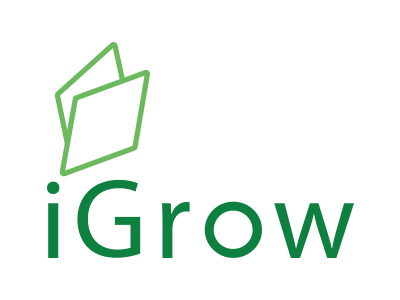
Welcome to iGrow News, Your Source for the World of Indoor Vertical Farming
Fifth Season Takes Vertical Farming to a Whole New Level
Fifth Season’s verdant baby spinach screams farm fresh even though it’s grown nowhere near traditional farmland. The sweet and slightly crunchy greens are grown in a Braddock warehouse on racks stacked 30 feet high. Located just a stone’s throw from U.S. Steel’s Mon Valley Works Edgar Thomson Plant, it is urban farming at its core
Image from: Pittsburgh Post-Gazzette
Fifth Season’s verdant baby spinach screams farm fresh even though it’s grown nowhere near traditional farmland. The sweet and slightly crunchy greens are grown in a Braddock warehouse on racks stacked 30 feet high. Located just a stone’s throw from U.S. Steel’s Mon Valley Works Edgar Thomson Plant, it is urban farming at its core.
What makes the vertical farming operation especially unique is that it is automated and robots call the shots. About 40 to 60 machines are involved in every step of the life of the spinach and other leafy greens, from planting the seed to providing nutrients to the final packing.
Fifth Season does employ local “farm workers” to assist the robots in seeding, harvesting, packaging, quality assurance and control using computer software, but there is no human touch involved through it all.
“The first time someone ever touches the spinach leaf with a finger is when the package is opened,” says Grant Vandenbussche, chief category officer.
Co-founded by brothers Austin and Brac Webb and Austin Lawrence, Fifth Season started a year ago. Within months it was rolling out its baby spinach, leafy greens and salad kits.
“We wanted a name that represents what we are doing,” says Austin Webb, 32, who also is the CEO. “It is a call to the fact we have created an entirely new season. It is 24/7, 365 with the technology we have built.”
None of them planned to become modern farmers, says the Carnegie Mellon University grad, but they turned to vertical farming because it was an efficient, economically sustainable way to solve land and water woes.
Image from: thespoon.tech
‘Fields’ of Greens
Fifth Season grows an equivalent production of 200 acres in 25,000 square feet of grow space. Its “fields” are stacked on top of one another in vertical shelves. When you add up all that surface area of grow space, it is more like 126,000 square feet.
“We also quickly turn crops at the farm,” Mr. Vandenbussche says.
While spinach takes about 40 days to grow outdoors and can be harvested only twice during its peak season, it takes the crop only three or four weeks to grow in the controlled environment and is harvested 19 times. Once the plants are harvested, a new cycle of reseeding begins with fresh media, seeds and nutrients.
“That’s why we get so much more productivity,” he says. “We are immediately reseeding our ‘land.’”
This controlled environment yields quality produce because it is always peak season at Fifth Season, says Chris Cerveny, who heads the Grow R&D division. Greens are grown in the same conditions year-round, getting the exact amount of nutrients and water they need. Because pests and airborne toxins also are kept at bay, crops can be produced without pesticides.
All that TLC comes through in the slightly curled baby spinach, which is sweet and not grassy. The leaf doesn’t wilt or get slimy or lose its slight crunch even after two weeks of refrigeration.
A lot of thought was given even for the curl, which gives the spinach a stronger volume, making it look full and bountiful. The curl also makes the spinach more forkable unlike its flat-leaf counterpart that is hard to stab on a plate.
Other leafy greens such as kale, mustard, Chinese cabbage, green tatsoi and purple pac choi are featured in two blends — Bridge City and Three Rivers. Fifth Season plans to roll out its Romaine lettuce in spring.
The greens also are found in four types of salad kits — Sweet Grains (blended greens, quinoa, chickpeas, corn, feta and poppy seed dressing), Crunchy Sesame (blended greens, farro, sesame sticks, dried cranberries and ginger-mandarin dressing), Toasted Tuscan (spinach, lentils, sun-dried tomatoes, bagel chips and vinaigrette), and Spiced Southwest (blended greens, black beans, pepitas, cotija cheese, corn-salsa sticks and chipotle ranch dressing) — which are available online and in Giant Eagle stores. A fifth salad kit is in the works and is being called “a shakeup of one of the most classic salads.”
While machines are a big part of what Fifth Season does, it seeks to keep human connection alive. It recently launched a recipe blog for those who have an appetite for cooking and writing, The Green Room is devoted to cataloging personal memories, dream meals and recipes via short stories.
Fifth Season also has partnered with the Penguins and is providing greens for the team’s pregame meals for the 2020-21 season.
“We want people in Pittsburgh to be able to eat the exact same delicious blend of greens that Sidney Crosby and company are eating,” Mr. Webb says. “We want people to know that there’s a new way to grow food and to eat and experience it.”
Image from: Next Pittsburgh
It’s All Under Control
Everything from seeding to packaging is done in four rooms. The process starts in the seeding and processing room, where seeds and growing media are placed inside black planter-like boxes called inserts. Each has a unique code that’s traced by a software system. The inserts go on white trays that pass through a photo station, feeding information to the computer system, and then glide into the bio dome.
There are two rooms in the bio dome, each with a grow space of 12,500 square feet. They’re lit up with a pinkish-purplish glow from high-efficiency LED light bulbs that mimic the different seasons of the year.
“They are positioned over the plants at different heights depending on stage of growth,” Mr. Cerveny says. “This is partly how we can provide consistently ideal growing conditions.”
As the plants grow, they are moved by a robot to optimize their growth cycle. Full-grown crops are transferred to the harvesting room by another robot.
“Harvesting is where it becomes like a Willy Wonka factory,” Mr. Vandenbussche says.
Long rows of trays filled with tiny plants are sent on a conveyor system to a station where workers inspect them for quality with surgical tools. After inspection, the plants are harvested by a robot and then immediately ride up a tall conveyor to be packaged and sealed in a 34- to 36-degree room so they remain fresh.
“Every crop we grow gets evaluated for maximum flavor, volume, crunch and color,” he says.
The plants’ intense, dark color is controlled by LED light bulbs, which are dialed up or down to get the correct hue. Although they never see the sun, the greens don’t get into a funk as humans might.
“What humans see in terms of light and how chlorophyll responds during photosynthesis are two different things,” Mr. Cerveny says. “Plants really only need red and blue light to grow effectively. We include some additional colors to help bring out other quality aspects of our crops, but providing the full sunlight spectrum is effectively a waste of energy, especially indoors.
“To the human eye, it looks like the plants live in a land of purple and pink lights, but they are perfectly happy there.”
Even though the environment is controlled and the software system is constantly updated, no two plants are exactly the same. Some fight for light more than others. Some might fail the quality control test and end up in a compost waste facility if their flavor is off or their color is not right.
“That is what is so amazing. We have more control than any other farmer, and yet we have limitations. Every seed is different,” Mr. Vandenbussche says. “They are plants. They are real living organisms.”
Agritecture Partners With Harvest Returns Crowdfunding Platform To Modernize Urban Agriculture Financing
The two companies will work together to accelerate the urban farming and controlled environment agriculture (CEA) industry across the country by offering new entrepreneurs a more accessible way to raise capital. This type of farming can reduce the environmental impact of the food system and increase local food security
Image from: Harvest Returns
Fort Worth, Texas – Agritecture, LLC, an urban farming consulting and digital services firm, announced it has partnered with Harvest Returns, an agriculture investing platform.
The two companies will work together to accelerate the urban farming and controlled environment agriculture (CEA) industry across the country by offering new entrepreneurs a more accessible way to raise capital. This type of farming can reduce the environmental impact of the food system and increase local food security.
“The COVID-19 pandemic has revealed the fragility of centralized food production,” said Chris Rawley, CEO of Harvest Returns. “Developing additional indoor farms will distribute growing operations closer to where food is consumed, creating a more resilient food system.”
In 2020, the USDA offered the availability of only $3M in grants for urban agriculture and innovative production. Agritecture notes that the average CapEx, or startup cost, for controlled environment farms modeled via their Agritecture Designer digital platform is $512,000, and nearly one-third are over $1M.
Image from: Urban Ag News
“Since our founding in 2014, we’ve seen sustained, year-over-year growth in interest toward urban agriculture, especially amongst industry newcomers,” said Henry Gordon-Smith, Founder and CEO of Agritecture. This growth has only accelerated since the onset of the pandemic, according to the team at Agritecture, which reported nearly a 2x increase in website traffic since Q1 of 2020.
“Despite this increasing interest and the record levels of funding for the handful of indoor mega farms, financing continues to be one of the primary challenges for small and medium-scale CEA businesses,” Gordon-Smith notes. “Yet, we know these farms can achieve profitability with competitive payback periods, while still serving their local markets and communities.”
Gordon-Smith cites Agritecture’s 2019 and 2020 Global CEA Census Reports, produced alongside agtech solutions provider Autogrow, which show that nearly half of all CEA facilities are being started by those with no previous farming experience.
Furthermore, per their recent census, 78 percent of CEA business founders who attempted to raise money were unsuccessful in doing so through traditional financing sources, such as banks.
“By teaming up with Harvest Returns and their innovative financing platform, we can now deliver a direct link from our planning services and digital platform, Agritecture Designer, to funding opportunities for these smaller-scale facilities,” added Gordon-Smith.
How Vertical Farming Will Shape The Post Pandemic Food Supply Chain
We're building for a future where modular vertical farming solutions are an accessible means of food production in urban areas. By modular vertical farming solution, we are referring to turnkey grow systems from the size of a shipping container down to a household appliance.
We're building for a future where modular vertical farming solutions are an accessible means of food production in urban areas. By modular vertical farming solution, we are referring to turnkey grow systems from the size of a shipping container down to a household appliance.
Q&A with Alexander Olesen, Co-Founder | Babylon Micro-Farms
Tell us about yourselves and Babylon Micro-Farms.
While still taking full course loads at the University of Virginia, we were actively involved in the Social Entrepreneur Program, a reflection of our values and determination to incubate a socially good company. Our original vision of starting an environmentally responsible company to provide fresh food to refugees living in camps by building hydroponic farms was put to the test when logistical realities of adequate power supply and access to clean water forced them to put that aspect of the business on hold. We became determined to develop a technology-based solution reducing the cost, complexity, and infrastructure requirements to grow fresh food. This technology is the backbone of Babylon’s platform today, the R&D has taken a dedicated effort for over 4 years. Our commitment to building Babylon into a successful company required an unforeseen amount of perseverance and we ran into a few issues along the way. We're now a team of 23 people working tirelessly towards the same goal of creating an integrated platform for modular vertical farming. It's inspiring to work alongside so many talented people and it's so rewarding to see how well our products are being received in the market and we're just getting started.
How have your customers' priorities shifted due to the pandemic?
Our institutional customers, predominantly from the education, healthcare, hospitality, and senior living spaces, have had a completely different set of priorities since the advent of COVID. We have been amazed at their complete commitment to their people - staff, students, patients, residents, and visitors. They were required to do an incredibly hard, fast pivot to safeguard the safety of the people they are responsible for and to and have done an outstanding job. Schools had to close their doors and learn how to operate virtually, hospitals were hit hard and continue to be, and the hospitality industry will take some time to recover. Senior living community residents have been the most vulnerable to the pandemic and the protocols that were put in place almost instantly have saved many lives. We are proud of how our partners responded to the ongoing public health crisis and that in the midst of all the challenges we continued to be able to supply them with fresh food, despite the lockdowns and quarantines. Our remote management system enabled us to make sure at least one thing stayed consistent for our partners during a difficult time for them.
How do you feel urban farming, and specifically modular indoor farming, addresses these new problems and priorities?
1. Supply chain resiliency - We provide peace of mind that fresh produce is being grown there on-site.
2. Reduced Food waste - Our customers love harvesting highly-perishable produce as needed and not having to waste anything
3. Improved Nutrition - We have much higher quality produce that is free from pesticides and it's helping our customers improve their diets.
How has the pandemic shaped the trajectory of indoor farming?
The pandemic has focused a very bright light on the frailty of our food systems and supply chain. The growth of the indoor farming industry has been rapidly escalating as a result, as demonstrated by the enormous sums being raised by companies that are actively involved in addressing the vulnerabilities and trying to ensure a safer, more sustainable, and hopefully a more equitable food system for the future.
Why is Babylon’s software platform important to the industry? How is it different from what’s out there today?
We're solving a very different set of problems to most people in this industry. We're building for a future where modular vertical farming solutions are an accessible means of food production in urban areas. By modular vertical farming solution, we are referring to turnkey grow systems typically from the size of a shipping container down to a household appliance. We do not compete with the large industrial growers at all. Most companies in this emerging segment are focused on creating configurations of hydroponic systems to optimize specific markets, aesthetics, or certain crop varieties, etc. There's nothing wrong with that and it's exciting to see all the innovation. However, our firm belief is that there is not a one size fits all solution to this market and that every modular vertical farming solution shares the same scalability challenges. These are the challenges we are trying to address through our remote management platform. The platform enables us to control semi-automated hydroponic systems through the cloud and aggregate the data from all the farms in our fleet. We combine this with an automated inventory fulfillment system that enables us to prepare and ship consumables to our customers while they interact with their farm through a simple app. The software infrastructure we are developing creates a superior user experience for the end consumer and provides data analysis that is critical to scaling support for a distributed network of vertical farms. In this way, we seek to be an enabling platform that can help grow the market for modular vertical farming solutions as an accessible alternative to large scale, capital intensive, commercial growers.
What is Babylon’s vision for the future?
See above. We envision a world where controlled environment crop cultivation becomes the predominant source of major highly-perishable produce categories, such as, leafy greens, herbs, vine crops, berries, etc.. As the market grows we need modular vertical farming solutions that are accessible and can scale more easily than the large scale, capital intensive, commercial operations that dominate the headlines today. These solutions are not mutually exclusive and we need both in order to reform our food system. New technologies and new business models are making modular vertical farms viable. We're aiming to be the platform that drives this segment forward.
About Alexander Olesen
Alexander Olesen, CEO, and Co-founder of Babylon has embraced and excelled at every opportunity he has encountered, from academic challenges to bootstrapping his second company, Babylon Micro-Farms, at the age of just 21 while still taking a full course load at the University of Virginia. Originally from England, Alexander relocated to attend the University and was actively involved in the Social Entrepreneur Program, a reflection of his values and determination to incubate a socially good company. The original research into the technology that became the basis for Babylon's success was based on research to provide low-cost food systems for refugees. He maintains the vision for the company and is an expert at managing people and bringing on partners and investors.
The content & opinions in this article are the author’s and do not necessarily represent the views of AgriTechTomorrow
[WEBINAR] Hiring For Indoor Farming | Human Resources In 2021
During this insightful session, our panel will touch on the hot areas of hiring in the Indoor Vertical Farming market today
WHAT'S HAPPENING IN THE INDOOR FARMING JOB MARKET? JOIN THE CONVERSATION & FIND OUT!
SAVE YOUR SPOT
HIRING FOR INDOOR VERTICAL FARMING: HUMAN RESOURCES IN 2021
WEDNESDAY, FEBRUARY 17, 2021
2-3 PM EDT
During this insightful session, our panel will touch on the hot areas of hiring in the Indoor Vertical Farming market today, including:
• Disciplines Hiring Manager are Seeking (computer science, A/I, robotics, engineering, & more)
• Expansion and Hiring Regions
• How Academia Can Help With Farmers of the Future | NextGen Farmers
MODERATOR
Tim Hammerich, Senior Director for Strategic Communications, Cogent Consulting and creator |host of “Future of Agriculture” podcast
PANELISTS
MaryAlice Feinstein, Chief People Officer, People Operations, AeroFarms
Brac Webb, Co-founder, and CTO, Fifth Season
Keri Gasiorowski, Chief Human Resources Officer, Kalera Inc.
LEARN MORE & REGISTER
SPECIAL THANKS TO OUR INDOOR AG-CON
EXHIBITORS, SPONSORS, MEDIA ALLIES &
INDUSTRY PARTNERS
Indoor Ag-Con, 950 Scales Road, Building #200, Suwanee, GA 30024, United States
Pontus Submits Building Permit Application for Surrey Aquaponics Facility
The Company has submitted a construction application to the City of Surrey for its 20,570 square foot aquaponics facility. The approval process is estimated to be completed within 6 weeks and is expected to be followed by the immediate commencement of construction of the Facility's leasehold improvements. Accordingly, the leasehold improvements are to consist of a complete retrofit of the Facility to establish Pontus' solar-powered, water recycling CEVASTM aquaponic system
VANCOUVER, BC, Feb. 3, 2021 /CNW/ - Pontus Protein Ltd. ("Pontus" or the "Company"), is pleased to announce it has made significant progress towards the development of its state of the art, integrated aquaponics facility located in Surrey, British Columbia, Canada (the "Facility").
Image from: CNW Group/Pontus Protein Ltd
The Company has submitted a construction application to the City of Surrey for its 20,570 square foot aquaponics facility. The approval process is estimated to be completed within 6 weeks and is expected to be followed by the immediate commencement of construction of the Facility's leasehold improvements. Accordingly, the leasehold improvements are to consist of a complete retrofit of the Facility to establish Pontus' solar-powered, water recycling CEVASTM aquaponic system.
The installation of all required equipment for the growth and production is forecasted to take between four and six months to complete. Upon completion, the Facility will be approximately 20 times the size of Pontus' prior prototype facility. The prototype facility has been used to test and develop the technology for the Company's proprietary growing process.
The Facility, as seen in the image above and video below, will utilize an array of additional technologies to create a clean and sustainable aquaponics ecosystem. Solar energy panels will be installed to capture renewable energy and power the closed-loop water system, which recycles up to 95% of all water inputs. The implementation of the Facility's unique, sustainable technology in conjunction with Pontus' proprietary CEVAS™ automated growth technology will allow the Company to emphasize biosecurity in its agricultural production processes, removing the need for additional chemicals, pesticides, and other non-native components.
Pontus CEO, Conner Yuen states: "Entering the construction application process is a major milestone for the Company as we move toward the commissioning of the Facility. Our aim is to create a state of the art process that will incorporate the latest in sustainable agriculture technology. The ability to implement this highly efficient technology solves many issues we see with current methods of food production such as land scarcity and low yields and contamination.
Pontus' biosecurity and renewable food sources are intended to create a proactive solution to these issues by reducing the potential for contamination and the need for pesticides. Pontus hopes the Facility will revolutionize how traditional agriculture is conducted and show the power of technological food advancements."
Plant-based Protein Powder Market
The Company's plant-based protein powder is a premium entry into the global protein and supplements market, which is currently valued at USD$15 Billion and is expected to grow to USD$20 Billion by 2025 according to Grand View Research. This growth is expected to be fuelled by many North Americans reducing or eliminating the regular consumption of animal products. The North American plant-based protein market is also anticipated to grow at a compound annual growth rate of 14% from 2019 through 2025.
About Pontus Protein Ltd
Pontus Protein Ltd. makes pure plant-based protein powder sourced from nutritious water lentils, farm-grown in Vancouver, BC, with development plans to expand to Surrey, B.C.. Not only does Pontus Protein Powder exceed certified organic standards, but it's also gluten-free, pure and allergen safe. It's jam-packed full of antioxidants, minerals, vitamins and ALL the essential amino acids.
This is not your average lentil, these are water lentils; a crop that can be harvested every 24 hours in an indoor aquaponic farm that uses 95% less water than traditional agriculture, using Pontus' proprietary Closed Environment Vertical Aquaponics System (or CEVAS™) aquaponic agritech technology. This is wonderful news for a planet populated with us hungry and health-conscious humans.
Reminder For Tomorrow: WIA Meet Up
Take a moment to get a fresh perspective from your peers
There is still time to sign up for tomorrow's
WIA Meet Up.
Take a moment to get a fresh perspective
from your peers.
Register Today
See you there!
Women in Agribusiness Team
eventinfo@highquestgroup.com
Farm In A Box Planned For Bridgeport's East End
BRIDGEPORT — You will not find any vast acres of fertile soil and crops in the East End neighbourhood. So the state, city and area activists have teamed with an entrepreneur on what they all said they believe is the next best thing: farmland in a box
Image from: CT Post
BRIDGEPORT — You will not find any vast acres of fertile soil and crops in the East End neighbourhood. So the state, city and area activists have teamed with an entrepreneur on what they all said they believe is the next best thing: farmland in a box.
Joe Alvarez, founder of High Ridge Hydroponics of Ridgefield, describes it on his website as “an indoor, vertical, hydroponic, shipping container farm to be located in the most urban settings throughout the world.” And the East End — which has been labeled a “food desert” because of the lack of fresh edibles easily available to residents there — will be that urban setting.
“We’re very excited about this,” Keith Williams, head of the East End Neighborhood Revitalization Zone community group, said during a teleconference Friday announcing a $49,999 state grant for Alvarez’s project. “Fresh vegetables. Healthy. That’s what we’re all about — healthy eating.”
High Ridge’s container will produce young micro-greens from broccoli, kale, cabbage, arugula and other plants to be sold at the East End NRZ’s market as a salad mix.
“These greens are harvested after only 10 to 14 days from being planted, which is extremely quick (and) they are super concentrated in nutrition,” Alvarez said.
Friday’s teleconference included several dignitaries who pledged to do everything they can to ensure High Ridge’s success in town, including Lt. Gov. Susan Bysiewicz, state Agriculture Commissioner Bryan Hurlburt, state Sen. Marilyn Moore, state Rep. Andre Baker, Mayor Joe Ganim and Edward Lavernoich of the Bridgeport Economic Development Corporation.
“I hope this project has a lasting and positive impact on your community,” Bysiewicz said. “And I hope it will become a model for other urban areas in our state to grow their own food using innovative technology and techniques.”
“This is not just a shipping container in the city,” Hurlburt said. “This is a much larger, deeper and richer project that we get to celebrate today.”
State Rep. Joe Gresko, D-Stratford, was also included, but wearing a different hat. Gresko works for Ganim continuing a mission started by former Mayor Bill Finch to turn Bridgeport from an ex-manufacturing hub into a leader in the green and environmentally sustainable economy.
It was under Finch that the East End was previously promised an urban green house on the site of the former “Mt. Trashmore” illegal dump. That project, dubbed “Boot Camp Farms” because it would hire veterans, was announced in 2013 and was also supposed to have financial backing from the state. But the developers had no prior experience in that field and the proposal never broke ground.
Alvarez, according to his online biography, “studied environmental science at Fordham University in New York City, graduated in May of 2017 (and) has worked as a private organic gardener, an aquaponic farmer, built greenhouses, maintained greenhouses and designed several custom hydroponic growing systems.”
Hurlburt said he felt confident the new project would be a success.
Alvarez “has limited experience but he knows what he’s doing. ... I know how much Joe was calling us and emailing us and how badly he wanted this grant to make it a reality. I know his heart is right where it needs to be to make it a success.”
“We’re all in this together to make sure Joe has the support he needs to be successful,” Hurlburt emphasized.
There are still important details to be finalized, including getting a site for the shipping container and additional money to cover the full, nearly $150,000 cost. Gresko said that the NRZ was negotiating to use some property and that “when the time comes” Bridgeport will “match” additional private funds Alvarez obtains.
“We’re going to keep an eye on this and troubleshoot as we go forward any issues,” Gresko said.
Alvarez said he hopes to complete construction by the fall. And the colder months are when his crops will be the most needed, said Deborah Sims, who operates the NRZ market.
“After farmer’s market season is over, we have difficulty sourcing (fresh food),” Sims said.
“Three hundred sixty five (days) we’re going to have the greens available,” said Gresko.
Baker recalled how his East End funeral home has hosted some farmer’s markets and called the High Ridge project “a long time coming.” He also told Bysiewicz he hoped similar initiatives to offer more fresh food to his constituents will follow.
“Lieutenant governor, we’re going to be leaning on you and the governor for more support,” he said. “You’re going to hear more from us.”
Forget Politics, Danny Ayalon Wants to Effect Change on The Ground
Having transitioned from politics to agriculture, Danny Ayalon shares how vertical farming, which provides fresh fruits and vegetables all year round, and lab-grown meat can rehabilitate the environment and dramatically reduce household expenditures
Having transitioned from politics to agriculture, Danny Ayalon shares how vertical farming, which provides fresh fruits and vegetables all year round, and lab-grown meat can rehabilitate the environment and dramatically reduce household expenditures.
Image from: Yehoshua Yosef
The coronavirus pandemic has drawn attention to humankind's carbon footprint. More than ever before we ask ourselves, how can we become more sustainable? Can we prevent pollution? How can we minimize waste? What about lowering emission levels? Will there be enough food for everyone in the future?
Danny Ayalon, a former ambassador and foreign policy adviser to three prime ministers-turned entrepreneur, believes that the answer to many of the world's problems lies in modern agriculture.
Having transitioned from politics to agriculture, he works with Future Crops, an Amsterdam-based company focused on vertical farming – the practice of growing crops in vertically stacked layers that often incorporates controlled-environment agriculture, which aims to optimize plant growth – and MeaTech, a company that creates lab-grown meat.
"Ever since the coronavirus came into our lives, we realized that man is not in charge of the universe," Ayalon told Israel Hayom.
"Our control over the forces of nature, of Earth, of our future is more limited than we had thought. And when we are no longer in charge of the world, only three things guarantee our lives here: food, water, and energy security. Food, water, and energy are three resources that can be depleted and therefore literally cast a cloud on our world.
"Experts have come to a conclusion that one of the most important fields to focus on is agriculture, and indeed we are currently witnessing the most significant agricultural revolution ever since the first agricultural revolution that took place about 10,00 years ago."
Q: Back then, in the first agricultural revolution, there was a need for a lot of land.
"But today we have technology. The name of the game is to reach maximum output with minimum input in the smallest space possible. This is the holy grail of the new revolution. And that is how technology enters the picture. To grow fruits, vegetables and spices today requires lots of space. The technology we developed at Future Crops allows us to minimize the space, increase production and redefine the food supply chain."
Q: How exactly?
"We have a nine-story hangar in Amsterdam to grow crops like coriander, basil, dill, and parsley. It has LED lights, and each plant gets exactly the amount of light it needs. We are the plant psychologists, [we] listen to all its needs and do everything to make sure the plant grows in the most optimal way.
Image from: Future Crops
"If it lacks something, it immediately receives water. Everything is done without a human's touch. We use algorithms and big data in collaboration with world-class researchers from the Weizmann Institute. It is essentially the application of vertical farming, growing various crops in vertically stacked layers, in enclosed structures, on soil platforms.
"For example, if it takes a month to grow lettuce in an open field, in a vertical farm, it takes two weeks, half that time. There's also a significant reduction in water consumption, and no pesticides or sprays are used at all. Also, the produce is available in all seasons; it does not depend on the temperature. Whoever likes mangos and strawberries, for example, will be able to enjoy them all year round."
Q: So if produce is grown faster and within a smaller space, is it going to cost less?
"The prices might be a bit higher today because this technology and the various infrastructures require an economic return of the initial investment in them. With time, the process will become more efficient, and the investments will be repaid, so in the end, the prices that the consumer will need to pay will be lower than today.
"Let me give you a simple example. Do you know how much a kilogram [2.2 pounds] of basil costs in Europe today? €90 ($108). In Israel, the price is €20 ($24). In the [United Arab] Emirates, where almost everything connected to food is imported – the prices go accordingly as well. Once you have more innovative vertical farms, consumers will pay much less."
Q: Should we expect vertical farm skyscrapers to pop up all over?
"I'm not sure that we will need skyscrapers, as with time the facilities will become smaller. Imagine that in every supermarket there will be a vertical produce stand with all the vegetables and spices, and later also fruits which you pick on the spot, without the need to move the produce from place to place. That is why vertical farming is also called urban farming, meaning there is no need for fields; you can grow [produce] on the rooftop. No resource limits you."
Q: What about the taste?
"Ours is a fresher and tastier product. I ought to give credit to the Weizmann Institute here. The challenge for them wasn't the quality of the vitamins but the taste, and they managed to achieve a great taste. In the Netherlands, Future Crops already sells parsley, and it tastes outstanding."
Q: Regular parsley lasts for about two weeks in the fridge. What about Future Crops parsley?
"Our parsley has a two-month shelf life, and it does not oxidize within a week or two."
Q: If every country will be self-reliant in terms of agriculture, do you think it will affect relations between countries?
"Economies will become self-sufficient eventually, which will ensure security with far fewer conflicts. There is less and less water in the Middle East, which might someday lead to tensions. We hope technology will reduce the tensions between countries, and territory will be less critical. Our world faces crucial challenges. Food and water security have the potential to either divide or bring us together and ensure our long-term existence.
"By the way, in every developed Western country, like the United States, Australia, and also in Europe, issues of food security, climate, and greenhouse emissions are on the top of the political agenda. We are not talking about it [in Israel,] as security and foreign affairs take the central stage, but Israel does have a lot to offer here."
Q: Do we have the potential to become the Silicon Valley of advanced agriculture?
"Israel takes tremendous pride in its actions that help save the world. Will we become the Silicon Valley of agriculture? There is no doubt about it. We can already see foreign investors who come here to look for opportunities, including my business partner Lior Maimon, co-founder and CEO of Silver Road Capital, and Steven Levin, one of the leaders of the US food industry. Silver Road Capital is a holdings and financial advisory firm with a broad portfolio of high-tech companies, as well as agricultural and food technologies, and represents international companies and funds in investments in Israel and the world.
"Future Crops's goal is to raise 35 million shekels on the Israeli stock exchange to invest in enlarging the existing facilities and [set up] other production lines and facilities in Europe and other continents. We cooperate with the Albert Heijn supermarket chain [in the Netherlands] and a leading food chain in France."
Q: Vertical farming is estimated at $3 billion. Google and Amazon have invested hundreds of millions in the field as well. What is their goal?
"A simple answer would be profit. A longer answer is that they [large corporations] understand that food has the highest demand. People cannot live without food and water, and Google and Amazon understand that potential."
Q: US President Joe Biden took office with the largest team of climate experts ever. That ought to give the field momentum.
"Green energy and vertical farming will get a considerable boost. Climate change and green energy are well-rooted in the Democratic Party's ideology.
"It is also possible that large companies entered the agriculture fields precisely because of the Biden administration; they are worried about their future. They are afraid of a certain dismantling, so focusing on secondary fields is part of a security scenario for them."
Q: Biden also wants to address greenhouse emissions, which are the result of the food production industry, mainly meat. Are Amazon and Google's food counterparts - McDonald's and Burger King - looking for meat substitutes?
"Firstly, cultured [lab-grown] meat does not require grazing land, cows do not need to be fed, and so much land can instead be turned into forests that support the environment. This is an optimistic industry that leaves us with a better world.
"As for the meat alternatives market, there are two major companies in the US that produce plant-based protein, Beyond Meat, and Impossible Foods.
"Impossible's burgers are already at Burger King, McDonald's has partnered up with Beyond Meat, and last November, it announced that it would create its own plant-based burger.
"The problem is that pea protein [used in plant-based burgers,] does not have all the amino acids that animal protein contains. Also, they need to add additives to supplement for taste and smell.
"At MeaTech, where I'm a director, we are on our way to producing animal meat, cultured meat, real stakes: we take a cow's own stem cell from which meat can be produced in almost unlimited quantities. We also use 3D digital printing technology. And we also created a thin layer of meat, carpaccio. Needless to say, no cow was harmed in the process."
Image from: MeaTech
Q: Why do you use 3D printers?
"Because there is no need for a human being's involvement. It is relevant now during the coronavirus pandemic when the food supply chain is disrupted. With such printers, your production can continue without delays, whenever you want.
Also, it is theoretically possible to provide food for space flights. Astronauts who go out into space will not have to take food with them; rather, they will be able to produce it on the spot.
"People understand that crises like the coronavirus can disrupt the supply chain and are looking for alternatives. A 3D printer allows restaurants, supermarkets, and butcher shops to have meat without relying on the supply chain."
Q: The death rate from obesity is higher than the death rate from hunger. How will cultured meat affect these statistics?
"It is possible to create meat with much less fat and more protein in each portion and add various nutrients in the future to strengthen the immune system and prevent disease. This, of course, requires a lot of research and approvals. Just like there's talk about customized medicine, so it will be possible to produce food that suits a person's genetic structure and body in the most optimal way."
Q: Will the cost of this meat also be optimal?
"They will cost more in the beginning compared to regular meat because there are initial costs that have to be repaid. When it becomes a mass production, prices will drop over time."
Q: With your vast experience in politics, what do you think of Israeli politics these days? Do you ever consider a political comeback?
"No election campaign goes by without someone making me an offer [to return to politics] but I'm not interested. Unfortunately, the Israeli government, and all governments in the Western world, have not been able to run their countries properly in recent years.
"For example, more of the government's national taks are transitioning to the private market or the third sector. We see that associations [are the ones] who take care of the needy, establish settlements in the Negev and in the Galilee, bring immigrants to Israel and provide Israelis with information. All these things should be done by the government.
"The Israeli government lacks vision, ideologies, every matter is personal and is charged with negative sentiments. If I do return one day, it will only happen after we change the government system which will take its power from small [political] parties.
"In my opinion, we need to transition to a regional choice, by district. This will result in higher quality politicians. How so? Because whoever wants to be elected will need to run and convince the people who live in his area and district, and they are the ones who know his activities best. Also, closed primaries should be avoided because they make all kinds of deals possible. That needs to change."
“Autonomy Will Not Happen Until We Start Sharing Data”
In an emerging industry with companies eager to prove their technologies’ worth, Sensei Ag remains form-factor agnostic, meaning that the agtech company remains unbiased towards different farm hardware solutions – focusing more on software and plant biology. Sensei Ag is a market-changing agtech company that develops agile growing solutions through a highly iterative approach to farming, focused on improving the nutritional quality of fruits and vegetables while also reducing production costs. The company combines plant science, computer vision, machine learning, automation and artificial intelligence into its growing systems
In an emerging industry with companies eager to prove their technologies’ worth, Sensei Ag remains form-factor agnostic, meaning that the agtech company remains unbiased towards different farm hardware solutions – focusing more on software and plant biology.
Sensei Ag is a market-changing agtech company that develops agile growing solutions through a highly iterative approach to farming, focused on improving the nutritional quality of fruits and vegetables while also reducing production costs. The company combines plant science, computer vision, machine learning, automation and artificial intelligence into its growing systems.
According to Sensei Ag CEO Sonia Lo, remaining form factor agnostic is key to the company’s mission of providing hyper-nutritious food to as large a consumer base as possible, which it achieves through both vertical farms and greenhouses.
Image from: Sensei Ag
“We believe that the most robust data comes from operating farms of multiple types. So, not just vertical farms, but also low-tech and high-tech greenhouses. And with vertical farms, we are looking at a number of form factors. Our end goal is to be a grower’s resource and know more about growing at scale with different form factors than anyone else.”
The company is also a strong advocate for open data in the vertical farming industry, which is currently lacking, as evidenced by the siloed development of multiple systems and products, some of which cannot be easily integrated into third-party systems.
“There are lots of data flows and increasingly inexpensive farm management systems. The question, then, is the organization of data into intelligence. Intelligence facilitates autonomy, and as we manage data flows, more farms can become autonomous. But I don’t think autonomy will happen until we start sharing data. For example, we saw an automation supplier with a great robot.
The problem was the robot only works in their ecosystem, so you have to buy the whole farming solution in order for the one robot to work. Ideally, that robot would be plug and play and be able to work in greenhouses and vertical farms,” says Sonia.
Image from: Sensei Ag
According to Sonia, open data in the vertical farming industry may currently be restricted by the dominance of venture financing, which has its own return mandates to fulfill and sometimes wants a “winner takes it all” mentality for the ventures it chooses to back. While such financing has allowed the vertical farming industry to emerge, it may ultimately hinder the industry’s scalability and information sharing.
“There is definitely a capital model in Silicon Valley and in venture capital world in general which is not focused on profitability but is focused on technological achievement and market penetration. We saw this in solar and in the renewables industry when multiple venture capital funds invested in solar assets. Then, the bottom fell out because government subsidies fell away in certain jurisdictions.
I hope that agricultural infrastructure currently financed by venture capital will not necessarily follow the same pathway as solar, but will instead find a public-private partnership model. At some point, these farms need to demonstrate a profit for the debt capital markets to allow scale to occur.”
Image from: Sensei Ag
By embracing open data and transparency, Sonia explains that the vertical farming industry can further mature and iterate with technology to continue lowering costs. By continuously collecting and sharing data from different farm forms, the vertical farming industry would have better insights into the true costs which, according to Sonia, “helps drive scale because it enables the finance community to understand how the farms can be risk assessed and financed.”
Looking ahead, Sensei Ag hopes to form partnerships around the world to bring its innovative, data-driven growing systems across the globe. Taking the Middle East, China and Japan as examples, Sonia explained that the goal would be to choose strategic partners in each region whose local knowledge and business prowess would allow Sensei Ag to iterate its technologies appropriately and serve local markets, bringing cost-competitive farming techniques and nutritious, local produce around the world.
Nanobubble Tech Could Revolutionize Aquaculture & Aquaponics
“There is a pressing need to develop an alternative to the current highly energy-intensive conventional aeration,” said Khanal. “Nanobubble technology has a potential to revolutionize aquaculture and aquaponic systems, with higher productivity and resource recovery.” Khanal was initially awarded CTAHR’s Team Science grant, which was critically important to obtaining preliminary data for his grant proposal to NIFA
Image from: University of Hawai’i News
The burgeoning fields of aquaculture and aquaponics hold vast potential for growing food. Yet, the efficacy of these microbial-mediated processes is governed by the availability of dissolved oxygen in water. Generally, oxygen has poor solubility in water, which has a negative effect on fish growth and plant yields.
Almost $200,000 in new funding from the USDA-National Institute of Food and Agriculture’s (NIFA) Water Quantity and Quality Program may expand researchers’ understanding of how nanobubbles could improve aeration and oxygen supplies.
Under the grant, Samir Khanal of the University of Hawaiʻi at Mānoa’s College of Tropical Agriculture and Human Resources (CTAHR ) Department of Molecular Biosciences and Bioengineering, will apply the technology to these aqueous systems. His goal is to uncover new opportunities for improving fish and plant yields—with concomitant improvements in water quality.
Image from: University of Hawai’i News
“There is a pressing need to develop an alternative to the current highly energy-intensive conventional aeration,” said Khanal. “Nanobubble technology has a potential to revolutionize aquaculture and aquaponic systems, with higher productivity and resource recovery.”
Khanal was initially awarded CTAHR’s Team Science grant, which was critically important to obtaining preliminary data for his grant proposal to NIFA.
“Thanks to the CTAHR and NIFA grants, we hope our findings will benefit existing Hawaiʻi businesses, as well as a new generation of growers, across the state and beyond,” Khanal added.
Ensuring Singapore's Food Security Despite the Odds
As with most issues that impact national security in Singapore, it often seems that the odds are stacked against us. Food security — access to safe and nutritious food — is a challenge on several fronts. Singapore is a small city-state with limited resources, with only 1 per cent of land available for food production, and over 90 per cent of food is imported from an increasingly disrupted world. The Covid-19 pandemic has further amplified the gravity of safeguarding food security
Image from: Reuters
As with most issues that impact national security in Singapore, it often seems that the odds are stacked against us. Food security — access to safe and nutritious food — is a challenge on several fronts.
Singapore is a small city-state with limited resources, with only 1 per cent of land available for food production, and over 90 per cent of food is imported from an increasingly disrupted world. The Covid-19 pandemic has further amplified the gravity of safeguarding food security. The city-state has been proactively planning for long-term food security through the Singapore Food Agency’s (SFA) strategy of “three food baskets” — diversifying food sources, growing locally and growing overseas. This approach has served the Republic well in securing a supply of safe food.
DIVERSIFIED SOURCING IS KEY
Singapore’s food importers leverage the nation’s connectivity and the global free trade environment to import from multiple sources in about 170 countries and regions worldwide. Should there be a disruption to any one source, importers are able to tap alternative food sources and ensure supply remains stable. Lockdown measures brought about by Covid-19 underscored Singapore’s vulnerabilities to supply disruptions in food.
It was not by luck that the Republic’s food supply remained stable and market shelves continued to be promptly restocked — it was the result of a deliberate whole-of-government strategy to diversify food sources. To keep the nation’’s diversified food supply lines intact amid the Covid-19 global pandemic, SFA worked closely with the Ministry of Trade and Industry and Enterprise Singapore (ESG) to monitor Singapore’s food supply situation. Together with the Ministry of Foreign Affairs, these economic agencies worked with like-minded countries to maintain open trade links.
LOCAL PRODUCTION AN IMPORTANT BUFFER
SFA drives innovation in local farms with the ambitious goal of producing 30 per cent of Singapore’s nutritional needs by 2030 as part of our “30 by 30” plan. To meet this goal, we need a holistic and long-term approach to space-planning, boosting agri-food technology and developing local agri-specialists. To facilitate and support the establishment of high-technology and productive farms in Singapore, SFA tenders out land based on qualitative criteria such as production capability, production track record, relevant experience and qualifications, innovation and sustainability.
In addition, a masterplan for the greater Lim Chu Kang (LCK) region, spanning about 390ha of land, will be undertaken in consultation with stakeholders over the next two to three years. The redeveloped LCK agri-food cluster will produce more than three times its current food production.
Building on the above efforts to grow Singapore’s high-tech agri-tech sector, SFA will continue to partner with the Economic Development Board and ESG to attract best-in-class global agri-tech companies, as well as to nurture promising homegrown agri-tech companies into local champions and help them to expand overseas.
EXPLORING ALTERNATIVE, UNDERUTILISED SPACES
Urban food solutions are expected to play a key role in global food security. While there are progressive enterprises operating out of farmlands and industrial estates, some agricultural game-changers are also taking root in unconventional areas — indoors, on rooftops and in underutilised spaces.
SFA worked with the Singapore Land Authority to introduce an urban farm at the former Henderson Secondary School site, which was transformed into Singapore’s first integrated space comprising an urban farm, childcare centre and nursing home within a state property. The farm space within the site was awarded in May 2019 to social enterprise City Sprouts, and it has become a vibrant destination for the young and old to learn about urban farming and enjoy a relaxing day out.
Citiponics, the first commercial farm located on a multi-storey car park in a residential neighbourhood, harvested its first yield of vegetables in April 2019. In September 2020, another nine sites atop multi-storey car parks were awarded for urban farming.
The successful bidders included proposals for hydroponic and vertical farming systems with a variety of innovative features, such as the Internet of Things (IoT), blockchain technology and automated climate control. These sites have the potential to collectively produce around 1,600 tonnes of vegetables annually.
Image from: Ciitiponics
TAPPING TECH
The Agriculture Productivity Fund (APF) supports local farms in their capability development and drive towards higher productivity. Through APF, SFA co-funds the adoption of farming systems to better control environmental variables, test-bed technologies and boost production capabilities. Between October 2014 and September 2020, a total of almost S$42 million has been committed to 115 farms.
The Covid-19 pandemic presented greater impetus to speed up local food production capacities. In September 2020, SFA awarded S$39.4 million to nine companies under the 30x30 Express Grant to quickly ramp up food-farm outputs over the next six months to two years. With advanced robotic and digital systems increasingly being used in farming, Singapore’s vegetables farmers have also become innovative agri-engineers and specialists in their own right.
With support from the 30x30 Express Grant, urban farming engineering solutions firm Indoor Farm Factory Innovation will set up an indoor vegetable farm with a vertical integration growth system up to 8m in height in a fully controlled and pesticide-free environment. The farm will leverage artificial intelligence farming systems integrated with IoT monitoring, dosing irrigation and an advanced environmental control system to achieve optimum growing conditions all year round.
Seng Choon, a chicken egg farm that has been in business for more than 30 years, has also proved itself a modernist in its operations. The company uses a computer that scans eggs to ascertain if they are clean; while feeding systems, temperature controls and waste cleaning systems have been automated with SFA’s support. Singapore’s efforts at ensuring food security would not be complete without support from consumers. To boost recognition of local produce among consumers, SFA brought the industry and public together to create a new “SG Fresh Produce” logo.
Farmers have been using this emblem on their packaging since August 2020. A website was also launched to provide a trove of information on locally farmed food. While the Covid-19 pandemic has led to import restrictions, it also helped to accelerate support for local produce. With public support for local farmers and other key measures, Singapore can beat the odds in ensuring food security in this ever-evolving, ever-disrupted world.
Farming Fish in the Sky
Sometime soon, Apollo Aquaculture Group will have one of the world’s largest vertical fish farms up and running in Singapore. Though construction has been delayed by COVID-19, the farm, once complete, will scale eight stories. Crucially, says the company, it won’t only be the farm’s height that sets it apart from the competition
Image from: Hakai Magazine
Sometime soon, Apollo Aquaculture Group will have one of the world’s largest vertical fish farms up and running in Singapore. Though construction has been delayed by COVID-19, the farm, once complete, will scale eight stories. Crucially, says the company, it won’t only be the farm’s height that sets it apart from the competition.
The high-tech facility will produce up to 3,000 tonnes of hybridized grouper, coral trout, and shrimp each year—with an efficiency, measured in fish per tonne of water, that is six times higher than established aquaculture operations in the Southeast Asian city-state, says spokesperson Crono Lee.
In doing so, the company hopes to become a major contributor to an ambitious plan to boost the food security of the small island city-state, which currently imports 90 percent of its food.
According to Ethan Chong Yih Tng, an engineer at the Singapore Institute of Technology who is not involved with the company, this stacking of fish farms is one of the key initiatives that geographically small Singapore is looking at to achieve its ambitious “30 by 30” target for food security—to produce 30 percent of its nutritional needs locally by 2030.
Founded in 1969, Apollo isn’t a new arrival to aquaculture in Singapore. Since the 1970s, it has been breeding ornamental fish across its 300-odd farms in the region. But when Eric Ng took over the family business in 2009, he was quick to diversify into producing marine fish as food, borrowing methods from operations in Germany, Japan, and Israel, says Lee. The outcome was a three-story farm in Lim Chu Kang, a rare green spot on the outskirts of Singapore. That aquaculture facility has been in operation for nearly a decade.
Each level of the Lim Chu Kang operation has two 135-square-meter tanks supplied with seawater by a system that filters, purifies, monitors, and recirculates water through the farm. As a result, only around five percent of the water needs to be replaced when contaminated by effluent from the fish—though Lee says the goal at both the new and existing facilities is to reduce that to zero using aquatic plants that clean and treat water naturally. That’s in contrast to significant levels of waste at Singapore’s traditional onshore pond farms, where farmers routinely clean out and replace entire tanks.
Image from: Apollo Aquaculture Group
In nearly 10 years of operating the Lim Chu Kang farm, which produces up to 200 tonnes of fish per year, the company has built up meticulous data sets on how to increase yields, says Lee—data they will apply to the new, larger facility.
“We understand the amount of water required, the condition of the water, and the amount of feed—measured down to a single gram per cubic meter of water. As a result, we’re able to produce fish in a much shorter time frame, at the right size for the market,” says Lee.
The decision to build this system up, rather than out, is a response to the lack of space in the Asian city-state. “We’re a very small country, and it’s very difficult to secure land,” says Lee. “So rather than building sideways, and expanding horizontally, why not expand vertically?”
Ever larger onshore fish farms is not the only approach the city-state is using to reach its 30 by 30 goal, however. In late 2019, for example, an offshore fish farm opened about five kilometers off Singapore’s Changi Point Ferry Terminal. Using a closed-containment system, it produces around 166 tonnes of barramundi, red snapper, and grouper each year across four tanks. The system “effectively isolates the fishes from the seawater when the quality of the surrounding water turns poor,” says Yih Tng. The self-contained system offers the control of Apollo’s vertical farm without the initial outlay on expensive land, or the high power costs.
Though Lee insists Apollo’s new eight-story farm will be economically competitive with traditional fish farms, high operating costs remain one of the primary reasons that commercial vertical closed loop fish farms remain limited globally.
In the United States, the majority of farms represented by the Recirculating Farms Coalition are outdoors, and much smaller than the Singapore operation, says founder and executive director Marianne Cufone. “That means we’re not as dependent on artificial inputs, such as temperature controls,” she explains.
“A lot of the larger systems sacrifice some of the natural benefits of [recirculating] systems in that they use a lot of energy for cooling, for heating, and for the circulating pumps. That’s not to say these outweigh the benefits, but a smaller, well-designed system can be extremely eco-efficient versus some of the larger-scale ones.”
The increased operational costs of a large facility translate to the price of the product: a 150-gram pack of Apollo’s ready-to-cook hybridised grouper fillet will set a customer back around US $12—roughly double the price of a frozen red grouper on sale at Singapore’s biggest grocer, Fair Price.
However, Cufone adds, large enclosed fish farms are becoming more prevalent in North America and the rest of the world. Few places is that growth more urgent than in Singapore—a fact only exacerbated by the spread of COVID-19.
“COVID-19 has exploded the awareness of [food insecurity] exponentially to local Singaporeans, and right now there’s a big shift in thinking toward local production,” says Lee. A shift that Apollo plans to take full advantage of.
Organic: The Battle for a Single Word
Throughout history, when we see great leaps forward in technology, there are always pushbacks from the old world who want to maintain the status-quo. This can be for a variety of reasons and come from a variety of people. Sometimes, the resistance comes from workers, an example of this would be the fierce opposition from workers who protested the mechanisation of their jobs brought about by the industrial revolution. They were often referred to as luddites because of the propensity to destroy the new machines that were taking their jobs
Throughout history, when we see great leaps forward in technology, there are always pushbacks from the old world who want to maintain the status-quo. This can be for a variety of reasons and come from a variety of people. Sometimes, the resistance comes from workers, an example of this would be the fierce opposition from workers who protested the mechanisation of their jobs brought about by the industrial revolution. They were often referred to as luddites because of the propensity to destroy the new machines that were taking their jobs.
On the other hand, there can be examples of when the resistance to innovations come from industry competitors who don’t want to lose the dominance they once had. An example of this can be seen through the fossil fuel industries continuous attempts to limit the growth of renewables by lobbying governments to pursue policies more favourable to them.
Today we are seeing resistance to a new green revolution through innovation in the vertical farming sector primarily from industry competitors or even protective policy makers. Politico recently reported on a story regarding a fight between a Danish vertical farming company, called Nordic Harvest, and the EU whereby the former was prohibited from labelling their crops as organically produced. The reason given for this was that EU regulation demanded that anything being described as organic had to be produced in soil. This seems to be the antithesis to their Farm to Fork strategy as it heavily handicaps innovative indoor vertical farming companies.
Image from: Nord Harvest
Now this may not seem much like a significant infringement on the indoor vertical farming sector, but what this does is make it more difficult for companies, such as Nordic Harvest, to indicate to consumers their green credentials. Moreover, under the EU’s Green Public Procurement rules, indoor vertical farming companies gain a smaller share in food market than it normally would have due to the ruling on the definition of organics. The unfortunate aspect of this is that words only mean what we define them as, so the personal opinions of the individuals who made this decision are going down this direction for reasons not non-partisan.
Now there may so semi-legitimate reasons to resist the rise of indoor vertical farming, but it is clear that this will be the future of farming and it must not be kneecapped by ill-intentioned actors. The limitations of the sector, such as intense energy use or limited crop varieties, can only be solved if there is financial and legislative support from the powers that be.
This is clear with the recent certification of Sky Greens in Singapore as organic whereby the central government has been forward thinking. Speaking of their decision, the chair of the Food Standards Committee stated:
“The certification may allow local urban farms to expand into markets outside of Singapore. Having a national organic certification will help local urban farms to be on equal footing with the US…”
The Food Standards Committee in Singapore defined organic differently from the EU affirming that as long as they avoid mineral fertilisers or other pesticides and herbicides, which indoor vertical farms operating on controlled environment agriculture adheres to. At full capacity, Sky Greens can produce up to half a tonne of salads daily without LEDs and using gravity to collect rainwater to avoid pests. An important point to note however is that the vast majority of Singapore is urbanised with no domestic traditional rural farming industry.
Image from: Sky Greens
Another problematic component of this EU ruling is that may prove controversial is its impact on trade. Any vertical farming company from a country not with the restrictive rules and the EU that wanted to export their food produced in a vertical farm, they would as need to abide by these rules. For example, with basil being one of the major herbs produced in vertical farms, we often see it being used in Pesto. Unfortunately, this would not be able to be marketed as organic. With the EU being the largest trading bloc in the entire world, this will affect the global fortunes of the sector. We are also seeing this happen in the US but due to many legal appeals and challenges, they have not currently implemented the same rules as the EU.
So, with all this in mind, it is important to be aware of the pushback that will inevitably happen due to a green revolution brought about by innovation in the indoor vertical farming sector. The debate surrounding the definition of the word organic is only the start. We already see concerted efforts to ban synthetic meat companies from using words such as hamburger, hot dog or steak. However, even with this uneven playing field, indoor vertical farming is on track to increase its market share significantly over the next decade and beyond while traditional farming methods are on the decline.
Warehouse Becoming Vertical Farms — And They’re Feeding New Jersey
New Jersey's vertical farms are transforming agriculture by helping farmers meet growing food demand. New Jersey Agriculture Secretary Doug Fisher said that while conventional farming in outdoor fields remains critical, vertical farming has its advantages because of its efficiency and resistance to pests and thus less need for chemicals
Image from: New Jersey 101.5
New Jersey's vertical farms are transforming agriculture by helping farmers meet growing food demand.
New Jersey Agriculture Secretary Doug Fisher said that while conventional farming in outdoor fields remains critical, vertical farming has its advantages because of its efficiency and resistance to pests and thus less need for chemicals.
Vertical farming is the process of growing food vertically in stacked layers indoors under artificial light and temperature, mainly in buildings. These plants receive the same nutrients and all the elements needed to grow plants for food.
Vertical farms are also versatile. Plants may be growing in containers, in old warehouses, in shipping containers, in abandoned buildings.
"That's one of the great advantages — that we can put agriculture in the midst of many landscapes that have lost their vitality," said Fisher.
ResearchandMarkets.com says the U.S. vertical farming market is projected to reach values of around $3 billion by the year 2024.
The one drawback is that its operational and labor costs make it expensive to get up and running.
Image from: AeroFarms
In the past decade, however, vertical farming has become more popular, creating significant crop yields all over the state.
AeroFarms in Newark is the world's largest indoor vertical farm. The farm converted a 75-year-old 70,000-square-foot steel mill into a vertical farming operation. AeroFarms' key products include Dream Greens, its retail brand of baby and micro-greens, available year-round in several ShopRite supermarkets.
Kula Urban Farm in Asbury Park opened in 2014. Vacant lots are transformed into urban farms and there's a hydroponic greenhouse on site. That produce is sold to local restaurants.
Beyond Organic Growers in Freehold uses no pesticides and all seeds and nutrients are organic. There's a minimum of 12,000 plants growing on 144 vertical towers. On its website, it says the greenhouse utilizes a new growing technique called aeroponics, which involves vertical towers where the plant roots hang in the air while a nutrient solution is delivered with a fine mist. It also boasts that by using this method, plants can grow with less land and water while yielding up to 30% more three times faster than traditional soil farming.
Vertical farms in New Jersey help feed local communities. Many are in urban areas and are a form of urban farming.
Fisher predicts that vertical farms will be operational in stores and supermarkets around the state.
"It's continued to expand. There's going to be many, many ways and almost any area in the state has the opportunity to have a vertical farm," Fisher said.
Vertical Farming: Ugandan Company Develops Solution for Urban Agriculture
We speak to Lilian Nakigozi, founder of Women Smiles Uganda, a company that manufactures and sells vertical farms used to grow crops in areas where there is limited space
We speak to Lilian Nakigozi, founder of Women Smiles Uganda, a company that manufactures and sells vertical farms used to grow crops in areas where there is limited space.
Image from: How We Made It in Africa
1. How Did You Come Up with the Idea to Start Women Smiles Uganda?
Women Smiles Uganda is a social enterprise formed out of passion and personal experience. I grew up with a single mother and eight siblings in Katanga, one of the biggest slums in Kampala, Uganda. I experienced hunger and poverty where we lived. There was no land for us to grow crops and we didn’t have money to buy food. Life was hard; we would often go to sleep on empty stomachs and our baby sister starved to death.
Growing up like that, I pledged to use my knowledge and skills to come up with an idea that could solve hunger and, at the same time, improve people’s livelihoods, particularly women and young girls living in the urban slums. In 2017, while studying business at Makerere University, I had the idea of developing a vertical farm. This came amid so many challenges: a lack of finance and moral support. I would use the money provided to me for lunch as a government student to save for the initial capital of my venture.
I managed to accumulate $300 and used this to buy materials to manufacture the first 20 vertical farms. I gave these to 20 families and, in 2018, we fully started operations in different urban slums.
2. Tell Us About Your Vertical Farms and How They Work.
Women Smiles vertical farms are made out of wood and recycled plastic materials. Each unit is capable of growing up to 200 plants. The product also has an internal bearing system which turns 360° to guarantee optimal use of the sunlight and is fitted with an inbuilt drip irrigation system and greenhouse material to address any agro-climatic challenges.
The farms can be positioned on a rooftop, veranda, walkway, office building or a desk. This allows the growth of crops throughout the year, season after season, unaffected by climatic changes like drought.
In addition, we train our customers on how to make compost manure using vermicomposting and also provide them with a market for their fresh produce.
Image from: How We Made It in Africa
3. Explain Your Revenue Model.
Women Smiles Uganda generates revenue by selling affordable, reliable and modern vertical farms at $35, making a profit margin of $10 on each unit. The women groups are recruited into our training schemes and we teach them how to use vertical farming to grow crops and make compost manure by vermicomposting. Women groups become our outgrowers of fruits and vegetables. We buy the fresh produce from our outgrowers and resell to restaurants, schools and hotels.
We also make money through partnering with NGOs and other small private organisations to provide training in urban farming concepts to the beneficiaries of their projects.
4. What Are Some of the Major Challenges of Running This Business?
The major challenge we face is limited funds by the smallholder farmers to purchase the vertical farms. However, we mitigate this by putting some of them into our outgrower scheme which helps them to generate income from the fresh produce we buy. We have also linked some of them to financial institutions to access finance.
5. How Do You Generate Sales?
We reach our customers directly via our marketing team which moves door to door, identifying organised women groups and educating them about the benefits of vertical farming for improved food security. Most of our customers are low-income earners and very few of them have access to the internet.
However, we do also make use of social media platforms like Facebook to reach out to our customers, especially the youth.
In addition, we organise talk shows and community gatherings with the assistance of local leaders with whom we work hand in hand to provide educational and inspirational materials to people, teaching them about smart agriculture techniques.
6. Who Are Your Main Competitors?
Just like any business, we have got competitors; our major competitors include Camp Green and Spark Agro-Initiatives.
Image from: The Conversation
7. What Mistakes Have You Made in Business and What Did You Learn From Them?
As a victim of hunger and poverty, my dream was for every family in slums to have a vertical farm. I ended up giving some vertical farms on credit. Unfortunately, most of them failed to pay and we ended up with huge losses.
This taught me to shift the risk of payment default to a third party. Every customer who may need our farms on credit is now linked to our partner micro-finance bank. By doing this, it is the responsibility of the bank to recover the funds from our customers and it has worked well.
8. Apart from This Industry, Name an Untapped Business Opportunity in Uganda.
Manufacturing of cooler sheds for the storage of perishable agricultural produce is one untapped opportunity. Currently, Ugandan smallholder farmers lose up to 40% of their fresh produce because of a lack of reliable cold storage systems.
Providing a cheap and reliable 24/7 cold storage system would dramatically reduce post-harvest losses for these farmers.
Feeding Leeds: A Fair and Self-Sustaining Food System for the City
A bold vision for feeding the population of Leeds would transform the city into a far more food secure, fair and sustainable place to live. Analysts from the University of Leeds’ Global Food and Environment Institute studied the city’s food system to assess its resilience in the face of supply chain and delivery disruptions caused by severe weather, climate change and events such as the COVID-19 pandemic and Brexit
Image from: University of Leeds
A bold vision for feeding the population of Leeds would transform the city into a far more food secure, fair and sustainable place to live.
Analysts from the University of Leeds’ Global Food and Environment Institute studied the city’s food system to assess its resilience in the face of supply chain and delivery disruptions caused by severe weather, climate change and events such as the COVID-19 pandemic and Brexit.
The urban food system includes all the activities involved in the production, distribution and consumption of food within a city.
They mapped and analysed publicly available data relating to agricultural production and human health in the metropolitan district and discovered that 48.4% of the city’s total calorific demand can be met by current commercial food production activities.
This is relatively high for such an urbanised space, but there is little diversity in what is being produced. Three cereal crops (wheat, barley, oats) dominate the Leeds production system, reflecting a post-war food system that focused on energy supply. This means that most of the fruits and vegetables consumed in the city are transported in from elsewhere.
The researchers’ findings also show that the most deprived areas of the district, which have higher rates of obesity, diabetes, and cardiovascular disease, are also likely to be the first to be impacted by supply disruptions. The resulting food shortages can increase prices, and people on low incomes may not have the option to travel to larger supermarkets or afford to bulk buy.
The researchers say there are no quick and easy options for significantly increasing the security, fairness, or sustainability of the food system supplying Leeds.
But they say the metropolitan district’s sizeable number of farmers, manufacturers, suppliers, and food services could all contribute to improving its food resilience by creating a system which provides easy access to healthy foods, shares energy, reuses water and nutrients and repurposes local infrastructure and resources.
Caroline Orfila, who led the study, published today in the journal Food Security, is Professor of Plant Biochemistry and Nutrition in the School of Food Science and Nutrition. She said: “Our work demonstrates the inequalities in food production and dietary health.
“The local food production system can only provide around 50% of the calories needed by the population, highlighting that ‘eating local’ is not currently possible for everyone. In particular, the local food system would not provide sufficient protein or fats. The lack of food diversity suggests current food production is also unlikely to meet vitamin and mineral requirements.
“Any disruptions to food production, distribution or retail, from flooding, longer term climate change, COVID-19 or Brexit, is likely to impact those in deprived areas the most.
“Disruptions tend to cause shortages in some food categories, which then increase food prices. People on low incomes spend more of their income on food; any increases in food prices will limit what they can afford to buy.
“People in deprived areas have limited choice of where to buy foods, they may not have private transport to access larger supermarkets or access to online shopping. They may also not have the cash flow or storage space to buy items in bulk, relying on what is available.
“Interventions are needed to level up those areas.”
Researchers identified more than 1,000km2 of warehousing, derelict land, and unused floor space in abandoned buildings, with direct or possible connections to renewable energy and water.
Half of this land lay near food banks, community centres and numerous food processors and outlets.
The land could potentially be used for no waste innovative farming techniques, including vertical food farms, where crops are grown in vertically stacked layers; green walls, where plants grow on vertical surfaces, and rooftop agriculture, where fresh produce is grown on top of buildings.
The study found that within the metropolitan district of Leeds there is substantial food activity with more than 5,500 businesses and charities supplying fresh and prepared food, including fast food providers, restaurants, and supermarkets. Some 23 food banks are located within the inner-city area.
There are almost 100 hectares of allotment controlled by Leeds City Council, and approximately 39 hectares of private allotment and community growing areas in the Leeds Metropolitan District.
Lead author Dr Paul Jensen, also from Leeds' School of Food Science and Nutrition at the University of Leeds, said: “We found there are numerous underutilised city assets that could be incorporated into a resource efficient urban food ecosystem, which could include a mix of vertical farming, hydroponics, or more conventional growing methods.
“Most notably, many of these areas are within those suffering most from food poverty, diet related health issues and a limited intake of fruit and vegetables - those who are usually the first to suffer during a crisis situation.”
The research identified locations for ‘food hubs’ that connect producers to consumers and discuss the need for a coordinated approach between producers, government, charitable groups and consumers in creating a more sustainable food system.
The research was carried out with FoodWise Leeds, a not-for-profit campaign by Leeds City Council, the University of Leeds, businesses and charities to address food health and sustainability issues.
FoodWise Leeds co-ordinator Sonja Woodcock, said: “This past year has highlighted how vulnerable the local food system is. Taking a coordinated approach and implementing available policy levers, such as including local food within public procurement contracts, increasing access to land for both commercial and community food growing, as well as investing in cooking and food skills will help to create a more resilient and fair local food system.”
Professor Orfila added: “These findings are significant because it shows the vulnerability and inequality of UK cities and urban food systems. The situation in Leeds mirrors the situation in many other cities worldwide.”
Professor Steve Banwart, Global Food and Environment Institute Director said: “The results of this study provide essential evidence to guide access to nutrition for the entire population. The project dramatically changes our view of what is a city and what is a farm and catalyses our partnerships to build a more resilient community.”
Further Information
‘Mapping the Production-Consumption Gap of an Urban Food System: An Empirical Case Study of Food Security and Resilience’ and is published on 8 February in the journal Food Security. It is available online here:https://link.springer.com/article/10.1007/s12571-021-01142-2.
For media enquiries, contact University of Leeds press office via pressoffice@leeds.ac.uk.
The Future of the Food Supply Chain Lives on a Rooftop in Montreal
The world’s biggest commercial rooftop greenhouse sits atop a former Sears warehouse in a semi-industrial northwestern quarter of Montreal. Early every morning, staff pick fresh vegetables, then bring them downstairs, where they get packed into heavy-duty plastic totes along with the rest of the day’s grocery orders.
Image from: Lufa Farms
The world’s biggest commercial rooftop greenhouse sits atop a former Sears warehouse in a semi-industrial northwestern quarter of Montreal. Early every morning, staff pick fresh vegetables, then bring them downstairs, where they get packed into heavy-duty plastic totes along with the rest of the day’s grocery orders.
Tablets loaded with custom pick-and-pack software tell them where to put what: This basket has lettuce, tomatoes, and cucumbers, plus some chicken, eggs, and milk. The next one has eggplant, cashew Parmesan, tomato sauce, fresh pasta, and vegan ground round crumble. Whatever Luca doesn’t grow in its four greenhouses comes from local farms and producers, mostly from within 100 miles.
This is a modern foodie’s dream: a tech-forward online shop full of locally grown, pesticide-free, ethically-sourced products at reasonable price points, delivered once a week to either your doorstep or a local pickup point in your neighborhood.
It’s stunning to think Lufa was founded by two people who’d never even grown a tomato before, let alone sold one. “We said, ‘Instead of learning how the food world works, let’s just come up with what we feel the food world should be,’” says Mohamed Hage, 39, who cofounded Lufa with Lauren Rathmell in 2009.
To them, it looked like this: rooftop greenhouses that bring agriculture into cities. No pesticides, herbicides, or fungicides. Composting their green waste. Selling direct-to-consumer the same day the food is harvested. Capturing and reusing rainwater. Reusable packaging.
That’s exactly what they now have—and they feed a portion of Montreal, the second-biggest city in Canada, with it.
Image from: Lufa Farms
Back in the warehouse, workers poke at their tablets, checking off items as they’re packed into the boxes.
Customers—Lufavores, as the company calls them—typically place their orders a few days before delivery through the online store, dubbed “the Marketplace,” which Lufa built from scratch in 2012. That’s how Lufa’s suppliers know how much product to provide: They get forecasts first, then final order numbers, through their Lufa software. Some items, like frozen meat, can be delivered to the warehouse once a week. Others, like bread, arrive fresh every day.
Artisanal Montreal bakery la Fabrique Arhoma started supplying Lufa with bread and pastries about six years ago, co-owner Ariane Beaumont tells Fortune. Today, they hand-make 6,000 individual items a day for Lufa. Beaumont said Lufa now accounts for between 30% to 40% of her commercial sales; since pandemic shutdowns, a lot of the product destined for restaurants got redirected to Lufa. “They’re an exceptional company. I don’t know how they do it,” Beaumont says. “And they pay the fastest, too.”
Technology is the underpinning of Lufa’s success, and the owners know it.
“We see ourselves as a technology company, in the sense that we solve with software,” Rathmell, 32, says. They didn’t really have any other choice. To fulfill that dream they had back in 2009—years before COVID-19 forced most grocery stores to enable online shopping—they had to do it themselves.
“Nothing off-the-shelf can be applied to what we do, because it’s so complex,” Rathmell notes. “We harvest food ourselves; we gather from farmers and food makers throughout the province; most of it’s arriving just in time throughout the night to be packed in baskets for that day, and every order is fully unique.”
Lufa now has a team of eight programmers working on software and systems that manage e-commerce, warehouse management, routing, customer relationships, supplier fulfillment, pick-and-pack, vendor payments, delivery ETAs, and more.
Those technologies were tested on that fateful Friday the 13th last March, when Quebec and Canada each announced their first waves of COVID-19 lockdowns. People panicked, rushing to the grocery store to stock up on flour and toilet paper.
Online, new sign-ups for Lufa’s weekly grocery baskets exploded, and existing subscribers began ordering more than they’d ever ordered before—all while Lufa’s pickup points were shutting down. “We essentially doubled overnight,” Rathmell recalls. Lufa was forced beyond its operational capacity, and the cracks started showing in the systems and software that had, until that point, done a fine job getting the company by.
Lufa temporarily closed the website and opened a wait list. The staff analyzed the pandemic’s trajectory and how they had to adapt at each step; reconfigured their warehouse floor to station workers further apart; then relaunched at the capacity they could handle, gradually scaling each week until they hit their usual stride. Today, they’re humming along at 25,000 baskets a week.
Leading with tech helped make them nimble and strategic during those hairy early pandemic days, said Hage and Rathmell. After some recalibrations and new developments, their software and processes can now handle more customers, vendors, and processes—critical elements as the company continues to scale its greenhouse operations. In August of 2020, Lufa opened its fourth greenhouse, doubling its square footage. The four greenhouses combined produce 57,000 pounds of food a week. A fifth is planned for this year.
“Our objective at Lufa is to get to the point where we’re feeding everyone in the city,” Hage says.
And after Montreal? They’re planning on a yet to be determined second site in the northeastern pocket of North America, ideally this year. “Our vision is to grow food closer to where people live, and grow it more sustainably,” Rathmell says.
Image from: Lufa Farms
Bringing high-yield crop production into cities is a smart answer to many modern challenges in environmental and human health.
Mark Lefsrud, an associate professor of agricultural and environmental sciences at McGill University, points out that embracing technologies like LEDs and automation to grow indoors and in urban greenhouses means shorter supply chains, better nutritional integrity, less food waste, and reduced vulnerability to climate swings. In cities fed primarily by low-carbon energy (hydroelectricity in Montreal’s case), indoor growing versus importation becomes even more of a no-brainer.
“I’ve been working in the controlled environment and greenhouse industry for 20-some years, and having a company like Lufa has brought a lot of attention to not just urban agriculture, but also the need for greenhouse production,” Lefsrud says, adding that Lufa’s success has prompted more government investment in the sector overall.
“The Quebec government now takes this as a serious venture system, which then means that the students that I’m training, and research we’re doing here at the university, now have employment and have the possibility of setting up their own system,” says the McGill professor.
That idea, of developing more vertically integrated food systems, is a passion of Hage’s—not only for the idea of cutting out production and transformation middlemen to improve profit margins, but also to improve quality, traceability, and ultimately the ethics of food production.
“You know, every time we talk to someone about it, we feel like it’s the ’80s, and we’re holding a big solar panel trying to convince the room that this is the future,” Hage says.
As the larger agricultural industry catches on to vertical integration, it seems Hage and Rathmell are no longer mad scientists with a crazy dream. Instead, they are the voice of reason—and a new generation of food.
As the larger agricultural industry catches on to vertical integration, it seems Hage and Rathmell are no longer mad scientists with a crazy dream. Instead, they are the voice of reason—and a new generation of food.
As the larger agricultural industry catches on to vertical integration, it seems Hage and Rathmell are no longer mad scientists with a crazy dream. Instead, they are the voice of reason—and a new generation of food.
NASA's Challenge To Grow Food In Space Can Win You Up To $500,000
There are thousands of bizarre challenges doing the rounds on the internet. These unique challenges soon go viral on the internet, with countless participants hopping on board. A number of these challenges also involve some form of food. If you're a food innovator who's looking for the next interesting challenge to take up, NASA (National Aeronautics and Space Administration) may have something for you. The NASA, in collaboration with Canada's CSA (Central Space Agency), has launched a 'Deep Space Food Challenge'. The one-of-a-kind competition seeks to find food production technologies which are sustainable in long duration missions to outer space.
NASA has launched a 'Deep Space Food Challenge' to prompt innovation of food production techniques and technologies viable in outer space.
Image from: Deep Space Food
There are thousands of bizarre challenges doing the rounds on the internet. These unique challenges soon go viral on the internet, with countless participants hopping on board. A number of these challenges also involve some form of food. If you're a food innovator who's looking for the next interesting challenge to take up, NASA (National Aeronautics and Space Administration) may have something for you.
The NASA, in collaboration with Canada's CSA (Central Space Agency), has launched a 'Deep Space Food Challenge'. The one-of-a-kind competition seeks to find food production technologies which are sustainable in long duration missions to outer space.
Our cargo resupply missions can only go so far! That's why we need your help to design a food system to keep our astronauts feed during long duration space exploration.
— NASA Wallops (@NASA_Wallops) January 30, 2021
Check out the @NASAPrize Deep Space Food Challenge: https://t.co/9mxtZXbwaC pic.twitter.com/izU8nSqPDc
A short video explaining the purpose behind the challenge was shared by the official handle. The 56-second clip elaborated on how astronauts embarking on lunar space exploration missions usually rely on pre-packaged meals or resupply of food through shuttles from Earth.
Thus, creating a brand, new food production system with minimal input and nutritious output with minimal wastage can go a long way in fuelling longer duration space explorations. The challenge's focus is on identifying food production technologies that can help feed a crew of four astronauts and help fill food gaps for a three-year round-trip mission with no resupply required from Earth.
These innovative food production methods may also help communities on Earth living in harsh conditions and extreme climates. This could also help tackle food insecurity in the future, which is one of the biggest issues that loom large today. "Solutions identified through this Challenge could support these harsh environments, and also support greater food production in other milder environments, including major urban centres where vertical farming, urban agriculture and other novel food production techniques can play a more significant role," stated the Deep Space Food Challenge's official website.
.@NASA & @csa_asc are launching a Deep Space Food Challenge to develop food production tech in space.
— NASA STI Program (@NASA_STI) January 28, 2021
Hey @GuyFieri, how about Diners, Drive-Ins, Dives & Deep Space? #STIdocs #Flavortown 🚀🥘
Read about it: https://t.co/fnz80uwpJT
See research: https://t.co/18q6RG3L2G pic.twitter.com/lSRTiiAFes
Registrations for the challenge close on 28th May, and submissions are due 30th July, 2021. Winners of Phase 1 of the challenge will be announced in the month of September this year. The prize money for winners of Phase 1 can go up to USD 500,000 (Rs. 3.64 crores approximately). So, if you have an exciting idea to produce food which could help future space missions - you know what to do!
Is AppHarvest the Future of Farming?
In this video from Motley Fool Live, recorded on Jan. 28, Industry Focus host Nick Sciple and Motley Fool contributor Lou Whiteman discuss AppHarvest, one such SPAC that is looking to disrupt the agriculture industry. Here are the details on what AppHarvest wants to do, and a look at whether the company represents the future of farming.
Special purpose acquisition companies, or SPACs, are red-hot right now, with investors clamoring to get into promising young companies.
In this video from Motley Fool Live, recorded on Jan. 28, Industry Focus host Nick Sciple and Motley Fool contributor Lou Whiteman discuss AppHarvest, one such SPAC that is looking to disrupt the agriculture industry. Here are the details on what AppHarvest wants to do, and a look at whether the company represents the future of farming.
Nick Sciple: One last company I wanted to talk about, Lou, and this is one I think it's -- you pay attention to, but not one I'm super excited to run in and buy. It was a company called AppHarvest. It's coming public via a [SPAC] this year. This vertical farming space. We talked about Gladstone Land buying traditional farmland. AppHarvest is taking a very different approach, trying to lean into some of the ESG-type movements.
Lou Whiteman: Yeah. Let's look at this. It probably wouldn't surprise you that the U.S. is the biggest global farm exporter as we said, but it might surprise you that the Netherlands, the tiny little country, is No. 2. The way they do that is tech: Greenhouse farm structure. AppHarvest has taken that model and brought it to the U.S. They have, I believe, three farms in Appalachia. The pitches can produce 30x the yields using 90% less water. Right now, it's mostly tomatoes and it is early-stage. I don't own this stock either. I love this idea. There's some reasons that I'm not buying in right now that we can get into. But this is fascinating to me. We talked about making the world a better place. This is the company that we need to be successful to make the world a better place. The warning on it is that it is a SPAC. So it's not public yet. Right now, I believe N-O-V-S. That deal should close soon. [Editor's note: The deal has since closed.] I'm not the only one excited about it. I tend not to like to buy IPOs and new companies anyway. I think the caution around buying into the excitement applies here. There is a Martha Stewart video on their website talking up the company, which I love Martha Stewart, but that's a hype level that makes me want to just watch and see what they produce. This is just three little farms in Appalachia right now and a great idea. This was all over my watchlist. I would imagine I would love to hold it at some point, but just be careful because this is, as we saw SPACs last year in other areas, people are very excited about this.
Sciple: Yeah. I think, like we've said, for a lot of these companies, the prospects are great. I think when you look at the reduced water usage, better, environmentally friendly, all those sorts of things. I like that they are in Appalachia. As someone who is from the South, I like it when more rural areas get some people actually investing money there. But again, there's a lot of execution between now and really getting to a place where this is the future of farming and they're going to reach scale and all those sorts of things. But this is a company I'm definitely going to have my radar on and pay attention to as they continue to report earnings. Because you can tell yourself a story about how this type of vertical farming, indoor farming disrupts this traditional model, can be more efficient, cleaner, etc. Something to continue paying attention to as we have more information, because this company, like you said, Lou, isn't all the way public yet. We still got to have this SPAC deal finalized and then we get all our fun SEC filings and quarterly calls and all those sorts of things. Once we have that, I will be very much looking forward to seeing what the company has to say.
Whiteman: Right. Just to finish up along too, the interesting thing here is that it is a proven concept because it has worked elsewhere. The downside of that is that it needed to work there. Netherlands just doesn't have -- and this is an expensive proposition to get started, to get going. There's potential there, but in a country blessed with almost seemingly unlimited farmland for now, for long term it makes sense. But in the short term, it could be a hard thing to really get up and running. I think you're right, just one to watch.
Signify Adds Automatic Intensity Adjustment Plus Year-Long Recipe Modulations To Horticultural Controls
There’s something for both the greenhouse and the vertical farm in the GrowWise tweaks, which in some cases rely on tying to other systems’ sensors.
The Signify toplights at Belgium’s De Glastuin lettuce greenhouse automatically dim or brighten as daylight levels changes. (Photo credit: All images courtesy of Signify.)
Signify has enhanced the control system for its greenhouse LED lighting so that toplights can react immediately to changes in daylight conditions and adjust brightness accordingly. The company has also added year-long control settings intended to allow vertical farmers — but not greenhouses — to program seasonal variations in LED spectral content over a 365-day period.
Both upgrades are intended to reduce manual labor and improve overall cost efficiencies, Signify said.
Until now, greenhouse farmers could dim or brighten their Signify toplights by instructing the lights to do so via the control system, called GrowWise. Signify has now modified GrowWise software so that it can take readings from daylight sensors that are part of separate systems. GrowWise then instantly and automatically adjusts artificial light intensity emitted by the toplights, called Philips GreenPower LED.
“The lighting can be used much more efficiently since it gives us the flexibility to reduce light levels at any moment we need to,” said Wouter de Bruyn, the owner of Belgian lettuce grower De Glastuin, an early user of the new automatic feature.
Whereas Signify is known in office settings to build sensors into its smart luminaires, the GrowWise controls make use of sensors that are part of climate control systems and greenhouse management systems from companies such as Priva, Hoogendern Growth Management, and Ridder, all based in Holland.
Planet Farms’ Luca Travaglini backs up Signify’s point that prescribing a year of spectral content improves efficiency and helps keep down manual labor costs in controlled environment agriculture (CEA) operations such as vertical farms.
“The climate computer is equipped with a daylight sensor that sends actual light measurements to the GrowWise Control System so we can adapt our light levels automatically to ensure an even light level throughout the day and season,” de Bruyn said at De Glastuin, based in Kontich.
“Dynamic lighting in a greenhouse is the next step in improving the cost efficiency and quality for the cultivation process,” said Udo van Slooten, business leader, horticulture LED solutions at Signify. “It allows growers to effortlessly maintain a consistent level of light throughout the day to produce the best possible crops. The system compensates for cloudy weather and creates a more controlled growing environment for your crop.”
In another upgrade to GrowWise, vertical farmers who want to prescribe modulations in spectral content are no longer limited to 24 hours of looped recipe cycles. Rather, they can order up a year’s worth of shifts for controlled environment agriculture (CEA) operations.
The year-long programming feature is aimed at vertical farmers rather than at greenhouses because the lights that Signify provides for vertical farms support controllable spectral changes, whereas the greenhouse toplights do not. Signify refers to its GreenPower LED vertical farm lights as “production modules” rather than as “toplights.” Toplights and production modules can both be programmed for intensity over a year, but the intention of the year-long feature is oriented toward spectral content.
Compared to greenhouses, vertical farms tend to make much less, if any, use of natural light. In vertical farms, the lights are mounted much closer to the crop in stacked shelves.
One of the first users of the year-round feature is Italy’s greens and lettuce grower Planet Farms.
“Now we can easily create custom light recipes and set them to run year-round to provide the right light recipe with the right light intensity at the right time throughout the crop’s growth cycle,” said Planet Farms co-founder Luca Travaglini. “By automating our full light strategy during the growth cycle, for the whole year, we can run our operations very efficiently and keep our manual labor costs low. That makes it easier for us to maintain consistent quality as we scale up our production.”
The horticultural market is a key growth sector for Signify, especially as it maps out a strategy to maintain profits in the pandemic economy, in which last week it reported a yearly rise amid rigorous cost controls that now include a small number of layoffs. CEO Eric Rondolat is targeting a big chunk of what he has quantified as a $2 billion general horticultural lighting market by 2023.
MARK HALPER is a contributing editor for LEDs Magazine, and an energy, technology, and business journalist (markhalper@aol.com).