen meat, can be delivered to the warehouse once a week. Others, like bread, arrive fresh every day.
Artisanal Montreal bakery la Fabrique Arhoma started supplying Lufa with bread and pastries about six years ago, co-owner Ariane Beaumont tells Fortune. Today, they hand-make 6,000 individual items a day for Lufa. Beaumont said Lufa now accounts for between 30% to 40% of her commercial sales; since pandemic shutdowns, a lot of the product destined for restaurants got redirected to Lufa. “They’re an exceptional company. I don’t know how they do it,” Beaumont says. “And they pay the fastest, too.”
Technology is the underpinning of Lufa’s success, and the owners know it.
“We see ourselves as a technology company, in the sense that we solve with software,” Rathmell, 32, says. They didn’t really have any other choice. To fulfill that dream they had back in 2009—years before COVID-19 forced most grocery stores to enable online shopping—they had to do it themselves.
“Nothing off-the-shelf can be applied to what we do, because it’s so complex,” Rathmell notes. “We harvest food ourselves; we gather from farmers and food makers throughout the province; most of it’s arriving just in time throughout the night to be packed in baskets for that day, and every order is fully unique.”
Lufa now has a team of eight programmers working on software and systems that manage e-commerce, warehouse management, routing, customer relationships, supplier fulfillment, pick-and-pack, vendor payments, delivery ETAs, and more.
Those technologies were tested on that fateful Friday the 13th last March, when Quebec and Canada each announced their first waves of COVID-19 lockdowns. People panicked, rushing to the grocery store to stock up on flour and toilet paper.
Online, new sign-ups for Lufa’s weekly grocery baskets exploded, and existing subscribers began ordering more than they’d ever ordered before—all while Lufa’s pickup points were shutting down. “We essentially doubled overnight,” Rathmell recalls. Lufa was forced beyond its operational capacity, and the cracks started showing in the systems and software that had, until that point, done a fine job getting the company by.
Lufa temporarily closed the website and opened a wait list. The staff analyzed the pandemic’s trajectory and how they had to adapt at each step; reconfigured their warehouse floor to station workers further apart; then relaunched at the capacity they could handle, gradually scaling each week until they hit their usual stride. Today, they’re humming along at 25,000 baskets a week.
Leading with tech helped make them nimble and strategic during those hairy early pandemic days, said Hage and Rathmell. After some recalibrations and new developments, their software and processes can now handle more customers, vendors, and processes—critical elements as the company continues to scale its greenhouse operations. In August of 2020, Lufa opened its fourth greenhouse, doubling its square footage. The four greenhouses combined produce 57,000 pounds of food a week. A fifth is planned for this year.
“Our objective at Lufa is to get to the point where we’re feeding everyone in the city,” Hage says.
And after Montreal? They’re planning on a yet to be determined second site in the northeastern pocket of North America, ideally this year. “Our vision is to grow food closer to where people live, and grow it more sustainably,” Rathmell says.
Image from: Lufa Farms
Bringing high-yield crop production into cities is a smart answer to many modern challenges in environmental and human health.
Mark Lefsrud, an associate professor of agricultural and environmental sciences at McGill University, points out that embracing technologies like LEDs and automation to grow indoors and in urban greenhouses means shorter supply chains, better nutritional integrity, less food waste, and reduced vulnerability to climate swings. In cities fed primarily by low-carbon energy (hydroelectricity in Montreal’s case), indoor growing versus importation becomes even more of a no-brainer.
“I’ve been working in the controlled environment and greenhouse industry for 20-some years, and having a company like Lufa has brought a lot of attention to not just urban agriculture, but also the need for greenhouse production,” Lefsrud says, adding that Lufa’s success has prompted more government investment in the sector overall.
“The Quebec government now takes this as a serious venture system, which then means that the students that I’m training, and research we’re doing here at the university, now have employment and have the possibility of setting up their own system,” says the McGill professor.
That idea, of developing more vertically integrated food systems, is a passion of Hage’s—not only for the idea of cutting out production and transformation middlemen to improve profit margins, but also to improve quality, traceability, and ultimately the ethics of food production.
“You know, every time we talk to someone about it, we feel like it’s the ’80s, and we’re holding a big solar panel trying to convince the room that this is the future,” Hage says.
As the larger agricultural industry catches on to vertical integration, it seems Hage and Rathmell are no longer mad scientists with a crazy dream. Instead, they are the voice of reason—and a new generation of food.
As the larger agricultural industry catches on to vertical integration, it seems Hage and Rathmell are no longer mad scientists with a crazy dream. Instead, they are the voice of reason—and a new generation of food.
As the larger agricultural industry catches on to vertical integration, it seems Hage and Rathmell are no longer mad scientists with a crazy dream. Instead, they are the voice of reason—and a new generation of food.
Is AppHarvest the Future of Farming?
In this video from Motley Fool Live, recorded on Jan. 28, Industry Focus host Nick Sciple and Motley Fool contributor Lou Whiteman discuss AppHarvest, one such SPAC that is looking to disrupt the agriculture industry. Here are the details on what AppHarvest wants to do, and a look at whether the company represents the future of farming.
Special purpose acquisition companies, or SPACs, are red-hot right now, with investors clamoring to get into promising young companies.
In this video from Motley Fool Live, recorded on Jan. 28, Industry Focus host Nick Sciple and Motley Fool contributor Lou Whiteman discuss AppHarvest, one such SPAC that is looking to disrupt the agriculture industry. Here are the details on what AppHarvest wants to do, and a look at whether the company represents the future of farming.
Nick Sciple: One last company I wanted to talk about, Lou, and this is one I think it's -- you pay attention to, but not one I'm super excited to run in and buy. It was a company called AppHarvest. It's coming public via a [SPAC] this year. This vertical farming space. We talked about Gladstone Land buying traditional farmland. AppHarvest is taking a very different approach, trying to lean into some of the ESG-type movements.
Lou Whiteman: Yeah. Let's look at this. It probably wouldn't surprise you that the U.S. is the biggest global farm exporter as we said, but it might surprise you that the Netherlands, the tiny little country, is No. 2. The way they do that is tech: Greenhouse farm structure. AppHarvest has taken that model and brought it to the U.S. They have, I believe, three farms in Appalachia. The pitches can produce 30x the yields using 90% less water. Right now, it's mostly tomatoes and it is early-stage. I don't own this stock either. I love this idea. There's some reasons that I'm not buying in right now that we can get into. But this is fascinating to me. We talked about making the world a better place. This is the company that we need to be successful to make the world a better place. The warning on it is that it is a SPAC. So it's not public yet. Right now, I believe N-O-V-S. That deal should close soon. [Editor's note: The deal has since closed.] I'm not the only one excited about it. I tend not to like to buy IPOs and new companies anyway. I think the caution around buying into the excitement applies here. There is a Martha Stewart video on their website talking up the company, which I love Martha Stewart, but that's a hype level that makes me want to just watch and see what they produce. This is just three little farms in Appalachia right now and a great idea. This was all over my watchlist. I would imagine I would love to hold it at some point, but just be careful because this is, as we saw SPACs last year in other areas, people are very excited about this.
Sciple: Yeah. I think, like we've said, for a lot of these companies, the prospects are great. I think when you look at the reduced water usage, better, environmentally friendly, all those sorts of things. I like that they are in Appalachia. As someone who is from the South, I like it when more rural areas get some people actually investing money there. But again, there's a lot of execution between now and really getting to a place where this is the future of farming and they're going to reach scale and all those sorts of things. But this is a company I'm definitely going to have my radar on and pay attention to as they continue to report earnings. Because you can tell yourself a story about how this type of vertical farming, indoor farming disrupts this traditional model, can be more efficient, cleaner, etc. Something to continue paying attention to as we have more information, because this company, like you said, Lou, isn't all the way public yet. We still got to have this SPAC deal finalized and then we get all our fun SEC filings and quarterly calls and all those sorts of things. Once we have that, I will be very much looking forward to seeing what the company has to say.
Whiteman: Right. Just to finish up along too, the interesting thing here is that it is a proven concept because it has worked elsewhere. The downside of that is that it needed to work there. Netherlands just doesn't have -- and this is an expensive proposition to get started, to get going. There's potential there, but in a country blessed with almost seemingly unlimited farmland for now, for long term it makes sense. But in the short term, it could be a hard thing to really get up and running. I think you're right, just one to watch.
Advice For New Vertical Farmers: Grower Spotlight on Andrew Worrall
Andrew is LettUs Grow’s Farm Manager, he manages two of our sites across Bristol and has brought a wealth of knowledge into the company through his previous experience in indoor farming roles across the UK including at Grow Up, Raynor Foods & RootLabs. In this three part interview, we explore what it’s been like to move from animal husbandry to indoor farming, the lessons he’s learned along the way, what it’s like working at LettUs Grow and his advice for those new to indoor growing.
Last week we spoke about running a farm at LettUs Grow. What excites you about vertical farming?
It’s the future of the industry. Also, the amount of salad that these farms can produce for their local community. We want to be able to eat salad all year round and we import to make that happen. However, just a small farm can easily provide for its local community, very efficiently and all year round. The sustainability element is also exciting: with our salad there’s no food miles, it’s very minimalistic. You could use an electric van or bike to distribute this crop if you wanted to. It’s a step forward in terms of what we need to do to take care of our planet.
What do you think are the biggest downsides to vertical farming?
It’s still a new technology and it can be expensive. The biggest roadblock facing the industry is that we need more people and companies to collaborate together to make sure we can build these farms at a sensible rate, so we can provide farms to anyone. We want to be able to provide farms to people, communities and countries that don’t have a lot of money, so that they can provide affordable fresh produce to local people.
How has vertical farming impacted your life?
Massively! I wanted to find my passion, a job that I loved - that was very important to me. It’s satisfying to be in a position now where I’m very happy to be doing what I do and I look forward to going into work. I was happy to make the move from London to Bristol. I would have moved even further if it meant being able to continue working within this industry.
Image from: LettUs Grow
How do you see vertical farming playing a part in the future?
When indoor farming first came about, it had a reputation of being competition for outdoor farming, which just isn’t the case. There’s so much we can’t grow that outdoor farming can provide, such as cereal crops. I’m glad we’re at a stage where indoor and outdoor farms can start to work together to optimise both methods. With these new relationships, there should be a good increase in the amount of indoor farms you’ll be seeing. What LettUs Grow offers with DROP & GROW™ is an exciting project because that’s a 40ft shipping container which can be placed pretty much anywhere. It’s not that big - it could go in a car park or behind a restaurant, but actually provide quite a lot of salad to that area.
How much of our food should be grown this way?
Good question. If you had asked me a while back I would have just said salad, but now I’ve changed my mind. Indoor farming can have a massive impact on propagation, especially aeroponics, because of how we aerate and nourish our roots. We could start lettuce for greenhouse projects and we can also propagate tomatoes, strawberries and tree whips. Propagating trees in this way could potentially be hugely beneficial and it’s something we want to do more of.
We can also quickly grow large amounts of microgreens, baby leafs, herbs and we can grow fruiting crops like strawberries. We are slowly chipping away and it’s really exciting. I’m waiting to see if I can ever say I’ve grown or propagated every crop that can be grown in these farms!
What do you think are the biggest benefits of vertical farming?
How fast these crops can grow! The turnover can be as short as 5 days from seed, depending on the crop. Also how clean it can be - I’m very dedicated to making sure these farms are built to ensure they are easy to be maintained and clean. The most exciting part is the crop growth rate though - it’s incredible how fast our crop grows from seed to plate. In a very well maintained growing calendar, which Ostara® is great for supporting, you can optimise your beds so that the day you harvest can also be the day you germinate onto that same bed. Your farms can be forever providing salad at very fast rates.
Image from: LettUs Grow
What was the biggest change you encountered during your years indoor farming?
Moving from being a production grower to an R&D grower. It has been a great change! As a production grower I knew what I needed to know about growing the plant safely and getting it onto a plate so it was good for the consumer. Now I’m fully optimising, learning and understanding the plants completely, so that I can help the grower that I used to be. We spend a lot of time on crop recipes to make sure that whoever we sell our farms to can start up very quickly and they won’t have to spend months developing their crops. If they have the customers and clients behind them, they can buy DROP & GROW and start producing salad as soon as it's been commissioned.
What was the biggest change you encountered in the industry?
More and more people are speaking about what’s going on in the industry and getting involved. I get so many messages on LinkedIn with people who want to get into this career. It’s exciting to see that indoor growing is a career people can access now. When I was developing my skills I didn’t know I would end up in indoor farming. There are more opportunities than ever before. For example, our Crop Technician is doing a placement here for 2 years. The aim is that they can gain the skill sets and knowledge they need to then go off and do the same practice in any farm they want.
What advice do you have for people who are looking to start a career in growing?
Reach out to companies who are already out there. You could start off part-time or as an assistant. If you are patient and dedicated then it’s a journey I promise you won’t regret. It takes a lot of work, but the outcome is amazing - you’ll be learning so much about this new technology. You’ll also build great relationships: there are so many amazing people in this industry who are so interesting, with different backgrounds, who are willing to share their knowledge. You can always learn more and other people are a great source of that.
What about for those looking to start a vertical farming business?
Do your homework. There are people out there who you can reach out to and it’s very easy to get information. It’s very easy to get excited about the idea and jump straight into it, because it is exciting and can be very rewarding, but it’s really important to do it step by step. Know how to scale properly, learning the differences between a small and larger farm. Understand how many people you’ll need and the logistics. I’d also advise people to get some practical work experience before you buy. You want to start the company knowing the tricks of the trade.
Image from: LettUs Grow
LettUs Grow Blog: www.lettusgrow.com/blog/advice-for-vertical-farmers
Offering The Complete Package, Thinking From A Plant Perspective
KG Systems has about any solution to vertical farming that can be thought of
“Nowadays, there’s very little growing space. Many growers have to grow in several places at the same time, moving their products around,” says Floris Berghout, International business development manager at KG Systems. “Therefore, when taking this problem into account, vertical farming is a valuable addition to horticulture. However, I do not think that vertical farming will replace traditional greenhouse growers.”
Over 15 years ago, KG Systems became involved with vertical farming. In 2006, the company constructed its first vertical farm inside a greenhouse, used for Lilly production, soon after that, a propagation cell followed for orchids. KG Systems has about any solution to vertical farming that can be thought of. This thanks to the experience they gained because of their involvement in many diverse projects over the years.
(F.l.t.r.) Matthias Haakman and Floris Berghout
“Many growers are involved with researching the propagation process in vertical farms as this cultivation process delivers stronger plants and better performance in the greenhouse,” Matthias Haakman, Account manager at KG Systems. “We always sit down with the client to analyze what the most appropriate solution would be for them. Here, we’re looking at the plants and what they need. We’re basically building a product around the plant the grower aims to grow. In terms of seeds, the system, etc.”
Floris says that the great thing about KG Systems’ technique is that they’re able to adjust any system to the plants. The team is working closely with flora, tomato, etc. growers. These systems are one big puzzle, but the company can deliver either one piece of it or more. “We’re working with many customers that are either upgrading their systems or wanting to install a complete new farm inside a warehouse, or elsewhere. In all these cases the same knowledge is implemented,” he says.
“The more projects we have done, the more we have been taught about the market. It has enabled us to see what techniques are available and that’s in our benefit. Therefore we can offer the best tailored solutions to our customers nowadays,” says Matthias.
KG Systems' installation at a tulip grower
According to Floris, it’s the trick to outline the situation. Meaning, what does the customer have in mind and then reason back to the plant. The client has its eye on a certain market where the product will be sold at a certain price. Therefore we need to know the following things in order to create the best solution for them. Such as, what does the plant need in order to grow, and how do we fit this into a multiple layer system, using what technique? Then we’ll draw up a balance in terms of budget.
KG’s technology is scalable in complexity. In other words, the company can deliver any system at any price, depending on the growers’ end goal. “We are there to help out with their market, potential buyers, you name it. If clients lack of market-, product- or customer knowledge, etc., the company directs them to a consultancy agency,” says Floris. This agency will educate them in every area needed and guide them into the right direction.
For more information:
KG Systems
Matthias Haakman, Account manager
Floris Berghout, International business development manager
info@kgsystems.nl
www.kgsystems.nl
Author: Rebekka Boekhout
© VerticalFarmDaily.com
Hydroponic Indoor Farm Plans To Be Among First Tenants In Downtown Piqua's Zolo Building
It was strategically placed in front of the Zollinger's building, a 40,000-square-foot former grocery warehouse planned as a mixed-use development with 16 loft-style residential units, a roof deck, community market/kitchen incubator and co-working space.
Fifth Season Farm, founded by a local brother-sister duo, has launched a hydroponic indoor farm inside a shipping container along Main Street in downtown Piqua.
By John Bush – Senior Reporter, Dayton Business Journal
A unique farming business has set up shop in downtown Piqua, and if all goes to plan the concept will be among the first tenants in an historic building being redeveloped in the city core.
Fifth Season Farm, founded by brother-sister duo Britt Decker and Laura Jackson, launched a hydroponic indoor farm inside a shipping container along Main Street. It was strategically placed in front of the Zollinger's building, a 40,000-square-foot former grocery warehouse planned as a mixed-use development with 16 loft-style residential units, a roof deck, community market/kitchen incubator and co-working space.
While the farm has been operating there for months, the long-term intention is to occupy space inside the the century-old building, which will be renamed the "Zolo." Chris Schmiesing, Piqua's community and economic development director, said the community market concept fits well with Fifth Season's business, and would be a welcome addition to the building.
"Part of the Zolo concept is the community market space, where local growers and producers can come and put their product on the shelves and begin to grow their business," Schmiesing said. "We're really excited to have Fifth Season Farm in there because we think it really represents the kind of innovative, entrepreneurial activity we want to see more of."
Unlike some traditional farms, Fifth Season does not use pesticides or herbicides, and utilizes non-GMO seeds. Powerful LEDs create a specific light recipe for each plant, allowing control over size and shape. There is no dirt, meaning the crops are free of bugs. The hydroponic system uses 90% less water by recycling the nutrient rich infused water in a loop system. Since it is weather controlled, temperature, relative humidity and CO2 levels remain constant all year.
"It is a complete, self-contained unit," Decker said. "The products also have a much longer shelf life because they are harvested to order."
Fifth Season currently grows about half-a-dozen varieties of lettuce, as well as specialty greens such as Swiss chard and kale. Decker said they are also growing small root vegetables such as radishes.
Currently, Fifth Season offers delivery through its website. Orders can be delivered up to five miles from its farm location, where customers can also come to pick up their products. Fifth Season produce can also be found on the Miami County Locally Grown Virtual Market. Decker said they are in discussions with local grocery stores, restaurants and gyms to carry their product as well.
When their space in the Zolo building is ready, Decker said they plan to open a marketplace and pickup location inside. He added the entire reason they placed the farm in that location was to be ready for when the redevelopment project is complete.
In June 2020, the Piqua Planning Commission unanimously approved a zoning change that allows for residential use within the building. The rezoning was a big administrative hurdle the project needed to cross, but the project still needs to be fully financed. The project missed out on the latest round of Ohio Historic Preservation Tax Credits, though Schmiesing said additional funding sources are being finalized.
Gamble Associates, a Massachusetts-based urban design and planning firm, is taking the lead on the Zolo project. Gamble Associates Principal David Gamble previously said the interior build-out will take between nine and 10 months to complete once it gets started.
Assuming everything aligns, Gamble said this project will create a "critical mass" that could have ripple effects throughout the city of Piqua.
"Piqua, in my mind, has reached an inflection point," he said in July 2020. "While there may not be a lot of transformation to date, there's been a lot of good planning and the city has very good leadership. Piqua is due for that next phase of growth. We like working here, and we're excited about this opportunity and what it can do for the city."
The One Thing You’re Probably Overlooking In Your Greenhouse
We often overlook the value of light in southern parts of the continent.
The cost of natural sunlight is an important thing for producers to understand because there is an economic value that they should be placing on sunlight. It’s one of the main inputs to production!
If you ask a good greenhouse operator, “What is your cost of natural gas? Electricity? Building cost per square foot? Operational cost per square foot?”, he’ll give you detailed answers.
Ask him, “What is the value of the light you receive?” and you’ll get a different response.
“…Uh, what?” he might respond.
You clarify. “The light, the sunlight. What is the value of the sunlight?
“I don’t know.” He will be taken off guard because he’s never thought about it before. Why?
Because people take light for granted. After all, sunlight is free. Why place a value on it?
But light is a “free” resource!
The cost of natural sunlight is an important thing for producers to understand because there is an economic value that they should be placing on sunlight. It’s one of the main inputs to production! If they’re placing an economic value on supplemental lighting, then they should be placing an economic value on natural light.
Why do they make that mistake? Because it’s free. Most people don’t put a value on free things.
And if a person places no value on a thing, they’re not going to use it efficiently. When something is free you don’t think about trying to use it in the most economical sense. When something is free you just use it.
Why would you try to conserve something that’s free? Why would you try to maximize the value of something that’s free? In your mind, it has no value.
This is true with sunlight. Because it’s (supposedly) a free resource, people don’t place an economic value on it and then they don’t build their model to maximize that value. The problem with this is that light does have a cost that can act as a limiting factor on your operation. This inefficiency poses a significant problem.
For instance, say you want to grow in Alaska. You want to grow year round but in the middle of the winter you might only have an hour of daylight – all of a sudden the economic value of that light becomes alarmingly apparent. Because you actually have to pay to replace it in the wintertime. So if you’re growing in Alaska in the wintertime, you’re freaking out about how you get the maximum value out of that light. You’re may choose to use red and blue LEDs instead of white because you can get more efficiency from them – even if it’s at a higher initial cost. You’re going to do everything you can to maximize the value of that resource.
We often overlook the value of light in southern parts of the continent.
And that’s why, even though light is a resource like everything else, no one actually figures it into any of their calculations, including the cost of goods sold. This mistake often limits growers to much lower production, or missing out on key observations that inform their model. (Among other things.)
In reality, the value of light is high
Note that the value and the cost of light are very comparable here. The value of something can be defined by it’s cost. Keep that in mind.
If you did think about light use efficiency, you would probably find yourself at the same destination that we did: volumetric farming, and much higher production because of it.
How to Place a Value on Light
If you don’t have light, then the easiest way to calculate it is by calculating the cost of replacing that light. What is the cost of replacing it with LEDs or HID or whatever supplemental lighting you choose?
If you do have light, then you’re probably growing in a greenhouse. In that case, you can find the cost of light by comparing the cost of growing in a greenhouse (which is how you are acquiring that light) with the cost of growing in a facility without that sunlight. (So the value of the sunlight is essentially the difference in operational cost between a warehouse of the same size and a greenhouse.)
These operating costs are going to include things like replacing a covering, heating (heating a greenhouse is always a lot more expensive), and maybe things like building permits.
Those costs can add up, and you’ll find that light is a costly resource even if you don’t think about it much. When you understand the costs of light, you will begin to use it more efficiently. You’ll start thinking about maximizing light use the same way that you maximize water and electrical and natural gas and other resources.
Initially this will result in lower overall costs, but we think you’ll find that your efforts toward efficiency will lead to even more benefits.
Once you do understand the value of your light, how do you get more out of it?
To increase light use efficiency, you first have to identify the main areas of waste and eliminate them. To do that, you start by identifying what’s happening with most of the light that enters your greenhouse: absorption and reflection.
ZipGrow Towers were designed to reflect light through the mass of towers to reduce shadowing and light waste.
Absorption is happening either when the light hits photosynthesizing plants or when it hits another absorptive surface and is either used by plants or turns to heat. Reflection happens when light hits a surface and bounces back. This is what you want, because if it’s not being absorbed by plants, then we reflect it to be absorbed by plants. (The less light energy that’s converted to heat, the more is conserved for use by your plants.)
The most obvious way to promote reflectance is to use reflective surfaces wherever possible. This doesn’t necessarily mean using silver or mirror finish, but it does mean white finishes to reflect that light. It also means that we think about growing plants on multiple planes, and arranging the production apparatus to conserve light within the greenhouse through reflection as opposed to reflecting it out of the greenhouse.
If you’re growing on a horizontal plane, know that if that light doesn’t hit a plant, oftentimes light will just be reflected back up and out of your greenhouse. When we switch the plane around so that the photons are conserved to the bottom of the mass, our absorption rates are higher, we have more plants absorbing energy rather than energy just being reflected up and out of the greenhouse. That’s the idea behind volumetric farming with ZipGrow™ Towers.
Source and Photo Courtesy of Agritech Tomorrow
Vertical Farming Takes Root In Taiwan
Taiwan is uniquely placed to benefit from the application of information technology to agriculture, enabling it to help provide food for an expanding global population.
Exposed root system for hydroponically grown plants at YesHealth's iFarm in Taoyuan. Photo: Jules Quartly
After becoming a world leader in semiconductors and other electronic products, Taiwan is now looking to smart agriculture as its next vine to climb. The island aims to supply much of the world’s fruit and vegetables within the next 30 years.
This might seem rather unlikely until you consider that the future of farming is not land and labor but factories and robots. Furthermore, Taiwan already possesses in abundance the tools that tomorrow’s smart farmers will use, including solar and advanced light technology, chemicals, gene editing, drones, smart sensors, software, algorithms, data mining, and big data.
Many of these technologies are being put to use in a glittering new 14-story vertical farm at Copenhagen Markets in Denmark’s capital. The first phase of construction of the 7,000-square-meter facility finished in early December. It is one of Europe’s biggest and most efficient vertical farms and was built using a blueprint of patented technologies from Taiwan’s YesHealth Group.
The result of a partnership between YesHealth and Danish agritech startup Nordic Harvest, the farm looks like a fancy warehouse from the outside. The interior is fitted with rows upon rows and columns upon columns of trays containing leafy greens, growing under an intense battery of more than 20,000 smart LED lights. The plants are tended by engineers in lab coats and guided by software that processes over 5,000 individual data points to optimize plant health.
Rows of fresh produce grown under batteries of LED lights at iFarm. Photo: Jules Quartly
The LEDs provide variable spectrum light for 100 different kinds of plants, nanobubble hydroponics oxygenate the roots and inhibit bacterial growth, and liquid microbial fertilizers derived from oyster shells, brown sugar, and soy milk provide essential nutrients for plants and soil. Even the music played to the plants is science-infused, with classical or light jazz music ranging between 115 and 250 Hertz seeming to work best.
Production at the new vertical farm is set to begin in the new year and will scale up to around 3,000 kilograms of leafy vegetables per day by the end of 2021, equating to approximately 1,000 tons of greens annually. Crucially, unlike most farms, these figures are close to guaranteed since production is not at the mercy of climate, the weather, pests and disease, pesticide residue, nitrate levels, or hundreds of other variables that affect traditional farming.
According to Jesper Hansen, YesHealth Group’s Chief Communications Officer, the partnership with Nordic Harvest has been a productive one so far. It took just five months to install the farm and all the produce is pre-sold to ensure the operation is profitable by Q3 of 2021.
“This collaboration is just the start of a long-term journey together,” Hansen said in an email from Denmark. He notes that the two partners plan to expand to other Scandinavian countries over the next several years.
Hansen credits Taiwan for its efficient development of the technology and know-how to reproduce vertical farms all over the world and calls the Danish development “a crucial milestone in our international expansion.” He adds that the company is eyeing new partners in Europe, Asia, and the MENA (the Middle East and North Africa) region.
YesHealth is the brainchild of serial tech entrepreneur Winston Tsai, who started an LCD screen company at age 21. His “eureka moment” came after being diagnosed with liver cancer and partly linking his illness to pollution in foods. After recovering, he made it his mission to produce affordable, pesticide-free produce by harnessing the power of technology.
He founded YesHealth Agri-Biotechnology Co. Ltd. in 2011 and six years later established YesHealth iFarm in Taoyuan’s Luzhu District. The iFarm cultivates an ever-expanding range of leafy vegetables and herbs in a 2,500-square-meter warehouse factory. It produces 1,500 kilograms of leafy greens per day, a yield which the company says is 100 times more efficient than a traditional farm using the same space and requires only 10% as much water. In addition, YesHealth has a farm in China’s Shenzhen, which harvests up to 2,500 kilograms per day.
A tour of iFarm is well worth a visit and introduces the wide variety of plants grown there. Photo: Jules Quartly
YesHealth’s products are sold to major retailers both in Taiwan and abroad, including restaurants, hotels, and airports. Its stated aim is to supply a total of 7,000 kilograms of leafy greens per day worldwide in 2021.
Diners enjoy a meal at iFarm’s restaurant, which overlooks the vertical farm. Photo: Jules Quartly
Having sampled the produce at the iFarm, I can confirm the arugula grown there is as tasty as any I have tried, while the lettuce and leguminous alfalfa is a perfectly clean, green, and crunchy eating experience – the result, I was informed, of an optimal growing environment and harvesting at exactly the right time.
A plate of salad featuring leafy greens grown at the iFarm site. Photo: Jules Quartly
In a sense, it’s back to the future for Taiwan, which had a largely agricultural economy up until the 1950s. Agriculture was one of the pillars supporting the nation’s economic miracle after World War II. With the help of mechanization and productivity gains, agricultural production at that time contributed around a third of Taiwan’s GDP.
In more recent times it has accounted for just 1.8-1.9% of GDP. That greatly reduced figure, which includes animal husbandry, fishing, and forestry, is not due to a decline in agricultural output per se, so much as the growth in manufacturing and the emergence of a pervasive service sector.
Taiwan has a wide range of rich, often volcanic soils that are exceptionally fertile, along with a subtropical climate that provides plentiful sun and rain. It is known as the “Fruit Kingdom” because of the quality of its fruit, with dozens of varieties ranging from bananas and papayas to wax apples and guavas. More than 100 kinds of vegetables grow all year round.
On the other hand, Taiwan’s mainly mountainous geography means just 25% of the land is suitable for farming. Meanwhile, climate change is affecting agricultural production by increasing summer temperatures and making rainfall more unpredictable. At the same time, considerable soil erosion, acidification, contamination by chemicals and heavy metals, and strong pesticide use have diminished soil quality over the last 50 years.
Furthermore, the proportion of Taiwanese involved in farming has rapidly declined, from 37% of the population in the early 1970s to the current 15% or less, according to the Yearbook of the Republic of China. Not only is the farming population declining, but it’s also ageing as well.
Those factors may not pose as much of an issue, however, since the old model of agriculture is being disrupted so dramatically that even economies of scale are being upended. Given the large size and advanced technology of the U.S., it may come as no surprise that it is the world’s biggest exporter of food as measured by value. Second on the list, however, is the Netherlands, which has just 0.045% the area of the U.S.
According to a National Geographic report in September 2017, the Netherlands’ achievement can be attributed to the work coming out of Wageningen University & Research, 80 kilometres from Amsterdam in the heart of Food Valley – the world’s agricultural equivalent of Silicon Valley in California. The university strives to come up with ways to increase yields and sustainability, and then to disseminate that knowledge.
New generation
With its strong background in information technology, Taiwan is in a good position to follow that example. The island manufactures everything required for what is known as precision agriculture, a farming management concept that uses IT to collect data from multiple sources as a means of increasing crop yields and boosting profitability. Taiwan is thus the ideal place for putting together prototypes relatively quickly and cheaply.
YesHealth, for example, makes its own LED lights through a local contractor rather than relying on a major manufacturer like Philips, which means it’s nimbler in terms of bringing focused, new tech to the market – and reaping the dividends. According to the company’s Program Manager, Dennis Jan, Taoyuan’s iFarm has the sixth generation LED lighting, while new iterations that are increasingly productive and energy-efficient are being rolled out on an almost annual basis.
The Council of Agriculture (COA) recognized some time ago the need for a precision approach to farming. In 2016, it developed the “Smart Agriculture 4.0 Program,” which was passed by the legislature a year later.
COA realized that the nation’s “calorie-based food self-sufficiency rate is relatively low” and that “shortages in food supplies and escalations in food prices” will inevitably occur as the world’s population expands from 7.5 billion to an expected 10.5 billion by 2050.
The Food and Agriculture Organization of the United Nations says that in order to meet the needs of all these additional people, about 70% more food needs to be produced. Gains achieved in improving crop yields have plateaued and are unlikely to rise again without a complete transformation of the agricultural landscape through the introduction of city farms, vertical farming, and the application of information technology.
In a written response to Taiwan Business TOPICS, COA commented: “With the rapid development of sensing technology, smart machinery devices, IoT, and big data analysis, smart agriculture has been growing in various fields.
“For example, it can monitor and control the production environment automatically to keep animals and crops in the best condition,” COA said. “It can predict harvesting dates and yields through data analysis and make adjustments to maintain a balance of production and marketing, and it can use smart automated machinery in agricultural operation to significantly reduce the labor burden.” Such uses, says the Council, “make agriculture more competitive.”
Fruitful results
Besides fruit orchards, other sectors that COA has included within Agriculture 4.0 include seedlings, mushrooms, rice, aquaculture, poultry, livestock, and offshore fisheries.
COA cites Taiwan Lettuce Village as an enterprise that has benefited from precision farming. The company halved fertilizer use but improved harvest efficiency 1.5 times by introducing a fertilization recommendation system, a harvesting date and yield prediction system, synchronous fertilizing technology, and transplanter and harvester technology.
According to COA the application of precision farming increased yield prediction accuracy by 5% and prevented 350 metric tons of overstocking. In addition, plant disease and pest control were improved through the use of a cloud-based system and machine learning algorithm. “The results were very fruitful,” COA concluded.
Agriculture 4.0 doesn’t just apply to the growing of produce; it also looks at the storage, transport, and export of goods. As an example, COA points to a relatively new fruit hybrid that was originally developed in Israel in the late 1960s. The atemoya – or pineapple sugar apple (鳳梨釋迦), as it is known in Taiwan – is a heart-shaped fruit with green, scaly skin. A cross between wax apples and the cherimoya (often referred to as Buddha’s head fruit locally), it has become synonymous with Taiwan and export success, much like the kiwi fruit and New Zealand.
Previously, 90% of the country’s atemoya exports went to China because it is so close. Later, the Taitung District Agricultural Research and Extension Station introduced a frozen whole-fruit technique that enables 95% of thawed fruit to have a “consistent ripening texture and dramatically improved the raw material quality.”
The technique involves a quick freeze to -40° Celsius, which inhibits bacteria, allowing the whole fruit to be transported at a fairly standard -18°C. After thawing, it can meet the rigorous food safety standards of Japan and South Korea.
Traditional farmers may harbor concerns about agriculture becoming a primarily manufacturing process, taking place under artificial light. However, Kevin Lin, Head of Business Development at YesHealth, insists that what the company is doing is still agriculture.
“This is nature; we are just optimizing it,” he says. “Sustainability is at the forefront of what we do, and our focus now is on ensuring the energy costs of vertical farming – such as heating and lights – are lowered and the source is sustainable.”
In this way, Lin says, Taiwan can produce cheap, healthy, and environmentally friendly food that can help feed the world, even as the global population approaches the staggering 10.5 billion mark.
IPO Planned To Improve Revenues Indoors
Light Science Technologies has gained the funding from Intuitive Investments Group plc (IIG), ahead of going public on the London Stock Exchange in the next six months.
8-01-2021| Business Live
“We believe that there is no better time to be involved in both agritech and medtech." A company which makes technology to improve indoor crop yields has received a £1 million investment ahead of a planned IPO.
Light Science Technologies has gained the funding from Intuitive Investments Group plc (IIG), ahead of going public on the London Stock Exchange in the next six months.
The business, based on the Hilton Business Park, Derby, provides lighting and plant growing and monitoring technology for agriculture in partnership with university research teams.
Its agricultural tech can be used in three main indoor settings – vertical farming (where crops such as tomatoes are grown in vertically stacked layers), greenhouses and medicinal plants.
Its patent-pending, sustainable light unit combines interchangeable LEDs, power and technology to help reduce costs and generate maximum yields over 25 years.
Its real-time monitoring and control technology can also be used to link technicians, farmers, and facility managers with their crops to provide instant production data.
Management said that with better light quality and energy savings, its light, science and technology products increase cycles.
It also supplies technology to clients in the electronics, audio, automotive, AI technology and pest control sectors.
The move to become a publicly listed company follows significant investment in its team and operations over the past few years which, the business said, has “brought to market a fully updateable, bespoke and intelligent lighting solution that provides optimal yield”.
The company is also due to launch its own in-house growth and laboratory service in the spring, focusing on plant growth and performance to help farmers with their crops.
Chief executive Simon Deacon said: “We believe that there is no better time to be involved in both agritech and medtech as two rapidly expanding sectors which are going to be responsible for spearheading some of the most significant global developments over the coming decade and beyond.
“IIG’s investment is not just a reflection of its commitment to LSTH as a fast-growing business backed by almost 30 years’ expertise in light technology but also of its awareness of the importance in achieving a better, more sustainable approach to agricultural production as well as pioneering potential life-saving solutions in digital health innovation.”
Light Science Technologies is IIG’s first investment following its own successful IPO and admission to AIM in December, as it seeks to attract investors with its life sciences portfolio.
IIG chairman David Evans said: “LSTH has the key ingredients for success; it has an excellent management team, a deep knowledge of the light spectrum and the application of that knowledge to areas where substantial growth can be obtained.
“I am personally excited about the potential diagnostic applications in the digital health sector, such as non-invasive haemoglobin measurement, as well as the developments in vertical farming technology that will underpin the long-term growth of LSTH.”
The investment follows recent funding for Light Science Technologies from Innovate UK which will see it work over the next six months with Nottingham Trent University to develop a growing sensor and transmission node for vertical farms.
Photo: Light Science Technologies designs lighting, science and plant monitoring technology.
Source and Photo Courtesy of BusinessLive
Combining Hydroponic And Aeroponic In Vertical Farming
Growers are finding new ways to drive the efficiency up and the cost down, and one of these solutions is vertical farming.
Generally speaking, horticulture operations can be quite expensive to operate; yet, growers can rely on hundreds of years of knowledge to improve the efficiency, so that those costs go down. At the same time, indoor farming cannot rely on such knowledge, and it is not uncommon to see cultivation facilities with huge bills at the end of the month. As the industry matures, growers are finding new ways to drive the efficiency up and the cost down, and one of these solutions is vertical farming.
LED technology
Nowadays, LED technology has made a huge leap forward, and Alvis Ma, the CEO of GrowSpec claims they are the industry standard. “Growers generally make the switch from HPS to LED for three reasons: increased yield, improved cannabinoid, and terpene content, and energy efficiency,” he explains. Thus, LEDs allow for vertical cultivation, which has a host of benefits, especially when it comes to space optimization.
“The VetriAero Planter system uses a mobile planting rack that reduces the ‘required’ indoor grow space area and extends the plant cultivation space by multiple tiers, maximizing growth space, increasing the yield and thus the profit,” Alvis Ma points out. “And if a grower wants to use one rack only initially, other tiers can be added later on: the helves can be connected to one another so that growers can modify the VetriAero Planter system length according to the size of the room.”
A very peculiar feature of this system is the integration of both aeroponic and hydroponic methods. “Instead of growing in soil, the roots are suspended in mid-air and surrounded by oxygen,” he adds. “The plant roots get misted directly with a nutrient-dense solution that gets sprayed to the roots every 3-5 minutes. At the same time, the remaining liquid at the bottom of our container ensures that, in the event of an emergency, there is still enough nutrient-dense liquid to sustain your plants for up to 48 hours.”
“Commercial indoor cultivation operations can be very expensive,” says Alvis Ma with GrowSpec. “And if you look at the cost of the real estate, added on top of substantial
power bills and staffing requirements, it becomes critical to find a way to increase profit and reduce overhead costs.” Exactly to respond to such a demand, GrowSpec has developed the VertiAero Planter system, a new vertical growing system. “One of the primary reasons why vertical farming is so attractive for growers is the improved performance of current LEDs,” Alvis Ma continues. “This is something that could not happen back in the day, as HPS has been the go-to lights for decades, and they produce a lot of heat; generally speaking, the plants have to be placed a couple of feet away from light to stay safe and healthy.”
Controlling the environment
Indoor growing, especially vertical growing, requires a particularly efficient airflow system to guarantee healthy growth for the plants. This has direct consequences on the growing environment. “Maintaining optimum temperature, humidity, and air circulation is challenging for all cannabis operations,” Alvis Ma remarks. “But in vertical growing, there is even more variability in macro and micro environmental conditions, because more plants make control more difficult.
That’s why the GrowSpec VertiAero’s multi-layer airflow solution improves the airflow rate in the micro-environment of the plant canopy by maintaining consistent plant canopy temperature and humidity, reducing the cultivation potential of harmful pathogens, and increasing the rate of photosynthesis by evenly distributing CO2 over the plant canopy. The system utilizes various sensors to detect crucial data points such as moisture change, for instance.”
Although such a system might sound complicated to use, user-friendliness and easiness of use are very well implemented. “The VertiAero Planter system integrates intelligent control and touchscreen control system so that your business can save up exponentially on overhead costs,” Alvis Ma points out. “At our core, we operate according to the highest standard, combining this with technology that respects our planet.”
For more information:
GrowSpec
Yuxin Industry Zone, Shishan Town, Nanhai, Foshan, Guangdong, China
+86-15914220731
Valoya Announces Departure of CEO
The company will continue to execute its strategy of bringing high quality, research-based horticultural LED lighting solutions to its crop science, medicinal plant and vertical farming customers globally
Valoya's CEO, Mr. Lars Aikala will leave the company in early 2021, by which time he will have served it from its founding, a total of 12 years. A search for the new Chief Executive Officer is undergoing. The company will continue to execute its strategy of bringing high quality, research-based horticultural LED lighting solutions to its crop science, medicinal plant and vertical farming customers globally.
“Valoya has come a long way from when we founded it in 2009. We now have a unique position in the market with our research-based, proven horticultural lighting solutions, which are appreciated by our customers globally. Our innovations and over 600 plant trials have enabled us to pioneer this market for more than a decade. We have built an international patent portfolio of 100+ granted patents, which demonstrates and protects our innovation. Our amazing team and our great resellers serve our customers in more than 50 countries with commitment and dedication.”, says Mr Aikala. He continues “Naturally we have also had to overcome several challenges during the years. The latest one, COVID-19 has again proven that the team strongly pulls together to win. I am very proud of the fact that in these challenging times we managed to deliver revenue growth in 2020 and more importantly we also exceeded our profitability targets. Valoya now has a strong foundation and I am sure Valoya’s future will be very bright.”
The change comes from Lars’s desire to go back to the intensity, thrills and challenges of creating new business. The Board of Directors and Lars agree that now is a good time to make the change. To ensure a smooth transition, Mr Aikala will continue working as CEO until a successor is in place.
"With his passion, relentless drive and unique expertise Lars made Valoya into the great company it is today. On behalf of the Board of Directors and the owners, I would like to extend sincere and best thank you to Lars for his very valuable contribution to Valoya's development", says Christer Härkönen, Chairman of the Board at Valoya.
About Valoya
Valoya is a provider of high end, energy-efficient LED grow lights for use in crop science, vertical farming and medicinal plants cultivation. Valoya LED grow lights have been developed using Valoya's proprietary LED technology and extensive plant photobiology research. Valoya's customer base includes numerous vertical farms, greenhouses and research institutions all over the world (including 8 out of 10 world’s largest agricultural companies).
Additional information:
Valoya Ltd, Finland
Tel: +358 10 2350300
Email: sales@valoya.com
Web: www.valoya.com
Facebook: https://www.facebook.com/valoyafi/
Twitter: https://twitter.com/valoya